Industrial and Social Applications of Wireless Sensor Nets
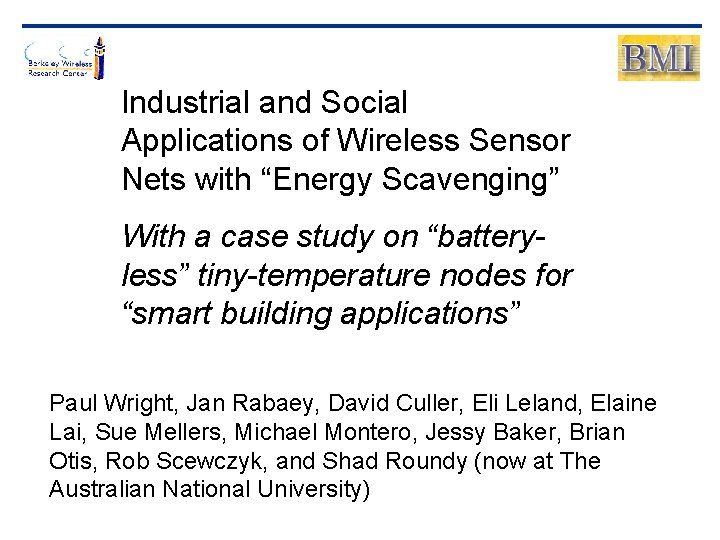
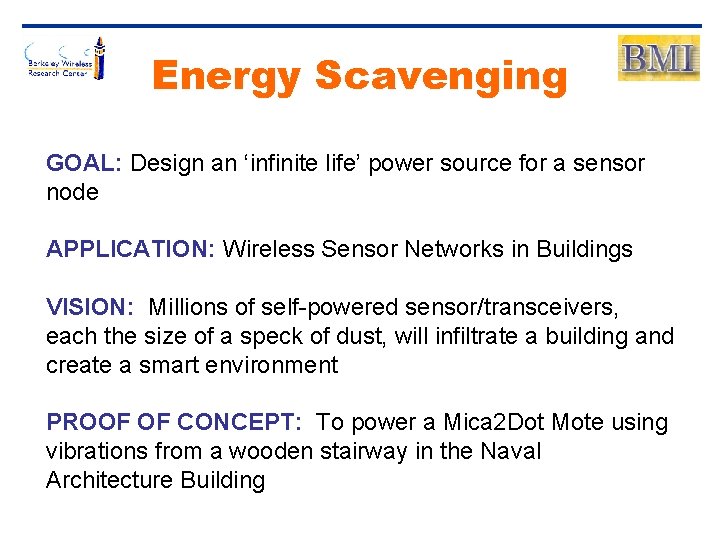
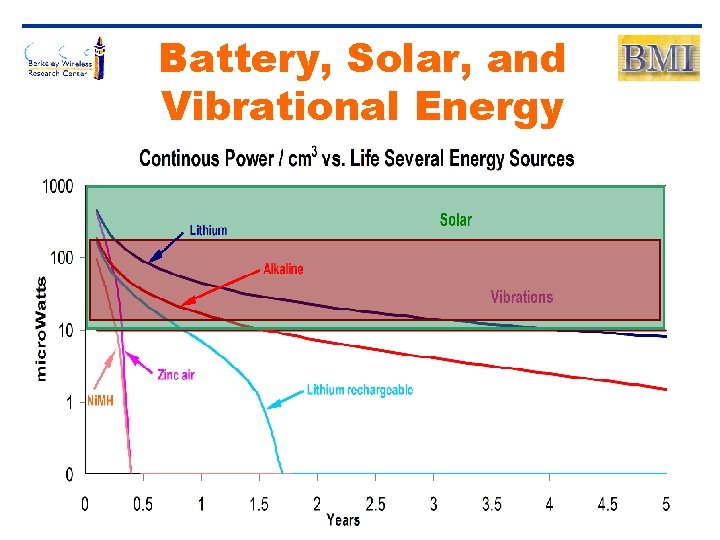
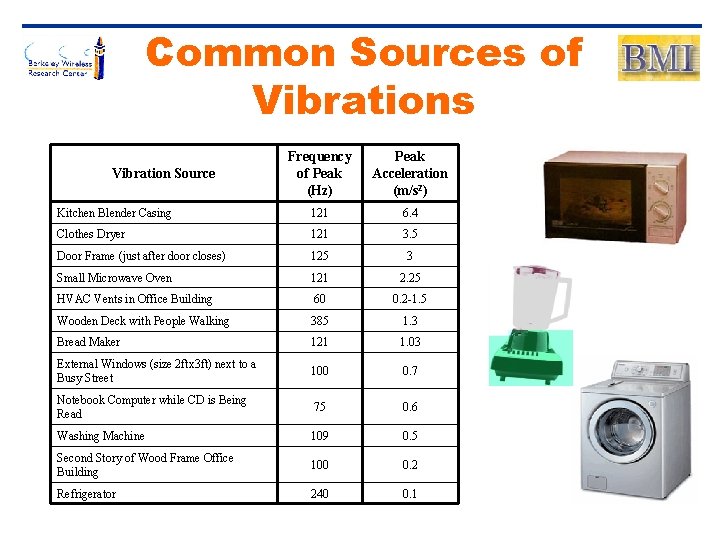
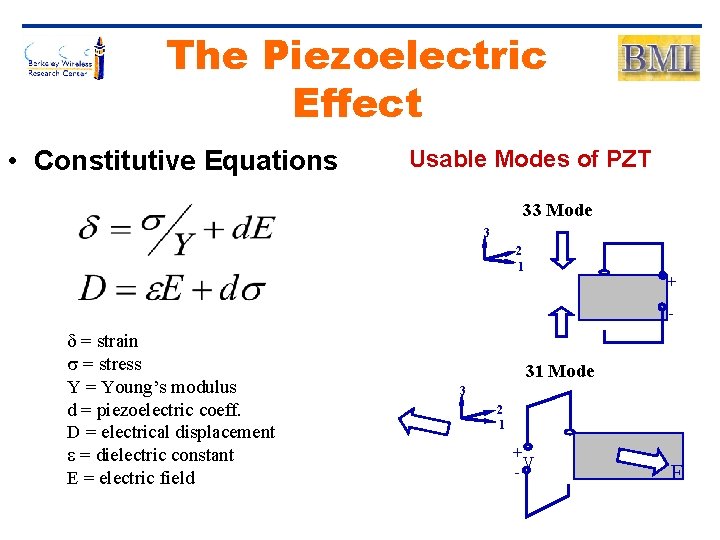
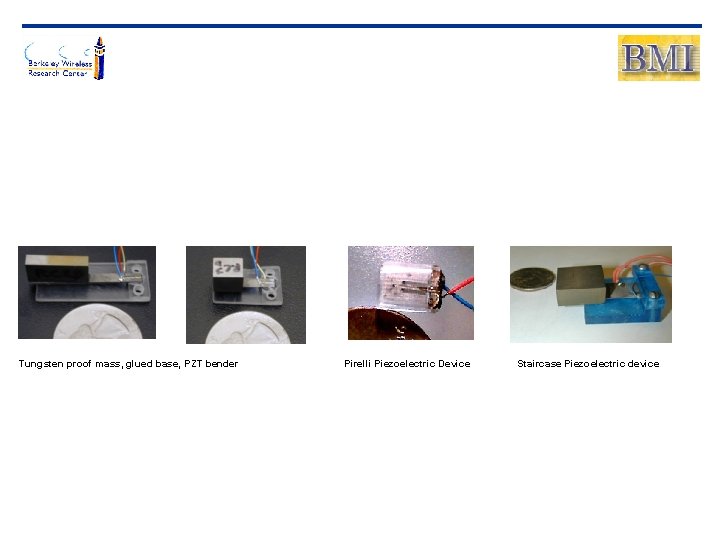
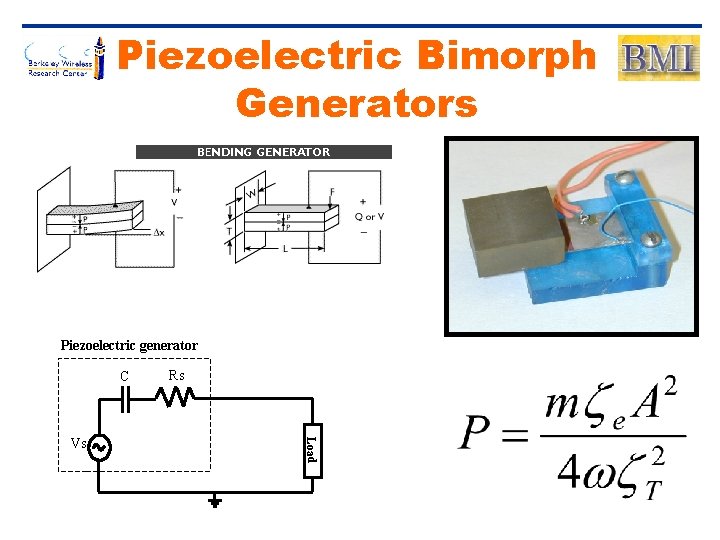
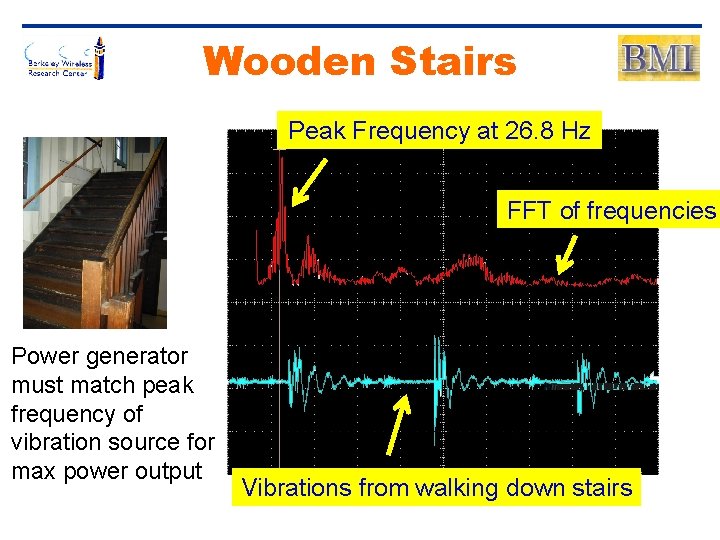
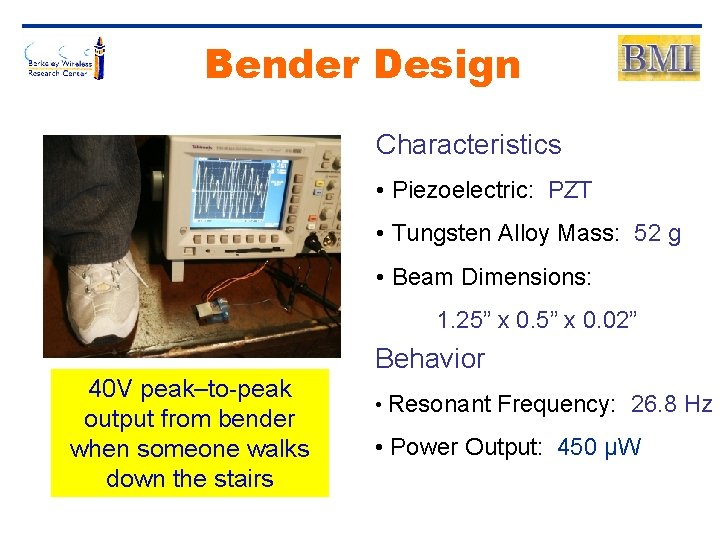
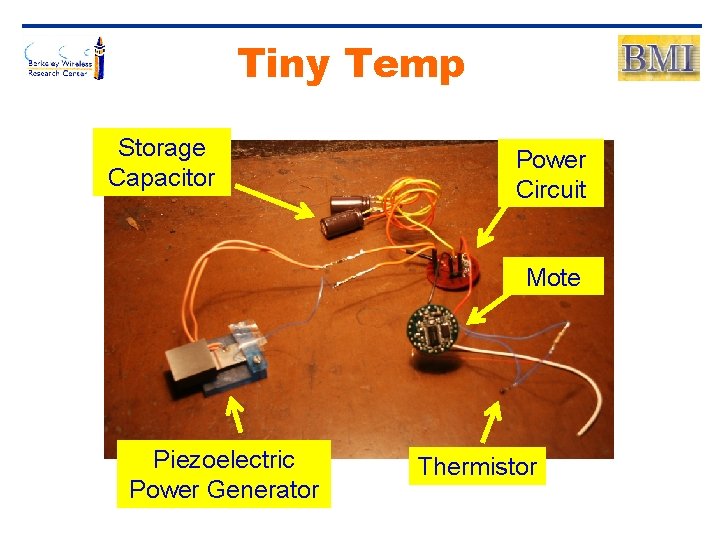
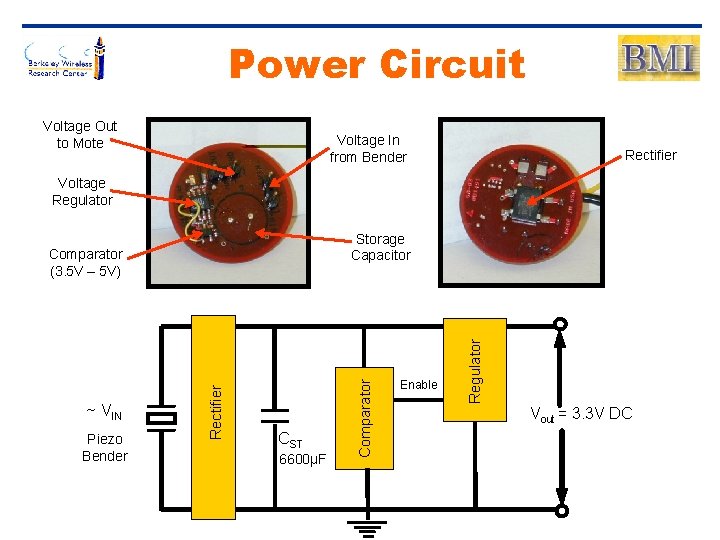
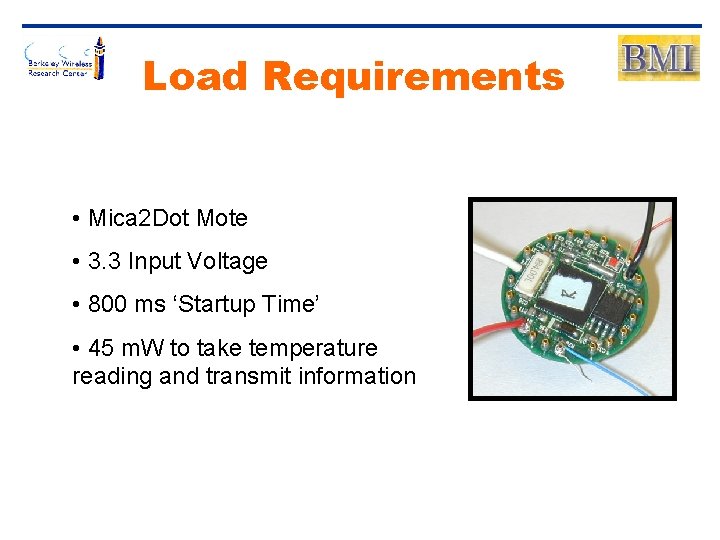
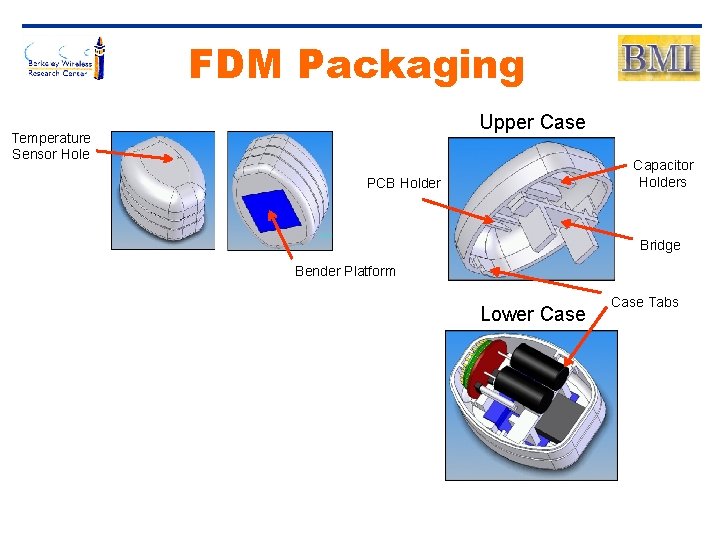
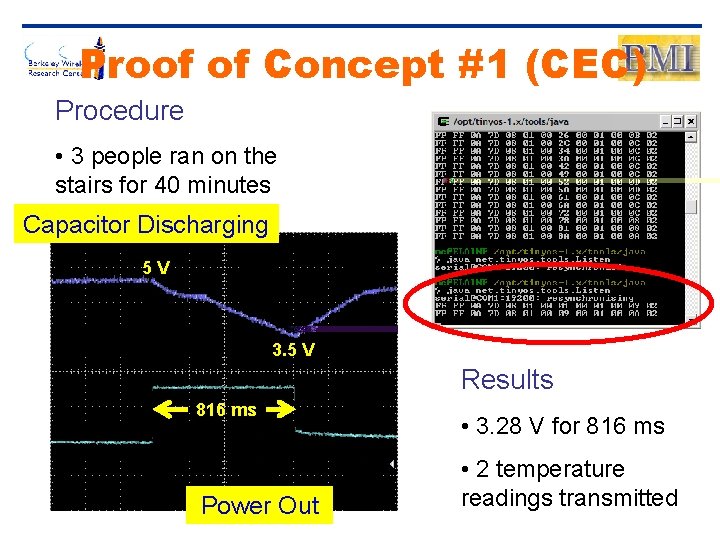
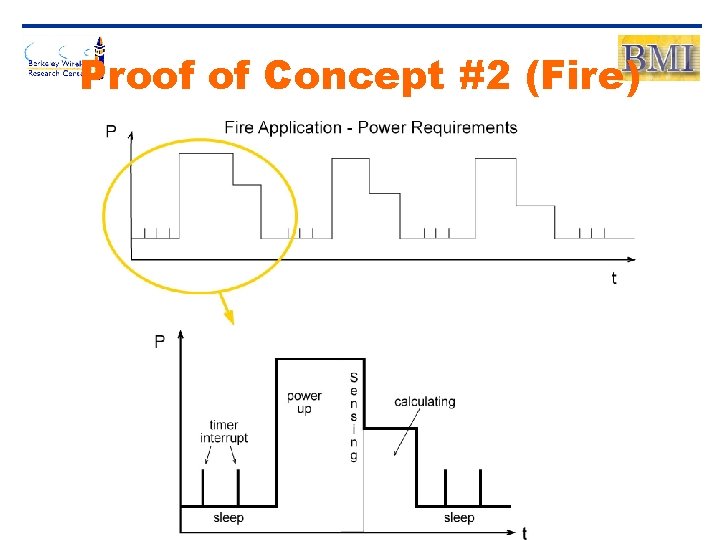
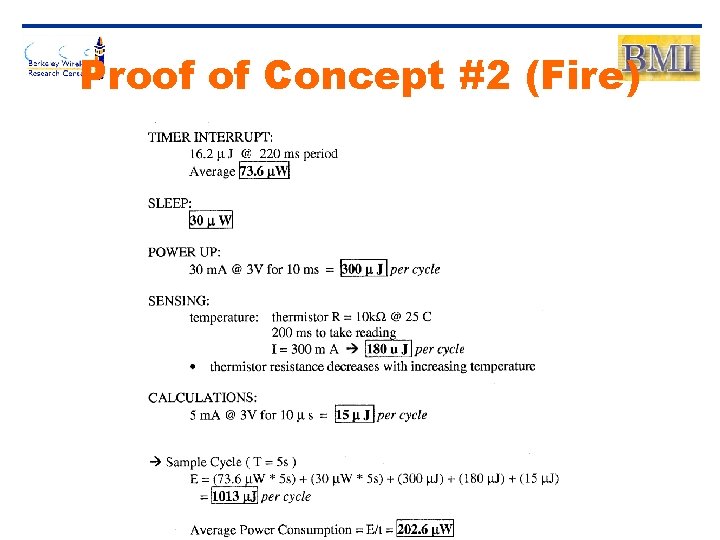
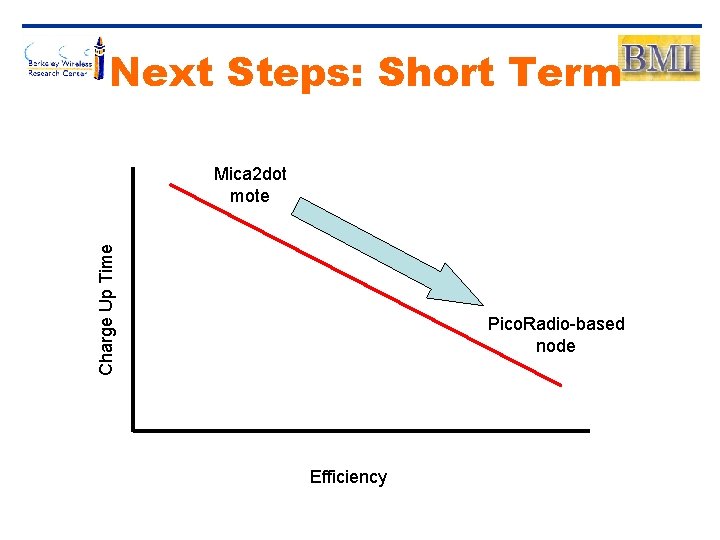
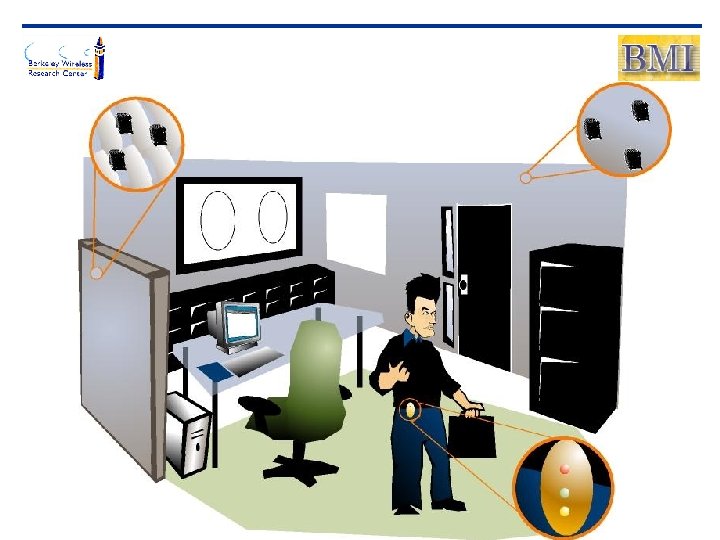
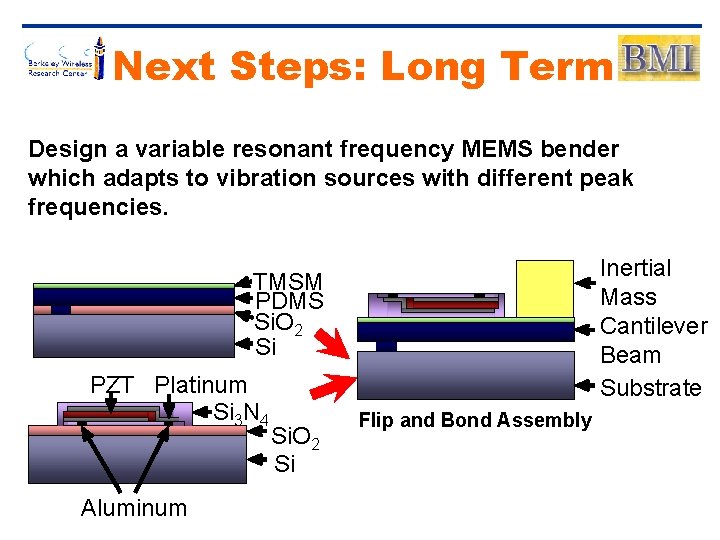
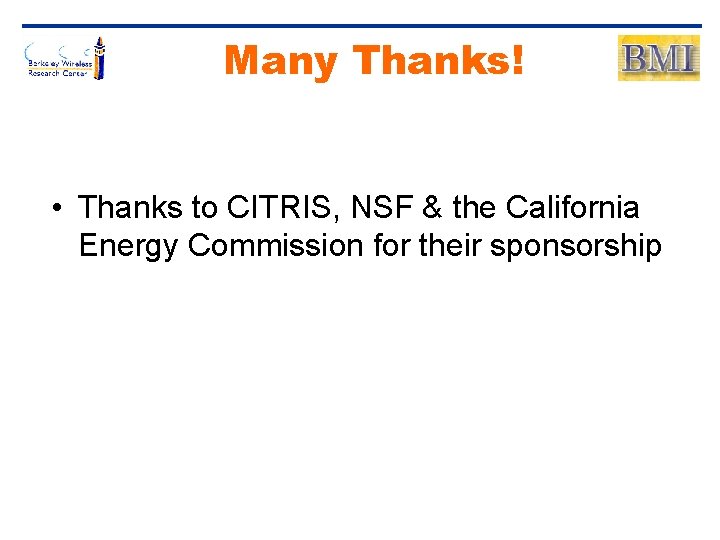
- Slides: 20
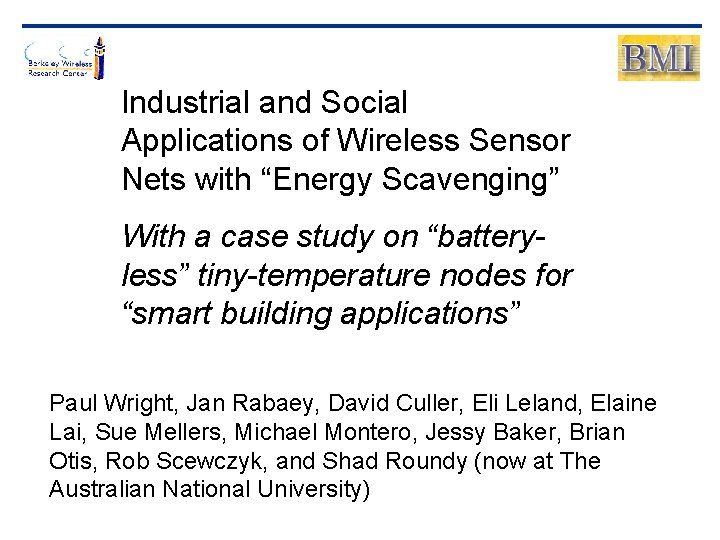
Industrial and Social Applications of Wireless Sensor Nets with “Energy Scavenging” With a case study on “batteryless” tiny-temperature nodes for “smart building applications” Paul Wright, Jan Rabaey, David Culler, Eli Leland, Elaine Lai, Sue Mellers, Michael Montero, Jessy Baker, Brian Otis, Rob Scewczyk, and Shad Roundy (now at The Australian National University)
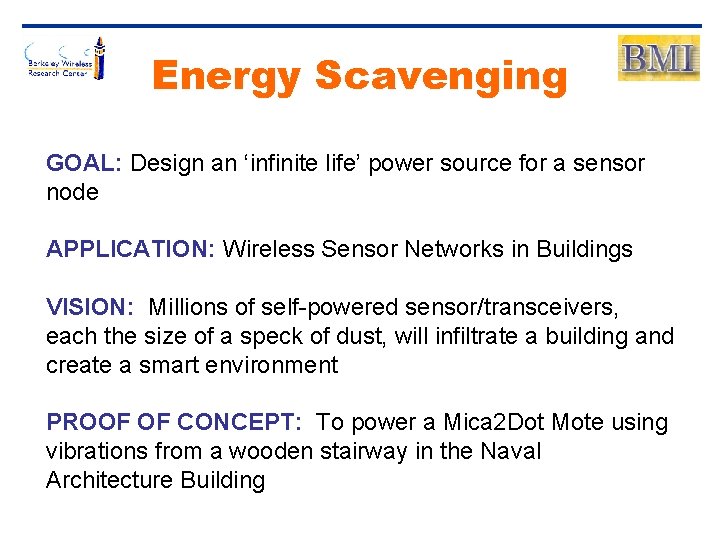
Energy Scavenging GOAL: Design an ‘infinite life’ power source for a sensor node APPLICATION: Wireless Sensor Networks in Buildings VISION: Millions of self-powered sensor/transceivers, each the size of a speck of dust, will infiltrate a building and create a smart environment PROOF OF CONCEPT: To power a Mica 2 Dot Mote using vibrations from a wooden stairway in the Naval Architecture Building
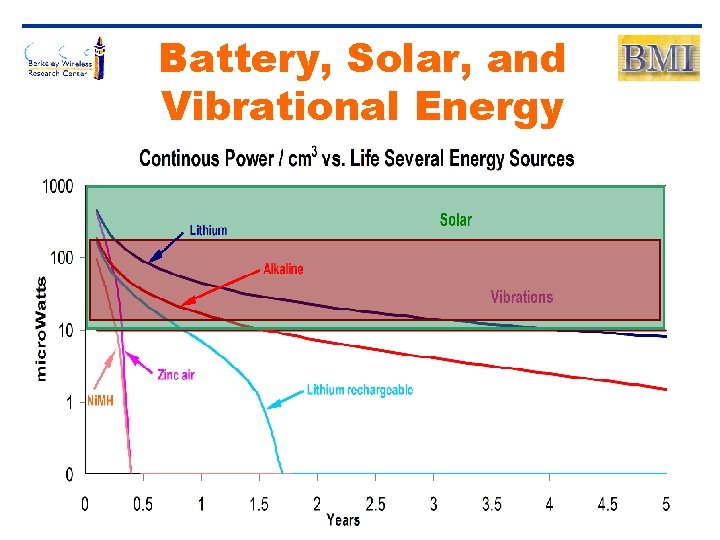
Battery, Solar, and Vibrational Energy
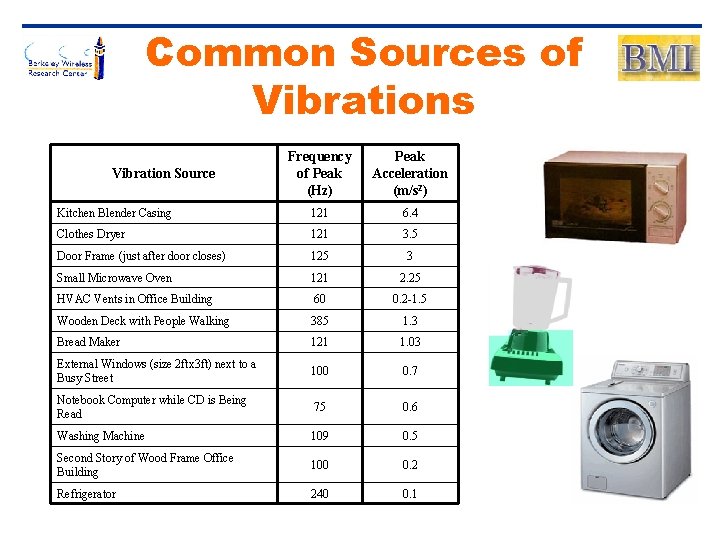
Common Sources of Vibrations Frequency of Peak (Hz) Peak Acceleration (m/s 2) Kitchen Blender Casing 121 6. 4 Clothes Dryer 121 3. 5 Door Frame (just after door closes) 125 3 Small Microwave Oven 121 2. 25 HVAC Vents in Office Building 60 0. 2 -1. 5 Wooden Deck with People Walking 385 1. 3 Bread Maker 121 1. 03 External Windows (size 2 ftx 3 ft) next to a Busy Street 100 0. 7 Notebook Computer while CD is Being Read 75 0. 6 Washing Machine 109 0. 5 Second Story of Wood Frame Office Building 100 0. 2 Refrigerator 240 0. 1 Vibration Source
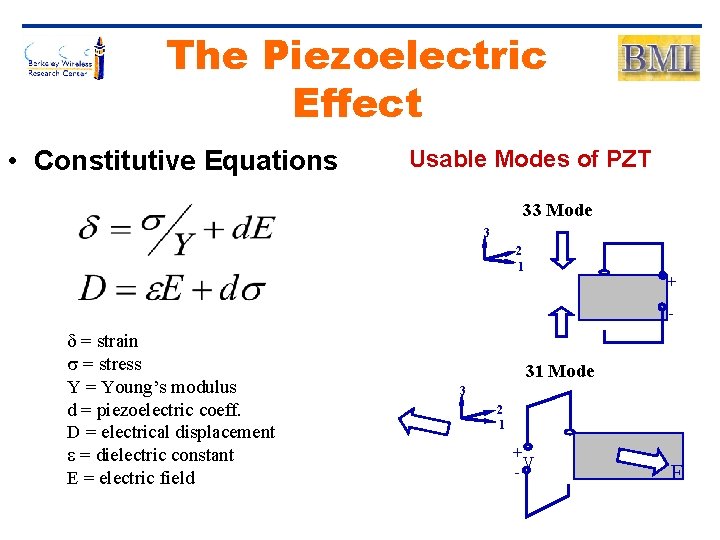
The Piezoelectric Effect • Constitutive Equations Usable Modes of PZT 33 Mode 3 2 1 d = strain s = stress Y = Young’s modulus d = piezoelectric coeff. D = electrical displacement e = dielectric constant E = electric field + V - 31 Mode 3 2 1 + V - F
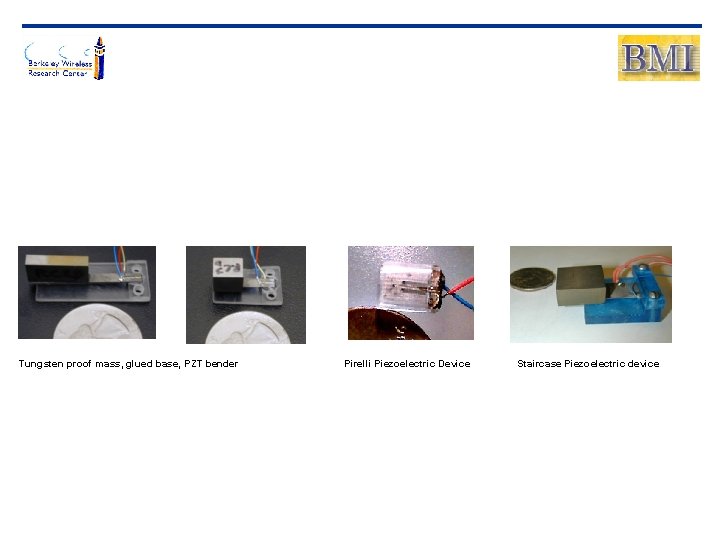
Tungsten proof mass, glued base, PZT bender Pirelli Piezoelectric Device Staircase Piezoelectric device
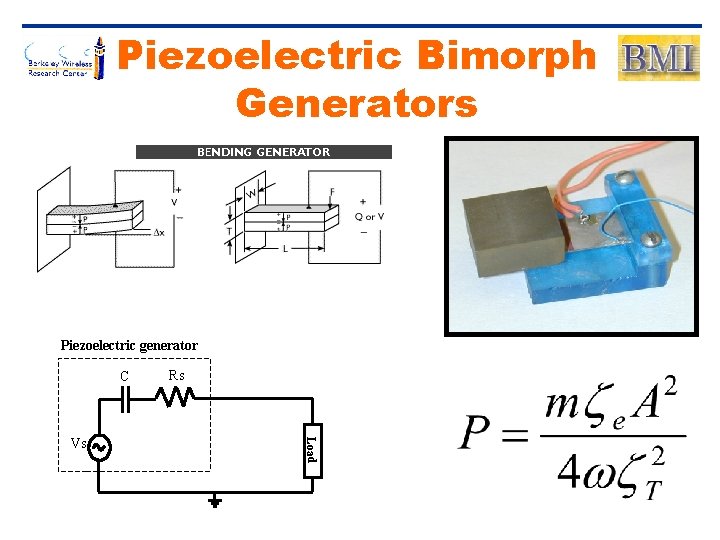
Piezoelectric Bimorph Generators Piezoelectric generator C Load Vs Rs
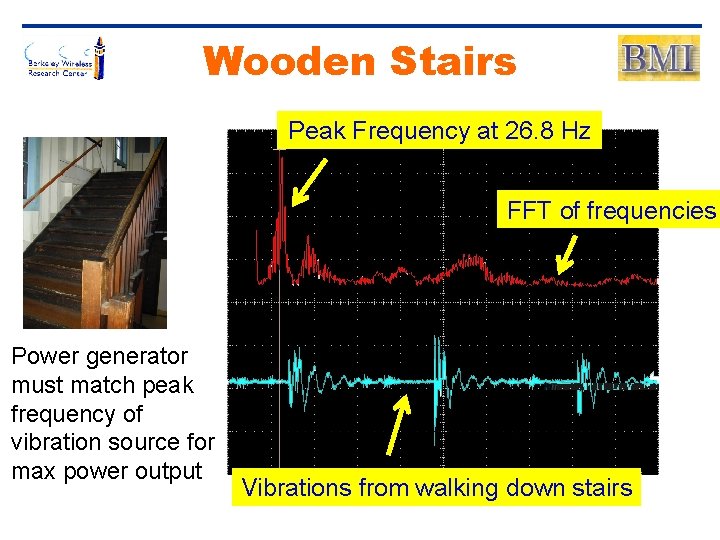
Wooden Stairs Peak Frequency at 26. 8 Hz FFT of frequencies Power generator must match peak frequency of vibration source for max power output Vibrations from walking down stairs
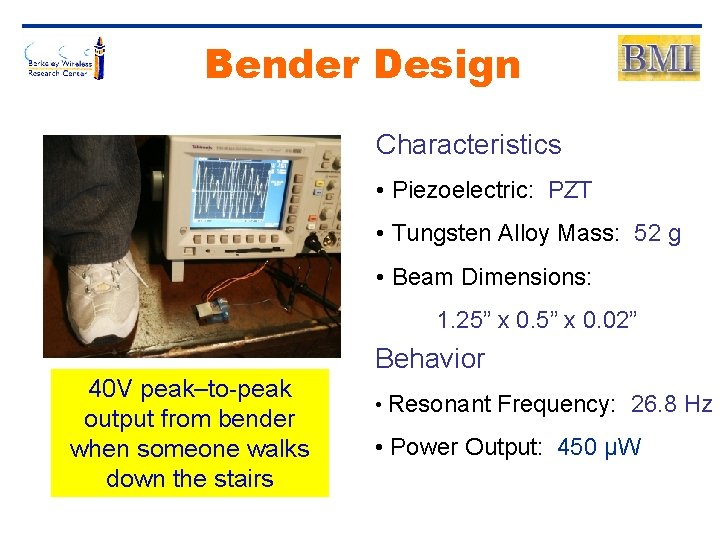
Bender Design Characteristics • Piezoelectric: PZT • Tungsten Alloy Mass: 52 g • Beam Dimensions: 1. 25” x 0. 02” Behavior 40 V peak–to-peak output from bender when someone walks down the stairs • Resonant Frequency: 26. 8 Hz • Power Output: 450 μW
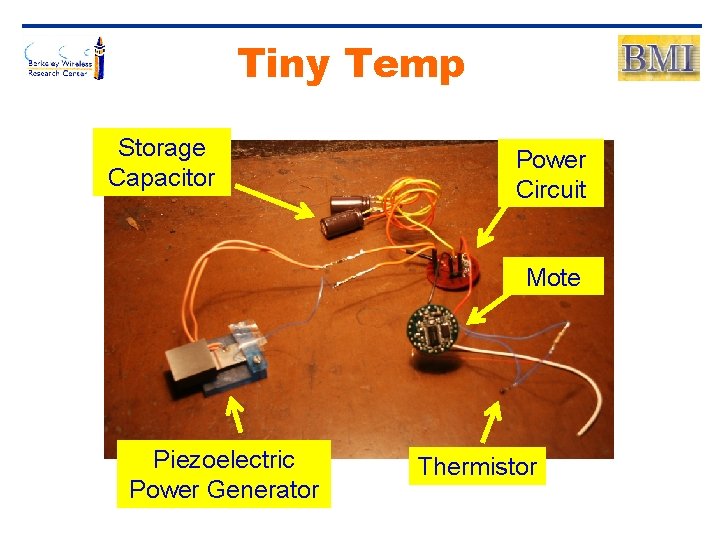
Tiny Temp Storage Capacitor Power Circuit Mote Piezoelectric Power Generator Thermistor
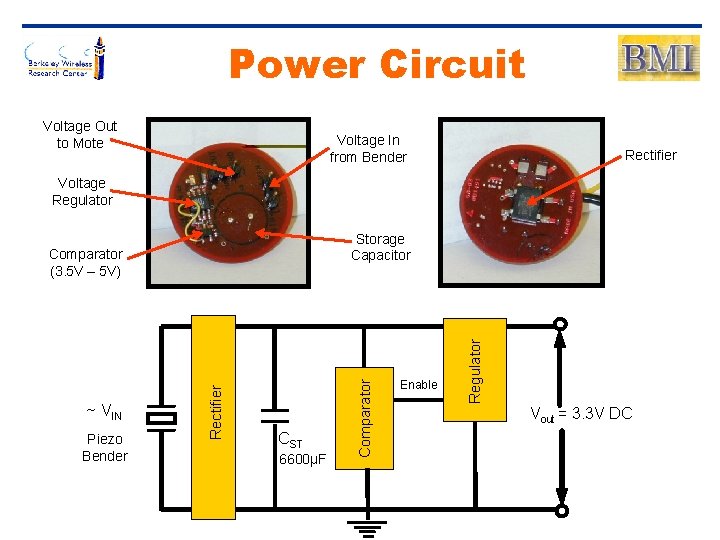
Power Circuit Voltage Out to Mote Voltage In from Bender Rectifier Voltage Regulator Piezo Bender CST 6600μF Enable Regulator ~ VIN Rectifier Comparator (3. 5 V – 5 V) Comparator Storage Capacitor Vout = 3. 3 V DC
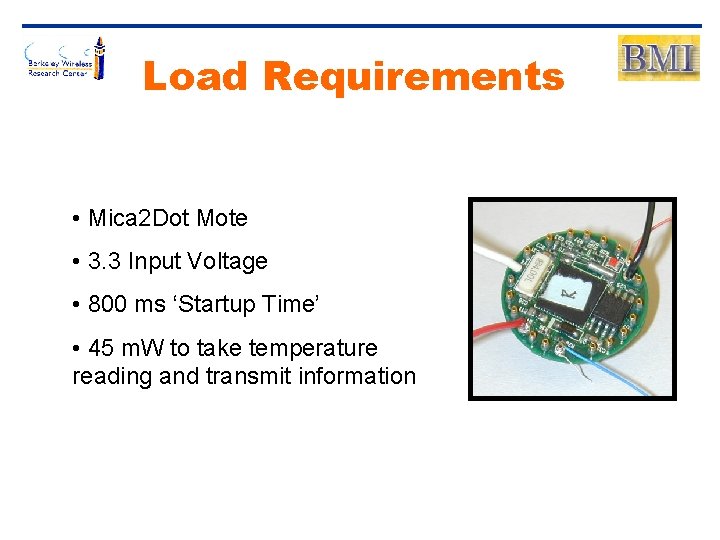
Load Requirements • Mica 2 Dot Mote • 3. 3 Input Voltage • 800 ms ‘Startup Time’ • 45 m. W to take temperature reading and transmit information
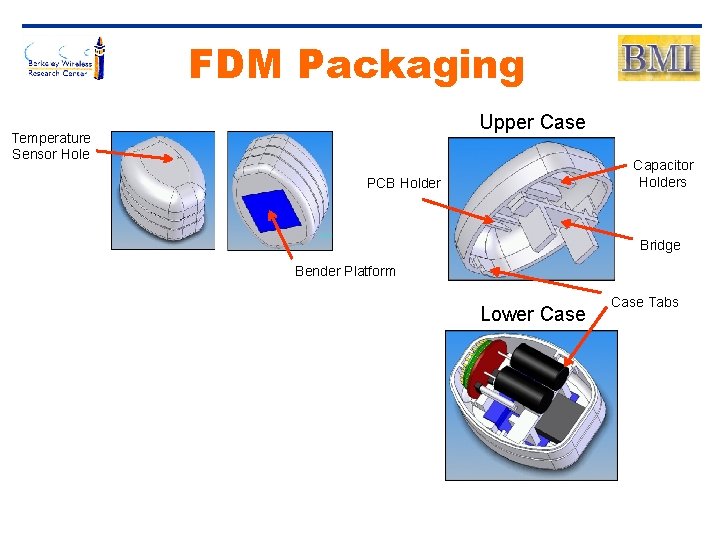
FDM Packaging Upper Case Temperature Sensor Hole Capacitor Holders PCB Holder Bridge Bender Platform Lower Case Tabs
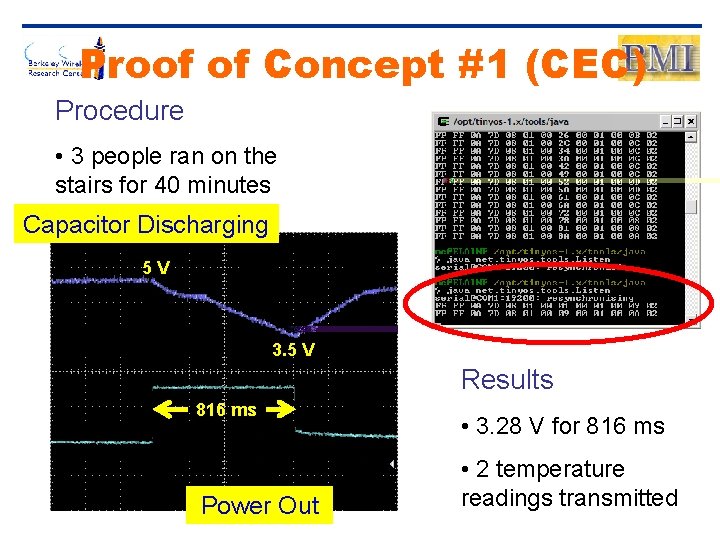
Proof of Concept #1 (CEC) Procedure • 3 people ran on the stairs for 40 minutes Capacitor Discharging 5 V 3. 5 V Results 816 ms Power Out • 3. 28 V for 816 ms • 2 temperature readings transmitted
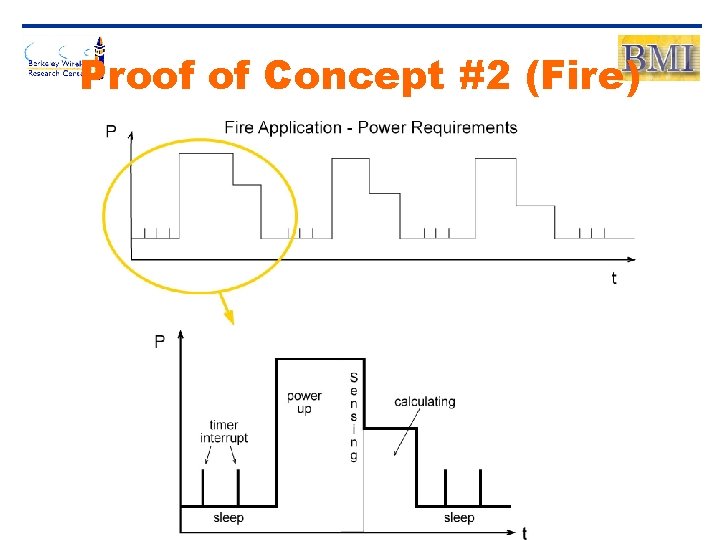
Proof of Concept #2 (Fire)
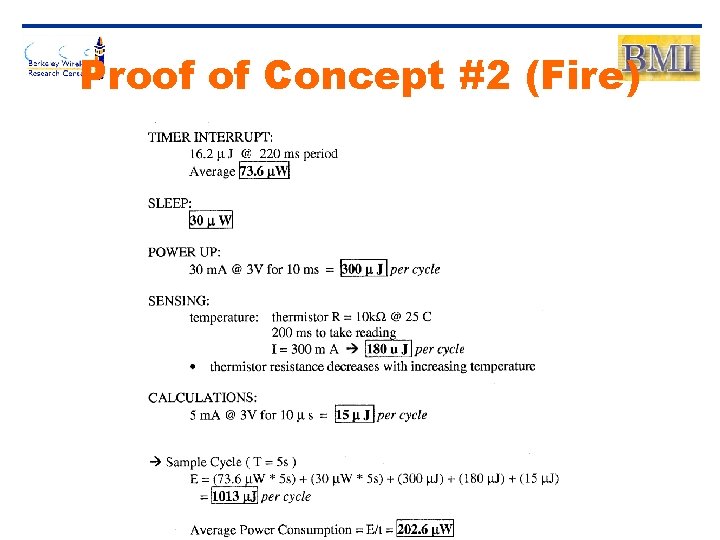
Proof of Concept #2 (Fire)
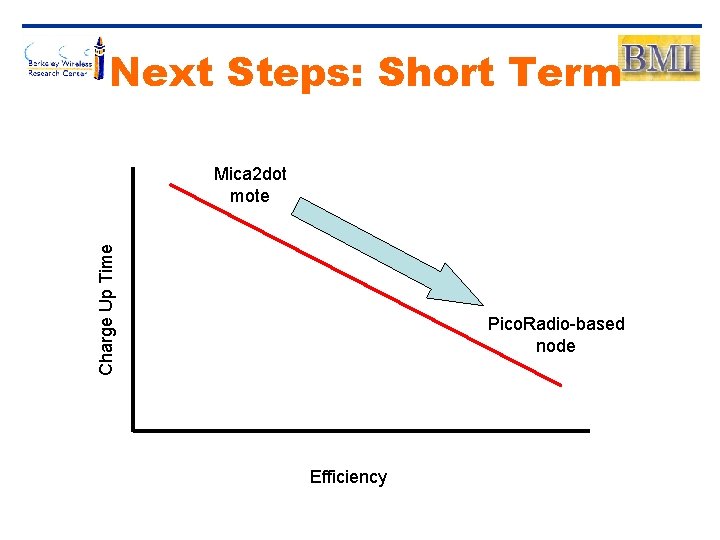
Next Steps: Short Term Charge Up Time Mica 2 dot mote Pico. Radio-based node Efficiency
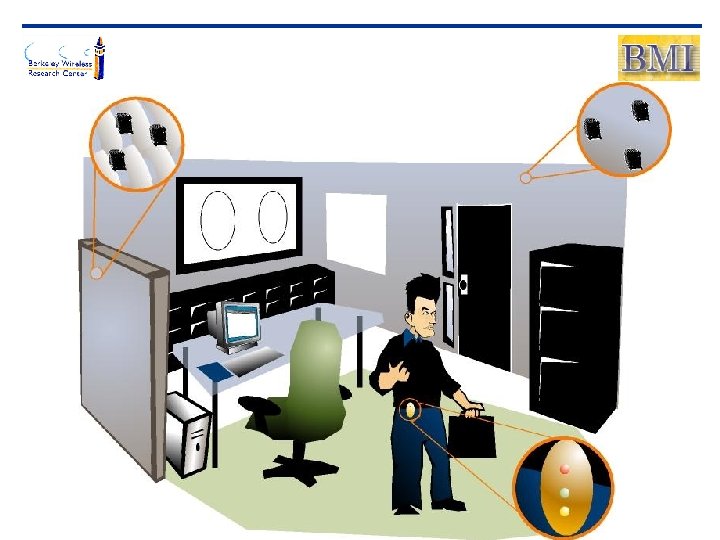
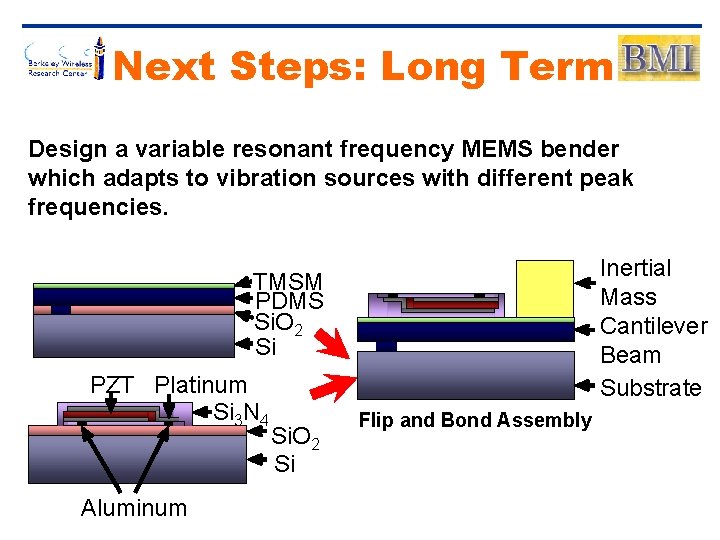
Next Steps: Long Term Design a variable resonant frequency MEMS bender which adapts to vibration sources with different peak frequencies. Inertial Mass Cantilever Beam Substrate TMSM PDMS Si. O 2 Si PZT Platinum Si 3 N 4 Aluminum Si. O 2 Si Flip and Bond Assembly
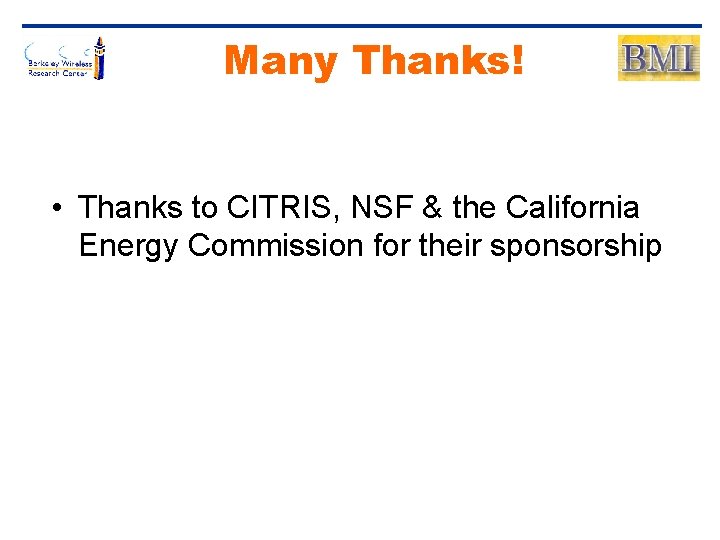
Many Thanks! • Thanks to CITRIS, NSF & the California Energy Commission for their sponsorship
Petri nets properties analysis and applications
Petri y gabriel
What are wireless devices and the wireless revolution
Wireless sensor network protocols
Single node architecture in wireless sensor networks
Habitat monitoring sensor
Wireless sensor network ppt
Forest geove
Sst wireless
Wireless sensor networks for habitat monitoring
Wireless lan solution
Nets and drawings for visualizing geometry
Nets and drawing for visualizing geometry
Semantic nets and frames
Nets and drawings for visualizing geometry
Net of a cube
Bayes nets
Represent solid figures using nets
Partitioned semantic network in artificial intelligence
Surface area using nets
Net triangular prism