UNICAMP Experimental Analysis of Swirl Tubes as Downhole
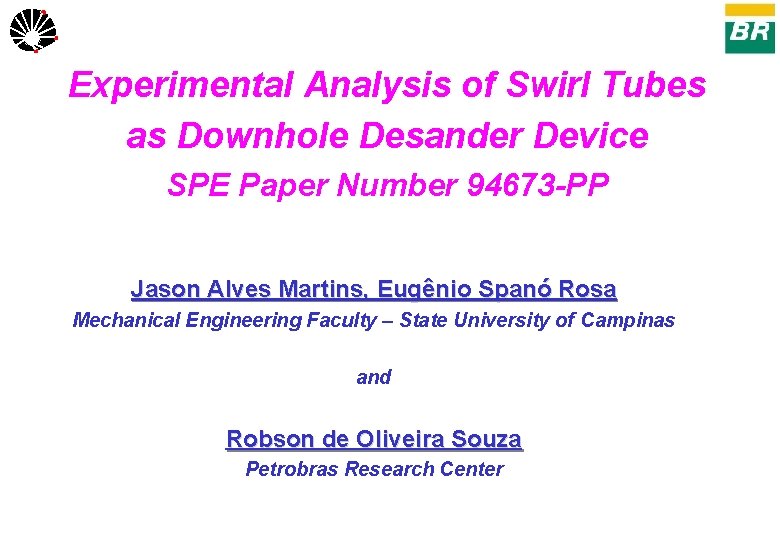
UNICAMP Experimental Analysis of Swirl Tubes as Downhole Desander Device SPE Paper Number 94673 -PP Jason Alves Martins, Eugênio Spanó Rosa Mechanical Engineering Faculty – State University of Campinas and Robson de Oliveira Souza Petrobras Research Center

UNICAMP Introduction • Swirl tube main function: act as desander device to reduce well workover. • Flow capacities: 20 m 3/d to 600 m 3/d • Liquid characteristics: light crude or high water cuts > 95%

Application Scenario UNICAMP • It works downhole, usually positioned above the production zone at vertical or near vertical line. • The solid-liquid mixture inlet is at the top side openings. • The separation occurs; the sand is collected at the sand reservoir and the clear liquid goes up thru the production pipe.

UNICAMP This Work Motivation & Objectives • • It has a successful operation record for light oils or high water cuts but it is reported fault operation when the liquid viscosity increases or oil in water emulsions are found. • This work objective is to study experimentally the impact of the liquid viscosity increase on the separation efficiency!
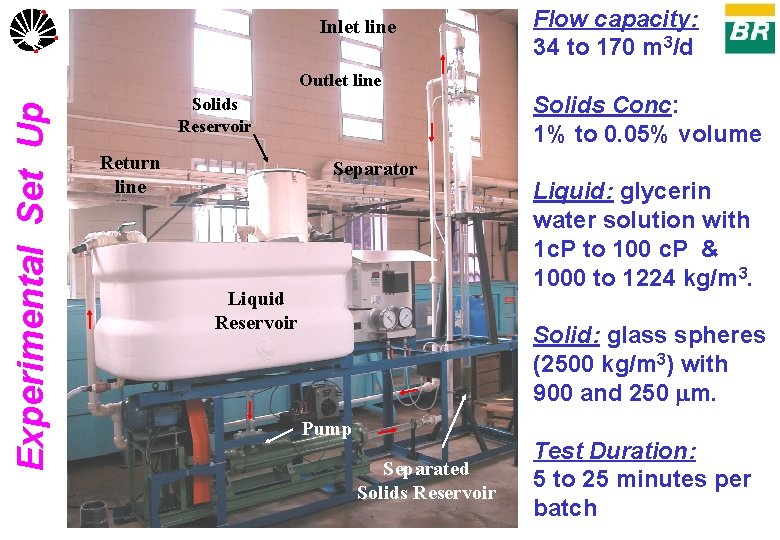
Inlet line UNICAMP Flow capacity: 34 to 170 m 3/d Experimental Set Up Outlet line Solids Conc: 1% to 0. 05% volume Solids Reservoir Return line Separator Liquid Reservoir Liquid: glycerin water solution with 1 c. P to 100 c. P & 1000 to 1224 kg/m 3. Solid: glass spheres (2500 kg/m 3) with 900 and 250 mm. Pump Separated Solids Reservoir Test Duration: 5 to 25 minutes per batch

Schematic of the Swirling Tube UNICAMP Upward flow Production pipe Downward flow from inlet

Dimensional Analysis UNICAMP The separation efficiency depends on 11 variables which are classified for convenience in: i. Variables related to the solid particle: particle diameter dp, solid density rp and solids concentration Ci and gravity acceleration g. ii. Variables related to the liquid stream: liquid density and viscosity r and m, mean axial and swirl velocity - W and U. iii. Variables related to the geometrical properties: production pipe diameter – Dp , external pipe diameter De and chicane length L.

Dimensionless Variables UNICAMP The 11 dimensional variables can be grouped in 8 dimensionless variables to express the separation efficiency dependence: , where and

Analysis Simplification UNICAMP • , and • It is rather cumbersome to draw an analysis with eight dimensionless groups. . . But, considering the following hypothesis: i. The geometrical parameters De/Dp and L/Dp remain fixed, ii. The relative density ratio Dr/r also remain fixed iii. The solids inlet concentration, Ci < 0. 1% does not affect the separation efficiency The separation efficiency dependence reduces to three dimensionless groups:
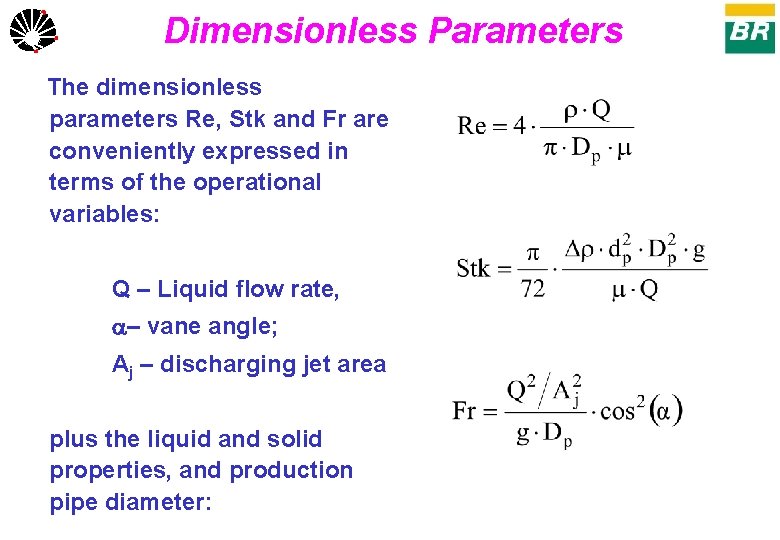
Dimensionless Parameters UNICAMP The dimensionless parameters Re, Stk and Fr are conveniently expressed in terms of the operational variables: Q – Liquid flow rate, a– vane angle; Aj – discharging jet area plus the liquid and solid properties, and production pipe diameter:
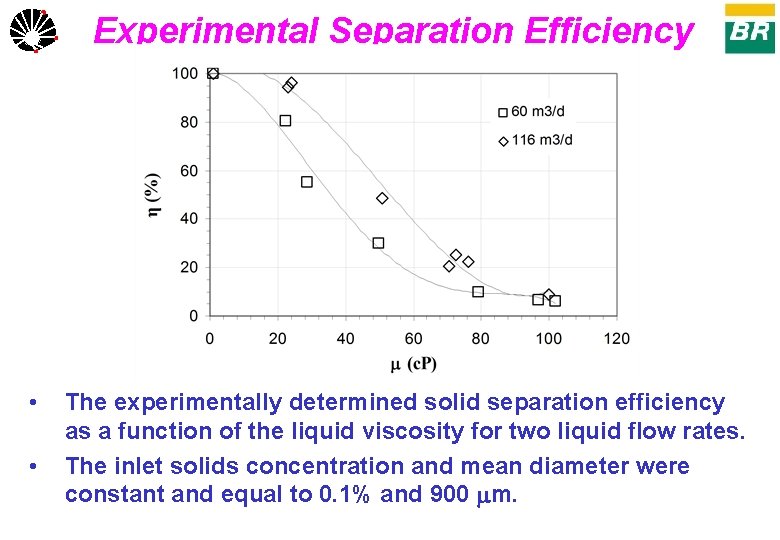
Experimental Separation Efficiency UNICAMP • • The experimentally determined solid separation efficiency as a function of the liquid viscosity for two liquid flow rates. The inlet solids concentration and mean diameter were constant and equal to 0. 1% and 900 mm.

UNICAMP Functional Dependence of the Separation Efficiency • The swirl tube separation efficiency, as any other separator, has an efficiency curve with and S shape! • It is proposed to fit the efficiency curve with an error function: • the c parameter is defined by: • and x is: • and s, m, a and b are constants experimentally determined

Predicted x Experimental Separation Efficiency UNICAMP The predicted (continuous line) and the experimentally (open symbols) separation efficiency as a function of c parameter, c = f(Re, Stk, Fr).

Separation Efficiency x Particle Size UNICAMP Predicted separation efficiency as a function of the solid particle diameter for liquid viscosities of 10 c. P, 20 c. P and 50 c. P. The volumetric flow rate is 120 m 3/d.

Separation Efficiency x Liquid Flow Rate UNICAMP Predicted separation efficiency as a function of the volumetric flow rate for liquid viscosities of 1 c. P, 40 c. P, 60 c. P and 100 c. P. The particle size is 900 mm.

Separation Efficiency x Jet Area UNICAMP Predicted separation efficiency as a function of the jet discharge area for liquid viscosities of 10 c. P, 30 c. P and 60 c. P. The particle size is 250 mm. The volumetric flow rate is 120 m 3/d
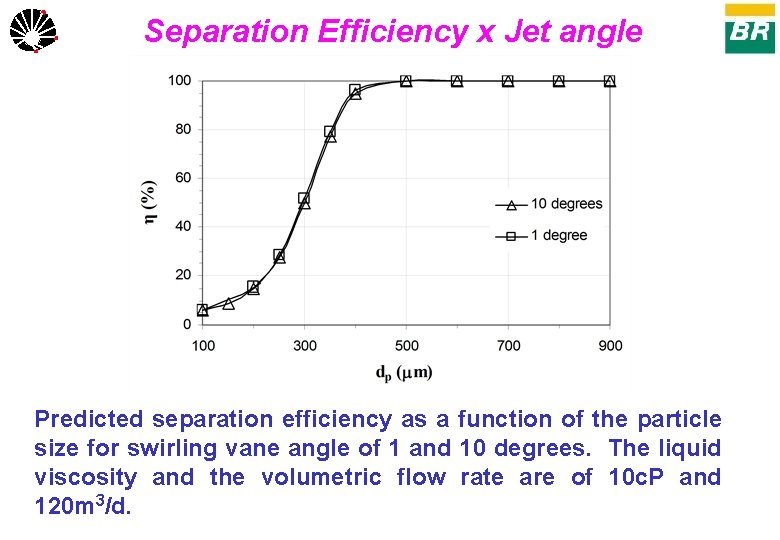
Separation Efficiency x Jet angle UNICAMP Predicted separation efficiency as a function of the particle size for swirling vane angle of 1 and 10 degrees. The liquid viscosity and the volumetric flow rate are of 10 c. P and 120 m 3/d.

Conclusions UNICAMP • A simple correlation formula discloses how the separation efficiency changes with the viscosity change as well as with the liquid flow rate, particle size, jet area and jet angle. • The separation efficiency is augmented by increasing: the liquid flow rate and the particle diameter (obvious) or decreasing the jet area and the liquid viscosity. • Surprisingly enough, the swirl angle variations from 1 to 10 degrees with the horizontal do not affect the separation efficiency.
- Slides: 18