Transient Analysis of Heat Transfer and Fluid Flow
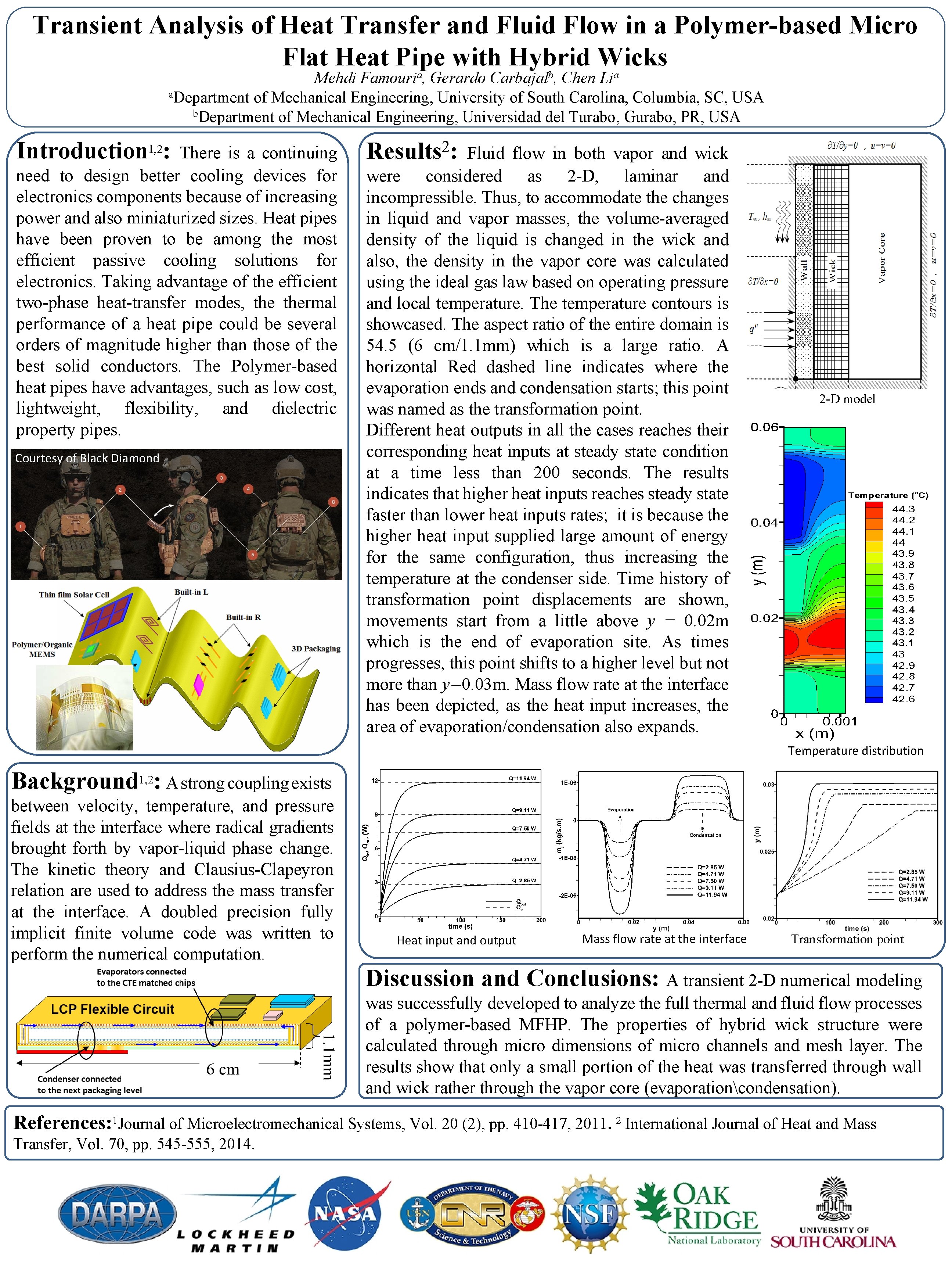
- Slides: 1
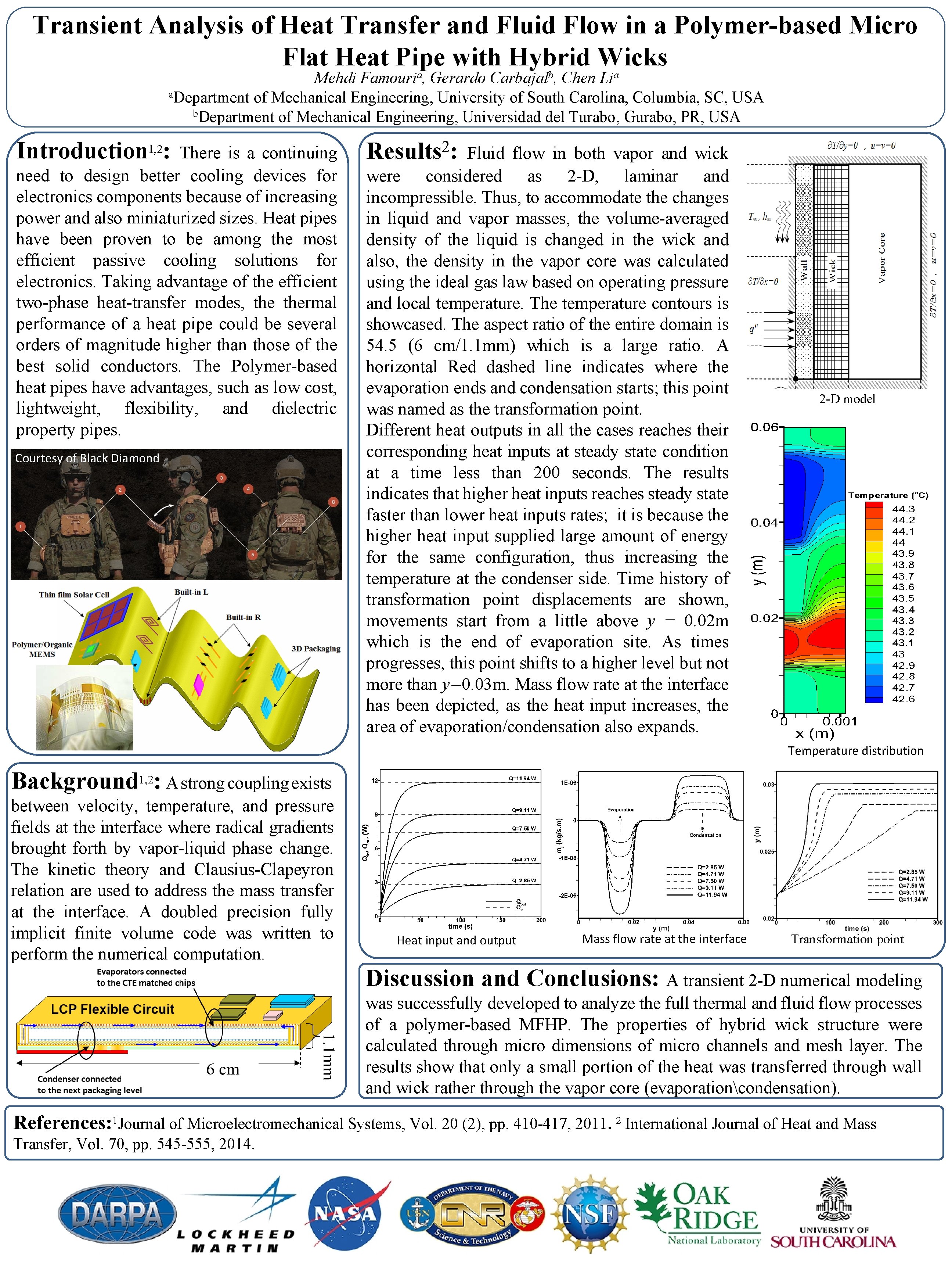
Transient Analysis of Heat Transfer and Fluid Flow in a Polymer-based Micro Flat Heat Pipe with Hybrid Wicks a b a Mehdi Famouri , Gerardo Carbajal , Chen Li a. Department of Mechanical Engineering, University of South Carolina, Columbia, SC, USA b. Department of Mechanical Engineering, Universidad del Turabo, Gurabo, PR, USA Introduction : There is a continuing need to design better cooling devices for electronics components because of increasing power and also miniaturized sizes. Heat pipes have been proven to be among the most efficient passive cooling solutions for electronics. Taking advantage of the efficient two-phase heat-transfer modes, thermal performance of a heat pipe could be several orders of magnitude higher than those of the best solid conductors. The Polymer-based heat pipes have advantages, such as low cost, lightweight, flexibility, and dielectric property pipes. 1, 2 Courtesy of Black Diamond 2 Results : Fluid flow in both vapor and wick were considered as 2 -D, laminar and incompressible. Thus, to accommodate the changes in liquid and vapor masses, the volume-averaged density of the liquid is changed in the wick and also, the density in the vapor core was calculated using the ideal gas law based on operating pressure and local temperature. The temperature contours is showcased. The aspect ratio of the entire domain is 54. 5 (6 cm/1. 1 mm) which is a large ratio. A horizontal Red dashed line indicates where the evaporation ends and condensation starts; this point was named as the transformation point. Different heat outputs in all the cases reaches their corresponding heat inputs at steady state condition at a time less than 200 seconds. The results indicates that higher heat inputs reaches steady state faster than lower heat inputs rates; it is because the higher heat input supplied large amount of energy for the same configuration, thus increasing the temperature at the condenser side. Time history of transformation point displacements are shown, movements start from a little above y = 0. 02 m which is the end of evaporation site. As times progresses, this point shifts to a higher level but not more than y=0. 03 m. Mass flow rate at the interface has been depicted, as the heat input increases, the area of evaporation/condensation also expands. 2 -D model Temperature distribution Background : A strong coupling exists 1, 2 between velocity, temperature, and pressure fields at the interface where radical gradients brought forth by vapor-liquid phase change. The kinetic theory and Clausius-Clapeyron relation are used to address the mass transfer at the interface. A doubled precision fully implicit finite volume code was written to perform the numerical computation. Heat input and output Mass flow rate at the interface Transformation point Discussion and Conclusions: A transient 2 -D numerical modeling was successfully developed to analyze the full thermal and fluid flow processes of a polymer-based MFHP. The properties of hybrid wick structure were calculated through micro dimensions of micro channels and mesh layer. The results show that only a small portion of the heat was transferred through wall and wick rather through the vapor core (evaporationcondensation). References: 1 Journal of Microelectromechanical Systems, Vol. 20 (2), pp. 410 -417, 2011. 2 International Journal of Heat and Mass Transfer, Vol. 70, pp. 545 -555, 2014.