UNIT 6 Unit 6 Fasteners Lesson 1 Nut
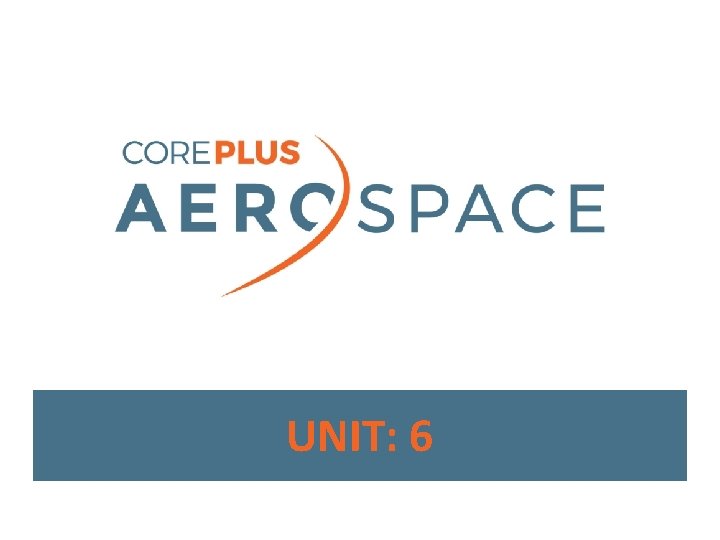
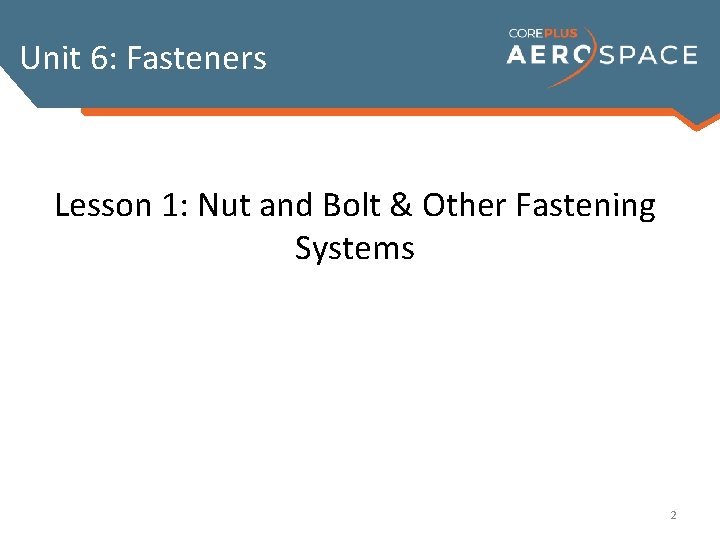
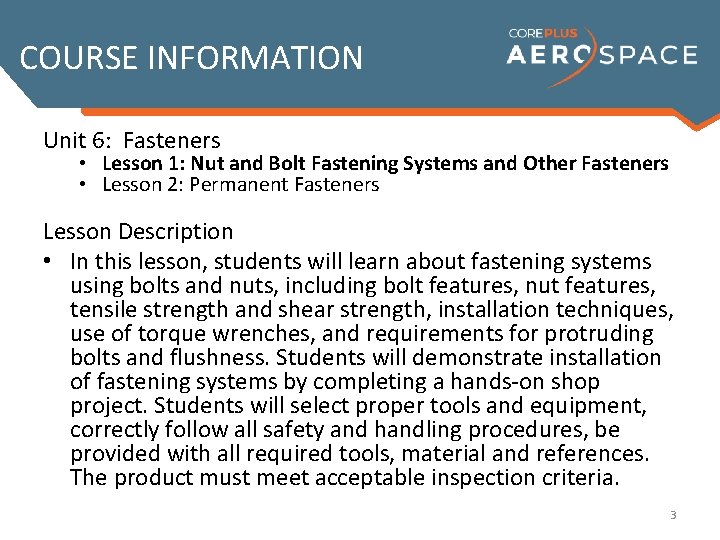
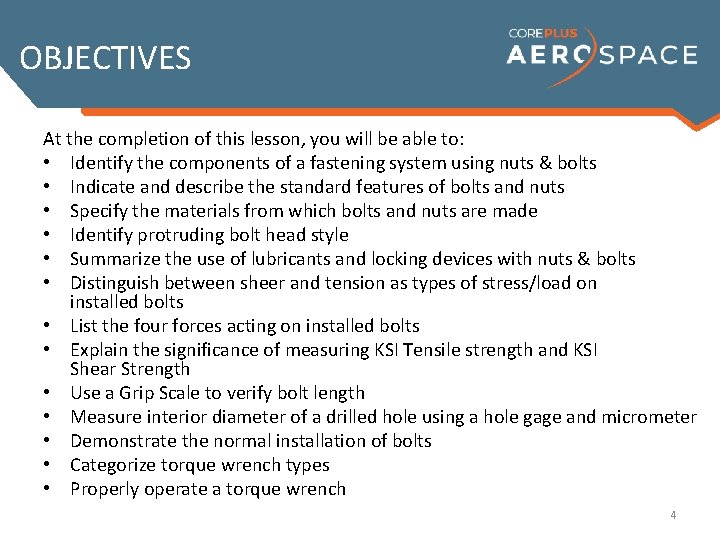
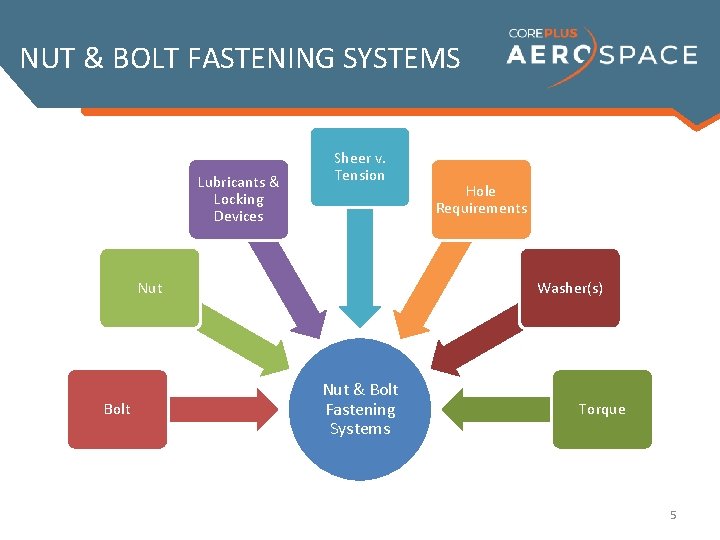
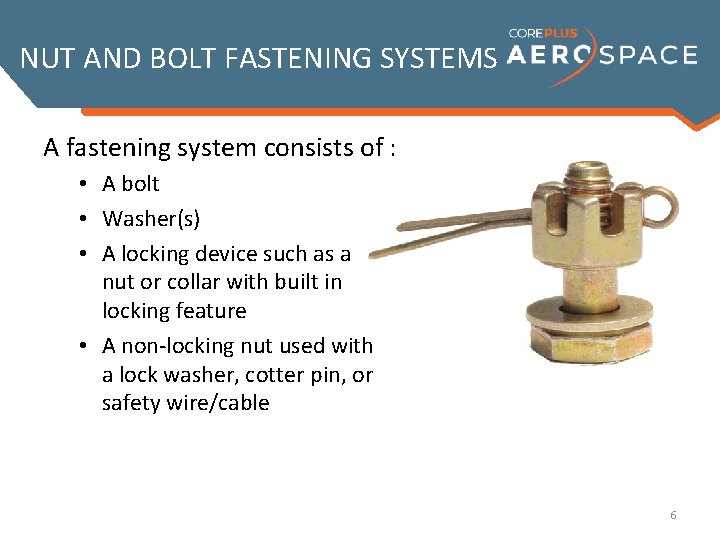
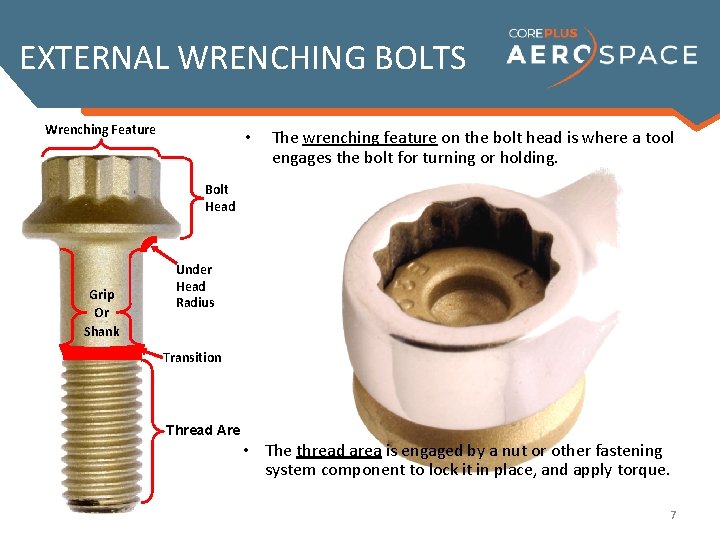
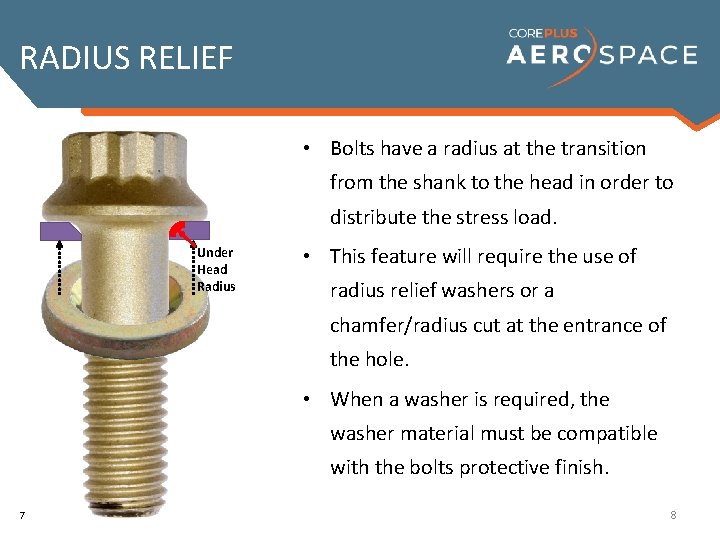
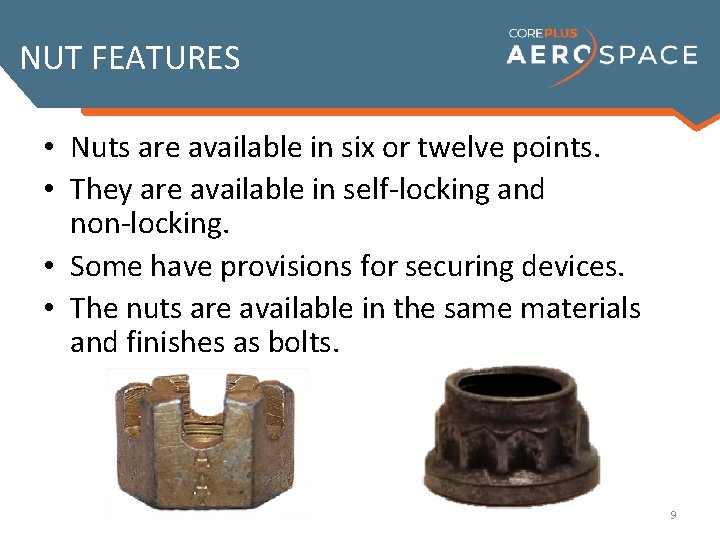
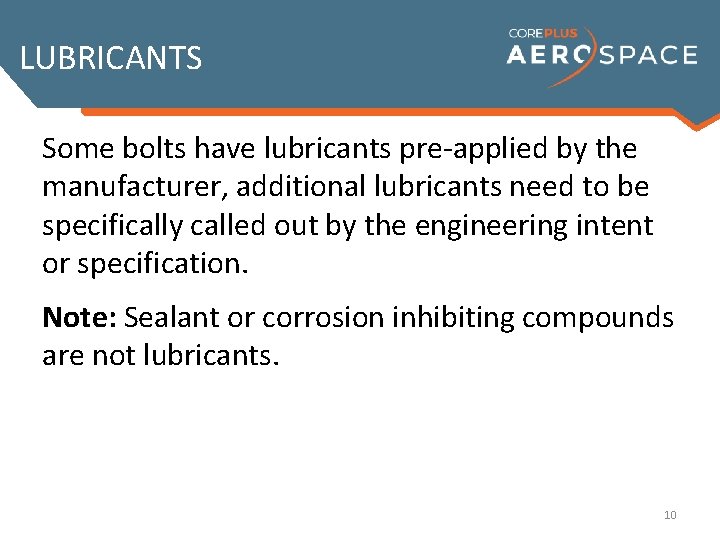
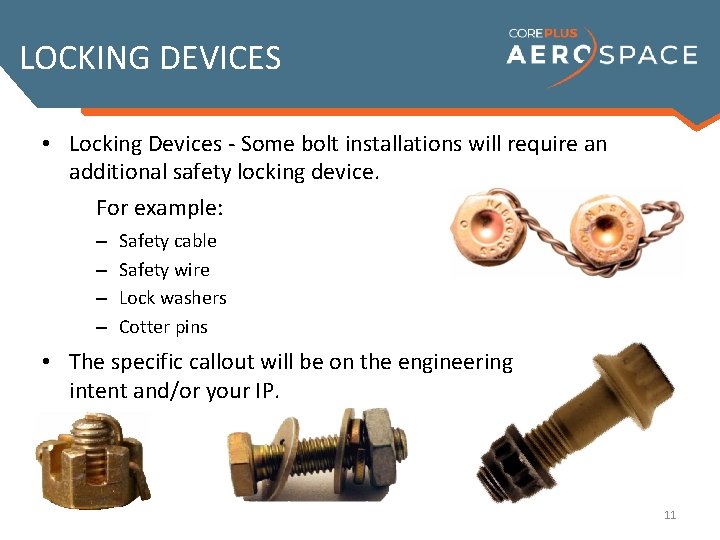
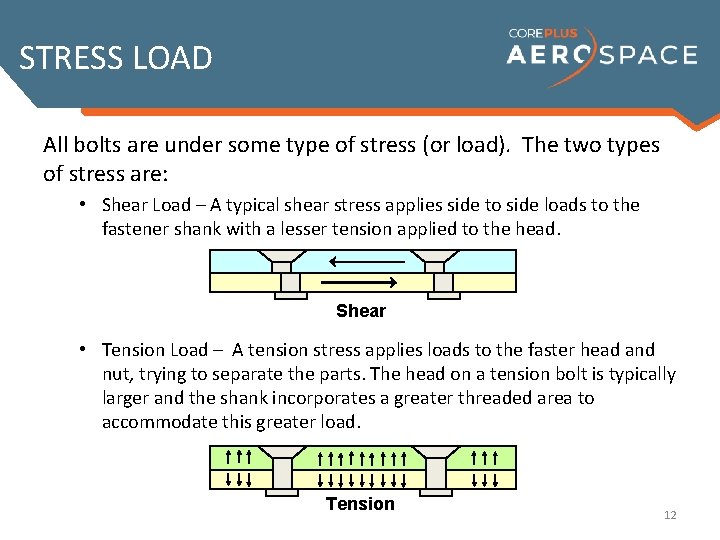
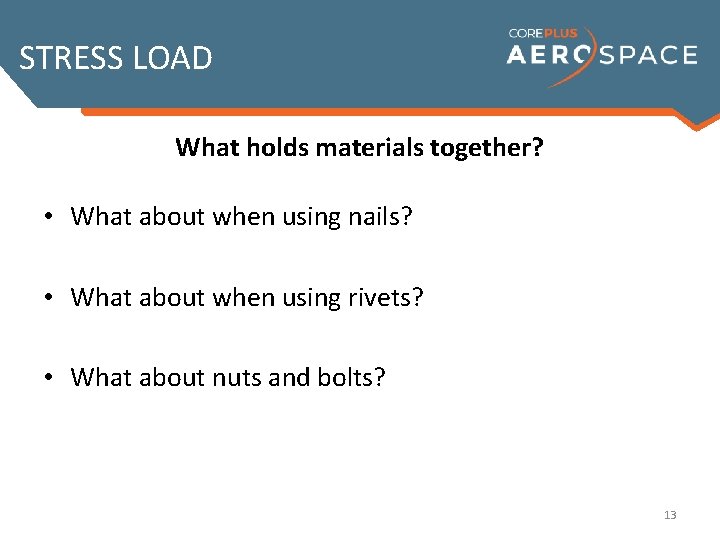
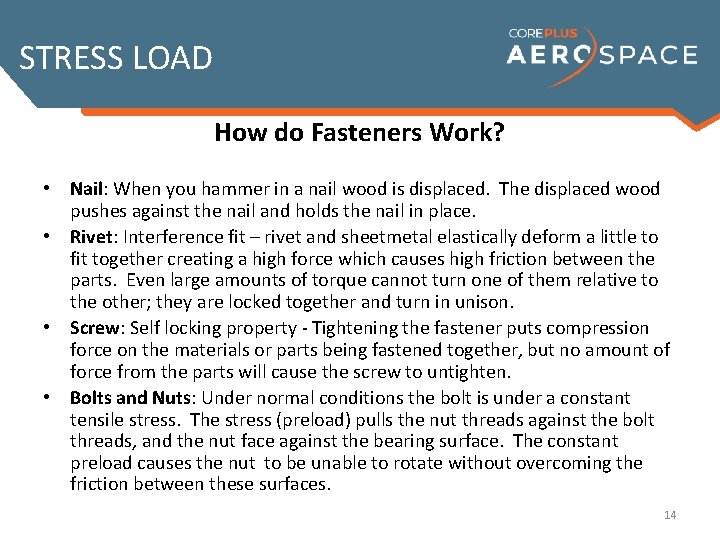
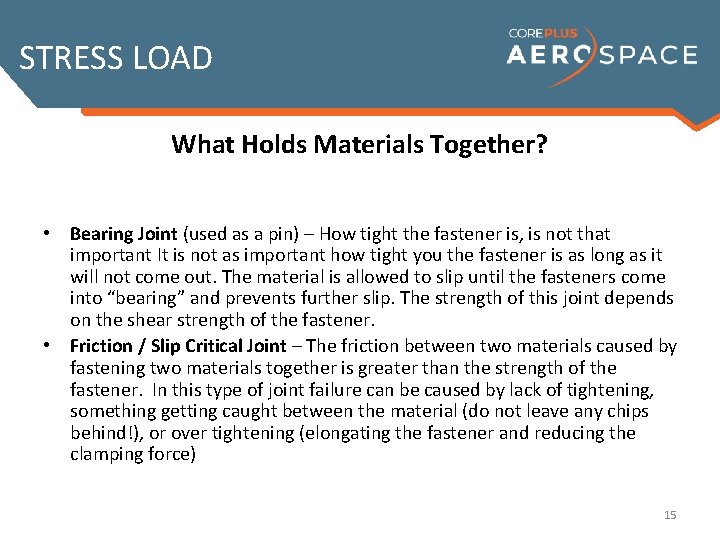
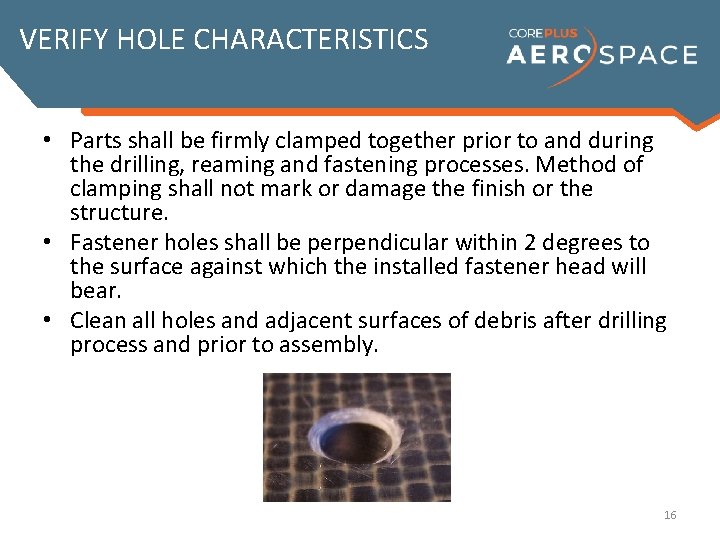
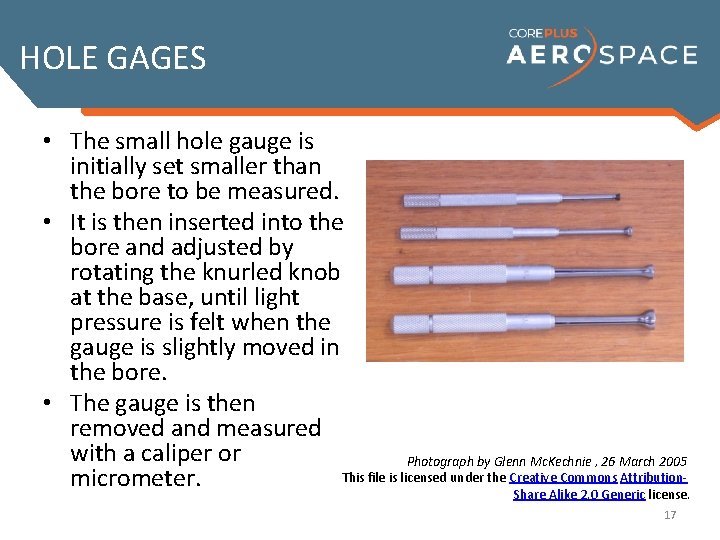
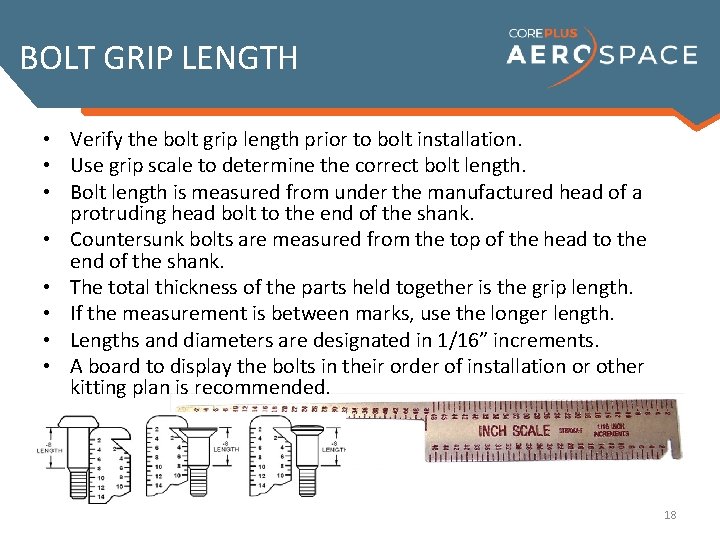
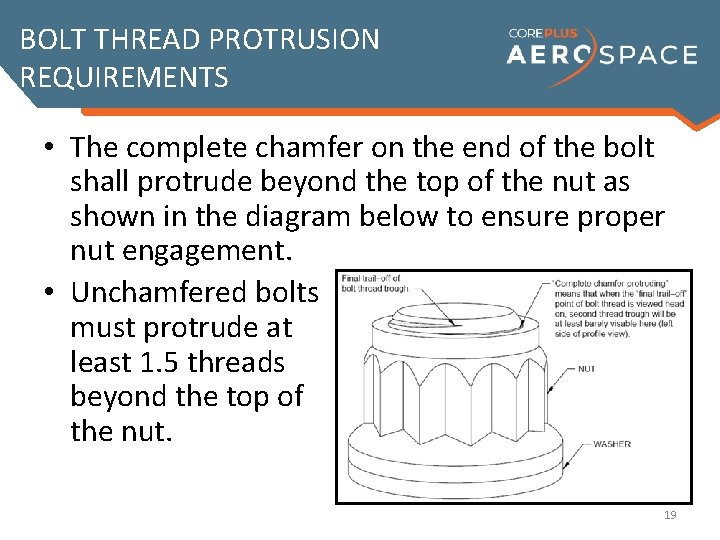
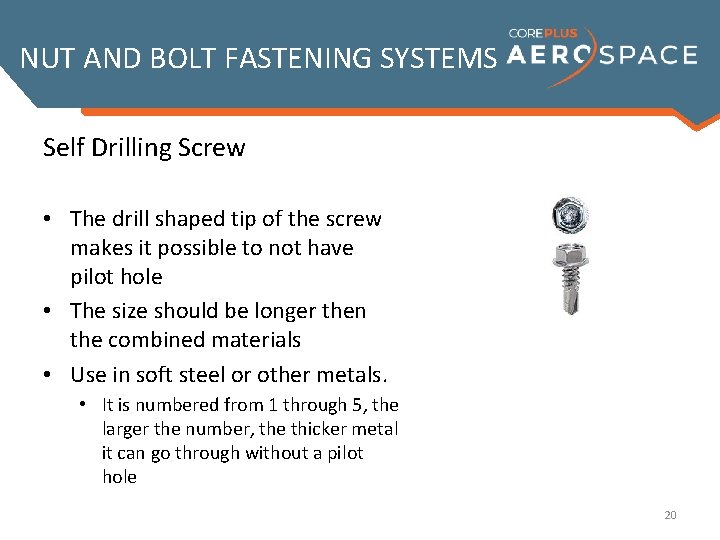
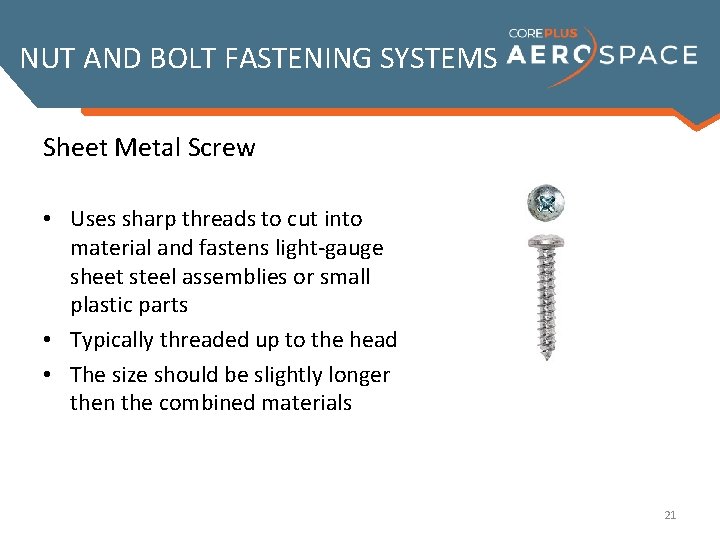
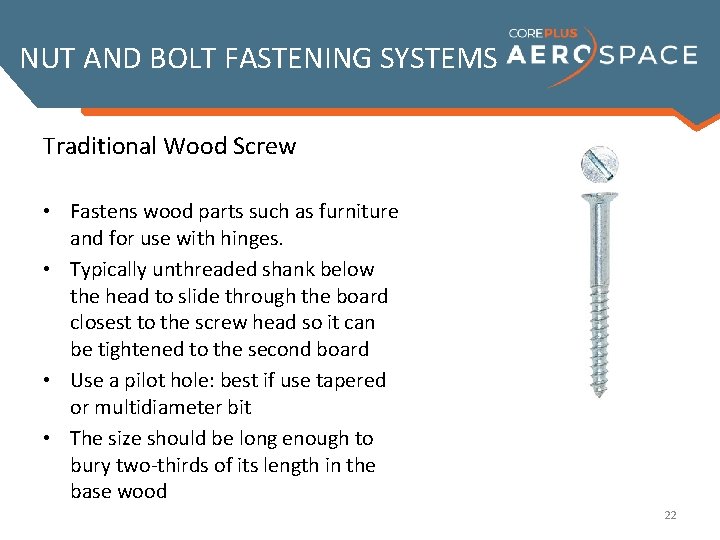
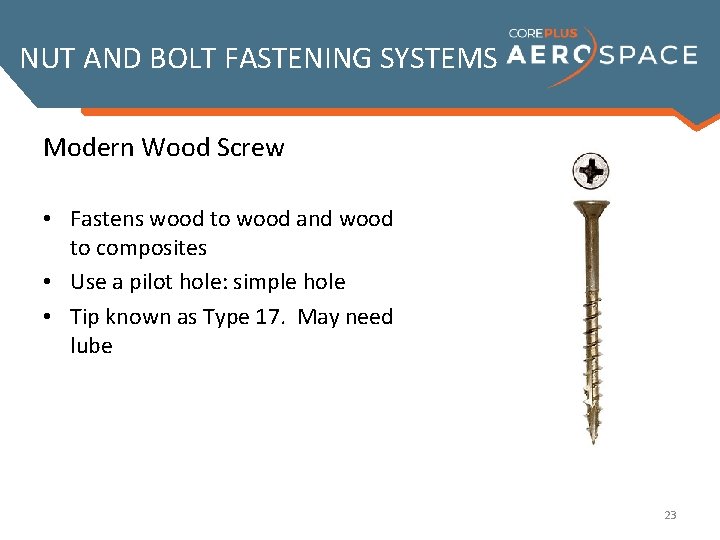
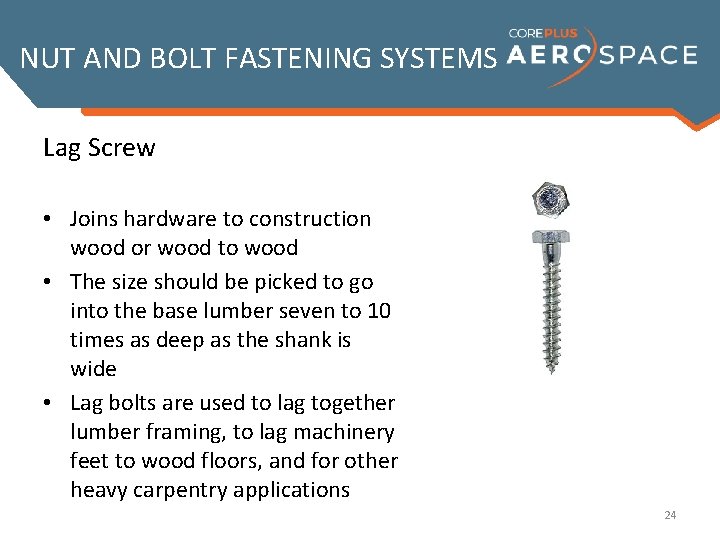
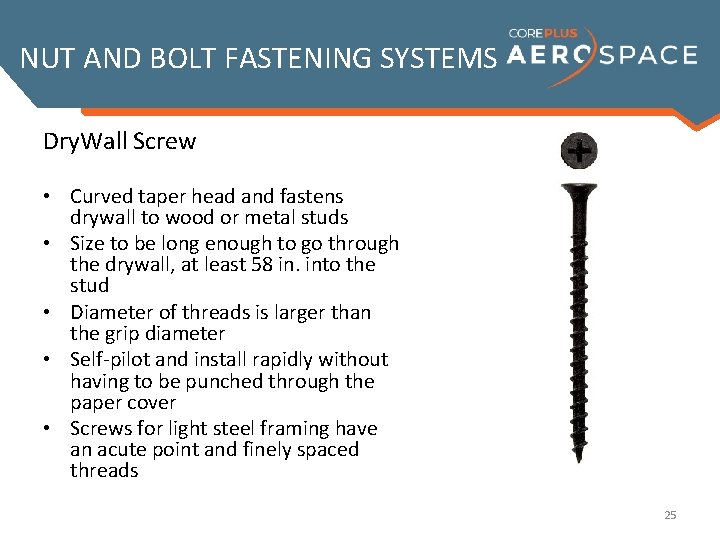
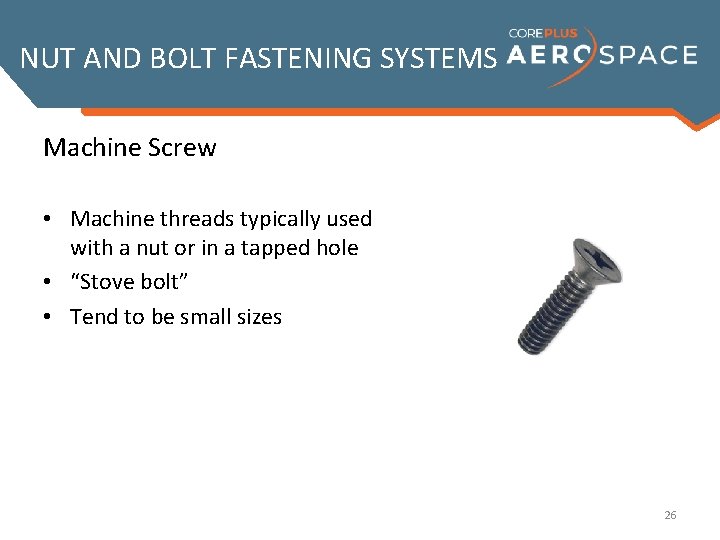
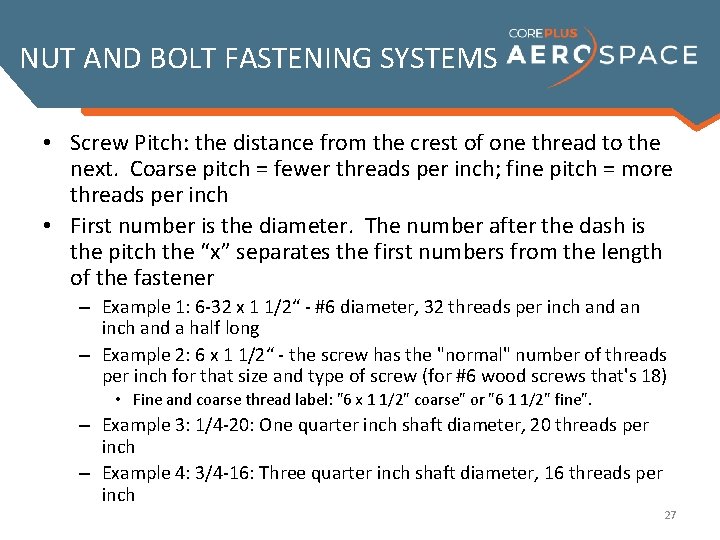
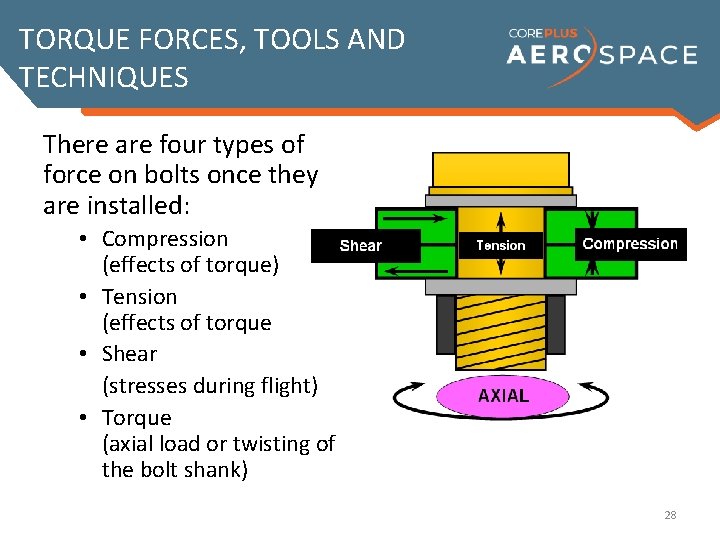
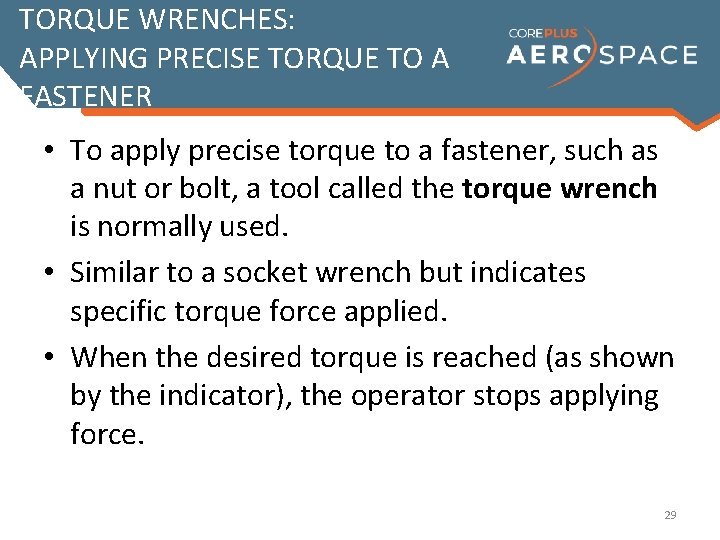
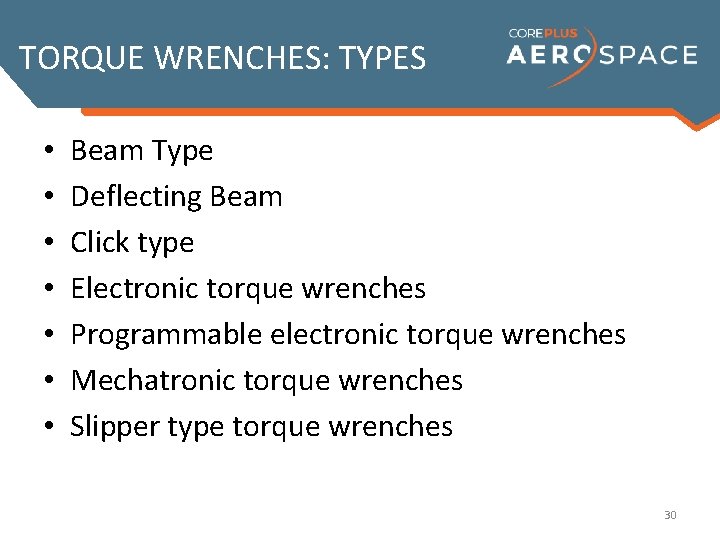
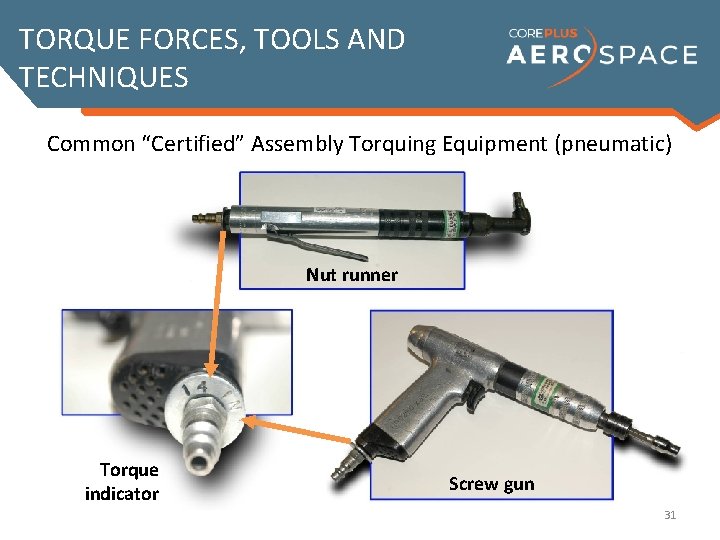
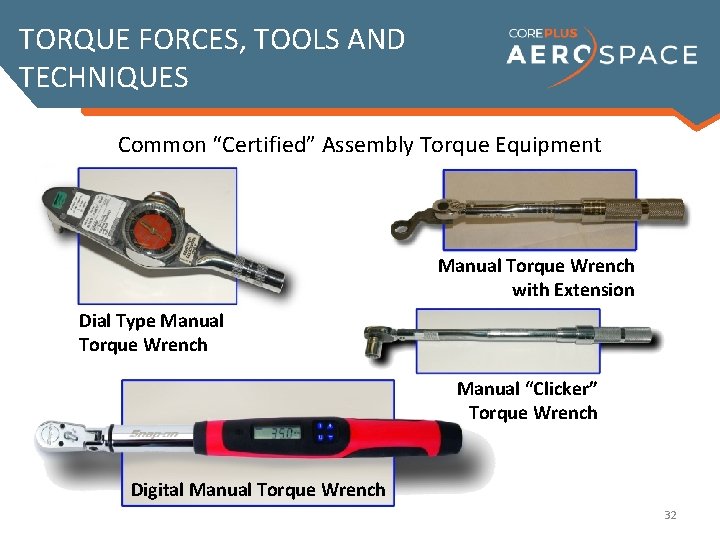
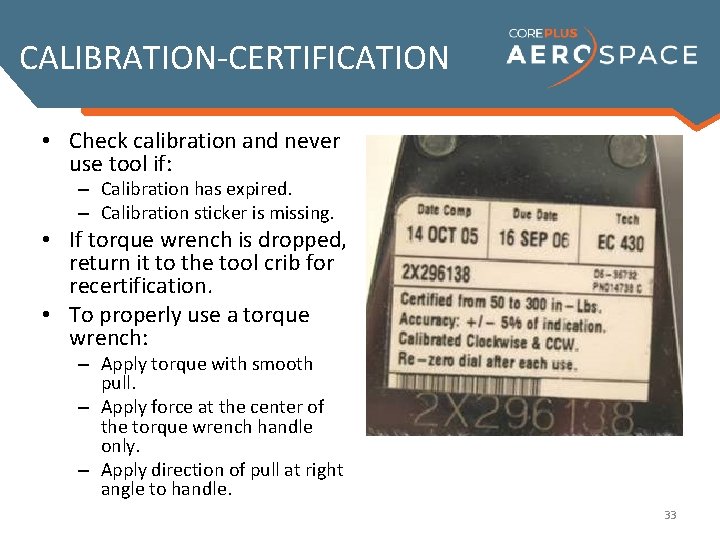
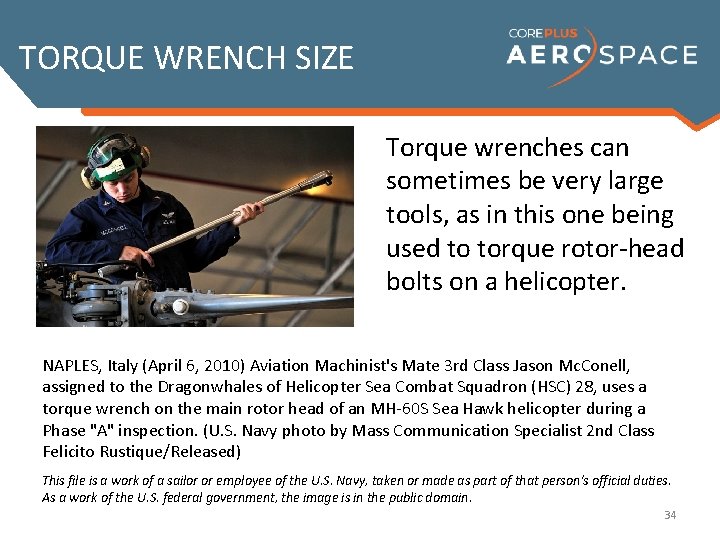
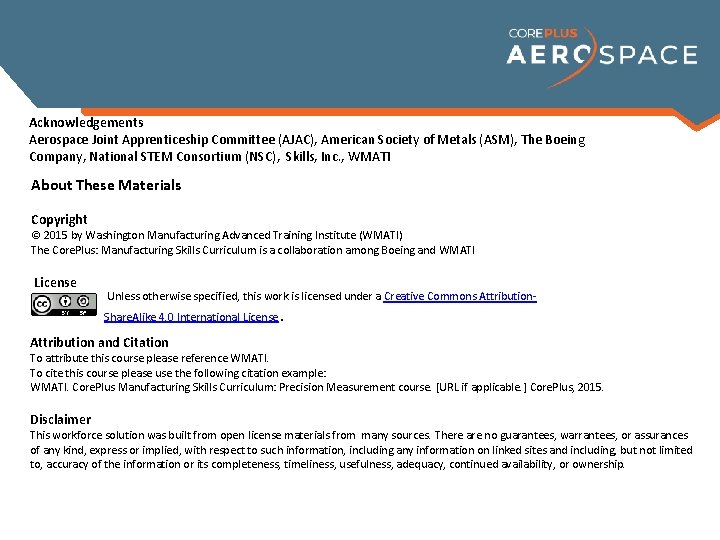
- Slides: 35
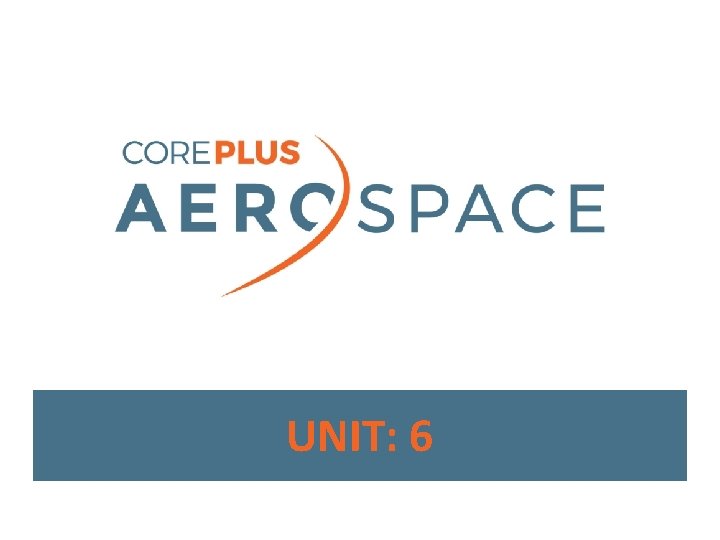
UNIT: 6
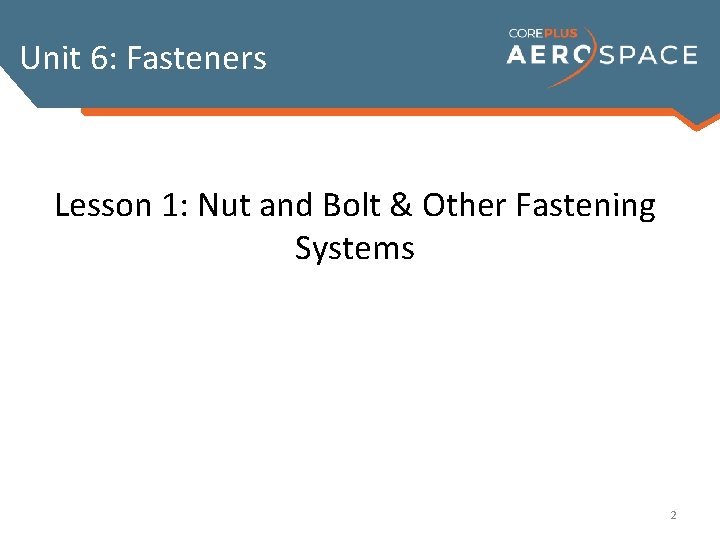
Unit 6: Fasteners Lesson 1: Nut and Bolt & Other Fastening Systems 2
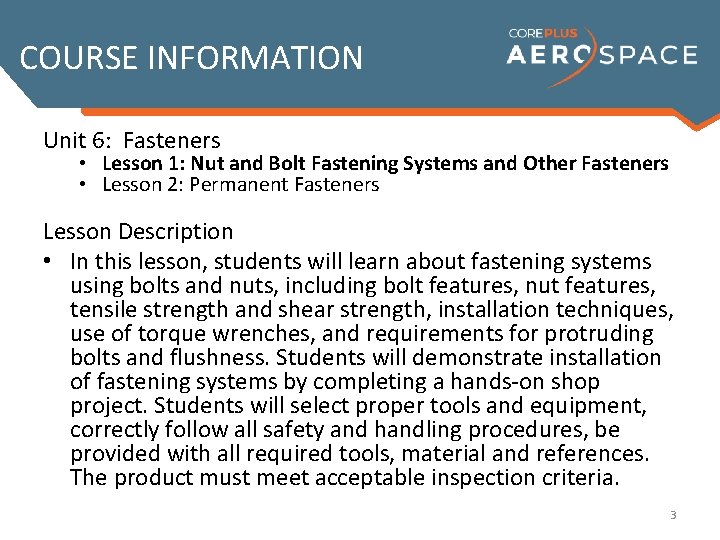
COURSE INFORMATION Unit 6: Fasteners • Lesson 1: Nut and Bolt Fastening Systems and Other Fasteners • Lesson 2: Permanent Fasteners Lesson Description • In this lesson, students will learn about fastening systems using bolts and nuts, including bolt features, nut features, tensile strength and shear strength, installation techniques, use of torque wrenches, and requirements for protruding bolts and flushness. Students will demonstrate installation of fastening systems by completing a hands-on shop project. Students will select proper tools and equipment, correctly follow all safety and handling procedures, be provided with all required tools, material and references. The product must meet acceptable inspection criteria. 3
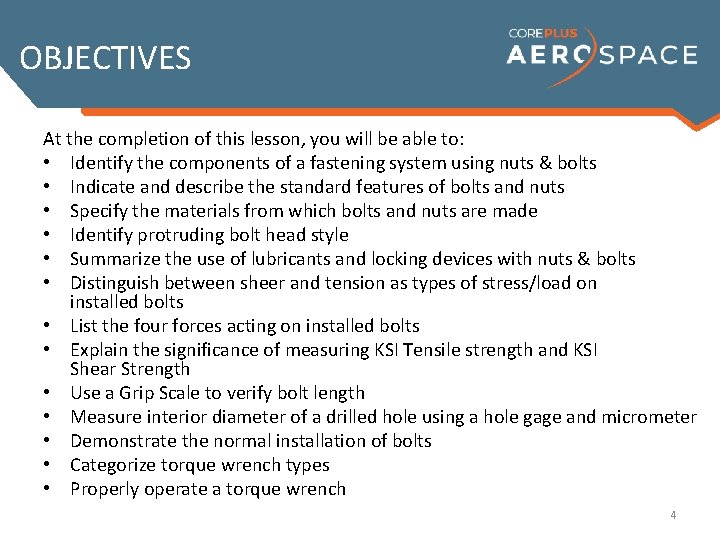
OBJECTIVES At the completion of this lesson, you will be able to: • Identify the components of a fastening system using nuts & bolts • Indicate and describe the standard features of bolts and nuts • Specify the materials from which bolts and nuts are made • Identify protruding bolt head style • Summarize the use of lubricants and locking devices with nuts & bolts • Distinguish between sheer and tension as types of stress/load on installed bolts • List the four forces acting on installed bolts • Explain the significance of measuring KSI Tensile strength and KSI Shear Strength • Use a Grip Scale to verify bolt length • Measure interior diameter of a drilled hole using a hole gage and micrometer • Demonstrate the normal installation of bolts • Categorize torque wrench types • Properly operate a torque wrench 4
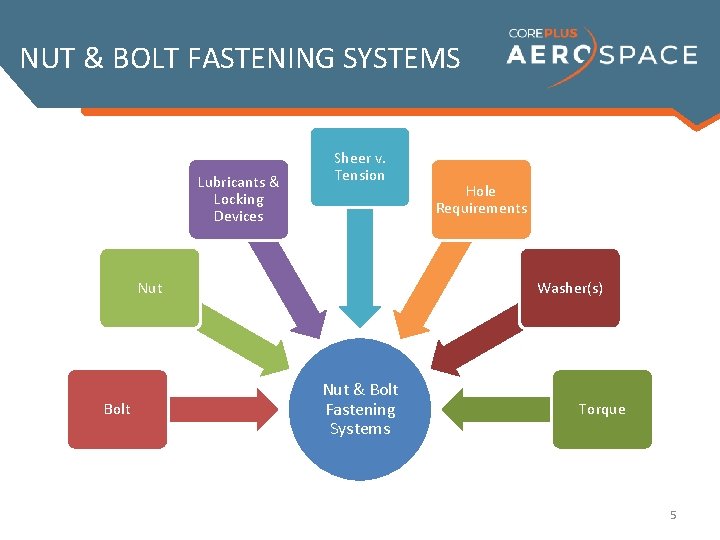
NUT & BOLT FASTENING SYSTEMS Lubricants & Locking Devices Sheer v. Tension Nut Bolt Hole Requirements Washer(s) Nut & Bolt Fastening Systems Torque 5
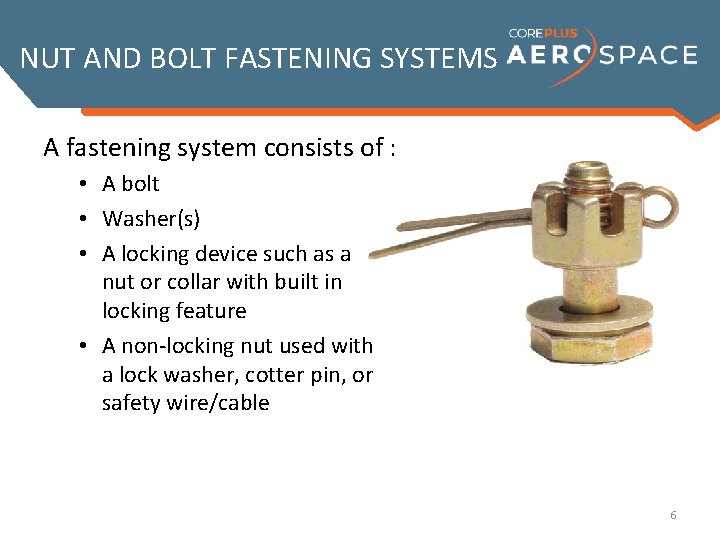
NUT AND BOLT FASTENING SYSTEMS A fastening system consists of : • A bolt • Washer(s) • A locking device such as a nut or collar with built in locking feature • A non-locking nut used with a lock washer, cotter pin, or safety wire/cable 6
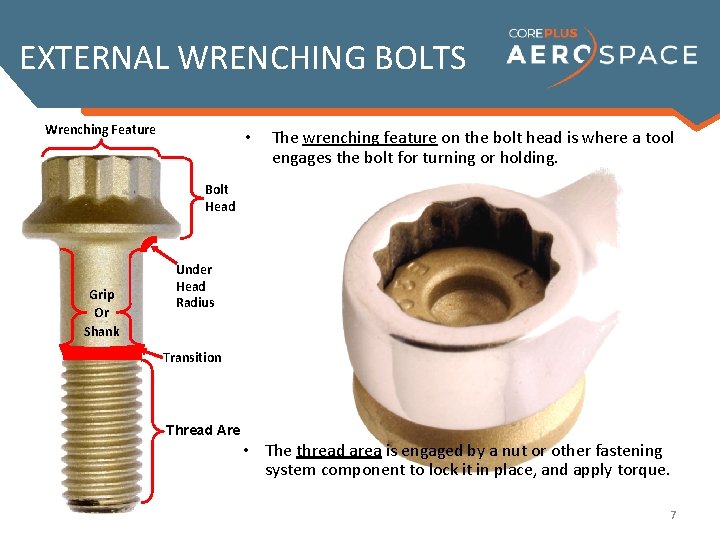
EXTERNAL WRENCHING BOLTS Wrenching Feature Bolt Head Grip Or Shank Under Head Radius • The wrenching feature on the bolt head is where a tool engages the bolt for turning or holding. • The bolt head is everything above the grip or shank. • The under head fillet is a small radius that helps better distribute the stress between the head and grip or shank. • The grip or shank is the smooth area below the head (no threads) that remains in the hole after installation. • The transition is the area of the bolt between the grip or shank and the threaded end of the bolt. Transition 1 -2 Thread Area • The thread area is engaged by a nut or other fastening system component to lock it in place, and apply torque. 7
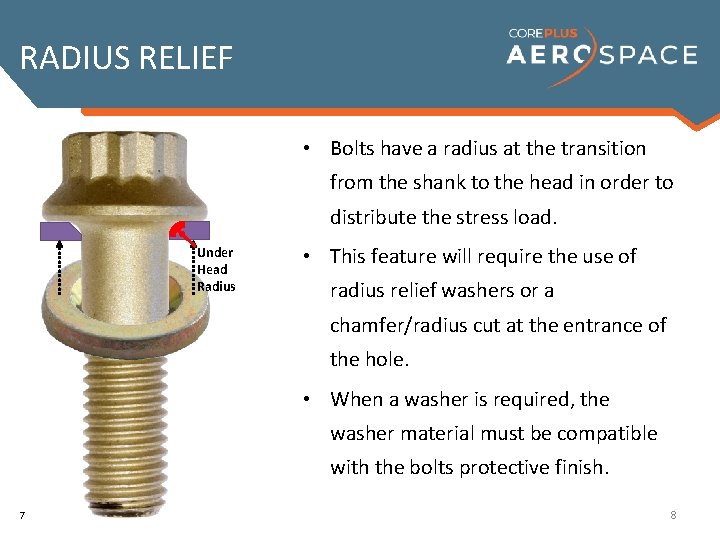
RADIUS RELIEF • Bolts have a radius at the transition from the shank to the head in order to distribute the stress load. Under Head Radius • This feature will require the use of radius relief washers or a chamfer/radius cut at the entrance of the hole. • When a washer is required, the washer material must be compatible with the bolts protective finish. 7 8
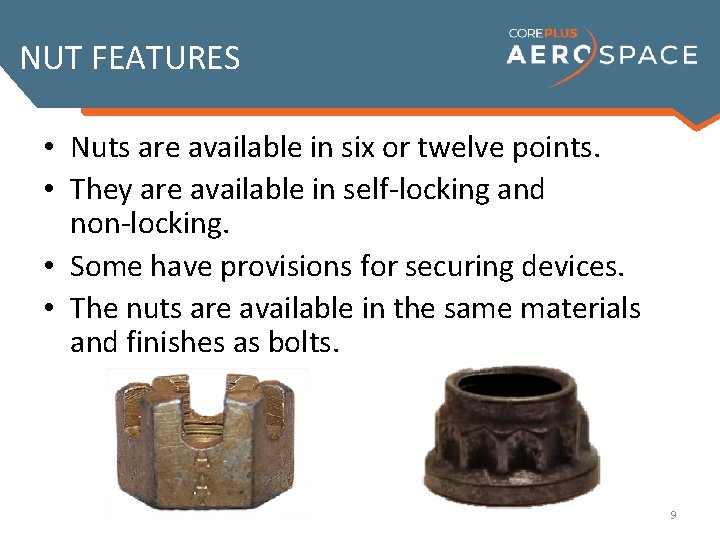
NUT FEATURES • Nuts are available in six or twelve points. • They are available in self-locking and non-locking. • Some have provisions for securing devices. • The nuts are available in the same materials and finishes as bolts. 9
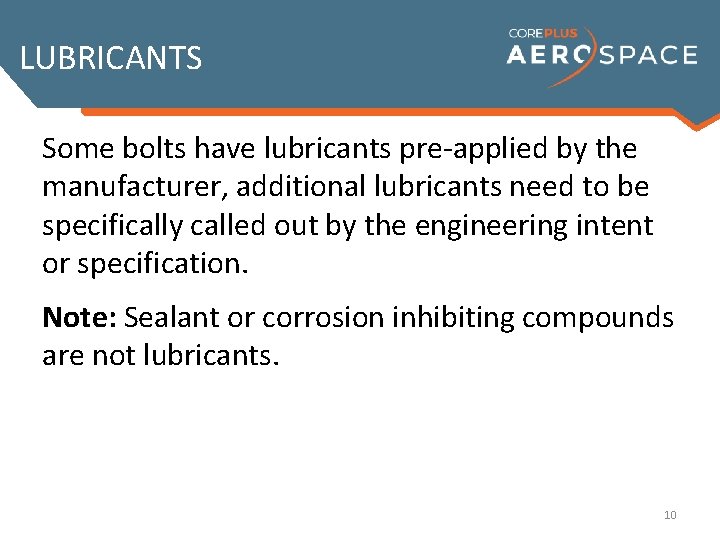
LUBRICANTS Some bolts have lubricants pre-applied by the manufacturer, additional lubricants need to be specifically called out by the engineering intent or specification. Note: Sealant or corrosion inhibiting compounds are not lubricants. 10
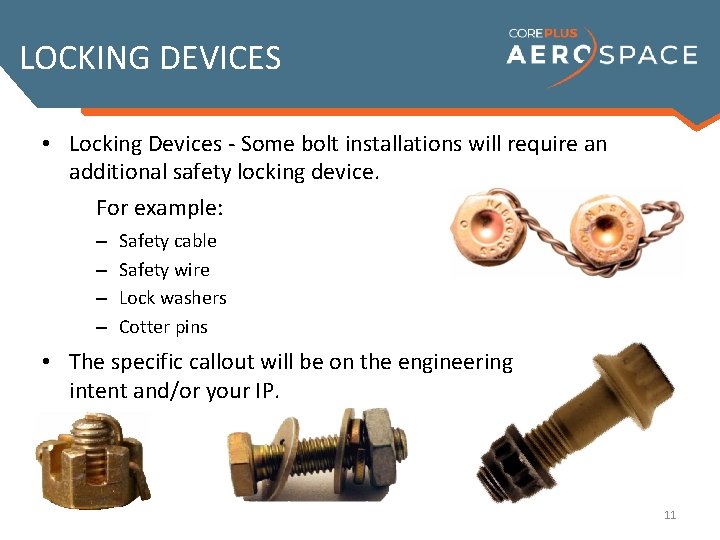
LOCKING DEVICES • Locking Devices - Some bolt installations will require an additional safety locking device. For example: – – Safety cable Safety wire Lock washers Cotter pins • The specific callout will be on the engineering intent and/or your IP. 11
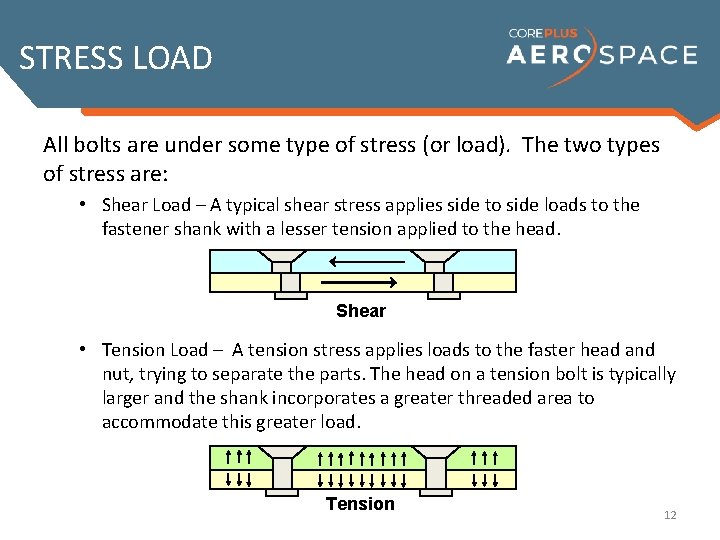
STRESS LOAD All bolts are under some type of stress (or load). The two types of stress are: • Shear Load – A typical shear stress applies side to side loads to the fastener shank with a lesser tension applied to the head. Shear • Tension Load – A tension stress applies loads to the faster head and nut, trying to separate the parts. The head on a tension bolt is typically larger and the shank incorporates a greater threaded area to accommodate this greater load. Tension 12
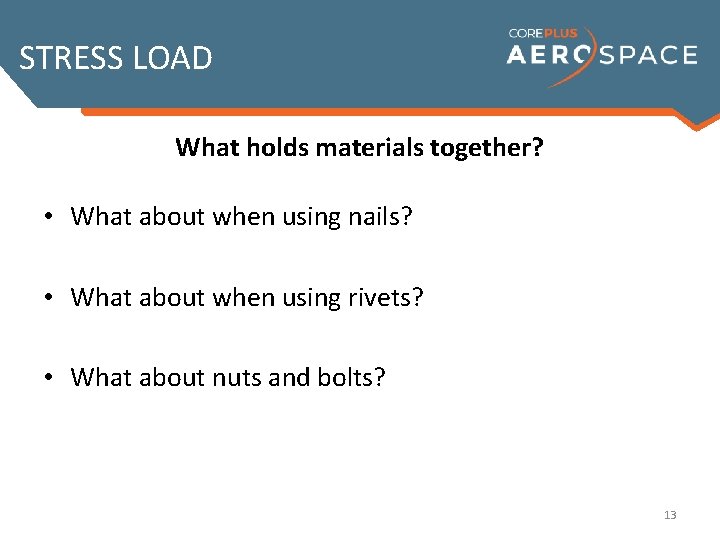
STRESS LOAD What holds materials together? • What about when using nails? • What about when using rivets? • What about nuts and bolts? 13
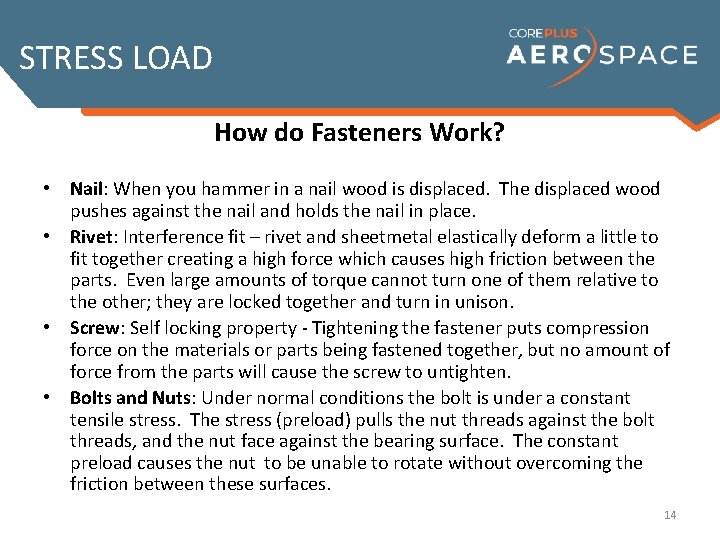
STRESS LOAD How do Fasteners Work? • Nail: When you hammer in a nail wood is displaced. The displaced wood pushes against the nail and holds the nail in place. • Rivet: Interference fit – rivet and sheetmetal elastically deform a little to fit together creating a high force which causes high friction between the parts. Even large amounts of torque cannot turn one of them relative to the other; they are locked together and turn in unison. • Screw: Self locking property - Tightening the fastener puts compression force on the materials or parts being fastened together, but no amount of force from the parts will cause the screw to untighten. • Bolts and Nuts: Under normal conditions the bolt is under a constant tensile stress. The stress (preload) pulls the nut threads against the bolt threads, and the nut face against the bearing surface. The constant preload causes the nut to be unable to rotate without overcoming the friction between these surfaces. 14
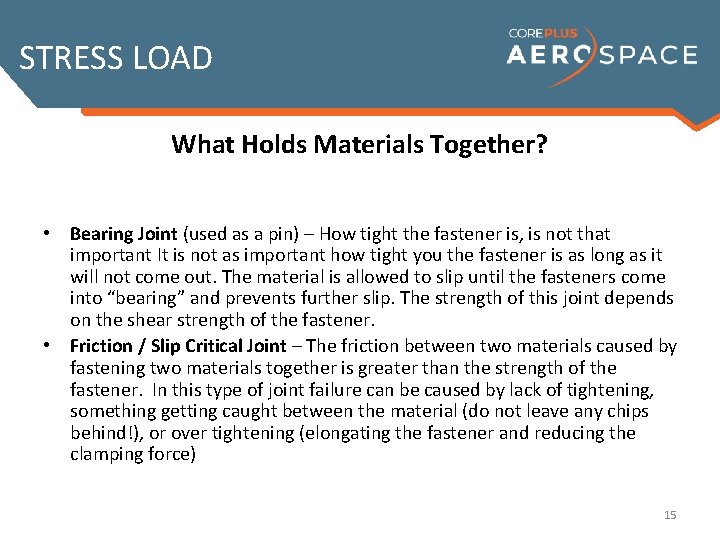
STRESS LOAD What Holds Materials Together? • Bearing Joint (used as a pin) – How tight the fastener is, is not that important It is not as important how tight you the fastener is as long as it will not come out. The material is allowed to slip until the fasteners come into “bearing” and prevents further slip. The strength of this joint depends on the shear strength of the fastener. • Friction / Slip Critical Joint – The friction between two materials caused by fastening two materials together is greater than the strength of the fastener. In this type of joint failure can be caused by lack of tightening, something getting caught between the material (do not leave any chips behind!), or over tightening (elongating the fastener and reducing the clamping force) 15
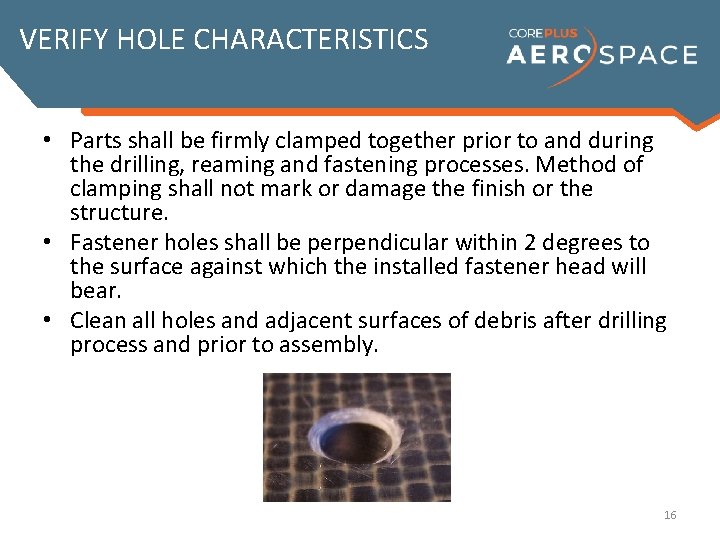
VERIFY HOLE CHARACTERISTICS • Parts shall be firmly clamped together prior to and during the drilling, reaming and fastening processes. Method of clamping shall not mark or damage the finish or the structure. • Fastener holes shall be perpendicular within 2 degrees to the surface against which the installed fastener head will bear. • Clean all holes and adjacent surfaces of debris after drilling process and prior to assembly. 16
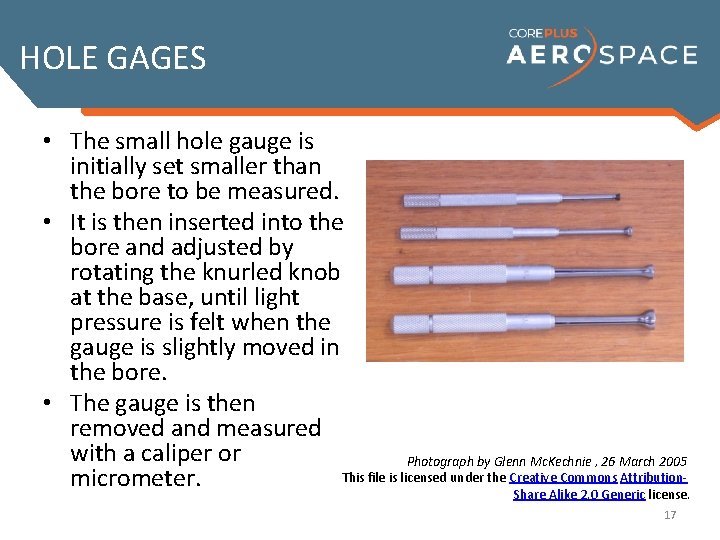
HOLE GAGES • The small hole gauge is initially set smaller than the bore to be measured. • It is then inserted into the bore and adjusted by rotating the knurled knob at the base, until light pressure is felt when the gauge is slightly moved in the bore. • The gauge is then removed and measured with a caliper or Photograph by Glenn Mc. Kechnie , 26 March 2005 This file is licensed under the Creative Commons Attributionmicrometer. Share Alike 2. 0 Generic license. 17
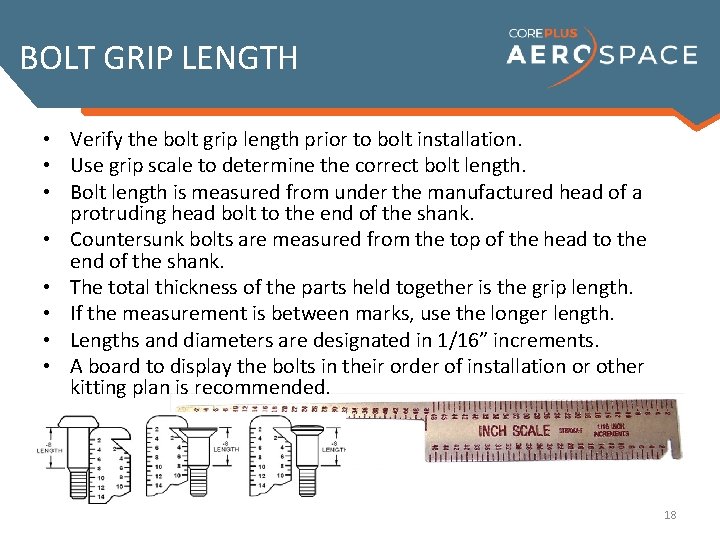
BOLT GRIP LENGTH • Verify the bolt grip length prior to bolt installation. • Use grip scale to determine the correct bolt length. • Bolt length is measured from under the manufactured head of a protruding head bolt to the end of the shank. • Countersunk bolts are measured from the top of the head to the end of the shank. • The total thickness of the parts held together is the grip length. • If the measurement is between marks, use the longer length. • Lengths and diameters are designated in 1/16” increments. • A board to display the bolts in their order of installation or other kitting plan is recommended. 18
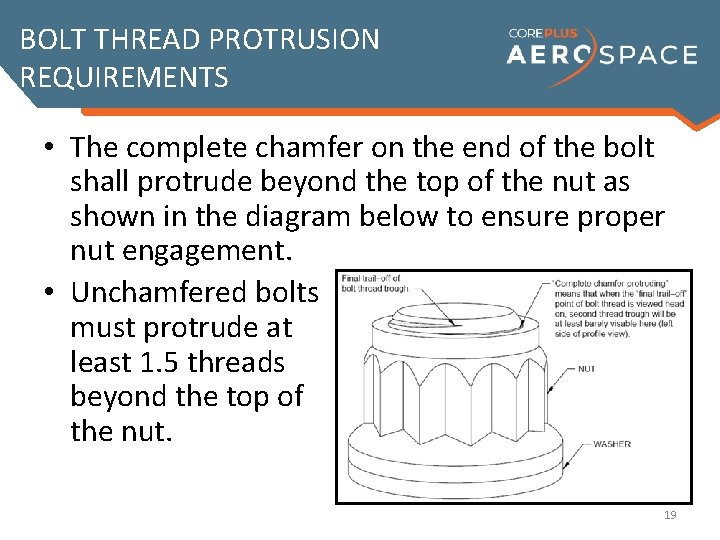
BOLT THREAD PROTRUSION REQUIREMENTS • The complete chamfer on the end of the bolt shall protrude beyond the top of the nut as shown in the diagram below to ensure proper nut engagement. • Unchamfered bolts must protrude at least 1. 5 threads beyond the top of the nut. 19
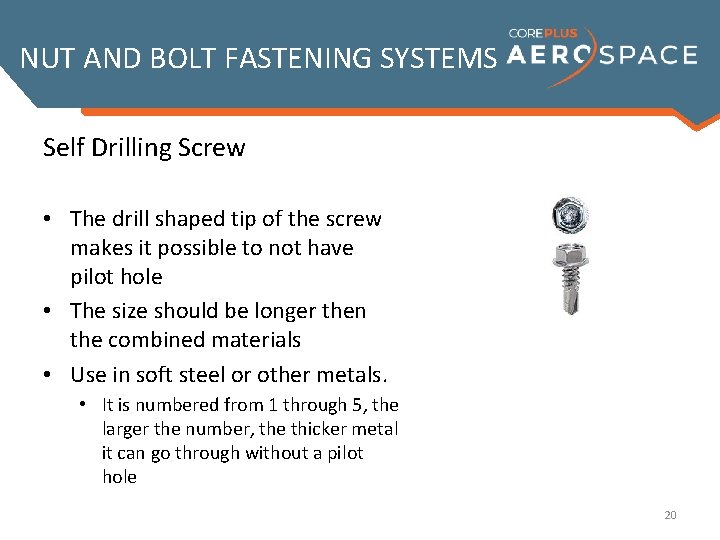
NUT AND BOLT FASTENING SYSTEMS Self Drilling Screw • The drill shaped tip of the screw makes it possible to not have pilot hole • The size should be longer then the combined materials • Use in soft steel or other metals. • It is numbered from 1 through 5, the larger the number, the thicker metal it can go through without a pilot hole 20
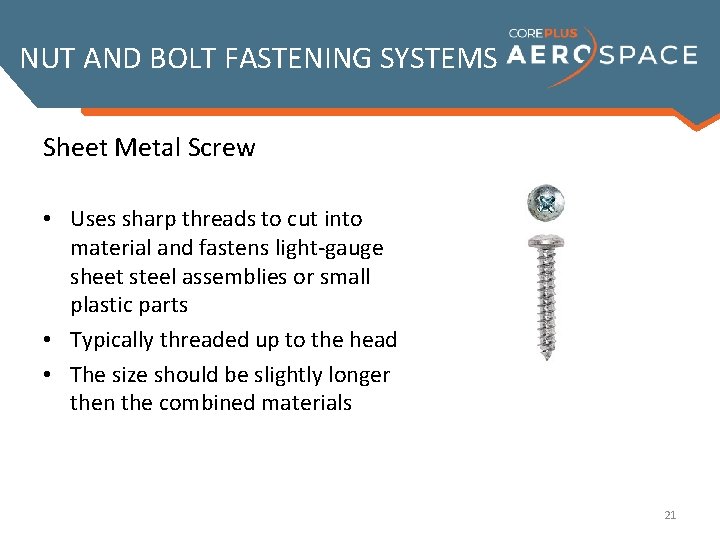
NUT AND BOLT FASTENING SYSTEMS Sheet Metal Screw • Uses sharp threads to cut into material and fastens light-gauge sheet steel assemblies or small plastic parts • Typically threaded up to the head • The size should be slightly longer then the combined materials 21
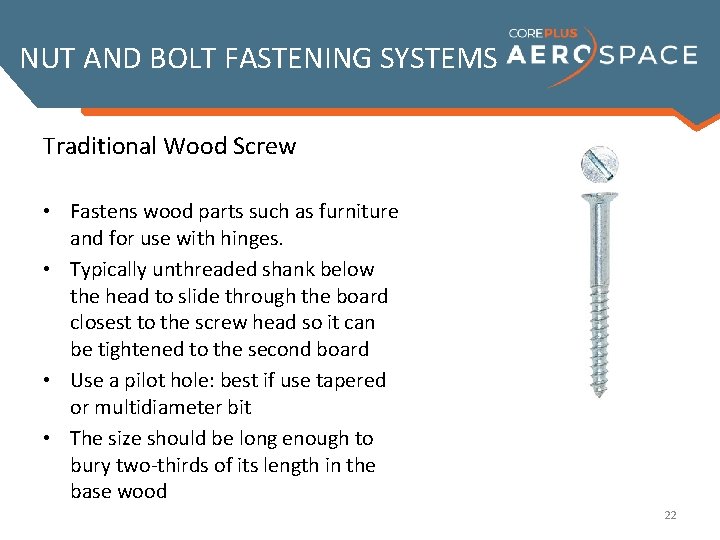
NUT AND BOLT FASTENING SYSTEMS Traditional Wood Screw • Fastens wood parts such as furniture and for use with hinges. • Typically unthreaded shank below the head to slide through the board closest to the screw head so it can be tightened to the second board • Use a pilot hole: best if use tapered or multidiameter bit • The size should be long enough to bury two-thirds of its length in the base wood 22
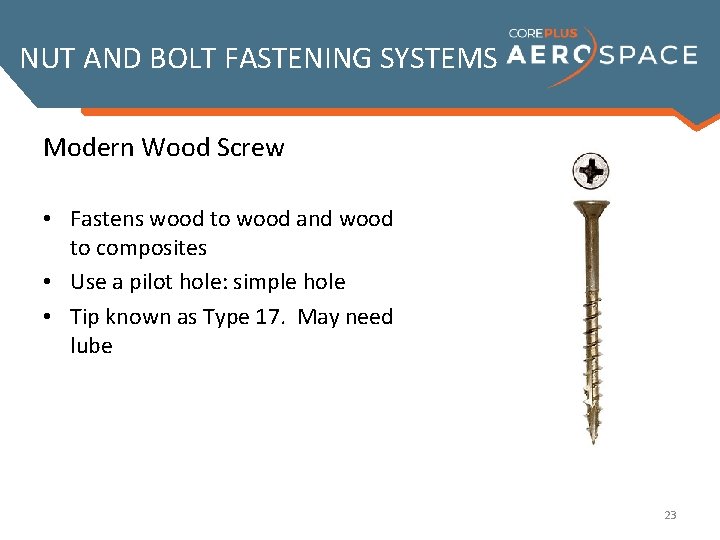
NUT AND BOLT FASTENING SYSTEMS Modern Wood Screw • Fastens wood to wood and wood to composites • Use a pilot hole: simple hole • Tip known as Type 17. May need lube 23
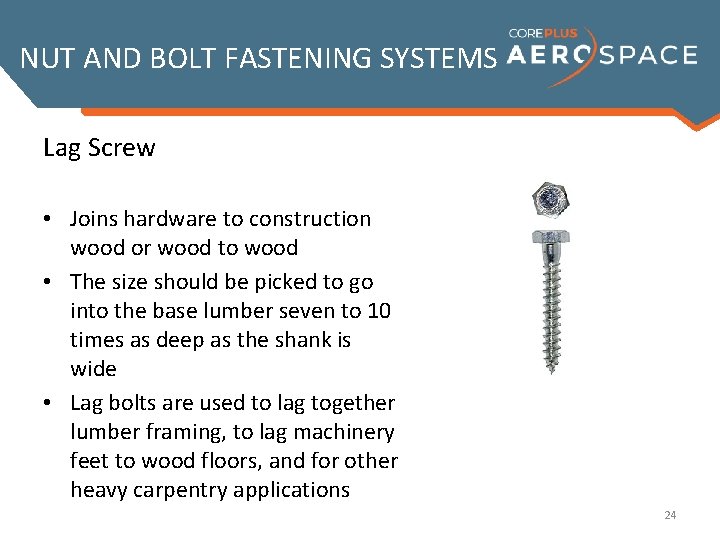
NUT AND BOLT FASTENING SYSTEMS Lag Screw • Joins hardware to construction wood or wood to wood • The size should be picked to go into the base lumber seven to 10 times as deep as the shank is wide • Lag bolts are used to lag together lumber framing, to lag machinery feet to wood floors, and for other heavy carpentry applications 24
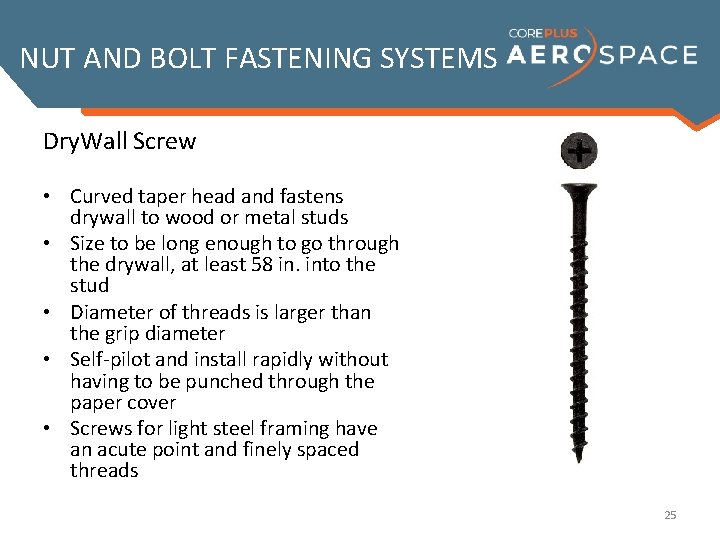
NUT AND BOLT FASTENING SYSTEMS Dry. Wall Screw • Curved taper head and fastens drywall to wood or metal studs • Size to be long enough to go through the drywall, at least 58 in. into the stud • Diameter of threads is larger than the grip diameter • Self-pilot and install rapidly without having to be punched through the paper cover • Screws for light steel framing have an acute point and finely spaced threads 25
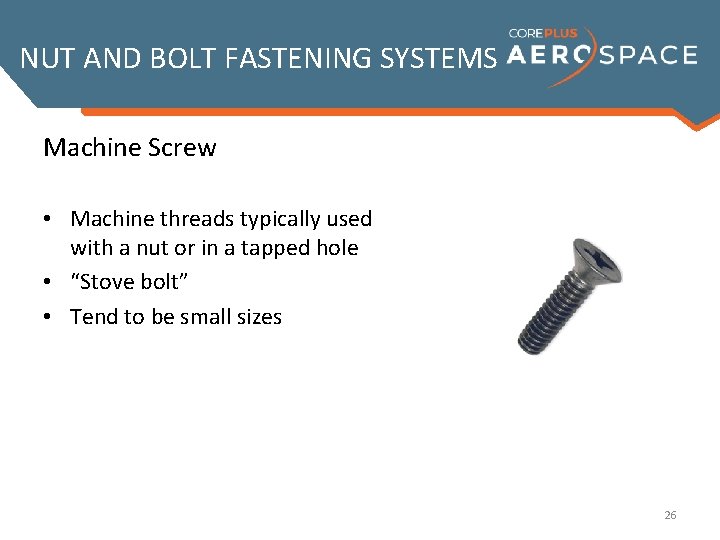
NUT AND BOLT FASTENING SYSTEMS Machine Screw • Machine threads typically used with a nut or in a tapped hole • “Stove bolt” • Tend to be small sizes 26
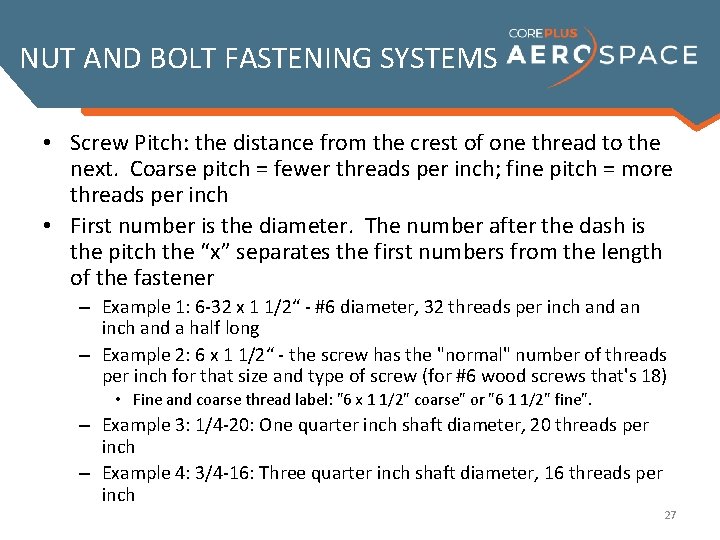
NUT AND BOLT FASTENING SYSTEMS • Screw Pitch: the distance from the crest of one thread to the next. Coarse pitch = fewer threads per inch; fine pitch = more threads per inch • First number is the diameter. The number after the dash is the pitch the “x” separates the first numbers from the length of the fastener – Example 1: 6 -32 x 1 1/2“ - #6 diameter, 32 threads per inch and an inch and a half long – Example 2: 6 x 1 1/2“ - the screw has the "normal" number of threads per inch for that size and type of screw (for #6 wood screws that's 18) • Fine and coarse thread label: "6 x 1 1/2" coarse" or "6 1 1/2" fine". – Example 3: 1/4 -20: One quarter inch shaft diameter, 20 threads per inch – Example 4: 3/4 -16: Three quarter inch shaft diameter, 16 threads per inch 27
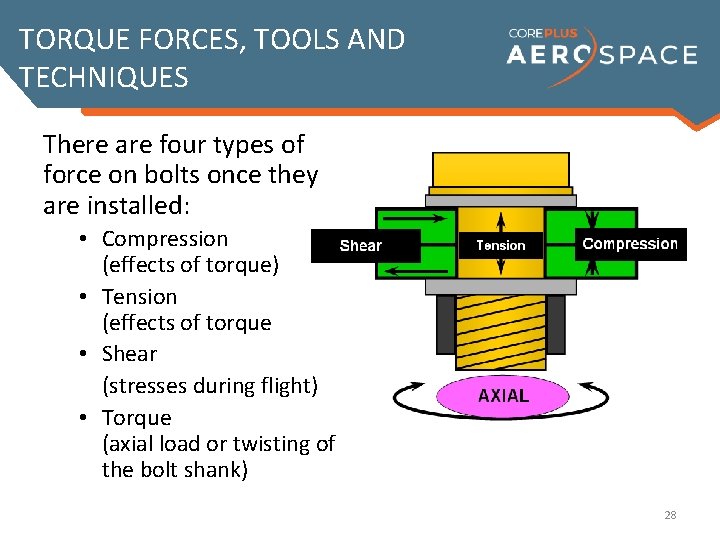
TORQUE FORCES, TOOLS AND TECHNIQUES There are four types of force on bolts once they are installed: • Compression (effects of torque) • Tension (effects of torque • Shear (stresses during flight) • Torque (axial load or twisting of the bolt shank) 28
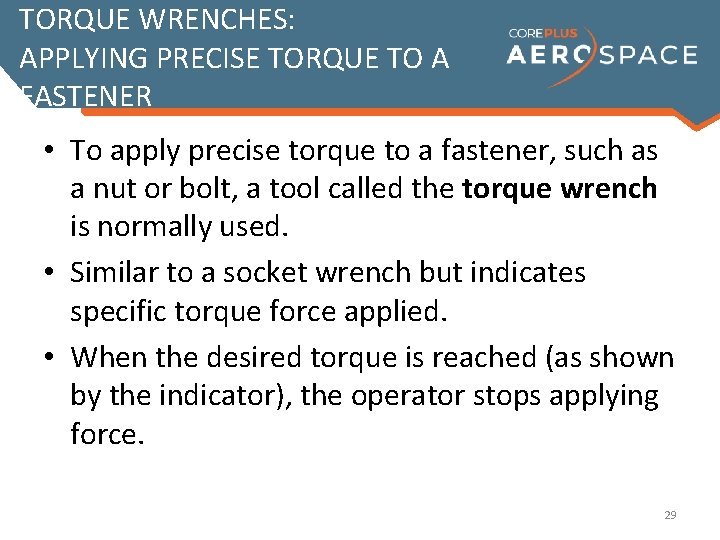
TORQUE WRENCHES: APPLYING PRECISE TORQUE TO A FASTENER • To apply precise torque to a fastener, such as a nut or bolt, a tool called the torque wrench is normally used. • Similar to a socket wrench but indicates specific torque force applied. • When the desired torque is reached (as shown by the indicator), the operator stops applying force. 29
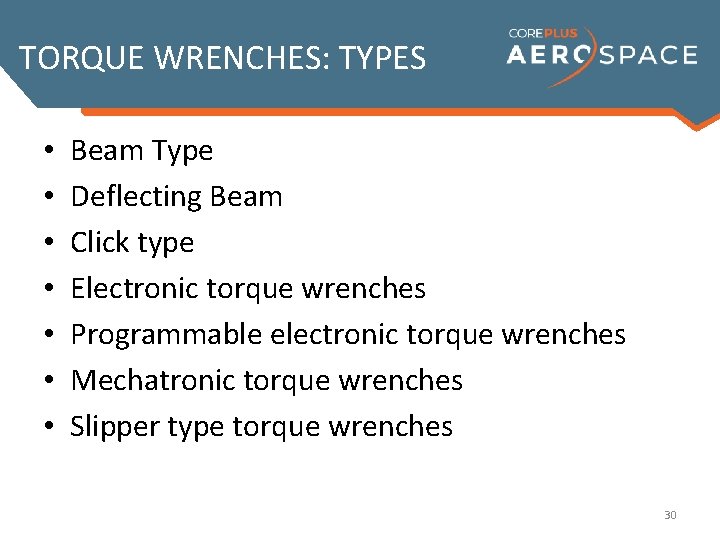
TORQUE WRENCHES: TYPES • • Beam Type Deflecting Beam Click type Electronic torque wrenches Programmable electronic torque wrenches Mechatronic torque wrenches Slipper type torque wrenches 30
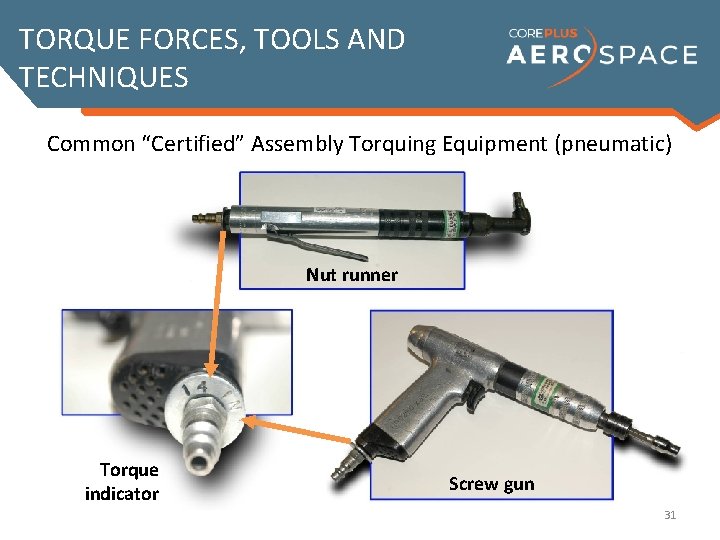
TORQUE FORCES, TOOLS AND TECHNIQUES Common “Certified” Assembly Torquing Equipment (pneumatic) Nut runner Torque indicator Screw gun 31
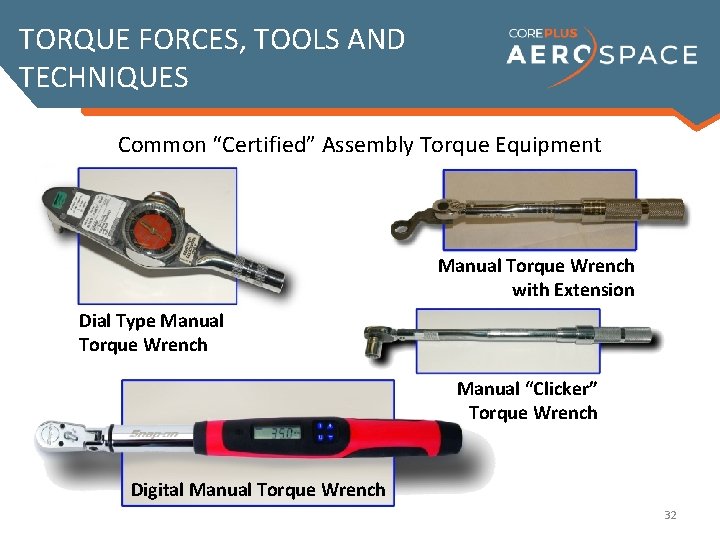
TORQUE FORCES, TOOLS AND TECHNIQUES Common “Certified” Assembly Torque Equipment Manual Torque Wrench with Extension Dial Type Manual Torque Wrench Manual “Clicker” Torque Wrench Digital Manual Torque Wrench 32
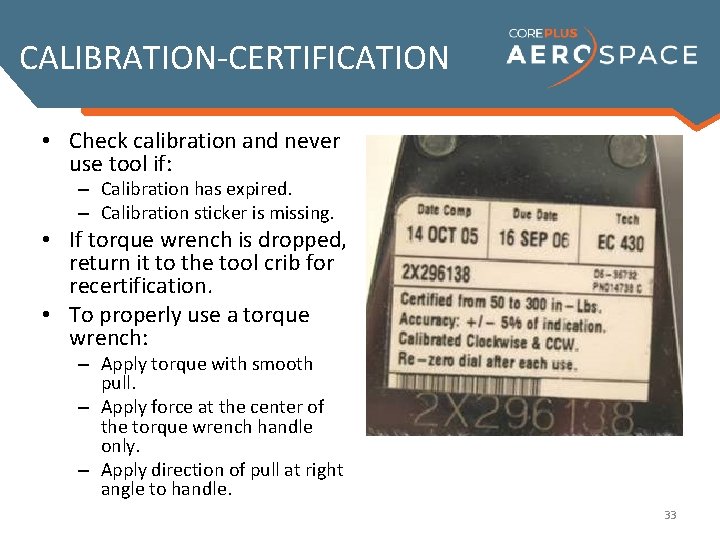
CALIBRATION-CERTIFICATION • Check calibration and never use tool if: – Calibration has expired. – Calibration sticker is missing. • If torque wrench is dropped, return it to the tool crib for recertification. • To properly use a torque wrench: – Apply torque with smooth pull. – Apply force at the center of the torque wrench handle only. – Apply direction of pull at right angle to handle. 33
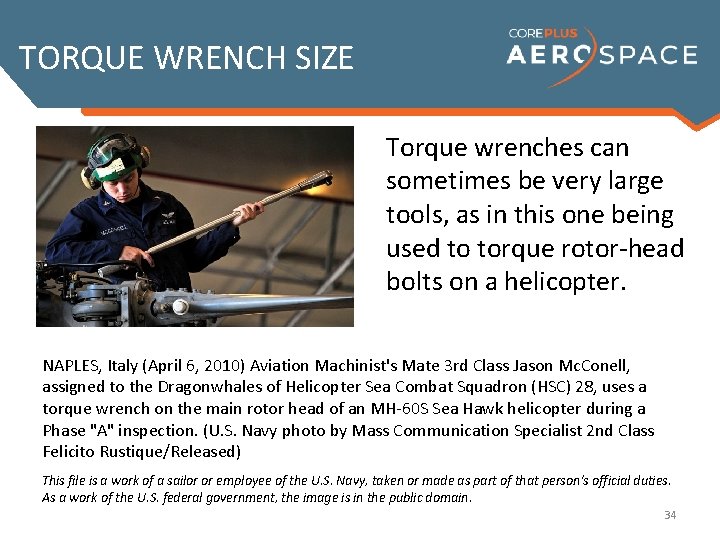
TORQUE WRENCH SIZE Torque wrenches can sometimes be very large tools, as in this one being used to torque rotor-head bolts on a helicopter. NAPLES, Italy (April 6, 2010) Aviation Machinist's Mate 3 rd Class Jason Mc. Conell, assigned to the Dragonwhales of Helicopter Sea Combat Squadron (HSC) 28, uses a torque wrench on the main rotor head of an MH-60 S Sea Hawk helicopter during a Phase "A" inspection. (U. S. Navy photo by Mass Communication Specialist 2 nd Class Felicito Rustique/Released) This file is a work of a sailor or employee of the U. S. Navy, taken or made as part of that person's official duties. As a work of the U. S. federal government, the image is in the public domain. 34
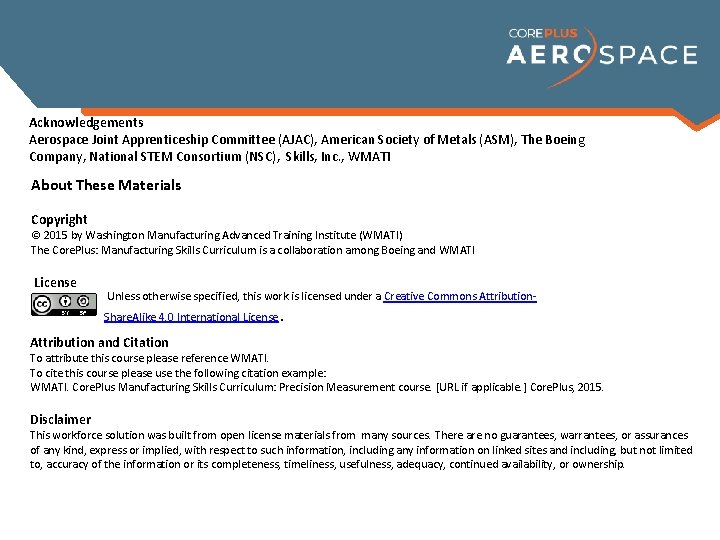
Acknowledgements Aerospace Joint Apprenticeship Committee (AJAC), American Society of Metals (ASM), The Boeing Company, National STEM Consortium (NSC), Skills, Inc. , WMATI About These Materials Copyright © 2015 by Washington Manufacturing Advanced Training Institute (WMATI) The Core. Plus: Manufacturing Skills Curriculum is a collaboration among Boeing and WMATI License Unless otherwise specified, this work is licensed under a Creative Commons Attribution. Share. Alike 4. 0 International License. Attribution and Citation To attribute this course please reference WMATI. To cite this course please use the following citation example: WMATI. Core. Plus Manufacturing Skills Curriculum: Precision Measurement course. [URL if applicable. ] Core. Plus, 2015. Disclaimer This workforce solution was built from open license materials from many sources. There are no guarantees, warrantees, or assurances of any kind, express or implied, with respect to such information, including any information on linked sites and including, but not limited to, accuracy of the information or its completeness, timeliness, usefulness, adequacy, continued availability, or ownership.