Production Technology IV Metal Forming INTRODUCTION TO METAL
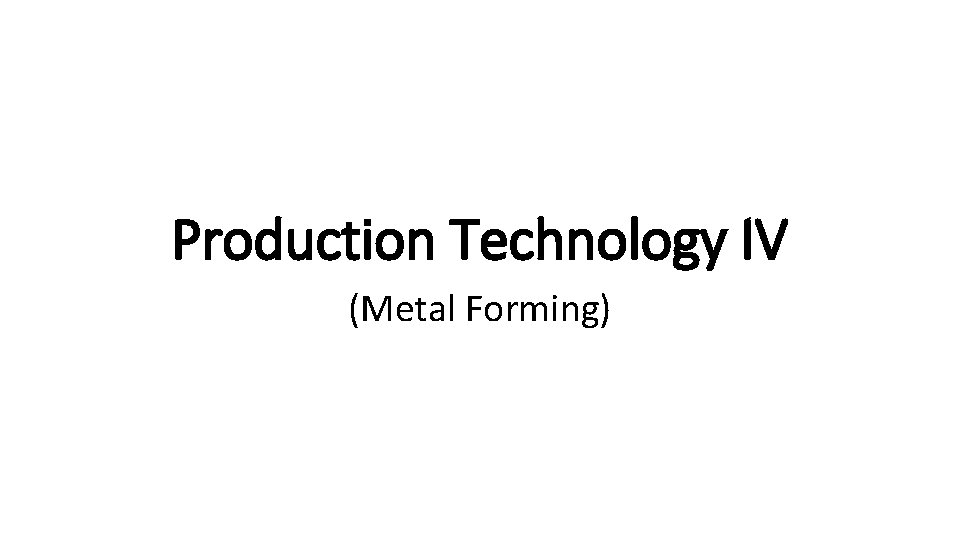
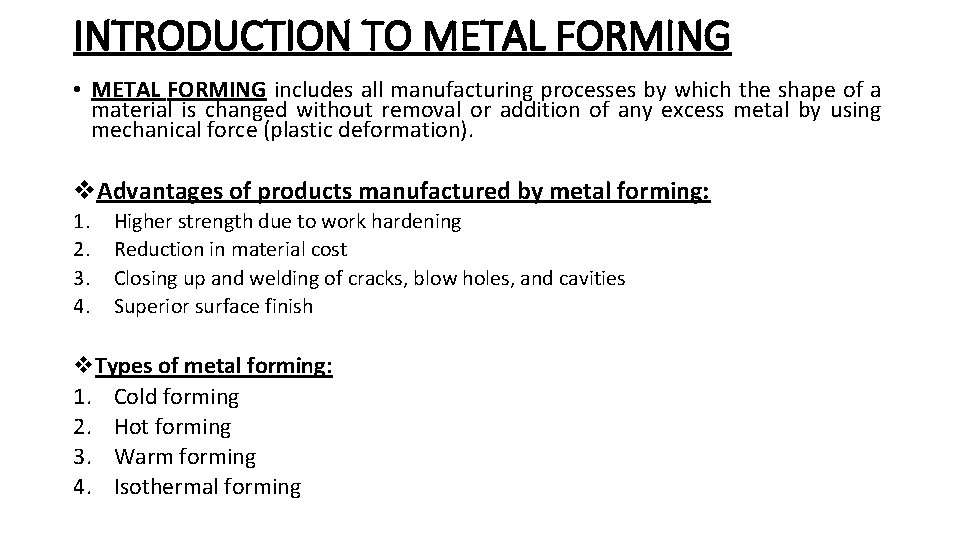
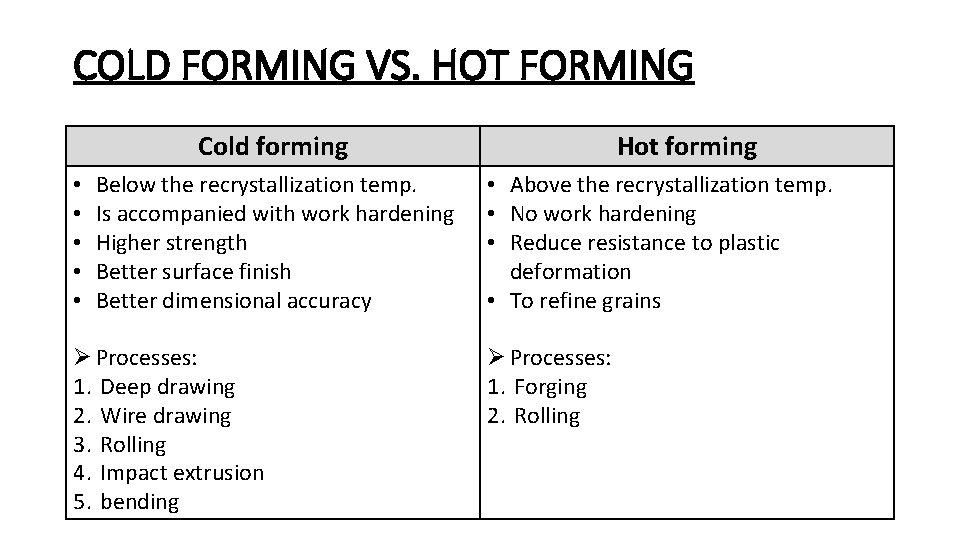
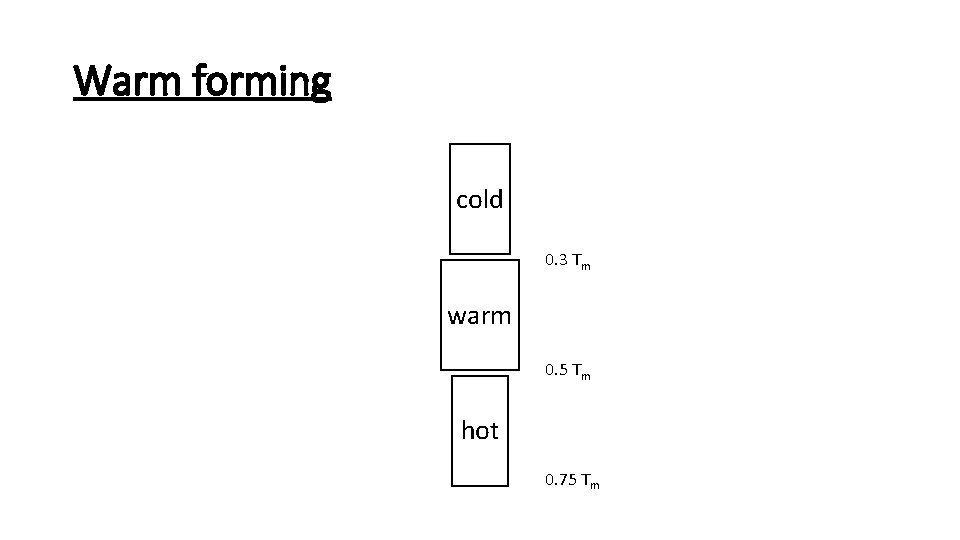
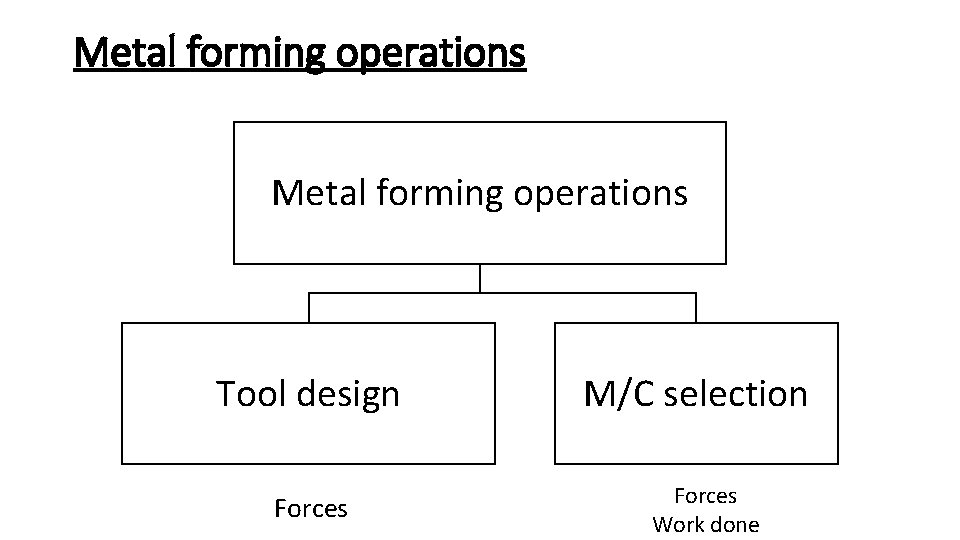
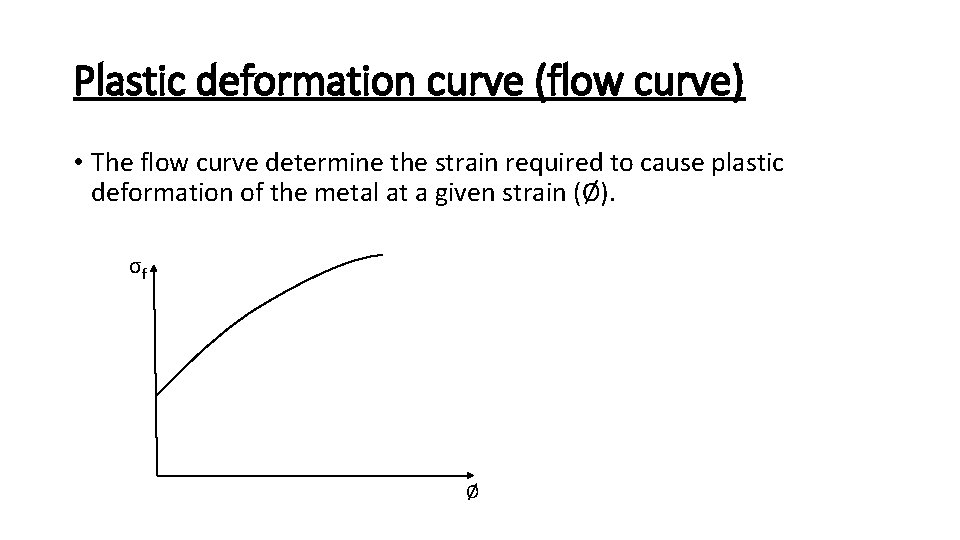
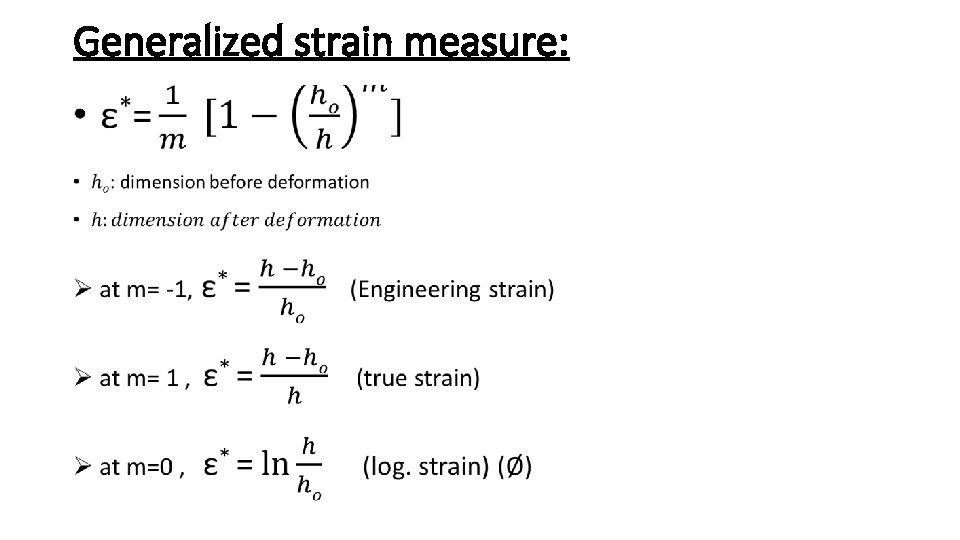
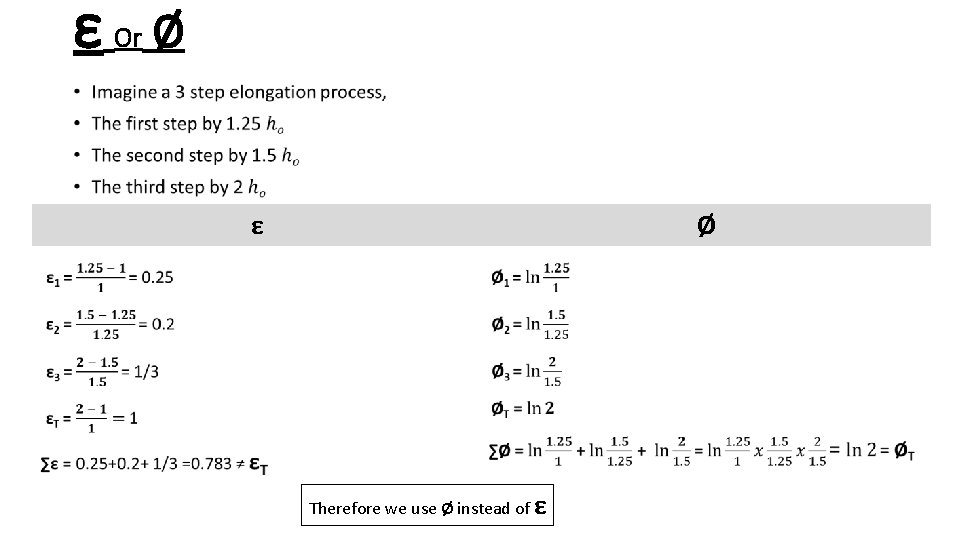
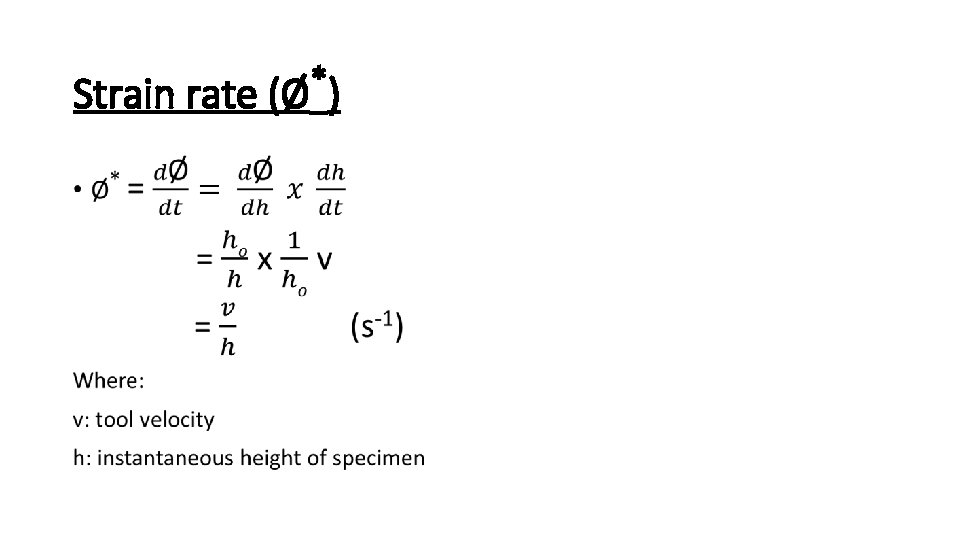
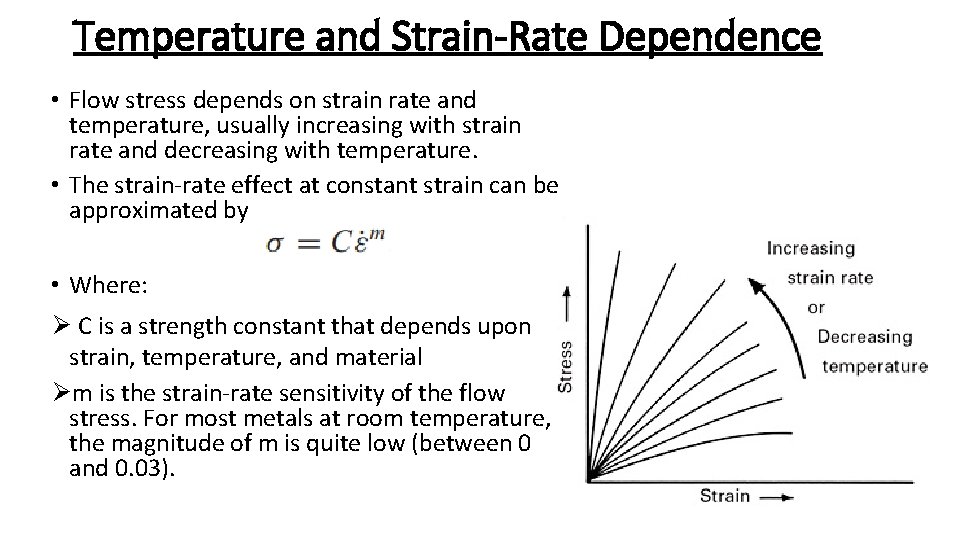
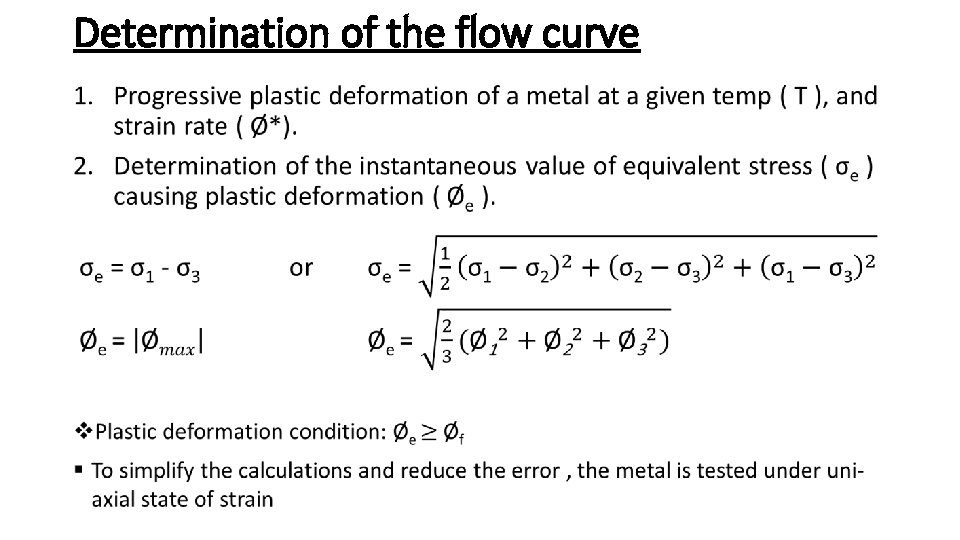
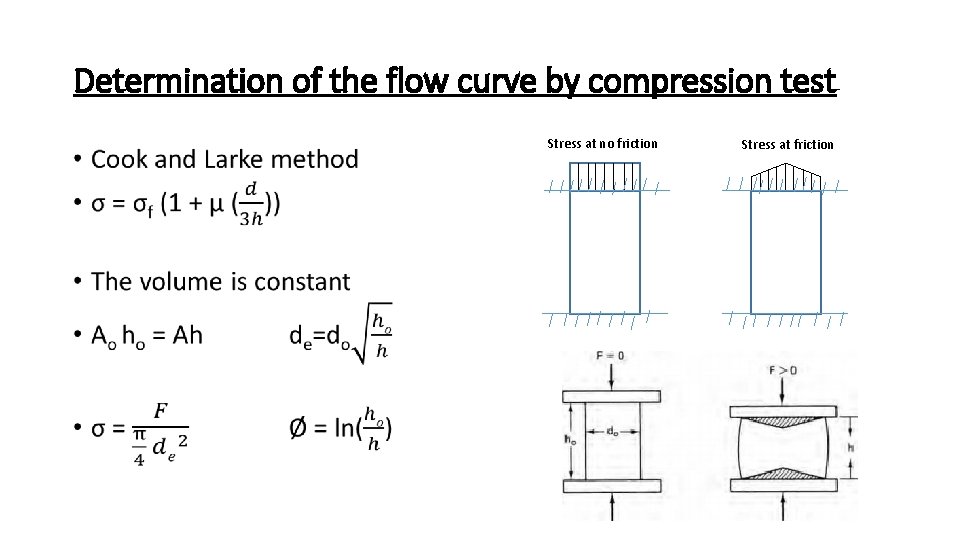
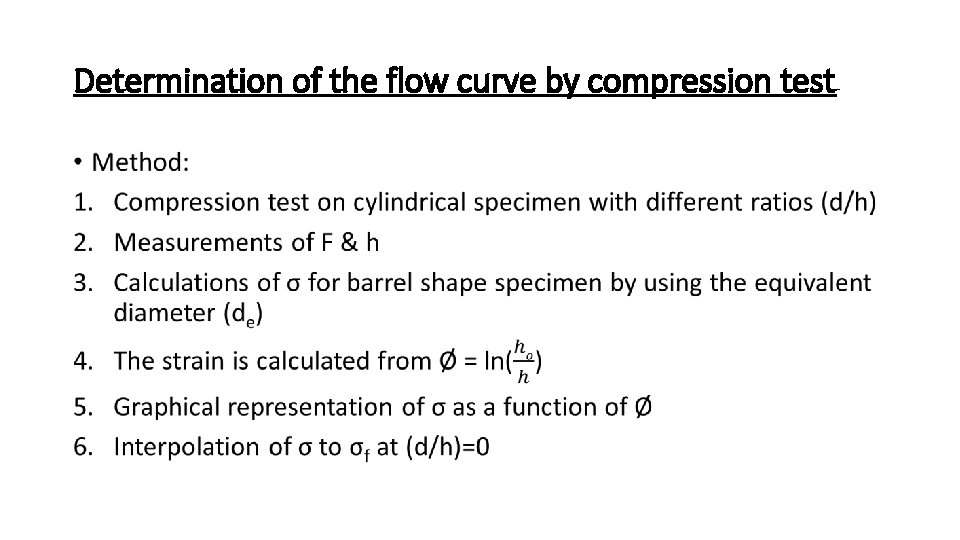
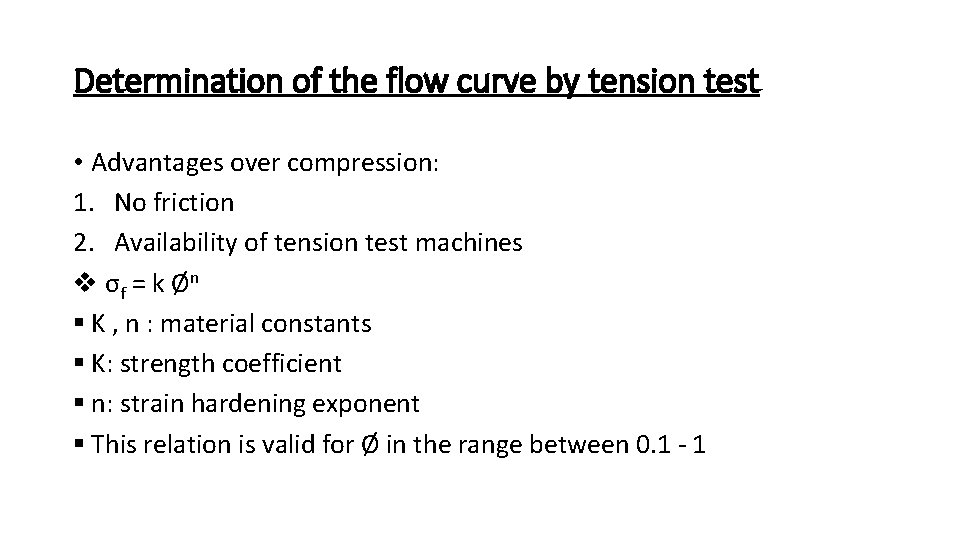
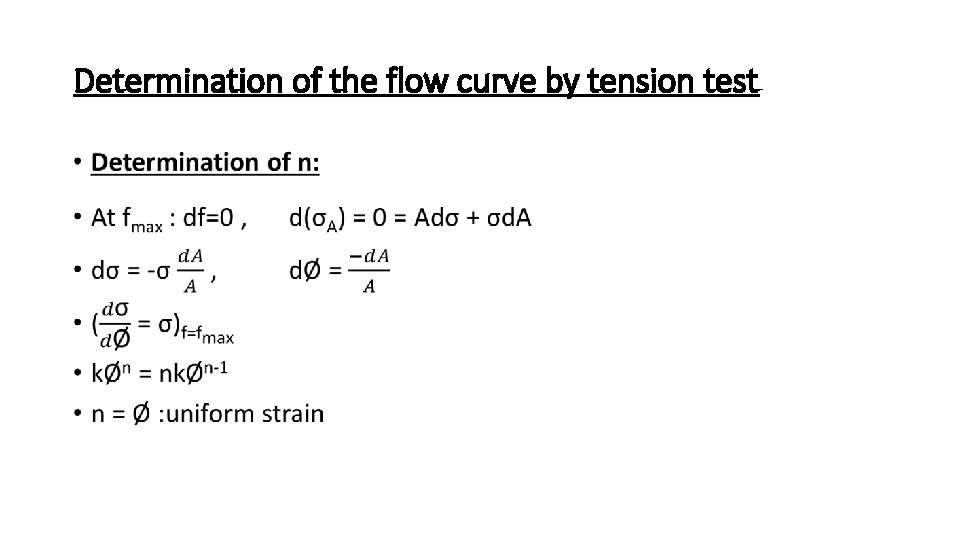
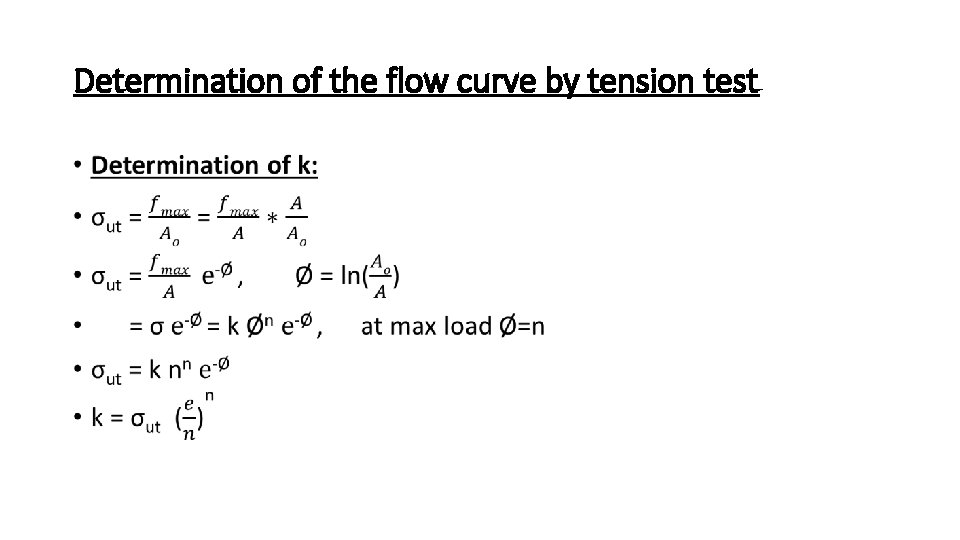
- Slides: 16
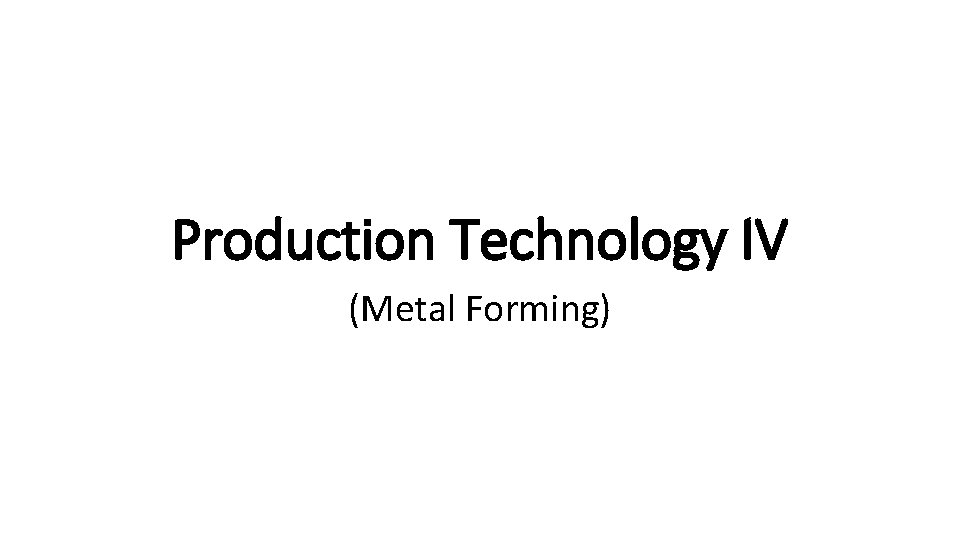
Production Technology IV (Metal Forming)
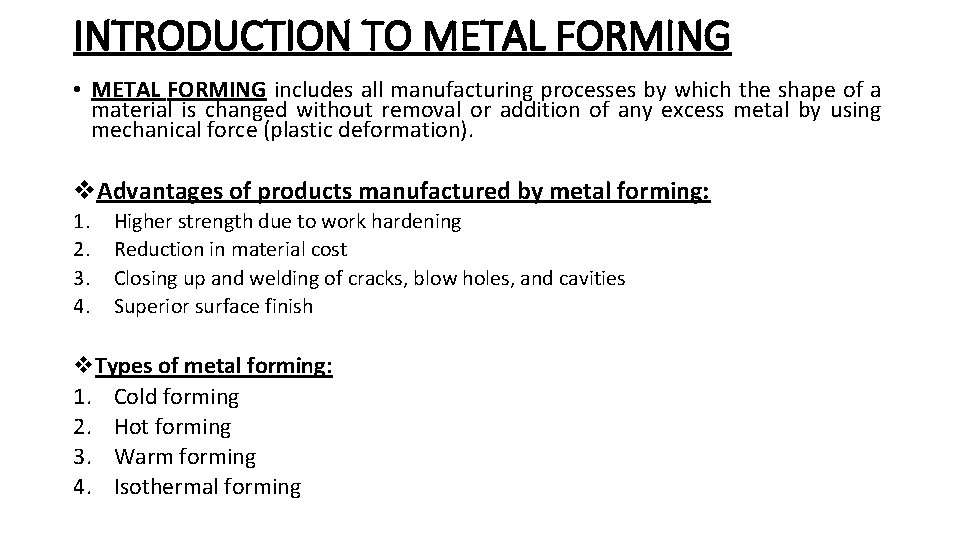
INTRODUCTION TO METAL FORMING • METAL FORMING includes all manufacturing processes by which the shape of a material is changed without removal or addition of any excess metal by using mechanical force (plastic deformation). v. Advantages of products manufactured by metal forming: 1. 2. 3. 4. Higher strength due to work hardening Reduction in material cost Closing up and welding of cracks, blow holes, and cavities Superior surface finish v. Types of metal forming: 1. Cold forming 2. Hot forming 3. Warm forming 4. Isothermal forming
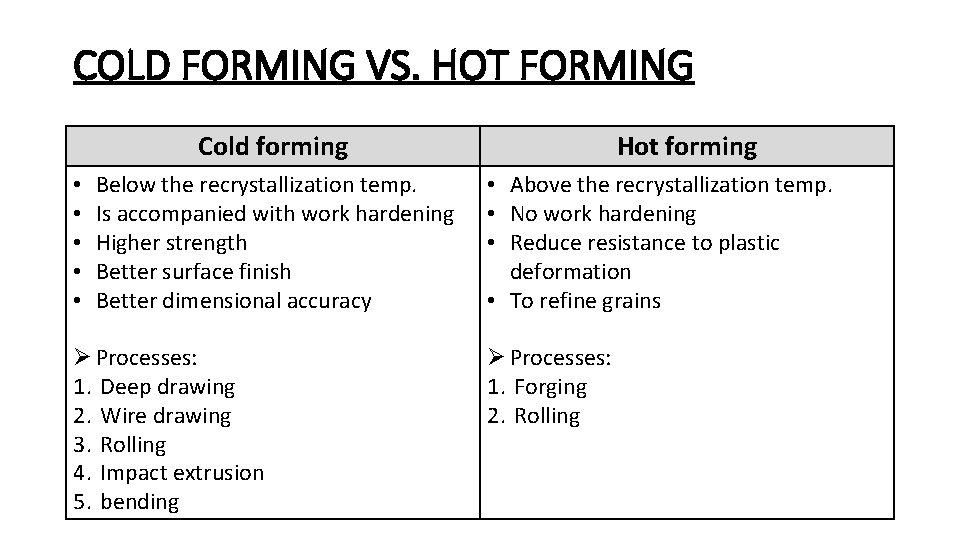
COLD FORMING VS. HOT FORMING Cold forming • • • Below the recrystallization temp. Is accompanied with work hardening Higher strength Better surface finish Better dimensional accuracy Ø Processes: 1. Deep drawing 2. Wire drawing 3. Rolling 4. Impact extrusion 5. bending Hot forming • Above the recrystallization temp. • No work hardening • Reduce resistance to plastic deformation • To refine grains Ø Processes: 1. Forging 2. Rolling
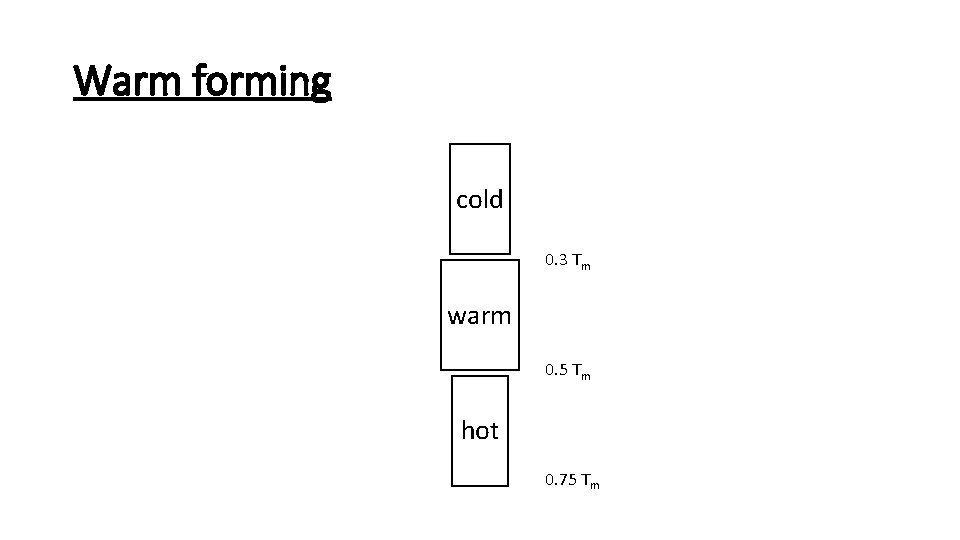
Warm forming cold 0. 3 Tm warm 0. 5 Tm hot 0. 75 Tm
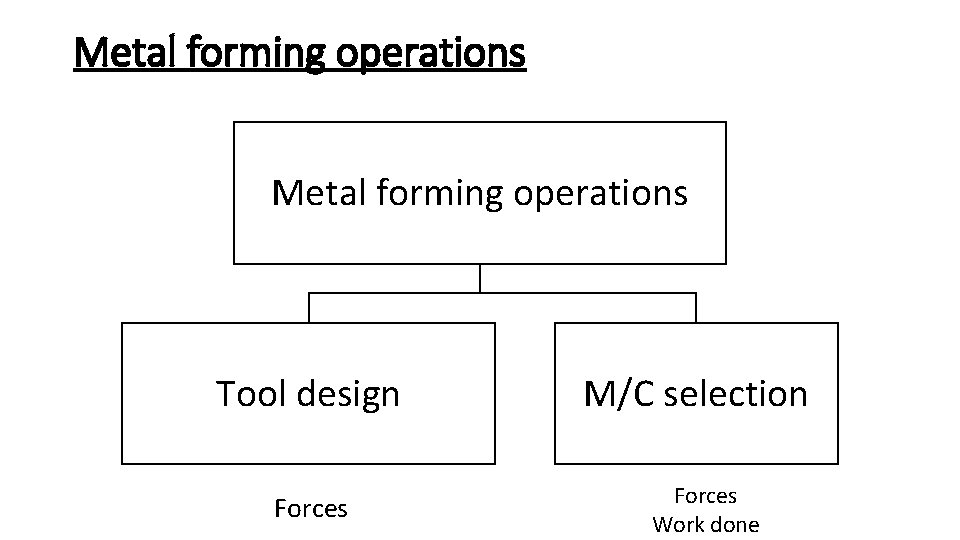
Metal forming operations Tool design Forces M/C selection Forces Work done
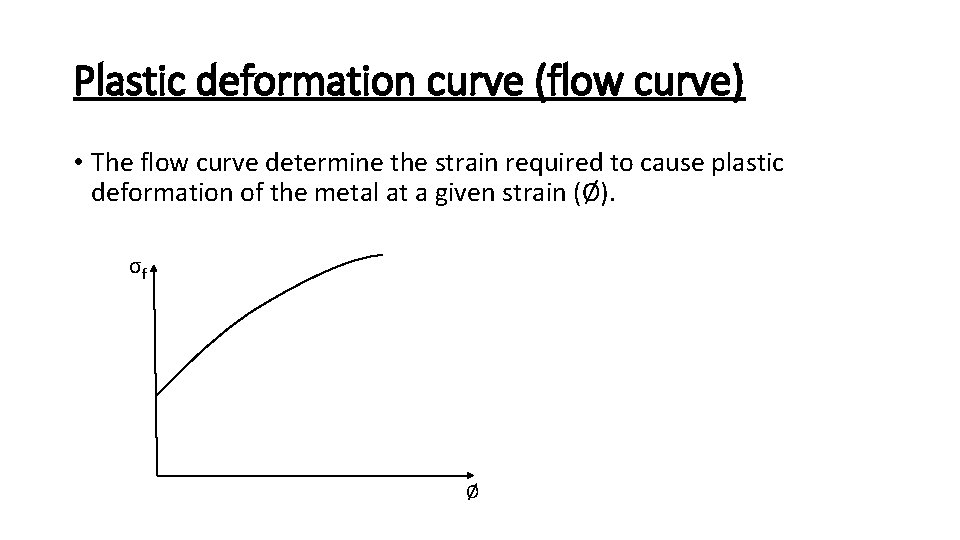
Plastic deformation curve (flow curve) • The flow curve determine the strain required to cause plastic deformation of the metal at a given strain (Ø). σf Ø
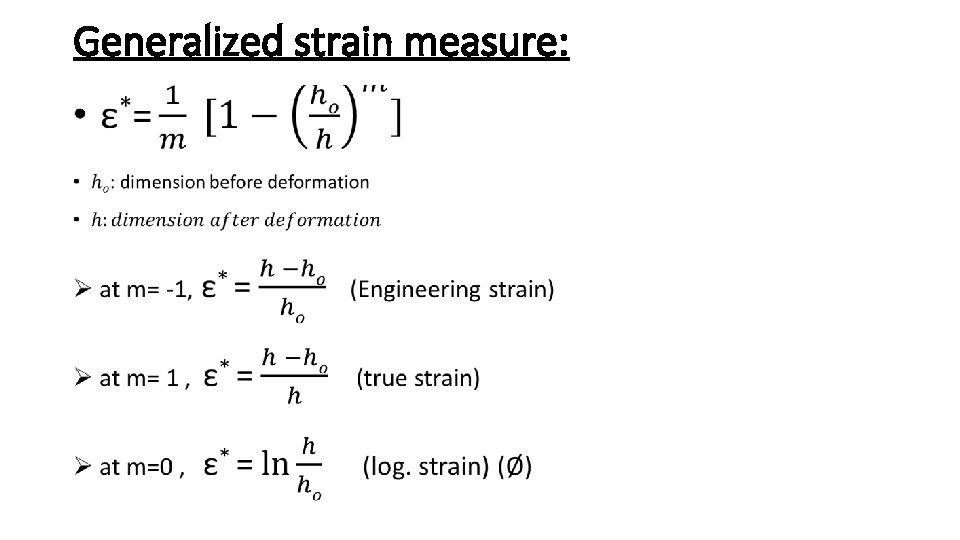
Generalized strain measure: •
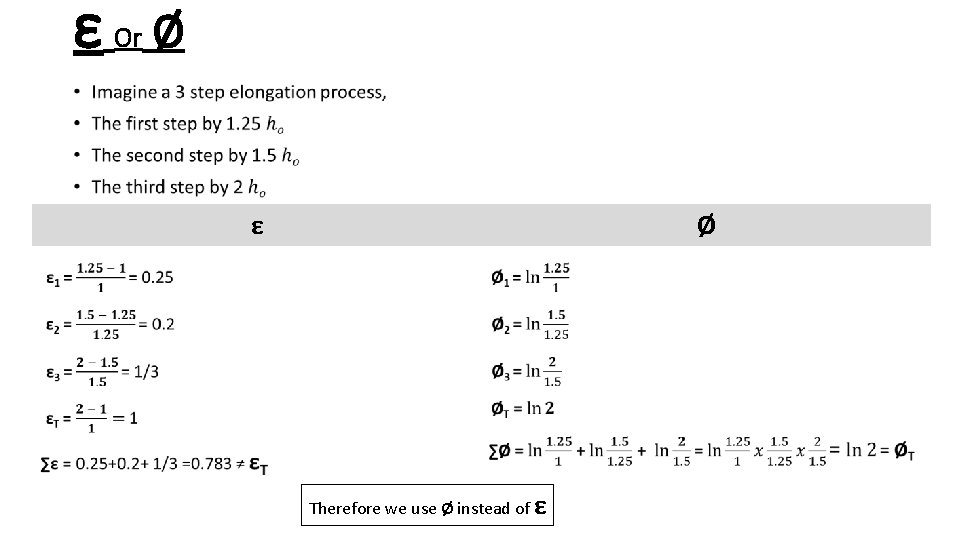
ε Or Ø • ε Ø Therefore we use Ø instead of ε
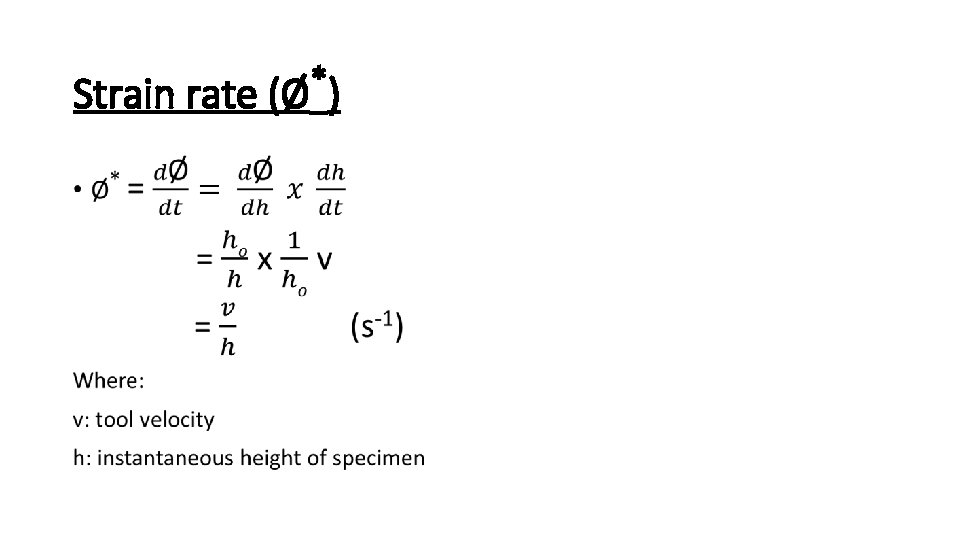
* Strain rate (Ø ) •
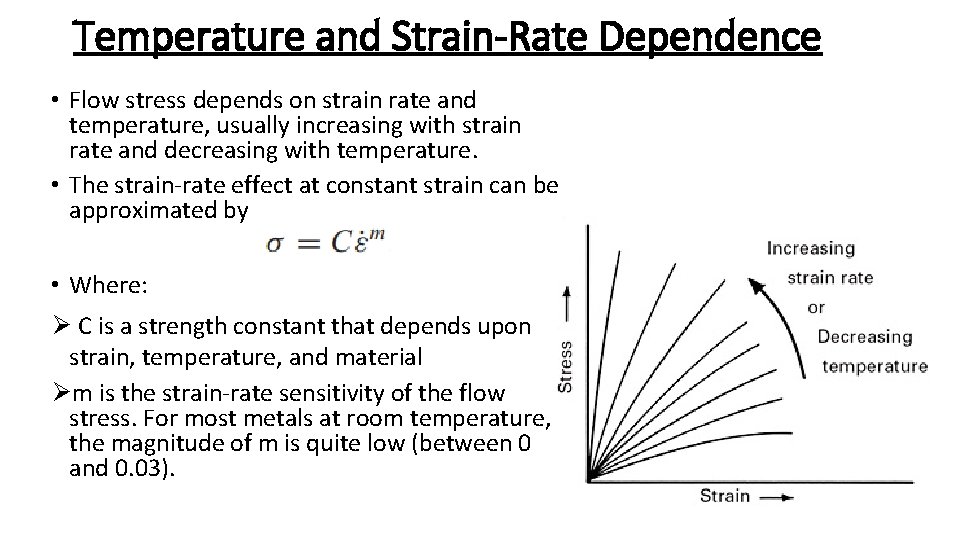
Temperature and Strain-Rate Dependence • Flow stress depends on strain rate and temperature, usually increasing with strain rate and decreasing with temperature. • The strain-rate effect at constant strain can be approximated by • Where: Ø C is a strength constant that depends upon strain, temperature, and material Øm is the strain-rate sensitivity of the flow stress. For most metals at room temperature, the magnitude of m is quite low (between 0 and 0. 03).
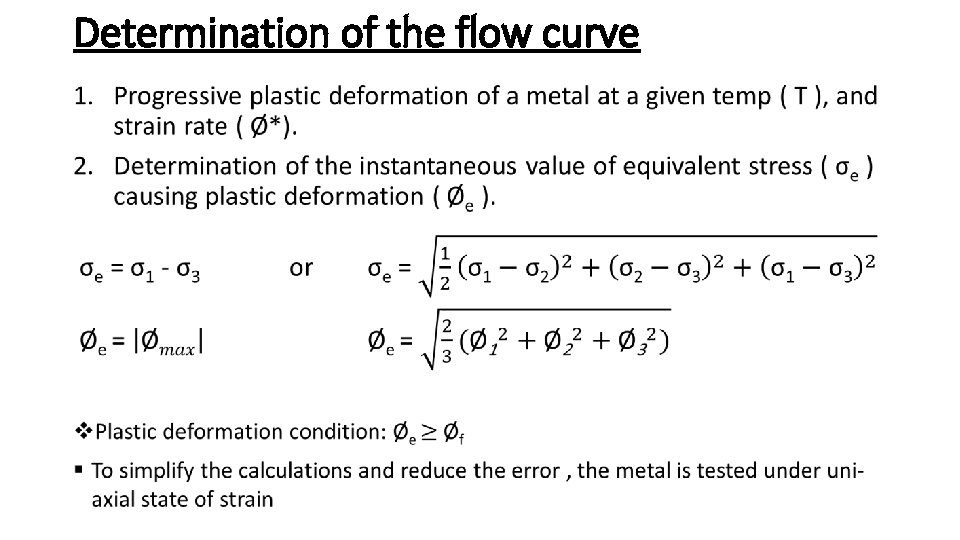
Determination of the flow curve •
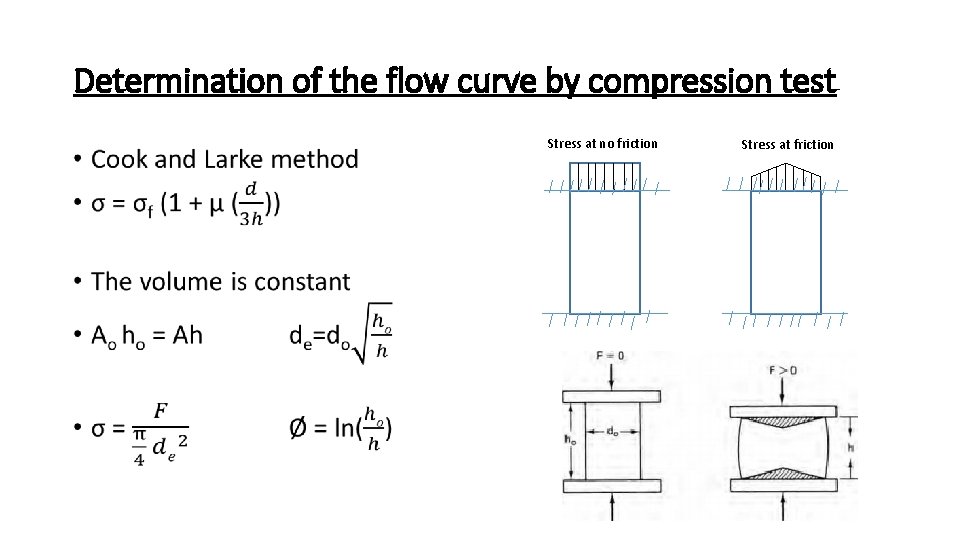
Determination of the flow curve by compression test • Stress at no friction Stress at friction
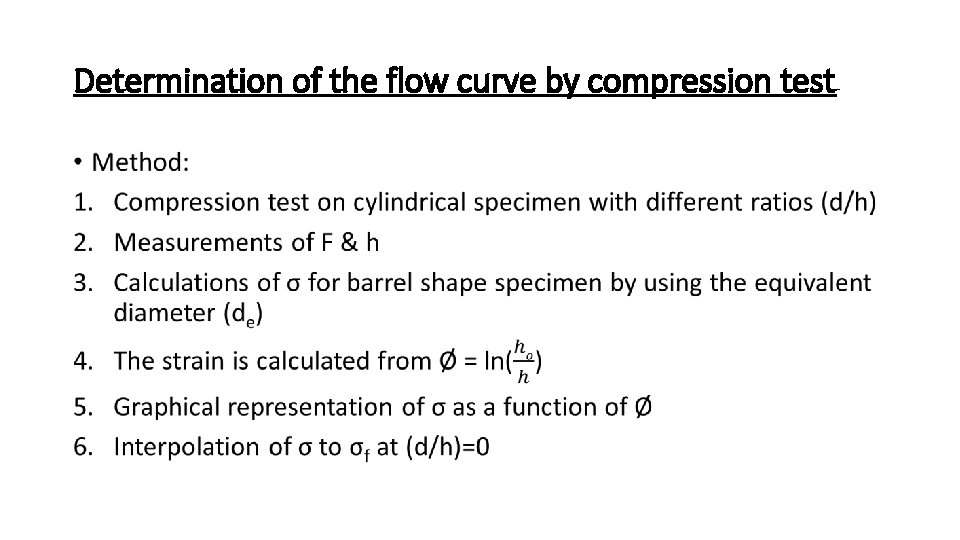
Determination of the flow curve by compression test •
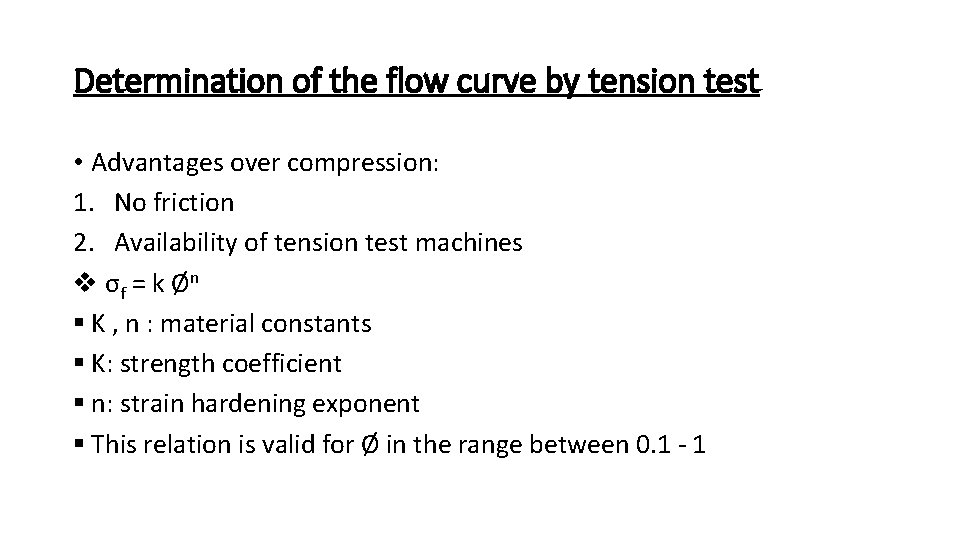
Determination of the flow curve by tension test • Advantages over compression: 1. No friction 2. Availability of tension test machines v σf = k Ø n § K , n : material constants § K: strength coefficient § n: strain hardening exponent § This relation is valid for Ø in the range between 0. 1 - 1
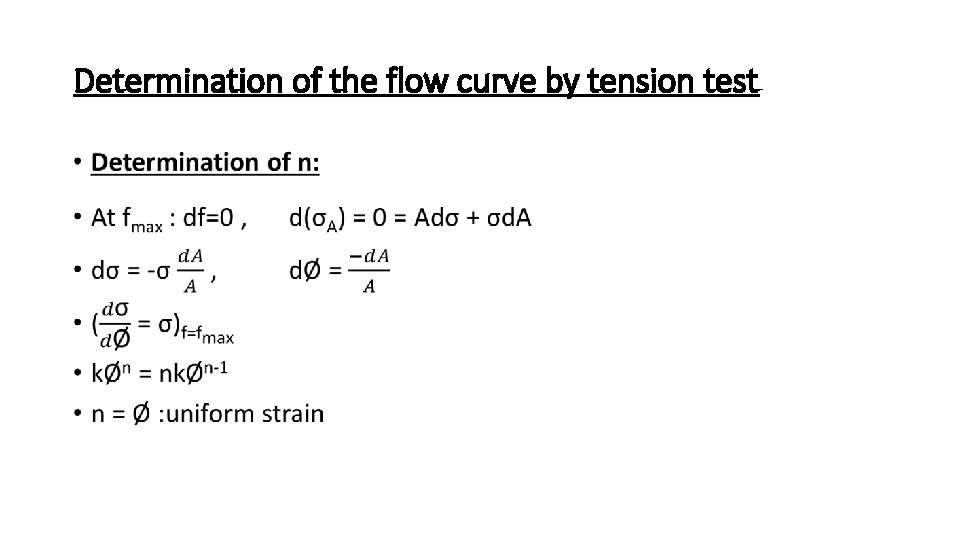
Determination of the flow curve by tension test •
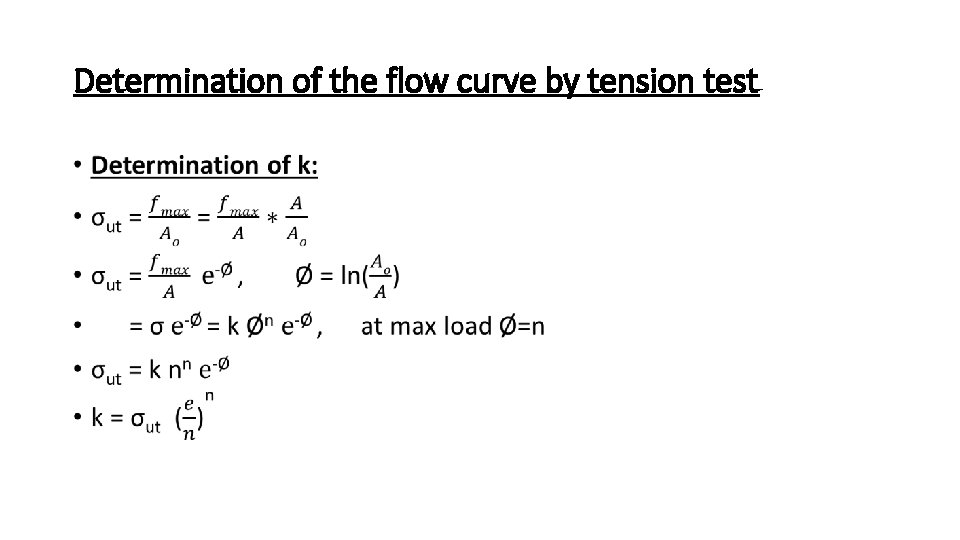
Determination of the flow curve by tension test •
Alur proses produksi produk
Flanging adalah
Advantages of hot working over cold working
Fine blanking
Forming process in sheet metal
Fundamentals of metal forming
Metal forming analysis gtu
Explosive metal forming
Mcq on sheet metal forming
Slitting and shearing
Fundamentals of metal forming
New grilling technology cuts production time in half
New grilling technology cuts production time in half
New grilling technology cuts production time in half
Maize production technology
Cylindrical grinding machine
Production technology of lucerne