Implementing Quality MGT420 Introduction q Motorolas Major Quality

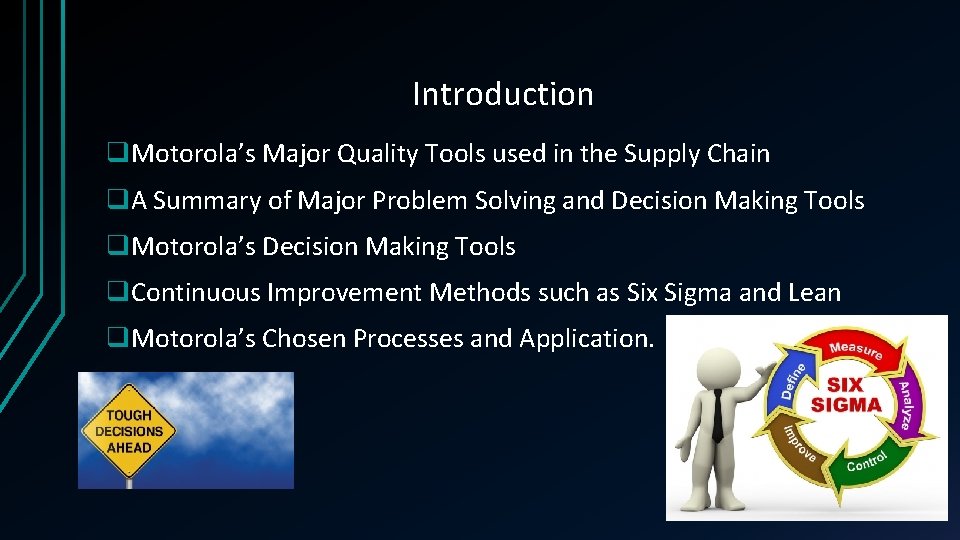
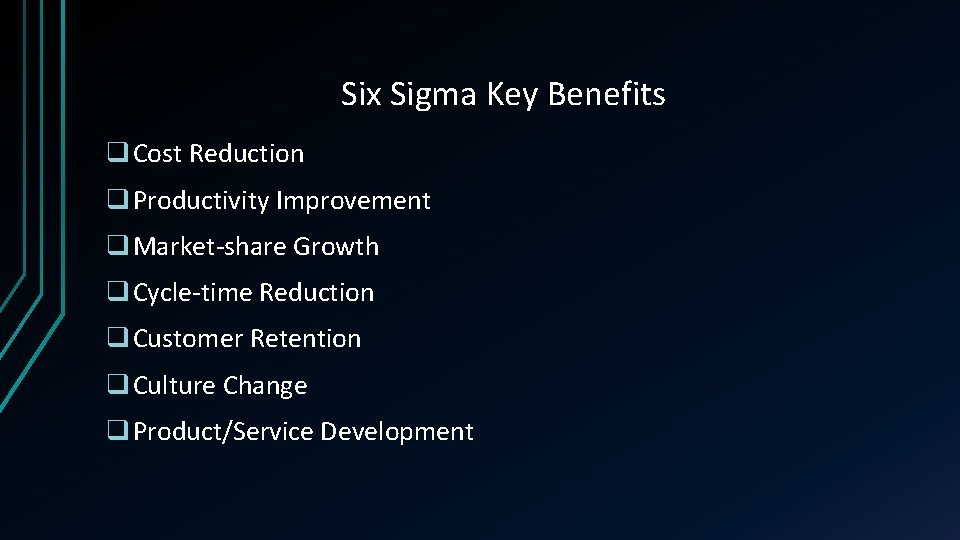
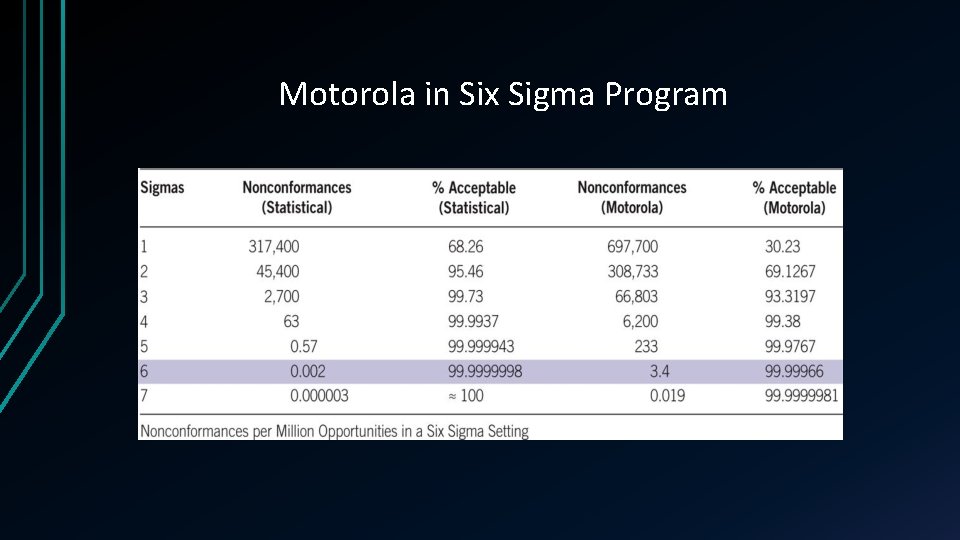
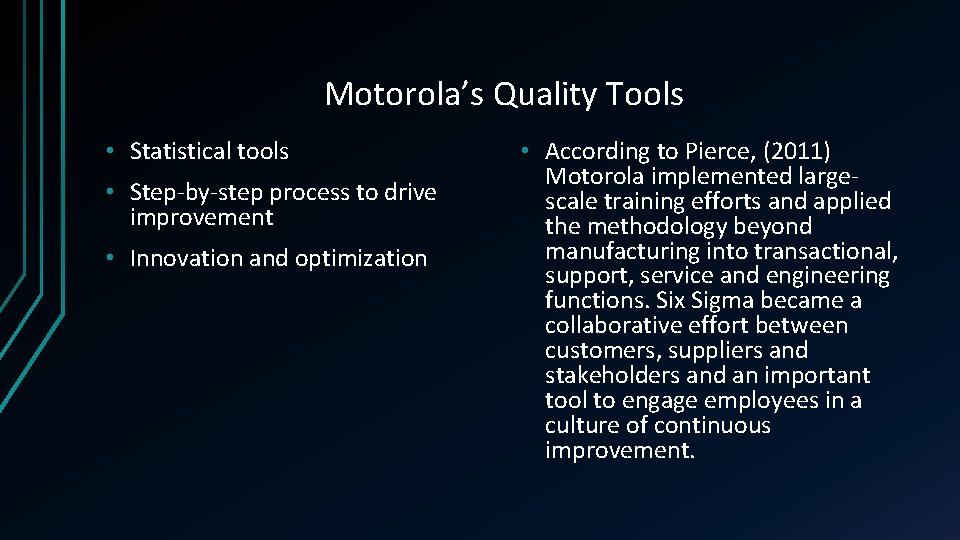

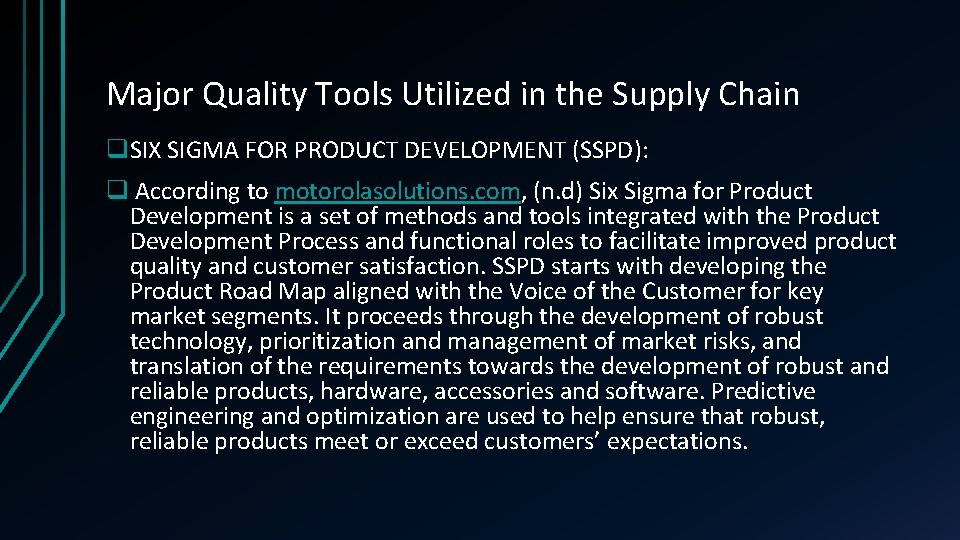
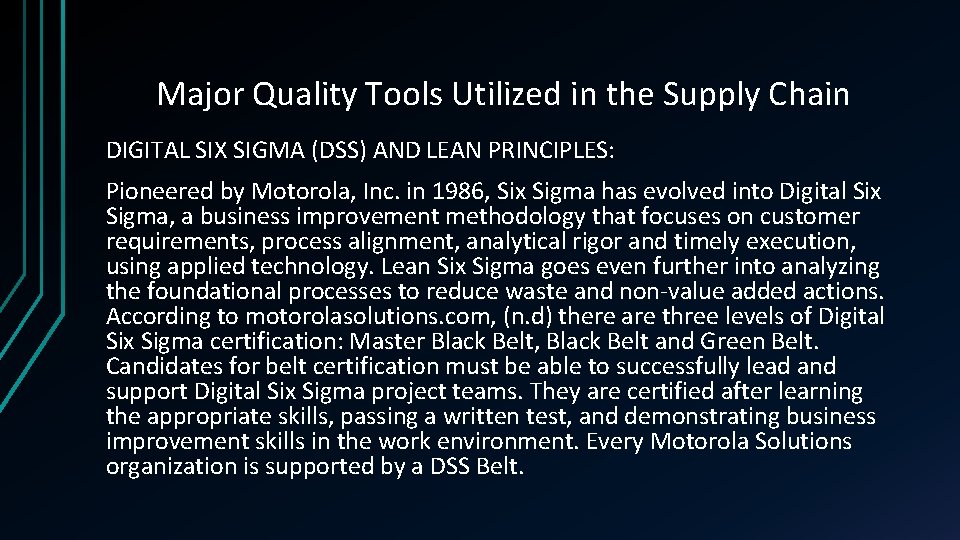
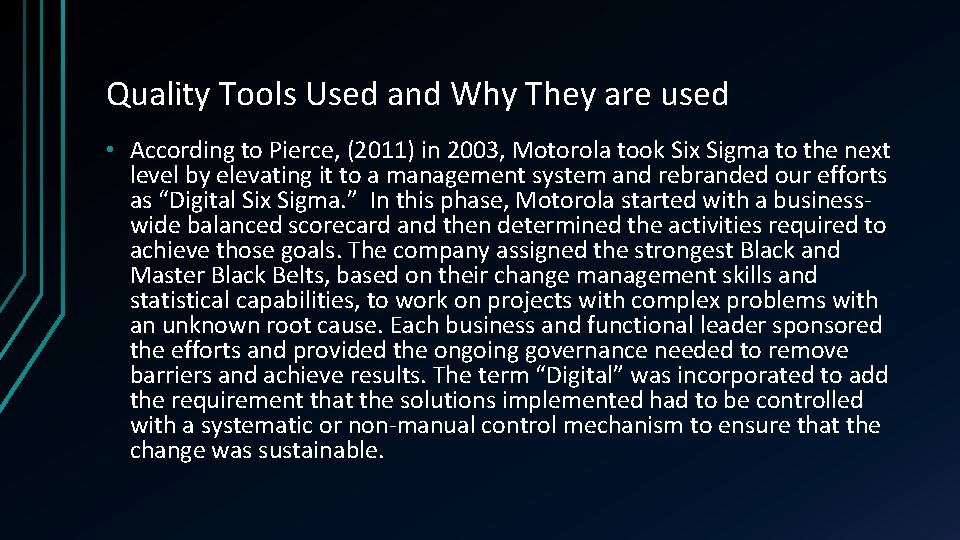
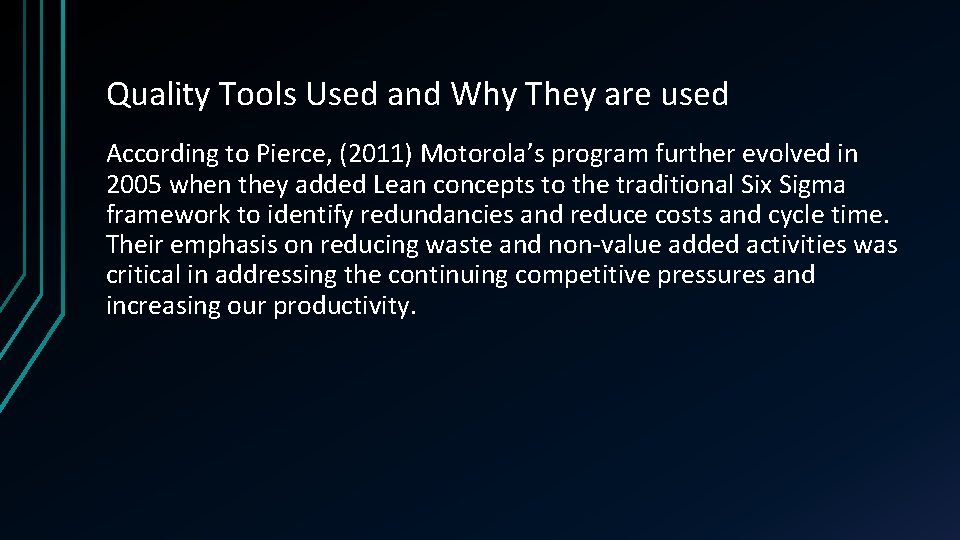
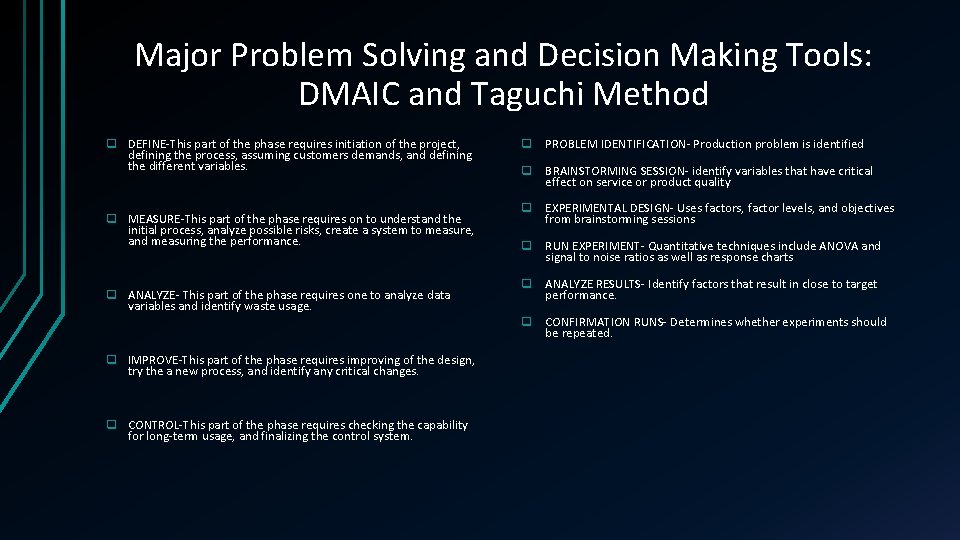

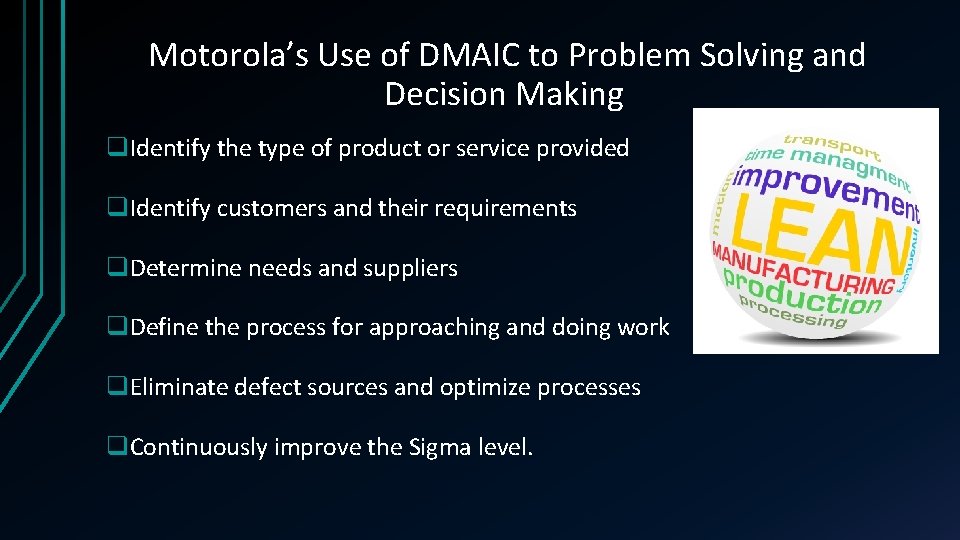
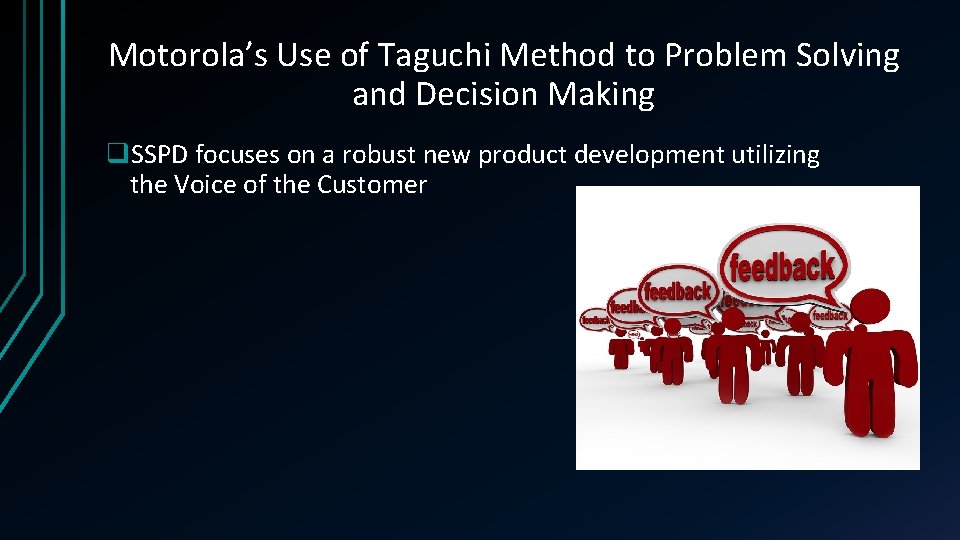
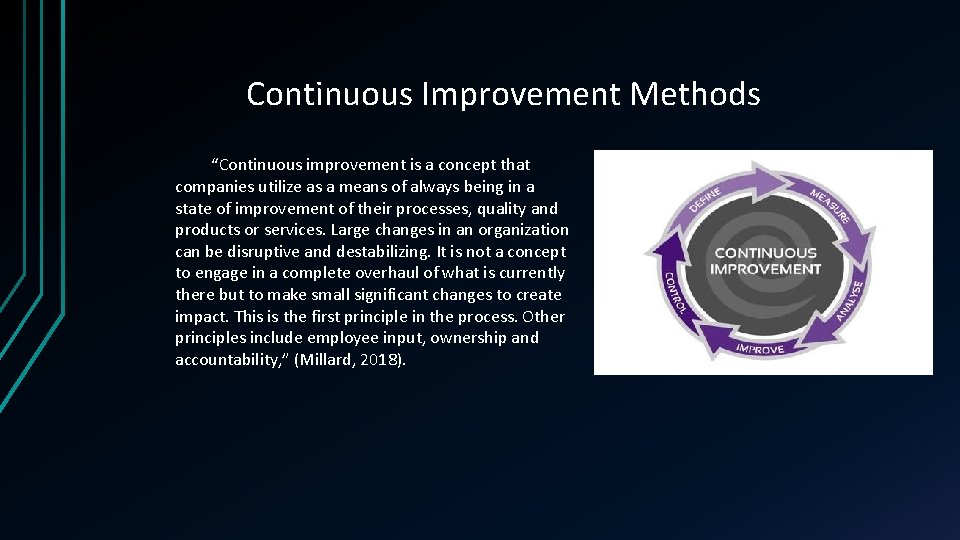
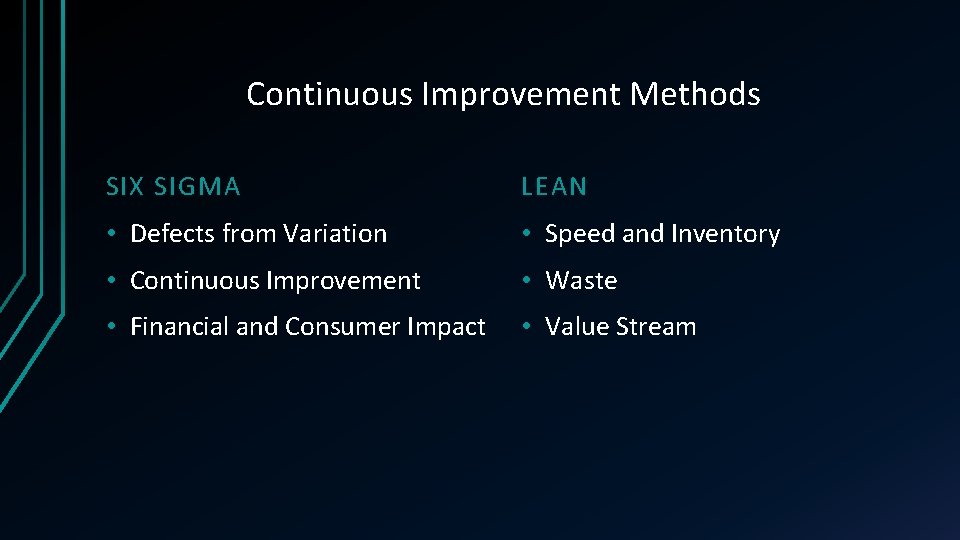
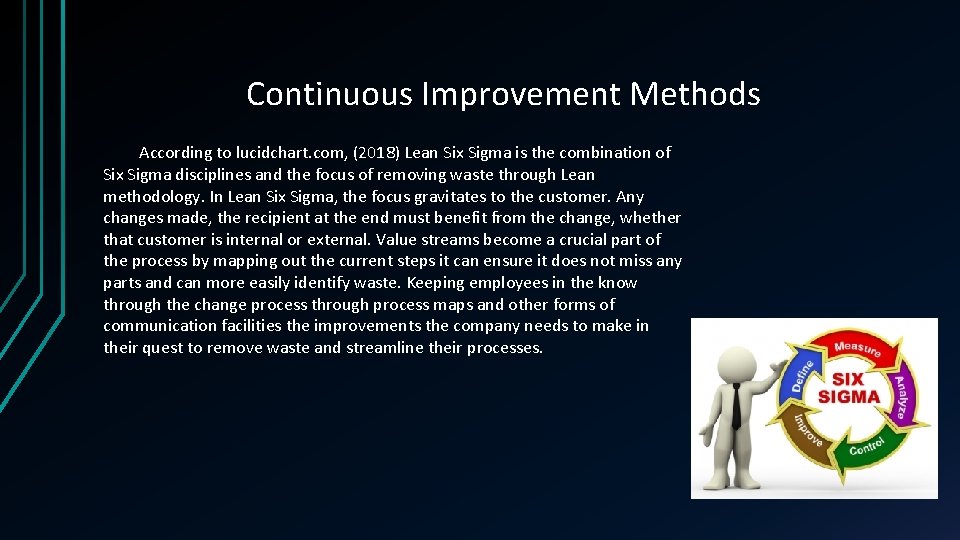
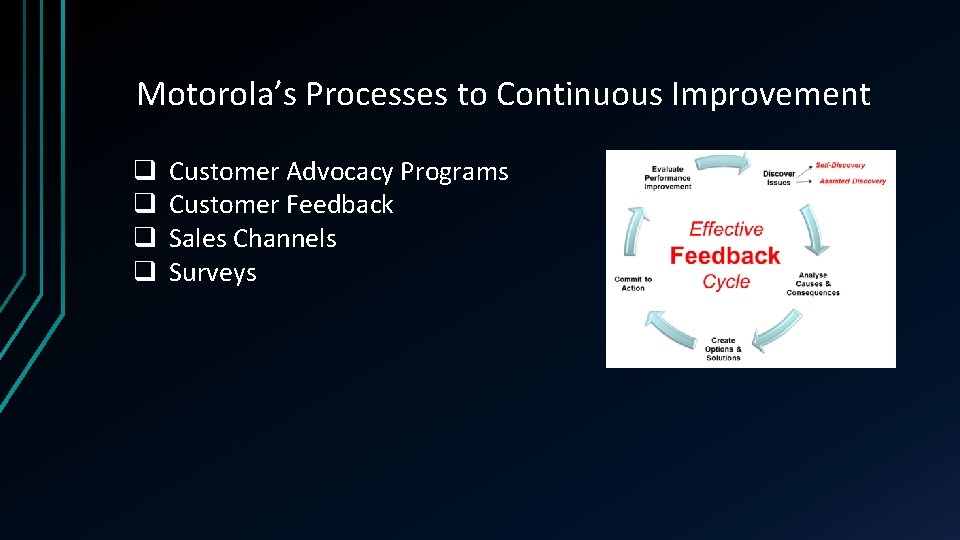
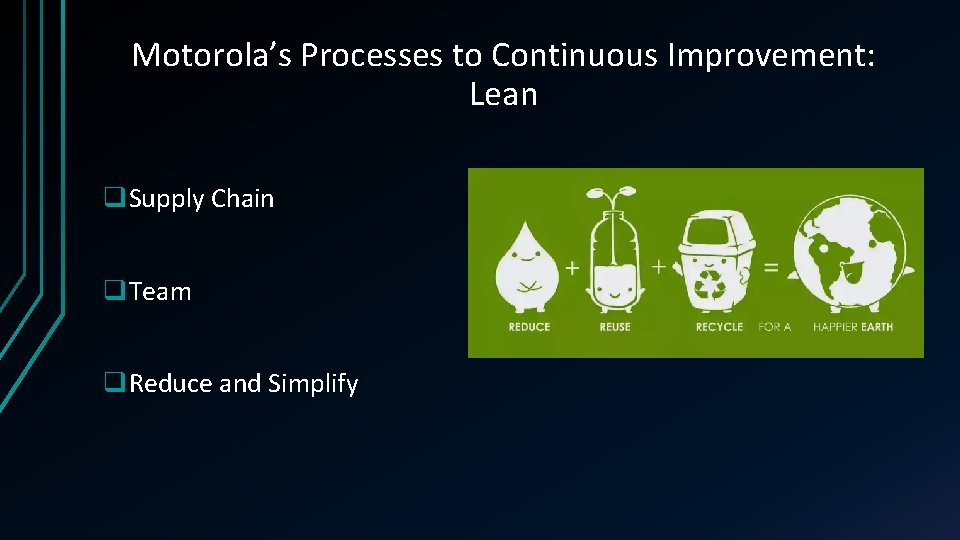
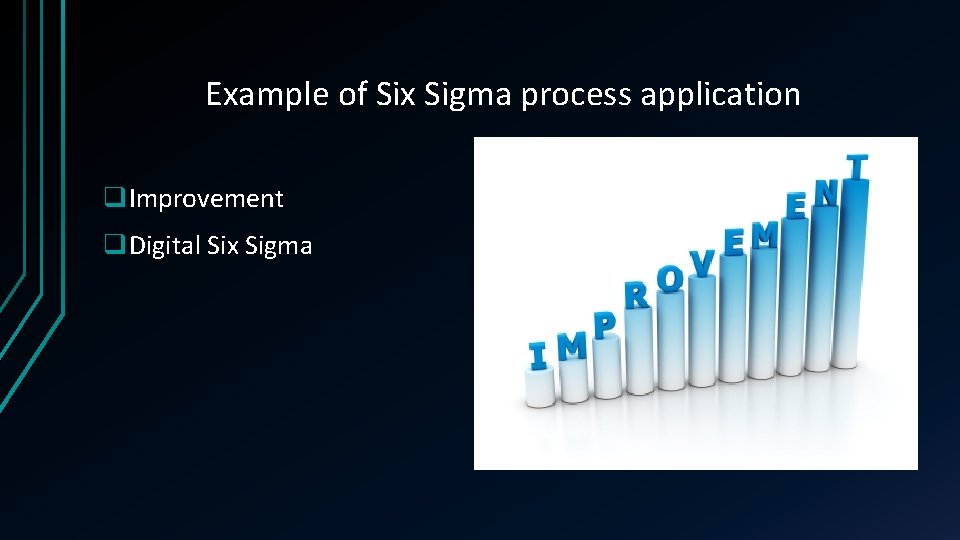
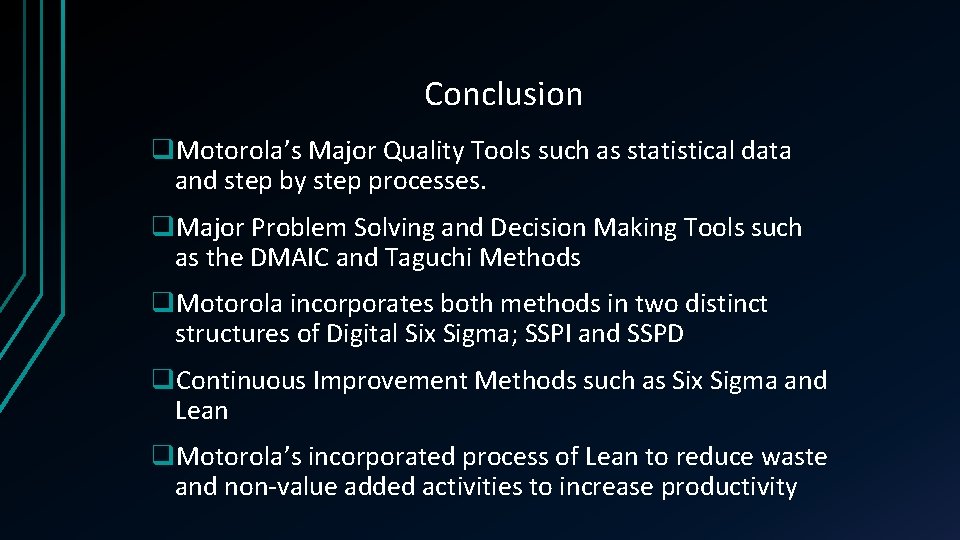
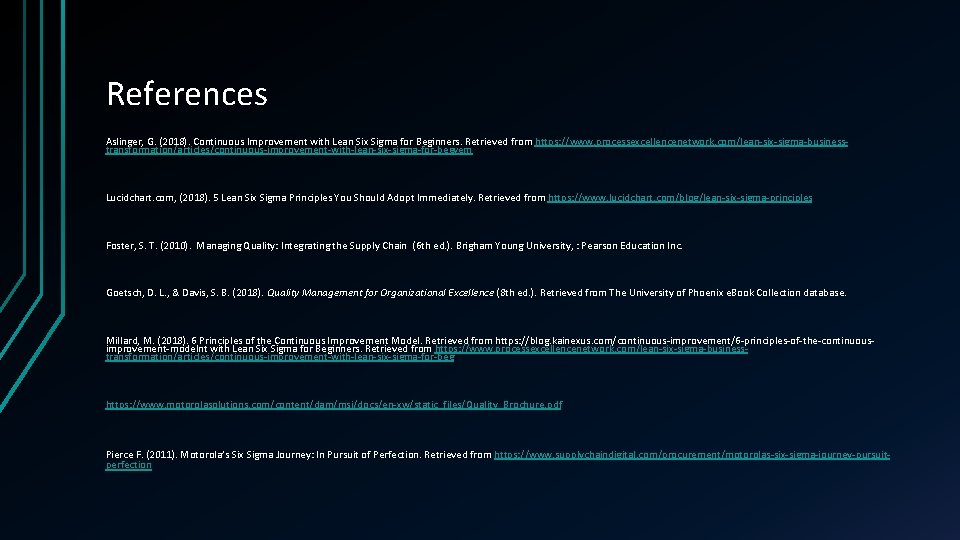
- Slides: 22

Implementing Quality MGT/420
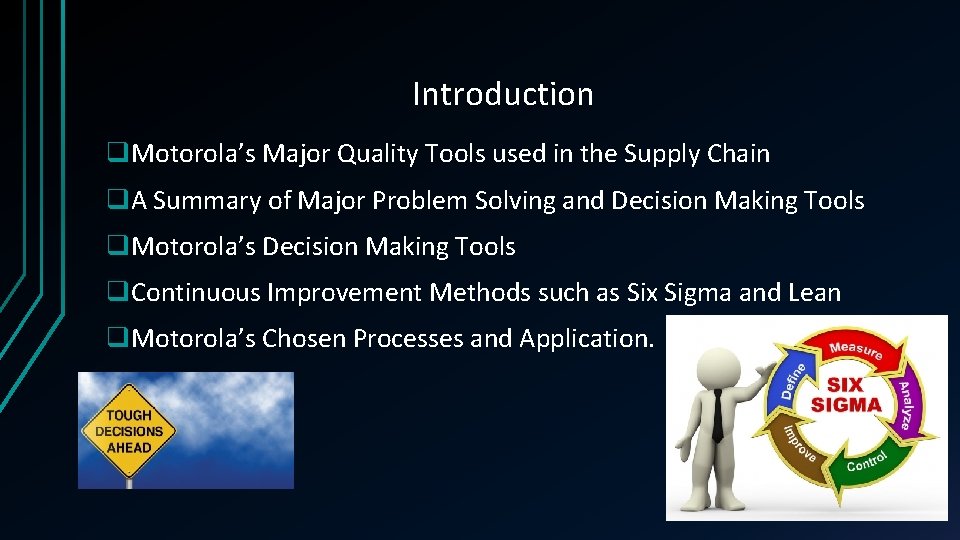
Introduction q. Motorola’s Major Quality Tools used in the Supply Chain q. A Summary of Major Problem Solving and Decision Making Tools q. Motorola’s Decision Making Tools q. Continuous Improvement Methods such as Six Sigma and Lean q. Motorola’s Chosen Processes and Application.
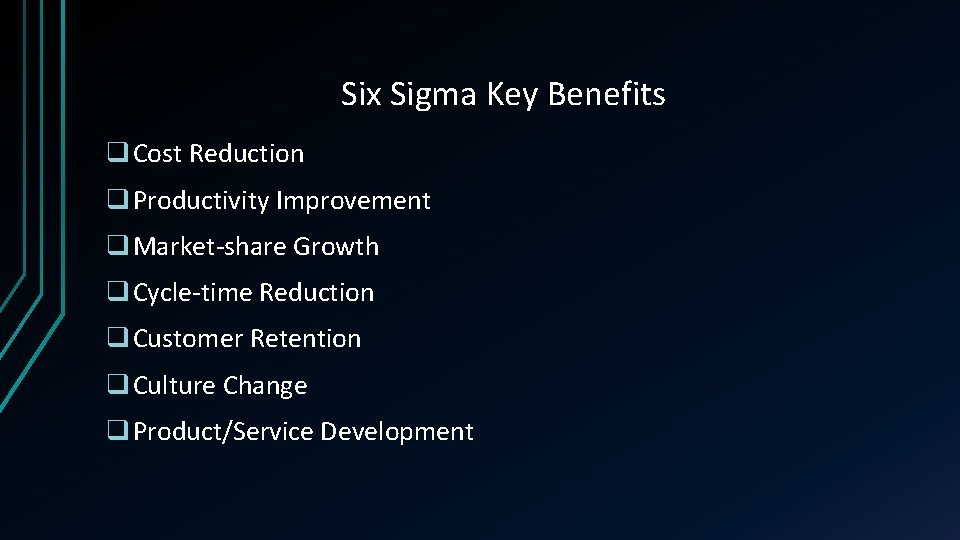
Six Sigma Key Benefits q Cost Reduction q Productivity Improvement q Market-share Growth q Cycle-time Reduction q Customer Retention q Culture Change q Product/Service Development
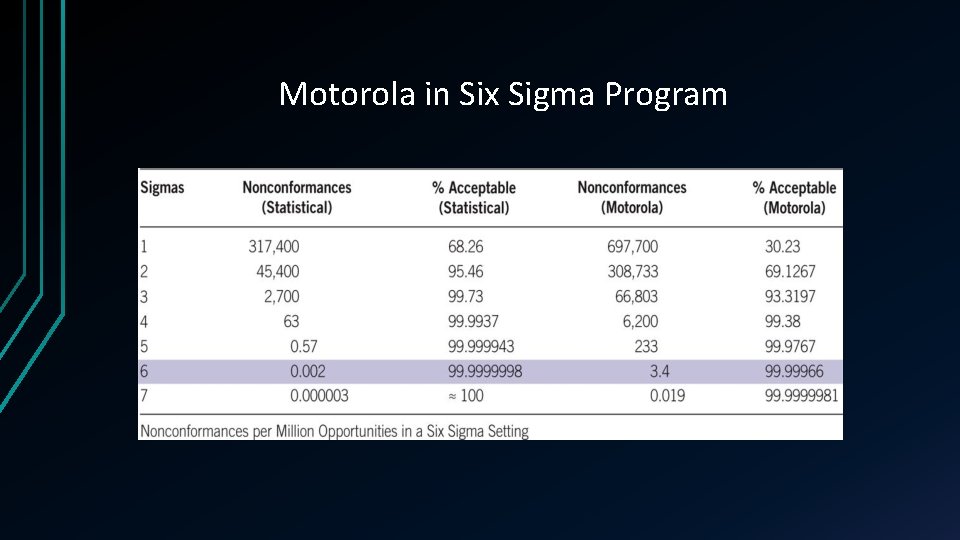
Motorola in Six Sigma Program
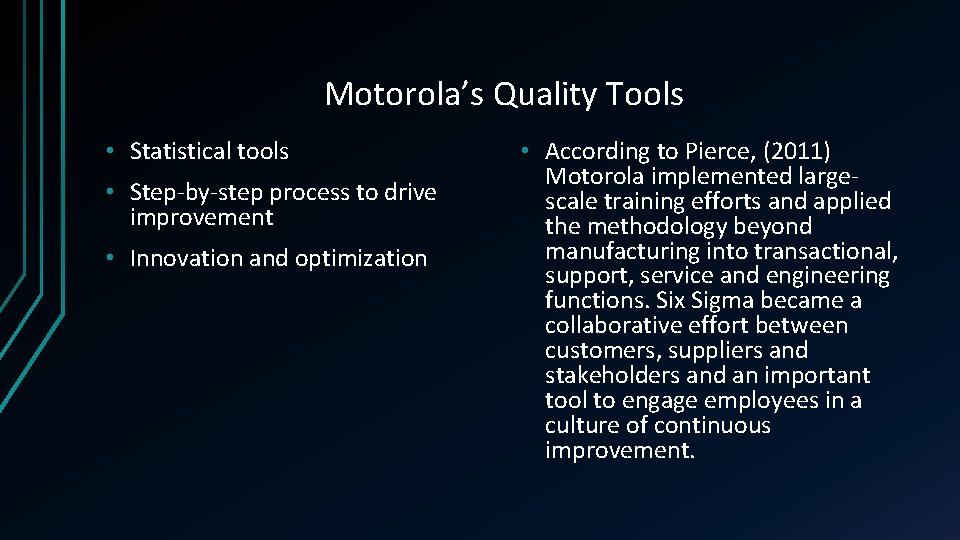
Motorola’s Quality Tools • Statistical tools • Step-by-step process to drive improvement • Innovation and optimization • According to Pierce, (2011) Motorola implemented largescale training efforts and applied the methodology beyond manufacturing into transactional, support, service and engineering functions. Six Sigma became a collaborative effort between customers, suppliers and stakeholders and an important tool to engage employees in a culture of continuous improvement.

Major Quality Tools Utilized in the Supply Chain q. SIX SIGMA FOR PROCESS IMPROVEMENT (SSPI): q. No matter where employees work—in Product Development, Manufacturing, Distribution, Finance, HR, Services, etc. —they use processes every day. To maximize value to customers and our business, every employee must focus on process improvement. Six Sigma for Process Improvement is Motorola’s proven way of systematically removing waste and variation in processes by effectively applying Lean Six Sigma principles, methodologies, and tools.
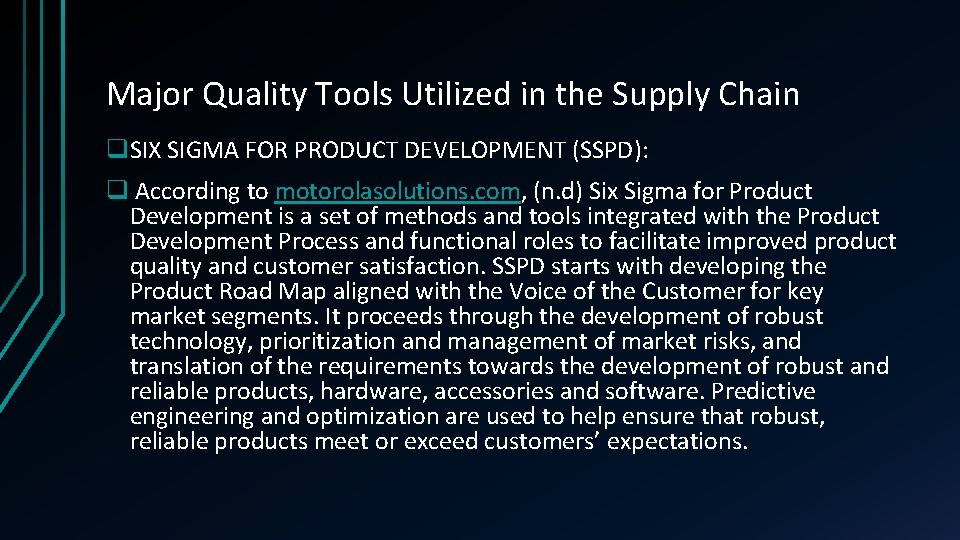
Major Quality Tools Utilized in the Supply Chain q. SIX SIGMA FOR PRODUCT DEVELOPMENT (SSPD): q According to motorolasolutions. com, (n. d) Six Sigma for Product Development is a set of methods and tools integrated with the Product Development Process and functional roles to facilitate improved product quality and customer satisfaction. SSPD starts with developing the Product Road Map aligned with the Voice of the Customer for key market segments. It proceeds through the development of robust technology, prioritization and management of market risks, and translation of the requirements towards the development of robust and reliable products, hardware, accessories and software. Predictive engineering and optimization are used to help ensure that robust, reliable products meet or exceed customers’ expectations.
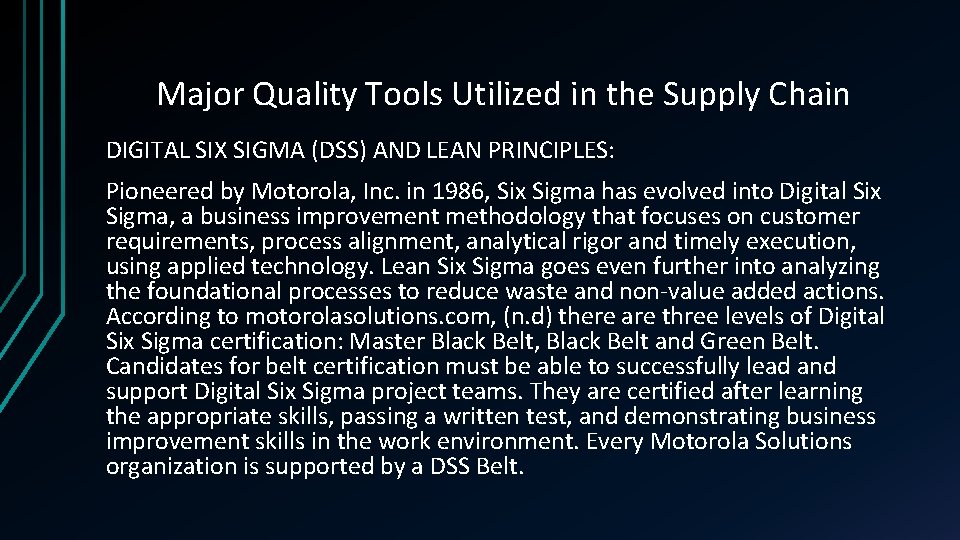
Major Quality Tools Utilized in the Supply Chain DIGITAL SIX SIGMA (DSS) AND LEAN PRINCIPLES: Pioneered by Motorola, Inc. in 1986, Six Sigma has evolved into Digital Six Sigma, a business improvement methodology that focuses on customer requirements, process alignment, analytical rigor and timely execution, using applied technology. Lean Six Sigma goes even further into analyzing the foundational processes to reduce waste and non-value added actions. According to motorolasolutions. com, (n. d) there are three levels of Digital Six Sigma certification: Master Black Belt, Black Belt and Green Belt. Candidates for belt certification must be able to successfully lead and support Digital Six Sigma project teams. They are certified after learning the appropriate skills, passing a written test, and demonstrating business improvement skills in the work environment. Every Motorola Solutions organization is supported by a DSS Belt.
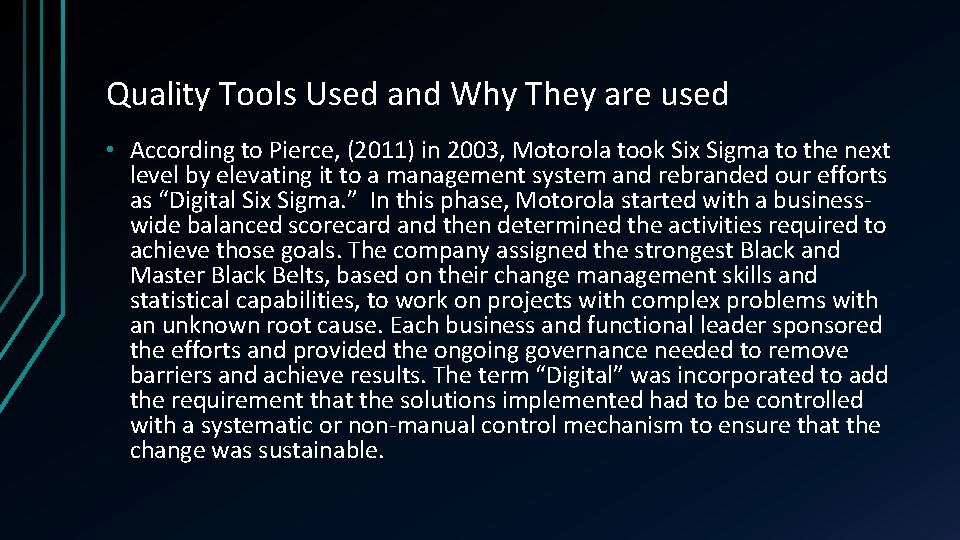
Quality Tools Used and Why They are used • According to Pierce, (2011) in 2003, Motorola took Six Sigma to the next level by elevating it to a management system and rebranded our efforts as “Digital Six Sigma. ” In this phase, Motorola started with a businesswide balanced scorecard and then determined the activities required to achieve those goals. The company assigned the strongest Black and Master Black Belts, based on their change management skills and statistical capabilities, to work on projects with complex problems with an unknown root cause. Each business and functional leader sponsored the efforts and provided the ongoing governance needed to remove barriers and achieve results. The term “Digital” was incorporated to add the requirement that the solutions implemented had to be controlled with a systematic or non-manual control mechanism to ensure that the change was sustainable.
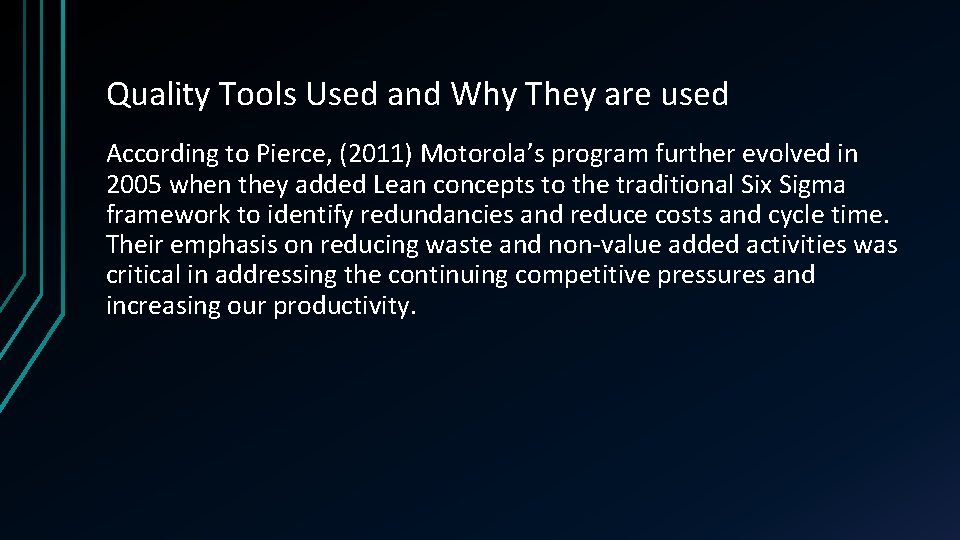
Quality Tools Used and Why They are used According to Pierce, (2011) Motorola’s program further evolved in 2005 when they added Lean concepts to the traditional Six Sigma framework to identify redundancies and reduce costs and cycle time. Their emphasis on reducing waste and non-value added activities was critical in addressing the continuing competitive pressures and increasing our productivity.
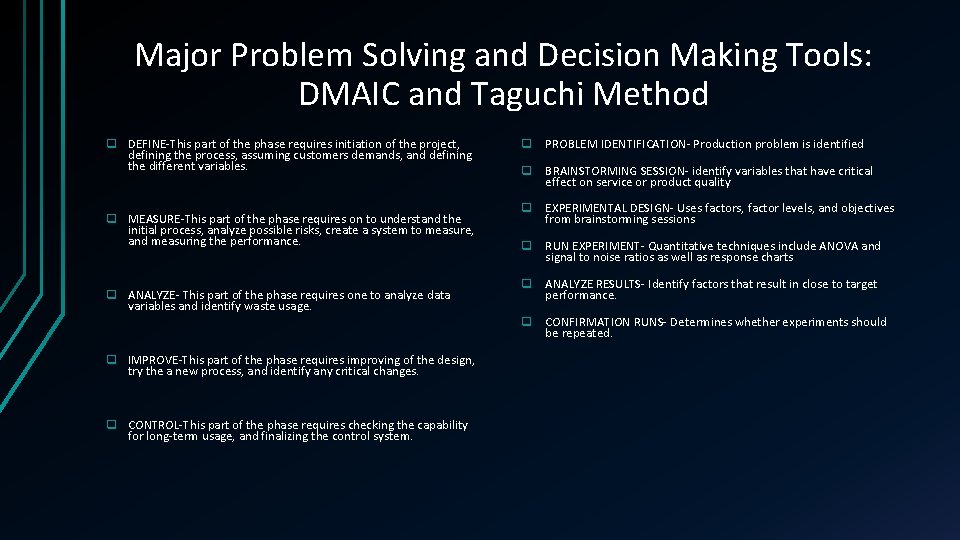
Major Problem Solving and Decision Making Tools: DMAIC and Taguchi Method q DEFINE-This part of the phase requires initiation of the project, defining the process, assuming customers demands, and defining the different variables. q MEASURE-This part of the phase requires on to understand the initial process, analyze possible risks, create a system to measure, and measuring the performance. q ANALYZE- This part of the phase requires one to analyze data variables and identify waste usage. q PROBLEM IDENTIFICATION- Production problem is identified q BRAINSTORMING SESSION- identify variables that have critical effect on service or product quality q EXPERIMENTAL DESIGN- Uses factors, factor levels, and objectives from brainstorming sessions q RUN EXPERIMENT- Quantitative techniques include ANOVA and signal to noise ratios as well as response charts q ANALYZE RESULTS- Identify factors that result in close to target performance. q CONFIRMATION RUNS- Determines whether experiments should be repeated. q IMPROVE-This part of the phase requires improving of the design, try the a new process, and identify any critical changes. q CONTROL-This part of the phase requires checking the capability for long-term usage, and finalizing the control system.

Major Problem Solving and Decision Making Tools qincludes Pareto Analysis and Project Evaluation q. Measurement tools such as Process map, XY matrix, FMEA, Gauge R&R and Capability Assessments q. Taguchi Method: A foundation for determining the relationship between controlled product or service design factors and their outcomes. This process optimizes controlled variables. A procedure for examining the relationship between random noise in product or variability.
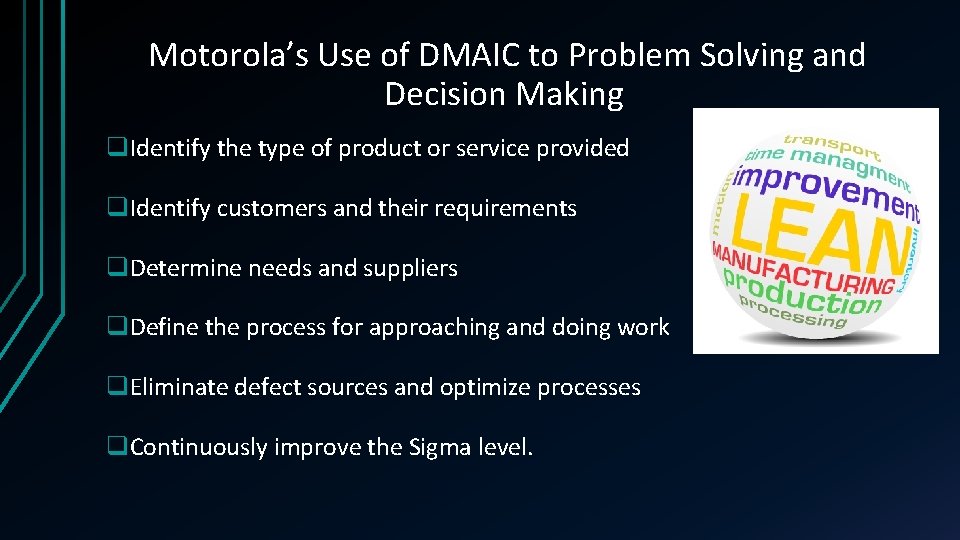
Motorola’s Use of DMAIC to Problem Solving and Decision Making q. Identify the type of product or service provided q. Identify customers and their requirements q. Determine needs and suppliers q. Define the process for approaching and doing work q. Eliminate defect sources and optimize processes q. Continuously improve the Sigma level.
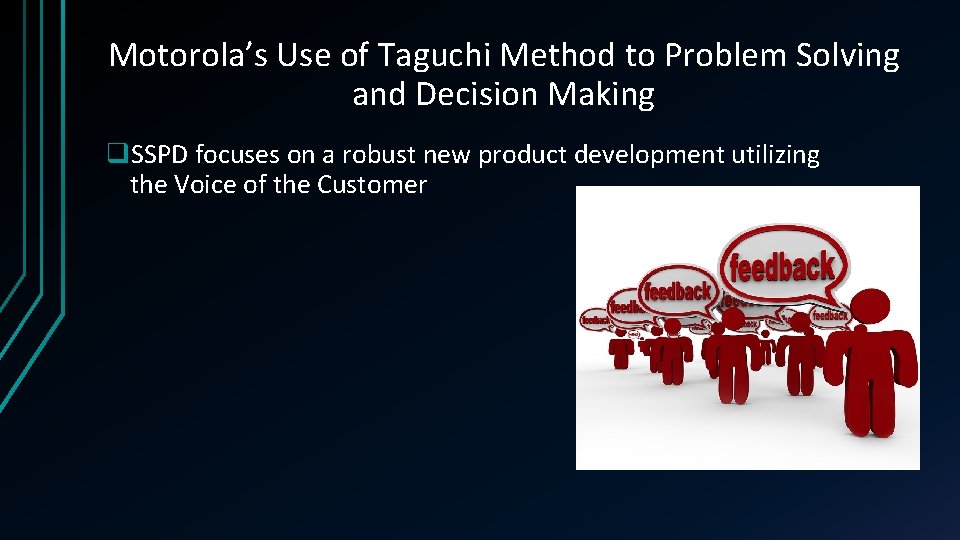
Motorola’s Use of Taguchi Method to Problem Solving and Decision Making q. SSPD focuses on a robust new product development utilizing the Voice of the Customer
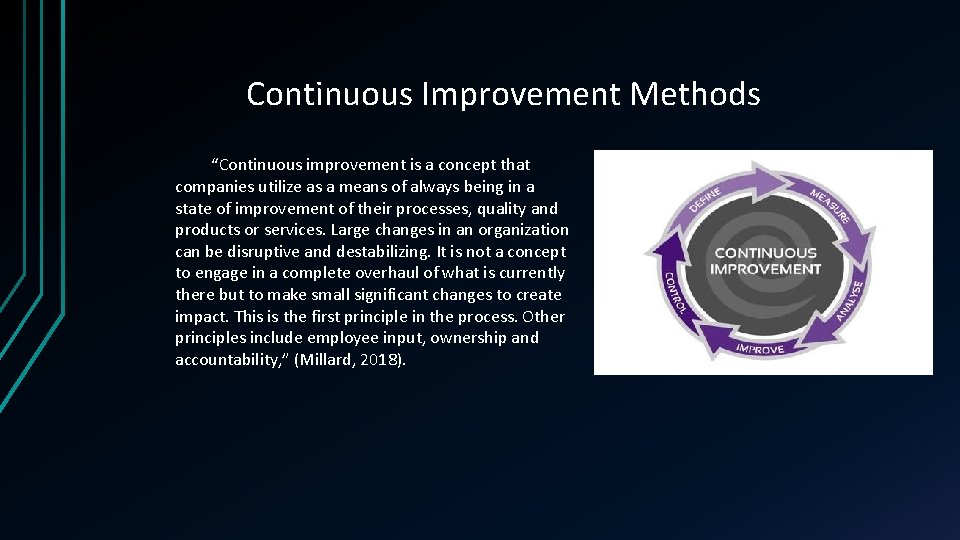
Continuous Improvement Methods “Continuous improvement is a concept that companies utilize as a means of always being in a state of improvement of their processes, quality and products or services. Large changes in an organization can be disruptive and destabilizing. It is not a concept to engage in a complete overhaul of what is currently there but to make small significant changes to create impact. This is the first principle in the process. Other principles include employee input, ownership and accountability, ” (Millard, 2018).
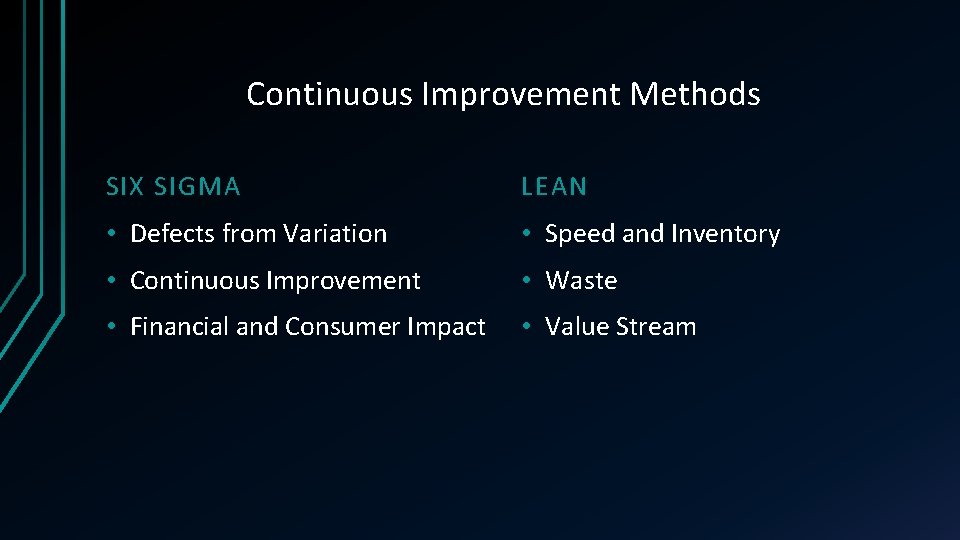
Continuous Improvement Methods SIX SIGMA LEAN • Defects from Variation • Speed and Inventory • Continuous Improvement • Waste • Financial and Consumer Impact • Value Stream
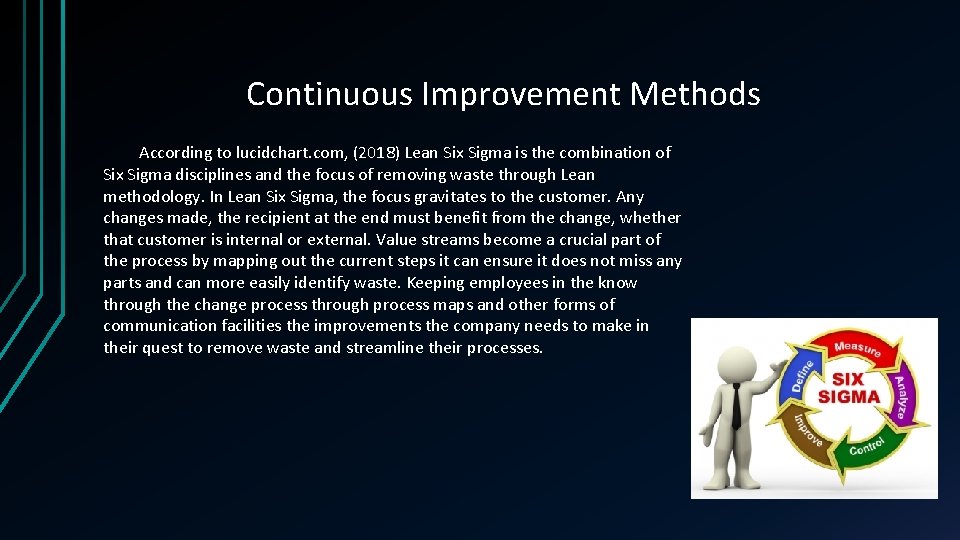
Continuous Improvement Methods According to lucidchart. com, (2018) Lean Six Sigma is the combination of Six Sigma disciplines and the focus of removing waste through Lean methodology. In Lean Six Sigma, the focus gravitates to the customer. Any changes made, the recipient at the end must benefit from the change, whether that customer is internal or external. Value streams become a crucial part of the process by mapping out the current steps it can ensure it does not miss any parts and can more easily identify waste. Keeping employees in the know through the change process through process maps and other forms of communication facilities the improvements the company needs to make in their quest to remove waste and streamline their processes.
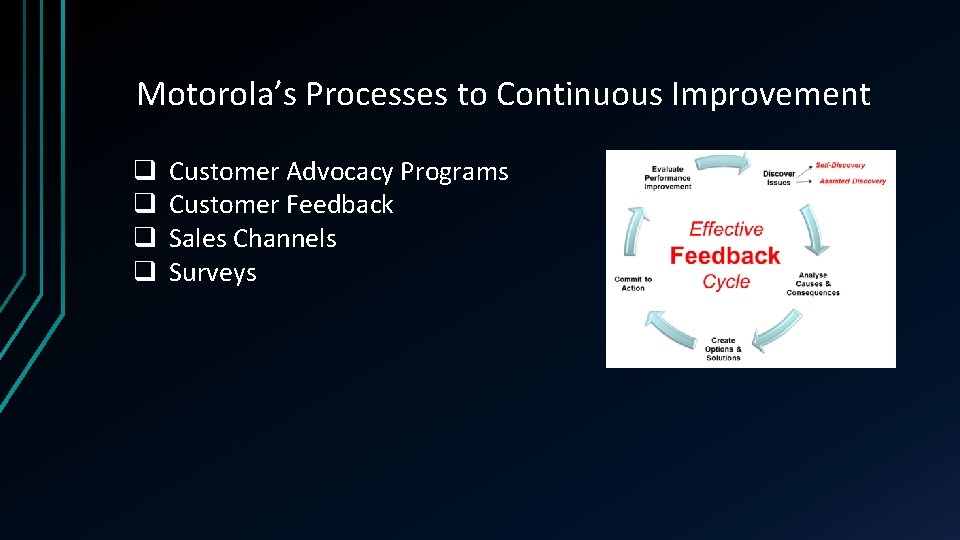
Motorola’s Processes to Continuous Improvement q q Customer Advocacy Programs Customer Feedback Sales Channels Surveys
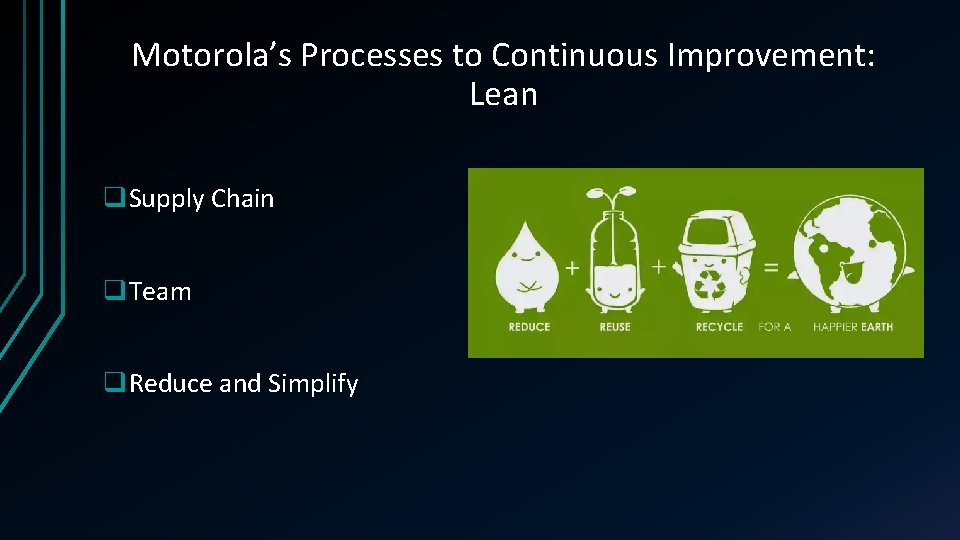
Motorola’s Processes to Continuous Improvement: Lean q. Supply Chain q. Team q. Reduce and Simplify
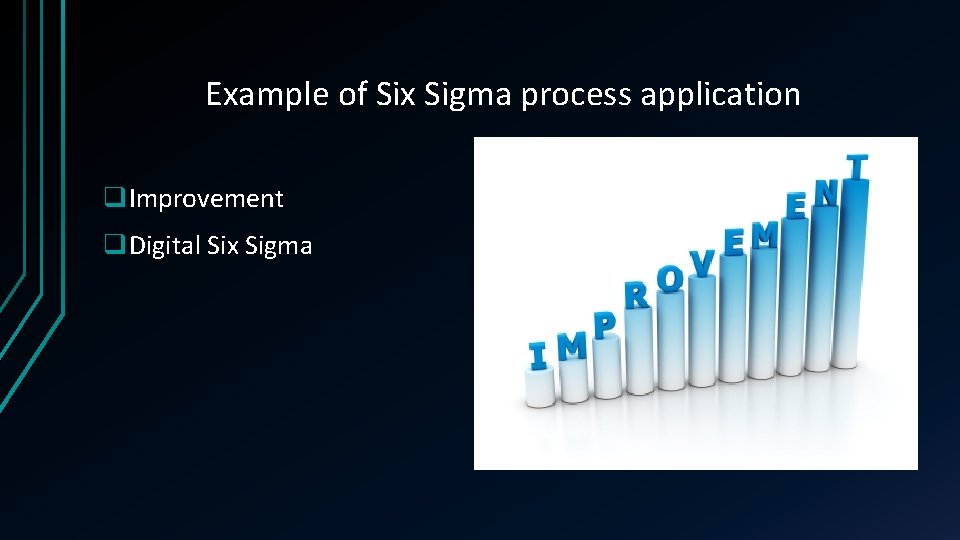
Example of Six Sigma process application q. Improvement q. Digital Six Sigma
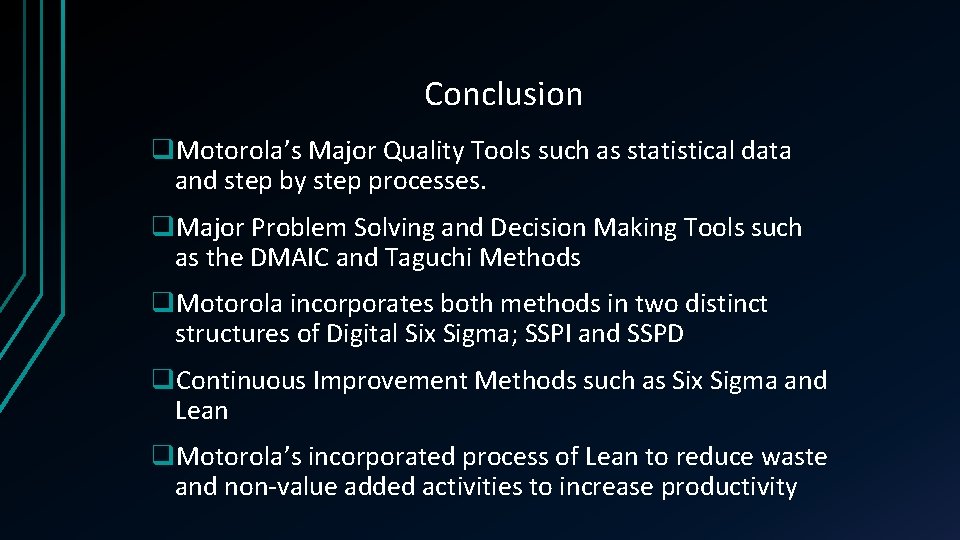
Conclusion q. Motorola’s Major Quality Tools such as statistical data and step by step processes. q. Major Problem Solving and Decision Making Tools such as the DMAIC and Taguchi Methods q. Motorola incorporates both methods in two distinct structures of Digital Six Sigma; SSPI and SSPD q. Continuous Improvement Methods such as Six Sigma and Lean q. Motorola’s incorporated process of Lean to reduce waste and non-value added activities to increase productivity
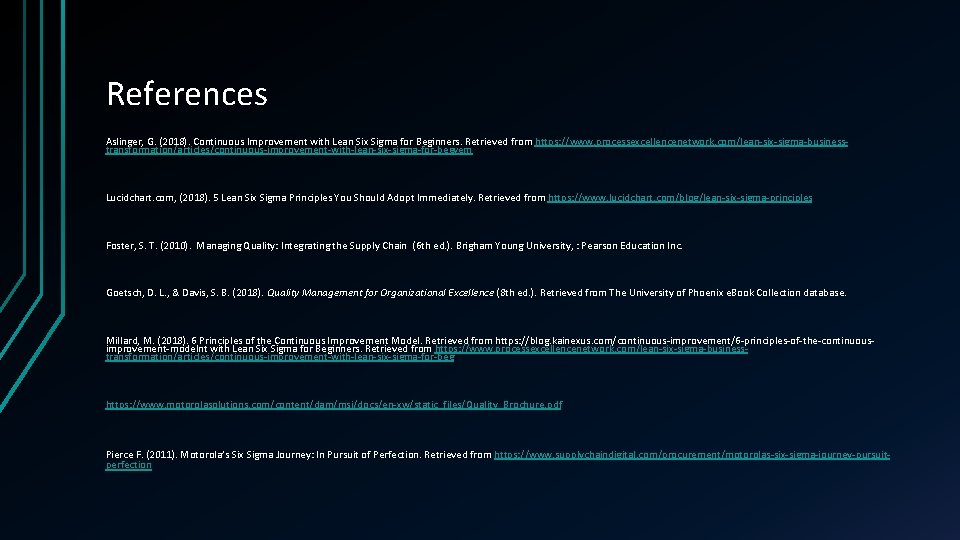
References Aslinger, G. (2018). Continuous Improvement with Lean Six Sigma for Beginners. Retrieved from https: //www. processexcellencenetwork. com/lean-six-sigma-businesstransformation/articles/continuous-improvement-with-lean-six-sigma-for-begvem Lucidchart. com, (2018). 5 Lean Six Sigma Principles You Should Adopt Immediately. Retrieved from https: //www. lucidchart. com/blog/lean-six-sigma-principles Foster, S. T. (2010). Managing Quality: Integrating the Supply Chain (6 th ed. ). Brigham Young University, : Pearson Education Inc. Goetsch, D. L. , & Davis, S. B. (2018). Quality Management for Organizational Excellence (8 th ed. ). Retrieved from The University of Phoenix e. Book Collection database. Millard, M. (2018). 6 Principles of the Continuous Improvement Model. Retrieved from https: //blog. kainexus. com/continuous-improvement/6 -principles-of-the-continuousimprovement-modelnt with Lean Six Sigma for Beginners. Retrieved from https: //www. processexcellencenetwork. com/lean-six-sigma-businesstransformation/articles/continuous-improvement-with-lean-six-sigma-for-beg https: //www. motorolasolutions. com/content/dam/msi/docs/en-xw/static_files/Quality_Brochure. pdf Pierce F. (2011). Motorola’s Six Sigma Journey: In Pursuit of Perfection. Retrieved from https: //www. supplychaindigital. com/procurement/motorolas-six-sigma-journey-pursuitperfection
Implementing hrd programs
Implementing strategies management and operations issues
Strategy implementation example
Chapter 7 strategic management
The pricing tripod
Implementing merchandise plans
Designing and implementing brand architecture strategies
Designing and implementing brand marketing programs
Characteristics of portfolio assessment
Crm vision statement example
Teamwork and collaboration qsen
Challenges of implementing predictive analytics
Bert spector
Implementing strategies marketing finance/accounting
Is the traditional method of implementing access control
Problems in implementing portfolio management
Matching structure with strategy
Designing and implementing brand architecture strategies
Implementing nfpa 1600 national preparedness standard
Implementing organizational change theory into practice
Ubmta signatories
Nfpa 1600 business continuity programs
Implementing firewall technologies