Unit II Impulse Water Turbines Introduction to Hydro
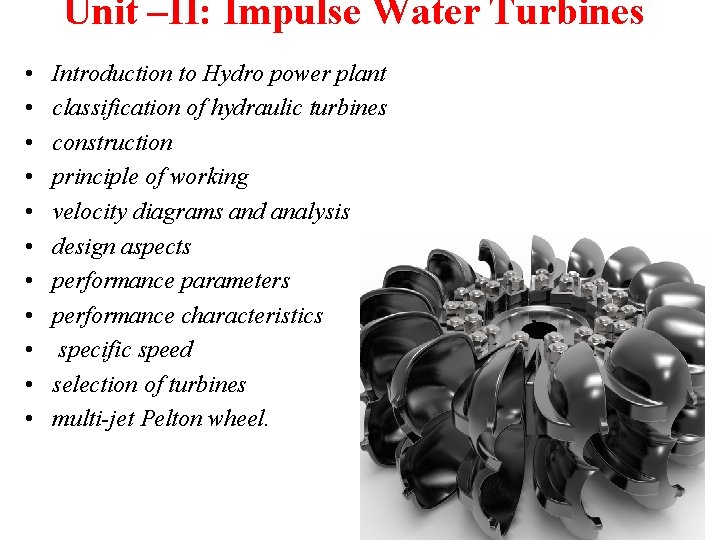
Unit –II: Impulse Water Turbines • • • Introduction to Hydro power plant classification of hydraulic turbines construction principle of working velocity diagrams and analysis design aspects performance parameters performance characteristics specific speed selection of turbines multi-jet Pelton wheel.


Early Hydraulic Turbines • Hydraulic Turbines (water wheels) have been in use for centuries. • Hydraulic Turbines convert the potential energy of water into work. • Basic Turbines are either Reaction or Impulse. • First developed in the mid 1800’s. • Power outputs range up to 1, 000 Mw. • Included are Tidal and Wind Turbines. Overshot Style Undershot Style

Introduction • The device which converts hydraulic energy into mechanical energy or vice versa is known as Hydraulic Machines. • The hydraulic machines which convert hydraulic energy in to mechanical energy is called as turbine • A water turbine is a rotary machine that converts kinetic and potential energy of water into mechanical work. • Water turbines are mostly found in dams to generate electric power from water kinetic energy. • Water turbines take energy from moving water. Flowing water is directed on to the blades of a turbine runner, creating a force on the blades. Since the runner is spinning, the force acts through a distance to produce work. In this way, energy is transferred from the water flow to the turbine.

Turbine TURBINES: - Turbines are defined as hydraulic machine which converts hydraulic energy into mechanical energy. Turbine is a device that extracts energy from a fluid (converts the energy held by the fluid to mechanical energy) PRINCIPLE: - This mechanical energy is used in running an electric generator which is directly coupled to the shaft of turbine Thus mechanical energy is converted into electrical energy.

DEFINATION OF TURBINES: IMPULSE TURBINE: - If at inlet of turbine, the energy available only kinectic energy, the turbine is known as impulse turbine. Ex. Pelton Wheel Turbine REACTION TURBINE: - If at inlet of turbine, the water possesses kinetic energy, the turbine iss known as reaction turbine. Ex. Francis Turbine, Kaplan Turbine RADIAL FLOW TURBINNE: - If the water flow in radial direction through runner, the turbine is called radial flow turbine.

INWARD RADIAL FLOW TURBINE: - If the water flows from outward to inward radial flow turbine. OUTWARD RADIAL FLOW TURBINE: - If the water flows from inward to outward radial flow turbine. AXIAL FLOW TURBINE: - If the water flow through the runner along the direction parallel to the axis of rotation of the runner, the turbine is called axial flow turbine. MIXED FLOW TURBINE: - If the water flows the runner in the radial direction but leaves in the direction parallel to the axis of rotation of the runner, the turbine is called mixed floe turbine. TANGENTIAL FLOW TURBINE: - If the water flows along the tangent of runner, the turbine is known as tangential flow turbine.

Power from water • In both types of turbines the fluid passes through a runner having blades. The momentum of the fluid in the tangential direction is changed and so a tangential force on the runner is produced. The important feature of the impulse machine is that there is no change in static pressure, across the runner, while for the reaction turbine there are considerable changes in pressure energy.
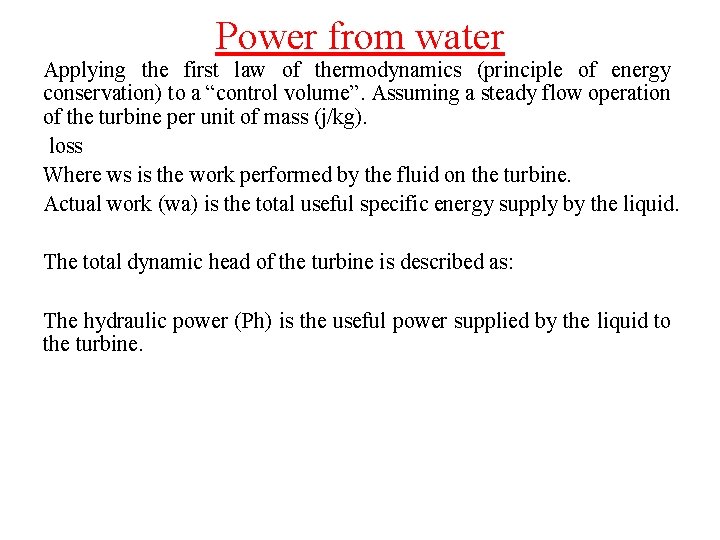
Power from water Applying the first law of thermodynamics (principle of energy conservation) to a “control volume”. Assuming a steady flow operation of the turbine per unit of mass (j/kg). loss Where ws is the work performed by the fluid on the turbine. Actual work (wa) is the total useful specific energy supply by the liquid. The total dynamic head of the turbine is described as: The hydraulic power (Ph) is the useful power supplied by the liquid to the turbine.

OR

Power from water •


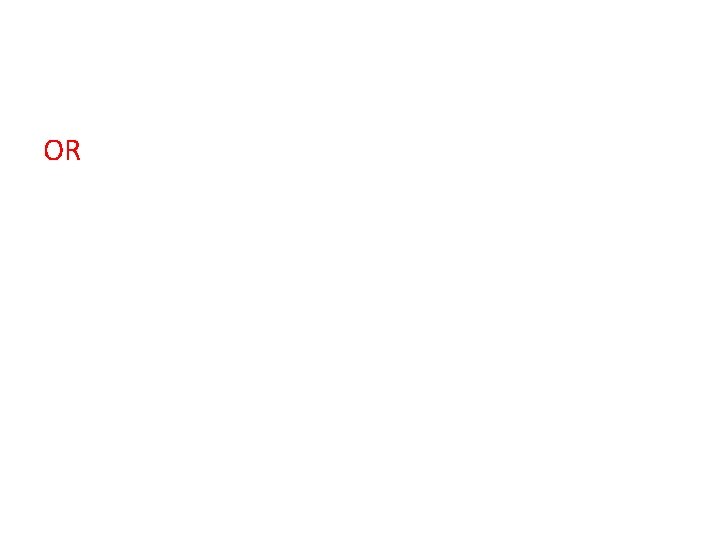
OR

Power from water If a mass M of water falls through a distance H, its loss of potential energy is Mg. H As it falls, the water could be made to do work, and in theory this work would also equal Mg. H In a hydro power plant, the water flows continuously, and the rate of doing work is is the mass flow rate H

Hydro-electric power plant Water collects in the upper reservoir, flows through the turbine and is then discharged at low level. The rate of power production is Generator Turbine ideally, and in practice, where η is the efficiency of the process. In a real system, energy will be dissipated as heat in the generator, the turbine and in the connecting pipelines

Introduction to Hydro power plant






Hg = Gross Head hf = Head Loss due to Friction = Where V = Velocity of Flow in Penstock L = Length of Penstock D = Dia. of Penstock H = Net Head = H g- hf

Layout of a Hydroelectric Power Plant Tail Race Dam Penstock Buckets Nozzle Tail Race Jet of water

Parts Of A Hydroelectric Plant • Dam. Raises the water level of the river to create falling water. Also controls the flow of water. The reservoir that is formed is, in effect, stored energy. This is also known as head race level • Penstock. Pipes of large diameter called Penstocks which carry water under pressure from storage reservoir to the turbines. These pipes are usually made of steel or reinforced concrete. • Turbine. The force of falling water pushing against the turbine's blades causes the turbine to spin. The turbine converts the kinetic energy of falling water into mechanical energy. • Generator. Connected to the turbine by shafts and possibly gears so when the turbine spins it causes the generator to spin also. Converts the mechanical energy from the turbine into electric energy. Generators in hydropower plants work just like the generators in other types of power plants. • Transmission lines. Conduct electricity from the hydropower plant to homes and business • Tailrace which is a channel carrying water away from the turbine after the water has worked on the turbines. The water surface in the tailrace is also referred to as tailrace.


Basic Elements in Hydro Electric Power Plant 1. Reservoir : Reservoir is used to Store Large amount water. 2. Dam : It is Structure of considerable height built across the reservoir. It develops a reservoir to store water & Built Head for power generation. 3. Trash Rack : It is provided for preventing entry of debris like dust, dirt etc. from the dam. Because it may damage to turbine blades & Chock the flow. 4. Gate : It is provided to control the flow of water from the reservoir to the turbine. 5. Penstock : A Pipe which carries water from reservoir to turbine house is called penstock. It is a large of 1 m to 2 m in diameter made up of concrete to withstand high pressure. 6. Turbine : Turbine is used to convert Kinetic Energy to Mechanical Energy.

Head of Turbine Gross Head ( Hg ) It is the difference between head race level and tail race level when no water is flowing. It is also known as total head of the turbine Effective Head or Net Head (H) Net head or effective head is the actual head available at the inlet of the turbine. When water is flowing from head race to the turbine, a loss of head due to friction between water and penstock occurs. Though there are other losses also such as loss due to bend, pipe fittings, loss at entrance of the penstock, etc. These all having small magnitude as compared to head loss due to friction. Euler's Head: It is defined as energy transfer per unit weight H = Hg- hf Where , H = Net head Hg = Gross head hf = Head Loss due to Friction= Where F= cofficient of friction of penstock V = Velocity of Flow in Penstock L = Length of Penstock D = Dia. of Penstock g = acceleration due to gravity

Efficiency of Turbine Hydraulic Efficiency It is the ratio of the power developed by the runner of a turbine to the power supplied by the water at the inlet of a turbine. Since the power supplied is hydraulic, and the probable loss is between the striking jet and vane it is rightly called hydraulic efficiency. Mechanical Efficiency The power delivered by water to the runner of a turbine is transmitted to the shaft of the turbine. It is the ratio of the power available at the shaft of the turbine to the power developed by the runner of a turbine. This depends on the slips and other mechanical problems that will create a loss of energy i. e. friction.
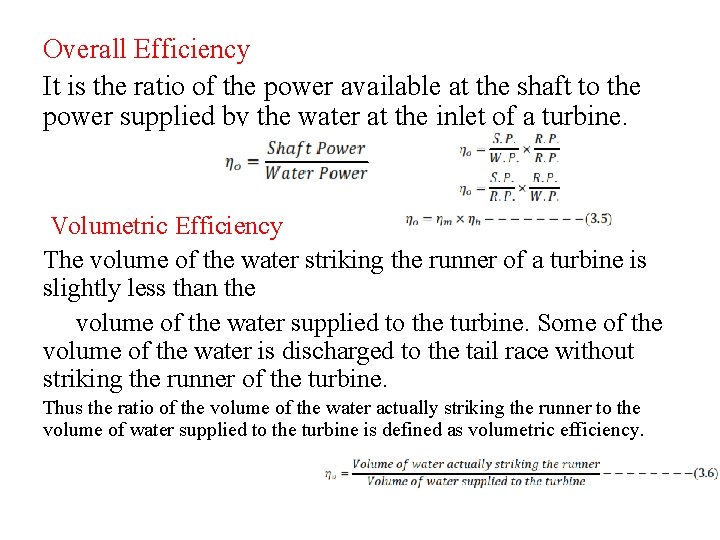
Overall Efficiency It is the ratio of the power available at the shaft to the power supplied by the water at the inlet of a turbine. Volumetric Efficiency The volume of the water striking the runner of a turbine is slightly less than the volume of the water supplied to the turbine. Some of the volume of the water is discharged to the tail race without striking the runner of the turbine. Thus the ratio of the volume of the water actually striking the runner to the volume of water supplied to the turbine is defined as volumetric efficiency.

• Different Efficiencies 1. Mechanical Efficiency 2. Volumetric Efficiency Some quantity of water always misses the bucket and directly passes to the tail race without doing any useful work, hence volumetric efficiency is always less than 100% (97% to 99 %)

3. Overall Efficiency From all efficiencies we have

Losses of Hydraulic Turbines • Various types of losses that occur in a power plant are given below: (a) Head loss in the penstock: This is the friction loss in the pipe of a penstock. (b) Head loss in the nozzle: In case of impulse turbines, there is head loss due to nozzle friction. (c) Hydraulic losses: In case of impulse turbines, these losses occur due to blade friction, eddy formation and kinetic energy of the leaving water. In a reaction turbine, apart from above losses, losses due to friction in the draft tube and disc friction also occur. (d) Leakage losses: In case of impulse turbines, whole of the water may not be striking the buckets and therefore some of the water power may go waste. In a reaction turbine, some of the water may be passing through the clearance between the casing and the runner without striking the blades and thus not doing any work. These losses are called leakage losses. (e) Mechanical losses: The power produced by the runner is not available as useful work of the shaft because some power may be lost in bearing friction as mechanical losses. f) Generator losses: Due to generator loss, power produced by the generator is still lesser than the power obtained at the shaft output.

Classification of Hydraulic Turbines

Classification of Hydraulic Turbines • According to the type of energy at inlet or the action of the water on the blade – Impulse turbine • In an Impulse turbine, all the available energy of the water is converted into kinetic energy or velocity head by passing it through a convergent nozzle provided at the end of penstock. • So at the inlet of the turbine, only kinetic energy is available. • Here the pressure of water flowing over the turbine blades remains constant. (i. e. atmospheric pressure) • Examples: Pelton wheel, Turgo-impulse turbine, Girard turbine, Banki turbine, Jonval. – Reaction turbine • In a reaction turbine, at the entrance to the runner, only a part of the available energy of water is converted into kinetic energy and a substantial part remains in the form of pressure energy. • So at the inlet of the turbine, water possesses kinetic energy as well as pressure energy. • As the water flows through the turbine blades, the change from pressure energy to kinetic energy takes place gradually. • For this gradual change of pressure, the runner must be completely enclosed in an airtight casing and the passage should be full of water. • The difference of pressure between the inlet and outlet of the runner is called reaction pressure, and hence these turbines are known as reaction turbine. • Examples: Francis turbine, Kaplan turbine, Propeller turbine, Thomson turbine,

According to the direction of flow through runner Tangential flow turbine In tangential flow, the water strikes the runner in the direction of tangent to the path of rotation of runner. OR The water strikes the vane/bucket along the tangent of the runner. Example: Pelton wheel Radial flow turbine In radial flow, water flows through the turbine along the direction normal to the axis of rotation (i. e. radial direction). A radial flow turbine is further classified as inward or outward flow depending upon whether the flow is inward from the periphery to the center or outward from center to periphery. Example: Old Francis turbine Axial flow turbine In an axial flow, water flows along the direction parallel to the axis of rotation of the runner. Here water flows parallel to the turbine shaft. Examples: Kaplan turbine, Propeller turbine Mixed flow turbine In mixed flow, water enters the runner in the radial direction and leaves in the direction parallel to the axis of rotation (i. e. axial direction). Example: Modern Francis turbine.

According to the head at the inlet of the turbine High head turbines which operates under high head (above 250 m) and requires relatively less quantity of water. Example: Pelton wheel turbine Medium head turbines which operate under medium head (60 m to 250 m) and require medium flow rate. Example: Modern Francis turbine Low head turbines which operate under head up to 30 m and require very large quantity of water. Example: Kaplan and Propeller turbine According to specifice speed Low specific speed turbine For Pelton wheel turbine with single jet, For Pelton wheel turbine with double jet, Medium specific speed turbine For Francis turbine, High specific speed turbine Kaplan and other Propeller turbine,

OR

Types of turbines Turbines can be classified on the basis of: • Head and quantity of water available • Hydraulic action of water • Direction of flow of water in the runner • Specific speed of turbines • Disposition of the shaft of the runner

Classification of turbines • Based on head and quantity of water According to head and quantity of water available, the turbines can be classified into a) High head turbines b) Medium head turbines c) Low head turbines a) High head turbines are the turbines which work under heads more than 250 m. The quantity of water needed in case of high head turbines is usually small. The Pelton turbines are the usual choice for high heads. b) Medium head turbines The turbines that work under a head of 45 m to 250 m are called medium head turbines. It requires medium flow of water. Francis turbines are used for medium heads. c) Low head turbines Turbines which work under a head of less than 45 m are called low head turbines. Owing to low head, large quantity of water is required. Kaplan turbines are used for low heads.

Classification of turbines • Based on hydraulic action of water According to hydraulic action of water, turbines can be classified into a) Impulse turbines b) Reaction turbines a) Impulse turbines If the runner of a turbine rotates by the impact or impulse action of water, it is an impulse turbine. b) Reaction turbines These turbines work due to reaction of the pressure difference between the inlet and the outlet of the runner.

Classification of turbines • Based on direction of flow of water in the runner Depending upon the direction of flow through the runner, following types of turbines are there a) Tangential flow turbines b) Radial flow turbines c) Axial flow turbines d) Mixed flow turbines a) Tangential flow turbines When the flow is tangential to the wheel circle, it is a tangential flow turbine. A Pelton turbine is a Tangential flow turbine. b) Radial flow turbines In a radial flow, the path of the flow of water remains in the radial direction and in a plane normal to the runner shaft. No pure radial flow turbine is in use these days. c) Axial flow turbines When the path of flow water remains parallel to the axis of the shaft, it is an axial flow turbine. The Kaplan turbine is axial flow turbine d) Mixed flow turbines When there is gradual change of flow from radial to axial in the runner, the flow is called mixed flow. The Francis turbine is a mixed flow turbine.

Classification of turbines • Based on specific speed of turbines Specific speed of a turbine is defined as the speed of a geometrically similar turbine which produces a unit power when working under a unit head. The specific speed of Pelton turbine ranges between 8 -30, Francis turbines have specific speed between 50 -250, Specific speed of Kaplan lies between 250 -850. • Based on disposition of shaft of runner Usually, Pelton turbines are setup with horizontal shafts, where as other types have vertical shafts.

Pelton Wheel It is impulse , tangential flow, high head and law specific turbine. It require comparatively less quantity of water. A pelton wheel name after the American engineer lester pelton who contriute much to its development. The energy available at inlet is only kinetic energy. therefore it is a tangential flow impulse turbine. It is used with heads of more than 500 m. A head is the distance by which the water falls before it strikes the turbine blades The flow of water is tangential to the runner. So it is a tangential flow impulse turbine. A Pelton’s runner consists of a single wheel mounted on a horizontal shaft. Water falls towards the turbine through a pipe called penstock and flows through a nozzle. The high speed jet of water coming out from the nozzle hits the buckets (vanes) on the wheel and causes the wheel to rotate producing torque and power. The Pelton wheel extracts energy from the impulse (momentum) of moving water as opposed to its weight like traditional overshot water wheel.

Pelton Wheel


Runner of a Pelton Turbine BUCKETS OR VANES SPLITTER RUNNER 47
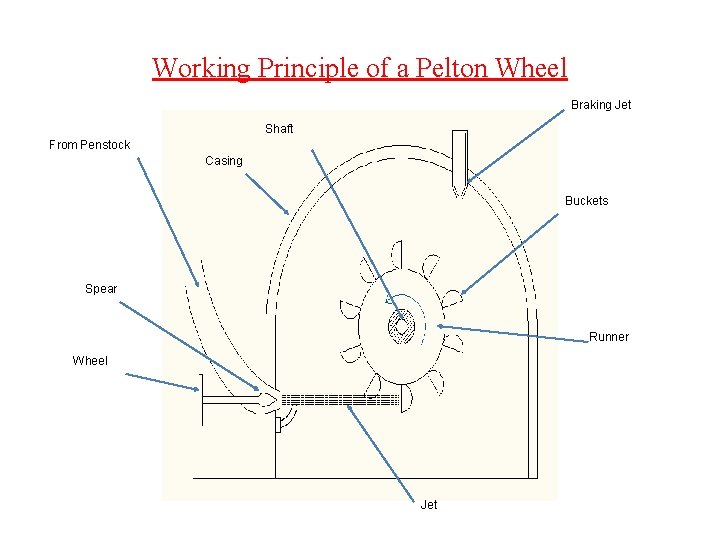
Working Principle of a Pelton Wheel Braking Jet Shaft From Penstock Casing Buckets Spear Runner Wheel Jet

Pelton Wheel rated at 117 MW under a head of 686 m

Pelton Wheel Pelton wheel is generally used at a very high head and low discharge. Components of Pelton Wheel Nozzle and Flow Regulating Arrangement (Spear) Runner and Buckets Casing and Breaking Jet Nozzle and Flow Regulating Arrangement (Spear) Depending on load fluctuations, the speed of the turbine is to be kept constant by controlling the quantity of water flowing through the nozzle.

Spear and needle arrangement with nozzle The amount of water striking the buckets of the runner is controlled by providing a spear in the nozzle as shown in Fig. The spear is a conical needle which is operated either by a hand wheel or automatically by governor in an axial direction depending upon the size of the unit. Spear reciprocates in nozzle and hence changes the annular area through which water can pass. When the spear is pushed forward into the nozzle, the amount of water striking the runner is reduced. On the other hand, if the spear is pushed back, the amount of water striking the runner increases.

• Runner and Buckets • It consists of a circular disc, on the periphery of which a number of buckets evenly spaced are fixed. • The shape of the buckets is of a double hemispherical cup or bowl. Each bucket is divided into two symmetrical parts by a dividing wall which is known as splitter. • The jet of water strikes on the splitter. The splitter divides the jet into two equal parts and the jet comes out at the outer edge of the bucket. • The buckets are shaped in such a way that the jet gets deflected through 160° or 170°. Maximum work is obtained if the jet is deflected through 180° i. e. the bucket is semicircular. • If semicircular bucket is used, an outgoing jet may strikes to the next incoming bucket and hence opposes the motion of the rotor. Hence the angle of jet deflection is generally kept 160° to 170°.

Casing The function of the casing is to prevent the splashing of the water and to discharge water to the tailrace. It also acts as a safe-guard against accidents. Material: Cast iron or fabricated steel plates. The casing of the Pelton wheel does not perform any hydraulic function. Breaking Jet When the nozzle is completely closed by moving the spear in the forward direction, the amount of water striking the runner reduces to zero. But the runner due to inertia goes on revolving for a long time. To stop the runner in a shorter time, a small nozzle is provided which directs the jet of water on the back of the vanes as shown in Fig. 3. 2. This jet of water is called breaking jet.

Working of Pelton Wheel Pelton wheel works on Impulse-Momentum principle. The water from the reservoir (or head race) is conveyed to turbine house through a penstock, at the outlet of which a nozzle is fitted. When water flows through a penstock and comes out of nozzle, all pressure energy and potential energy is converted into kinetic energy. Hence at the outlet of the nozzle, the water out in the form of jet (at atmospheric pressure) and strikes the buckets/vanes of the runner. The impact of water on the bucket makes runner to rotate. Runner is mounted on the shaft and hence mechanical energy is available at the shaft which is coupled with generator, which converts mechanical energy into electrical energy and produce electricity. After performing work on the buckets water is discharged into the tail race.

• Working Principle of Pelton Turbine • High speed water jets emerging from the nozzles (obtained by expanding high pressure water to the atmospheric pressure in the nozzle) strike a series of spoon-shaped buckets mounted around the edge of the pelton wheel. High pressure water can be obtained from any water body situated at some height or streams of water flowing down the hills. • As water flows into the bucket, the direction of the water velocity changes to follow the contour of the bucket. These jets flow along the inner curve of the bucket and leave it in the direction opposite to that of incoming jet. When the water-jet contacts the bucket, the water exerts pressure on the bucket and the water is decelerated as it does a "u-turn" and flows out the other side of the bucket at low velocity. • The change in momentum (direction as well as speed) of water jet produces an impulse on the blades of the wheel of Pelton Turbine. This "impulse" does work on the turbine and generates the torque and rotation in the shaft of Pelton Turbine.

• To obtain the optimum output from the Pelton Turbine the impulse received by the blades should be maximum. For that, change in momentum of the water jet should be maximum possible. This is obtained when the water jet is deflected in the direction opposite to which it strikes the buckets and with the same speed relative to the buckets. • For maximum power and efficiency, the turbine system is designed such that the water-jet velocity is twice the velocity of the bucket. A very small percentage of the water's original kinetic energy will still remain in the water. However, this allows the bucket to be emptied at the same rate at which it is filled, thus allowing the water flow to continue uninterrupted. • Often two buckets are mounted side-by-side, thus splitting the water jet in half (see photo). The high speed water jets emerging form the nozzles strike the buckets at splitters, placed at the middle of the buckets, from where jets are divided into two equal streams. • This balances the side-load forces on the wheel, and helps to ensure smooth, efficient momentum transfer of the fluid jet to the turbine wheel. • Because water and most liquids are nearly incompressible, almost all of the available energy is extracted in the first stage of the hydraulic turbine. • Therefore, Pelton wheels have only one turbine stage, unlike gas turbines that operate with compressible fluid.


• Velocity Triangles, Work done and Efficiency of Pelton Wheel • The jet of water from the nozzle strikes the bucket at the splitter, which splits up the jet into two parts. • These parts of the jet, glides over the inner surfaces and comes out at the outer edge of the bucket. • The splitter is the inlet tip and outer edge of the bucket is the outlet tip of the bucket.





velocity at maximum hydraulic efficiency : V = u 1/2



Inlet diagram

Outlet diagram (since jet is striking series of buckets) 1)Force exerted by jet in direction of motion is , β < 90°, Vw 2 = -ve

2) Work done by jet on runner per second, W 3) Power developed, P 4) Hydraulic Efficiency(Bucket Efficiency), 5) Maximum Hydraulic efficiency from inlet diagram from outlet diagram

Substitute above values in efficiency equation we get, d. w. r. t ‘u’ to the above equation for maximum hydraulic efficiency…. . we get…………………. . We observe that the maximum hydraulic efficiency of a Pelton Wheel occurs when the velocity of runner is half the velocity of the jet Putting value of u in maximum efficiency equation we get If friction is neglected then K=1 For a hemispherical bucket the deflection angle is 180°, hence φ = 0°

Design of Pelton wheel Design of the Pelton wheel means following data is to be determine: a) Diameter of the jet (d) b) Diameter of wheel (D) c) Width of bucket = 5 x d) d) Depth of the bucket = 1. 2 x d e) No of buckets on the wheel = total rate of flow through the turbine/ rate of flow of water through a single jet.


Dimensions of bucket • The minimum possible width B of the bucket is approximately 2 d, where d is the diameter of jet. This dimension is usually taken as 2. 8 to 3. 2 d to avoid losses. Some prefer to take it as 3 to 4 d. • The depth of the bucket (T) usually lies between 0. 8 to 1. 2 d. • The height (H) of the bucket is 2. 4 to 2. 8 d. • Other dimensions of the bucket are taken as below: E = 1. 2 d F = 0. 4 d G = 0. 9 to 1. 0 d βi = 3 – 6 degrees βo = 10 - 20 degrees


Diameter of Jet • The velocity of jet out of a nozzle is given by, where, Vi = Velocity of jet Cv = Coefficient of velocity for the nozzle; value lies between 0. 96 – 0. 99 d = diameter of the jet Discharge through the nozzle,
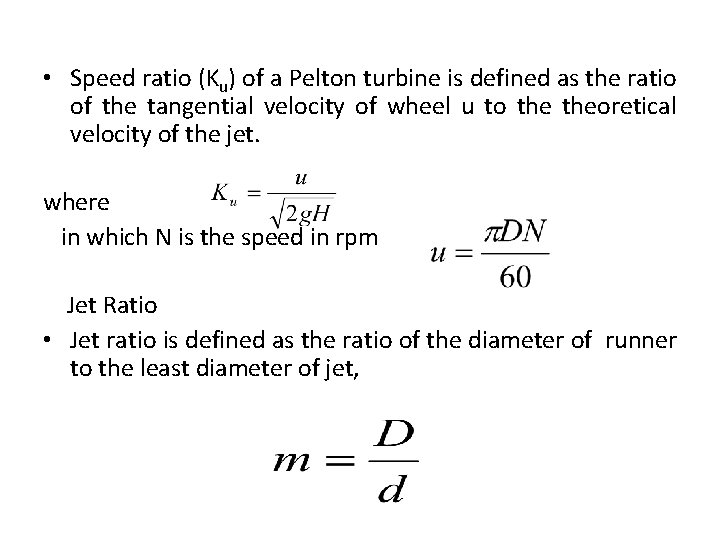
• Speed ratio (Ku) of a Pelton turbine is defined as the ratio of the tangential velocity of wheel u to theoretical velocity of the jet. where in which N is the speed in rpm Jet Ratio • Jet ratio is defined as the ratio of the diameter of runner to the least diameter of jet,

Design Aspects an important points of a Pelton wheel • Velocity of the jet, V 1 H=net head over turbine • Velocity of wheel, u Cv= 0. 97 to 0. 98 • Speed Ratio, Ku • Jet Ratio, m Varies from 0. 43 to 0. 47 Varies from 11 to 15, mostly taken as 12
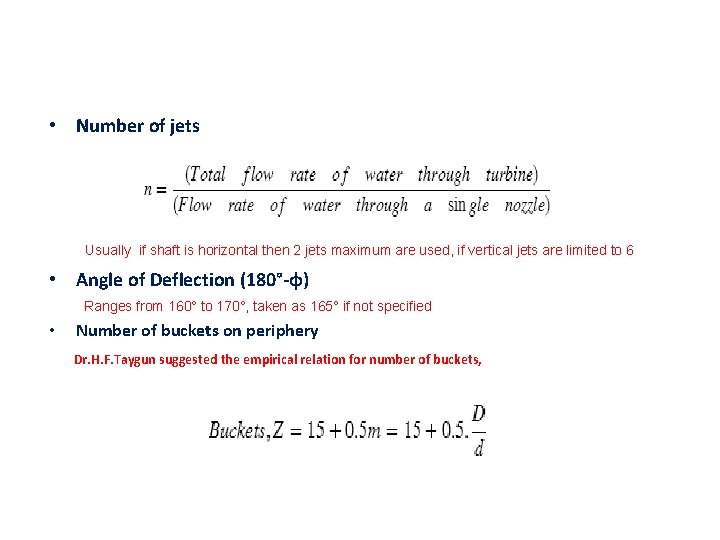
• Number of jets Usually if shaft is horizontal then 2 jets maximum are used, if vertical jets are limited to 6 • Angle of Deflection (180°-φ) Ranges from 160° to 170°, taken as 165° if not specified • Number of buckets on periphery Dr. H. F. Taygun suggested the empirical relation for number of buckets,

Governing of Hydraulic Turbines The governing of a turbine is defined as the operation by which the speed of the turbine is kept constant under all working conditions (irrespective of the load variation) Governing of a turbine is necessary as, a turbine is directly coupled to an electric generator, which is required to run at constant speed under all fluctuating loads conditions. It is done automatically by means of a governor, which regulates the rate of flow through the turbines according to the changing load conditions on the turbine. The governor used in hydraulic turbines should be very strong as it has to deal with the water coming at very large force and huge quantity. • Functions: • Control speed of turbine with fluctuating load at synchronous speed of generator. • Synchronous speed is the constant speed of the generator

Why governing of hydraulic turbines is required? ? ? As turbine is directly coupled to the electric generator which is required to run at constant sped. The load on turbine is not constant through out the day or hour, hence speed of turbine varies with respect to load at constant head and discharge . Therefore in order to have constant speed of generator , governing of turbine is required to maintain the constant speed of turbine with respect to load. Main part for governing of pelton wheel…. 1 Centrifugal governor 2 Oil pump-gear pump with oil sump 3 Relay or control valve 4 Servomotor with spear rod and spear 5 Deflector mechanism.

Governor and linkages : • A centrifugal governor is used as the measuring element of the closed loop control system. It is driven by the turbine shaft through bevel gears. The sleeve of the governor is connected through linkages to relay valve. The movement of is transferred through the lever to move the piston rod of relay valve • Oil pump and oil sump : . System uses oil in servomotor or relay cylinder since the force required to actuate the spear valve would be enormous. For this reason, the system requires an oil sump to store the oil and an oil pump to regulate the oil supply in the mechanism. Oil pump is a positive displacement type of pump like gear pump or axial piston pump. lt's function is to pressurize the oil.

Relay or control valve : Relay valve is a spool valve having 5 ports. It is also called as control valve or distributor valve. It receives the pressurised oil from the oil pump which is diverted towards the ports to pipe A or pipe B. Through these pipes the oil is transferred to corresponding sides of double` acting servomotor cylinder. Simultaneously, the oil will be returned from the servomotor from the opposite pipe to the sump. System uses oil in servomotor or relay cylinder since the force required to actuate the spear valve would be enormous. For this reason, the system requires an oil sump to store the oil and an oil pump to regulate the oil supply in the mechanism. Oil pump is a positive displacement type of pump like gear pump or axial piston pump. lt's function is to pressurize the oil. Servomotor or relay cylinder : It is a double acting cylinder which acts as hydraulic actuator. It receives oil from relay valve say through pipe A. The piston of the cylinder will be displaced towards left, thus forcing the oil through the pipe B into the relay valve and finally to oil sump. It will simultaneously more the spear valve to the left and increase the area of flow through the nozzle.



Working: When the load on the generator decreases, the speed of the generator increases. Hence speed of the turbine also increases beyond the normal speed. The centrifugal governor which is connected to the turbine main shaft will be rotating at an increased speed and hence centrifugal force on the fly ball increases and it moves upward. Sleeve of the governor will also moves upward. As the sleeve moves upward, a horizontal lever turns about the fulcrum and the piston rod of the control valve moves downward. This closes the valve V 1 and opens the valve V 2 as shown in fig The oil pumped from the oil pump to the control valve under pressure will flow through the valve V 2 to the servomotor and will exert force on the face A of the piston of the relay cylinder. Piston along with piston rod and spear will move towards right. This will decrease the area of flow of water at the outlet of the nozzle and it will reduce the rate of flow to the turbine which consequently reduces the speed of the turbine. Mean while bell crank lever moves downward, the jet deflector will operate and divert whole or part of the jet away from the buckets. As soon as speed becomes normal, the fly balls, sleeves, lever and piston rod come to its normal position.
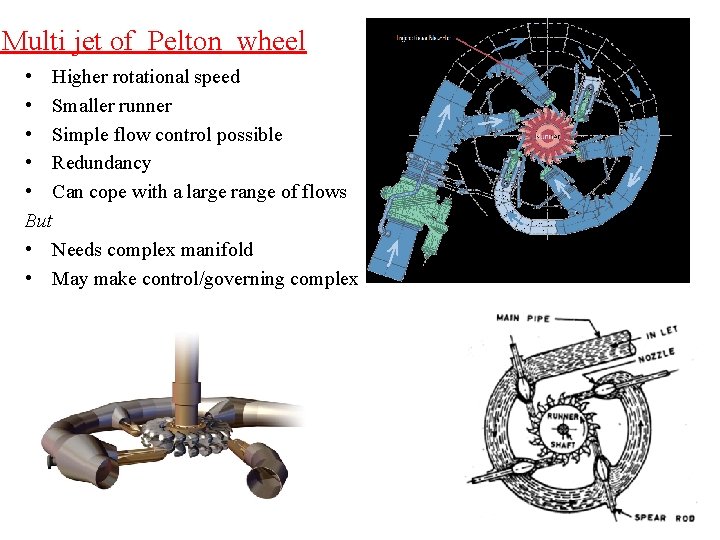
Multi jet of Pelton wheel • Higher rotational speed • Smaller runner • Simple flow control possible • Redundancy • Can cope with a large range of flows But • Needs complex manifold • May make control/governing complex

Number of Jets • Number of jets may be increased, usually upto 4, but never more than 6 because higher number of jets makes the governing complicated.
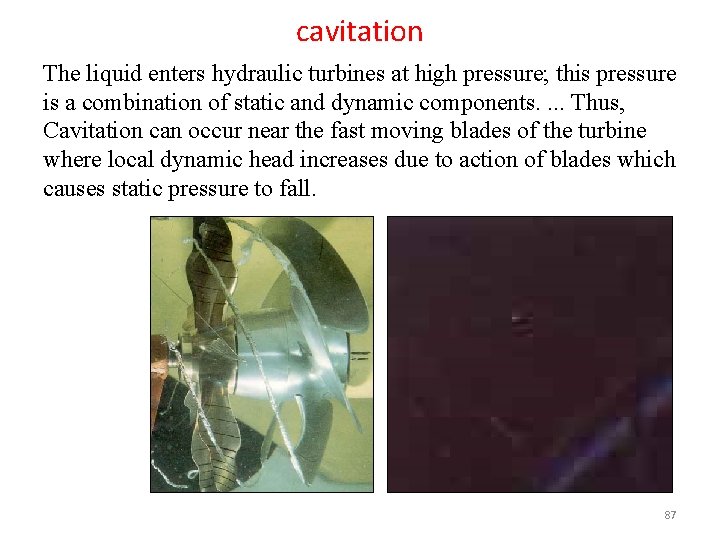
cavitation The liquid enters hydraulic turbines at high pressure; this pressure is a combination of static and dynamic components. . Thus, Cavitation can occur near the fast moving blades of the turbine where local dynamic head increases due to action of blades which causes static pressure to fall. 87
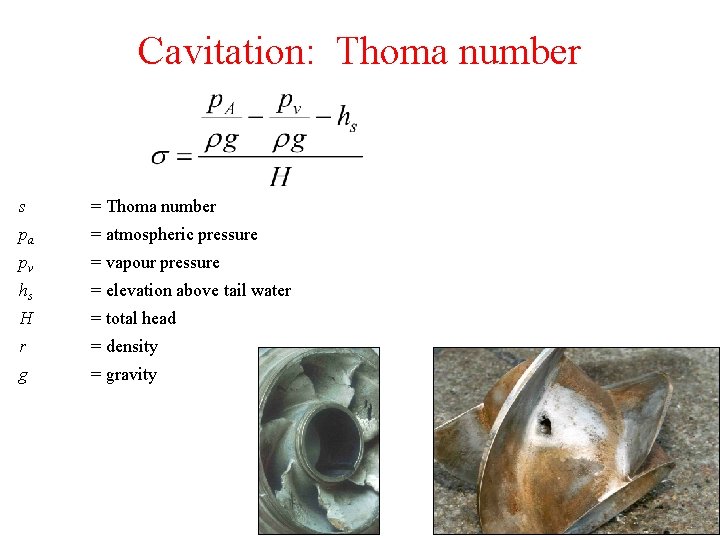
Cavitation: Thoma number s = Thoma number pa = atmospheric pressure pv = vapour pressure hs = elevation above tail water H = total head r = density g = gravity

Difference between Impulse and Reaction Turbine In Hydro-Electric Power Plant mainly Impulse or Reaction Turbines are used to generate electric power. From the engineering point of view both have some differences in working or parts. Here in this article I am trying to share the knowledge with you. Main Differences of Impulse and Reaction Turbine 1) In impulse turbine the water flows through the nozzles and impinges on the buckets where as in reaction turbine the water is guided by the guide blades to flow over the moving vanes. 2) In impulse turbine the entire water energy is first converted in kinetic energy but there is no energy conversion in reaction turbine. 3) ) In impulse turbine the water impinges on the buckets with kinetic energy where as in reaction turbine the water glides over the moving vanes with pressure energy.

4) In impulse turbine the work is done only by the change in the kinetic energy of the jet but in reaction turbine the work is done partly by the change in the velocity head, but almost entirely by the change in pressure head. 5) In impulse turbine the pressure of flowing water remains unchanged and is equal to the atmospheric pressure but in reaction turbine the pressure of flowing water is reduced after gliding over the vanes. 6) In impulse turbine it is not essential that the wheel should run full. Moreover, there should be free access of air between the vanes and the wheel where as it is essential that the wheel should always run full and kept full of water in reaction turbine. 7) In impulse turbine the water may be admitted over a part of the circumference or over the whole circumference of the wheel but in reaction turbine the water must be admitted over the whole circumference of the wheel. 8) It is possible to regulate the flow of water without loss in impulse turbine but in reaction turbine it is not possible to regulate the flow without loss.

Applications of Pelton Wheel • Pelton wheels are the preferred turbine for hydro-power, when the available water source has relatively high hydraulic head at low flow rates. • Pelton wheels are made in all sizes. There exist multi-ton Pelton wheels mounted on vertical oil pad bearings in hydroelectric plants. • The largest units can be up to 200 megawatts. The smallest Pelton wheels are only a few inches across, and can be used to tap power from mountain streams having flows of a few gallons per minute. • Depending on water flow and design, Pelton wheels operate best with heads from 15 meters to 1, 800 meters, although there is no theoretical limit. • Pelton wheel is most efficient. Thus, more power can be extracted from a water source with high-pressure and low-flow than from a source with low-pressure and high-flow. • These small units are recommended for use with thirty meters or more of head, in order to generate significant power levels.

Selection of water turbine • Hydropower turbines use water pressure to rotate its blades and generate energy. Selecting the appropriate type of turbine depends primarily on available head and less so on available flow rate. The three primary types of turbines are: the Pelton turbine, for high heads; the Francis turbine, for low to medium heads; and the Kaplan turbine for a wide range of heads. Several other types of turbines exist on the market, described below. • To understand the operating characteristics of the reaction and impulse turbines encompassed in their governing mechanical laws that predicts their work and performance. • Demonstrate the mechanism of the turbine-speed control in relationship with the various forms of energy explained in the mechanical laws that predicts their behavior. 9/17/2020 Mahesh Kumar(ME Deptt. ) 92

Selection of a type of turbine : The selection of the best turbine for any particular hydro site depends on the site characteristics, the dominant ones being the head and flow available. Selection also depends on the desired running speed of the generator or other device loading the turbine. Other considerations such as whether the turbine is expected to produce power under part-flow conditions also play an important role in the selection. All turbines have a power-speed characteristic. They will tend to run most efficiently at a particular speed, head and flow combination. In large scale hydro installation Pelton turbines are normally only considered for heads above 150 m, but for micro-hydro applications Pelton turbines can be used effectively at heads down to about 20 m. Pelton turbines are not used at lower heads because their rotational speeds become very slow and the runner required is very large and heavy. If runner size and low speed do not pose a problem for a particular installation, then a Pelton turbine can be used efficiently with fairly low heads. If a higher running speed and smaller runner are required then there are two further options • Increasing the number of jets. Having two or more jets enables a smaller runner to be used for a given flow and increases the rotational speed. The required power can still be attained and the part-flow efficiency is especially good because the wheel can be run on a reduced number of jets with each jet in use still receiving the optimum flow. • Twin runners. Two runners can be placed on the same shaft either side by side or on opposite sides of the generator. This configuration is unusual and would only be used if number of jets per runner had already been maximized, but it allows the use of smaller diameter and hence faster rotating runners.

Characteristic curves of a Turbine These are curves which are characteristic of a particular turbine which helps in studying the performance of the turbine under various conditions. These curves pertaining to any turbine are supplied by its manufacturers based on actual tests. The data that must be obtained in testing a turbine are the following: 1. The speed of the turbine N 2. The discharge Q 3. The net head H 4. The power developed P 5. The overall efficiency 6. Gate opening (this refers to the percentage of the inlet passages provided for water to enter the turbine) The characteristic curves obtained are the following: a)Constant head curves or main characteristic curves b)Constant speed curves or operating characteristic curves c)Constant efficiency curves or Muschel curves



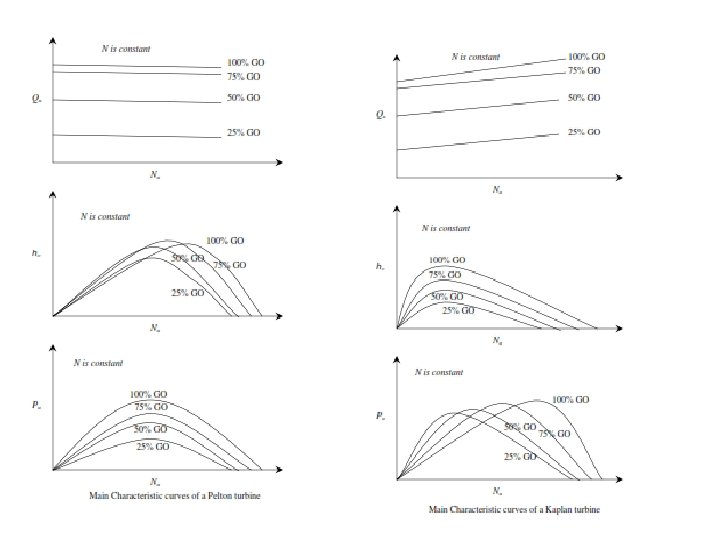


Main Characteristics 1) • Discharge unaffected by speed of the rotor • Jet comes out as a free jet from the casing of the turbine Unit speed vs Unit discharge

2) • Power increases first to maximum with the increase in speed and then decreases with the increase in speed • This is due to the fact that the as the speed of the rotor increases the jet does not have enough time to make an impact on the buckets. Unit speed vs Unit Power

3) • Similar to the Unit discharge vs unit speed graph. • Two extreme speeds at which efficiency is zero. • Highest speed called as runaway speed Unit Speed vs Overall Efficiency

Operating Characteristics/Constant Speed characteristics 1) • Maximum Efficiency at 20 % to 30 % of load and constant afterwards Load vs efficiency

Operating Characteristics/Constant Speed characteristics………. . 2) • Discharge increases parabolically • Output varies linearly • Power is zero for initial discharge as it is lost in overcoming the friction and inertia effects of the rotating parts

Iso efficiency curves • The Turbine is tested under a constant head H, for each of several gate openings, and the values of Power output, P and speed, N are reduced to unit conditions

Specific speed (Ns) It is the speed of a turbine which is identical in shape, geometrical dimension, blade angles, gate opening etc. with the actual turbine but of such a size that it will develop unit power when working under unit head. It is used in comparing the different types of turbines as every type of turbine has different specific speed. It plays an important role for selecting the type of the turbine & predicting the performance of turbine. Consider P as the power developed by the turbine. • • • Where N = specific speed of turbine, H= Head, N= speedof the turbine, and P= power developed by the turbine Use: To predict the performance of a turbine and to compare different types of turbine


In above eqn, if P is taken in metric horse power, the specific speed is obtained in MKS units. But if P is taken in kilowatts, the specific speed is obtained in SI units.

Unit Quantities The results of a turbine when expressed in terms of unit head, unit discharge and unit power output are called as results on unit quantities. • The conditions of turbine under unit head are such that the efficiency of turbine remains unaffected. 1) Unit Head Defined as the speed of a turbine working under a unit head (under 1 m head) denoted by Nu N = speed of turbine under head H H = head under which a turbine is working u = tangential velocity Derivation: where so where D is diameter of the wheel

For a given turbine the diameter (D) is a constant Now if head on the turbine becomes unity the speed becomes unit speed or Using these values in the equation of K 1 we get

2) Unit Discharge Defined as discharge passing through a turbine working under a unit head (under 1 m head) denoted by Qu Q = Discharge passing through the turbine when head H is on the turbine H = head under which a turbine is working a = area of flow of water Derivation:

2) Unit Power Defined as power developed by a turbine working under a unit head (under 1 m head) denoted by Pu Q = Discharge passing through the turbine when head H is on the turbine H = head under which a turbine is working P= Power developed by the turbine under a head H Derivation: Hence for similarly designed turbines we can write,
- Slides: 112