Silica fume 1 fine microcrystalline silica produced in
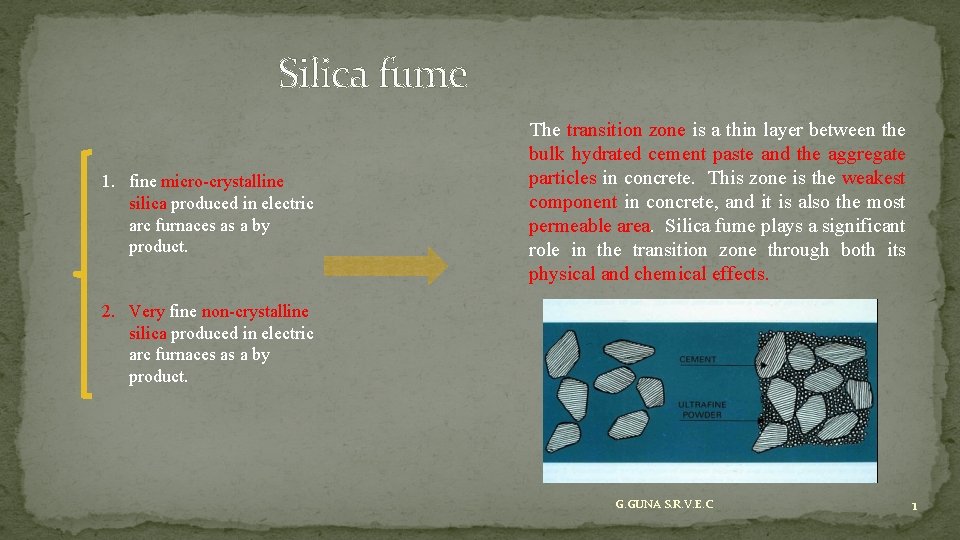
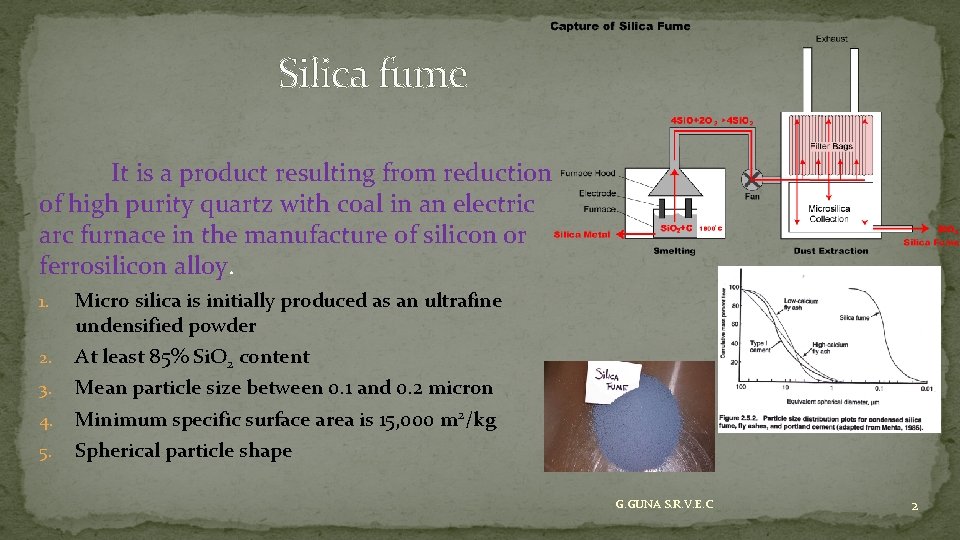
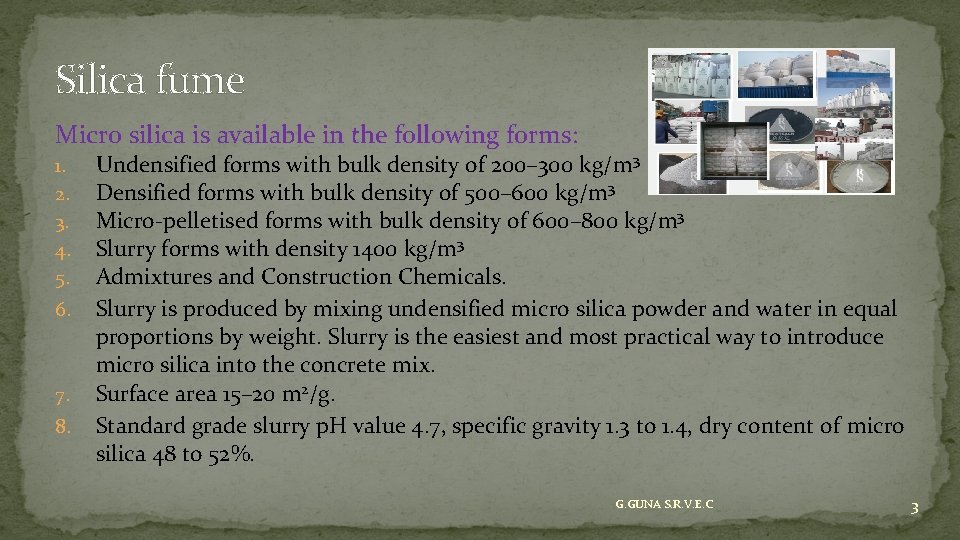
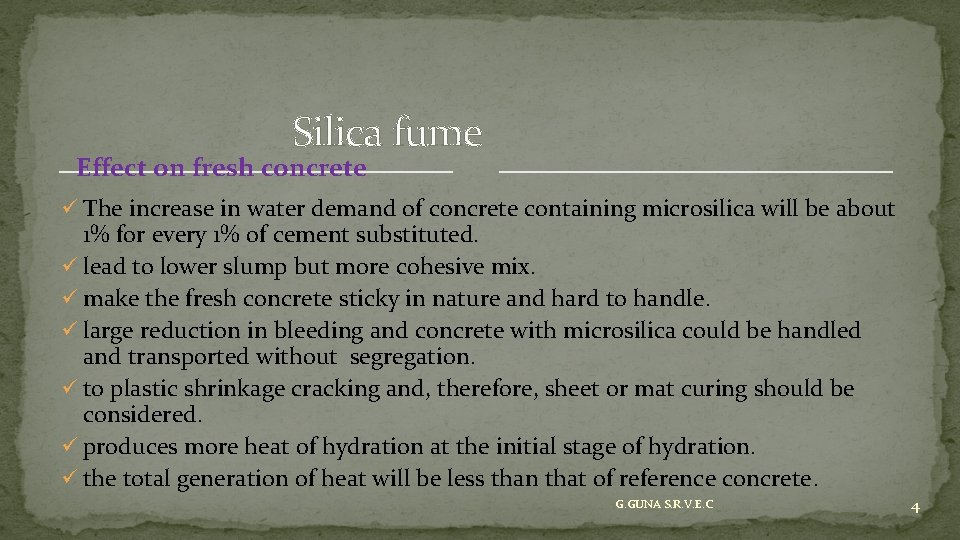
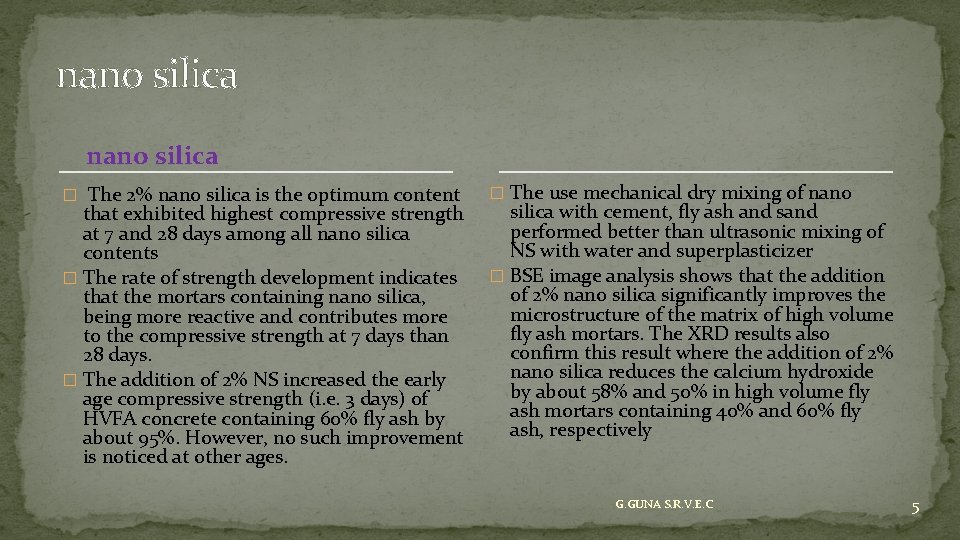
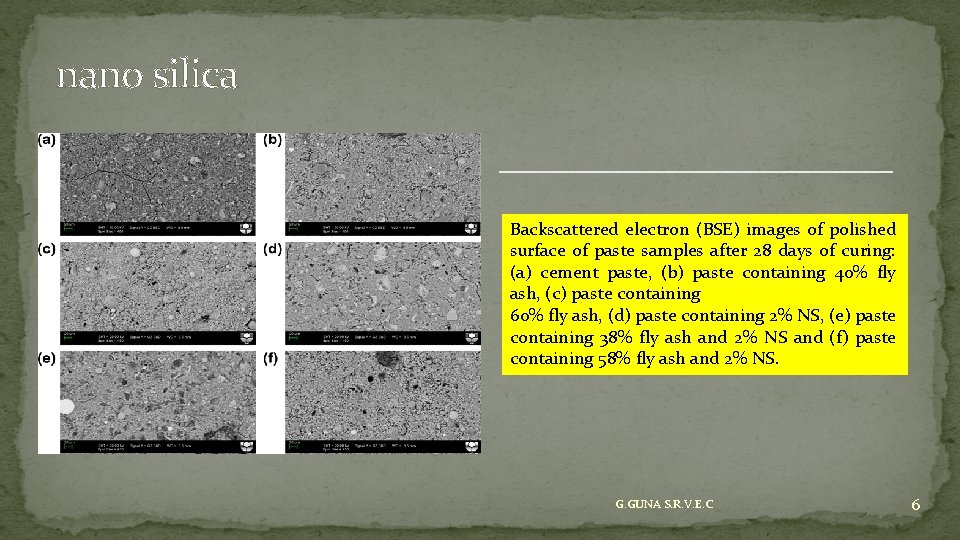
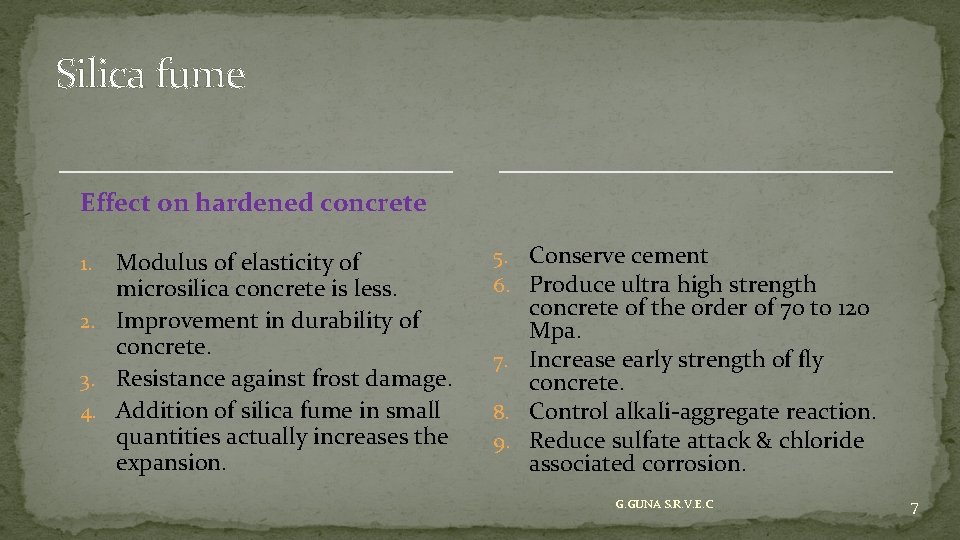
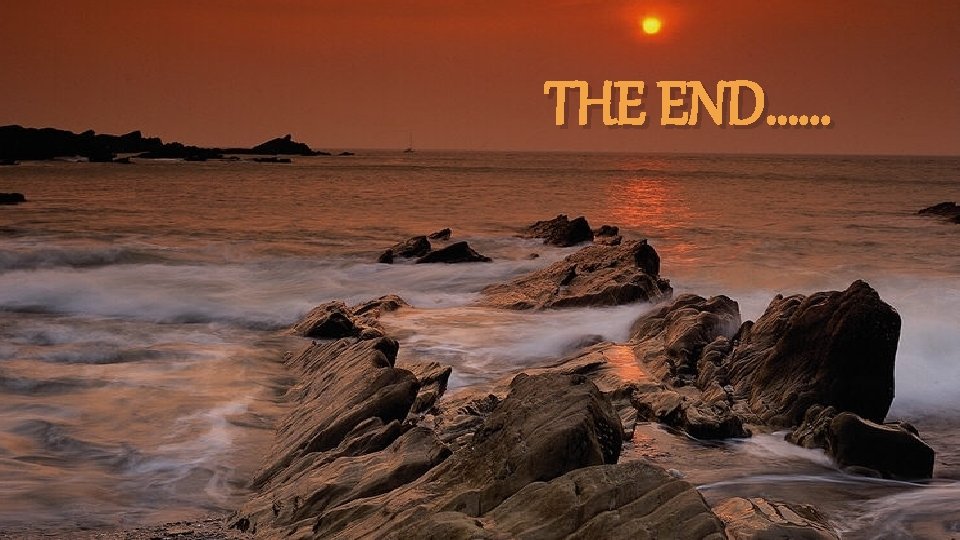
- Slides: 8
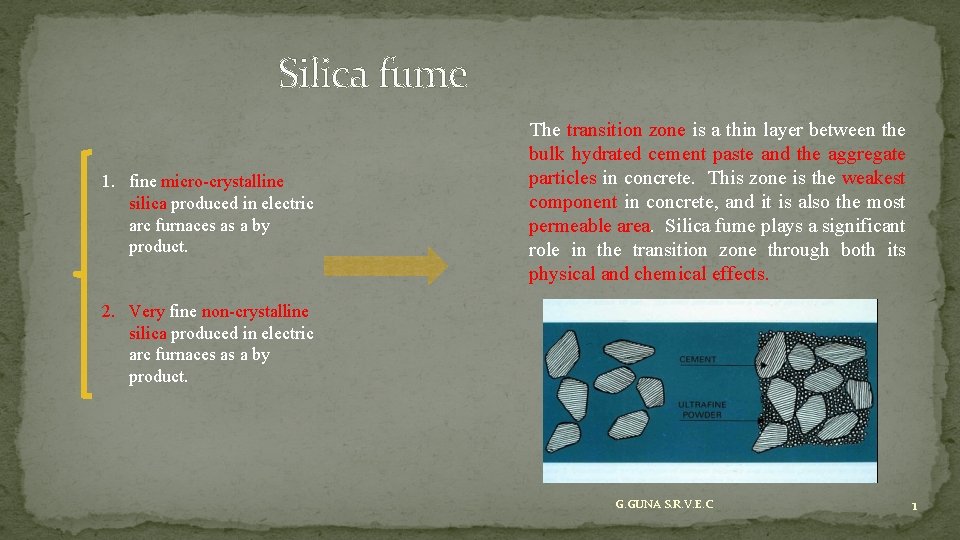
Silica fume 1. fine micro-crystalline silica produced in electric arc furnaces as a by product. The transition zone is a thin layer between the bulk hydrated cement paste and the aggregate particles in concrete. This zone is the weakest component in concrete, and it is also the most permeable area. Silica fume plays a significant role in the transition zone through both its physical and chemical effects. 2. Very fine non-crystalline silica produced in electric arc furnaces as a by product. G. GUNA S. R. V. E. C 1
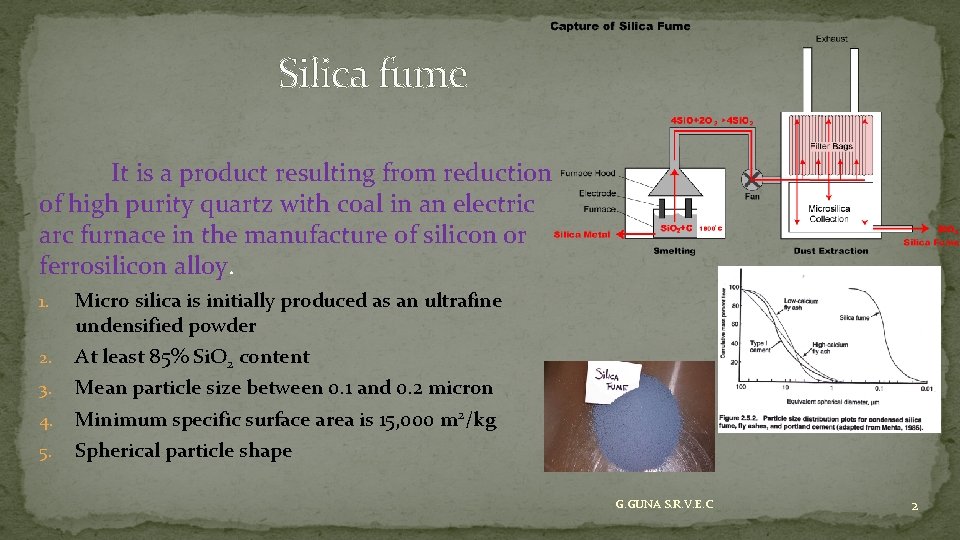
Silica fume It is a product resulting from reduction of high purity quartz with coal in an electric arc furnace in the manufacture of silicon or ferrosilicon alloy. 1. 2. 3. 4. 5. Micro silica is initially produced as an ultrafine undensified powder At least 85% Si. O 2 content Mean particle size between 0. 1 and 0. 2 micron Minimum specific surface area is 15, 000 m 2/kg Spherical particle shape G. GUNA S. R. V. E. C 2
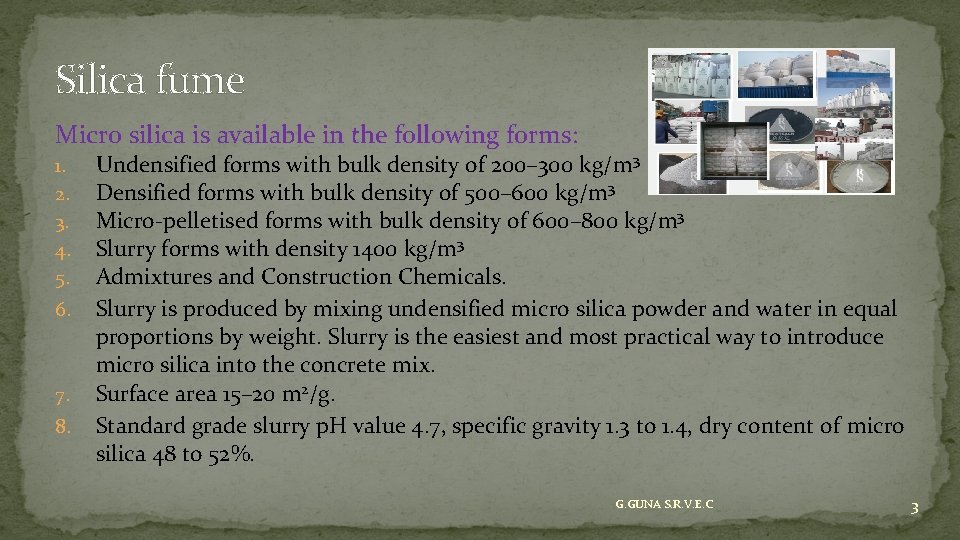
Silica fume Micro silica is available in the following forms: 1. 2. 3. 4. 5. 6. 7. 8. Undensified forms with bulk density of 200– 300 kg/m 3 Densified forms with bulk density of 500– 600 kg/m 3 Micro-pelletised forms with bulk density of 600– 800 kg/m 3 Slurry forms with density 1400 kg/m 3 Admixtures and Construction Chemicals. Slurry is produced by mixing undensified micro silica powder and water in equal proportions by weight. Slurry is the easiest and most practical way to introduce micro silica into the concrete mix. Surface area 15– 20 m 2/g. Standard grade slurry p. H value 4. 7, specific gravity 1. 3 to 1. 4, dry content of micro silica 48 to 52%. G. GUNA S. R. V. E. C 3
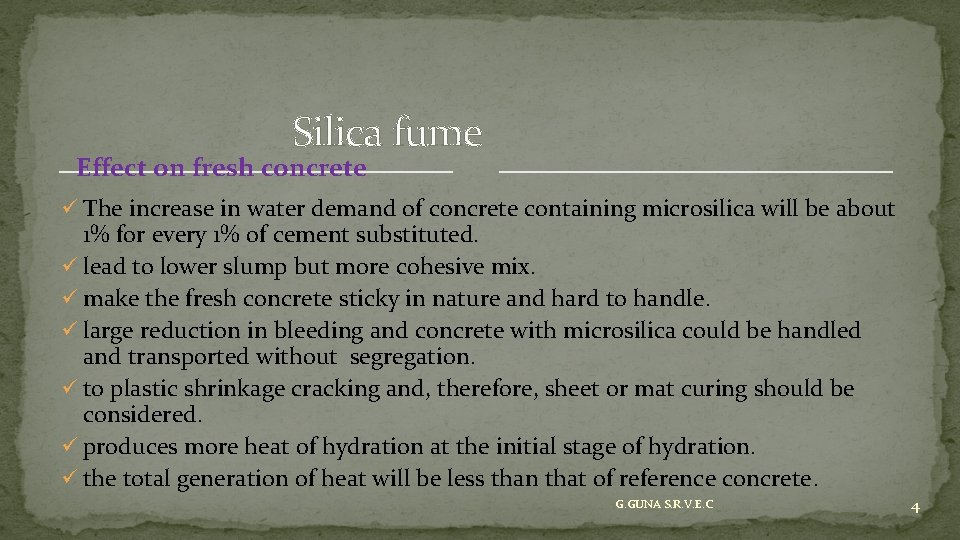
Silica fume Effect on fresh concrete ü The increase in water demand of concrete containing microsilica will be about 1% for every 1% of cement substituted. ü lead to lower slump but more cohesive mix. ü make the fresh concrete sticky in nature and hard to handle. ü large reduction in bleeding and concrete with microsilica could be handled and transported without segregation. ü to plastic shrinkage cracking and, therefore, sheet or mat curing should be considered. ü produces more heat of hydration at the initial stage of hydration. ü the total generation of heat will be less than that of reference concrete. G. GUNA S. R. V. E. C 4
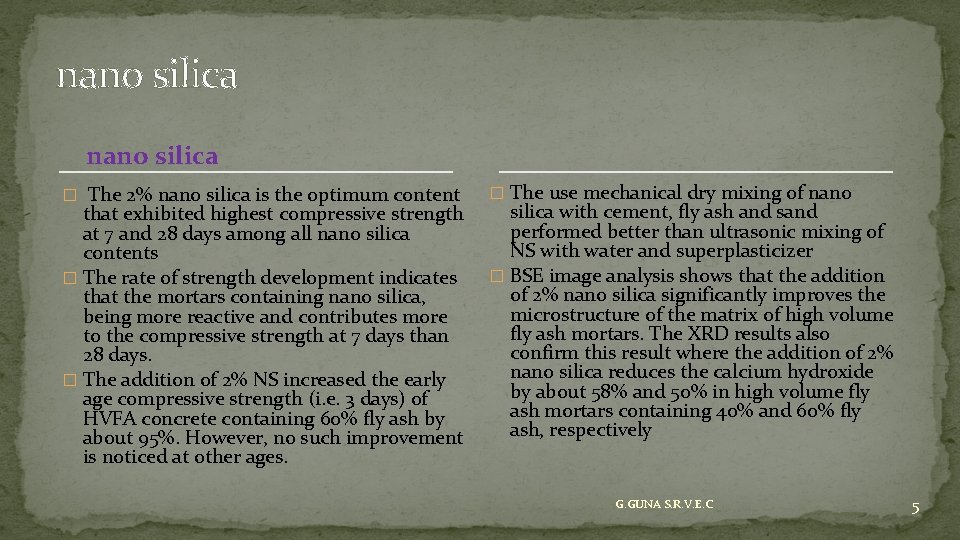
nano silica � The 2% nano silica is the optimum content that exhibited highest compressive strength at 7 and 28 days among all nano silica contents � The rate of strength development indicates that the mortars containing nano silica, being more reactive and contributes more to the compressive strength at 7 days than 28 days. � The addition of 2% NS increased the early age compressive strength (i. e. 3 days) of HVFA concrete containing 60% fly ash by about 95%. However, no such improvement is noticed at other ages. � The use mechanical dry mixing of nano silica with cement, fly ash and sand performed better than ultrasonic mixing of NS with water and superplasticizer � BSE image analysis shows that the addition of 2% nano silica significantly improves the microstructure of the matrix of high volume fly ash mortars. The XRD results also confirm this result where the addition of 2% nano silica reduces the calcium hydroxide by about 58% and 50% in high volume fly ash mortars containing 40% and 60% fly ash, respectively G. GUNA S. R. V. E. C 5
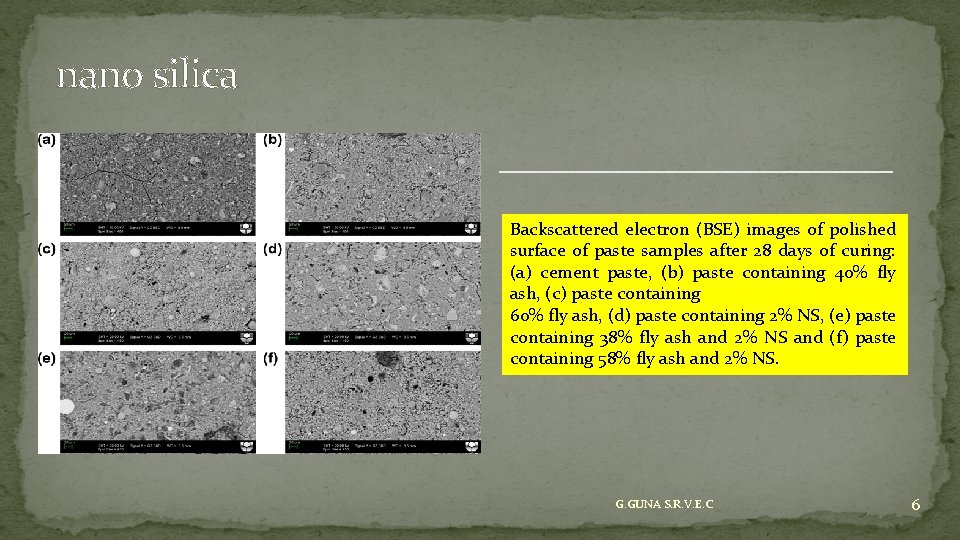
nano silica Backscattered electron (BSE) images of polished surface of paste samples after 28 days of curing: (a) cement paste, (b) paste containing 40% fly ash, (c) paste containing 60% fly ash, (d) paste containing 2% NS, (e) paste containing 38% fly ash and 2% NS and (f) paste containing 58% fly ash and 2% NS. G. GUNA S. R. V. E. C 6
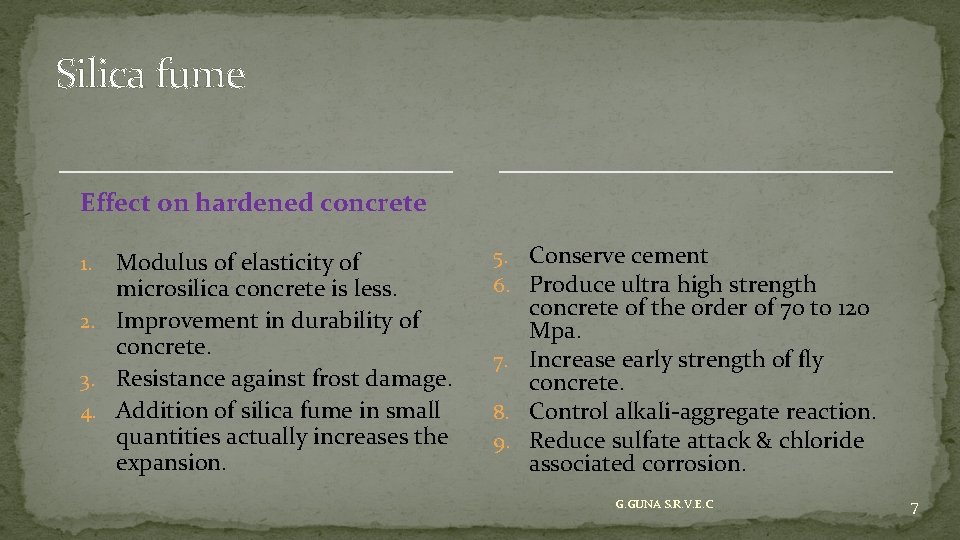
Silica fume Effect on hardened concrete Modulus of elasticity of microsilica concrete is less. 2. Improvement in durability of concrete. 3. Resistance against frost damage. 4. Addition of silica fume in small quantities actually increases the expansion. 1. 5. Conserve cement 6. Produce ultra high strength concrete of the order of 70 to 120 Mpa. 7. Increase early strength of fly concrete. 8. Control alkali-aggregate reaction. 9. Reduce sulfate attack & chloride associated corrosion. G. GUNA S. R. V. E. C 7
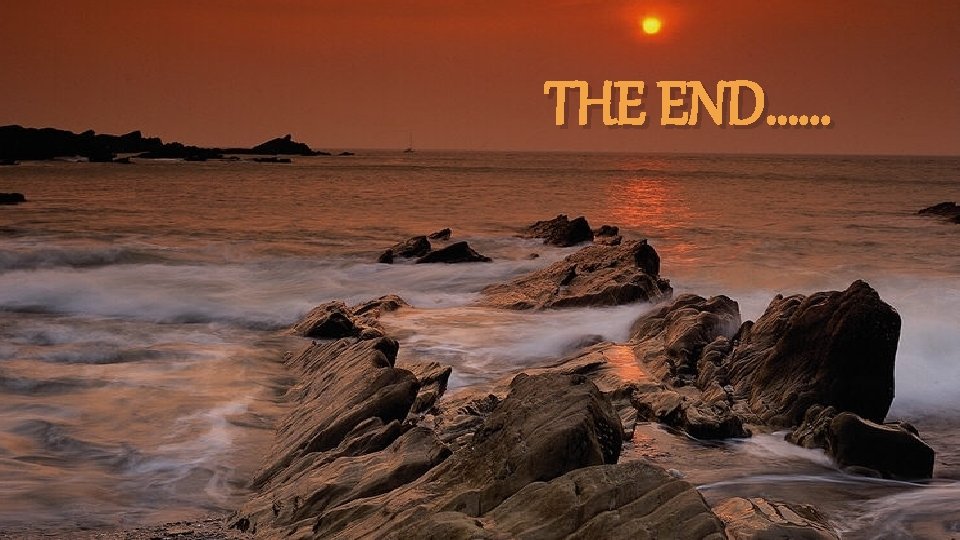
THE END…… G. GUNA S. R. V. E. C 8