Value Engineering Dresser Rand Compressor Case System Review
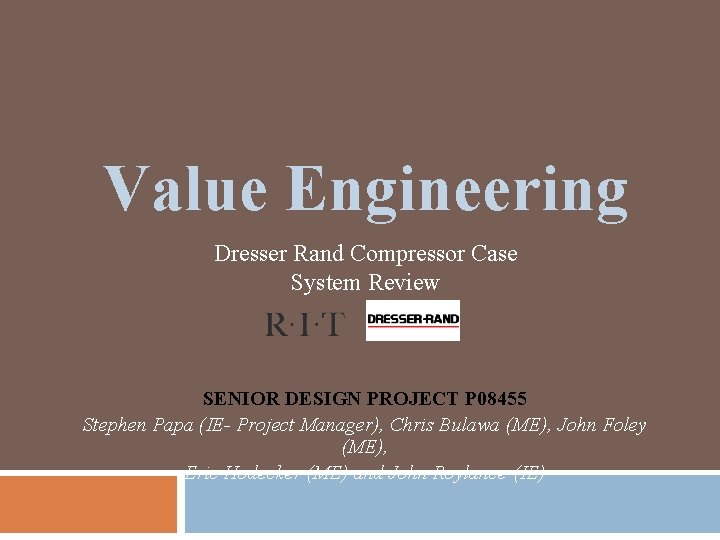
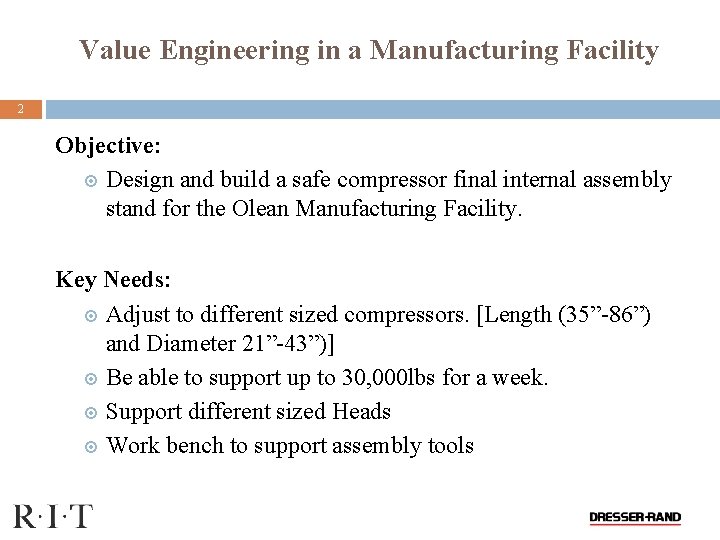
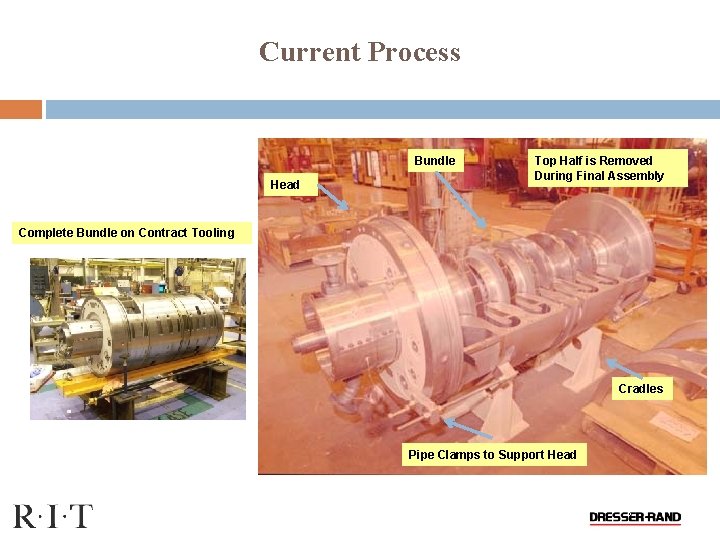
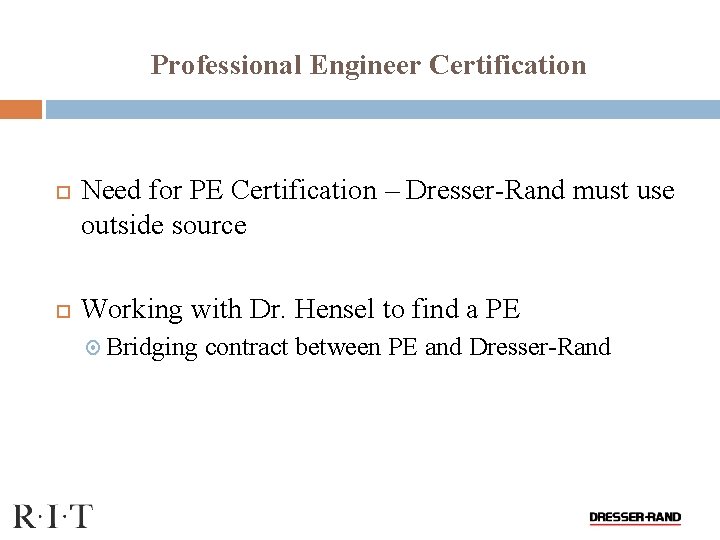
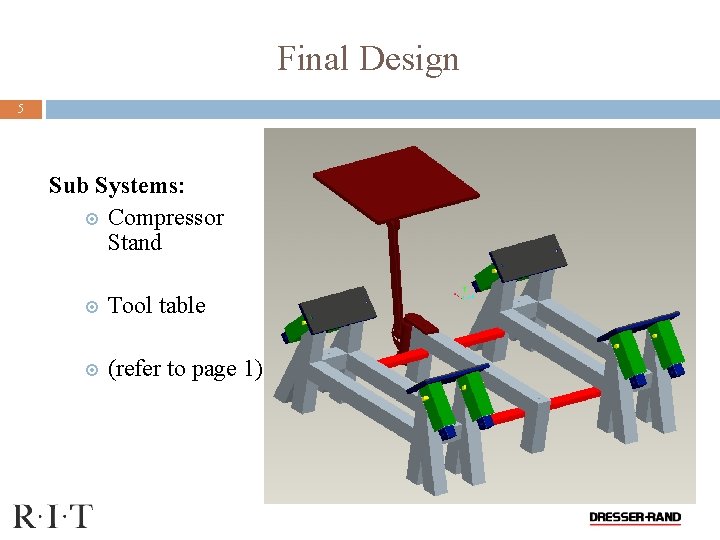
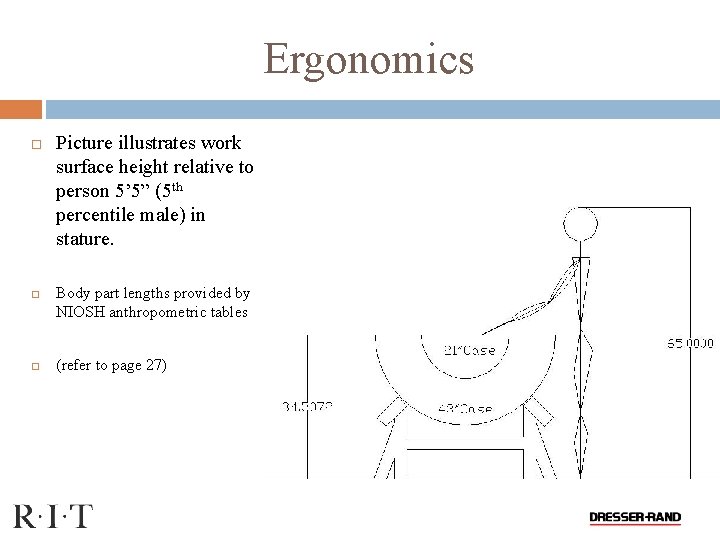
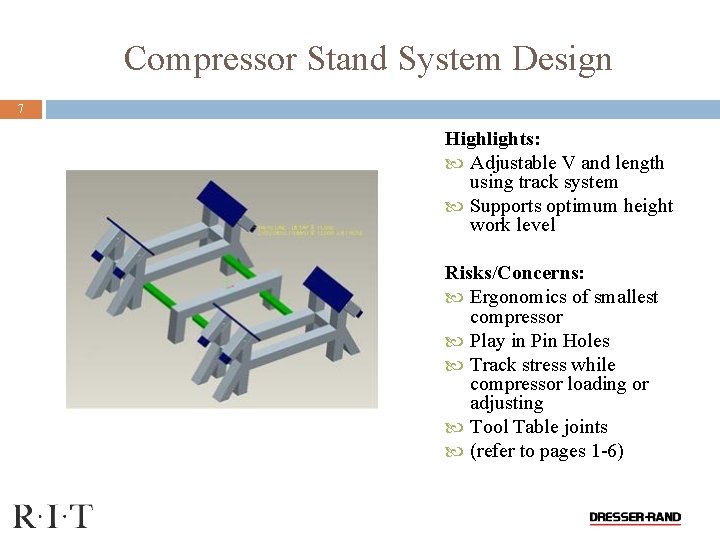
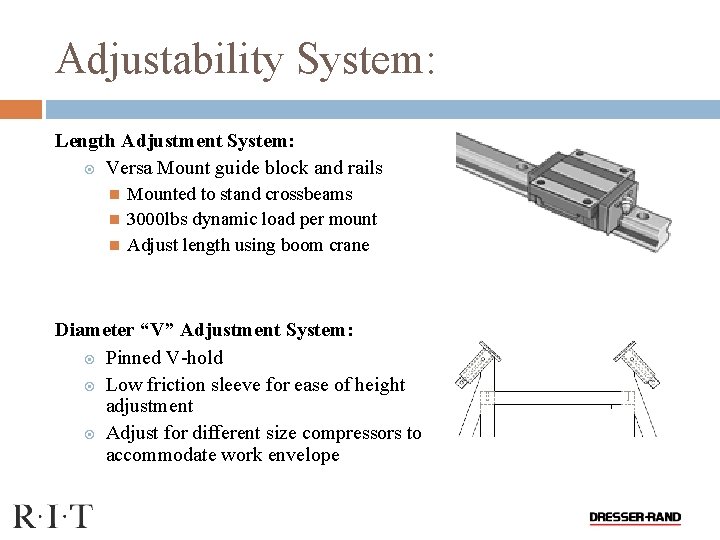
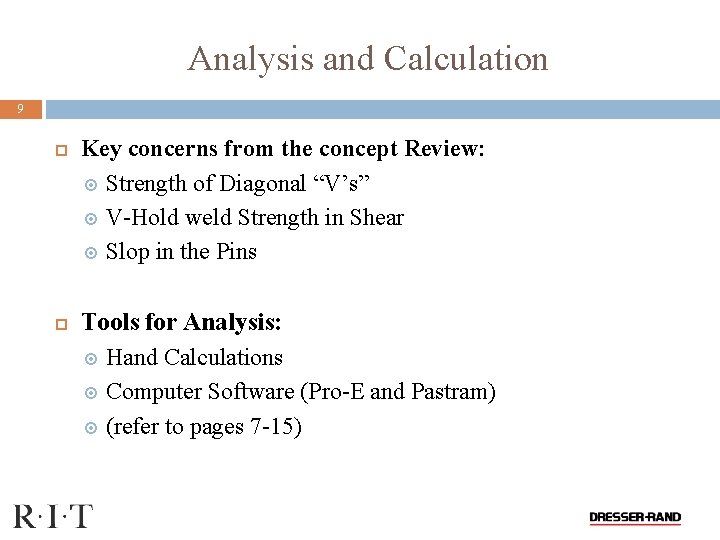
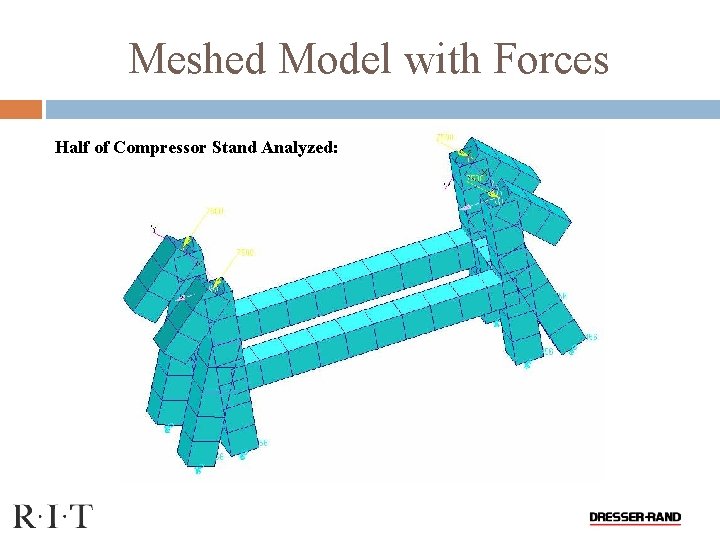
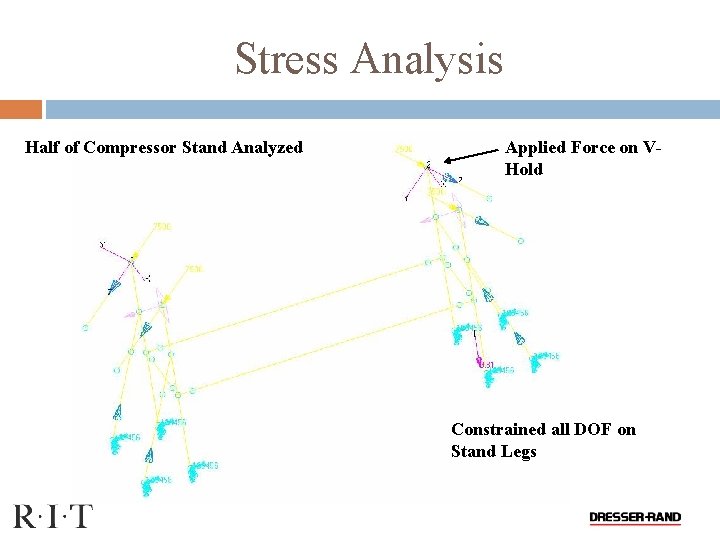
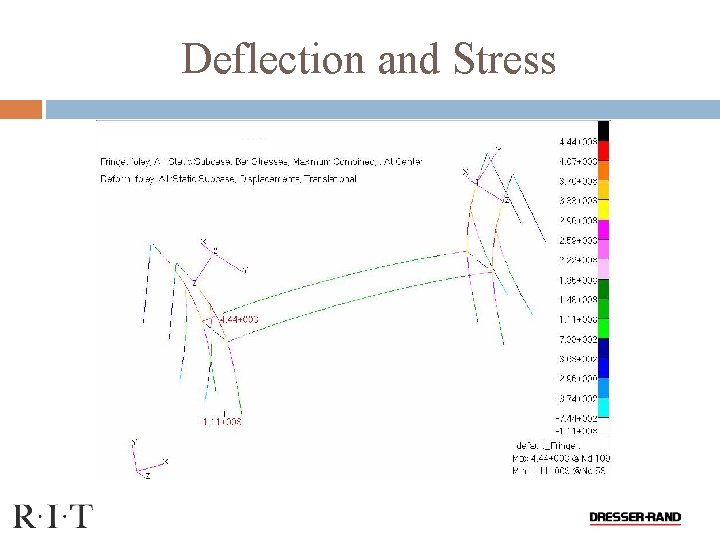
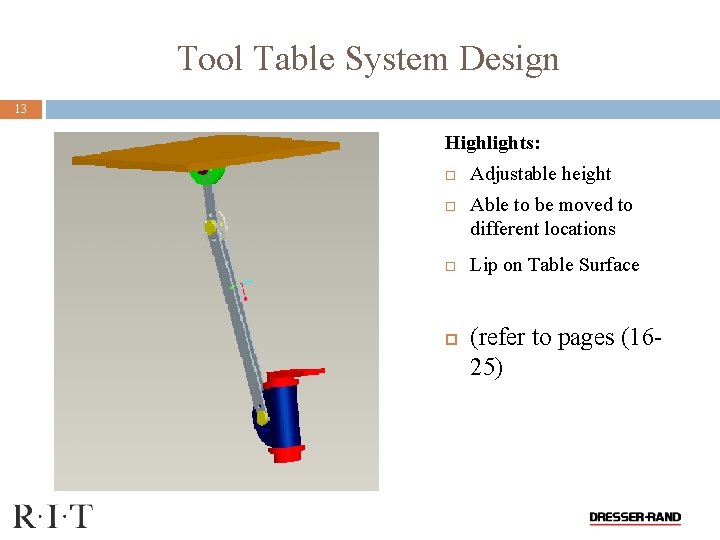
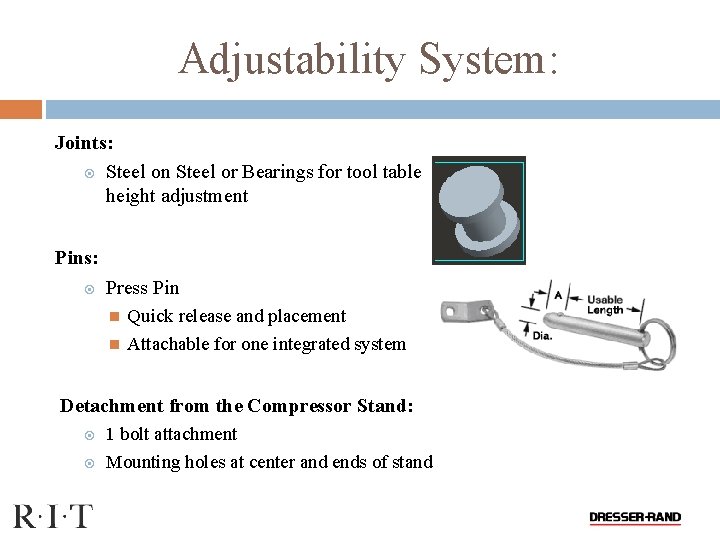
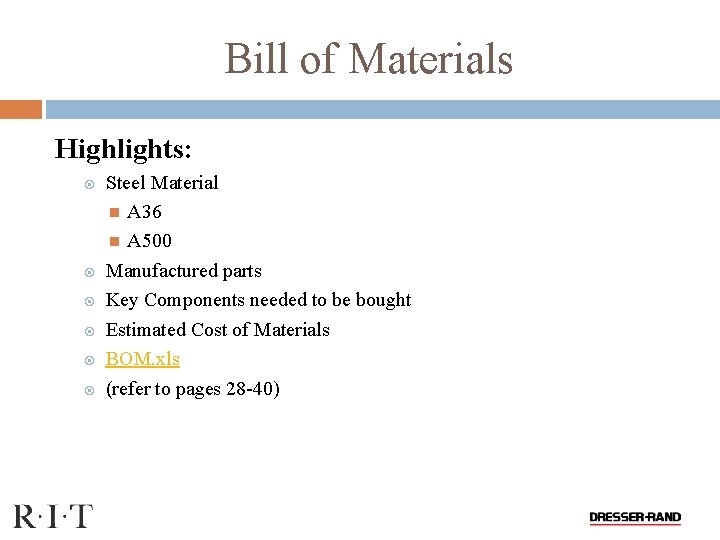
- Slides: 15
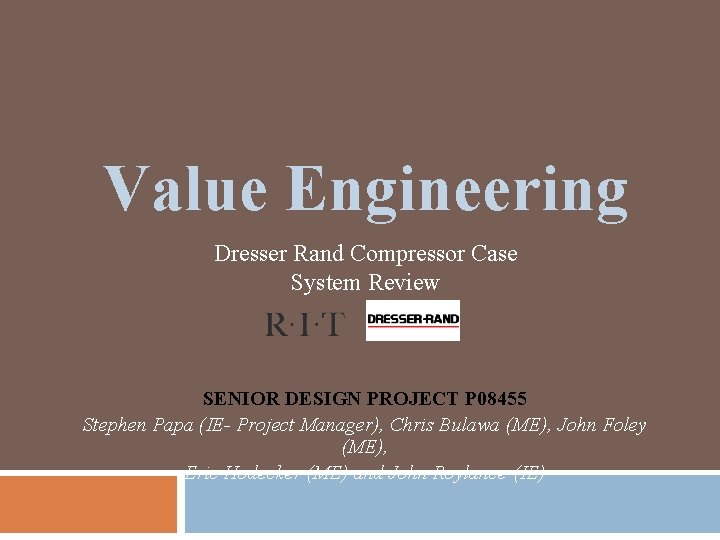
Value Engineering Dresser Rand Compressor Case System Review SENIOR DESIGN PROJECT P 08455 Stephen Papa (IE- Project Manager), Chris Bulawa (ME), John Foley (ME), Eric Hodecker (ME) and John Roylance-(IE)
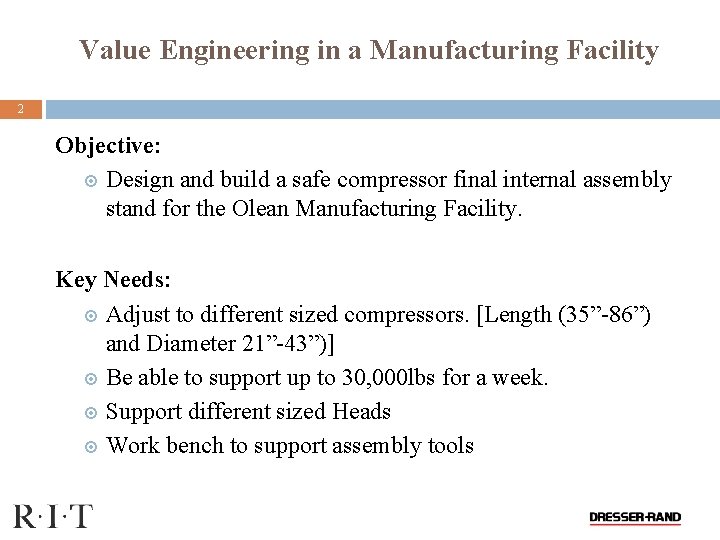
Value Engineering in a Manufacturing Facility 2 Objective: Design and build a safe compressor final internal assembly stand for the Olean Manufacturing Facility. Key Needs: Adjust to different sized compressors. [Length (35”-86”) and Diameter 21”-43”)] Be able to support up to 30, 000 lbs for a week. Support different sized Heads Work bench to support assembly tools
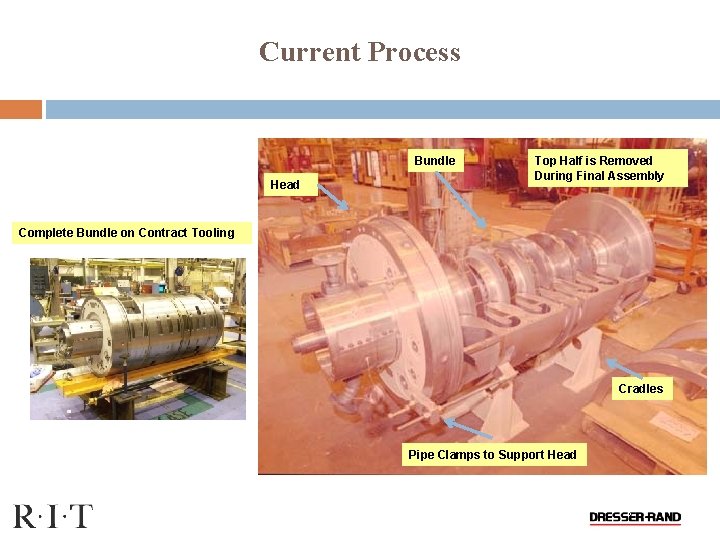
Current Process Bundle Head Top Half is Removed During Final Assembly Complete Bundle on Contract Tooling Cradles Pipe Clamps to Support Head 3
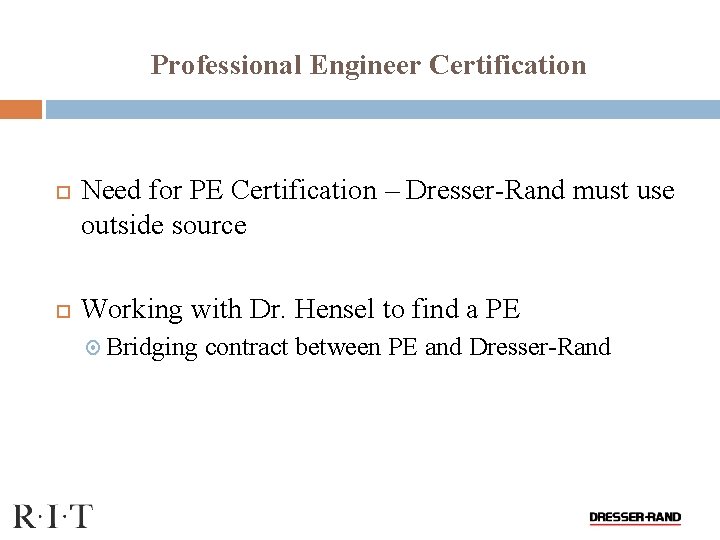
Professional Engineer Certification Need for PE Certification – Dresser-Rand must use outside source Working with Dr. Hensel to find a PE Bridging contract between PE and Dresser-Rand
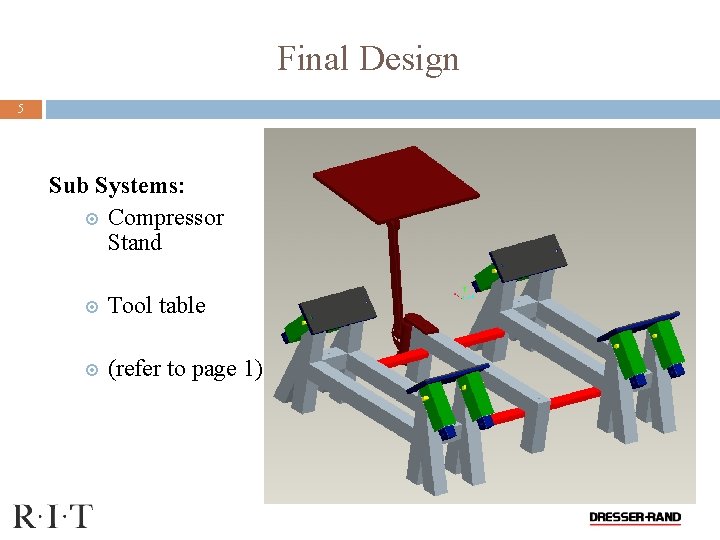
Final Design 5 Sub Systems: Compressor Stand Tool table (refer to page 1)
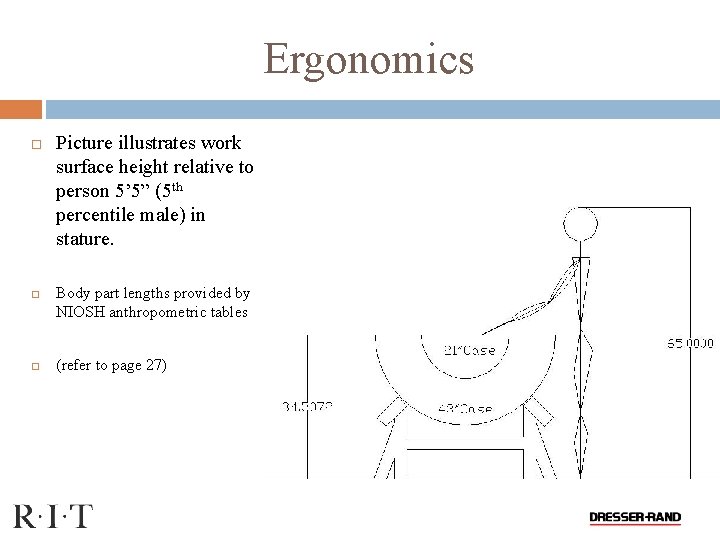
Ergonomics Picture illustrates work surface height relative to person 5’ 5” (5 th percentile male) in stature. Body part lengths provided by NIOSH anthropometric tables (refer to page 27)
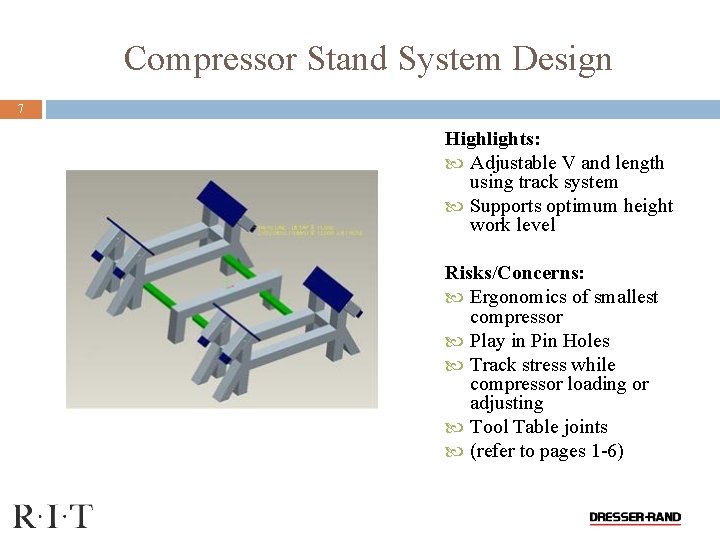
Compressor Stand System Design 7 Highlights: Adjustable V and length using track system Supports optimum height work level Risks/Concerns: Ergonomics of smallest compressor Play in Pin Holes Track stress while compressor loading or adjusting Tool Table joints (refer to pages 1 -6)
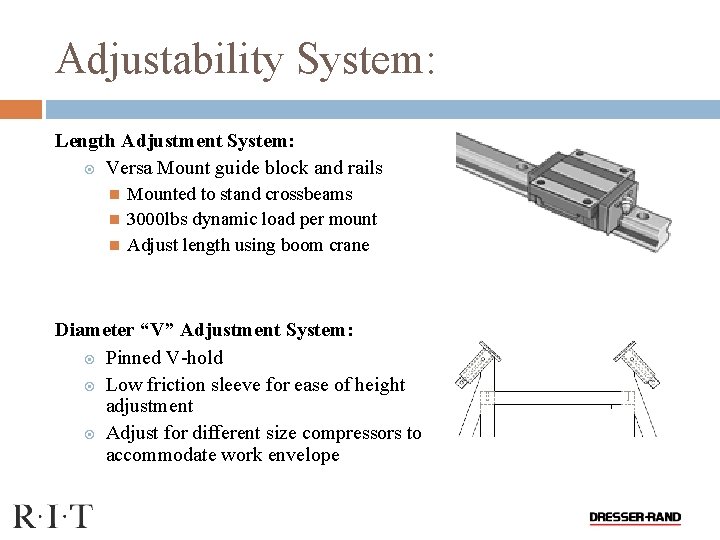
Adjustability System: Length Adjustment System: Versa Mount guide block and rails Mounted to stand crossbeams 3000 lbs dynamic load per mount Adjust length using boom crane Diameter “V” Adjustment System: Pinned V-hold Low friction sleeve for ease of height adjustment Adjust for different size compressors to accommodate work envelope
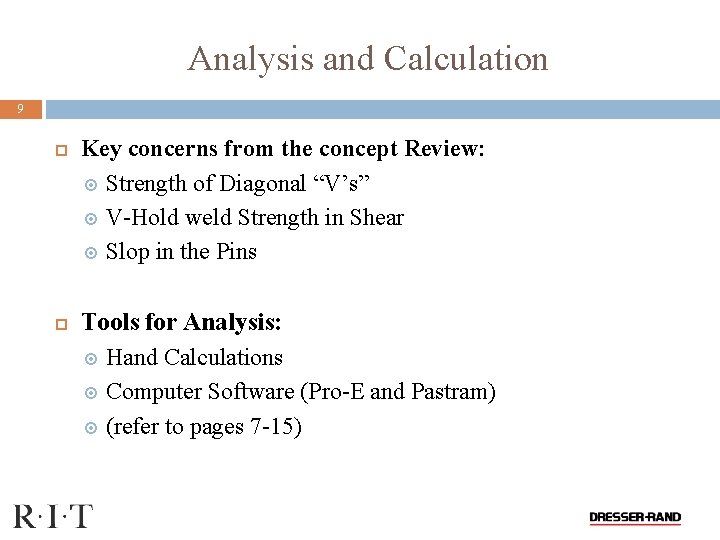
Analysis and Calculation 9 Key concerns from the concept Review: Strength of Diagonal “V’s” V-Hold weld Strength in Shear Slop in the Pins Tools for Analysis: Hand Calculations Computer Software (Pro-E and Pastram) (refer to pages 7 -15)
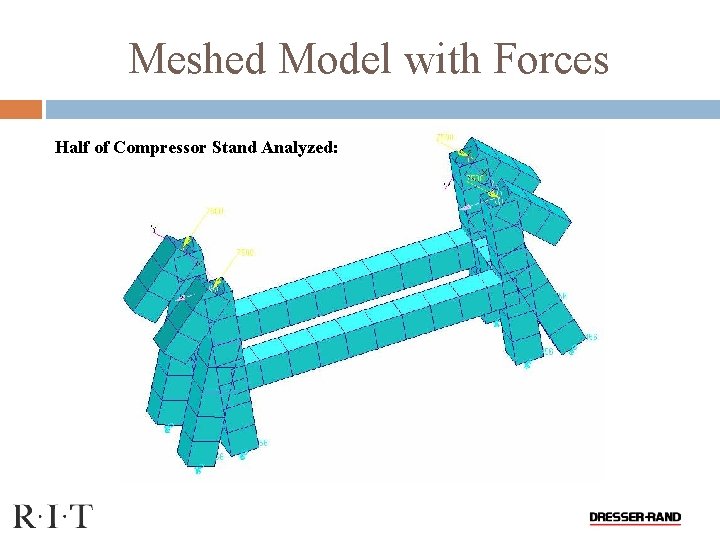
Meshed Model with Forces Half of Compressor Stand Analyzed:
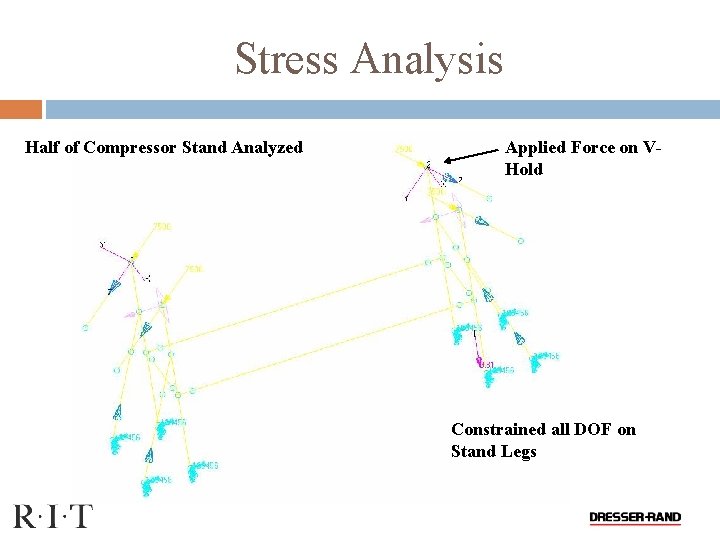
Stress Analysis Half of Compressor Stand Analyzed Applied Force on VHold Constrained all DOF on Stand Legs
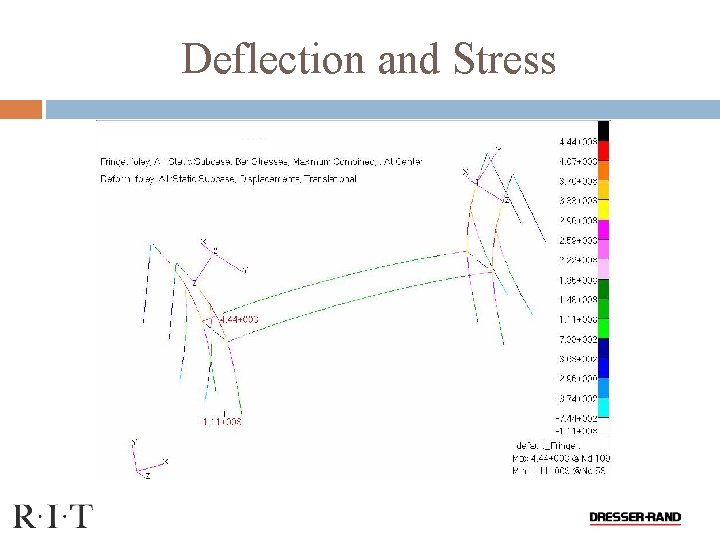
Deflection and Stress
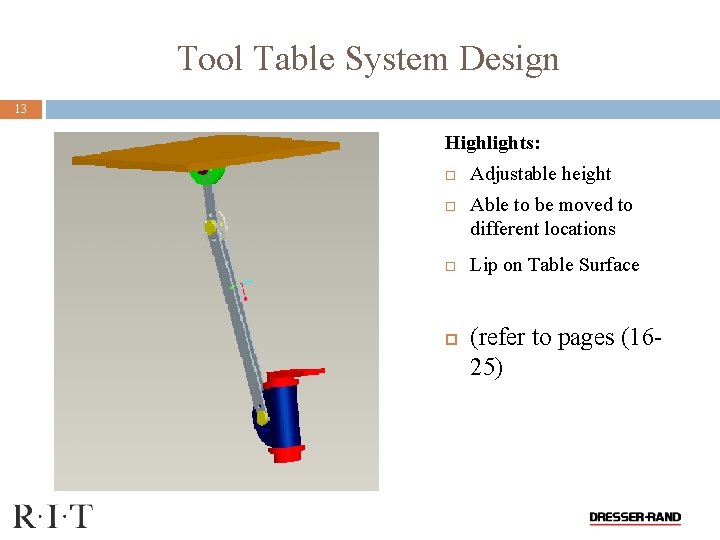
Tool Table System Design 13 Highlights: Adjustable height Able to be moved to different locations Lip on Table Surface (refer to pages (1625)
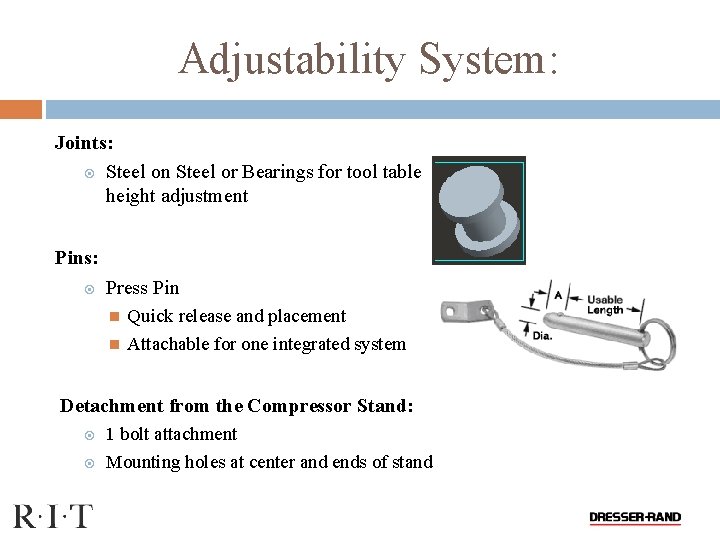
Adjustability System: Joints: Steel on Steel or Bearings for tool table height adjustment Pins: Press Pin Quick release and placement Attachable for one integrated system Detachment from the Compressor Stand: 1 bolt attachment Mounting holes at center and ends of stand
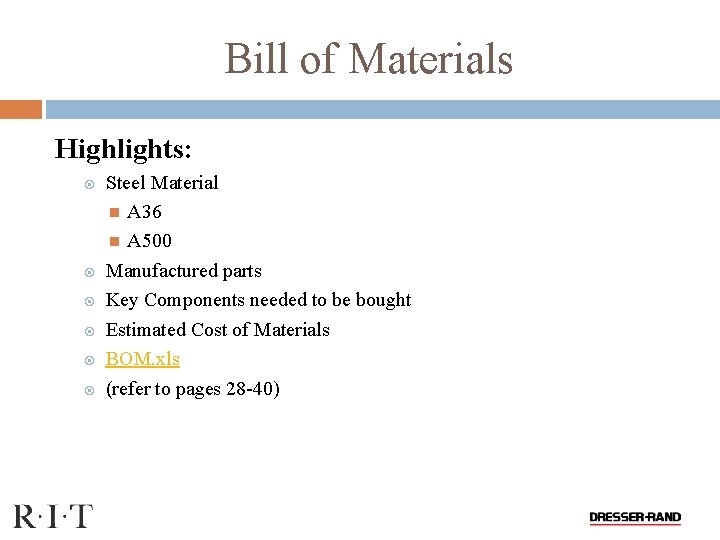
Bill of Materials Highlights: Steel Material A 36 A 500 Manufactured parts Key Components needed to be bought Estimated Cost of Materials BOM. xls (refer to pages 28 -40)
Best worst and average case
Penciptaan nilai adalah
Case western reserve university case school of engineering
A dresser drawer contains one pair of socks
Perspective drawing examples
Christopher dresser teapot
Solve the following riddles
On one corner of my dresser sits a smiling toy clown
What is the purpose of descriptive writing?
System architecture example
Cutii lungi cu scaunele stau scolarii in rand in ele
Paul rand
Rand afrikaans university
Anthem author rand
Rand() % 10
Iscilab