Wspczesne koncepcje ZP Zakres zarzdzania USA APICS JAPONIA
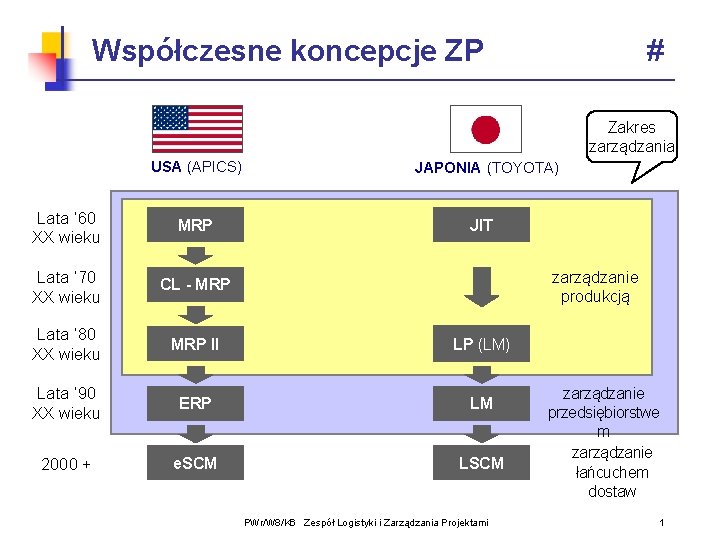
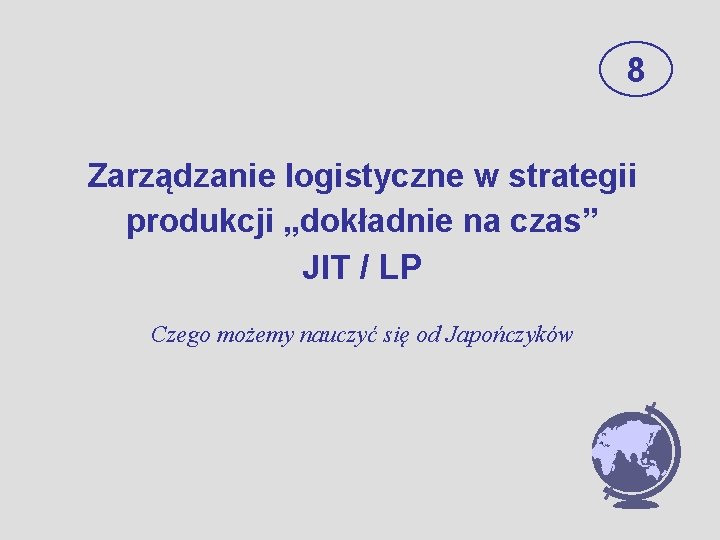
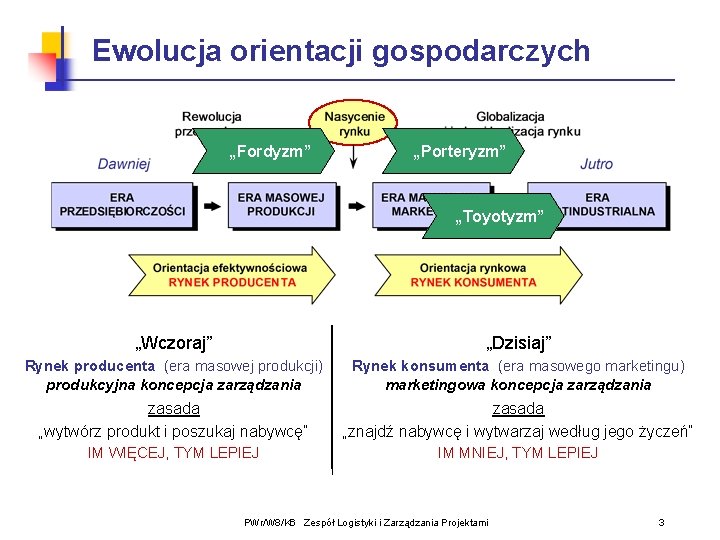
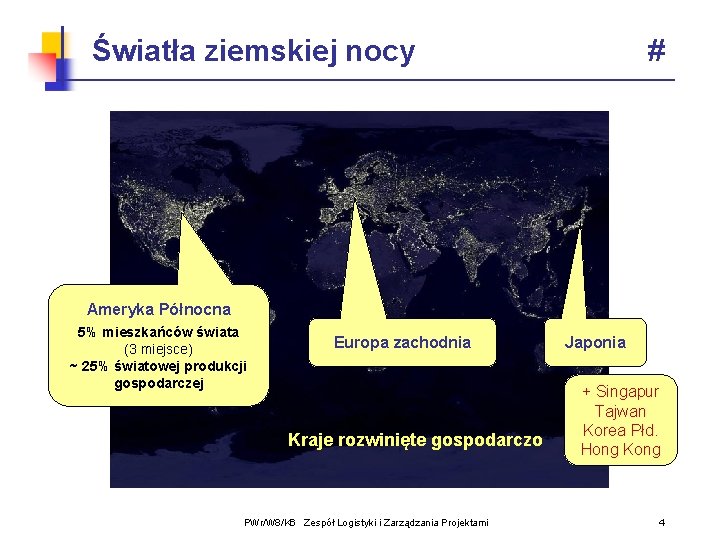
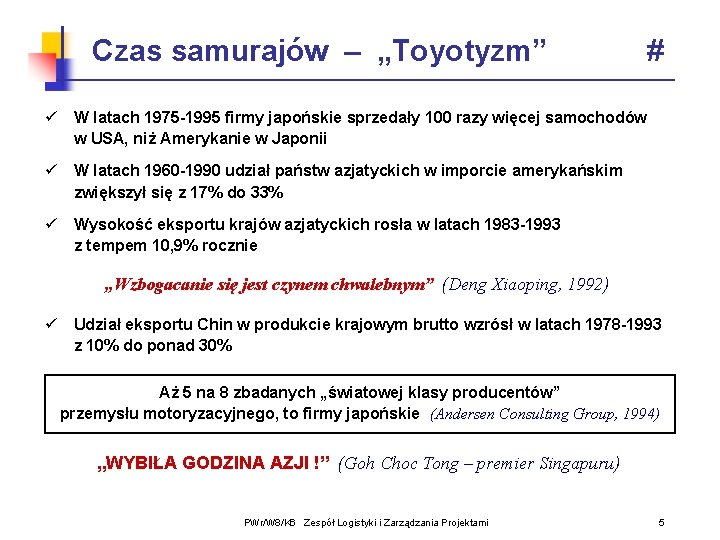
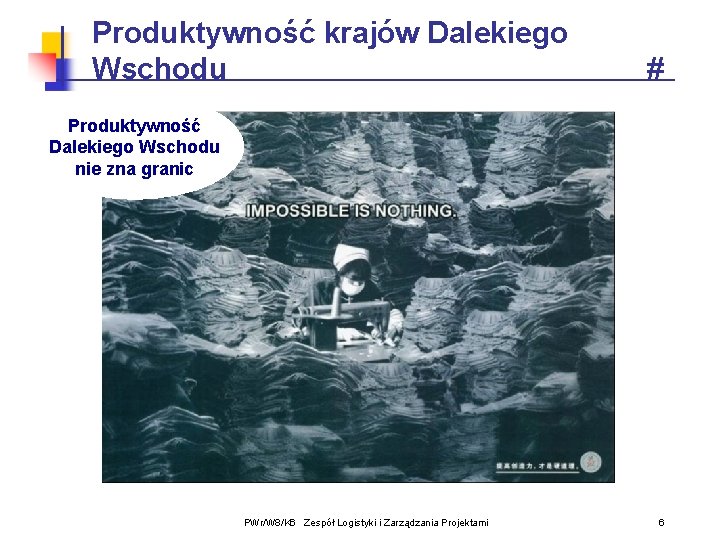
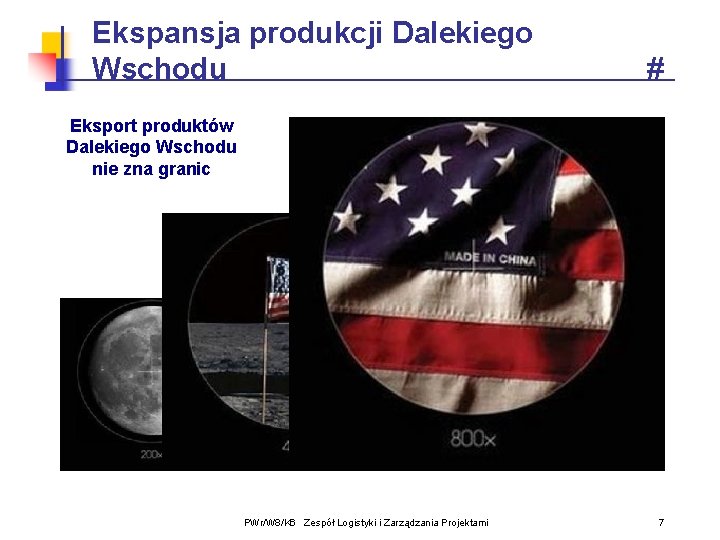
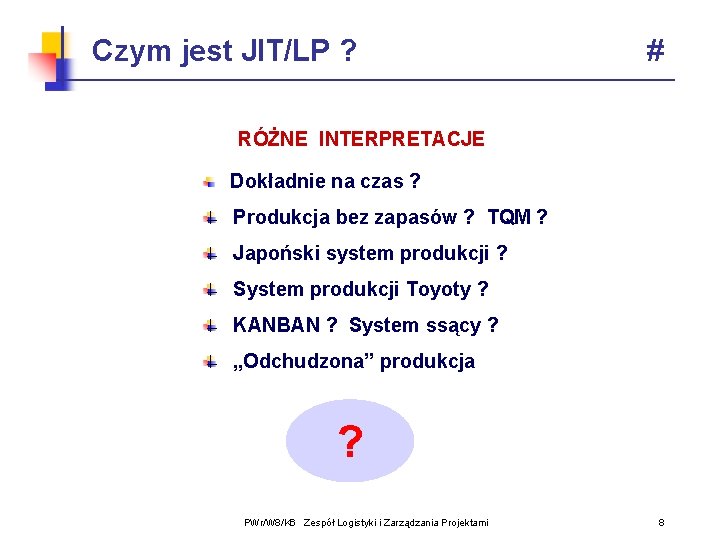
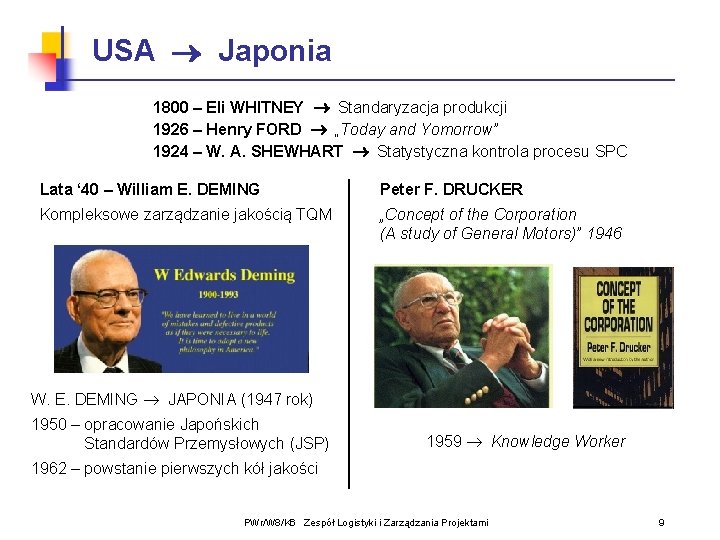
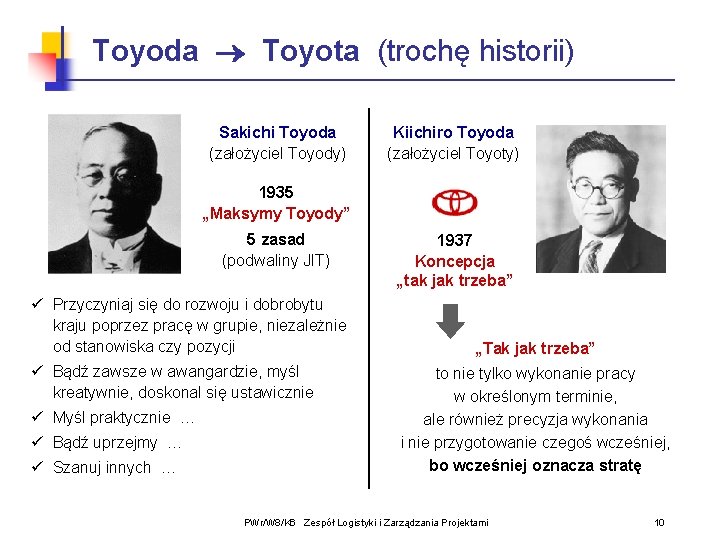
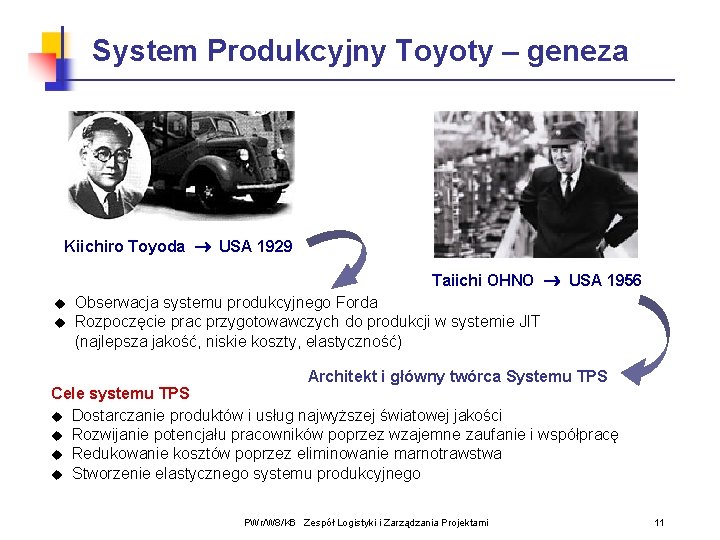
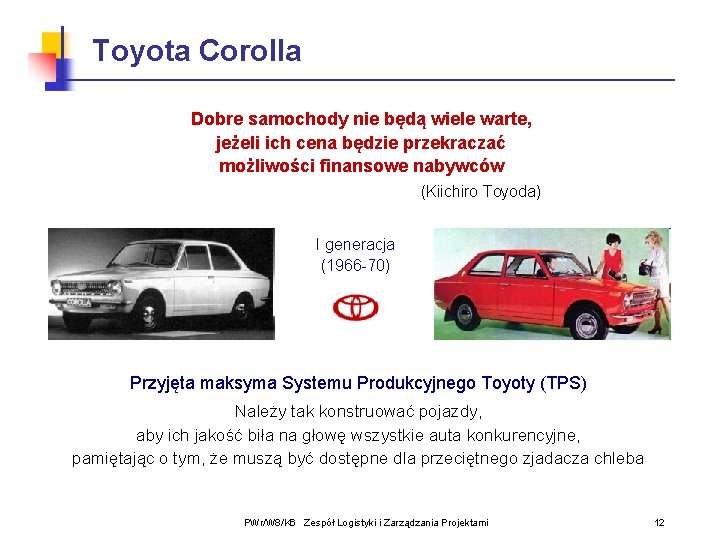
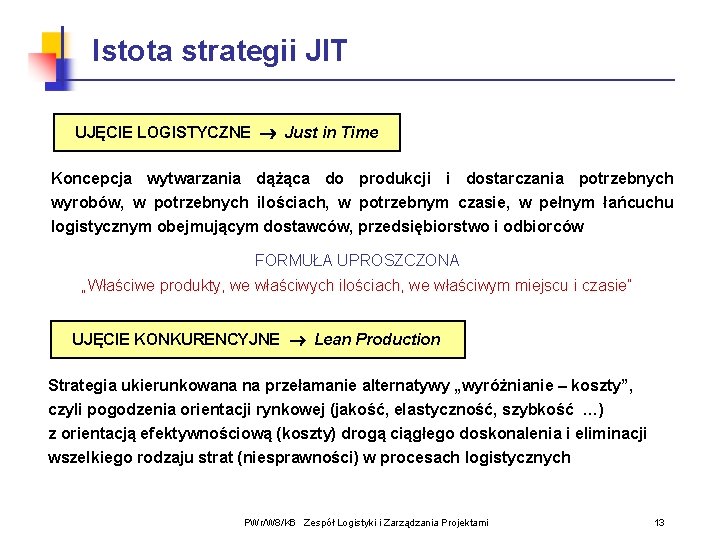
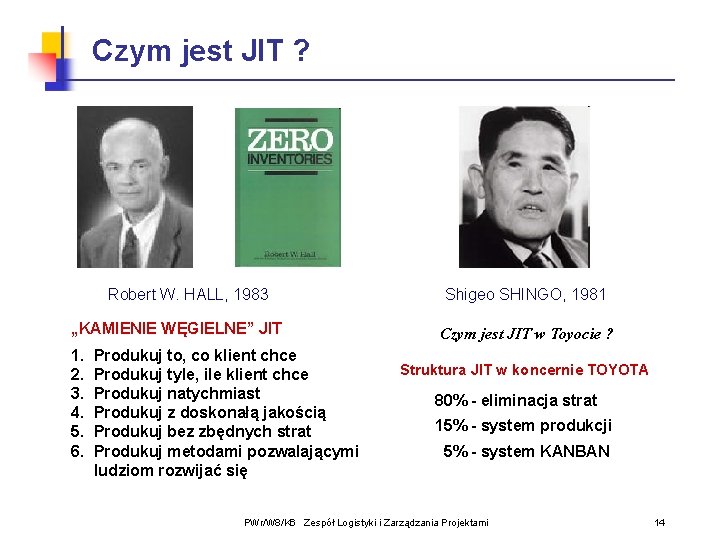
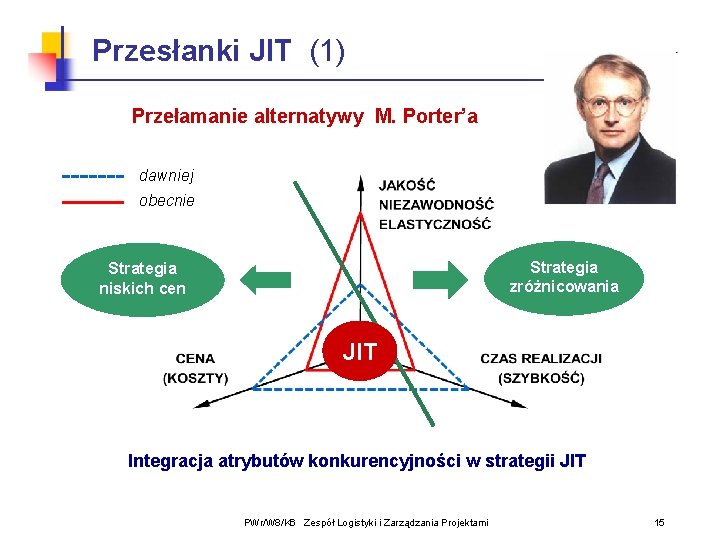
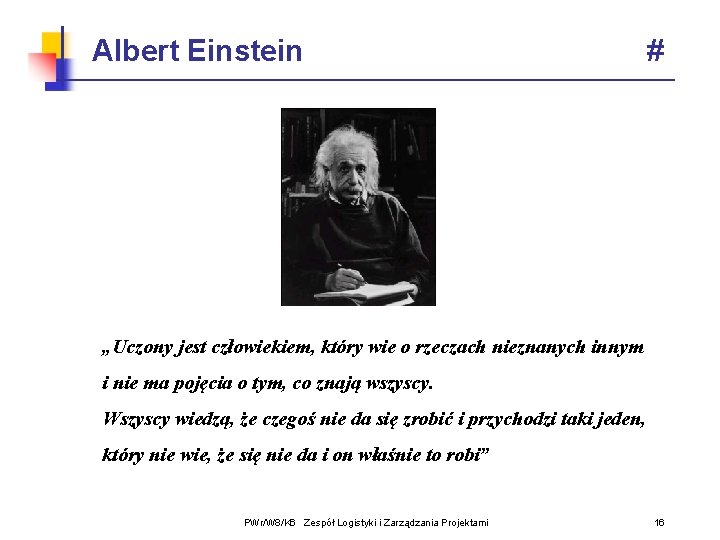

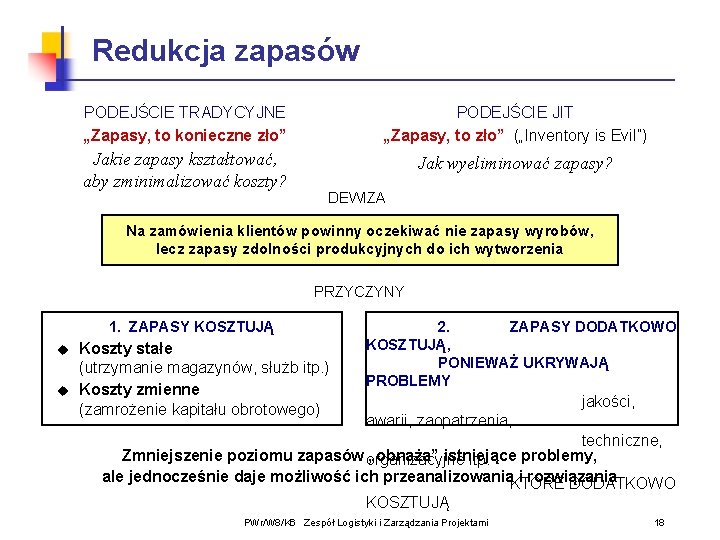
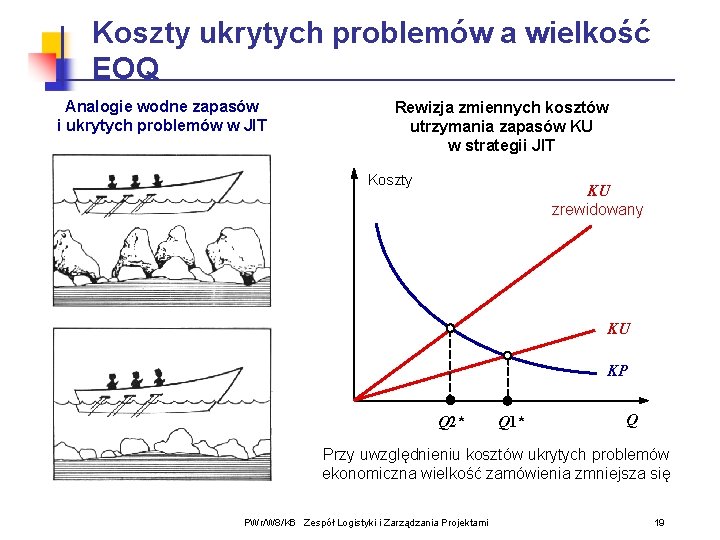
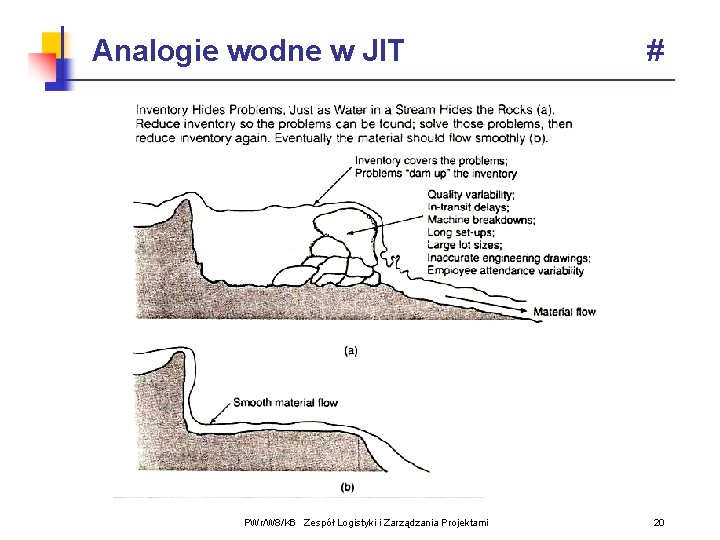
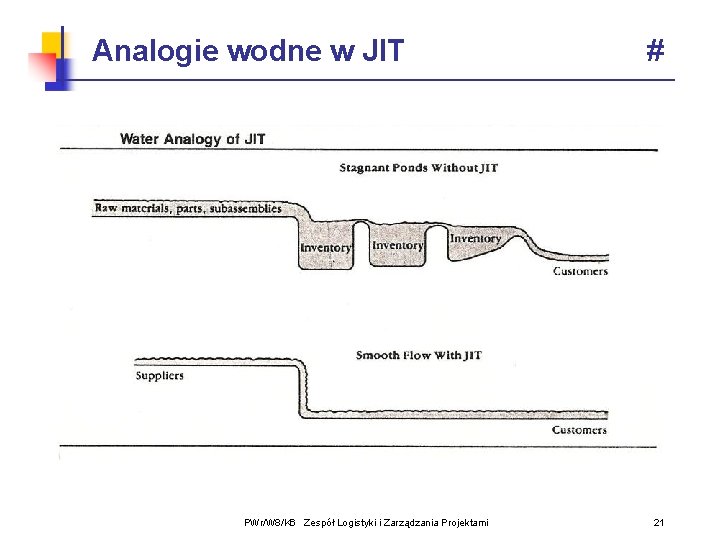
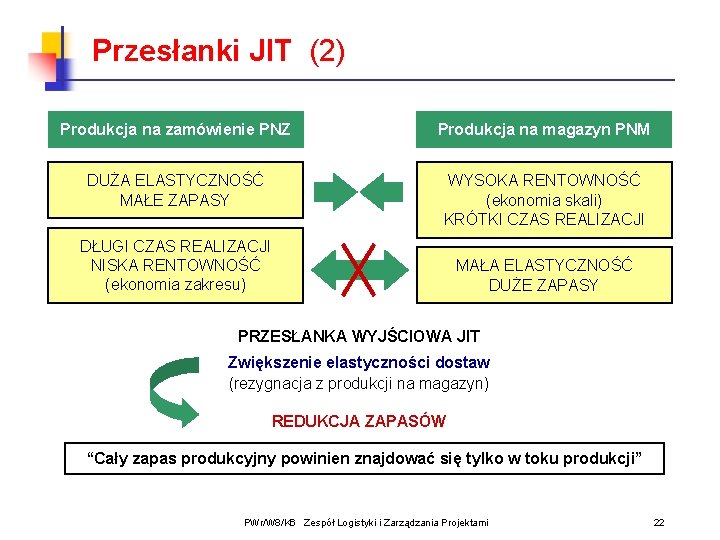
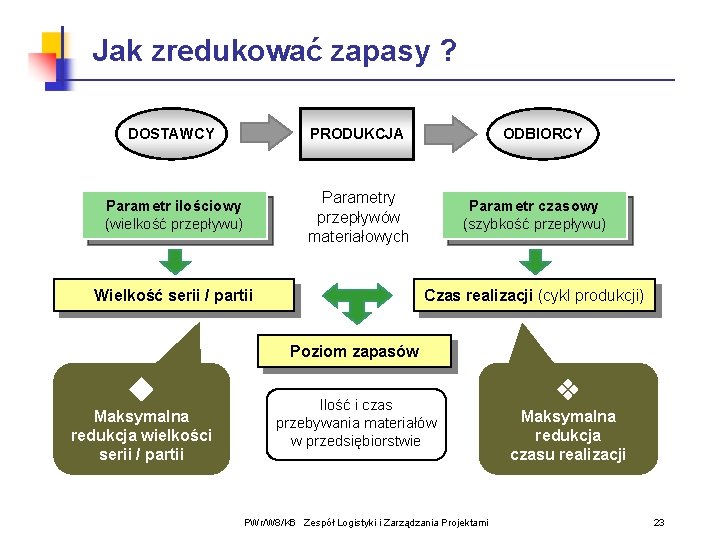
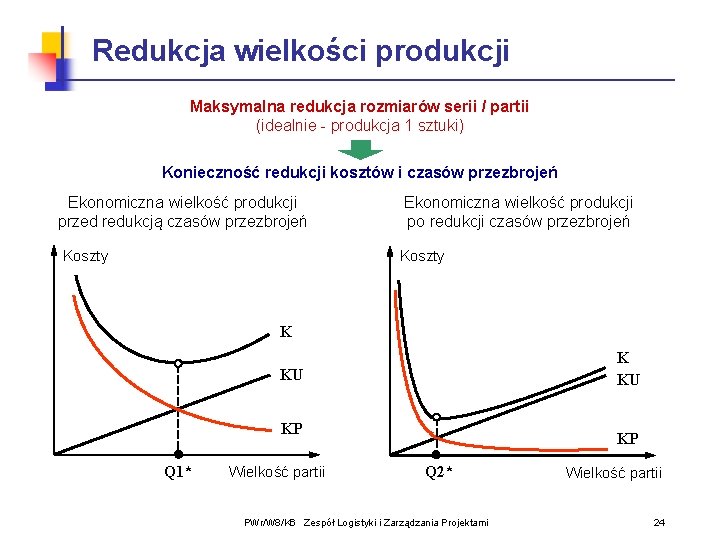
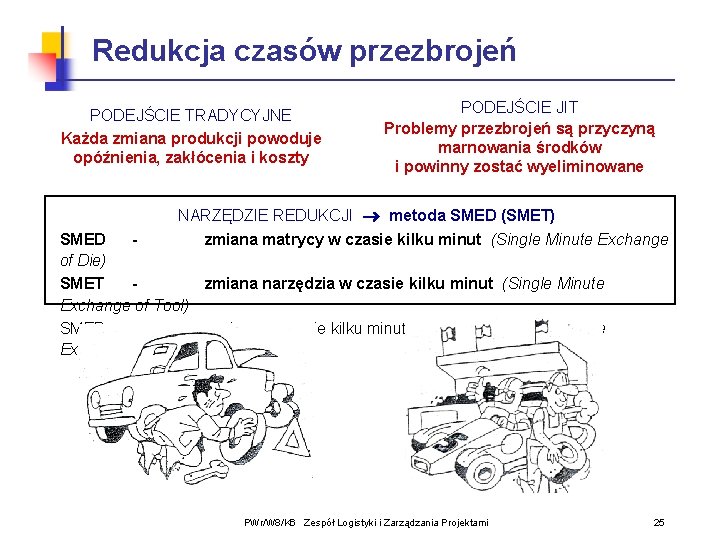
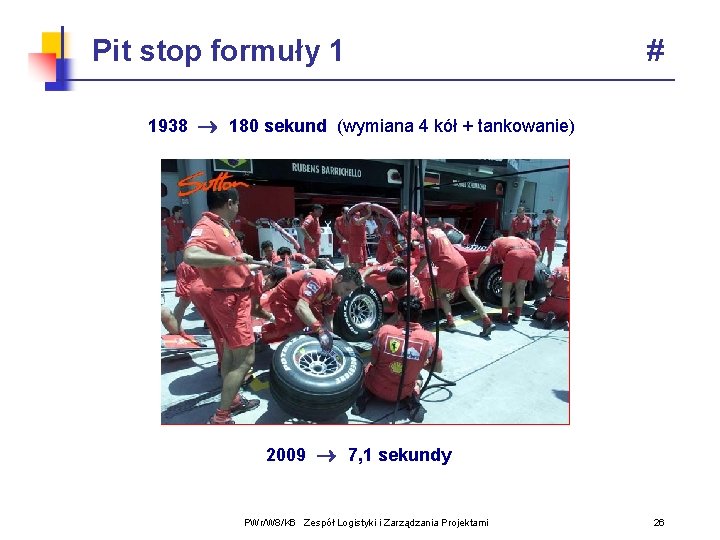
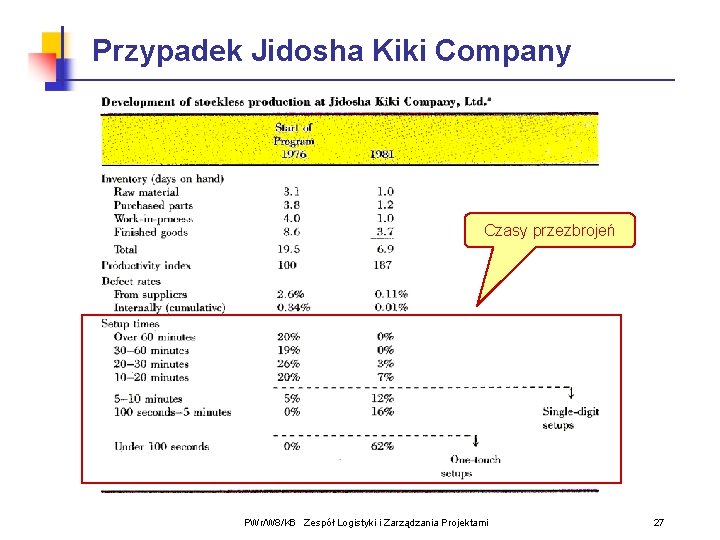
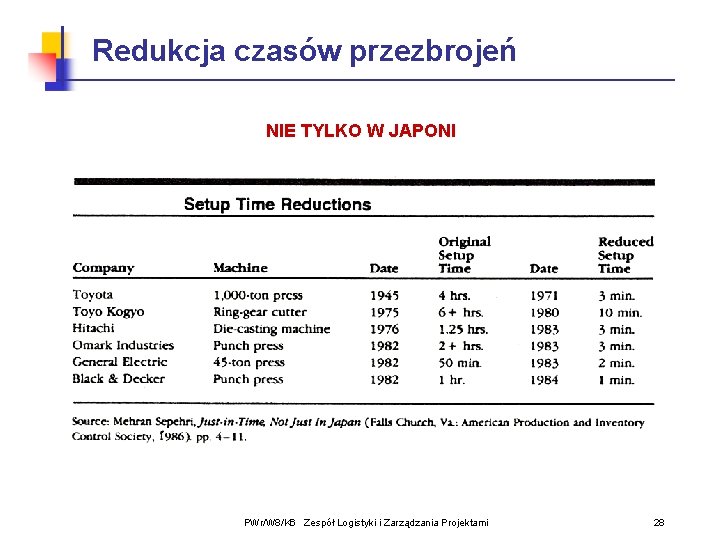
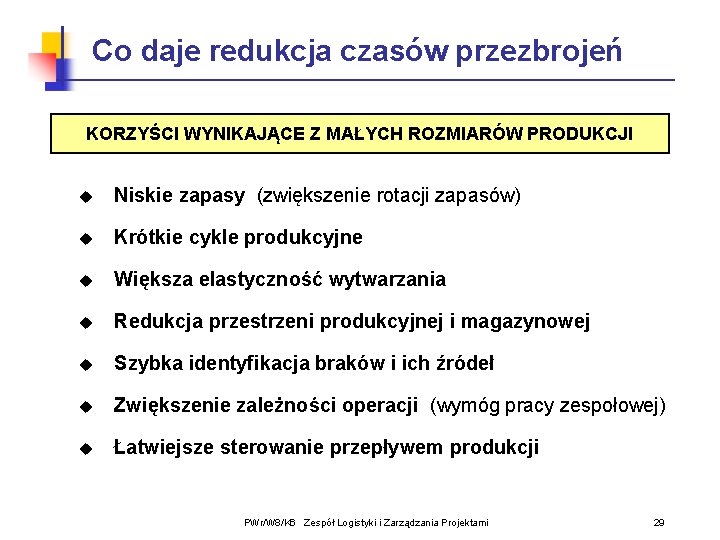
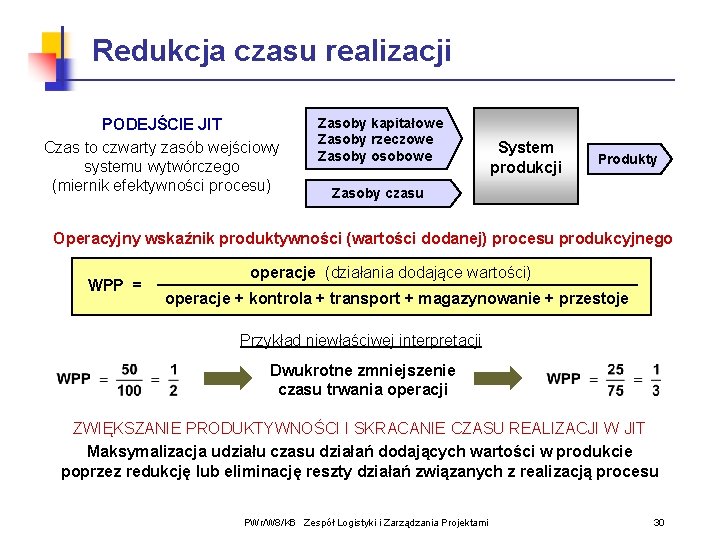
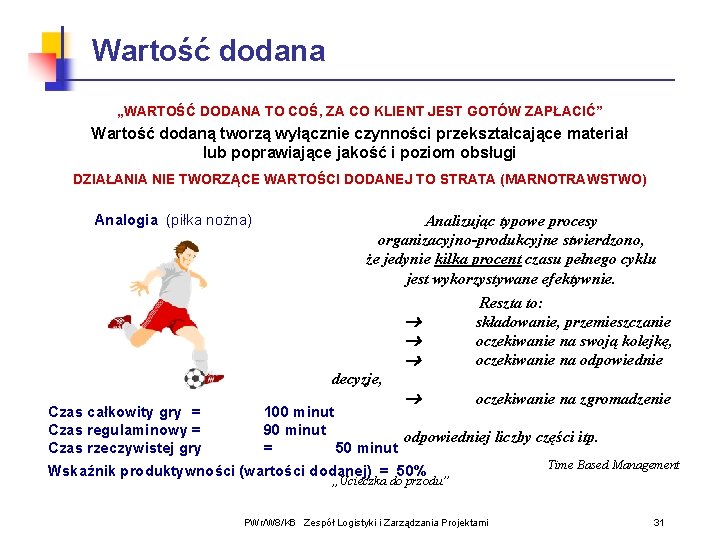
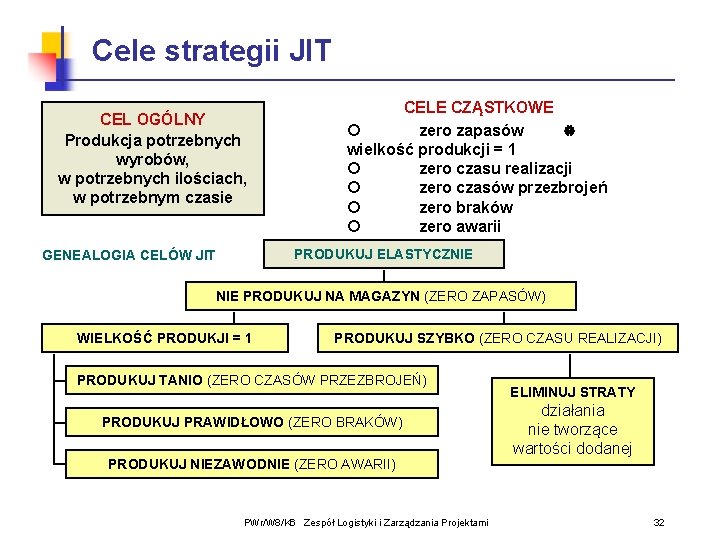
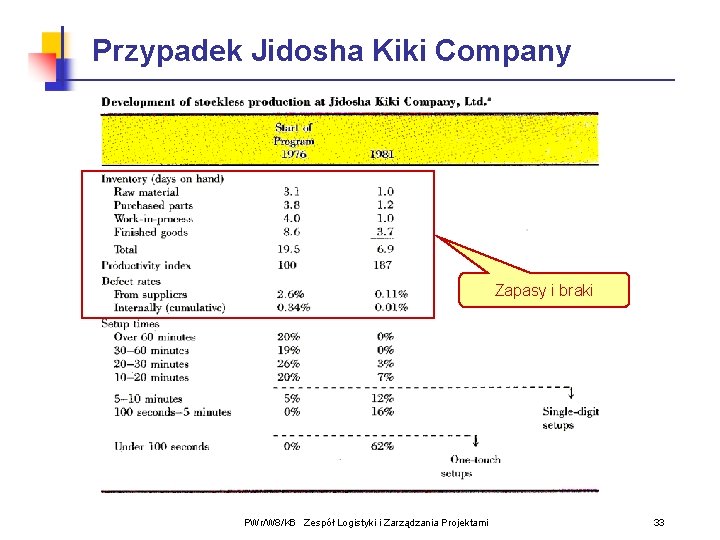
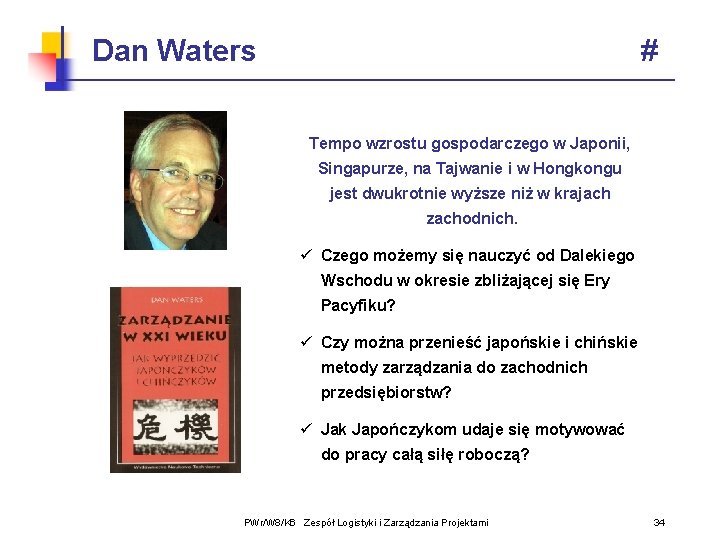
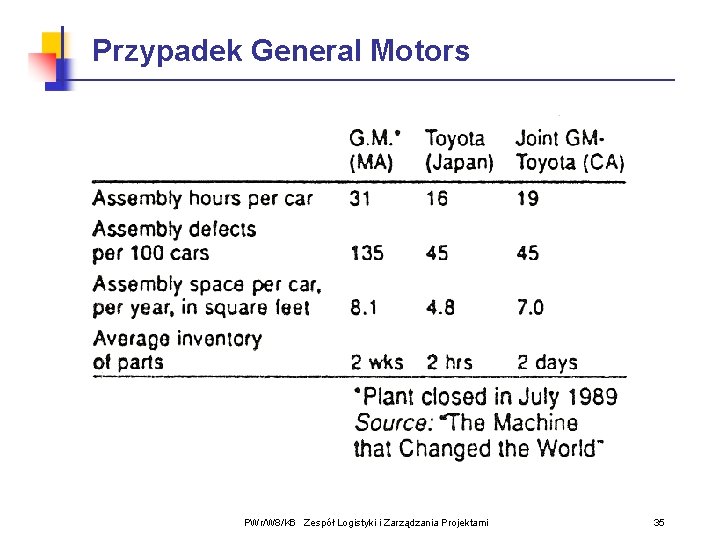
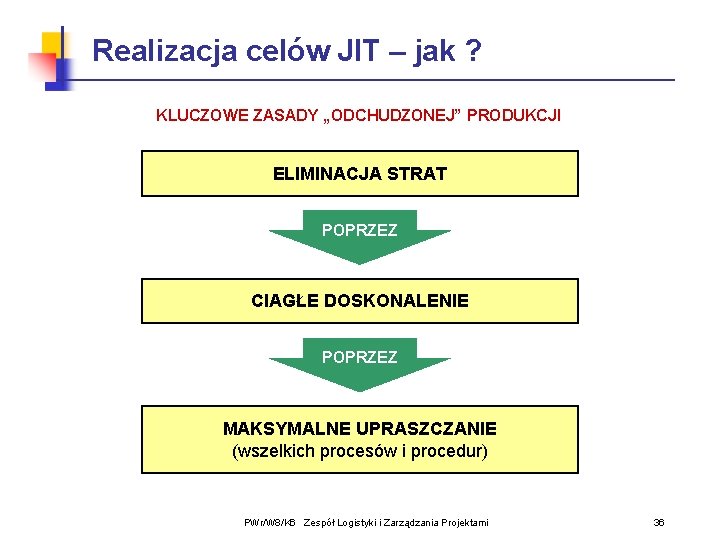
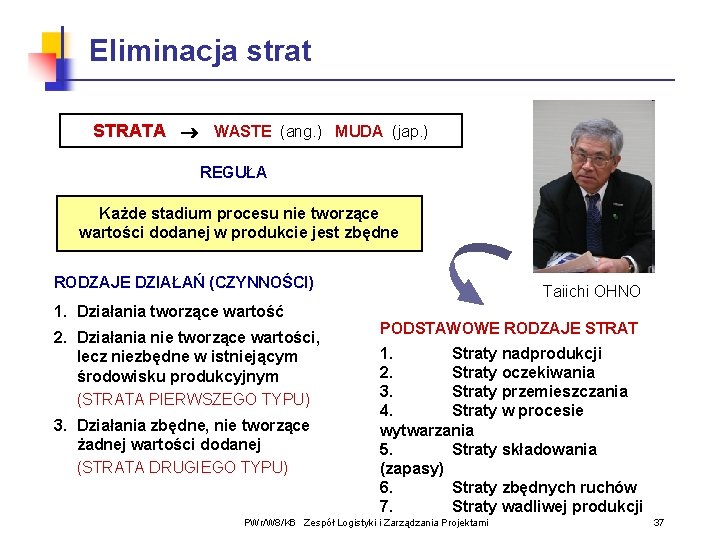
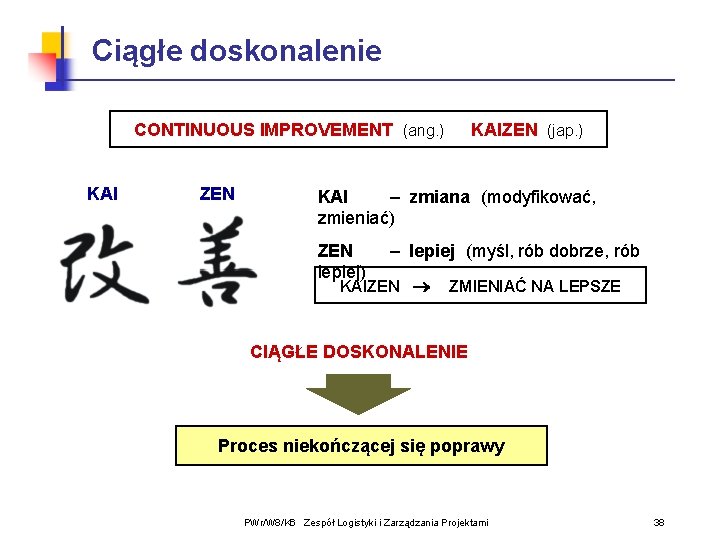
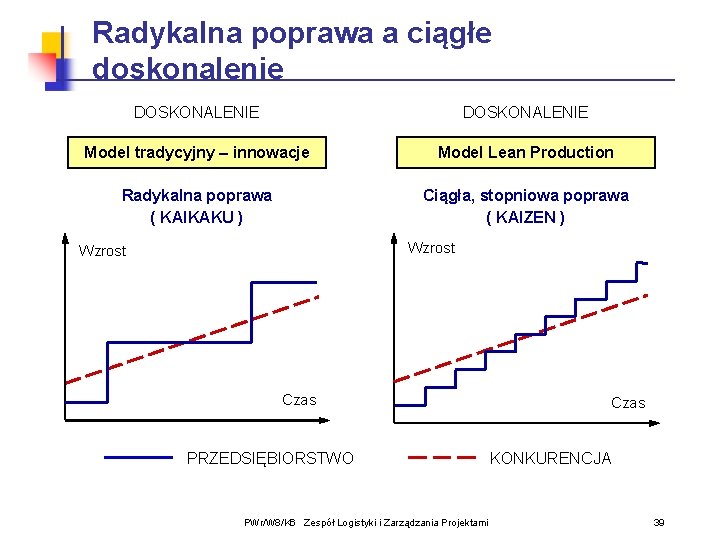
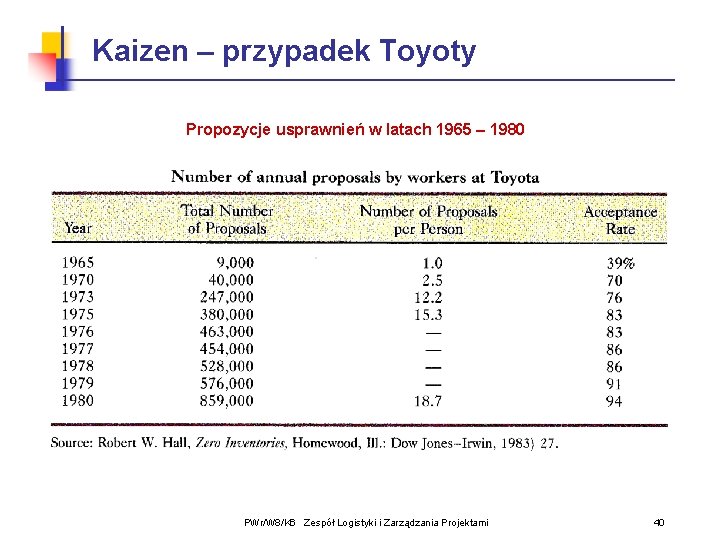
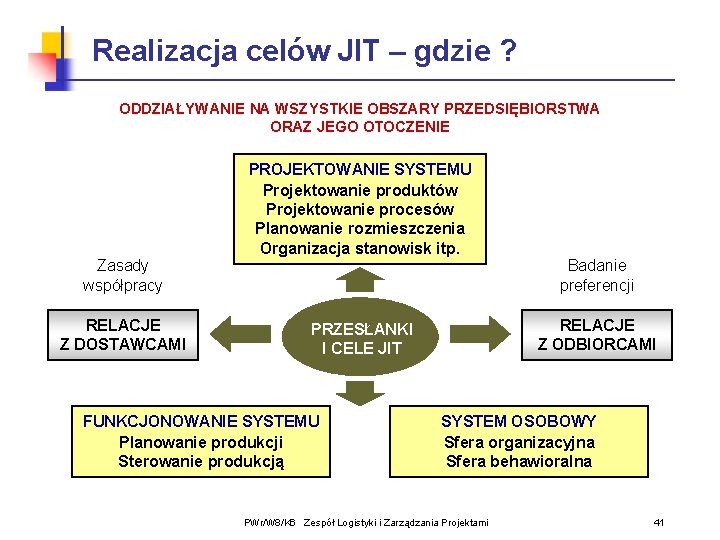
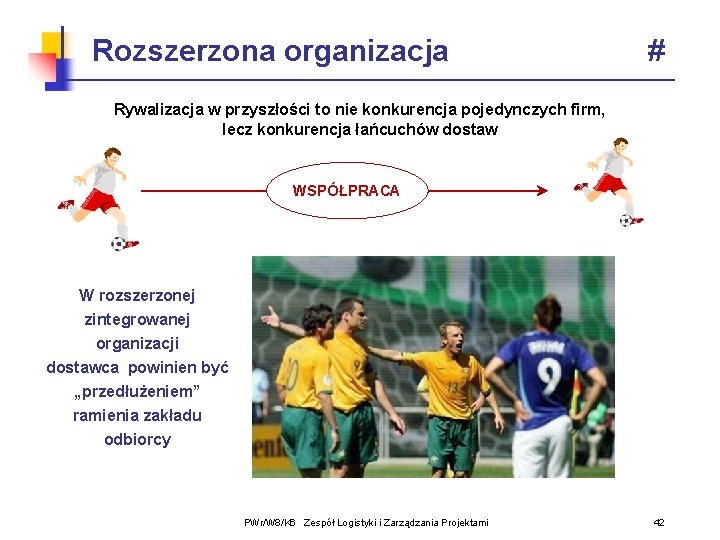
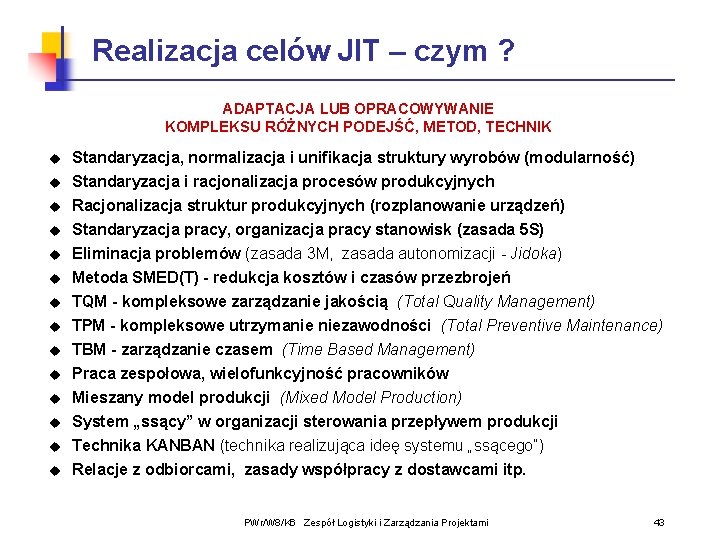
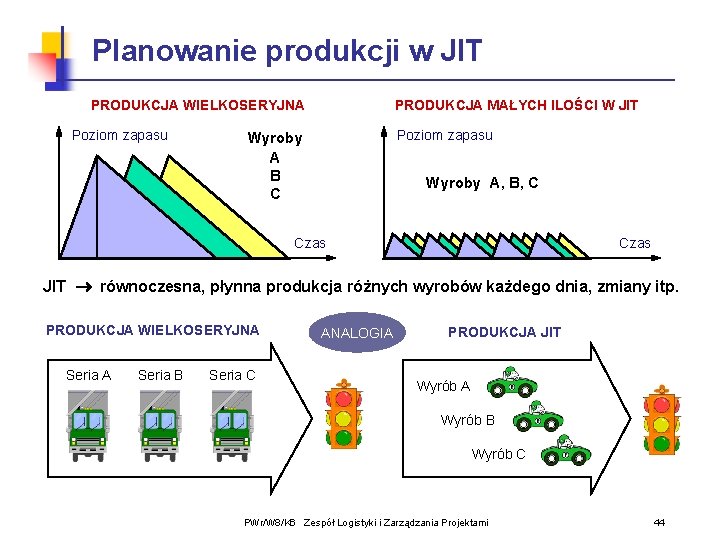
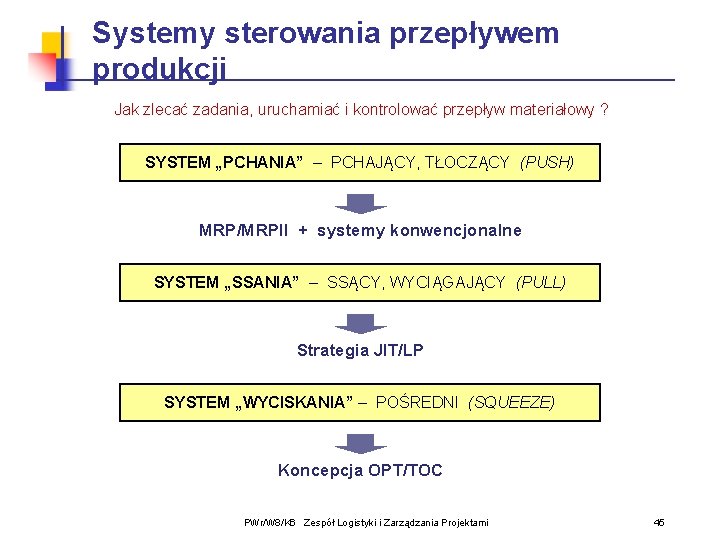
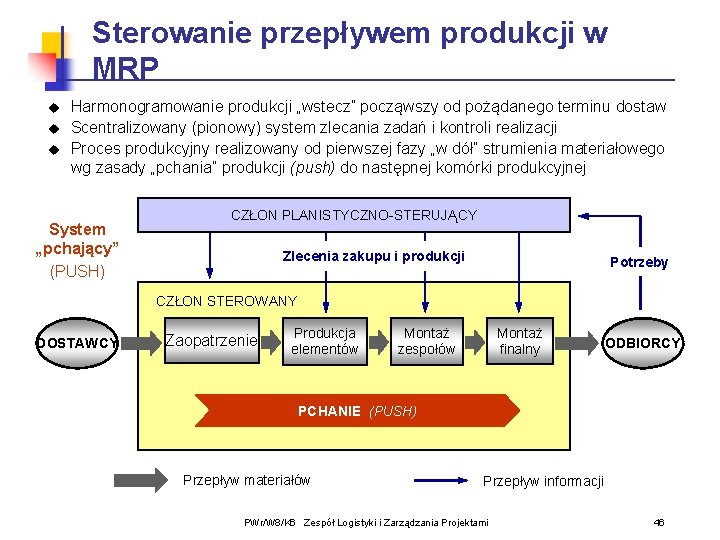
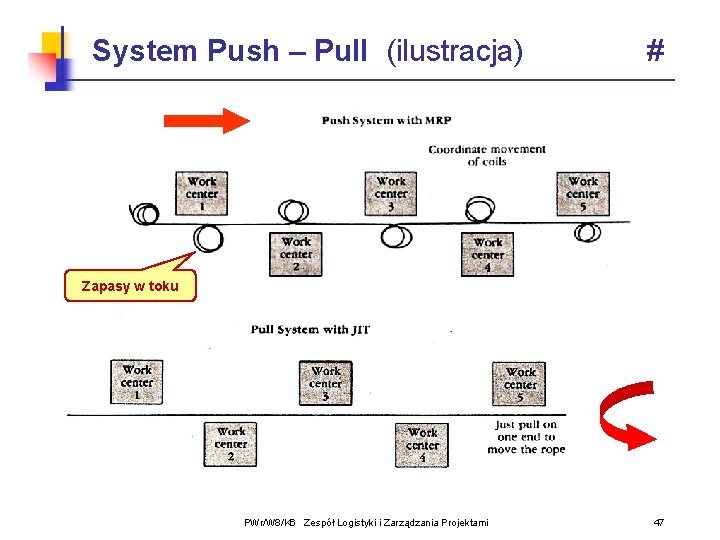
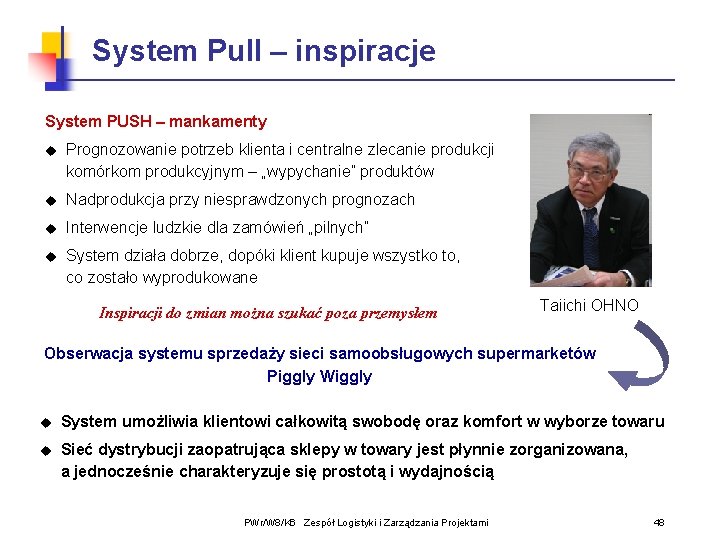
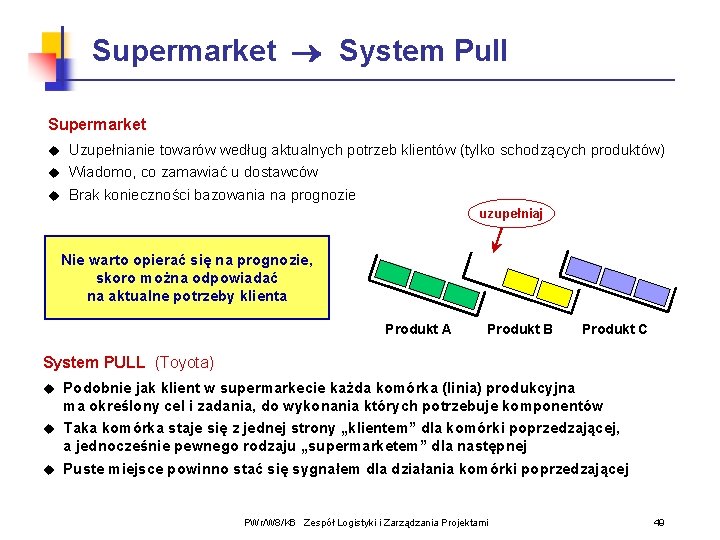
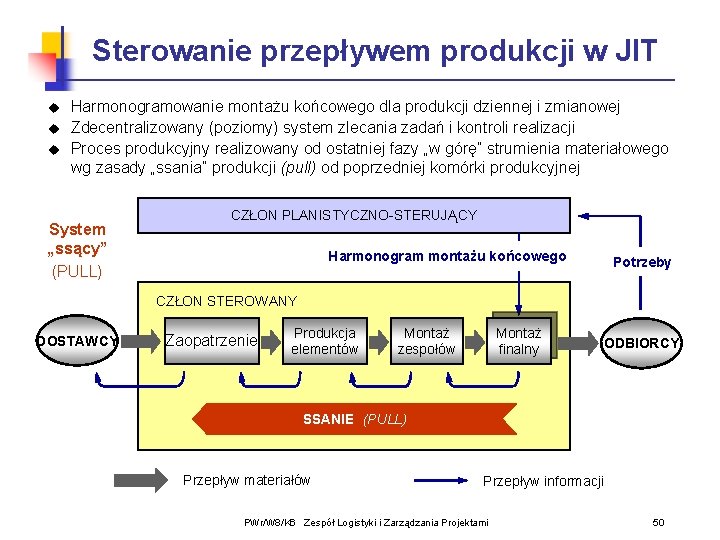
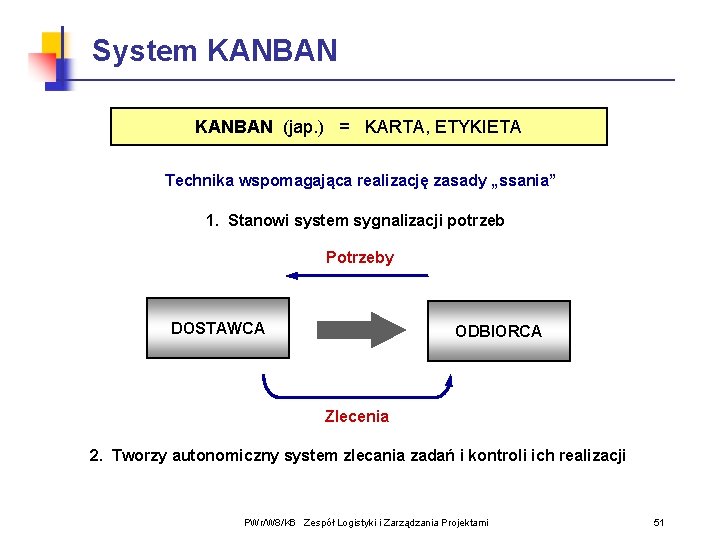
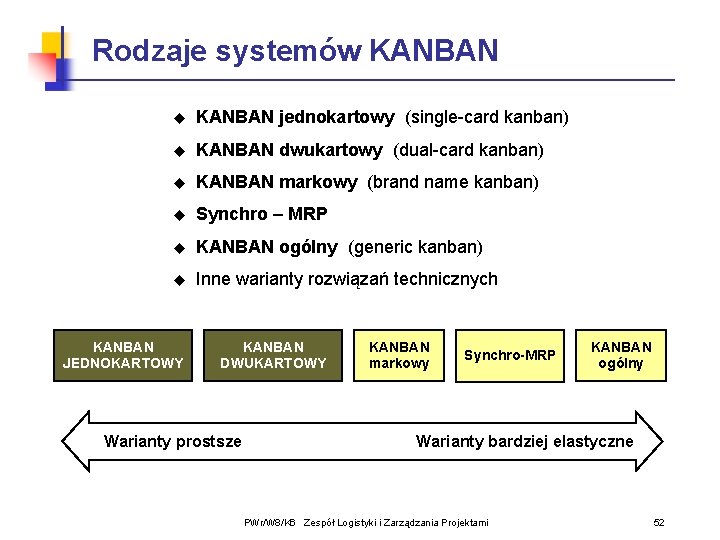
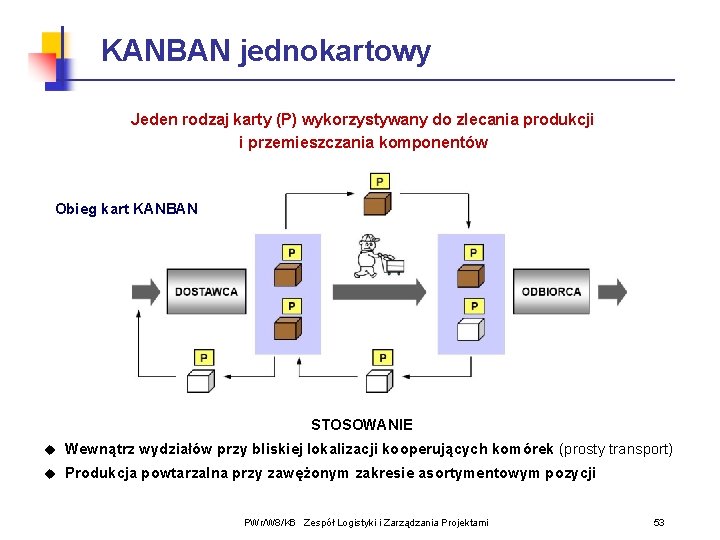
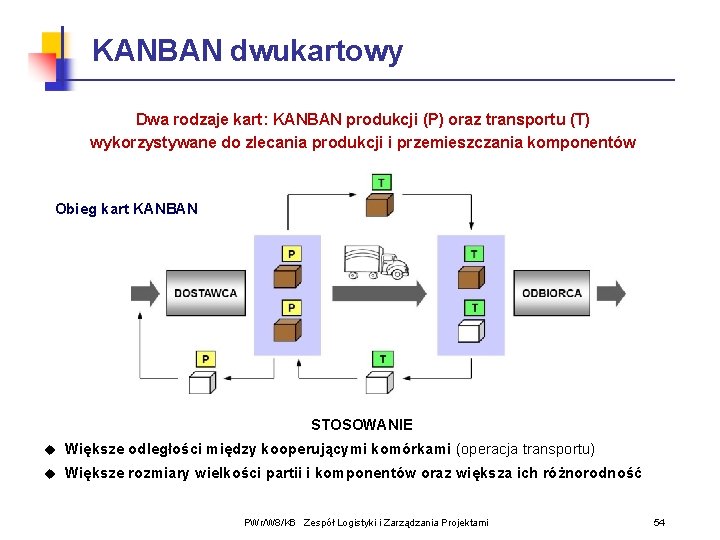
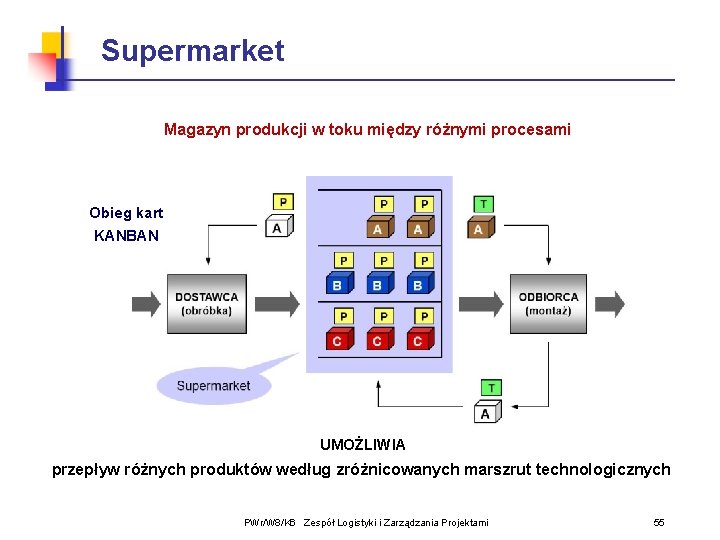
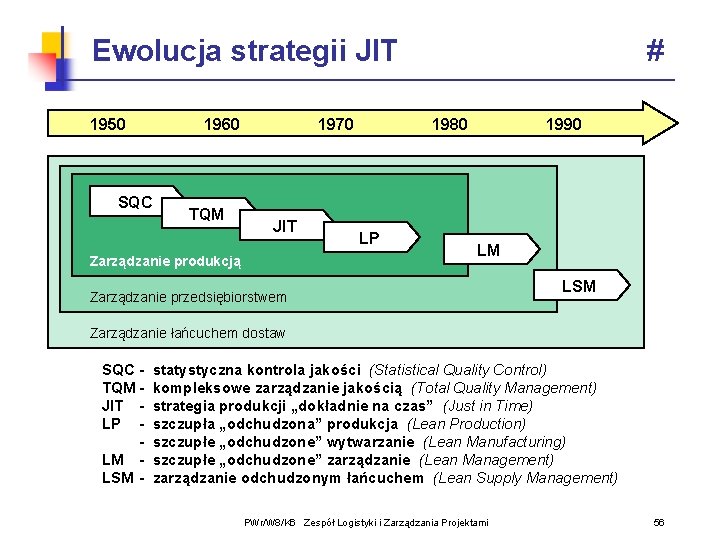
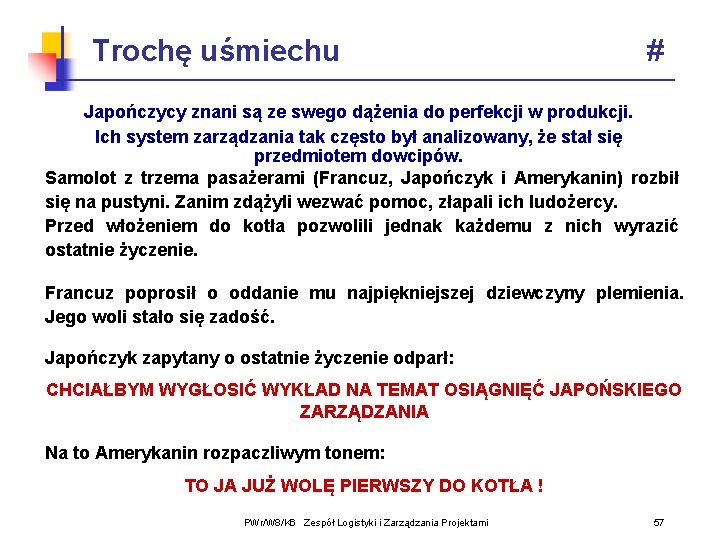
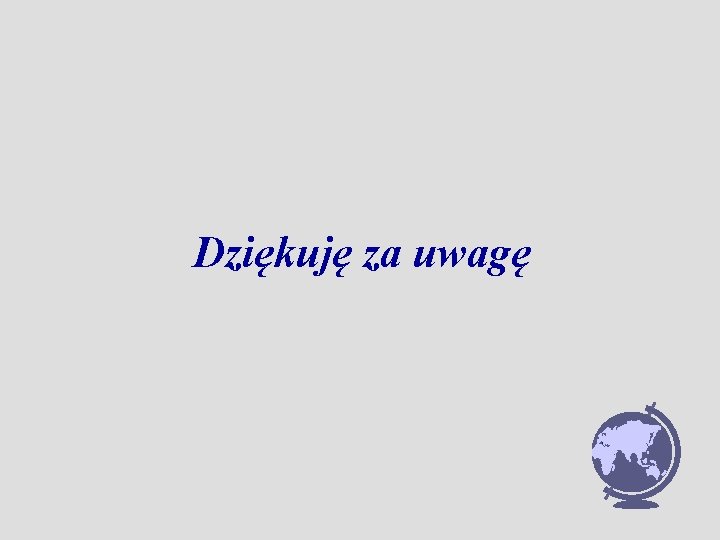
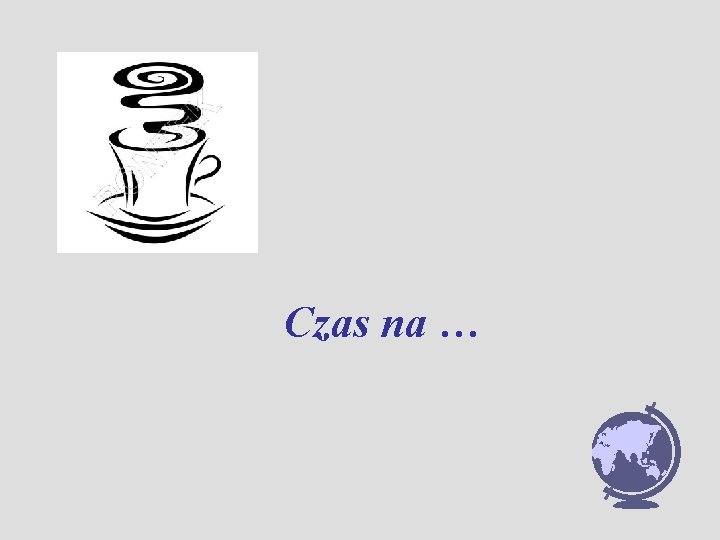
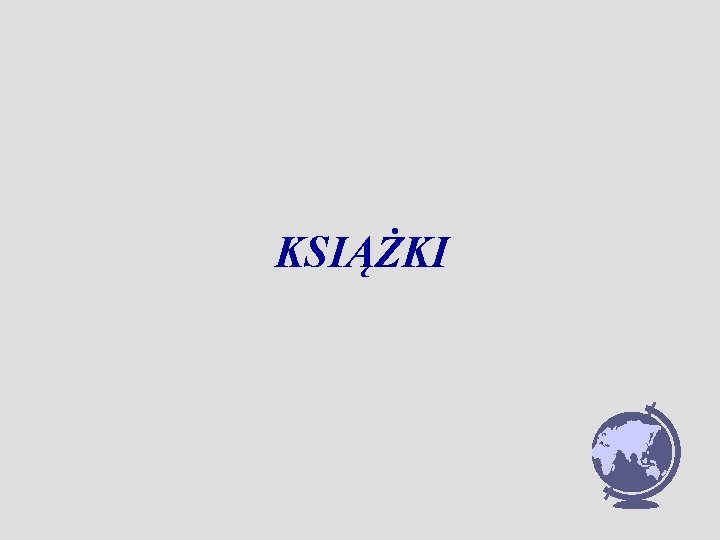
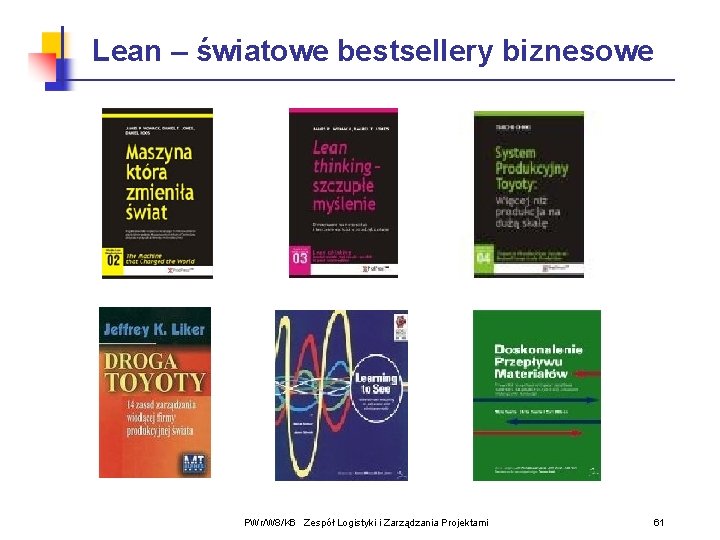
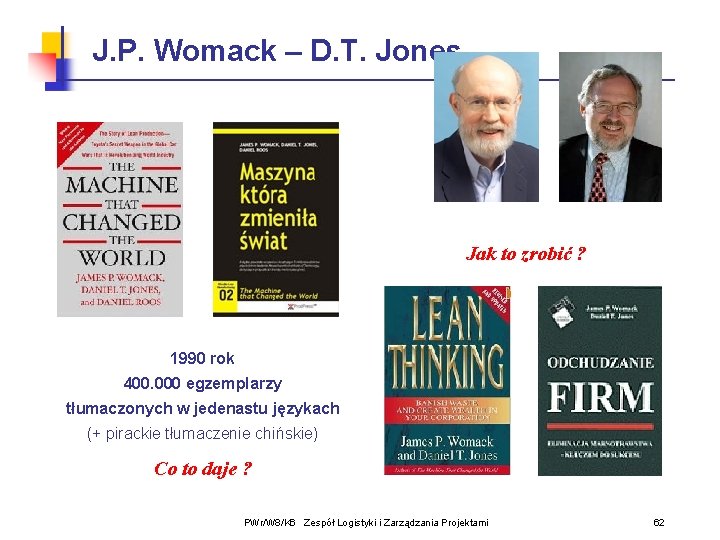
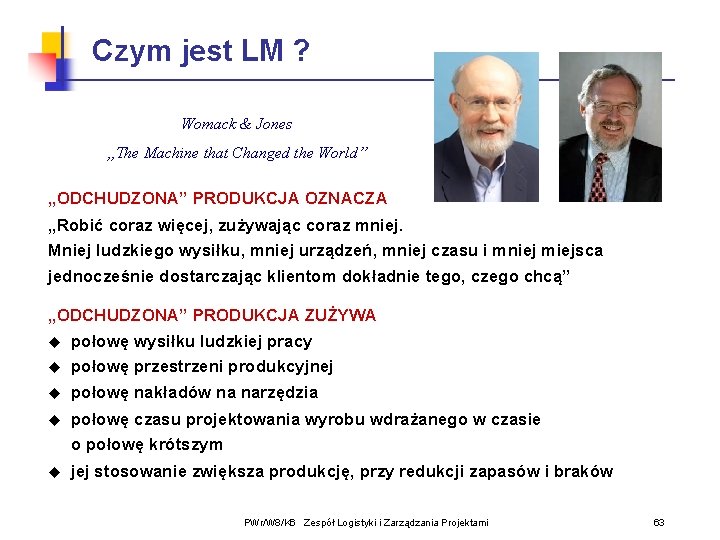

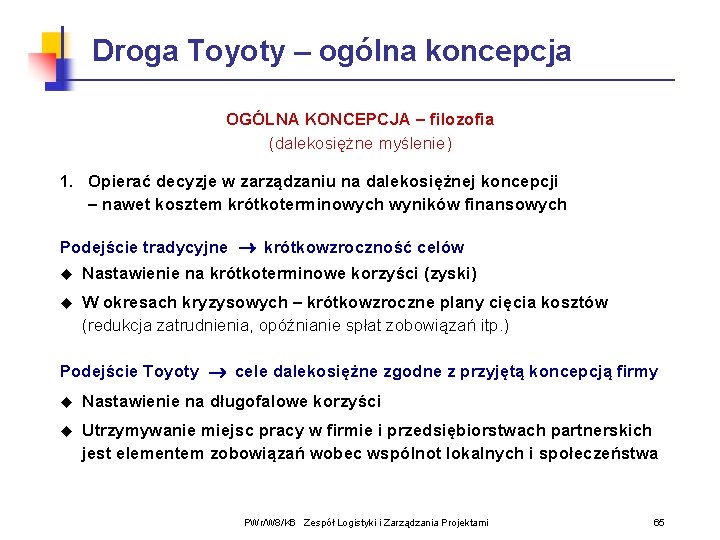
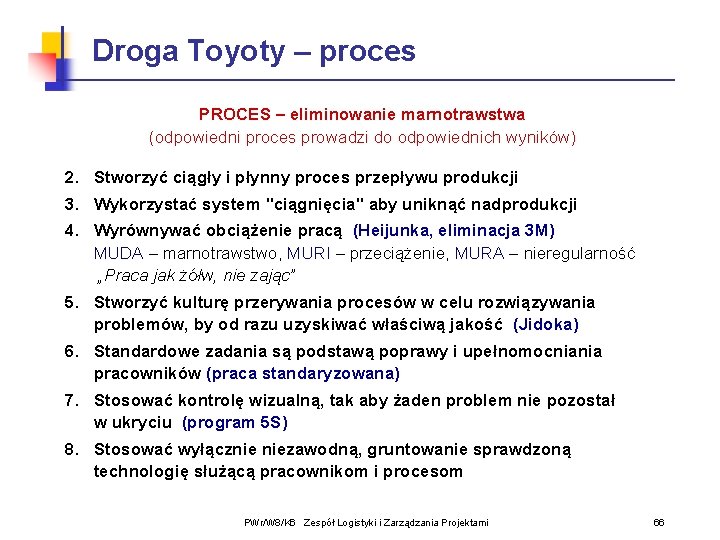
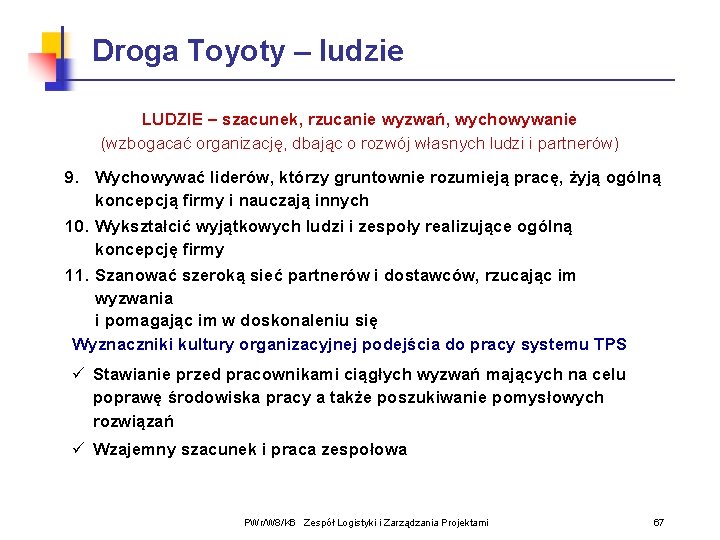
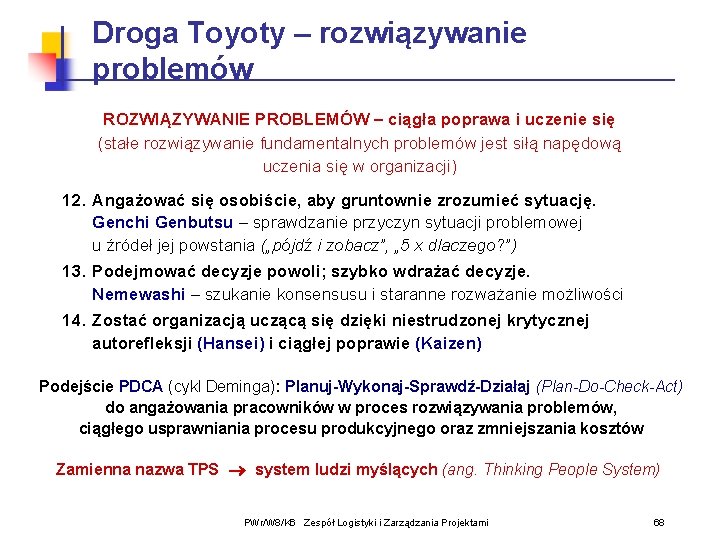
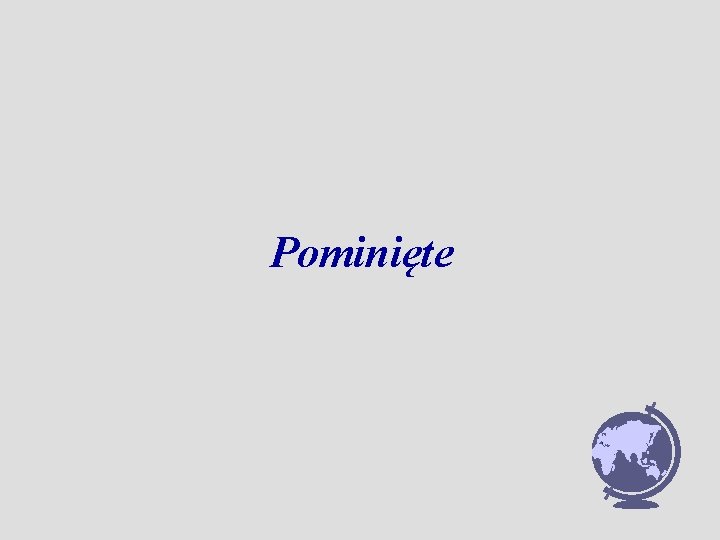
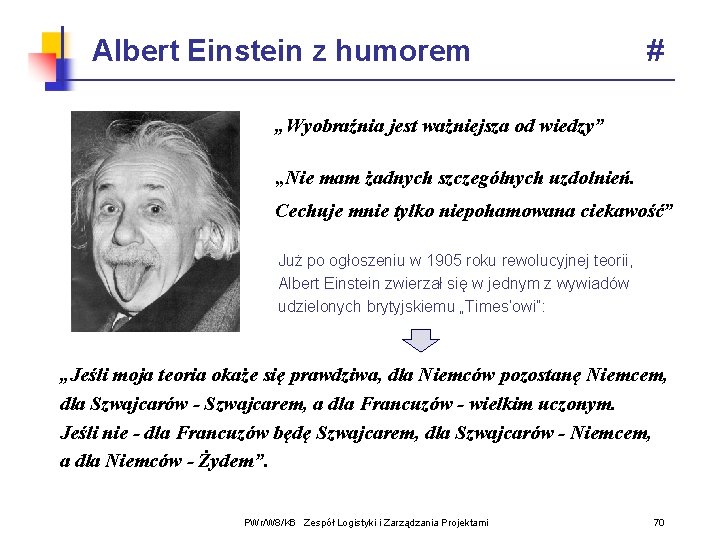
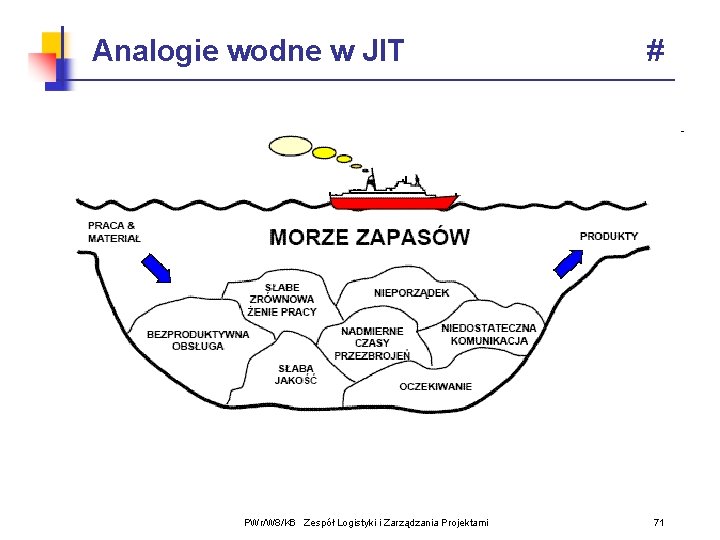
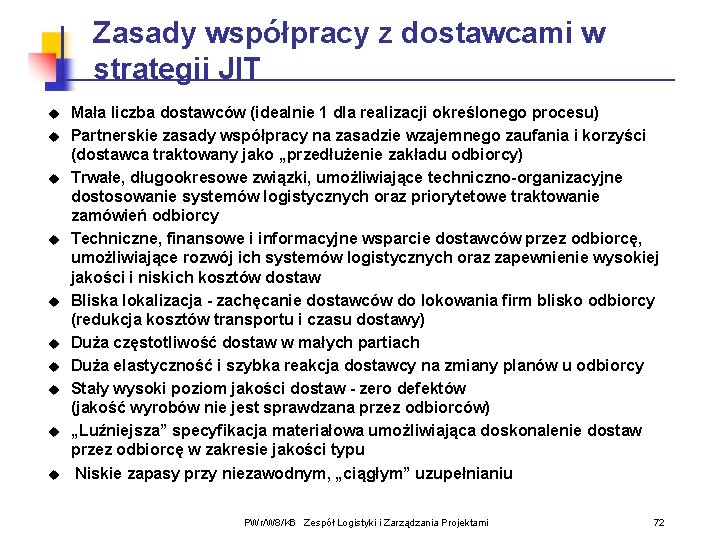
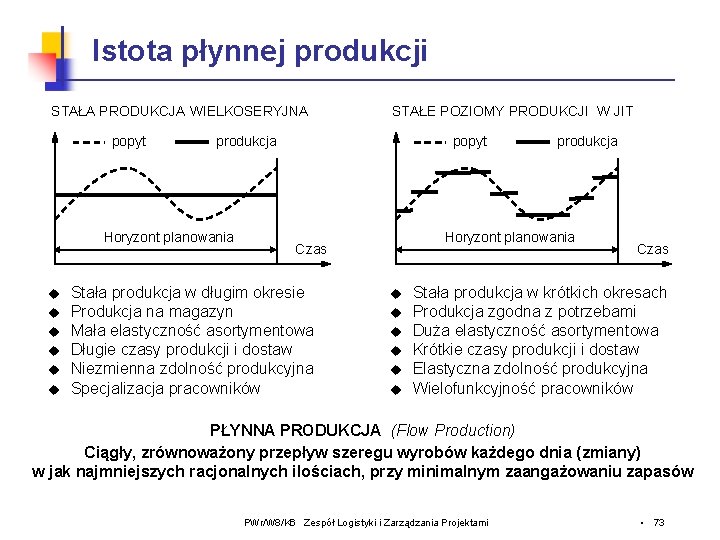
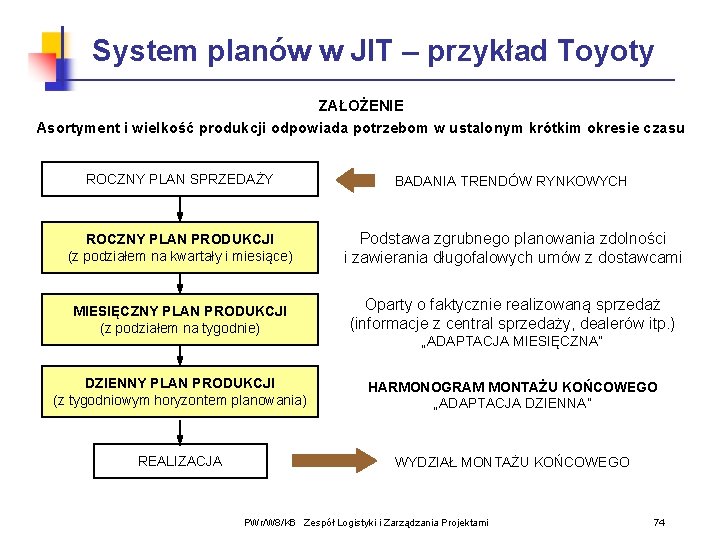
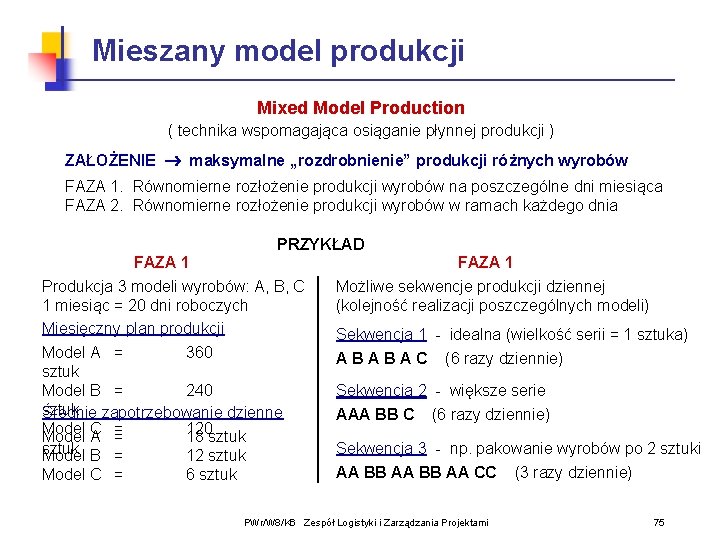
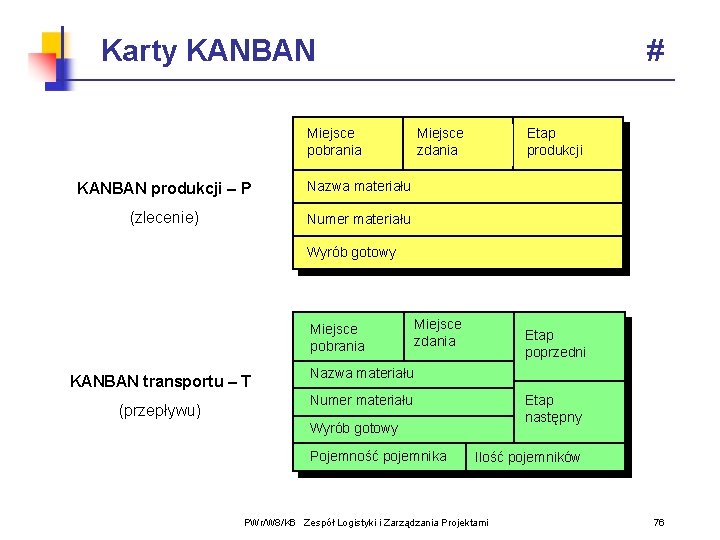
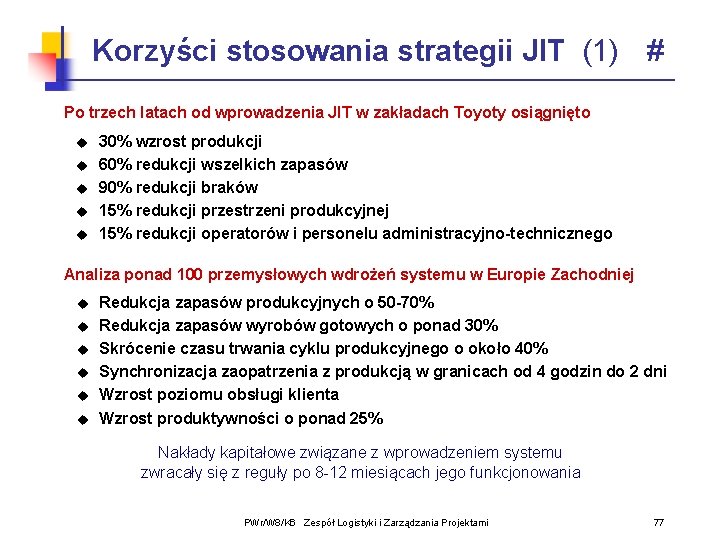
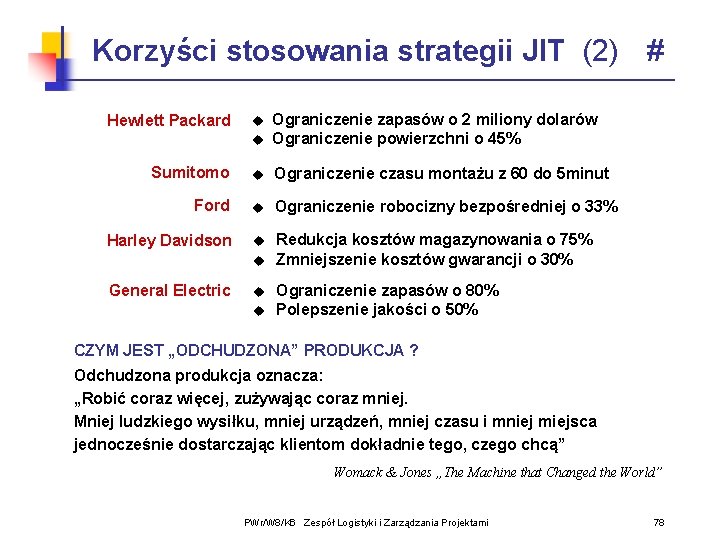
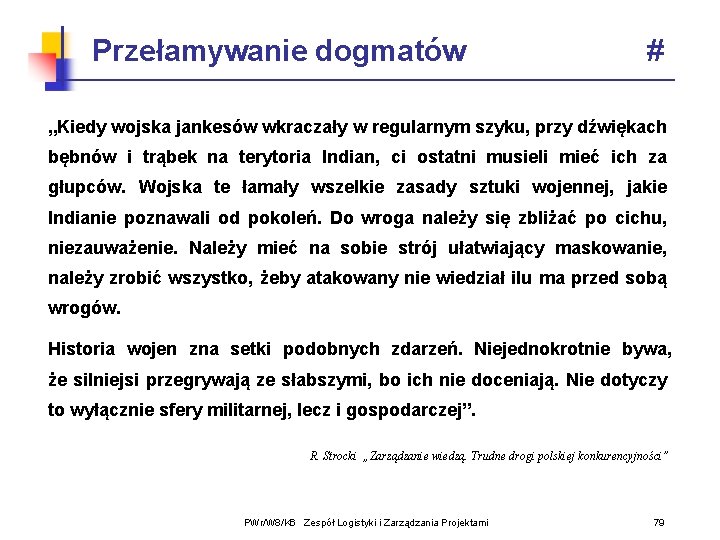
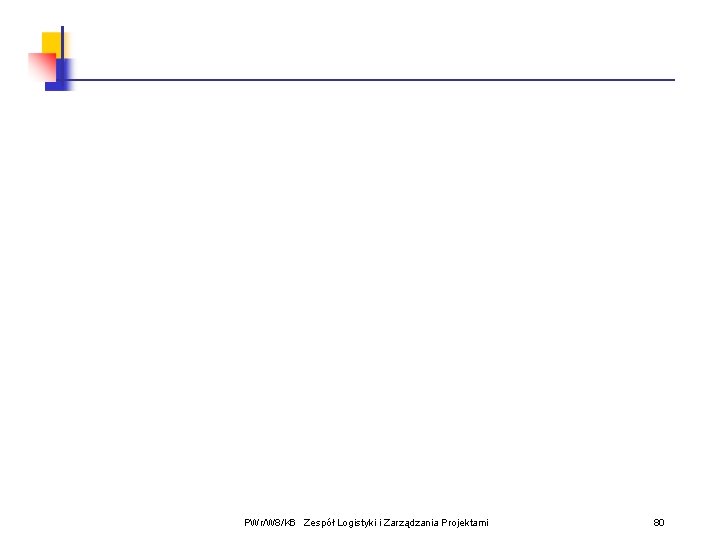
- Slides: 80
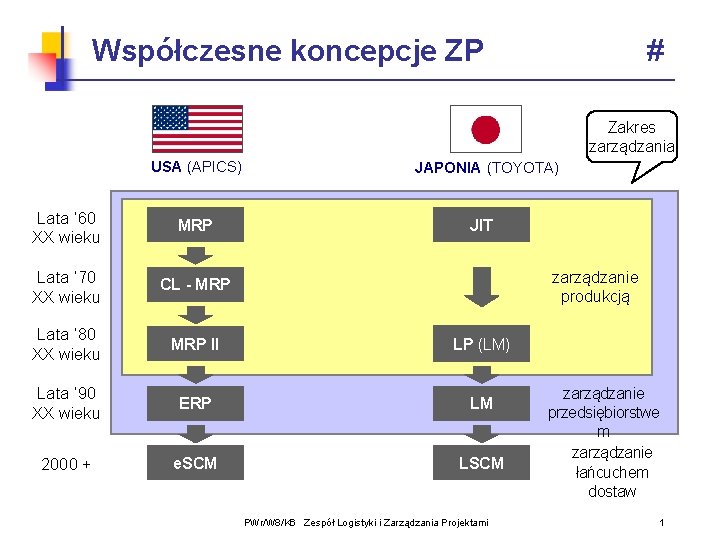
Współczesne koncepcje ZP # Zakres zarządzania USA (APICS) JAPONIA (TOYOTA) Lata ’ 60 XX wieku MRP Lata ’ 70 XX wieku CL - MRP Lata ’ 80 XX wieku MRP II LP (LM) Lata ’ 90 XX wieku ERP LM 2000 + e. SCM LSCM JIT zarządzanie produkcją PWr/W 8/K 6 Zespół Logistyki i Zarządzania Projektami zarządzanie przedsiębiorstwe m zarządzanie łańcuchem dostaw 1
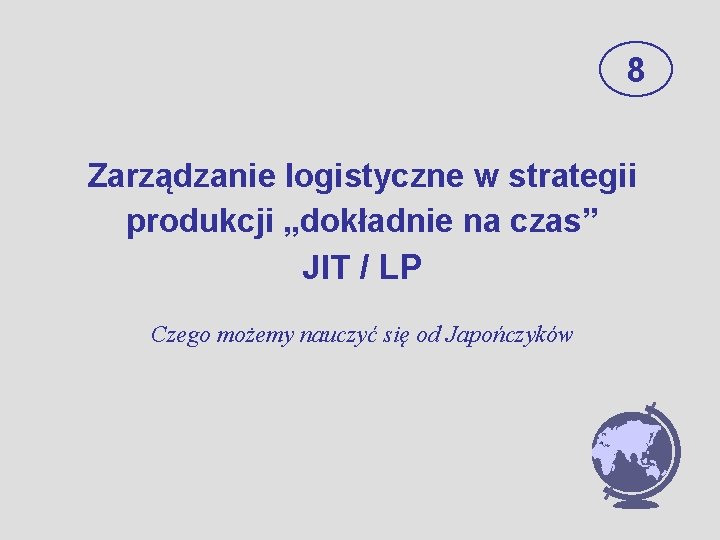
8 Zarządzanie logistyczne w strategii produkcji „dokładnie na czas” JIT / LP Czego możemy nauczyć się od Japończyków
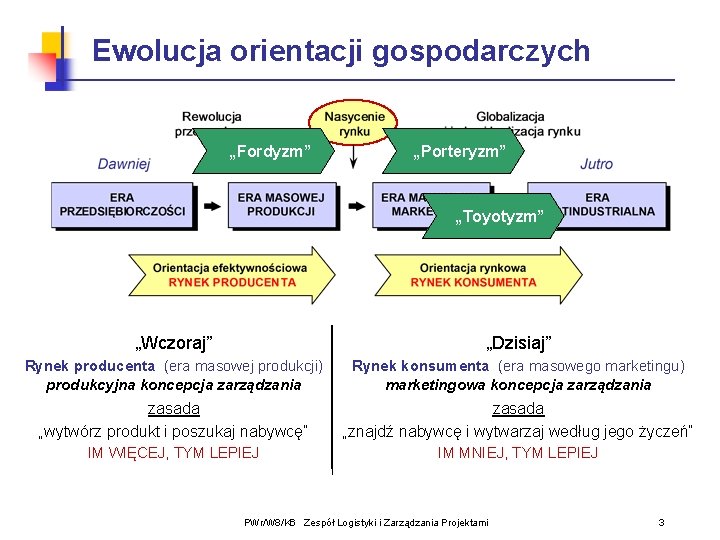
Ewolucja orientacji gospodarczych „Fordyzm” „Porteryzm” „Toyotyzm” „Wczoraj” „Dzisiaj” Rynek producenta (era masowej produkcji) produkcyjna koncepcja zarządzania Rynek konsumenta (era masowego marketingu) marketingowa koncepcja zarządzania zasada „wytwórz produkt i poszukaj nabywcę” zasada „znajdź nabywcę i wytwarzaj według jego życzeń” IM WIĘCEJ, TYM LEPIEJ IM MNIEJ, TYM LEPIEJ PWr/W 8/K 6 Zespół Logistyki i Zarządzania Projektami 3
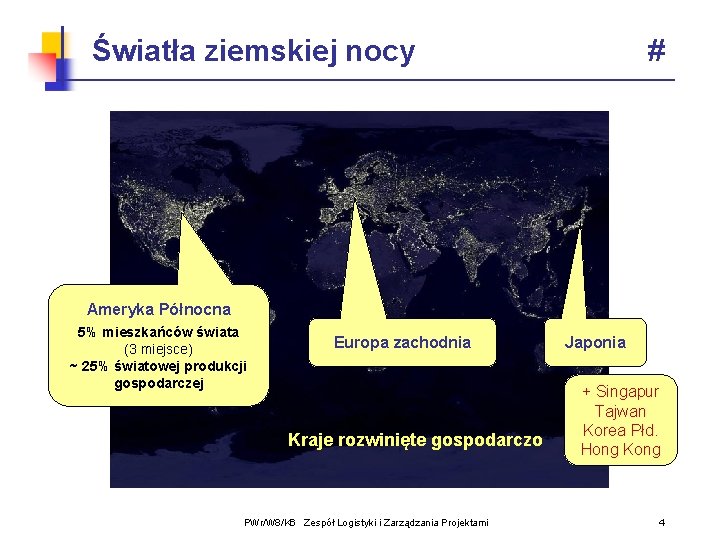
Światła ziemskiej nocy # Ameryka Północna 5% mieszkańców świata (3 miejsce) ~ 25% światowej produkcji gospodarczej Europa zachodnia Kraje rozwinięte gospodarczo PWr/W 8/K 6 Zespół Logistyki i Zarządzania Projektami Japonia + Singapur Tajwan Korea Płd. Hong Kong 4
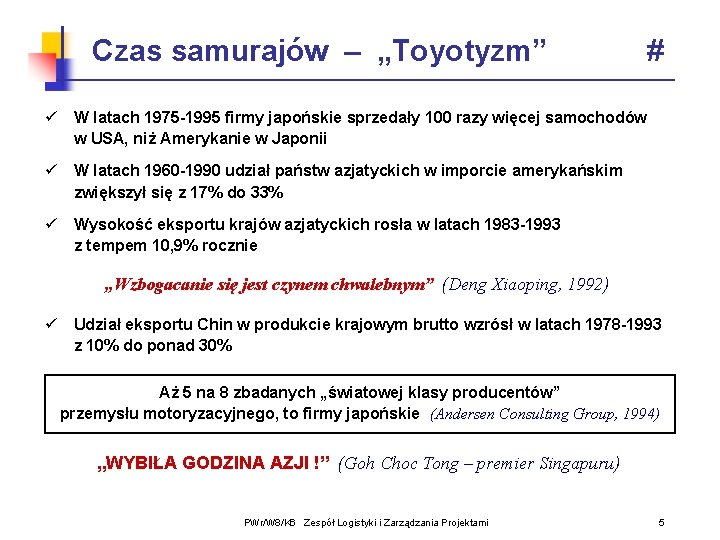
Czas samurajów – „Toyotyzm” # ü W latach 1975 -1995 firmy japońskie sprzedały 100 razy więcej samochodów w USA, niż Amerykanie w Japonii ü W latach 1960 -1990 udział państw azjatyckich w imporcie amerykańskim zwiększył się z 17% do 33% ü Wysokość eksportu krajów azjatyckich rosła w latach 1983 -1993 z tempem 10, 9% rocznie „Wzbogacanie się jest czynem chwalebnym” (Deng Xiaoping, 1992) ü Udział eksportu Chin w produkcie krajowym brutto wzrósł w latach 1978 -1993 z 10% do ponad 30% Aż 5 na 8 zbadanych „światowej klasy producentów” przemysłu motoryzacyjnego, to firmy japońskie (Andersen Consulting Group, 1994) „WYBIŁA GODZINA AZJI !” (Goh Choc Tong – premier Singapuru) PWr/W 8/K 6 Zespół Logistyki i Zarządzania Projektami 5
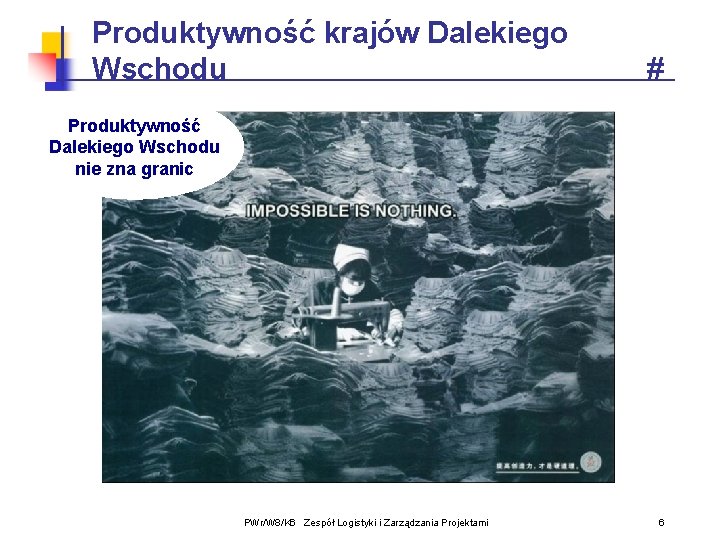
Produktywność krajów Dalekiego Wschodu # Produktywność Dalekiego Wschodu nie zna granic PWr/W 8/K 6 Zespół Logistyki i Zarządzania Projektami 6
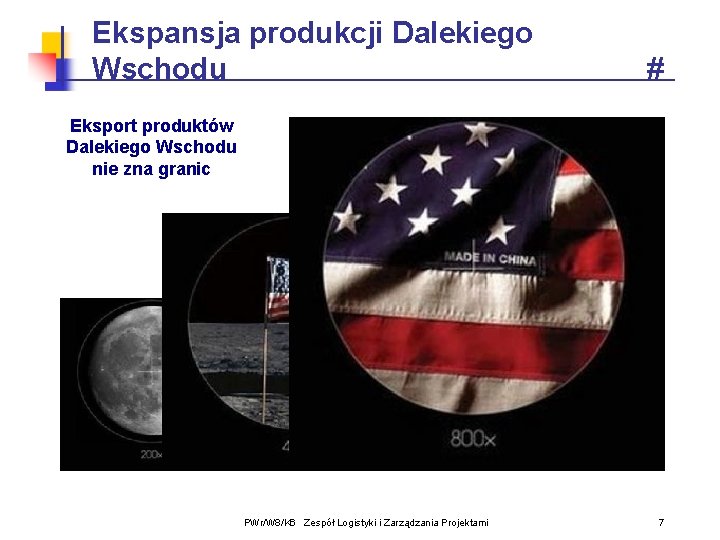
Ekspansja produkcji Dalekiego Wschodu # Eksport produktów Dalekiego Wschodu nie zna granic PWr/W 8/K 6 Zespół Logistyki i Zarządzania Projektami 7
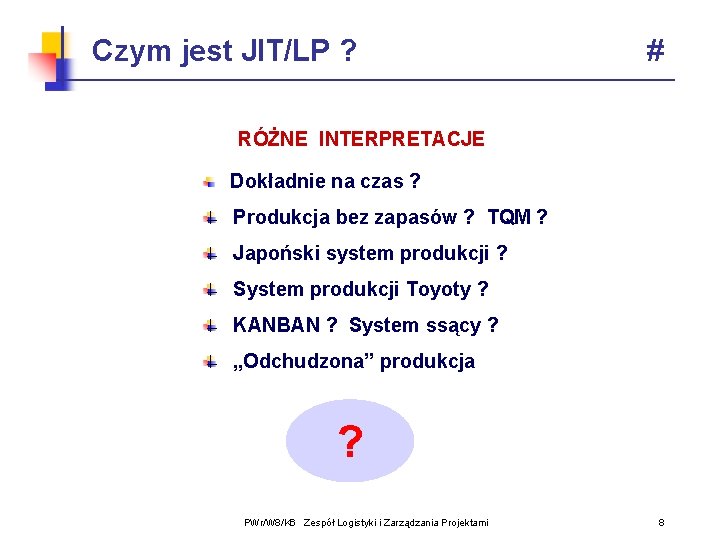
Czym jest JIT/LP ? # RÓŻNE INTERPRETACJE Dokładnie na czas ? Produkcja bez zapasów ? TQM ? Japoński system produkcji ? System produkcji Toyoty ? KANBAN ? System ssący ? „Odchudzona” produkcja ? PWr/W 8/K 6 Zespół Logistyki i Zarządzania Projektami 8
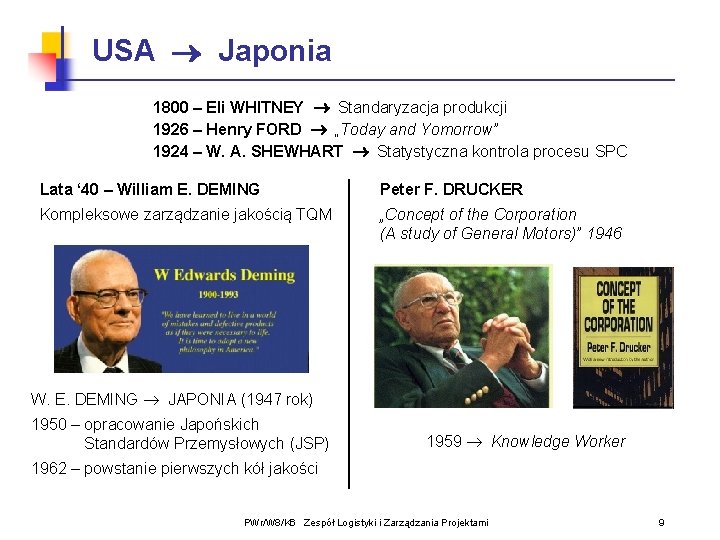
USA Japonia 1800 – Eli WHITNEY Standaryzacja produkcji 1926 – Henry FORD „Today and Yomorrow” 1924 – W. A. SHEWHART Statystyczna kontrola procesu SPC Lata ‘ 40 – William E. DEMING Peter F. DRUCKER Kompleksowe zarządzanie jakością TQM „Concept of the Corporation (A study of General Motors)” 1946 W. E. DEMING JAPONIA (1947 rok) 1950 – opracowanie Japońskich Standardów Przemysłowych (JSP) 1959 Knowledge Worker 1962 – powstanie pierwszych kół jakości PWr/W 8/K 6 Zespół Logistyki i Zarządzania Projektami 9
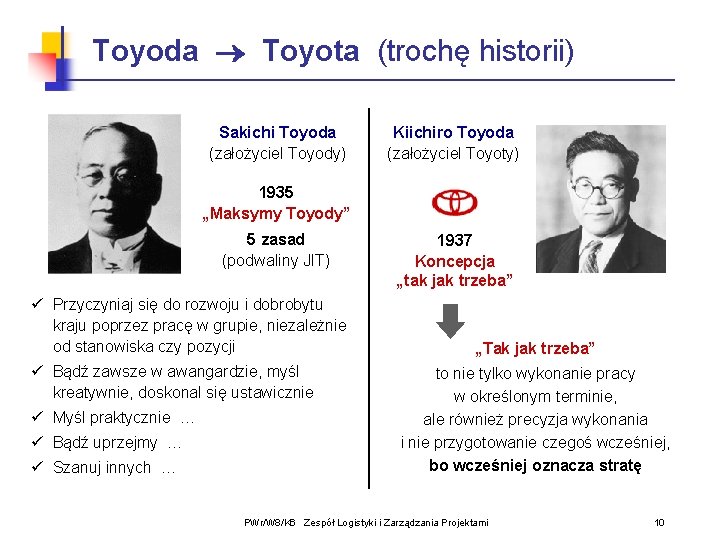
Toyoda Toyota (trochę historii) Sakichi Toyoda (założyciel Toyody) Kiichiro Toyoda (założyciel Toyoty) 1935 „Maksymy Toyody” 5 zasad (podwaliny JIT) ü Przyczyniaj się do rozwoju i dobrobytu kraju poprzez pracę w grupie, niezależnie od stanowiska czy pozycji ü Bądź zawsze w awangardzie, myśl kreatywnie, doskonal się ustawicznie ü Myśl praktycznie … ü Bądź uprzejmy … ü Szanuj innych … 1937 Koncepcja „tak jak trzeba” „Tak jak trzeba” to nie tylko wykonanie pracy w określonym terminie, ale również precyzja wykonania i nie przygotowanie czegoś wcześniej, bo wcześniej oznacza stratę PWr/W 8/K 6 Zespół Logistyki i Zarządzania Projektami 10
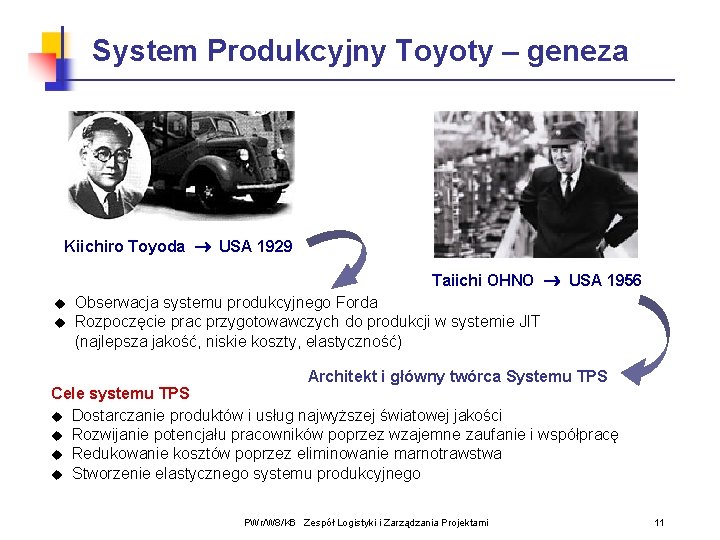
System Produkcyjny Toyoty – geneza Kiichiro Toyoda USA 1929 Taiichi OHNO USA 1956 u u Obserwacja systemu produkcyjnego Forda Rozpoczęcie prac przygotowawczych do produkcji w systemie JIT (najlepsza jakość, niskie koszty, elastyczność) Architekt i główny twórca Systemu TPS Cele systemu TPS u Dostarczanie produktów i usług najwyższej światowej jakości u Rozwijanie potencjału pracowników poprzez wzajemne zaufanie i współpracę u Redukowanie kosztów poprzez eliminowanie marnotrawstwa u Stworzenie elastycznego systemu produkcyjnego PWr/W 8/K 6 Zespół Logistyki i Zarządzania Projektami 11
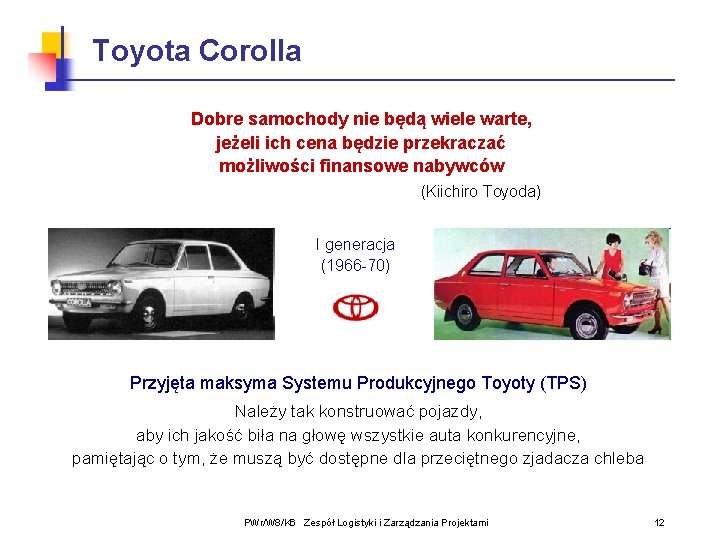
Toyota Corolla Dobre samochody nie będą wiele warte, jeżeli ich cena będzie przekraczać możliwości finansowe nabywców (Kiichiro Toyoda) I generacja (1966 -70) Przyjęta maksyma Systemu Produkcyjnego Toyoty (TPS) Należy tak konstruować pojazdy, aby ich jakość biła na głowę wszystkie auta konkurencyjne, pamiętając o tym, że muszą być dostępne dla przeciętnego zjadacza chleba PWr/W 8/K 6 Zespół Logistyki i Zarządzania Projektami 12
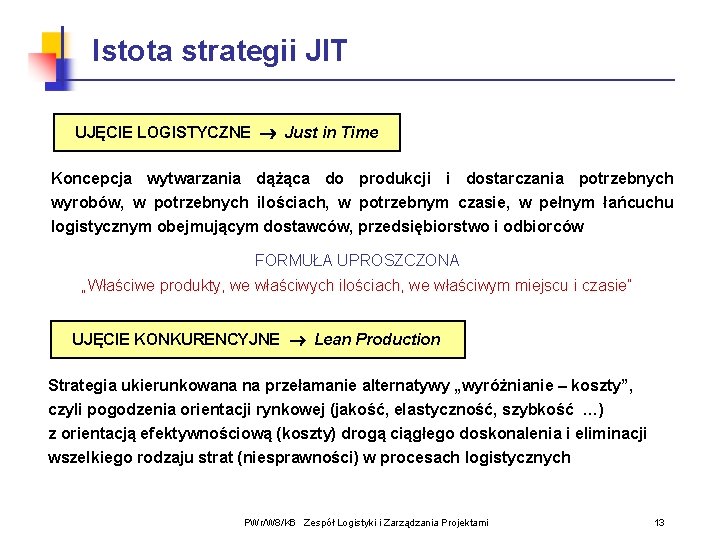
Istota strategii JIT UJĘCIE LOGISTYCZNE Just in Time Koncepcja wytwarzania dążąca do produkcji i dostarczania potrzebnych wyrobów, w potrzebnych ilościach, w potrzebnym czasie, w pełnym łańcuchu logistycznym obejmującym dostawców, przedsiębiorstwo i odbiorców FORMUŁA UPROSZCZONA „Właściwe produkty, we właściwych ilościach, we właściwym miejscu i czasie” UJĘCIE KONKURENCYJNE Lean Production Strategia ukierunkowana na przełamanie alternatywy „wyróżnianie – koszty”, czyli pogodzenia orientacji rynkowej (jakość, elastyczność, szybkość …) z orientacją efektywnościową (koszty) drogą ciągłego doskonalenia i eliminacji wszelkiego rodzaju strat (niesprawności) w procesach logistycznych PWr/W 8/K 6 Zespół Logistyki i Zarządzania Projektami 13
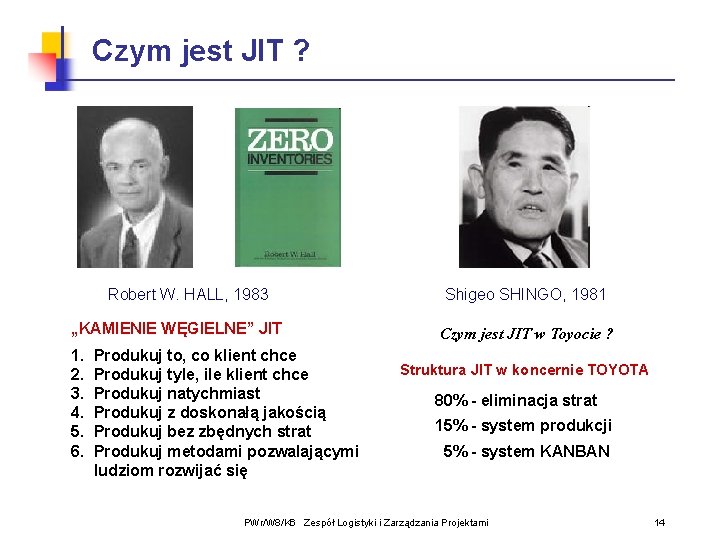
Czym jest JIT ? Robert W. HALL, 1983 „KAMIENIE WĘGIELNE” JIT 1. 2. 3. 4. 5. 6. Produkuj to, co klient chce Produkuj tyle, ile klient chce Produkuj natychmiast Produkuj z doskonałą jakością Produkuj bez zbędnych strat Produkuj metodami pozwalającymi ludziom rozwijać się Shigeo SHINGO, 1981 Czym jest JIT w Toyocie ? Struktura JIT w koncernie TOYOTA 80% - eliminacja strat 15% - system produkcji 5% - system KANBAN PWr/W 8/K 6 Zespół Logistyki i Zarządzania Projektami 14
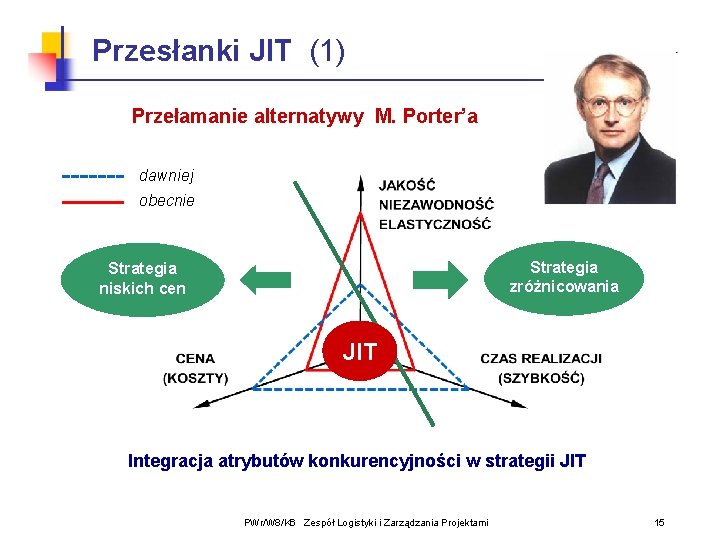
Przesłanki JIT (1) Przełamanie alternatywy M. Porter’a dawniej obecnie Strategia zróżnicowania Strategia niskich cen JIT Integracja atrybutów konkurencyjności w strategii JIT PWr/W 8/K 6 Zespół Logistyki i Zarządzania Projektami 15
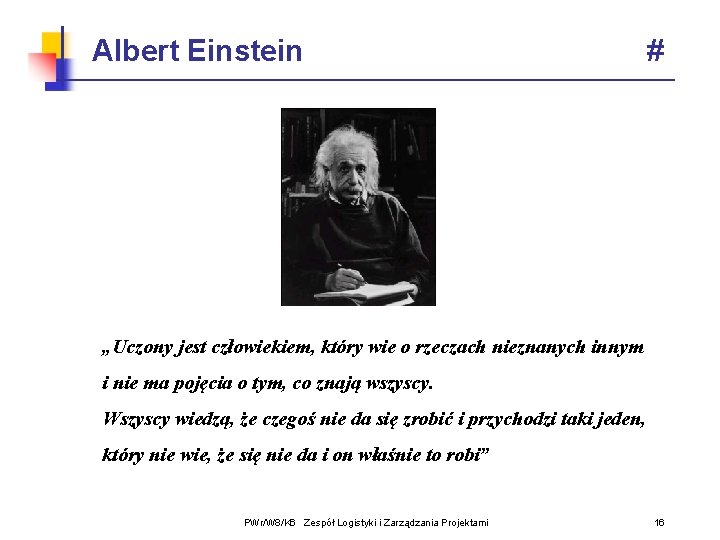
Albert Einstein # „Uczony jest człowiekiem, który wie o rzeczach nieznanych innym i nie ma pojęcia o tym, co znają wszyscy. Wszyscy wiedzą, że czegoś nie da się zrobić i przychodzi taki jeden, który nie wie, że się nie da i on właśnie to robi” PWr/W 8/K 6 Zespół Logistyki i Zarządzania Projektami 16

Przesłanki JIT (2) Produkcja na zamówienie PNZ Produkcja na magazyn PNM DUŻA ELASTYCZNOŚĆ MAŁE ZAPASY WYSOKA RENTOWNOŚĆ (ekonomia skali) KRÓTKI CZAS REALIZACJI DŁUGI CZAS REALIZACJI NISKA RENTOWNOŚĆ (ekonomia zakresu) MAŁA ELASTYCZNOŚĆ DUŻE ZAPASY PRZESŁANKA WYJŚCIOWA JIT Zwiększenie elastyczności dostaw (rezygnacja z produkcji na magazyn) REDUKCJA ZAPASÓW “Cały zapas produkcyjny powinien znajdować się tylko w toku produkcji” PWr/W 8/K 6 Zespół Logistyki i Zarządzania Projektami 17
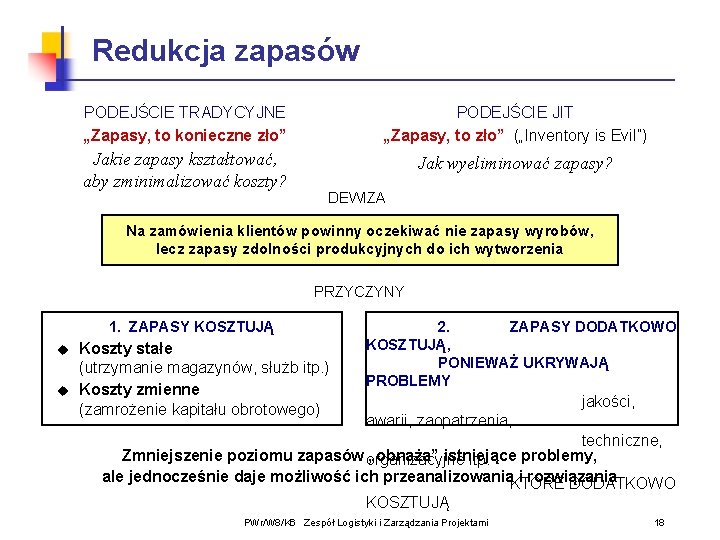
Redukcja zapasów PODEJŚCIE TRADYCYJNE „Zapasy, to konieczne zło” PODEJŚCIE JIT „Zapasy, to zło” („Inventory is Evil”) Jakie zapasy kształtować, aby zminimalizować koszty? Jak wyeliminować zapasy? DEWIZA Na zamówienia klientów powinny oczekiwać nie zapasy wyrobów, lecz zapasy zdolności produkcyjnych do ich wytworzenia PRZYCZYNY 1. ZAPASY KOSZTUJĄ u u Koszty stałe (utrzymanie magazynów, służb itp. ) Koszty zmienne (zamrożenie kapitału obrotowego) 2. ZAPASY DODATKOWO KOSZTUJĄ, PONIEWAŻ UKRYWAJĄ PROBLEMY jakości, awarii, zaopatrzenia, techniczne, Zmniejszenie poziomu zapasów organizacyjne „obnaża” istniejące problemy, itp. ale jednocześnie daje możliwość ich przeanalizowania. KTÓRE i rozwiązania DODATKOWO KOSZTUJĄ PWr/W 8/K 6 Zespół Logistyki i Zarządzania Projektami 18
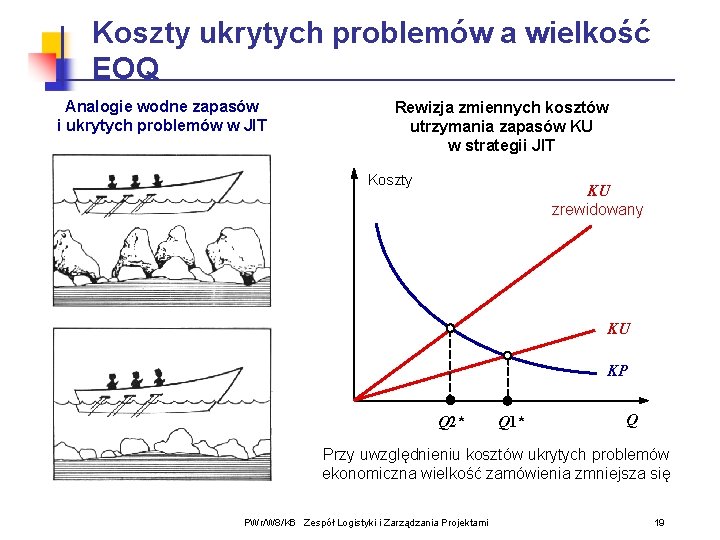
Koszty ukrytych problemów a wielkość EOQ Analogie wodne zapasów i ukrytych problemów w JIT Rewizja zmiennych kosztów utrzymania zapasów KU w strategii JIT Koszty KU zrewidowany KU KP Q 2* Q 1* Q Przy uwzględnieniu kosztów ukrytych problemów ekonomiczna wielkość zamówienia zmniejsza się PWr/W 8/K 6 Zespół Logistyki i Zarządzania Projektami 19
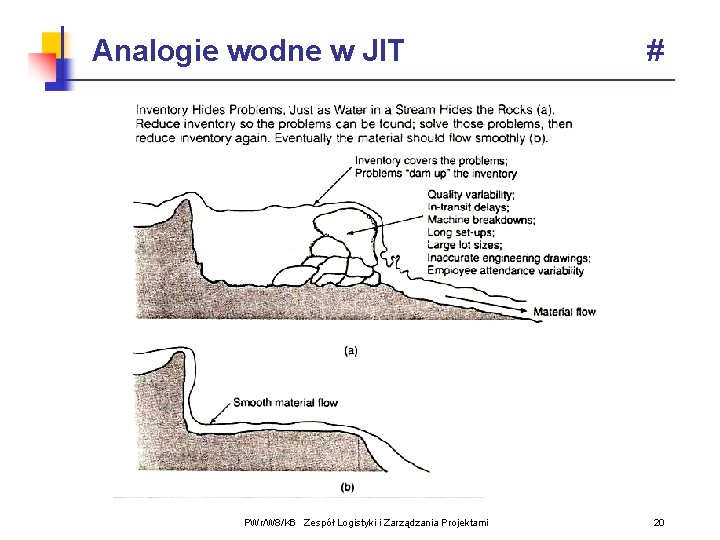
Analogie wodne w JIT PWr/W 8/K 6 Zespół Logistyki i Zarządzania Projektami # 20
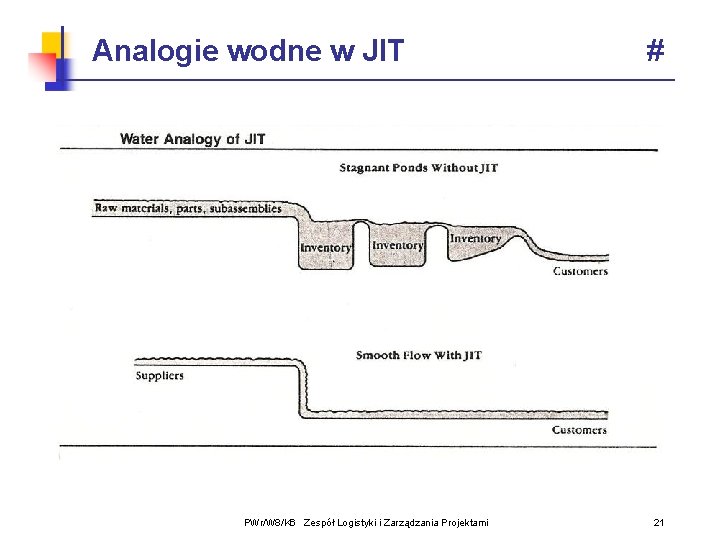
Analogie wodne w JIT PWr/W 8/K 6 Zespół Logistyki i Zarządzania Projektami # 21
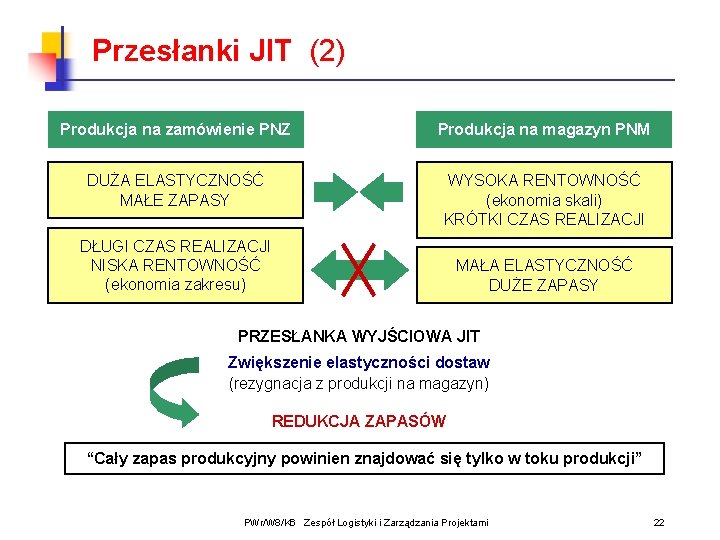
Przesłanki JIT (2) Produkcja na zamówienie PNZ Produkcja na magazyn PNM DUŻA ELASTYCZNOŚĆ MAŁE ZAPASY WYSOKA RENTOWNOŚĆ (ekonomia skali) KRÓTKI CZAS REALIZACJI DŁUGI CZAS REALIZACJI NISKA RENTOWNOŚĆ (ekonomia zakresu) MAŁA ELASTYCZNOŚĆ DUŻE ZAPASY PRZESŁANKA WYJŚCIOWA JIT Zwiększenie elastyczności dostaw (rezygnacja z produkcji na magazyn) REDUKCJA ZAPASÓW “Cały zapas produkcyjny powinien znajdować się tylko w toku produkcji” PWr/W 8/K 6 Zespół Logistyki i Zarządzania Projektami 22
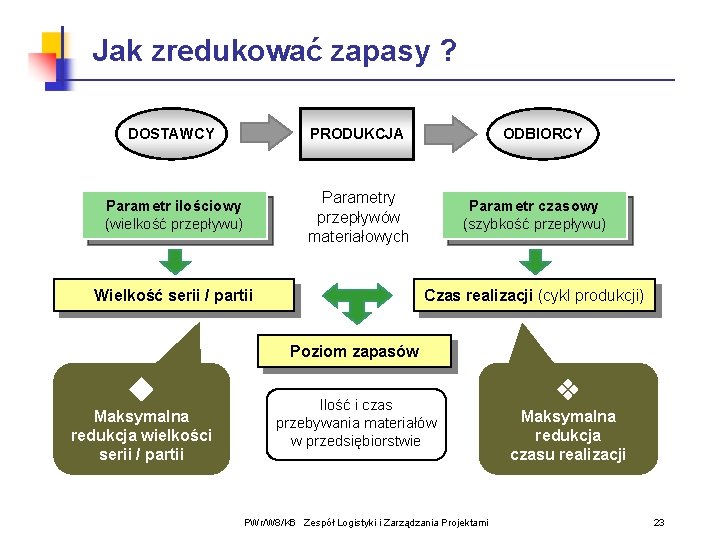
Jak zredukować zapasy ? DOSTAWCY PRODUKCJA Parametr ilościowy (wielkość przepływu) Parametry przepływów materiałowych Wielkość serii / partii ODBIORCY Parametr czasowy (szybkość przepływu) Czas realizacji (cykl produkcji) Poziom zapasów Maksymalna redukcja wielkości serii / partii Ilość i czas przebywania materiałów w przedsiębiorstwie PWr/W 8/K 6 Zespół Logistyki i Zarządzania Projektami Maksymalna redukcja czasu realizacji 23
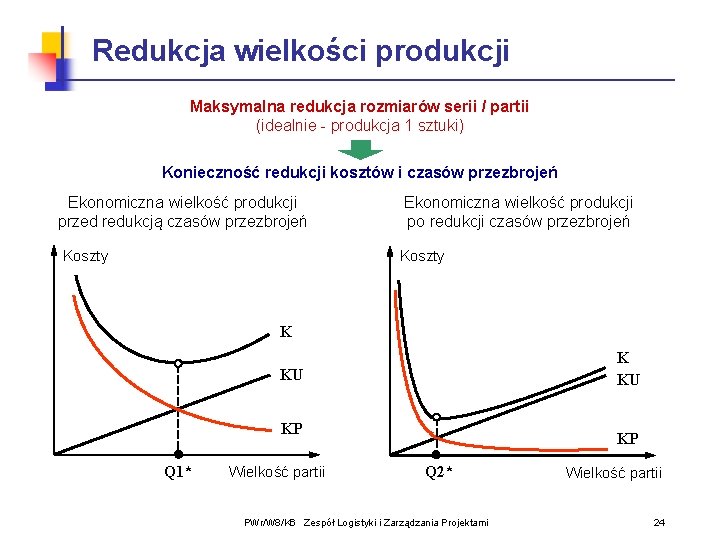
Redukcja wielkości produkcji Maksymalna redukcja rozmiarów serii / partii (idealnie - produkcja 1 sztuki) Konieczność redukcji kosztów i czasów przezbrojeń Ekonomiczna wielkość produkcji przed redukcją czasów przezbrojeń Ekonomiczna wielkość produkcji po redukcji czasów przezbrojeń Koszty K K KU KU KP Q 1* Wielkość partii KP Q 2* PWr/W 8/K 6 Zespół Logistyki i Zarządzania Projektami Wielkość partii 24
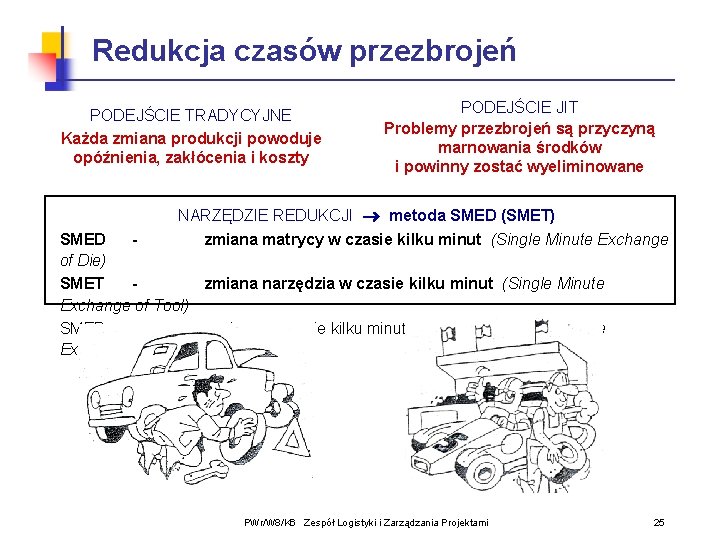
Redukcja czasów przezbrojeń PODEJŚCIE TRADYCYJNE Każda zmiana produkcji powoduje opóźnienia, zakłócenia i koszty PODEJŚCIE JIT Problemy przezbrojeń są przyczyną marnowania środków i powinny zostać wyeliminowane NARZĘDZIE REDUKCJI metoda SMED (SMET) SMED zmiana matrycy w czasie kilku minut (Single Minute Exchange of Die) SMET zmiana narzędzia w czasie kilku minut (Single Minute Exchange of Tool) SMED „zmiana w czasie kilku minut lub upadek” (Single Minute Exchange or Die) PWr/W 8/K 6 Zespół Logistyki i Zarządzania Projektami 25
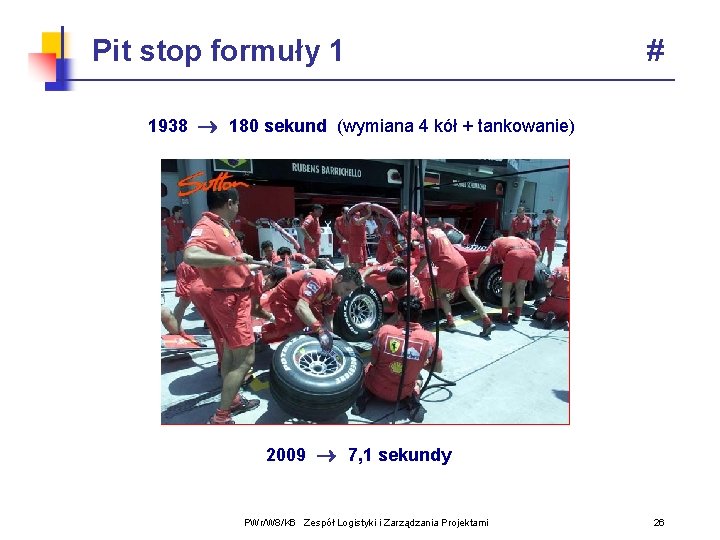
Pit stop formuły 1 # 1938 180 sekund (wymiana 4 kół + tankowanie) 2009 7, 1 sekundy PWr/W 8/K 6 Zespół Logistyki i Zarządzania Projektami 26
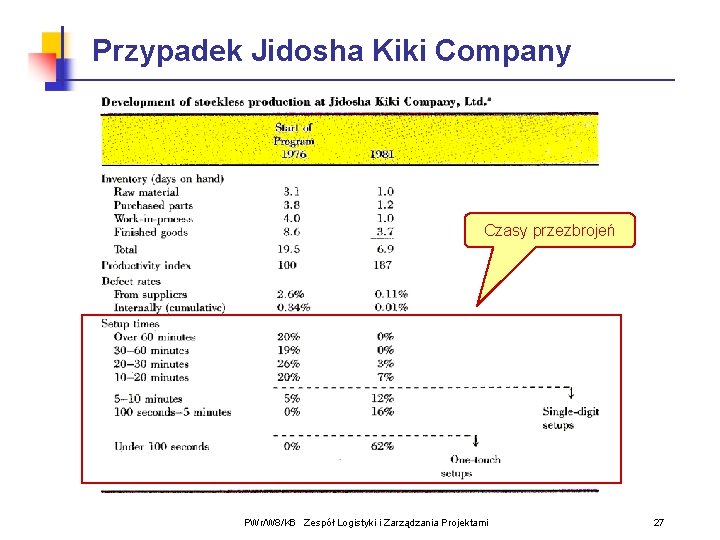
Przypadek Jidosha Kiki Company Czasy przezbrojeń PWr/W 8/K 6 Zespół Logistyki i Zarządzania Projektami 27
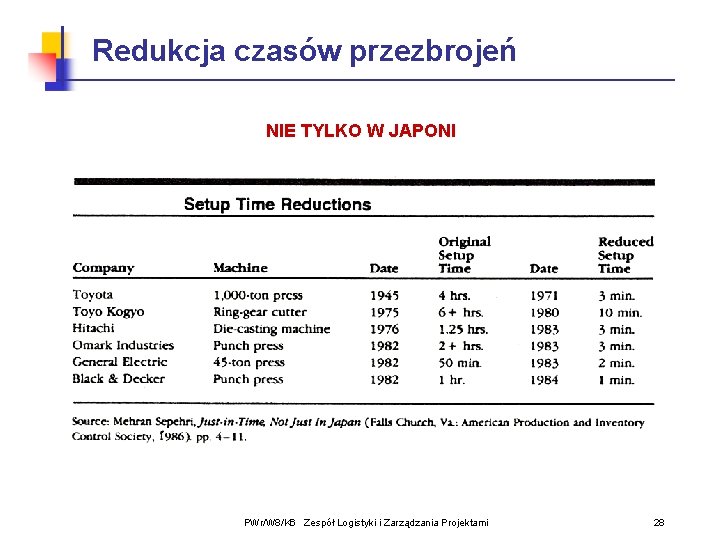
Redukcja czasów przezbrojeń NIE TYLKO W JAPONI PWr/W 8/K 6 Zespół Logistyki i Zarządzania Projektami 28
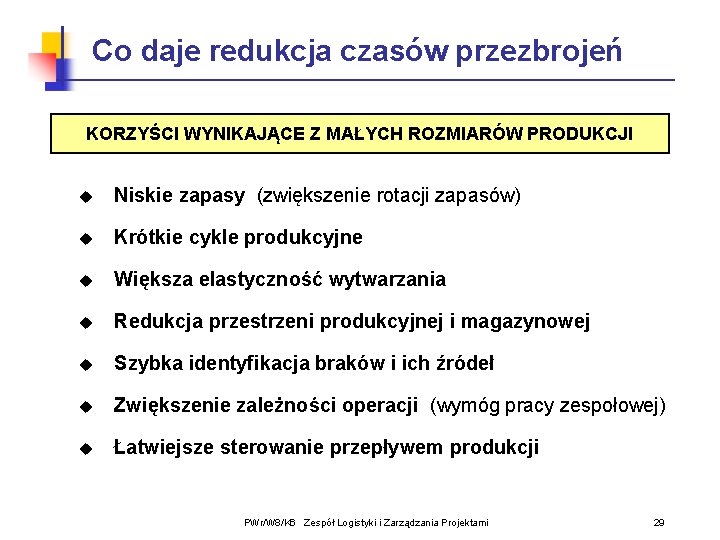
Co daje redukcja czasów przezbrojeń KORZYŚCI WYNIKAJĄCE Z MAŁYCH ROZMIARÓW PRODUKCJI u Niskie zapasy (zwiększenie rotacji zapasów) u Krótkie cykle produkcyjne u Większa elastyczność wytwarzania u Redukcja przestrzeni produkcyjnej i magazynowej u Szybka identyfikacja braków i ich źródeł u Zwiększenie zależności operacji (wymóg pracy zespołowej) u Łatwiejsze sterowanie przepływem produkcji PWr/W 8/K 6 Zespół Logistyki i Zarządzania Projektami 29
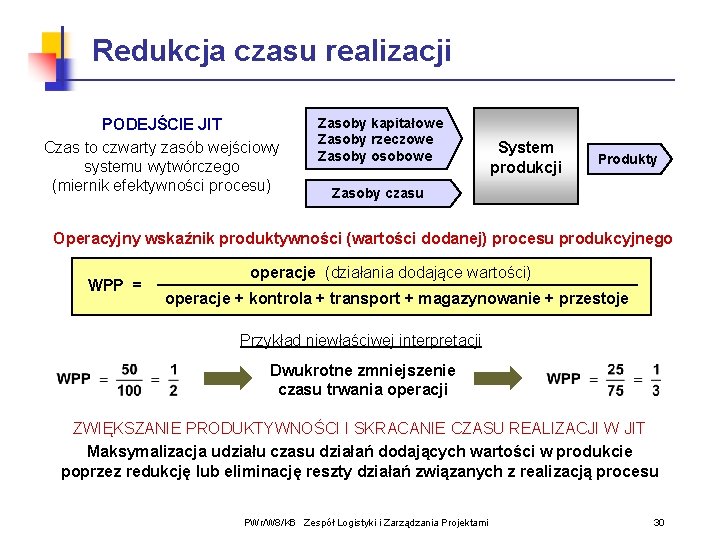
Redukcja czasu realizacji PODEJŚCIE JIT Czas to czwarty zasób wejściowy systemu wytwórczego (miernik efektywności procesu) Zasoby kapitałowe Zasoby rzeczowe Zasoby osobowe System produkcji Produkty Zasoby czasu Operacyjny wskaźnik produktywności (wartości dodanej) procesu produkcyjnego WPP = operacje (działania dodające wartości) operacje + kontrola + transport + magazynowanie + przestoje Przykład niewłaściwej interpretacji Dwukrotne zmniejszenie czasu trwania operacji ZWIĘKSZANIE PRODUKTYWNOŚCI I SKRACANIE CZASU REALIZACJI W JIT Maksymalizacja udziału czasu działań dodających wartości w produkcie poprzez redukcję lub eliminację reszty działań związanych z realizacją procesu PWr/W 8/K 6 Zespół Logistyki i Zarządzania Projektami 30
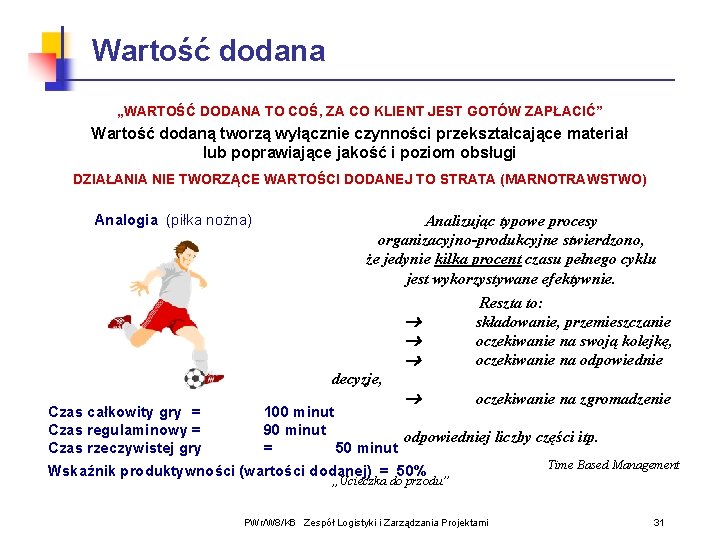
Wartość dodana „WARTOŚĆ DODANA TO COŚ, ZA CO KLIENT JEST GOTÓW ZAPŁACIĆ” Wartość dodaną tworzą wyłącznie czynności przekształcające materiał lub poprawiające jakość i poziom obsługi DZIAŁANIA NIE TWORZĄCE WARTOŚCI DODANEJ TO STRATA (MARNOTRAWSTWO) Analogia (piłka nożna) Analizując typowe procesy organizacyjno-produkcyjne stwierdzono, że jedynie kilka procent czasu pełnego cyklu jest wykorzystywane efektywnie. decyzje, Czas całkowity gry = Czas regulaminowy = Czas rzeczywistej gry Reszta to: składowanie, przemieszczanie oczekiwanie na swoją kolejkę, oczekiwanie na odpowiednie oczekiwanie na zgromadzenie 100 minut 90 minut odpowiedniej liczby części itp. = 50 minut Wskaźnik produktywności (wartości dodanej) = 50% Time Based Management „Ucieczka do przodu” PWr/W 8/K 6 Zespół Logistyki i Zarządzania Projektami 31
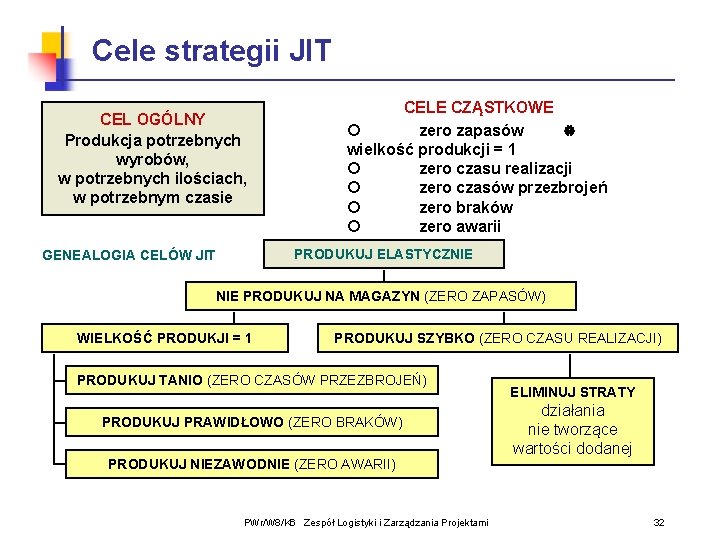
Cele strategii JIT CEL OGÓLNY Produkcja potrzebnych wyrobów, w potrzebnych ilościach, w potrzebnym czasie CELE CZĄSTKOWE zero zapasów wielkość produkcji = 1 zero czasu realizacji zero czasów przezbrojeń zero braków zero awarii PRODUKUJ ELASTYCZNIE GENEALOGIA CELÓW JIT NIE PRODUKUJ NA MAGAZYN (ZERO ZAPASÓW) WIELKOŚĆ PRODUKJI = 1 PRODUKUJ SZYBKO (ZERO CZASU REALIZACJI) PRODUKUJ TANIO (ZERO CZASÓW PRZEZBROJEŃ) PRODUKUJ PRAWIDŁOWO (ZERO BRAKÓW) PRODUKUJ NIEZAWODNIE (ZERO AWARII) PWr/W 8/K 6 Zespół Logistyki i Zarządzania Projektami ELIMINUJ STRATY działania nie tworzące wartości dodanej 32
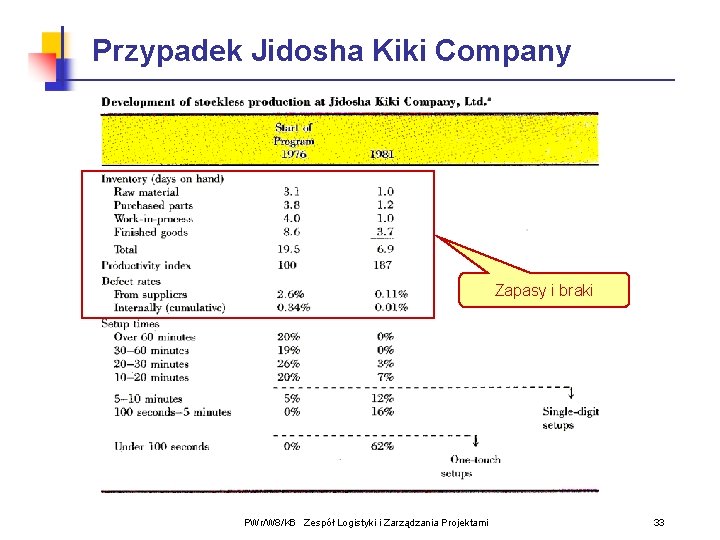
Przypadek Jidosha Kiki Company Zapasy i braki PWr/W 8/K 6 Zespół Logistyki i Zarządzania Projektami 33
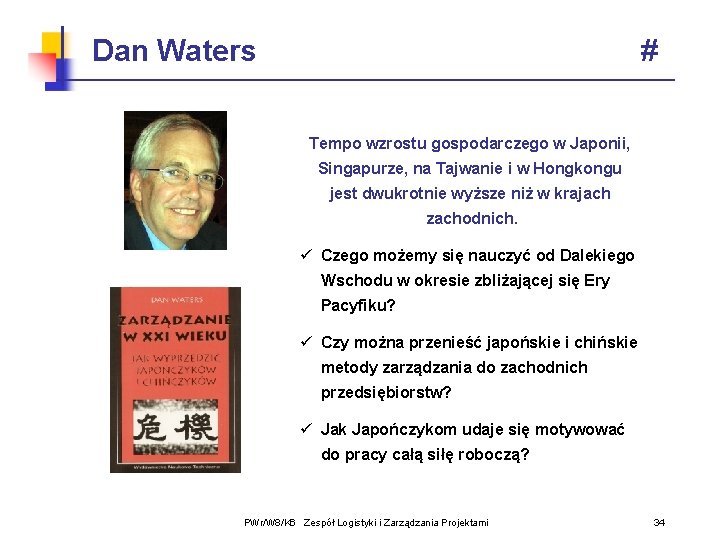
Dan Waters # Tempo wzrostu gospodarczego w Japonii, Singapurze, na Tajwanie i w Hongkongu jest dwukrotnie wyższe niż w krajach zachodnich. ü Czego możemy się nauczyć od Dalekiego Wschodu w okresie zbliżającej się Ery Pacyfiku? ü Czy można przenieść japońskie i chińskie metody zarządzania do zachodnich przedsiębiorstw? ü Jak Japończykom udaje się motywować do pracy całą siłę roboczą? PWr/W 8/K 6 Zespół Logistyki i Zarządzania Projektami 34
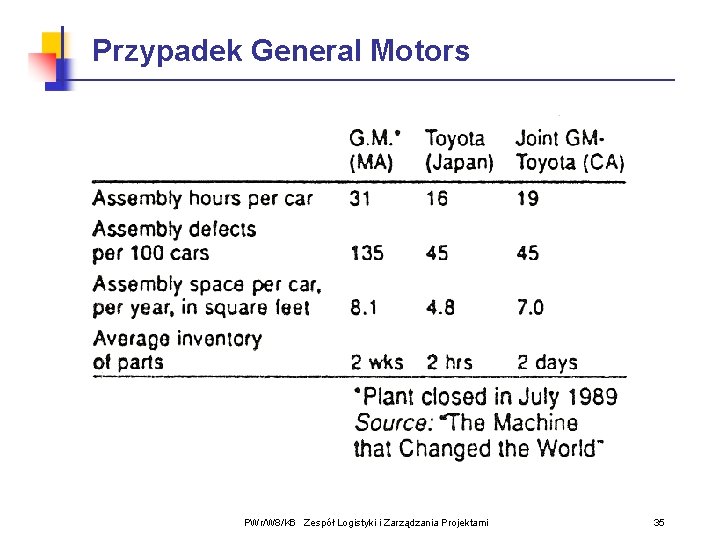
Przypadek General Motors PWr/W 8/K 6 Zespół Logistyki i Zarządzania Projektami 35
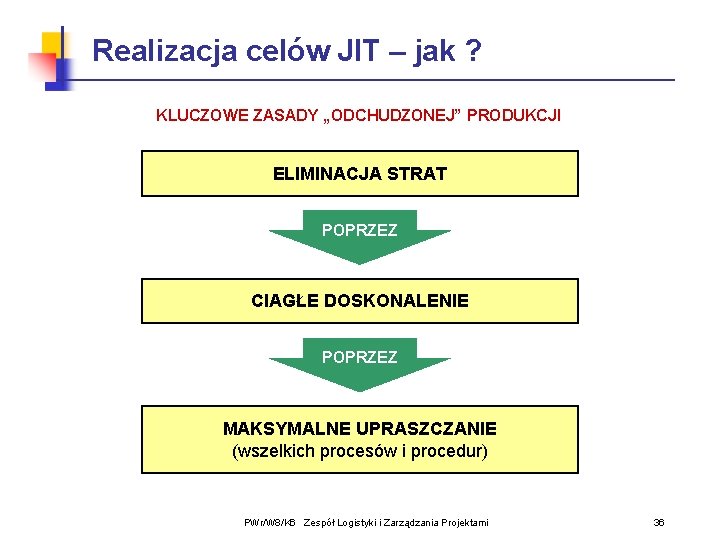
Realizacja celów JIT – jak ? KLUCZOWE ZASADY „ODCHUDZONEJ” PRODUKCJI ELIMINACJA STRAT POPRZEZ CIAGŁE DOSKONALENIE POPRZEZ MAKSYMALNE UPRASZCZANIE (wszelkich procesów i procedur) PWr/W 8/K 6 Zespół Logistyki i Zarządzania Projektami 36
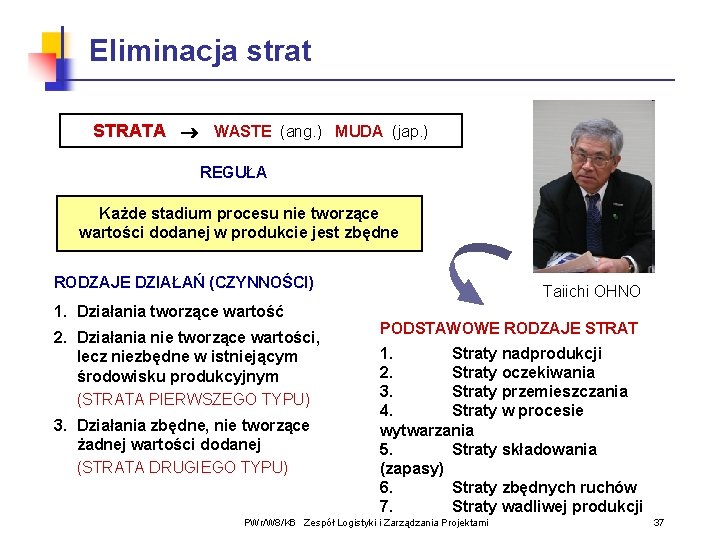
Eliminacja strat STRATA WASTE (ang. ) MUDA (jap. ) REGUŁA Każde stadium procesu nie tworzące wartości dodanej w produkcie jest zbędne RODZAJE DZIAŁAŃ (CZYNNOŚCI) 1. Działania tworzące wartość 2. Działania nie tworzące wartości, lecz niezbędne w istniejącym środowisku produkcyjnym (STRATA PIERWSZEGO TYPU) 3. Działania zbędne, nie tworzące żadnej wartości dodanej (STRATA DRUGIEGO TYPU) Taiichi OHNO PODSTAWOWE RODZAJE STRAT 1. Straty nadprodukcji 2. Straty oczekiwania 3. Straty przemieszczania 4. Straty w procesie wytwarzania 5. Straty składowania (zapasy) 6. Straty zbędnych ruchów 7. Straty wadliwej produkcji PWr/W 8/K 6 Zespół Logistyki i Zarządzania Projektami 37
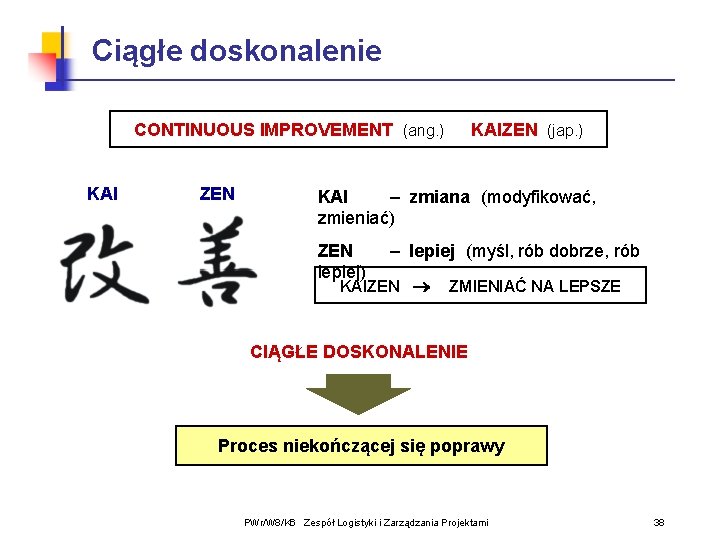
Ciągłe doskonalenie CONTINUOUS IMPROVEMENT (ang. ) KAI ZEN KAIZEN (jap. ) KAI – zmiana (modyfikować, zmieniać) ZEN lepiej) – lepiej (myśl, rób dobrze, rób KAIZEN ZMIENIAĆ NA LEPSZE CIĄGŁE DOSKONALENIE Proces niekończącej się poprawy PWr/W 8/K 6 Zespół Logistyki i Zarządzania Projektami 38
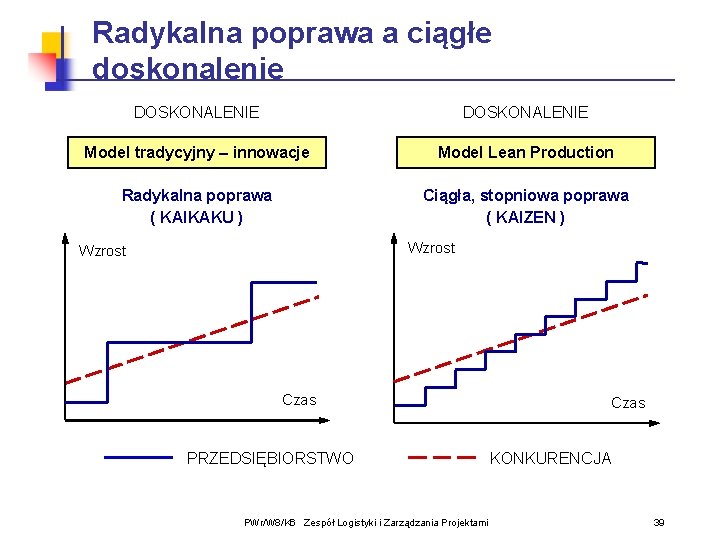
Radykalna poprawa a ciągłe doskonalenie DOSKONALENIE Model tradycyjny – innowacje Model Lean Production Radykalna poprawa ( KAIKAKU ) Ciągła, stopniowa poprawa ( KAIZEN ) Wzrost Czas PRZEDSIĘBIORSTWO PWr/W 8/K 6 Zespół Logistyki i Zarządzania Projektami Czas KONKURENCJA 39
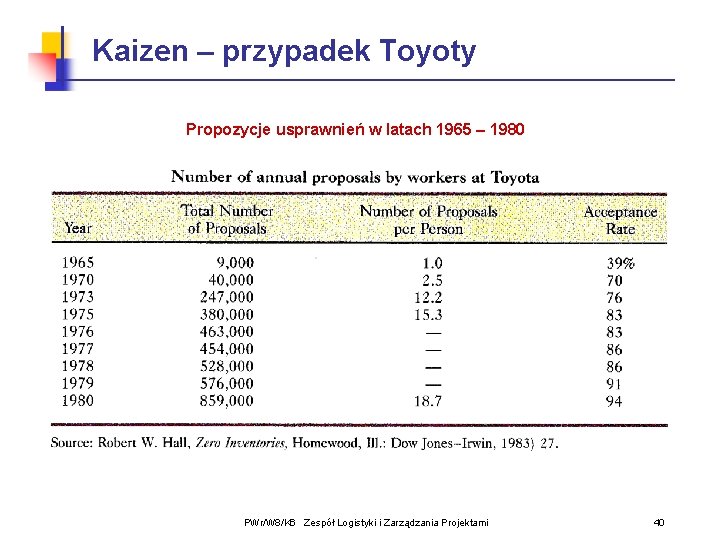
Kaizen – przypadek Toyoty Propozycje usprawnień w latach 1965 – 1980 PWr/W 8/K 6 Zespół Logistyki i Zarządzania Projektami 40
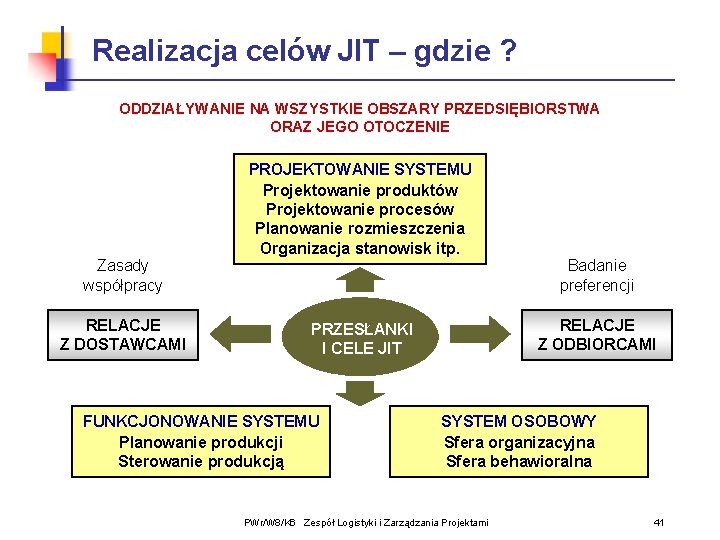
Realizacja celów JIT – gdzie ? ODDZIAŁYWANIE NA WSZYSTKIE OBSZARY PRZEDSIĘBIORSTWA ORAZ JEGO OTOCZENIE Zasady współpracy RELACJE Z DOSTAWCAMI PROJEKTOWANIE SYSTEMU Projektowanie produktów Projektowanie procesów Planowanie rozmieszczenia Organizacja stanowisk itp. RELACJE Z ODBIORCAMI PRZESŁANKI I CELE JIT FUNKCJONOWANIE SYSTEMU Planowanie produkcji Sterowanie produkcją Badanie preferencji SYSTEM OSOBOWY Sfera organizacyjna Sfera behawioralna PWr/W 8/K 6 Zespół Logistyki i Zarządzania Projektami 41
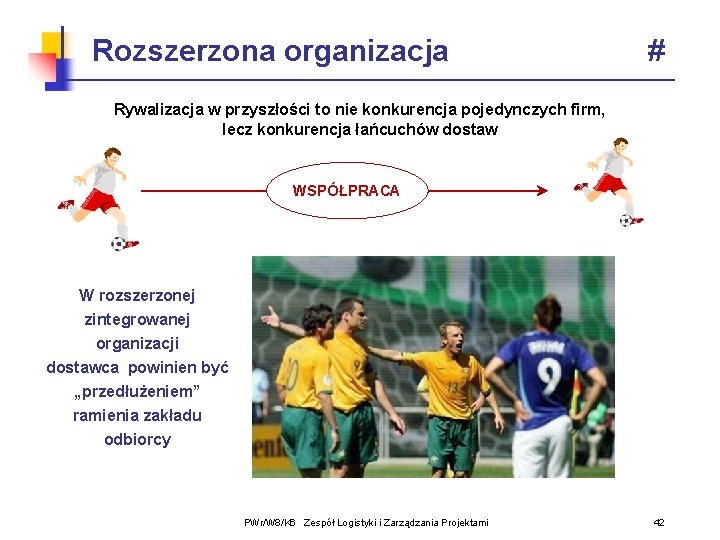
Rozszerzona organizacja # Rywalizacja w przyszłości to nie konkurencja pojedynczych firm, lecz konkurencja łańcuchów dostaw WSPÓŁPRACA W rozszerzonej zintegrowanej organizacji dostawca powinien być „przedłużeniem” ramienia zakładu odbiorcy PWr/W 8/K 6 Zespół Logistyki i Zarządzania Projektami 42
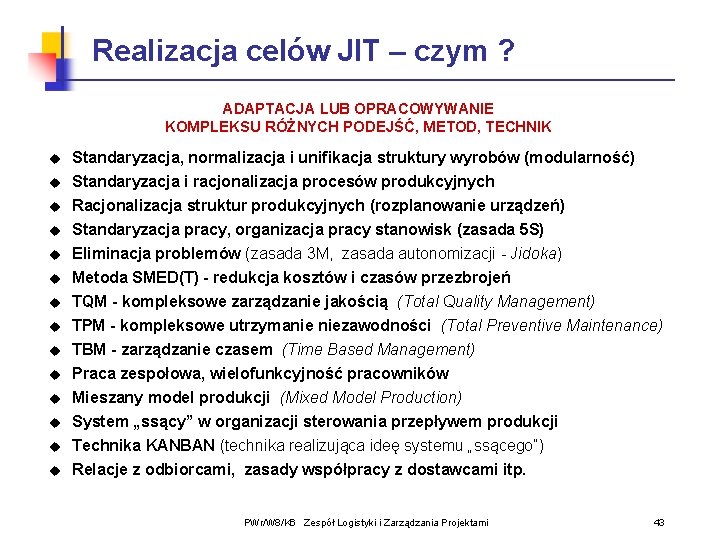
Realizacja celów JIT – czym ? ADAPTACJA LUB OPRACOWYWANIE KOMPLEKSU RÓŻNYCH PODEJŚĆ, METOD, TECHNIK u Standaryzacja, normalizacja i unifikacja struktury wyrobów (modularność) Standaryzacja i racjonalizacja procesów produkcyjnych Racjonalizacja struktur produkcyjnych (rozplanowanie urządzeń) u Standaryzacja pracy, organizacja pracy stanowisk (zasada 5 S) u Eliminacja problemów (zasada 3 M, zasada autonomizacji - Jidoka) u Metoda SMED(T) - redukcja kosztów i czasów przezbrojeń TQM - kompleksowe zarządzanie jakością (Total Quality Management) TPM - kompleksowe utrzymanie niezawodności (Total Preventive Maintenance) TBM - zarządzanie czasem (Time Based Management) Praca zespołowa, wielofunkcyjność pracowników Mieszany model produkcji (Mixed Model Production) System „ssący” w organizacji sterowania przepływem produkcji Technika KANBAN (technika realizująca ideę systemu „ssącego”) Relacje z odbiorcami, zasady współpracy z dostawcami itp. u u u u u PWr/W 8/K 6 Zespół Logistyki i Zarządzania Projektami 43
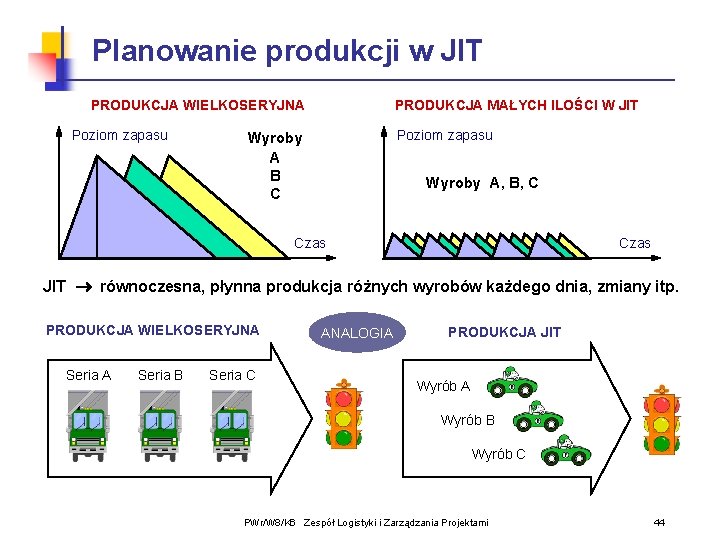
Planowanie produkcji w JIT PRODUKCJA WIELKOSERYJNA Poziom zapasu PRODUKCJA MAŁYCH ILOŚCI W JIT Poziom zapasu Wyroby A B C Wyroby A, B, C Czas JIT równoczesna, płynna produkcja różnych wyrobów każdego dnia, zmiany itp. PRODUKCJA WIELKOSERYJNA Seria B Seria C ANALOGIA PRODUKCJA JIT Wyrób A Wyrób B Wyrób C PWr/W 8/K 6 Zespół Logistyki i Zarządzania Projektami 44
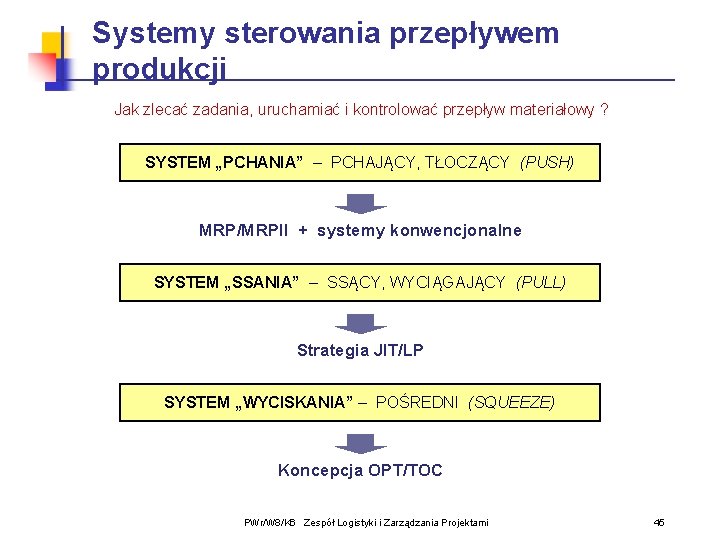
Systemy sterowania przepływem produkcji Jak zlecać zadania, uruchamiać i kontrolować przepływ materiałowy ? SYSTEM „PCHANIA” – PCHAJĄCY, TŁOCZĄCY (PUSH) MRP/MRPII + systemy konwencjonalne SYSTEM „SSANIA” – SSĄCY, WYCIĄGAJĄCY (PULL) Strategia JIT/LP SYSTEM „WYCISKANIA” – POŚREDNI (SQUEEZE) Koncepcja OPT/TOC PWr/W 8/K 6 Zespół Logistyki i Zarządzania Projektami 45
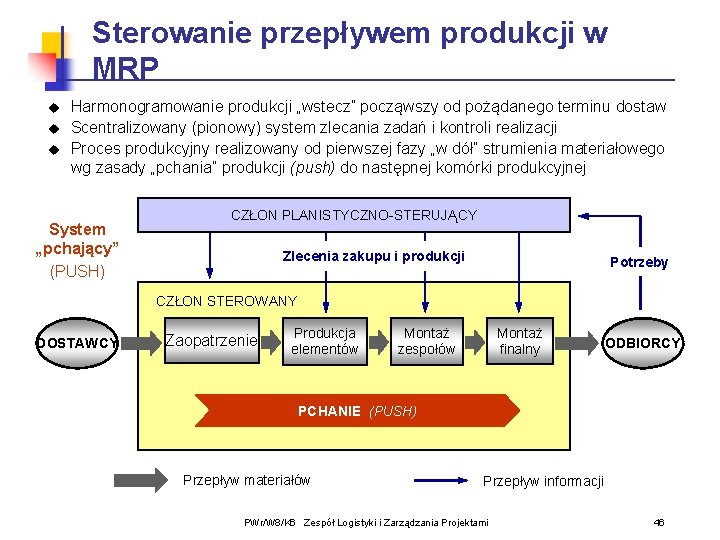
Sterowanie przepływem produkcji w MRP u u u Harmonogramowanie produkcji „wstecz” począwszy od pożądanego terminu dostaw Scentralizowany (pionowy) system zlecania zadań i kontroli realizacji Proces produkcyjny realizowany od pierwszej fazy „w dół” strumienia materiałowego wg zasady „pchania” produkcji (push) do następnej komórki produkcyjnej System „pchający” (PUSH) CZŁON PLANISTYCZNO-STERUJĄCY Zlecenia zakupu i produkcji Potrzeby CZŁON STEROWANY DOSTAWCY Zaopatrzenie Produkcja elementów Montaż zespołów Montaż finalny ODBIORCY PCHANIE (PUSH) Przepływ materiałów Przepływ informacji PWr/W 8/K 6 Zespół Logistyki i Zarządzania Projektami 46
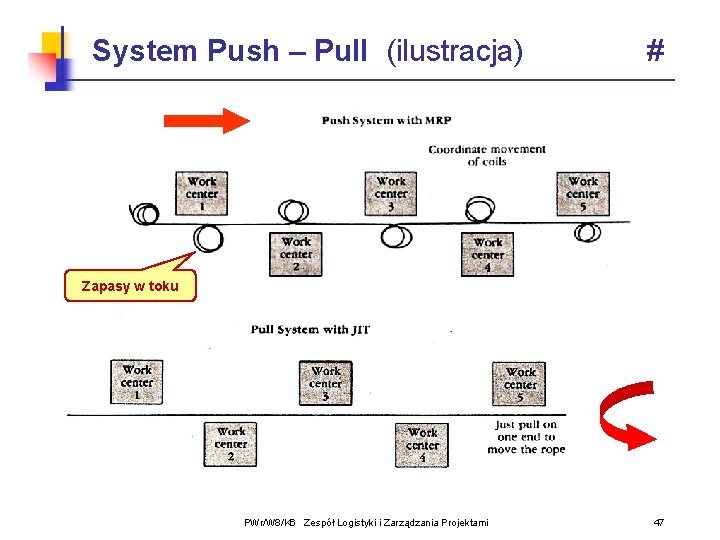
System Push – Pull (ilustracja) # Zapasy w toku PWr/W 8/K 6 Zespół Logistyki i Zarządzania Projektami 47
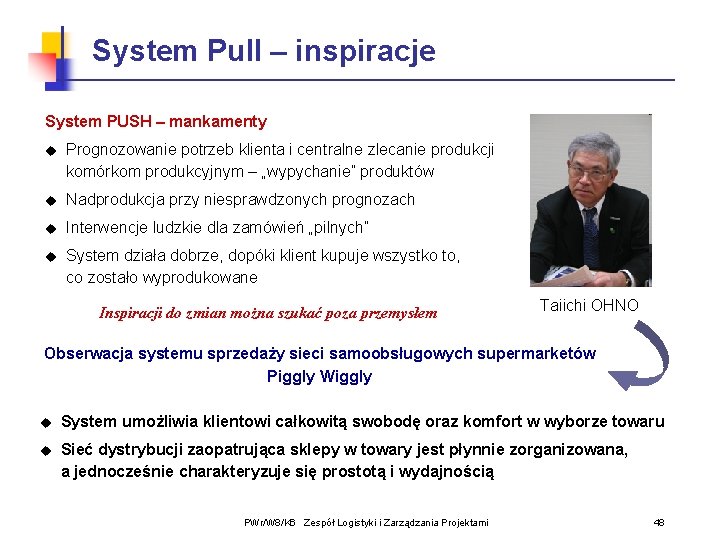
System Pull – inspiracje System PUSH – mankamenty u Prognozowanie potrzeb klienta i centralne zlecanie produkcji komórkom produkcyjnym – „wypychanie” produktów u Nadprodukcja przy niesprawdzonych prognozach u Interwencje ludzkie dla zamówień „pilnych” u System działa dobrze, dopóki klient kupuje wszystko to, co zostało wyprodukowane Inspiracji do zmian można szukać poza przemysłem Taiichi OHNO Obserwacja systemu sprzedaży sieci samoobsługowych supermarketów Piggly Wiggly u System umożliwia klientowi całkowitą swobodę oraz komfort w wyborze towaru u Sieć dystrybucji zaopatrująca sklepy w towary jest płynnie zorganizowana, a jednocześnie charakteryzuje się prostotą i wydajnością PWr/W 8/K 6 Zespół Logistyki i Zarządzania Projektami 48
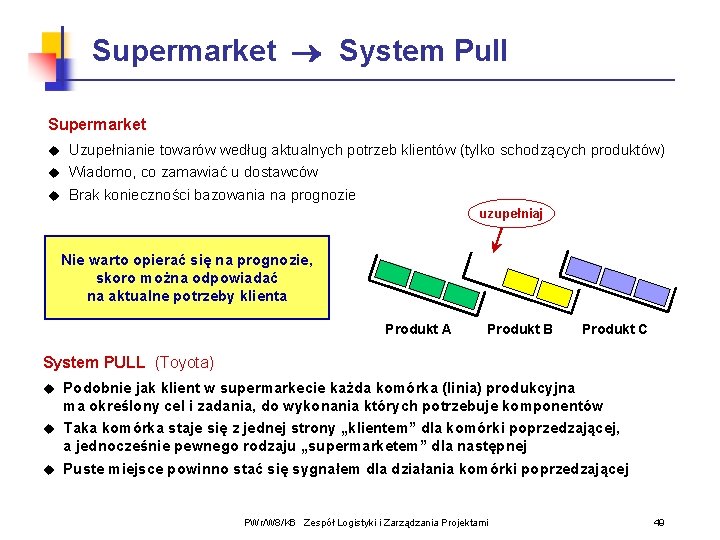
Supermarket System Pull Supermarket u Uzupełnianie towarów według aktualnych potrzeb klientów (tylko schodzących produktów) Wiadomo, co zamawiać u dostawców u Brak konieczności bazowania na prognozie u uzupełniaj Nie warto opierać się na prognozie, skoro można odpowiadać na aktualne potrzeby klienta Produkt A Produkt B Produkt C System PULL (Toyota) u u u Podobnie jak klient w supermarkecie każda komórka (linia) produkcyjna ma określony cel i zadania, do wykonania których potrzebuje komponentów Taka komórka staje się z jednej strony „klientem” dla komórki poprzedzającej, a jednocześnie pewnego rodzaju „supermarketem” dla następnej Puste miejsce powinno stać się sygnałem dla działania komórki poprzedzającej PWr/W 8/K 6 Zespół Logistyki i Zarządzania Projektami 49
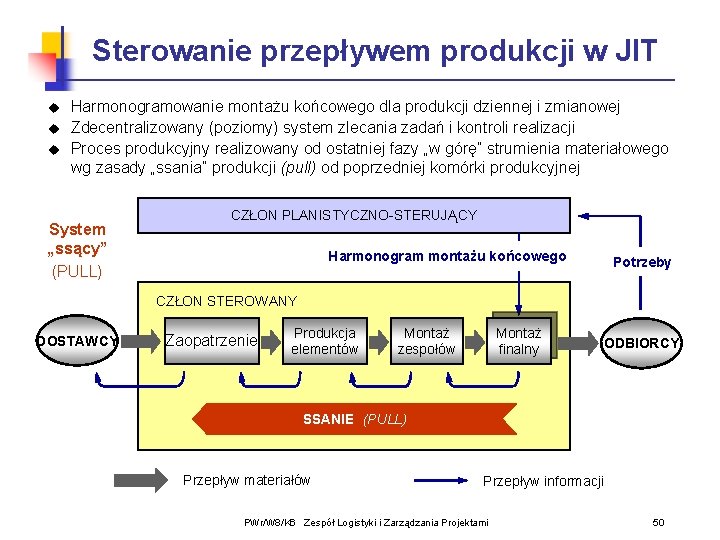
Sterowanie przepływem produkcji w JIT u u u Harmonogramowanie montażu końcowego dla produkcji dziennej i zmianowej Zdecentralizowany (poziomy) system zlecania zadań i kontroli realizacji Proces produkcyjny realizowany od ostatniej fazy „w górę” strumienia materiałowego wg zasady „ssania” produkcji (pull) od poprzedniej komórki produkcyjnej System „ssący” (PULL) CZŁON PLANISTYCZNO-STERUJĄCY Harmonogram montażu końcowego Potrzeby CZŁON STEROWANY DOSTAWCY Zaopatrzenie Produkcja elementów Montaż zespołów Montaż finalny ODBIORCY SSANIE (PULL) Przepływ materiałów Przepływ informacji PWr/W 8/K 6 Zespół Logistyki i Zarządzania Projektami 50
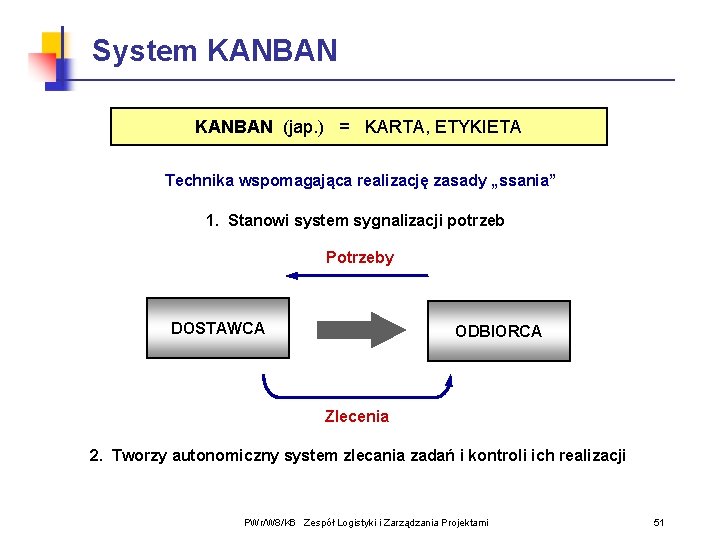
System KANBAN (jap. ) = KARTA, ETYKIETA Technika wspomagająca realizację zasady „ssania” 1. Stanowi system sygnalizacji potrzeb Potrzeby DOSTAWCA ODBIORCA Zlecenia 2. Tworzy autonomiczny system zlecania zadań i kontroli ich realizacji PWr/W 8/K 6 Zespół Logistyki i Zarządzania Projektami 51
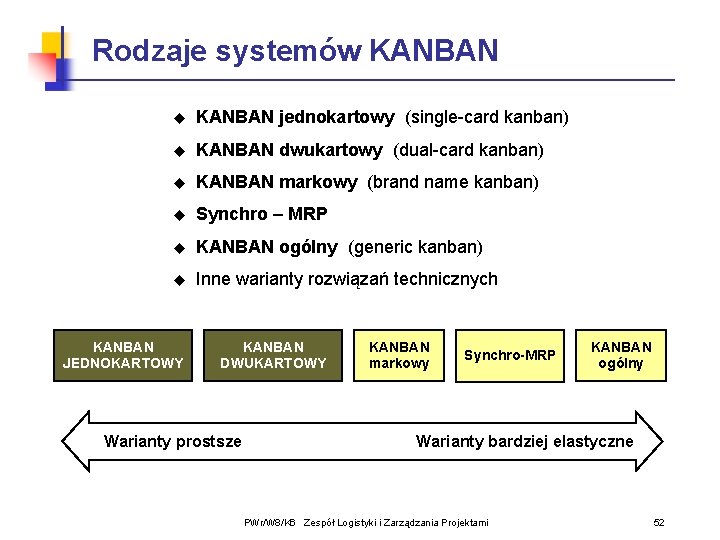
Rodzaje systemów KANBAN u KANBAN jednokartowy (single-card kanban) u KANBAN dwukartowy (dual-card kanban) u KANBAN markowy (brand name kanban) u Synchro – MRP u KANBAN ogólny (generic kanban) u Inne warianty rozwiązań technicznych KANBAN JEDNOKARTOWY KANBAN DWUKARTOWY Warianty prostsze KANBAN markowy Synchro-MRP KANBAN ogólny Warianty bardziej elastyczne PWr/W 8/K 6 Zespół Logistyki i Zarządzania Projektami 52
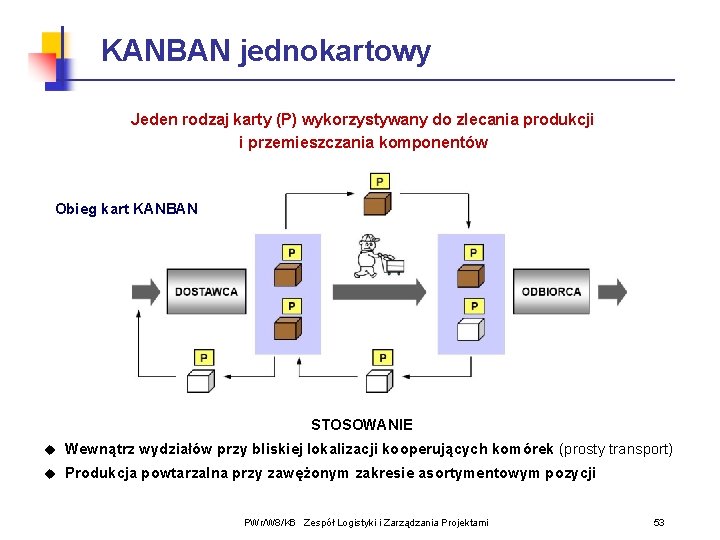
KANBAN jednokartowy Jeden rodzaj karty (P) wykorzystywany do zlecania produkcji i przemieszczania komponentów Obieg kart KANBAN STOSOWANIE u Wewnątrz wydziałów przy bliskiej lokalizacji kooperujących komórek (prosty transport) u Produkcja powtarzalna przy zawężonym zakresie asortymentowym pozycji PWr/W 8/K 6 Zespół Logistyki i Zarządzania Projektami 53
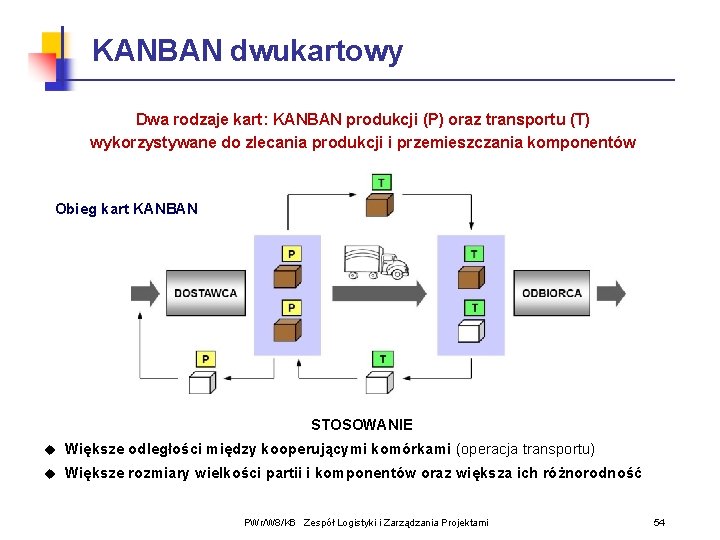
KANBAN dwukartowy Dwa rodzaje kart: KANBAN produkcji (P) oraz transportu (T) wykorzystywane do zlecania produkcji i przemieszczania komponentów Obieg kart KANBAN STOSOWANIE u Większe odległości między kooperującymi komórkami (operacja transportu) u Większe rozmiary wielkości partii i komponentów oraz większa ich różnorodność PWr/W 8/K 6 Zespół Logistyki i Zarządzania Projektami 54
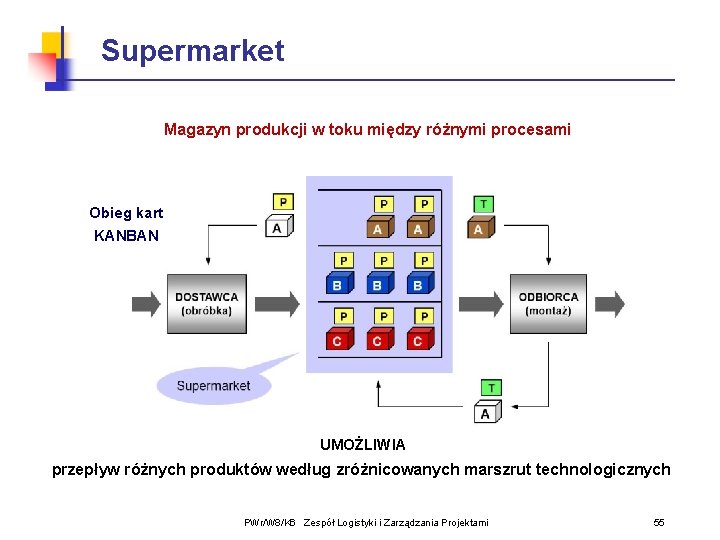
Supermarket Magazyn produkcji w toku między różnymi procesami Obieg kart KANBAN UMOŻLIWIA przepływ różnych produktów według zróżnicowanych marszrut technologicznych PWr/W 8/K 6 Zespół Logistyki i Zarządzania Projektami 55
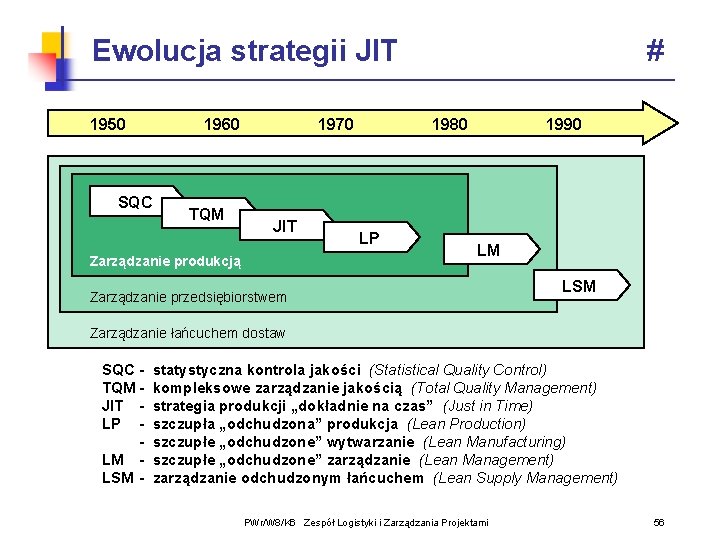
Ewolucja strategii JIT 1950 SQC 1960 TQM 1970 JIT Zarządzanie produkcją # 1980 LP 1990 LM Zarządzanie przedsiębiorstwem LSM Zarządzanie łańcuchem dostaw SQC TQM JIT LP LM LSM - statystyczna kontrola jakości (Statistical Quality Control) kompleksowe zarządzanie jakością (Total Quality Management) strategia produkcji „dokładnie na czas” (Just in Time) szczupła „odchudzona” produkcja (Lean Production) szczupłe „odchudzone” wytwarzanie (Lean Manufacturing) szczupłe „odchudzone” zarządzanie (Lean Management) zarządzanie odchudzonym łańcuchem (Lean Supply Management) PWr/W 8/K 6 Zespół Logistyki i Zarządzania Projektami 56
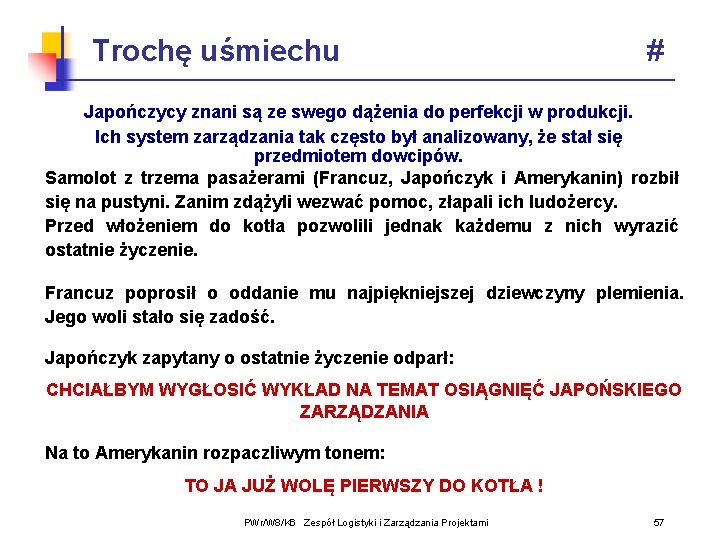
Trochę uśmiechu # Japończycy znani są ze swego dążenia do perfekcji w produkcji. Ich system zarządzania tak często był analizowany, że stał się przedmiotem dowcipów. Samolot z trzema pasażerami (Francuz, Japończyk i Amerykanin) rozbił się na pustyni. Zanim zdążyli wezwać pomoc, złapali ich ludożercy. Przed włożeniem do kotła pozwolili jednak każdemu z nich wyrazić ostatnie życzenie. Francuz poprosił o oddanie mu najpiękniejszej dziewczyny plemienia. Jego woli stało się zadość. Japończyk zapytany o ostatnie życzenie odparł: CHCIAŁBYM WYGŁOSIĆ WYKŁAD NA TEMAT OSIĄGNIĘĆ JAPOŃSKIEGO ZARZĄDZANIA Na to Amerykanin rozpaczliwym tonem: TO JA JUŻ WOLĘ PIERWSZY DO KOTŁA ! PWr/W 8/K 6 Zespół Logistyki i Zarządzania Projektami 57
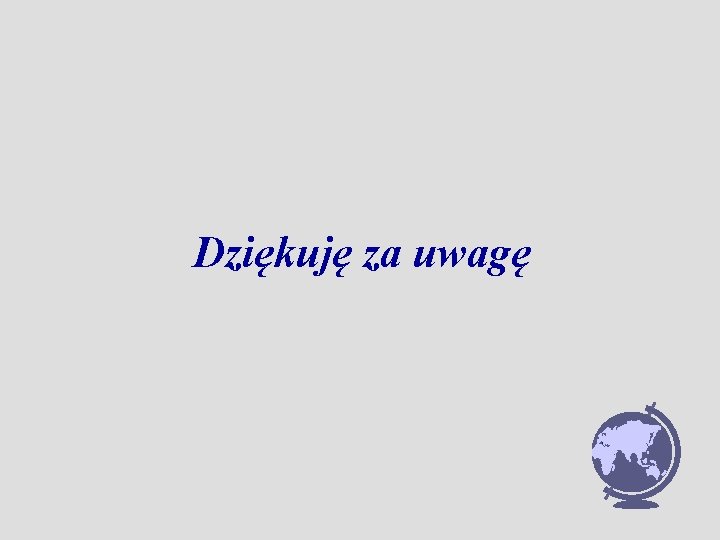
Dziękuję za uwagę
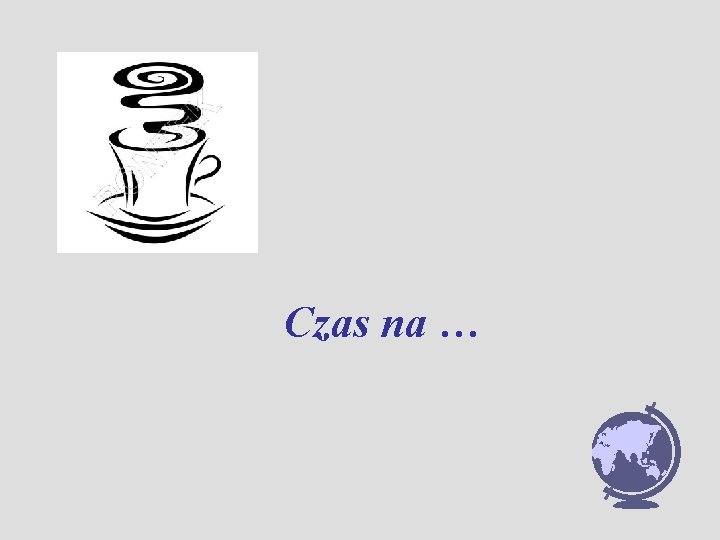
Czas na …
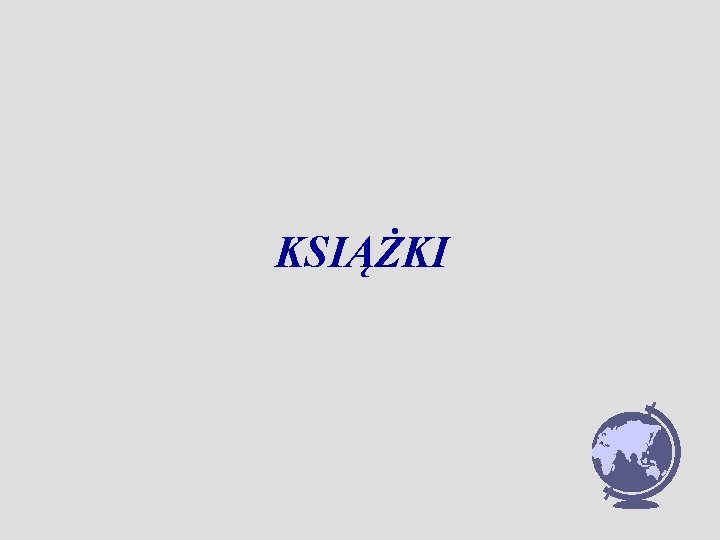
KSIĄŻKI
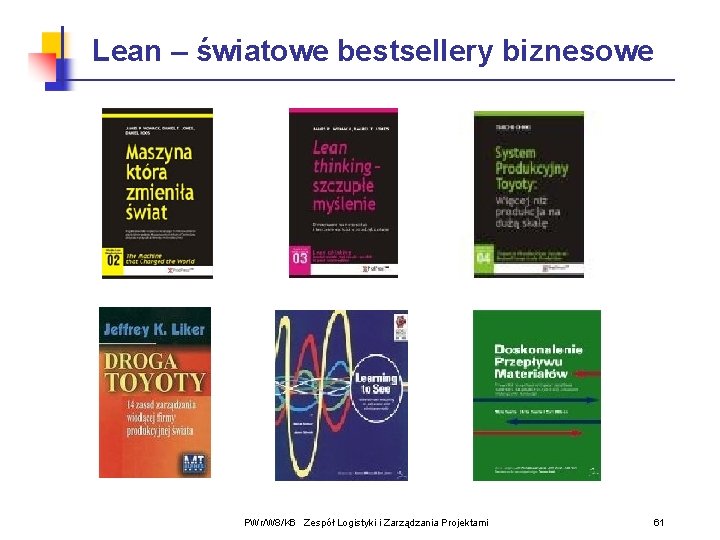
Lean – światowe bestsellery biznesowe PWr/W 8/K 6 Zespół Logistyki i Zarządzania Projektami 61
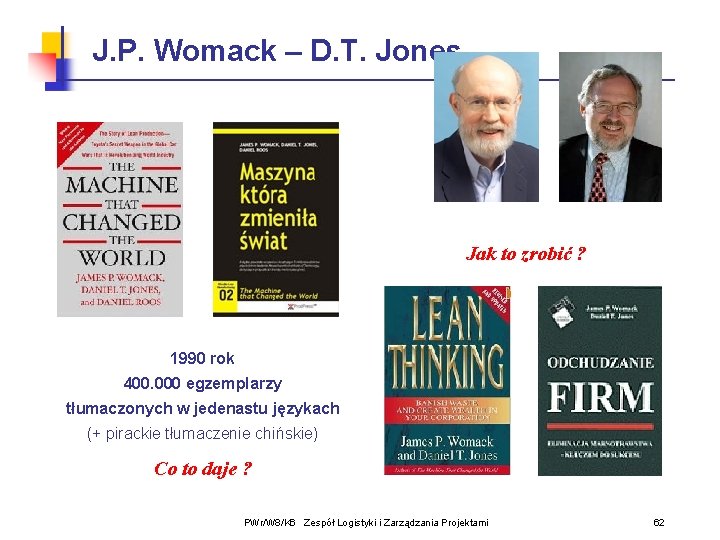
J. P. Womack – D. T. Jones Jak to zrobić ? 1990 rok 400. 000 egzemplarzy tłumaczonych w jedenastu językach (+ pirackie tłumaczenie chińskie) Co to daje ? PWr/W 8/K 6 Zespół Logistyki i Zarządzania Projektami 62
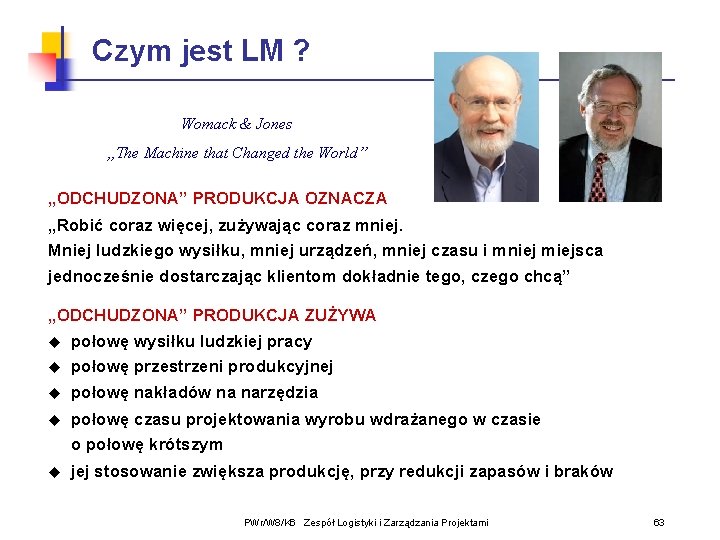
Czym jest LM ? Womack & Jones „The Machine that Changed the World” „ODCHUDZONA” PRODUKCJA OZNACZA „Robić coraz więcej, zużywając coraz mniej. Mniej ludzkiego wysiłku, mniej urządzeń, mniej czasu i mniej miejsca jednocześnie dostarczając klientom dokładnie tego, czego chcą” „ODCHUDZONA” PRODUKCJA ZUŻYWA u u u połowę wysiłku ludzkiej pracy połowę przestrzeni produkcyjnej połowę nakładów na narzędzia u połowę czasu projektowania wyrobu wdrażanego w czasie o połowę krótszym u jej stosowanie zwiększa produkcję, przy redukcji zapasów i braków PWr/W 8/K 6 Zespół Logistyki i Zarządzania Projektami 63

J. K. Liker – 14 zasad TPS # Ogólna koncepcja Procesy Ludzie i partnerzy Doskonalenie procesu Rozwiązywanie problemów anie iązyw Rozw lemów prob Filozofia Rozw iąz prob ywanie lemó w Ludzie i partnerzy Wykorzystując pełny potencjał koncepcji TPS należy połączyć wszystkie obszary i zasady w jeden system (organizm) PWr/W 8/K 6 Zespół Logistyki i Zarządzania Projektami 64
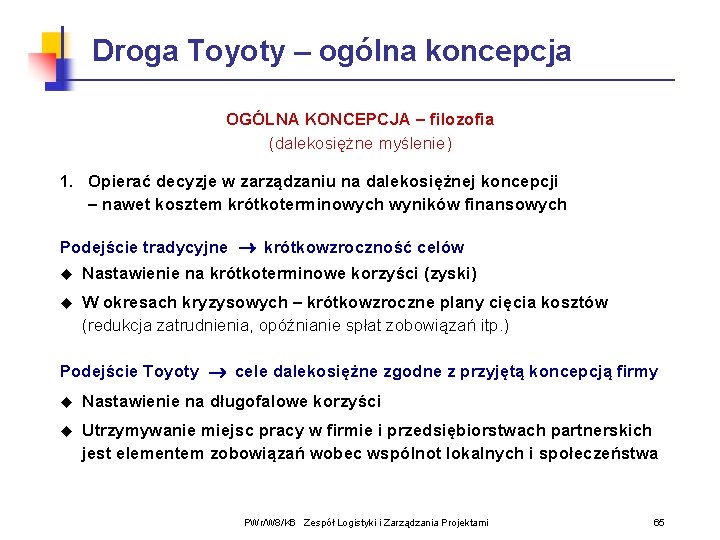
Droga Toyoty – ogólna koncepcja OGÓLNA KONCEPCJA – filozofia (dalekosiężne myślenie) 1. Opierać decyzje w zarządzaniu na dalekosiężnej koncepcji – nawet kosztem krótkoterminowych wyników finansowych Podejście tradycyjne krótkowzroczność celów u Nastawienie na krótkoterminowe korzyści (zyski) u W okresach kryzysowych – krótkowzroczne plany cięcia kosztów (redukcja zatrudnienia, opóźnianie spłat zobowiązań itp. ) Podejście Toyoty cele dalekosiężne zgodne z przyjętą koncepcją firmy u Nastawienie na długofalowe korzyści u Utrzymywanie miejsc pracy w firmie i przedsiębiorstwach partnerskich jest elementem zobowiązań wobec wspólnot lokalnych i społeczeństwa PWr/W 8/K 6 Zespół Logistyki i Zarządzania Projektami 65
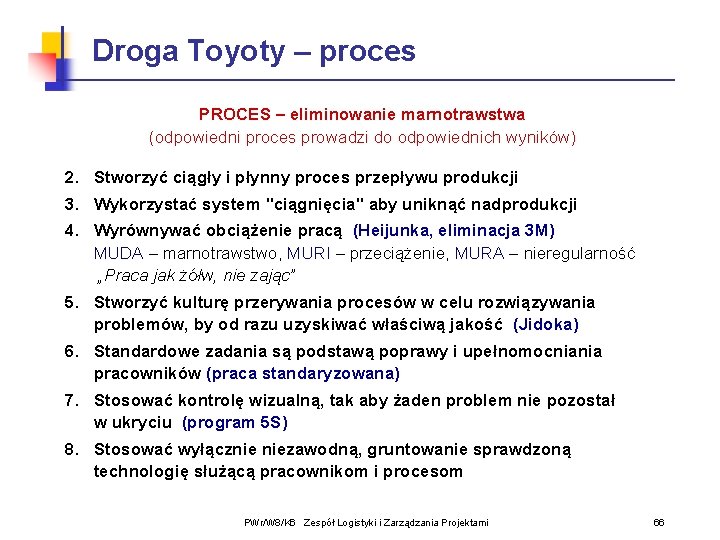
Droga Toyoty – proces PROCES – eliminowanie marnotrawstwa (odpowiedni proces prowadzi do odpowiednich wyników) 2. Stworzyć ciągły i płynny proces przepływu produkcji 3. Wykorzystać system "ciągnięcia" aby uniknąć nadprodukcji 4. Wyrównywać obciążenie pracą (Heijunka, eliminacja 3 M) MUDA – marnotrawstwo, MURI – przeciążenie, MURA – nieregularność „Praca jak żółw, nie zając” 5. Stworzyć kulturę przerywania procesów w celu rozwiązywania problemów, by od razu uzyskiwać właściwą jakość (Jidoka) 6. Standardowe zadania są podstawą poprawy i upełnomocniania pracowników (praca standaryzowana) 7. Stosować kontrolę wizualną, tak aby żaden problem nie pozostał w ukryciu (program 5 S) 8. Stosować wyłącznie niezawodną, gruntowanie sprawdzoną technologię służącą pracownikom i procesom PWr/W 8/K 6 Zespół Logistyki i Zarządzania Projektami 66
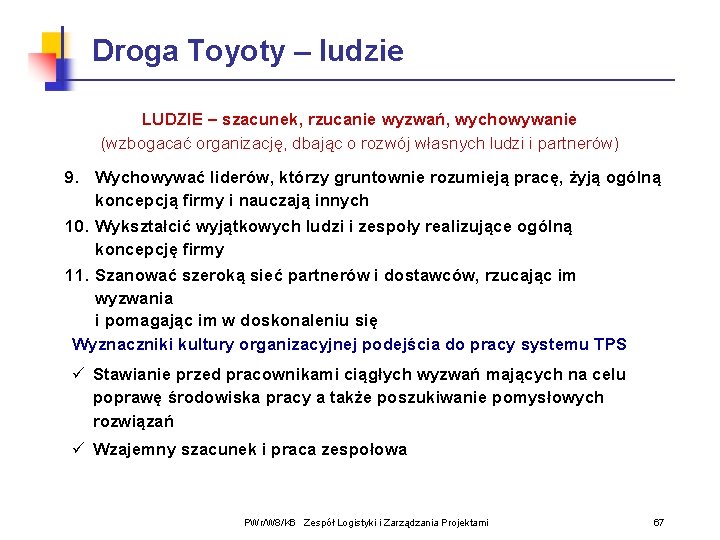
Droga Toyoty – ludzie LUDZIE – szacunek, rzucanie wyzwań, wychowywanie (wzbogacać organizację, dbając o rozwój własnych ludzi i partnerów) 9. Wychowywać liderów, którzy gruntownie rozumieją pracę, żyją ogólną koncepcją firmy i nauczają innych 10. Wykształcić wyjątkowych ludzi i zespoły realizujące ogólną koncepcję firmy 11. Szanować szeroką sieć partnerów i dostawców, rzucając im wyzwania i pomagając im w doskonaleniu się Wyznaczniki kultury organizacyjnej podejścia do pracy systemu TPS ü Stawianie przed pracownikami ciągłych wyzwań mających na celu poprawę środowiska pracy a także poszukiwanie pomysłowych rozwiązań ü Wzajemny szacunek i praca zespołowa PWr/W 8/K 6 Zespół Logistyki i Zarządzania Projektami 67
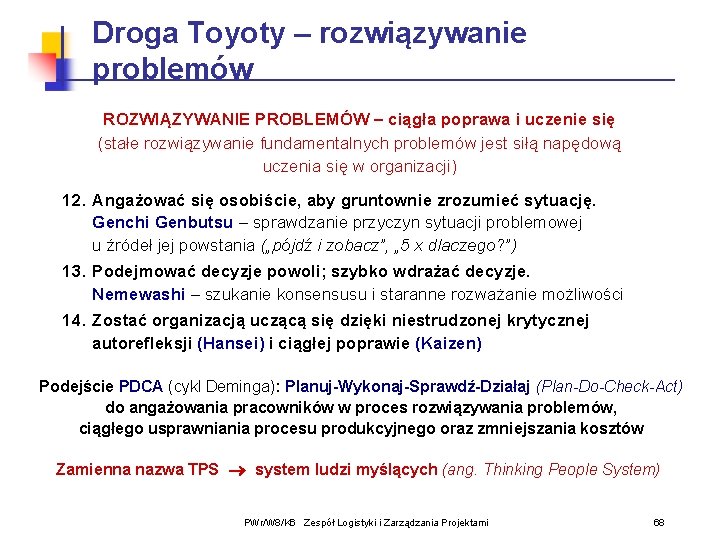
Droga Toyoty – rozwiązywanie problemów ROZWIĄZYWANIE PROBLEMÓW – ciągła poprawa i uczenie się (stałe rozwiązywanie fundamentalnych problemów jest siłą napędową uczenia się w organizacji) 12. Angażować się osobiście, aby gruntownie zrozumieć sytuację. Genchi Genbutsu – sprawdzanie przyczyn sytuacji problemowej u źródeł jej powstania („pójdź i zobacz”, „ 5 x dlaczego? ”) 13. Podejmować decyzje powoli; szybko wdrażać decyzje. Nemewashi – szukanie konsensusu i staranne rozważanie możliwości 14. Zostać organizacją uczącą się dzięki niestrudzonej krytycznej autorefleksji (Hansei) i ciągłej poprawie (Kaizen) Podejście PDCA (cykl Deminga): Planuj-Wykonaj-Sprawdź-Działaj (Plan-Do-Check-Act) do angażowania pracowników w proces rozwiązywania problemów, ciągłego usprawniania procesu produkcyjnego oraz zmniejszania kosztów Zamienna nazwa TPS system ludzi myślących (ang. Thinking People System) PWr/W 8/K 6 Zespół Logistyki i Zarządzania Projektami 68
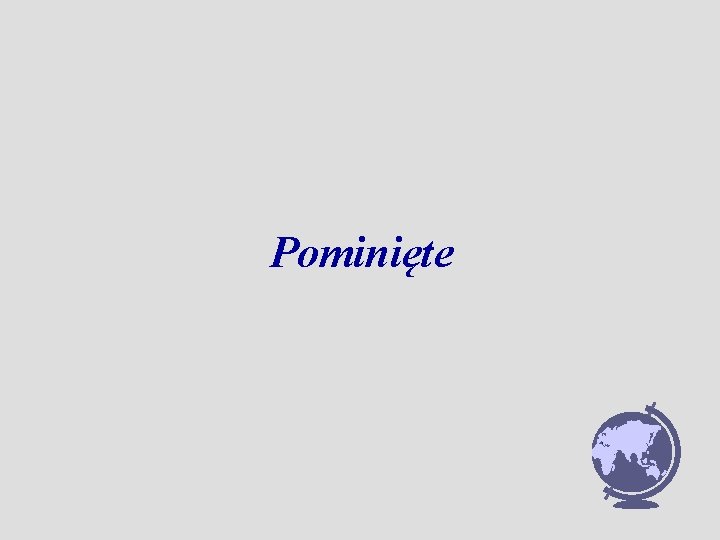
Pominięte
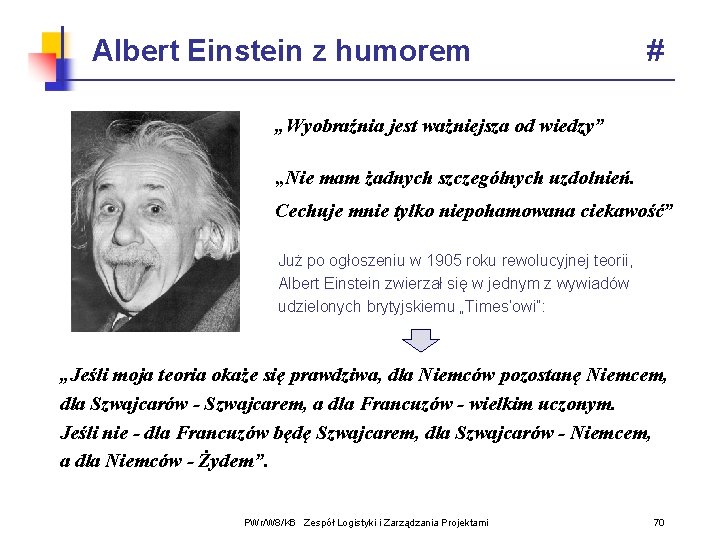
Albert Einstein z humorem # „Wyobraźnia jest ważniejsza od wiedzy” „Nie mam żadnych szczególnych uzdolnień. Cechuje mnie tylko niepohamowana ciekawość” Już po ogłoszeniu w 1905 roku rewolucyjnej teorii, Albert Einstein zwierzał się w jednym z wywiadów udzielonych brytyjskiemu „Times’owi”: „Jeśli moja teoria okaże się prawdziwa, dla Niemców pozostanę Niemcem, dla Szwajcarów - Szwajcarem, a dla Francuzów - wielkim uczonym. Jeśli nie - dla Francuzów będę Szwajcarem, dla Szwajcarów - Niemcem, a dla Niemców - Żydem”. PWr/W 8/K 6 Zespół Logistyki i Zarządzania Projektami 70
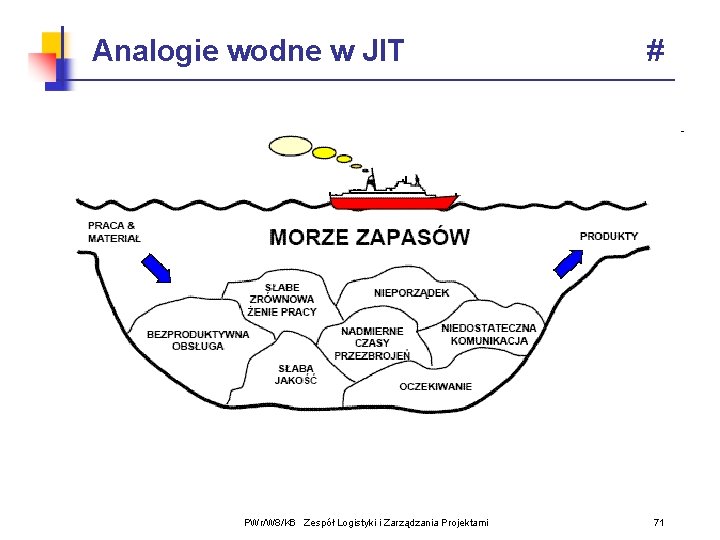
Analogie wodne w JIT PWr/W 8/K 6 Zespół Logistyki i Zarządzania Projektami # 71
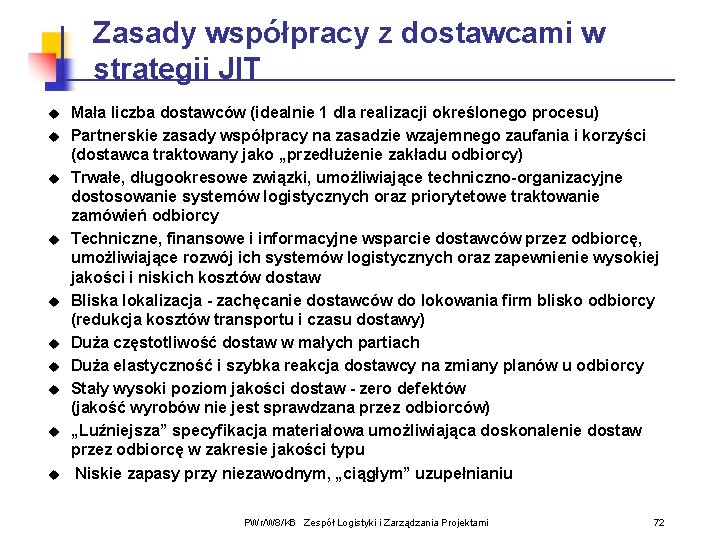
Zasady współpracy z dostawcami w strategii JIT u u u u u Mała liczba dostawców (idealnie 1 dla realizacji określonego procesu) Partnerskie zasady współpracy na zasadzie wzajemnego zaufania i korzyści (dostawca traktowany jako „przedłużenie zakładu odbiorcy) Trwałe, długookresowe związki, umożliwiające techniczno-organizacyjne dostosowanie systemów logistycznych oraz priorytetowe traktowanie zamówień odbiorcy Techniczne, finansowe i informacyjne wsparcie dostawców przez odbiorcę, umożliwiające rozwój ich systemów logistycznych oraz zapewnienie wysokiej jakości i niskich kosztów dostaw Bliska lokalizacja - zachęcanie dostawców do lokowania firm blisko odbiorcy (redukcja kosztów transportu i czasu dostawy) Duża częstotliwość dostaw w małych partiach Duża elastyczność i szybka reakcja dostawcy na zmiany planów u odbiorcy Stały wysoki poziom jakości dostaw - zero defektów (jakość wyrobów nie jest sprawdzana przez odbiorców) „Luźniejsza” specyfikacja materiałowa umożliwiająca doskonalenie dostaw przez odbiorcę w zakresie jakości typu Niskie zapasy przy niezawodnym, „ciągłym” uzupełnianiu PWr/W 8/K 6 Zespół Logistyki i Zarządzania Projektami 72
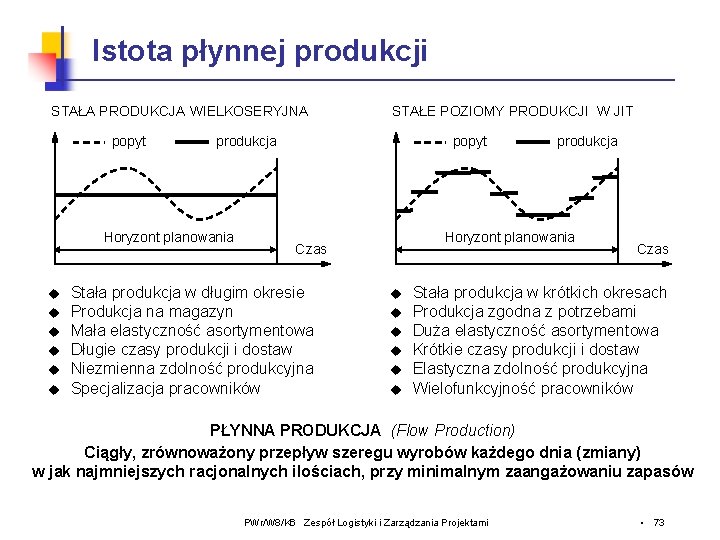
Istota płynnej produkcji STAŁA PRODUKCJA WIELKOSERYJNA popyt produkcja Horyzont planowania u u u STAŁE POZIOMY PRODUKCJI W JIT popyt Horyzont planowania Czas Stała produkcja w długim okresie Produkcja na magazyn Mała elastyczność asortymentowa Długie czasy produkcji i dostaw Niezmienna zdolność produkcyjna Specjalizacja pracowników produkcja u u u Czas Stała produkcja w krótkich okresach Produkcja zgodna z potrzebami Duża elastyczność asortymentowa Krótkie czasy produkcji i dostaw Elastyczna zdolność produkcyjna Wielofunkcyjność pracowników PŁYNNA PRODUKCJA (Flow Production) Ciągły, zrównoważony przepływ szeregu wyrobów każdego dnia (zmiany) w jak najmniejszych racjonalnych ilościach, przy minimalnym zaangażowaniu zapasów PWr/W 8/K 6 Zespół Logistyki i Zarządzania Projektami • 73
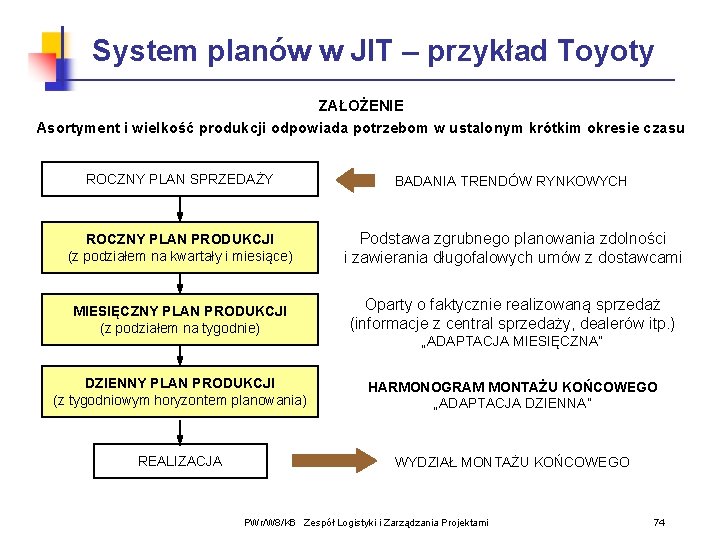
System planów w JIT – przykład Toyoty ZAŁOŻENIE Asortyment i wielkość produkcji odpowiada potrzebom w ustalonym krótkim okresie czasu ROCZNY PLAN SPRZEDAŻY BADANIA TRENDÓW RYNKOWYCH ROCZNY PLAN PRODUKCJI (z podziałem na kwartały i miesiące) Podstawa zgrubnego planowania zdolności i zawierania długofalowych umów z dostawcami MIESIĘCZNY PLAN PRODUKCJI (z podziałem na tygodnie) Oparty o faktycznie realizowaną sprzedaż (informacje z central sprzedaży, dealerów itp. ) DZIENNY PLAN PRODUKCJI (z tygodniowym horyzontem planowania) HARMONOGRAM MONTAŻU KOŃCOWEGO „ADAPTACJA DZIENNA” REALIZACJA WYDZIAŁ MONTAŻU KOŃCOWEGO „ADAPTACJA MIESIĘCZNA” PWr/W 8/K 6 Zespół Logistyki i Zarządzania Projektami 74
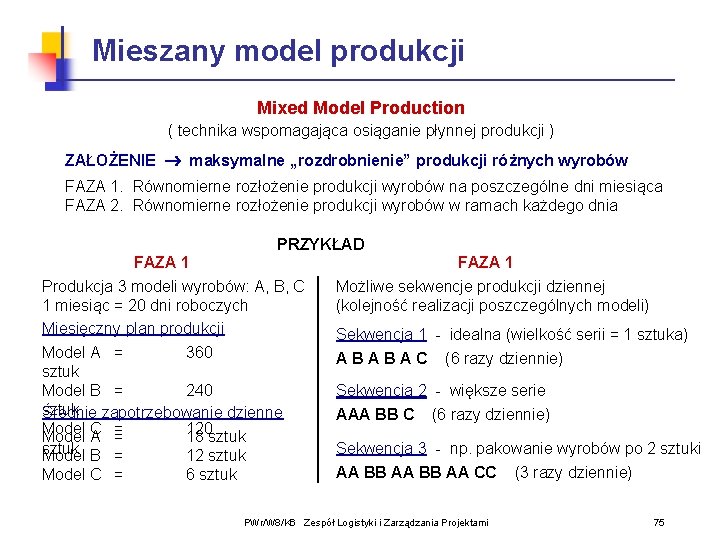
Mieszany model produkcji Mixed Model Production ( technika wspomagająca osiąganie płynnej produkcji ) ZAŁOŻENIE maksymalne „rozdrobnienie” produkcji różnych wyrobów FAZA 1. Równomierne rozłożenie produkcji wyrobów na poszczególne dni miesiąca FAZA 2. Równomierne rozłożenie produkcji wyrobów w ramach każdego dnia PRZYKŁAD FAZA 1 Produkcja 3 modeli wyrobów: A, B, C 1 miesiąc = 20 dni roboczych Miesięczny plan produkcji Model A = 360 sztuk Model B = 240 sztuk Średnie zapotrzebowanie dzienne Model 120 Model C A = = 18 sztuk Model B = 12 sztuk Model C = 6 sztuk FAZA 1 Możliwe sekwencje produkcji dziennej (kolejność realizacji poszczególnych modeli) Sekwencja 1 - idealna (wielkość serii = 1 sztuka) A B A C (6 razy dziennie) Sekwencja 2 - większe serie AAA BB C (6 razy dziennie) Sekwencja 3 - np. pakowanie wyrobów po 2 sztuki AA BB AA CC (3 razy dziennie) PWr/W 8/K 6 Zespół Logistyki i Zarządzania Projektami 75
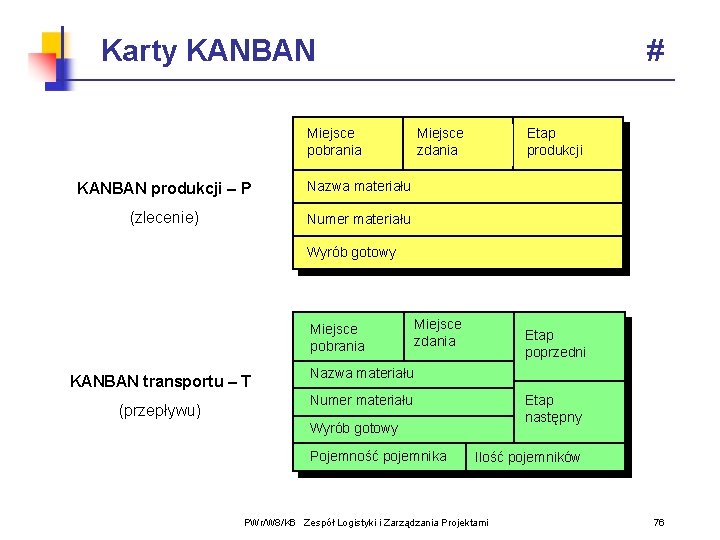
Karty KANBAN Miejsce pobrania KANBAN produkcji – P Nazwa materiału (zlecenie) Numer materiału # Miejsce zdania Etap produkcji Wyrób gotowy Miejsce pobrania KANBAN transportu – T (przepływu) Miejsce zdania Etap poprzedni Nazwa materiału Etap następny Numer materiału Wyrób gotowy Pojemność pojemnika Ilość pojemników PWr/W 8/K 6 Zespół Logistyki i Zarządzania Projektami 76
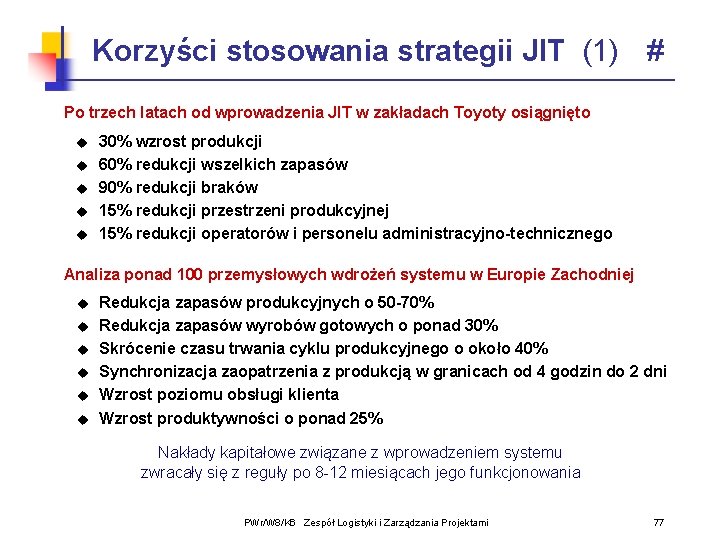
Korzyści stosowania strategii JIT (1) # Po trzech latach od wprowadzenia JIT w zakładach Toyoty osiągnięto u u u 30% wzrost produkcji 60% redukcji wszelkich zapasów 90% redukcji braków 15% redukcji przestrzeni produkcyjnej 15% redukcji operatorów i personelu administracyjno-technicznego Analiza ponad 100 przemysłowych wdrożeń systemu w Europie Zachodniej u u u Redukcja zapasów produkcyjnych o 50 -70% Redukcja zapasów wyrobów gotowych o ponad 30% Skrócenie czasu trwania cyklu produkcyjnego o około 40% Synchronizacja zaopatrzenia z produkcją w granicach od 4 godzin do 2 dni Wzrost poziomu obsługi klienta Wzrost produktywności o ponad 25% Nakłady kapitałowe związane z wprowadzeniem systemu zwracały się z reguły po 8 -12 miesiącach jego funkcjonowania PWr/W 8/K 6 Zespół Logistyki i Zarządzania Projektami 77
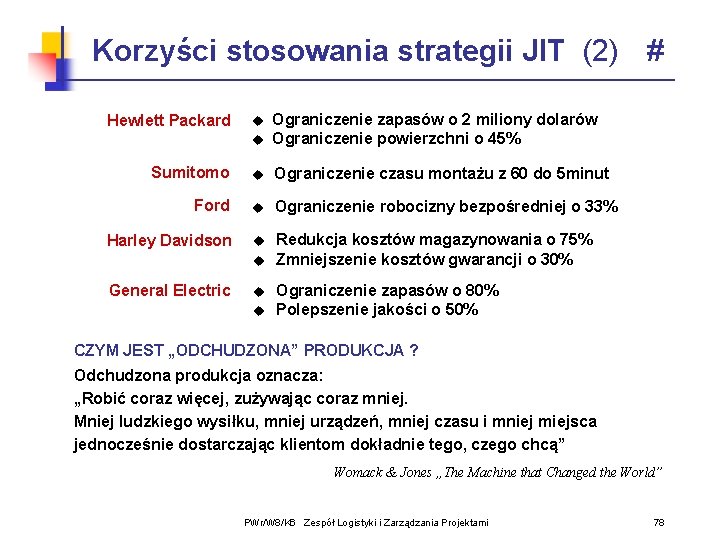
Korzyści stosowania strategii JIT (2) # u Ograniczenie zapasów o 2 miliony dolarów Ograniczenie powierzchni o 45% Sumitomo u Ograniczenie czasu montażu z 60 do 5 minut Ford u Ograniczenie robocizny bezpośredniej o 33% Harley Davidson u Redukcja kosztów magazynowania o 75% Zmniejszenie kosztów gwarancji o 30% Hewlett Packard u u General Electric u u Ograniczenie zapasów o 80% Polepszenie jakości o 50% CZYM JEST „ODCHUDZONA” PRODUKCJA ? Odchudzona produkcja oznacza: „Robić coraz więcej, zużywając coraz mniej. Mniej ludzkiego wysiłku, mniej urządzeń, mniej czasu i mniej miejsca jednocześnie dostarczając klientom dokładnie tego, czego chcą” Womack & Jones „The Machine that Changed the World” PWr/W 8/K 6 Zespół Logistyki i Zarządzania Projektami 78
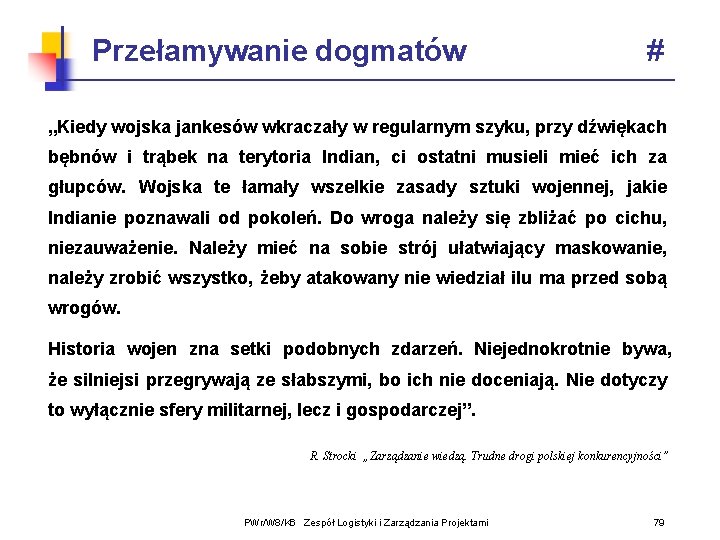
Przełamywanie dogmatów # „Kiedy wojska jankesów wkraczały w regularnym szyku, przy dźwiękach bębnów i trąbek na terytoria Indian, ci ostatni musieli mieć ich za głupców. Wojska te łamały wszelkie zasady sztuki wojennej, jakie Indianie poznawali od pokoleń. Do wroga należy się zbliżać po cichu, niezauważenie. Należy mieć na sobie strój ułatwiający maskowanie, należy zrobić wszystko, żeby atakowany nie wiedział ilu ma przed sobą wrogów. Historia wojen zna setki podobnych zdarzeń. Niejednokrotnie bywa, że silniejsi przegrywają ze słabszymi, bo ich nie doceniają. Nie dotyczy to wyłącznie sfery militarnej, lecz i gospodarczej”. R. Strocki „Zarządzanie wiedzą. Trudne drogi polskiej konkurencyjności” PWr/W 8/K 6 Zespół Logistyki i Zarządzania Projektami 79
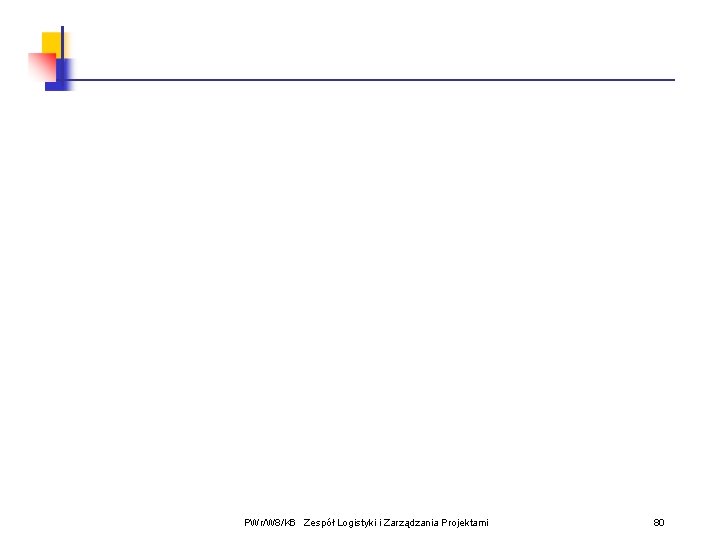
PWr/W 8/K 6 Zespół Logistyki i Zarządzania Projektami 80
Karta kanban
Teorietypu
Klasyczna teoria organizacji
Doua ape curgatoare din sydney
Magazynier bielizny w hotelu
"biznes plan"
Zakres pracy inżynierskiej przykład
Allianz poważne zachorowanie zakres podstawowy
Adcon electronics
Zakres stosowalności prawa hooke'a
Zakres niewiadomej pytania
Zakres tolerancji ekologicznej
Program zdrowie plus
Zakres pracy inżynierskiej przykład
Benefits of cpim certification
Frozen slushy liquid time fences
Apics operations management
Apics
Apics certification maintenance
Apics
Apics cpim learning system
Apics game
Apics adalah
Https //www.apics.org/tttwebinars
Apics membership renewal
Ejemplos de interogacion
Police alphabet code
Digimap for schools login
Usa.gov apps gallery
Mfccusa
Gucci legal counsel
Subsalve usa
Inclusive education in usa
Seasons in czech
Skills usa
Axel usa
Aco drains usa
Tabla de bonificaciones de amway usa
Aufstehen perfekt tense
Mountain ranges in the us
Rozloha usa
Open bim building smart
Egfe
Underspørgsmål engelsk
Skills usa emblem
Parrafo con signos de interrogacion y exclamacion
Allion usa
Orix usa corporation
Usajobs com
Akuo energy usa
Mellankrigstiden usa
Fox news misleading graphs
Banorte en usa
Tylft definisjon
What branch of the government makes treaties
Negativo presente
Nasirat usa
Usatestprep create account
Osmolality vs osmolarity
What makes a sonnet
Piramal glass usa
Usa patriot act pros and cons
Geographical position usa
Food waste usa
Webasap
Ipergeneralizzazione linguistica
Usa 1787
Vacations usa tours
Us longitude map
On the emblem, the hands represent the
Como se usan las comas
Preamble us constitution
Pro soccer us
Usa flood
Moda italia clothing
1 st president of usa
Usajobs vacancy question responses
Lions kidsight usa
Phone letter codes
Skills usa south dakota
Arlington regia