5 7 3 Cold Weather Cold weather causes
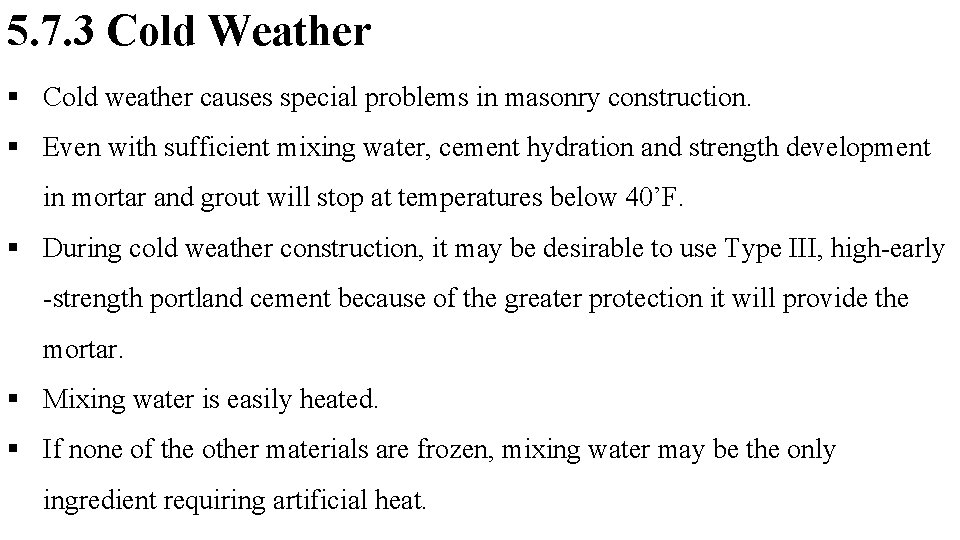
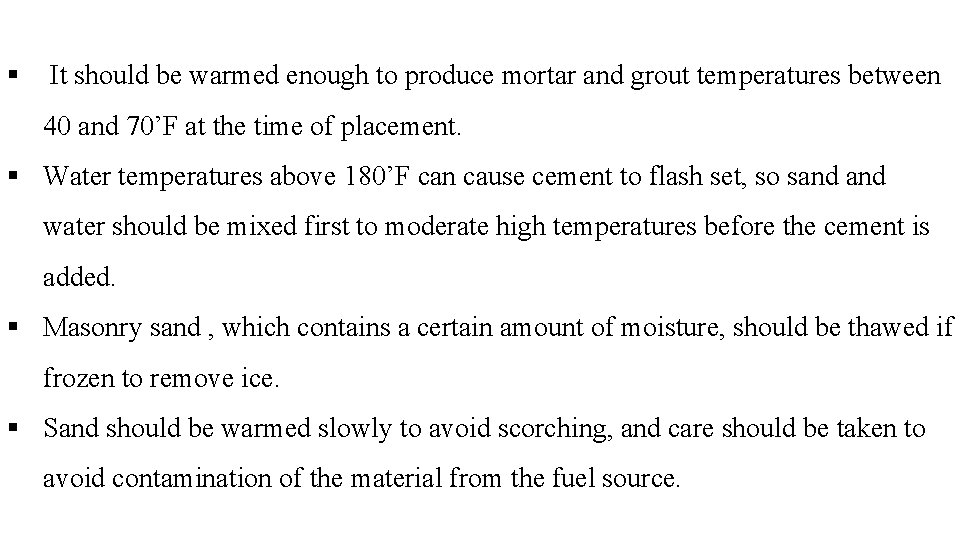
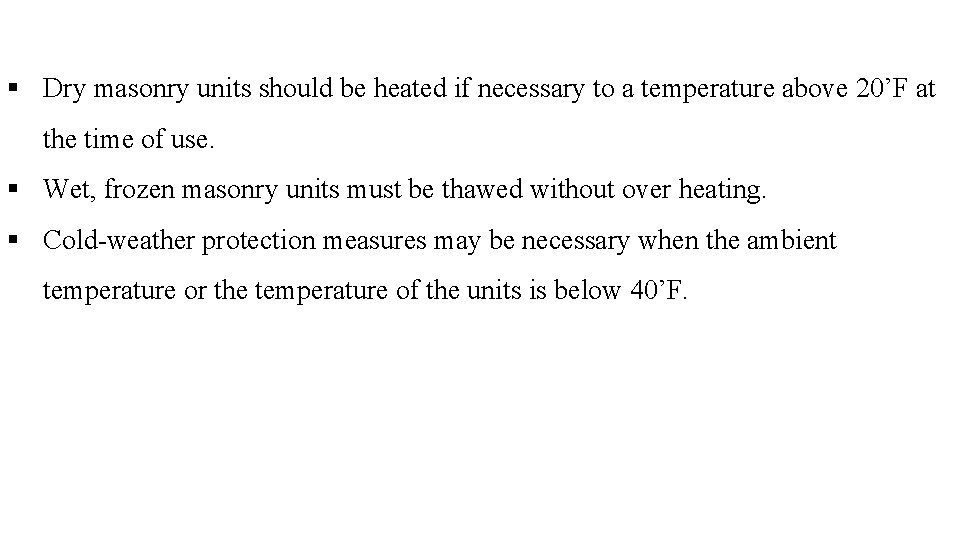
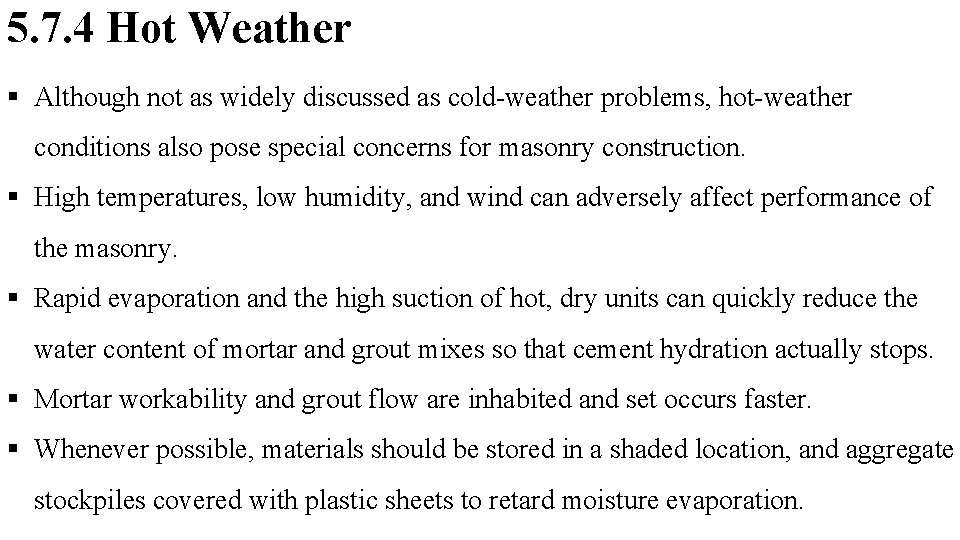
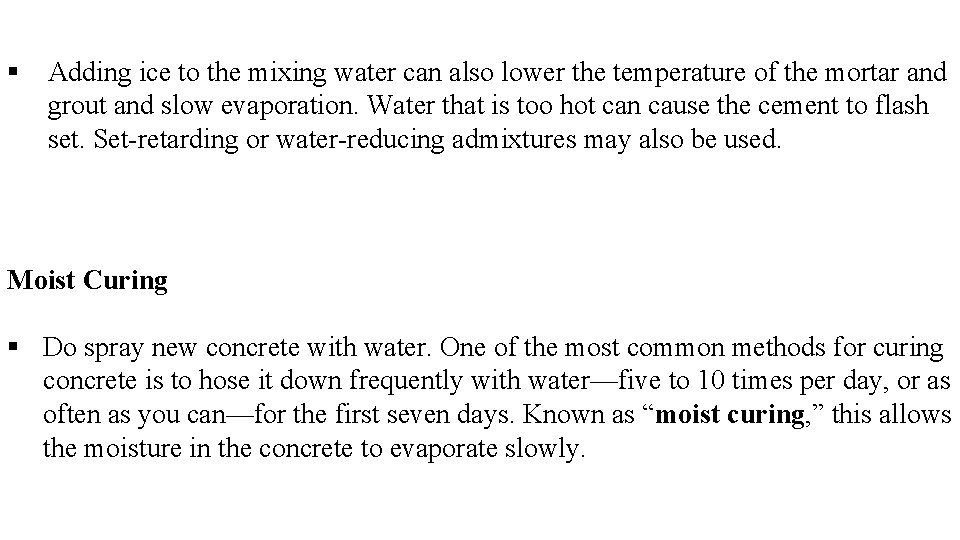
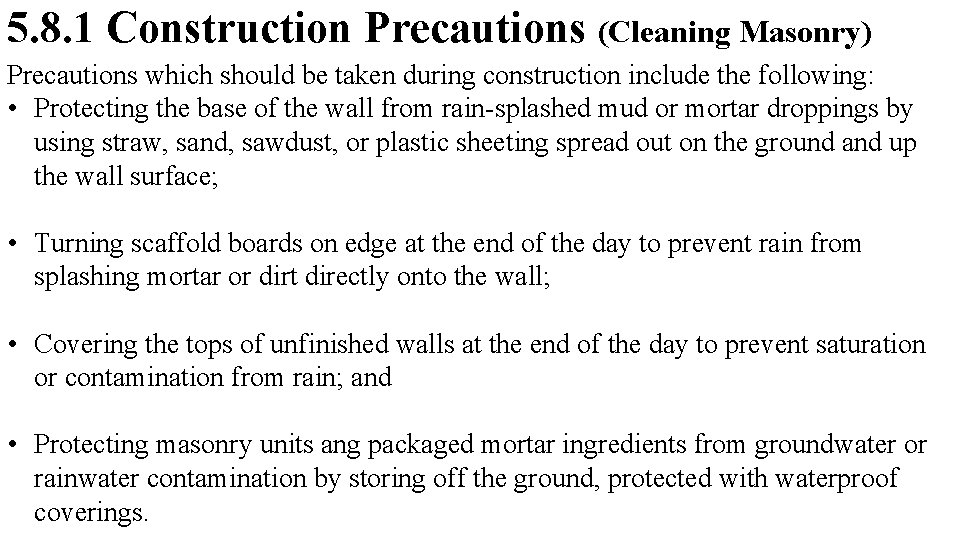
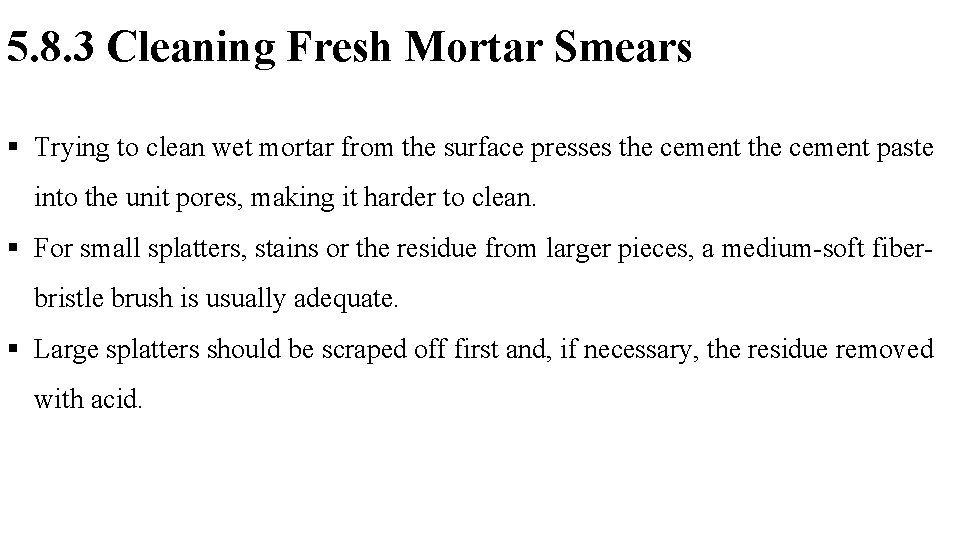
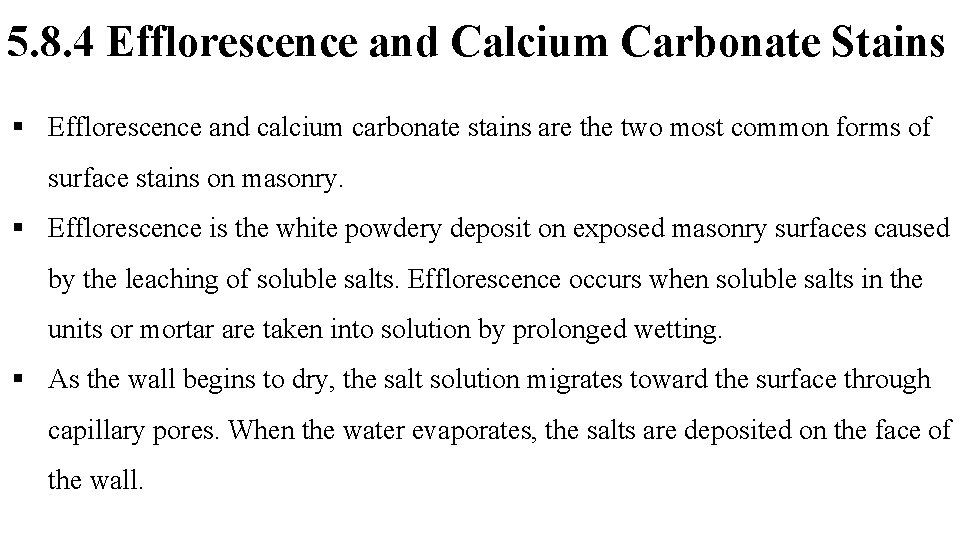
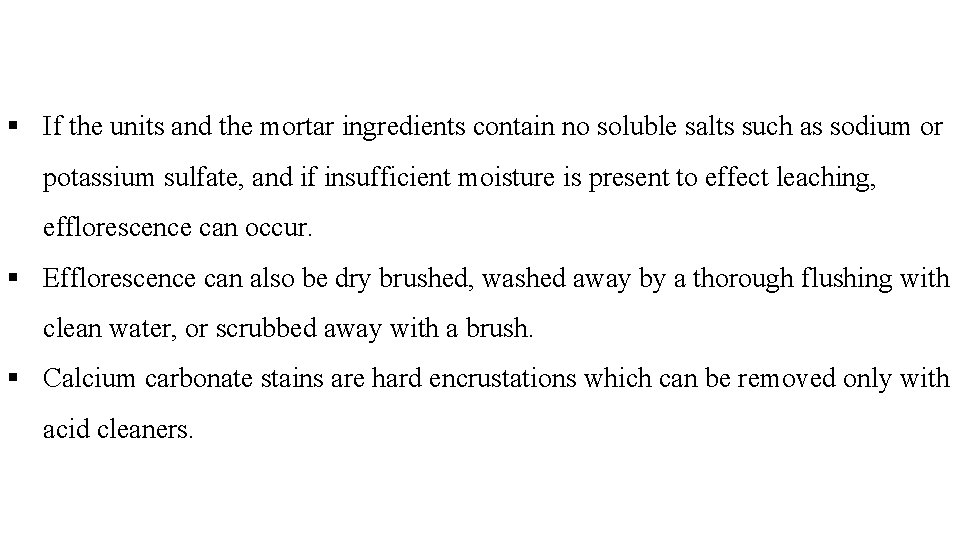
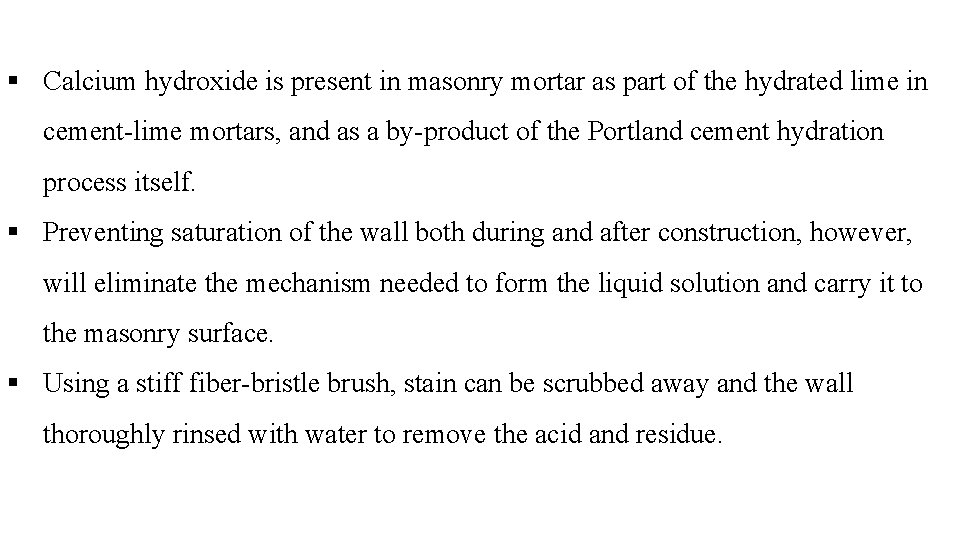
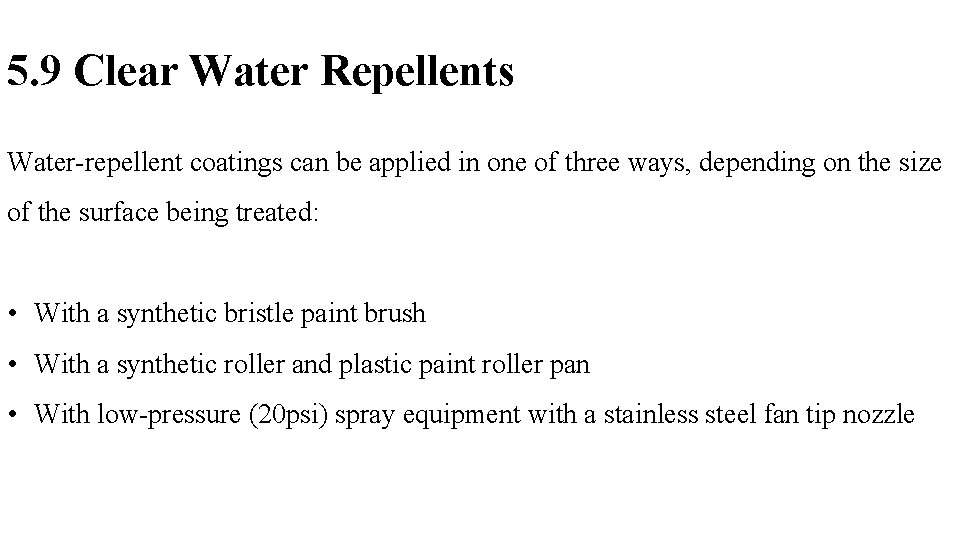
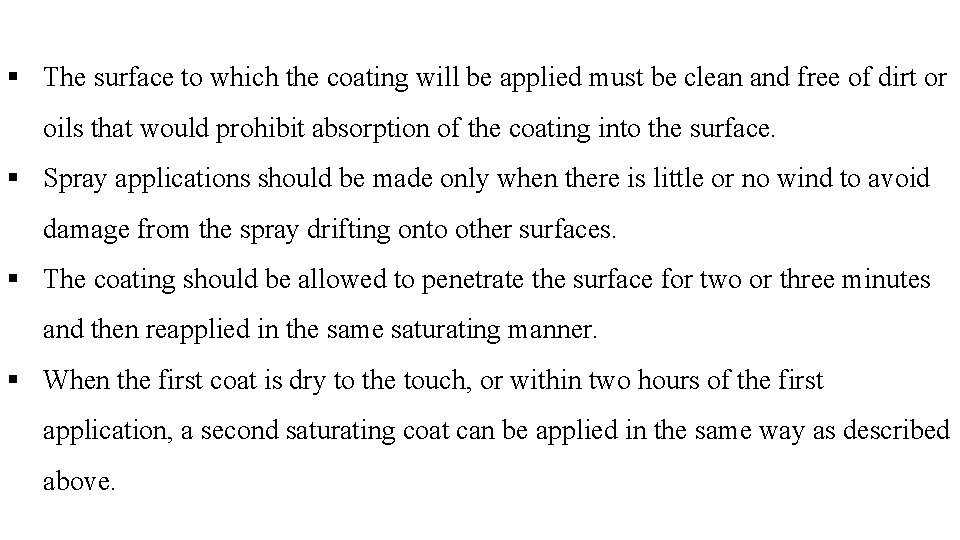
- Slides: 12
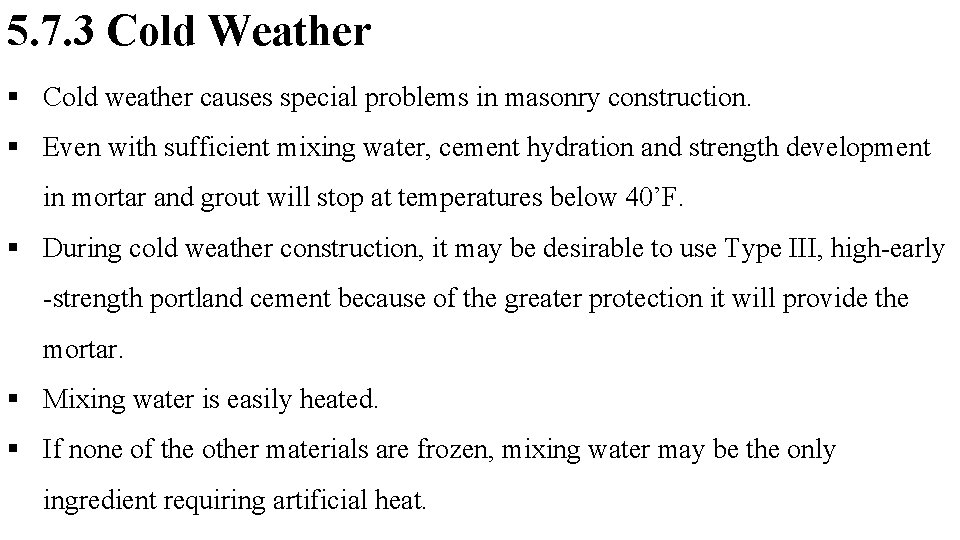
5. 7. 3 Cold Weather § Cold weather causes special problems in masonry construction. § Even with sufficient mixing water, cement hydration and strength development in mortar and grout will stop at temperatures below 40’F. § During cold weather construction, it may be desirable to use Type III, high-early -strength portland cement because of the greater protection it will provide the mortar. § Mixing water is easily heated. § If none of the other materials are frozen, mixing water may be the only ingredient requiring artificial heat.
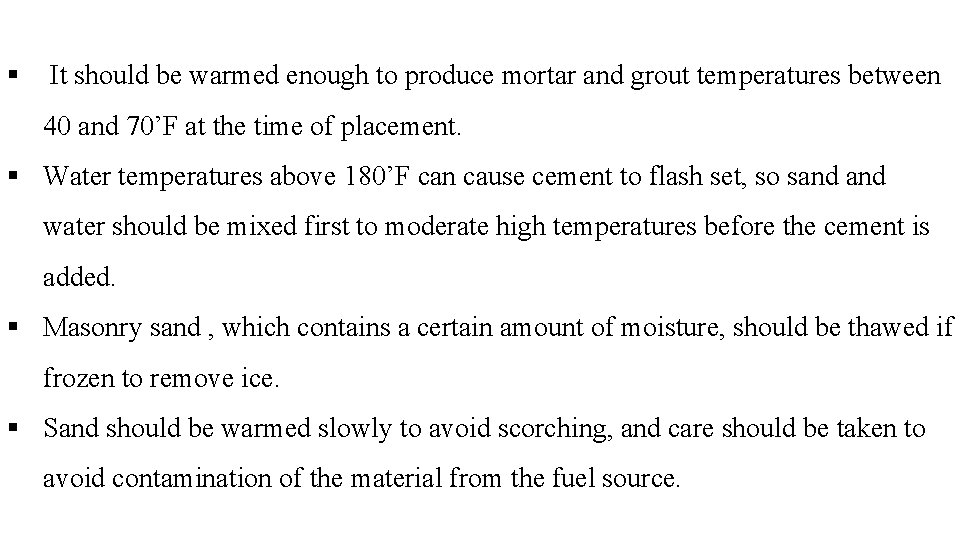
§ It should be warmed enough to produce mortar and grout temperatures between 40 and 70’F at the time of placement. § Water temperatures above 180’F can cause cement to flash set, so sand water should be mixed first to moderate high temperatures before the cement is added. § Masonry sand , which contains a certain amount of moisture, should be thawed if frozen to remove ice. § Sand should be warmed slowly to avoid scorching, and care should be taken to avoid contamination of the material from the fuel source.
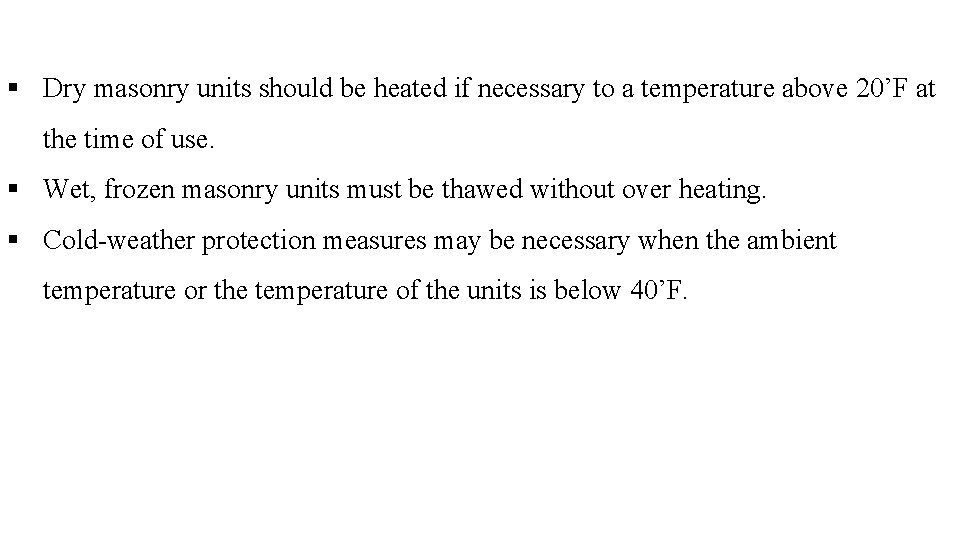
§ Dry masonry units should be heated if necessary to a temperature above 20’F at the time of use. § Wet, frozen masonry units must be thawed without over heating. § Cold-weather protection measures may be necessary when the ambient temperature or the temperature of the units is below 40’F.
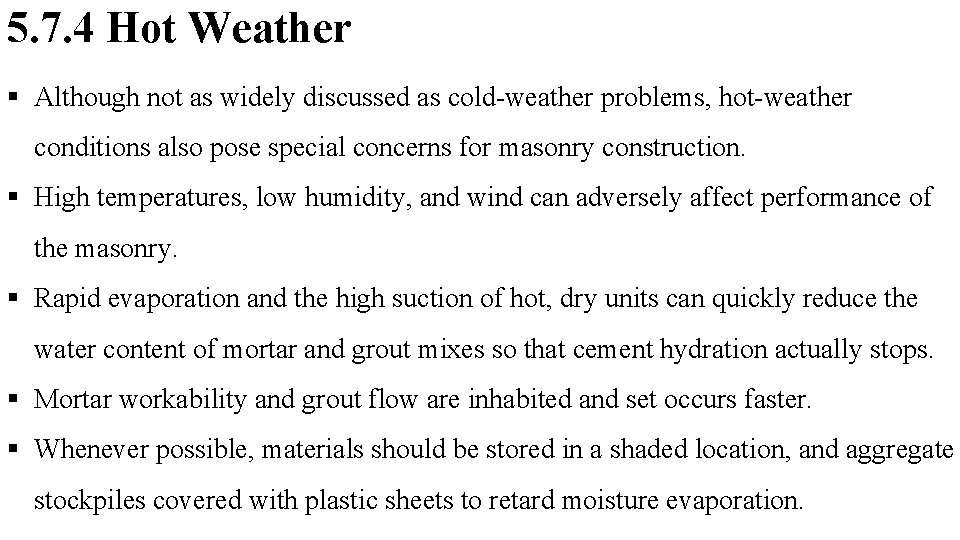
5. 7. 4 Hot Weather § Although not as widely discussed as cold-weather problems, hot-weather conditions also pose special concerns for masonry construction. § High temperatures, low humidity, and wind can adversely affect performance of the masonry. § Rapid evaporation and the high suction of hot, dry units can quickly reduce the water content of mortar and grout mixes so that cement hydration actually stops. § Mortar workability and grout flow are inhabited and set occurs faster. § Whenever possible, materials should be stored in a shaded location, and aggregate stockpiles covered with plastic sheets to retard moisture evaporation.
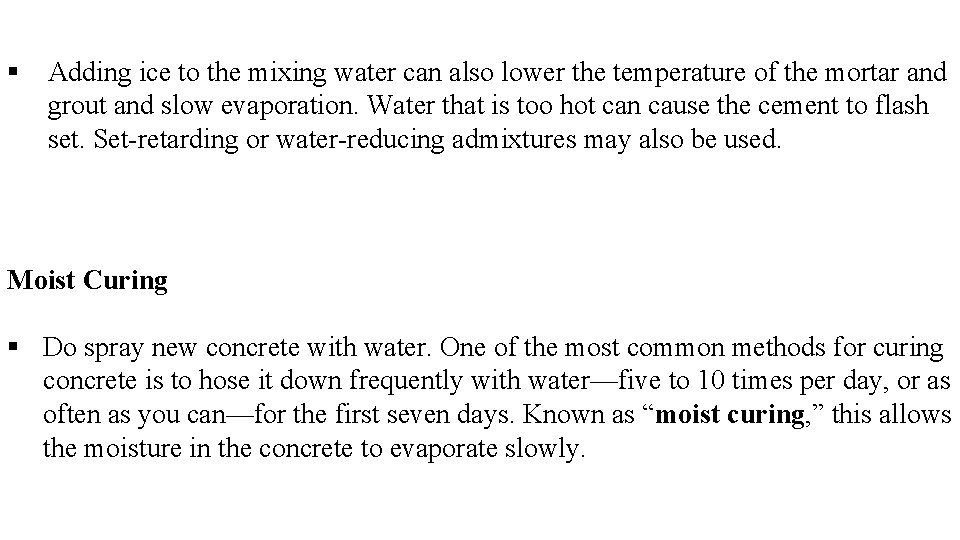
§ Adding ice to the mixing water can also lower the temperature of the mortar and grout and slow evaporation. Water that is too hot can cause the cement to flash set. Set-retarding or water-reducing admixtures may also be used. Moist Curing § Do spray new concrete with water. One of the most common methods for curing concrete is to hose it down frequently with water—five to 10 times per day, or as often as you can—for the first seven days. Known as “moist curing, ” this allows the moisture in the concrete to evaporate slowly.
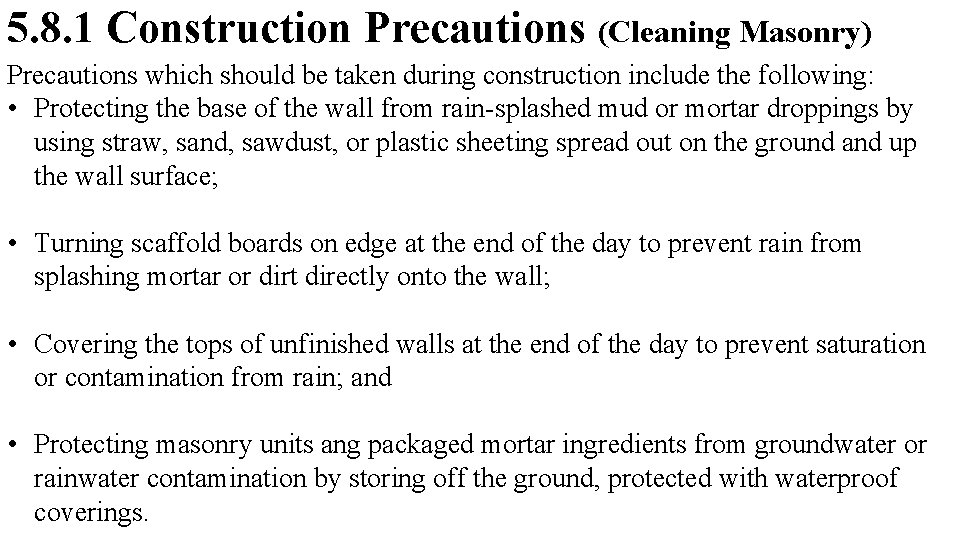
5. 8. 1 Construction Precautions (Cleaning Masonry) Precautions which should be taken during construction include the following: • Protecting the base of the wall from rain-splashed mud or mortar droppings by using straw, sand, sawdust, or plastic sheeting spread out on the ground and up the wall surface; • Turning scaffold boards on edge at the end of the day to prevent rain from splashing mortar or dirt directly onto the wall; • Covering the tops of unfinished walls at the end of the day to prevent saturation or contamination from rain; and • Protecting masonry units ang packaged mortar ingredients from groundwater or rainwater contamination by storing off the ground, protected with waterproof coverings.
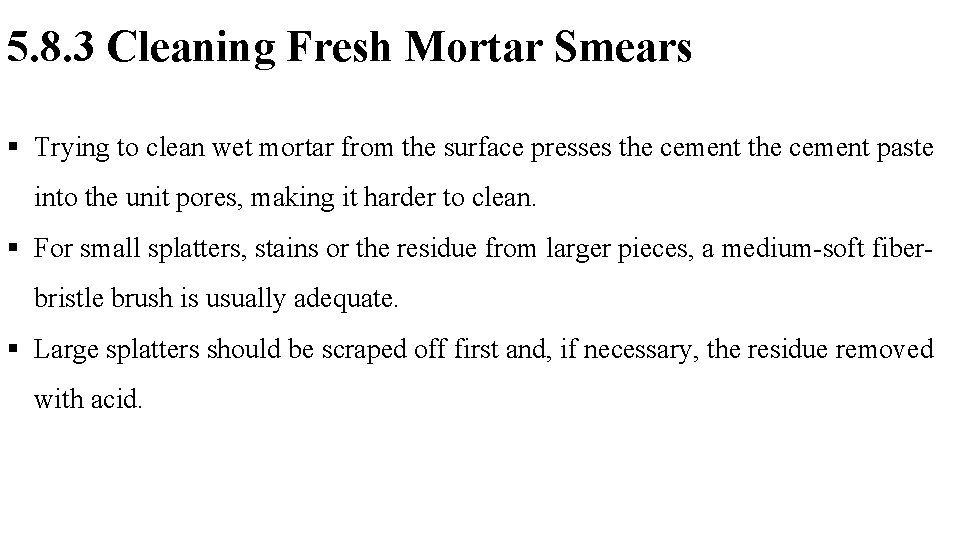
5. 8. 3 Cleaning Fresh Mortar Smears § Trying to clean wet mortar from the surface presses the cement paste into the unit pores, making it harder to clean. § For small splatters, stains or the residue from larger pieces, a medium-soft fiberbristle brush is usually adequate. § Large splatters should be scraped off first and, if necessary, the residue removed with acid.
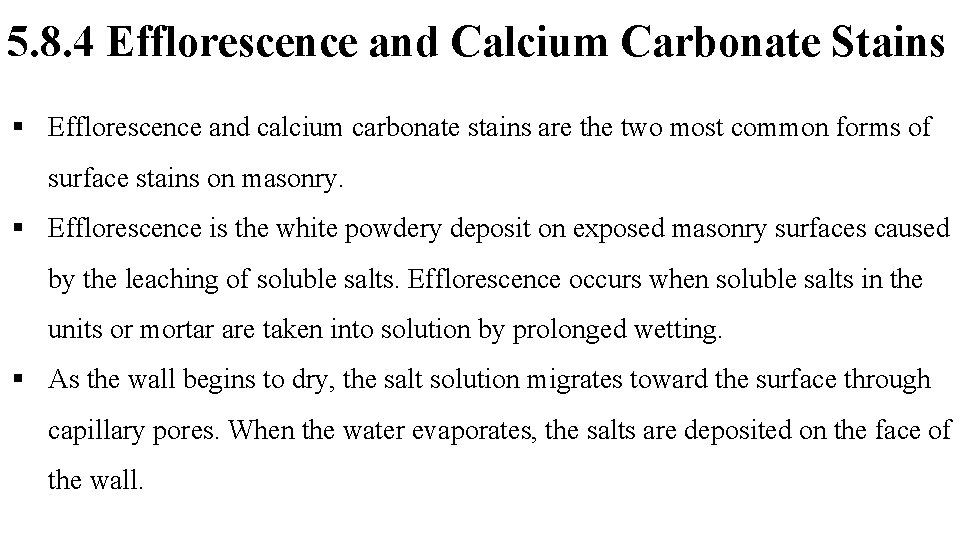
5. 8. 4 Efflorescence and Calcium Carbonate Stains § Efflorescence and calcium carbonate stains are the two most common forms of surface stains on masonry. § Efflorescence is the white powdery deposit on exposed masonry surfaces caused by the leaching of soluble salts. Efflorescence occurs when soluble salts in the units or mortar are taken into solution by prolonged wetting. § As the wall begins to dry, the salt solution migrates toward the surface through capillary pores. When the water evaporates, the salts are deposited on the face of the wall.
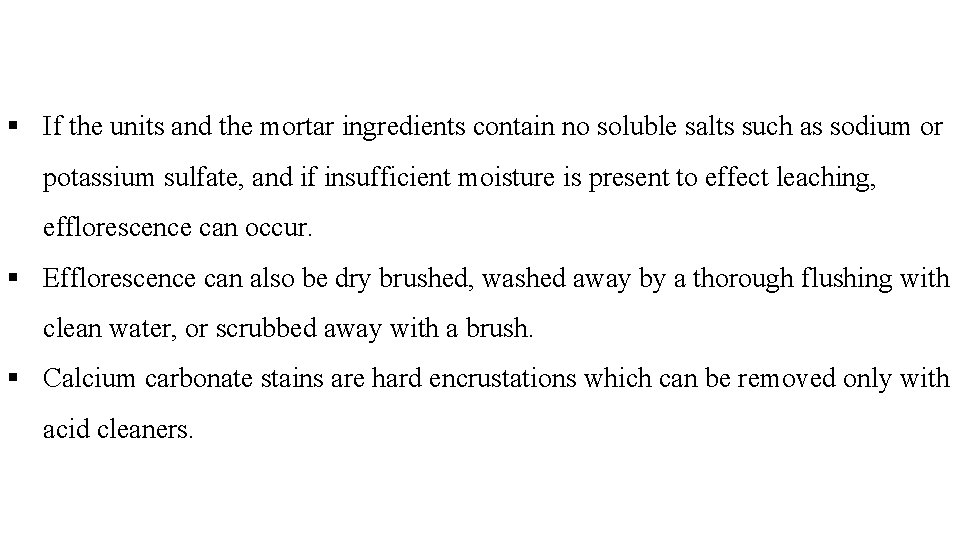
§ If the units and the mortar ingredients contain no soluble salts such as sodium or potassium sulfate, and if insufficient moisture is present to effect leaching, efflorescence can occur. § Efflorescence can also be dry brushed, washed away by a thorough flushing with clean water, or scrubbed away with a brush. § Calcium carbonate stains are hard encrustations which can be removed only with acid cleaners.
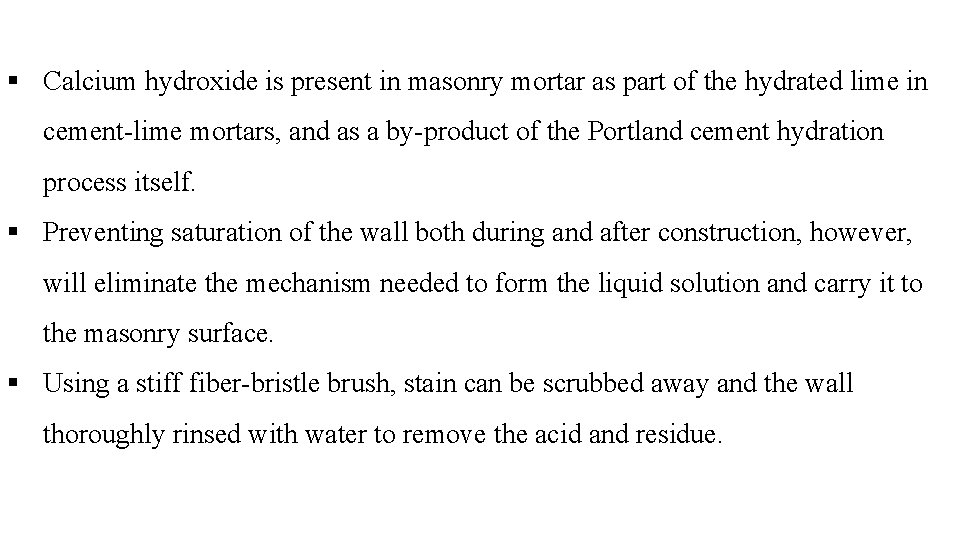
§ Calcium hydroxide is present in masonry mortar as part of the hydrated lime in cement-lime mortars, and as a by-product of the Portland cement hydration process itself. § Preventing saturation of the wall both during and after construction, however, will eliminate the mechanism needed to form the liquid solution and carry it to the masonry surface. § Using a stiff fiber-bristle brush, stain can be scrubbed away and the wall thoroughly rinsed with water to remove the acid and residue.
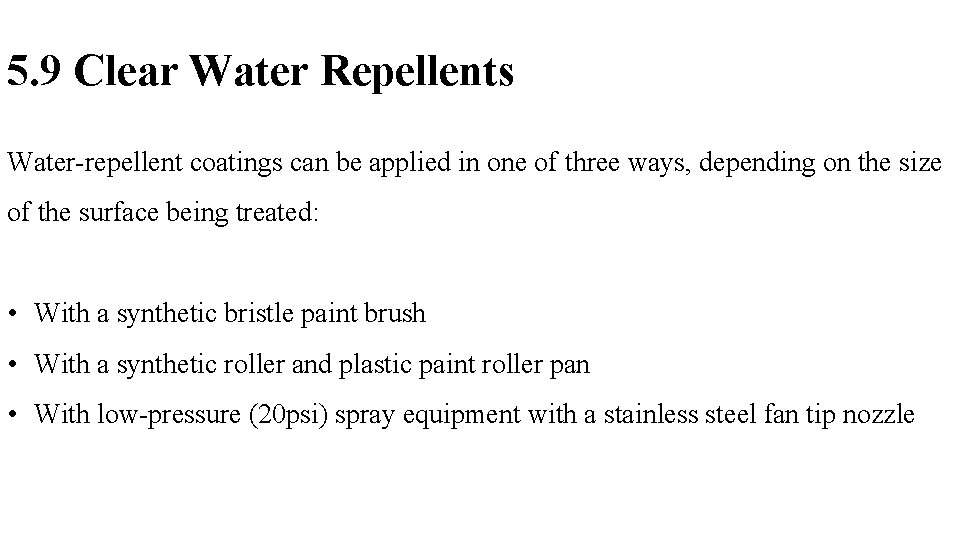
5. 9 Clear Water Repellents Water-repellent coatings can be applied in one of three ways, depending on the size of the surface being treated: • With a synthetic bristle paint brush • With a synthetic roller and plastic paint roller pan • With low-pressure (20 psi) spray equipment with a stainless steel fan tip nozzle
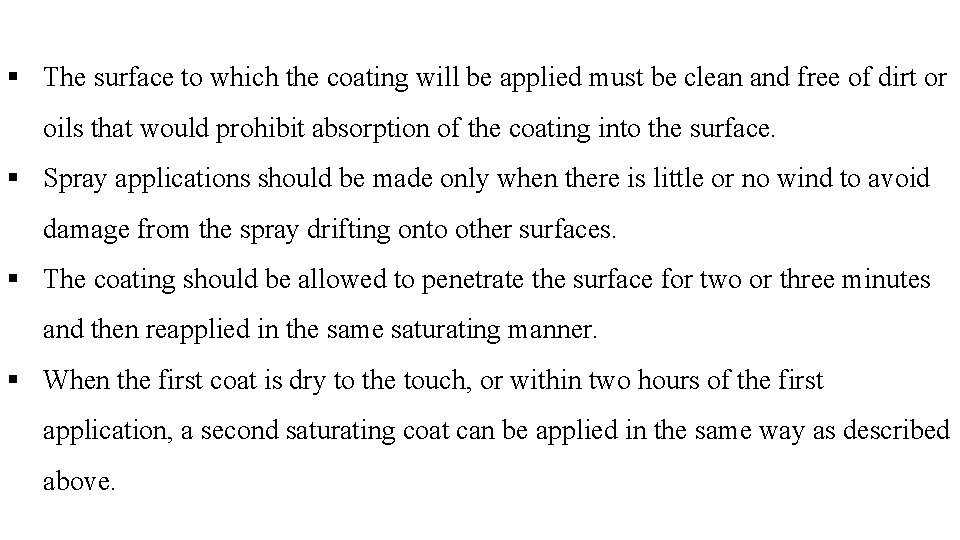
§ The surface to which the coating will be applied must be clean and free of dirt or oils that would prohibit absorption of the coating into the surface. § Spray applications should be made only when there is little or no wind to avoid damage from the spray drifting onto other surfaces. § The coating should be allowed to penetrate the surface for two or three minutes and then reapplied in the same saturating manner. § When the first coat is dry to the touch, or within two hours of the first application, a second saturating coat can be applied in the same way as described above.
Proximate vs ultimate causation
Proximate causation vs ultimate causation
Marshall plan apush
The causes of the cold war
Causes and effects of the korean war
Cpalms what causes weather
The cold war lesson 1 the cold war begins
Whenever the weather
Cold front weather
Cold weather patrolling
Expressing cause and effect
Tongue twister summer
Whether the weather be fine