Xenon Detector Status Report Xenon Detector Group Contents
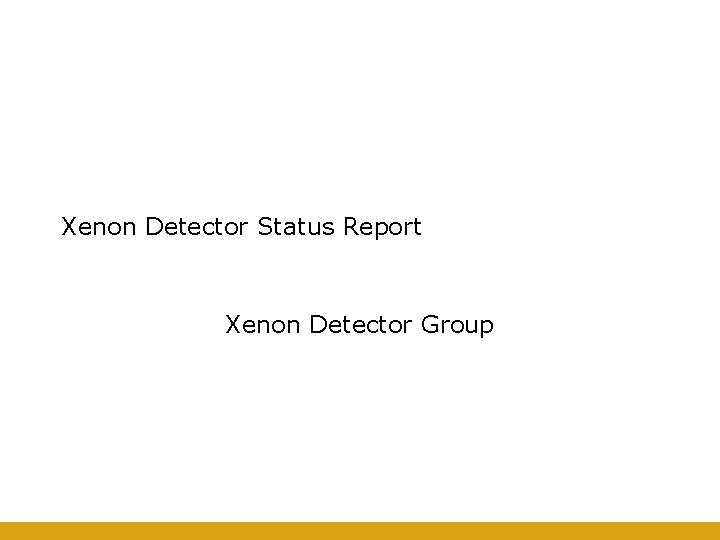
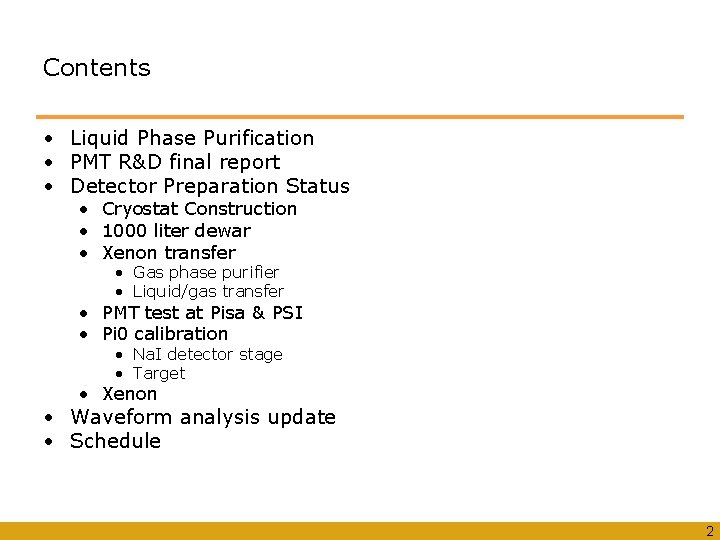
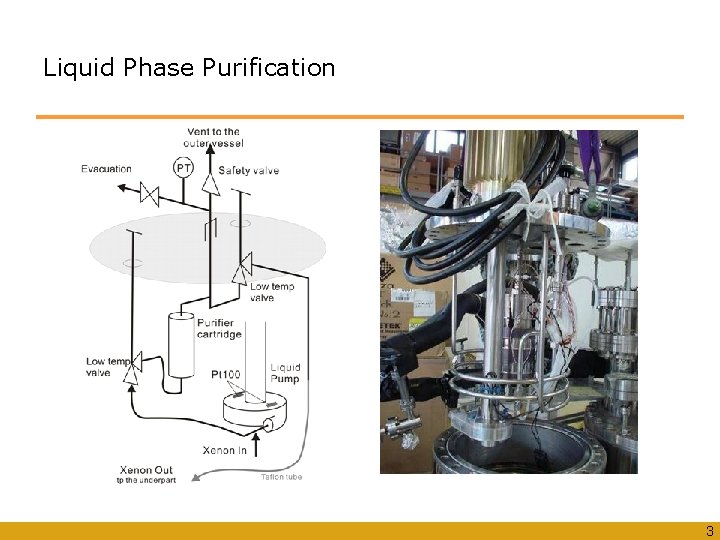
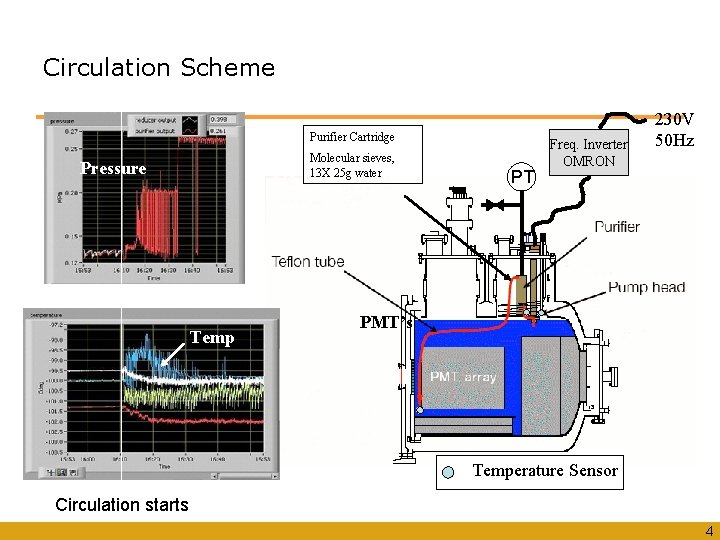
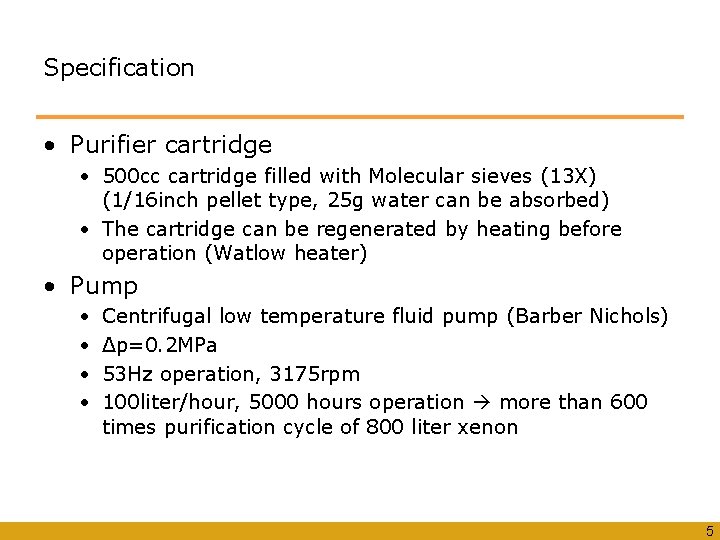
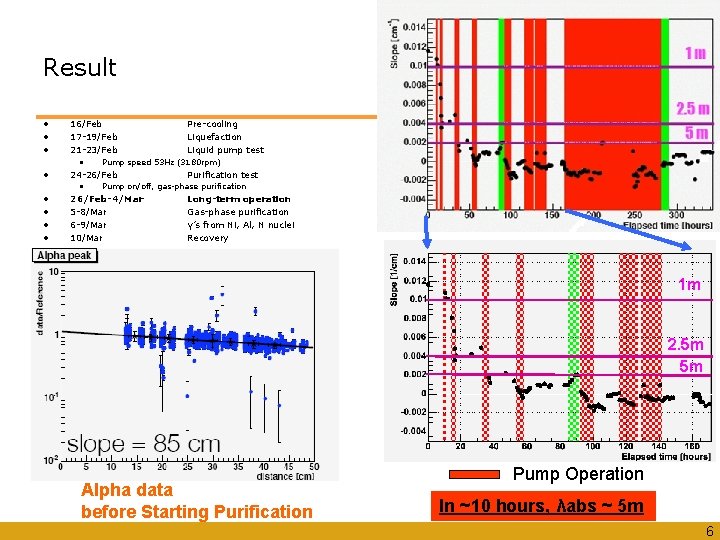
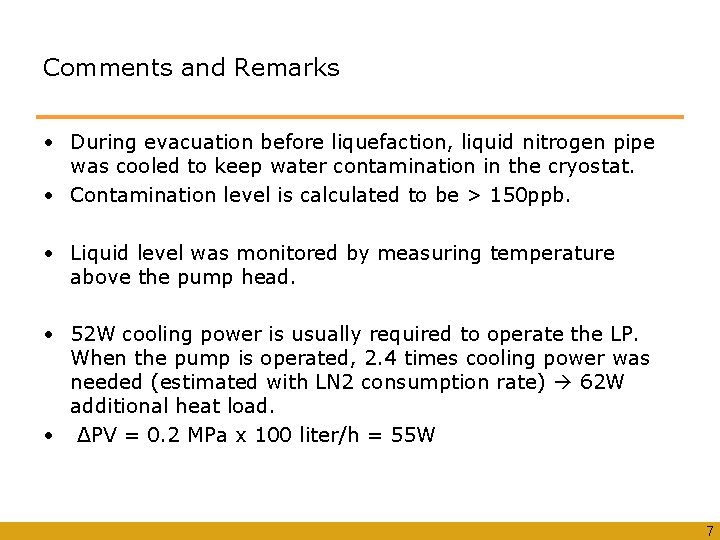
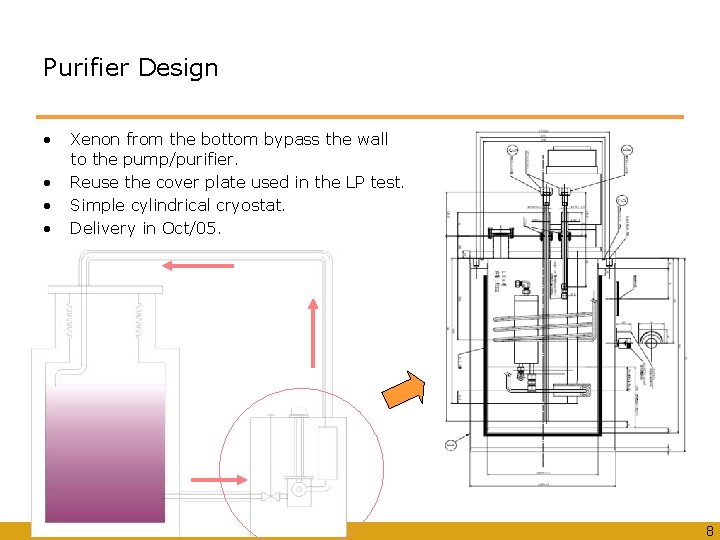
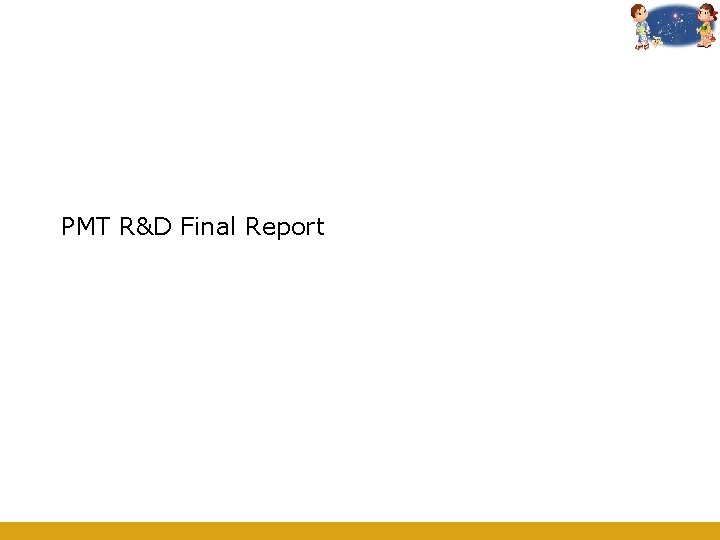
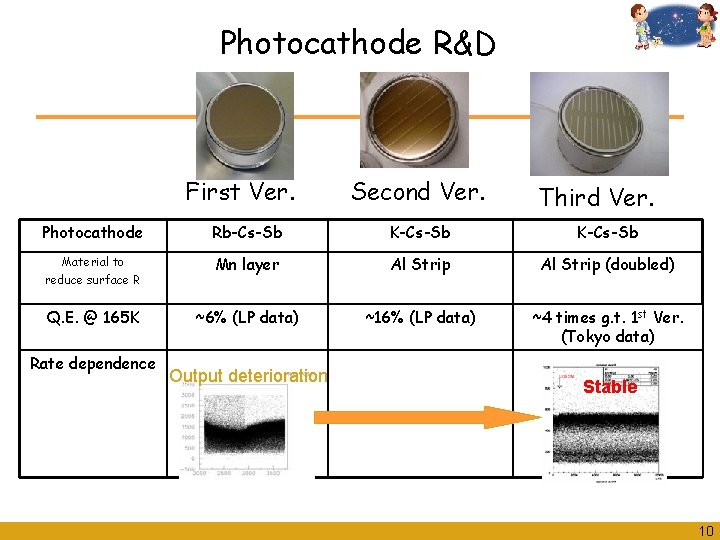
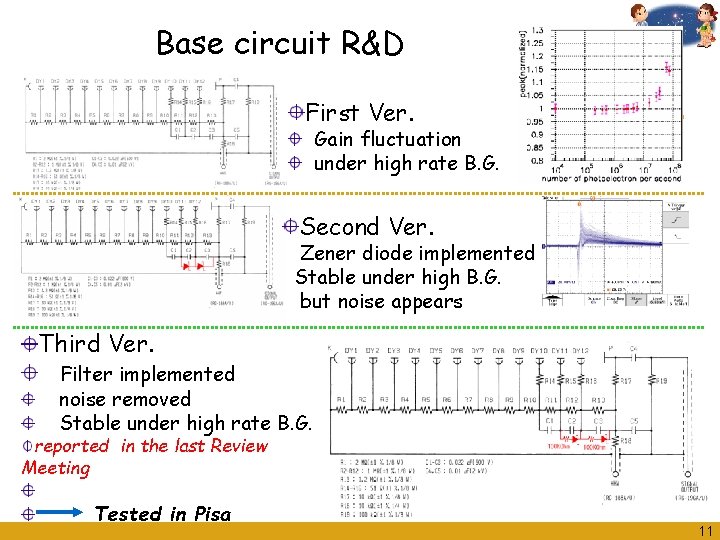

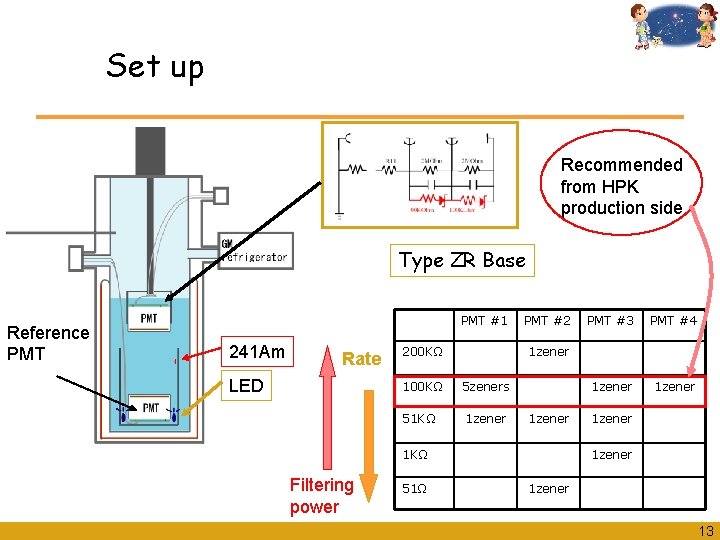
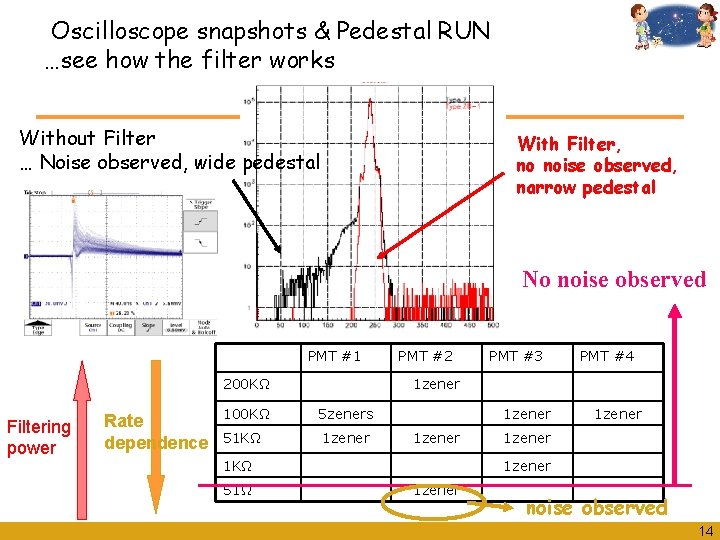
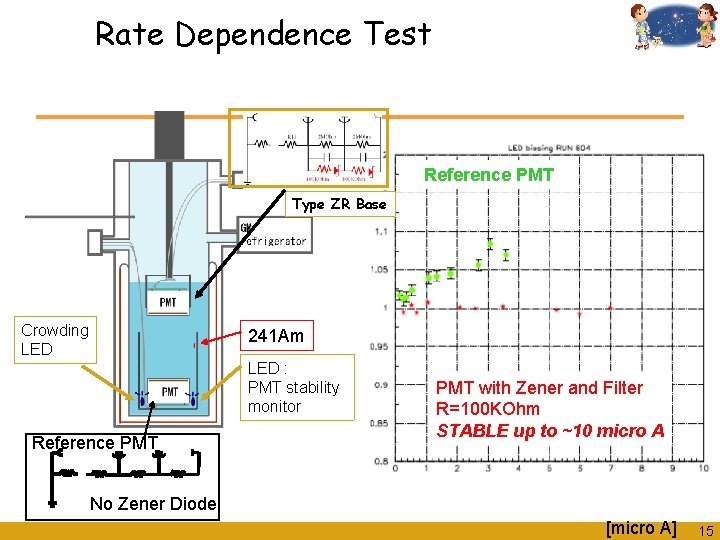
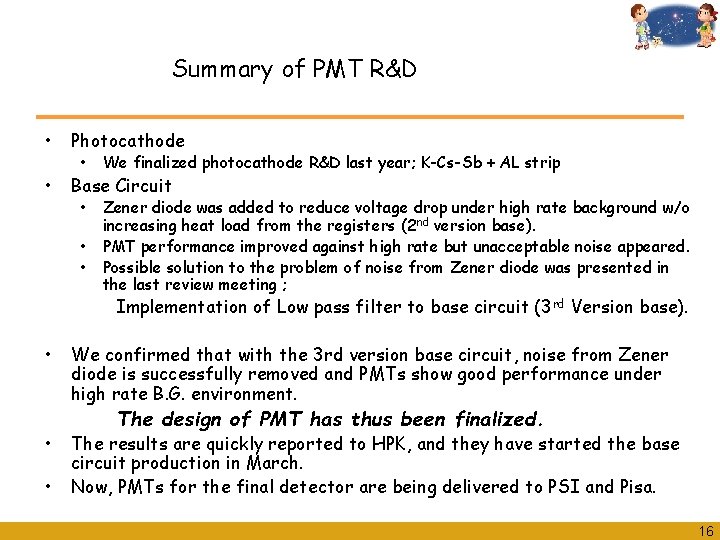
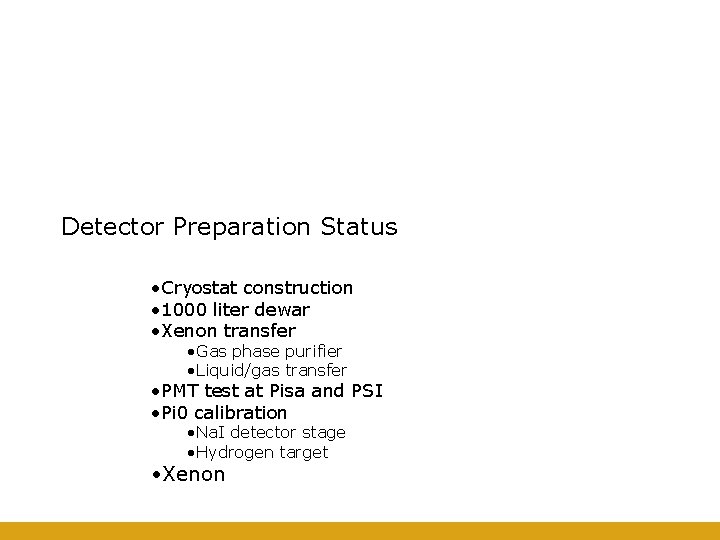
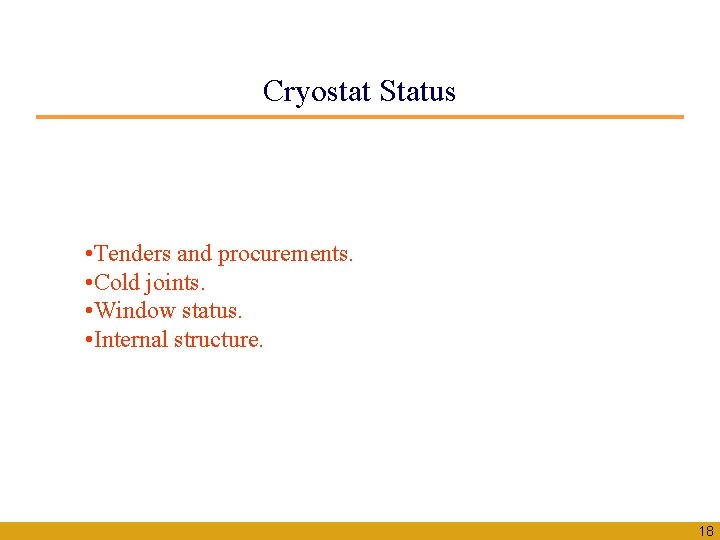
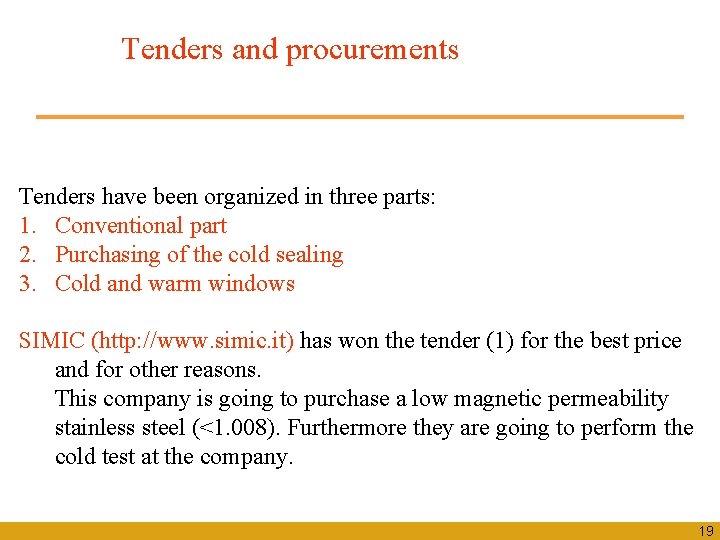
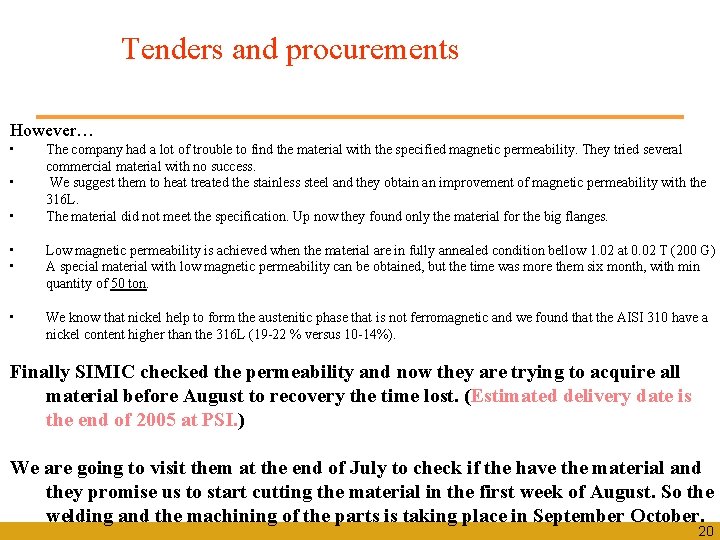
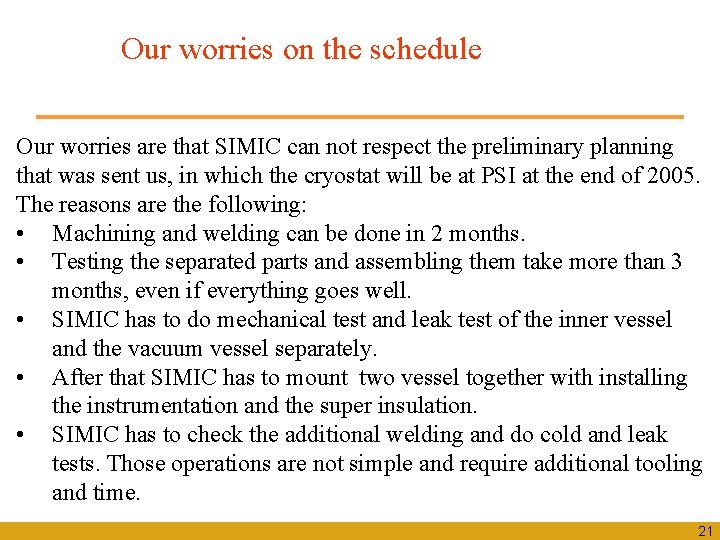
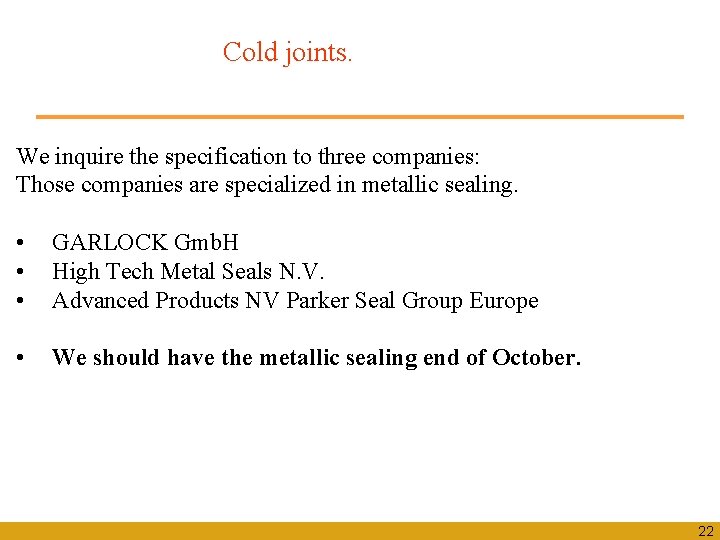
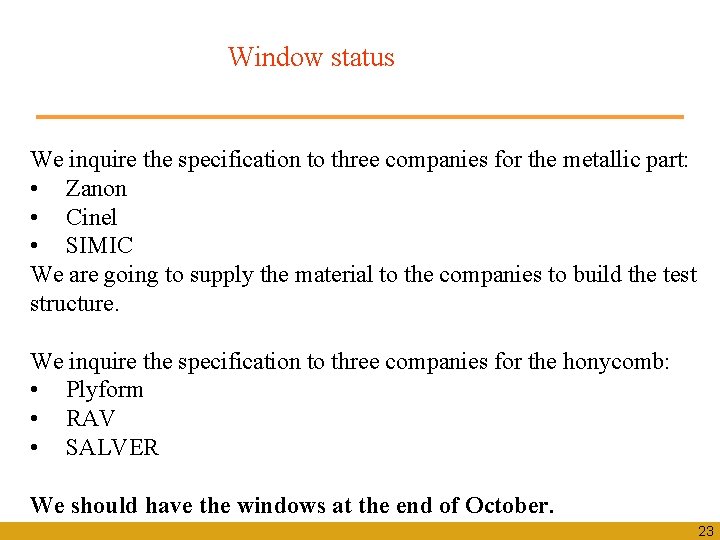
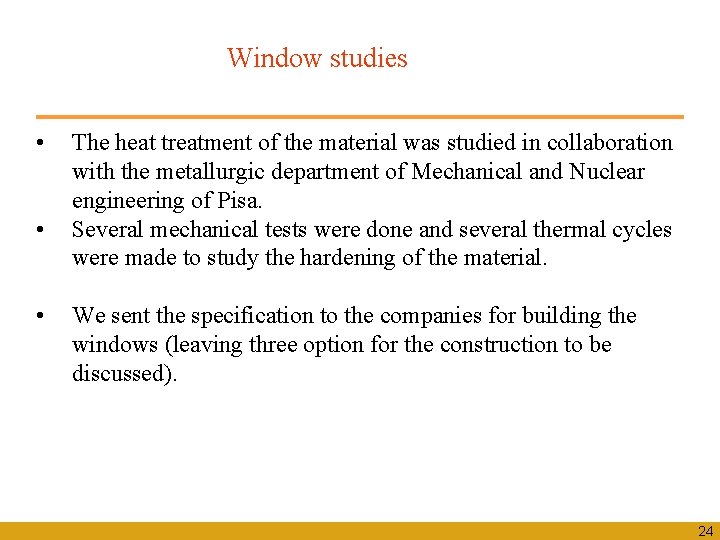
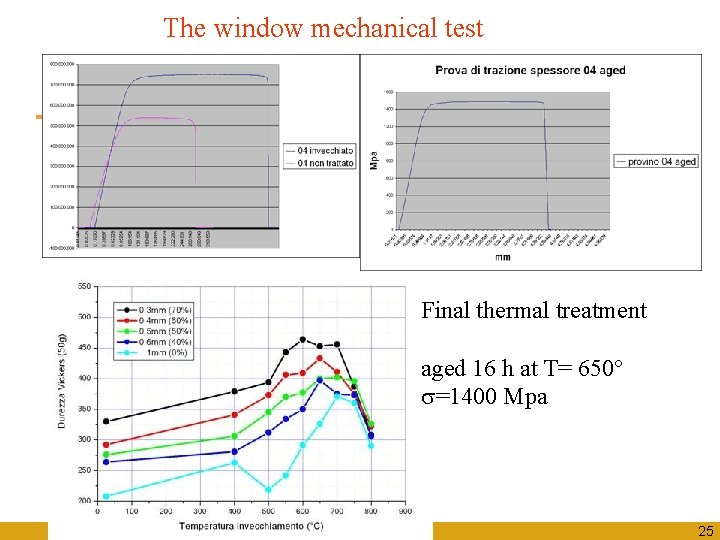
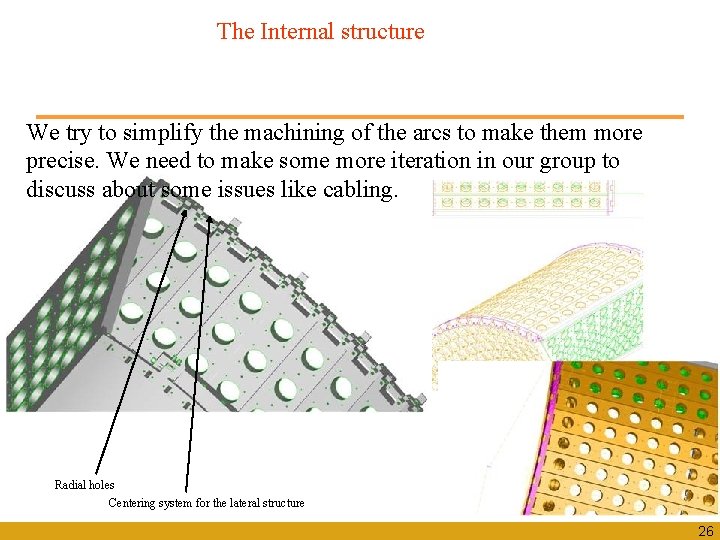
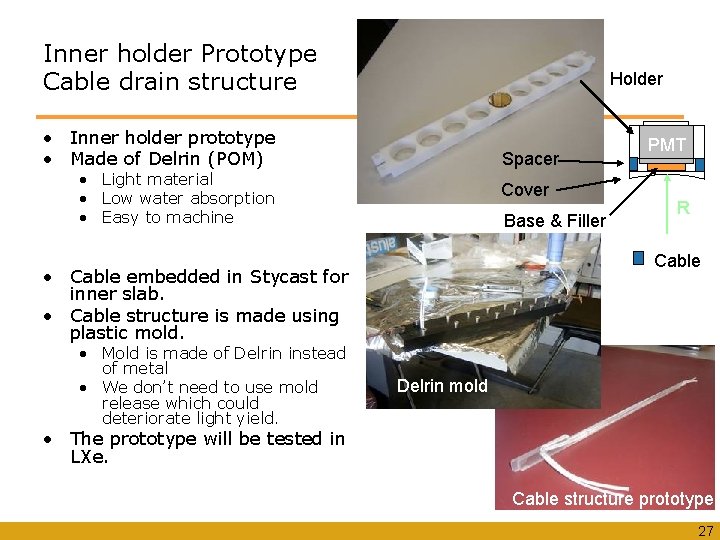
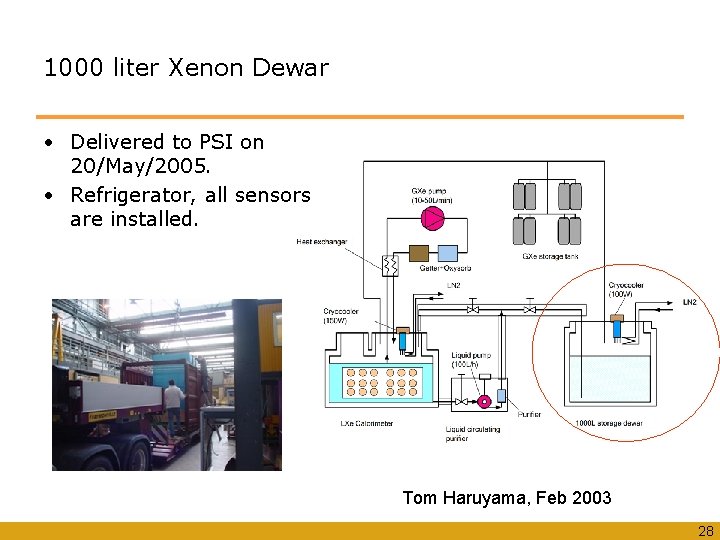
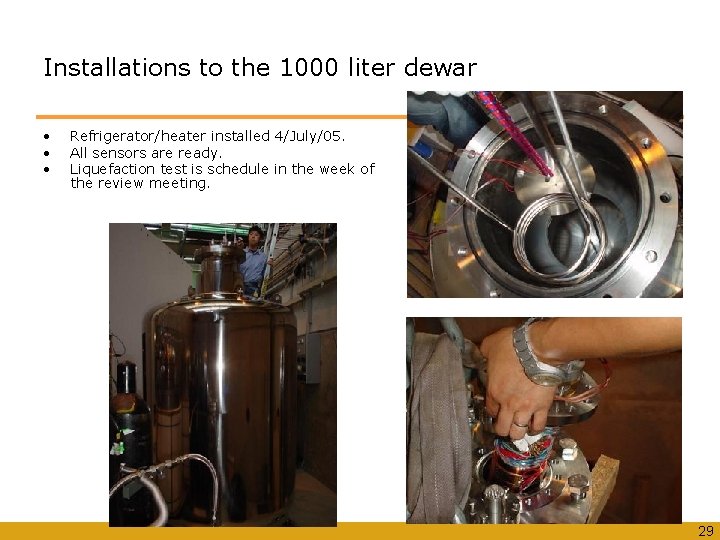
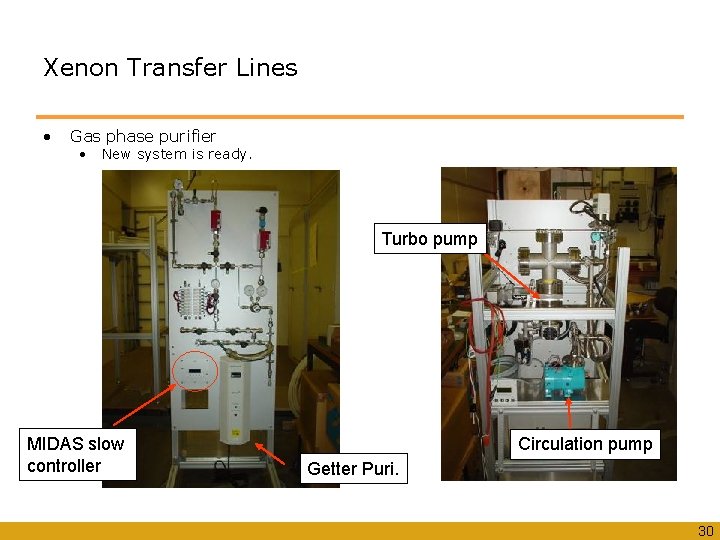
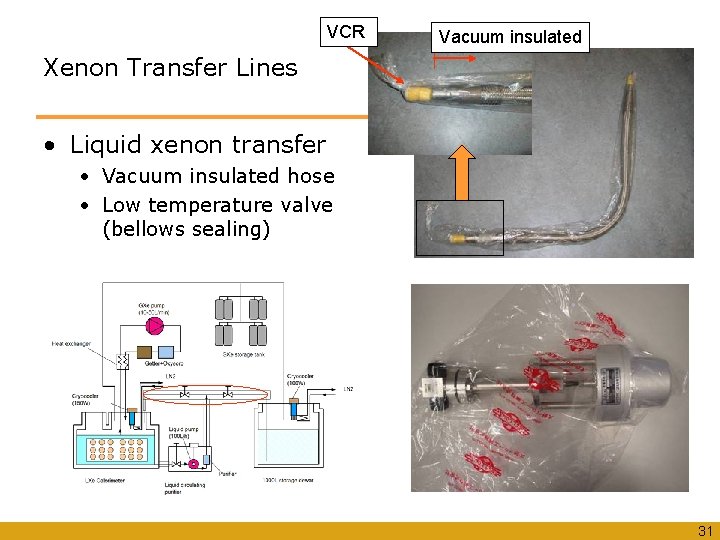
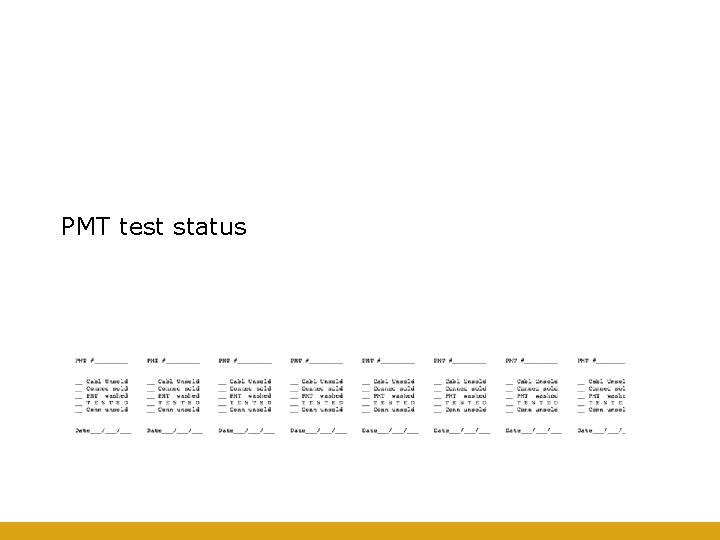
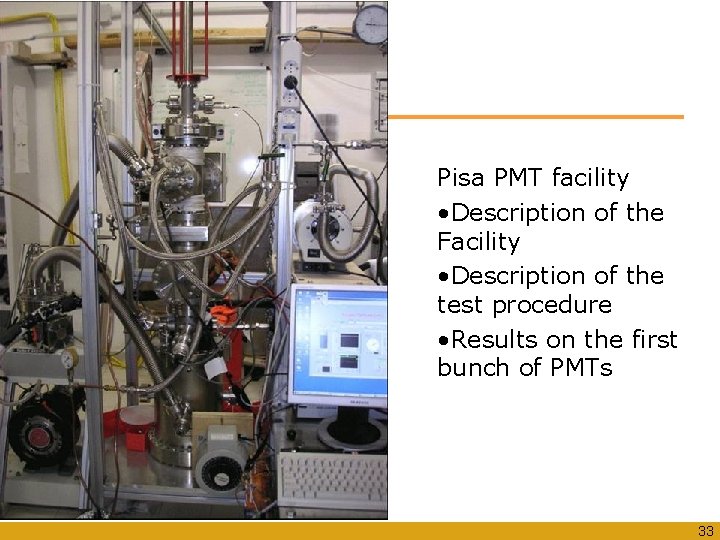
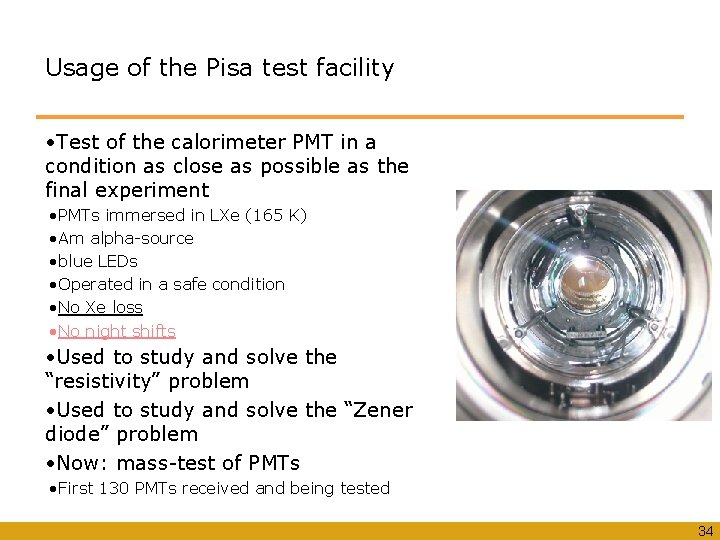
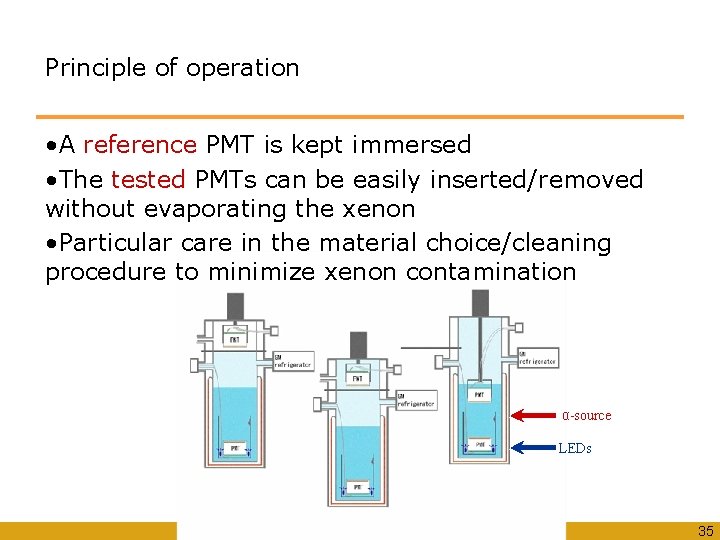
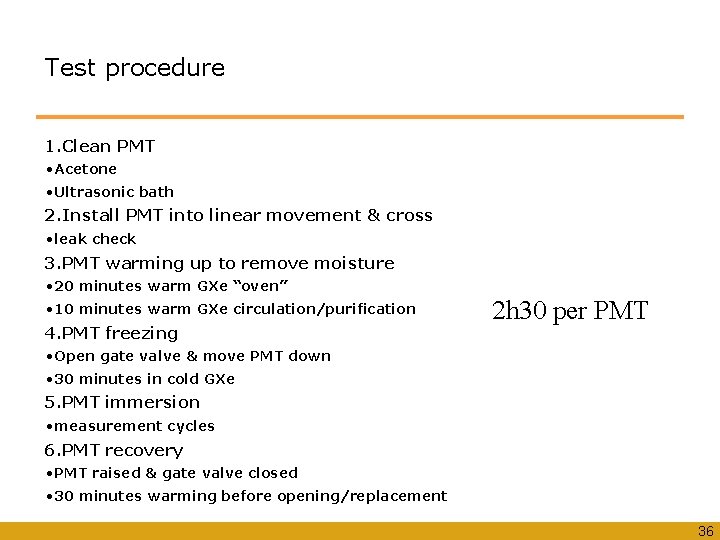
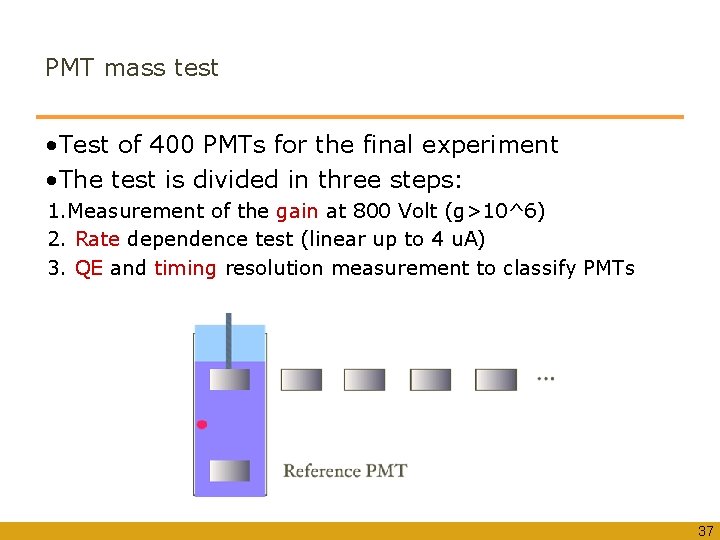
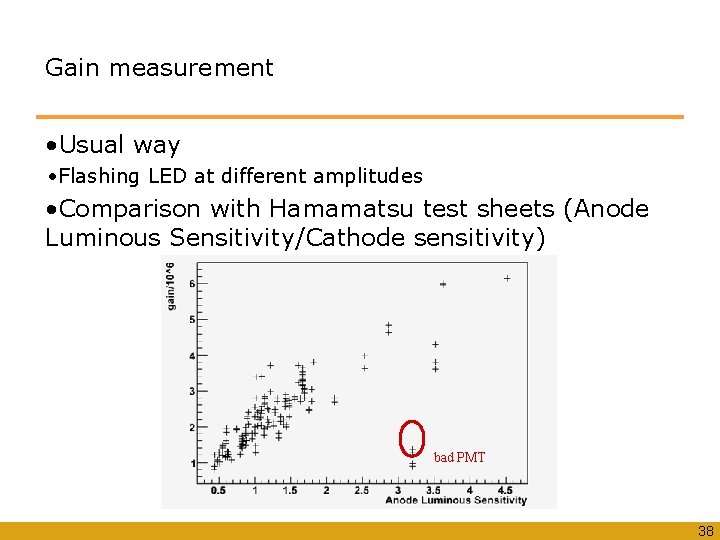
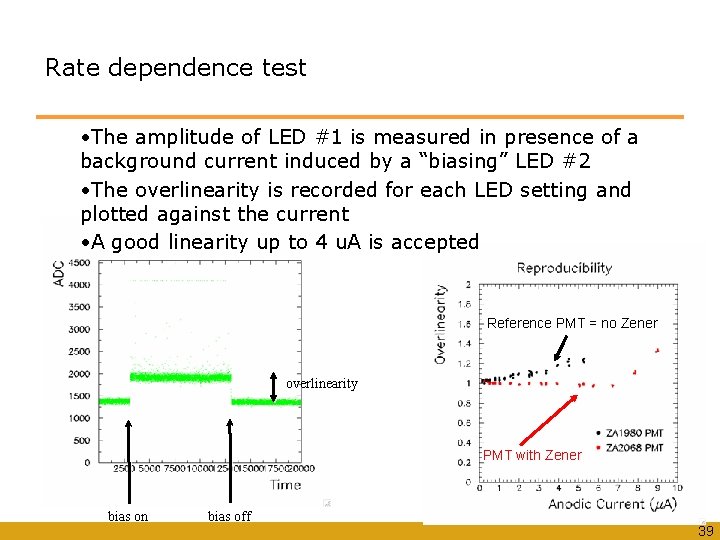
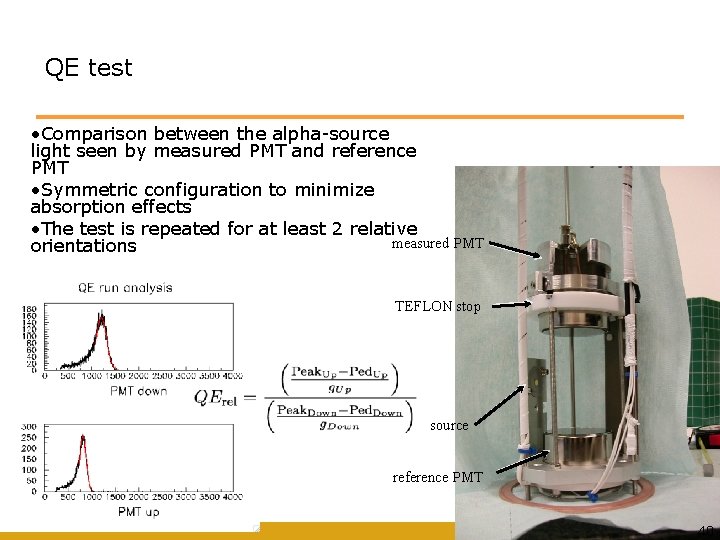
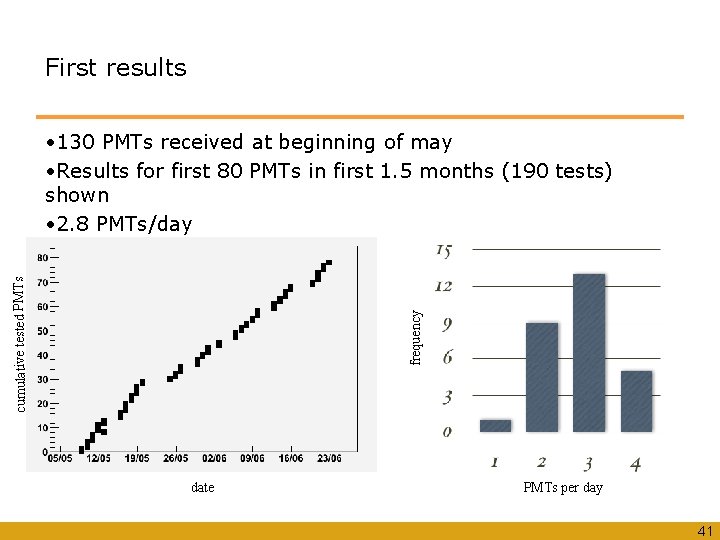
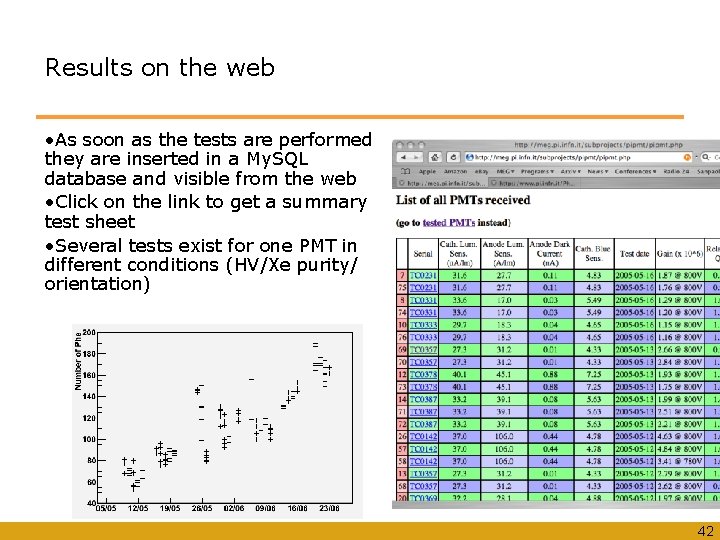
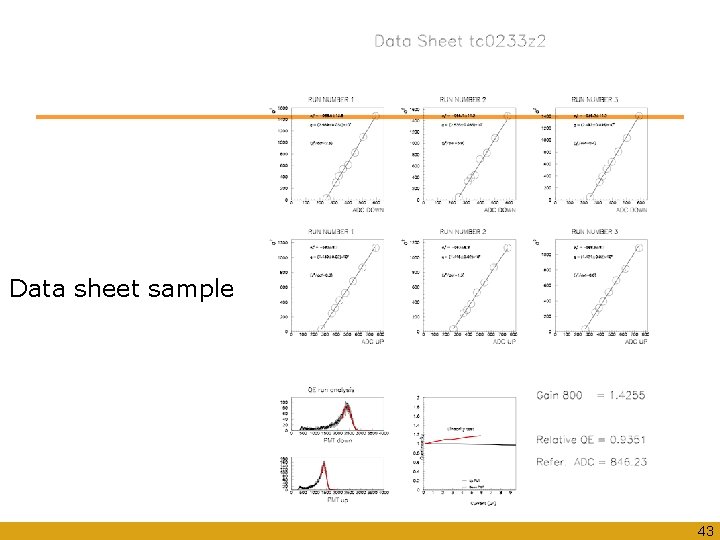
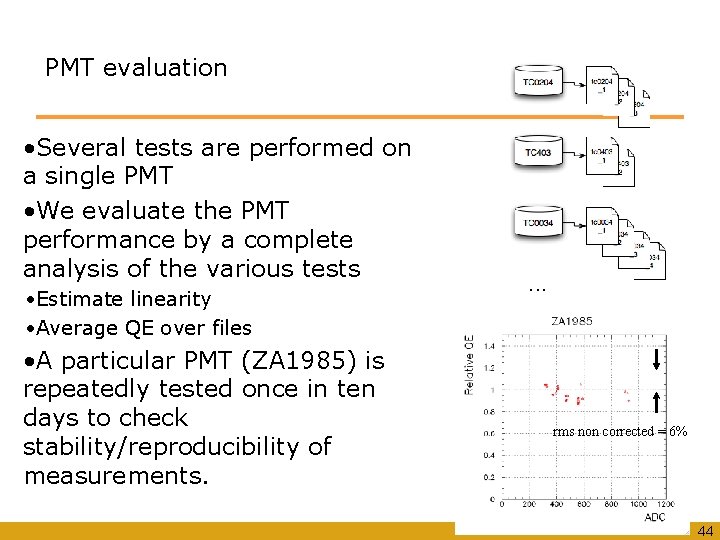
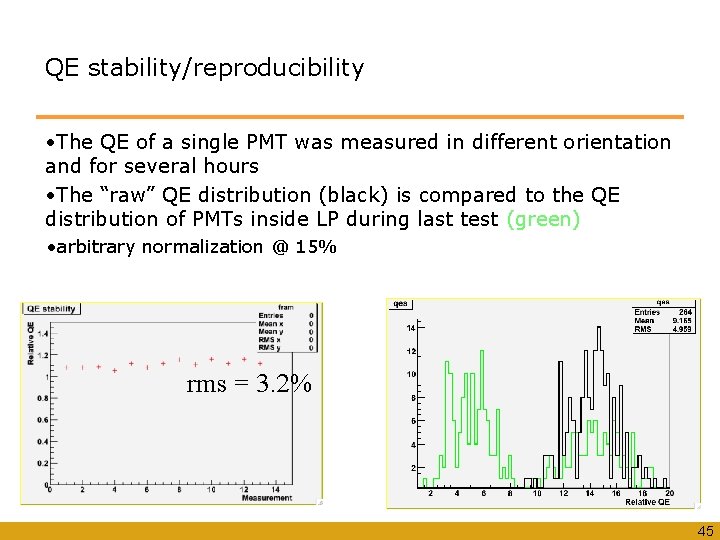
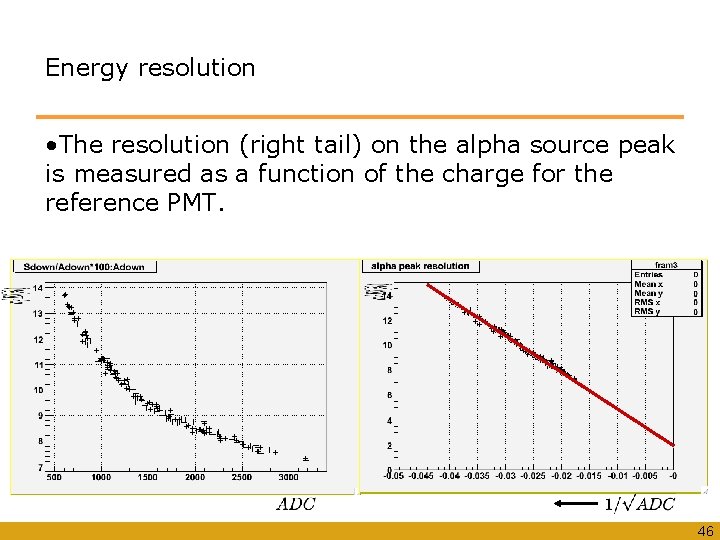
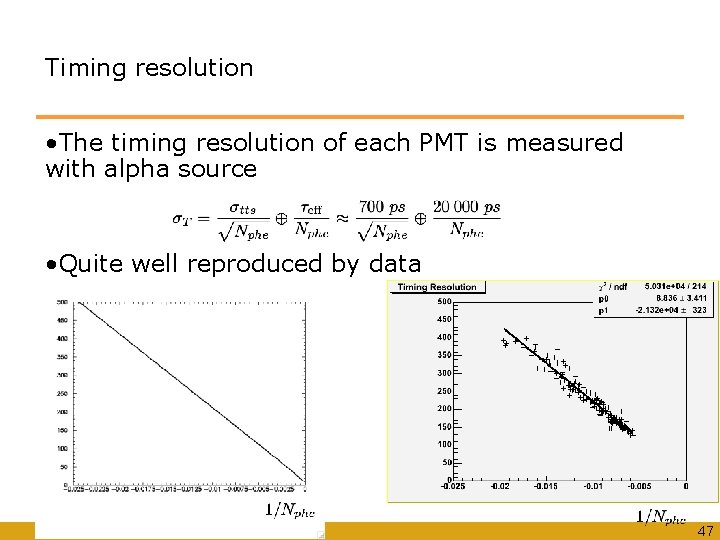
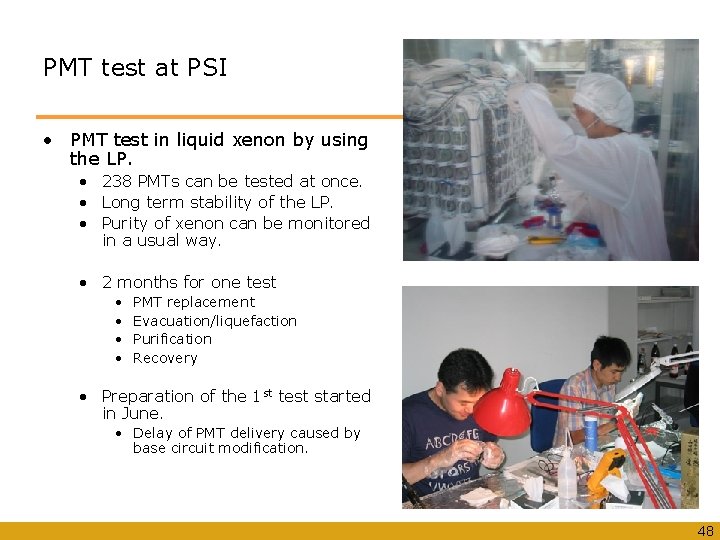
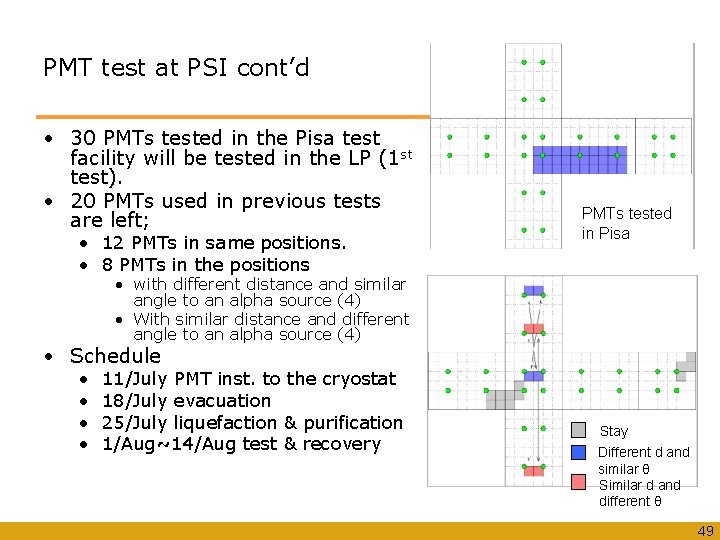
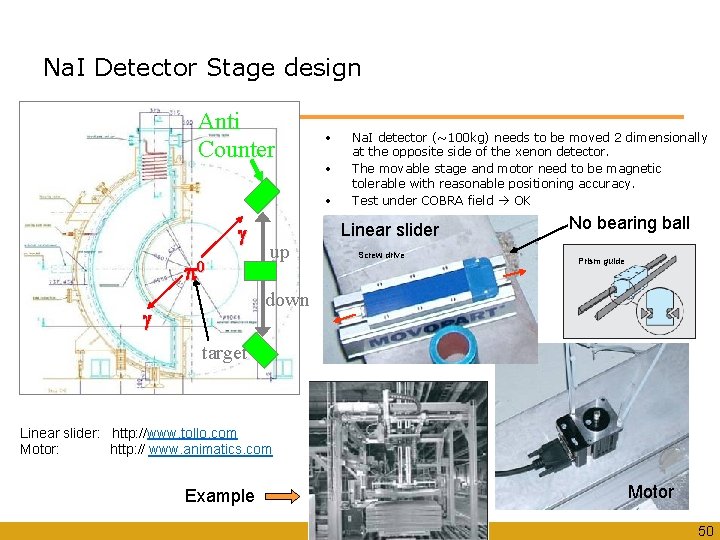
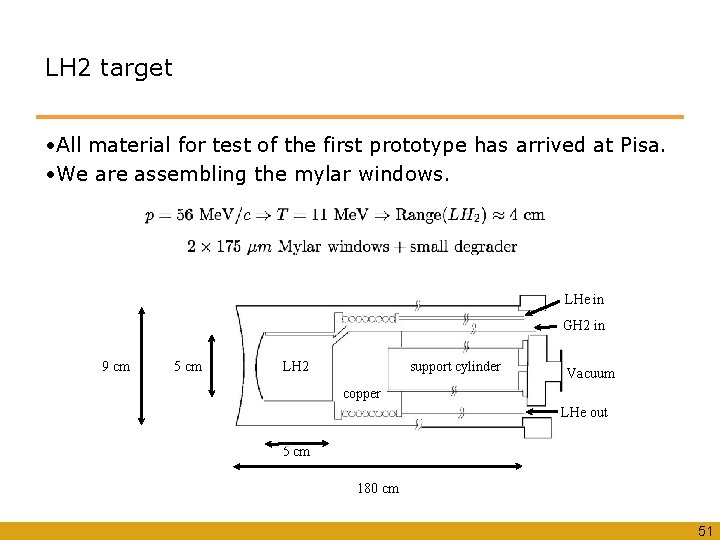
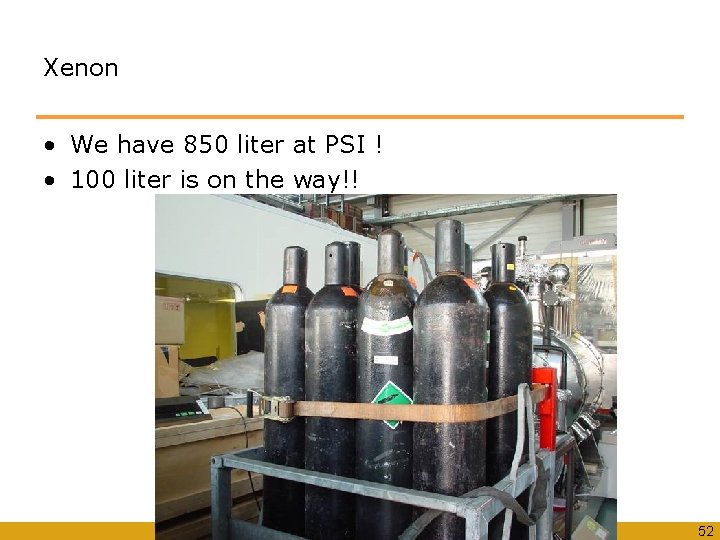
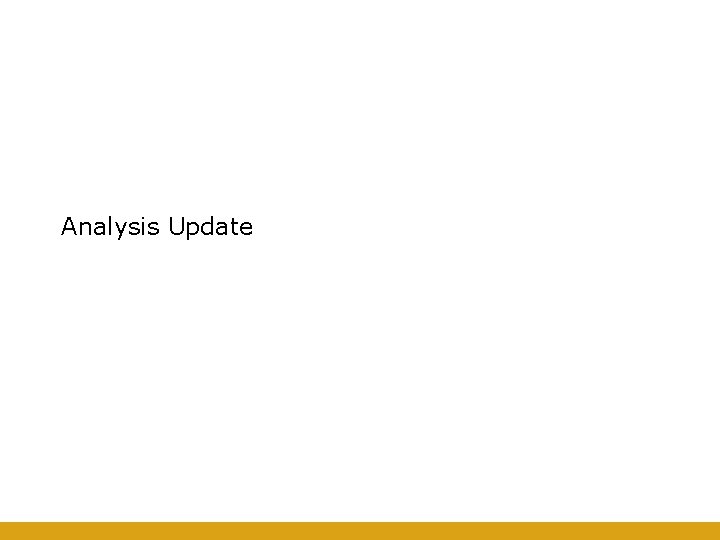
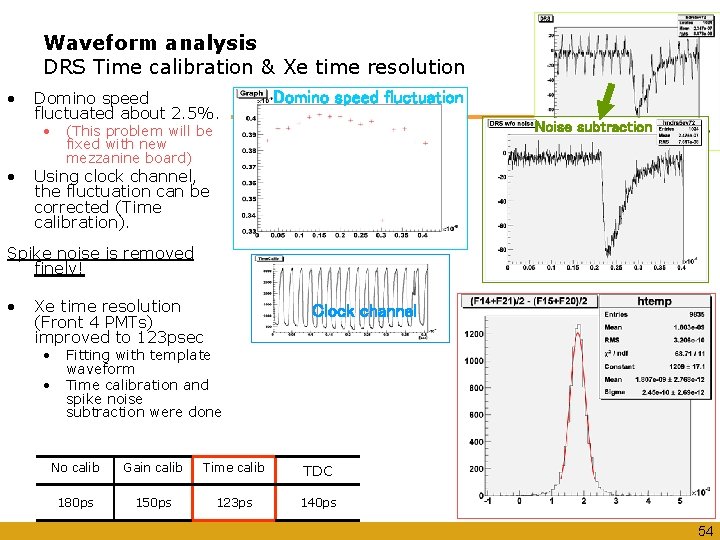
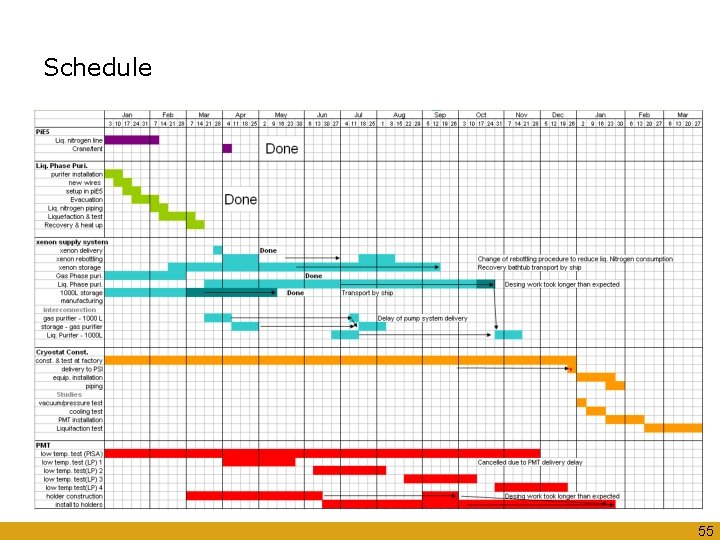
- Slides: 55
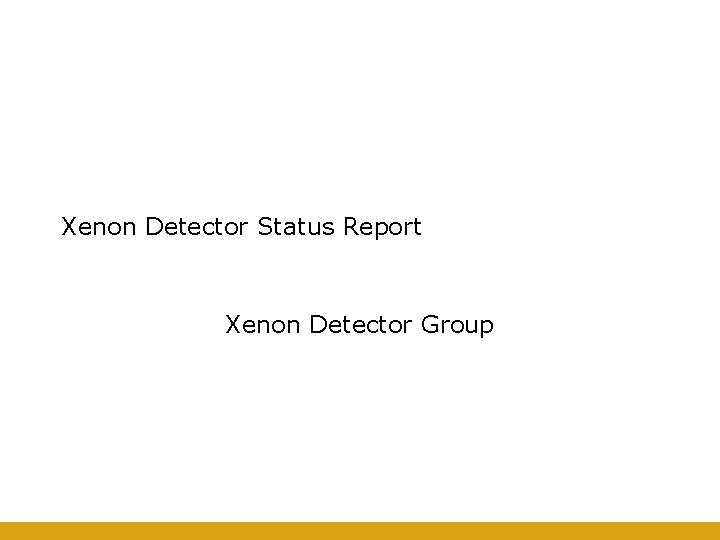
Xenon Detector Status Report Xenon Detector Group
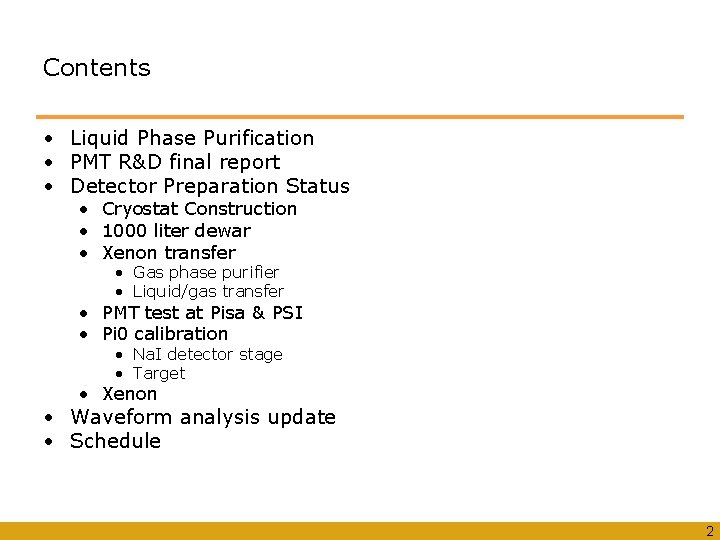
Contents • Liquid Phase Purification • PMT R&D final report • Detector Preparation Status • Cryostat Construction • 1000 liter dewar • Xenon transfer • Gas phase purifier • Liquid/gas transfer • PMT test at Pisa & PSI • Pi 0 calibration • Na. I detector stage • Target • Xenon • Waveform analysis update • Schedule 2
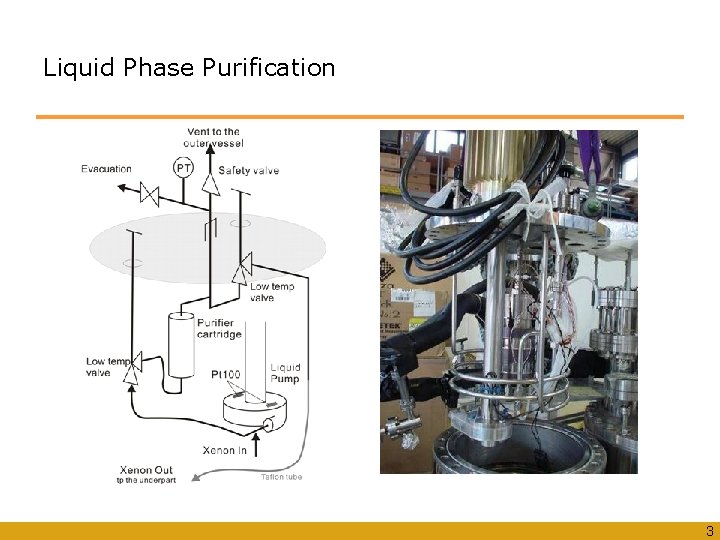
Liquid Phase Purification 3
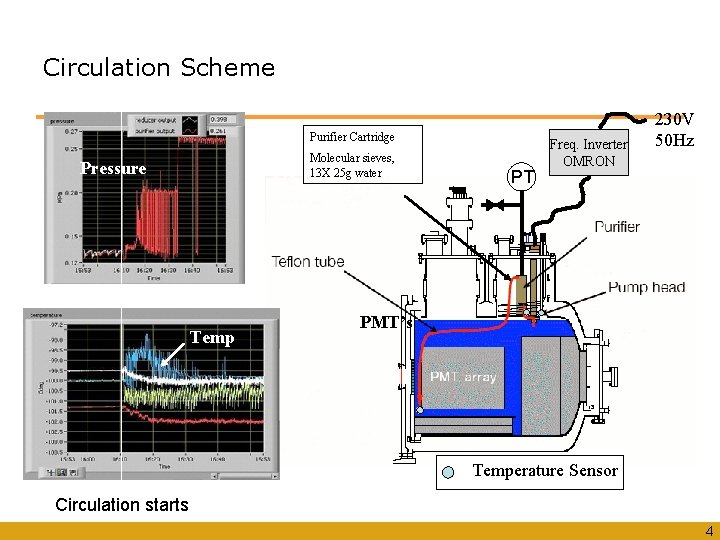
Circulation Scheme Purifier Cartridge Molecular sieves, 13 X 25 g water Pressure Temp PT Freq. Inverter OMRON 230 V 50 Hz PMT’s Temperature Sensor Circulation starts 4
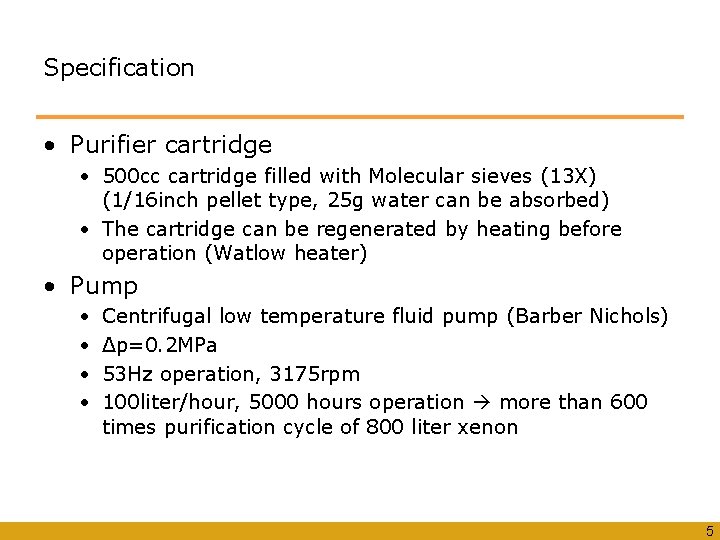
Specification • Purifier cartridge • 500 cc cartridge filled with Molecular sieves (13 X) (1/16 inch pellet type, 25 g water can be absorbed) • The cartridge can be regenerated by heating before operation (Watlow heater) • Pump • • Centrifugal low temperature fluid pump (Barber Nichols) Δp=0. 2 MPa 53 Hz operation, 3175 rpm 100 liter/hour, 5000 hours operation more than 600 times purification cycle of 800 liter xenon 5
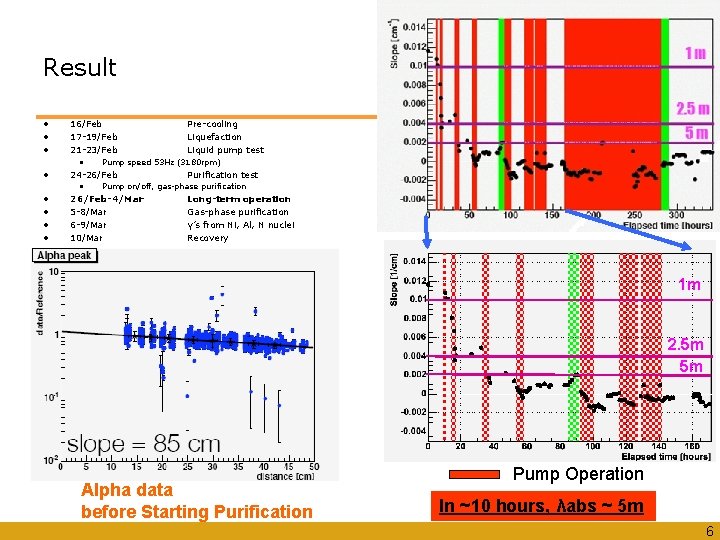
Result • • • 16/Feb 17 -19/Feb 21 -23/Feb • 24 -26/Feb • • • Pre-cooling Liquefaction Liquid pump test Pump speed 53 Hz (3180 rpm) Purification test Pump on/off, gas-phase purification 26/Feb-4/Mar 5 -8/Mar 6 -9/Mar 10/Mar Long-term operation Gas-phase purification γ’s from Ni, Al, N nuclei Recovery 1 m 2. 5 m 5 m Alpha data before Starting Purification Pump Operation In ~10 hours, λabs ~ 5 m 6
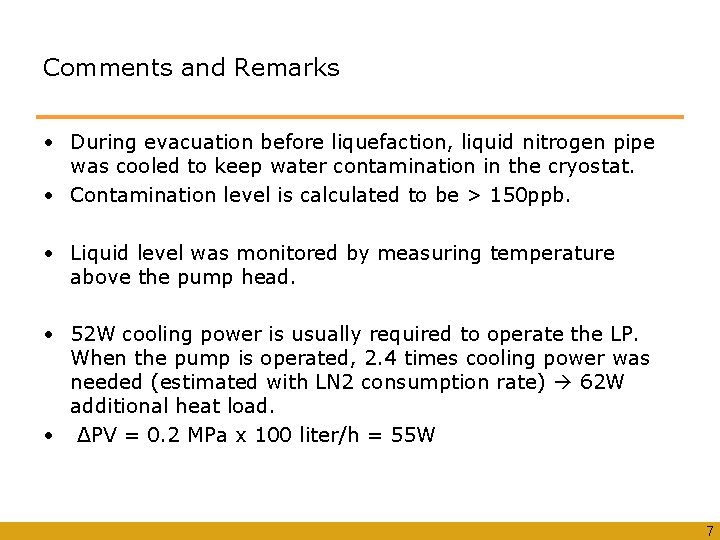
Comments and Remarks • During evacuation before liquefaction, liquid nitrogen pipe was cooled to keep water contamination in the cryostat. • Contamination level is calculated to be > 150 ppb. • Liquid level was monitored by measuring temperature above the pump head. • 52 W cooling power is usually required to operate the LP. When the pump is operated, 2. 4 times cooling power was needed (estimated with LN 2 consumption rate) 62 W additional heat load. • ΔPV = 0. 2 MPa x 100 liter/h = 55 W 7
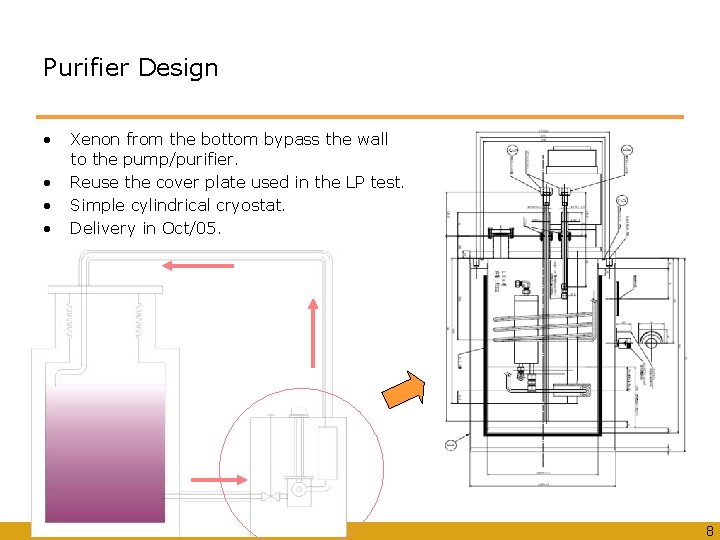
Purifier Design • • Xenon from the bottom bypass the wall to the pump/purifier. Reuse the cover plate used in the LP test. Simple cylindrical cryostat. Delivery in Oct/05. 8
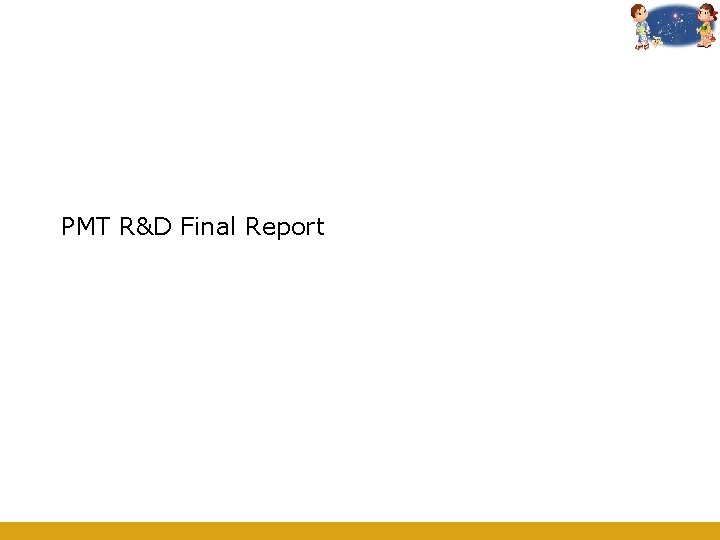
PMT R&D Final Report
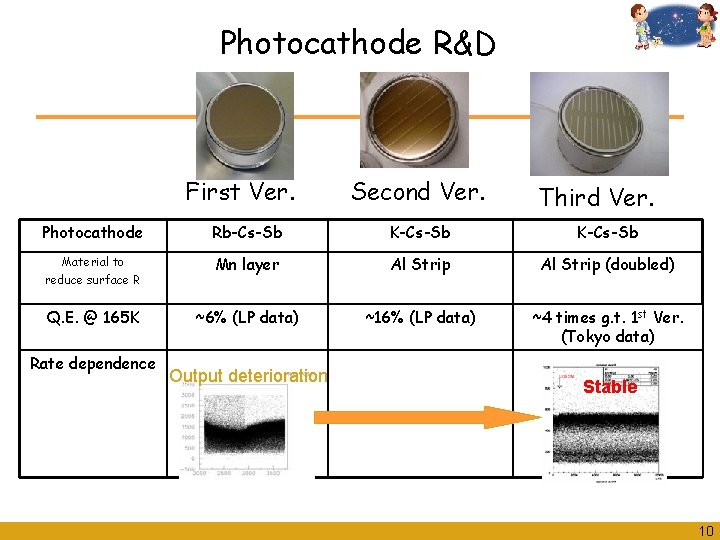
Photocathode R&D First Ver. Second Ver. Third Ver. Photocathode Rb-Cs-Sb K-Cs-Sb Material to reduce surface R Mn layer Al Strip (doubled) Q. E. @ 165 K ~6% (LP data) ~16% (LP data) ~4 times g. t. 1 st Ver. (Tokyo data) Rate dependence Output deterioration Stable 10
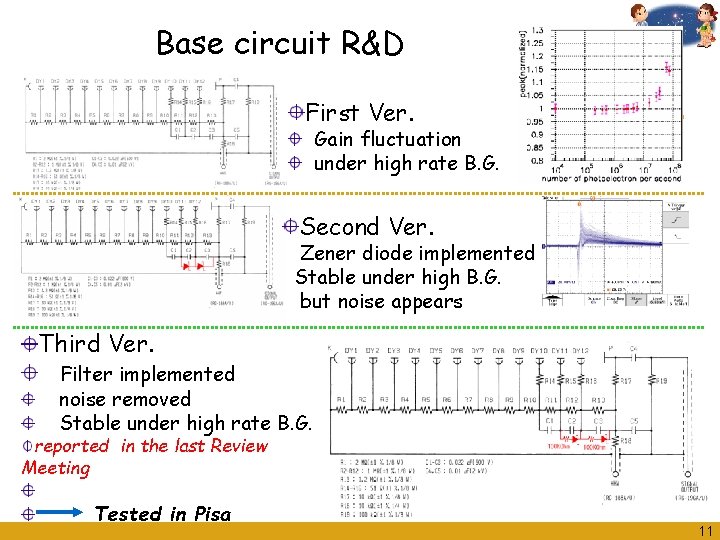
Base circuit R&D First Ver. Gain fluctuation under high rate B. G. Second Ver. Zener diode implemented Stable under high B. G. but noise appears Third Ver. Filter implemented noise removed Stable under high rate B. G. reported in the last Review Meeting Tested in Pisa 11

Mission : Finalize the low pass filter design Low pass filter is built in by adding resistors serial to Zener If the resistance is too small, filtering will not work. With too large resistance, the effect of Zener will be little under high rate BG environment Optimum resistance is ~100 KOhm, Let’s test ! Test the power of the filter by changing the resistance Test the gain stability under high rate B. G. (i. e. rate dependence test) 12
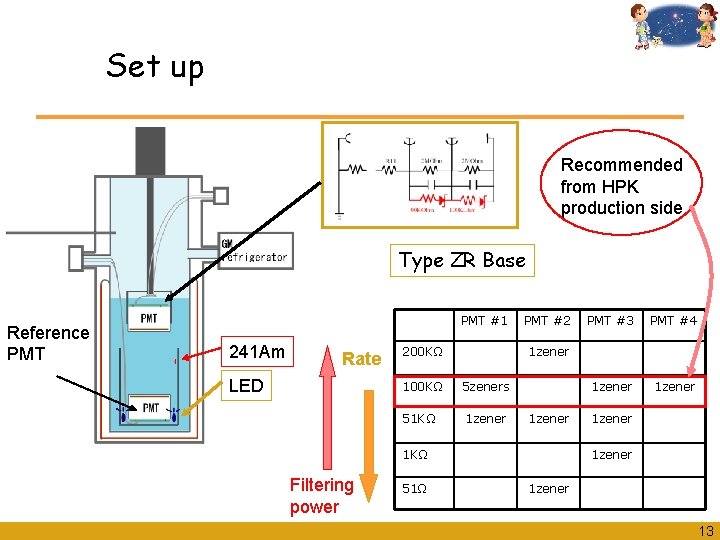
Set up Recommended from HPK production side Type ZR Base Reference PMT #1 241 Am Rate LED 200 KΩ PMT #2 100 KΩ 5 zeners 51 KΩ 1 zener 51Ω PMT #4 1 zener 1 KΩ Filtering power PMT #3 1 zener 13
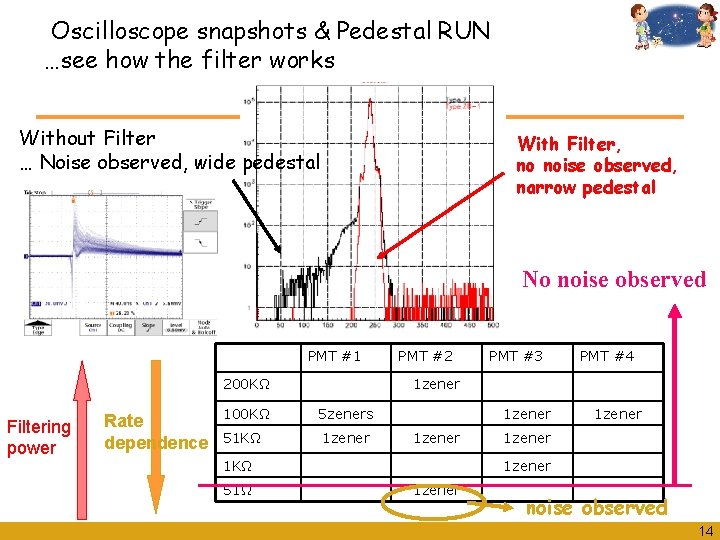
Oscilloscope snapshots & Pedestal RUN …see how the filter works Without Filter … Noise observed, wide pedestal With Filter, no noise observed, narrow pedestal No noise observed PMT #1 200 KΩ Filtering power Rate dependence PMT #2 PMT #4 1 zener 100 KΩ 5 zeners 51 KΩ 1 zener 1 KΩ 51Ω PMT #3 1 zener noise observed 14
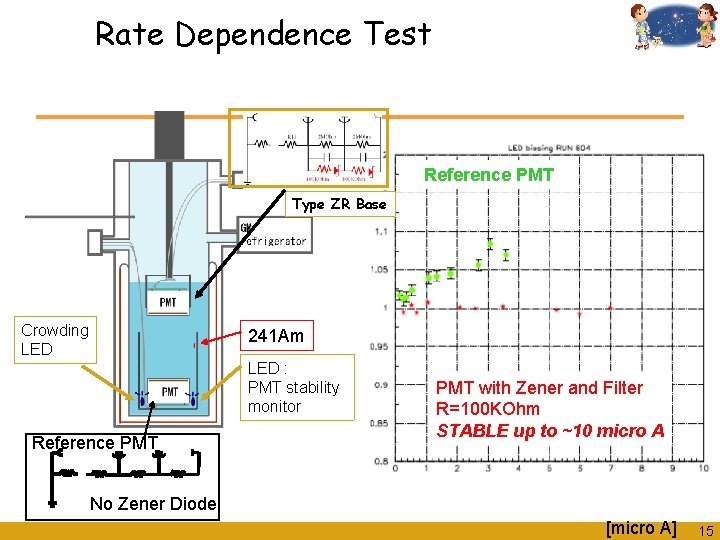
Rate Dependence Test Reference PMT Type ZR Base Crowding LED 241 Am LED : PMT stability monitor Reference PMT with Zener and Filter R=100 KOhm STABLE up to ~10 micro A No Zener Diode [micro A] 15
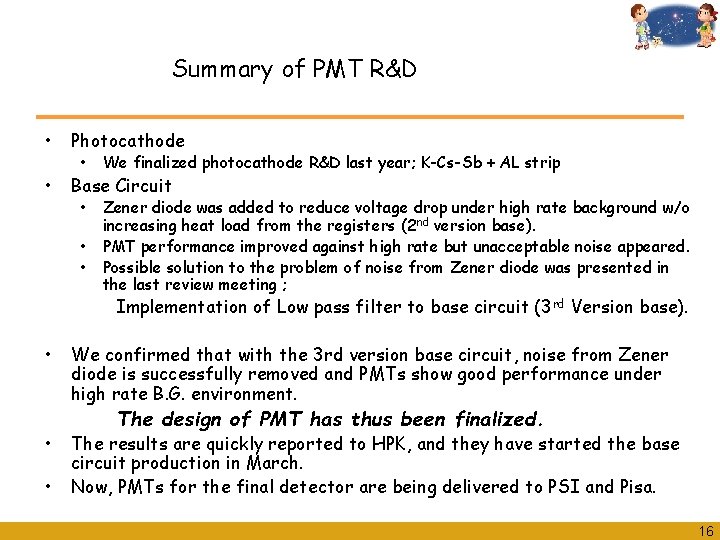
Summary of PMT R&D • Photocathode • Base Circuit • We finalized photocathode R&D last year; K-Cs-Sb + AL strip • Zener diode was added to reduce voltage drop under high rate background w/o increasing heat load from the registers (2 nd version base). • PMT performance improved against high rate but unacceptable noise appeared. • Possible solution to the problem of noise from Zener diode was presented in the last review meeting ; Implementation of Low pass filter to base circuit (3 rd Version base). • • • We confirmed that with the 3 rd version base circuit, noise from Zener diode is successfully removed and PMTs show good performance under high rate B. G. environment. The design of PMT has thus been finalized. The results are quickly reported to HPK, and they have started the base circuit production in March. Now, PMTs for the final detector are being delivered to PSI and Pisa. 16
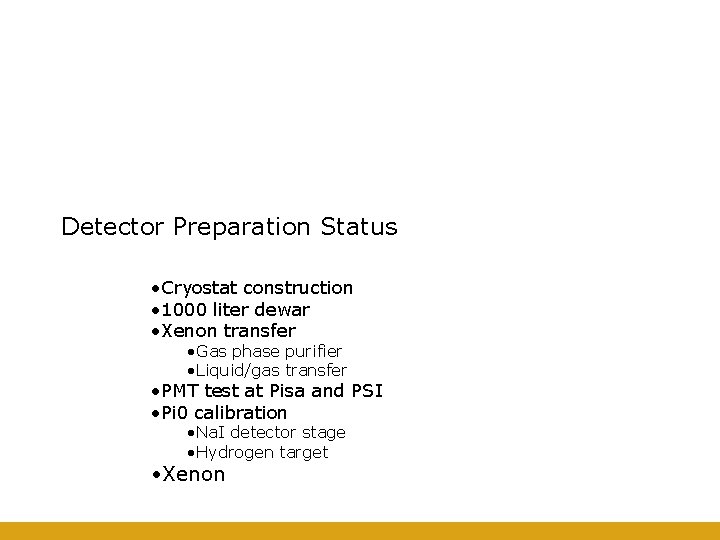
Detector Preparation Status • Cryostat construction • 1000 liter dewar • Xenon transfer • Gas phase purifier • Liquid/gas transfer • PMT test at Pisa and PSI • Pi 0 calibration • Na. I detector stage • Hydrogen target • Xenon
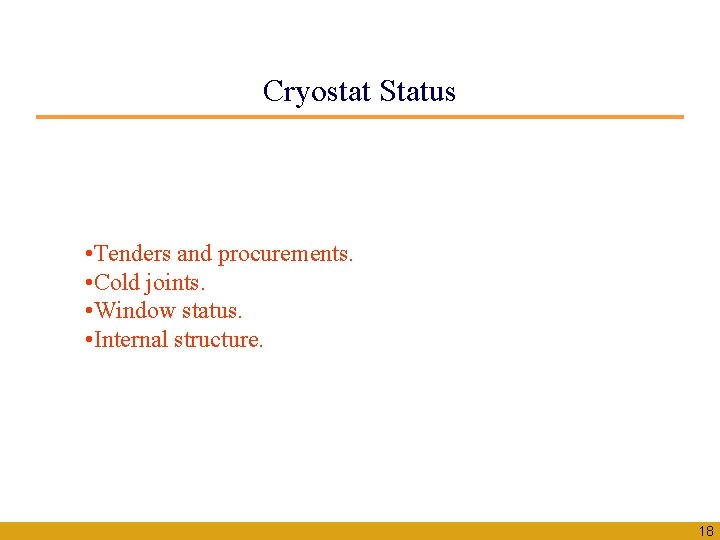
Cryostat Status • Tenders and procurements. • Cold joints. • Window status. • Internal structure. 18
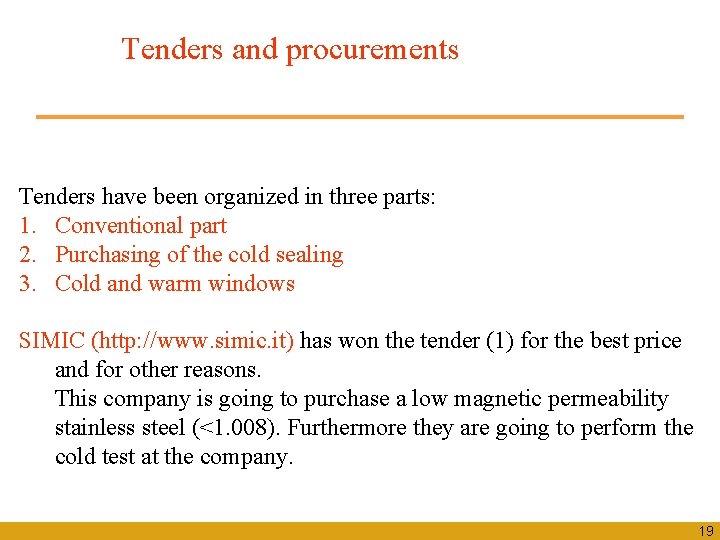
Tenders and procurements Tenders have been organized in three parts: 1. Conventional part 2. Purchasing of the cold sealing 3. Cold and warm windows SIMIC (http: //www. simic. it) has won the tender (1) for the best price and for other reasons. This company is going to purchase a low magnetic permeability stainless steel (<1. 008). Furthermore they are going to perform the cold test at the company. 19
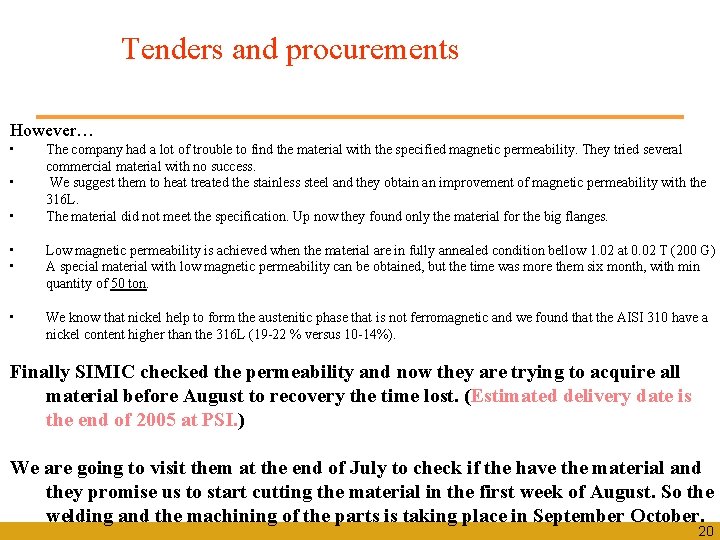
Tenders and procurements However… • • • The company had a lot of trouble to find the material with the specified magnetic permeability. They tried several commercial material with no success. We suggest them to heat treated the stainless steel and they obtain an improvement of magnetic permeability with the 316 L. The material did not meet the specification. Up now they found only the material for the big flanges. • • Low magnetic permeability is achieved when the material are in fully annealed condition bellow 1. 02 at 0. 02 T (200 G) A special material with low magnetic permeability can be obtained, but the time was more them six month, with min quantity of 50 ton. • We know that nickel help to form the austenitic phase that is not ferromagnetic and we found that the AISI 310 have a nickel content higher than the 316 L (19 -22 % versus 10 -14%). Finally SIMIC checked the permeability and now they are trying to acquire all material before August to recovery the time lost. (Estimated delivery date is the end of 2005 at PSI. ) We are going to visit them at the end of July to check if the have the material and they promise us to start cutting the material in the first week of August. So the welding and the machining of the parts is taking place in September October. 20
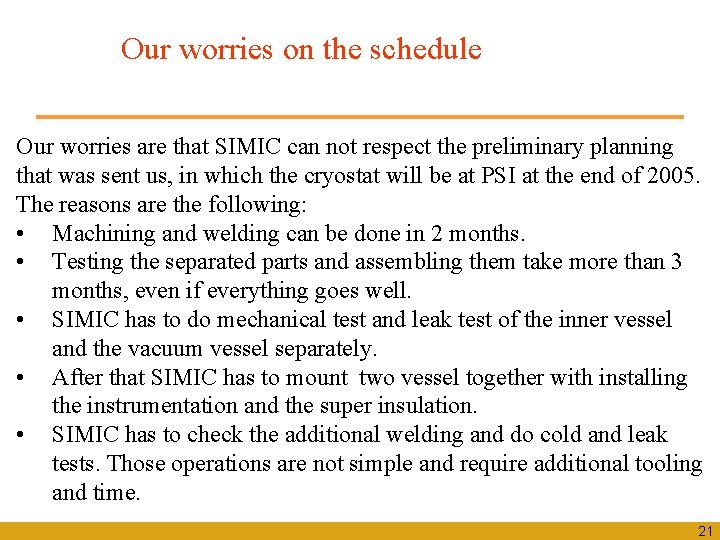
Our worries on the schedule Our worries are that SIMIC can not respect the preliminary planning that was sent us, in which the cryostat will be at PSI at the end of 2005. The reasons are the following: • Machining and welding can be done in 2 months. • Testing the separated parts and assembling them take more than 3 months, even if everything goes well. • SIMIC has to do mechanical test and leak test of the inner vessel and the vacuum vessel separately. • After that SIMIC has to mount two vessel together with installing the instrumentation and the super insulation. • SIMIC has to check the additional welding and do cold and leak tests. Those operations are not simple and require additional tooling and time. 21
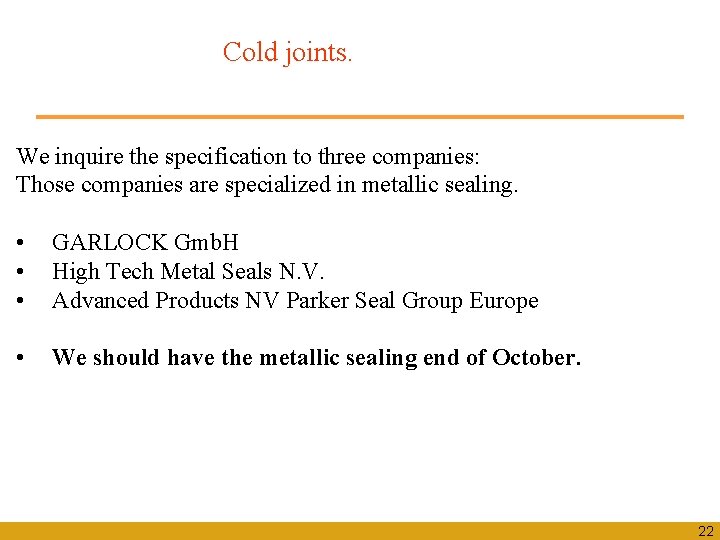
Cold joints. We inquire the specification to three companies: Those companies are specialized in metallic sealing. • • • GARLOCK Gmb. H High Tech Metal Seals N. V. Advanced Products NV Parker Seal Group Europe • We should have the metallic sealing end of October. 22
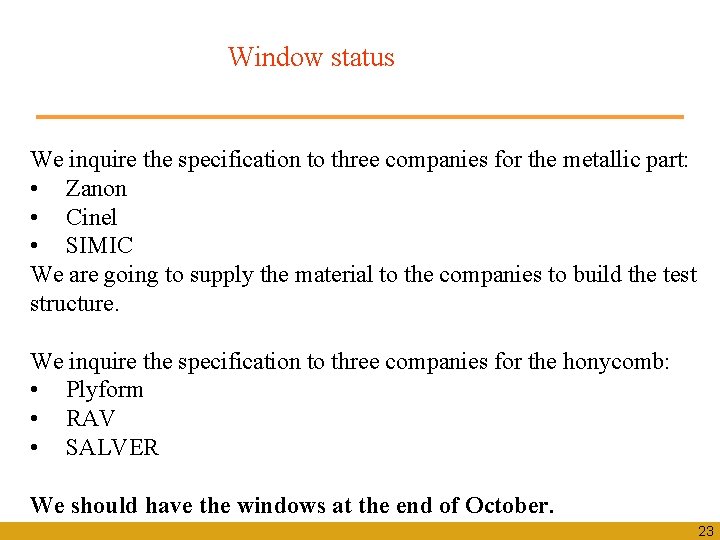
Window status We inquire the specification to three companies for the metallic part: • Zanon • Cinel • SIMIC We are going to supply the material to the companies to build the test structure. We inquire the specification to three companies for the honycomb: • Plyform • RAV • SALVER We should have the windows at the end of October. 23
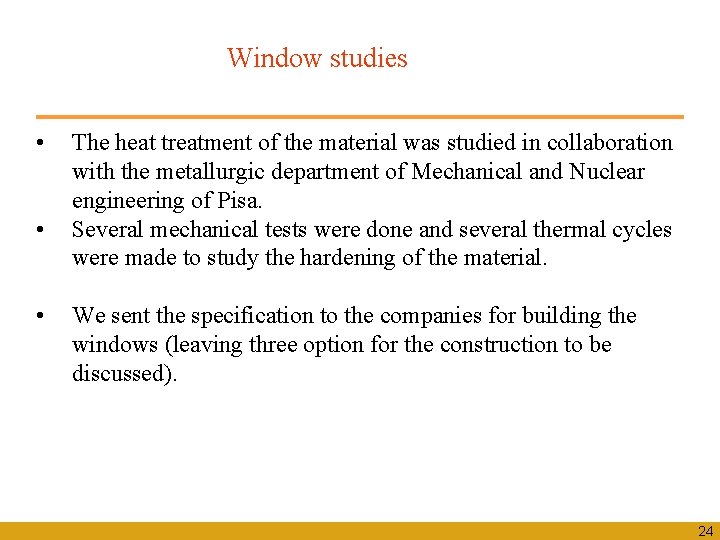
Window studies • • • The heat treatment of the material was studied in collaboration with the metallurgic department of Mechanical and Nuclear engineering of Pisa. Several mechanical tests were done and several thermal cycles were made to study the hardening of the material. We sent the specification to the companies for building the windows (leaving three option for the construction to be discussed). 24
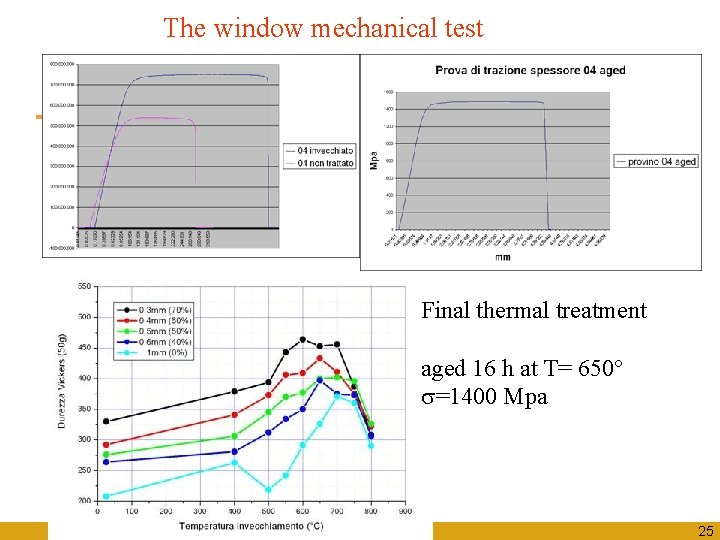
The window mechanical test Final thermal treatment aged 16 h at T= 650° s=1400 Mpa 25
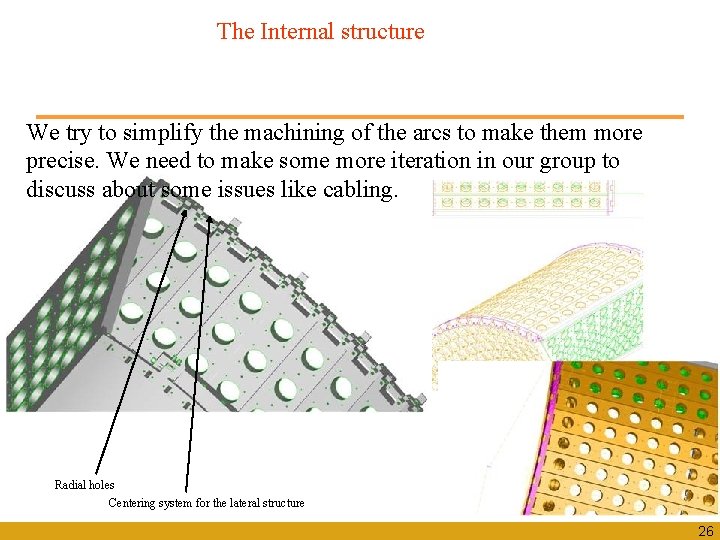
The Internal structure We try to simplify the machining of the arcs to make them more precise. We need to make some more iteration in our group to discuss about some issues like cabling. Radial holes Centering system for the lateral structure 26
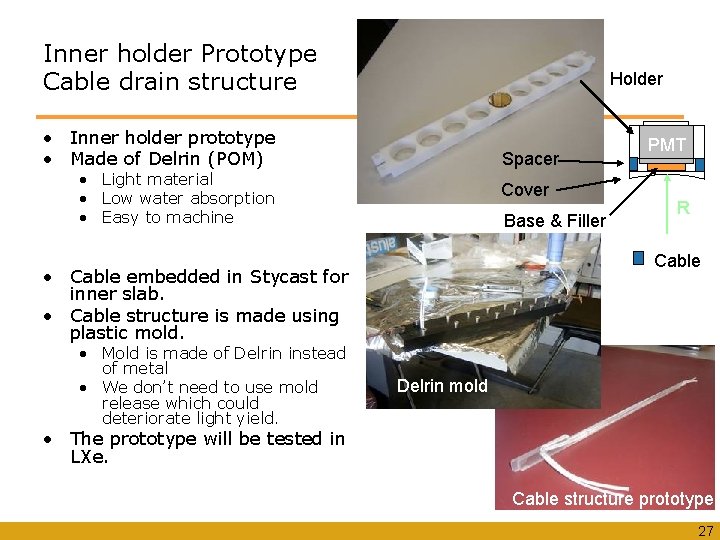
Inner holder Prototype Cable drain structure Holder • Inner holder prototype • Made of Delrin (POM) Spacer • Light material • Low water absorption • Easy to machine Cover Base & Filler R Cable • Cable embedded in Stycast for inner slab. • Cable structure is made using plastic mold. • Mold is made of Delrin instead of metal • We don’t need to use mold release which could deteriorate light yield. PMT Delrin mold • The prototype will be tested in LXe. Cable structure prototype 27
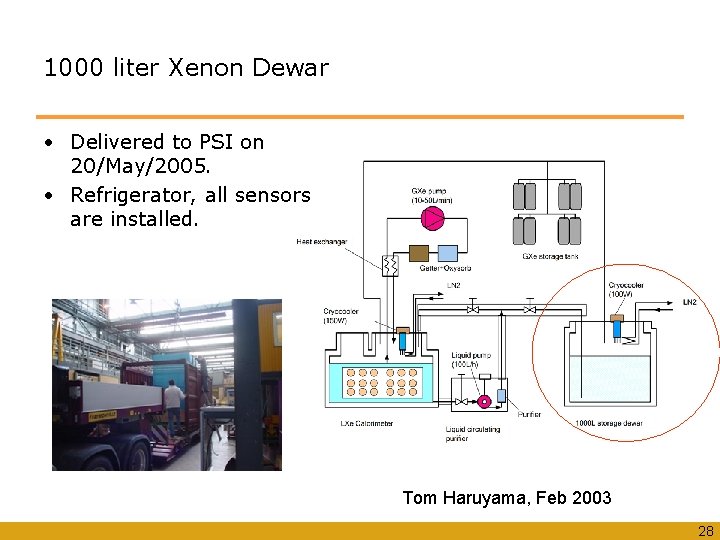
1000 liter Xenon Dewar • Delivered to PSI on 20/May/2005. • Refrigerator, all sensors are installed. Tom Haruyama, Feb 2003 28
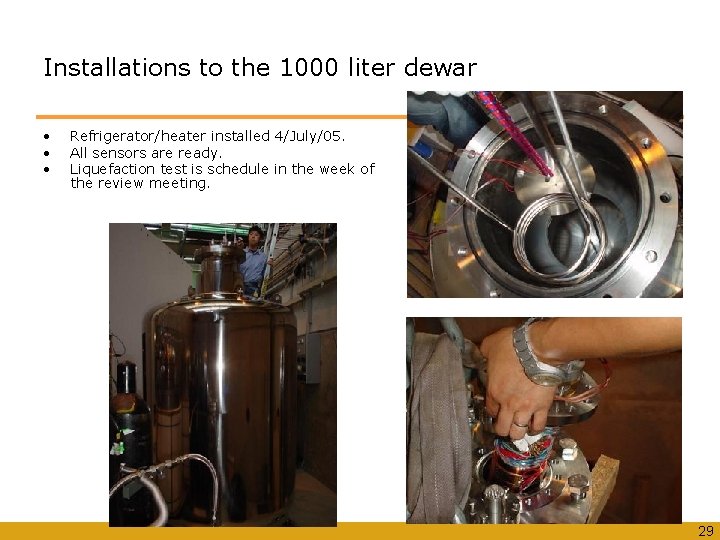
Installations to the 1000 liter dewar • • • Refrigerator/heater installed 4/July/05. All sensors are ready. Liquefaction test is schedule in the week of the review meeting. 29
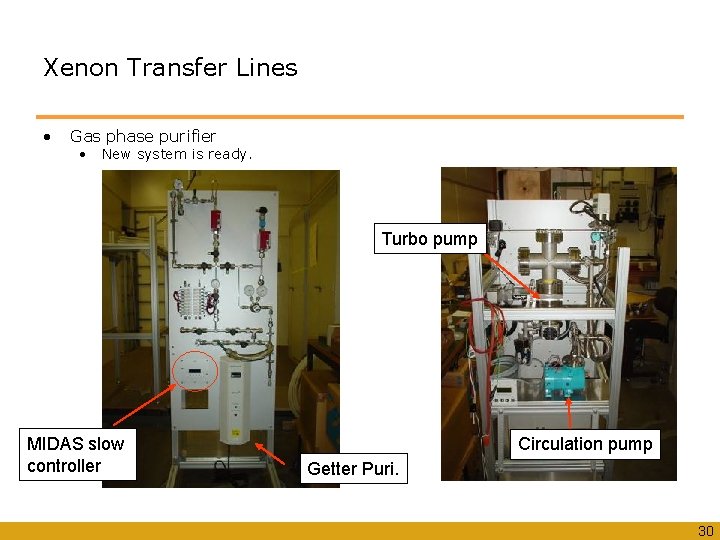
Xenon Transfer Lines • Gas phase purifier • New system is ready. Turbo pump MIDAS slow controller Circulation pump Getter Puri. 30
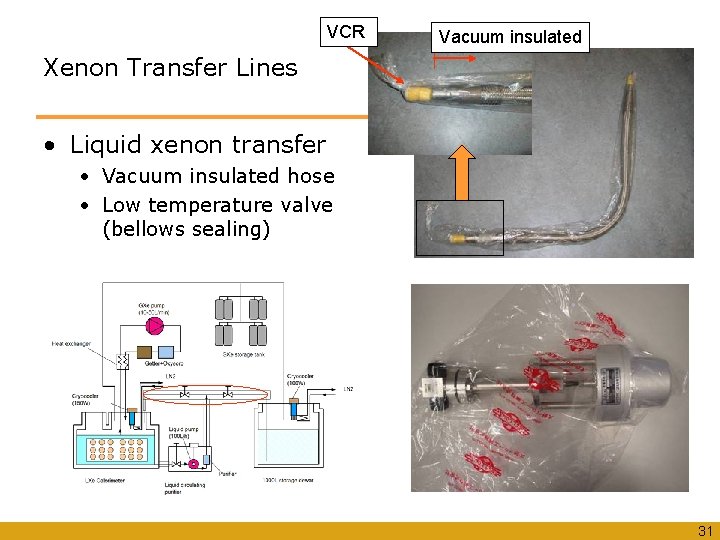
VCR Vacuum insulated Xenon Transfer Lines • Liquid xenon transfer • Vacuum insulated hose • Low temperature valve (bellows sealing) 31
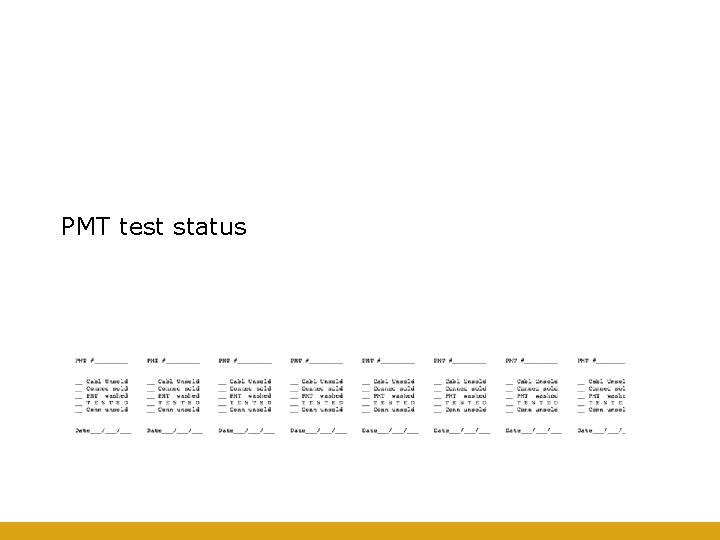
PMT test status
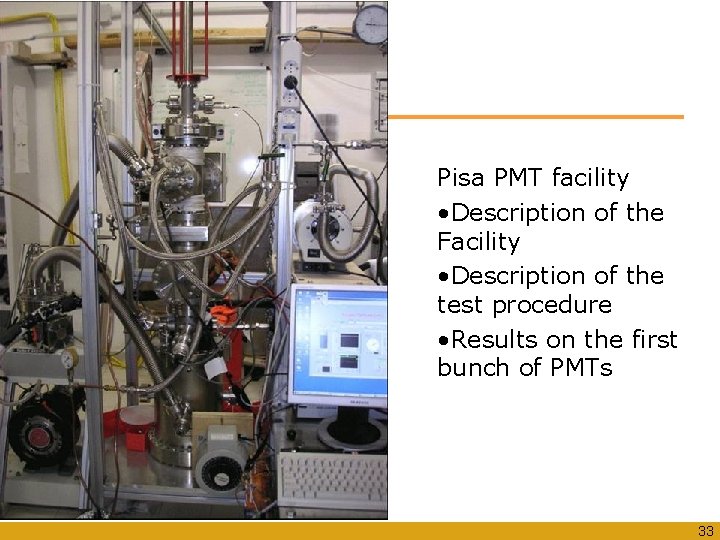
Pisa PMT facility • Description of the Facility • Description of the test procedure • Results on the first bunch of PMTs 33
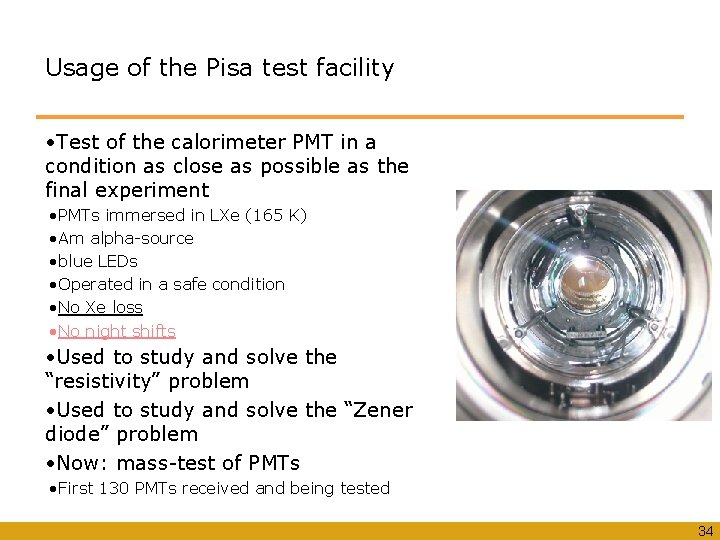
Usage of the Pisa test facility • Test of the calorimeter PMT in a condition as close as possible as the final experiment • PMTs immersed in LXe (165 K) • Am alpha-source • blue LEDs • Operated in a safe condition • No Xe loss • No night shifts • Used to study and solve the “resistivity” problem • Used to study and solve the “Zener diode” problem • Now: mass-test of PMTs • First 130 PMTs received and being tested 34
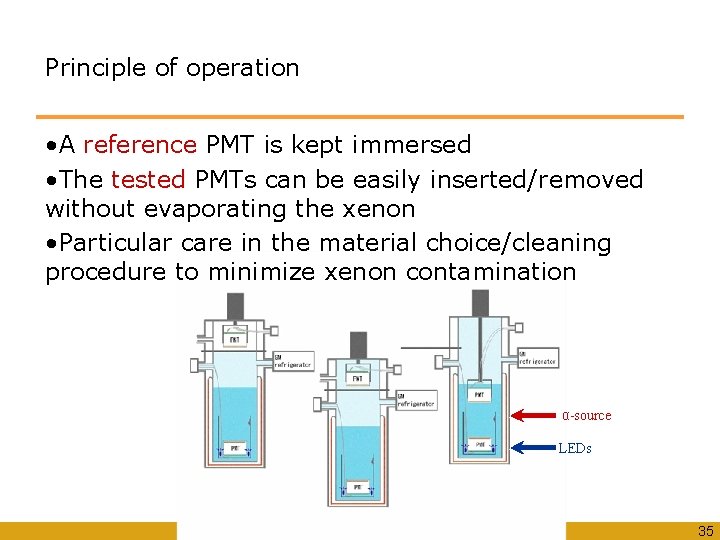
Principle of operation • A reference PMT is kept immersed • The tested PMTs can be easily inserted/removed without evaporating the xenon • Particular care in the material choice/cleaning procedure to minimize xenon contamination α-source LEDs 35
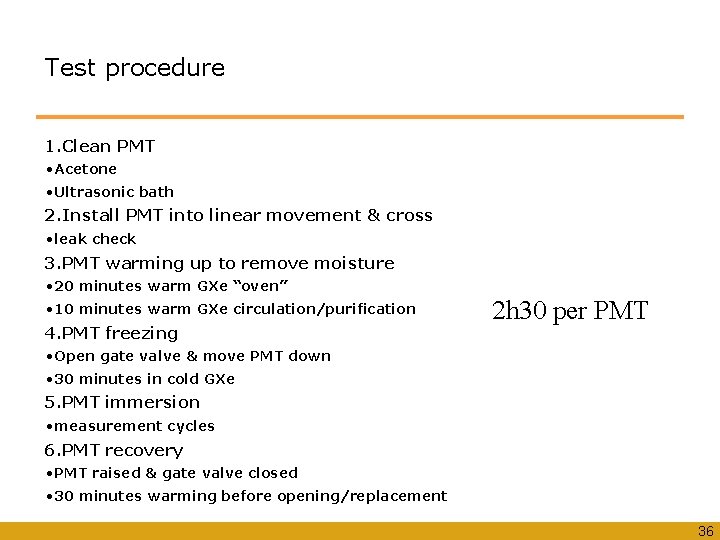
Test procedure 1. Clean PMT • Acetone • Ultrasonic bath 2. Install PMT into linear movement & cross • leak check 3. PMT warming up to remove moisture • 20 minutes warm GXe “oven” • 10 minutes warm GXe circulation/purification 4. PMT freezing 2 h 30 per PMT • Open gate valve & move PMT down • 30 minutes in cold GXe 5. PMT immersion • measurement cycles 6. PMT recovery • PMT raised & gate valve closed • 30 minutes warming before opening/replacement 36
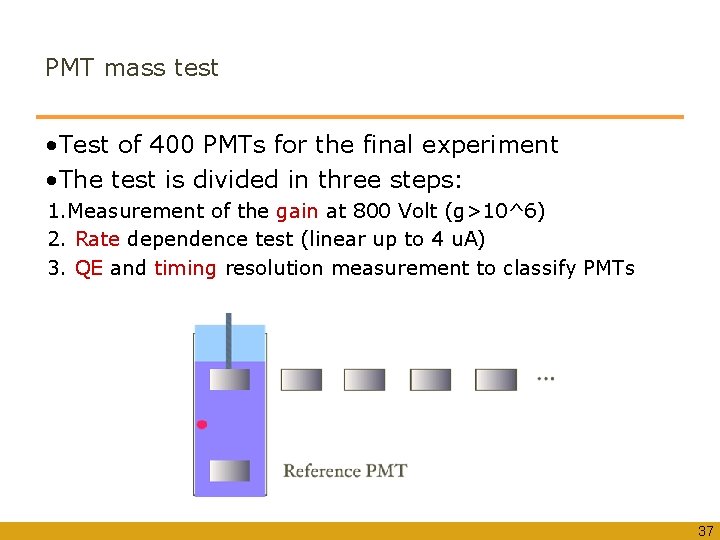
PMT mass test • Test of 400 PMTs for the final experiment • The test is divided in three steps: 1. Measurement of the gain at 800 Volt (g>10^6) 2. Rate dependence test (linear up to 4 u. A) 3. QE and timing resolution measurement to classify PMTs 37
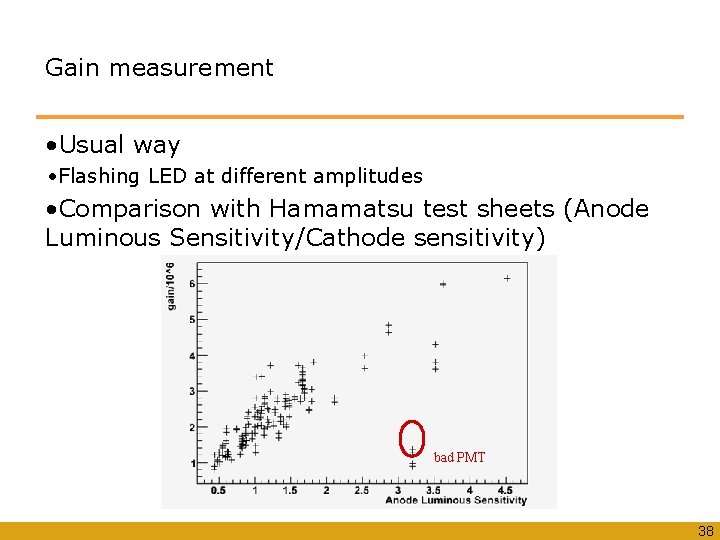
Gain measurement • Usual way • Flashing LED at different amplitudes • Comparison with Hamamatsu test sheets (Anode Luminous Sensitivity/Cathode sensitivity) bad PMT 38
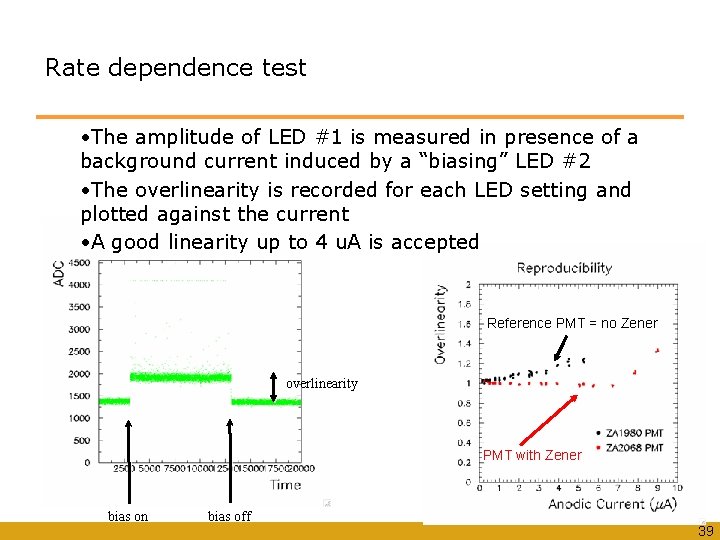
Rate dependence test • The amplitude of LED #1 is measured in presence of a background current induced by a “biasing” LED #2 • The overlinearity is recorded for each LED setting and plotted against the current • A good linearity up to 4 u. A is accepted Reference PMT = no Zener overlinearity PMT with Zener bias on bias off 39
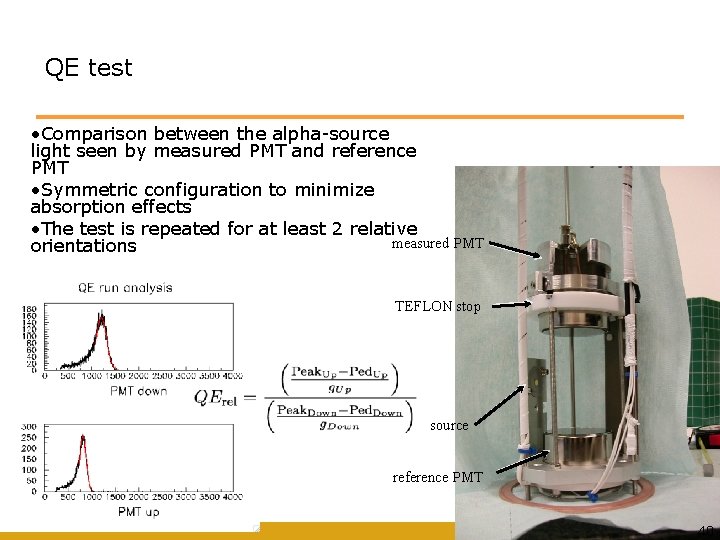
QE test • Comparison between the alpha-source light seen by measured PMT and reference PMT • Symmetric configuration to minimize absorption effects • The test is repeated for at least 2 relative measured PMT orientations TEFLON stop source reference PMT 40
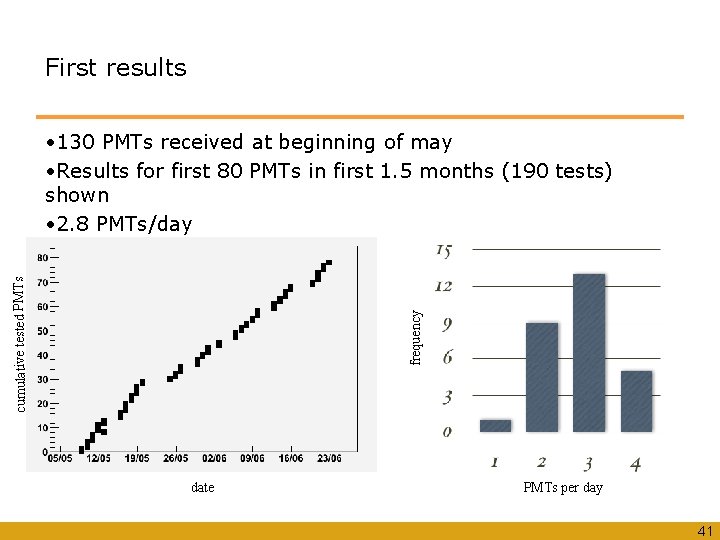
First results frequency cumulative tested PMTs • 130 PMTs received at beginning of may • Results for first 80 PMTs in first 1. 5 months (190 tests) shown • 2. 8 PMTs/day date PMTs per day 41
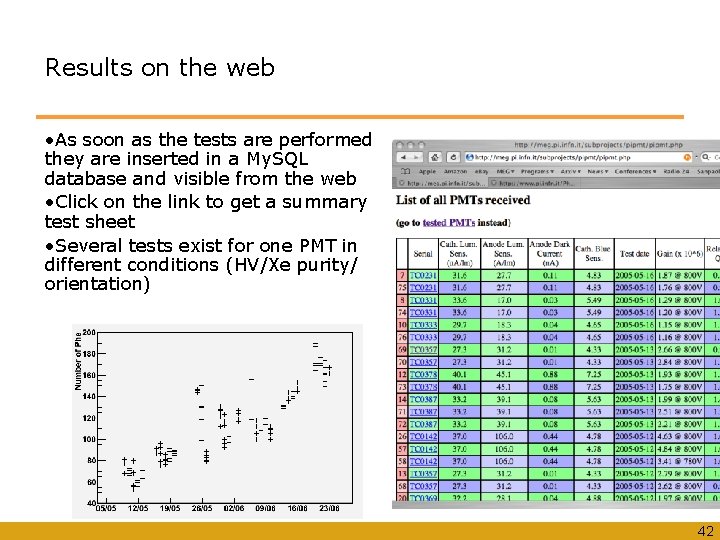
Results on the web • As soon as the tests are performed they are inserted in a My. SQL database and visible from the web • Click on the link to get a summary test sheet • Several tests exist for one PMT in different conditions (HV/Xe purity/ orientation) 42
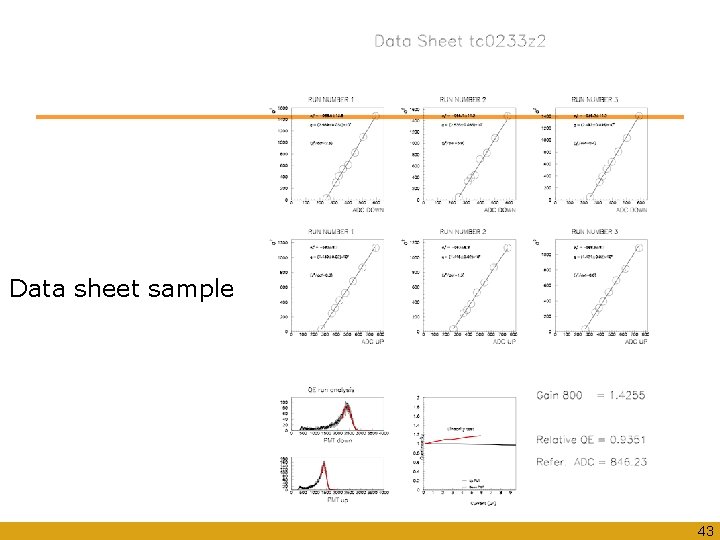
Data sheet sample 43
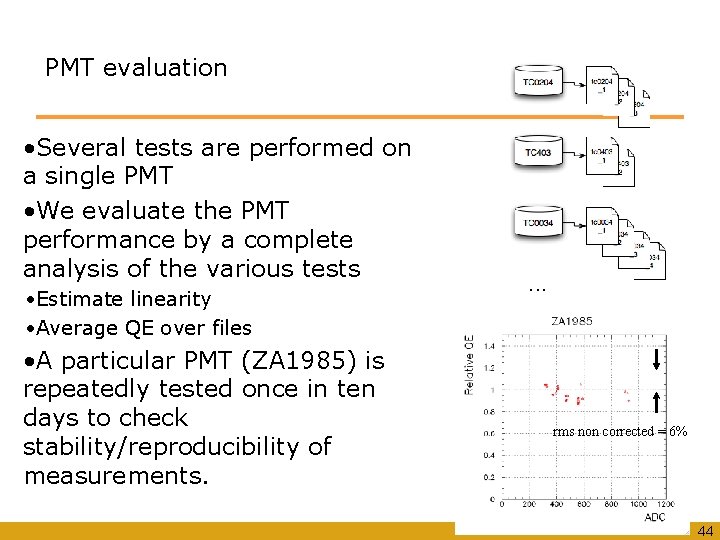
PMT evaluation • Several tests are performed on a single PMT • We evaluate the PMT performance by a complete analysis of the various tests • Estimate linearity • Average QE over files • A particular PMT (ZA 1985) is repeatedly tested once in ten days to check stability/reproducibility of measurements. . rms non corrected = 6% 44
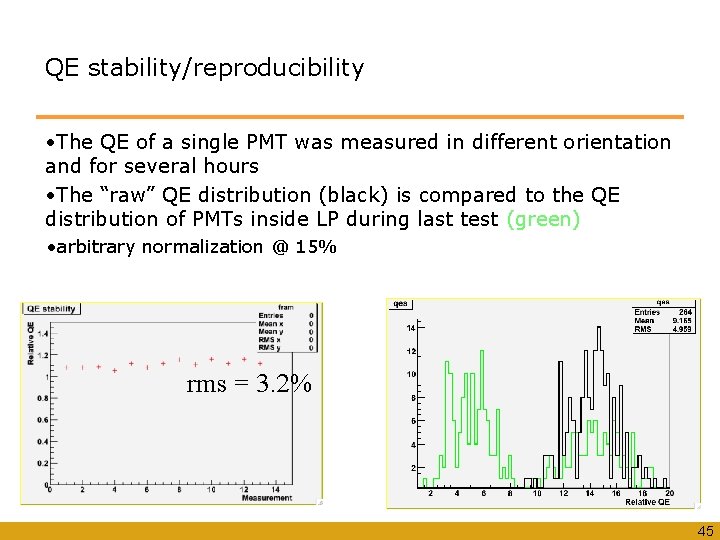
QE stability/reproducibility • The QE of a single PMT was measured in different orientation and for several hours • The “raw” QE distribution (black) is compared to the QE distribution of PMTs inside LP during last test (green) • arbitrary normalization @ 15% rms = 3. 2% 45
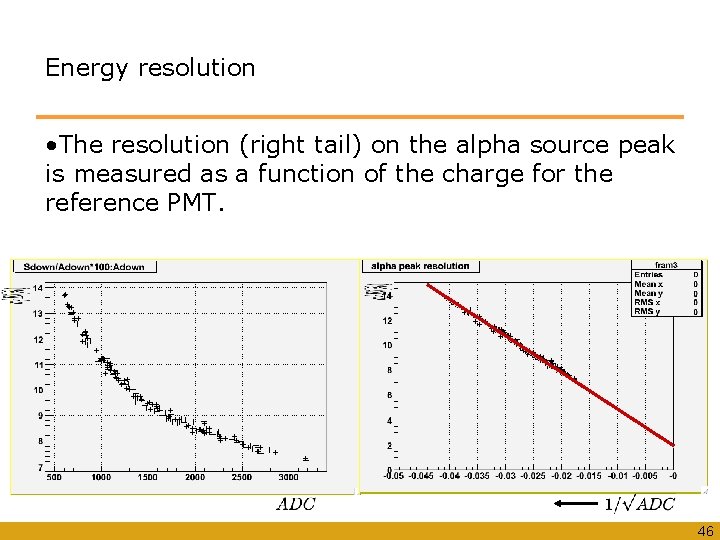
Energy resolution • The resolution (right tail) on the alpha source peak is measured as a function of the charge for the reference PMT. 46
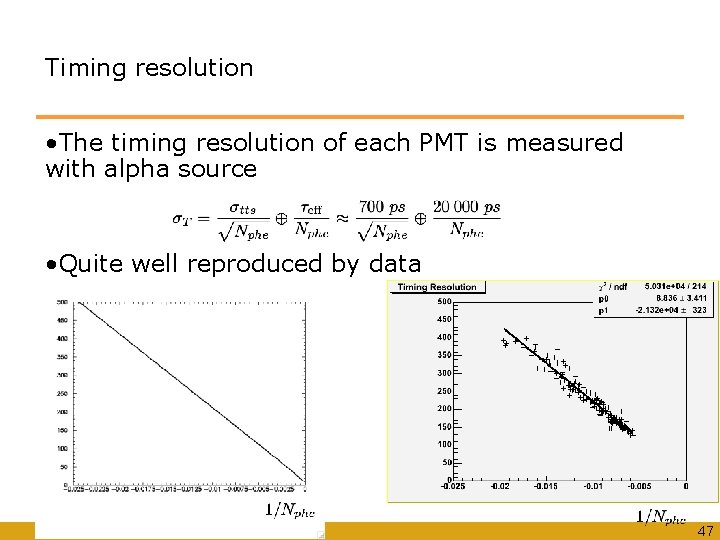
Timing resolution • The timing resolution of each PMT is measured with alpha source • Quite well reproduced by data 47
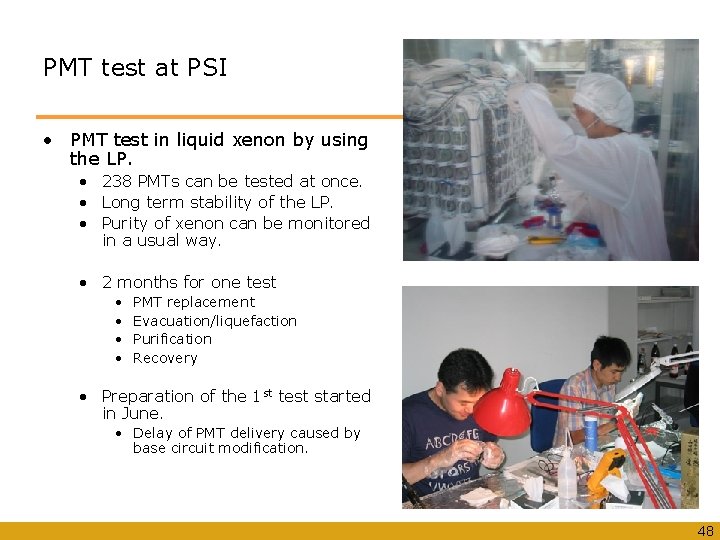
PMT test at PSI • PMT test in liquid xenon by using the LP. • 238 PMTs can be tested at once. • Long term stability of the LP. • Purity of xenon can be monitored in a usual way. • 2 months for one test • • PMT replacement Evacuation/liquefaction Purification Recovery • Preparation of the 1 st test started in June. • Delay of PMT delivery caused by base circuit modification. 48
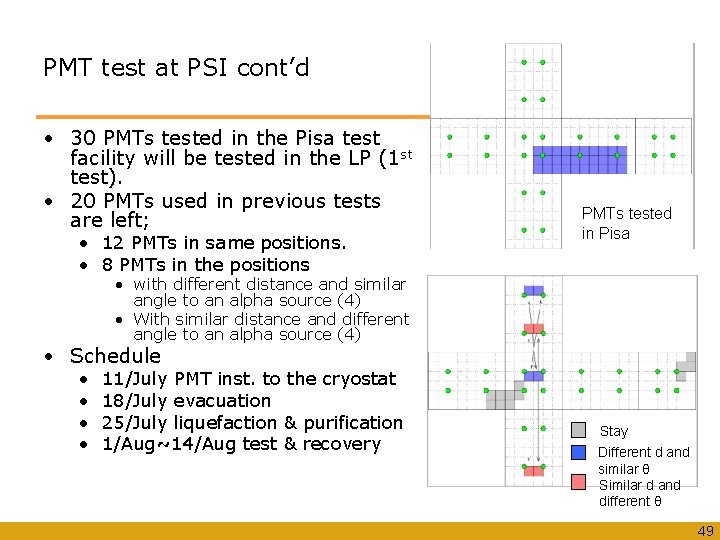
PMT test at PSI cont’d • 30 PMTs tested in the Pisa test facility will be tested in the LP (1 st test). • 20 PMTs used in previous tests are left; • 12 PMTs in same positions. • 8 PMTs in the positions PMTs tested in Pisa • with different distance and similar angle to an alpha source (4) • With similar distance and different angle to an alpha source (4) • Schedule • • 11/July PMT inst. to the cryostat 18/July evacuation 25/July liquefaction & purification 1/Aug~14/Aug test & recovery Stay Different d and similar θ Similar d and different θ 49
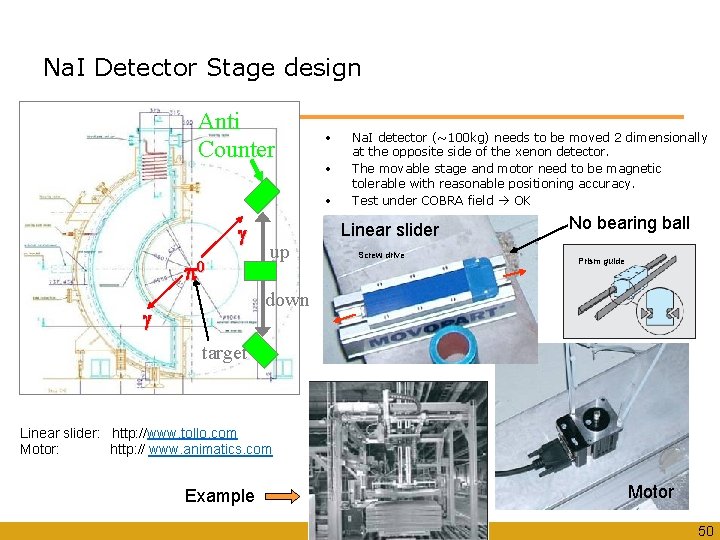
Na. I Detector Stage design Anti Counter • • • g p 0 Na. I detector (~100 kg) needs to be moved 2 dimensionally at the opposite side of the xenon detector. The movable stage and motor need to be magnetic tolerable with reasonable positioning accuracy. Test under COBRA field OK Linear slider up Screw drive No bearing ball Prism guide down g target Linear slider: http: //www. tollo. com Motor: http: // www. animatics. com Example Motor 50
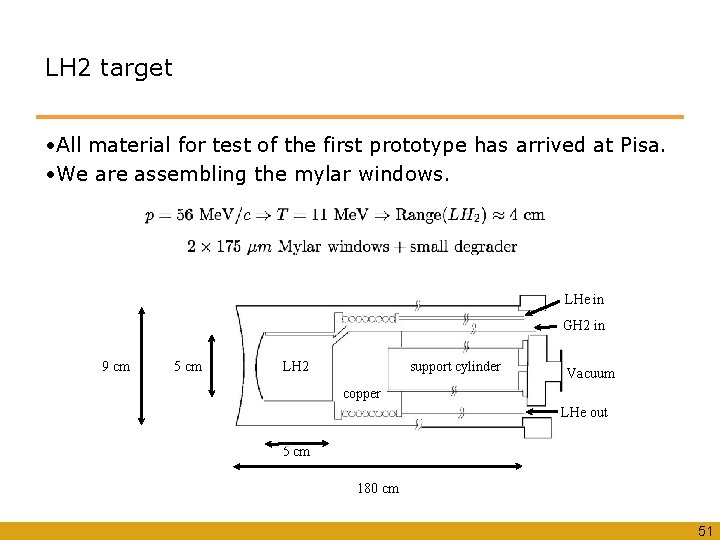
LH 2 target • All material for test of the first prototype has arrived at Pisa. • We are assembling the mylar windows. LHe in GH 2 in 9 cm 5 cm LH 2 support cylinder Vacuum copper LHe out 5 cm 180 cm 51
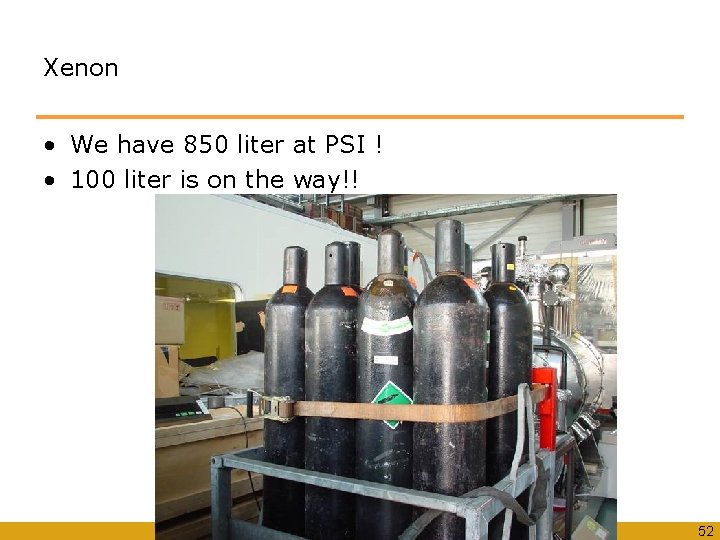
Xenon • We have 850 liter at PSI ! • 100 liter is on the way!! 52
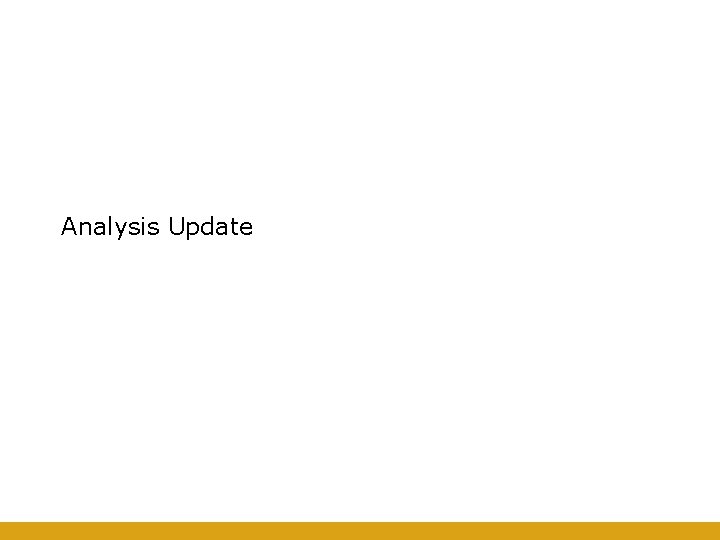
Analysis Update
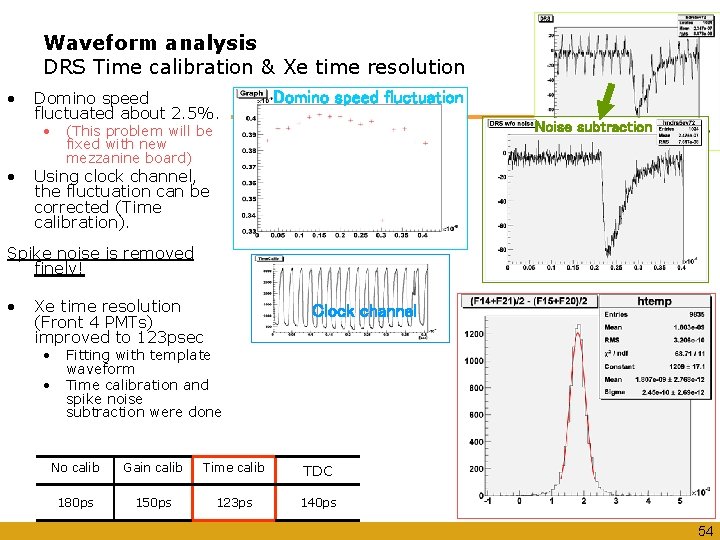
Waveform analysis DRS Time calibration & Xe time resolution • Domino speed fluctuated about 2. 5%. • • Domino speed fluctuation Noise subtraction (This problem will be fixed with new mezzanine board) Using clock channel, the fluctuation can be corrected (Time calibration). Spike noise is removed finely! • Xe time resolution (Front 4 PMTs) improved to 123 psec • • Clock channel Fitting with template waveform Time calibration and spike noise subtraction were done No calib Gain calib Time calib TDC 180 ps 150 ps 123 ps 140 ps 54
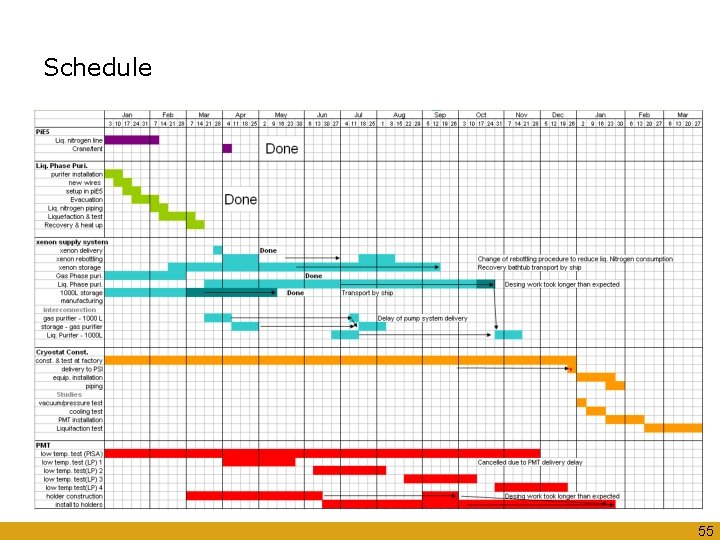
Schedule 55