Scaling Up of 3 D Printed Castings Team
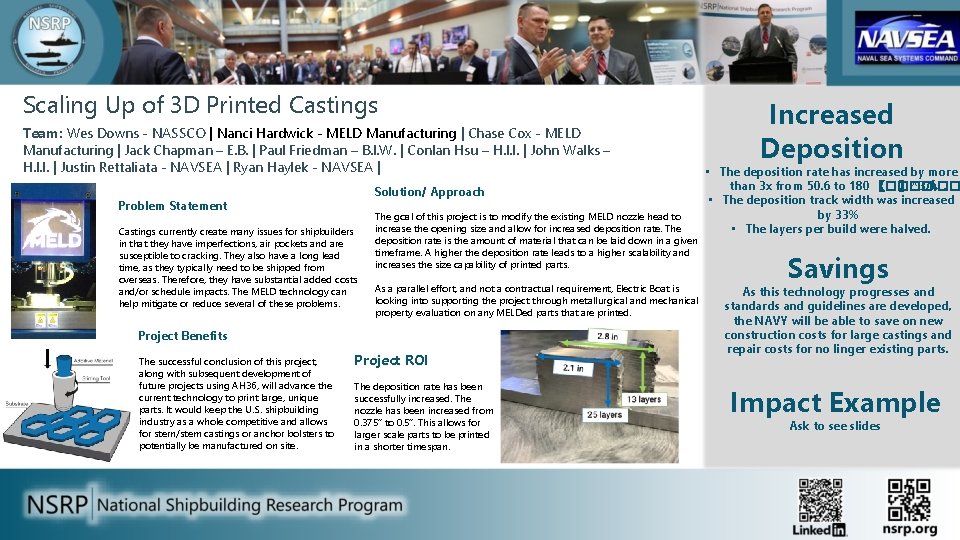
- Slides: 1
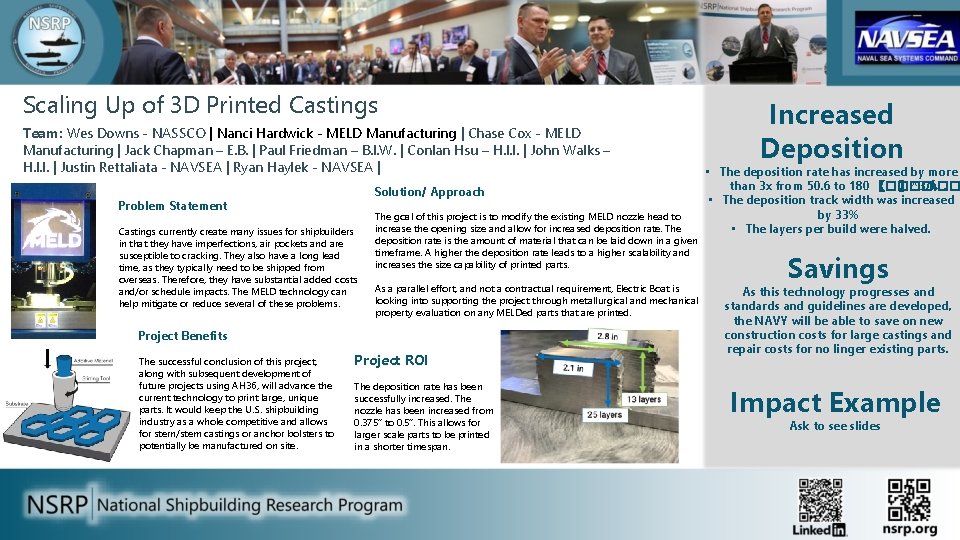
Scaling Up of 3 D Printed Castings Team: Wes Downs - NASSCO | Nanci Hardwick - MELD Manufacturing | Chase Cox - MELD Manufacturing | Jack Chapman – E. B. | Paul Friedman – B. I. W. | Conlan Hsu – H. I. I. | John Walks – H. I. I. | Justin Rettaliata - NAVSEA | Ryan Haylek - NAVSEA | Solution/ Approach Problem Statement Castings currently create many issues for shipbuilders in that they have imperfections, air pockets and are susceptible to cracking. They also have a long lead time, as they typically need to be shipped from overseas. Therefore, they have substantial added costs and/or schedule impacts. The MELD technology can help mitigate or reduce several of these problems. The goal of this project is to modify the existing MELD nozzle head to increase the opening size and allow for increased deposition rate. The deposition rate is the amount of material that can be laid down in a given timeframe. A higher the deposition rate leads to a higher scalability and increases the size capability of printed parts. As a parallel effort, and not a contractual requirement, Electric Boat is looking into supporting the project through metallurgical and mechanical property evaluation on any MELDed parts that are printed. Project Benefits The successful conclusion of this project, along with subsequent development of future projects using AH 36, will advance the current technology to print large, unique parts. It would keep the U. S. shipbuilding industry as a whole competitive and allows for stern/stem castings or anchor bolsters to potentially be manufactured on site. Project ROI The deposition rate has been successfully increased. The nozzle has been increased from 0. 375” to 0. 5”. This allows for larger scale parts to be printed in a shorter timespan. Increased Deposition • The deposition rate has increased by more than 3 x from 50. 6 to 180 〖���� 〗^3/ℎ��. • The deposition track width was increased by 33% • The layers per build were halved. Savings As this technology progresses and standards and guidelines are developed, the NAVY will be able to save on new construction costs for large castings and repair costs for no linger existing parts. Impact Example Ask to see slides