Introduction NonArc Welding Processes Resistive heating chemical reactions
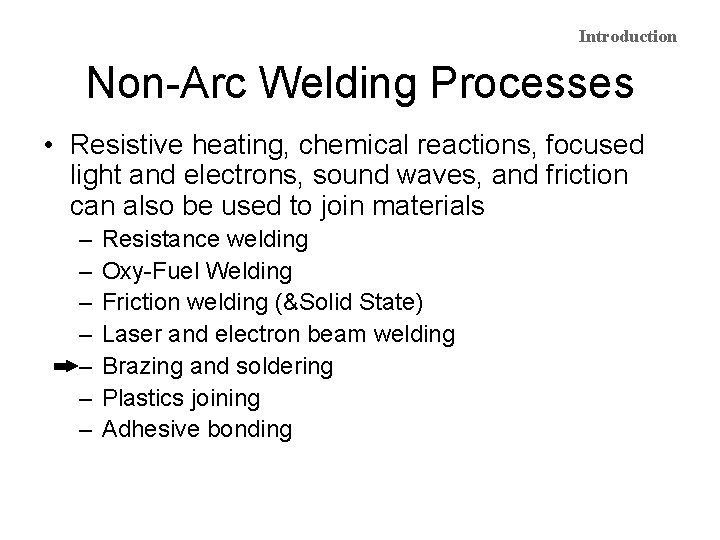
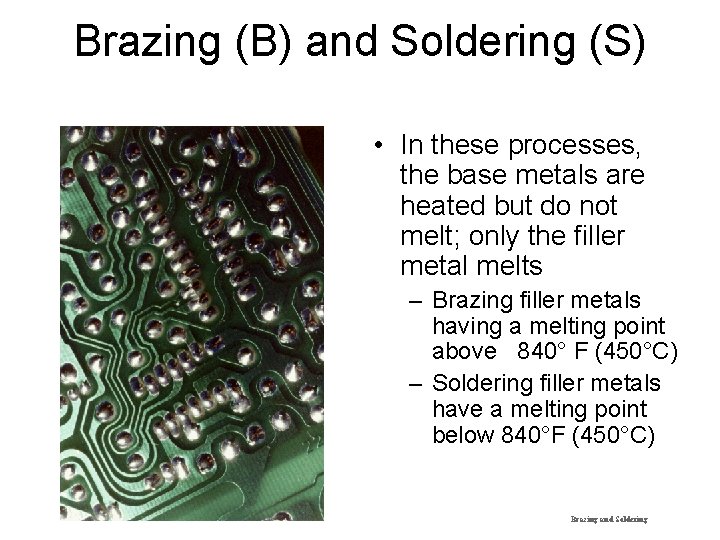
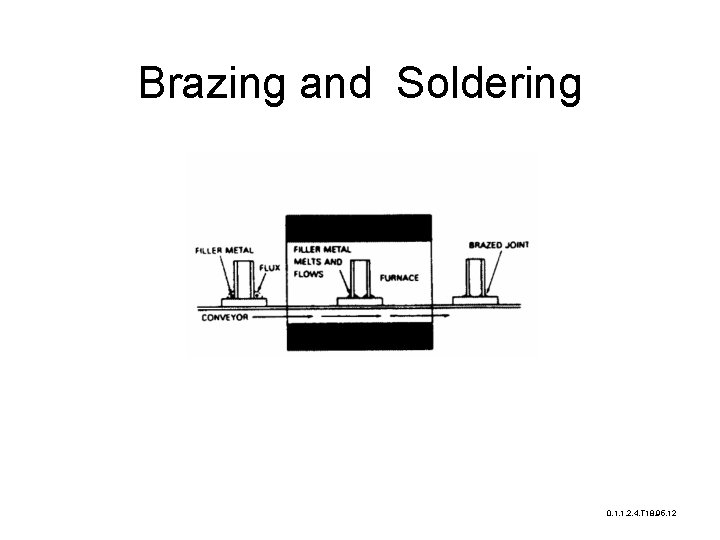
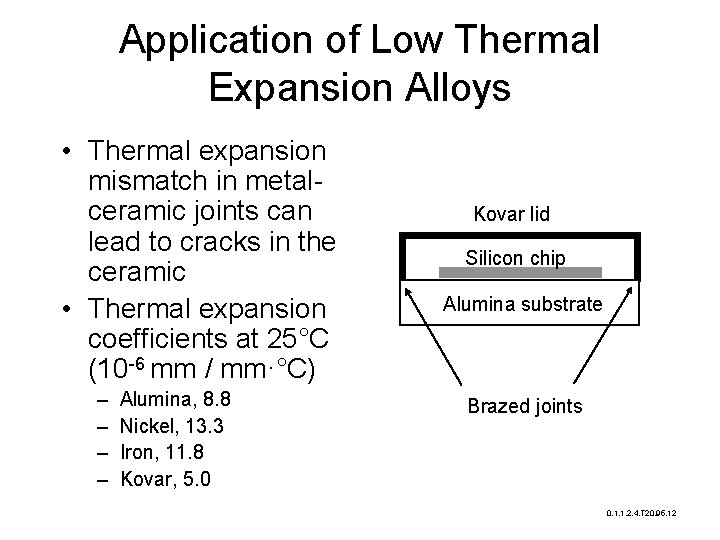
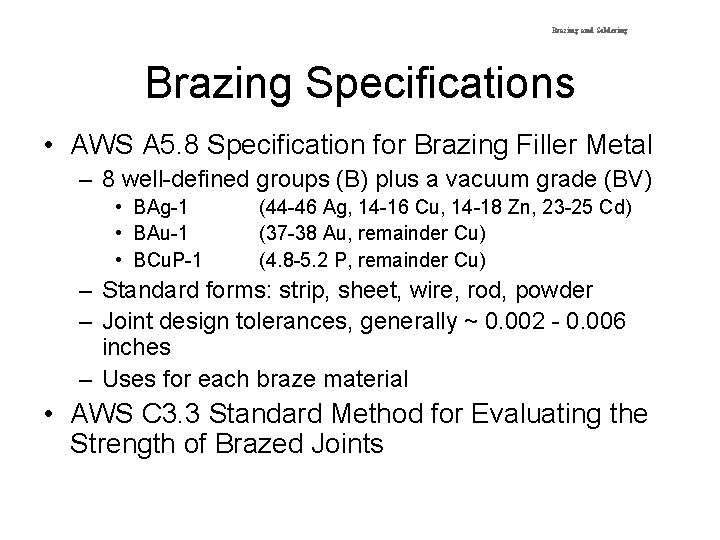
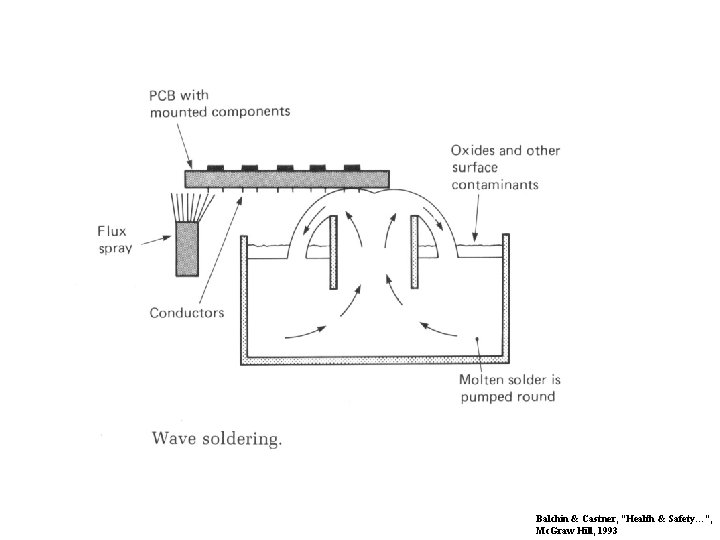
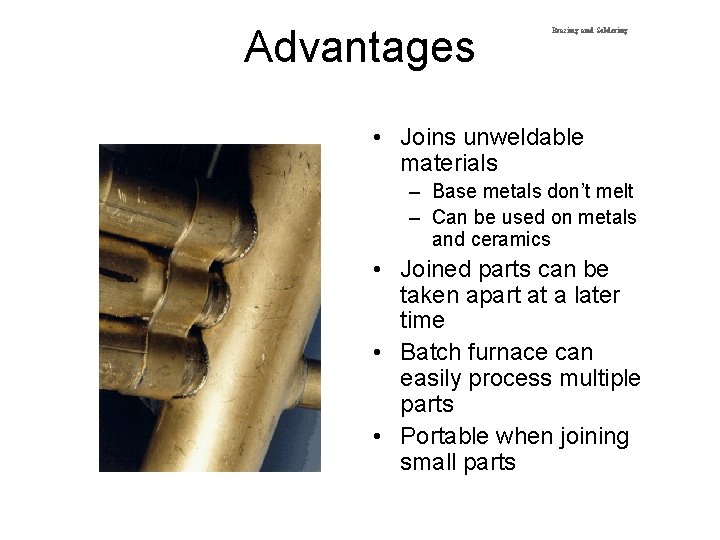
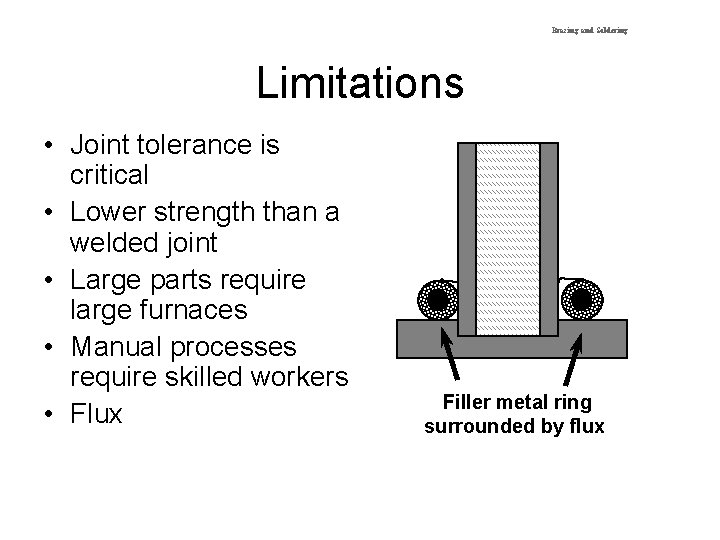
- Slides: 8
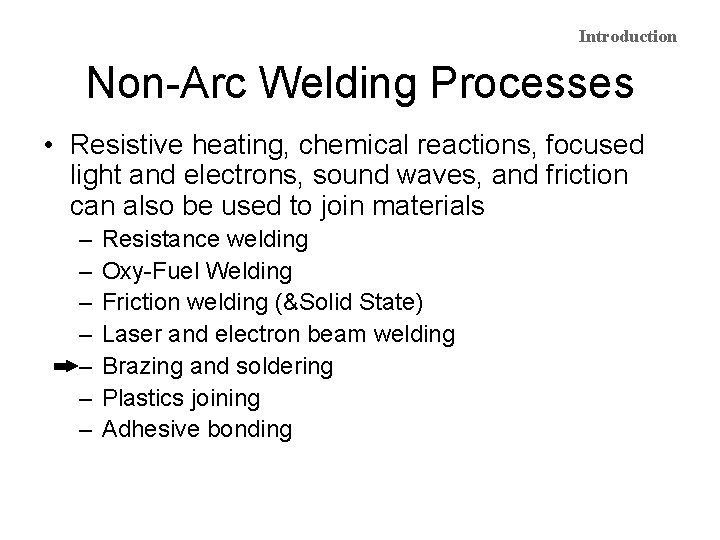
Introduction Non-Arc Welding Processes • Resistive heating, chemical reactions, focused light and electrons, sound waves, and friction can also be used to join materials – – – – Resistance welding Oxy-Fuel Welding Friction welding (&Solid State) Laser and electron beam welding Brazing and soldering Plastics joining Adhesive bonding
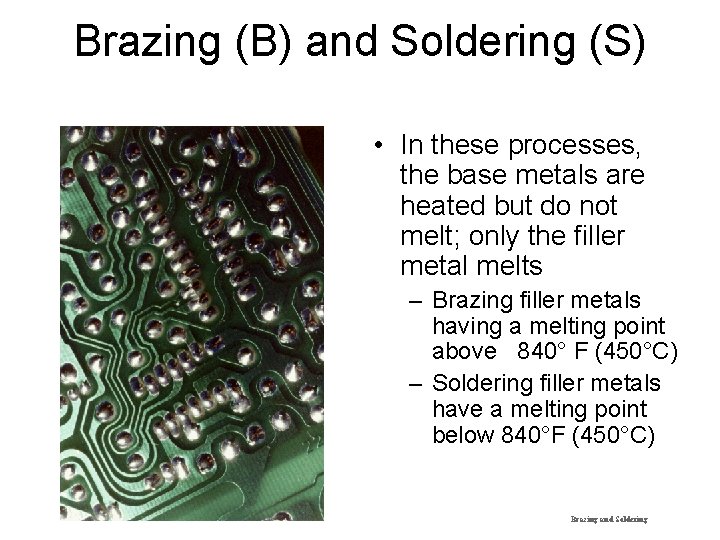
Brazing (B) and Soldering (S) • In these processes, the base metals are heated but do not melt; only the filler metal melts – Brazing filler metals having a melting point above 840° F (450°C) – Soldering filler metals have a melting point below 840°F (450°C) Brazing and Soldering
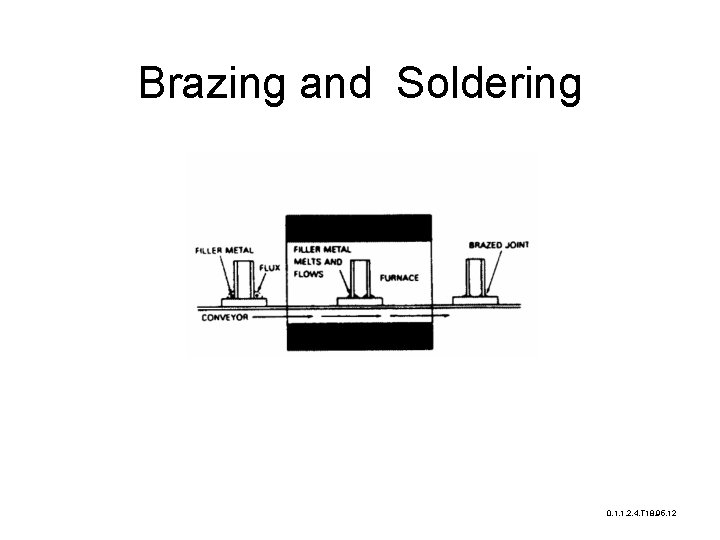
Brazing and Soldering 0. 1. 1. 2. 4. T 18. 95. 12
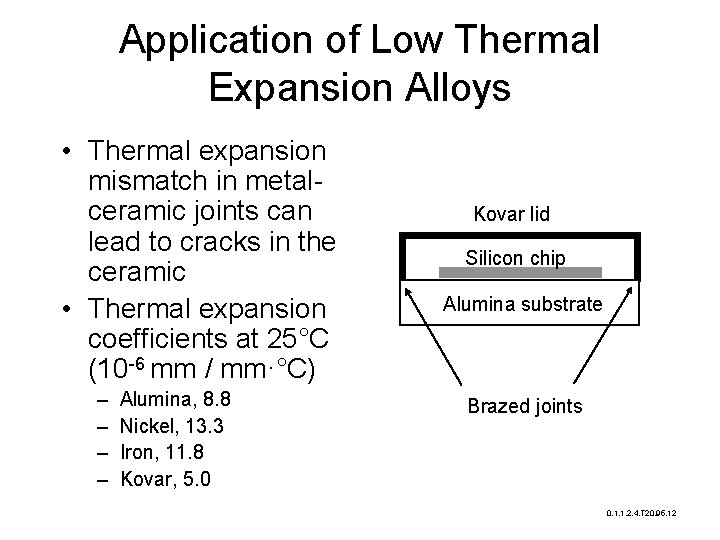
Application of Low Thermal Expansion Alloys • Thermal expansion mismatch in metalceramic joints can lead to cracks in the ceramic • Thermal expansion coefficients at 25°C (10 -6 mm / mm·°C) – – Alumina, 8. 8 Nickel, 13. 3 Iron, 11. 8 Kovar, 5. 0 Kovar lid Silicon chip Alumina substrate Brazed joints 0. 1. 1. 2. 4. T 20. 95. 12
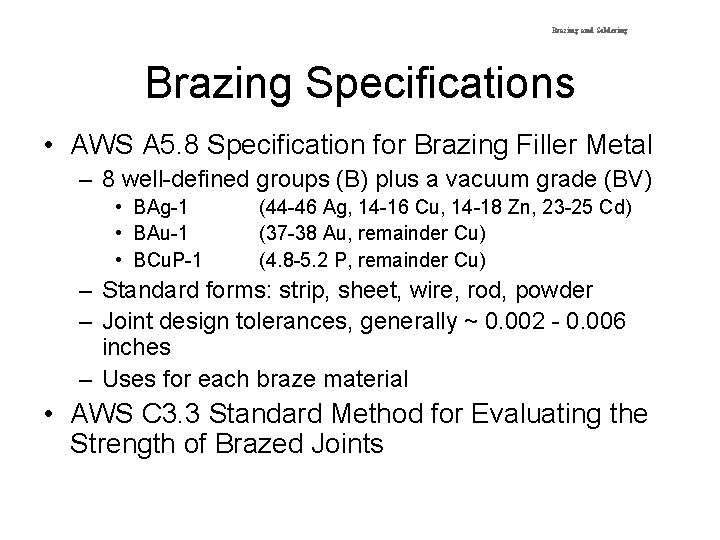
Brazing and Soldering Brazing Specifications • AWS A 5. 8 Specification for Brazing Filler Metal – 8 well-defined groups (B) plus a vacuum grade (BV) • BAg-1 • BAu-1 • BCu. P-1 (44 -46 Ag, 14 -16 Cu, 14 -18 Zn, 23 -25 Cd) (37 -38 Au, remainder Cu) (4. 8 -5. 2 P, remainder Cu) – Standard forms: strip, sheet, wire, rod, powder – Joint design tolerances, generally ~ 0. 002 - 0. 006 inches – Uses for each braze material • AWS C 3. 3 Standard Method for Evaluating the Strength of Brazed Joints
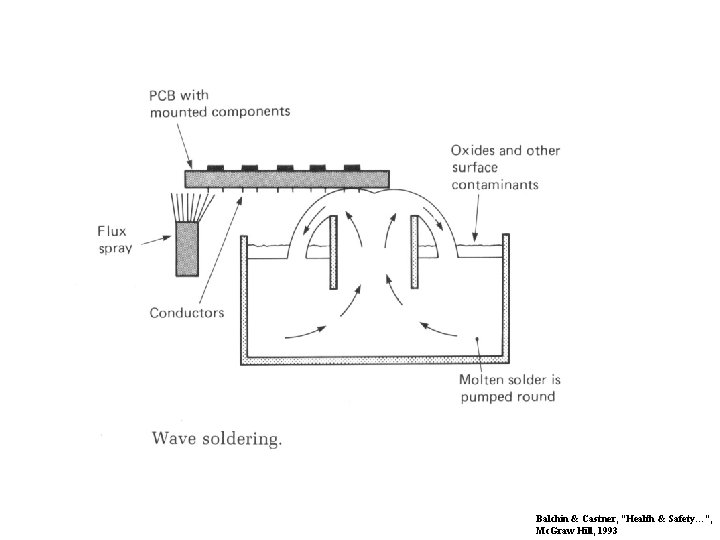
Balchin & Castner, “Health & Safety…”, Mc. Graw Hill, 1993
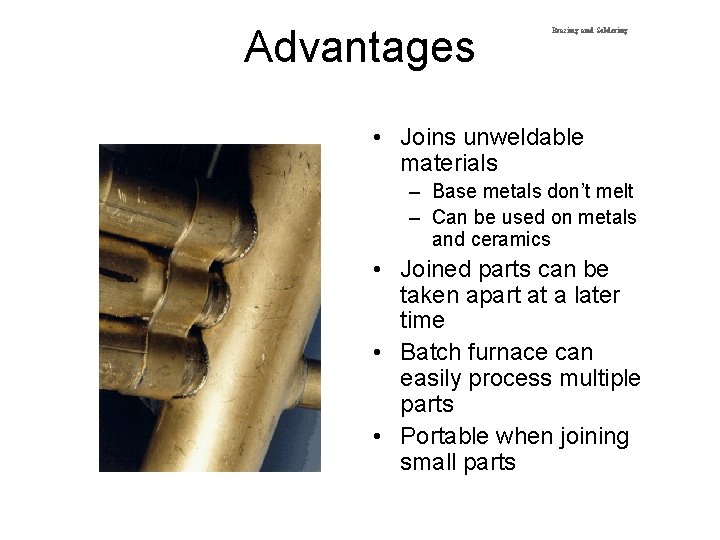
Advantages Brazing and Soldering • Joins unweldable materials – Base metals don’t melt – Can be used on metals and ceramics • Joined parts can be taken apart at a later time • Batch furnace can easily process multiple parts • Portable when joining small parts
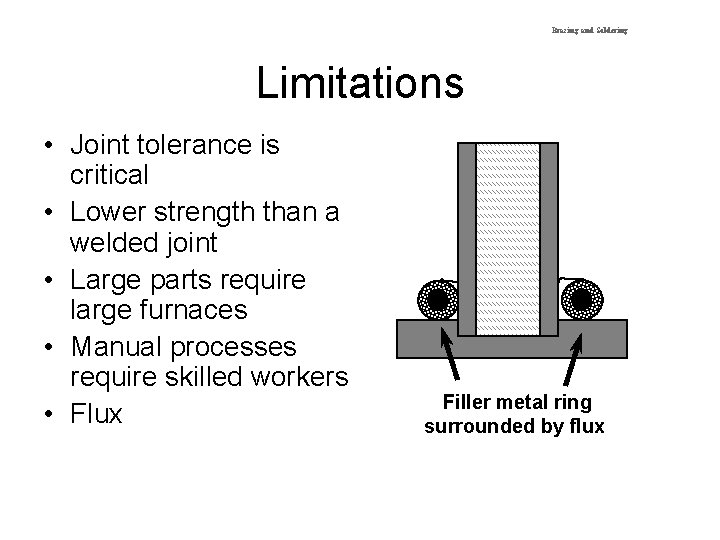
Brazing and Soldering Limitations • Joint tolerance is critical • Lower strength than a welded joint • Large parts require large furnaces • Manual processes require skilled workers • Flux Filler metal ring surrounded by flux
Section 2 classifying chemical reactions
Section 2 classifying chemical reactions
Chemical reactions section 3 reactions in aqueous solutions
Laser beam welding (lbw)
Difference between induction heating and dielectric heating
Chemical reactions section 1 chemical changes
Chapter 18 chemical reactions balancing chemical equations
Example of oxidation reduction reaction
Chemistry unit 5 reactions balancing reactions worksheet