Workflow Optimization of Kennestone Sterile Processing Department Kennestone
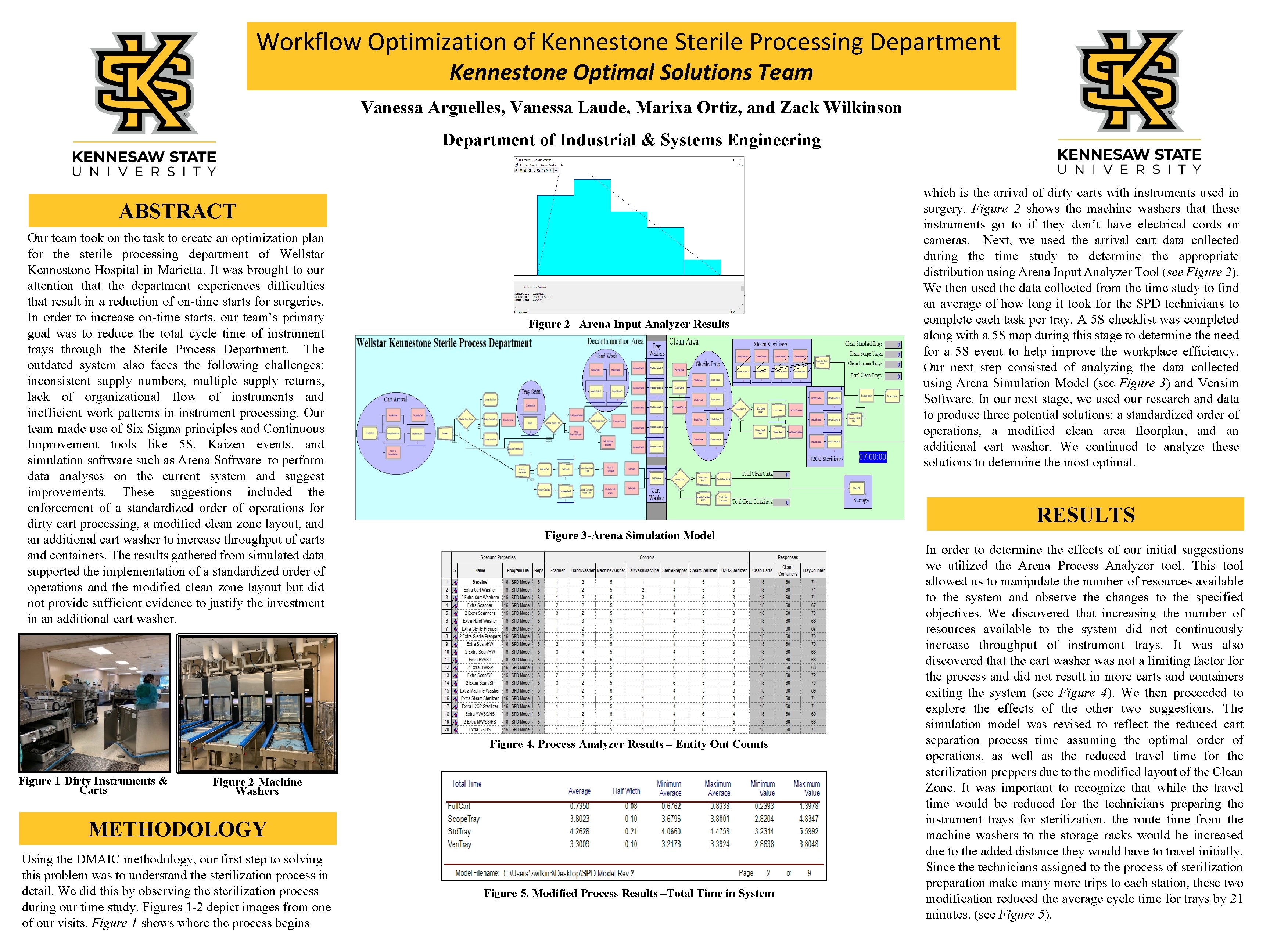
- Slides: 1
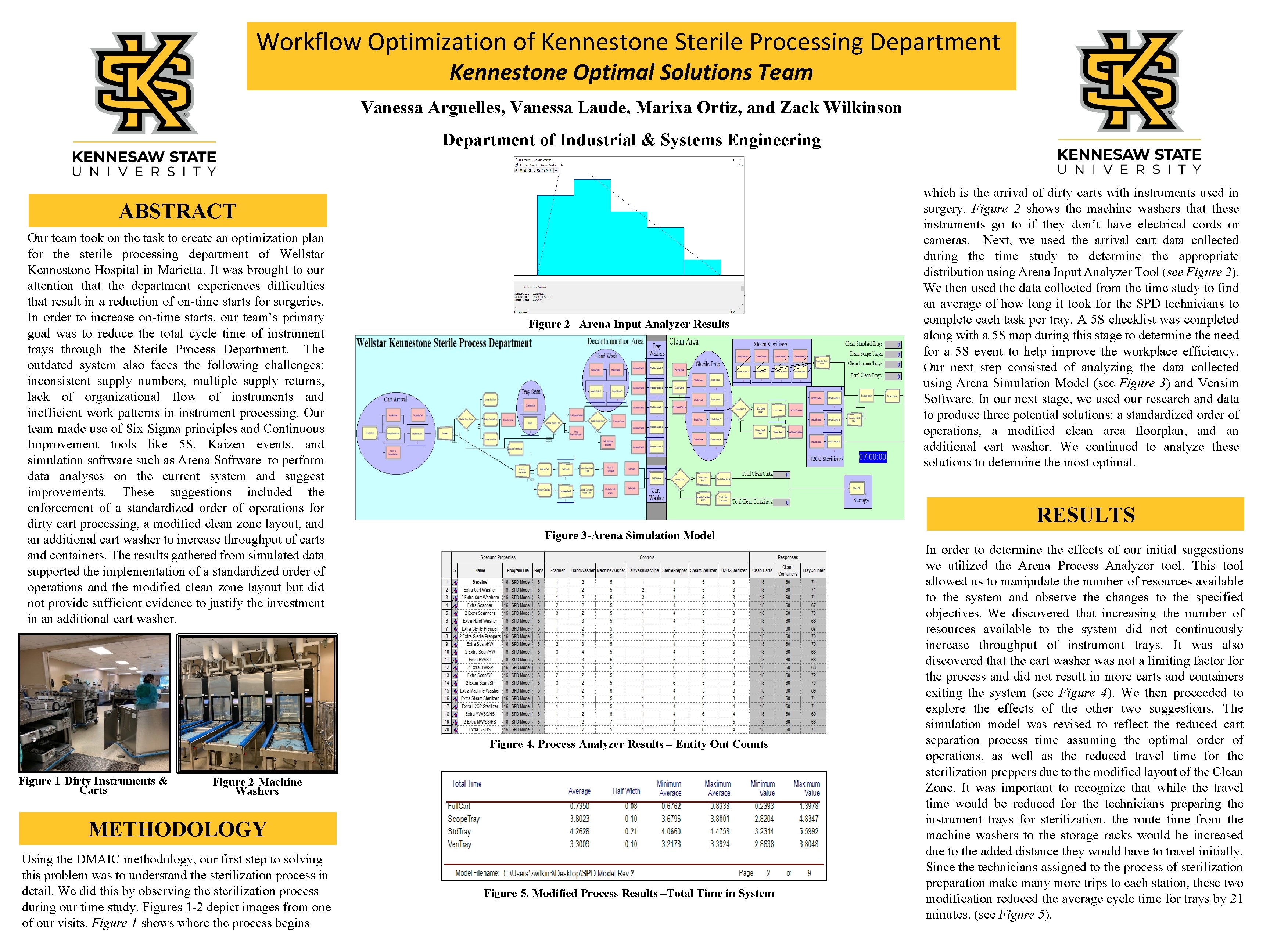
Workflow Optimization of Kennestone Sterile Processing Department Kennestone Optimal Solutions Team Vanessa Arguelles, Vanessa Laude, Marixa Ortiz, and Zack Wilkinson Department of Industrial & Systems Engineering ABSTRACT Our team took on the task to create an optimization plan for the sterile processing department of Wellstar Kennestone Hospital in Marietta. It was brought to our attention that the department experiences difficulties that result in a reduction of on-time starts for surgeries. In order to increase on-time starts, our team’s primary goal was to reduce the total cycle time of instrument trays through the Sterile Process Department. The outdated system also faces the following challenges: inconsistent supply numbers, multiple supply returns, lack of organizational flow of instruments and inefficient work patterns in instrument processing. Our team made use of Six Sigma principles and Continuous Improvement tools like 5 S, Kaizen events, and simulation software such as Arena Software to perform data analyses on the current system and suggest improvements. These suggestions included the enforcement of a standardized order of operations for dirty cart processing, a modified clean zone layout, and an additional cart washer to increase throughput of carts and containers. The results gathered from simulated data supported the implementation of a standardized order of operations and the modified clean zone layout but did not provide sufficient evidence to justify the investment in an additional cart washer. Figure 2– Arena Input Analyzer Results RESULTS Figure 3 -Arena Simulation Model Figure 4. Process Analyzer Results – Entity Out Counts Figure 1 -Dirty Instruments & Carts Figure 2 -Machine Washers METHODOLOGY Using the DMAIC methodology, our first step to solving this problem was to understand the sterilization process in detail. We did this by observing the sterilization process during our time study. Figures 1 -2 depict images from one of our visits. Figure 1 shows where the process begins which is the arrival of dirty carts with instruments used in surgery. Figure 2 shows the machine washers that these instruments go to if they don’t have electrical cords or cameras. Next, we used the arrival cart data collected during the time study to determine the appropriate distribution using Arena Input Analyzer Tool (see Figure 2). We then used the data collected from the time study to find an average of how long it took for the SPD technicians to complete each task per tray. A 5 S checklist was completed along with a 5 S map during this stage to determine the need for a 5 S event to help improve the workplace efficiency. Our next step consisted of analyzing the data collected using Arena Simulation Model (see Figure 3) and Vensim Software. In our next stage, we used our research and data to produce three potential solutions: a standardized order of operations, a modified clean area floorplan, and an additional cart washer. We continued to analyze these solutions to determine the most optimal. Figure 5. Modified Process Results –Total Time in System In order to determine the effects of our initial suggestions we utilized the Arena Process Analyzer tool. This tool allowed us to manipulate the number of resources available to the system and observe the changes to the specified objectives. We discovered that increasing the number of resources available to the system did not continuously increase throughput of instrument trays. It was also discovered that the cart washer was not a limiting factor for the process and did not result in more carts and containers exiting the system (see Figure 4). We then proceeded to explore the effects of the other two suggestions. The simulation model was revised to reflect the reduced cart separation process time assuming the optimal order of operations, as well as the reduced travel time for the sterilization preppers due to the modified layout of the Clean Zone. It was important to recognize that while the travel time would be reduced for the technicians preparing the instrument trays for sterilization, the route time from the machine washers to the storage racks would be increased due to the added distance they would have to travel initially. Since the technicians assigned to the process of sterilization preparation make many more trips to each station, these two modification reduced the average cycle time for trays by 21 minutes. (see Figure 5).