Unit3 Power converters 3 1 Polyphase rectifier Single
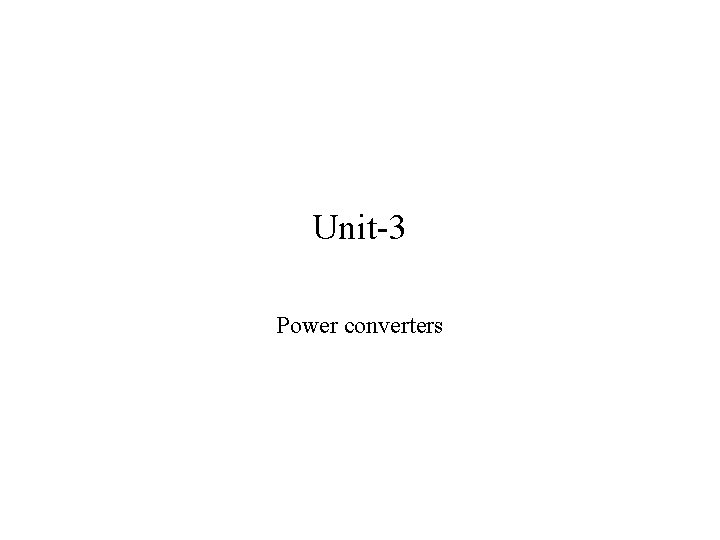
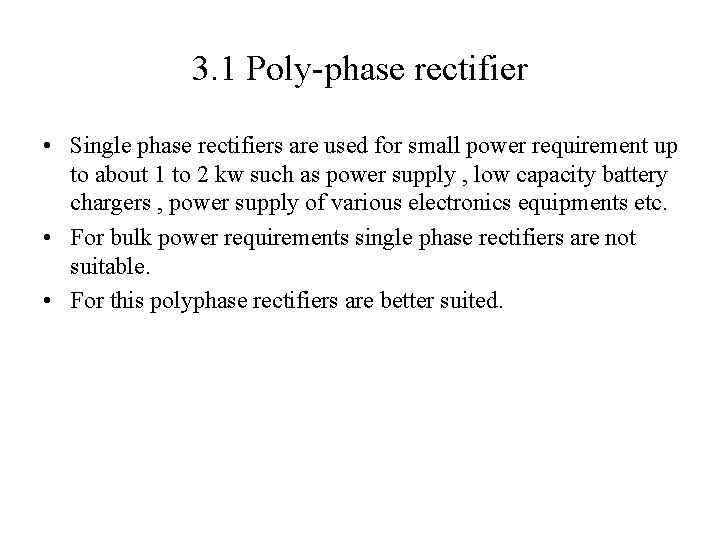
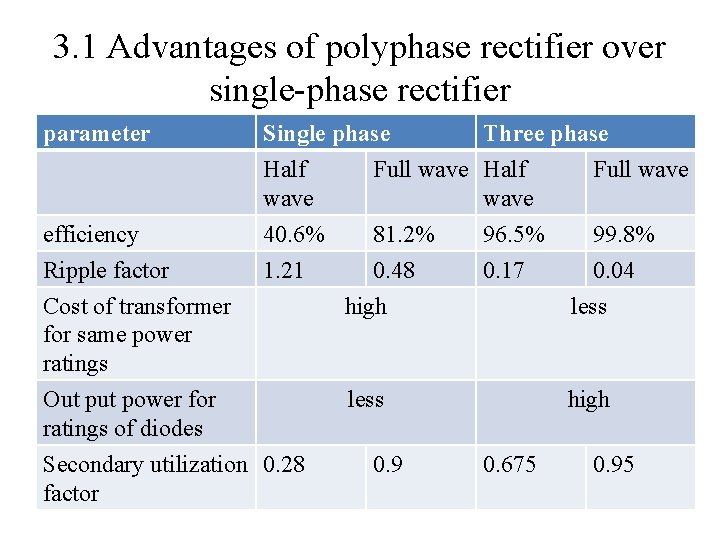
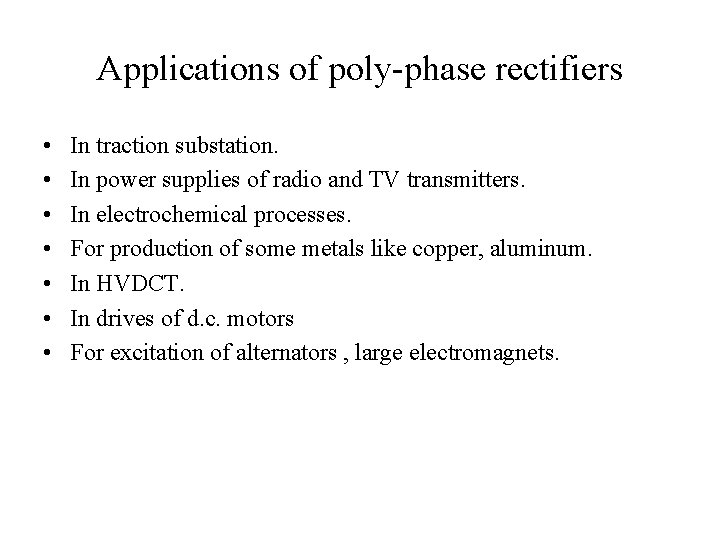
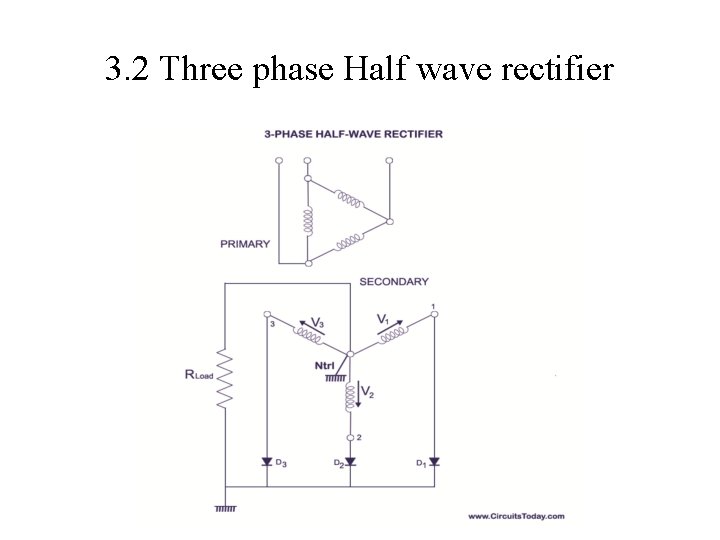
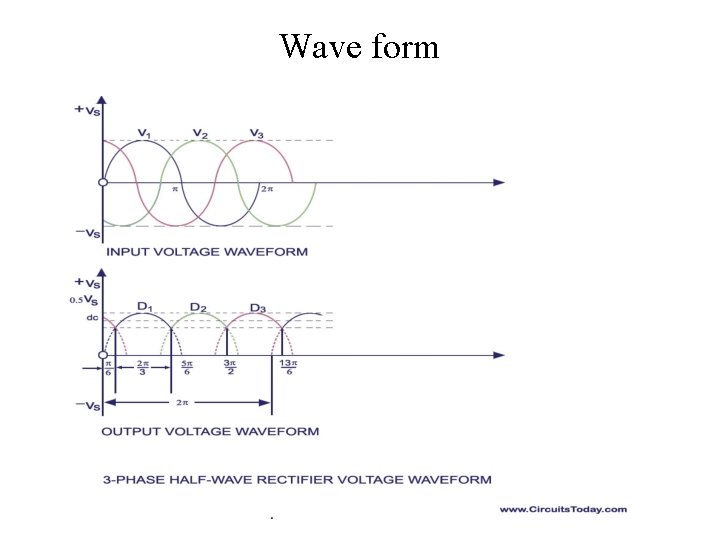
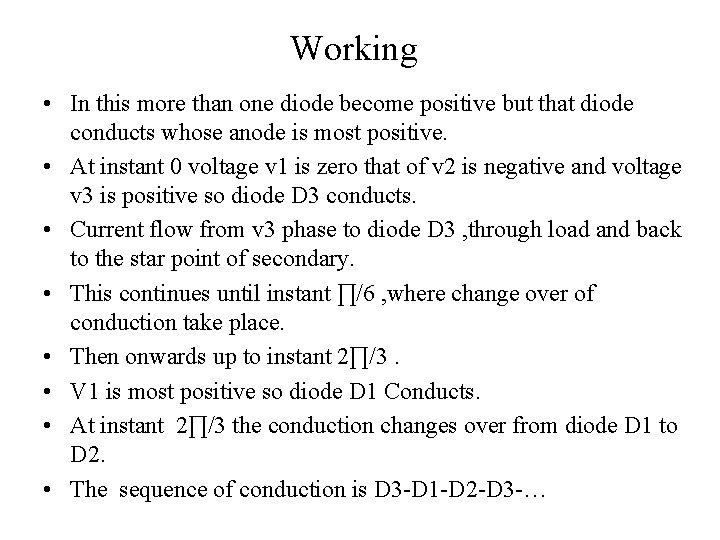
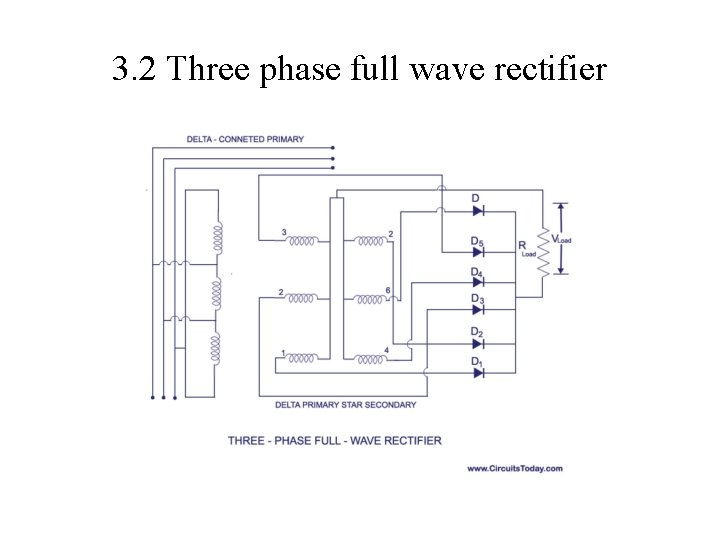
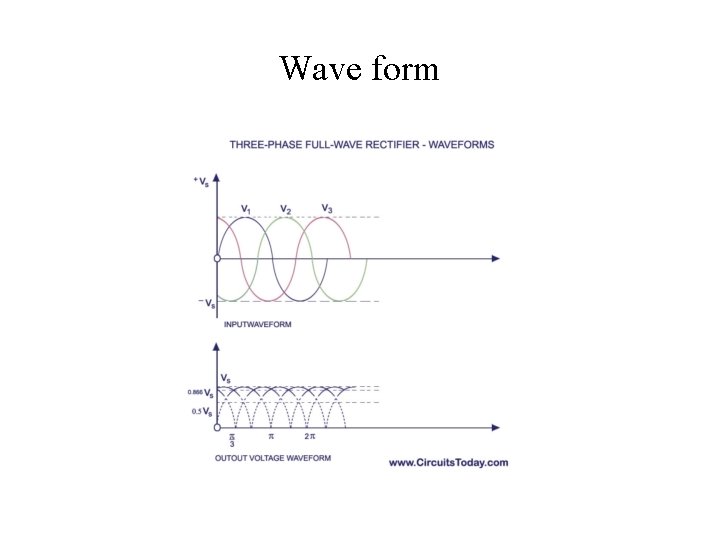
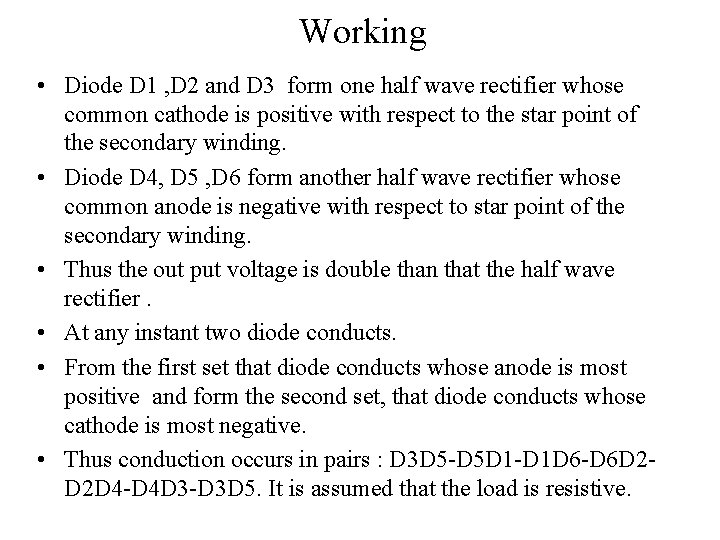
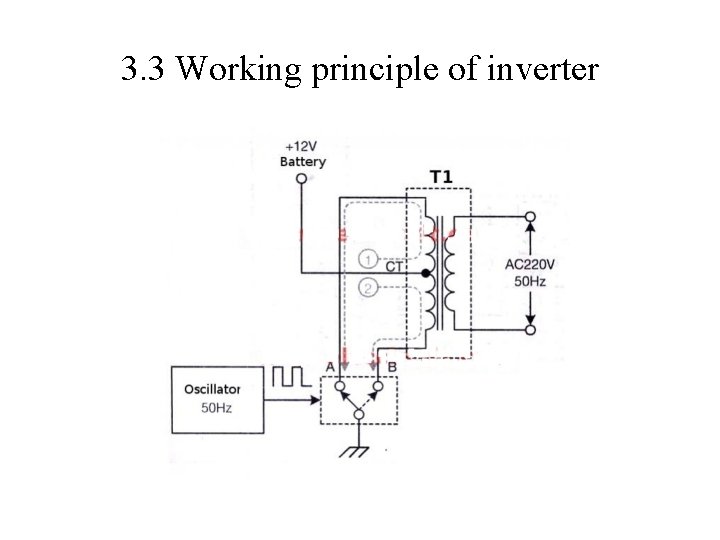
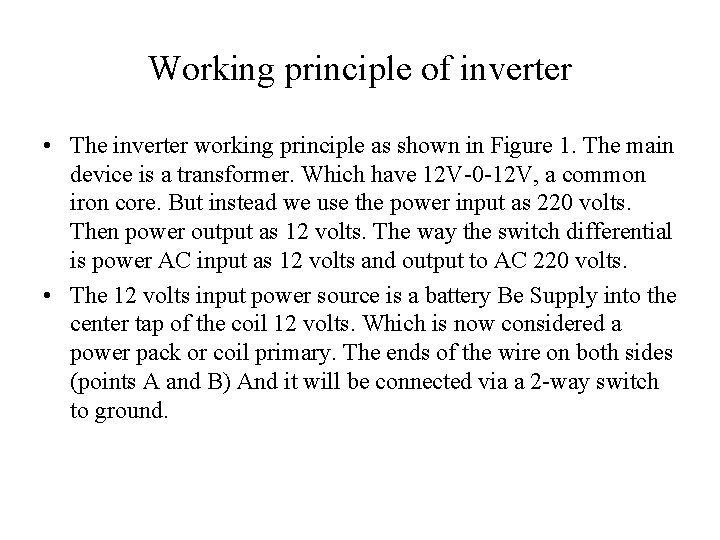
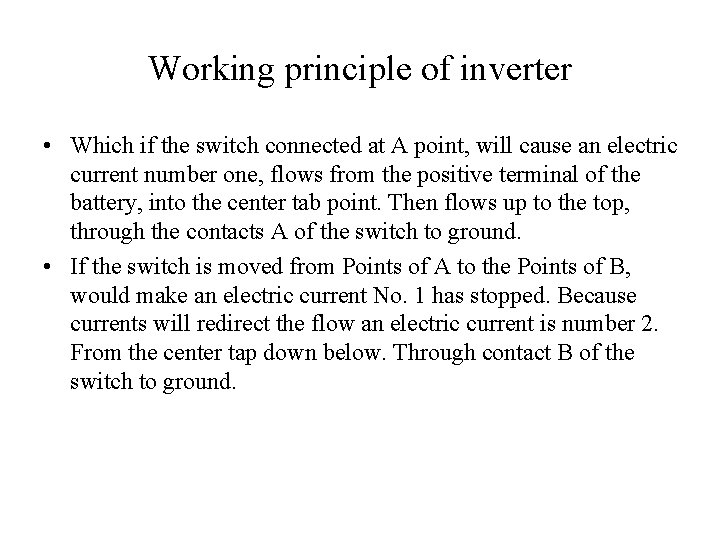
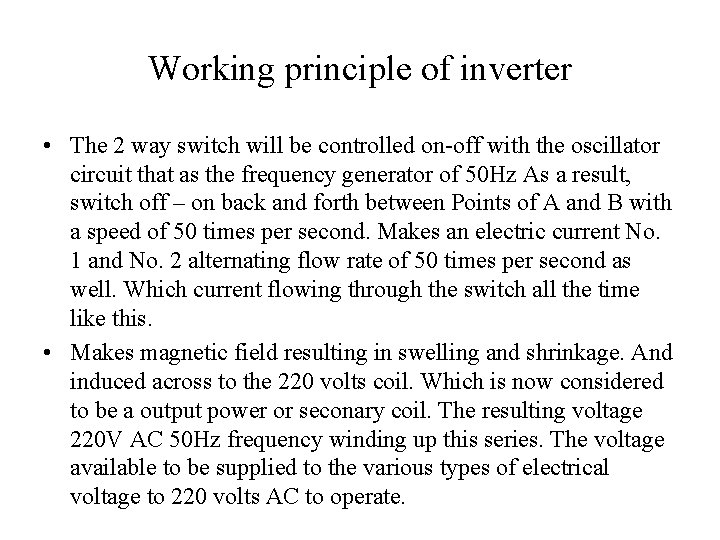
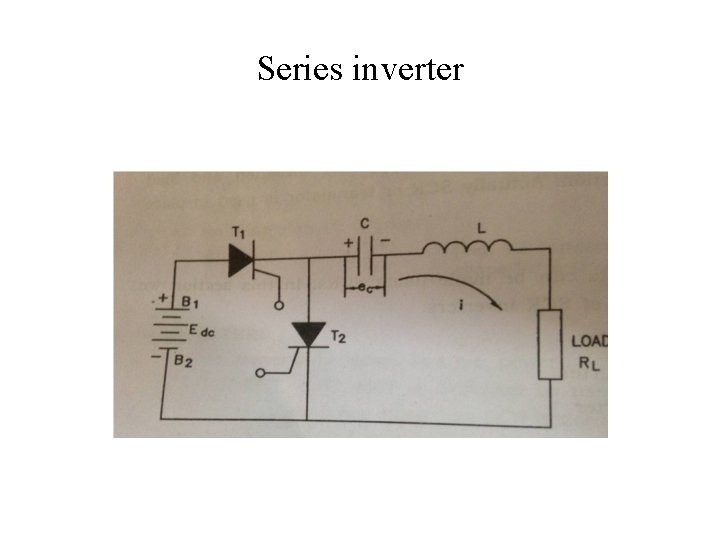
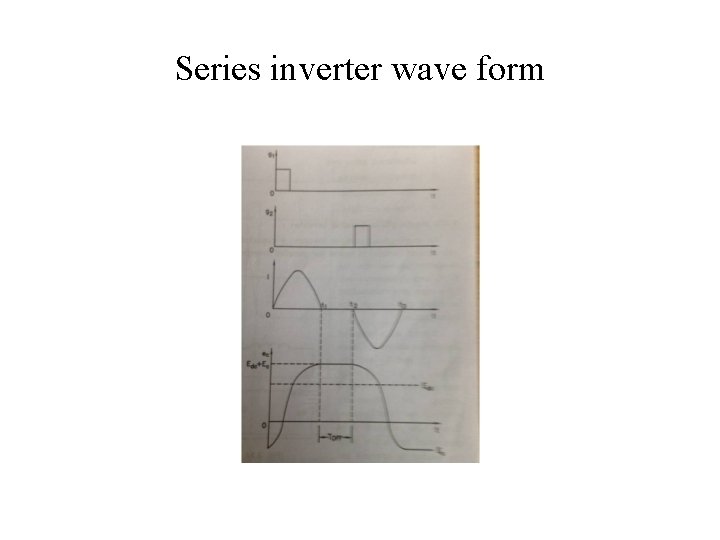
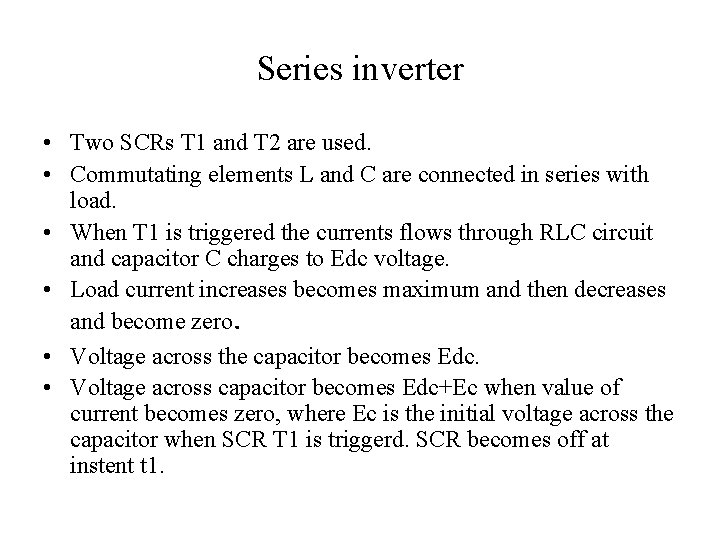
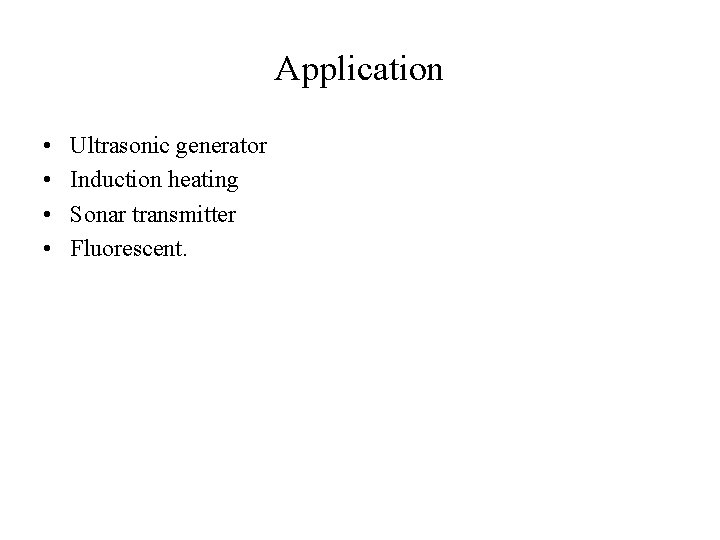
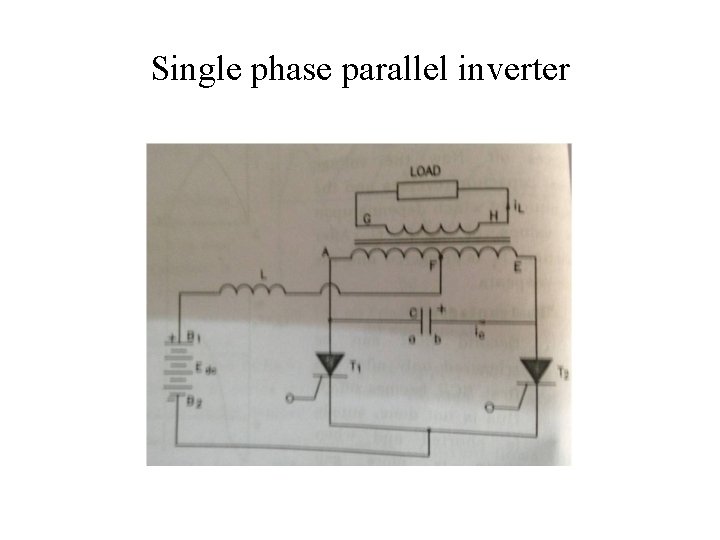
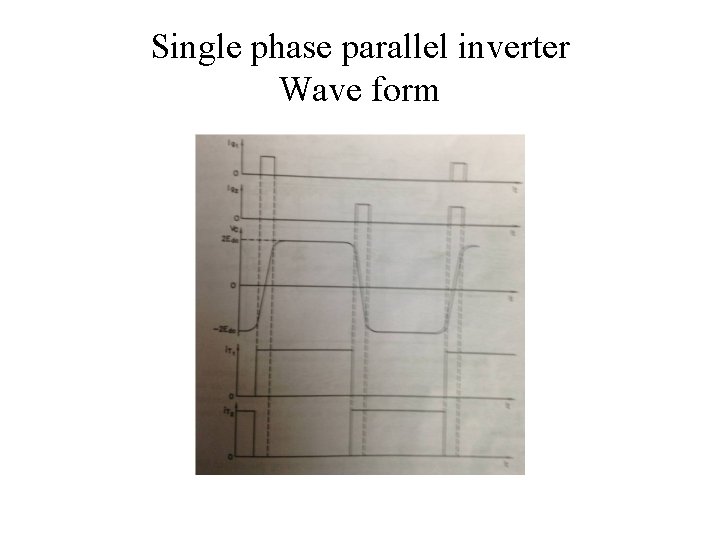
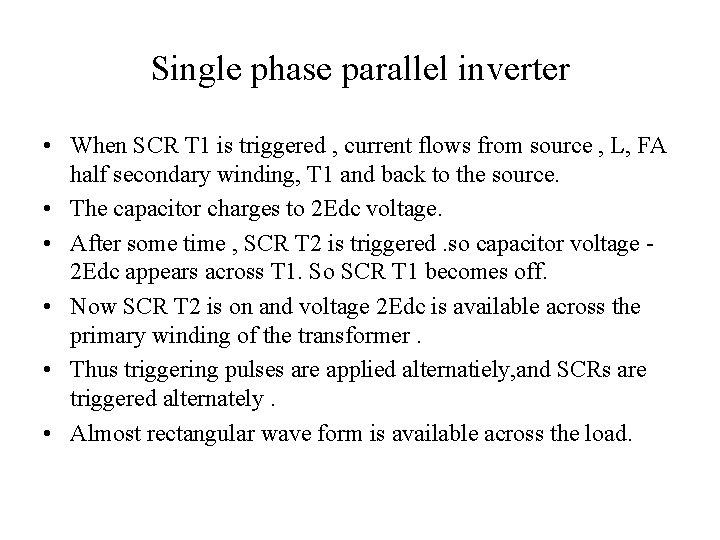
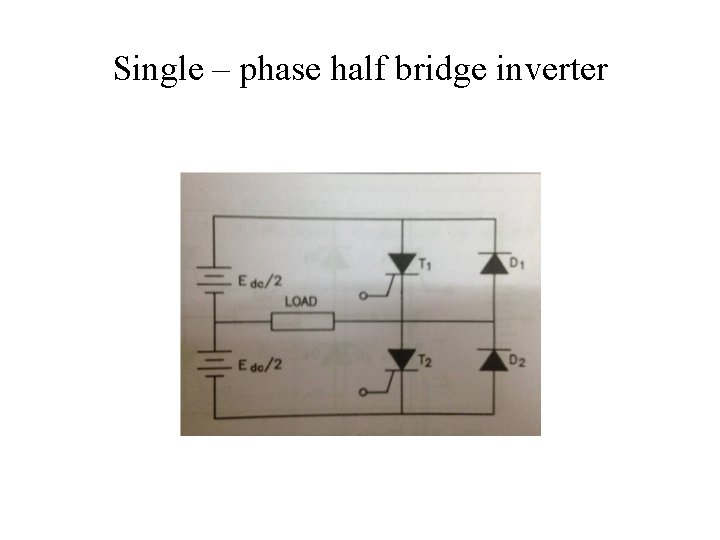
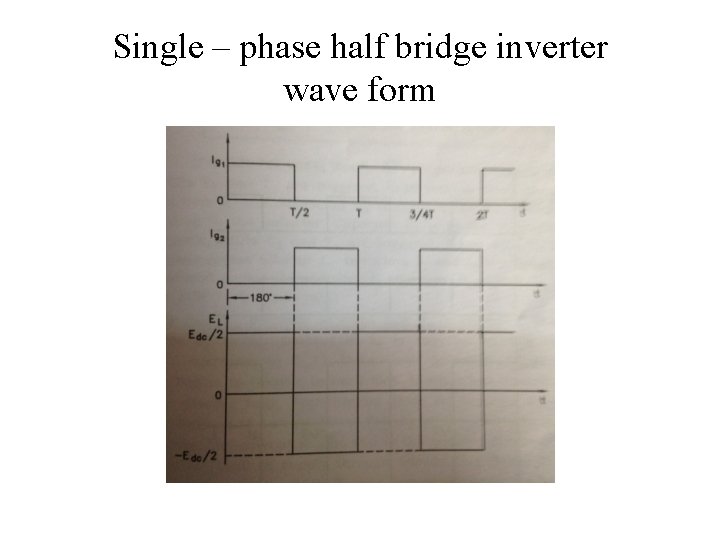
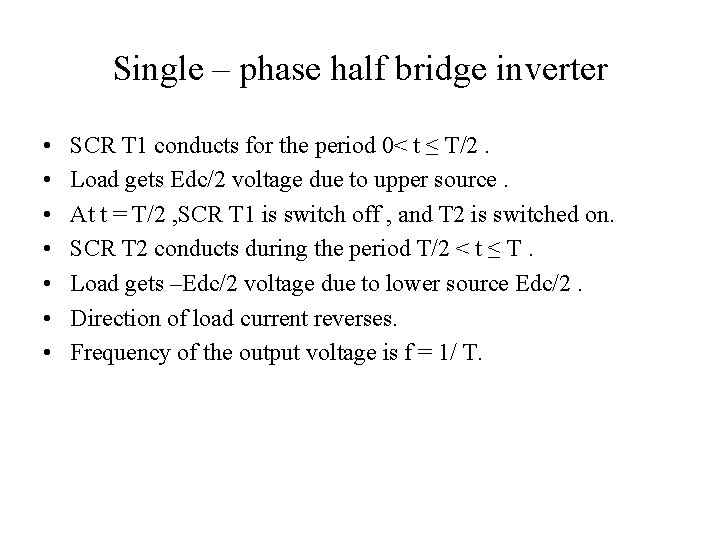
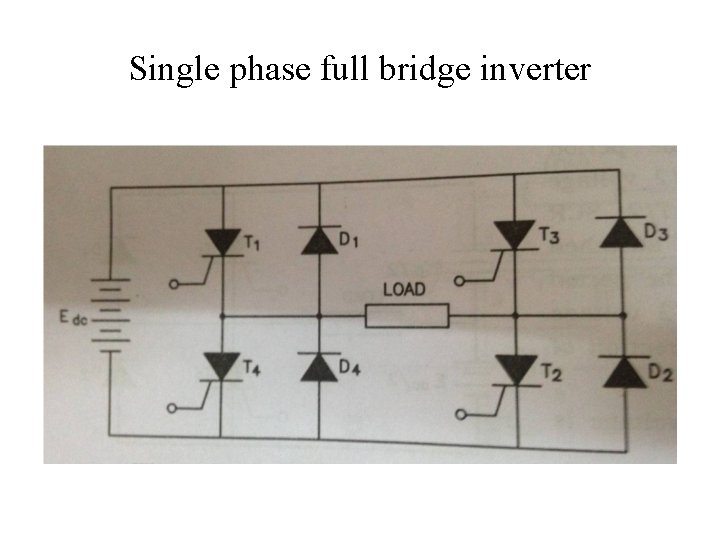
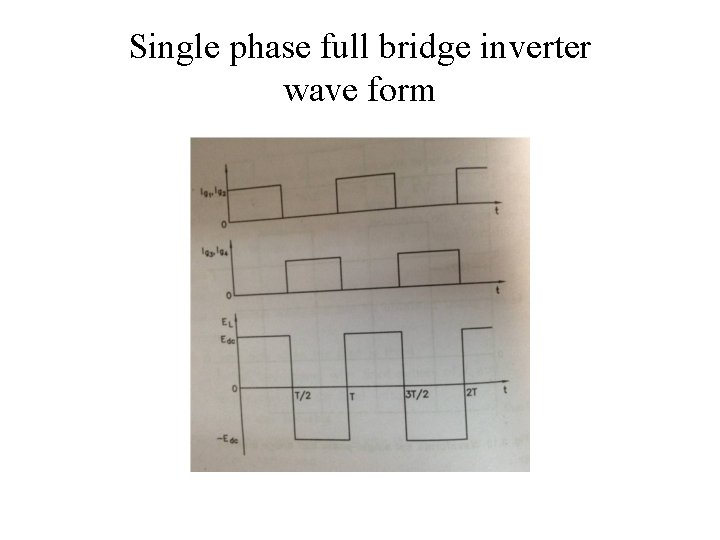
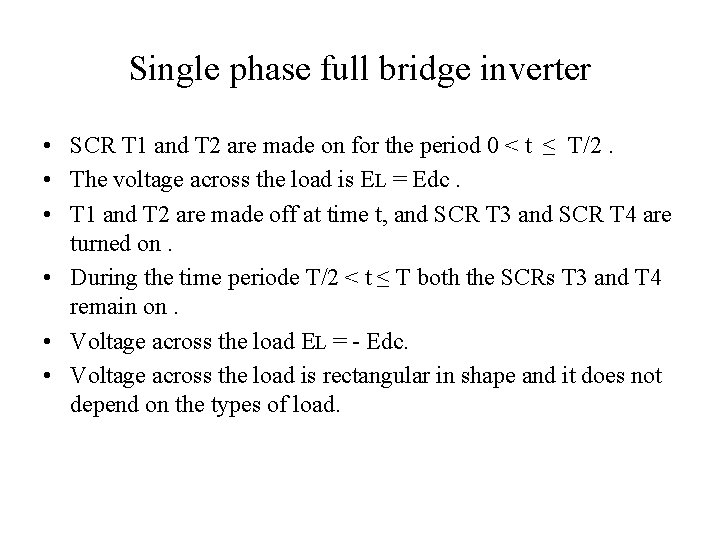
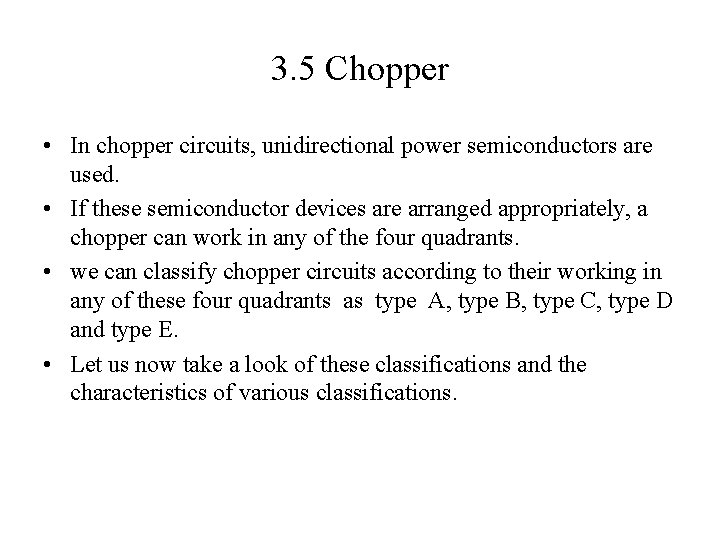
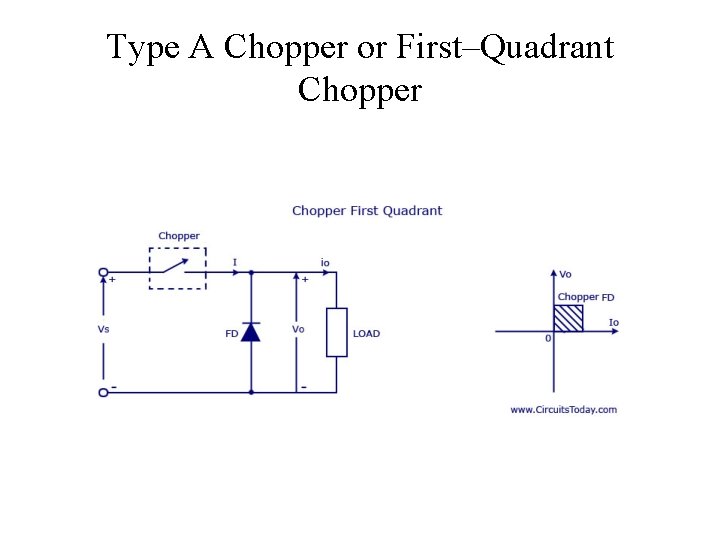
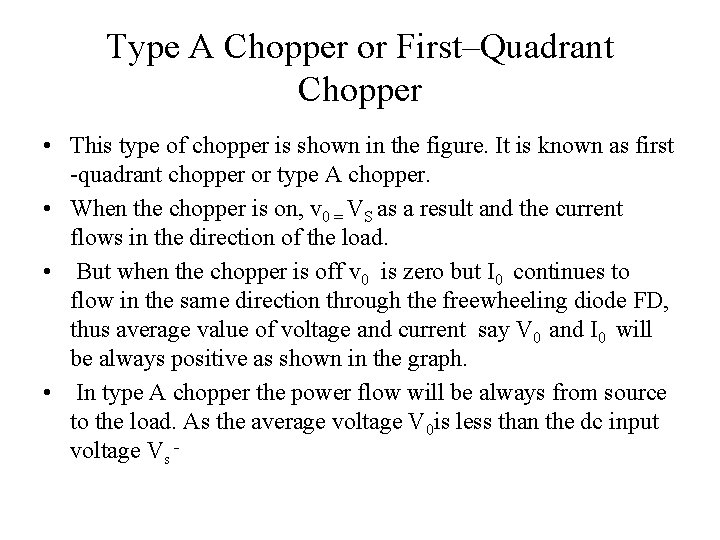
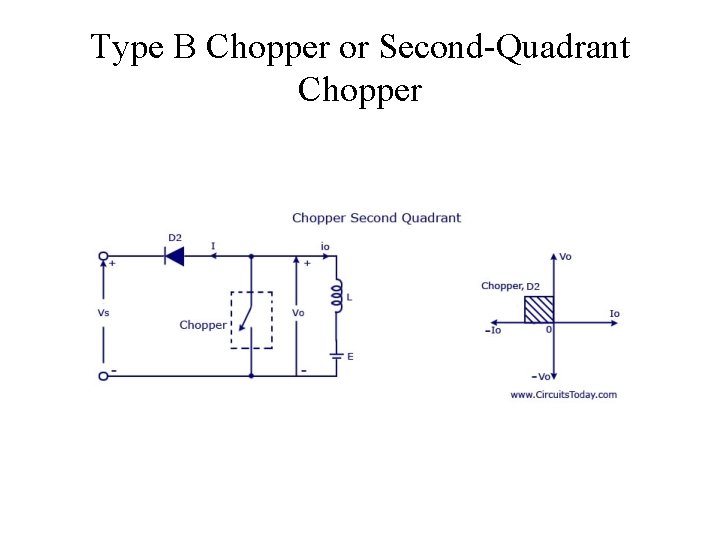
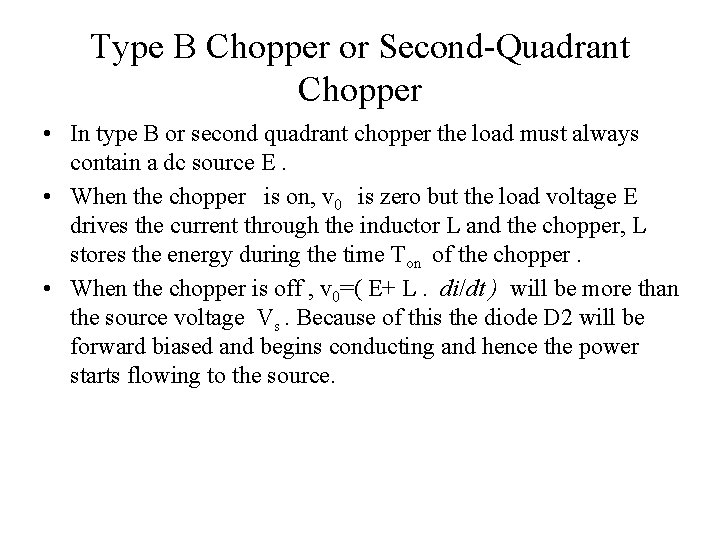
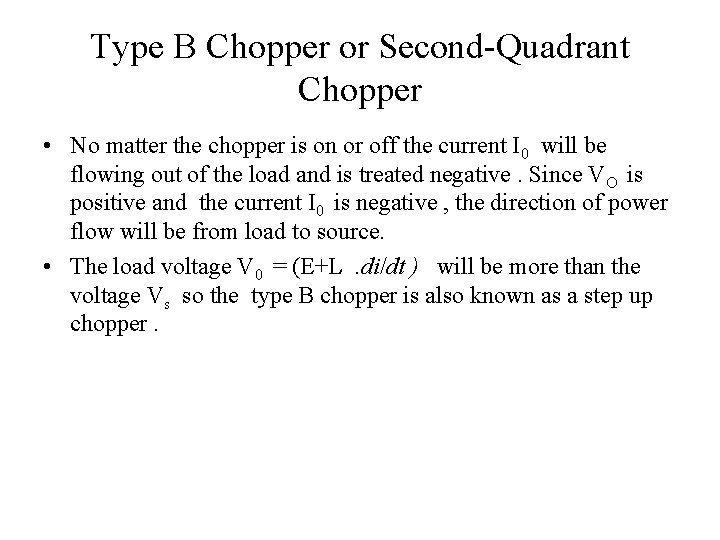
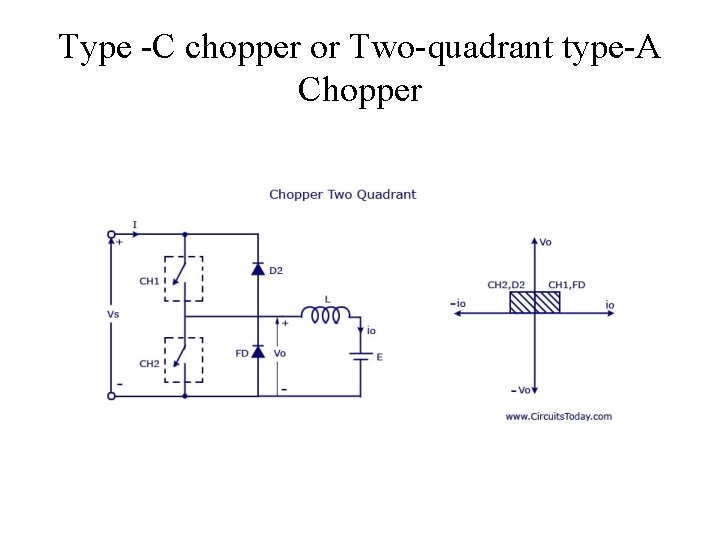
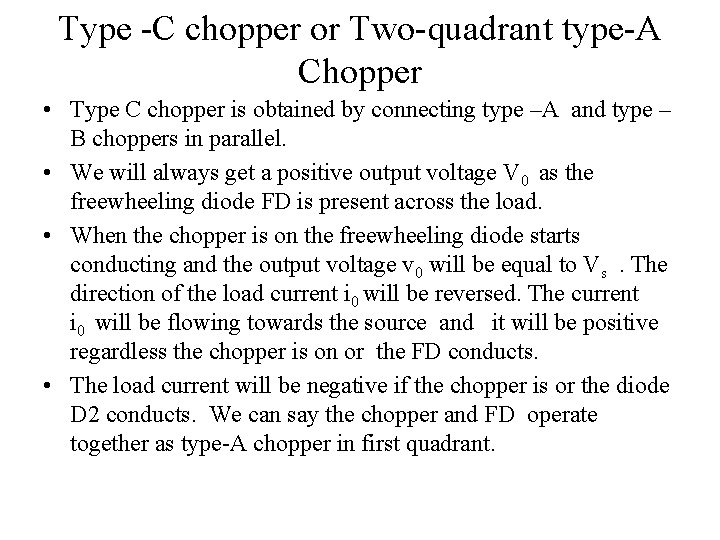
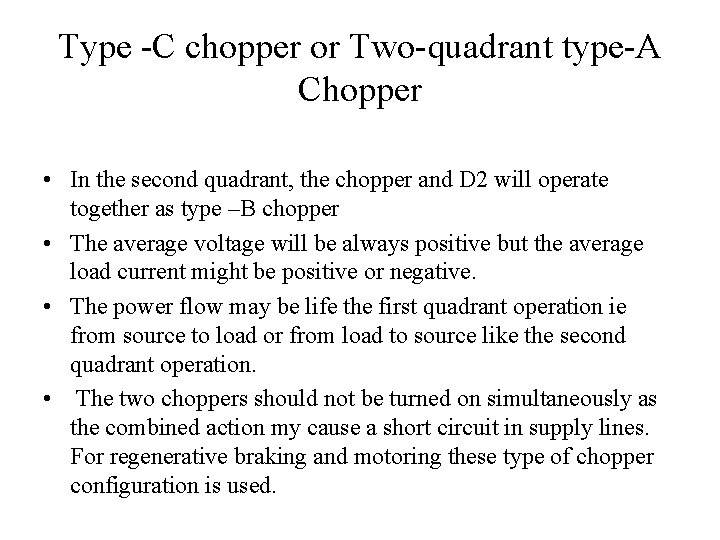
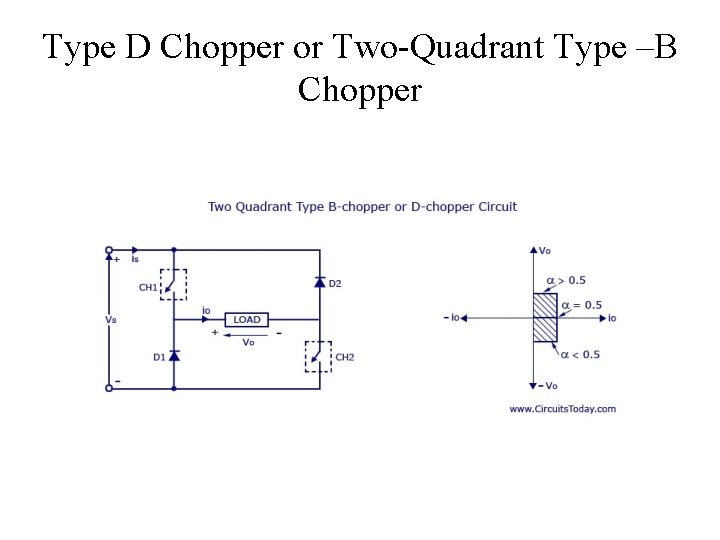
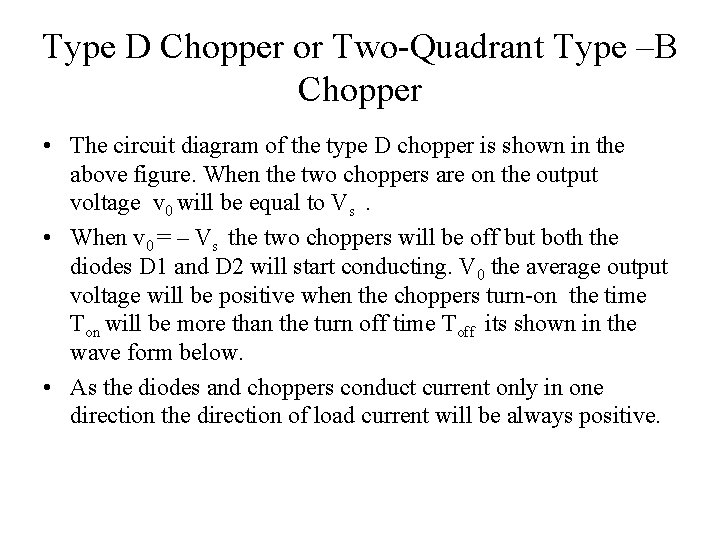
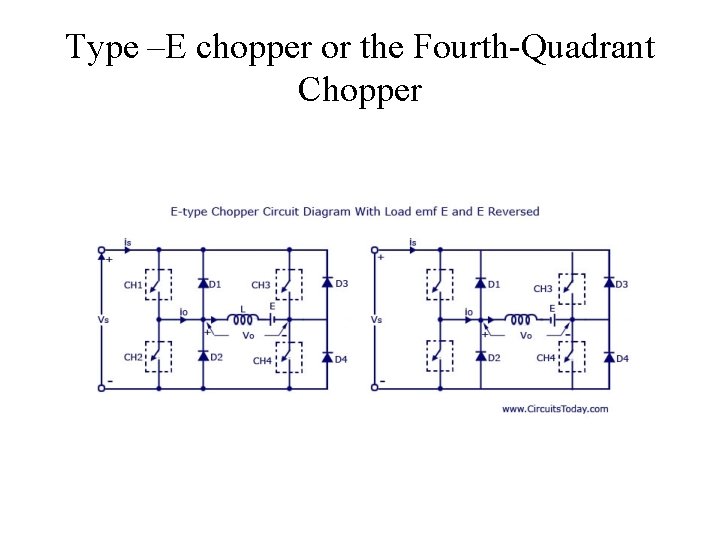
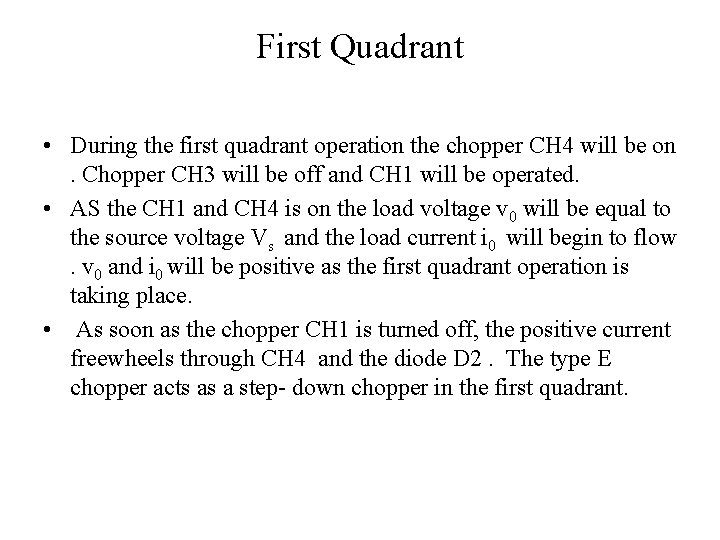
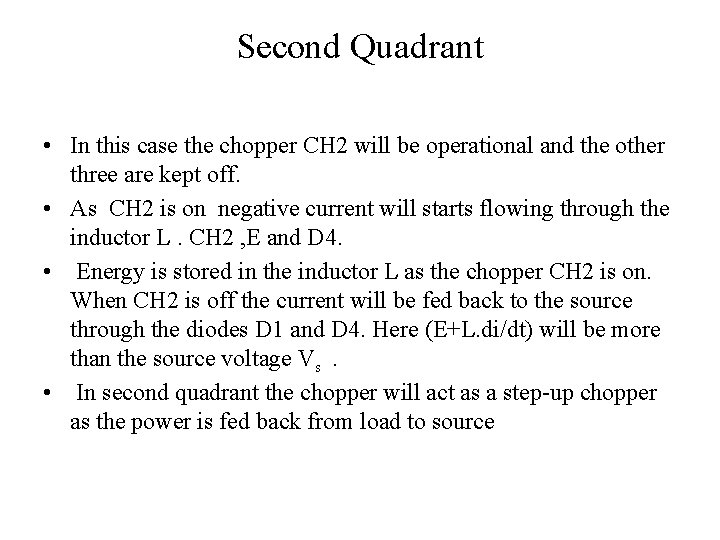
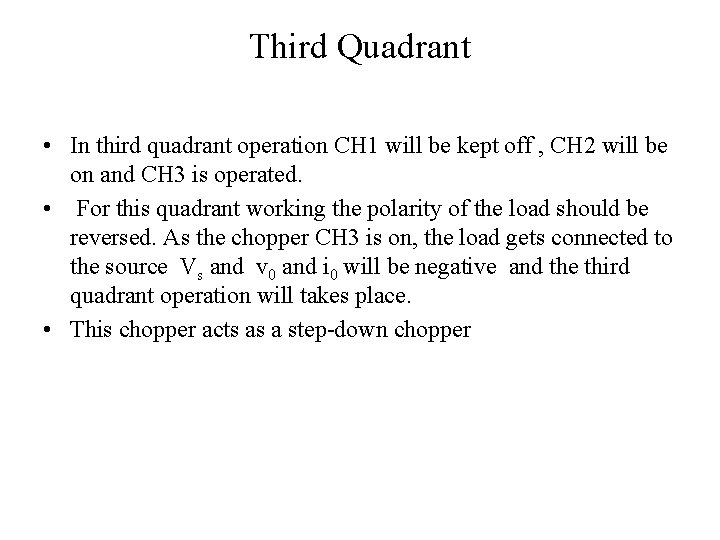
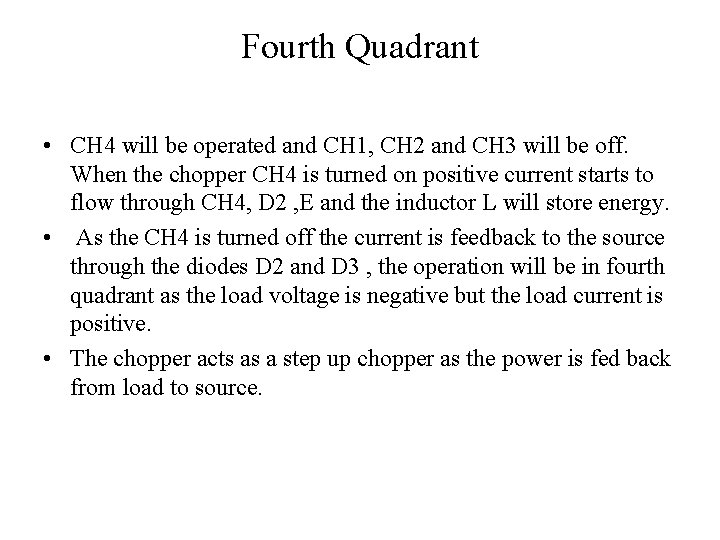
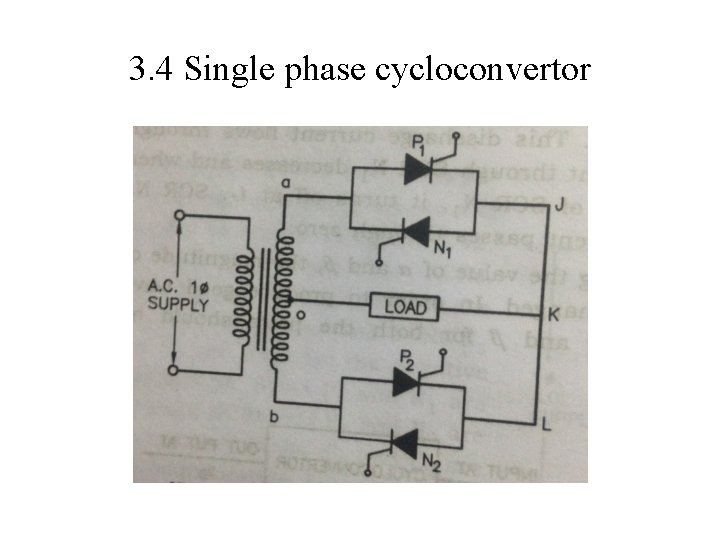
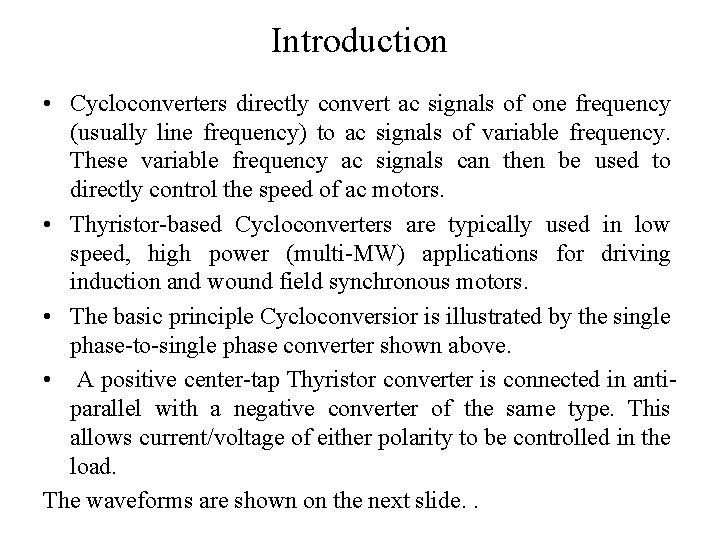
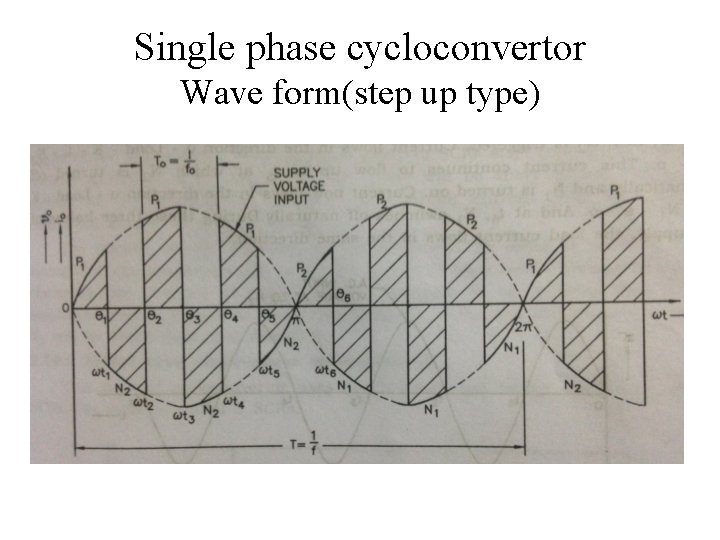
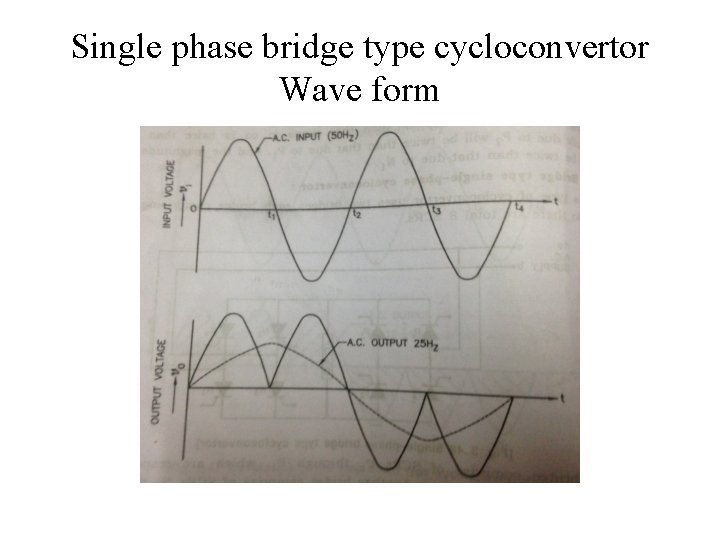
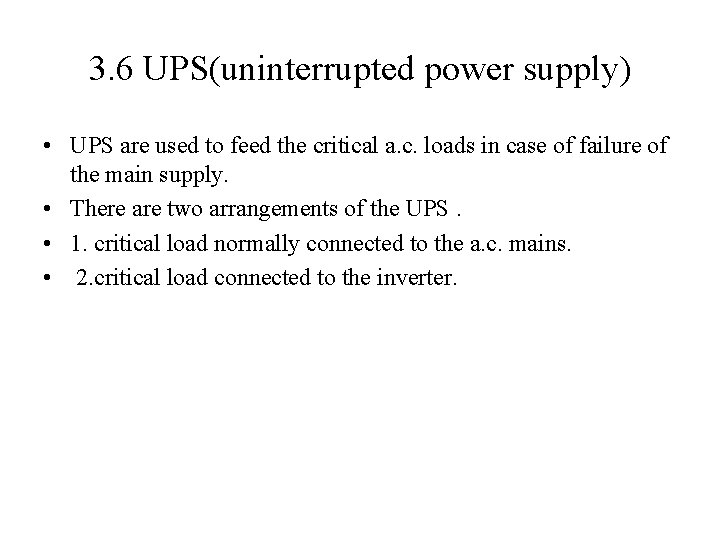
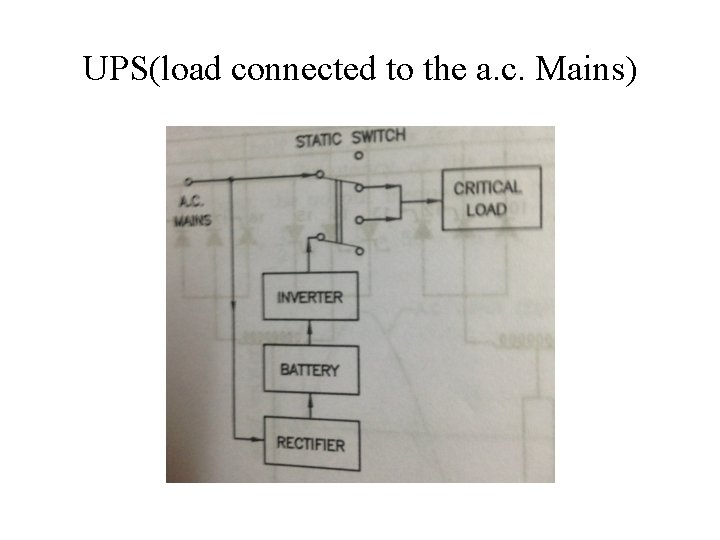
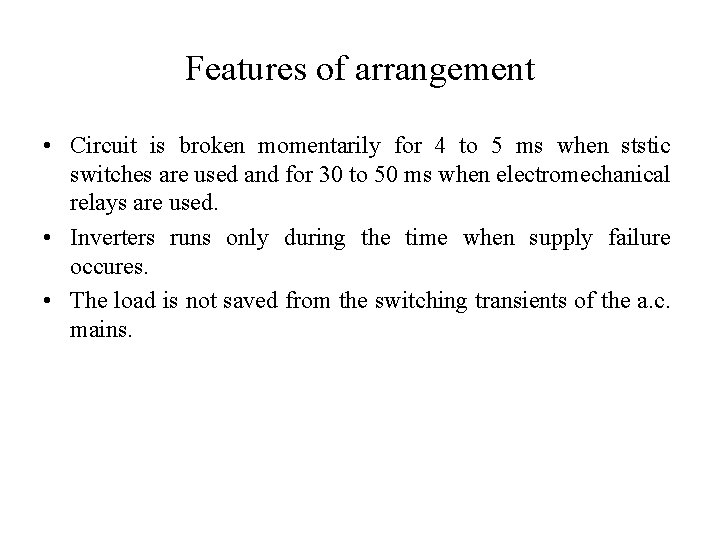
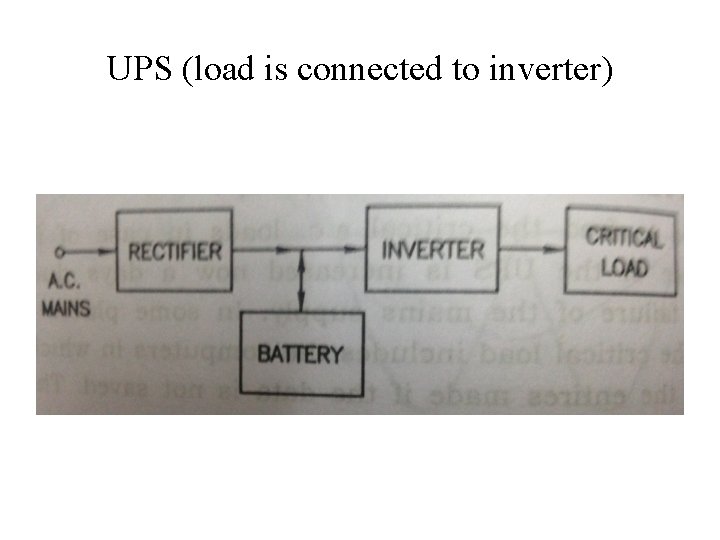
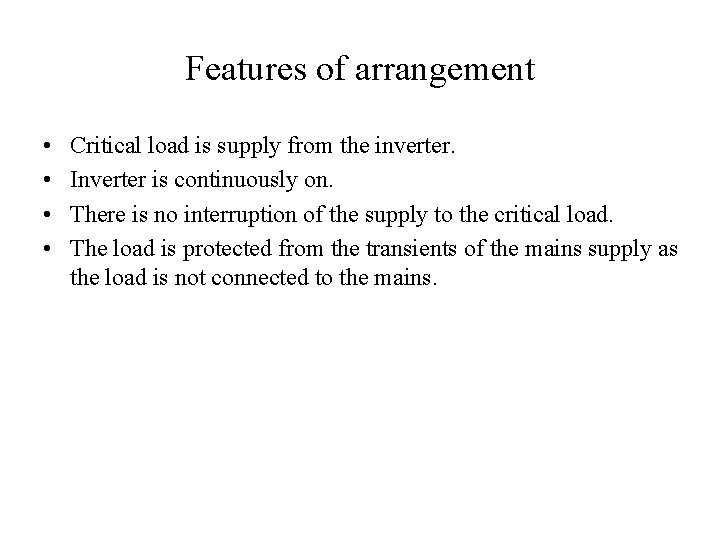
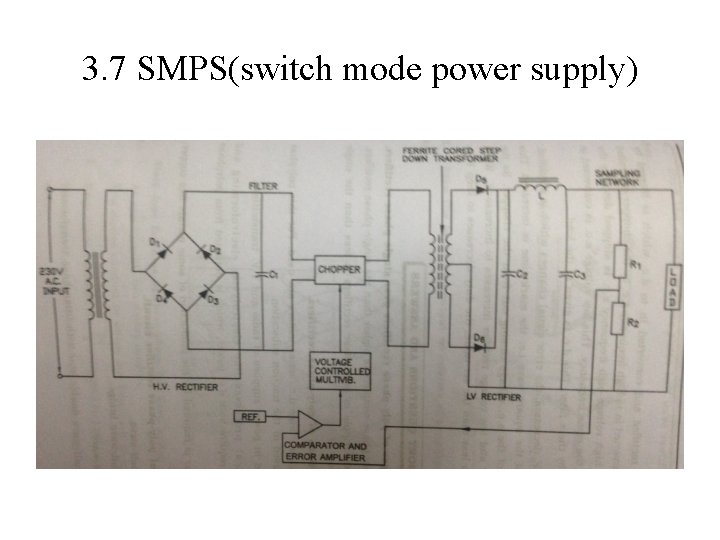
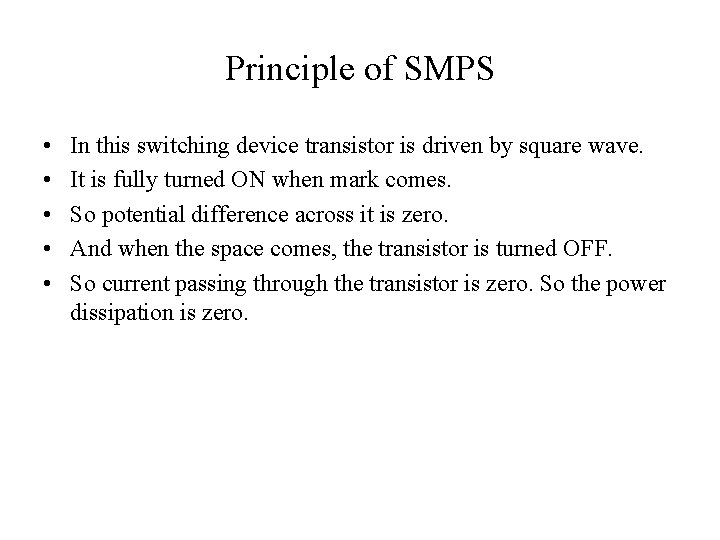
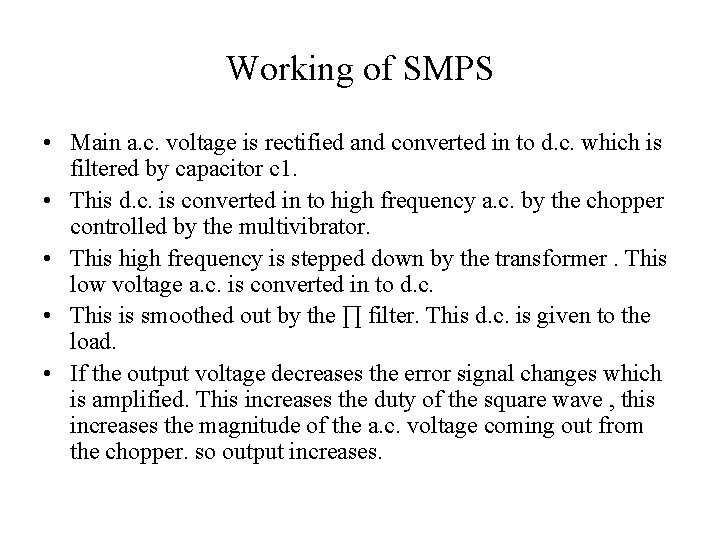
- Slides: 55
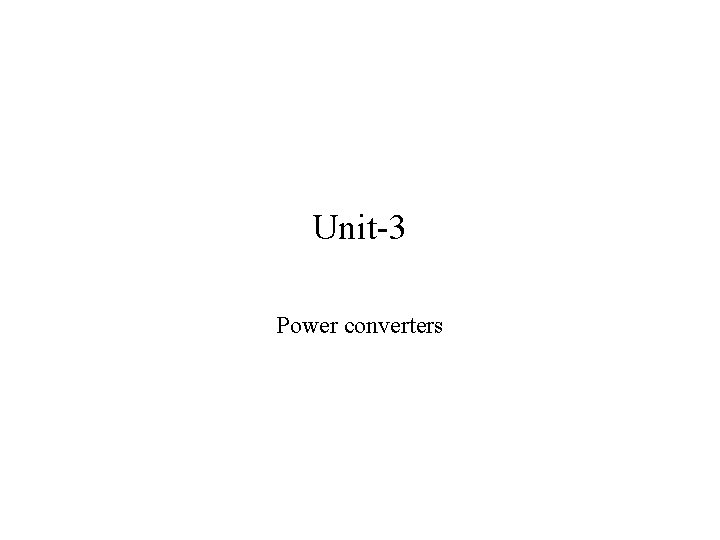
Unit-3 Power converters
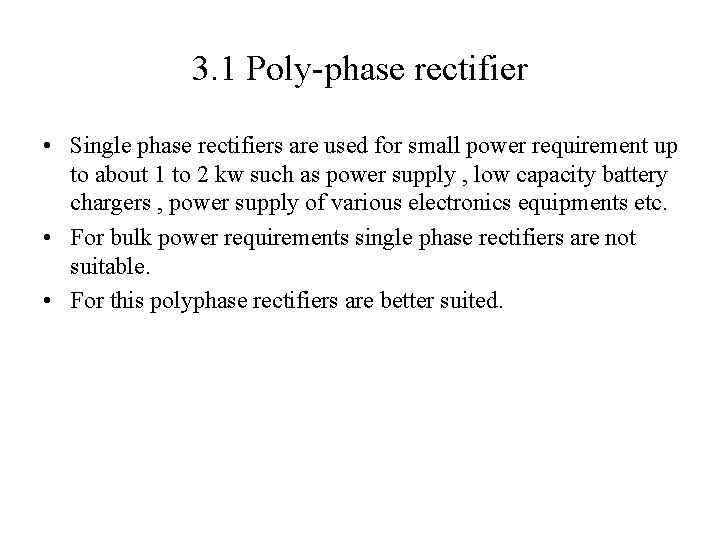
3. 1 Poly-phase rectifier • Single phase rectifiers are used for small power requirement up to about 1 to 2 kw such as power supply , low capacity battery chargers , power supply of various electronics equipments etc. • For bulk power requirements single phase rectifiers are not suitable. • For this polyphase rectifiers are better suited.
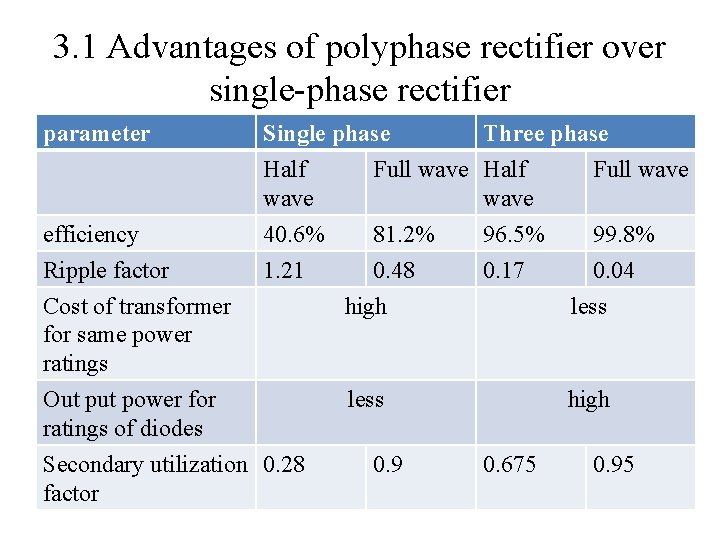
3. 1 Advantages of polyphase rectifier over single-phase rectifier parameter Single phase Three phase Half Full wave efficiency 40. 6% Ripple factor Cost of transformer for same power ratings 1. 21 Out power for ratings of diodes Secondary utilization 0. 28 factor 81. 2% 0. 48 high 96. 5% 0. 17 less 0. 9 99. 8% 0. 04 less high 0. 675 0. 95
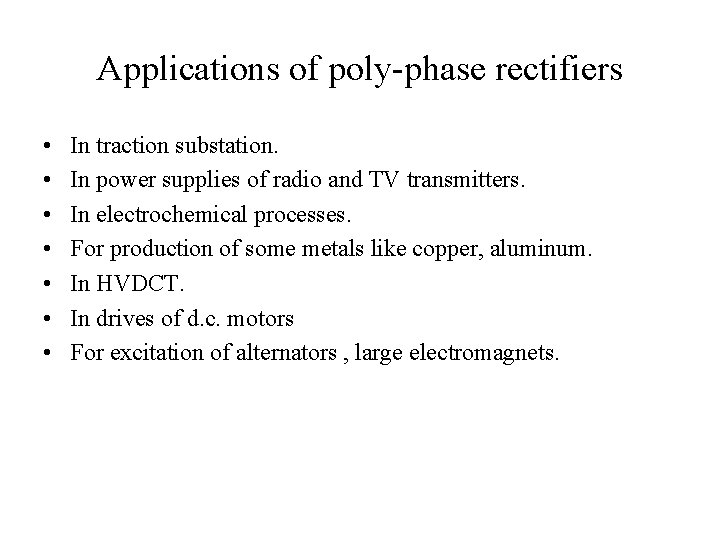
Applications of poly-phase rectifiers • • In traction substation. In power supplies of radio and TV transmitters. In electrochemical processes. For production of some metals like copper, aluminum. In HVDCT. In drives of d. c. motors For excitation of alternators , large electromagnets.
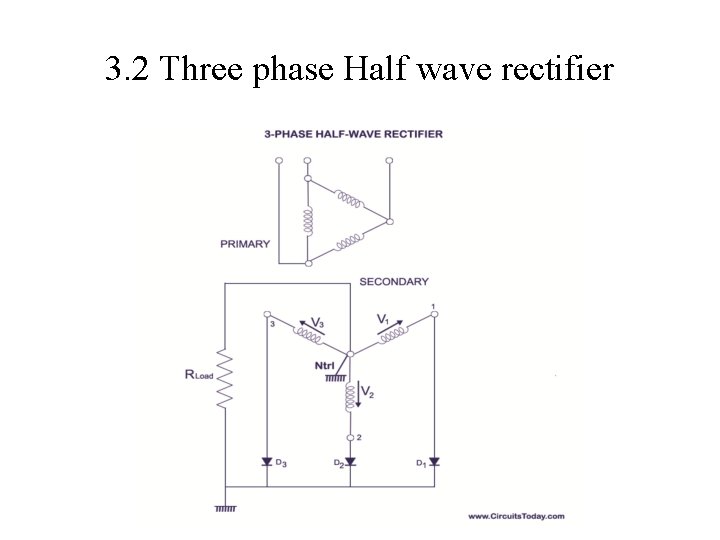
3. 2 Three phase Half wave rectifier
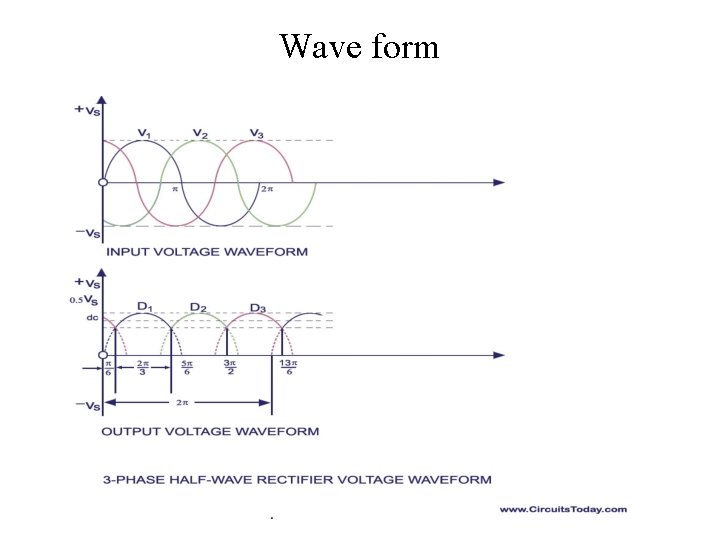
Wave form
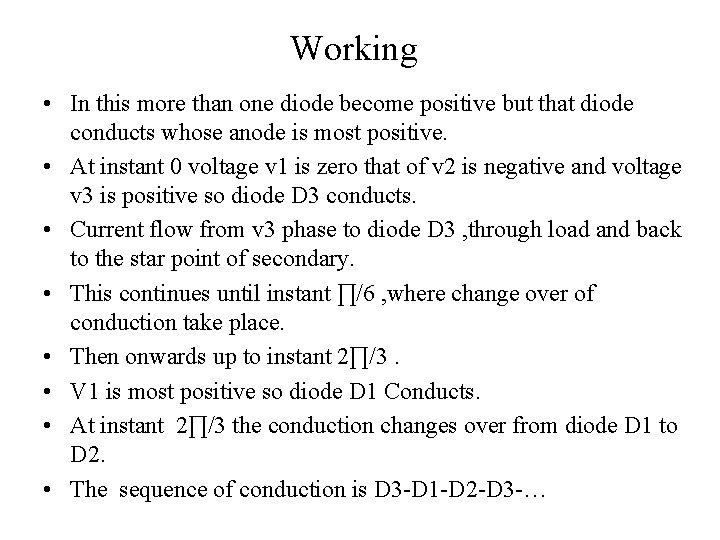
Working • In this more than one diode become positive but that diode conducts whose anode is most positive. • At instant 0 voltage v 1 is zero that of v 2 is negative and voltage v 3 is positive so diode D 3 conducts. • Current flow from v 3 phase to diode D 3 , through load and back to the star point of secondary. • This continues until instant ∏/6 , where change over of conduction take place. • Then onwards up to instant 2∏/3. • V 1 is most positive so diode D 1 Conducts. • At instant 2∏/3 the conduction changes over from diode D 1 to D 2. • The sequence of conduction is D 3 -D 1 -D 2 -D 3 -…
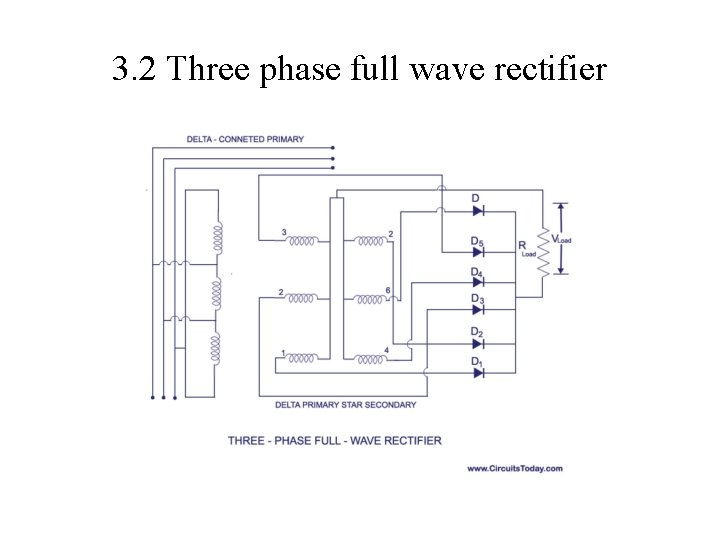
3. 2 Three phase full wave rectifier
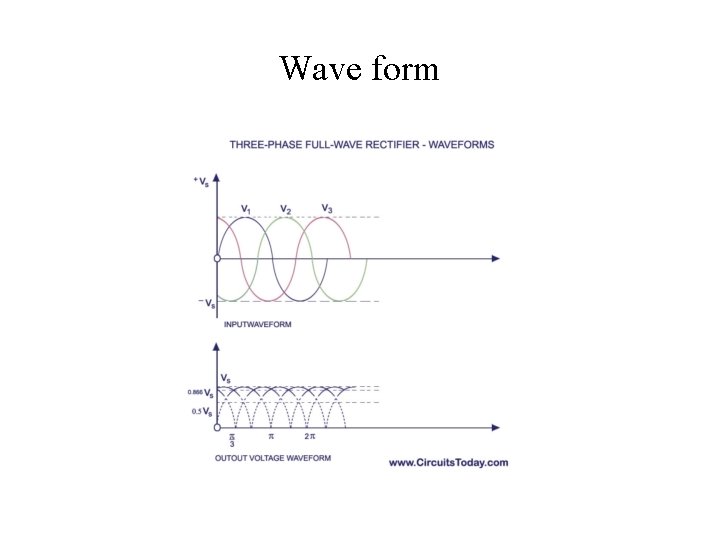
Wave form
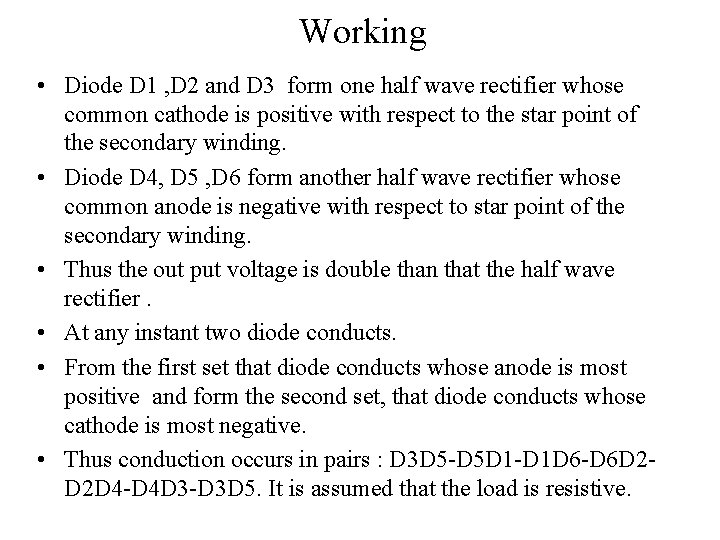
Working • Diode D 1 , D 2 and D 3 form one half wave rectifier whose common cathode is positive with respect to the star point of the secondary winding. • Diode D 4, D 5 , D 6 form another half wave rectifier whose common anode is negative with respect to star point of the secondary winding. • Thus the out put voltage is double than that the half wave rectifier. • At any instant two diode conducts. • From the first set that diode conducts whose anode is most positive and form the second set, that diode conducts whose cathode is most negative. • Thus conduction occurs in pairs : D 3 D 5 -D 5 D 1 -D 1 D 6 -D 6 D 2 D 2 D 4 -D 4 D 3 -D 3 D 5. It is assumed that the load is resistive.
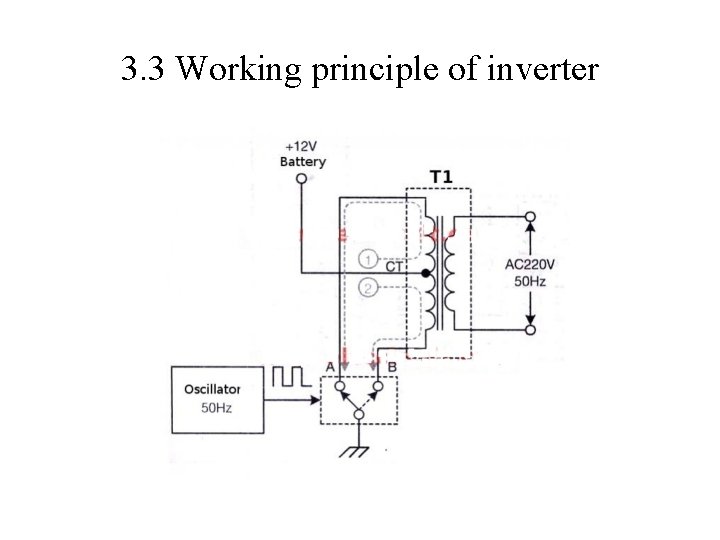
3. 3 Working principle of inverter
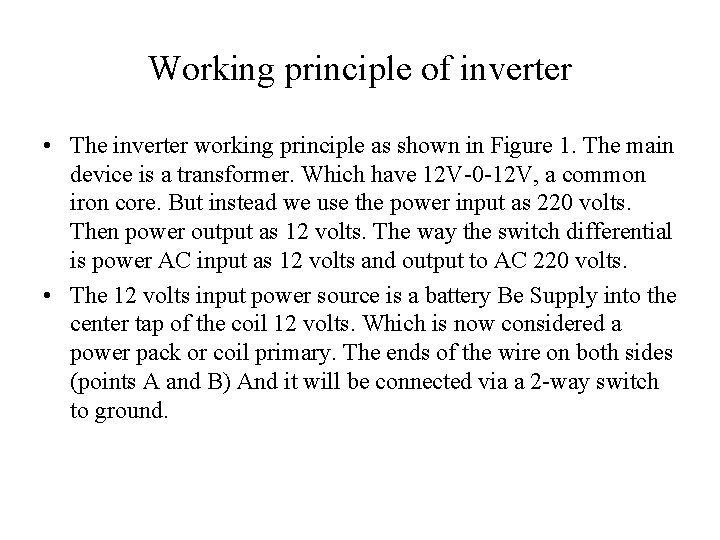
Working principle of inverter • The inverter working principle as shown in Figure 1. The main device is a transformer. Which have 12 V-0 -12 V, a common iron core. But instead we use the power input as 220 volts. Then power output as 12 volts. The way the switch differential is power AC input as 12 volts and output to AC 220 volts. • The 12 volts input power source is a battery Be Supply into the center tap of the coil 12 volts. Which is now considered a power pack or coil primary. The ends of the wire on both sides (points A and B) And it will be connected via a 2 -way switch to ground.
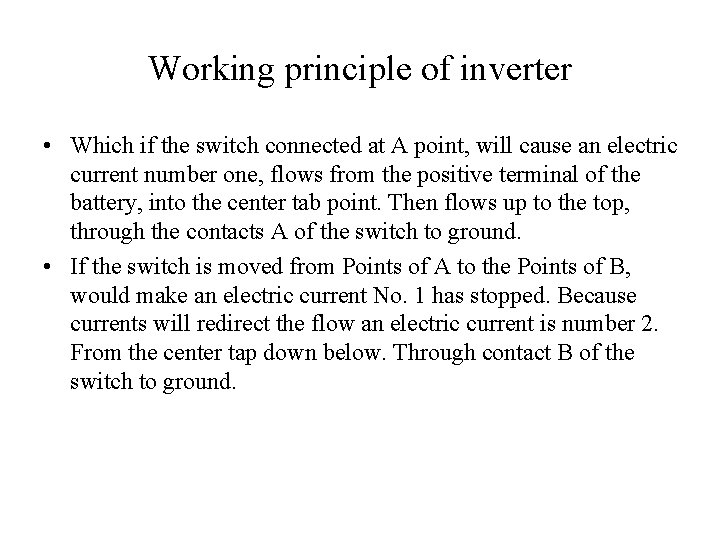
Working principle of inverter • Which if the switch connected at A point, will cause an electric current number one, flows from the positive terminal of the battery, into the center tab point. Then flows up to the top, through the contacts A of the switch to ground. • If the switch is moved from Points of A to the Points of B, would make an electric current No. 1 has stopped. Because currents will redirect the flow an electric current is number 2. From the center tap down below. Through contact B of the switch to ground.
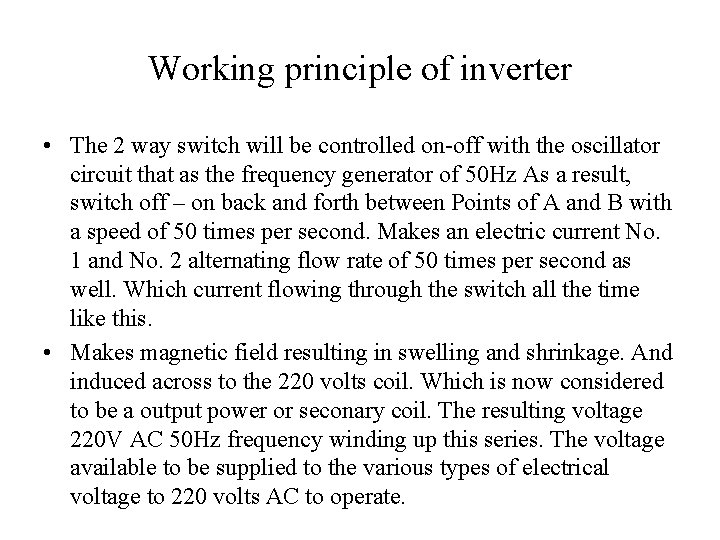
Working principle of inverter • The 2 way switch will be controlled on-off with the oscillator circuit that as the frequency generator of 50 Hz As a result, switch off – on back and forth between Points of A and B with a speed of 50 times per second. Makes an electric current No. 1 and No. 2 alternating flow rate of 50 times per second as well. Which current flowing through the switch all the time like this. • Makes magnetic field resulting in swelling and shrinkage. And induced across to the 220 volts coil. Which is now considered to be a output power or seconary coil. The resulting voltage 220 V AC 50 Hz frequency winding up this series. The voltage available to be supplied to the various types of electrical voltage to 220 volts AC to operate.
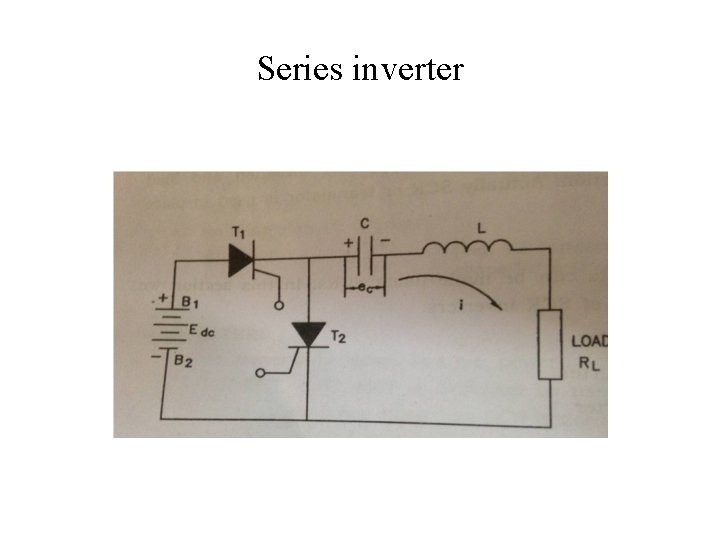
Series inverter
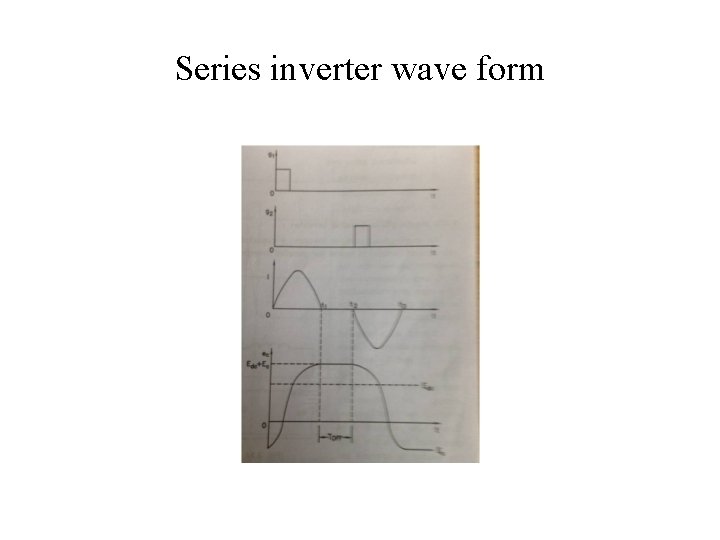
Series inverter wave form
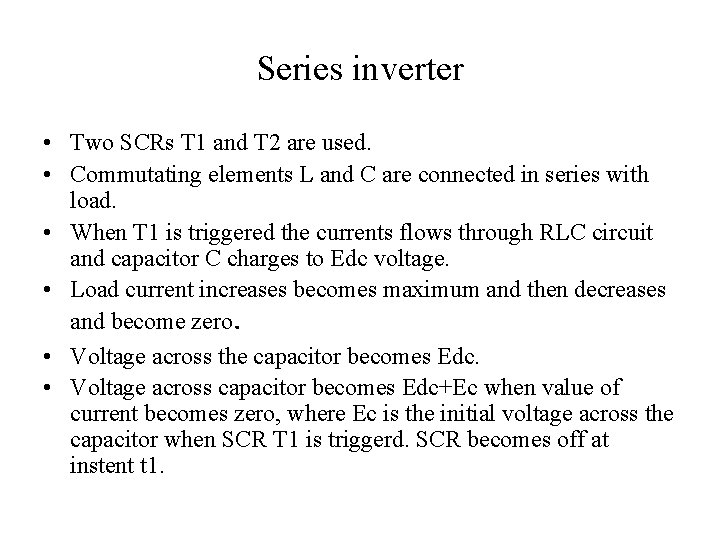
Series inverter • Two SCRs T 1 and T 2 are used. • Commutating elements L and C are connected in series with load. • When T 1 is triggered the currents flows through RLC circuit and capacitor C charges to Edc voltage. • Load current increases becomes maximum and then decreases and become zero. • Voltage across the capacitor becomes Edc. • Voltage across capacitor becomes Edc+Ec when value of current becomes zero, where Ec is the initial voltage across the capacitor when SCR T 1 is triggerd. SCR becomes off at instent t 1.
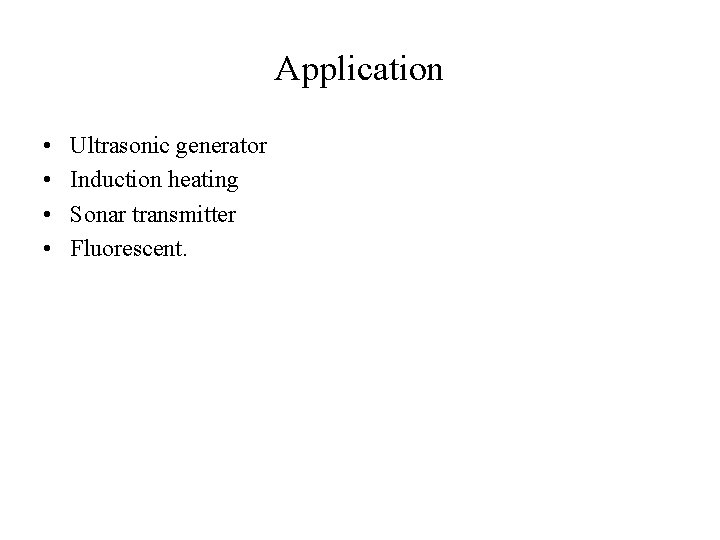
Application • • Ultrasonic generator Induction heating Sonar transmitter Fluorescent.
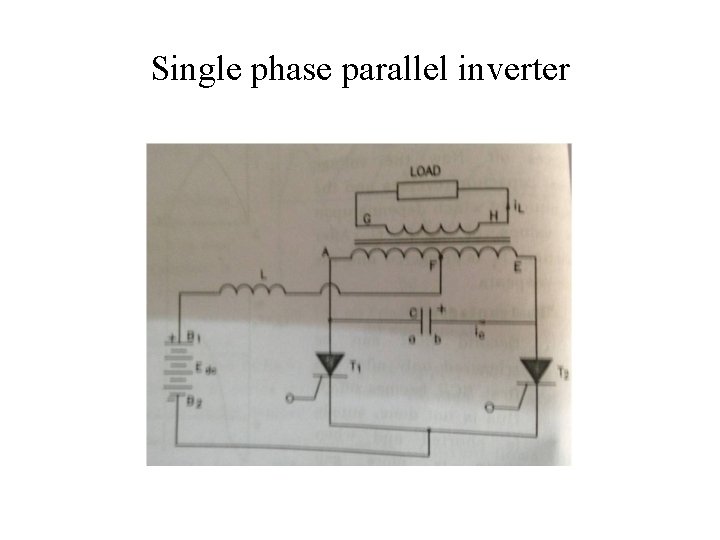
Single phase parallel inverter
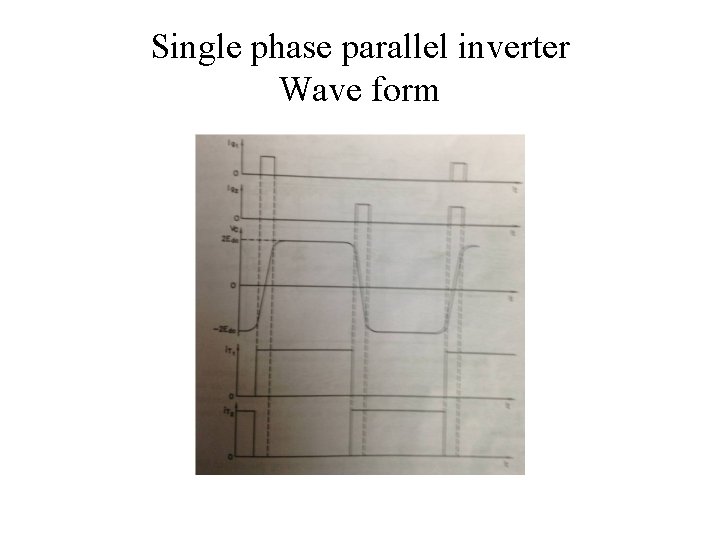
Single phase parallel inverter Wave form
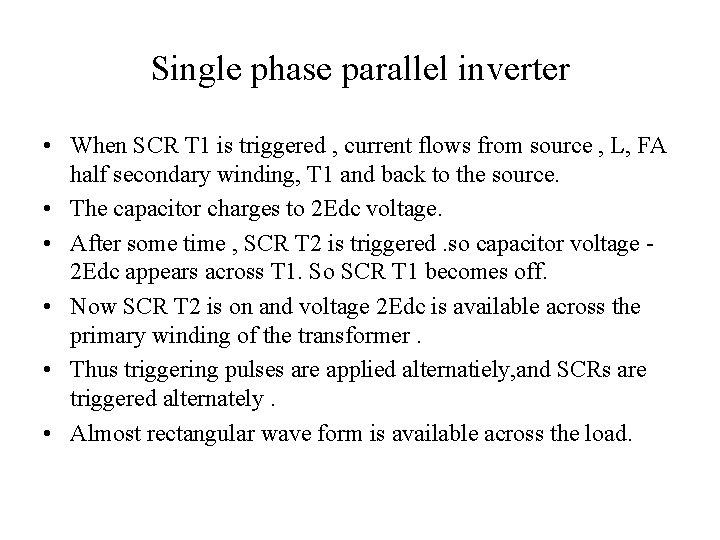
Single phase parallel inverter • When SCR T 1 is triggered , current flows from source , L, FA half secondary winding, T 1 and back to the source. • The capacitor charges to 2 Edc voltage. • After some time , SCR T 2 is triggered. so capacitor voltage 2 Edc appears across T 1. So SCR T 1 becomes off. • Now SCR T 2 is on and voltage 2 Edc is available across the primary winding of the transformer. • Thus triggering pulses are applied alternatiely, and SCRs are triggered alternately. • Almost rectangular wave form is available across the load.
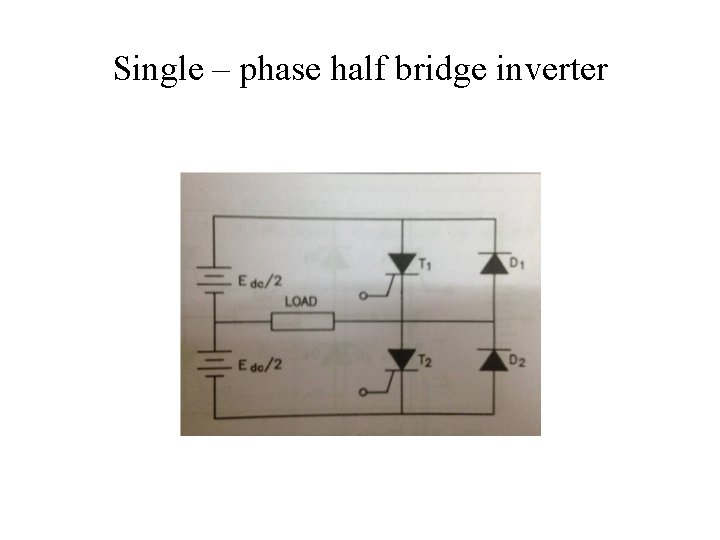
Single – phase half bridge inverter
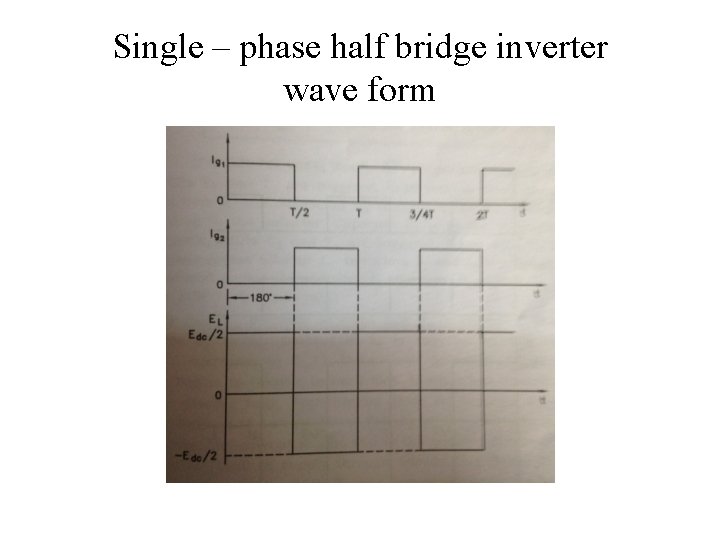
Single – phase half bridge inverter wave form
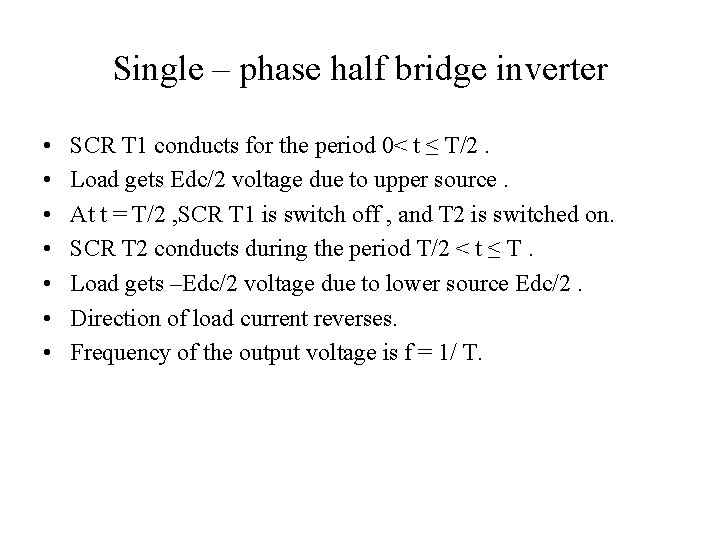
Single – phase half bridge inverter • • SCR T 1 conducts for the period 0< t ≤ T/2. Load gets Edc/2 voltage due to upper source. At t = T/2 , SCR T 1 is switch off , and T 2 is switched on. SCR T 2 conducts during the period T/2 < t ≤ T. Load gets –Edc/2 voltage due to lower source Edc/2. Direction of load current reverses. Frequency of the output voltage is f = 1/ T.
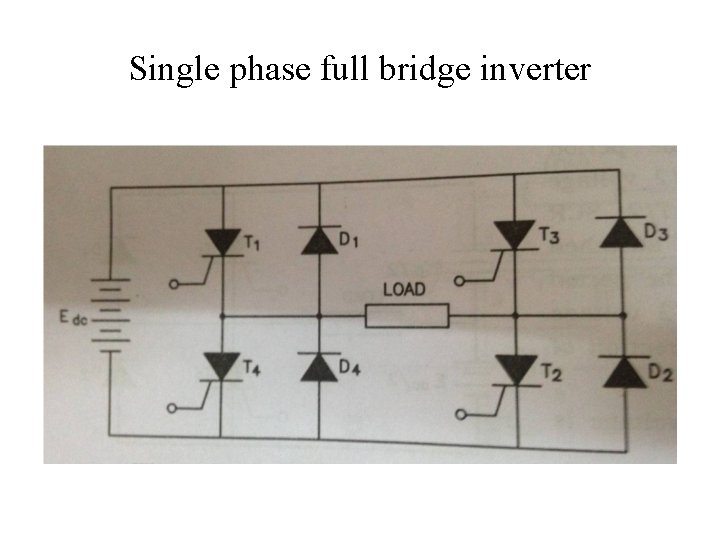
Single phase full bridge inverter
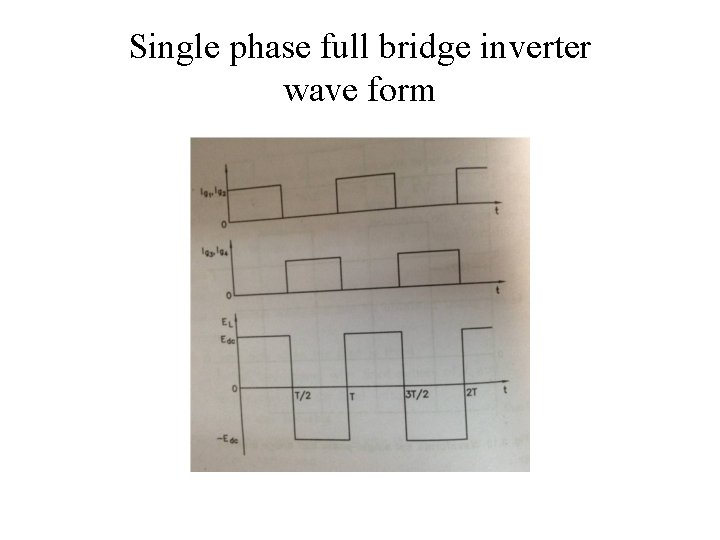
Single phase full bridge inverter wave form
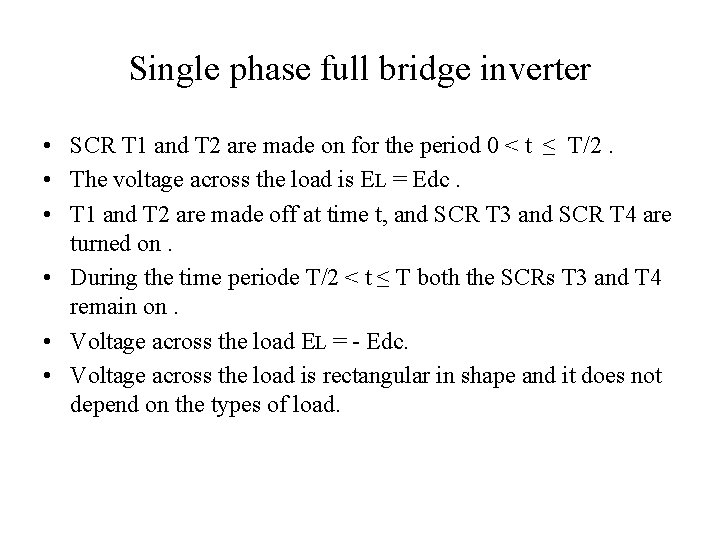
Single phase full bridge inverter • SCR T 1 and T 2 are made on for the period 0 < t ≤ T/2. • The voltage across the load is EL = Edc. • T 1 and T 2 are made off at time t, and SCR T 3 and SCR T 4 are turned on. • During the time periode T/2 < t ≤ T both the SCRs T 3 and T 4 remain on. • Voltage across the load EL = - Edc. • Voltage across the load is rectangular in shape and it does not depend on the types of load.
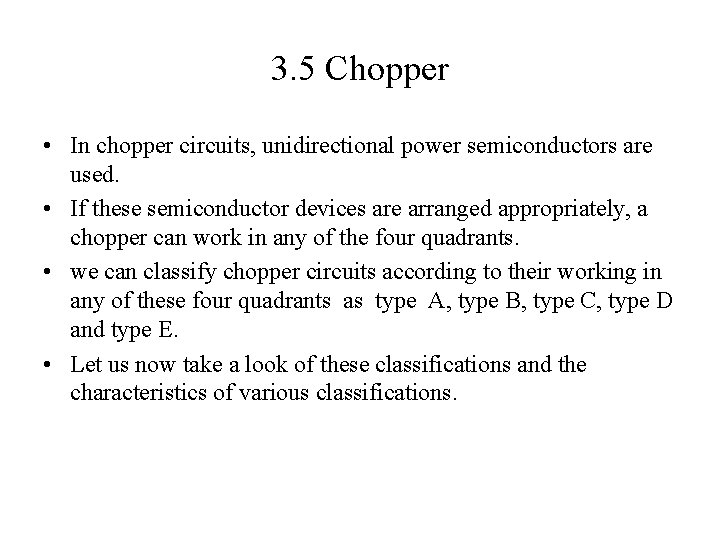
3. 5 Chopper • In chopper circuits, unidirectional power semiconductors are used. • If these semiconductor devices are arranged appropriately, a chopper can work in any of the four quadrants. • we can classify chopper circuits according to their working in any of these four quadrants as type A, type B, type C, type D and type E. • Let us now take a look of these classifications and the characteristics of various classifications.
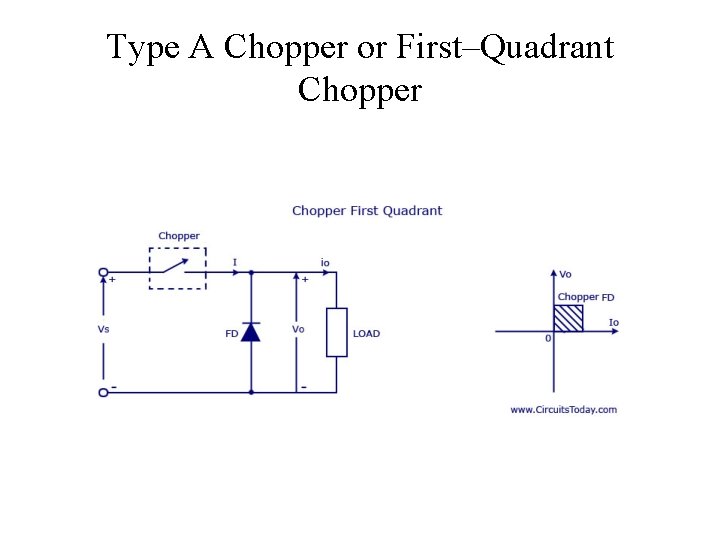
Type A Chopper or First–Quadrant Chopper
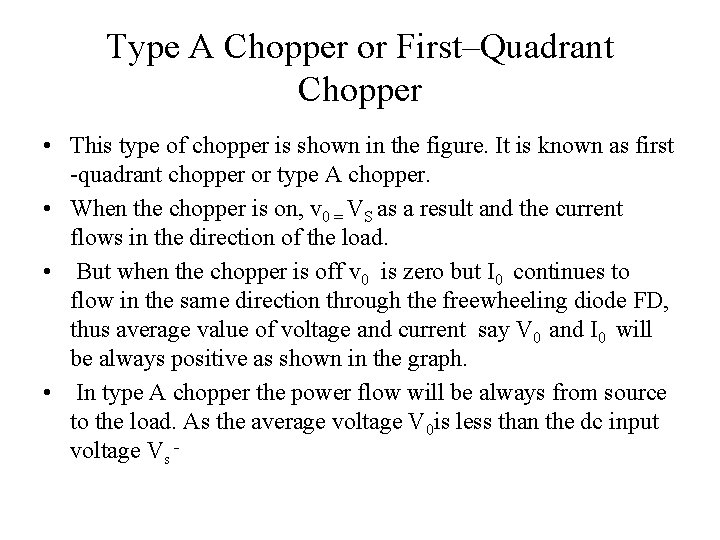
Type A Chopper or First–Quadrant Chopper • This type of chopper is shown in the figure. It is known as first -quadrant chopper or type A chopper. • When the chopper is on, v 0 = VS as a result and the current flows in the direction of the load. • But when the chopper is off v 0 is zero but I 0 continues to flow in the same direction through the freewheeling diode FD, thus average value of voltage and current say V 0 and I 0 will be always positive as shown in the graph. • In type A chopper the power flow will be always from source to the load. As the average voltage V 0 is less than the dc input voltage Vs
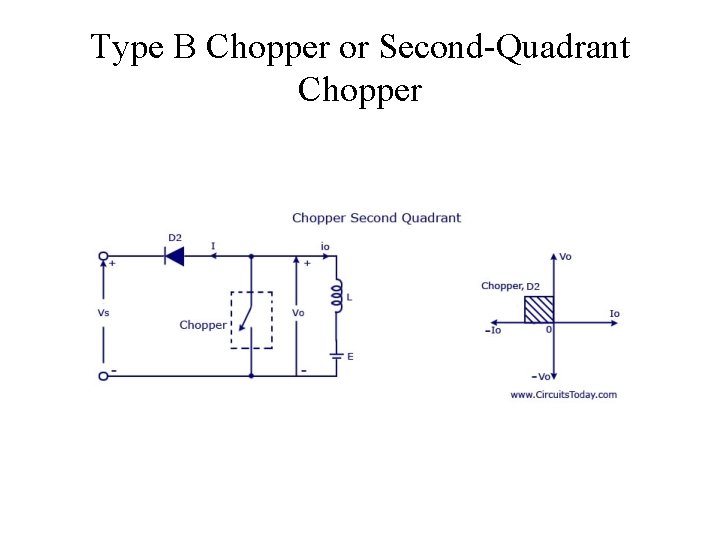
Type B Chopper or Second-Quadrant Chopper
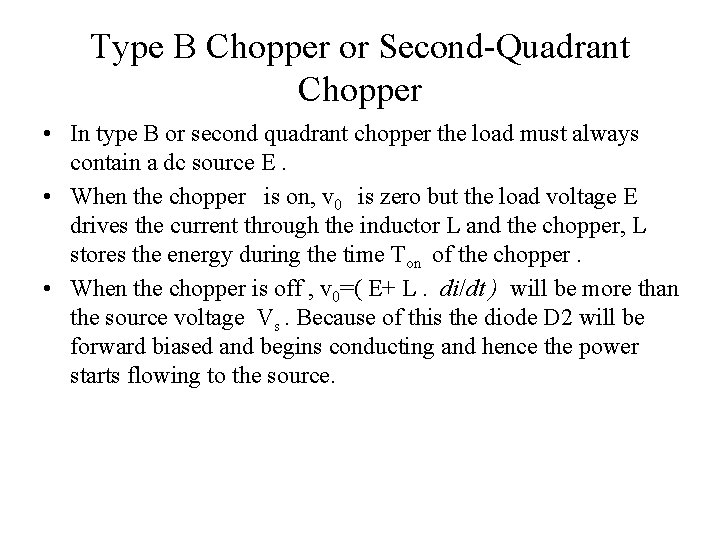
Type B Chopper or Second-Quadrant Chopper • In type B or second quadrant chopper the load must always contain a dc source E. • When the chopper is on, v 0 is zero but the load voltage E drives the current through the inductor L and the chopper, L stores the energy during the time Ton of the chopper. • When the chopper is off , v 0=( E+ L. di/dt ) will be more than the source voltage Vs. Because of this the diode D 2 will be forward biased and begins conducting and hence the power starts flowing to the source.
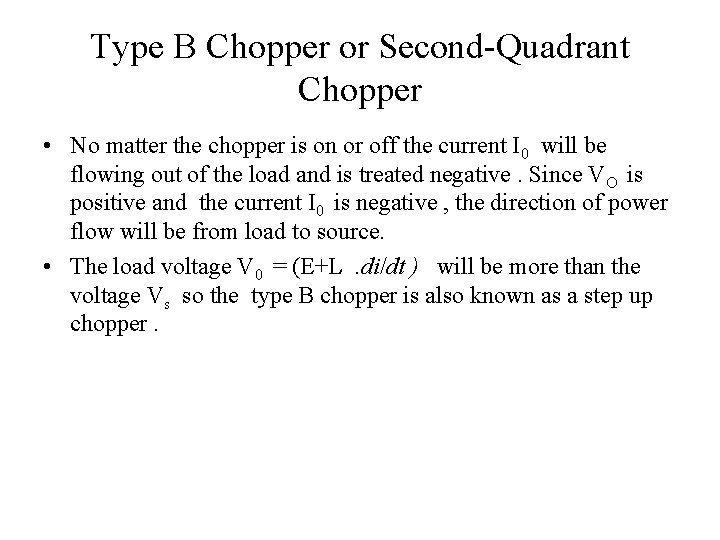
Type B Chopper or Second-Quadrant Chopper • No matter the chopper is on or off the current I 0 will be flowing out of the load and is treated negative. Since VO is positive and the current I 0 is negative , the direction of power flow will be from load to source. • The load voltage V 0 = (E+L . di/dt ) will be more than the voltage Vs so the type B chopper is also known as a step up chopper.
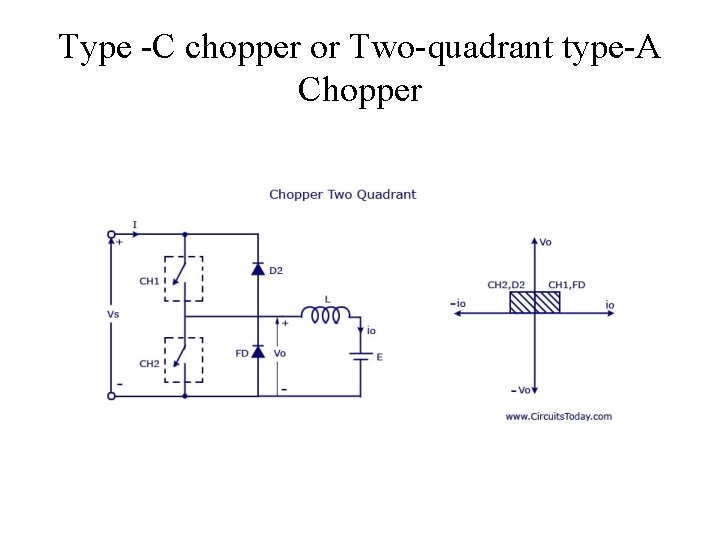
Type -C chopper or Two-quadrant type-A Chopper
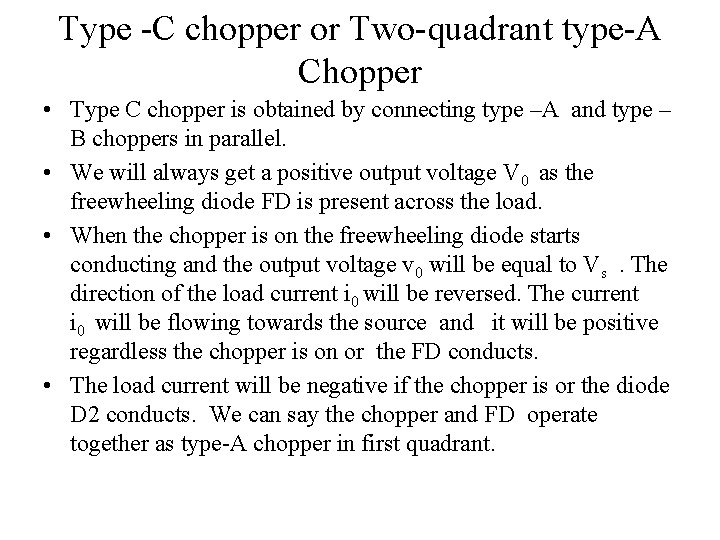
Type -C chopper or Two-quadrant type-A Chopper • Type C chopper is obtained by connecting type –A and type – B choppers in parallel. • We will always get a positive output voltage V 0 as the freewheeling diode FD is present across the load. • When the chopper is on the freewheeling diode starts conducting and the output voltage v 0 will be equal to Vs . The direction of the load current i 0 will be reversed. The current i 0 will be flowing towards the source and it will be positive regardless the chopper is on or the FD conducts. • The load current will be negative if the chopper is or the diode D 2 conducts. We can say the chopper and FD operate together as type-A chopper in first quadrant.
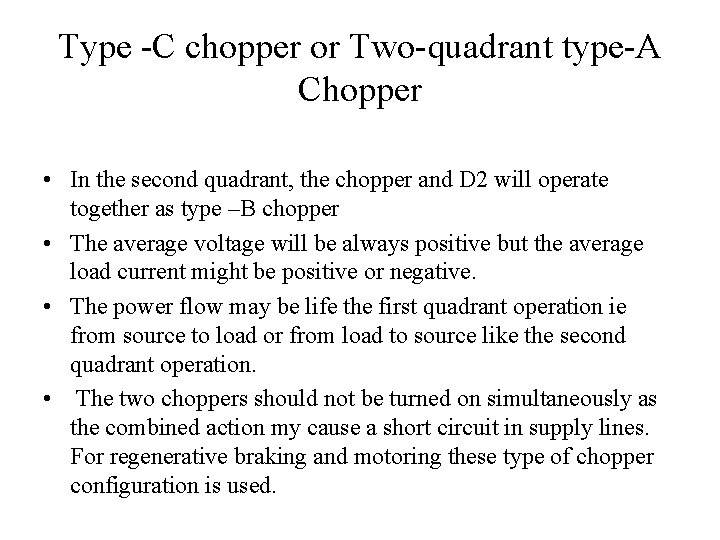
Type -C chopper or Two-quadrant type-A Chopper • In the second quadrant, the chopper and D 2 will operate together as type –B chopper • The average voltage will be always positive but the average load current might be positive or negative. • The power flow may be life the first quadrant operation ie from source to load or from load to source like the second quadrant operation. • The two choppers should not be turned on simultaneously as the combined action my cause a short circuit in supply lines. For regenerative braking and motoring these type of chopper configuration is used.
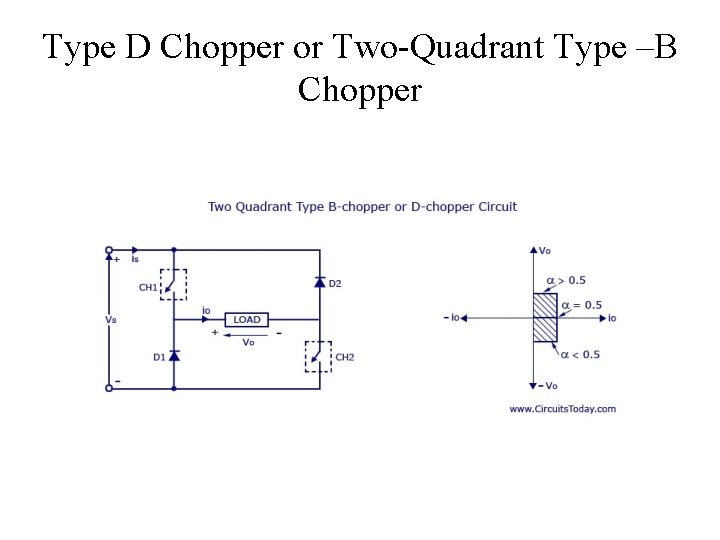
Type D Chopper or Two-Quadrant Type –B Chopper
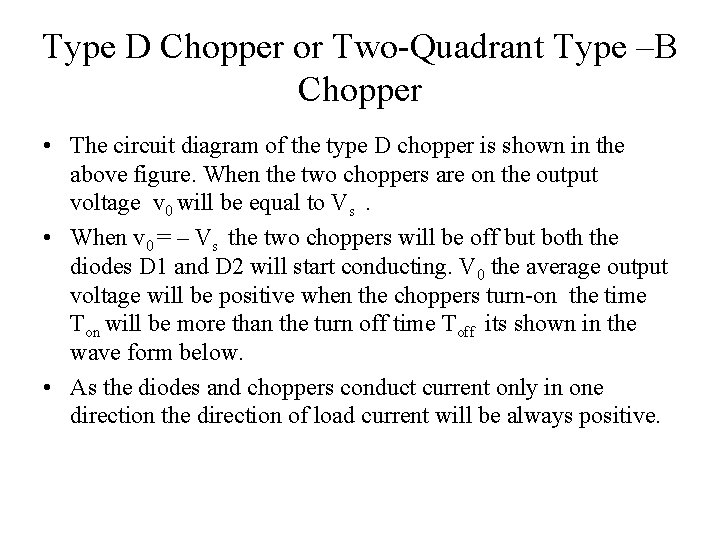
Type D Chopper or Two-Quadrant Type –B Chopper • The circuit diagram of the type D chopper is shown in the above figure. When the two choppers are on the output voltage v 0 will be equal to Vs . • When v 0 = – Vs the two choppers will be off but both the diodes D 1 and D 2 will start conducting. V 0 the average output voltage will be positive when the choppers turn-on the time Ton will be more than the turn off time Toff its shown in the wave form below. • As the diodes and choppers conduct current only in one direction the direction of load current will be always positive.
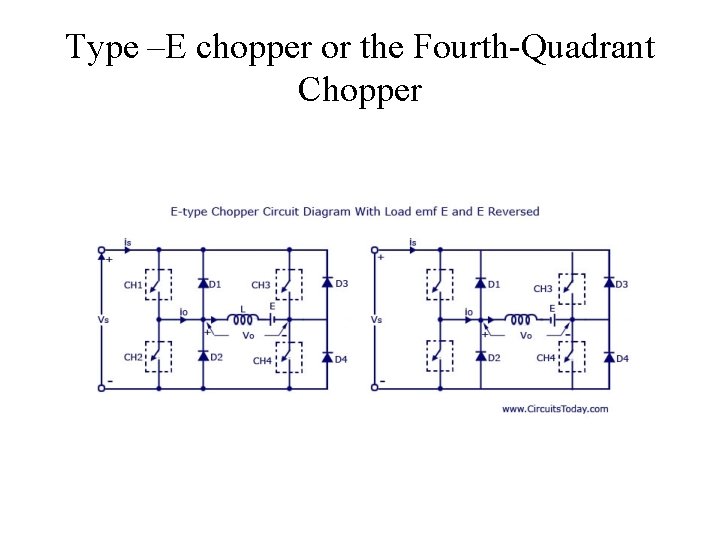
Type –E chopper or the Fourth-Quadrant Chopper
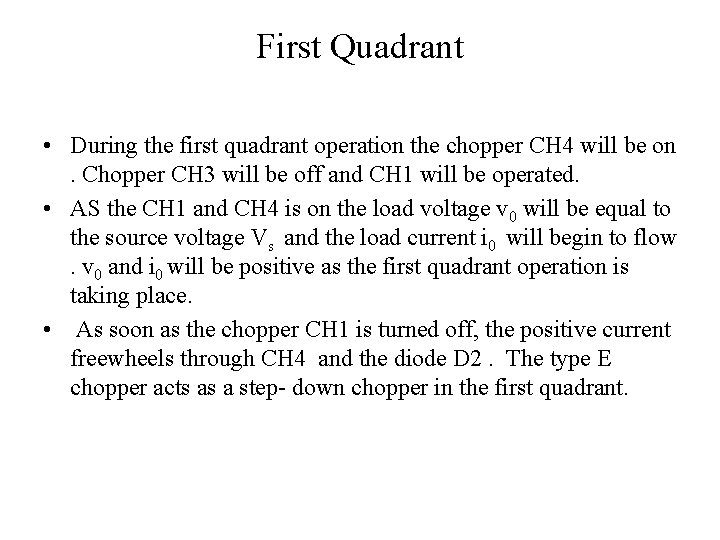
First Quadrant • During the first quadrant operation the chopper CH 4 will be on . Chopper CH 3 will be off and CH 1 will be operated. • AS the CH 1 and CH 4 is on the load voltage v 0 will be equal to the source voltage Vs and the load current i 0 will begin to flow . v 0 and i 0 will be positive as the first quadrant operation is taking place. • As soon as the chopper CH 1 is turned off, the positive current freewheels through CH 4 and the diode D 2. The type E chopper acts as a step- down chopper in the first quadrant.
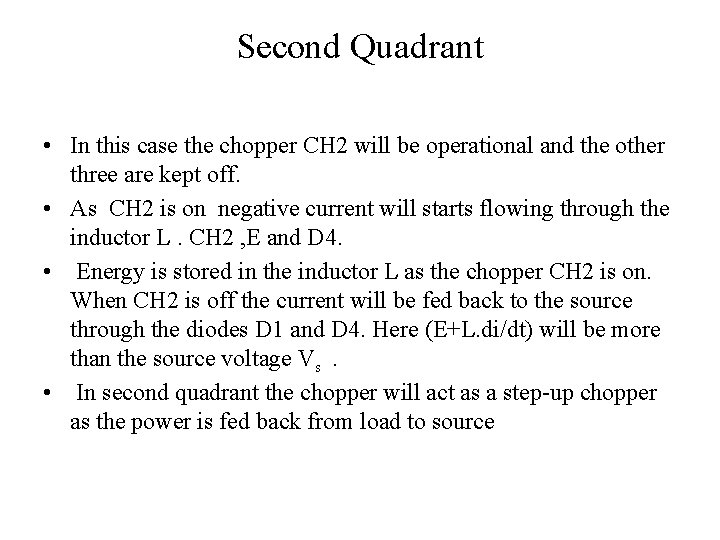
Second Quadrant • In this case the chopper CH 2 will be operational and the other three are kept off. • As CH 2 is on negative current will starts flowing through the inductor L. CH 2 , E and D 4. • Energy is stored in the inductor L as the chopper CH 2 is on. When CH 2 is off the current will be fed back to the source through the diodes D 1 and D 4. Here (E+L. di/dt) will be more than the source voltage Vs . • In second quadrant the chopper will act as a step-up chopper as the power is fed back from load to source
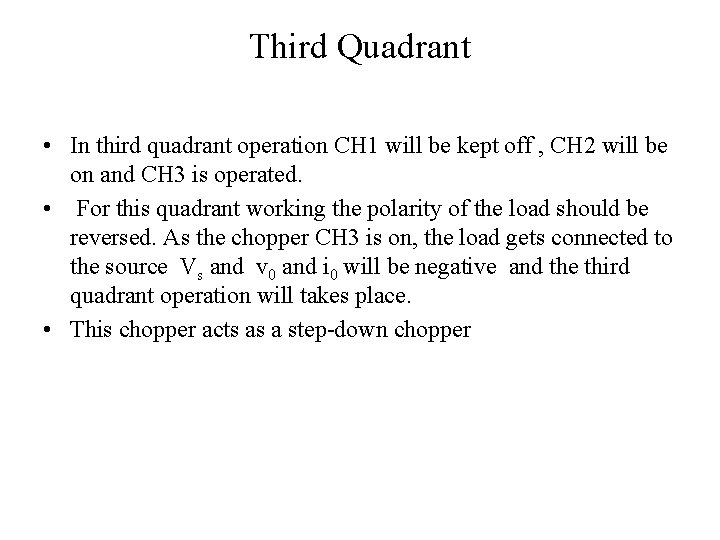
Third Quadrant • In third quadrant operation CH 1 will be kept off , CH 2 will be on and CH 3 is operated. • For this quadrant working the polarity of the load should be reversed. As the chopper CH 3 is on, the load gets connected to the source Vs and v 0 and i 0 will be negative and the third quadrant operation will takes place. • This chopper acts as a step-down chopper
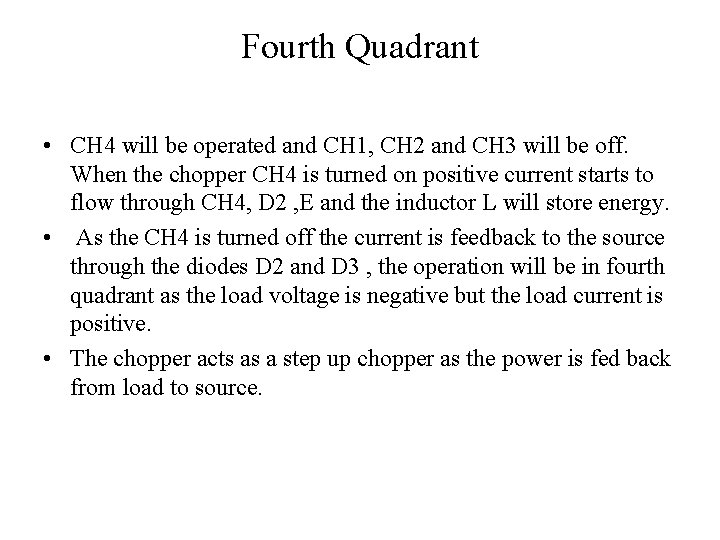
Fourth Quadrant • CH 4 will be operated and CH 1, CH 2 and CH 3 will be off. When the chopper CH 4 is turned on positive current starts to flow through CH 4, D 2 , E and the inductor L will store energy. • As the CH 4 is turned off the current is feedback to the source through the diodes D 2 and D 3 , the operation will be in fourth quadrant as the load voltage is negative but the load current is positive. • The chopper acts as a step up chopper as the power is fed back from load to source.
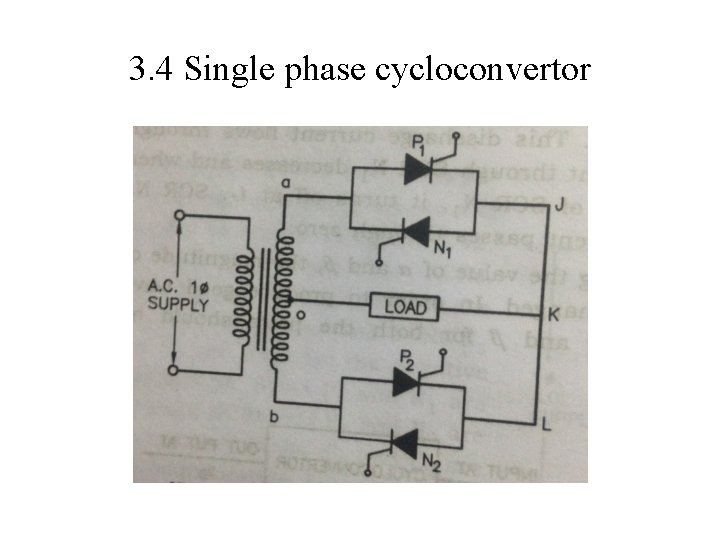
3. 4 Single phase cycloconvertor
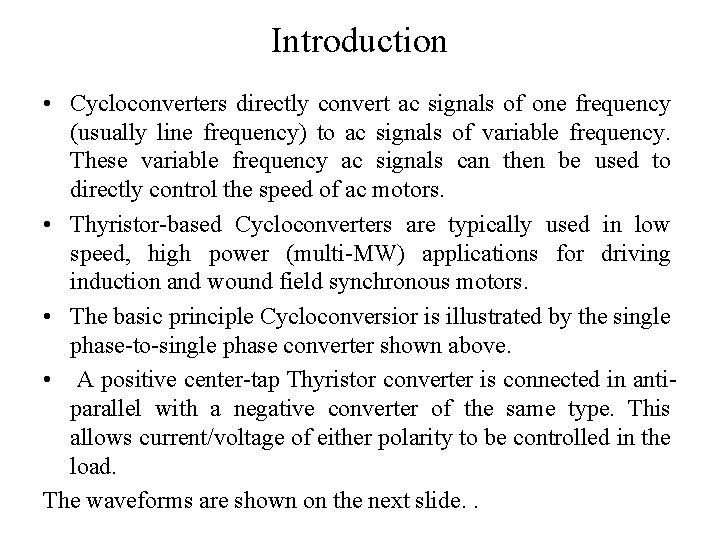
Introduction • Cycloconverters directly convert ac signals of one frequency (usually line frequency) to ac signals of variable frequency. These variable frequency ac signals can then be used to directly control the speed of ac motors. • Thyristor-based Cycloconverters are typically used in low speed, high power (multi-MW) applications for driving induction and wound field synchronous motors. • The basic principle Cycloconversior is illustrated by the single phase-to-single phase converter shown above. • A positive center-tap Thyristor converter is connected in antiparallel with a negative converter of the same type. This allows current/voltage of either polarity to be controlled in the load. The waveforms are shown on the next slide. .
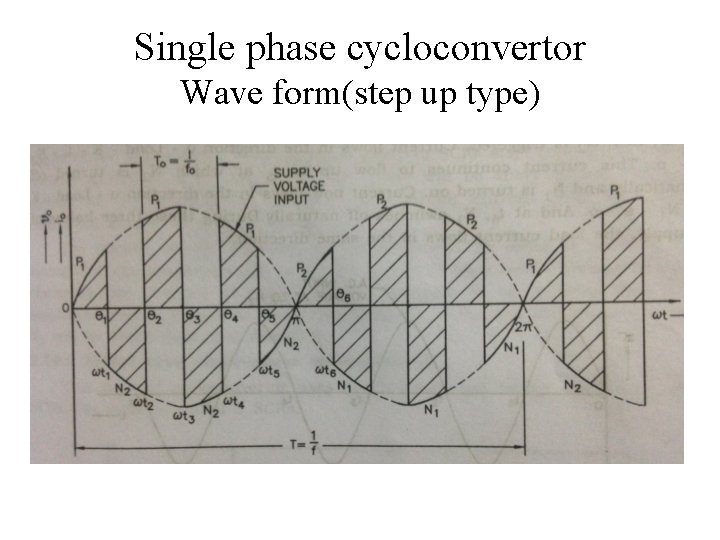
Single phase cycloconvertor Wave form(step up type)
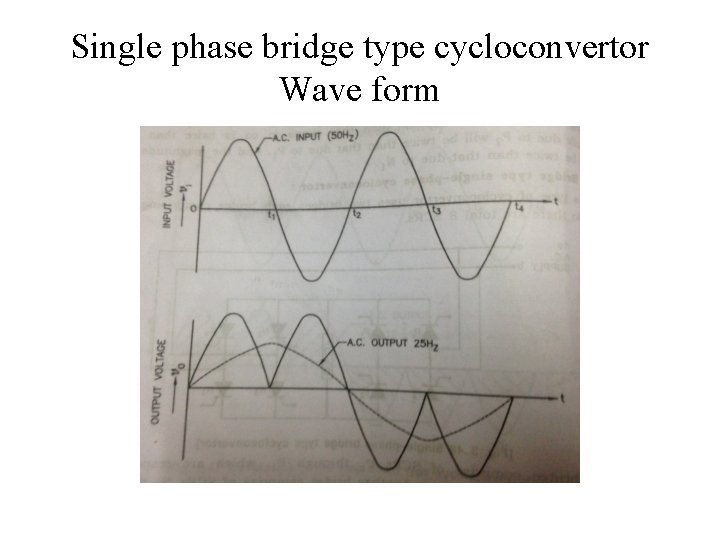
Single phase bridge type cycloconvertor Wave form
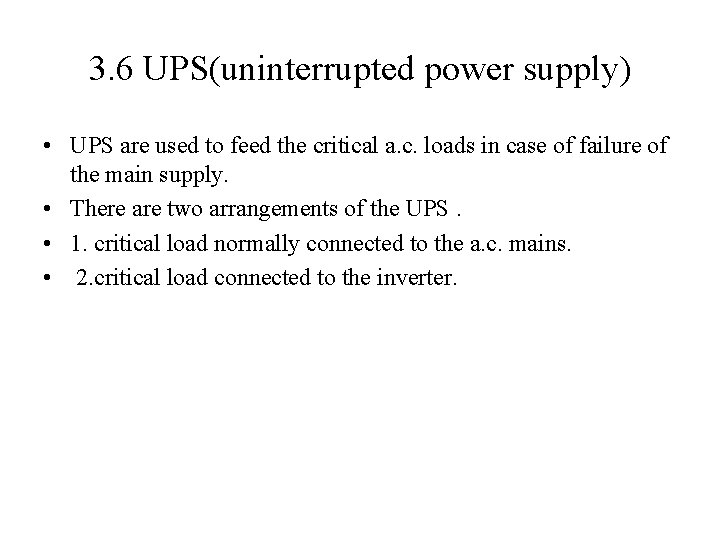
3. 6 UPS(uninterrupted power supply) • UPS are used to feed the critical a. c. loads in case of failure of the main supply. • There are two arrangements of the UPS. • 1. critical load normally connected to the a. c. mains. • 2. critical load connected to the inverter.
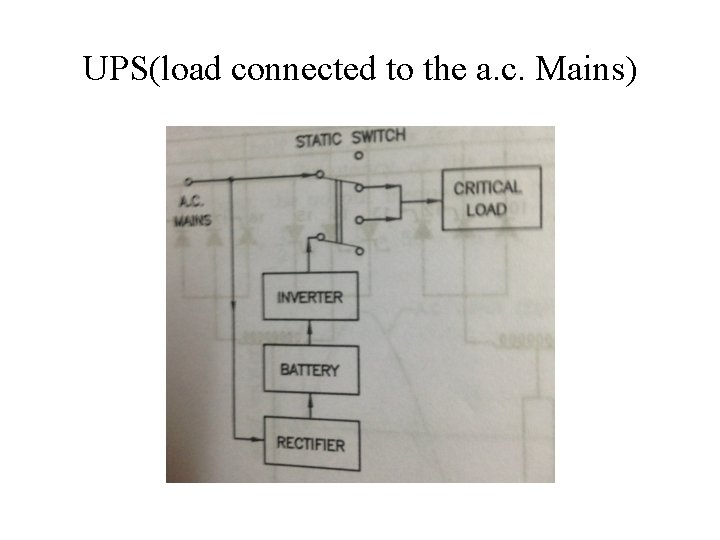
UPS(load connected to the a. c. Mains)
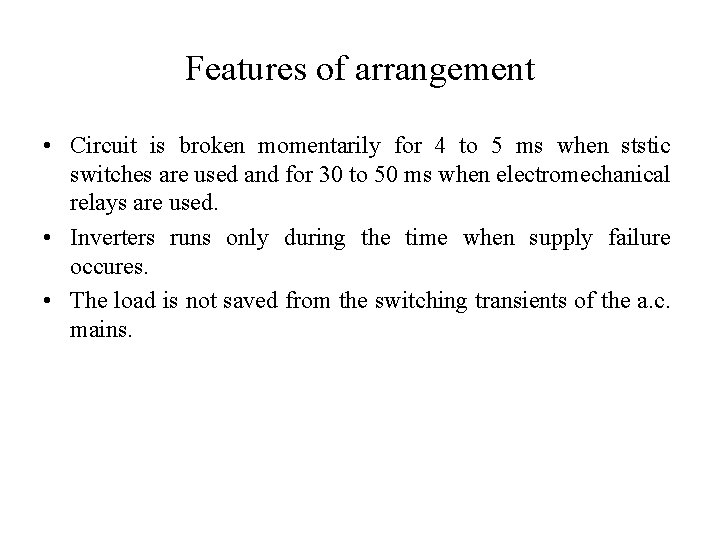
Features of arrangement • Circuit is broken momentarily for 4 to 5 ms when ststic switches are used and for 30 to 50 ms when electromechanical relays are used. • Inverters runs only during the time when supply failure occures. • The load is not saved from the switching transients of the a. c. mains.
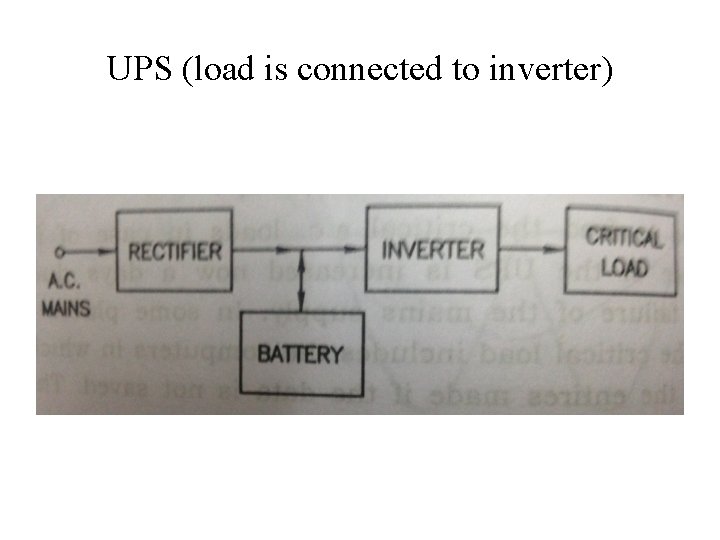
UPS (load is connected to inverter)
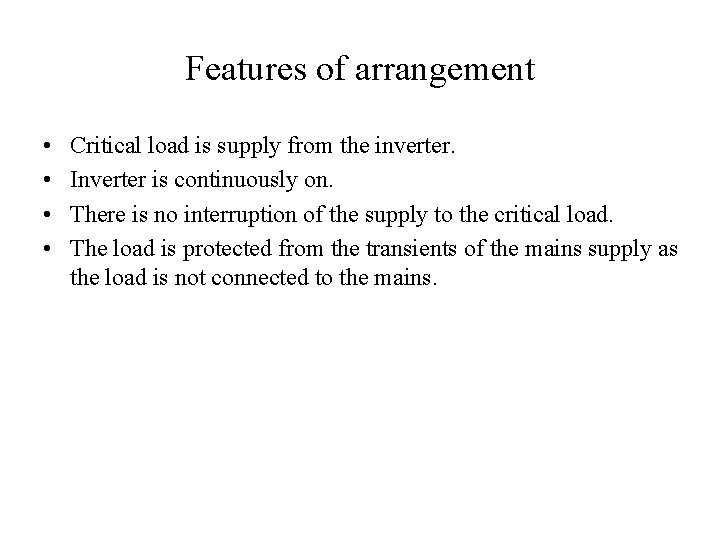
Features of arrangement • • Critical load is supply from the inverter. Inverter is continuously on. There is no interruption of the supply to the critical load. The load is protected from the transients of the mains supply as the load is not connected to the mains.
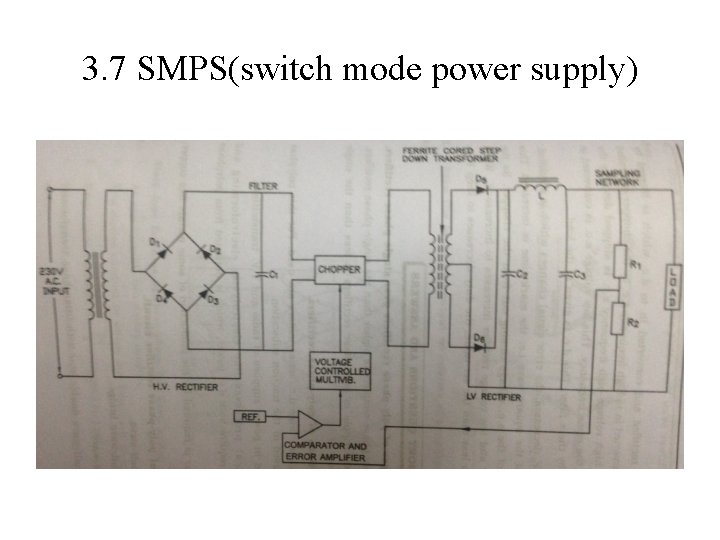
3. 7 SMPS(switch mode power supply)
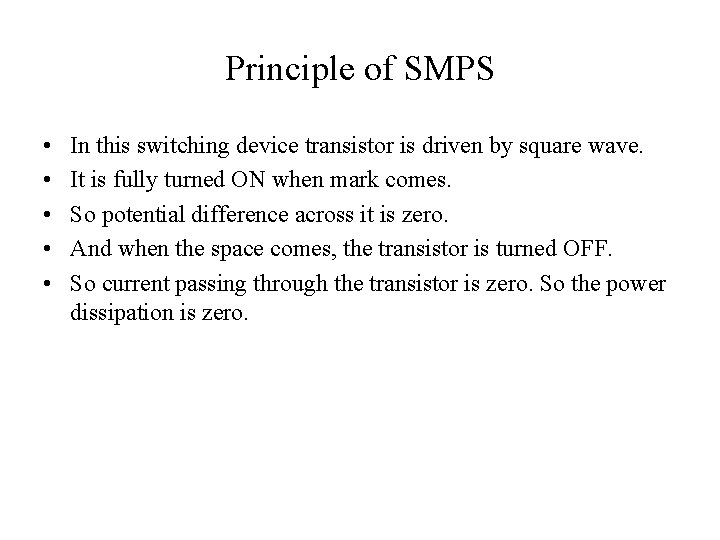
Principle of SMPS • • • In this switching device transistor is driven by square wave. It is fully turned ON when mark comes. So potential difference across it is zero. And when the space comes, the transistor is turned OFF. So current passing through the transistor is zero. So the power dissipation is zero.
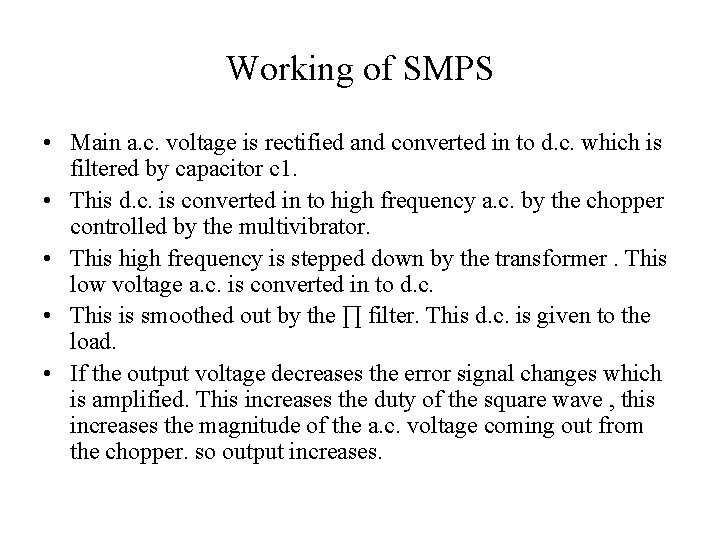
Working of SMPS • Main a. c. voltage is rectified and converted in to d. c. which is filtered by capacitor c 1. • This d. c. is converted in to high frequency a. c. by the chopper controlled by the multivibrator. • This high frequency is stepped down by the transformer. This low voltage a. c. is converted in to d. c. • This is smoothed out by the ∏ filter. This d. c. is given to the load. • If the output voltage decreases the error signal changes which is amplified. This increases the duty of the square wave , this increases the magnitude of the a. c. voltage coming out from the chopper. so output increases.