Total Productive Maintenance Chit Khin TEC 5133 Introduction
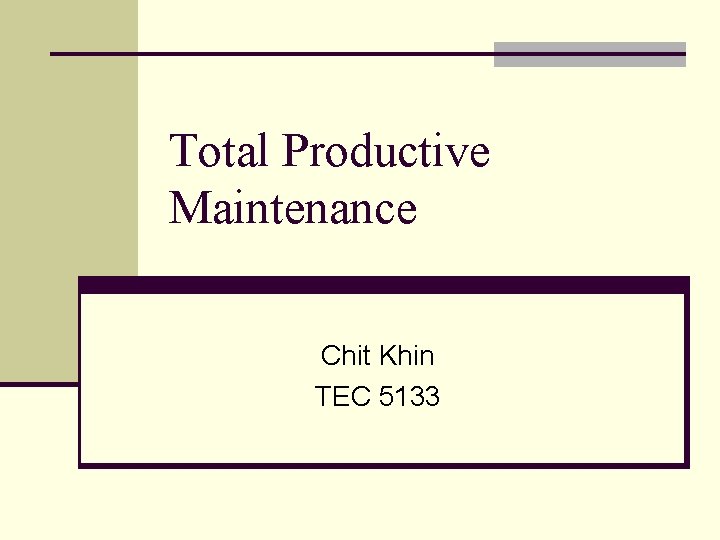
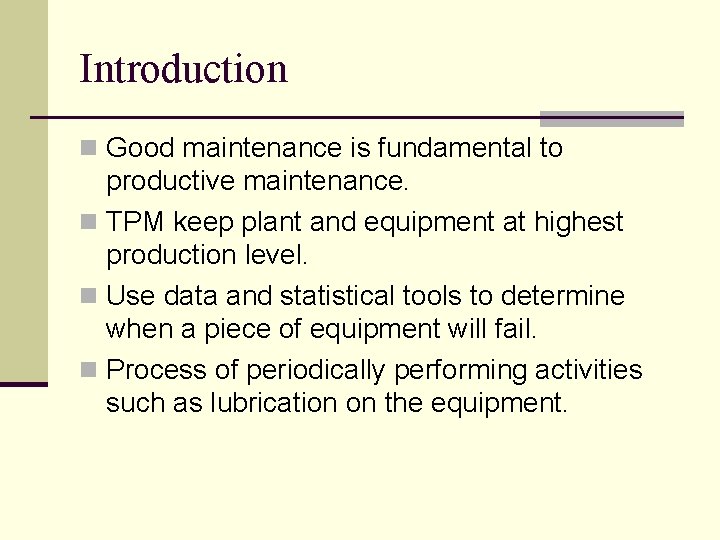
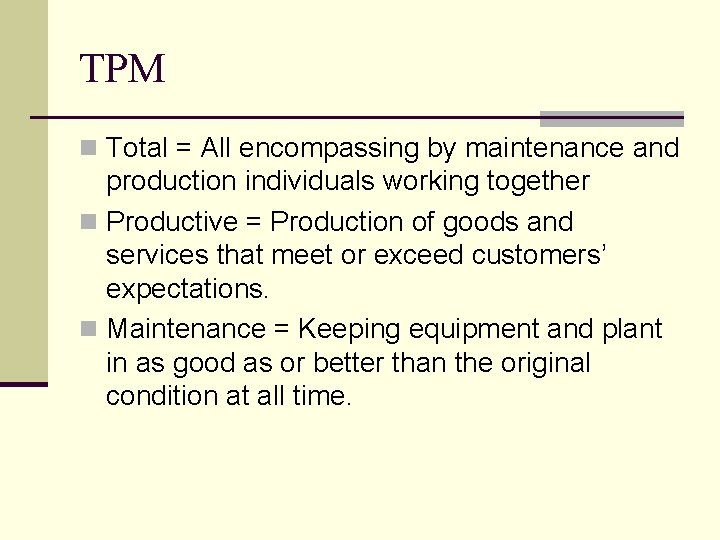
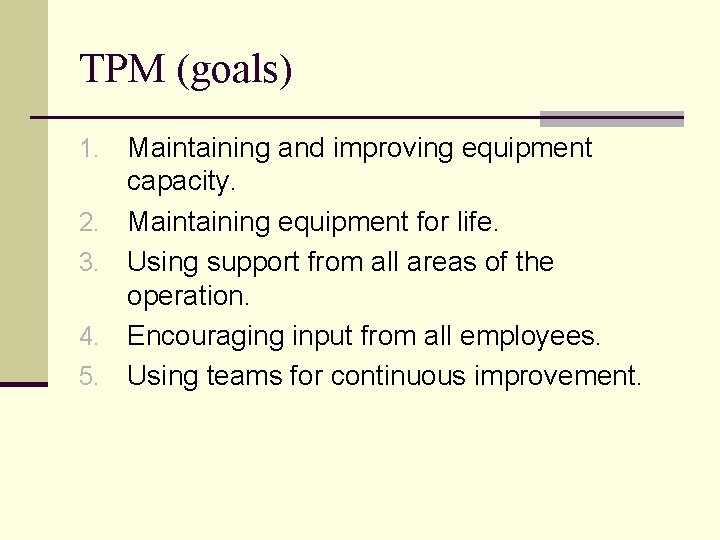
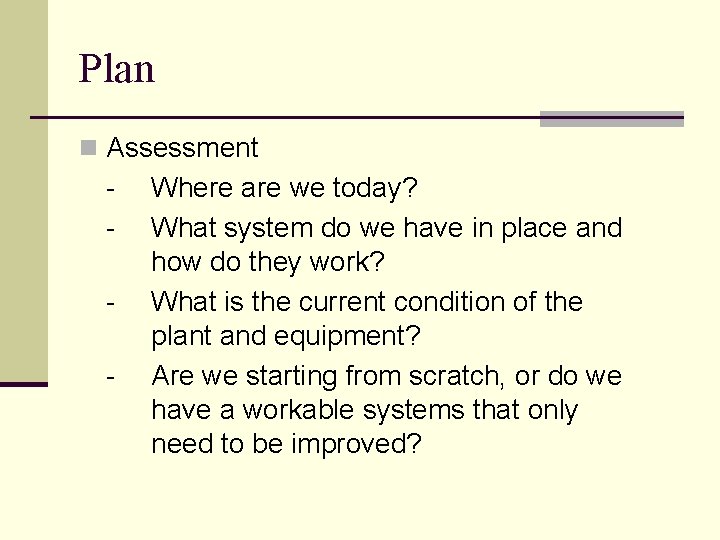
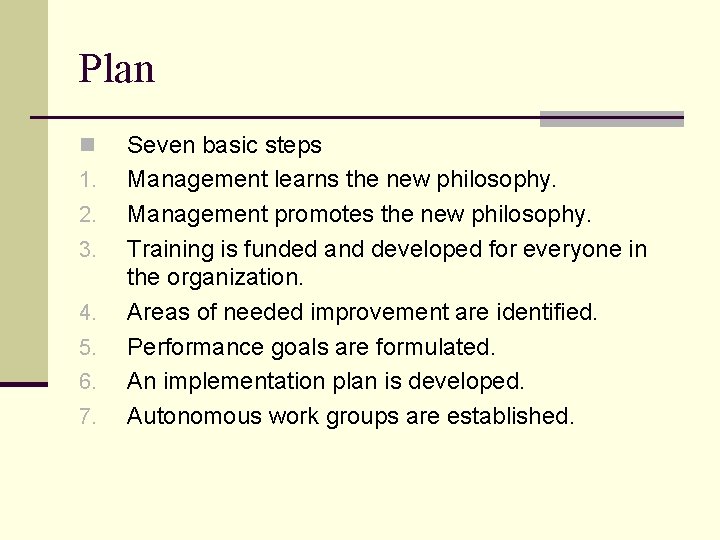
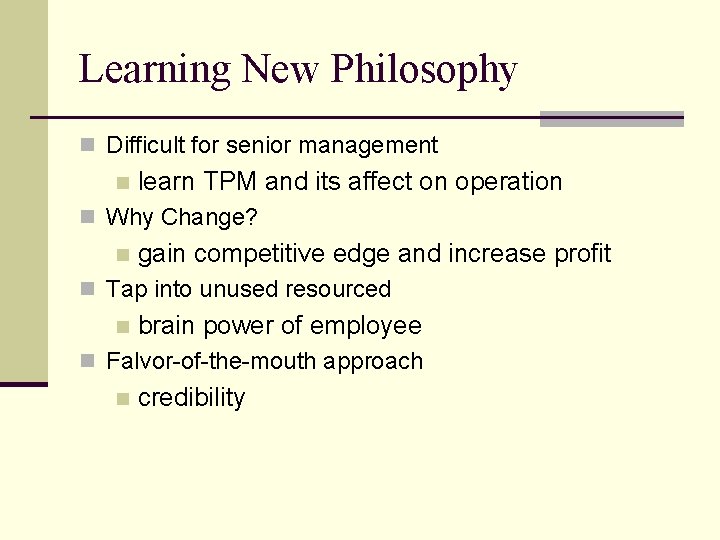
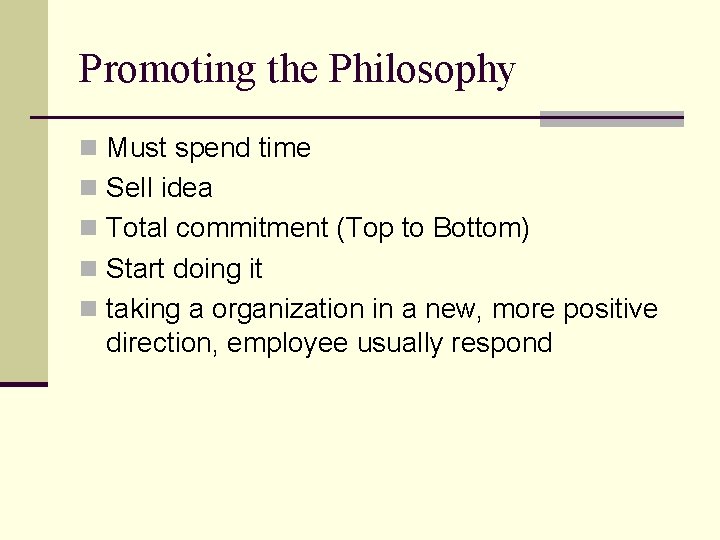
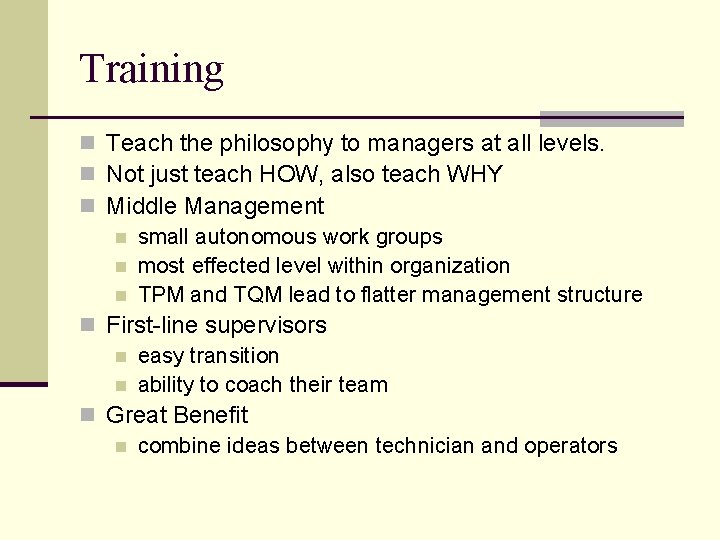
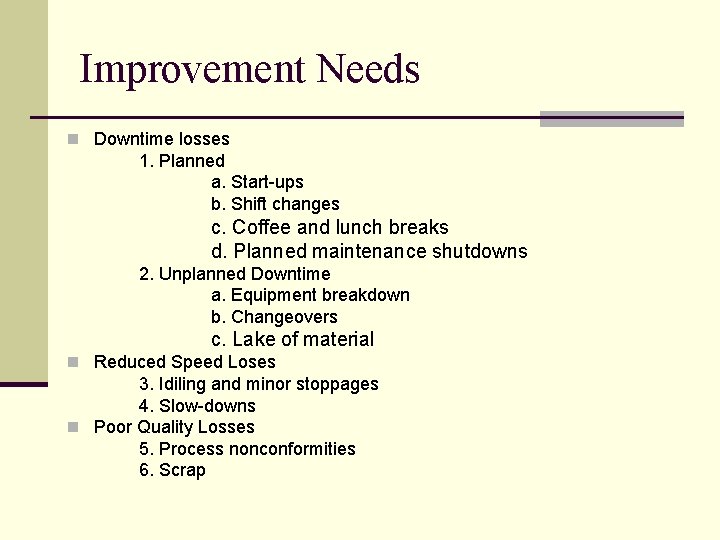
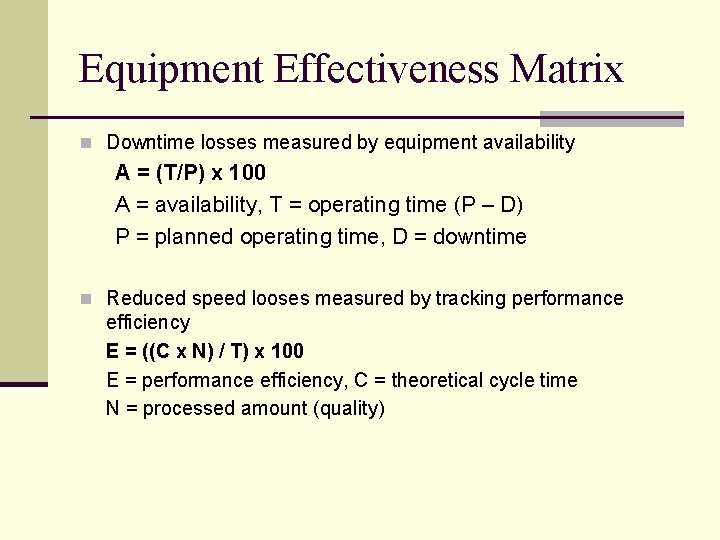
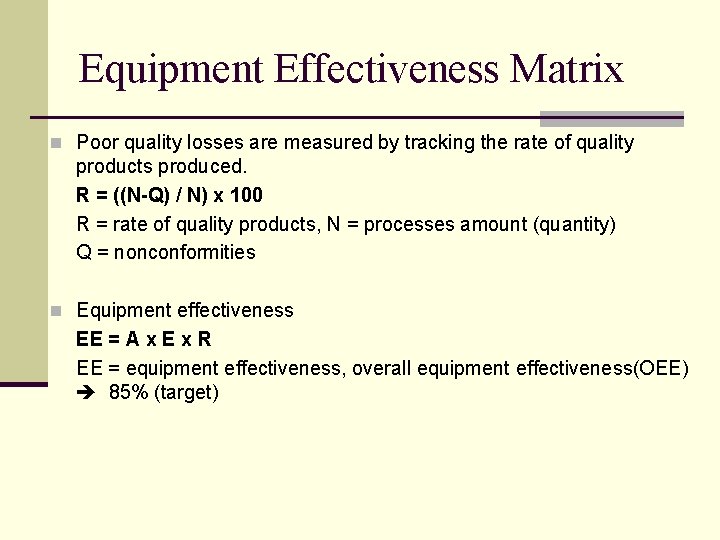
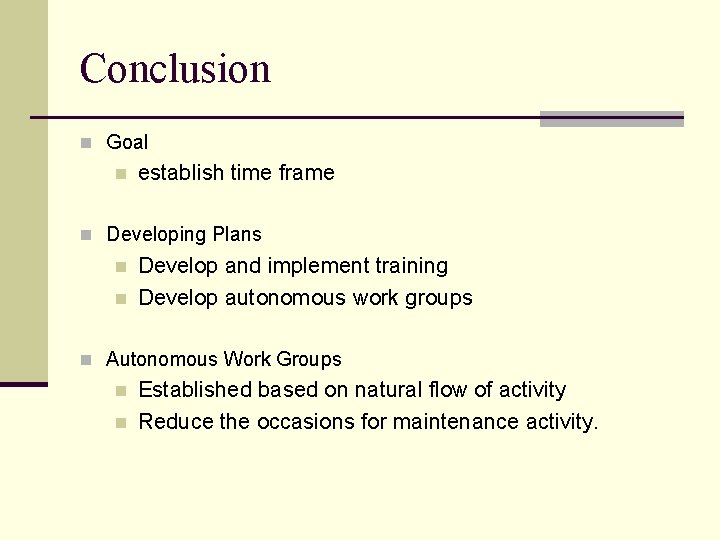
- Slides: 13
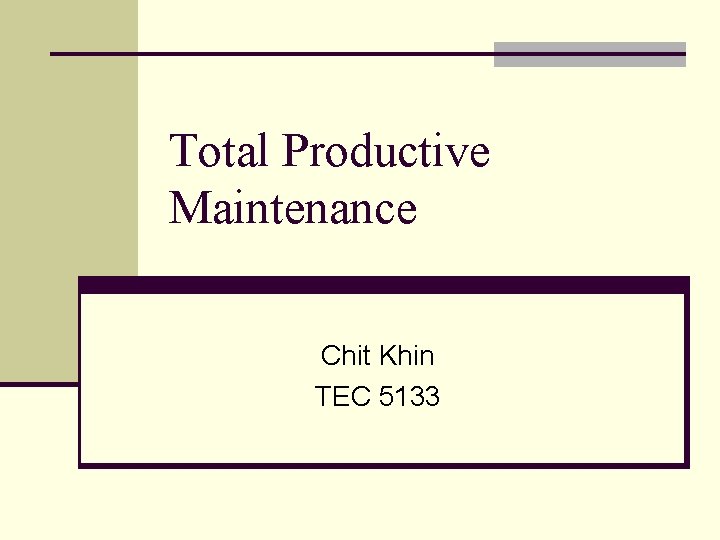
Total Productive Maintenance Chit Khin TEC 5133
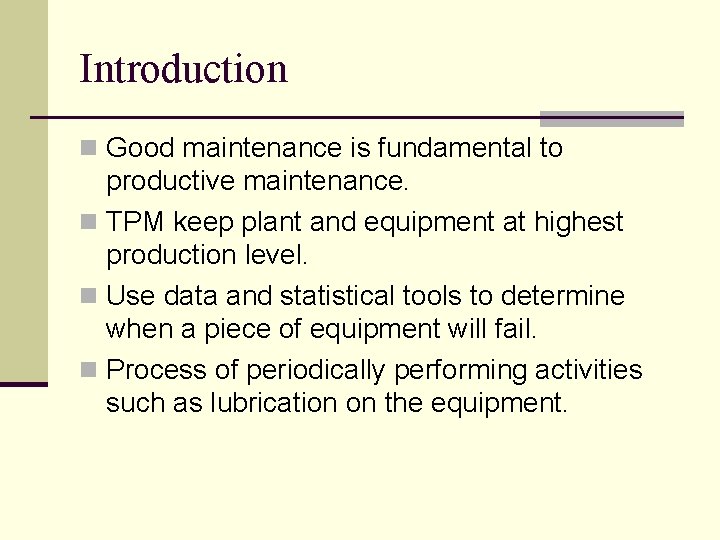
Introduction n Good maintenance is fundamental to productive maintenance. n TPM keep plant and equipment at highest production level. n Use data and statistical tools to determine when a piece of equipment will fail. n Process of periodically performing activities such as lubrication on the equipment.
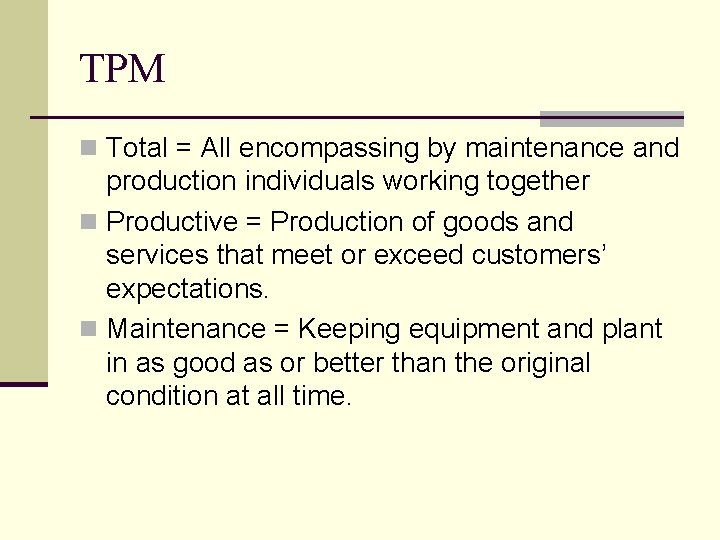
TPM n Total = All encompassing by maintenance and production individuals working together n Productive = Production of goods and services that meet or exceed customers’ expectations. n Maintenance = Keeping equipment and plant in as good as or better than the original condition at all time.
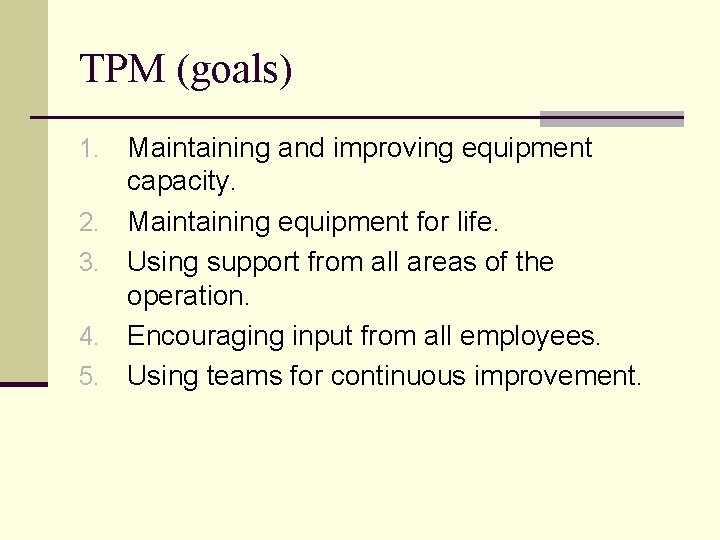
TPM (goals) 1. 2. 3. 4. 5. Maintaining and improving equipment capacity. Maintaining equipment for life. Using support from all areas of the operation. Encouraging input from all employees. Using teams for continuous improvement.
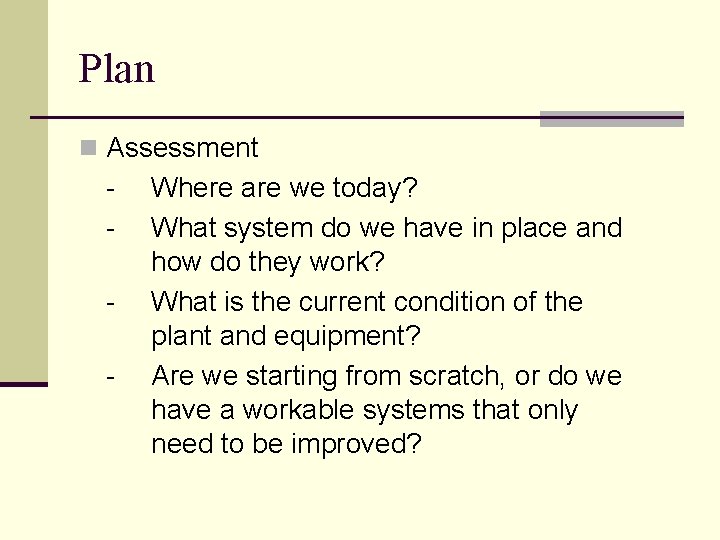
Plan n Assessment - Where are we today? What system do we have in place and how do they work? What is the current condition of the plant and equipment? Are we starting from scratch, or do we have a workable systems that only need to be improved?
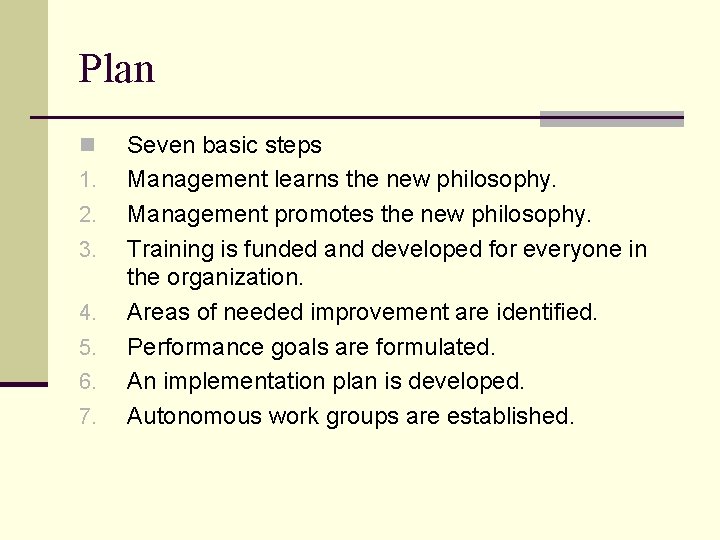
Plan n 1. 2. 3. 4. 5. 6. 7. Seven basic steps Management learns the new philosophy. Management promotes the new philosophy. Training is funded and developed for everyone in the organization. Areas of needed improvement are identified. Performance goals are formulated. An implementation plan is developed. Autonomous work groups are established.
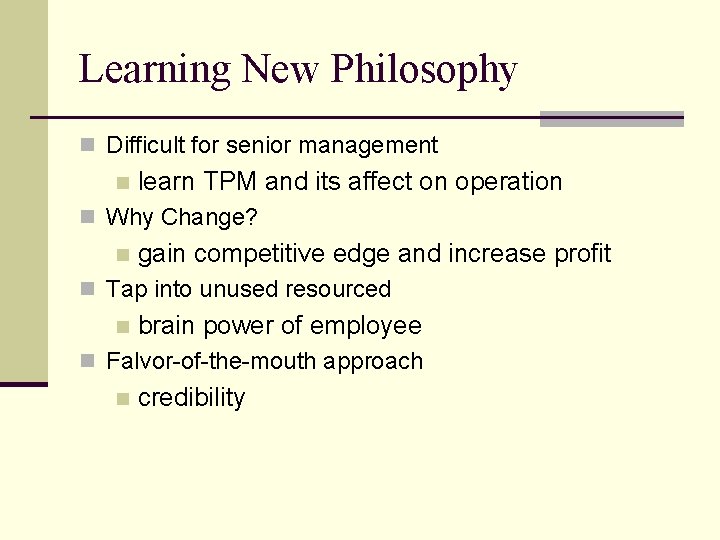
Learning New Philosophy n Difficult for senior management n learn TPM and its affect on operation n Why Change? n gain competitive edge and increase profit n Tap into unused resourced n brain power of employee n Falvor-of-the-mouth approach n credibility
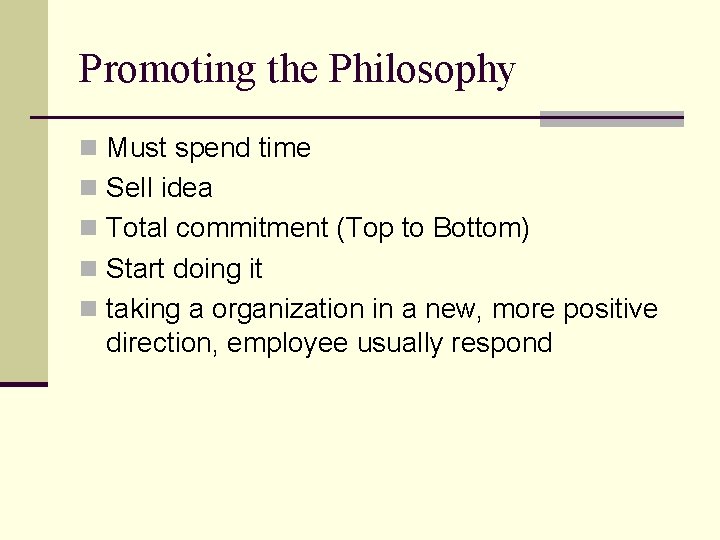
Promoting the Philosophy n Must spend time n Sell idea n Total commitment (Top to Bottom) n Start doing it n taking a organization in a new, more positive direction, employee usually respond
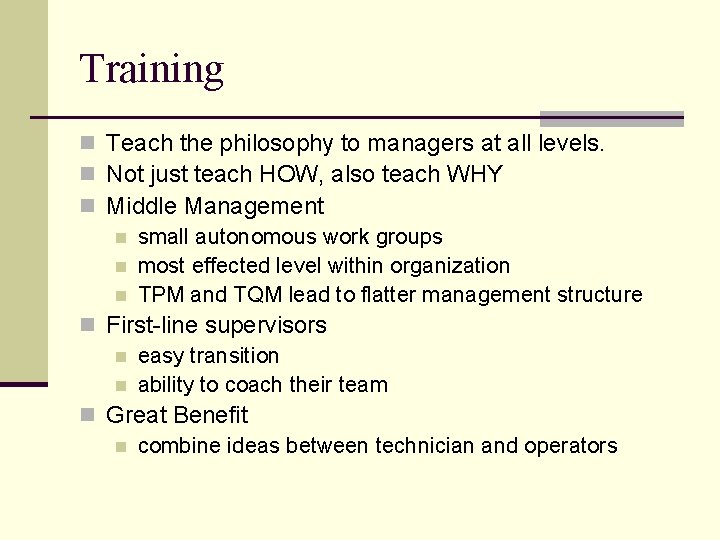
Training n Teach the philosophy to managers at all levels. n Not just teach HOW, also teach WHY n Middle Management n small autonomous work groups n most effected level within organization n TPM and TQM lead to flatter management structure n First-line supervisors n easy transition n ability to coach their team n Great Benefit n combine ideas between technician and operators
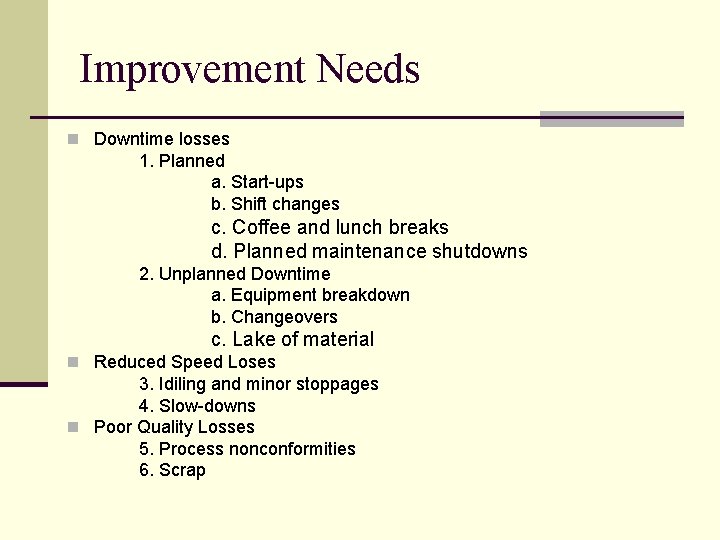
Improvement Needs n Downtime losses 1. Planned a. Start-ups b. Shift changes c. Coffee and lunch breaks d. Planned maintenance shutdowns 2. Unplanned Downtime a. Equipment breakdown b. Changeovers c. Lake of material n Reduced Speed Loses 3. Idiling and minor stoppages 4. Slow-downs n Poor Quality Losses 5. Process nonconformities 6. Scrap
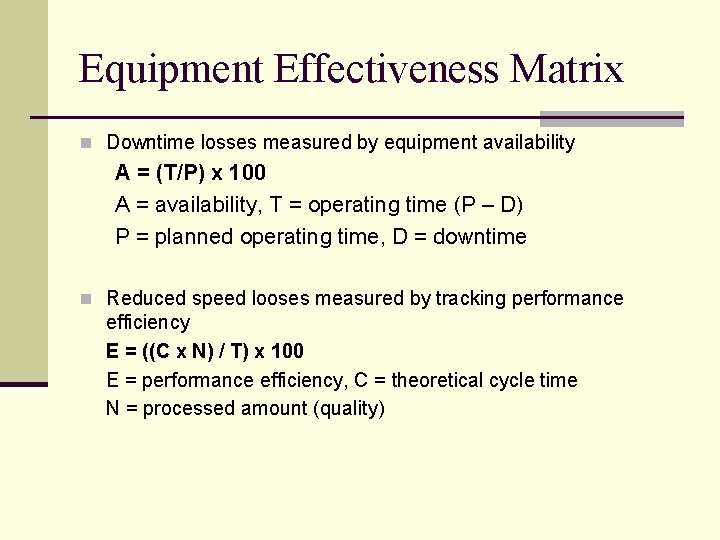
Equipment Effectiveness Matrix n Downtime losses measured by equipment availability A = (T/P) x 100 A = availability, T = operating time (P – D) P = planned operating time, D = downtime n Reduced speed looses measured by tracking performance efficiency E = ((C x N) / T) x 100 E = performance efficiency, C = theoretical cycle time N = processed amount (quality)
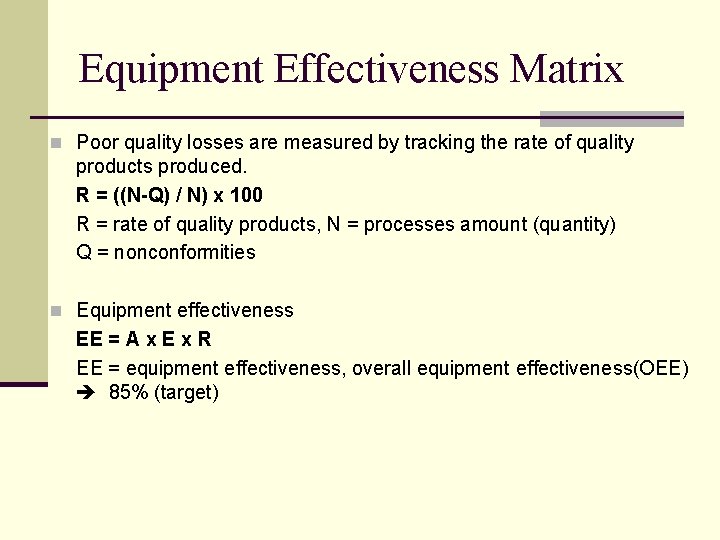
Equipment Effectiveness Matrix n Poor quality losses are measured by tracking the rate of quality products produced. R = ((N-Q) / N) x 100 R = rate of quality products, N = processes amount (quantity) Q = nonconformities n Equipment effectiveness EE = A x E x R EE = equipment effectiveness, overall equipment effectiveness(OEE) 85% (target)
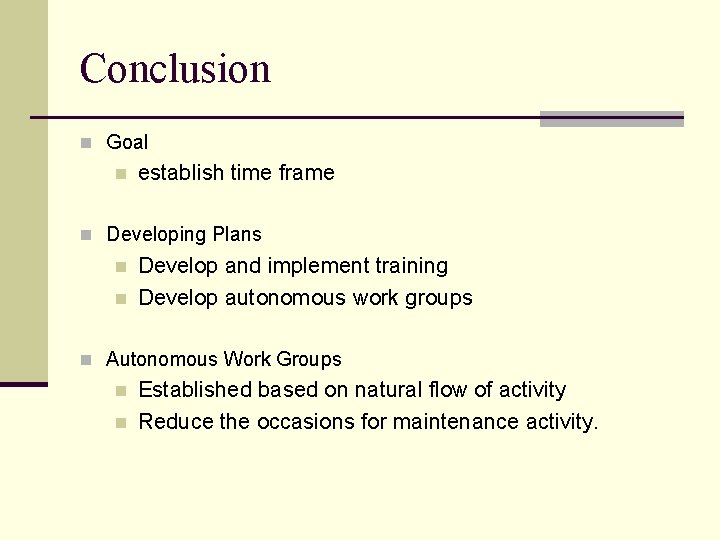
Conclusion n Goal n establish time frame n Developing Plans n n Develop and implement training Develop autonomous work groups n Autonomous Work Groups n n Established based on natural flow of activity Reduce the occasions for maintenance activity.