Support Systems TITLE Manager APPLYING SMED PRINCIPLES TO
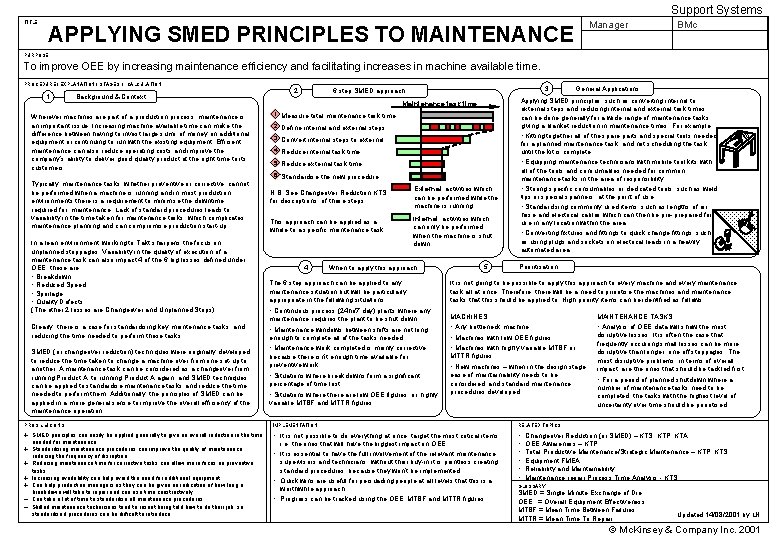
- Slides: 1
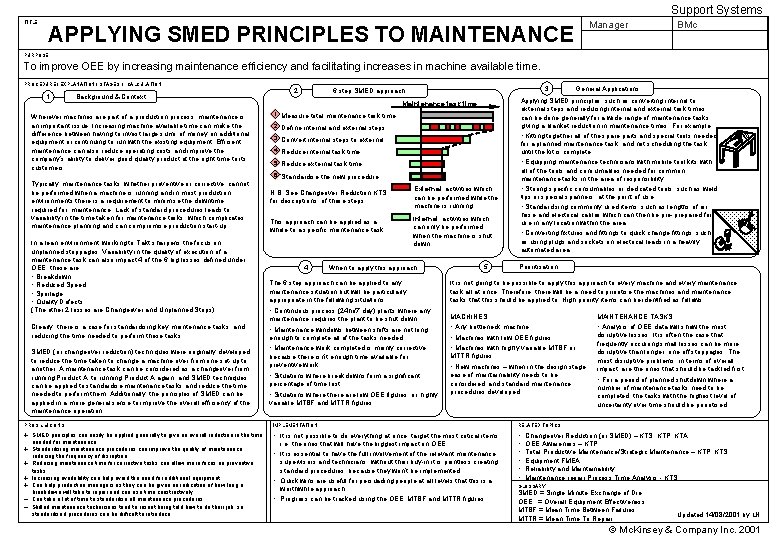
Support Systems TITLE Manager APPLYING SMED PRINCIPLES TO MAINTENANCE BMc PURPOSE To improve OEE by increasing maintenance efficiency and facilitating increases in machine available time. PROCEDURE / EXPLANATION / STAGES or CALCULATION 1 Background & Context Wherever machines are part of a production process, maintenance is an important issue. Increasing machine available time can make the difference between having to invest large sums of money on additional equipment or continuing to run with the existing equipment. Efficient maintenance can also reduce operating costs and improve the company’s ability to deliver good quality product at the right time to its customers. Typically, maintenance tasks, whether preventive or corrective, cannot be performed when a machine is running and in most production environments there is a requirement to minimise the downtime required for maintenance. Lack of standard procedures leads to variability in the time taken for maintenance tasks, which complicates maintenance planning and can compromise production start-up. In a lean environment, working to Takt sharpens the focus on unplanned stoppages. Variability in the quality of execution of a maintenance task can also impact 4 of the 6 big losses defined under OEE, these are: • Breakdown • Reduced Speed • Spoilage • Quality Defects (The other 2 losses are Changeover and Unplanned Stops). Clearly, there is a case for standardising key maintenance tasks, and reducing the time needed to perform these tasks. SMED (or changeover reduction) techniques were originally developed to reduce the time taken to change a machine over from one set-up to another. A maintenance task can be considered as a changeover from running Product A to running Product A again, and SMED techniques can be applied to standardise maintenance tasks and reduce the time needed to perform them. Additionally, the principles of SMED can be applied in a more general sense to improve the overall efficiency of the maintenance operation. 2 3 6 step SMED approach Maintenance task time 1 Measure total maintenance task time 2 Define internal and external steps 3 Convert internal steps to external 4 Reduce internal task time 5 Reduce external task time 6 Standardise the new procedure N. B. See Changeover Reduction KTS for descriptions of these steps External: activities which can be performed while the machine is running This approach can be applied as a whole to a specific maintenance task. Internal: activities which can only be performed when the machine is shut down 4 When to apply this approach The 6 step approach can be applied to any maintenance situation but will be particularly appropriate in the following situations: • Continuous process (24 hr/7 day) plants where any maintenance requires the plant to be shut down • Maintenance windows between shifts are not long enough to complete all of the tasks needed • Maintenance work completed is mainly corrective because there isn’t enough time available for preventive work • Situations where breakdowns form a significant percentage of time lost • Situations where there are low OEE figures, or highly variable MTBF and MTTR figures 5 Prioritisation It is not going to be possible to apply this approach to every machine and every maintenance task all at once. Therefore, there will be a need to prioritise the machines and maintenance tasks that this should be applied to. High priority items can be identified as follows: MACHINES MAINTENANCE TASKS • Any bottleneck machine • Machines with low OEE figures • Machines with highly variable MTBF or • Analysis of OEE data will show the most MTTR figures • New machines – when in the design stage, ease of maintainability needs to be considered, and standard maintenance procedures developed. PROS and CONS IMPLEMENTATION RELATED TOPICS + SMED principles can easily be applied generally to give an overall reduction in the time • It is not possible to do everything at once, target the most critical items • • • needed for maintenance. + Standardising maintenance procedures can improve the quality of maintenance, reducing the frequency of disruption. + Reducing maintenance time for corrective tasks can allow more focus on preventive tasks. + Increasing availability can help avoid the need for additional equipment. + Can help production managers as they can be given an indication of how long a breakdown will take to repair and can use time constructively – Can take a lot of time to standardise all maintenance procedures. – Skilled maintenance technicians tend to resent being told how to do their job, so standardised procedures can be difficult to introduce. General Applications Applying SMED principles, such as converting internal to external steps and reducing internal and external task times, can be done generally for a wide range of maintenance tasks, giving a blanket reduction in maintenance times. For example: • Kitting together all of the spare parts and special tools needed for a planned maintenance task, and not scheduling the task until the kit is complete. • Equipping maintenance technicians with mobile tool kits with all of the tools and consumables needed for common maintenance tasks in the area of responsibility. • Storing specific consumables or dedicated tools, such as weld tips or special spanners, at the point of use. • Standardising commonly used items, such as lengths of air hose and electrical cables which can then be pre-prepared for use in any location within the area. • Converting fixtures and fittings to quick change fittings, such as using plugs and sockets on electrical leads in a heavily automated area. i. e. the ones that will have the biggest impact on OEE. • It is essential to have the full involvement of the relevant maintenance supervisors and technicians, without their buy-in it is pointless creating standard procedures, because they won’t be implemented. • Quick wins are useful for persuading people at all levels that this is a worthwhile approach. • Progress can be tracked using the OEE, MTBF and MTTR figures. disruptive losses. It is often the case that frequently occurring small losses can be more disruptive than longer, one-off stoppages. The most disruptive problems, in terms of overall impact, are the ones that should be tackled first. • For a period of planned shutdown where a number of maintenance tasks need to be completed, the tasks with the highest level of uncertainty over time should be prioritised. Changeover Reduction (or SMED) – KTS, KTP, KTA OEE Awareness – KTP Total Productive Maintenance/Strategic Maintenance – KTP, KTS Equipment FMEA Reliability and Maintainability Maintenance repair Process Time Analysis - KTS GLOSSARY SMED = Single Minute Exchange of Die OEE = Overall Equipment Effectiveness MTBF = Mean Time Between Failures MTTR = Mean Time To Repair Updated 14/08/2001 by LN © Mc. Kinsey & Company Inc. 2001