2010 ISOE Asia ALARA Symposium Development of HiF
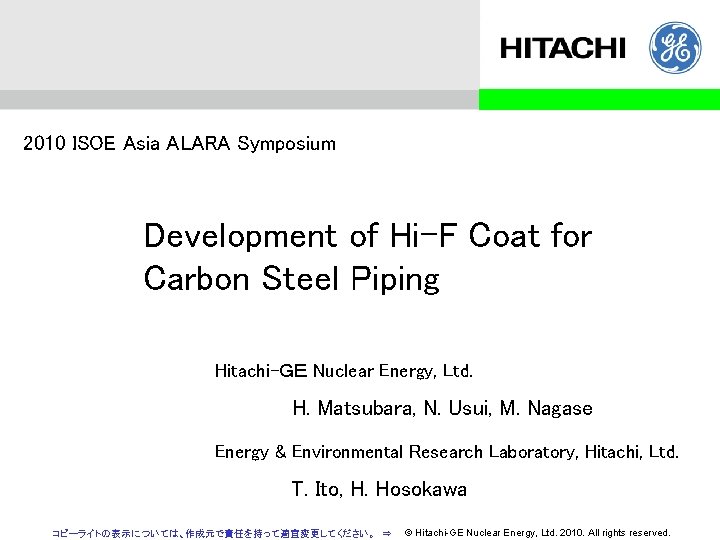
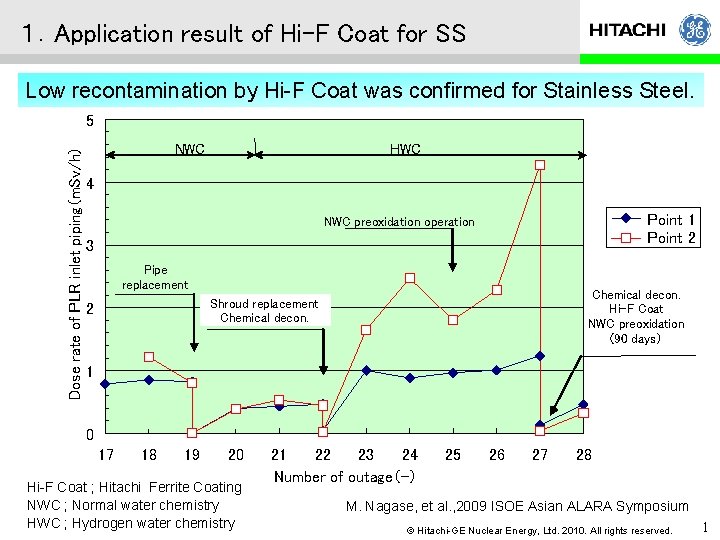
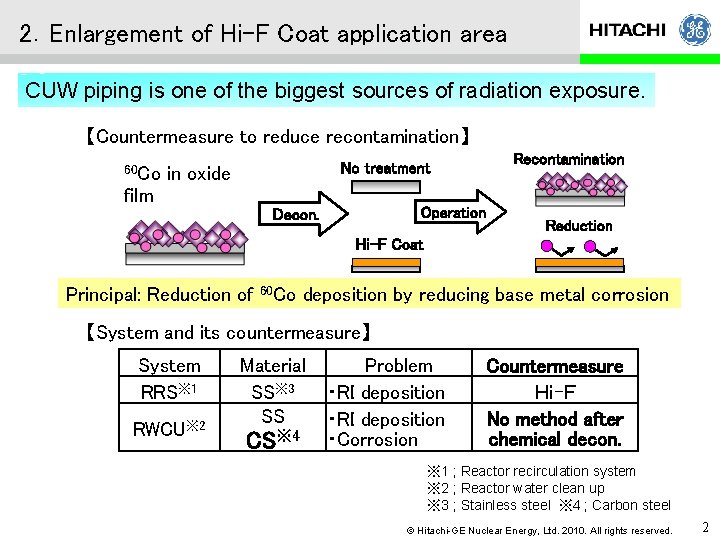
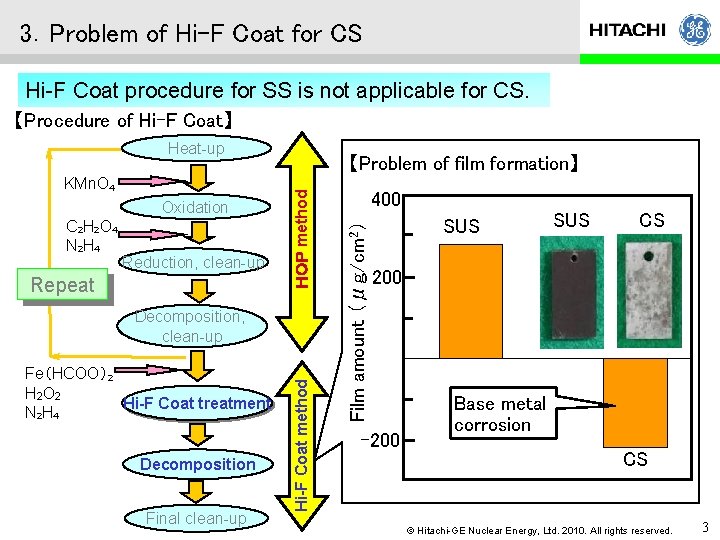
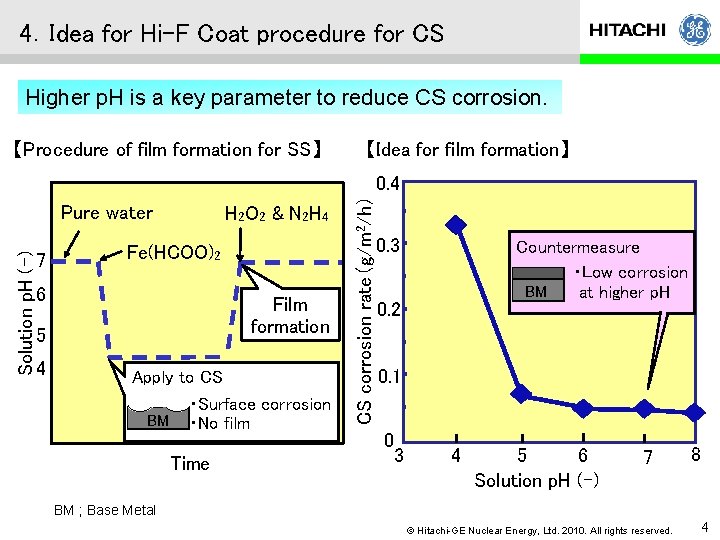
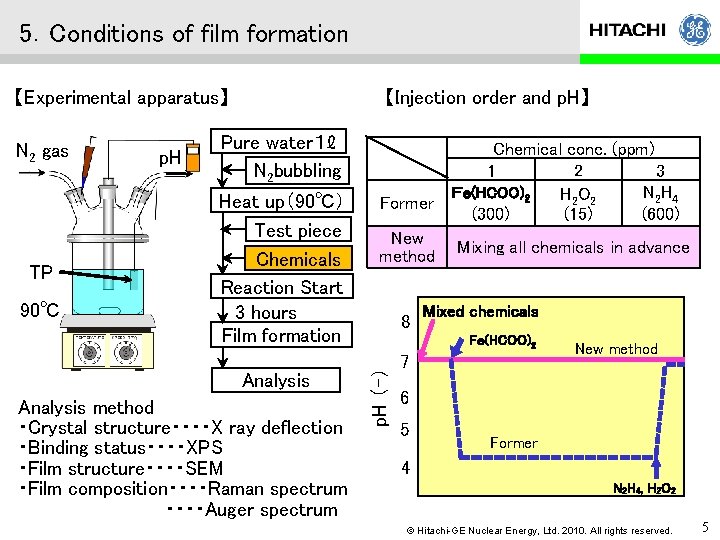
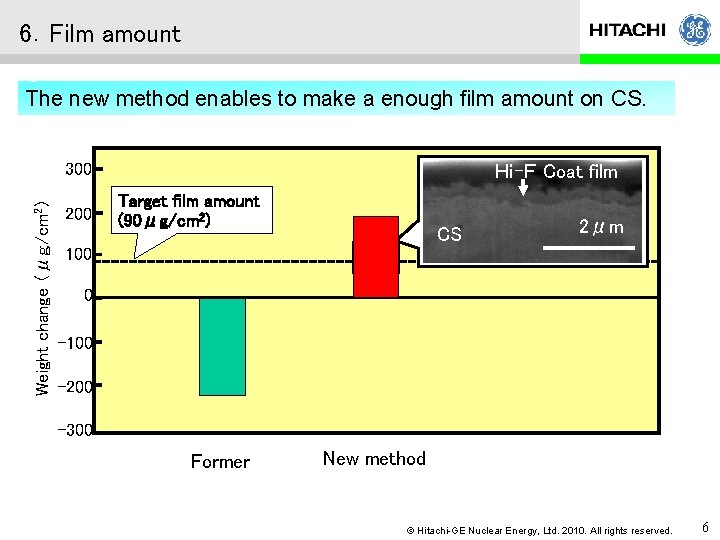
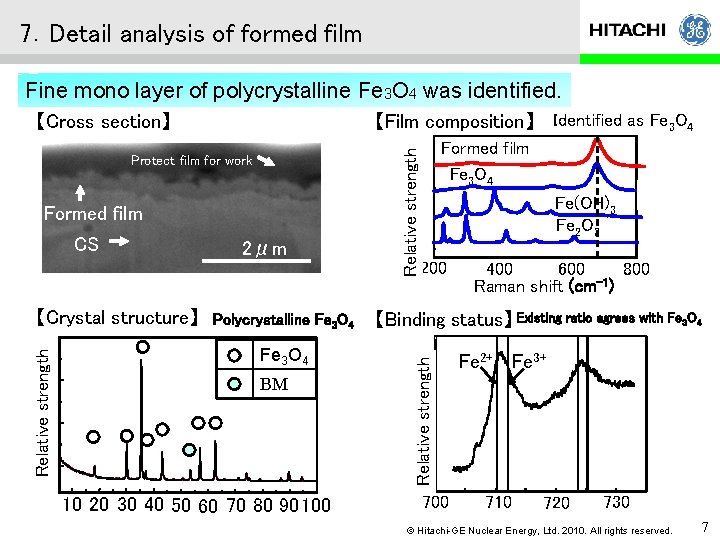
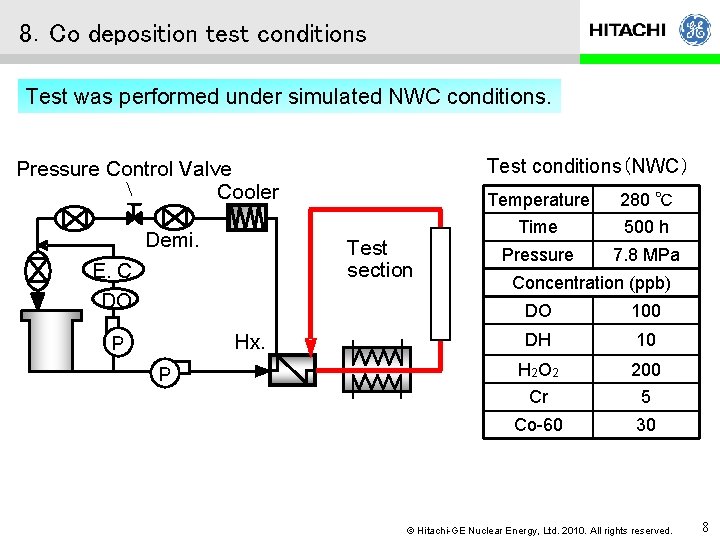
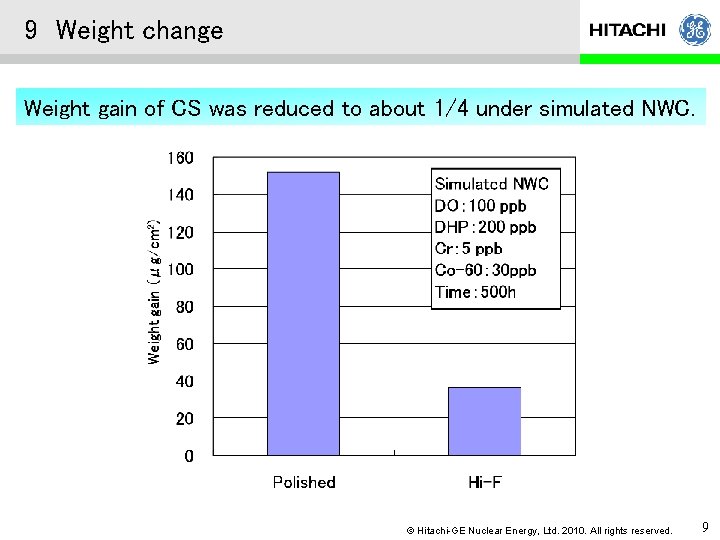
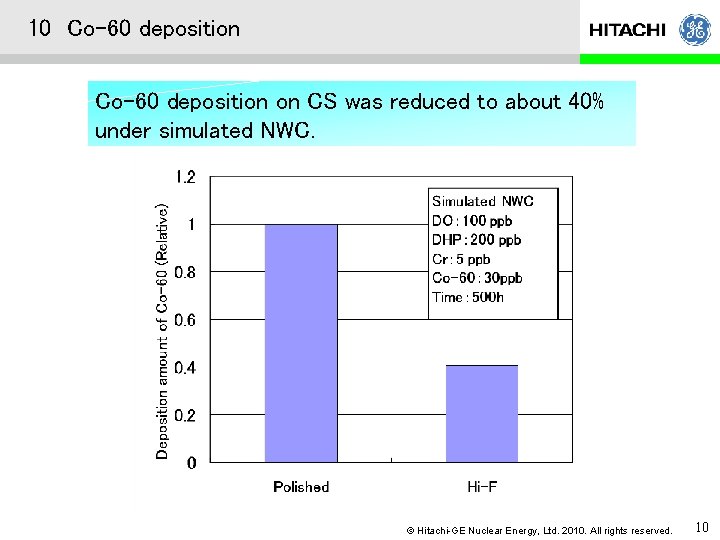
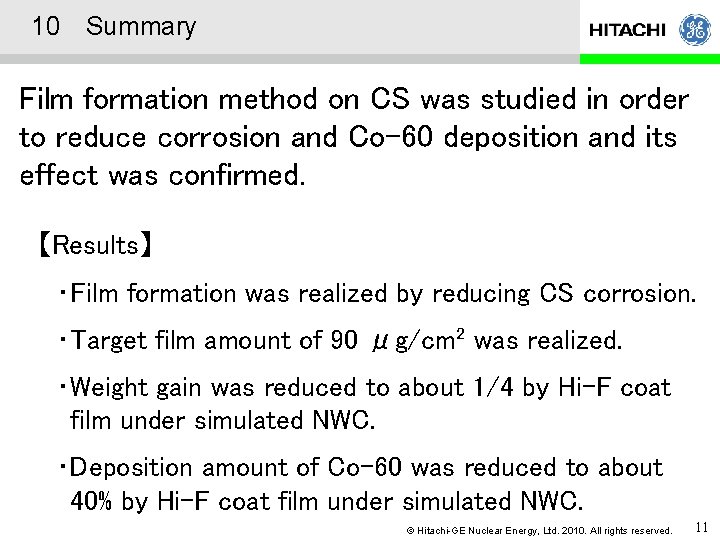
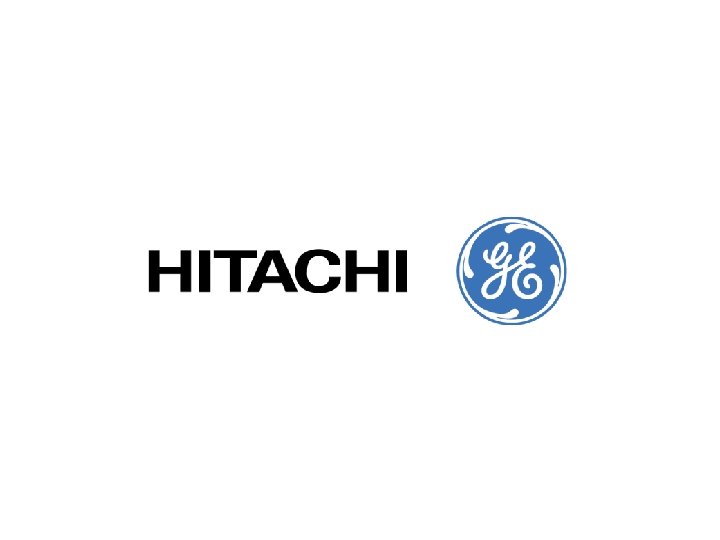
- Slides: 13
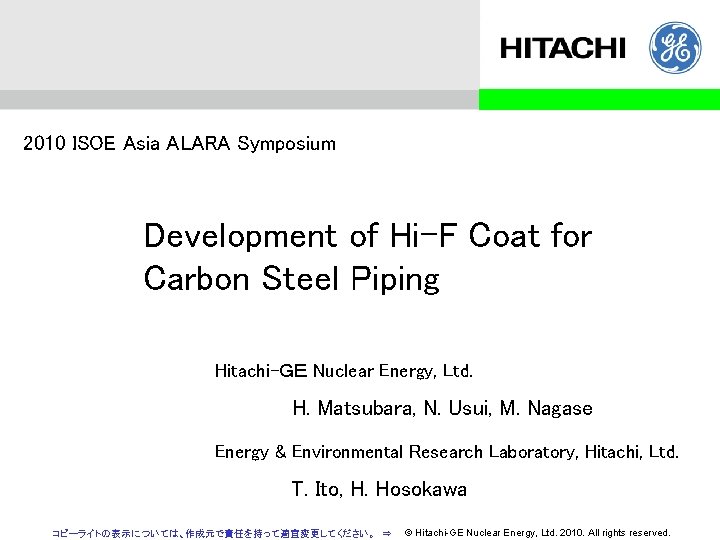
2010 ISOE Asia ALARA Symposium Development of Hi-F Coat for Carbon Steel Piping Hitachi-GE Nuclear Energy, Ltd. H. Matsubara, N. Usui, M. Nagase Energy & Environmental Research Laboratory, Hitachi, Ltd. T. Ito, H. Hosokawa コピーライトの表示については、作成元で責任を持って適宜変更してください。 ⇒ © Hitachi-GE Nuclear Energy, Ltd. 2010. All rights reserved.
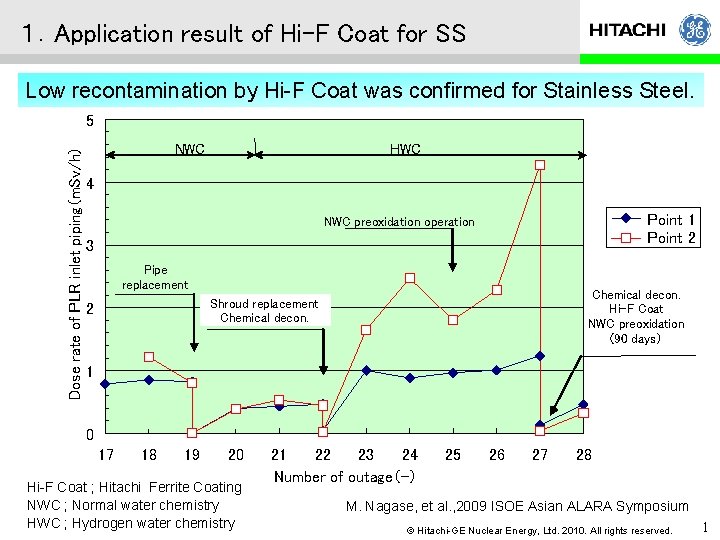
1.Application result of Hi-F Coat for SS Low recontamination by Hi-F Coat was confirmed for Stainless Steel. Dose rate of PLR inlet piping(m. Sv/h) 5 NWC HWC 4 PLR(A) Point 1 Point 2 PLR(B) NWC preoxidation operation 3 Pipe replacement Chemical decon. Hi-F Coat NWC preoxidation (90 days) Shroud replacement Chemical decon. 2 1 0 17 18 19 20 Hi-F Coat ; Hitachi Ferrite Coating NWC ; Normal water chemistry HWC ; Hydrogen water chemistry 21 22 23 24 Number of outage(-) 25 26 27 28 M. Nagase, et al. , 2009 ISOE Asian ALARA Symposium © Hitachi-GE Nuclear Energy, Ltd. 2010. All rights reserved. 1
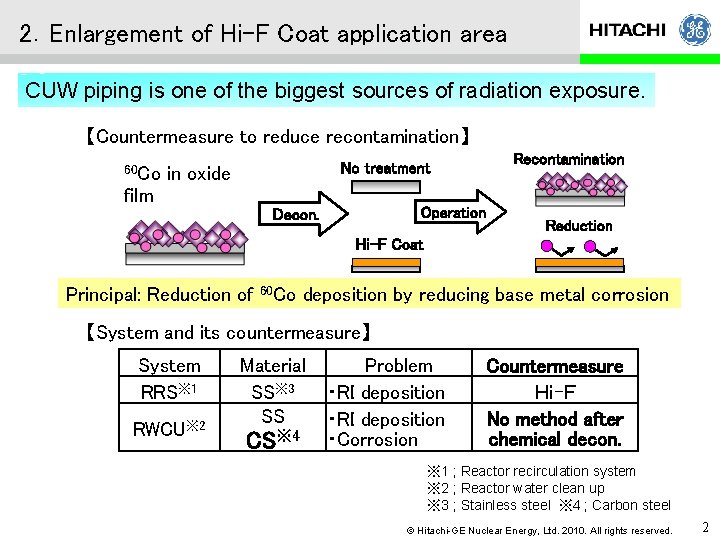
2.Enlargement of Hi-F Coat application area CUW piping is one of the biggest sources of radiation exposure. 【Countermeasure to reduce recontamination】 60 Co No treatment in oxide film Operation Decon. Recontamination Reduction Hi-F Coat Principal: Reduction of 60 Co deposition by reducing base metal corrosion 【System and its countermeasure】 System RRS※ 1 RWCU※ 2 Material SS※ 3 SS CS※ 4 Problem ・RI deposition ・Corrosion Countermeasure Hi-F No method after chemical decon. ※ 1 ; Reactor recirculation system ※ 2 ; Reactor water clean up ※ 3 ; Stainless steel ※ 4 ; Carbon steel © Hitachi-GE Nuclear Energy, Ltd. 2010. All rights reserved. 2
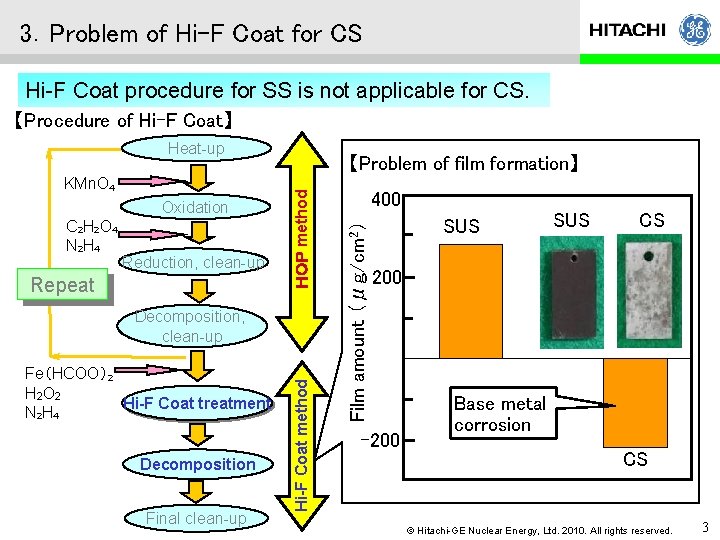
3.Problem of Hi-F Coat for CS Hi-F Coat procedure for SS is not applicable for CS. 【Procedure of Hi-F Coat】 Heat-up C 2 H 2 O 4 N 2 H 4 Reduction, clean-up Repeat Fe(HCOO)2 H 2 O 2 Hi-F Coat treatment N 2 H 4 Decomposition Final clean-up Hi-F Coat method Decomposition, clean-up 400 Film amount (μg/cm 2) Oxidation HOP method KMn. O 4 【Problem of film formation】 SUS CS 200 -200 Base metal corrosion CS © Hitachi-GE Nuclear Energy, Ltd. 2010. All rights reserved. 3
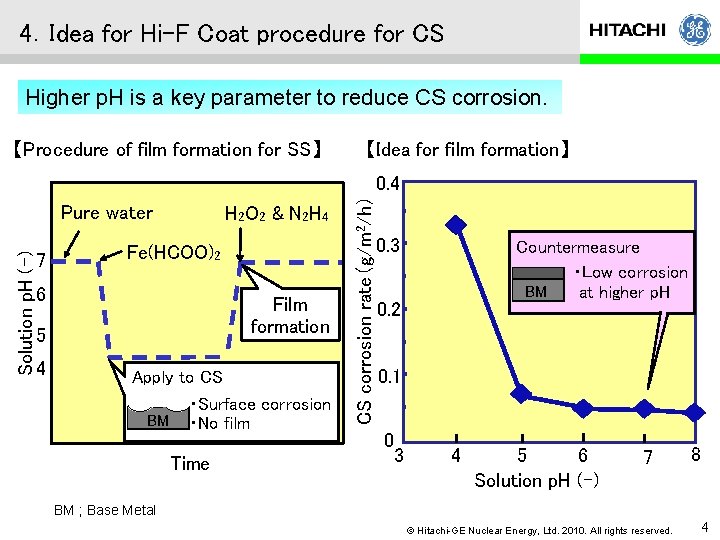
4.Idea for Hi-F Coat procedure for CS Higher p. H is a key parameter to reduce CS corrosion. 【Procedure of film formation for SS】 【Idea for film formation】 Solution p. H (-) Pure water 7 H 2 O 2 & N 2 H 4 Fe(HCOO)2 6 Film formation 5 4 Apply to CS ・Surface corrosion BM ・No film Time CS corrosion rate(g/m 2/h) 0. 4 0. 3 Countermeasure ・Low corrosion BM at higher p. H 0. 2 0. 1 0 3 4 5 6 Solution p. H (-) 7 8 BM ; Base Metal © Hitachi-GE Nuclear Energy, Ltd. 2010. All rights reserved. 4
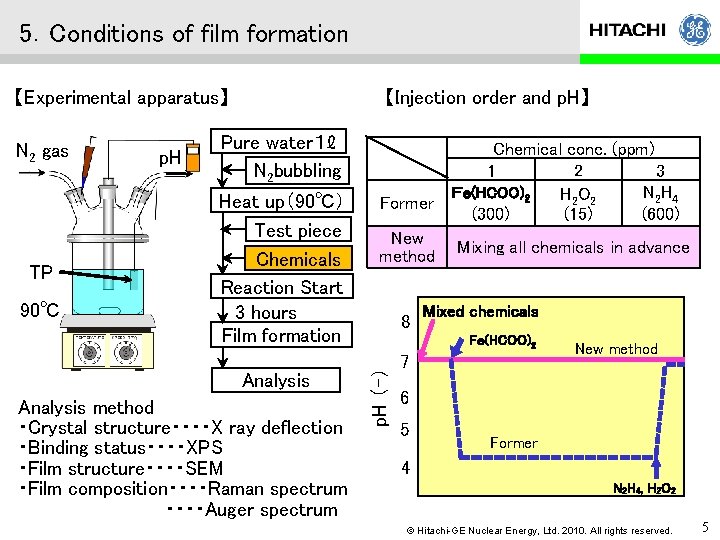
5.Conditions of film formation 【Experimental apparatus】 TP 90℃ p. H Pure water1ℓ N 2 bubbling Heat up(90℃) Test piece Chemicals Reaction Start 3 hours Film formation Analysis method ・Crystal structure・・・・X ray deflection ・Binding status・・・・XPS ・Film structure・・・・SEM ・Film composition・・・・Raman spectrum ・・・・Auger spectrum Former New method 8 Chemical conc. (ppm) 1 2 3 Fe(HCOO)2 N 2 H 4 H 2 O 2 (15) (300) (600) Mixing all chemicals in advance Mixed chemicals Fe(HCOO)2 p. H (-) N 2 gas 【Injection order and p. H】 7 New method 6 5 Ni金属皮膜形成 Former 4 N 2 H 4 , H 2 O 2 © Hitachi-GE Nuclear Energy, Ltd. 2010. All rights reserved. 5
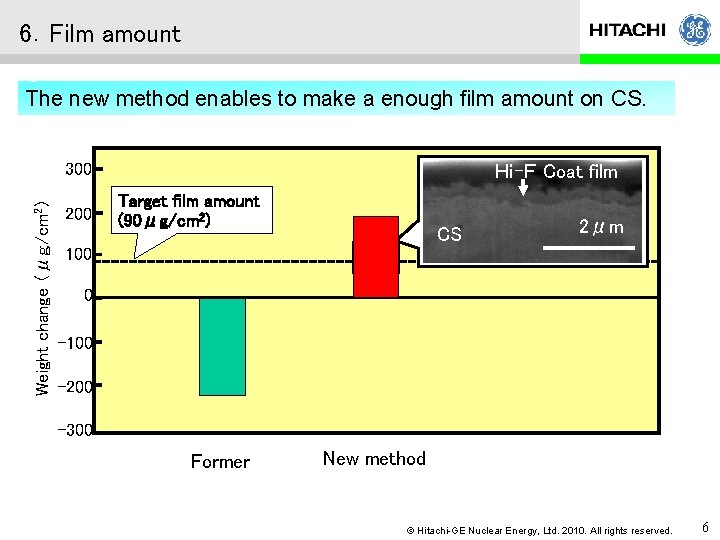
6.Film amount The new method enables to make a enough film amount on CS. Weight change (μg/cm 2) 300 200 Hi-F Coat film Target film amount (90μg/cm 2) CS 2μm 100 0 -100 -200 -300 Former New method © Hitachi-GE Nuclear Energy, Ltd. 2010. All rights reserved. 6
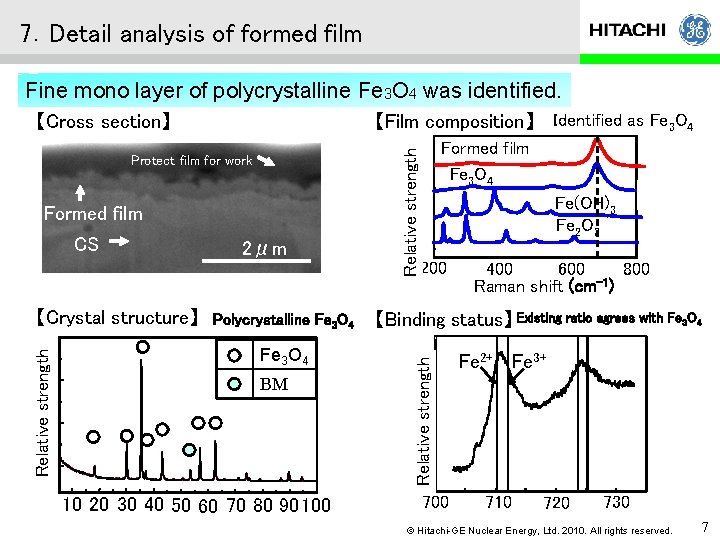
7.Detail analysis of formed film Fine mono layer of polycrystalline Fe 3 O 4 was identified. 【Film composition】 Identified as Fe 3 O 4 Formed film CS Relative strength 【Crystal structure】 2μm Polycrystalline Fe 3 O 4 BM 10 20 30 40 50 60 70 80 90 100 Formed film Fe 3 O 4 Fe(OH)3 Fe 2 O 3 200 600 800 400 -1 Raman shift (cm ) 【Binding status】 Existing ratio agrees with Fe 3 O 4 Relative strength Protect film for work Relative strength 【Cross section】 700 Fe 2+ Fe 3+ 710 720 730 © Hitachi-GE Nuclear Energy, Ltd. 2010. All rights reserved. 7
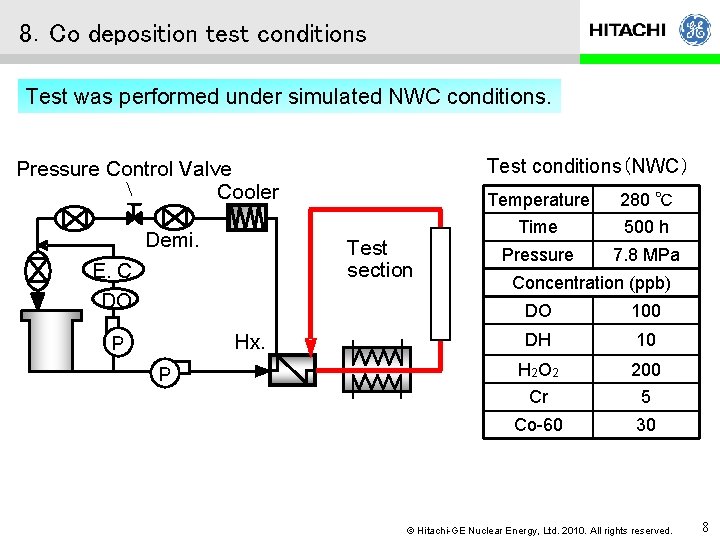
8.Co deposition test conditions Test was performed under simulated NWC conditions. Test conditions(NWC) Pressure Control Valve Cooler Demi. Test section E. C. DO Hx. P P Temperature 280 ℃ Time 500 h Pressure 7. 8 MPa Concentration (ppb) DO 100 DH 10 H 2 O 2 200 Cr 5 Co-60 30 © Hitachi-GE Nuclear Energy, Ltd. 2010. All rights reserved. 8
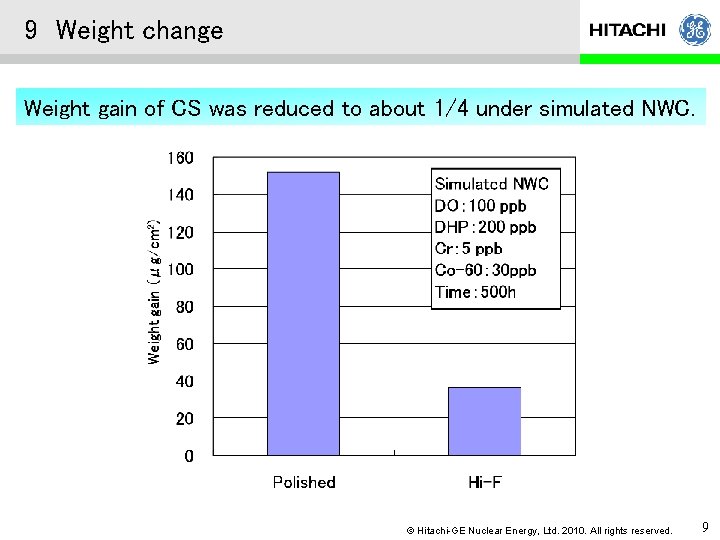
9 Weight change Weight gain of CS was reduced to about 1/4 under simulated NWC. © Hitachi-GE Nuclear Energy, Ltd. 2010. All rights reserved. 9
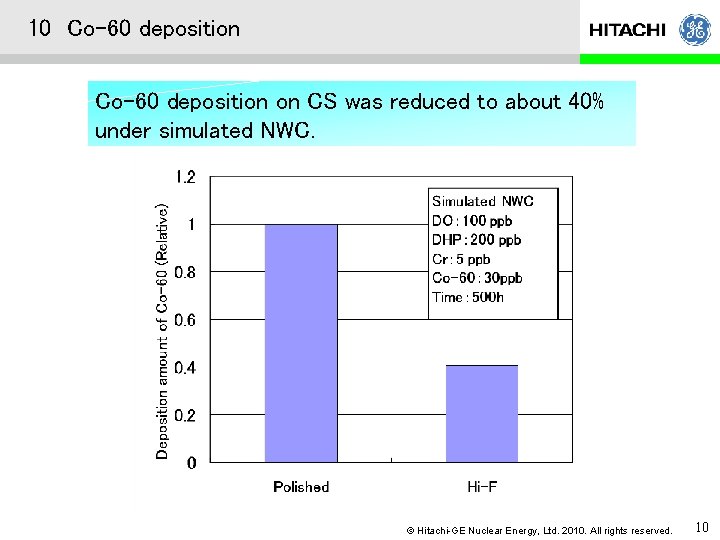
10 Co-60 deposition on CS was reduced to about 40% under simulated NWC. © Hitachi-GE Nuclear Energy, Ltd. 2010. All rights reserved. 10
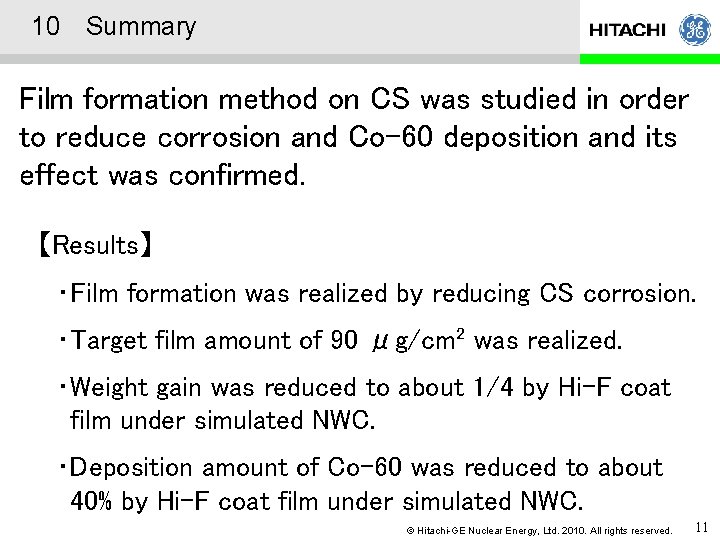
10 Summary Film formation method on CS was studied in order to reduce corrosion and Co-60 deposition and its effect was confirmed. 【Results】 ・Film formation was realized by reducing CS corrosion. ・Target film amount of 90 μg/cm 2 was realized. ・Weight gain was reduced to about 1/4 by Hi-F coat film under simulated NWC. ・Deposition amount of Co-60 was reduced to about 40% by Hi-F coat film under simulated NWC. © Hitachi-GE Nuclear Energy, Ltd. 2010. All rights reserved. 11
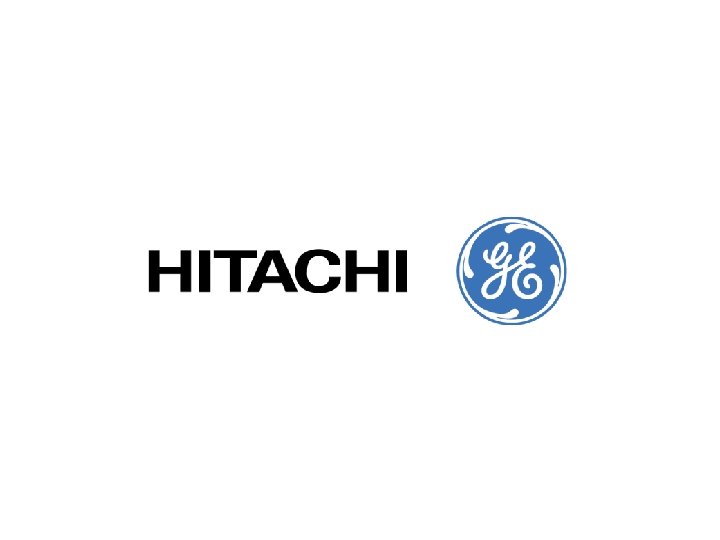
© Hitachi-GE Nuclear Energy, Ltd. 2010. All rights reserved. 12
Metodo iso e
Alara dirik
Alara ataacar
Alara şevket demirel ortaokulu
Alara princip
Alara facility management
Sporangiospor
Kalkoflor beyazı
Asia silicon valley development agency
Medium term development plan philippines
Riviere fabes symposium
Hixon symposium
Importance of symposium for students
International police executive symposium