TRC Project Experimental Force Coefficients for a Sealed
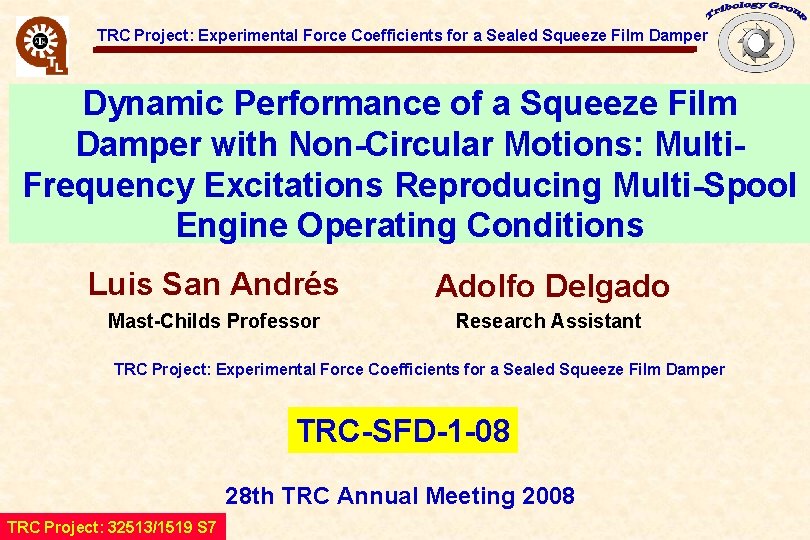
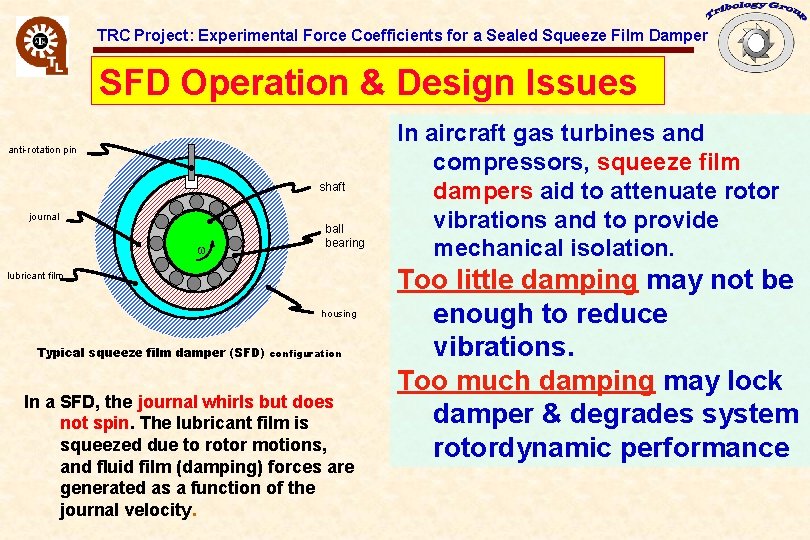
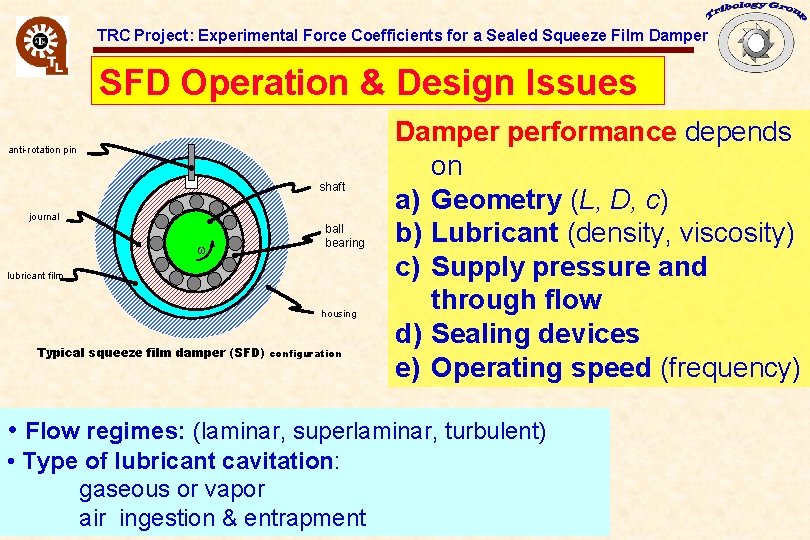
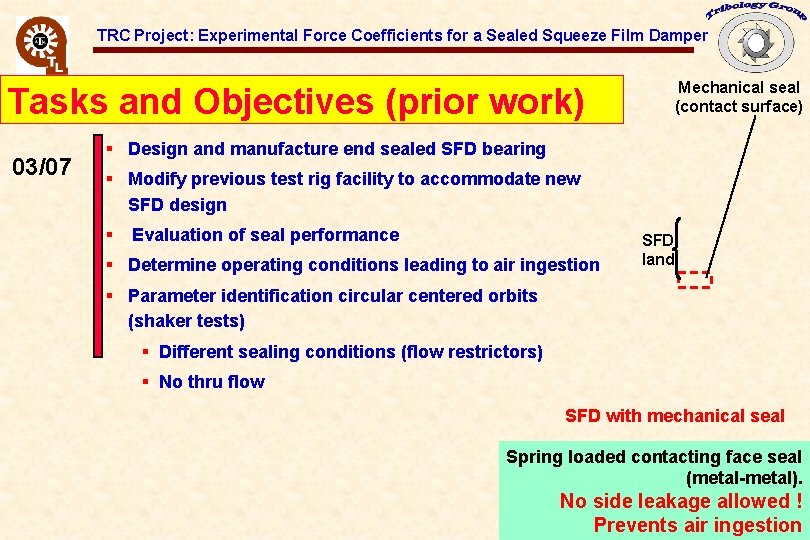
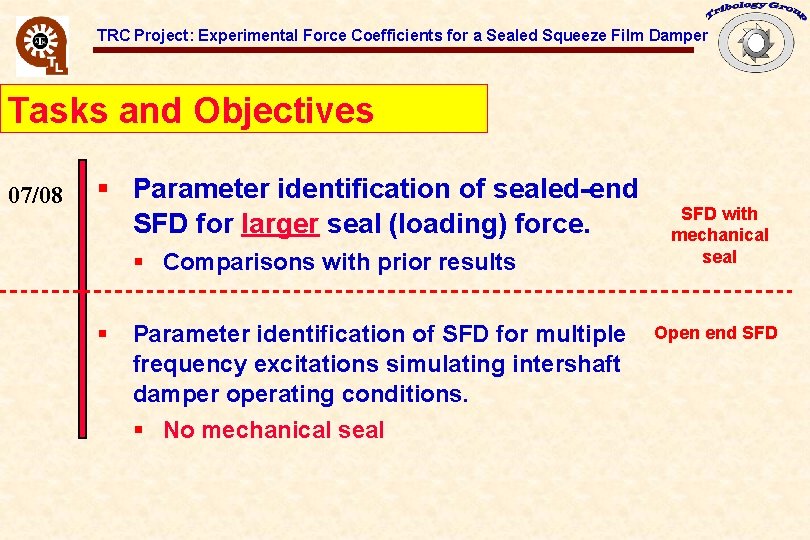
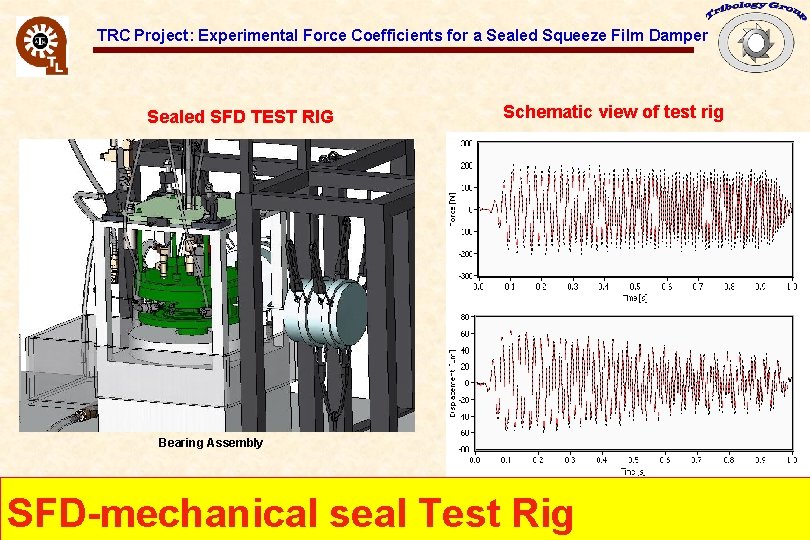
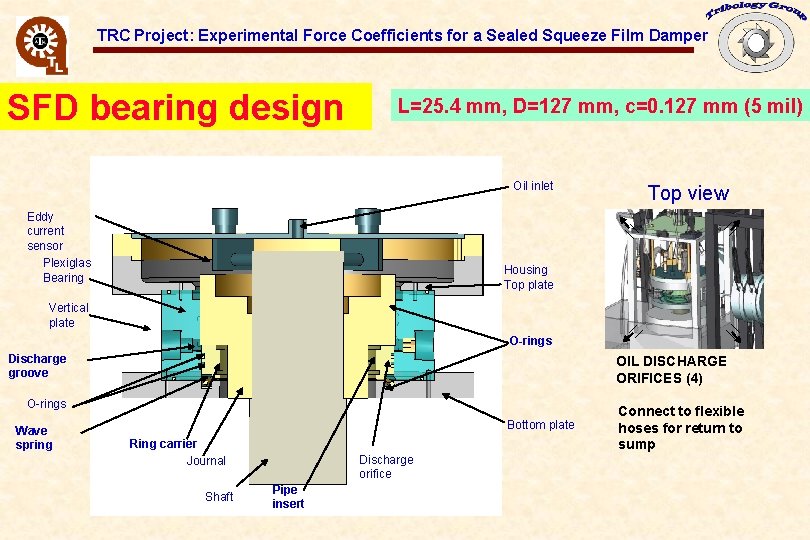
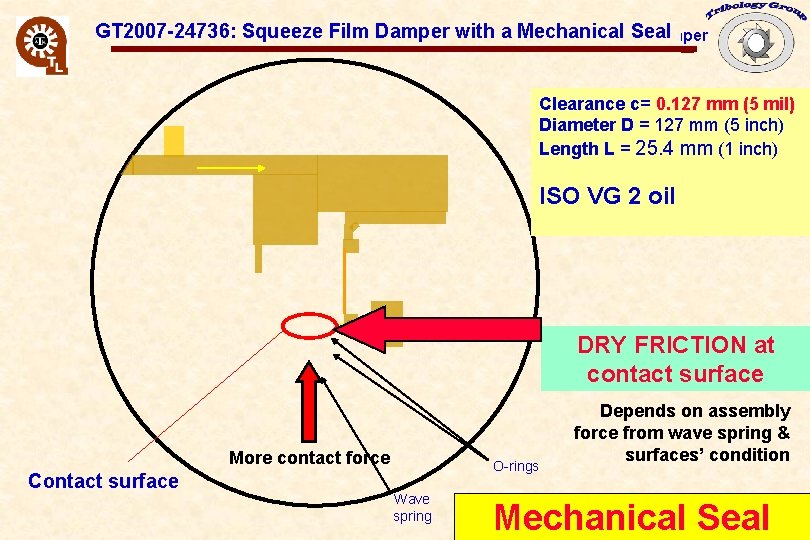
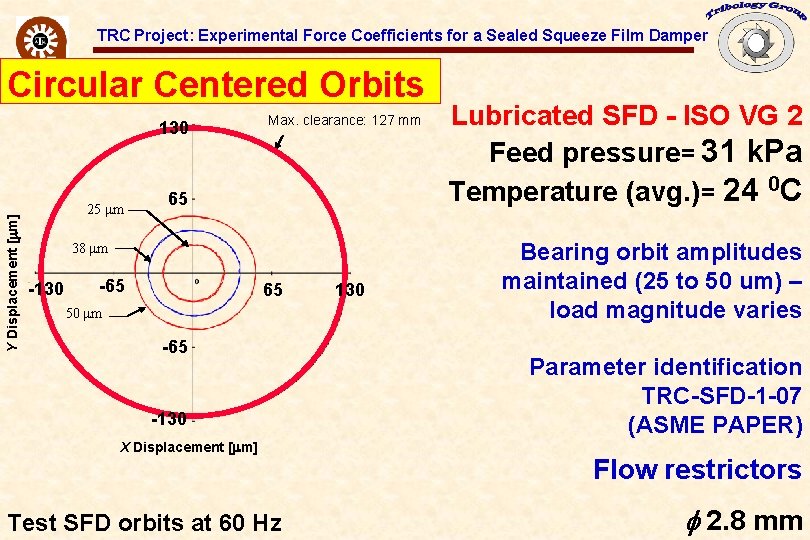
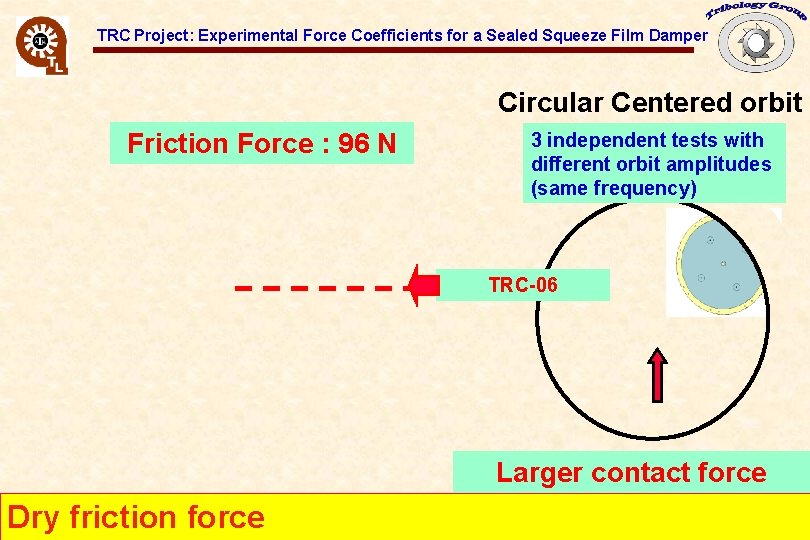
![Damping coefficient [k. N. s/m] TRC Project: Experimental Force Coefficients for a Sealed Squeeze Damping coefficient [k. N. s/m] TRC Project: Experimental Force Coefficients for a Sealed Squeeze](https://slidetodoc.com/presentation_image/536dd9c47d7626f4f73f882fad939e21/image-11.jpg)
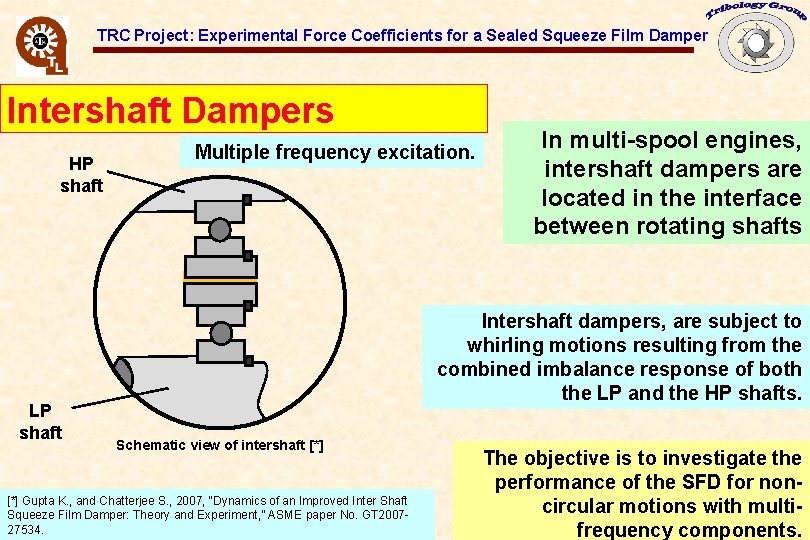
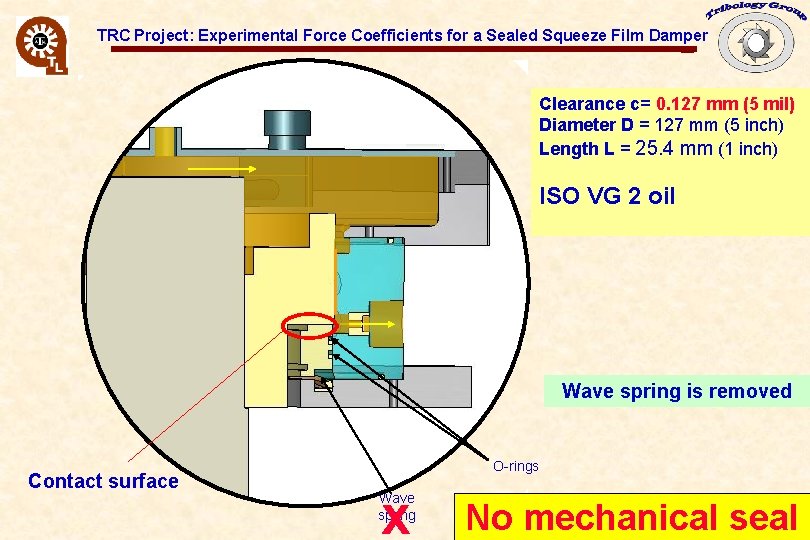
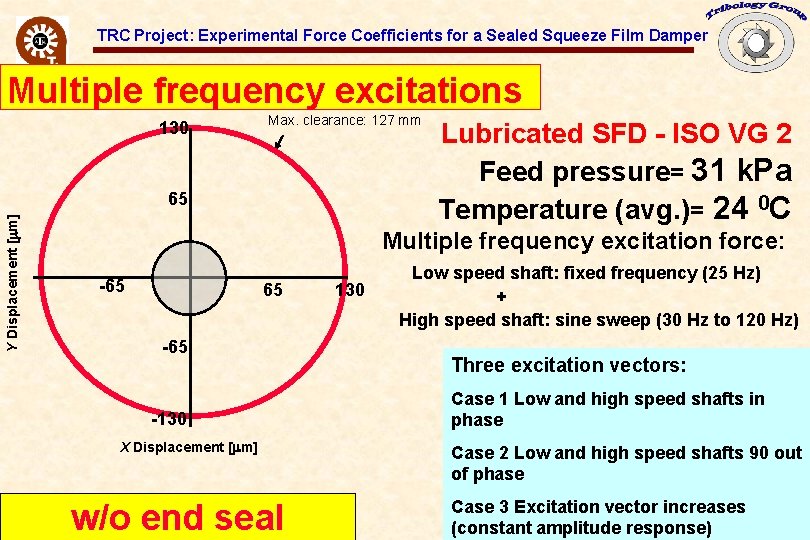
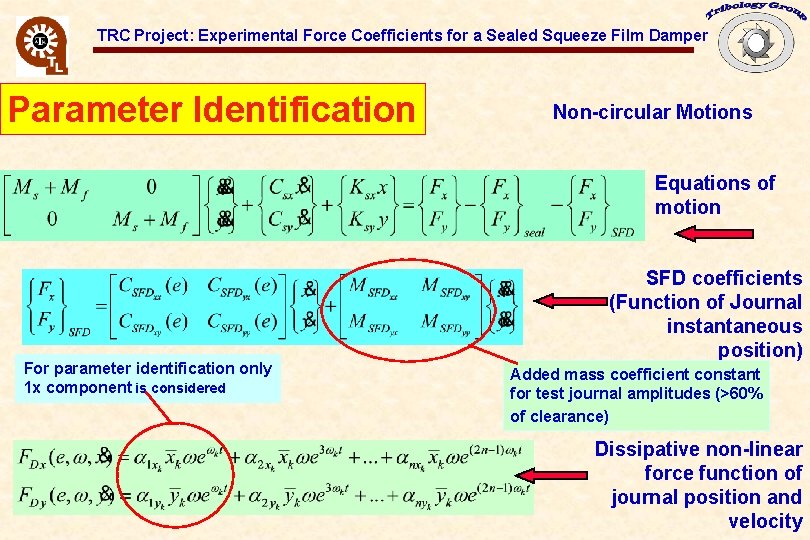
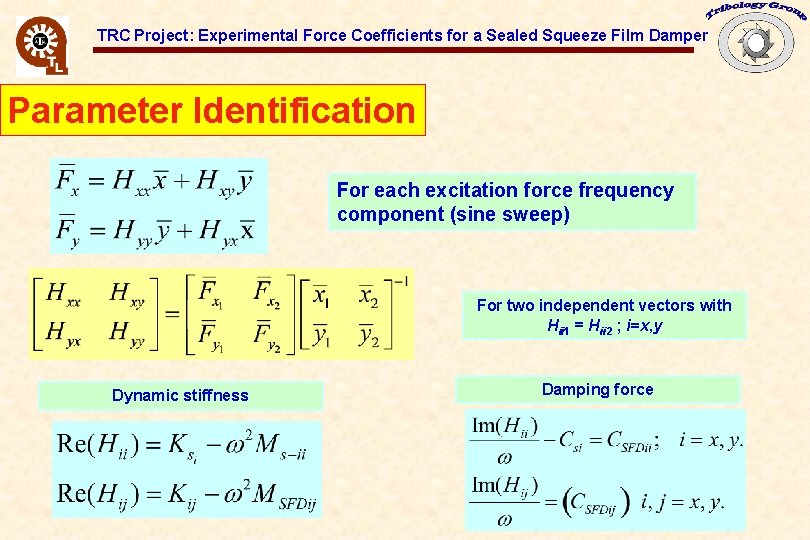
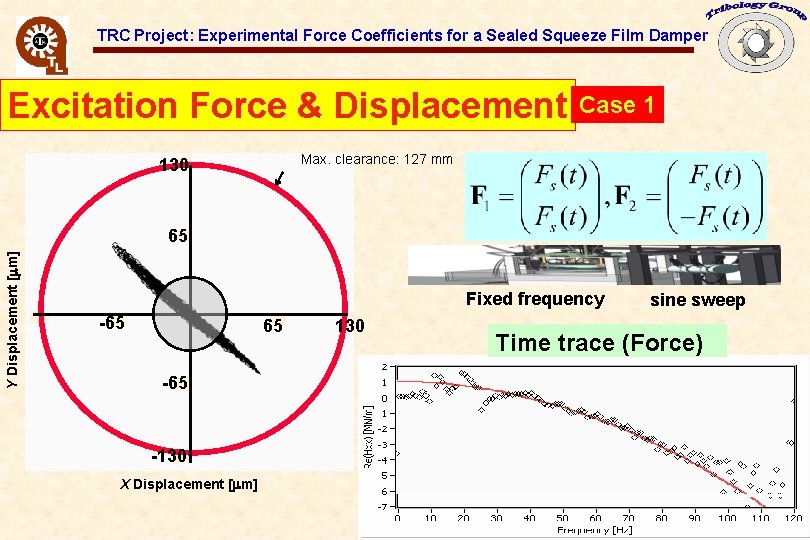
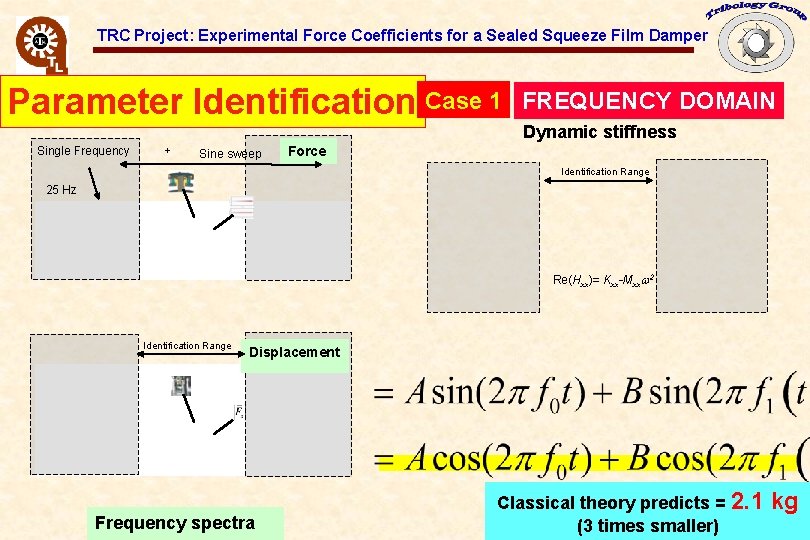
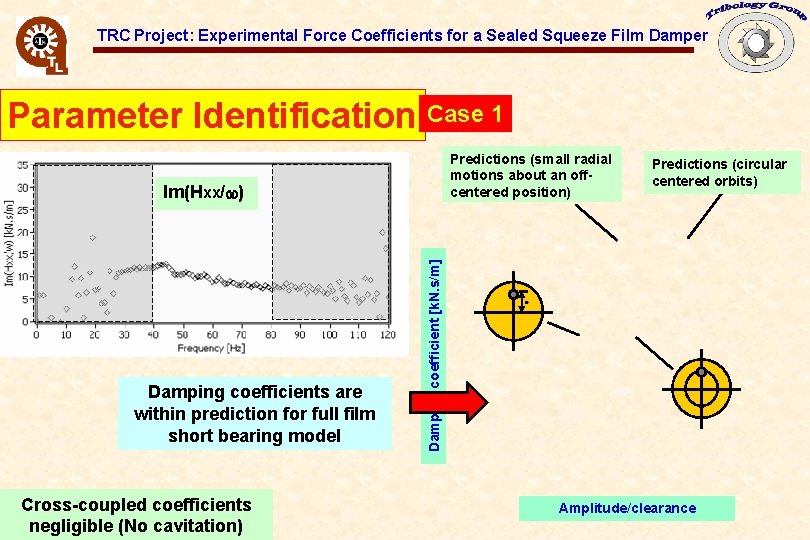
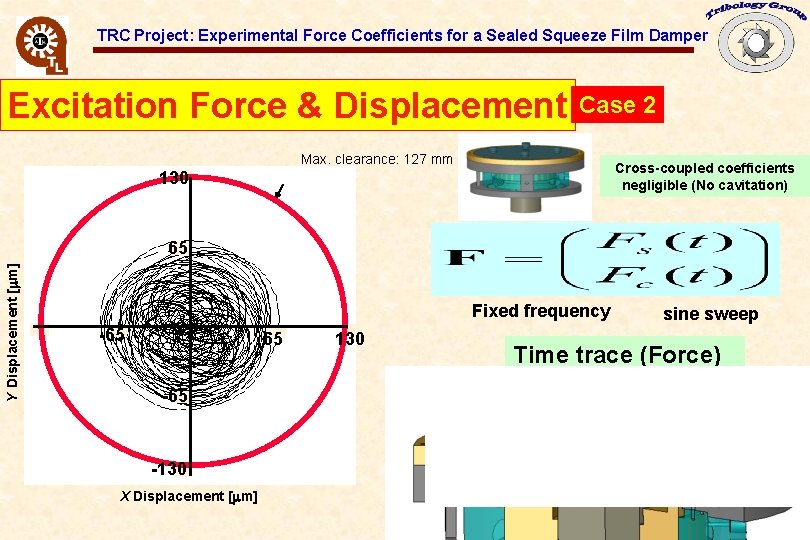
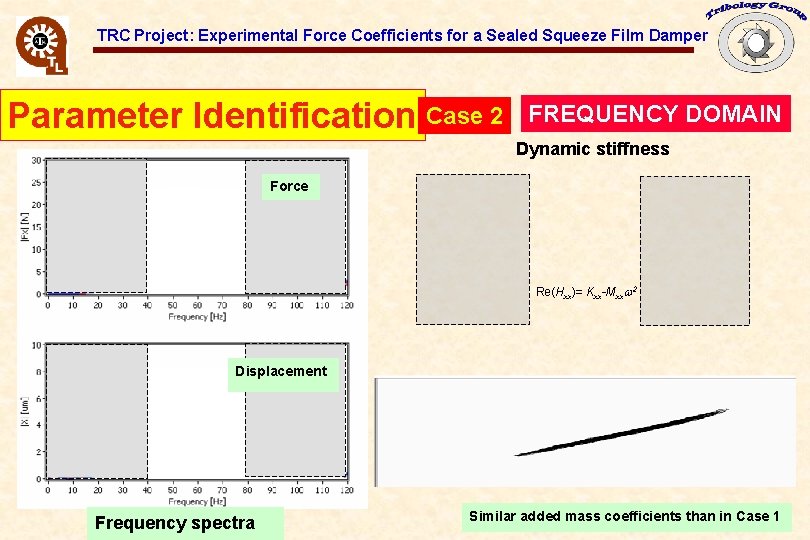
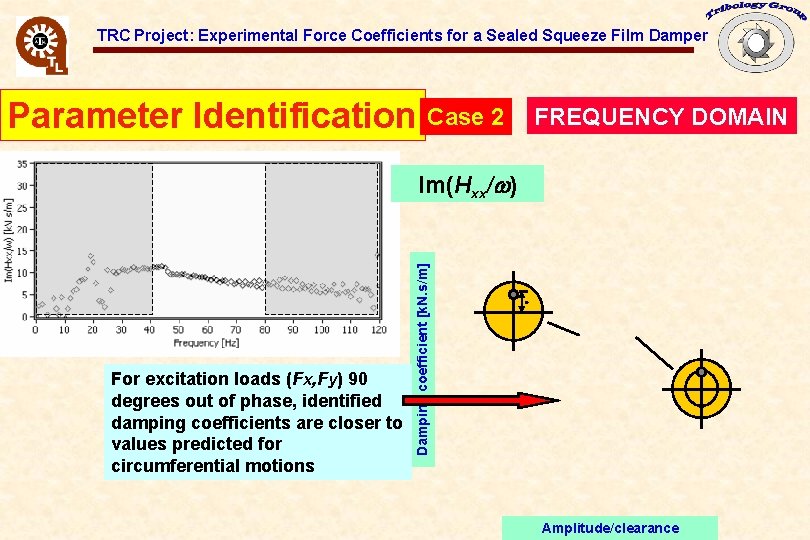
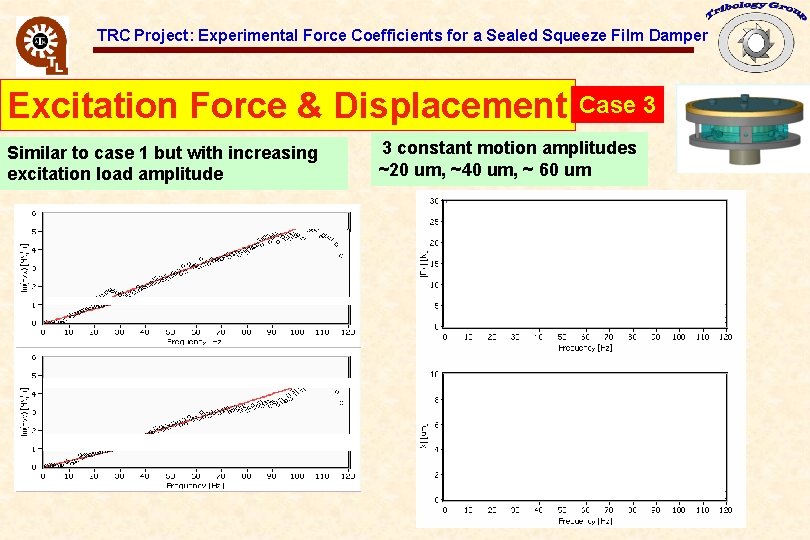
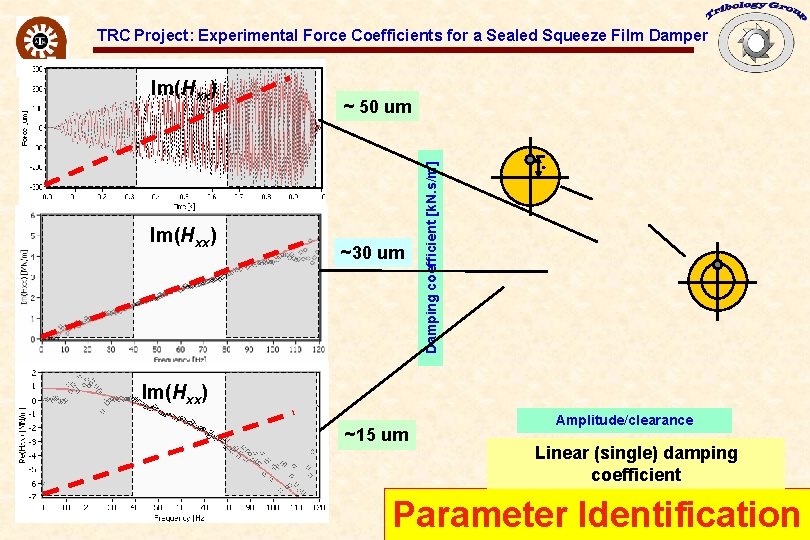
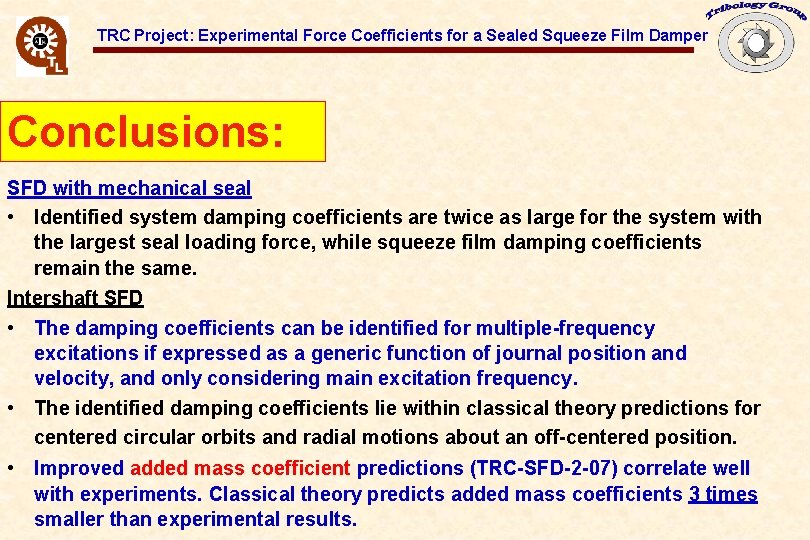
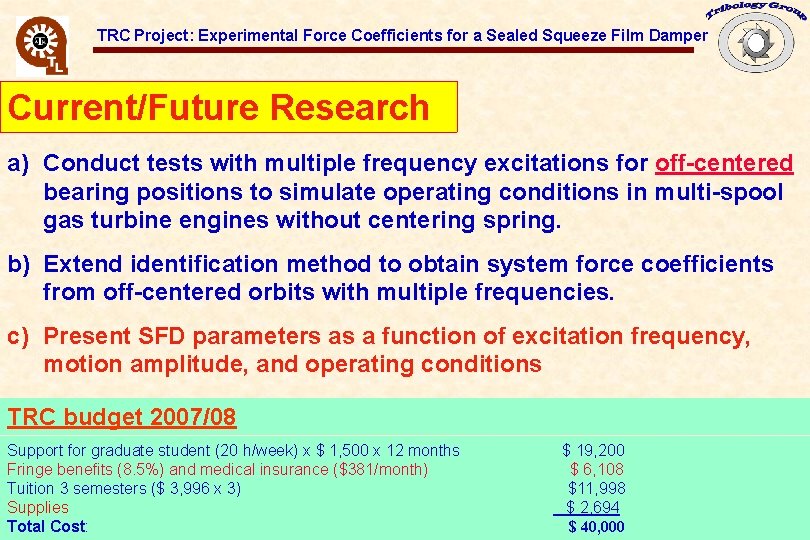

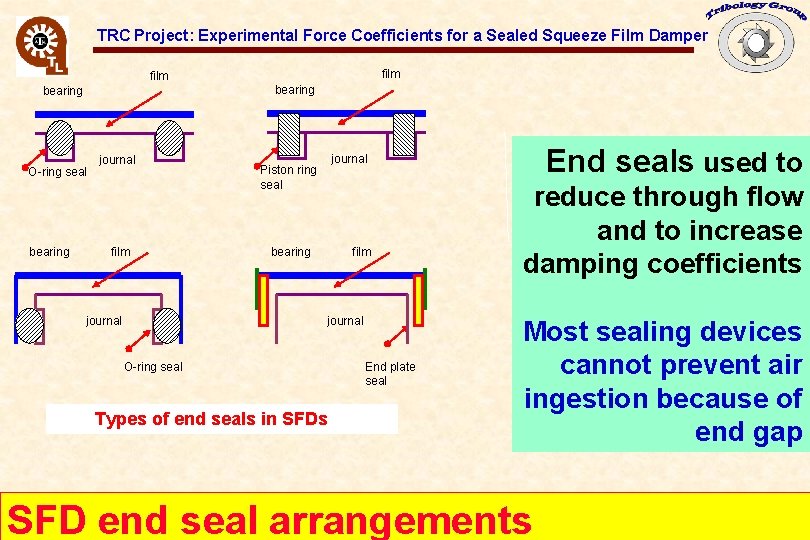
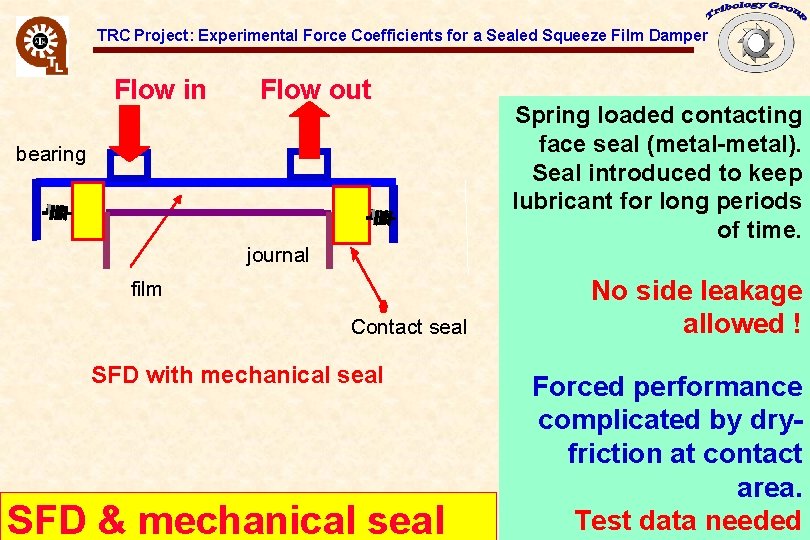
- Slides: 29
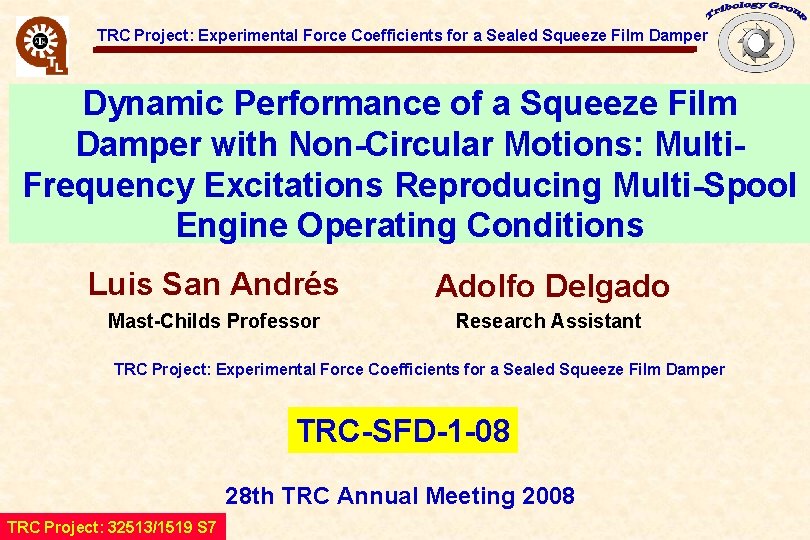
TRC Project: Experimental Force Coefficients for a Sealed Squeeze Film Damper Dynamic Performance of a Squeeze Film Damper with Non-Circular Motions: Multi. Frequency Excitations Reproducing Multi-Spool Engine Operating Conditions Luis San Andrés Adolfo Delgado Mast-Childs Professor Research Assistant TRC Project: Experimental Force Coefficients for a Sealed Squeeze Film Damper TRC-SFD-1 -08 28 th TRC Annual Meeting 2008 TRC Project: 32513/1519 S 7
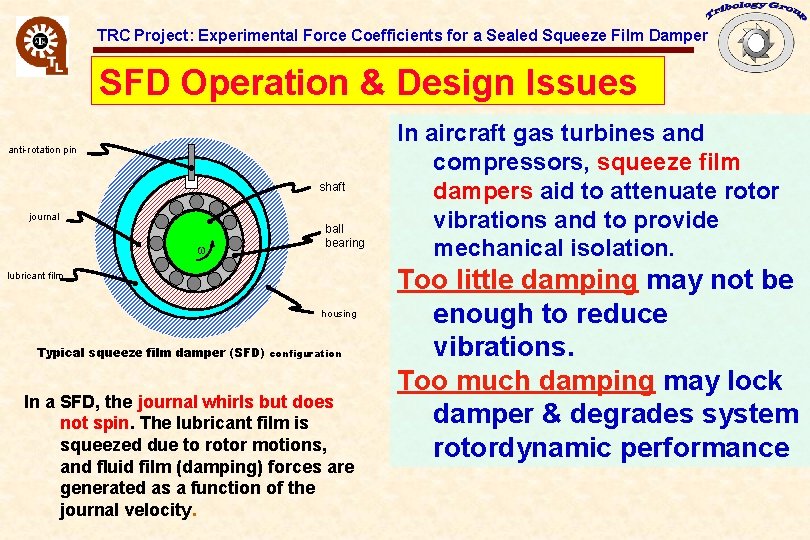
TRC Project: Experimental Force Coefficients for a Sealed Squeeze Film Damper SFD Operation & Design Issues anti-rotation pin shaft journal w ball bearing lubricant film housing Typical squeeze film damper (SFD) configuration In a SFD, the journal whirls but does not spin. The lubricant film is squeezed due to rotor motions, and fluid film (damping) forces are generated as a function of the journal velocity. In aircraft gas turbines and compressors, squeeze film dampers aid to attenuate rotor vibrations and to provide mechanical isolation. Too little damping may not be enough to reduce vibrations. Too much damping may lock damper & degrades system rotordynamic performance
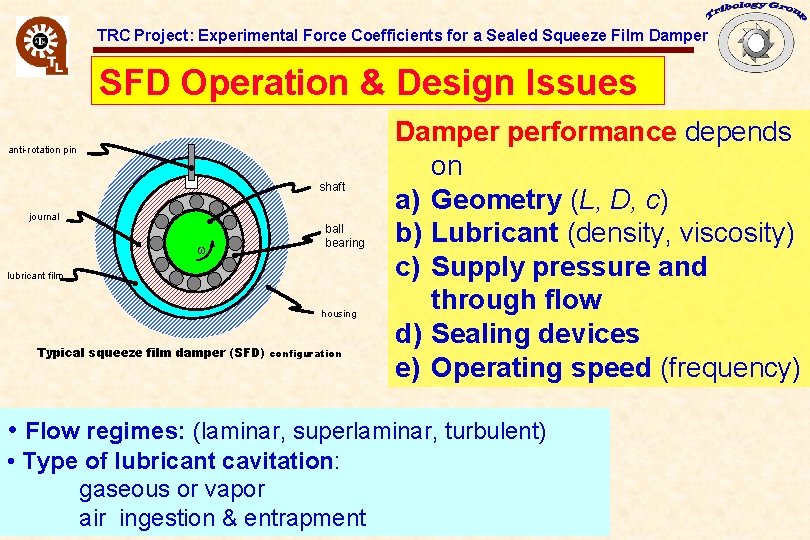
TRC Project: Experimental Force Coefficients for a Sealed Squeeze Film Damper SFD Operation & Design Issues anti-rotation pin shaft journal w ball bearing lubricant film housing Typical squeeze film damper (SFD) configuration Damper performance depends on a) Geometry (L, D, c) b) Lubricant (density, viscosity) c) Supply pressure and through flow d) Sealing devices e) Operating speed (frequency) • Flow regimes: (laminar, superlaminar, turbulent) • Type of lubricant cavitation: gaseous or vapor air ingestion & entrapment
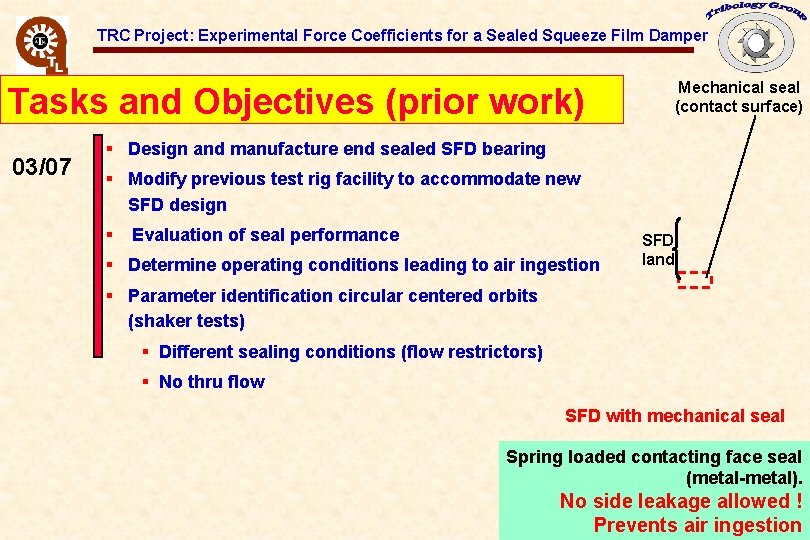
TRC Project: Experimental Force Coefficients for a Sealed Squeeze Film Damper Mechanical seal (contact surface) Tasks and Objectives (prior work) 03/07 § Design and manufacture end sealed SFD bearing § Modify previous test rig facility to accommodate new SFD design § Evaluation of seal performance § Determine operating conditions leading to air ingestion SFD land § Parameter identification circular centered orbits (shaker tests) § Different sealing conditions (flow restrictors) § No thru flow SFD with mechanical seal Spring loaded contacting face seal (metal-metal). No side leakage allowed ! Prevents air ingestion
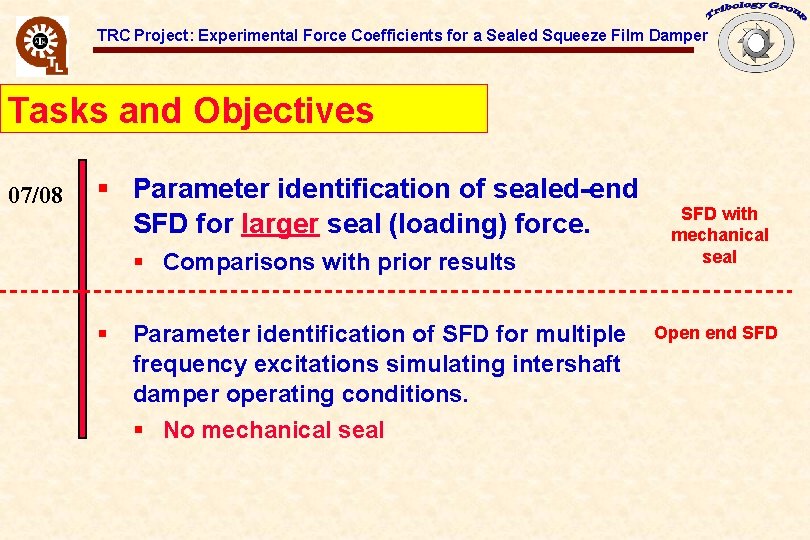
TRC Project: Experimental Force Coefficients for a Sealed Squeeze Film Damper Tasks and Objectives 07/08 § Parameter identification of sealed-end SFD for larger seal (loading) force. § Comparisons with prior results § Parameter identification of SFD for multiple frequency excitations simulating intershaft damper operating conditions. § No mechanical seal SFD with mechanical seal Open end SFD
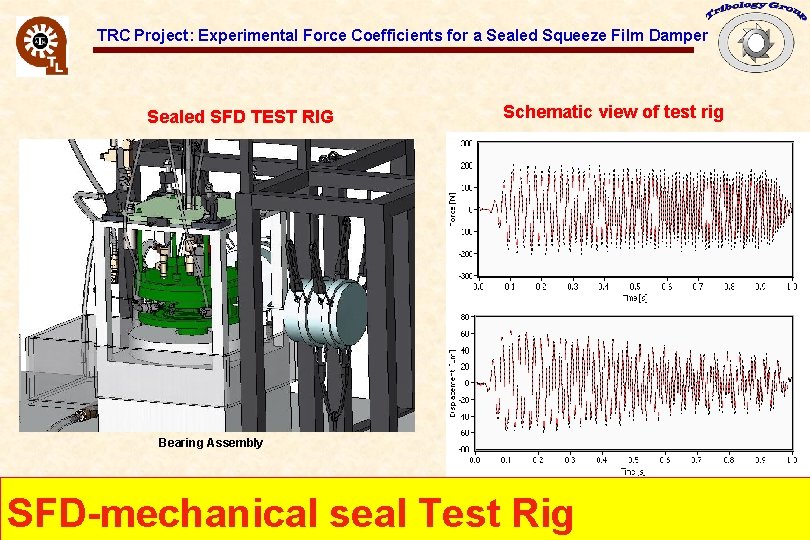
TRC Project: Experimental Force Coefficients for a Sealed Squeeze Film Damper Sealed SFD TEST RIG Schematic view of test rig Bearing Assembly SFD-mechanical seal Test Rig
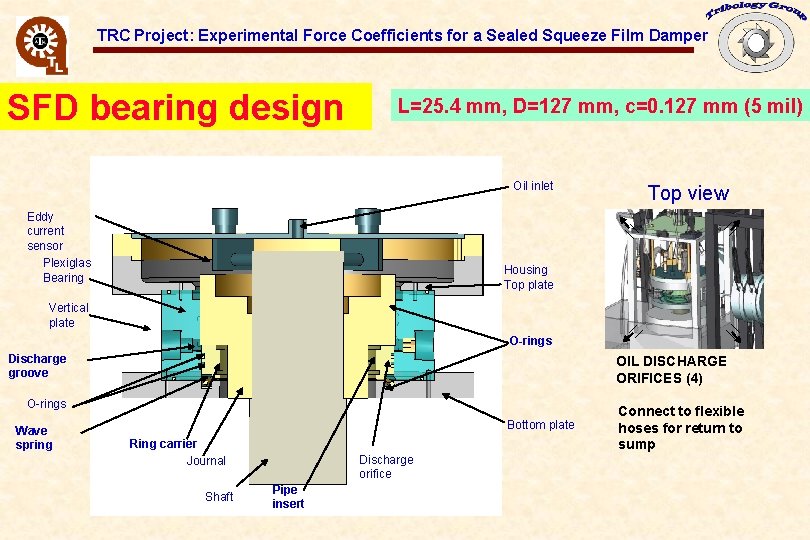
TRC Project: Experimental Force Coefficients for a Sealed Squeeze Film Damper SFD bearing design L=25. 4 mm, D=127 mm, c=0. 127 mm (5 mil) Oil inlet Eddy current sensor Plexiglas Bearing Top view Housing Top plate Vertical plate O-rings Discharge groove OIL DISCHARGE ORIFICES (4) O-rings Wave spring Bottom plate Ring carrier Journal Shaft Discharge orifice Pipe insert Connect to flexible hoses for return to sump
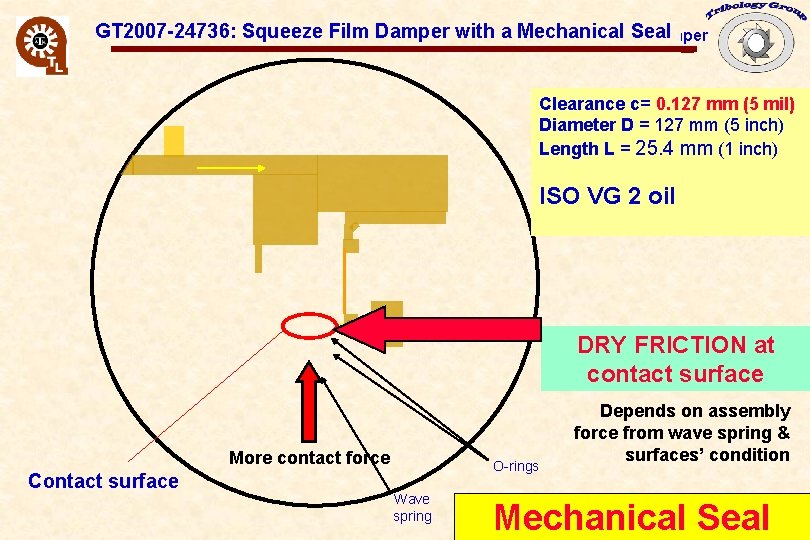
GT 2007 -24736: Squeeze Film Damperfor with a Mechanical Seal TRC Project: Experimental Force Coefficients a Sealed Squeeze Film Damper Clearance c= 0. 127 mm (5 mil) Diameter D = 127 mm (5 inch) Length L = 25. 4 mm (1 inch) ISO VG 2 oil DRY FRICTION at contact surface More contact force Contact surface O-rings Wave spring Depends on assembly force from wave spring & surfaces’ condition Mechanical Seal
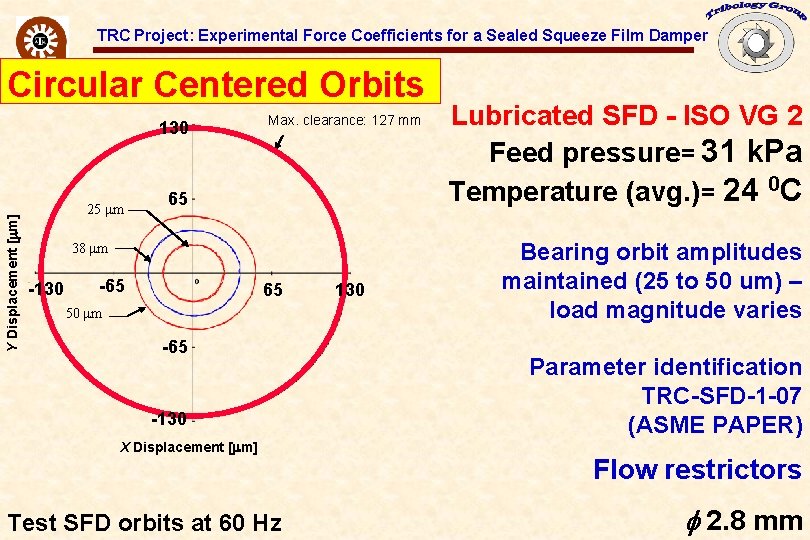
TRC Project: Experimental Force Coefficients for a Sealed Squeeze Film Damper Circular Centered Orbits Y Displacement [mm] 130 25 mm Max. clearance: 127 mm 65 38 mm -130 -65 65 50 mm -65 -130 X Displacement [mm] Test SFD orbits at 60 Hz 130 Lubricated SFD - ISO VG 2 Feed pressure= 31 k. Pa Temperature (avg. )= 24 0 C Bearing orbit amplitudes maintained (25 to 50 um) – load magnitude varies Parameter identification TRC-SFD-1 -07 (ASME PAPER) Flow restrictors f 2. 8 mm
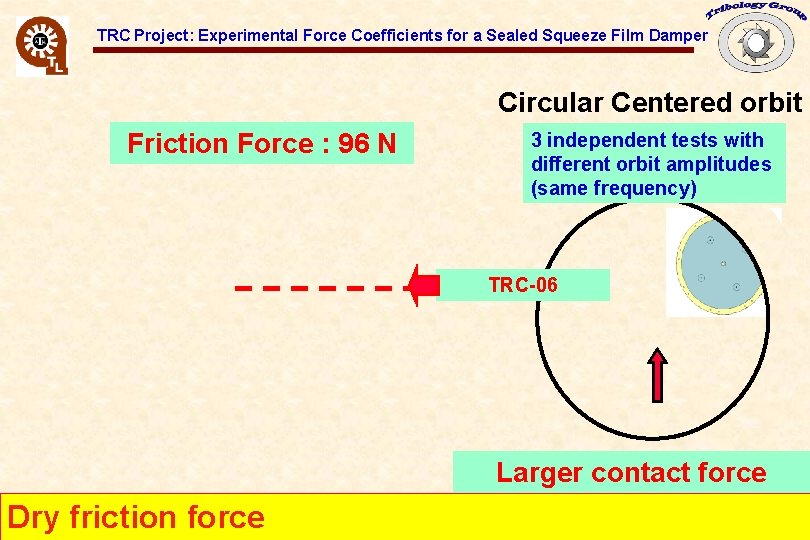
TRC Project: Experimental Force Coefficients for a Sealed Squeeze Film Damper Circular Centered orbit Friction Force : 96 N 3 independent tests with different orbit amplitudes (same frequency) TRC-06 Larger contact force Dry friction force
![Damping coefficient k N sm TRC Project Experimental Force Coefficients for a Sealed Squeeze Damping coefficient [k. N. s/m] TRC Project: Experimental Force Coefficients for a Sealed Squeeze](https://slidetodoc.com/presentation_image/536dd9c47d7626f4f73f882fad939e21/image-11.jpg)
Damping coefficient [k. N. s/m] TRC Project: Experimental Force Coefficients for a Sealed Squeeze Film Damper Dry friction force 97 N Cs-yy TRC-06 CSFDyy 34 N Equivalent “viscous” damping largest at low frequencies and smallest amplitudes of motion. Typical of systems with dryfriction (mechanical seal) System damping force is doubled (~3 x loading force) Squeeze film damping ~ independent of frequency and amplitude of motion. (for higher excitation frequencies) Squeeze film damper remains constant System Damping Coefficient vs. frequency
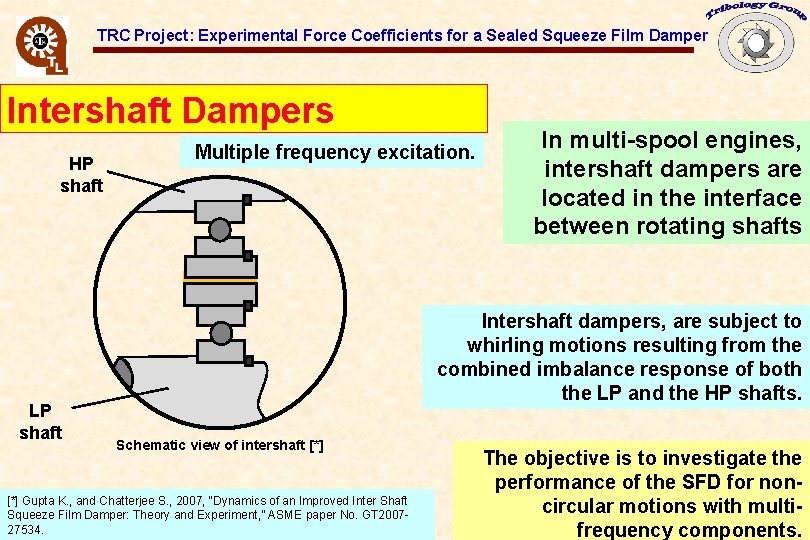
TRC Project: Experimental Force Coefficients for a Sealed Squeeze Film Damper Intershaft Dampers HP shaft LP shaft Multiple frequency excitation. In multi-spool engines, intershaft dampers are located in the interface between rotating shafts Intershaft dampers, are subject to whirling motions resulting from the combined imbalance response of both the LP and the HP shafts. Schematic view of intershaft [*] Gupta K. , and Chatterjee S. , 2007, “Dynamics of an Improved Inter Shaft Squeeze Film Damper: Theory and Experiment, ” ASME paper No. GT 200727534. The objective is to investigate the performance of the SFD for noncircular motions with multifrequency components.
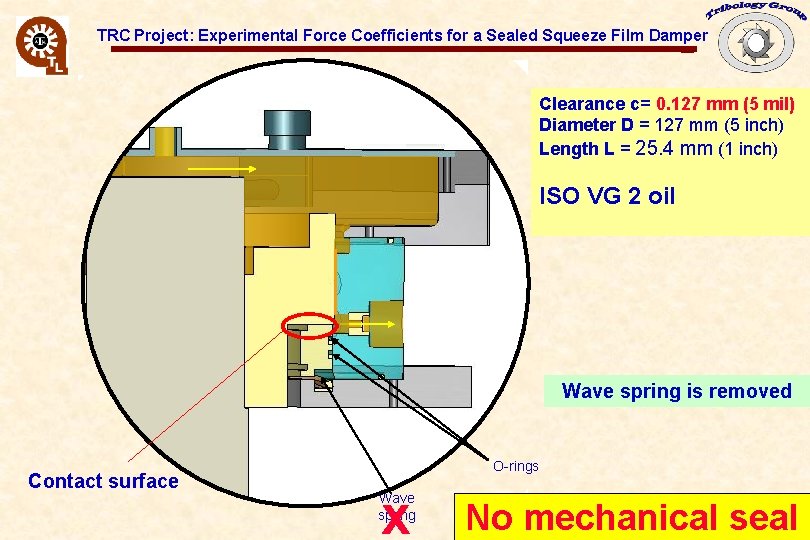
TRC Project: Experimental Force Coefficients for a Sealed Squeeze Film Damper Clearance c= 0. 127 mm (5 mil) Diameter D = 127 mm (5 inch) Length L = 25. 4 mm (1 inch) ISO VG 2 oil Wave spring is removed Contact surface O-rings x Wave spring No mechanical seal
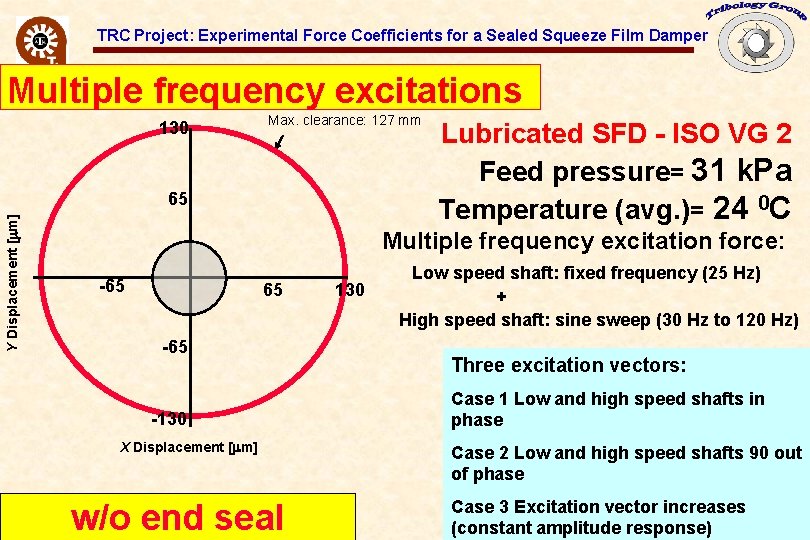
TRC Project: Experimental Force Coefficients for a Sealed Squeeze Film Damper Multiple frequency excitations 130 Max. clearance: 127 mm Y Displacement [mm] 65 Lubricated SFD - ISO VG 2 Feed pressure= 31 k. Pa Temperature (avg. )= 24 0 C Multiple frequency excitation force: -65 65 -130 X Displacement [mm] w/o end seal 130 Low speed shaft: fixed frequency (25 Hz) + High speed shaft: sine sweep (30 Hz to 120 Hz) Three excitation vectors: Case 1 Low and high speed shafts in phase Case 2 Low and high speed shafts 90 out of phase Case 3 Excitation vector increases (constant amplitude response)
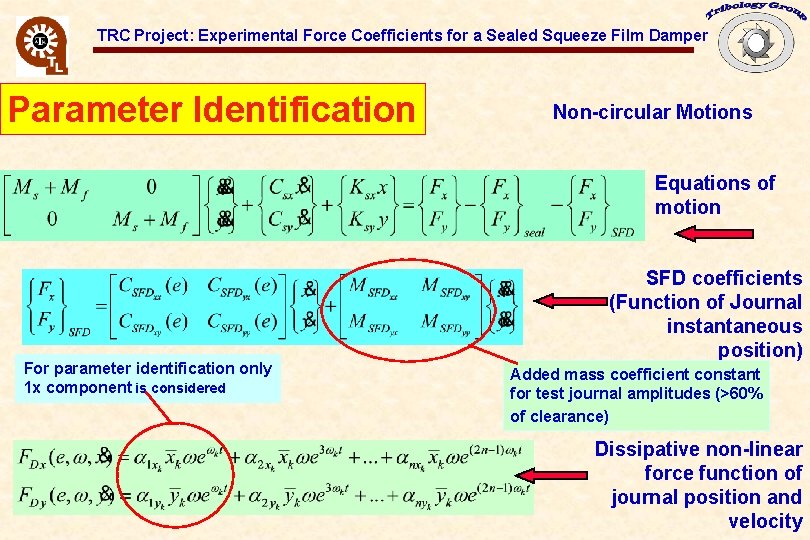
TRC Project: Experimental Force Coefficients for a Sealed Squeeze Film Damper Parameter Identification Non-circular Motions Equations of motion For parameter identification only 1 x component is considered SFD coefficients (Function of Journal instantaneous position) Added mass coefficient constant for test journal amplitudes (>60% of clearance) Dissipative non-linear force function of journal position and velocity
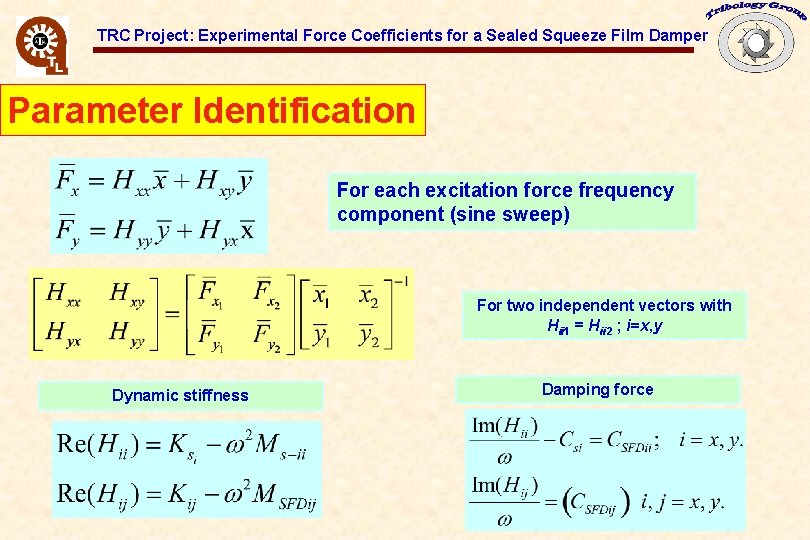
TRC Project: Experimental Force Coefficients for a Sealed Squeeze Film Damper Parameter Identification For each excitation force frequency component (sine sweep) For two independent vectors with Hii 1 = Hii 2 ; i=x, y Dynamic stiffness Damping force
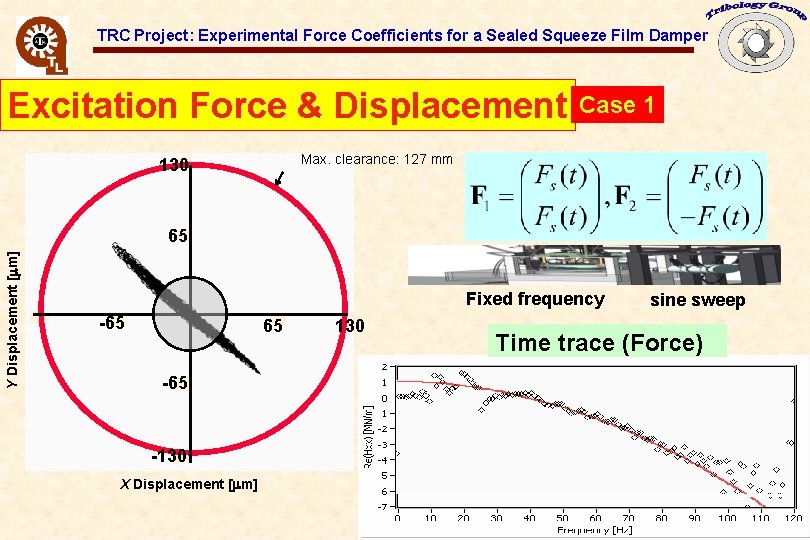
TRC Project: Experimental Force Coefficients for a Sealed Squeeze Film Damper Excitation Force & Displacement Case 1 Max. clearance: 127 mm 130 Y Displacement [mm] 65 Fixed frequency -65 65 -130 X Displacement [mm] 130 sine sweep Time trace (Force)
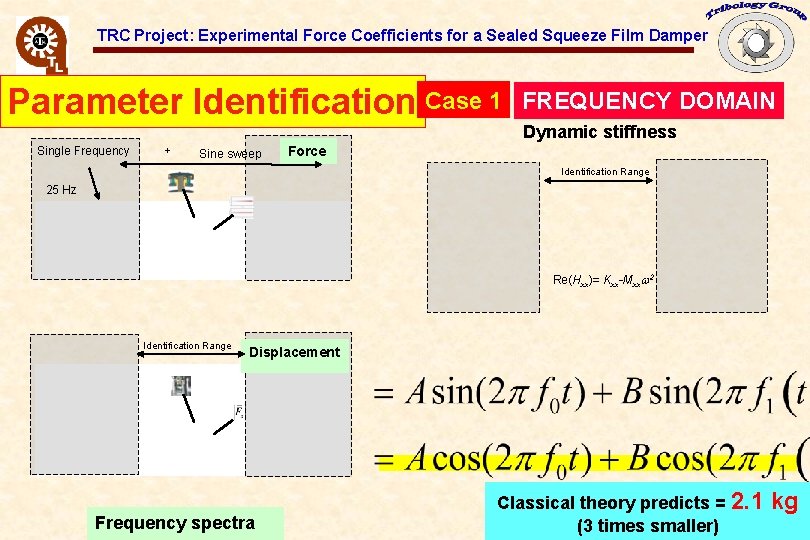
TRC Project: Experimental Force Coefficients for a Sealed Squeeze Film Damper Parameter Identification Case 1 Single Frequency + Sine sweep FREQUENCY DOMAIN Dynamic stiffness Force Identification Range 25 Hz Re(Hxx)= Kxx-Mxxw 2 Identification Range Displacement Frequency spectra Classical theory predicts = 2. 1 (3 times smaller) kg
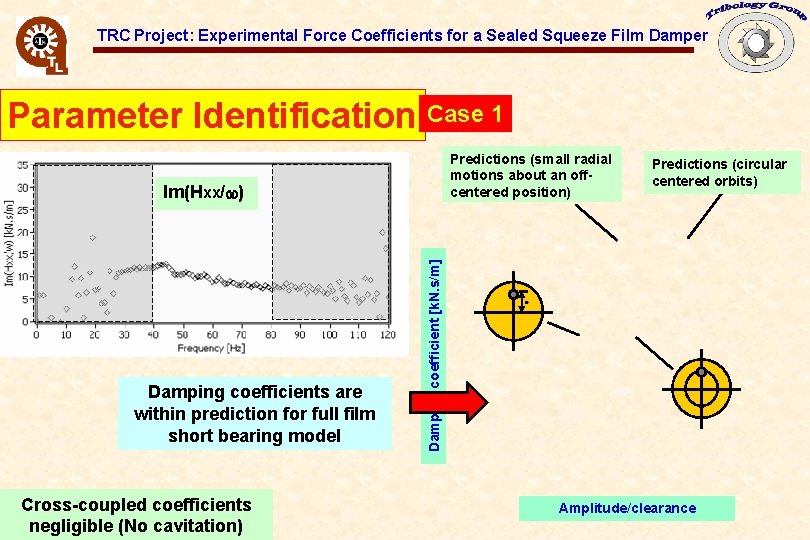
TRC Project: Experimental Force Coefficients for a Sealed Squeeze Film Damper Parameter Identification Case 1 Predictions (small radial motions about an offcentered position) Damping coefficients are within prediction for full film short bearing model Cross-coupled coefficients negligible (No cavitation) Damping coefficient [k. N. s/m] Im(Hxx/w) Predictions (circular centered orbits) e Amplitude/clearance
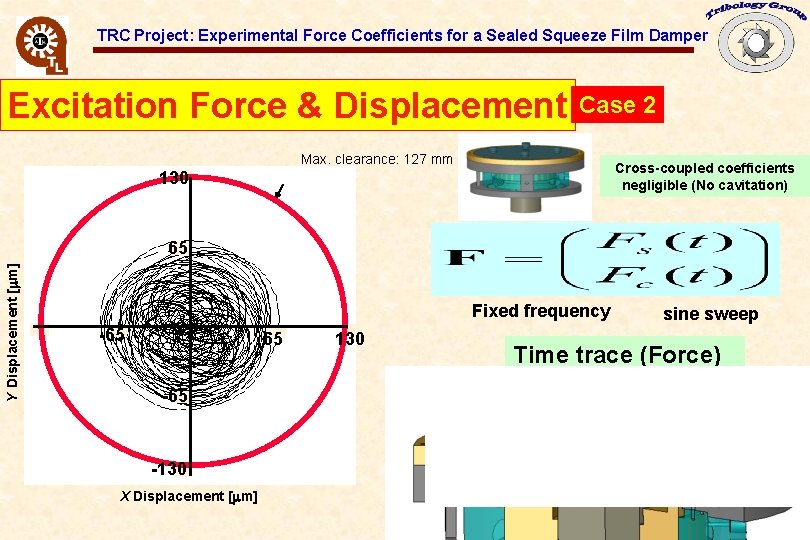
TRC Project: Experimental Force Coefficients for a Sealed Squeeze Film Damper Excitation Force & Displacement Case 2 Max. clearance: 127 mm Cross-coupled coefficients negligible (No cavitation) 130 Y Displacement [mm] 65 Fixed frequency -65 65 -130 X Displacement [mm] 130 sine sweep Time trace (Force)
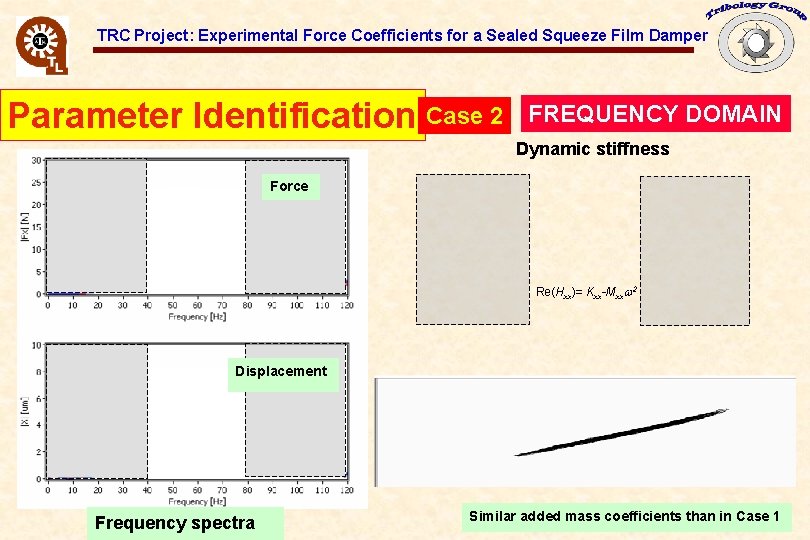
TRC Project: Experimental Force Coefficients for a Sealed Squeeze Film Damper Parameter Identification Case 2 FREQUENCY DOMAIN Dynamic stiffness Force Re(Hxx)= Kxx-Mxxw 2 Displacement Frequency spectra Similar added mass coefficients than in Case 1
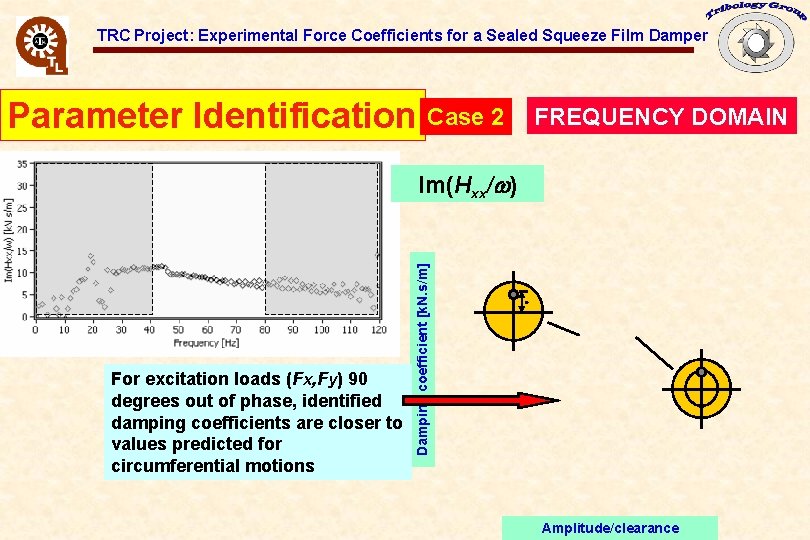
TRC Project: Experimental Force Coefficients for a Sealed Squeeze Film Damper Parameter Identification Case 2 FREQUENCY DOMAIN For excitation loads (Fx, Fy) 90 degrees out of phase, identified damping coefficients are closer to values predicted for circumferential motions Damping coefficient [k. N. s/m] Im(Hxx/w) e Amplitude/clearance
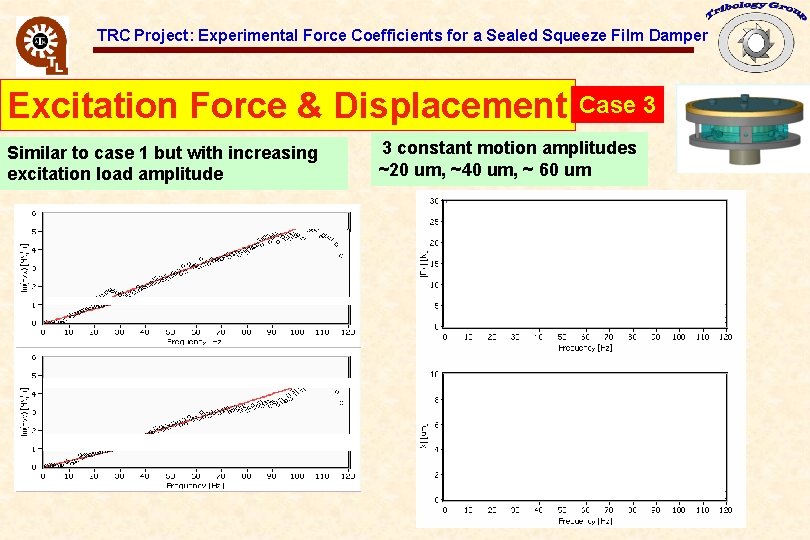
TRC Project: Experimental Force Coefficients for a Sealed Squeeze Film Damper Excitation Force & Displacement Similar to case 1 but with increasing excitation load amplitude Case 3 3 constant motion amplitudes ~20 um, ~40 um, ~ 60 um
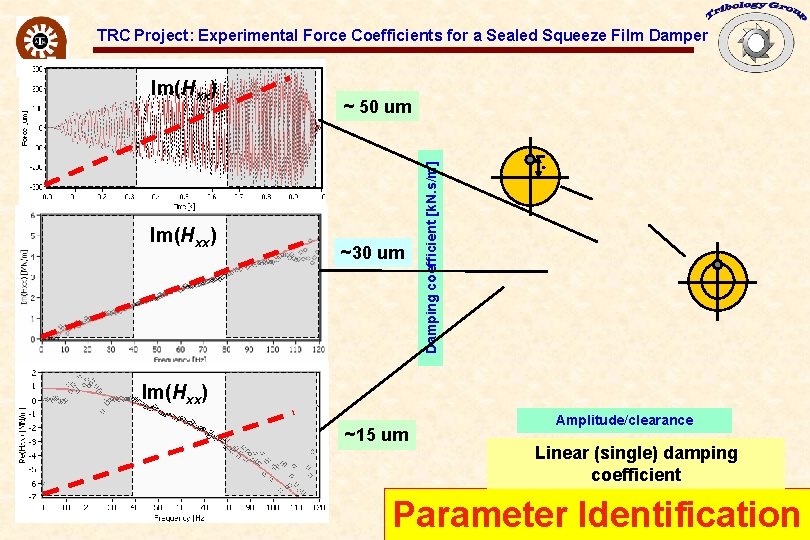
TRC Project: Experimental Force Coefficients for a Sealed Squeeze Film Damper Im(Hxx) ~ 50 um ~30 um Damping coefficient [k. N. s/m] Im(Hxx) e Im(Hxx) ~15 um Amplitude/clearance Linear (single) damping coefficient Parameter Identification
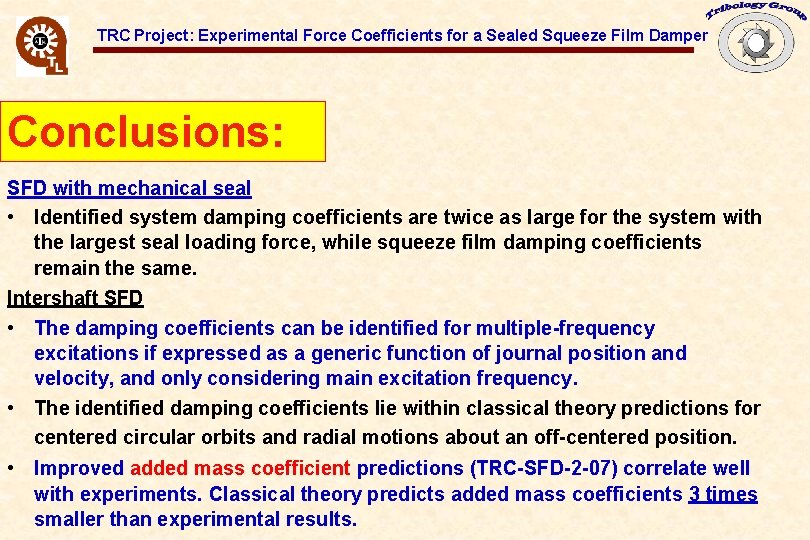
TRC Project: Experimental Force Coefficients for a Sealed Squeeze Film Damper Conclusions: SFD with mechanical seal • Identified system damping coefficients are twice as large for the system with the largest seal loading force, while squeeze film damping coefficients remain the same. Intershaft SFD • The damping coefficients can be identified for multiple-frequency excitations if expressed as a generic function of journal position and velocity, and only considering main excitation frequency. • The identified damping coefficients lie within classical theory predictions for centered circular orbits and radial motions about an off-centered position. • Improved added mass coefficient predictions (TRC-SFD-2 -07) correlate well with experiments. Classical theory predicts added mass coefficients 3 times smaller than experimental results.
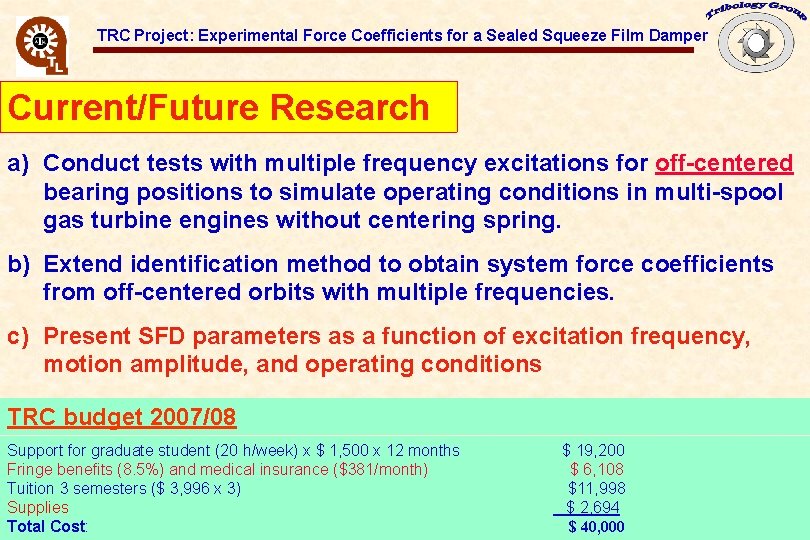
TRC Project: Experimental Force Coefficients for a Sealed Squeeze Film Damper Current/Future Research a) Conduct tests with multiple frequency excitations for off-centered bearing positions to simulate operating conditions in multi-spool gas turbine engines without centering spring. b) Extend identification method to obtain system force coefficients from off-centered orbits with multiple frequencies. c) Present SFD parameters as a function of excitation frequency, motion amplitude, and operating conditions TRC budget 2007/08 Support for graduate student (20 h/week) x $ 1, 500 x 12 months $ 19, 200 Fringe benefits (8. 5%) and medical insurance ($381/month) $ 6, 108 Tuition 3 semesters ($ 3, 996 X 3) $11, 998 Supplies $ 2, 694 Total Cost: $ 40, 000

TRC Project: Experimental Force Coefficients for a Sealed Squeeze Film Damper Relevant Past Work on SFDs • Della Pietra and Adilleta (2002): Comprehensive review of research conducted on SFDs over the last 40 years. • Parameter identification in SFDs: • • (1986) Roberts et al, (1990) Ellis et al. , (1995) Miller et al. (1999) Diaz and San Andrés Sealed SFDs • (1996) Levesley and Holmes • (1999) De Santiago and San Andrés (2005) Kim and Lee (2006, 2007) San Andrés and Delgado (SFD & MECHANICAL SEAL) • • IJTC 2006 -12041, GT 2006 -91238, GT 2007 -24736
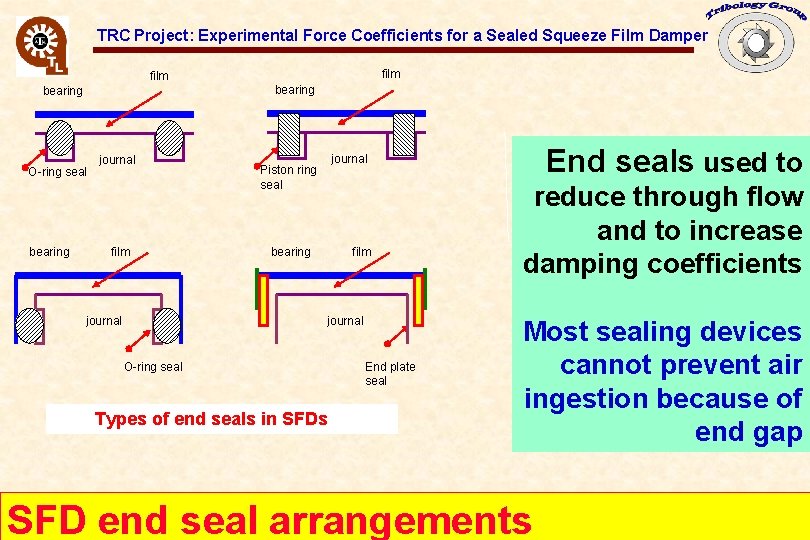
TRC Project: Experimental Force Coefficients for a Sealed Squeeze Film Damper film bearing O-ring seal bearing journal film journal End seals used to journal Piston ring seal bearing film journal O-ring seal Types of end seals in SFDs End plate seal reduce through flow and to increase damping coefficients Most sealing devices cannot prevent air ingestion because of end gap SFD end seal arrangements
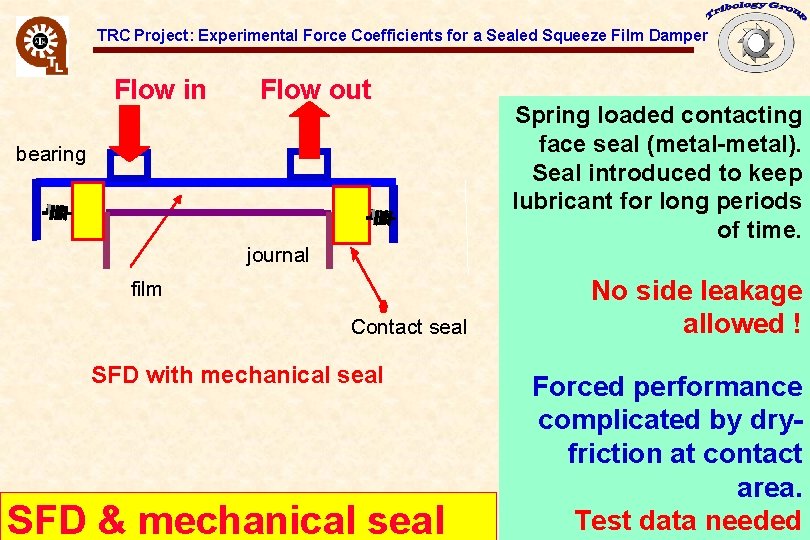
TRC Project: Experimental Force Coefficients for a Sealed Squeeze Film Damper Flow in Flow out bearing Spring loaded contacting face seal (metal-metal). Seal introduced to keep lubricant for long periods of time. journal film Contact seal SFD with mechanical seal SFD & mechanical seal No side leakage allowed ! Forced performance complicated by dryfriction at contact area. Test data needed