Topic31 LIMITATIONS of USFD Limitation of USFD 05
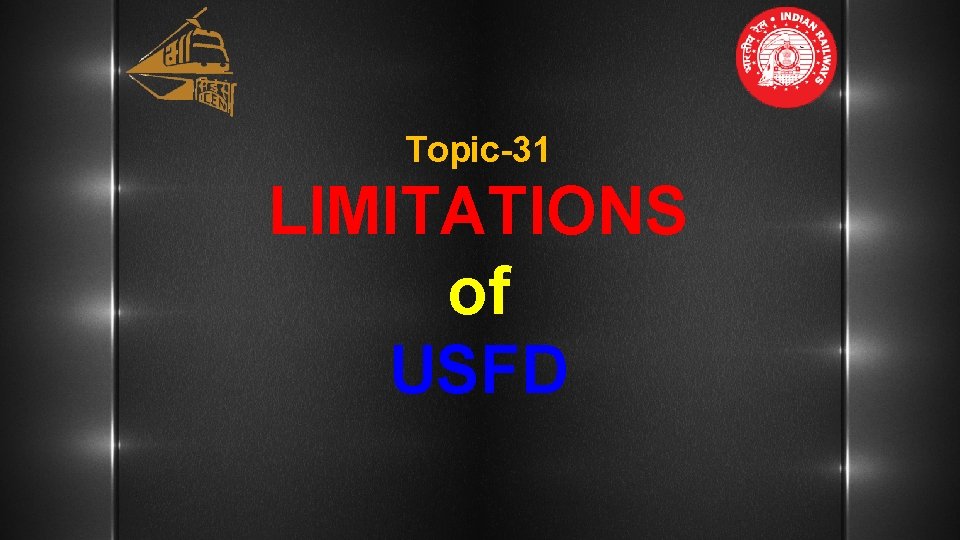
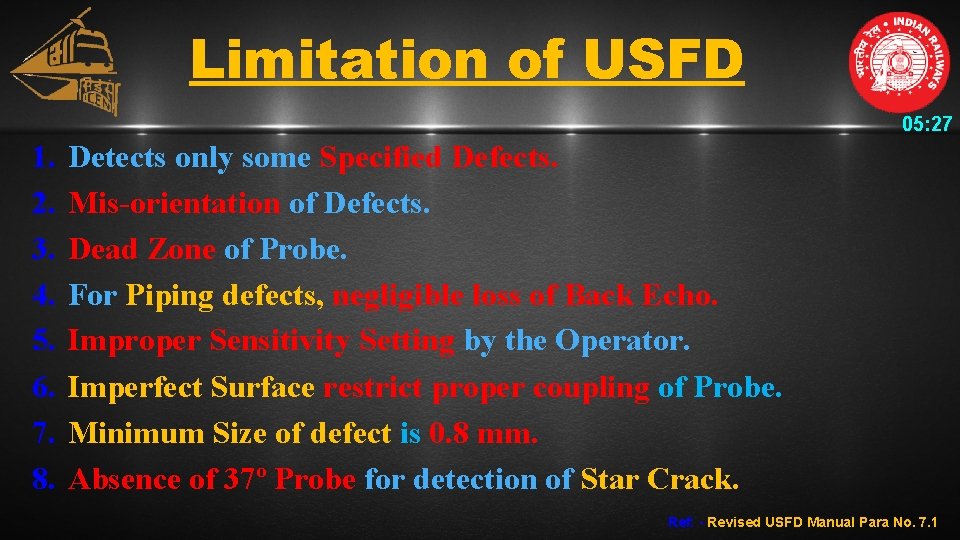
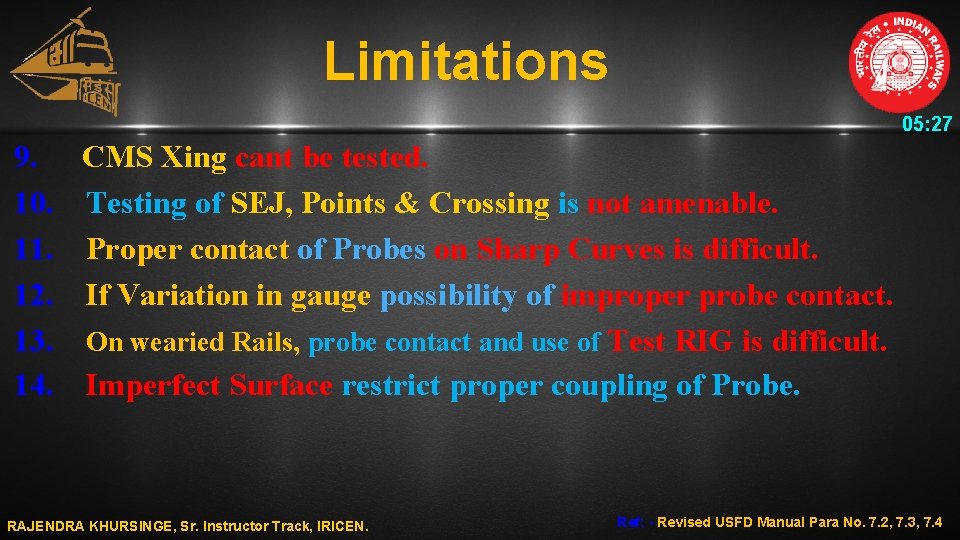
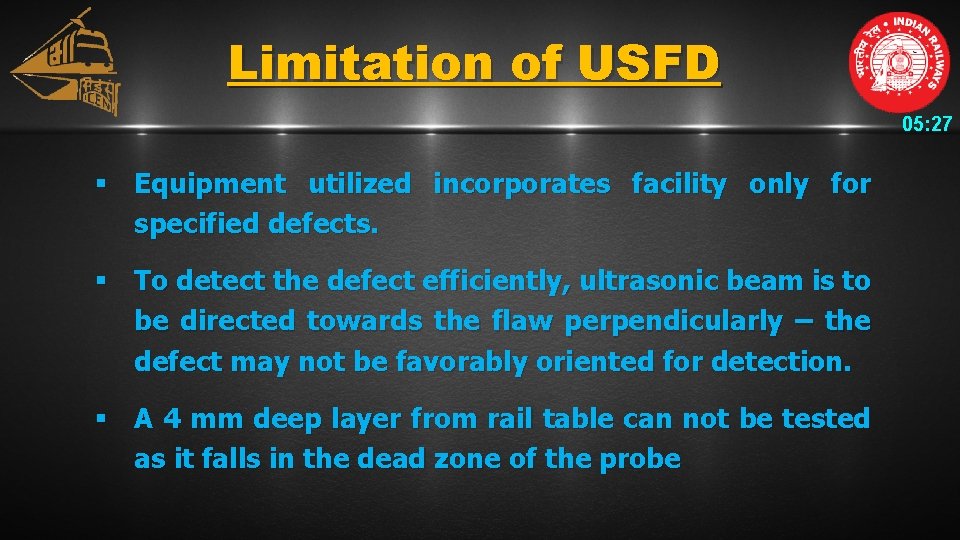
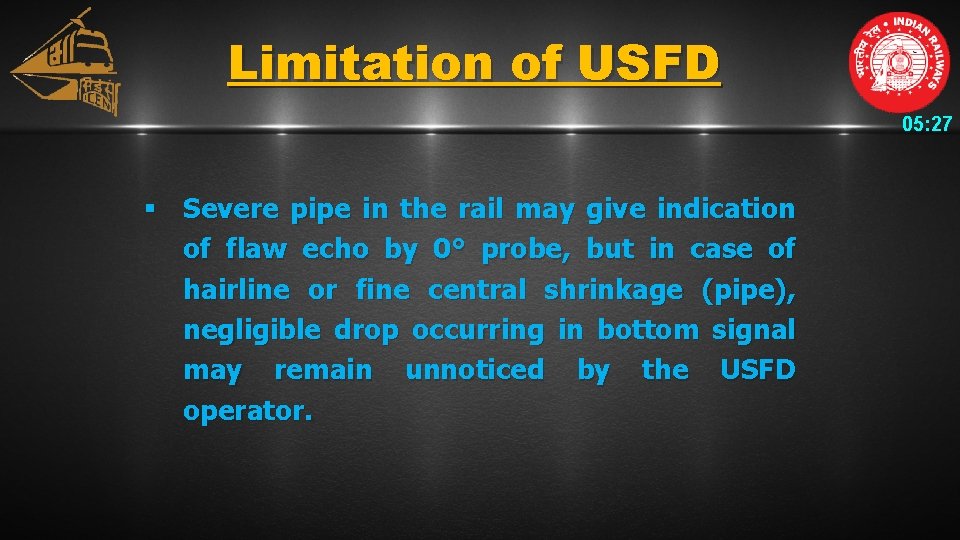
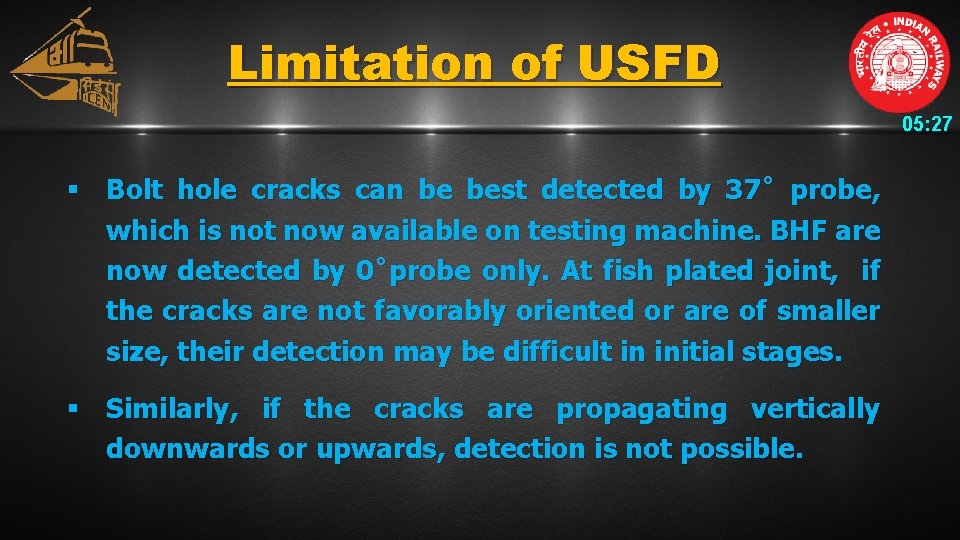
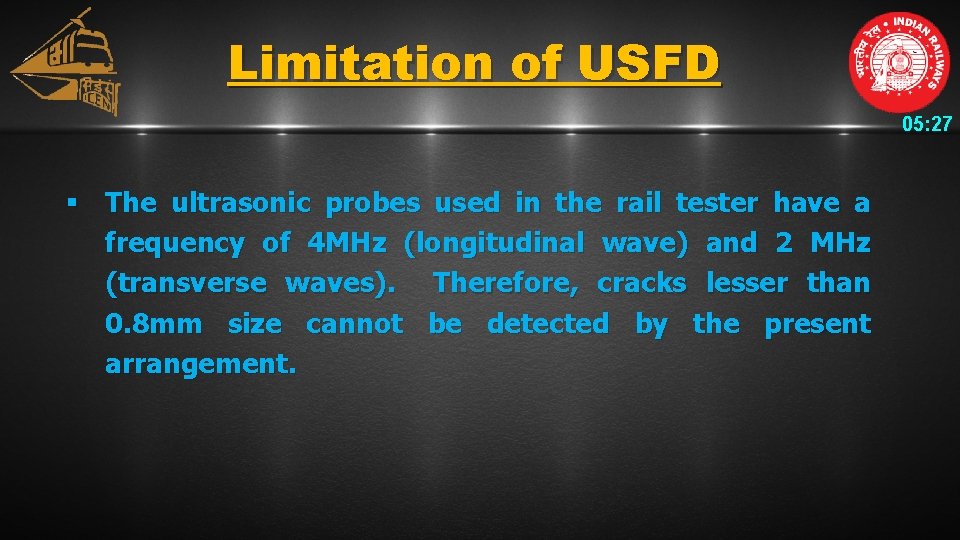
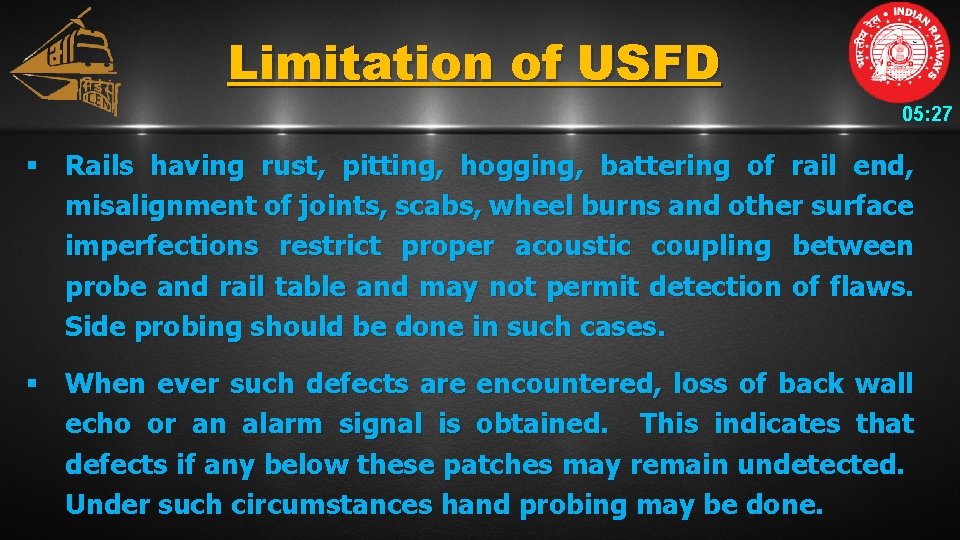
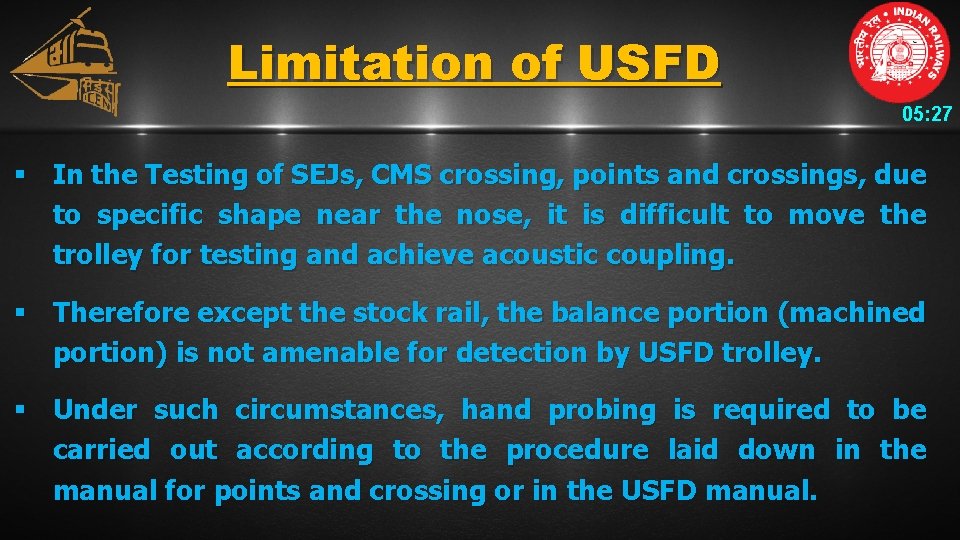
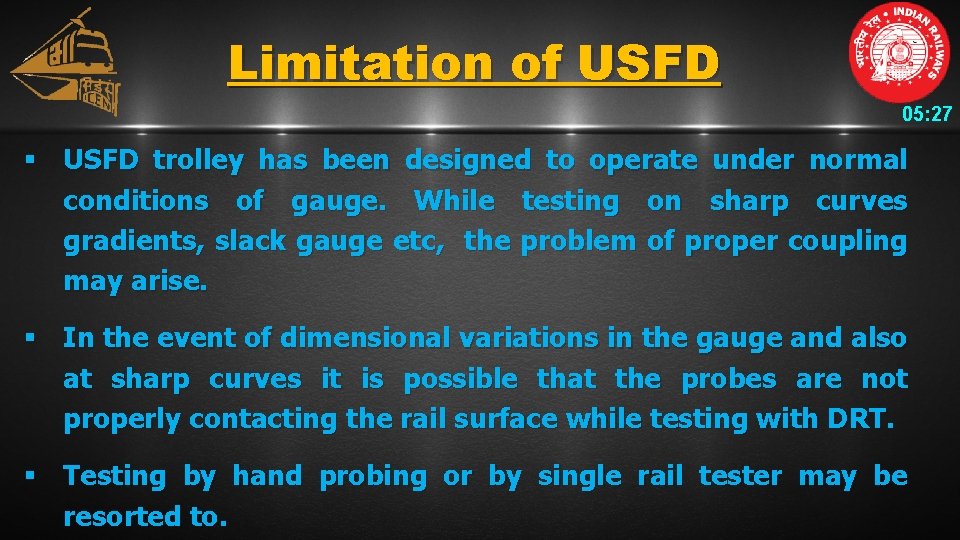
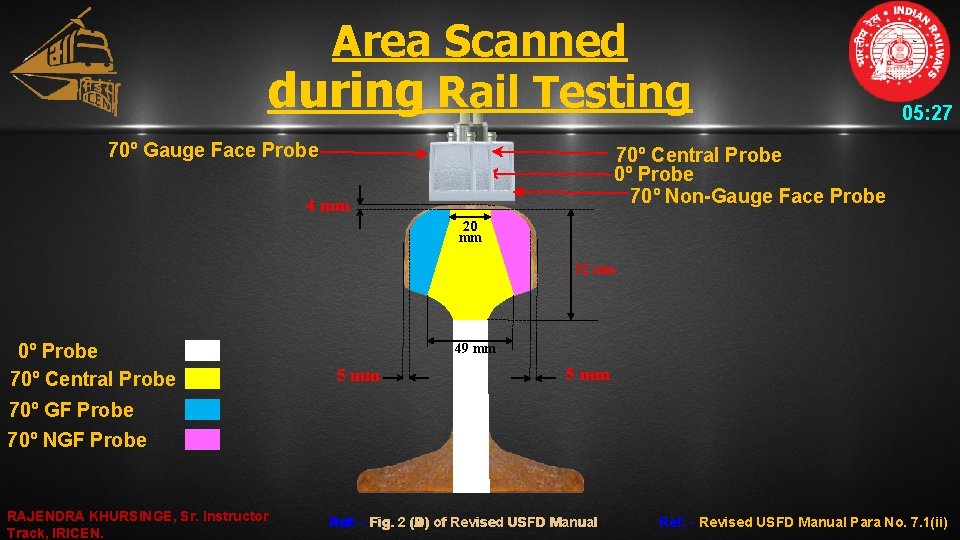
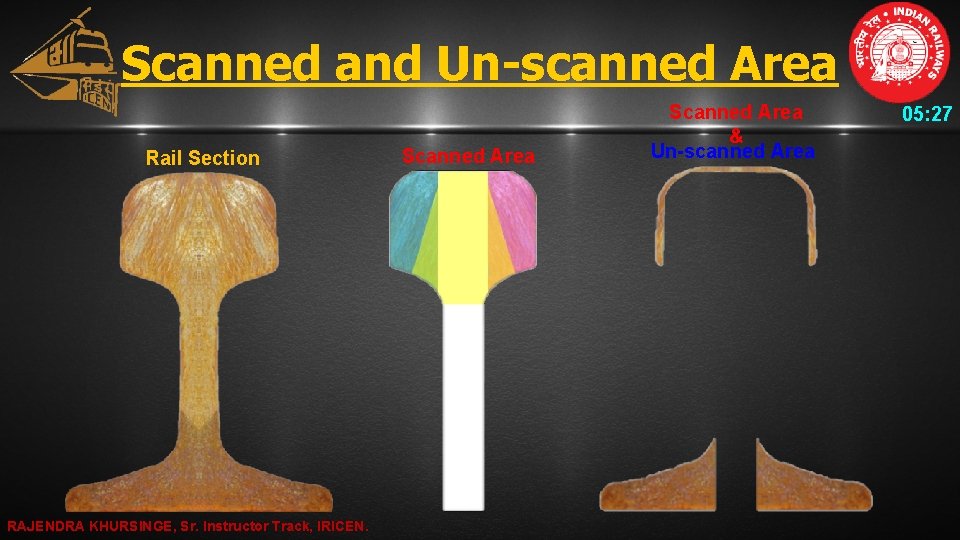
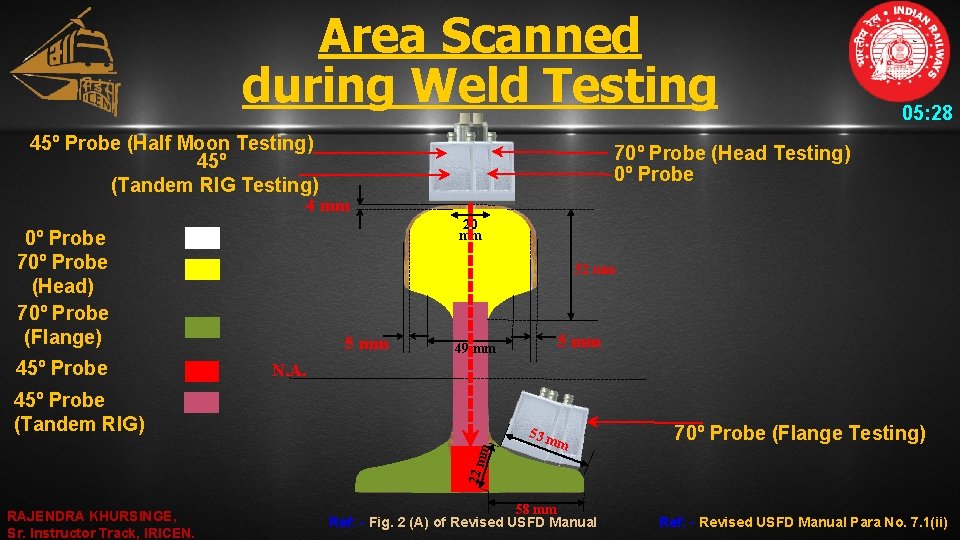
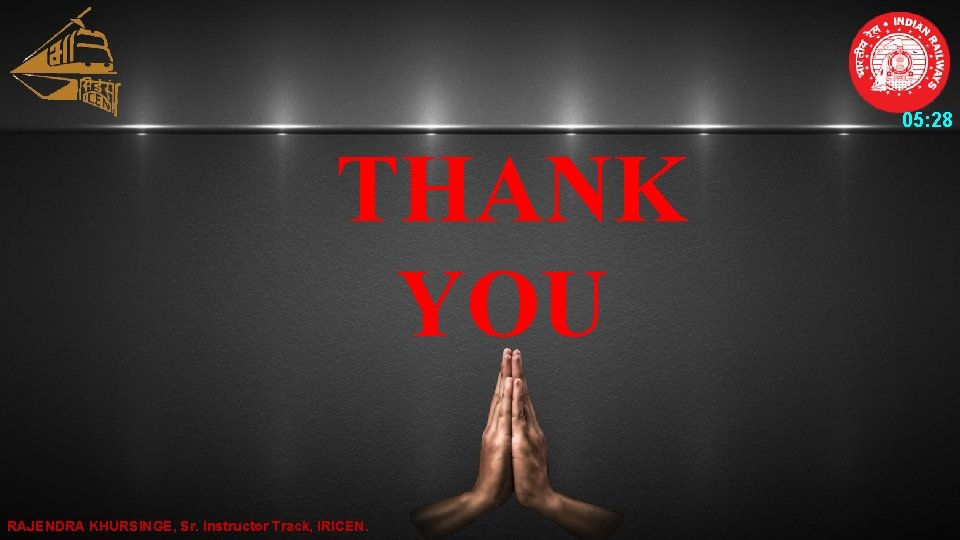
- Slides: 14
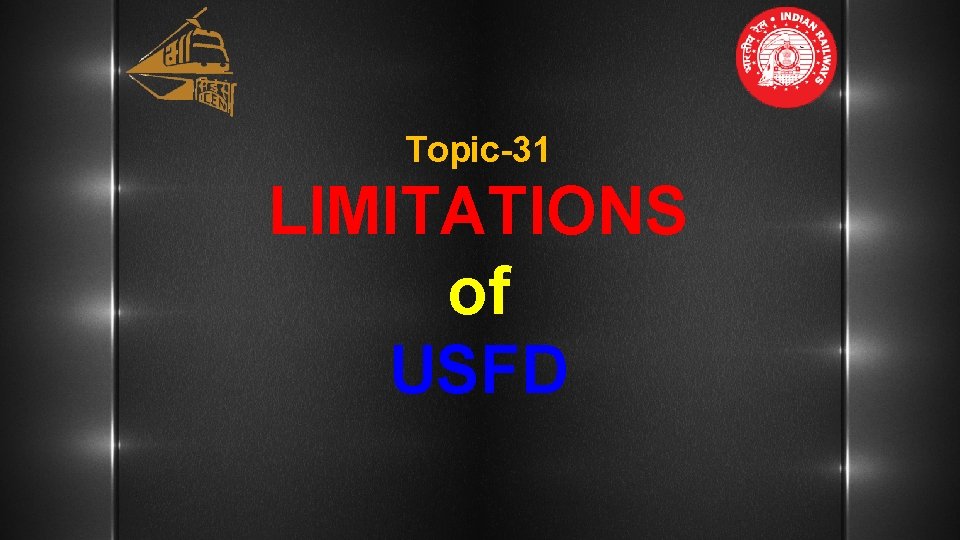
Topic-31 LIMITATIONS of USFD
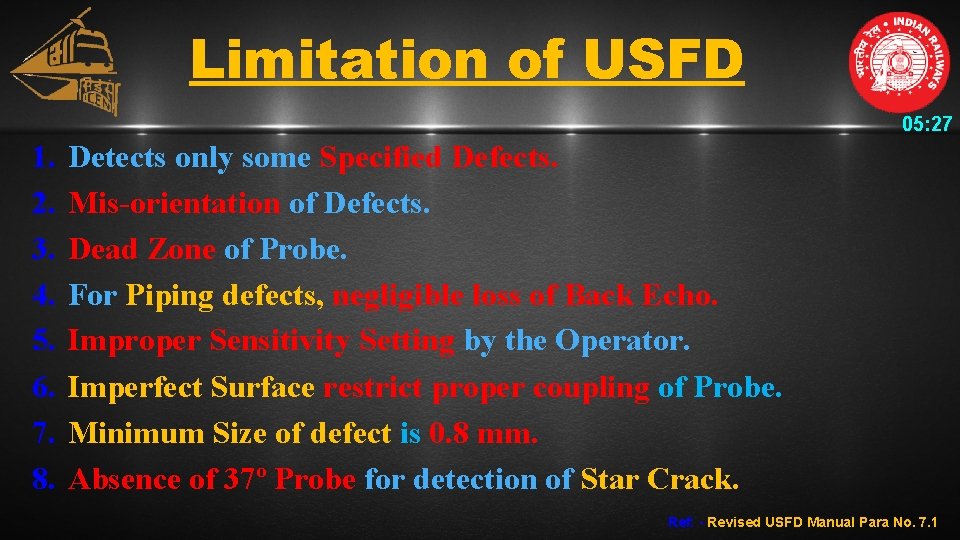
Limitation of USFD 05: 27 1. 2. 3. 4. 5. 6. 7. 8. Detects only some Specified Defects. Mis-orientation of Defects. Dead Zone of Probe. For Piping defects, negligible loss of Back Echo. Improper Sensitivity Setting by the Operator. Imperfect Surface restrict proper coupling of Probe. Minimum Size of defect is 0. 8 mm. Absence of 37º Probe for detection of Star Crack. Ref: - Revised USFD Manual Para No. 7. 1
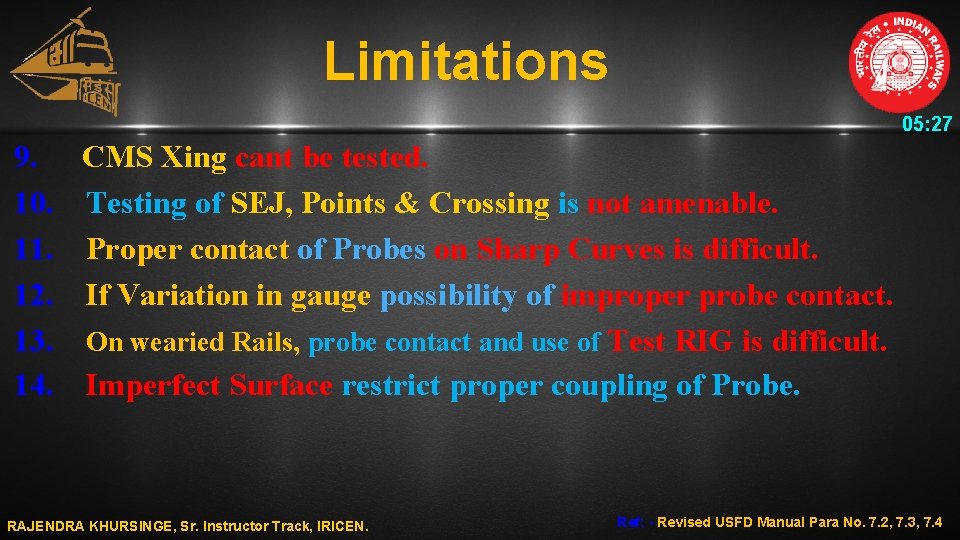
Limitations 05: 27 9. CMS Xing cant be tested. 10. Testing of SEJ, Points & Crossing is not amenable. 11. Proper contact of Probes on Sharp Curves is difficult. 12. If Variation in gauge possibility of improper probe contact. 13. On wearied Rails, probe contact and use of Test RIG is difficult. 14. Imperfect Surface restrict proper coupling of Probe. RAJENDRA KHURSINGE, Sr. Instructor Track, IRICEN. Ref: - Revised USFD Manual Para No. 7. 2, 7. 3, 7. 4
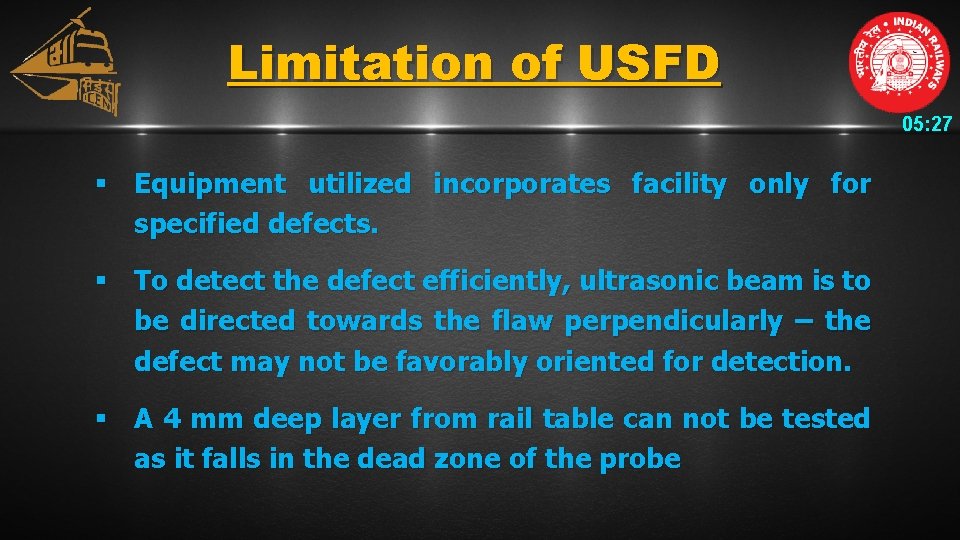
Limitation of USFD 05: 27 § Equipment utilized incorporates facility only for specified defects. § To detect the defect efficiently, ultrasonic beam is to be directed towards the flaw perpendicularly – the defect may not be favorably oriented for detection. § A 4 mm deep layer from rail table can not be tested as it falls in the dead zone of the probe
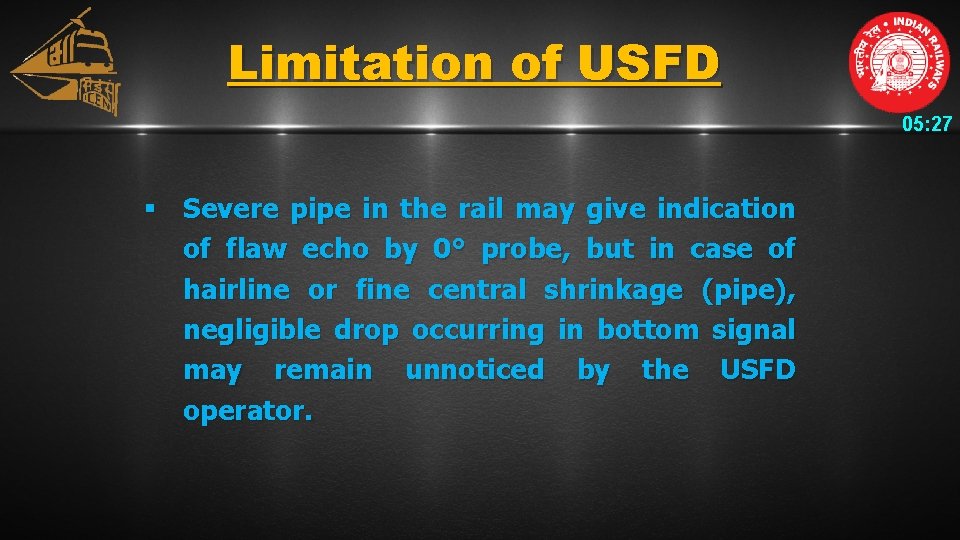
Limitation of USFD 05: 27 § Severe pipe in the rail may give indication of flaw echo by 0° probe, but in case of hairline or fine central shrinkage (pipe), negligible drop occurring in bottom signal may remain unnoticed by the USFD operator.
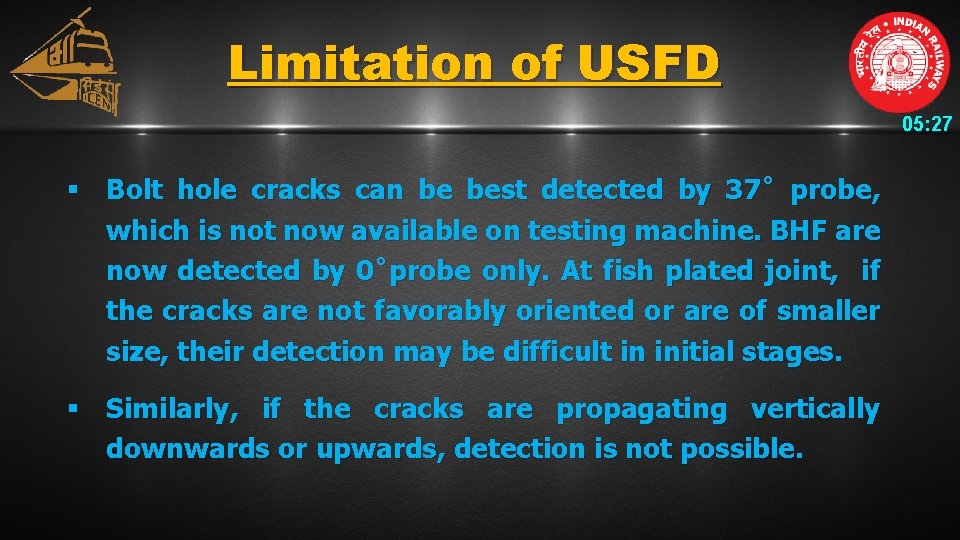
Limitation of USFD 05: 27 § Bolt hole cracks can be best detected by 37˚ probe, which is not now available on testing machine. BHF are now detected by 0˚probe only. At fish plated joint, if the cracks are not favorably oriented or are of smaller size, their detection may be difficult in initial stages. § Similarly, if the cracks are propagating vertically downwards or upwards, detection is not possible.
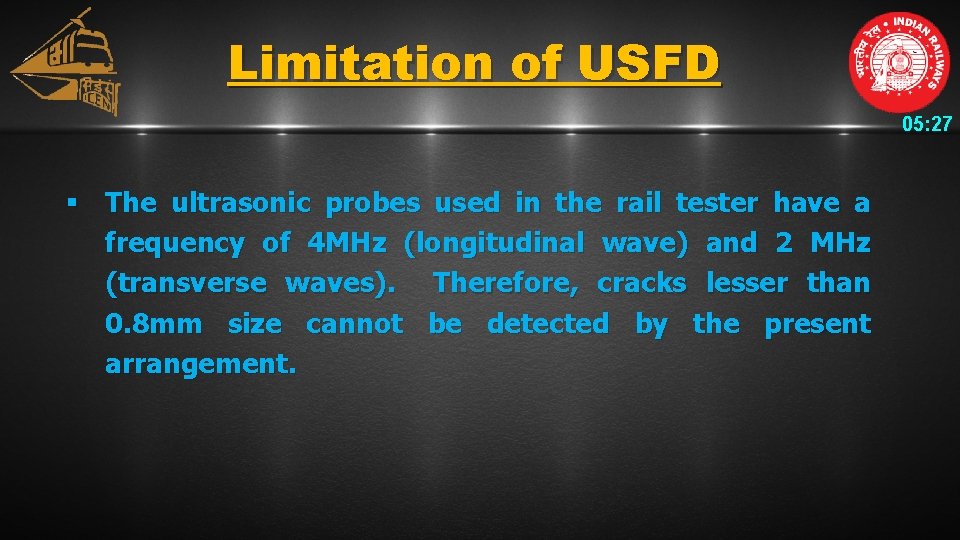
Limitation of USFD 05: 27 § The ultrasonic probes used in the rail tester have a frequency of 4 MHz (longitudinal wave) and 2 MHz (transverse waves). Therefore, cracks lesser than 0. 8 mm size cannot be detected by the present arrangement.
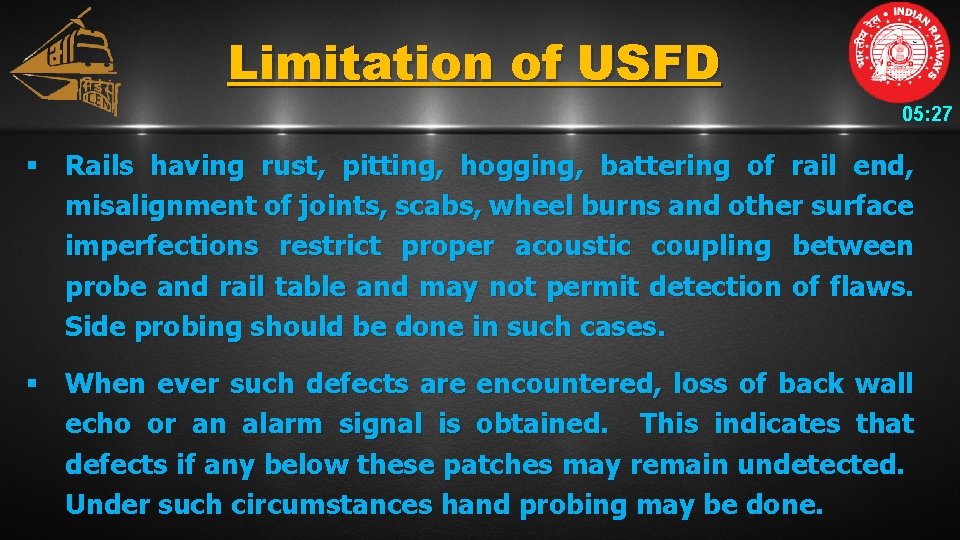
Limitation of USFD 05: 27 § Rails having rust, pitting, hogging, battering of rail end, misalignment of joints, scabs, wheel burns and other surface imperfections restrict proper acoustic coupling between probe and rail table and may not permit detection of flaws. Side probing should be done in such cases. § When ever such defects are encountered, loss of back wall echo or an alarm signal is obtained. This indicates that defects if any below these patches may remain undetected. Under such circumstances hand probing may be done.
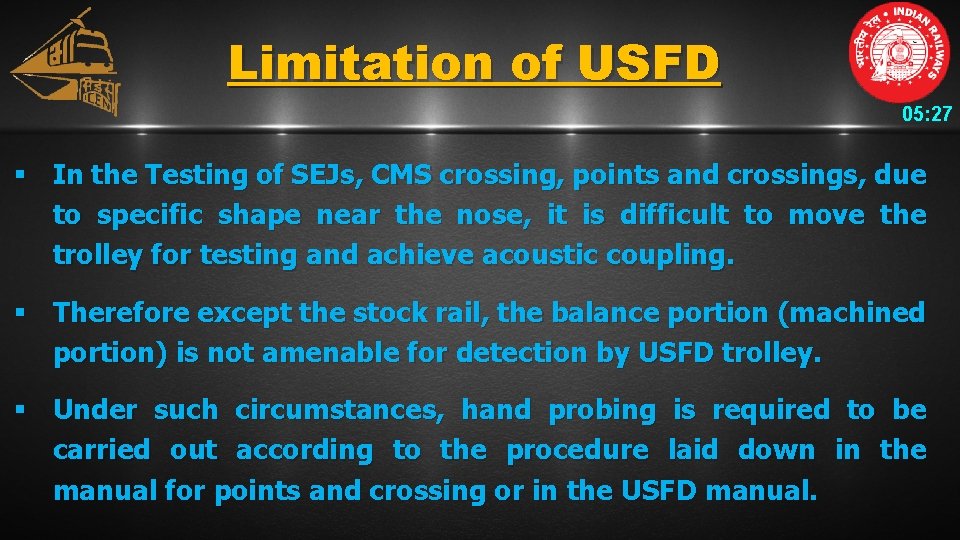
Limitation of USFD 05: 27 § In the Testing of SEJs, CMS crossing, points and crossings, due to specific shape near the nose, it is difficult to move the trolley for testing and achieve acoustic coupling. § Therefore except the stock rail, the balance portion (machined portion) is not amenable for detection by USFD trolley. § Under such circumstances, hand probing is required to be carried out according to the procedure laid down in the manual for points and crossing or in the USFD manual.
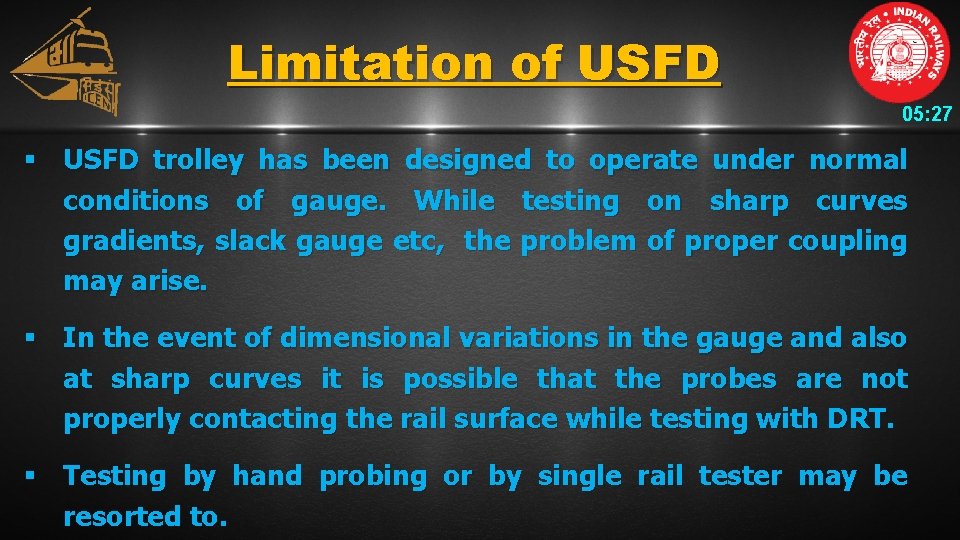
Limitation of USFD 05: 27 § USFD trolley has been designed to operate under normal conditions of gauge. While testing on sharp curves gradients, slack gauge etc, the problem of proper coupling may arise. § In the event of dimensional variations in the gauge and also at sharp curves it is possible that the probes are not properly contacting the rail surface while testing with DRT. § Testing by hand probing or by single rail tester may be resorted to.
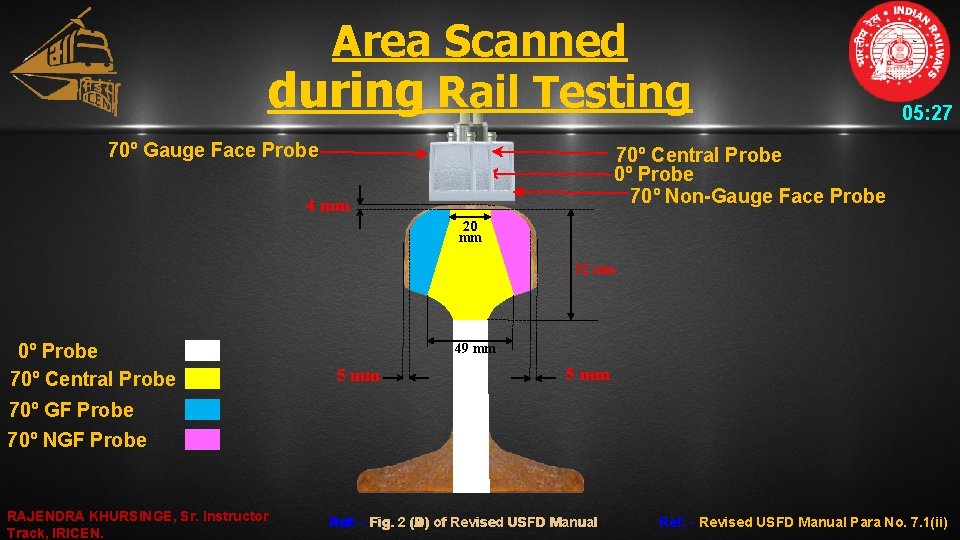
Area Scanned during Rail Testing 70º Gauge Face Probe 05: 27 70º Central Probe 0º Probe 70º Non-Gauge Face Probe 4 mm 20 mm 52 mm 0º Probe 70º Central Probe 49 mm 5 mm 70º GF Probe 70º NGF Probe RAJENDRA KHURSINGE, Sr. Instructor Track, IRICEN. (B) (D) of Revised USFD Manual Ref: - Fig. 2 (A) Ref: - Revised USFD Manual Para No. 7. 1(ii)
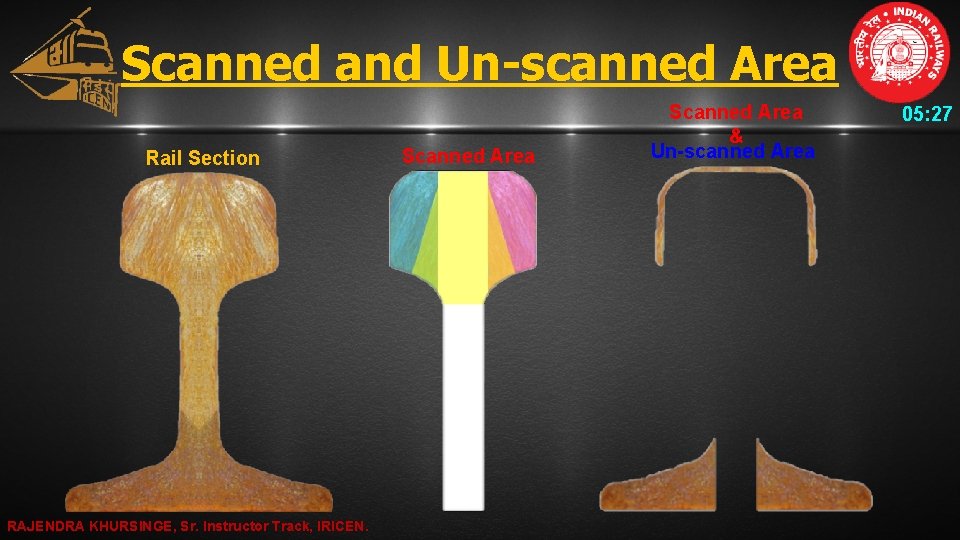
Scanned and Un-scanned Area Rail Section RAJENDRA KHURSINGE, Sr. Instructor Track, IRICEN. Scanned Area & Un-scanned Area 05: 27
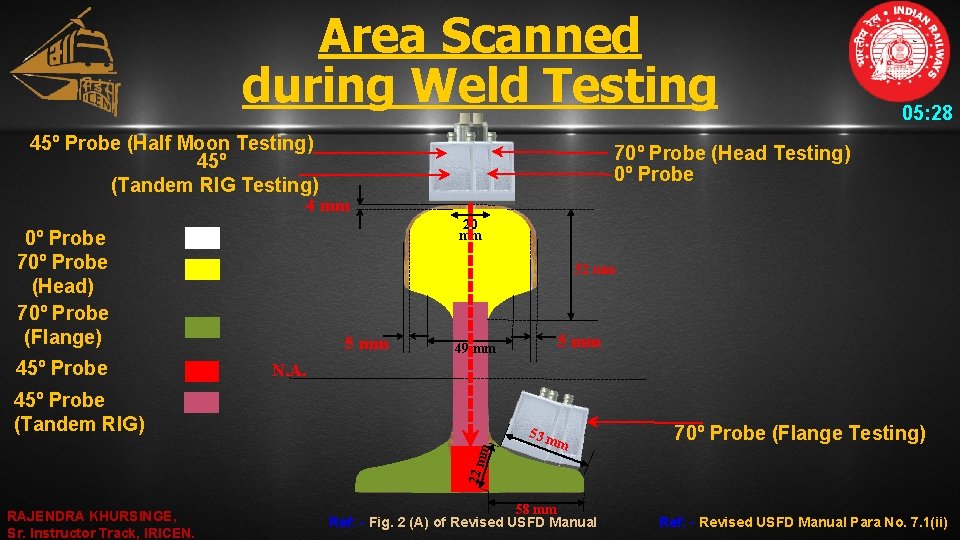
Area Scanned during Weld Testing 45º Probe (Half Moon Testing) 45º (Tandem RIG Testing) 05: 28 70º Probe (Head Testing) 0º Probe 4 mm 20 mm 0º Probe 70º Probe (Head) 70º Probe (Flange) 45º Probe 52 mm 5 mm 49 mm N. A. 53 m m 70º Probe (Flange Testing) 22 m m 45º Probe (Tandem RIG) RAJENDRA KHURSINGE, Sr. Instructor Track, IRICEN. 58 mm Ref: - Fig. 2 (A) of Revised USFD Manual Ref: - Revised USFD Manual Para No. 7. 1(ii)
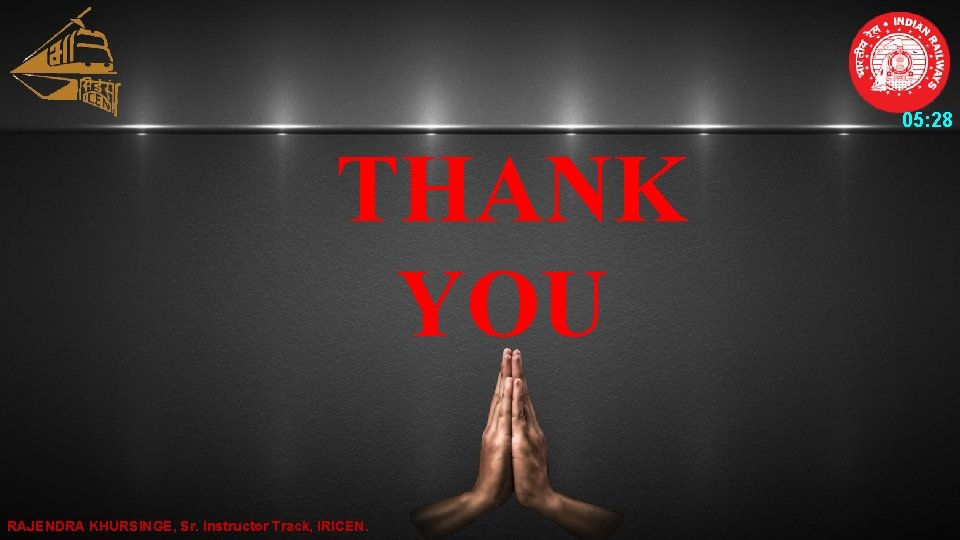
05: 28 THANK YOU RAJENDRA KHURSINGE, Sr. Instructor Track, IRICEN.
Usfd testing
Usfd machine in railway
Usfd testing frequency
Origin purpose value limitation
Short paper example
Capabilities and limitations of computer
Which is one limitation to technological design
Extraneous variables
Value and limitations ib history
Limitation of distributed system
Limitations of macroeconomics
Example of scope and limitation of the study
Research scope example
Inherently dangerous felony limitation
Schema theory limitations