API Winter Meeting 2016 API 17 TR 8
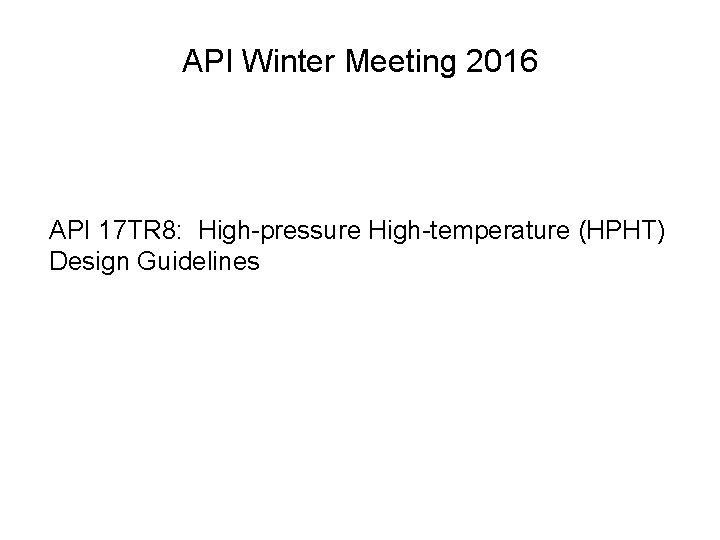
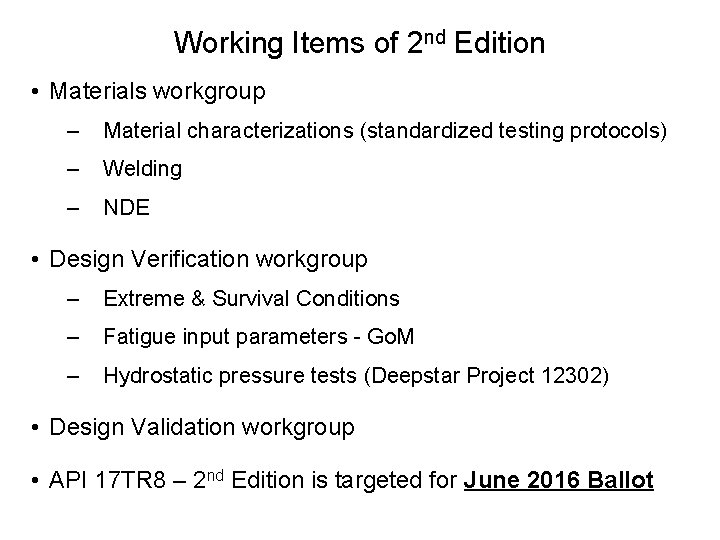
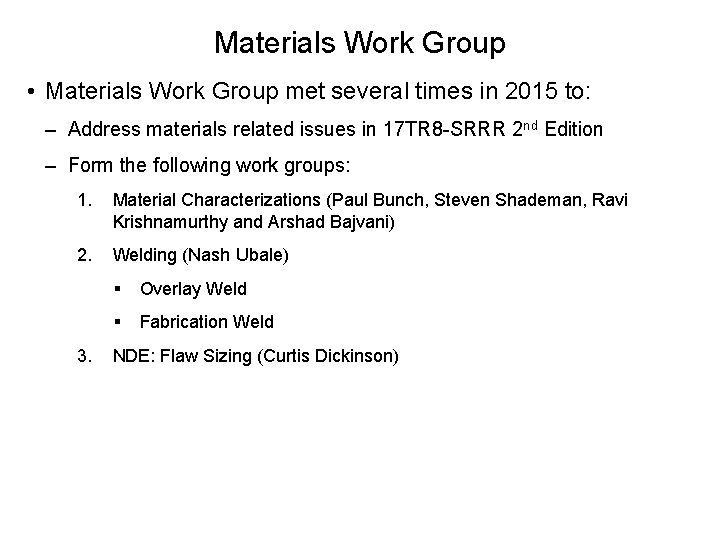
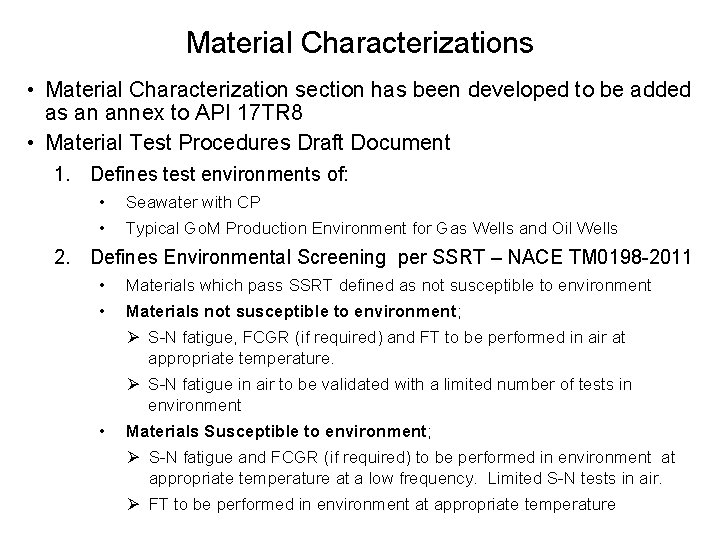
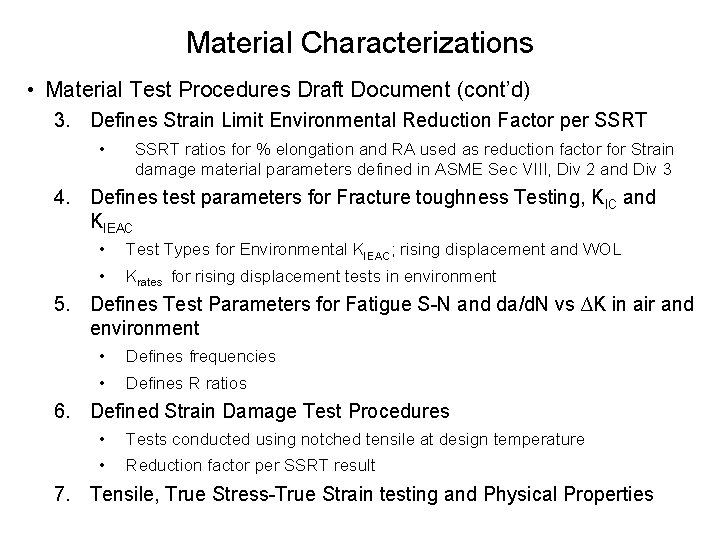
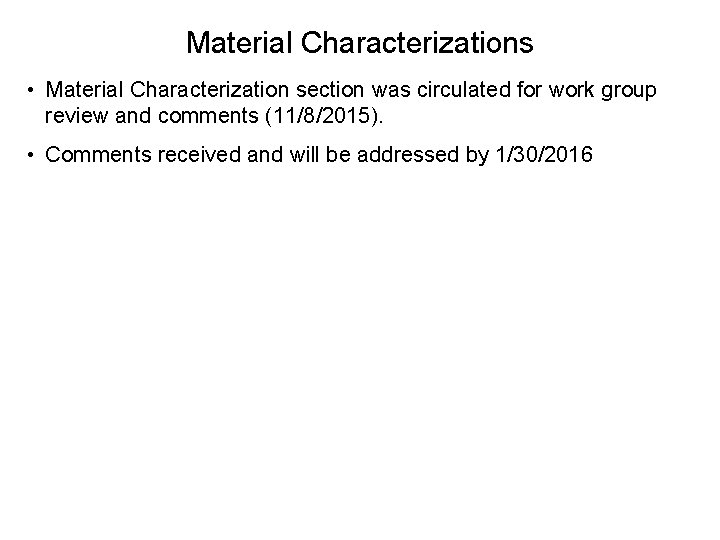
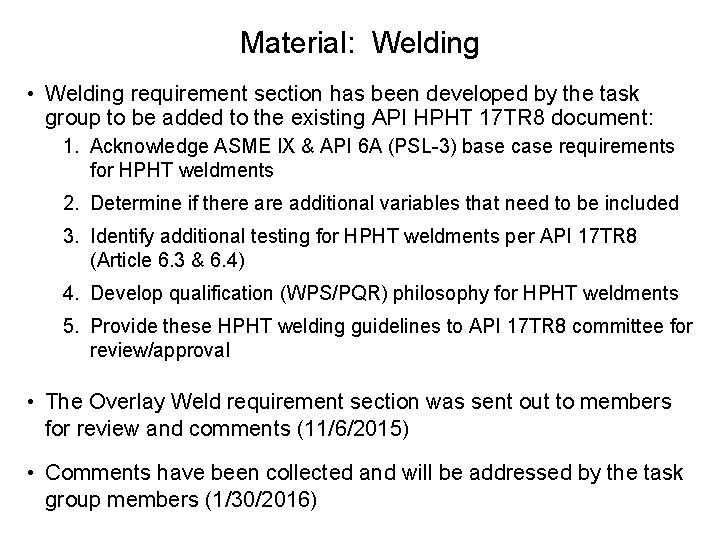
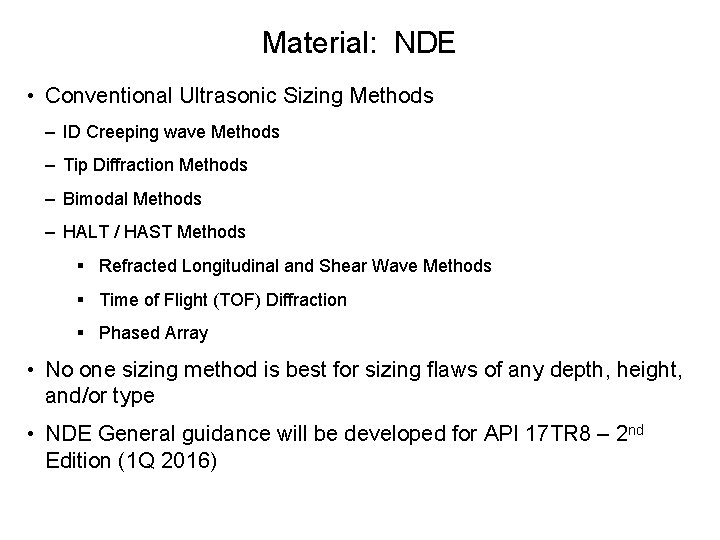
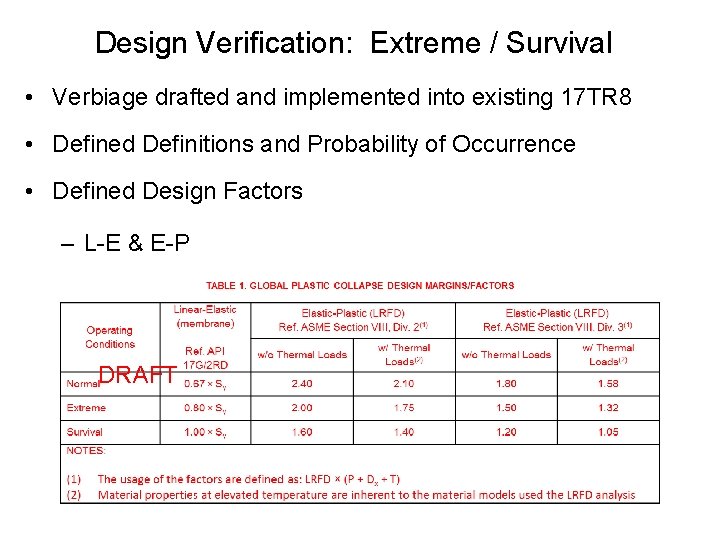
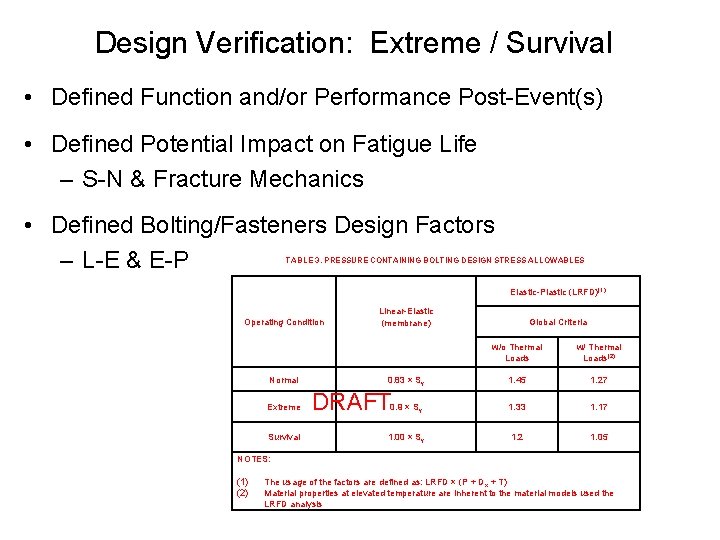
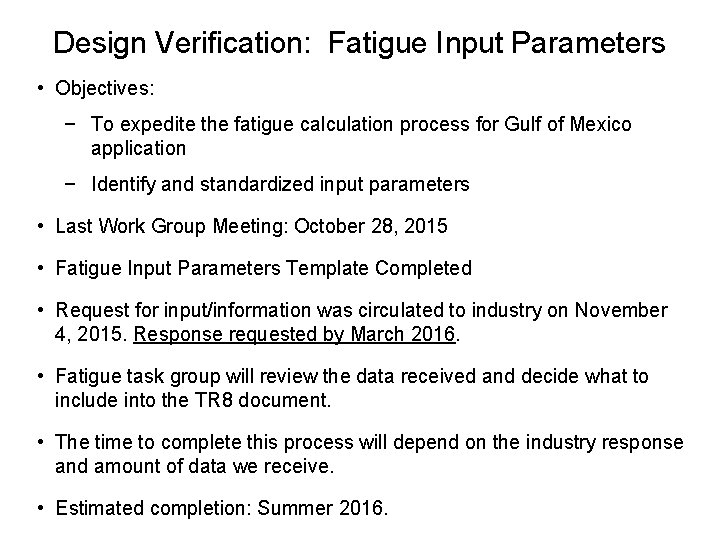
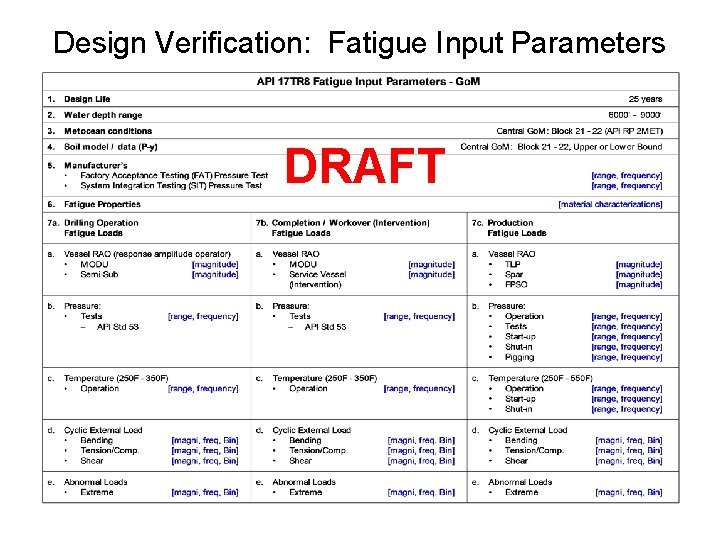

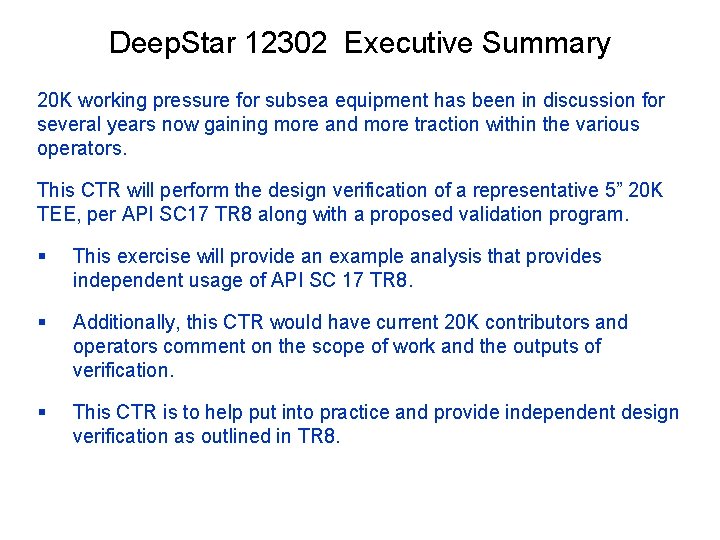
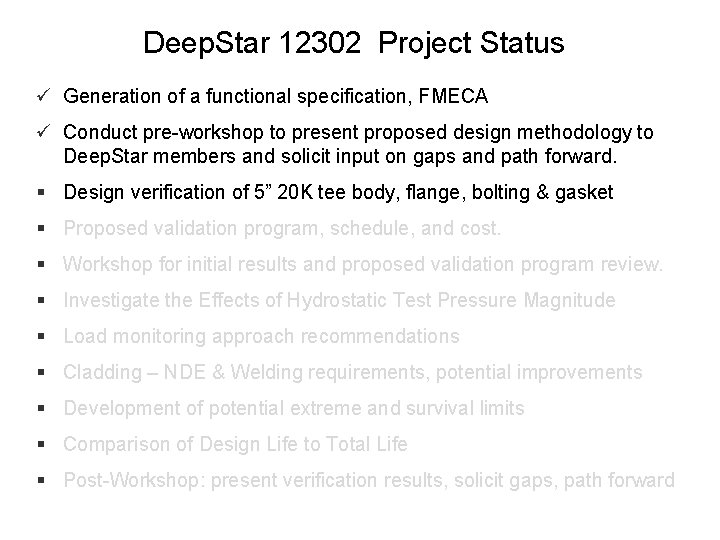
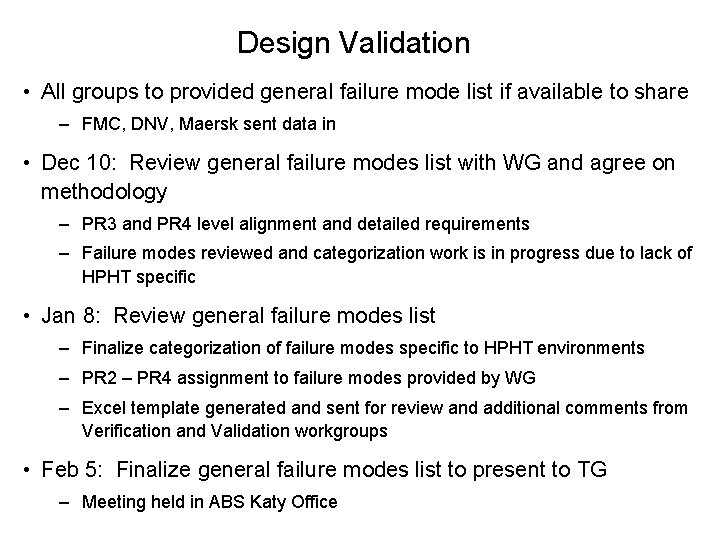
- Slides: 16
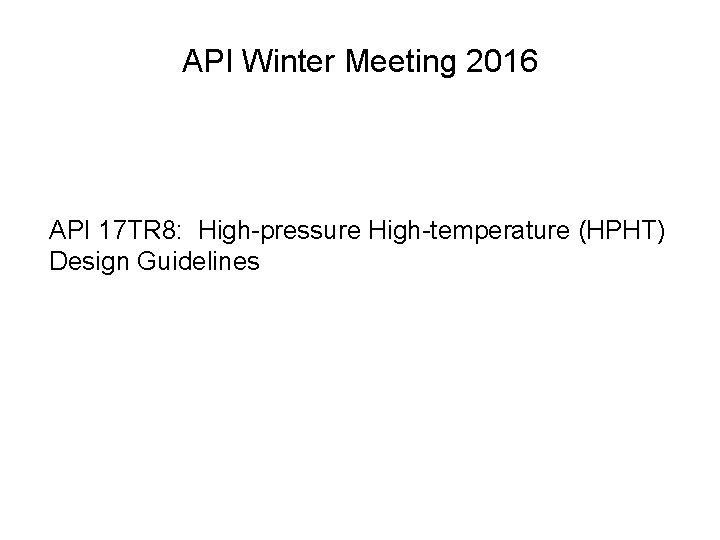
API Winter Meeting 2016 API 17 TR 8: High-pressure High-temperature (HPHT) Design Guidelines
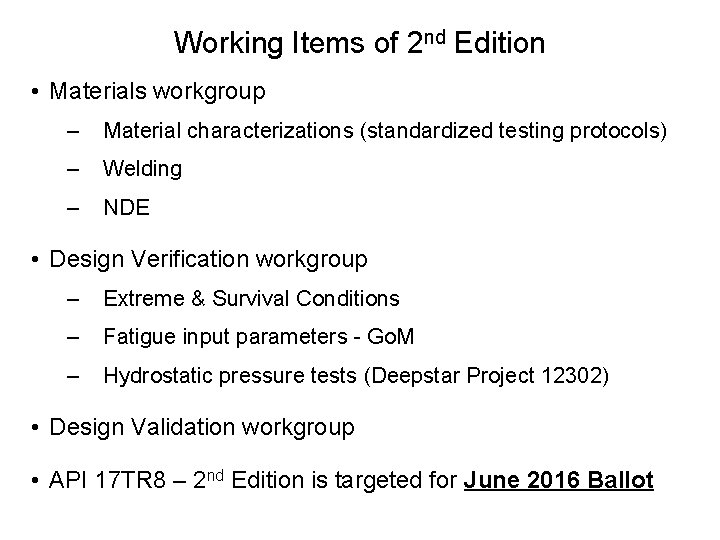
Working Items of 2 nd Edition • Materials workgroup – Material characterizations (standardized testing protocols) – Welding – NDE • Design Verification workgroup – Extreme & Survival Conditions – Fatigue input parameters - Go. M – Hydrostatic pressure tests (Deepstar Project 12302) • Design Validation workgroup • API 17 TR 8 – 2 nd Edition is targeted for June 2016 Ballot
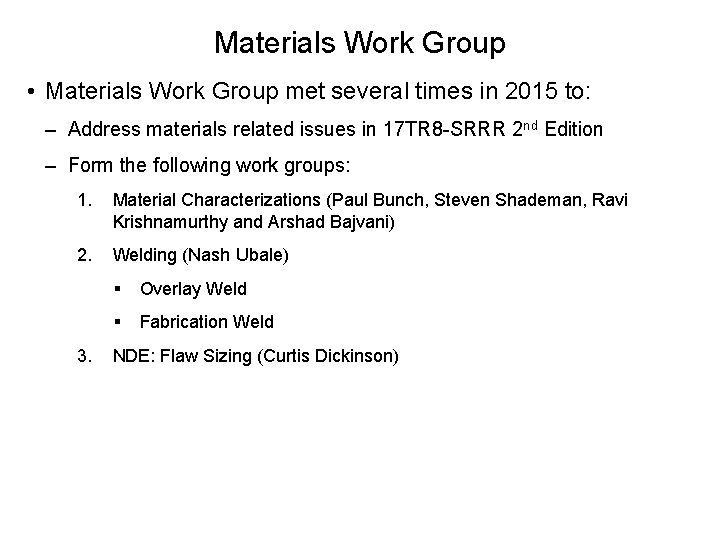
Materials Work Group • Materials Work Group met several times in 2015 to: – Address materials related issues in 17 TR 8 -SRRR 2 nd Edition – Form the following work groups: 1. Material Characterizations (Paul Bunch, Steven Shademan, Ravi Krishnamurthy and Arshad Bajvani) 2. Welding (Nash Ubale) 3. § Overlay Weld § Fabrication Weld NDE: Flaw Sizing (Curtis Dickinson)
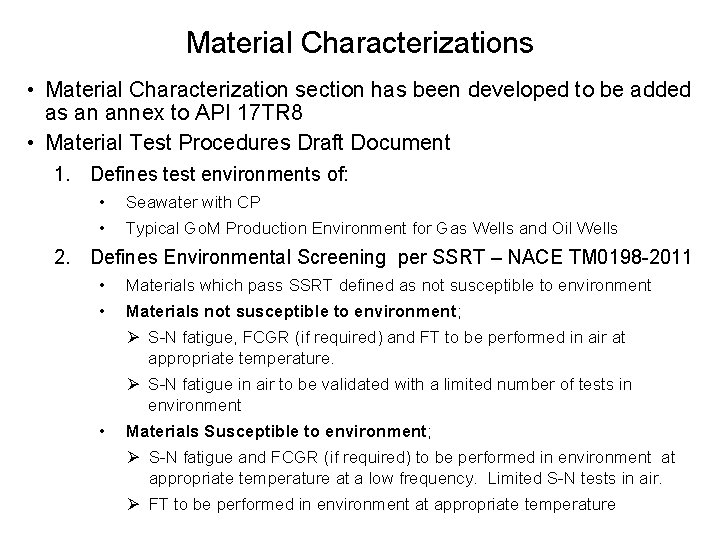
Material Characterizations • Material Characterization section has been developed to be added as an annex to API 17 TR 8 • Material Test Procedures Draft Document 1. Defines test environments of: • Seawater with CP • Typical Go. M Production Environment for Gas Wells and Oil Wells 2. Defines Environmental Screening per SSRT – NACE TM 0198 -2011 • Materials which pass SSRT defined as not susceptible to environment • Materials not susceptible to environment; Ø S-N fatigue, FCGR (if required) and FT to be performed in air at appropriate temperature. Ø S-N fatigue in air to be validated with a limited number of tests in environment • Materials Susceptible to environment; Ø S-N fatigue and FCGR (if required) to be performed in environment at appropriate temperature at a low frequency. Limited S-N tests in air. Ø FT to be performed in environment at appropriate temperature
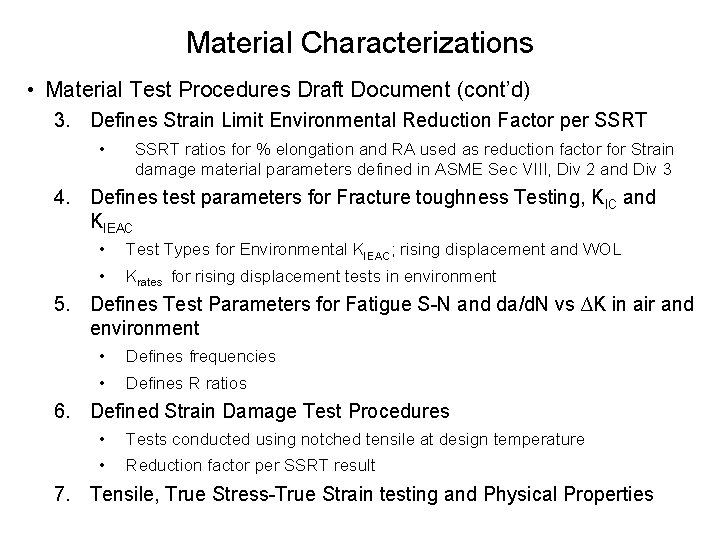
Material Characterizations • Material Test Procedures Draft Document (cont’d) 3. Defines Strain Limit Environmental Reduction Factor per SSRT • SSRT ratios for % elongation and RA used as reduction factor for Strain damage material parameters defined in ASME Sec VIII, Div 2 and Div 3 4. Defines test parameters for Fracture toughness Testing, KIC and KIEAC • Test Types for Environmental KIEAC; rising displacement and WOL • Krates for rising displacement tests in environment 5. Defines Test Parameters for Fatigue S-N and da/d. N vs ∆K in air and environment • Defines frequencies • Defines R ratios 6. Defined Strain Damage Test Procedures • Tests conducted using notched tensile at design temperature • Reduction factor per SSRT result 7. Tensile, True Stress-True Strain testing and Physical Properties
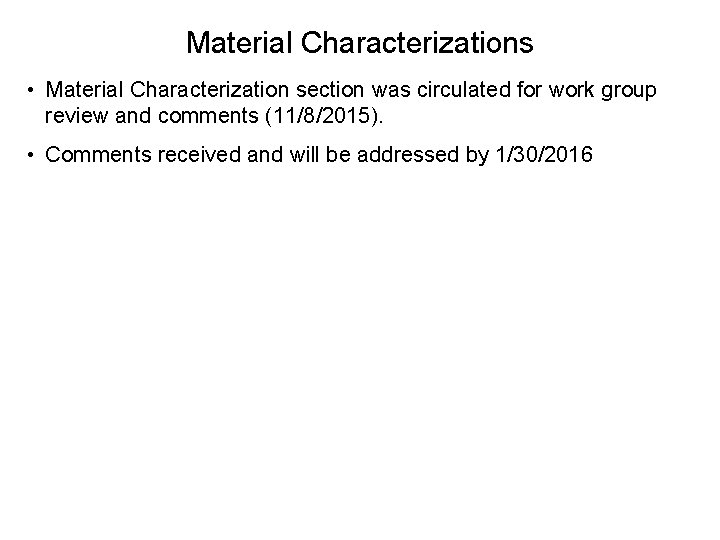
Material Characterizations • Material Characterization section was circulated for work group review and comments (11/8/2015). • Comments received and will be addressed by 1/30/2016
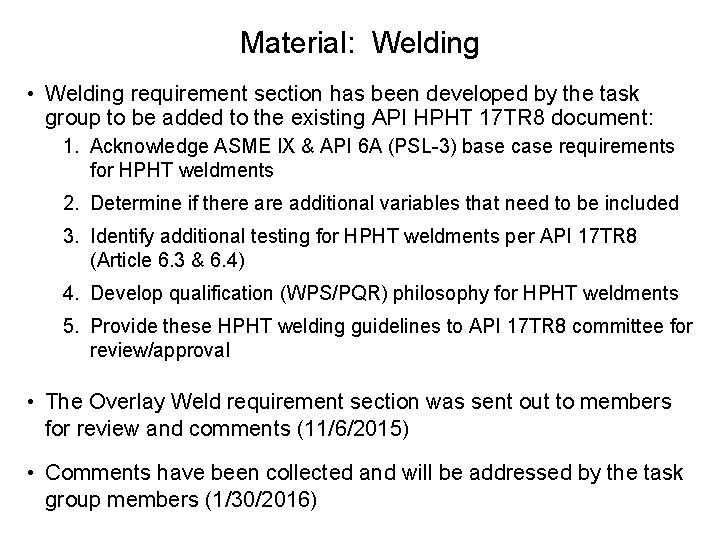
Material: Welding • Welding requirement section has been developed by the task group to be added to the existing API HPHT 17 TR 8 document: 1. Acknowledge ASME IX & API 6 A (PSL-3) base case requirements for HPHT weldments 2. Determine if there additional variables that need to be included 3. Identify additional testing for HPHT weldments per API 17 TR 8 (Article 6. 3 & 6. 4) 4. Develop qualification (WPS/PQR) philosophy for HPHT weldments 5. Provide these HPHT welding guidelines to API 17 TR 8 committee for review/approval • The Overlay Weld requirement section was sent out to members for review and comments (11/6/2015) • Comments have been collected and will be addressed by the task group members (1/30/2016)
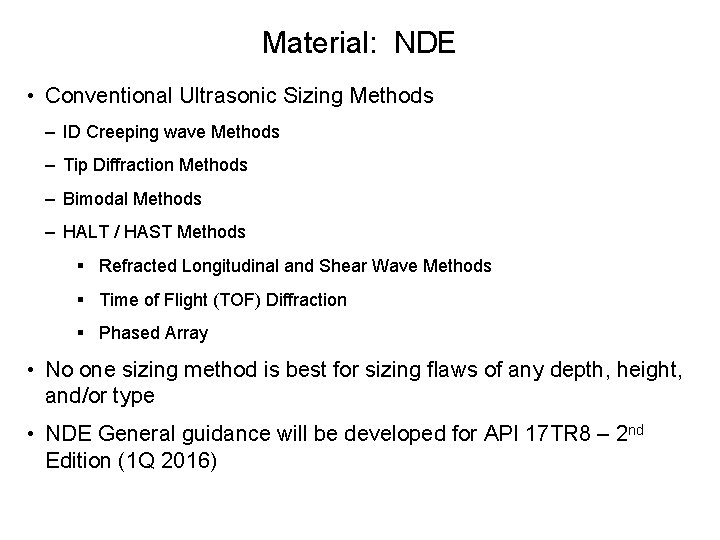
Material: NDE • Conventional Ultrasonic Sizing Methods – ID Creeping wave Methods – Tip Diffraction Methods – Bimodal Methods – HALT / HAST Methods § Refracted Longitudinal and Shear Wave Methods § Time of Flight (TOF) Diffraction § Phased Array • No one sizing method is best for sizing flaws of any depth, height, and/or type • NDE General guidance will be developed for API 17 TR 8 – 2 nd Edition (1 Q 2016)
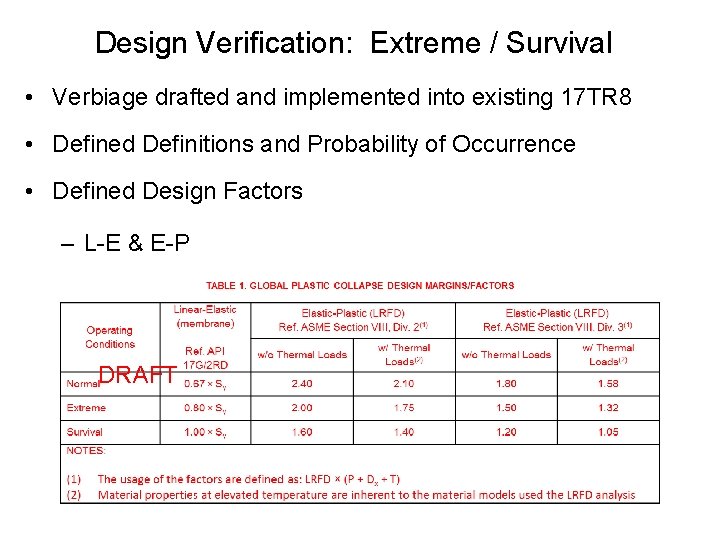
Design Verification: Extreme / Survival • Verbiage drafted and implemented into existing 17 TR 8 • Defined Definitions and Probability of Occurrence • Defined Design Factors – L-E & E-P DRAFT
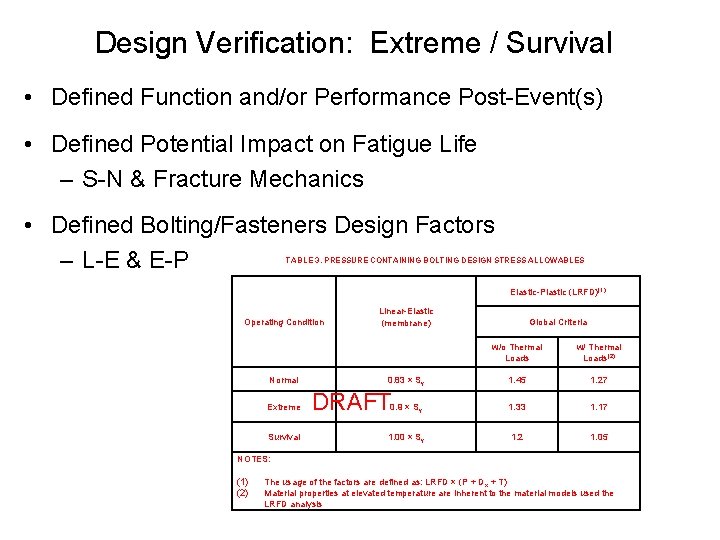
Design Verification: Extreme / Survival • Defined Function and/or Performance Post-Event(s) • Defined Potential Impact on Fatigue Life – S-N & Fracture Mechanics • Defined Bolting/Fasteners Design Factors – L-E & E-P TABLE 3. PRESSURE CONTAINING BOLTING DESIGN STRESS ALLOWABLES Elastic-Plastic (LRFD)(1) Operating Condition Normal Extreme Survival Linear-Elastic (membrane) Global Criteria w/o Thermal Loads w/ Thermal Loads(2) 1. 45 1. 27 0. 9 × Sy 1. 33 1. 17 1. 00 × Sy 1. 2 1. 05 0. 83 × Sy DRAFT NOTES: (1) (2) The usage of the factors are defined as: LRFD × (P + Dx + T) Material properties at elevated temperature are inherent to the material models used the LRFD analysis
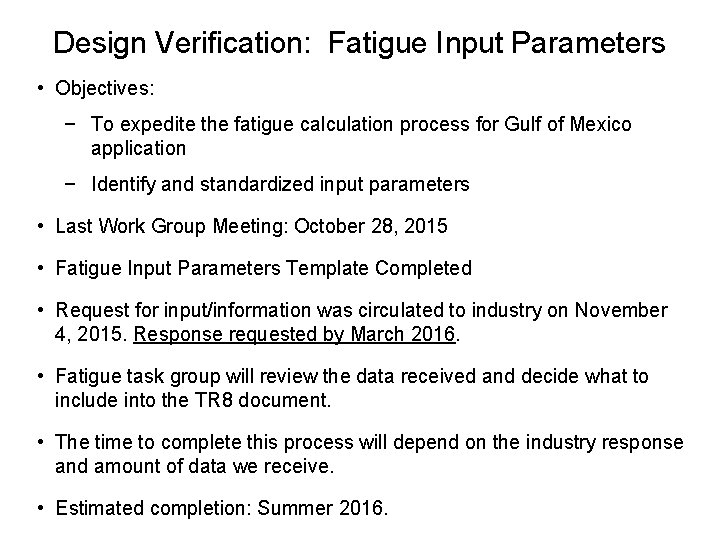
Design Verification: Fatigue Input Parameters • Objectives: − To expedite the fatigue calculation process for Gulf of Mexico application − Identify and standardized input parameters • Last Work Group Meeting: October 28, 2015 • Fatigue Input Parameters Template Completed • Request for input/information was circulated to industry on November 4, 2015. Response requested by March 2016. • Fatigue task group will review the data received and decide what to include into the TR 8 document. • The time to complete this process will depend on the industry response and amount of data we receive. • Estimated completion: Summer 2016.
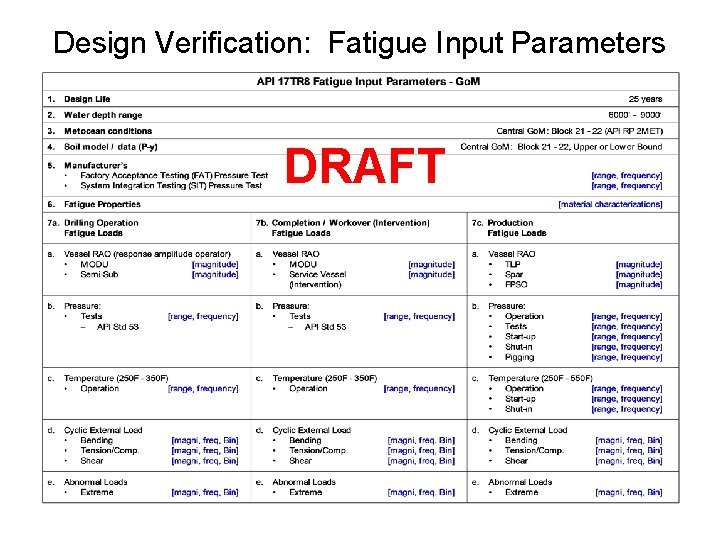
Design Verification: Fatigue Input Parameters DRAFT

Deep. Star Project: Hydrostatic Pressure Tests • Objectives: − − Industry’s studies to assess each design path of HPHT design flow chart and the effects of: • varying hydrostatic test pressures on equipment’s strain limit damage/equivalent plastic strain and • its effects on fatigue life estimation and environmental cracking resistance These studies are to include validation testing program of the analytical results • Deep. Star’s Project 12302 – 20 ksi Systems, incorporated 17 TR 8 objectives into their project work scope. − Project Champion: Chris Kocurek (COP)
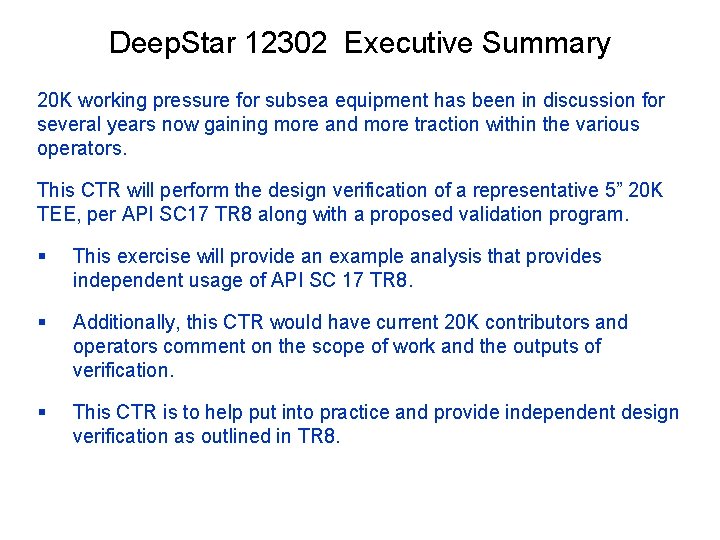
Deep. Star 12302 Executive Summary 20 K working pressure for subsea equipment has been in discussion for several years now gaining more and more traction within the various operators. This CTR will perform the design verification of a representative 5” 20 K TEE, per API SC 17 TR 8 along with a proposed validation program. § This exercise will provide an example analysis that provides independent usage of API SC 17 TR 8. § Additionally, this CTR would have current 20 K contributors and operators comment on the scope of work and the outputs of verification. § This CTR is to help put into practice and provide independent design verification as outlined in TR 8.
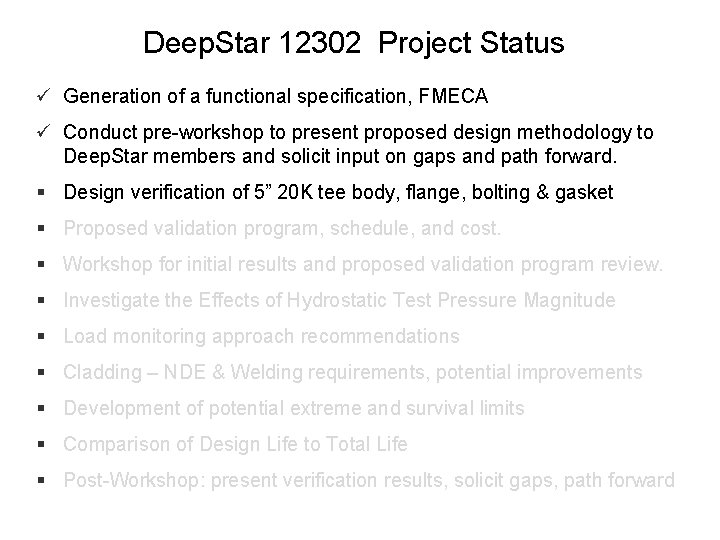
Deep. Star 12302 Project Status ü Generation of a functional specification, FMECA ü Conduct pre-workshop to present proposed design methodology to Deep. Star members and solicit input on gaps and path forward. § Design verification of 5” 20 K tee body, flange, bolting & gasket § Proposed validation program, schedule, and cost. § Workshop for initial results and proposed validation program review. § Investigate the Effects of Hydrostatic Test Pressure Magnitude § Load monitoring approach recommendations § Cladding – NDE & Welding requirements, potential improvements § Development of potential extreme and survival limits § Comparison of Design Life to Total Life § Post-Workshop: present verification results, solicit gaps, path forward
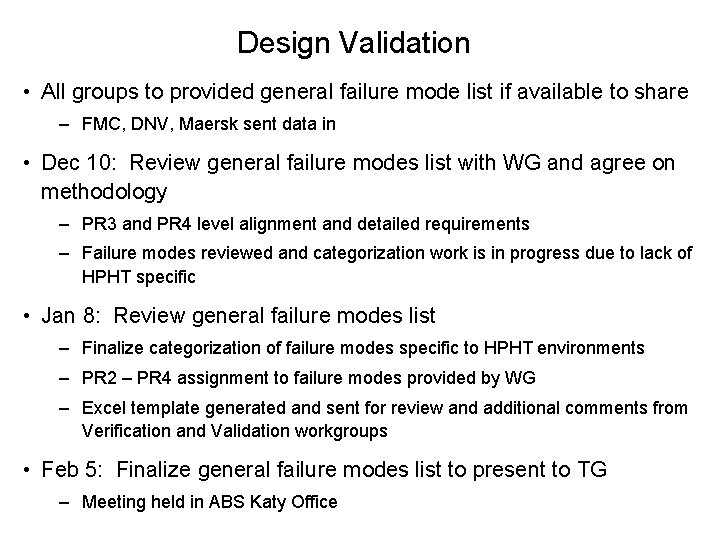
Design Validation • All groups to provided general failure mode list if available to share – FMC, DNV, Maersk sent data in • Dec 10: Review general failure modes list with WG and agree on methodology – PR 3 and PR 4 level alignment and detailed requirements – Failure modes reviewed and categorization work is in progress due to lack of HPHT specific • Jan 8: Review general failure modes list – Finalize categorization of failure modes specific to HPHT environments – PR 2 – PR 4 assignment to failure modes provided by WG – Excel template generated and sent for review and additional comments from Verification and Validation workgroups • Feb 5: Finalize general failure modes list to present to TG – Meeting held in ABS Katy Office
Es ist kalt es ist kalt flocken fallen nieder
Winter kommt winter kommt flocken fallen nieder
Winter kommt winter kommt flocken fallen nieder lied
Nrg oncology semiannual meeting
Nrg oncology conference
Nrg oncology semiannual meeting
Types of meeting
Today meeting or today's meeting
Proposal kickoff meeting agenda
What is meeting and types of meeting
Winter holidays japan
Winter storms facts
Personification sentences
Psa winter soccer
What happens in autum
Fall winter summer spring
Why evergreen trees never lose their leaves question answer