Magnetic Field Design of CEPC Detector Magnet Ning
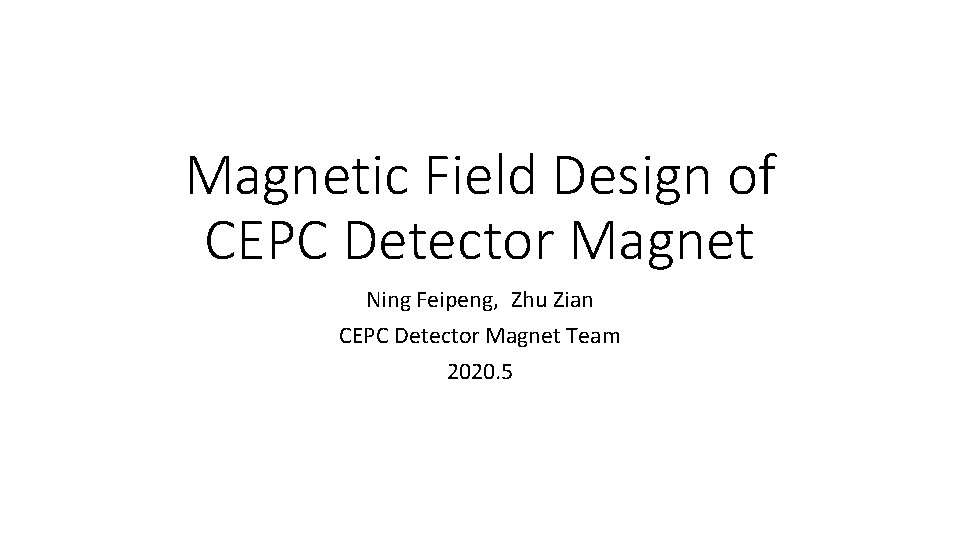
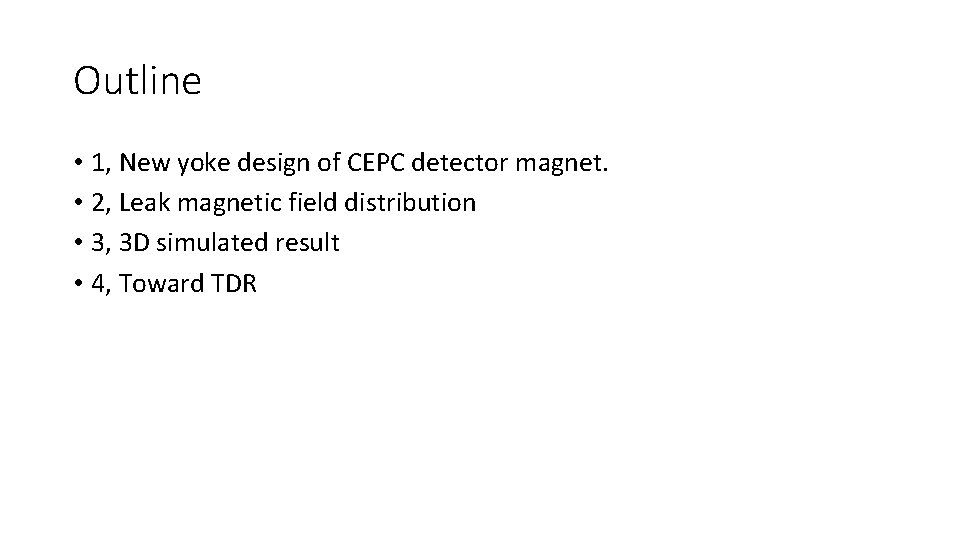
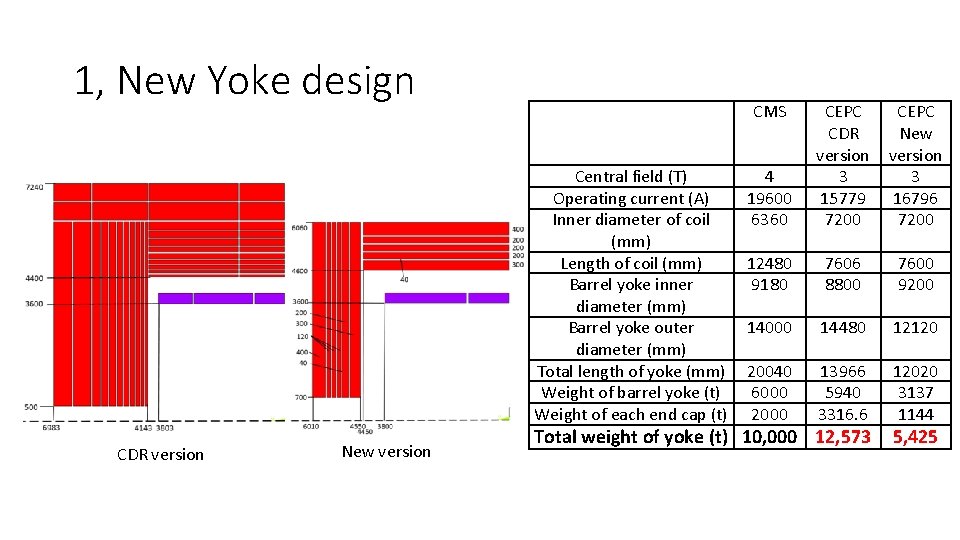
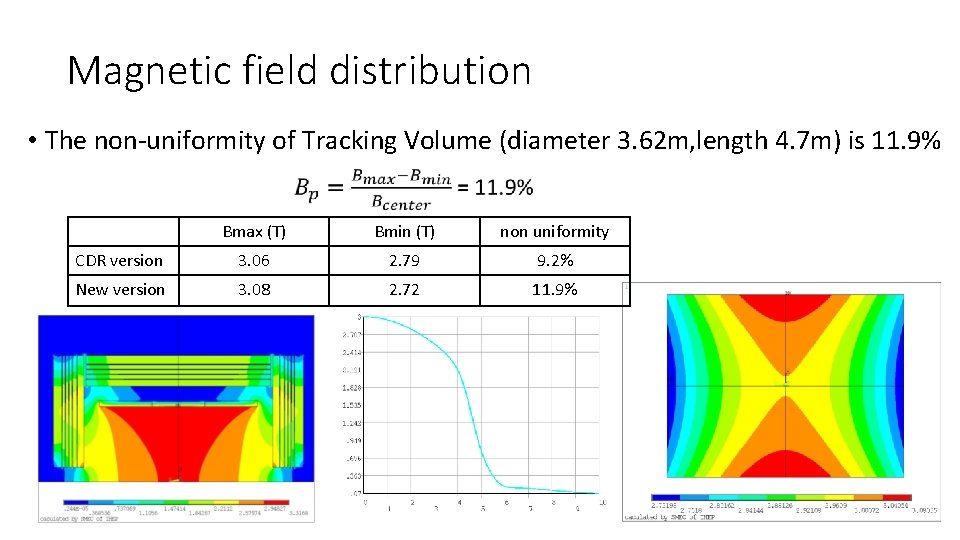
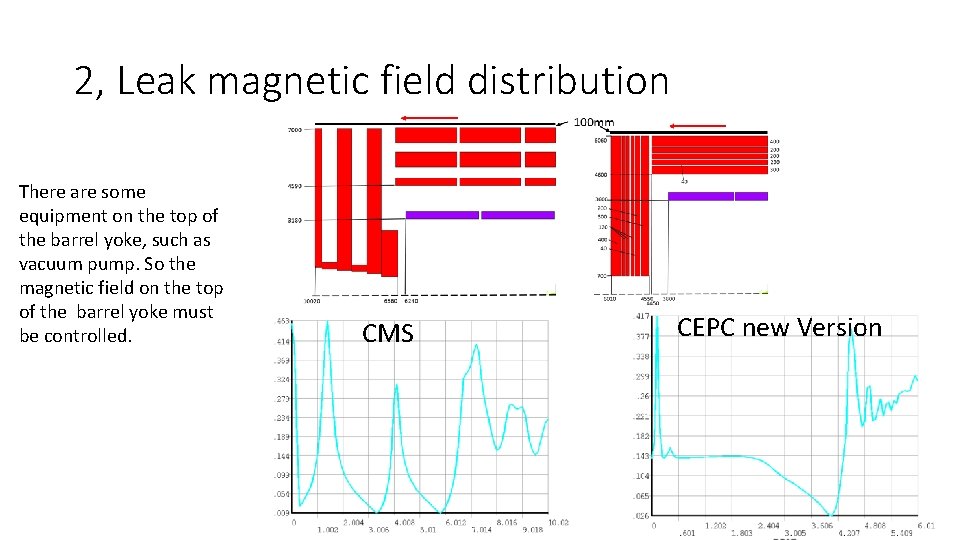
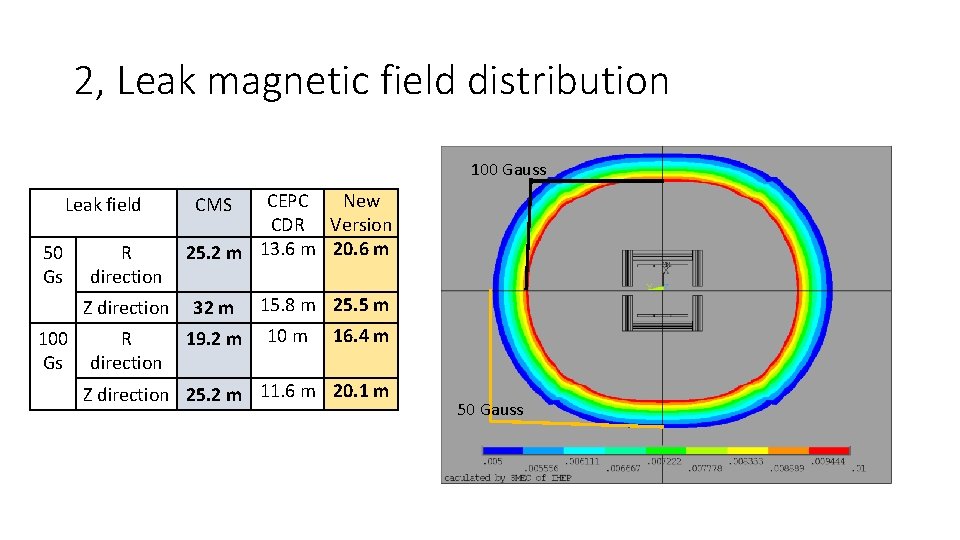
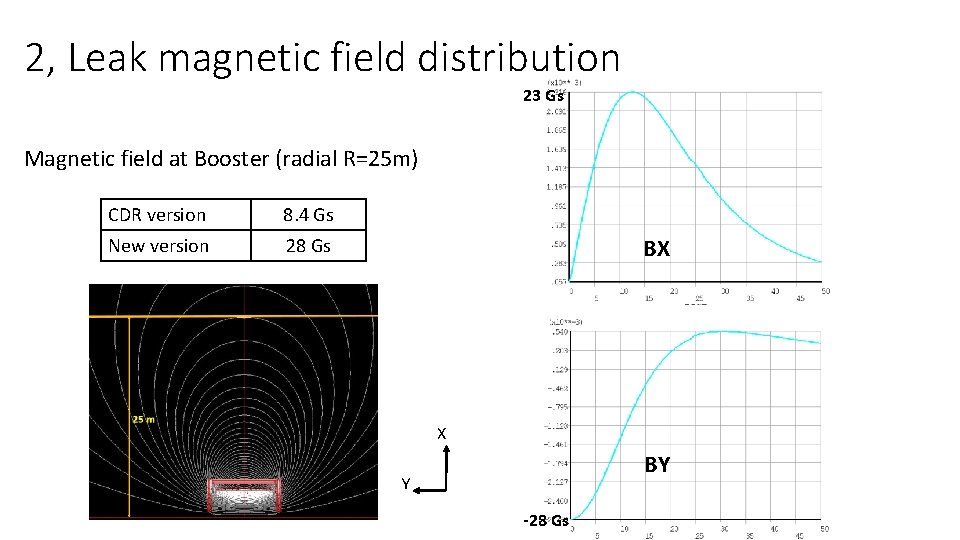
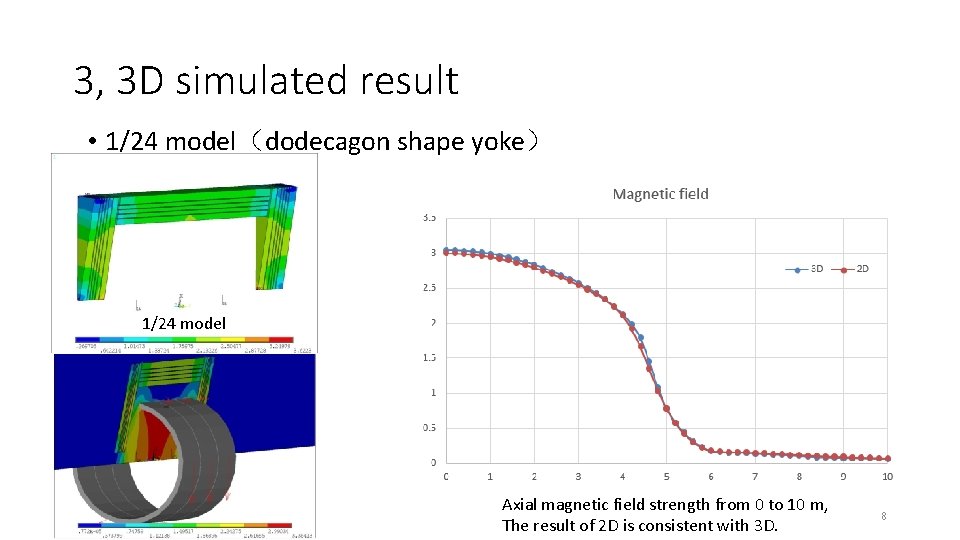
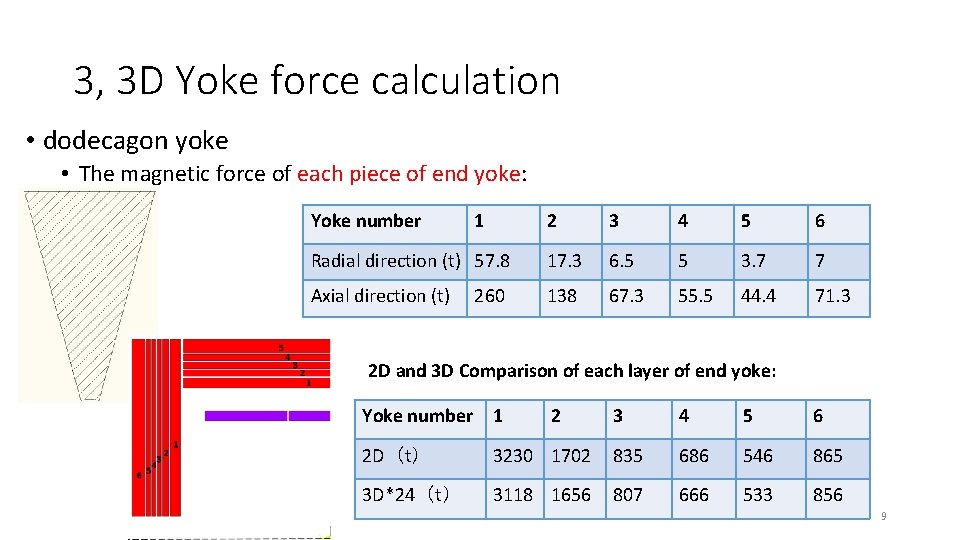
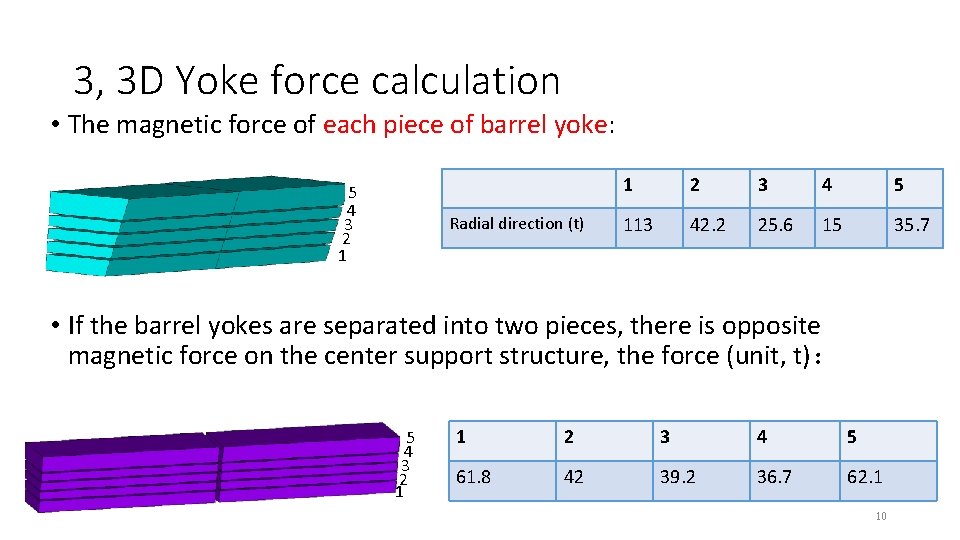
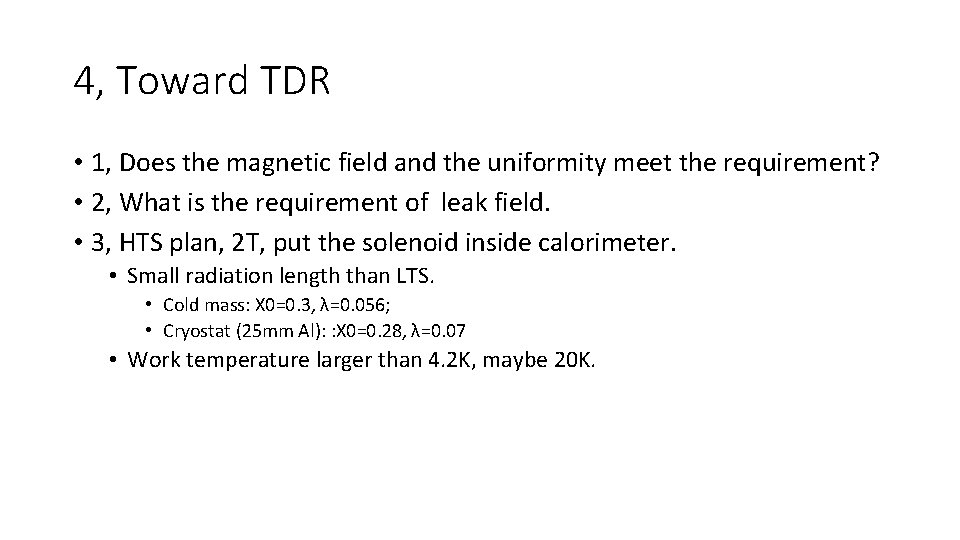
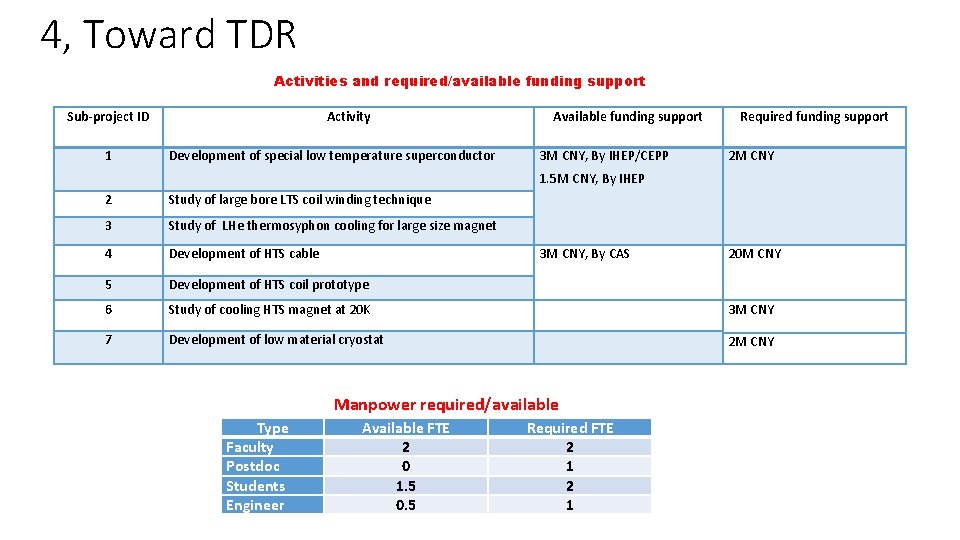
- Slides: 12
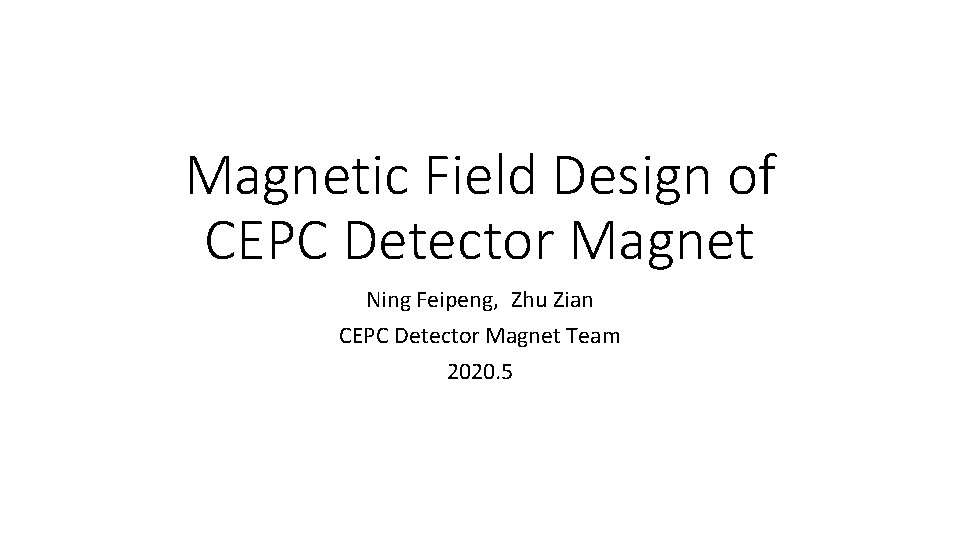
Magnetic Field Design of CEPC Detector Magnet Ning Feipeng, Zhu Zian CEPC Detector Magnet Team 2020. 5
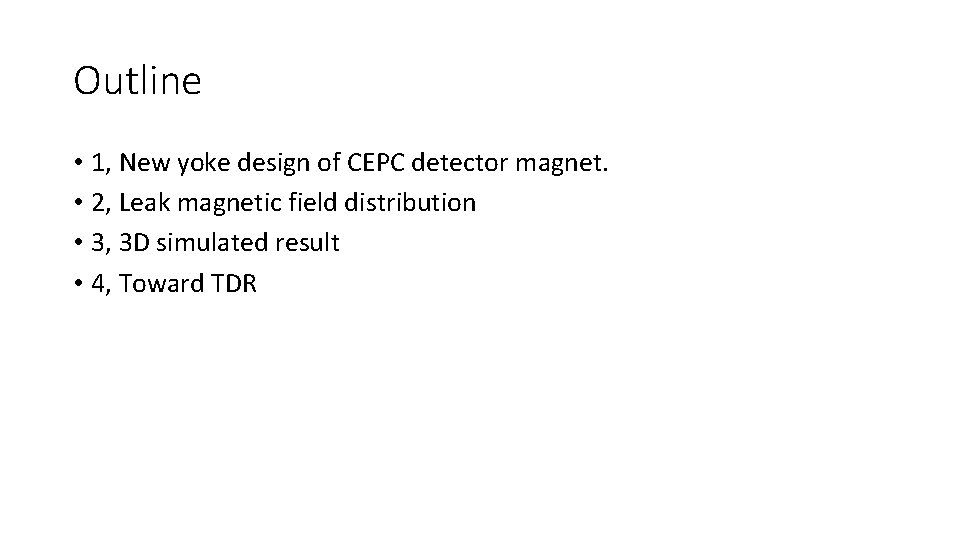
Outline • 1, New yoke design of CEPC detector magnet. • 2, Leak magnetic field distribution • 3, 3 D simulated result • 4, Toward TDR
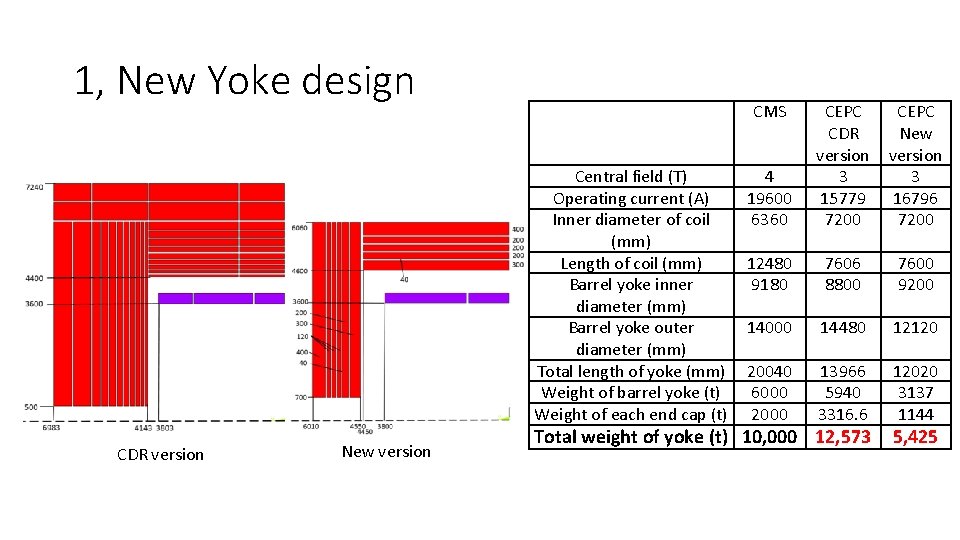
1, New Yoke design CDR version New version CMS 4 19600 6360 CEPC CDR version 3 15779 7200 CEPC New version 3 16796 7200 Central field (T) Operating current (A) Inner diameter of coil (mm) Length of coil (mm) Barrel yoke inner diameter (mm) Barrel yoke outer diameter (mm) Total length of yoke (mm) Weight of barrel yoke (t) Weight of each end cap (t) 12480 9180 7606 8800 7600 9200 14000 14480 12120 20040 6000 2000 13966 5940 3316. 6 12020 3137 1144 Total weight of yoke (t) 10, 000 12, 573 5, 425
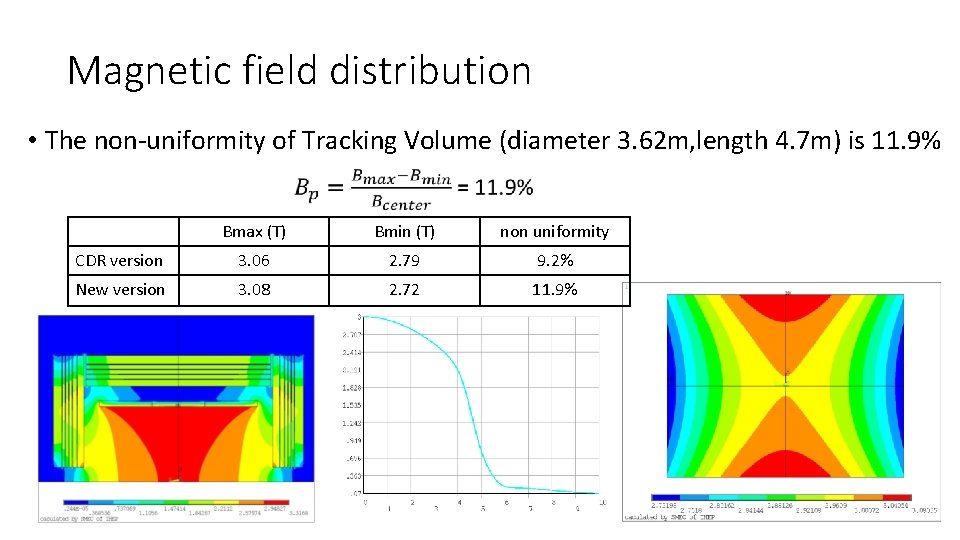
Magnetic field distribution • The non-uniformity of Tracking Volume (diameter 3. 62 m, length 4. 7 m) is 11. 9% Bmax (T) Bmin (T) non uniformity CDR version 3. 06 2. 79 9. 2% New version 3. 08 2. 72 11. 9%
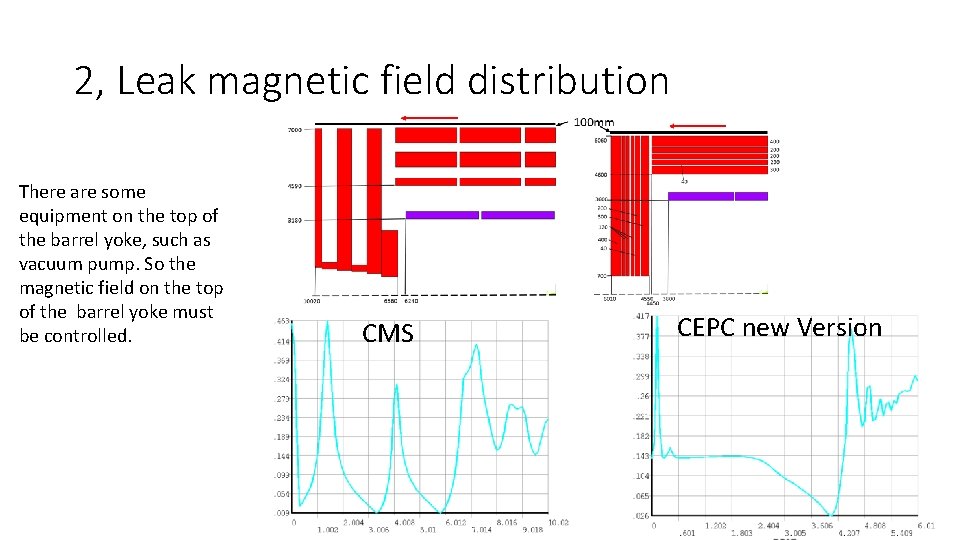
2, Leak magnetic field distribution There are some equipment on the top of the barrel yoke, such as vacuum pump. So the magnetic field on the top of the barrel yoke must be controlled. CMS CEPC new Version
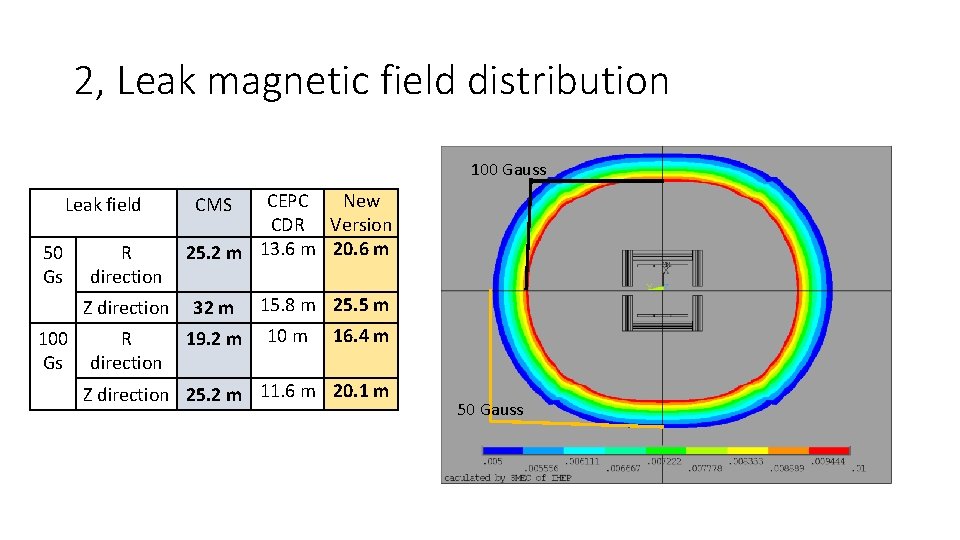
2, Leak magnetic field distribution 100 Gauss Leak field 50 Gs R direction Z direction 100 R Gs direction CEPC New CDR Version 25. 2 m 13. 6 m 20. 6 m CMS 32 m 19. 2 m 15. 8 m 25. 5 m 10 m 16. 4 m Z direction 25. 2 m 11. 6 m 20. 1 m 50 Gauss
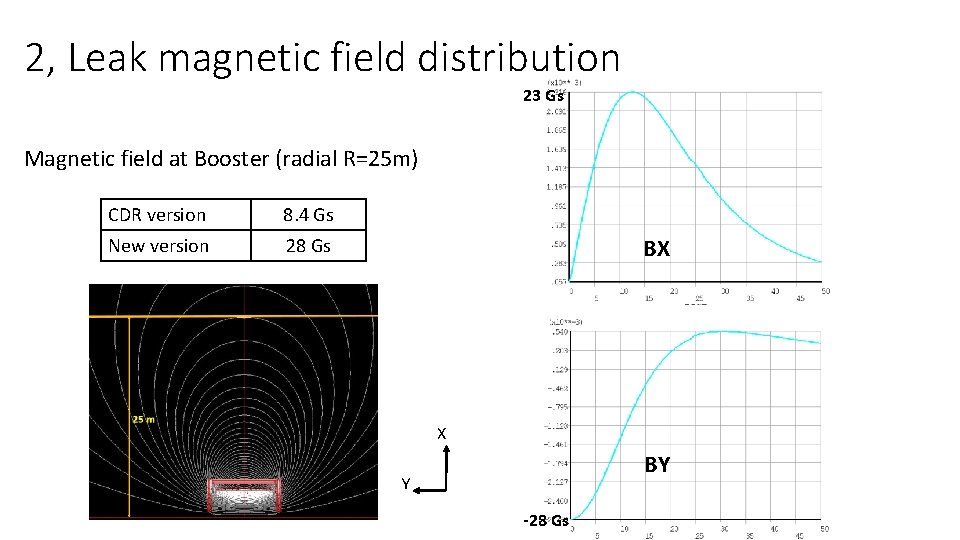
2, Leak magnetic field distribution 23 Gs Magnetic field at Booster (radial R=25 m) CDR version 8. 4 Gs New version 28 Gs BX X BY Y -28 Gs
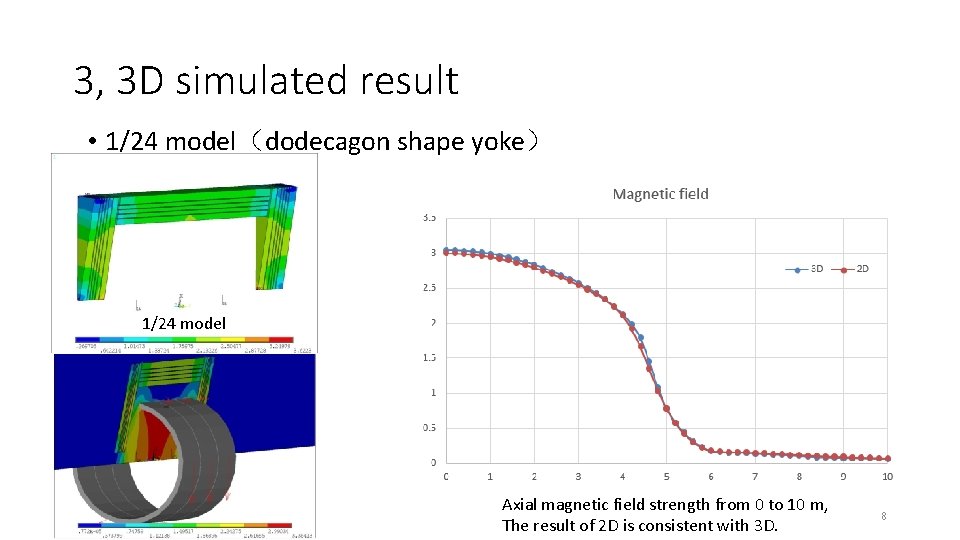
3, 3 D simulated result • 1/24 model(dodecagon shape yoke) 1/24 model Axial magnetic field strength from 0 to 10 m, The result of 2 D is consistent with 3 D. 8
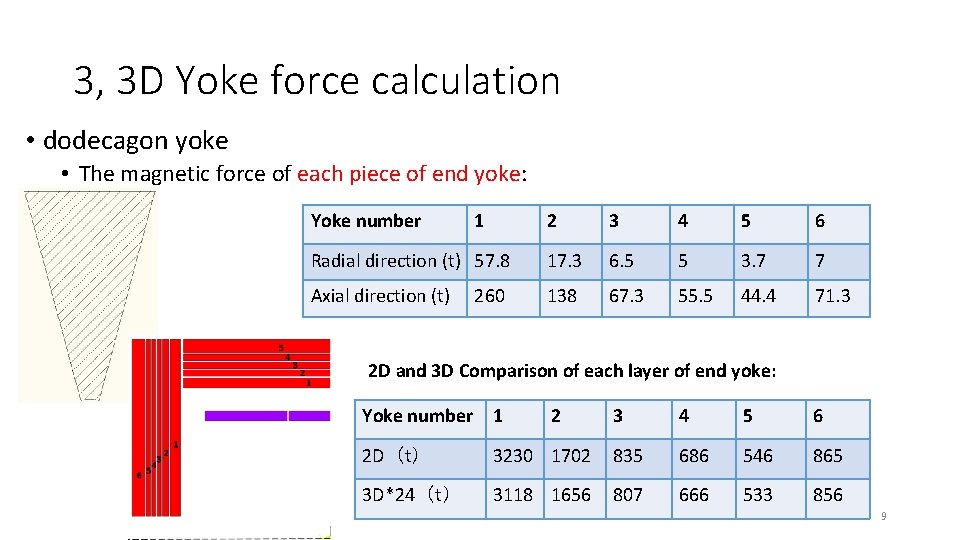
3, 3 D Yoke force calculation • dodecagon yoke • The magnetic force of each piece of end yoke: Yoke number 1 2 3 4 5 6 Radial direction (t) 57. 8 17. 3 6. 5 5 3. 7 7 Axial direction (t) 138 67. 3 55. 5 44. 4 71. 3 260 2 D and 3 D Comparison of each layer of end yoke: Yoke number 1 2 3 4 5 6 2 D(t) 3230 1702 835 686 546 865 3 D*24(t) 3118 1656 807 666 533 856 9
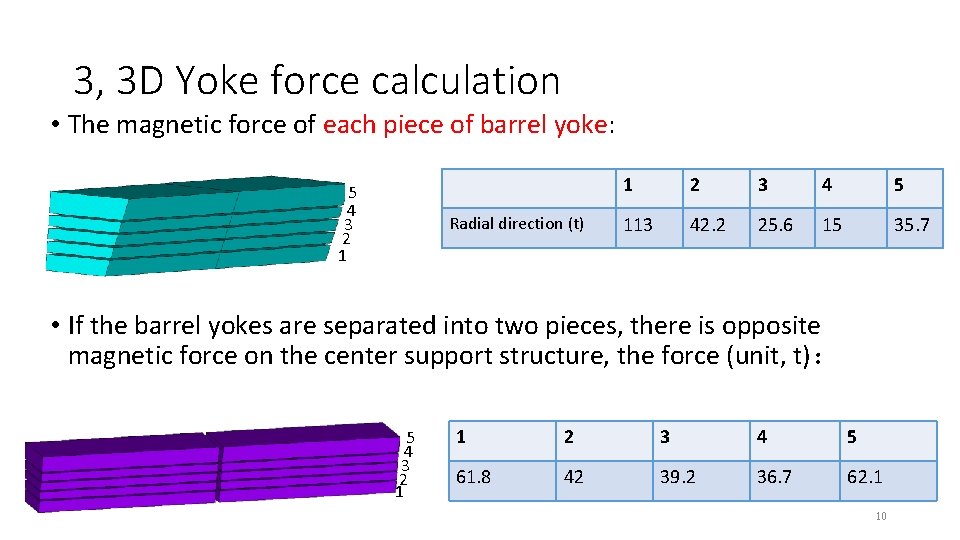
3, 3 D Yoke force calculation • The magnetic force of each piece of barrel yoke: 5 4 3 2 1 Radial direction (t) 1 2 3 4 5 113 42. 2 25. 6 15 35. 7 • If the barrel yokes are separated into two pieces, there is opposite magnetic force on the center support structure, the force (unit, t): 5 4 3 2 1 1 2 3 4 5 61. 8 42 39. 2 36. 7 62. 1 10
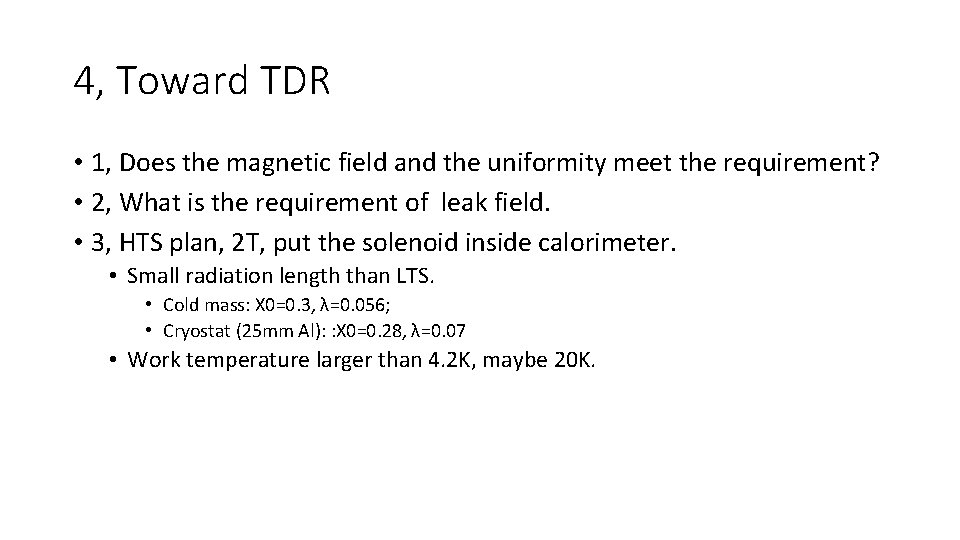
4, Toward TDR • 1, Does the magnetic field and the uniformity meet the requirement? • 2, What is the requirement of leak field. • 3, HTS plan, 2 T, put the solenoid inside calorimeter. • Small radiation length than LTS. • Cold mass: X 0=0. 3, λ=0. 056; • Cryostat (25 mm Al): : X 0=0. 28, λ=0. 07 • Work temperature larger than 4. 2 K, maybe 20 K.
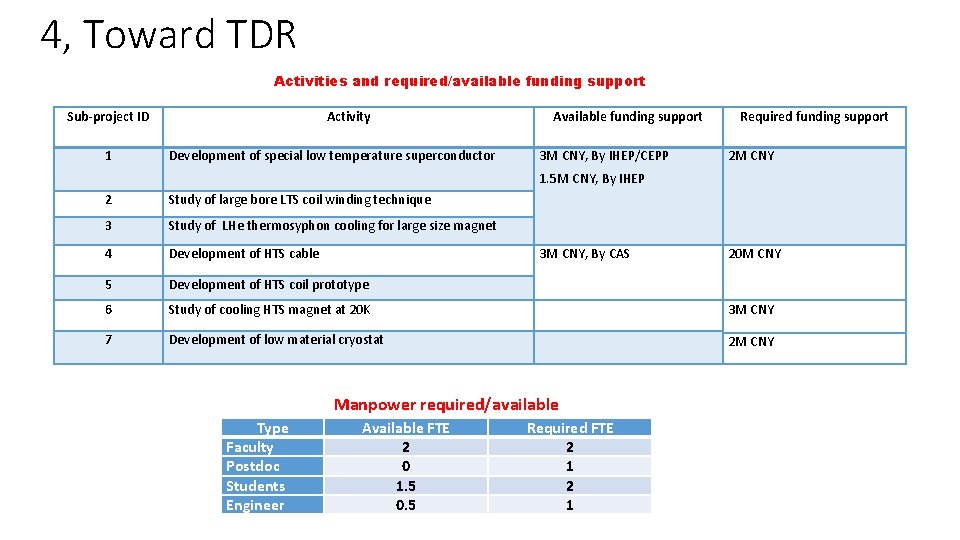
4, Toward TDR Activities and required/available funding support Sub-project ID 1 Activity Development of special low temperature superconductor Available funding support 3 M CNY, By IHEP/CEPP Required funding support 2 M CNY 1. 5 M CNY, By IHEP 2 Study of large bore LTS coil winding technique 3 Study of LHe thermosyphon cooling for large size magnet 4 Development of HTS cable 5 Development of HTS coil prototype 6 Study of cooling HTS magnet at 20 K 3 M CNY 7 Development of low material cryostat 2 M CNY 3 M CNY, By CAS Manpower required/available Type Faculty Postdoc Students Engineer Available FTE 2 0 1. 5 0. 5 Required FTE 2 1 20 M CNY
Solenoid bbc bitesize
Cow magnet magnetic field
A magnetic force
Horseshoe magnet magnetic field
Magnetic moment and magnetic field relation
Unit of flux
Force on charged particle
Gauss law in magnetism
Distinguish between magnetic and nonmagnetic materials
Difference between electric field and magnetic field
Cepc logo
Cepc logo
What happens if you break a magnet in half