Atomic Force Microscopy Fig2 schematic of AFM operation
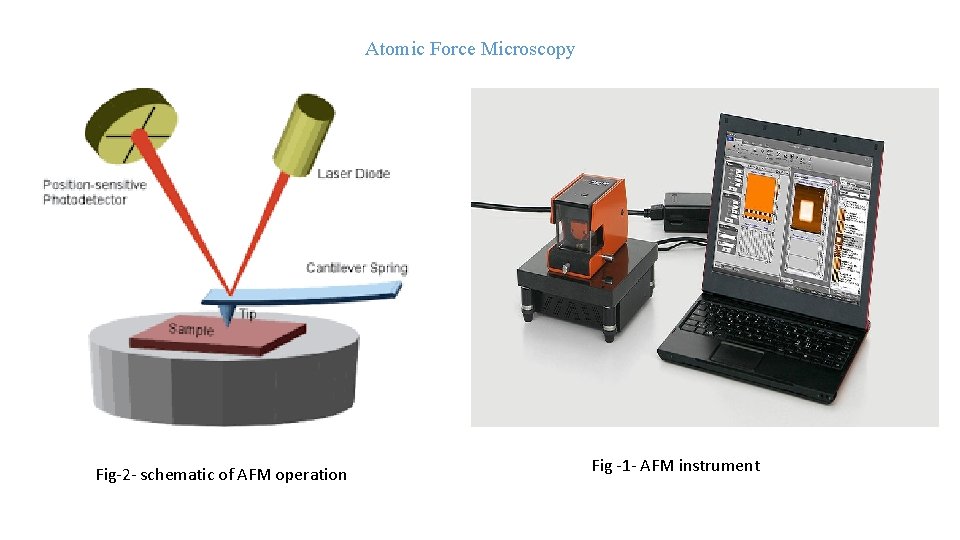
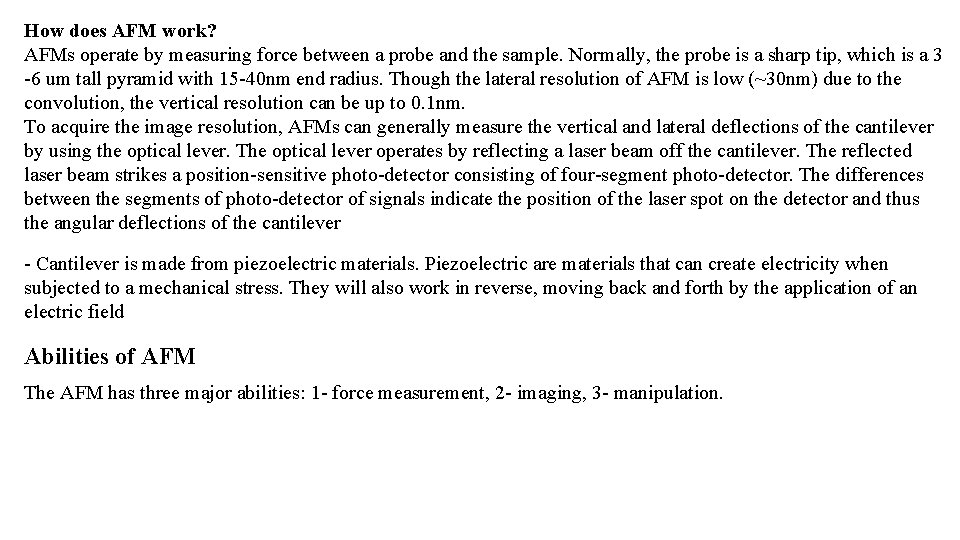
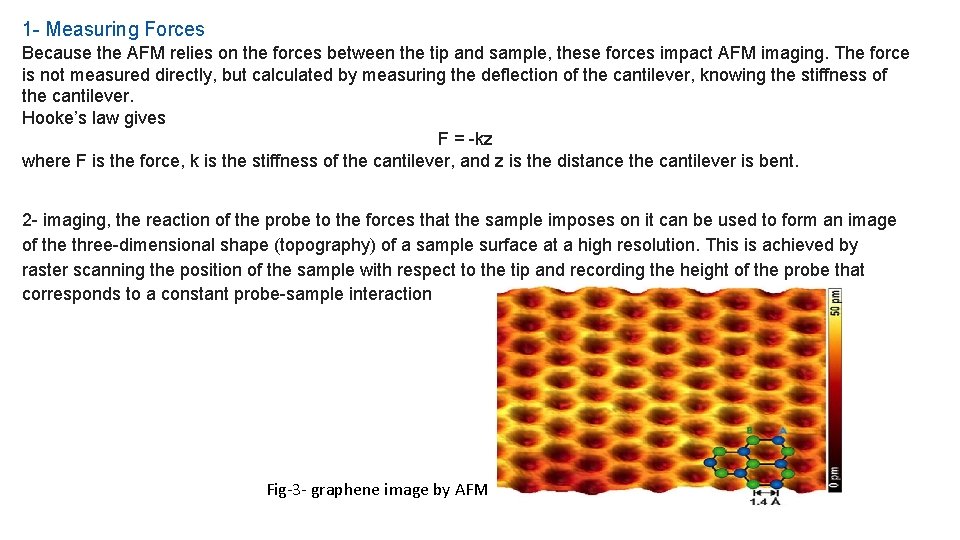
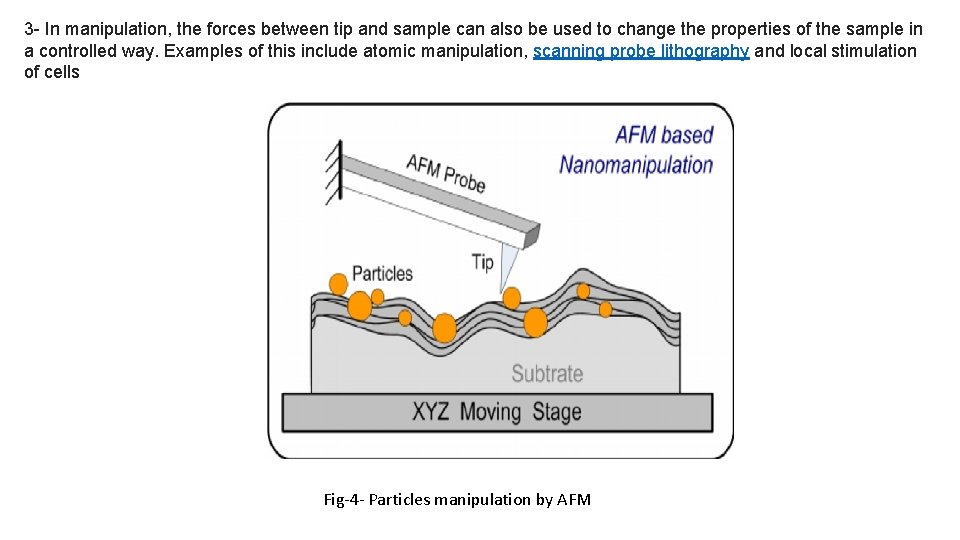
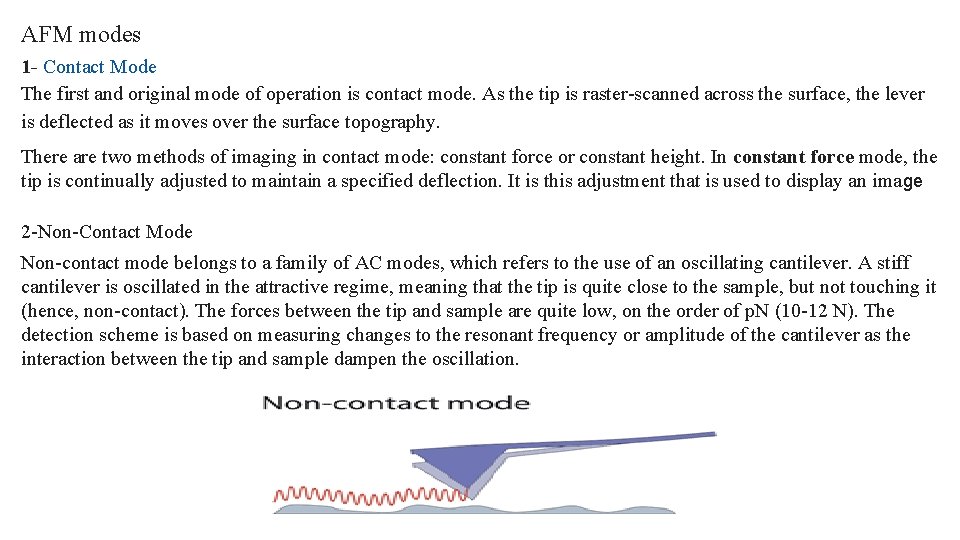
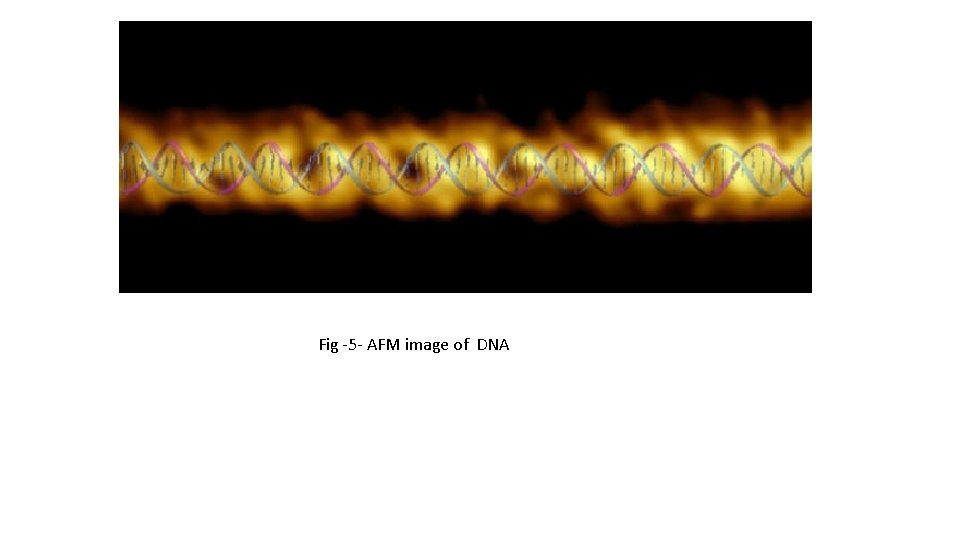
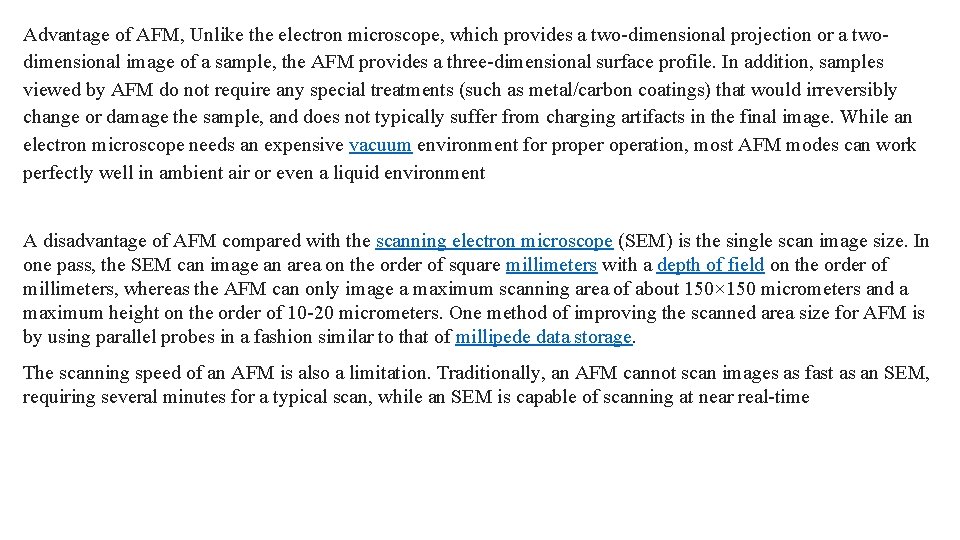
- Slides: 7
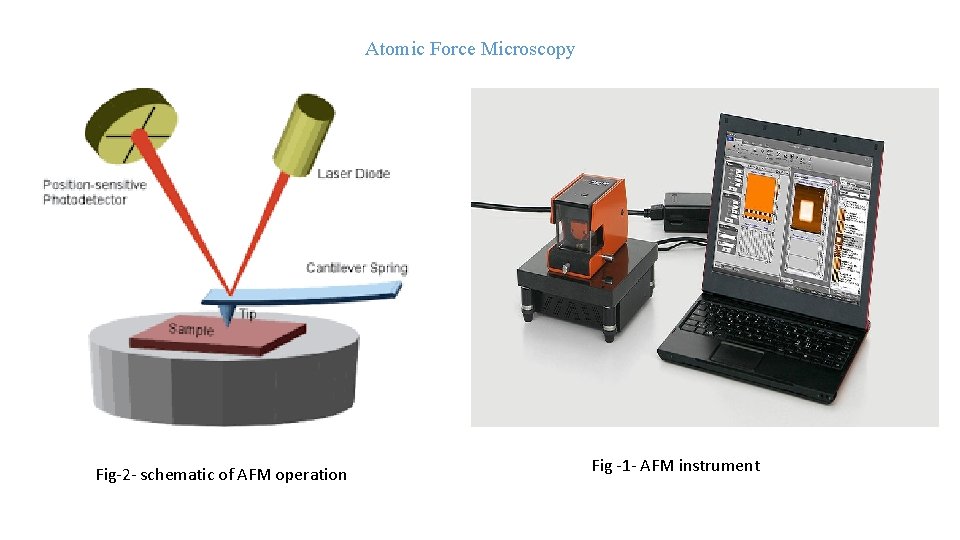
Atomic Force Microscopy Fig-2 - schematic of AFM operation Fig -1 - AFM instrument
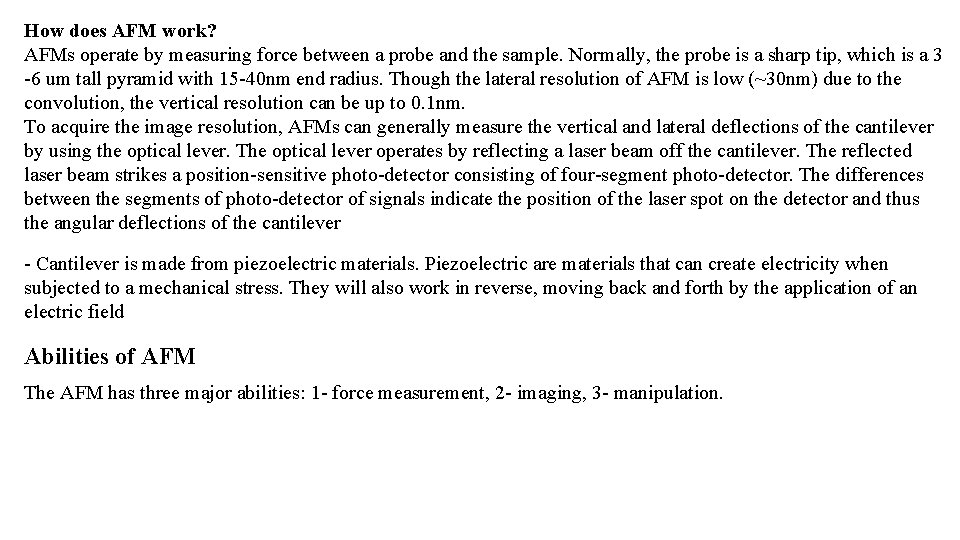
How does AFM work? AFMs operate by measuring force between a probe and the sample. Normally, the probe is a sharp tip, which is a 3 -6 um tall pyramid with 15 -40 nm end radius. Though the lateral resolution of AFM is low (~30 nm) due to the convolution, the vertical resolution can be up to 0. 1 nm. To acquire the image resolution, AFMs can generally measure the vertical and lateral deflections of the cantilever by using the optical lever. The optical lever operates by reflecting a laser beam off the cantilever. The reflected laser beam strikes a position-sensitive photo-detector consisting of four-segment photo-detector. The differences between the segments of photo-detector of signals indicate the position of the laser spot on the detector and thus the angular deflections of the cantilever - Cantilever is made from piezoelectric materials. Piezoelectric are materials that can create electricity when subjected to a mechanical stress. They will also work in reverse, moving back and forth by the application of an electric field Abilities of AFM The AFM has three major abilities: 1 - force measurement, 2 - imaging, 3 - manipulation.
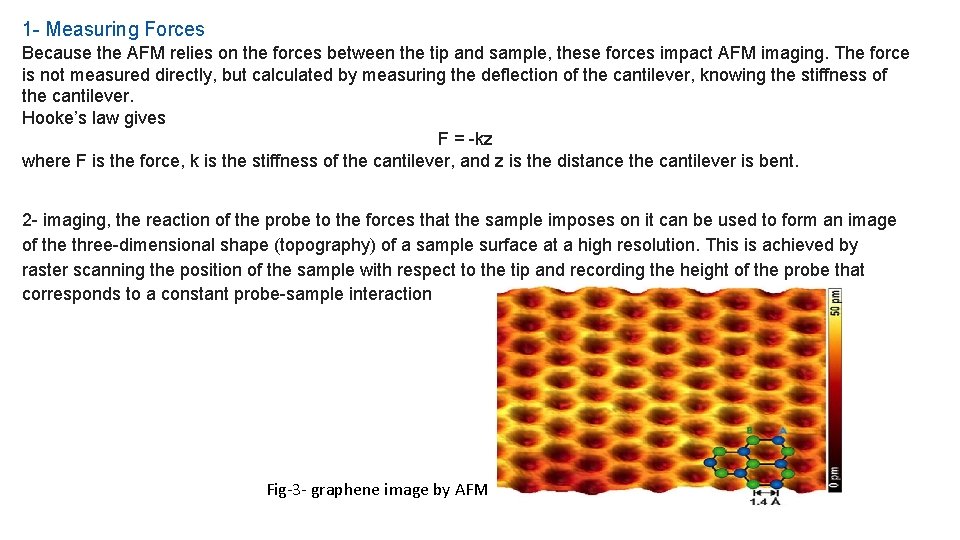
1 - Measuring Forces Because the AFM relies on the forces between the tip and sample, these forces impact AFM imaging. The force is not measured directly, but calculated by measuring the deflection of the cantilever, knowing the stiffness of the cantilever. Hooke’s law gives F = -kz where F is the force, k is the stiffness of the cantilever, and z is the distance the cantilever is bent. 2 - imaging, the reaction of the probe to the forces that the sample imposes on it can be used to form an image of the three-dimensional shape (topography) of a sample surface at a high resolution. This is achieved by raster scanning the position of the sample with respect to the tip and recording the height of the probe that corresponds to a constant probe-sample interaction Fig-3 - graphene image by AFM
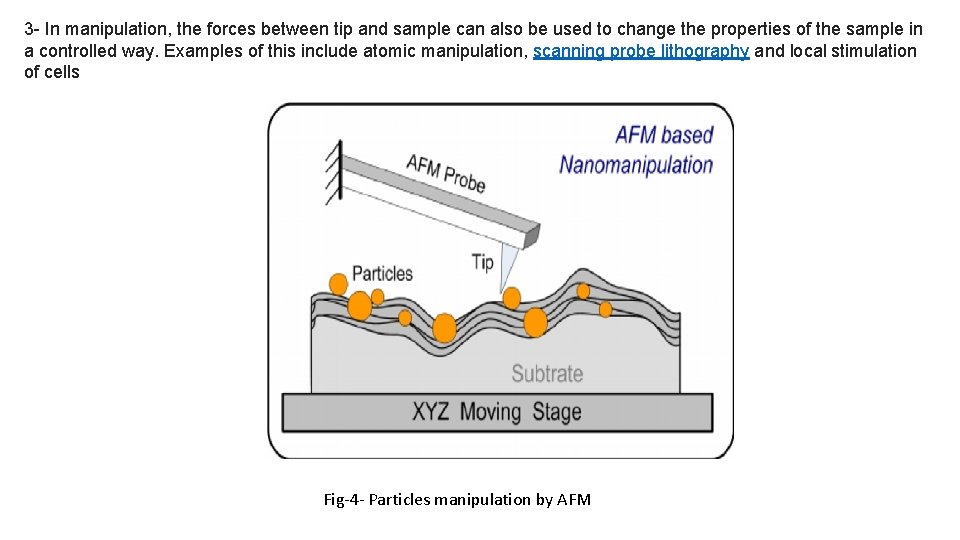
3 - In manipulation, the forces between tip and sample can also be used to change the properties of the sample in a controlled way. Examples of this include atomic manipulation, scanning probe lithography and local stimulation of cells Fig-4 - Particles manipulation by AFM
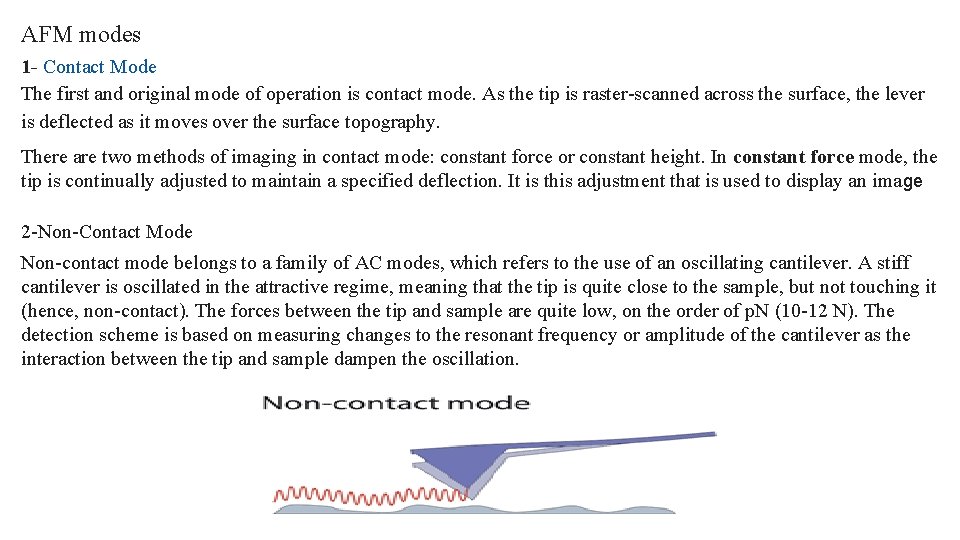
AFM modes 1 - Contact Mode The first and original mode of operation is contact mode. As the tip is raster-scanned across the surface, the lever is deflected as it moves over the surface topography. There are two methods of imaging in contact mode: constant force or constant height. In constant force mode, the tip is continually adjusted to maintain a specified deflection. It is this adjustment that is used to display an ima ge 2 -Non-Contact Mode Non-contact mode belongs to a family of AC modes, which refers to the use of an oscillating cantilever. A stiff cantilever is oscillated in the attractive regime, meaning that the tip is quite close to the sample, but not touching it (hence, non-contact). The forces between the tip and sample are quite low, on the order of p. N (10 -12 N). The detection scheme is based on measuring changes to the resonant frequency or amplitude of the cantilever as the interaction between the tip and sample dampen the oscillation.
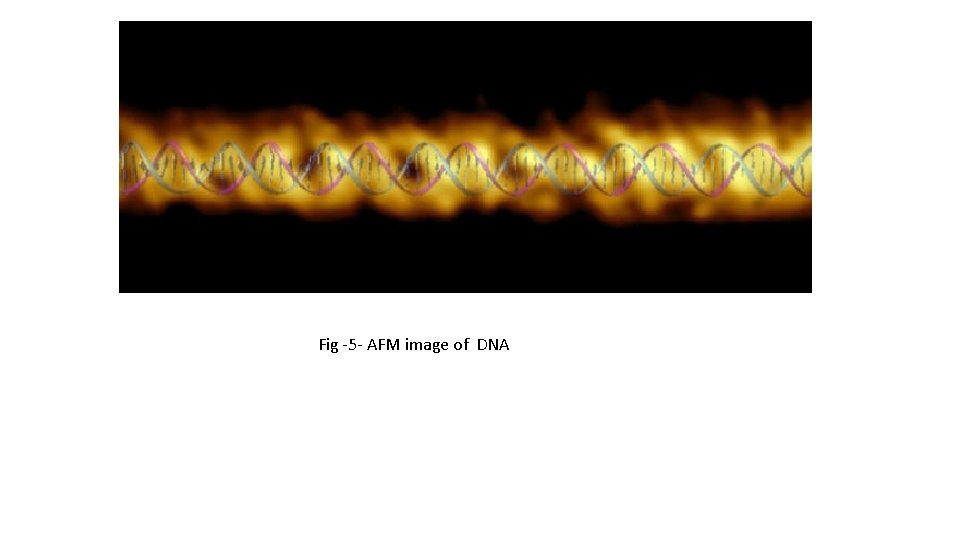
Fig -5 - AFM image of DNA
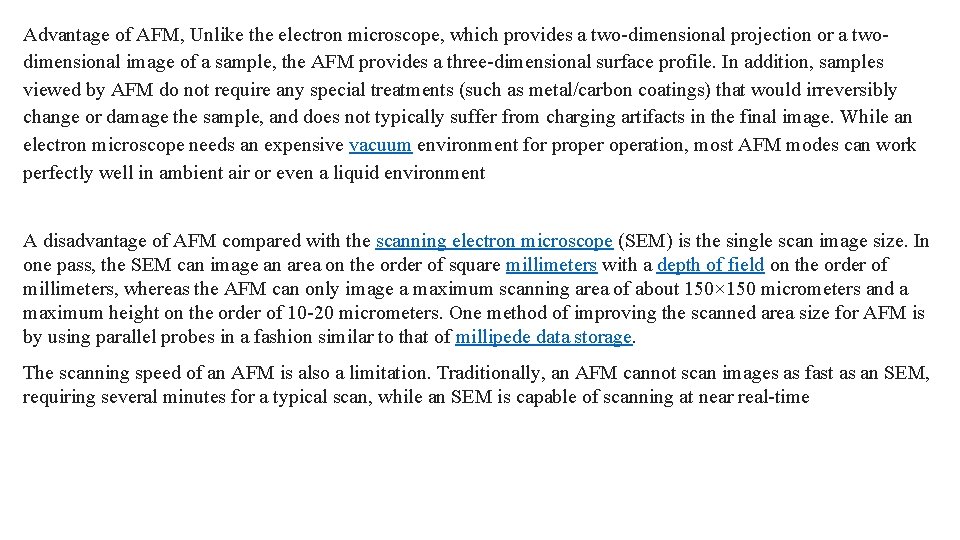
Advantage of AFM, Unlike the electron microscope, which provides a two-dimensional projection or a twodimensional image of a sample, the AFM provides a three-dimensional surface profile. In addition, samples viewed by AFM do not require any special treatments (such as metal/carbon coatings) that would irreversibly change or damage the sample, and does not typically suffer from charging artifacts in the final image. While an electron microscope needs an expensive vacuum environment for properation, most AFM modes can work perfectly well in ambient air or even a liquid environment A disadvantage of AFM compared with the scanning electron microscope (SEM) is the single scan image size. In one pass, the SEM can image an area on the order of square millimeters with a depth of field on the order of millimeters, whereas the AFM can only image a maximum scanning area of about 150× 150 micrometers and a maximum height on the order of 10 -20 micrometers. One method of improving the scanned area size for AFM is by using parallel probes in a fashion similar to that of millipede data storage. The scanning speed of an AFM is also a limitation. Traditionally, an AFM cannot scan images as fast as an SEM, requiring several minutes for a typical scan, while an SEM is capable of scanning at near real-time