Do D PACKAGING PILOT PROGRAM Status Update Packaging
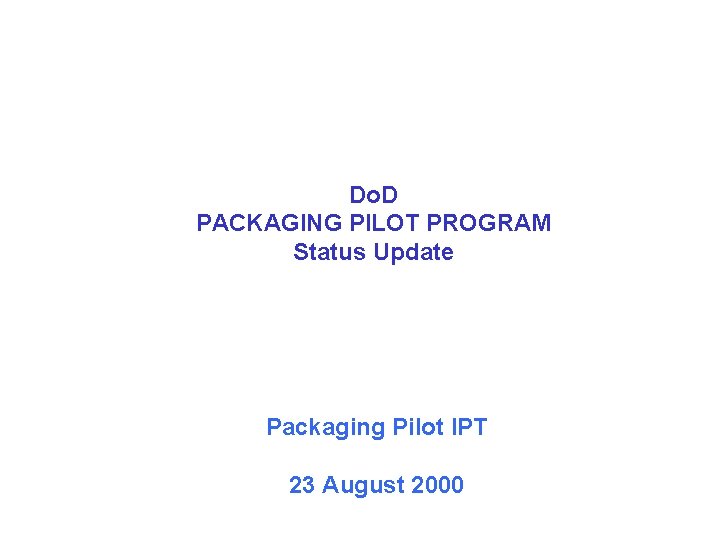
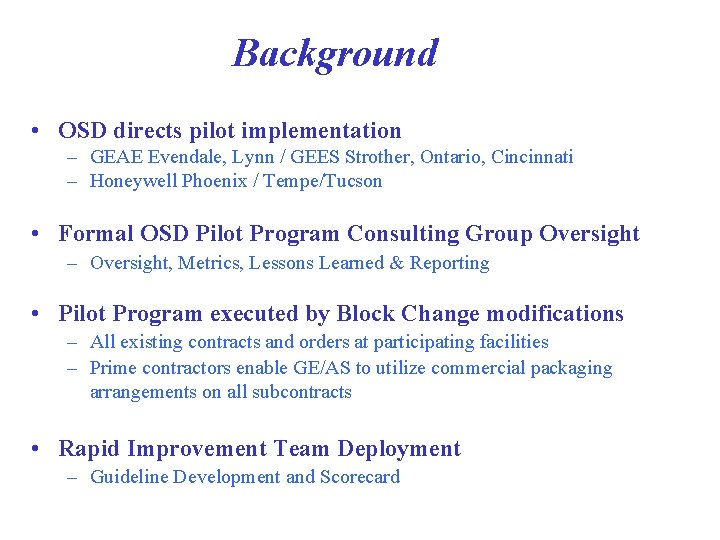
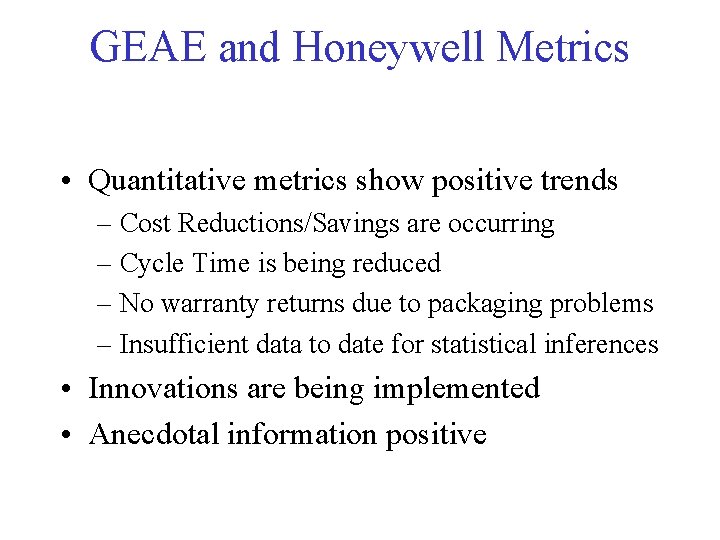
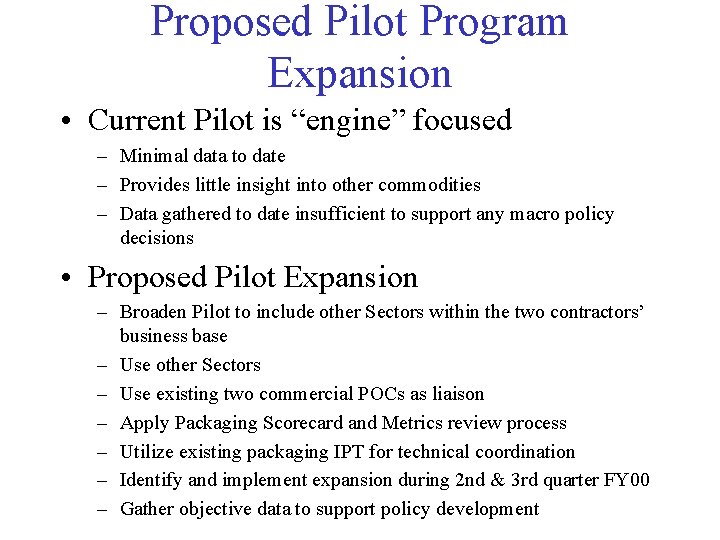
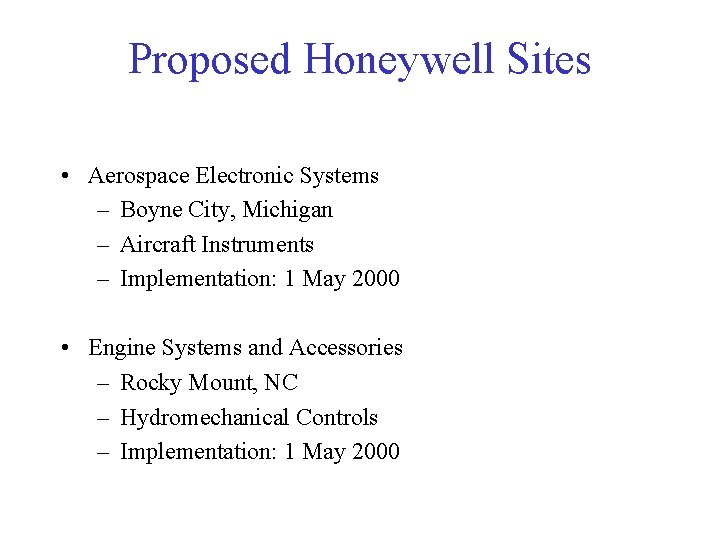
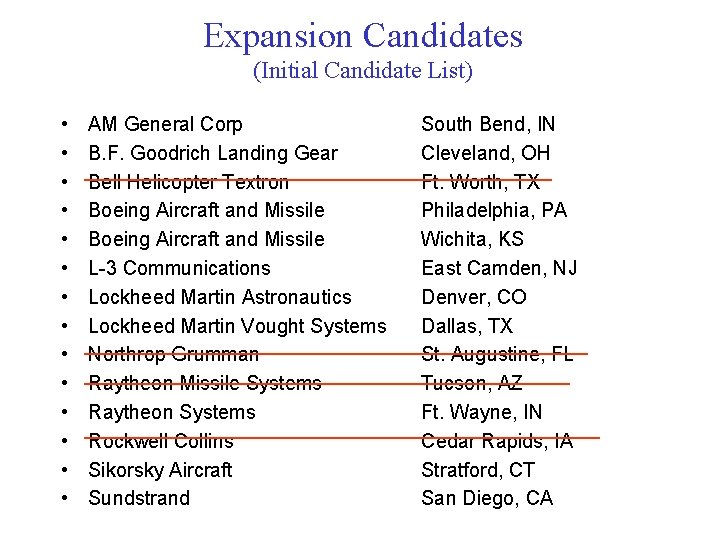
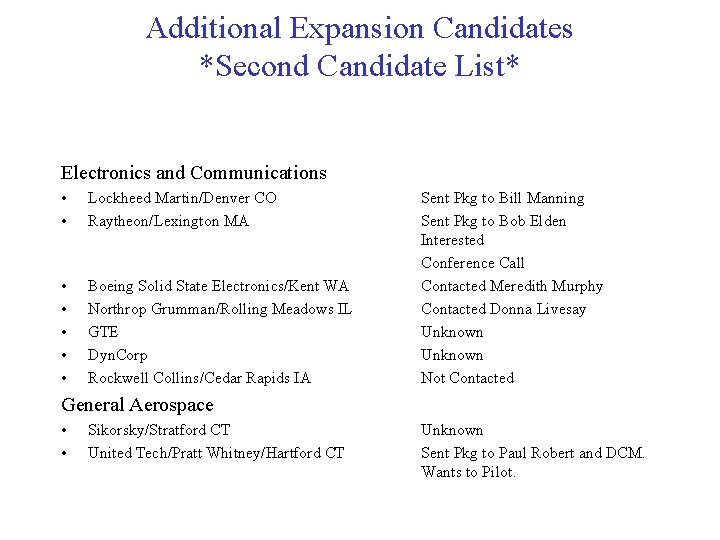
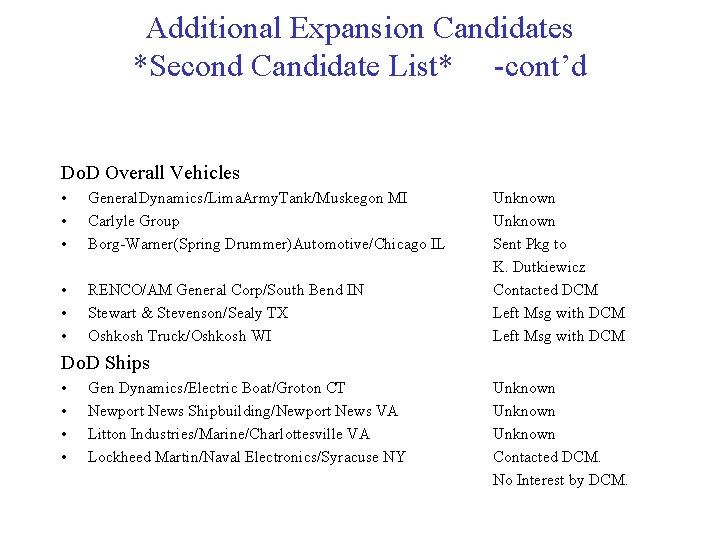
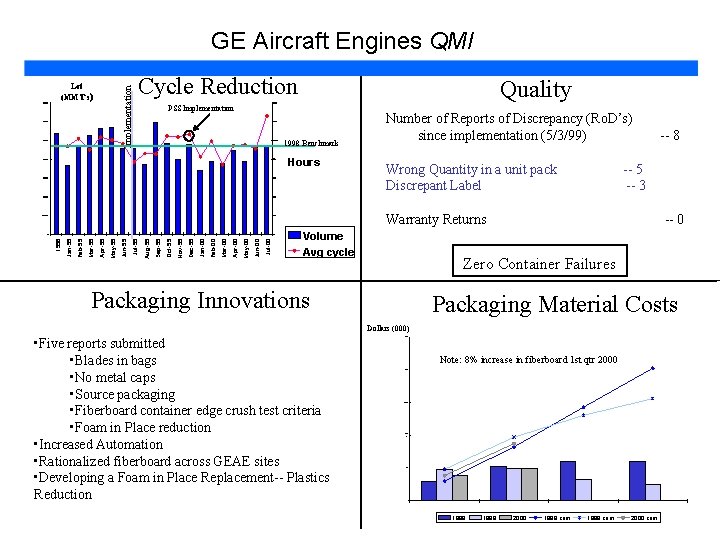
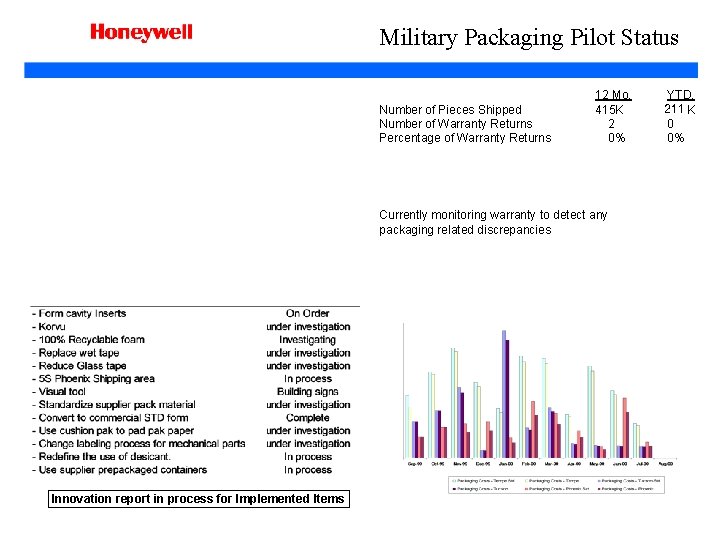
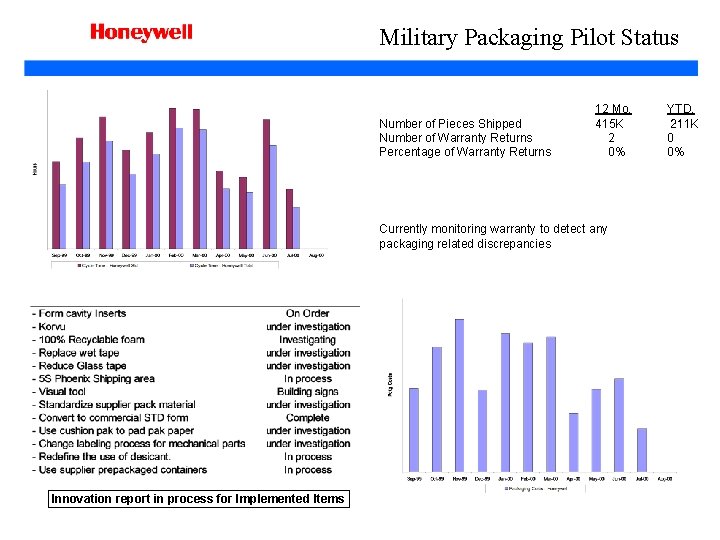
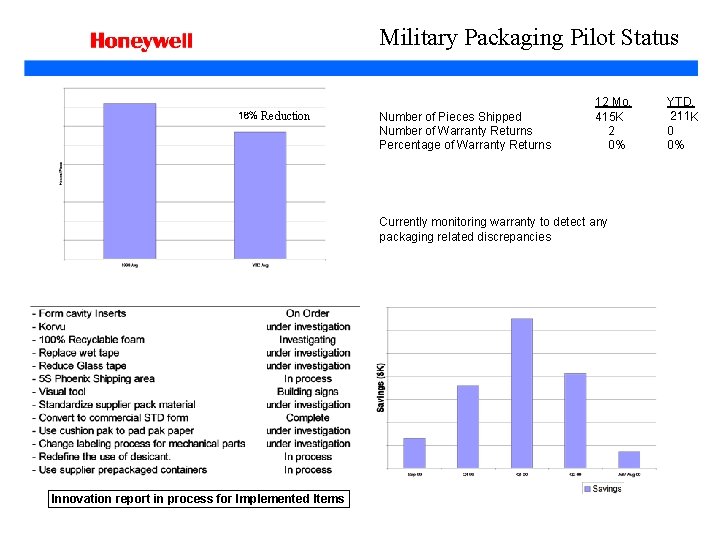
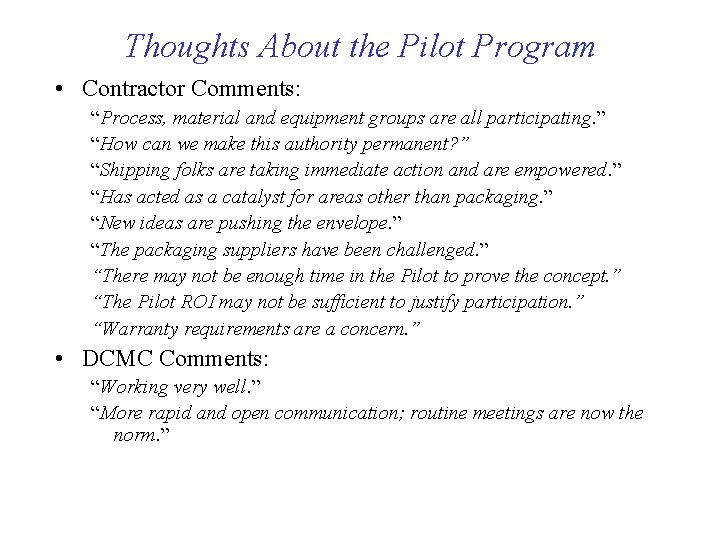
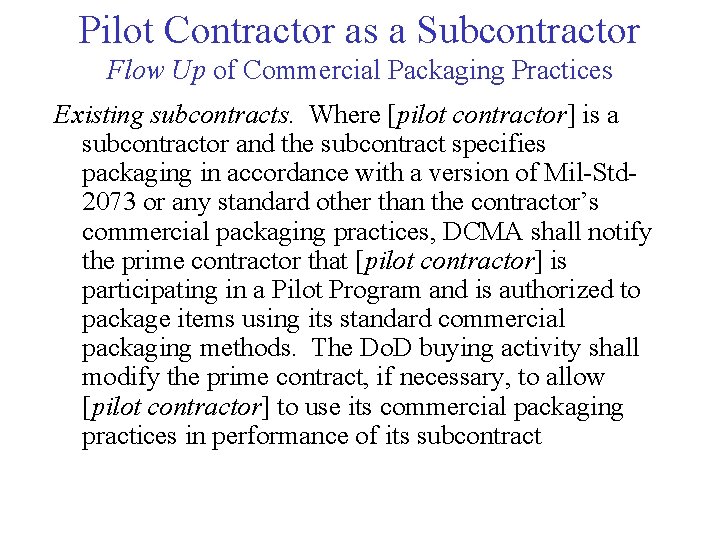
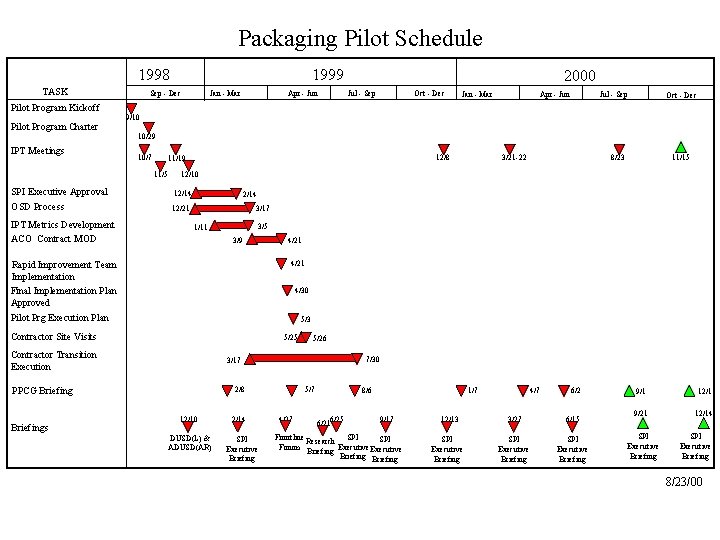
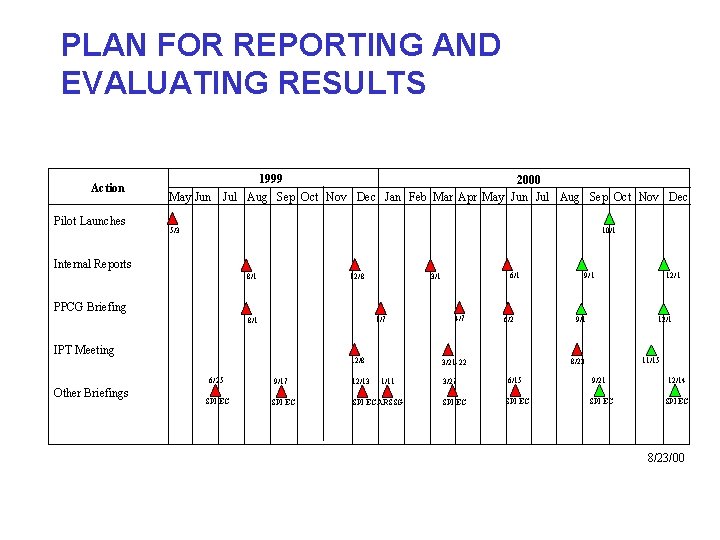
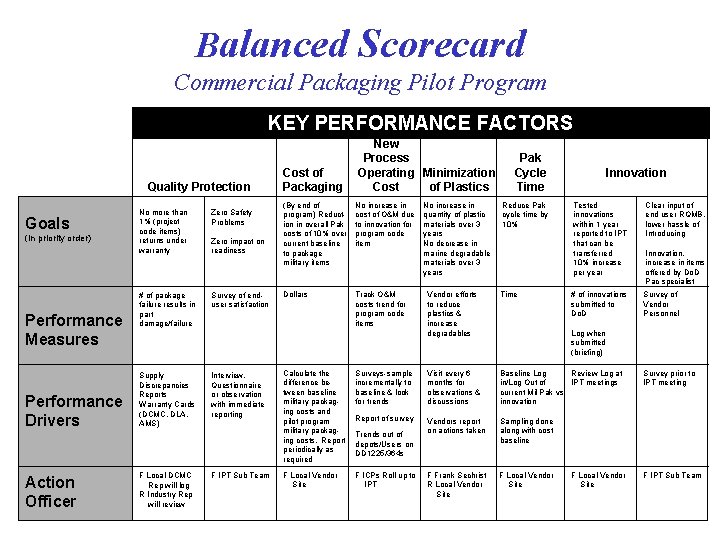
- Slides: 17
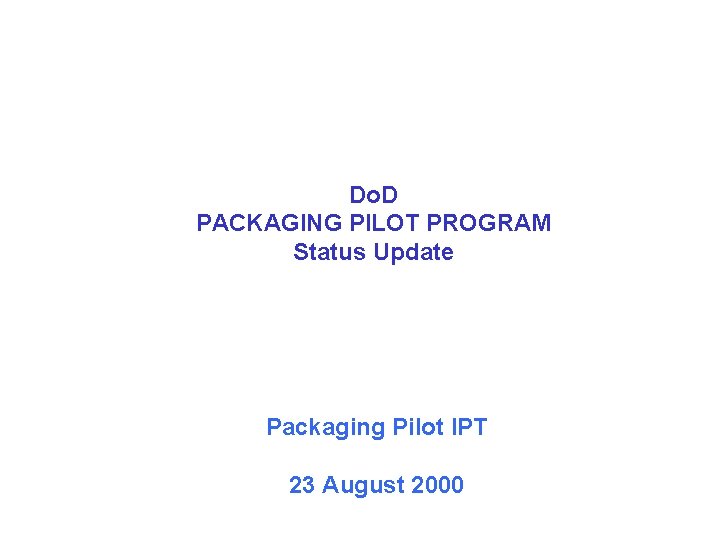
Do. D PACKAGING PILOT PROGRAM Status Update Packaging Pilot IPT 23 August 2000
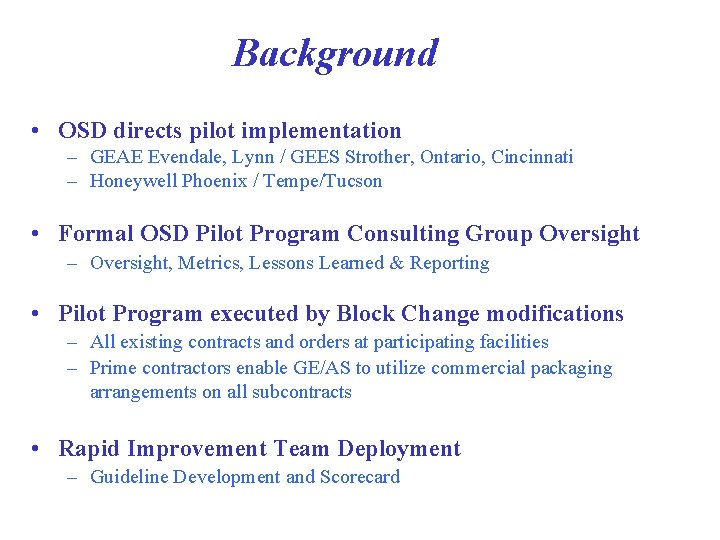
Background • OSD directs pilot implementation – GEAE Evendale, Lynn / GEES Strother, Ontario, Cincinnati – Honeywell Phoenix / Tempe/Tucson • Formal OSD Pilot Program Consulting Group Oversight – Oversight, Metrics, Lessons Learned & Reporting • Pilot Program executed by Block Change modifications – All existing contracts and orders at participating facilities – Prime contractors enable GE/AS to utilize commercial packaging arrangements on all subcontracts • Rapid Improvement Team Deployment – Guideline Development and Scorecard
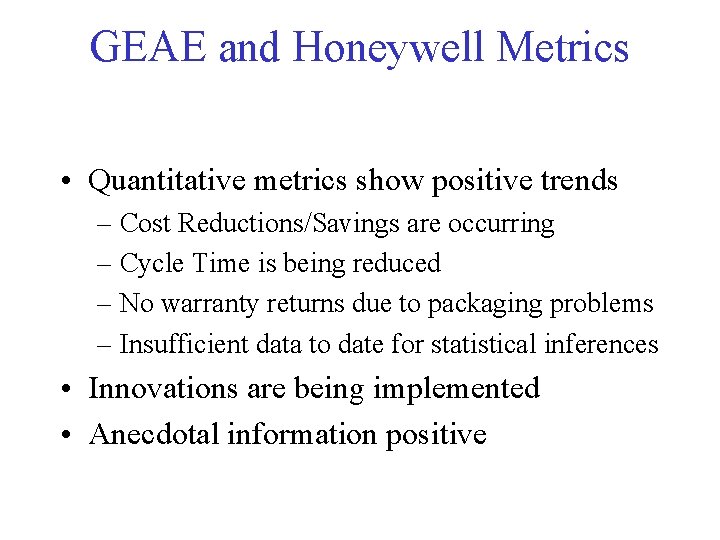
GEAE and Honeywell Metrics • Quantitative metrics show positive trends – Cost Reductions/Savings are occurring – Cycle Time is being reduced – No warranty returns due to packaging problems – Insufficient data to date for statistical inferences • Innovations are being implemented • Anecdotal information positive
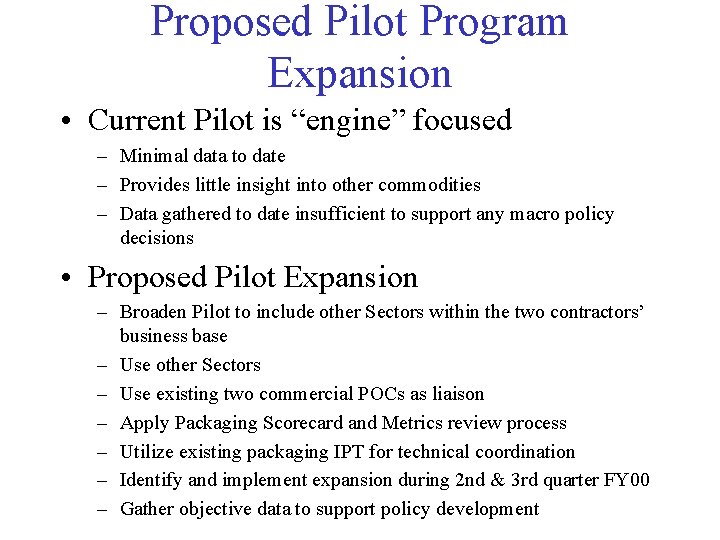
Proposed Pilot Program Expansion • Current Pilot is “engine” focused – Minimal data to date – Provides little insight into other commodities – Data gathered to date insufficient to support any macro policy decisions • Proposed Pilot Expansion – Broaden Pilot to include other Sectors within the two contractors’ business base – Use other Sectors – Use existing two commercial POCs as liaison – Apply Packaging Scorecard and Metrics review process – Utilize existing packaging IPT for technical coordination – Identify and implement expansion during 2 nd & 3 rd quarter FY 00 – Gather objective data to support policy development
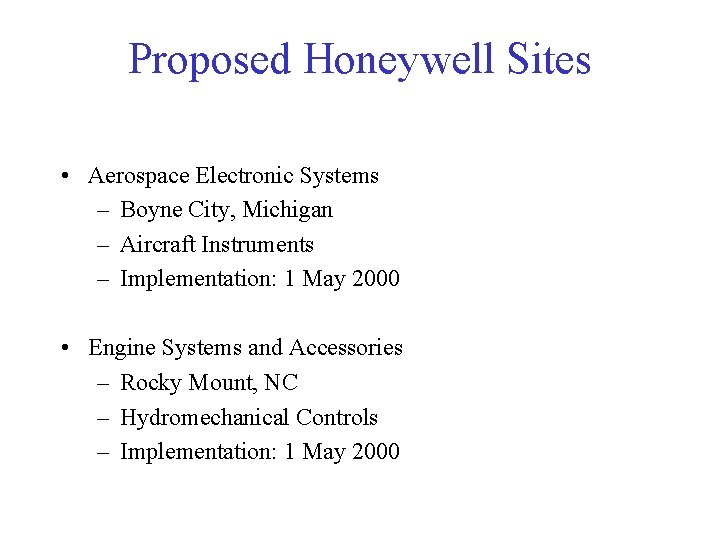
Proposed Honeywell Sites • Aerospace Electronic Systems – Boyne City, Michigan – Aircraft Instruments – Implementation: 1 May 2000 • Engine Systems and Accessories – Rocky Mount, NC – Hydromechanical Controls – Implementation: 1 May 2000
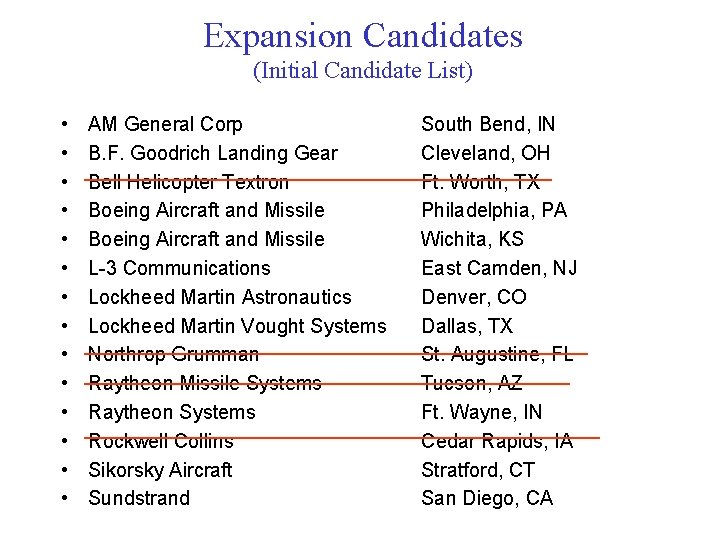
Expansion Candidates (Initial Candidate List) • • • • AM General Corp B. F. Goodrich Landing Gear Bell Helicopter Textron Boeing Aircraft and Missile L-3 Communications Lockheed Martin Astronautics Lockheed Martin Vought Systems Northrop Grumman Raytheon Missile Systems Raytheon Systems Rockwell Collins Sikorsky Aircraft Sundstrand South Bend, IN Cleveland, OH Ft. Worth, TX Philadelphia, PA Wichita, KS East Camden, NJ Denver, CO Dallas, TX St. Augustine, FL Tucson, AZ Ft. Wayne, IN Cedar Rapids, IA Stratford, CT San Diego, CA
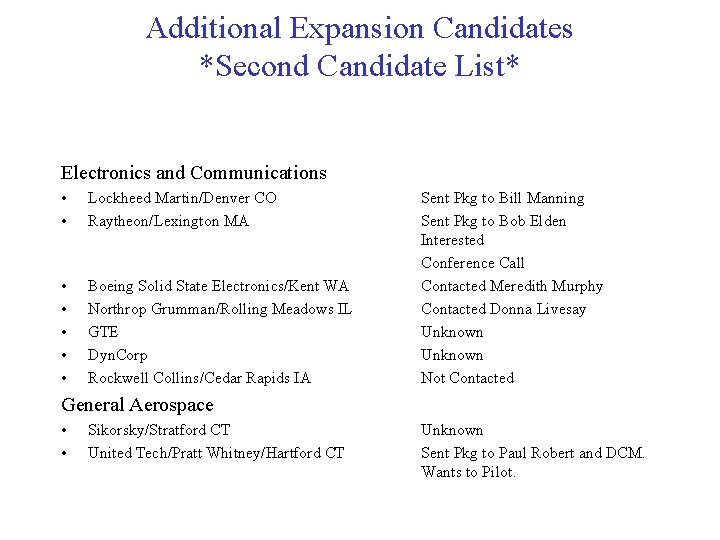
Additional Expansion Candidates *Second Candidate List* Electronics and Communications • • Lockheed Martin/Denver CO Raytheon/Lexington MA • • • Boeing Solid State Electronics/Kent WA Northrop Grumman/Rolling Meadows IL GTE Dyn. Corp Rockwell Collins/Cedar Rapids IA Sent Pkg to Bill Manning Sent Pkg to Bob Elden Interested Conference Call Contacted Meredith Murphy Contacted Donna Livesay Unknown Not Contacted General Aerospace • • Sikorsky/Stratford CT United Tech/Pratt Whitney/Hartford CT Unknown Sent Pkg to Paul Robert and DCM. Wants to Pilot.
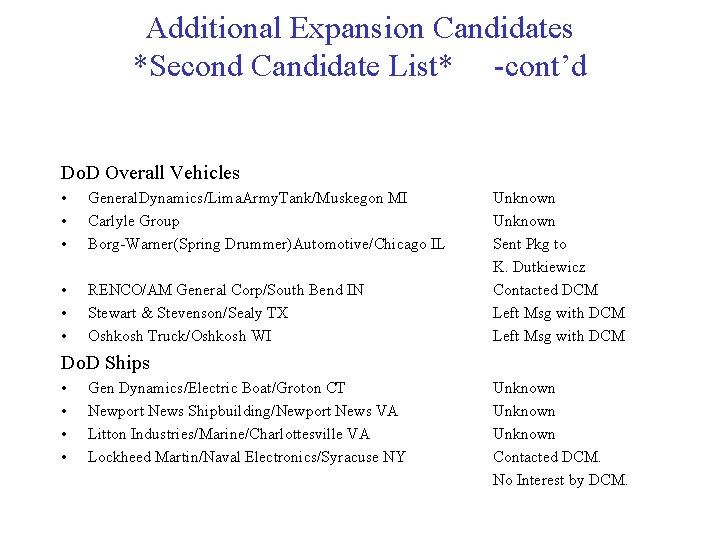
Additional Expansion Candidates *Second Candidate List* -cont’d Do. D Overall Vehicles • • • General. Dynamics/Lima. Army. Tank/Muskegon MI Carlyle Group Borg-Warner(Spring Drummer)Automotive/Chicago IL • • • RENCO/AM General Corp/South Bend IN Stewart & Stevenson/Sealy TX Oshkosh Truck/Oshkosh WI Unknown Sent Pkg to K. Dutkiewicz Contacted DCM Left Msg with DCM Do. D Ships • • Gen Dynamics/Electric Boat/Groton CT Newport News Shipbuilding/Newport News VA Litton Industries/Marine/Charlottesville VA Lockheed Martin/Naval Electronics/Syracuse NY Unknown Contacted DCM. No Interest by DCM.
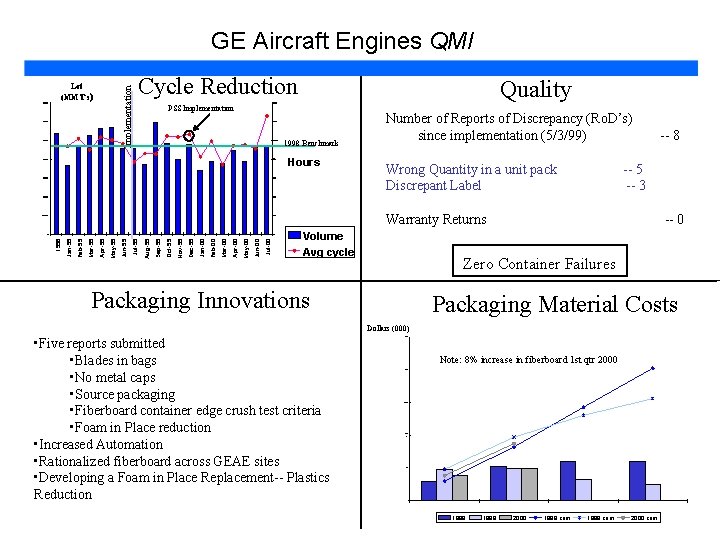
GE Aircraft Engines QMI Lot (MMT’s) Implementation 7000 6000 5000 Cycle Reduction 120 100 4000 80 3000 60 2000 40 1000 20 Jul-00 Jun-00 Apr-00 May-00 Mar-00 Jan-00 Feb-00 Dec-99 Oct-99 Nov-99 Sep-99 Aug-99 Jul-99 Jun-99 Apr-99 May-99 Mar-99 Feb-99 0 1998 0 Jan-99 Quality 140 PSS Implementation 1998 Benchmark Hours Number of Reports of Discrepancy (Ro. D’s) since implementation (5/3/99) Wrong Quantity in a unit pack Discrepant Label -- 5 -- 3 Warranty Returns Volume Avg cycle -- 0 Zero Container Failures Packaging Innovations Packaging Material Costs Dollars (000) • Five reports submitted • Blades in bags • No metal caps • Source packaging • Fiberboard container edge crush test criteria • Foam in Place reduction • Increased Automation • Rationalized fiberboard across GEAE sites • Developing a Foam in Place Replacement-- Plastics Reduction -- 8 2500 Note: 8% increase in fiberboard 1 st qtr 2000 1500 100 0 500 0 1998 1999 2000 1998 cum 1999 cum 2000 cum
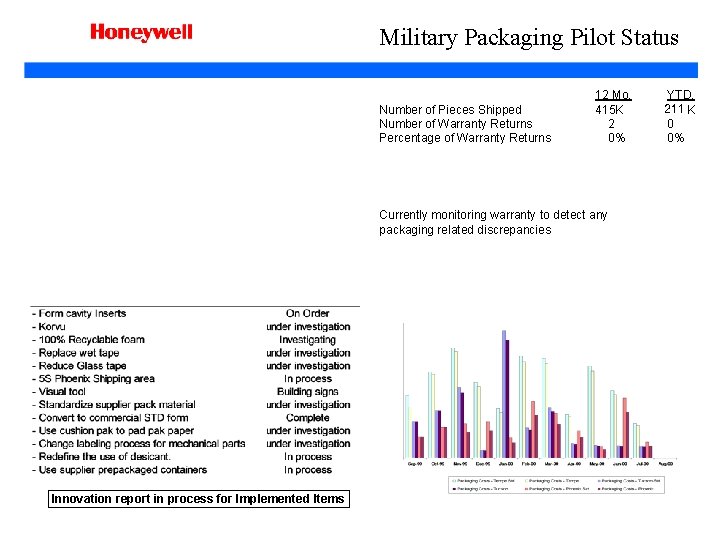
Military Packaging Pilot Status Number of Pieces Shipped Number of Warranty Returns Percentage of Warranty Returns 12 Mo. 415 K 2 0% Currently monitoring warranty to detect any packaging related discrepancies Innovation report in process for Implemented Items YTD. K 0 0%
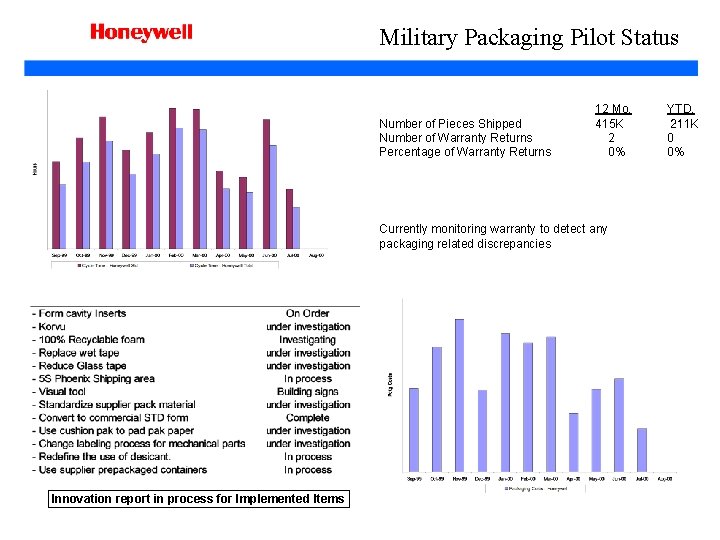
Military Packaging Pilot Status Number of Pieces Shipped Number of Warranty Returns Percentage of Warranty Returns 12 Mo. 415 K 2 0% Currently monitoring warranty to detect any packaging related discrepancies Innovation report in process for Implemented Items YTD. K 0 0%
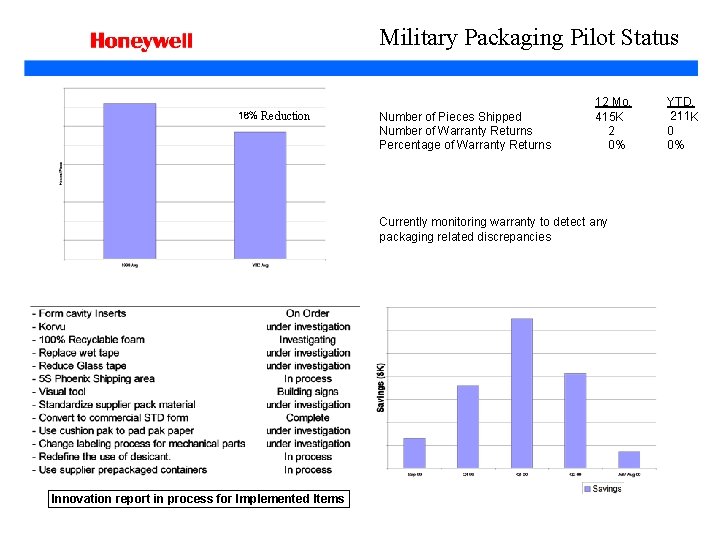
Military Packaging Pilot Status Reduction Number of Pieces Shipped Number of Warranty Returns Percentage of Warranty Returns 12 Mo. 415 K 2 0% Currently monitoring warranty to detect any packaging related discrepancies Innovation report in process for Implemented Items YTD. K 0 0%
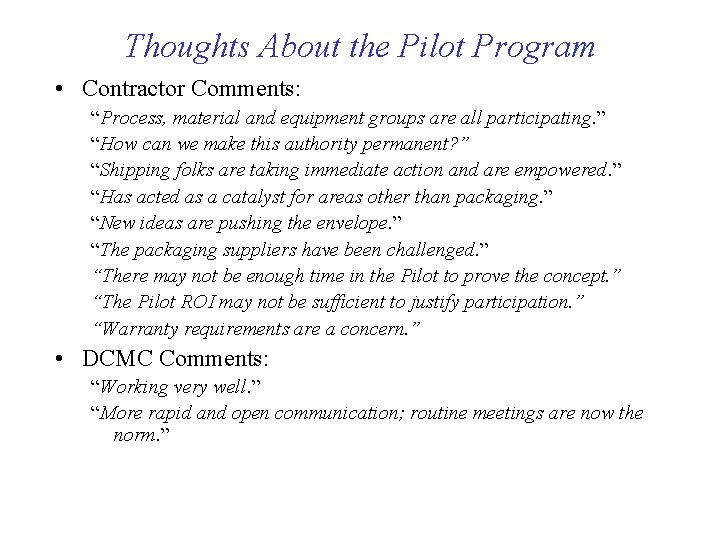
Thoughts About the Pilot Program • Contractor Comments: “Process, material and equipment groups are all participating. ” “How can we make this authority permanent? ” “Shipping folks are taking immediate action and are empowered. ” “Has acted as a catalyst for areas other than packaging. ” “New ideas are pushing the envelope. ” “The packaging suppliers have been challenged. ” “There may not be enough time in the Pilot to prove the concept. ” “The Pilot ROI may not be sufficient to justify participation. ” “Warranty requirements are a concern. ” • DCMC Comments: “Working very well. ” “More rapid and open communication; routine meetings are now the norm. ”
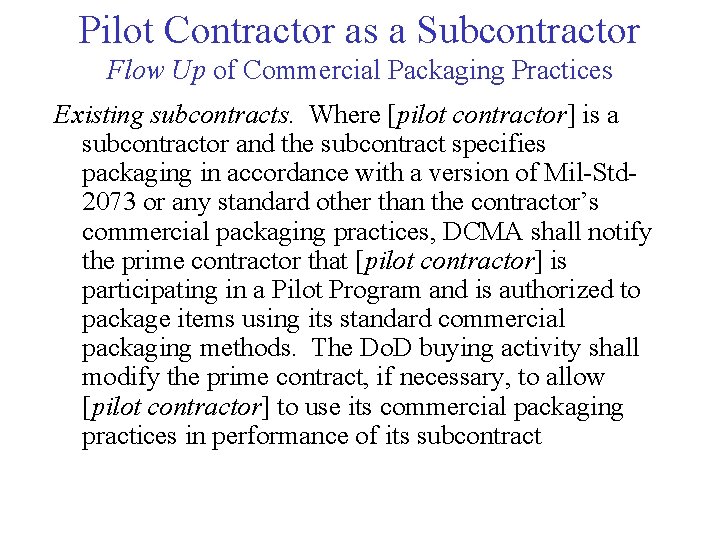
Pilot Contractor as a Subcontractor Flow Up of Commercial Packaging Practices Existing subcontracts. Where [pilot contractor] is a subcontractor and the subcontract specifies packaging in accordance with a version of Mil-Std 2073 or any standard other than the contractor’s commercial packaging practices, DCMA shall notify the prime contractor that [pilot contractor] is participating in a Pilot Program and is authorized to package items using its standard commercial packaging methods. The Do. D buying activity shall modify the prime contract, if necessary, to allow [pilot contractor] to use its commercial packaging practices in performance of its subcontract
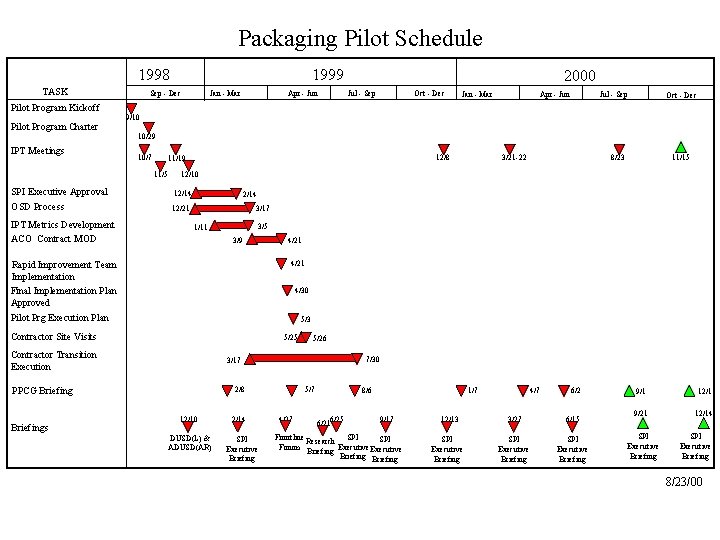
Packaging Pilot Schedule 1998 TASK Pilot Program Kickoff Pilot Program Charter IPT Meetings 1999 Sep - Dec Apr - Jun Oct - Dec Jan - Mar Apr - Jun Jul - Sep Oct - Dec 10/29 10/7 3/21 -22 12/8 11/19 11/15 8/23 12/10 SPI Executive Approval 12/14 OSD Process 12/21 2/14 3/17 3/5 1/11 3/9 Rapid Improvement Team Implementation Final Implementation Plan Approved Pilot Prg Execution Plan 4/21 4/30 5/3 Contractor Site Visits 5/25 Contractor Transition Execution 5/26 7/30 3/17 2/8 PPCG Briefings Jul - Sep 9/10 11/5 IPT Metrics Development ACO Contract MOD Jan - Mar 2000 12/10 DUSD(L) & ADUSD(AR) 2/14 SPI Executive Briefing 5/7 4/27 8/6 6/216/25 1/7 9/17 Frontline SPI Research Forum Executive Briefing 12/13 SPI Executive Briefing 4/7 6/2 3/27 6/15 SPI Executive Briefing 9/1 12/1 9/21 12/14 SPI Executive Briefing 8/23/00
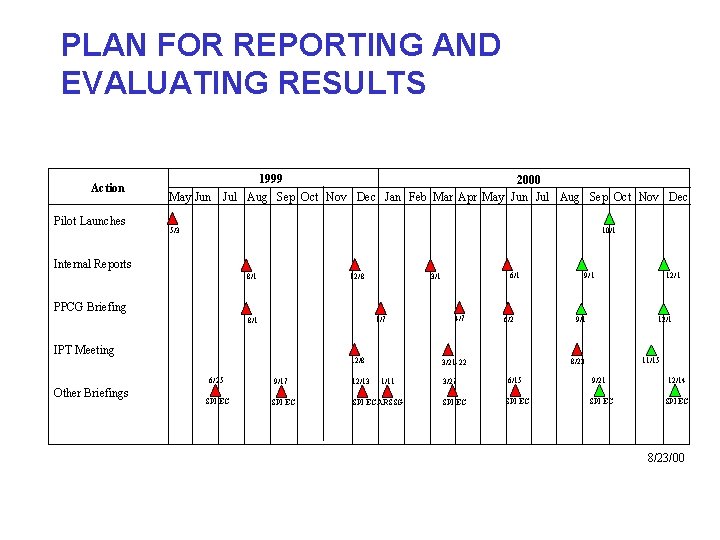
PLAN FOR REPORTING AND EVALUATING RESULTS Action Pilot Launches 1999 2000 May Jun Jul Aug Sep Oct Nov Dec Jan Feb Mar Apr May Jun Jul Aug Sep Oct Nov Dec 5/3 10/1 Internal Reports 12/8 8/1 6/1 3/1 9/1 12/1 PPCG Briefing 1/7 8/1 IPT Meeting Other Briefings 12/8 6/25 9/17 SPI EC 12/13 4/7 6/2 SPI EC ARSSG 3/27 SPI EC 12/1 11/15 8/23 3/21 -22 1/11 9/1 6/15 9/21 12/14 SPI EC 8/23/00
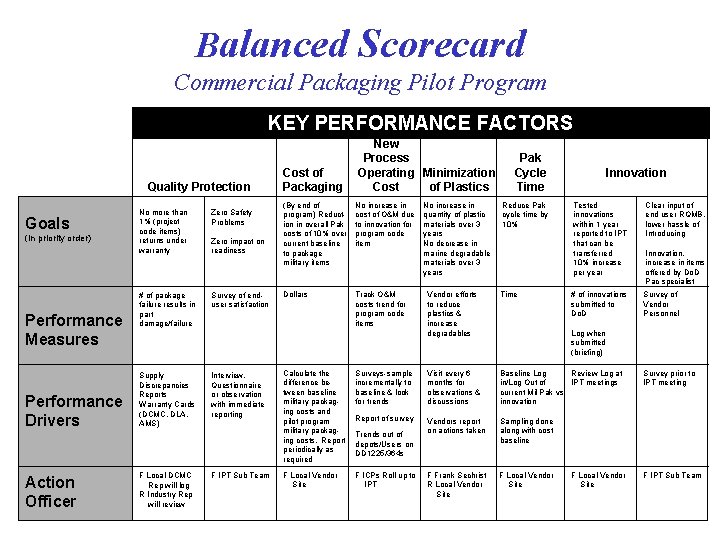
Balanced Scorecard Commercial Packaging Pilot Program KEY PERFORMANCE FACTORS Quality Protection Goals (in priority order) Performance Measures No more than 1% (project code items) returns under warranty Zero Safety Problems # of package failure results in part damage/failure Survey of enduser satisfaction Performance Drivers Supply Discrepancies Reports Warranty Cards (DCMC, DLA, AMS) Action Officer F Local DCMC Rep will log R Industry Rep will review Zero impact on readiness Interview, Questionnaire or observation with immediate reporting F IPT Sub Team Cost of Packaging New Process Operating Minimization of Plastics Cost (By end of program) Reduction in overall Pak costs of 10% over current baseline to package military items No increase in cost of O&M due to innovation for program code item Dollars Track O&M costs trend for program code items No increase in quantity of plastic materials over 3 years No decrease in marine degradable materials over 3 years Pak Cycle Time Reduce Pak cycle time by 10% Vendor efforts to reduce plastics & increase degradables Time Innovation Tested innovations within 1 year reported to IPT that can be transferred 10% increase per year Clear input of end user RQMB, lower hassle of Introducing # of innovations submitted to Do. D Survey of Vendor Personnel Log when submitted (briefing) Calculate the difference between baseline military packaging costs and pilot program military packaging costs. Report periodically as required Surveys-sample incrementally to baseline & look for trends Visit every 6 months for observations & discussions Baseline Log Review Log at in/Log Out of IPT meetings current Mil Pak vs innovation Report of survey Vendors report on actions taken Sampling done along with cost baseline F Local Vendor Site F ICPs Roll up to IPT F Frank Sechrist R Local Vendor Site F Local Vendor Site Trends out of depots/Users on DD 1225/364 s Innovation, increase in items offered by Do. D Pac specialist F Local Vendor Site Survey prior to IPT meeting F IPT Sub Team
Shadow paging recovery technique
Project status update examples
Fsu freight status update
Brc global standards directory
Packaging and packaging waste directive
Pilot proficiency award program
Wings pilot proficiency program
Section 502 guaranteed rural housing loan program
First action interview pilot program
Lion pilot program
Current program status register is
Md mizanur rahman pilot
Poisonwood bible theme
Sdlc parallel run
Direct conversion system
Plural of pilot
Landos co pilot
Small scale fermentation