Talents of tomorrow Aerodynamics and aeroelasticity Smart tip
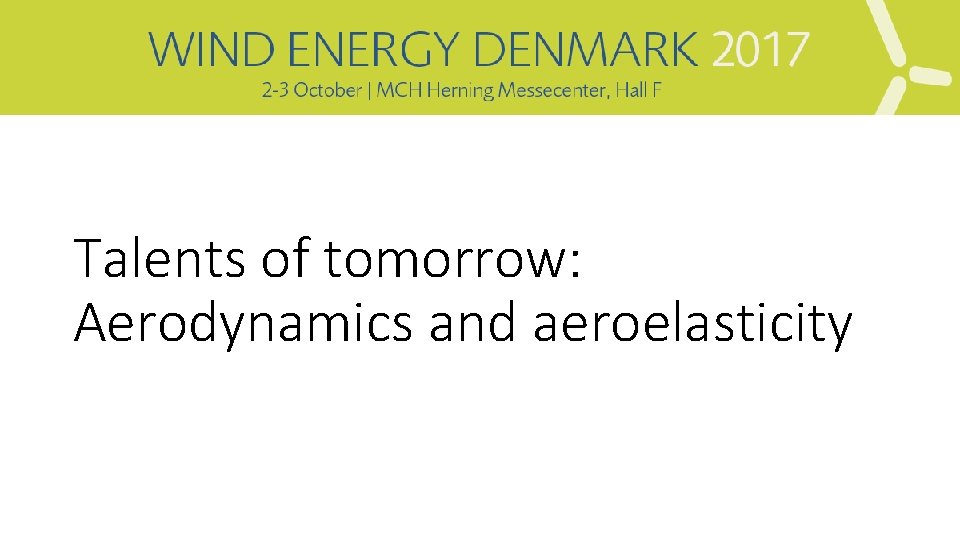
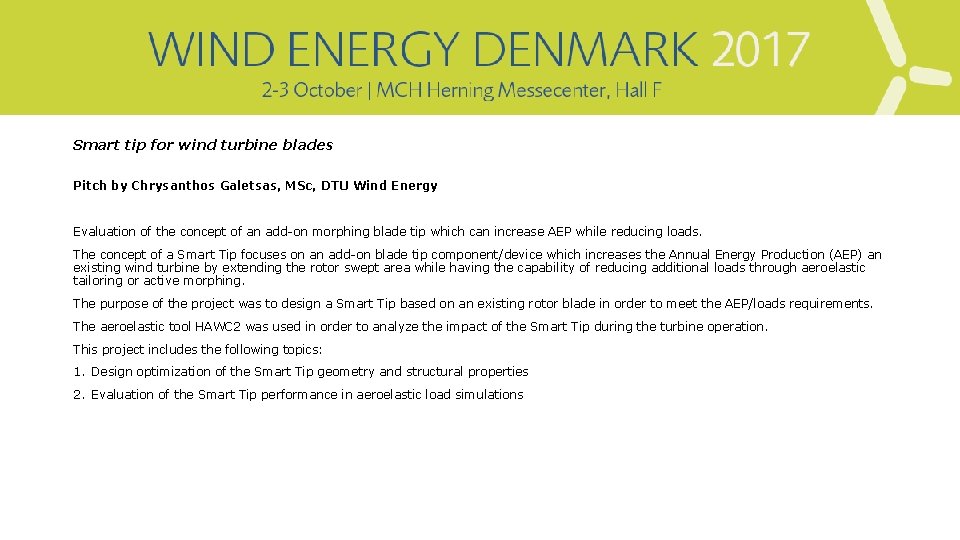
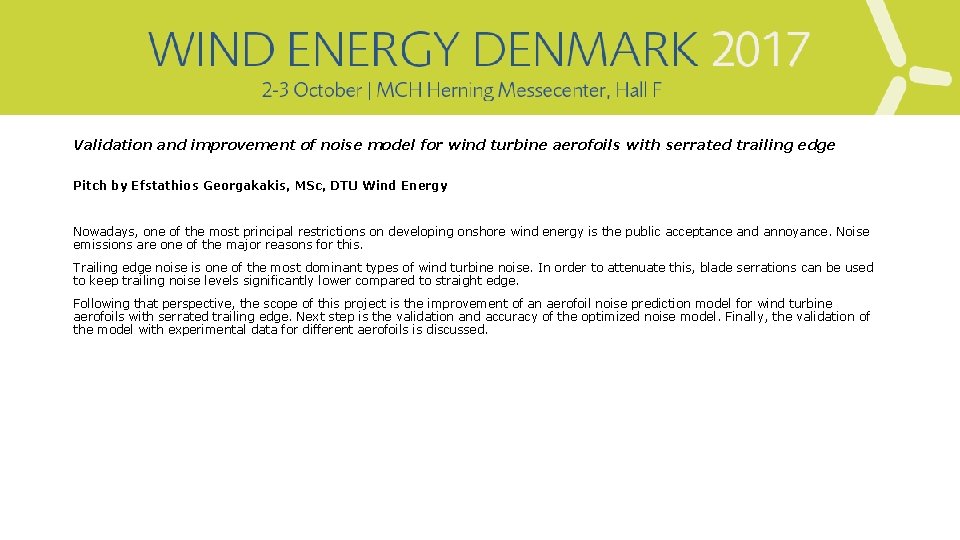
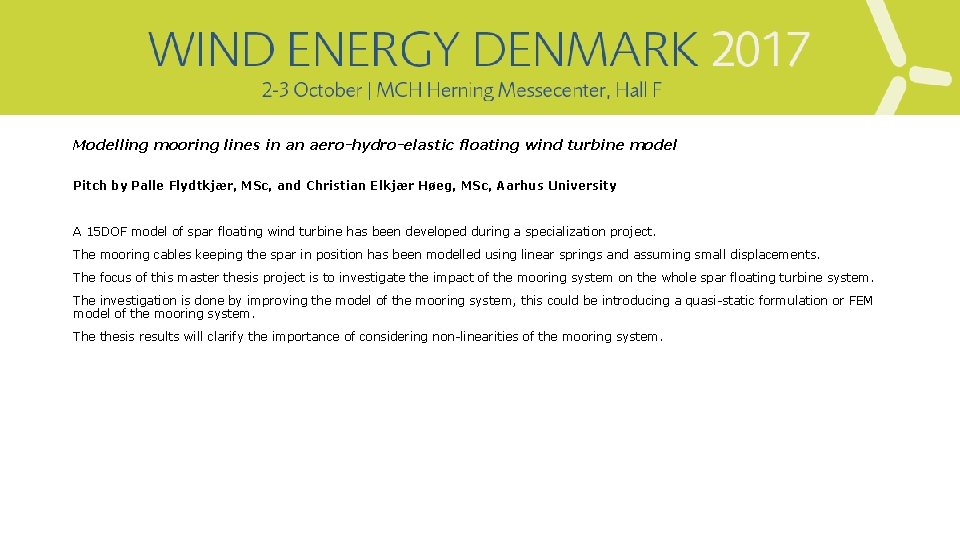
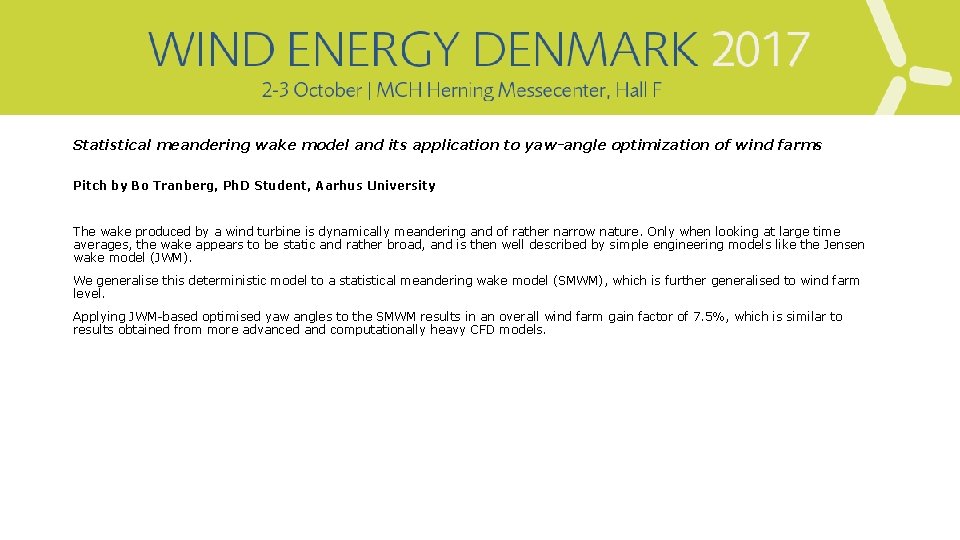
- Slides: 5
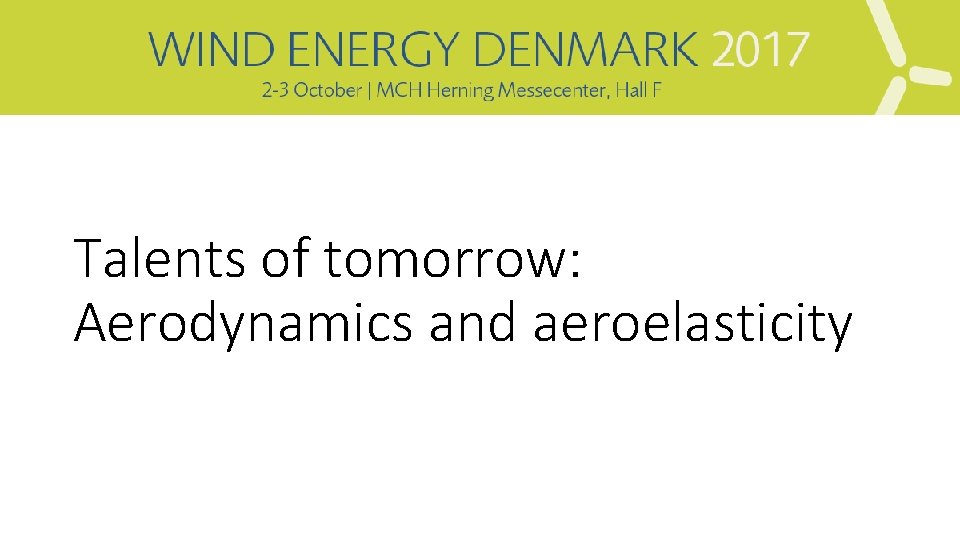
Talents of tomorrow: Aerodynamics and aeroelasticity
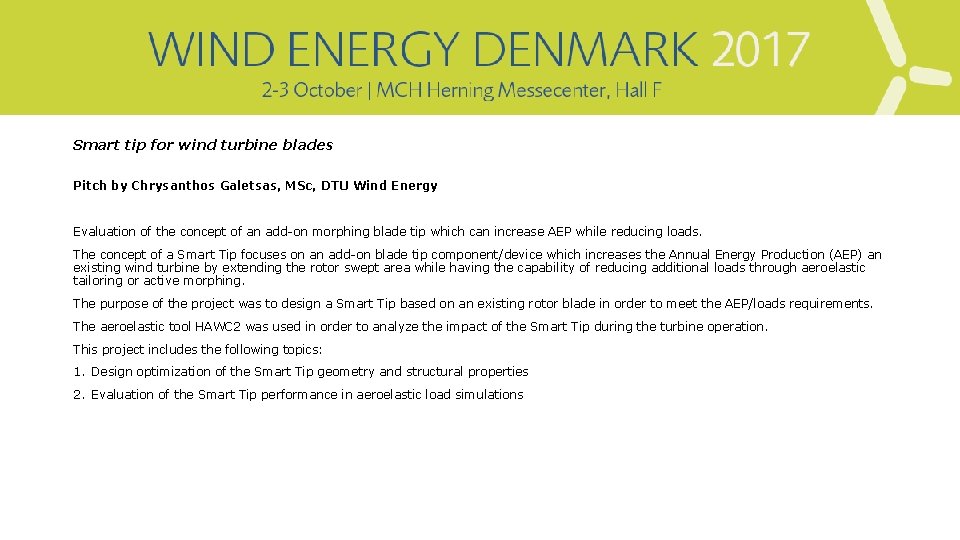
Smart tip for wind turbine blades Pitch by Chrysanthos Galetsas, MSc, DTU Wind Energy Evaluation of the concept of an add-on morphing blade tip which can increase AEP while reducing loads. The concept of a Smart Tip focuses on an add-on blade tip component/device which increases the Annual Energy Production (AEP) an existing wind turbine by extending the rotor swept area while having the capability of reducing additional loads through aeroelastic tailoring or active morphing. The purpose of the project was to design a Smart Tip based on an existing rotor blade in order to meet the AEP/loads requirements. The aeroelastic tool HAWC 2 was used in order to analyze the impact of the Smart Tip during the turbine operation. This project includes the following topics: 1. Design optimization of the Smart Tip geometry and structural properties 2. Evaluation of the Smart Tip performance in aeroelastic load simulations
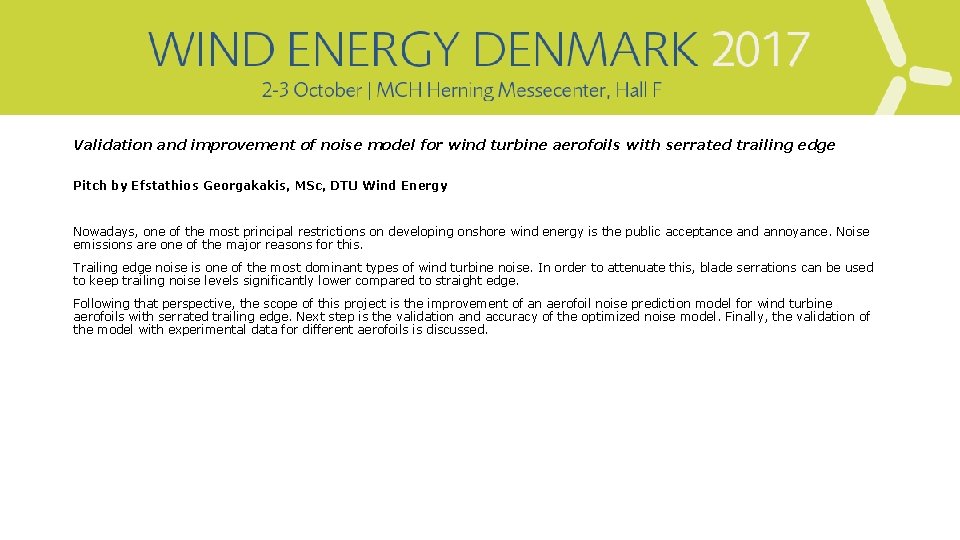
Validation and improvement of noise model for wind turbine aerofoils with serrated trailing edge Pitch by Efstathios Georgakakis, MSc, DTU Wind Energy Nowadays, one of the most principal restrictions on developing onshore wind energy is the public acceptance and annoyance. Noise emissions are one of the major reasons for this. Trailing edge noise is one of the most dominant types of wind turbine noise. In order to attenuate this, blade serrations can be used to keep trailing noise levels significantly lower compared to straight edge. Following that perspective, the scope of this project is the improvement of an aerofoil noise prediction model for wind turbine aerofoils with serrated trailing edge. Next step is the validation and accuracy of the optimized noise model. Finally, the validation of the model with experimental data for different aerofoils is discussed.
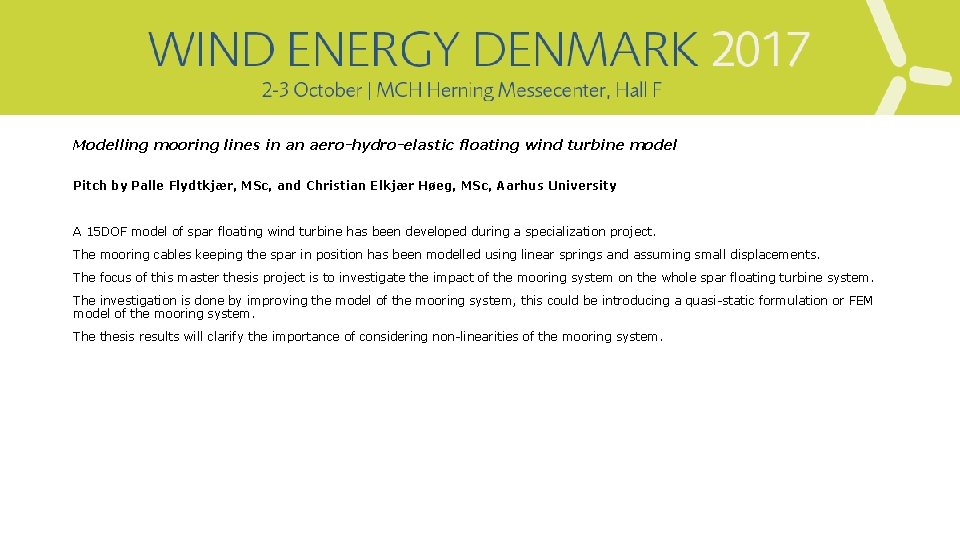
Modelling mooring lines in an aero-hydro-elastic floating wind turbine model Pitch by Palle Flydtkjær, MSc, and Christian Elkjær Høeg, MSc, Aarhus University A 15 DOF model of spar floating wind turbine has been developed during a specialization project. The mooring cables keeping the spar in position has been modelled using linear springs and assuming small displacements. The focus of this master thesis project is to investigate the impact of the mooring system on the whole spar floating turbine system. The investigation is done by improving the model of the mooring system, this could be introducing a quasi-static formulation or FEM model of the mooring system. The thesis results will clarify the importance of considering non-linearities of the mooring system.
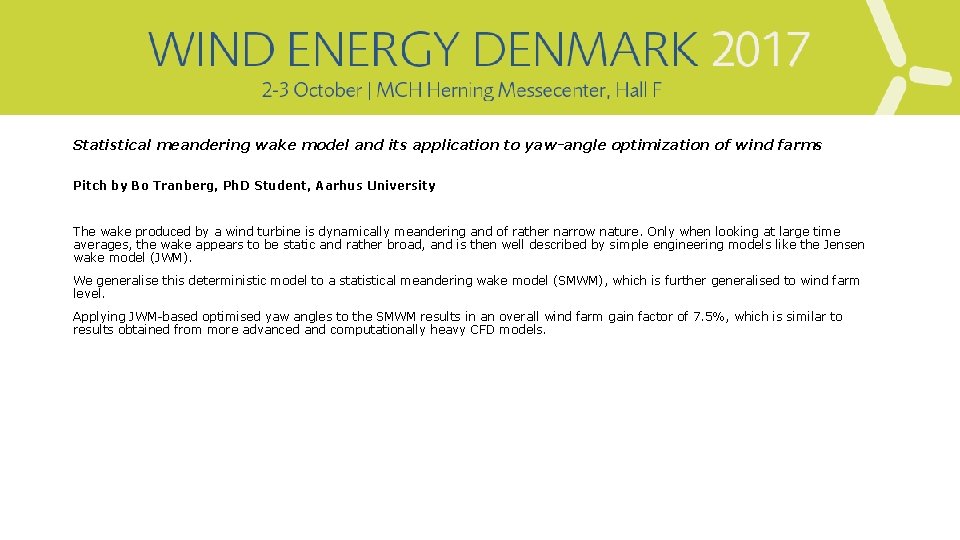
Statistical meandering wake model and its application to yaw-angle optimization of wind farms Pitch by Bo Tranberg, Ph. D Student, Aarhus University The wake produced by a wind turbine is dynamically meandering and of rather narrow nature. Only when looking at large time averages, the wake appears to be static and rather broad, and is then well described by simple engineering models like the Jensen wake model (JWM). We generalise this deterministic model to a statistical meandering wake model (SMWM), which is further generalised to wind farm level. Applying JWM-based optimised yaw angles to the SMWM results in an overall wind farm gain factor of 7. 5%, which is similar to results obtained from more advanced and computationally heavy CFD models.