Refill Friction Stir Spot Welding of Magnesium AZ
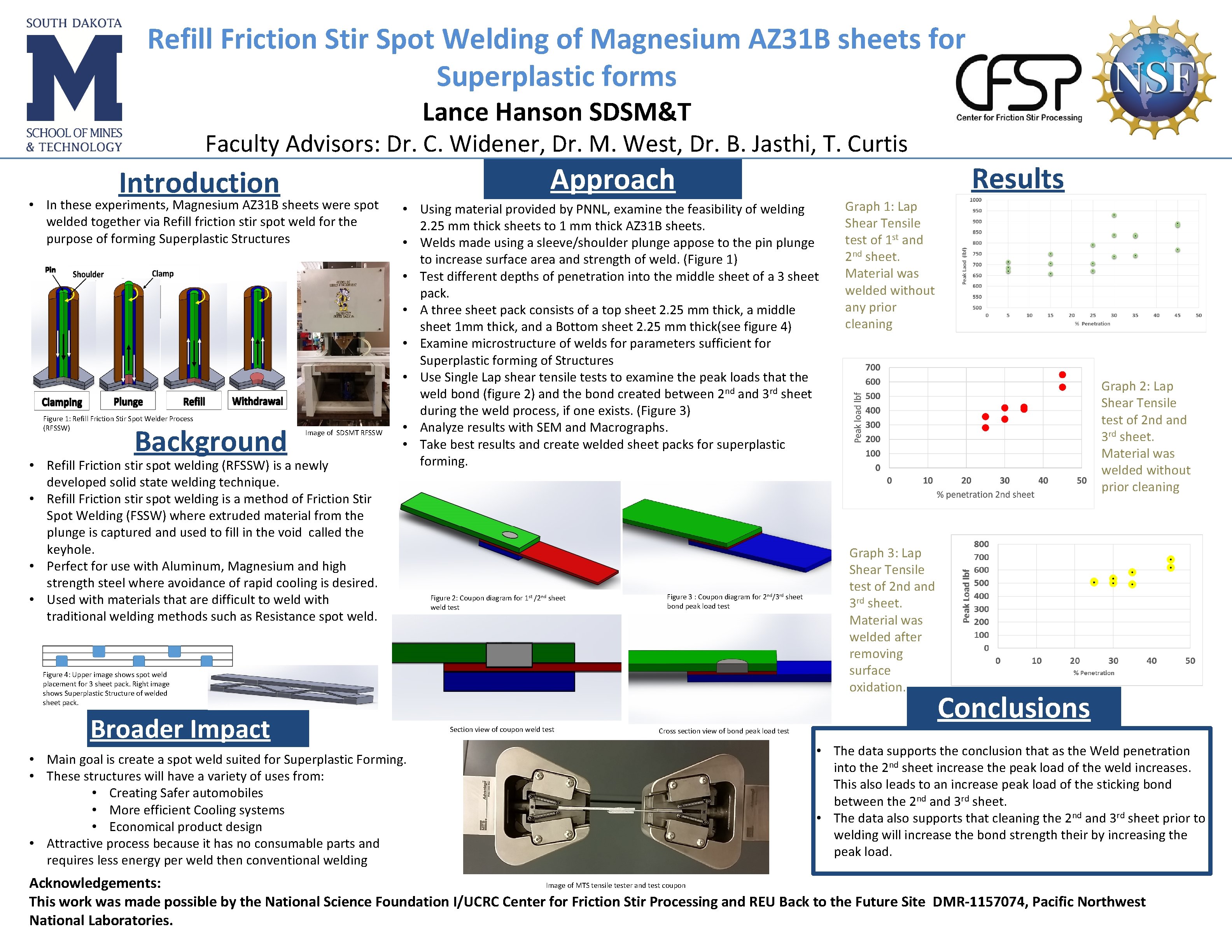
- Slides: 1
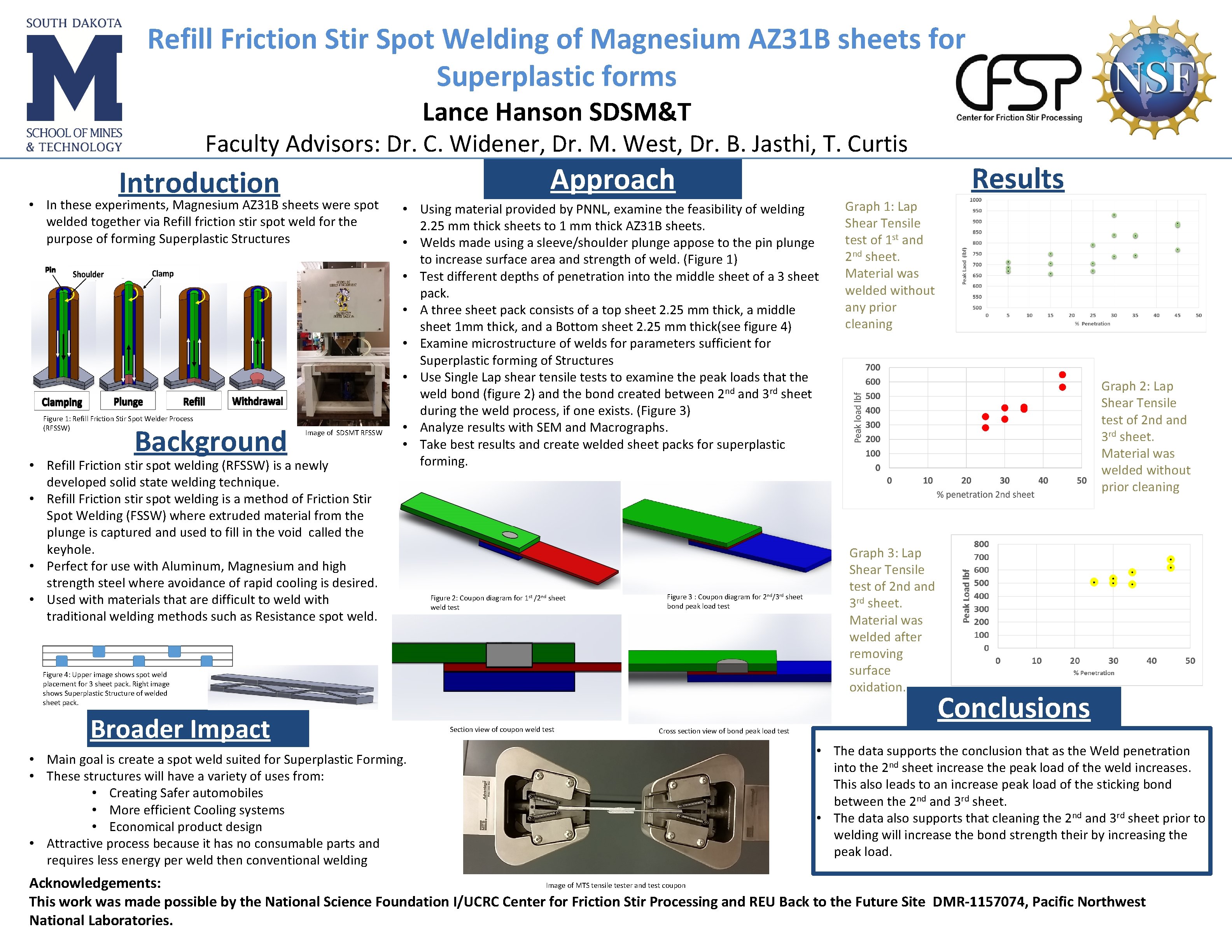
Refill Friction Stir Spot Welding of Magnesium AZ 31 B sheets for Superplastic forms Lance Hanson SDSM&T Faculty Advisors: Dr. C. Widener, Dr. M. West, Dr. B. Jasthi, T. Curtis Introduction • In these experiments, Magnesium AZ 31 B sheets were spot welded together via Refill friction stir spot weld for the purpose of forming Superplastic Structures Figure 1: Refill Friction Stir Spot Welder Process (RFSSW) Background Image of SDSMT RFSSW • Refill Friction stir spot welding (RFSSW) is a newly developed solid state welding technique. • Refill Friction stir spot welding is a method of Friction Stir Spot Welding (FSSW) where extruded material from the plunge is captured and used to fill in the void called the keyhole. • Perfect for use with Aluminum, Magnesium and high strength steel where avoidance of rapid cooling is desired. • Used with materials that are difficult to weld with traditional welding methods such as Resistance spot weld. Approach • Using material provided by PNNL, examine the feasibility of welding 2. 25 mm thick sheets to 1 mm thick AZ 31 B sheets. • Welds made using a sleeve/shoulder plunge appose to the pin plunge to increase surface area and strength of weld. (Figure 1) • Test different depths of penetration into the middle sheet of a 3 sheet pack. • A three sheet pack consists of a top sheet 2. 25 mm thick, a middle sheet 1 mm thick, and a Bottom sheet 2. 25 mm thick(see figure 4) • Examine microstructure of welds for parameters sufficient for Superplastic forming of Structures • Use Single Lap shear tensile tests to examine the peak loads that the weld bond (figure 2) and the bond created between 2 nd and 3 rd sheet during the weld process, if one exists. (Figure 3) • Analyze results with SEM and Macrographs. • Take best results and create welded sheet packs for superplastic forming. Figure 2: Coupon diagram for 1 st /2 nd sheet weld test Figure 3 : Coupon diagram for 2 nd/3 rd sheet bond peak load test Figure 4: Upper image shows spot weld placement for 3 sheet pack. Right image shows Superplastic Structure of welded sheet pack. Broader Impact • Main goal is create a spot weld suited for Superplastic Forming. • These structures will have a variety of uses from: • Creating Safer automobiles • More efficient Cooling systems • Economical product design • Attractive process because it has no consumable parts and requires less energy per weld then conventional welding Section view of coupon weld test Results Graph 1: Lap Shear Tensile test of 1 st and 2 nd sheet. Material was welded without any prior cleaning Graph 2: Lap Shear Tensile test of 2 nd and 3 rd sheet. Material was welded without prior cleaning Graph 3: Lap Shear Tensile test of 2 nd and 3 rd sheet. Material was welded after removing surface oxidation. Conclusions Cross section view of bond peak load test • The data supports the conclusion that as the Weld penetration into the 2 nd sheet increase the peak load of the weld increases. This also leads to an increase peak load of the sticking bond between the 2 nd and 3 rd sheet. • The data also supports that cleaning the 2 nd and 3 rd sheet prior to welding will increase the bond strength their by increasing the peak load. Image of MTS tensile tester and test coupon Acknowledgements: This work was made possible by the National Science Foundation I/UCRC Center for Friction Stir Processing and REU Back to the Future Site DMR-1157074, Pacific Northwest National Laboratories.