Protective Crane Design ET 494 Senior Design Spring

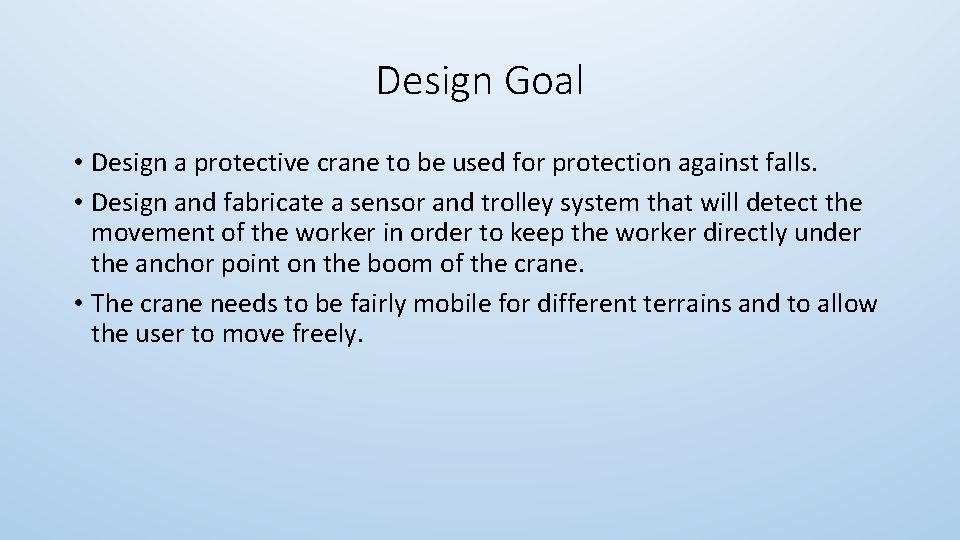
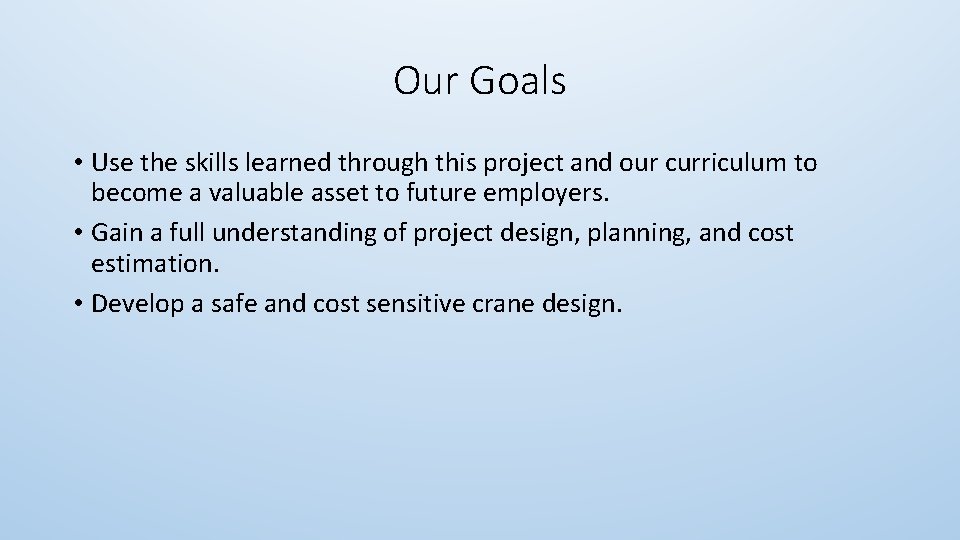
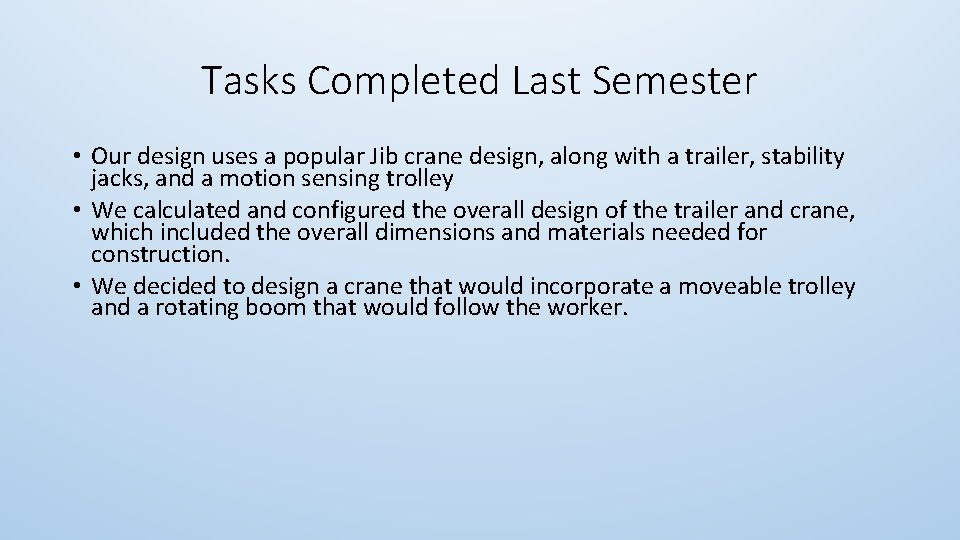
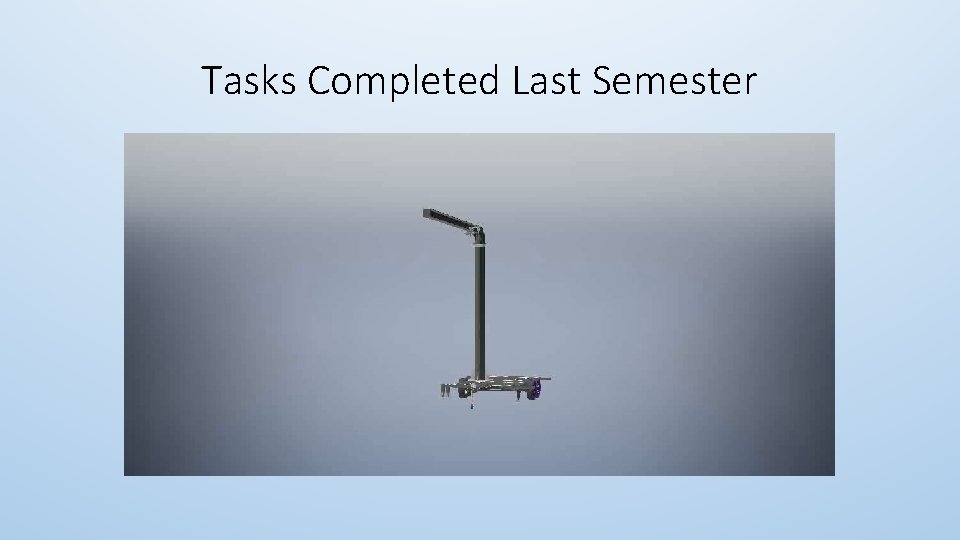
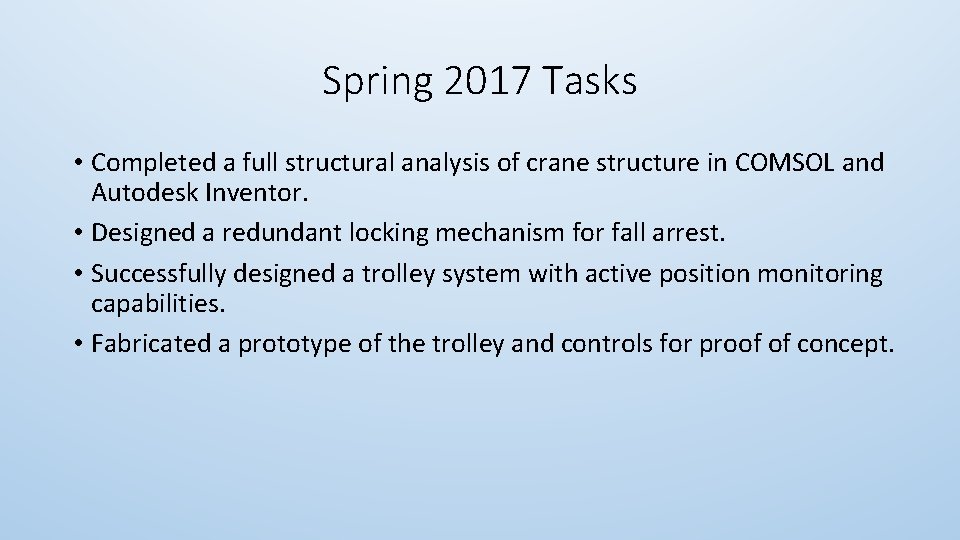
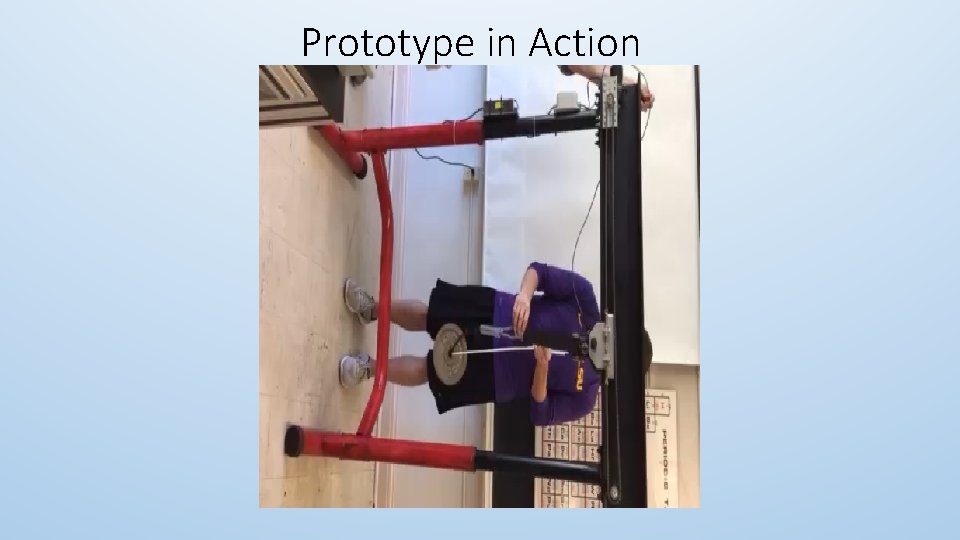
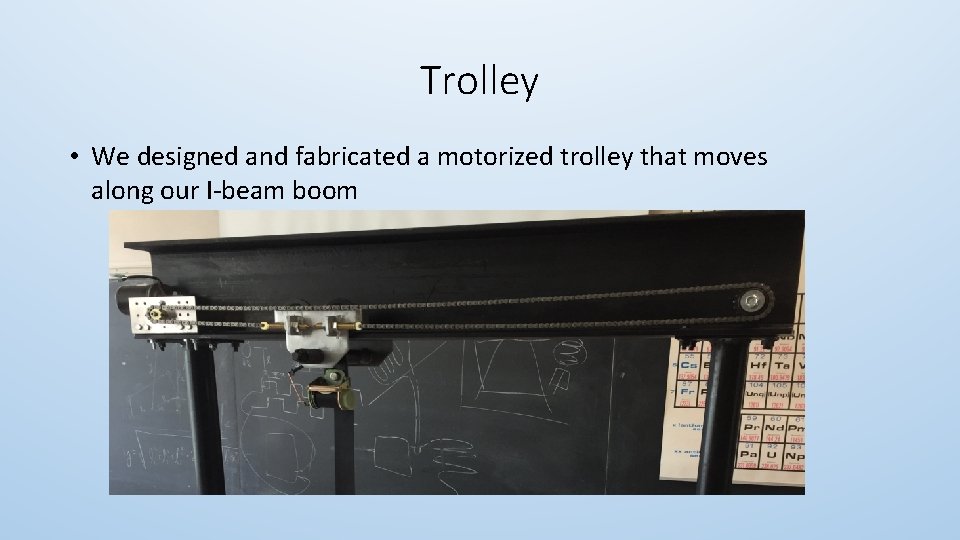
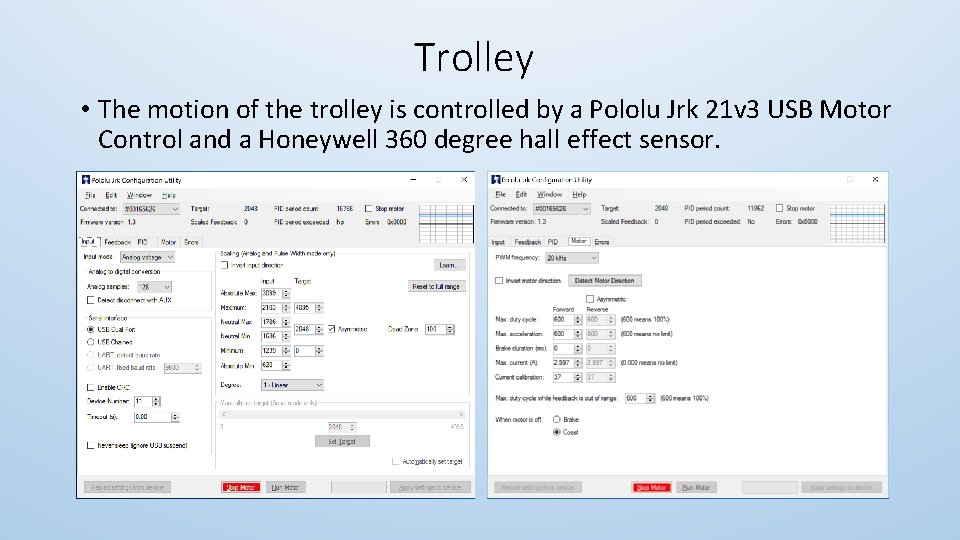
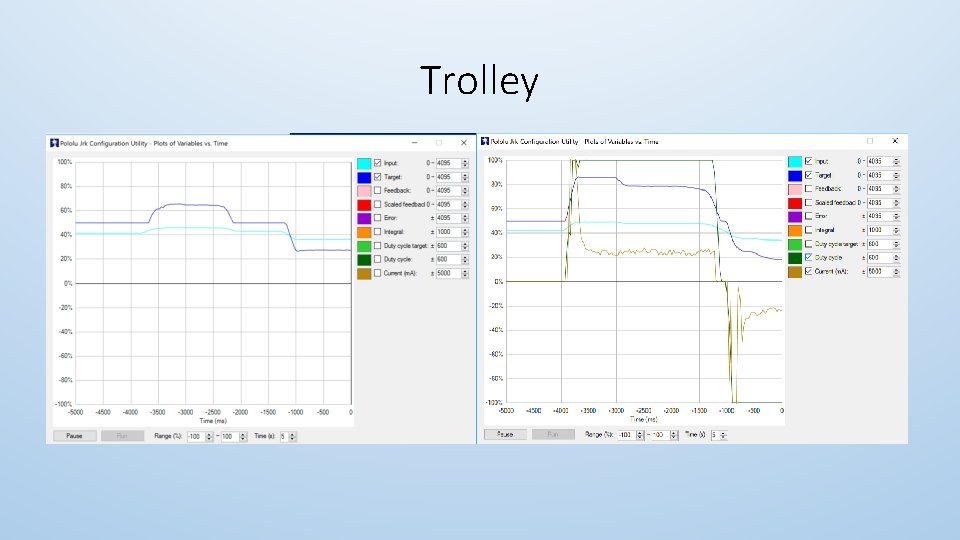
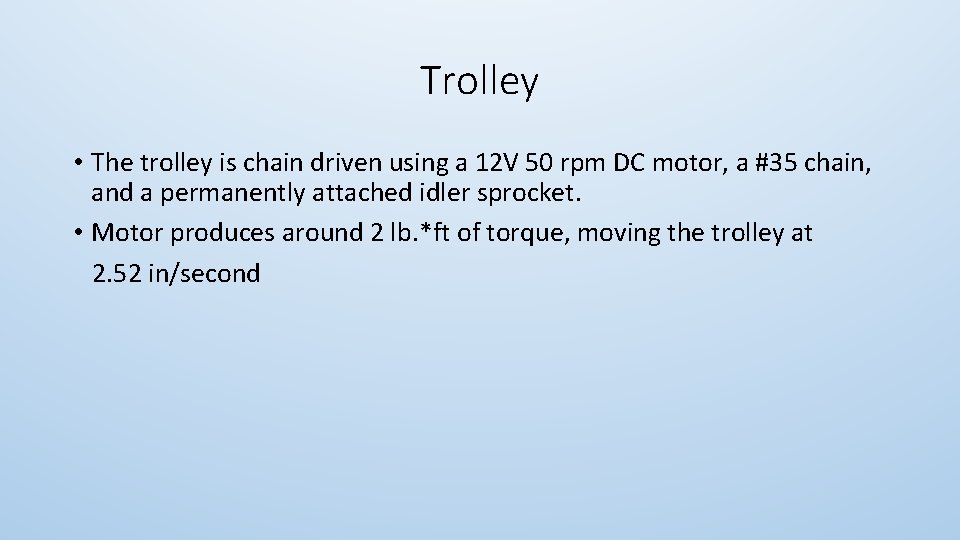
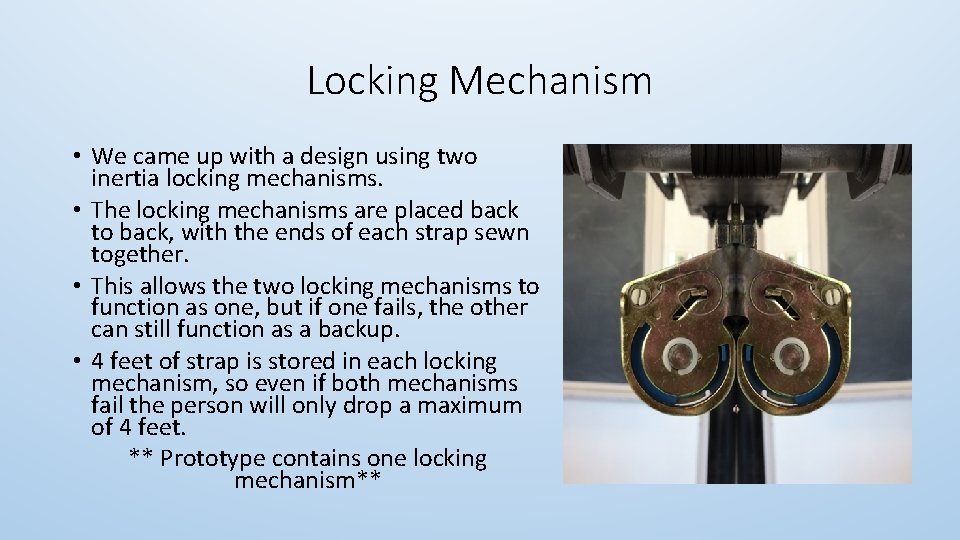
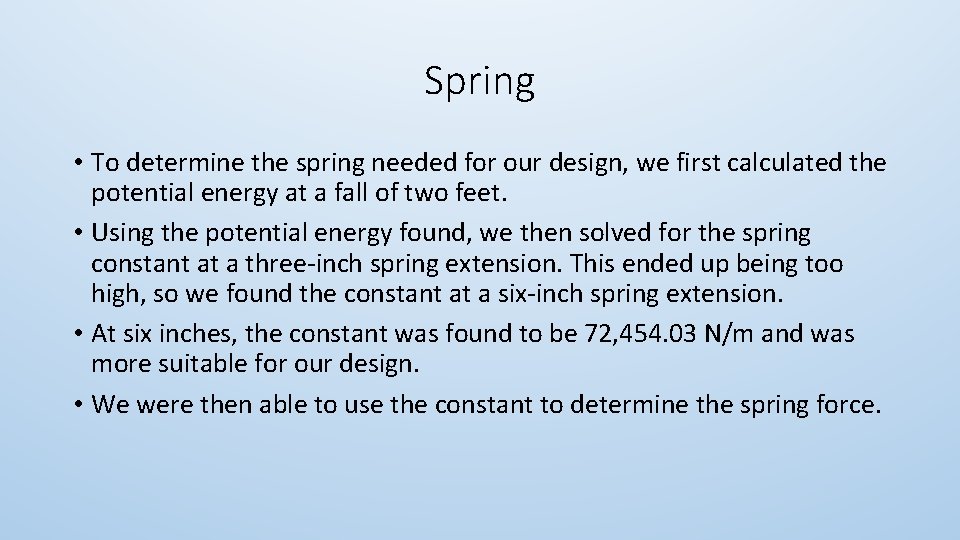
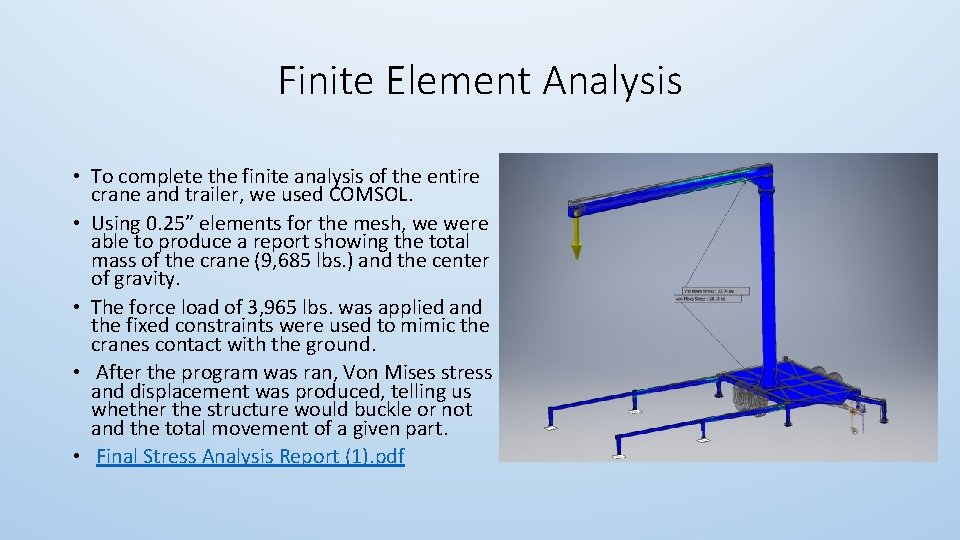
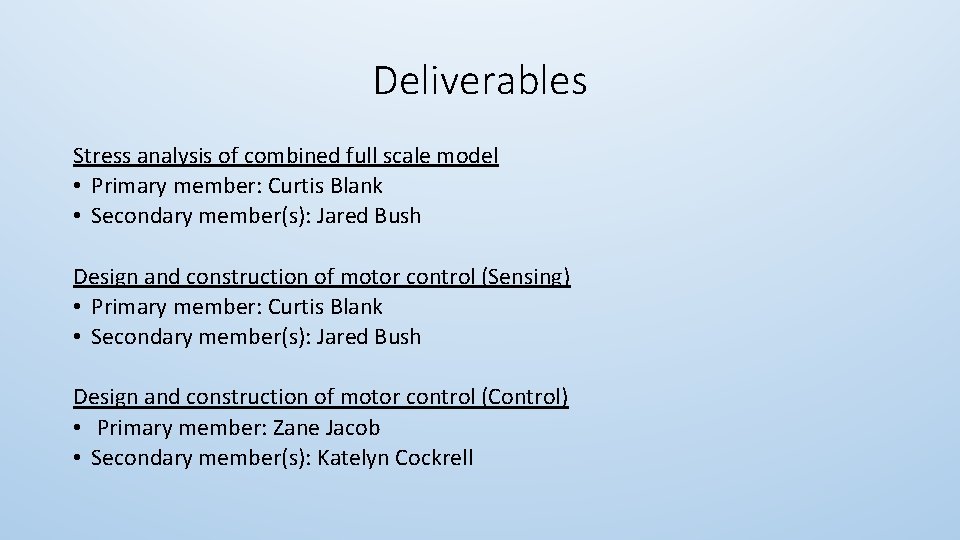
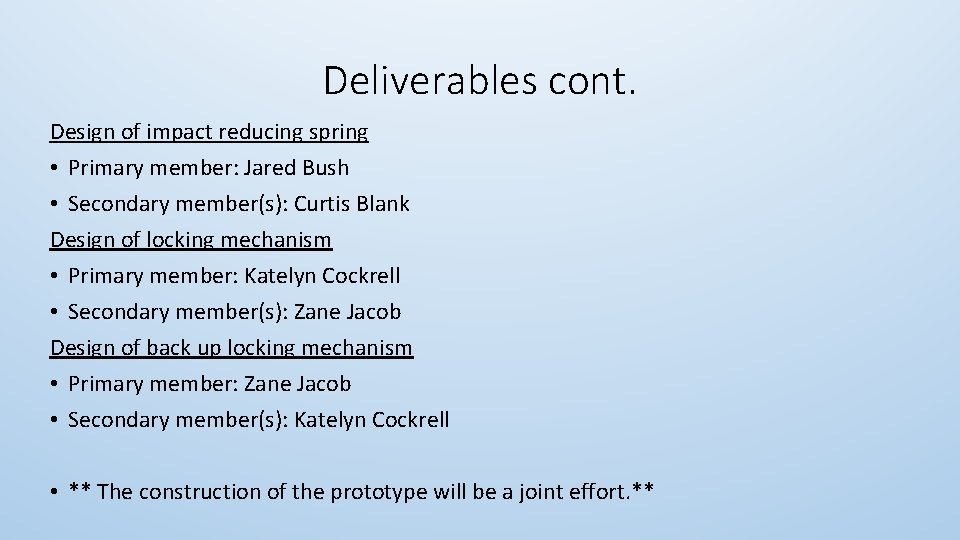
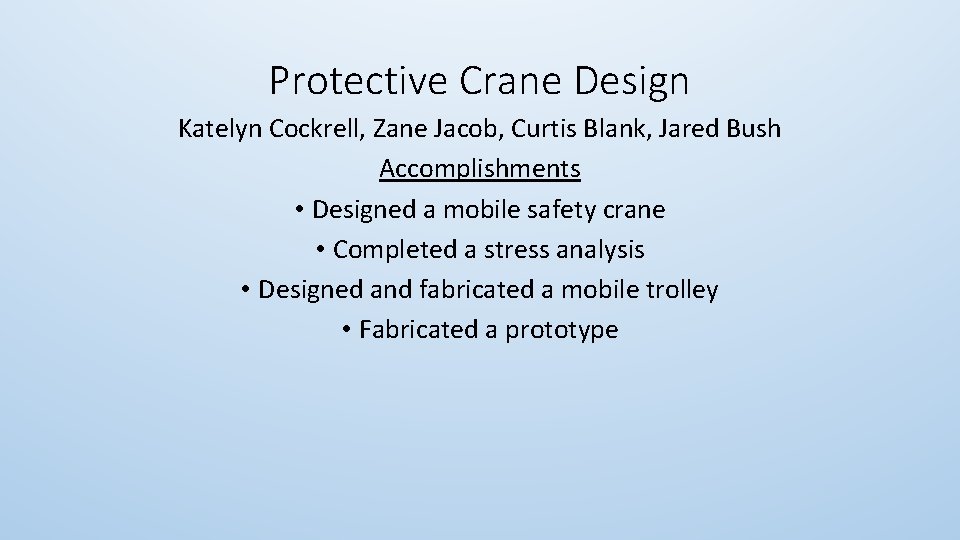
- Slides: 17

Protective Crane Design ET 494 - Senior Design Spring 2017 Katelyn Cockrell Curtis Blank Jared Bush Zane Jacob
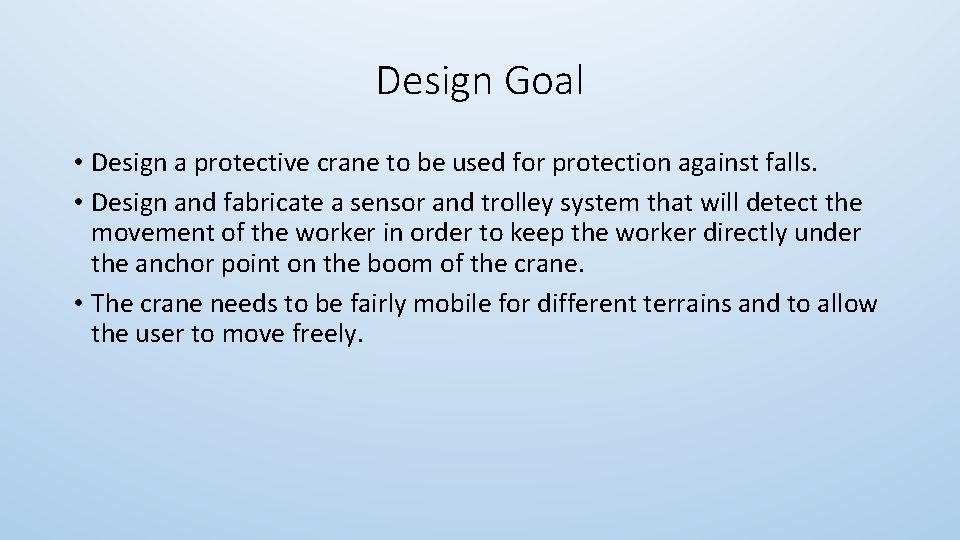
Design Goal • Design a protective crane to be used for protection against falls. • Design and fabricate a sensor and trolley system that will detect the movement of the worker in order to keep the worker directly under the anchor point on the boom of the crane. • The crane needs to be fairly mobile for different terrains and to allow the user to move freely.
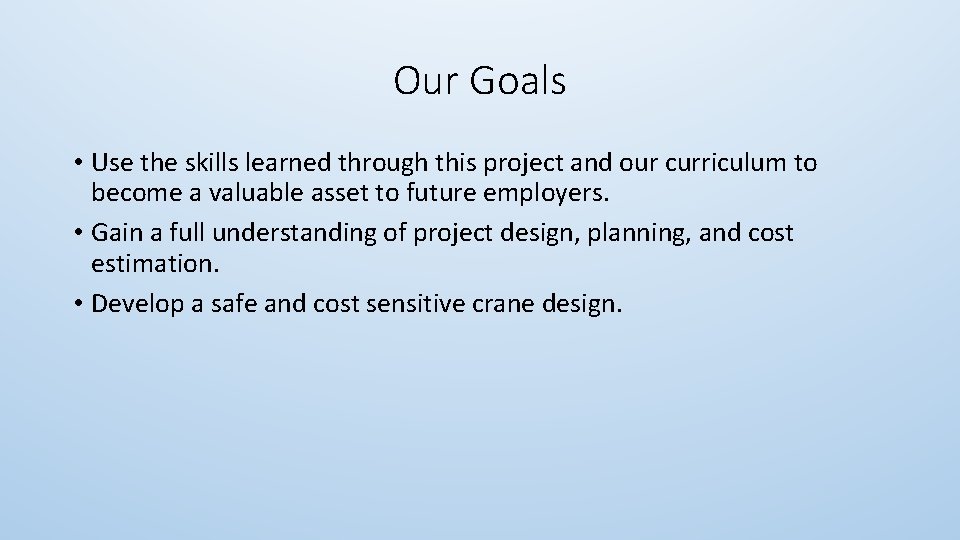
Our Goals • Use the skills learned through this project and our curriculum to become a valuable asset to future employers. • Gain a full understanding of project design, planning, and cost estimation. • Develop a safe and cost sensitive crane design.
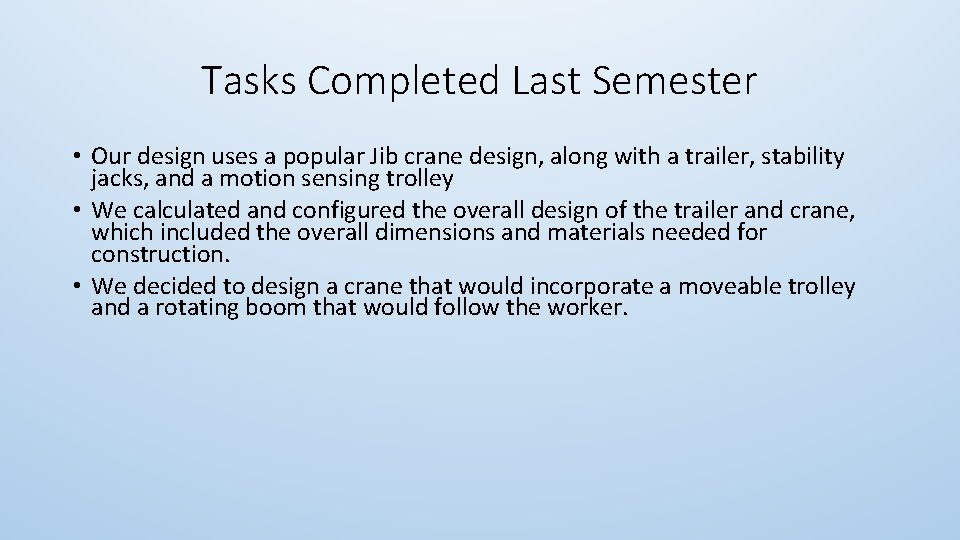
Tasks Completed Last Semester • Our design uses a popular Jib crane design, along with a trailer, stability jacks, and a motion sensing trolley • We calculated and configured the overall design of the trailer and crane, which included the overall dimensions and materials needed for construction. • We decided to design a crane that would incorporate a moveable trolley and a rotating boom that would follow the worker.
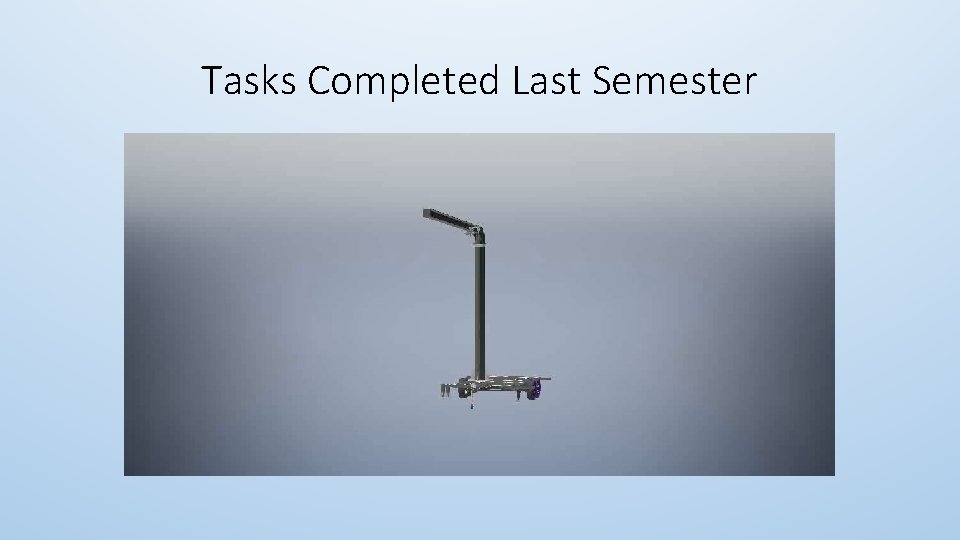
Tasks Completed Last Semester
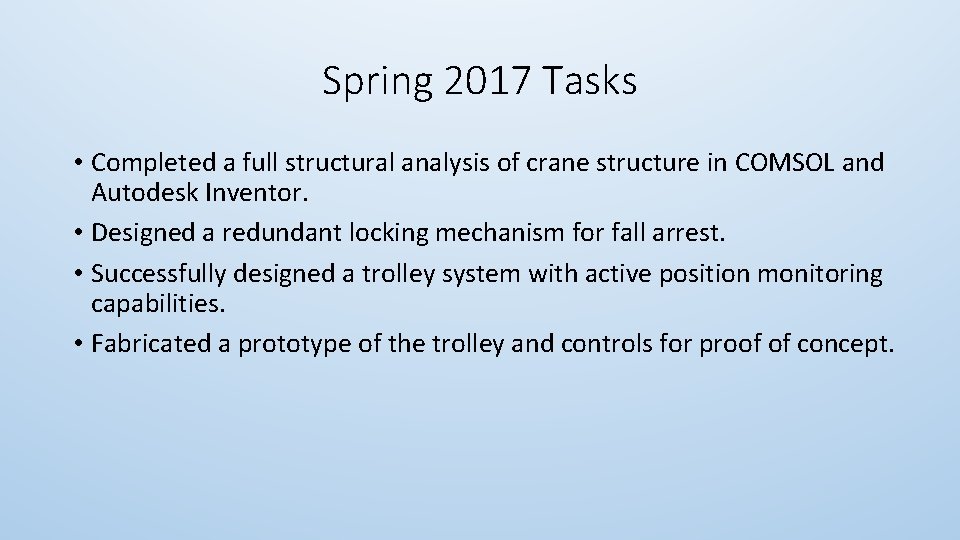
Spring 2017 Tasks • Completed a full structural analysis of crane structure in COMSOL and Autodesk Inventor. • Designed a redundant locking mechanism for fall arrest. • Successfully designed a trolley system with active position monitoring capabilities. • Fabricated a prototype of the trolley and controls for proof of concept.
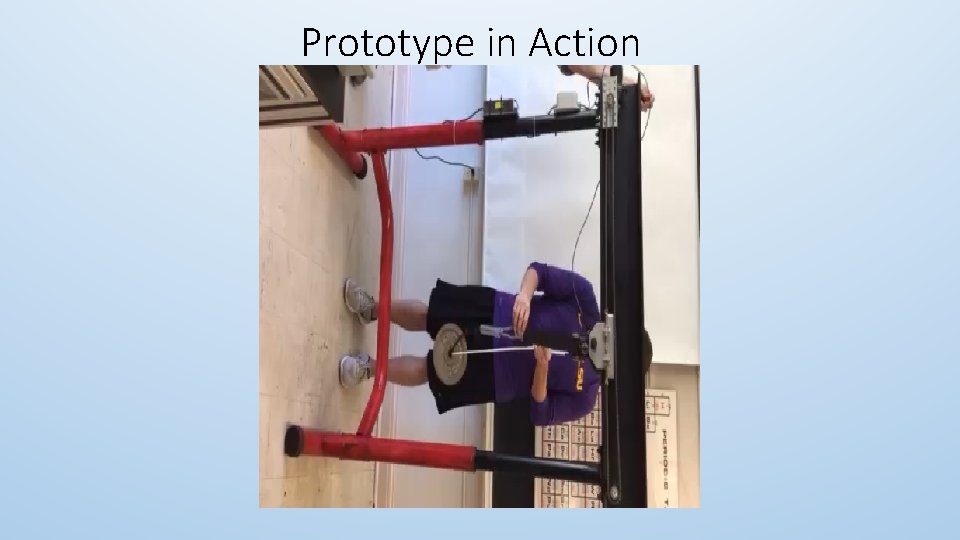
Prototype in Action
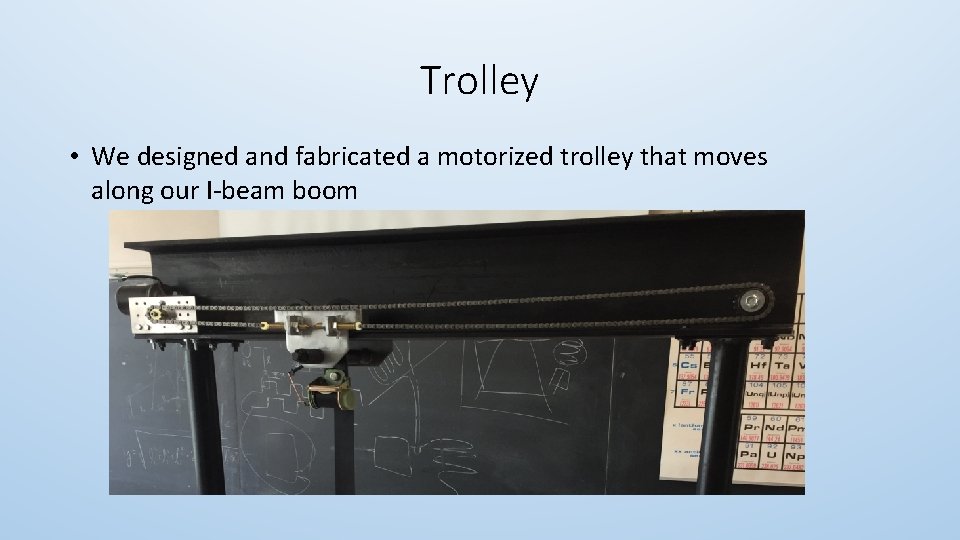
Trolley • We designed and fabricated a motorized trolley that moves along our I-beam boom
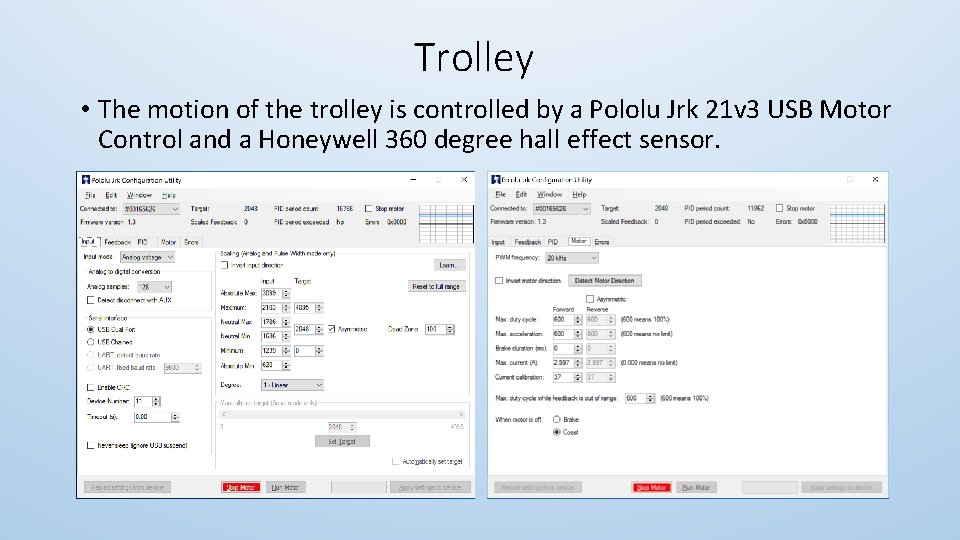
Trolley • The motion of the trolley is controlled by a Pololu Jrk 21 v 3 USB Motor Control and a Honeywell 360 degree hall effect sensor.
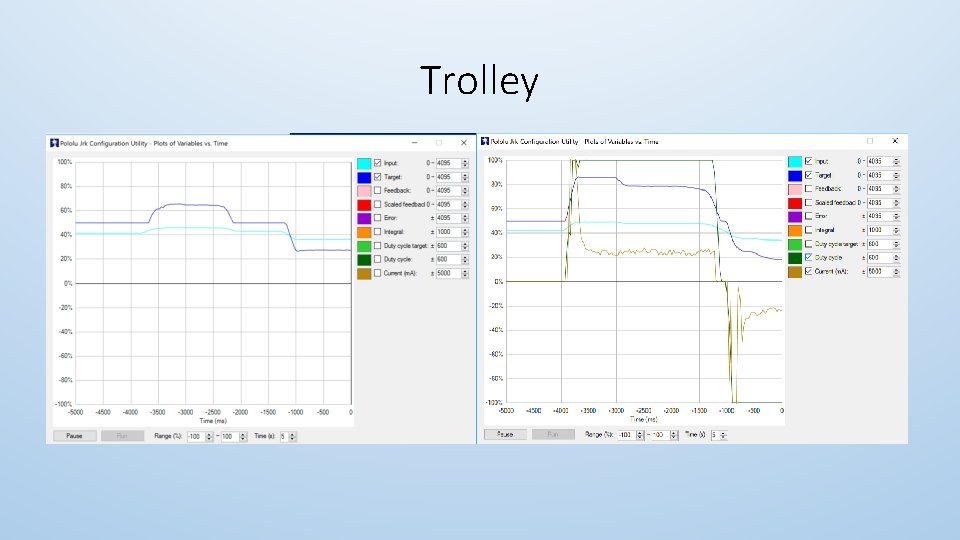
Trolley
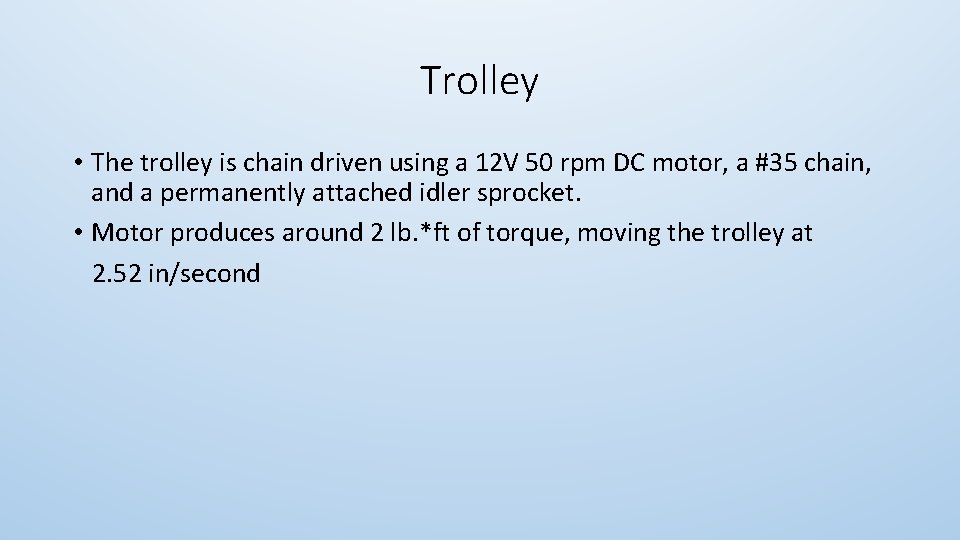
Trolley • The trolley is chain driven using a 12 V 50 rpm DC motor, a #35 chain, and a permanently attached idler sprocket. • Motor produces around 2 lb. *ft of torque, moving the trolley at 2. 52 in/second
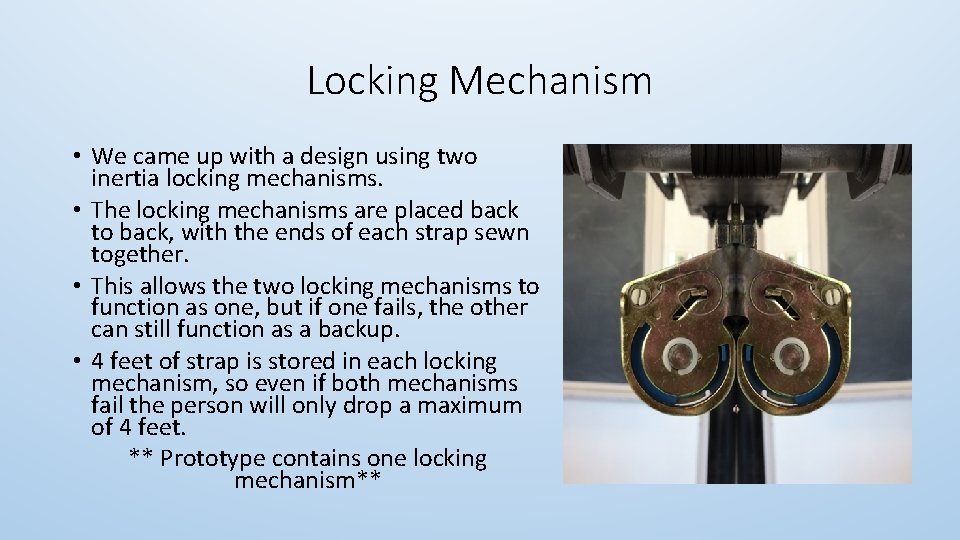
Locking Mechanism • We came up with a design using two inertia locking mechanisms. • The locking mechanisms are placed back to back, with the ends of each strap sewn together. • This allows the two locking mechanisms to function as one, but if one fails, the other can still function as a backup. • 4 feet of strap is stored in each locking mechanism, so even if both mechanisms fail the person will only drop a maximum of 4 feet. ** Prototype contains one locking mechanism**
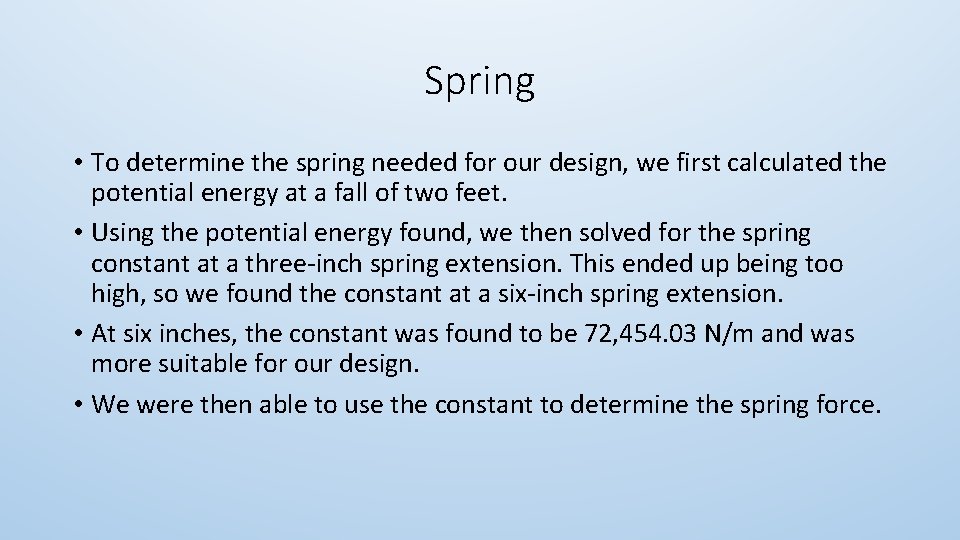
Spring • To determine the spring needed for our design, we first calculated the potential energy at a fall of two feet. • Using the potential energy found, we then solved for the spring constant at a three-inch spring extension. This ended up being too high, so we found the constant at a six-inch spring extension. • At six inches, the constant was found to be 72, 454. 03 N/m and was more suitable for our design. • We were then able to use the constant to determine the spring force.
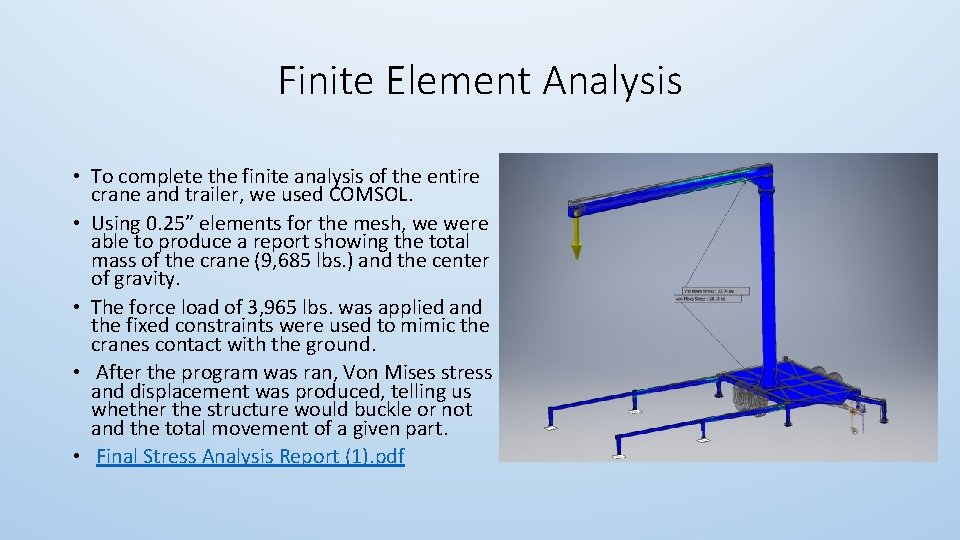
Finite Element Analysis • To complete the finite analysis of the entire crane and trailer, we used COMSOL. • Using 0. 25” elements for the mesh, we were able to produce a report showing the total mass of the crane (9, 685 lbs. ) and the center of gravity. • The force load of 3, 965 lbs. was applied and the fixed constraints were used to mimic the cranes contact with the ground. • After the program was ran, Von Mises stress and displacement was produced, telling us whether the structure would buckle or not and the total movement of a given part. • Final Stress Analysis Report (1). pdf
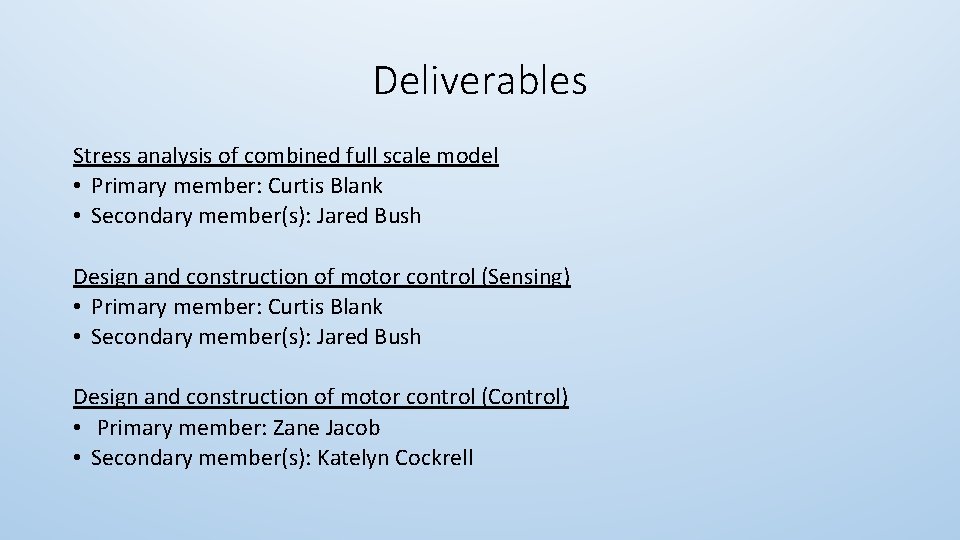
Deliverables Stress analysis of combined full scale model • Primary member: Curtis Blank • Secondary member(s): Jared Bush Design and construction of motor control (Sensing) • Primary member: Curtis Blank • Secondary member(s): Jared Bush Design and construction of motor control (Control) • Primary member: Zane Jacob • Secondary member(s): Katelyn Cockrell
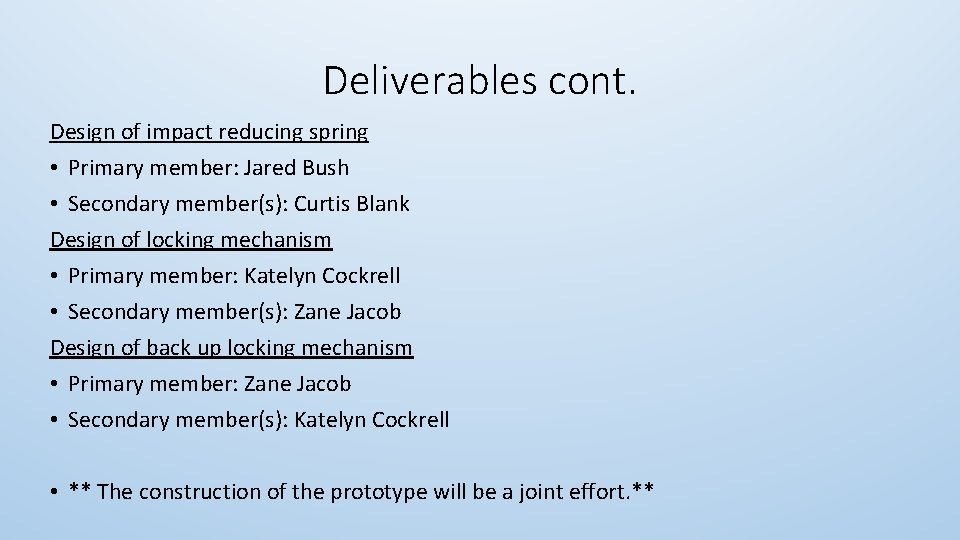
Deliverables cont. Design of impact reducing spring • Primary member: Jared Bush • Secondary member(s): Curtis Blank Design of locking mechanism • Primary member: Katelyn Cockrell • Secondary member(s): Zane Jacob Design of back up locking mechanism • Primary member: Zane Jacob • Secondary member(s): Katelyn Cockrell • ** The construction of the prototype will be a joint effort. **
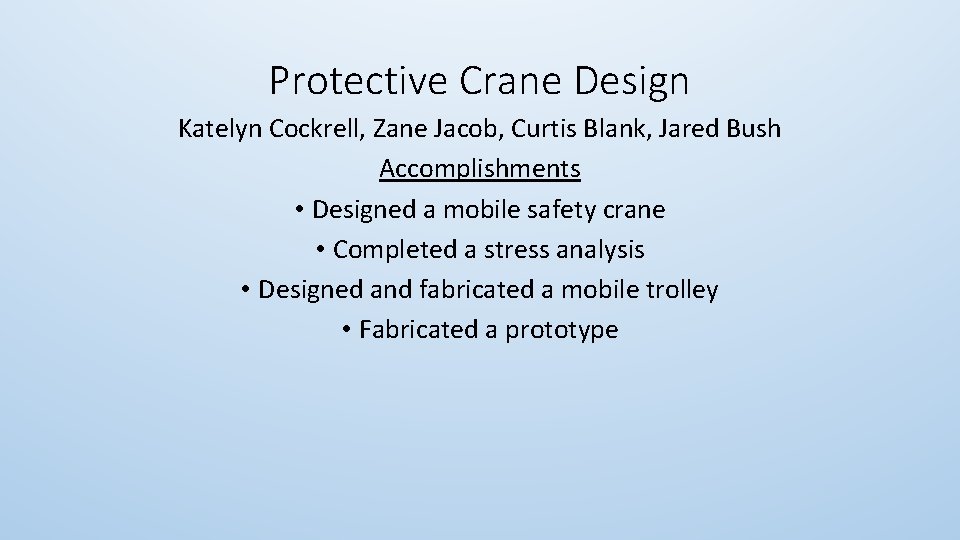
Protective Crane Design Katelyn Cockrell, Zane Jacob, Curtis Blank, Jared Bush Accomplishments • Designed a mobile safety crane • Completed a stress analysis • Designed and fabricated a mobile trolley • Fabricated a prototype
Chem 494
Konsep habis dibagi
Kim ki duk spring summer fall winter
Spring seasons months
What is a design brief of a crane
Crane mechanism design
Ucf senior design
Linda milor
Ncsu csc senior design
Ee senior design project ideas
Ist 331
Analysisist
Roll over protective structure (rops)
Rachel brooks attorney vancouver wa
Long call short call
What do you mean by topical agent
Protective ozone layer
The art and science of protective relaying