Topic 4 System Component Analysis Four basic functions
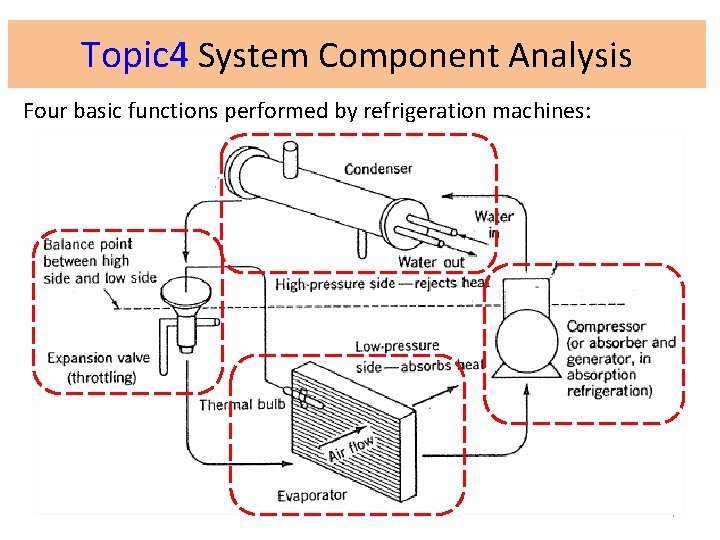
Topic 4 System Component Analysis Four basic functions performed by refrigeration machines: 1
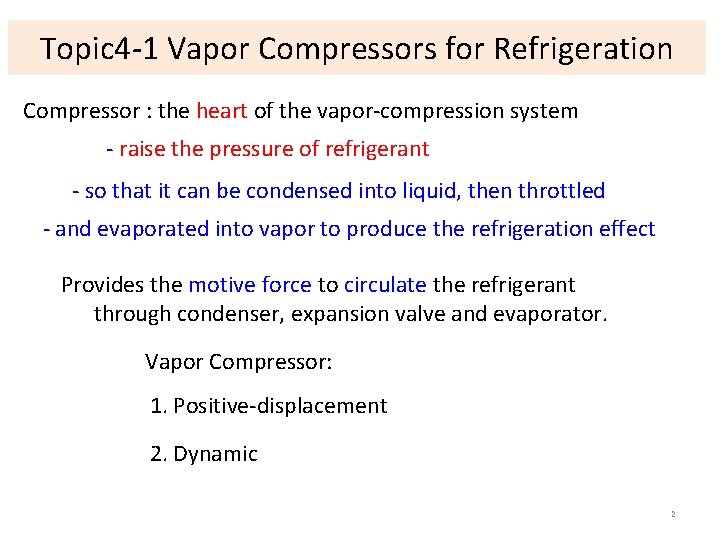
Topic 4 -1 Vapor Compressors for Refrigeration Compressor : the heart of the vapor-compression system - raise the pressure of refrigerant - so that it can be condensed into liquid, then throttled - and evaporated into vapor to produce the refrigeration effect Provides the motive force to circulate the refrigerant through condenser, expansion valve and evaporator. Vapor Compressor: 1. Positive-displacement 2. Dynamic 2
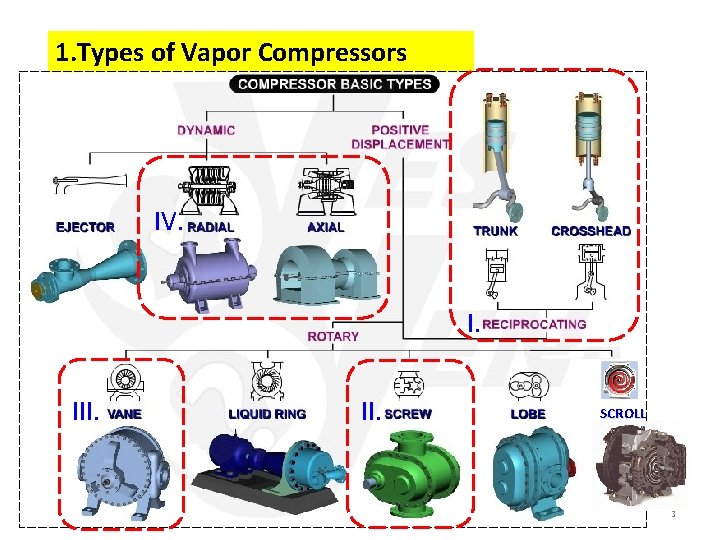
1. Types of Vapor Compressors IV. I. III. SCROLL 3
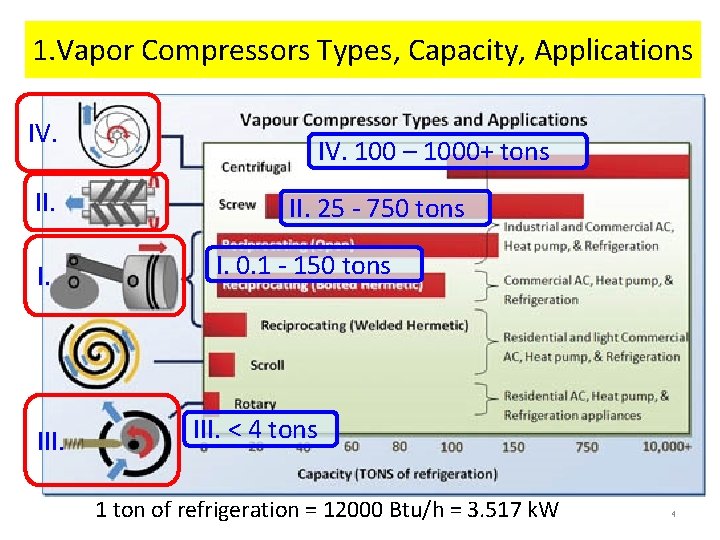
1. Vapor Compressors Types, Capacity, Applications IV. II. I. III. IV. 100 – 1000+ tons II. 25 - 750 tons I. 0. 1 - 150 tons III. < 4 tons 1 ton of refrigeration = 12000 Btu/h = 3. 517 k. W 4
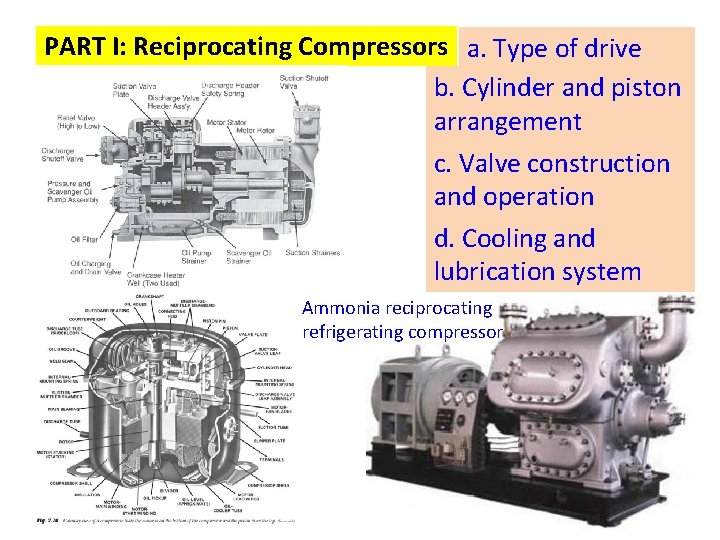
PART I: Reciprocating Compressors a. Type of drive b. Cylinder and piston arrangement c. Valve construction and operation d. Cooling and lubrication system Ammonia reciprocating refrigerating compressor 5
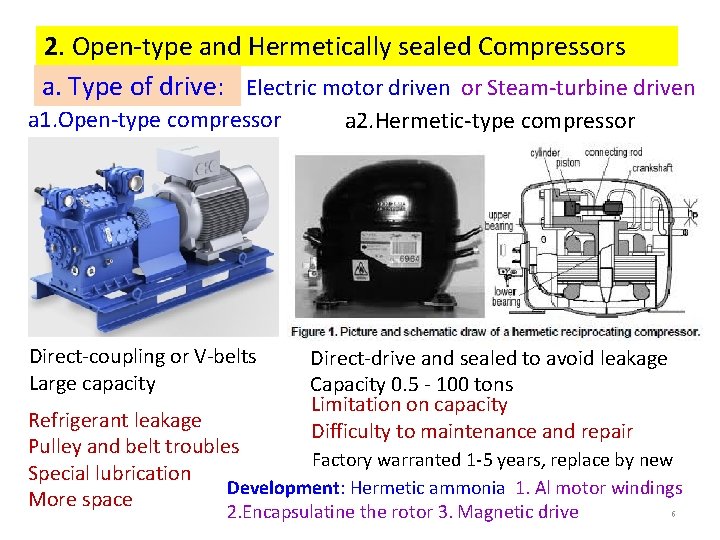
2. Open-type and Hermetically sealed Compressors a. Type of drive: Electric motor driven or Steam-turbine driven a 1. Open-type compressor Direct-coupling or V-belts Large capacity a 2. Hermetic-type compressor Direct-drive and sealed to avoid leakage Capacity 0. 5 - 100 tons Limitation on capacity Difficulty to maintenance and repair Refrigerant leakage Pulley and belt troubles Factory warranted 1 -5 years, replace by new Special lubrication Development: Hermetic ammonia 1. Al motor windings More space 6 2. Encapsulatine the rotor 3. Magnetic drive
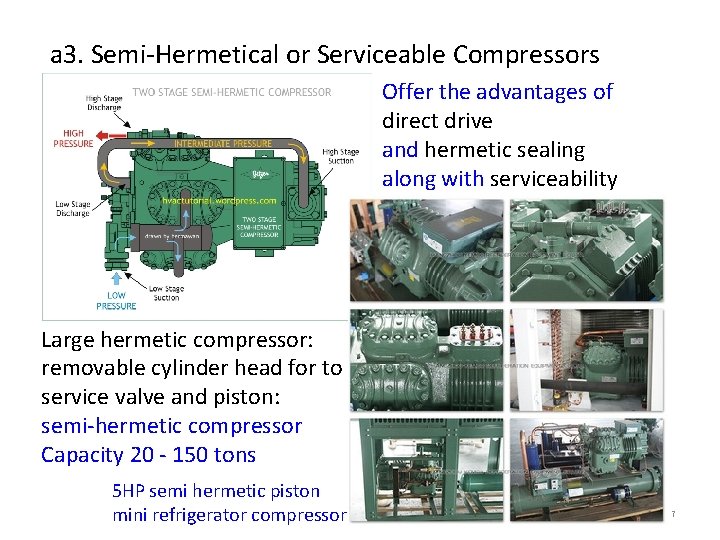
a 3. Semi-Hermetical or Serviceable Compressors Offer the advantages of direct drive and hermetic sealing along with serviceability Large hermetic compressor: removable cylinder head for to service valve and piston: semi-hermetic compressor Capacity 20 - 150 tons 5 HP semi hermetic piston mini refrigerator compressor 7
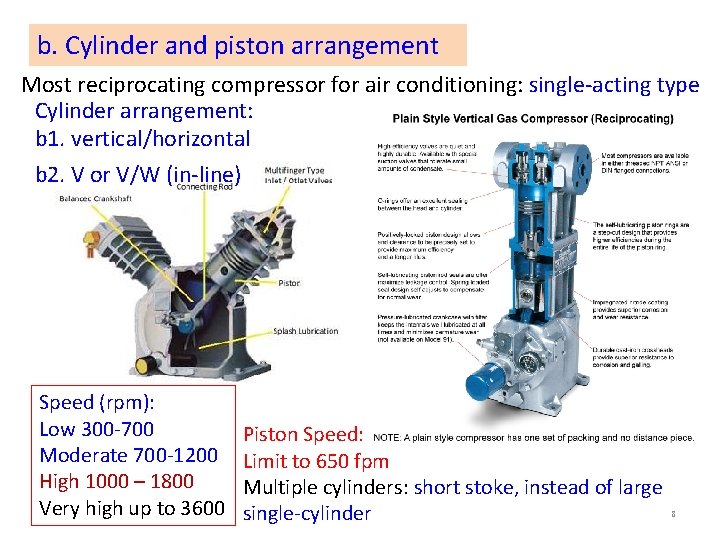
b. Cylinder and piston arrangement Most reciprocating compressor for air conditioning: single-acting type Cylinder arrangement: b 1. vertical/horizontal b 2. V or V/W (in-line) Speed (rpm): Low 300 -700 Moderate 700 -1200 High 1000 – 1800 Very high up to 3600 Piston Speed: Limit to 650 fpm Multiple cylinders: short stoke, instead of large single-cylinder 8
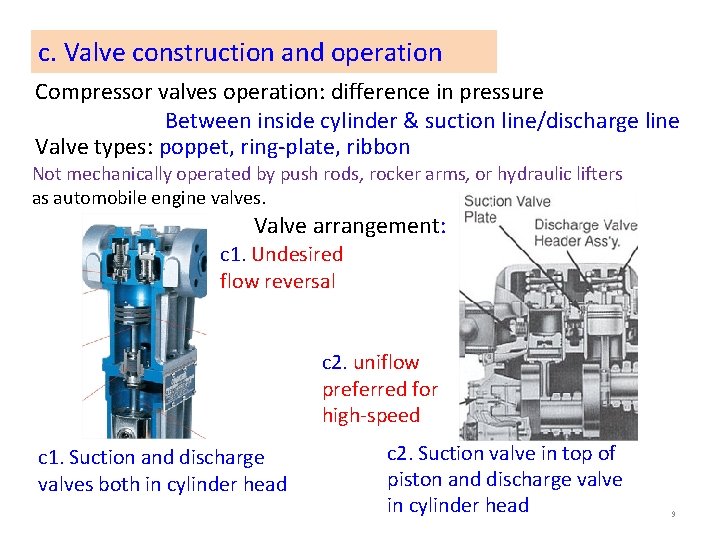
c. Valve construction and operation Compressor valves operation: difference in pressure Between inside cylinder & suction line/discharge line Valve types: poppet, ring-plate, ribbon Not mechanically operated by push rods, rocker arms, or hydraulic lifters as automobile engine valves. Valve arrangement: c 1. Undesired flow reversal c 2. uniflow preferred for high-speed c 1. Suction and discharge valves both in cylinder head c 2. Suction valve in top of piston and discharge valve in cylinder head 9
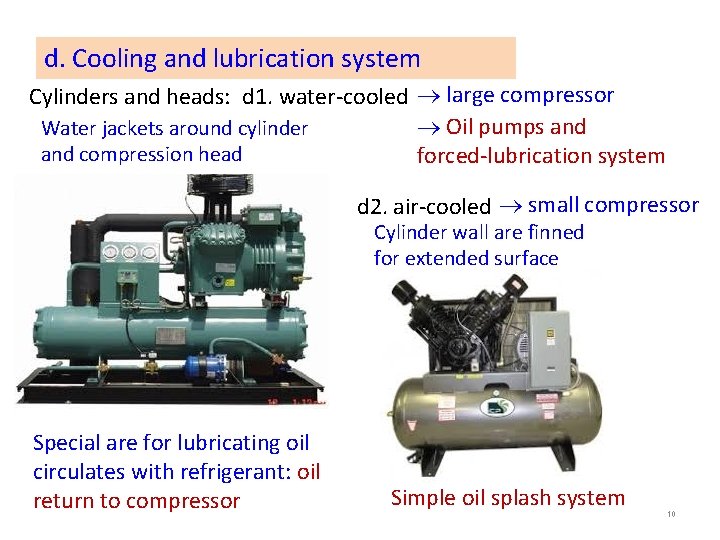
d. Cooling and lubrication system Cylinders and heads: d 1. water-cooled large compressor Oil pumps and Water jackets around cylinder and compression head forced-lubrication system d 2. air-cooled small compressor Cylinder wall are finned for extended surface Special are for lubricating oil circulates with refrigerant: oil return to compressor Simple oil splash system 10
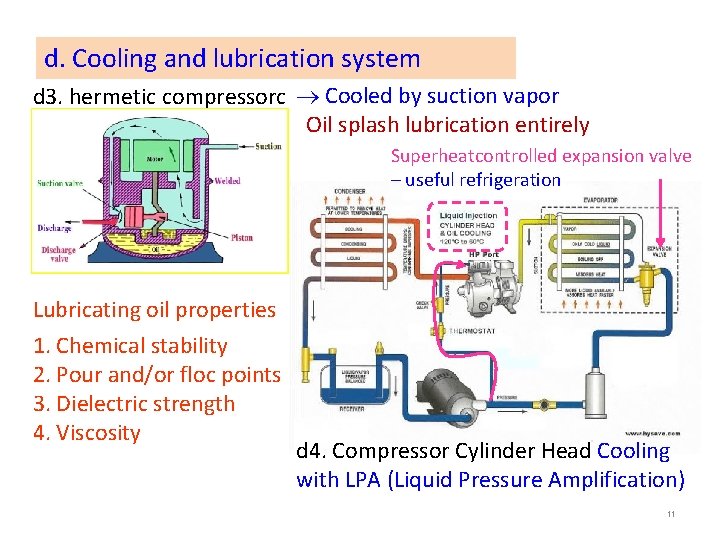
d. Cooling and lubrication system d 3. hermetic compressorc Cooled by suction vapor Oil splash lubrication entirely Superheatcontrolled expansion valve – useful refrigeration Lubricating oil properties 1. Chemical stability 2. Pour and/or floc points 3. Dielectric strength 4. Viscosity d 4. Compressor Cylinder Head Cooling with LPA (Liquid Pressure Amplification) 11
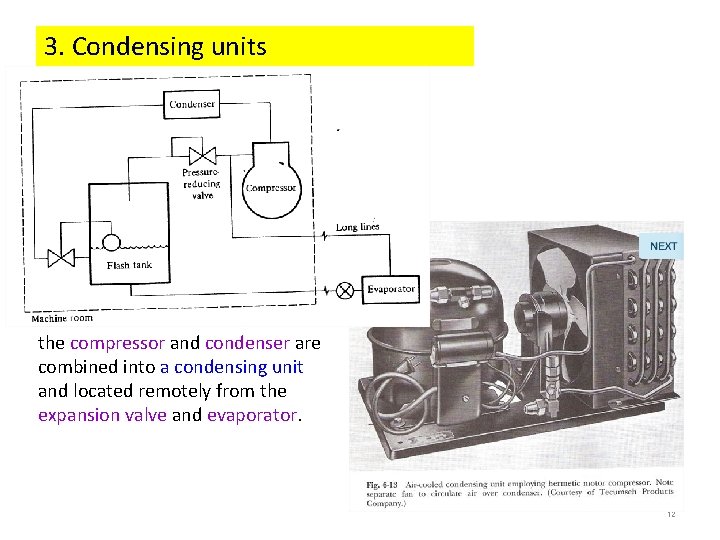
3. Condensing units the compressor and condenser are combined into a condensing unit and located remotely from the expansion valve and evaporator. 12
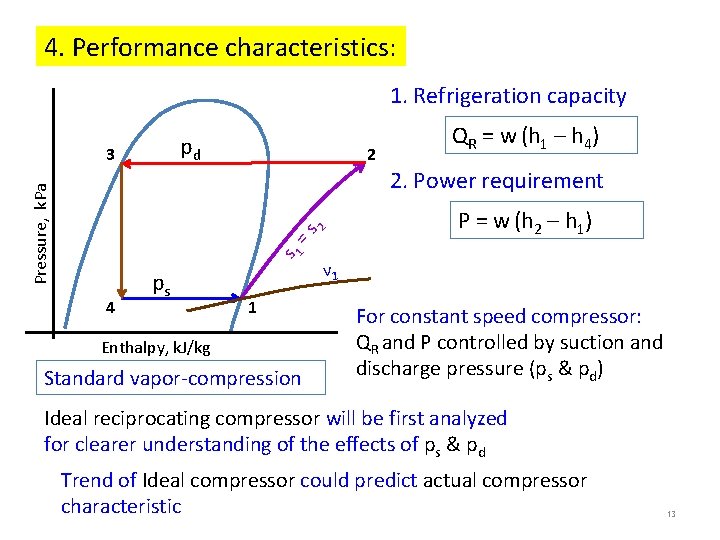
4. Performance characteristics: 1. Refrigeration capacity pd 3 2 QR = w (h 1 – h 4) s 1 =s 2 Pressure, k. Pa 2. Power requirement 4 ps 1 Enthalpy, k. J/kg Standard vapor-compression P = w (h 2 – h 1) v 1 For constant speed compressor: QR and P controlled by suction and discharge pressure (ps & pd) Ideal reciprocating compressor will be first analyzed for clearer understanding of the effects of ps & pd Trend of Ideal compressor could predict actual compressor characteristic 13
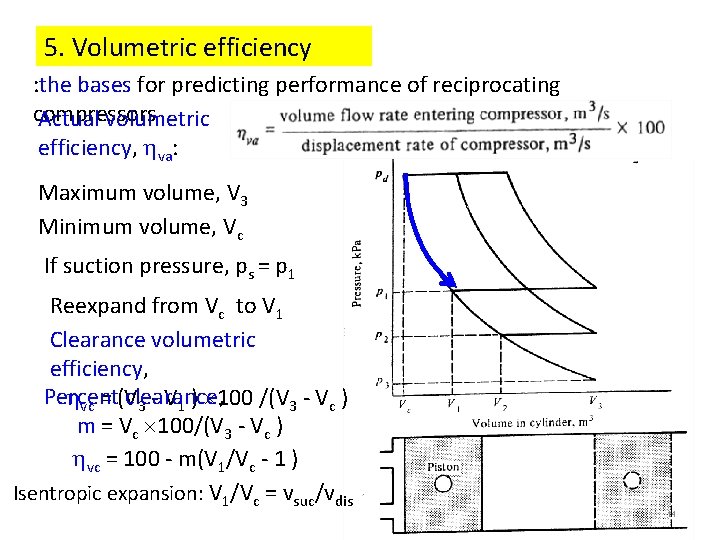
5. Volumetric efficiency : the bases for predicting performance of reciprocating compressors Actual volumetric efficiency, va: Maximum volume, V 3 Minimum volume, Vc If suction pressure, ps = p 1 Reexpand from Vc to V 1 Clearance volumetric efficiency, Percent clearance, vc = (V 3 - V 1 ) 100 /(V 3 - Vc ) m = Vc 100/(V 3 - Vc ) vc = 100 - m(V 1/Vc - 1 ) Isentropic expansion: V 1/Vc = vsuc/vdis 14
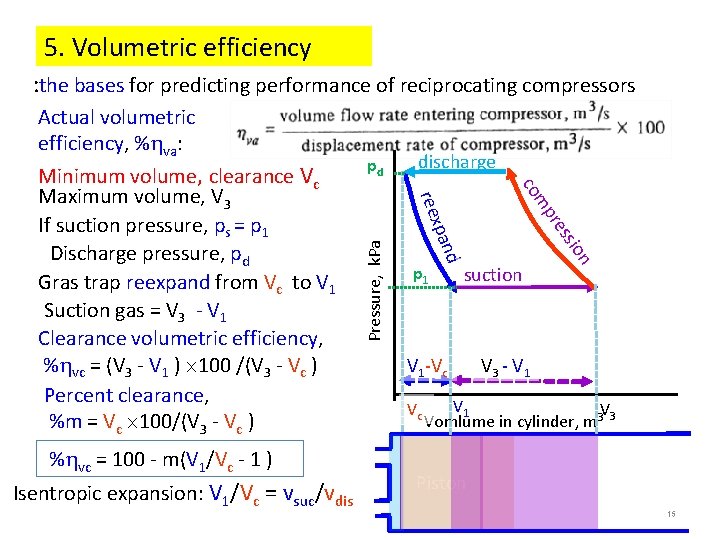
5. Volumetric efficiency : the bases for predicting performance of reciprocating compressors co Pressure, k. Pa suction V 1 -Vc Vc n sio es r mp p 1 nd Isentropic expansion: V 1/Vc = vsuc/vdis discharge xpa % vc = 100 - m(V 1/Vc - 1 ) pd ree Actual volumetric efficiency, % va: Minimum volume, clearance Vc Maximum volume, V 3 If suction pressure, ps = p 1 Discharge pressure, pd Gras trap reexpand from Vc to V 1 Suction gas = V 3 - V 1 Clearance volumetric efficiency, % vc = (V 3 - V 1 ) 100 /(V 3 - Vc ) Percent clearance, %m = Vc 100/(V 3 - Vc ) V 3 - V 1 V Vomlume in cylinder, m 3 3 Piston 15
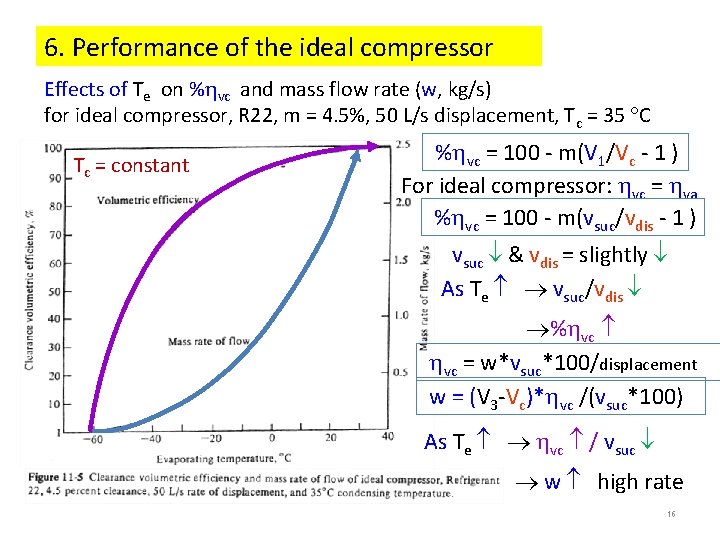
6. Performance of the ideal compressor Effects of Te on % vc and mass flow rate (w, kg/s) for ideal compressor, R 22, m = 4. 5%, 50 L/s displacement, Tc = 35 C Tc = constant % vc = 100 - m(V 1/Vc - 1 ) For ideal compressor: vc = va % vc = 100 - m(vsuc/vdis - 1 ) vsuc & vdis = slightly As Te vsuc/vdis % vc = w*vsuc*100/displacement w = (V 3 -Vc)* vc /(vsuc*100) As Te vc / vsuc w high rate 16
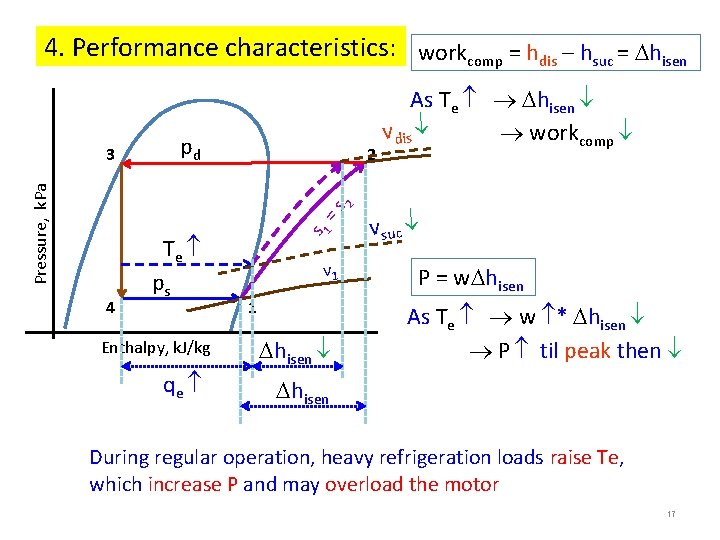
4. Performance characteristics: workcomp = hdis – hsuc = hisen pd 2 4 Te ps Enthalpy, k. J/kg qe s 1 =s 2 Pressure, k. Pa 3 v 1 1 hisen As Te hisen vdis workcomp vsuc P = w hisen As Te w * hisen P til peak then hisen During regular operation, heavy refrigeration loads raise Te, which increase P and may overload the motor 17
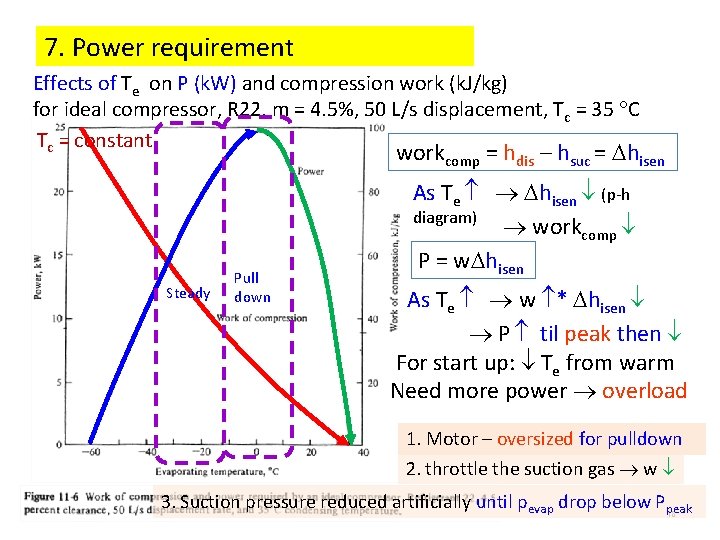
7. Power requirement Effects of Te on P (k. W) and compression work (k. J/kg) for ideal compressor, R 22, m = 4. 5%, 50 L/s displacement, Tc = 35 C Tc = constant workcomp = hdis – hsuc = hisen Steady Pull down As Te hisen (p-h diagram) workcomp P = w hisen As Te w * hisen P til peak then For start up: Te from warm Need more power overload 1. Motor – oversized for pulldown 2. throttle the suction gas w 3. Suction pressure reduced artificially until pevap drop below Ppeak 18

8. Refrigeration capacity Effects of Te on Qe (k. W) and refrigerating effect qe (k. J/kg) for ideal compressor, R 22, m = 4. 5%, 50 L/s displacement, Tc = 35 C Tc = constant qe = hsuc – hthrottling = h 1 – h 4 As Te (h 1 – h 4) (p-h diagram) qe Qe = w* (h 1 – h 4) As Te w * (h 1 – h 4) Qe high rate as Ten Qe – can be double from 0 to 20 C 19
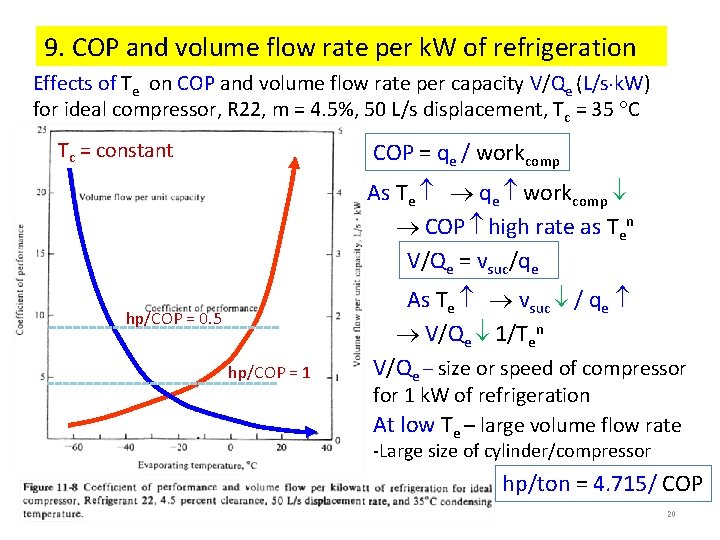
9. COP and volume flow rate per k. W of refrigeration Effects of Te on COP and volume flow rate per capacity V/Qe (L/s k. W) for ideal compressor, R 22, m = 4. 5%, 50 L/s displacement, Tc = 35 C Tc = constant COP = qe / workcomp As Te qe workcomp COP high rate as Ten V/Qe = vsuc/qe hp/COP = 0. 5 hp/COP = 1 As Te vsuc / qe V/Qe 1/Ten V/Qe – size or speed of compressor for 1 k. W of refrigeration At low Te – large volume flow rate -Large size of cylinder/compressor hp/ton = 4. 715/ COP 20
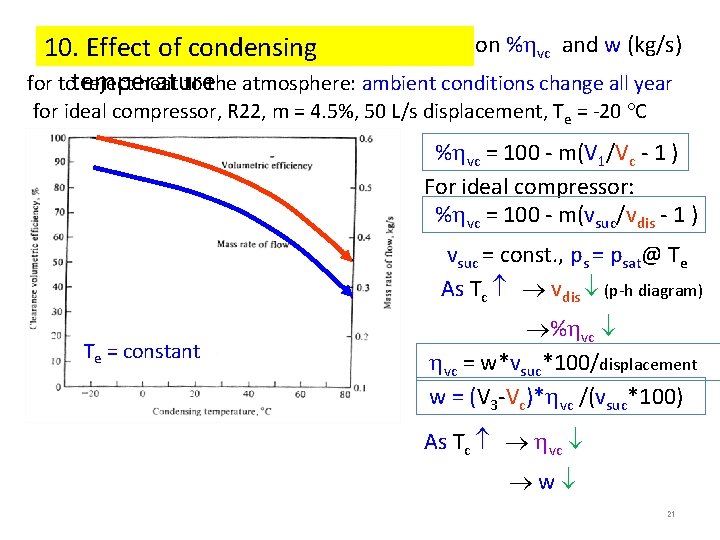
on % vc and w (kg/s) 10. Effect of condensing for totemperature reject heat to the atmosphere: ambient conditions change all year for ideal compressor, R 22, m = 4. 5%, 50 L/s displacement, Te = -20 C % vc = 100 - m(V 1/Vc - 1 ) For ideal compressor: % vc = 100 - m(vsuc/vdis - 1 ) vsuc = const. , ps = psat@ Te As Tc vdis (p-h diagram) Te = constant % vc = w*vsuc*100/displacement w = (V 3 -Vc)* vc /(vsuc*100) As Tc vc w 21
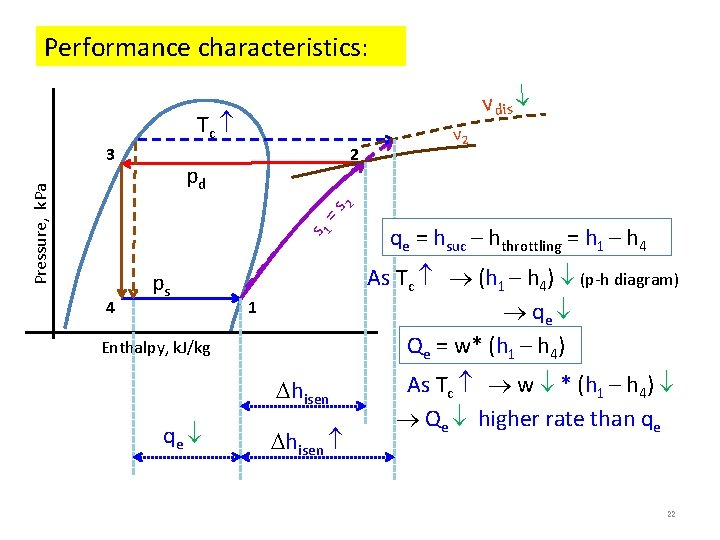
Performance characteristics: vdis Tc 2 pd s 1 =s 2 Pressure, k. Pa 3 v 2 4 ps As Tc (h 1 – h 4) (p-h diagram) qe Qe = w* (h 1 – h 4) 1 Enthalpy, k. J/kg hisen qe = hsuc – hthrottling = h 1 – h 4 hisen As Tc w * (h 1 – h 4) Qe higher rate than qe 22
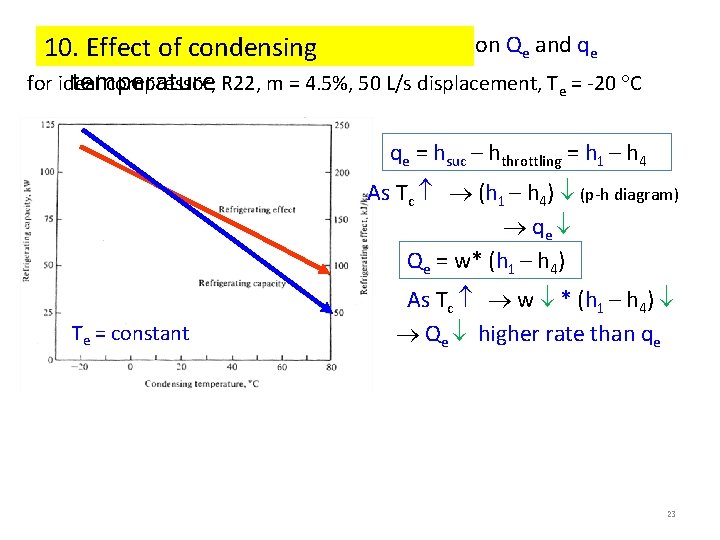
on Qe and qe 10. Effect of condensing temperature for ideal compressor, R 22, m = 4. 5%, 50 L/s displacement, Te = -20 C qe = hsuc – hthrottling = h 1 – h 4 As Tc (h 1 – h 4) (p-h diagram) qe Qe = w* (h 1 – h 4) Te = constant As Tc w * (h 1 – h 4) Qe higher rate than qe 23
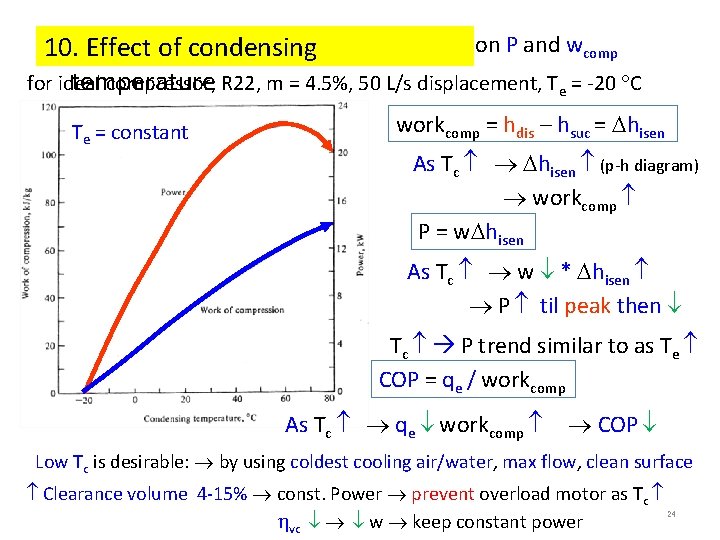
on P and wcomp 10. Effect of condensing temperature for ideal compressor, R 22, m = 4. 5%, 50 L/s displacement, Te = -20 C Te = constant workcomp = hdis – hsuc = hisen As Tc hisen (p-h diagram) workcomp P = w hisen As Tc w * hisen P til peak then Tc P trend similar to as Te COP = qe / workcomp As Tc qe workcomp COP Low Tc is desirable: by using coldest cooling air/water, max flow, clean surface Clearance volume 4 -15% const. Power prevent overload motor as Tc 24 vc w keep constant power
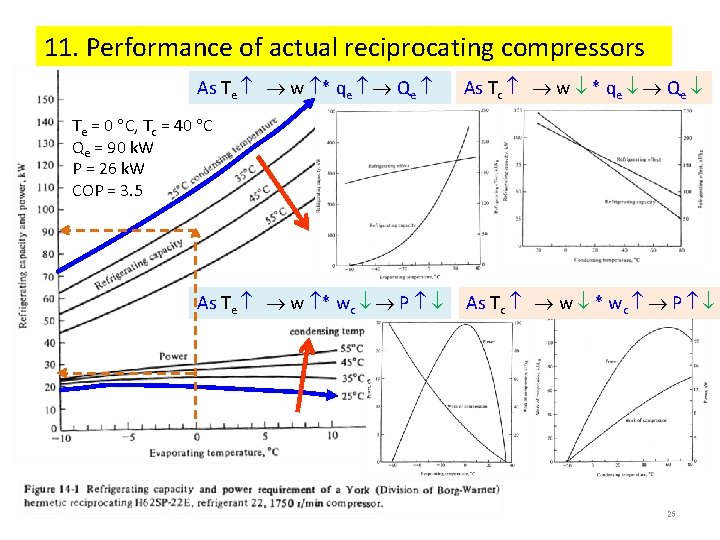
11. Performance of actual reciprocating compressors As Te w * qe Qe As Tc w * qe Qe Te = 0 C, Tc = 40 C Qe = 90 k. W P = 26 k. W COP = 3. 5 As Te w * wc P As Tc w * wc P 25
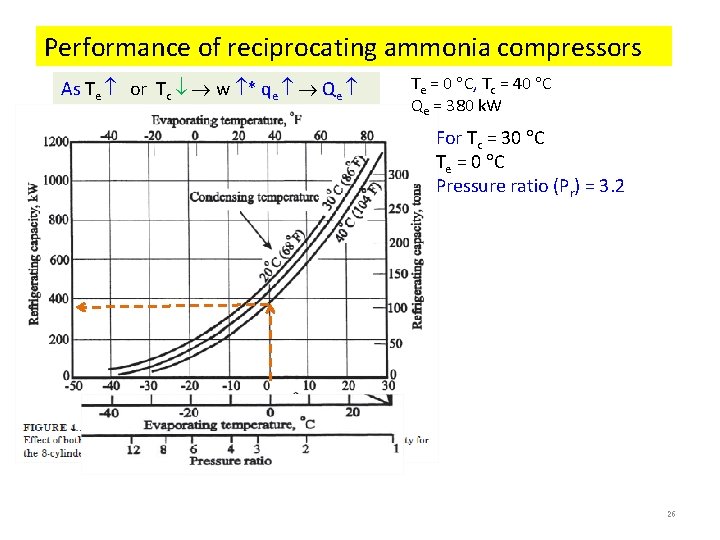
Performance of reciprocating ammonia compressors As Te or Tc w * qe Qe Te = 0 C, Tc = 40 C Qe = 380 k. W For Tc = 30 C Te = 0 C Pressure ratio (Pr) = 3. 2 26
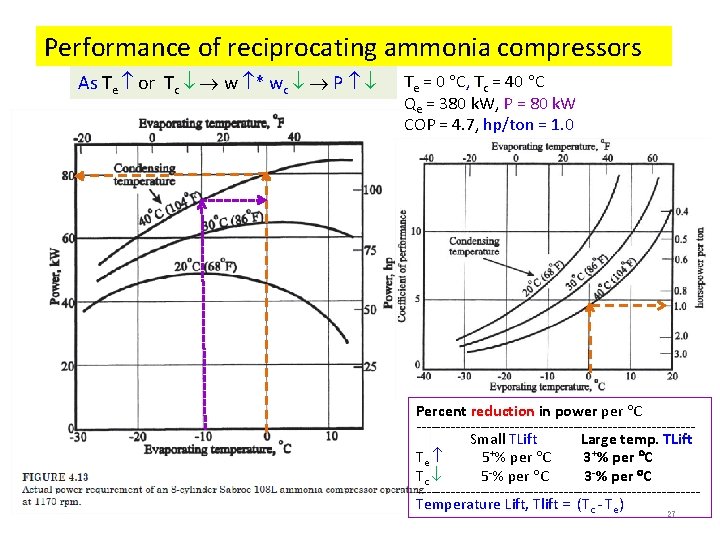
Performance of reciprocating ammonia compressors As Te or Tc w * wc P Te = 0 C, Tc = 40 C Qe = 380 k. W, P = 80 k. W COP = 4. 7, hp/ton = 1. 0 Percent reduction in power per C ----------------------------Small TLift Large temp. TLift + Te 5 % per C 3+% per C Tc 5 -% per C 3 -% per C -----------------------------Temperature Lift, Tlift = (Tc - Te) 27
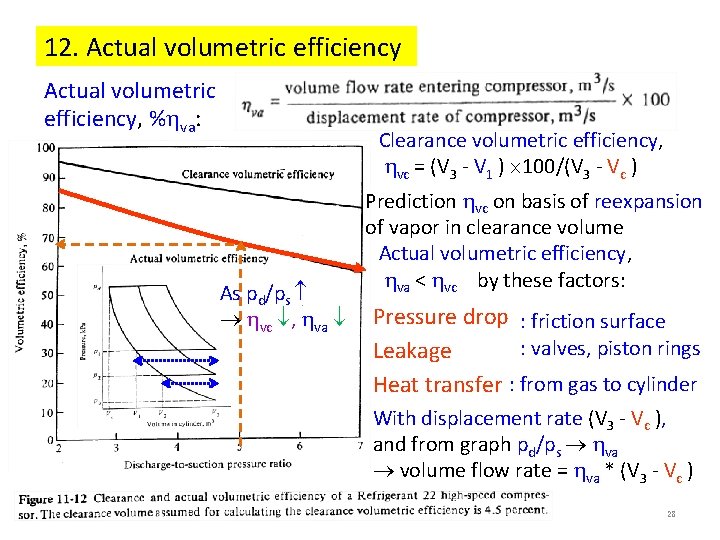
12. Actual volumetric efficiency, % va: Clearance volumetric efficiency, vc = (V 3 - V 1 ) 100/(V 3 - Vc ) As pd/ps vc , va Prediction vc on basis of reexpansion of vapor in clearance volume Actual volumetric efficiency, va < vc by these factors: Pressure drop : friction surface : valves, piston rings Leakage Heat transfer : from gas to cylinder With displacement rate (V 3 - Vc ), and from graph pd/ps va volume flow rate = va * (V 3 - Vc ) 28
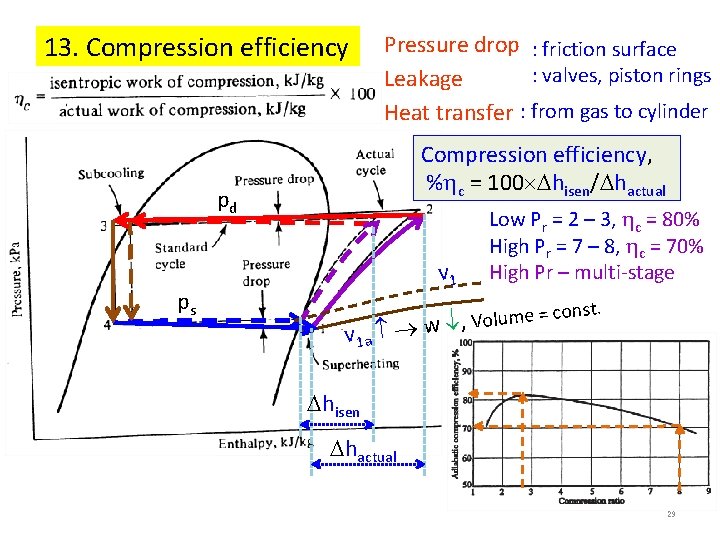
13. Compression efficiency Pressure drop : friction surface : valves, piston rings Leakage Heat transfer : from gas to cylinder Compression efficiency, % c = 100 hisen/ hactual pd ps v 1 a Low Pr = 2 – 3, c = 80% High Pr = 7 – 8, c = 70% High Pr – multi-stage t. ns o c = e m u l o w , V hisen hactual 29
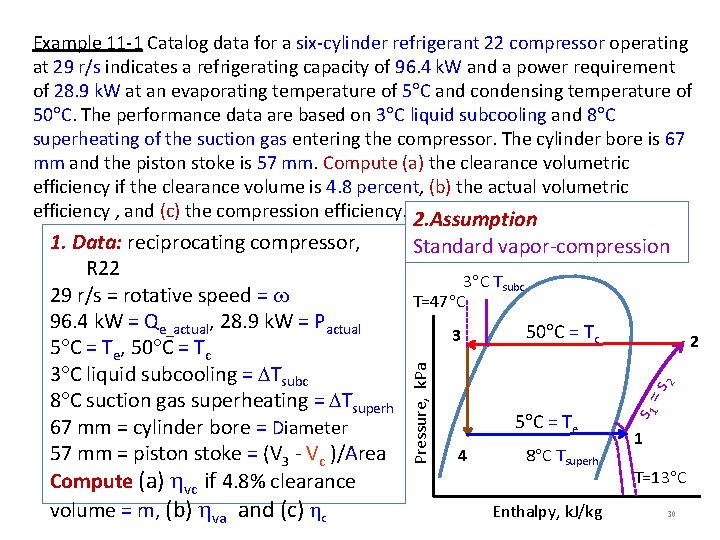
Example 11 -1 Catalog data for a six-cylinder refrigerant 22 compressor operating at 29 r/s indicates a refrigerating capacity of 96. 4 k. W and a power requirement of 28. 9 k. W at an evaporating temperature of 5 C and condensing temperature of 50 C. The performance data are based on 3 C liquid subcooling and 8 C superheating of the suction gas entering the compressor. The cylinder bore is 67 mm and the piston stoke is 57 mm. Compute (a) the clearance volumetric efficiency if the clearance volume is 4. 8 percent, (b) the actual volumetric efficiency , and (c) the compression efficiency. 2. Assumption s 1 = s 2 Pressure, k. Pa 1. Data: reciprocating compressor, Standard vapor-compression R 22 3 C Tsubc 29 r/s = rotative speed = T=47 C 96. 4 k. W = Qe_actual, 28. 9 k. W = Pactual 50 C = Tc 3 2 5 C = Te, 50 C = Tc 3 C liquid subcooling = Tsubc 8 C suction gas superheating = Tsuperh 5 C = Te 67 mm = cylinder bore = Diameter 1 57 mm = piston stoke = (V 3 - Vc )/Area 4 8 C Tsuperh T=13 C Compute (a) vc if 4. 8% clearance 30 volume = m, (b) va and (c) c Enthalpy, k. J/kg
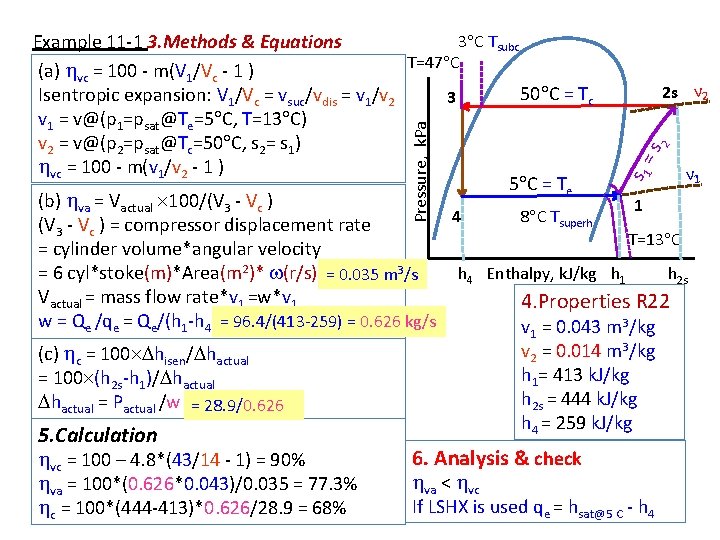
5. Calculation vc = 100 – 4. 8*(43/14 - 1) = 90% va = 100*(0. 626*0. 043)/0. 035 = 77. 3% c = 100*(444 -413)*0. 626/28. 9 = 68% s 1 = s 2 Pressure, k. Pa 3 C Tsubc Example 11 -1 3. Methods & Equations T=47 C (a) vc = 100 - m(V 1/Vc - 1 ) 2 s v 2 50 C = Tc Isentropic expansion: V 1/Vc = vsuc/vdis = v 1/v 2 3 v 1 = v@(p 1=psat@Te=5 C, T=13 C) v 2 = v@(p 2=psat@Tc=50 C, s 2= s 1) vc = 100 - m(v 1/v 2 - 1 ) v 1 5 C = Te (b) va = Vactual 100/(V 3 - Vc ) 1 4 8 C T superh (V 3 - Vc ) = compressor displacement rate T=13 C = cylinder volume*angular velocity h 4 Enthalpy, k. J/kg h 1 h 2 s = 6 cyl*stoke(m)*Area(m 2)* (r/s) = 0. 035 m 3/s Vactual = mass flow rate*v 1 =w*v 1 4. Properties R 22 w = Qe /qe = Qe/(h 1 -h 4) = 96. 4/(413 -259) = 0. 626 kg/s v 1 = 0. 043 m 3/kg v 2 = 0. 014 m 3/kg (c) c = 100 hisen/ hactual h 1= 413 k. J/kg = 100 (h 2 s-h 1)/ hactual h 2 s = 444 k. J/kg hactual = Pactual /w = 28. 9/0. 626 h 4 = 259 k. J/kg 6. Analysis & check va < vc If LSHX is used qe = hsat@5 C - h 4 31
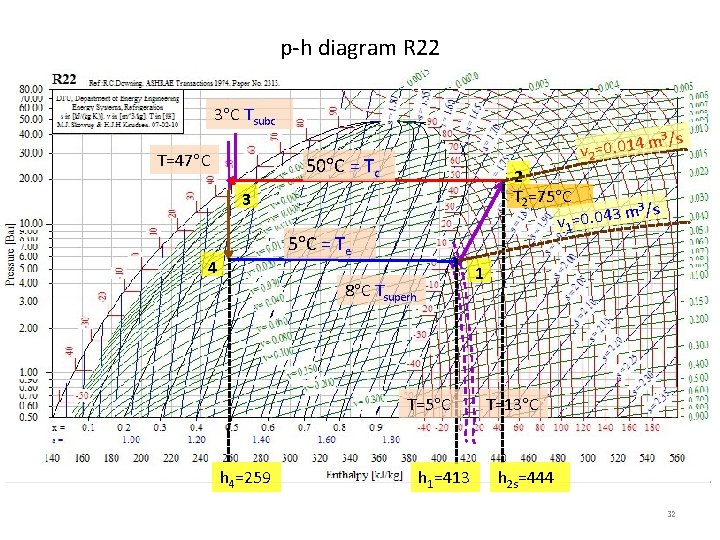
p-h diagram R 22 3 C Tsubc T=47 C m 3 /s 4 1 0. 0 = v 2 50 C = Tc 2 T 2=75 C 3 /s m 3 4 0. v 1=0 3 5 C = Te 4 1 8 C Tsuperh T=5 C h 4=259 h 1=413 T=13 C h 2 s=444 32
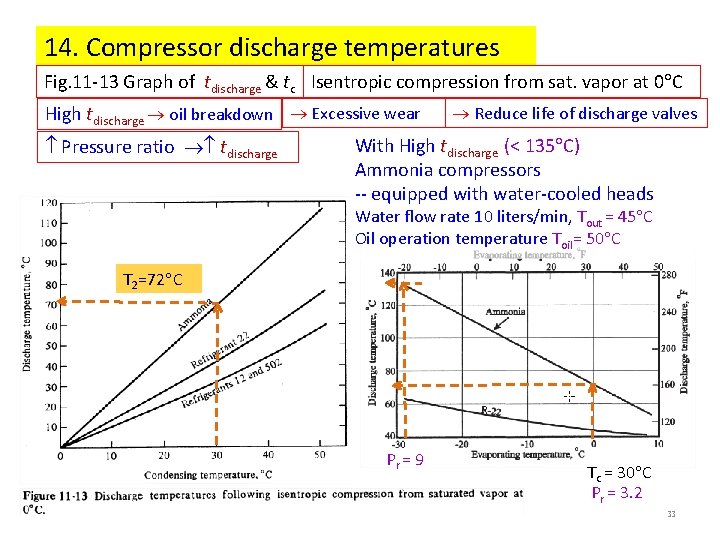
14. Compressor discharge temperatures Fig. 11 -13 Graph of tdischarge & tc Isentropic compression from sat. vapor at 0 C High tdischarge oil breakdown Excessive wear Pressure ratio tdischarge Reduce life of discharge valves With High tdischarge (< 135 C) Ammonia compressors -- equipped with water-cooled heads Water flow rate 10 liters/min, Tout = 45 C Oil operation temperature Toil= 50 C T 2=72 C Pr = 9 Tc = 30 C Pr = 3. 2 33
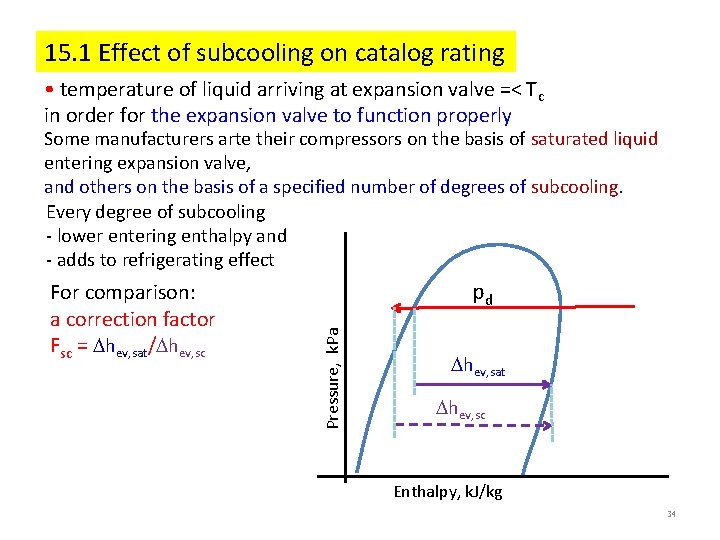
15. 1 Effect of subcooling on catalog rating • temperature of liquid arriving at expansion valve =< Tc in order for the expansion valve to function properly Some manufacturers arte their compressors on the basis of saturated liquid entering expansion valve, and others on the basis of a specified number of degrees of subcooling. Every degree of subcooling - lower entering enthalpy and - adds to refrigerating effect pd Pressure, k. Pa For comparison: a correction factor Fsc = hev, sat/ hev, sc hev, sat hev, sc Enthalpy, k. J/kg 34
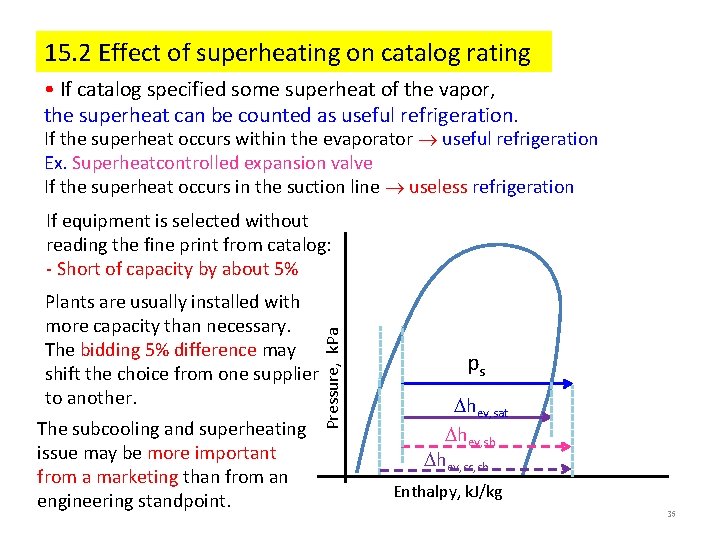
15. 2 Effect of superheating on catalog rating • If catalog specified some superheat of the vapor, the superheat can be counted as useful refrigeration. If the superheat occurs within the evaporator useful refrigeration Ex. Superheatcontrolled expansion valve If the superheat occurs in the suction line useless refrigeration Plants are usually installed with more capacity than necessary. The bidding 5% difference may shift the choice from one supplier to another. The subcooling and superheating issue may be more important from a marketing than from an engineering standpoint. Pressure, k. Pa If equipment is selected without reading the fine print from catalog: - Short of capacity by about 5% ps hev, sat hev, sh hev, sc, sh Enthalpy, k. J/kg 35
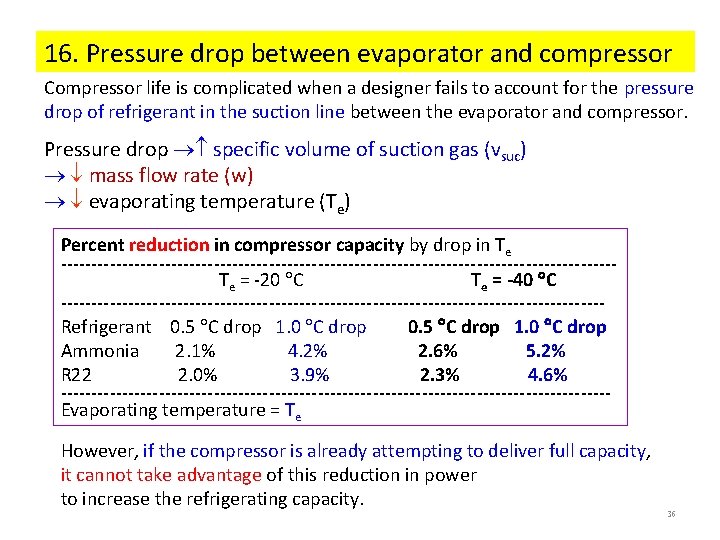
16. Pressure drop between evaporator and compressor Compressor life is complicated when a designer fails to account for the pressure drop of refrigerant in the suction line between the evaporator and compressor. Pressure drop specific volume of suction gas (vsuc) mass flow rate (w) evaporating temperature (Te) Percent reduction in compressor capacity by drop in Te ---------------------------------------------Te = -20 C Te = -40 C --------------------------------------------Refrigerant 0. 5 C drop 1. 0 C drop Ammonia 2. 1% 4. 2% 2. 6% 5. 2% R 22 2. 0% 3. 9% 2. 3% 4. 6% ---------------------------------------------Evaporating temperature = Te However, if the compressor is already attempting to deliver full capacity, it cannot take advantage of this reduction in power to increase the refrigerating capacity. 36
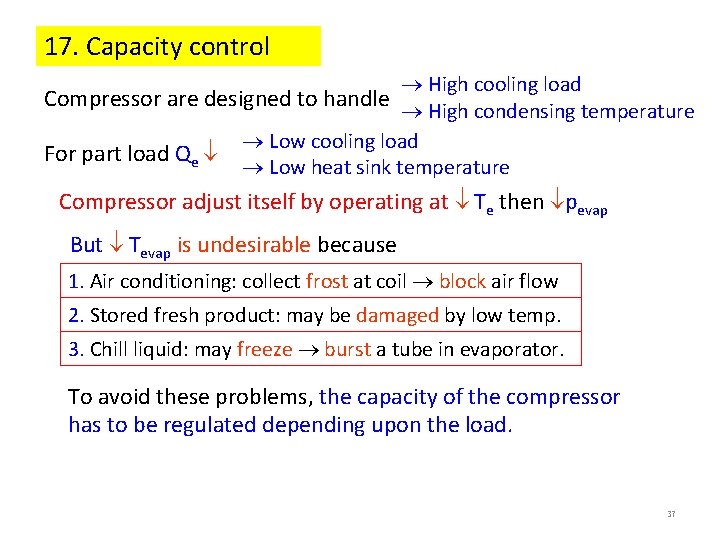
17. Capacity control High cooling load Compressor are designed to handle High condensing temperature Low cooling load For part load Qe Low heat sink temperature Compressor adjust itself by operating at Te then pevap But Tevap is undesirable because 1. Air conditioning: collect frost at coil block air flow 2. Stored fresh product: may be damaged by low temp. 3. Chill liquid: may freeze burst a tube in evaporator. To avoid these problems, the capacity of the compressor has to be regulated depending upon the load. 37
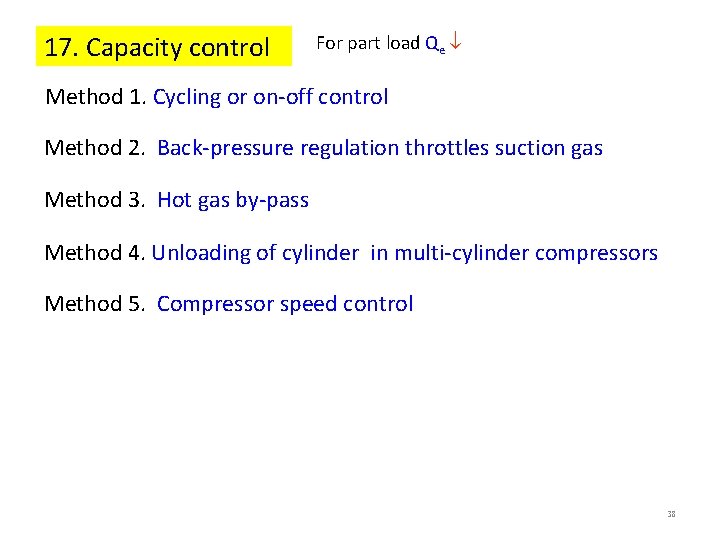
17. Capacity control For part load Qe Method 1. Cycling or on-off control Method 2. Back-pressure regulation throttles suction gas Method 3. Hot gas by-pass Method 4. Unloading of cylinder in multi-cylinder compressors Method 5. Compressor speed control 38
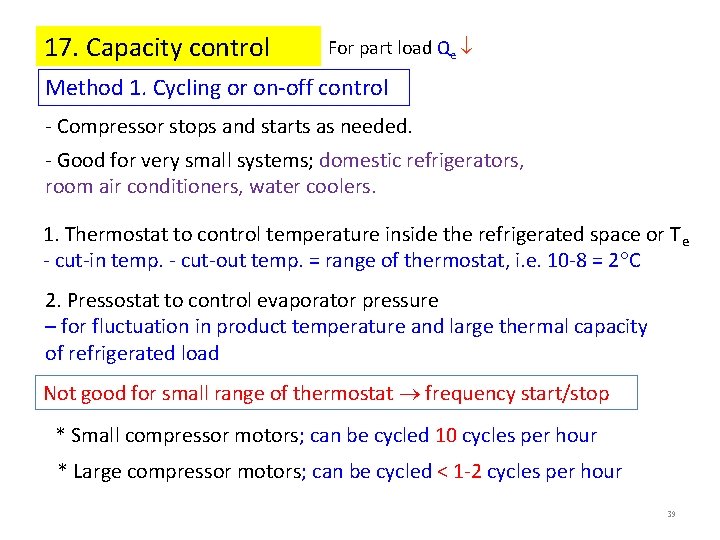
17. Capacity control For part load Qe Method 1. Cycling or on-off control - Compressor stops and starts as needed. - Good for very small systems; domestic refrigerators, room air conditioners, water coolers. 1. Thermostat to control temperature inside the refrigerated space or T e - cut-in temp. - cut-out temp. = range of thermostat, i. e. 10 -8 = 2 C 2. Pressostat to control evaporator pressure – for fluctuation in product temperature and large thermal capacity of refrigerated load Not good for small range of thermostat frequency start/stop * Small compressor motors; can be cycled 10 cycles per hour * Large compressor motors; can be cycled < 1 -2 cycles per hour 39
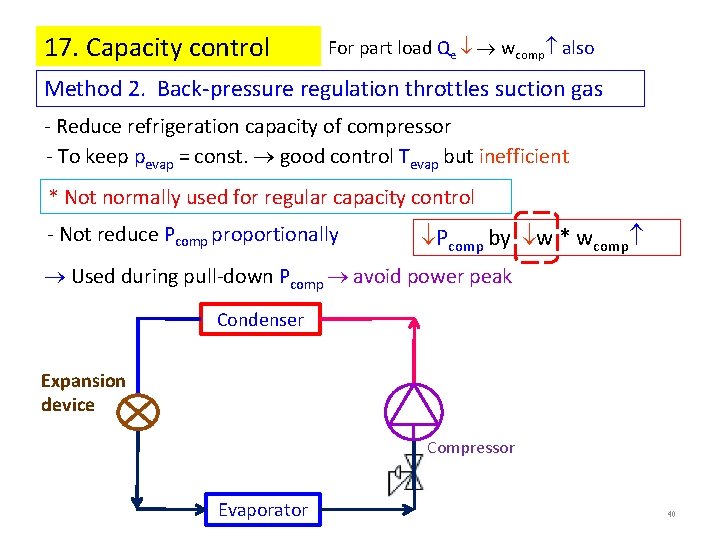
17. Capacity control For part load Qe wcomp also Method 2. Back-pressure regulation throttles suction gas - Reduce refrigeration capacity of compressor - To keep pevap = const. good control Tevap but inefficient * Not normally used for regular capacity control - Not reduce Pcomp proportionally Pcomp by w * wcomp Used during pull-down Pcomp avoid power peak Condenser Expansion device Compressor Evaporator 40
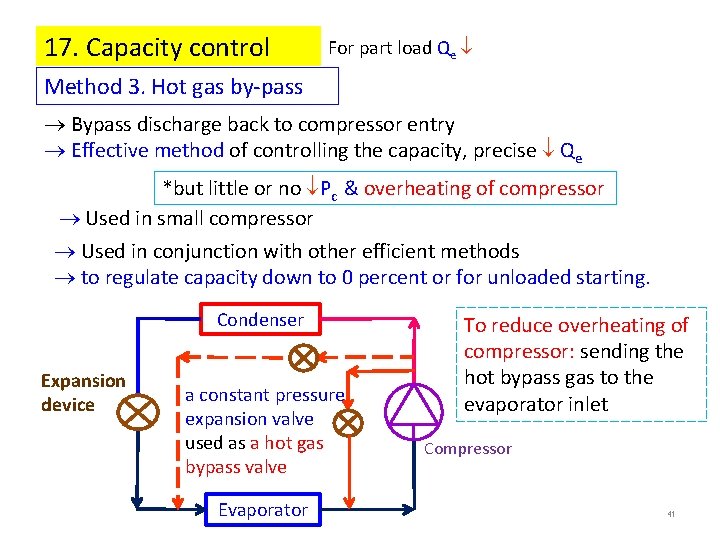
17. Capacity control For part load Qe Method 3. Hot gas by-pass Bypass discharge back to compressor entry Effective method of controlling the capacity, precise Qe *but little or no Pc & overheating of compressor Used in small compressor Used in conjunction with other efficient methods to regulate capacity down to 0 percent or for unloaded starting. Condenser Expansion device a constant pressure expansion valve used as a hot gas bypass valve Evaporator To reduce overheating of compressor: sending the hot bypass gas to the evaporator inlet Compressor 41
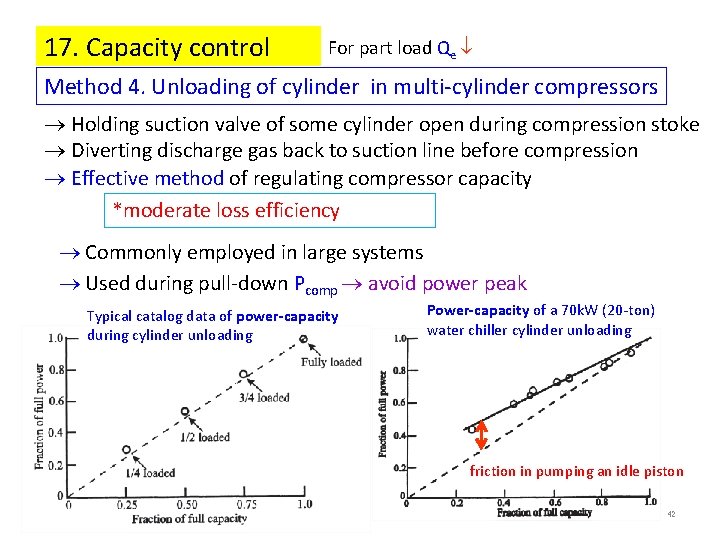
17. Capacity control For part load Qe Method 4. Unloading of cylinder in multi-cylinder compressors Holding suction valve of some cylinder open during compression stoke Diverting discharge gas back to suction line before compression Effective method of regulating compressor capacity *moderate loss efficiency Commonly employed in large systems Used during pull-down Pcomp avoid power peak Typical catalog data of power-capacity during cylinder unloading Power-capacity of a 70 k. W (20 -ton) water chiller cylinder unloading friction in pumping an idle piston 42
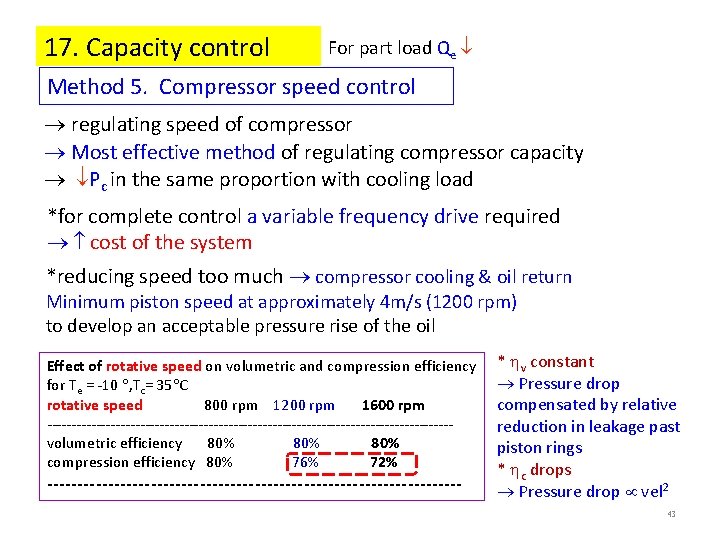
17. Capacity control For part load Qe Method 5. Compressor speed control regulating speed of compressor Most effective method of regulating compressor capacity Pc in the same proportion with cooling load *for complete control a variable frequency drive required cost of the system *reducing speed too much compressor cooling & oil return Minimum piston speed at approximately 4 m/s (1200 rpm) to develop an acceptable pressure rise of the oil Effect of rotative speed on volumetric and compression efficiency for Te = -10 , Tc= 35 C rotative speed 800 rpm 1200 rpm 1600 rpm -----------------------------------------volumetric efficiency 80% 80% compression efficiency 80% 76% 72% ---------------------------------- * v constant Pressure drop compensated by relative reduction in leakage past piston rings * c drops Pressure drop vel 2 43
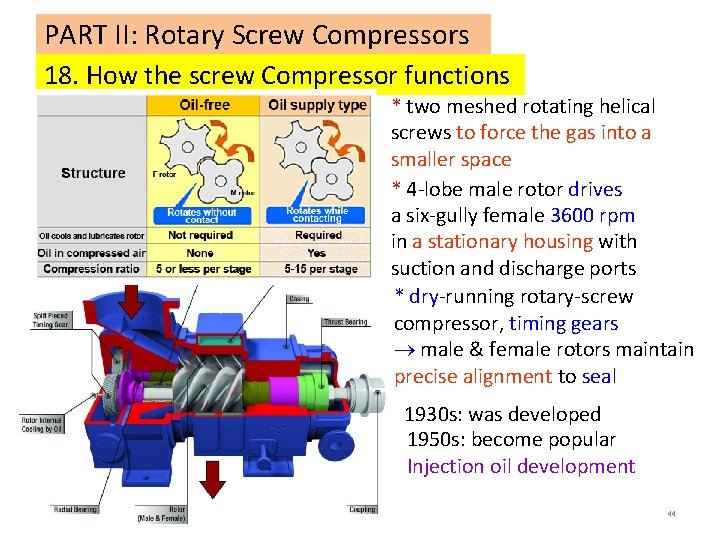
PART II: Rotary Screw Compressors 18. How the screw Compressor functions * two meshed rotating helical screws to force the gas into a smaller space * 4 -lobe male rotor drives a six-gully female 3600 rpm in a stationary housing with suction and discharge ports * dry-running rotary-screw compressor, timing gears male & female rotors maintain precise alignment to seal 1930 s: was developed 1950 s: become popular Injection oil development 44
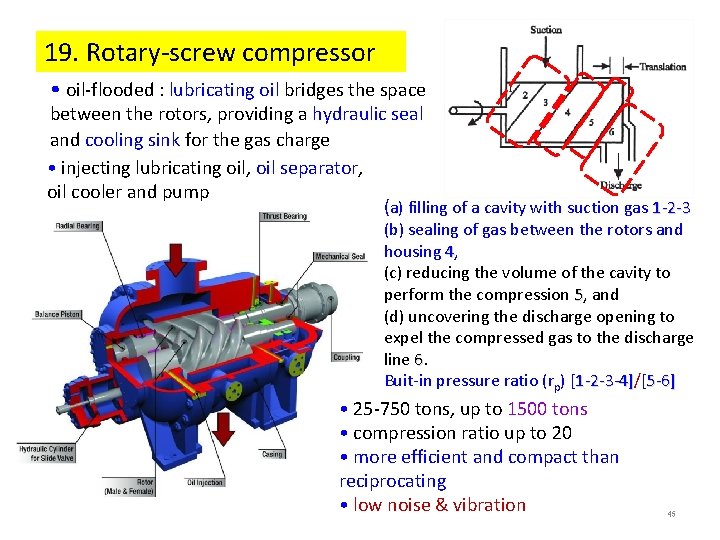
19. Rotary-screw compressor • oil-flooded : lubricating oil bridges the space between the rotors, providing a hydraulic seal and cooling sink for the gas charge • injecting lubricating oil, oil separator, oil cooler and pump (a) filling of a cavity with suction gas 1 -2 -3 (b) sealing of gas between the rotors and housing 4, (c) reducing the volume of the cavity to perform the compression 5, and (d) uncovering the discharge opening to expel the compressed gas to the discharge line 6. Buit-in pressure ratio (rp) [1 -2 -3 -4]/[ 1 -2 -3 -4] 5 -6] • 25 -750 tons, up to 1500 tons • compression ratio up to 20 • more efficient and compact than reciprocating • low noise & vibration 45
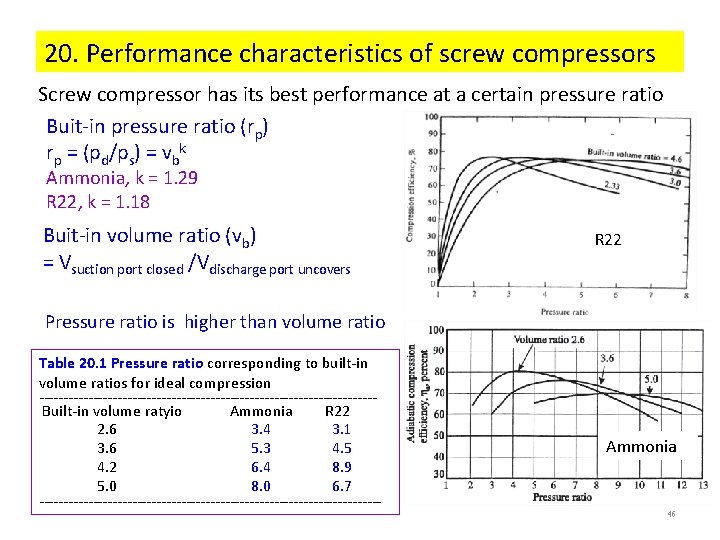
20. Performance characteristics of screw compressors Screw compressor has its best performance at a certain pressure ratio Buit-in pressure ratio (rp) rp = (pd/ps) = vbk Ammonia, k = 1. 29 R 22, k = 1. 18 Buit-in volume ratio (vb) = Vsuction port closed /Vdischarge port uncovers R 22 Pressure ratio is higher than volume ratio Table 20. 1 Pressure ratio corresponding to built-in volume ratios for ideal compression ----------------------------------Built-in volume ratyio Ammonia R 22 2. 6 3. 4 3. 1 3. 6 5. 3 4. 5 4. 2 6. 4 8. 9 5. 0 8. 0 6. 7 ----------------------------------- Ammonia 46
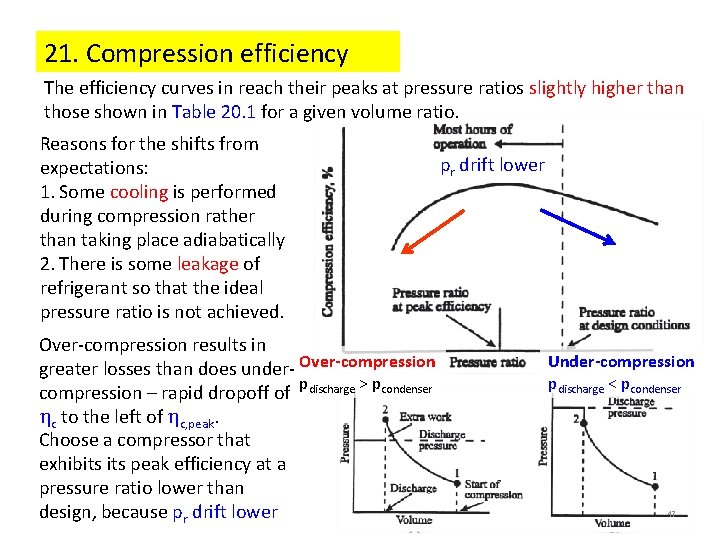
21. Compression efficiency The efficiency curves in reach their peaks at pressure ratios slightly higher than those shown in Table 20. 1 for a given volume ratio. Reasons for the shifts from expectations: 1. Some cooling is performed during compression rather than taking place adiabatically 2. There is some leakage of refrigerant so that the ideal pressure ratio is not achieved. Over-compression results in greater losses than does under- Over-compression – rapid dropoff of pdischarge > pcondenser c to the left of c, peak. Choose a compressor that exhibits peak efficiency at a pressure ratio lower than design, because pr drift lower Under-compression pdischarge < pcondenser 47
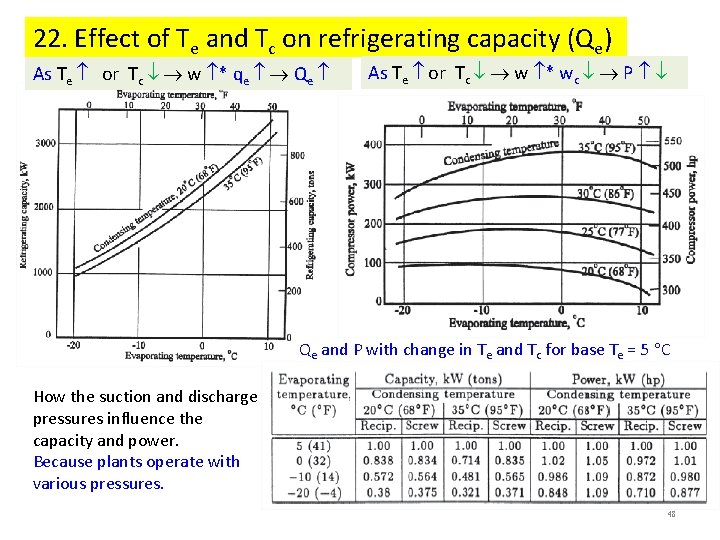
22. Effect of Te and Tc on refrigerating capacity (Qe) As Te or Tc w * qe Qe As Te or Tc w * wc P Qe and P with change in Te and Tc for base Te = 5 C How the suction and discharge pressures influence the capacity and power. Because plants operate with various pressures. 48
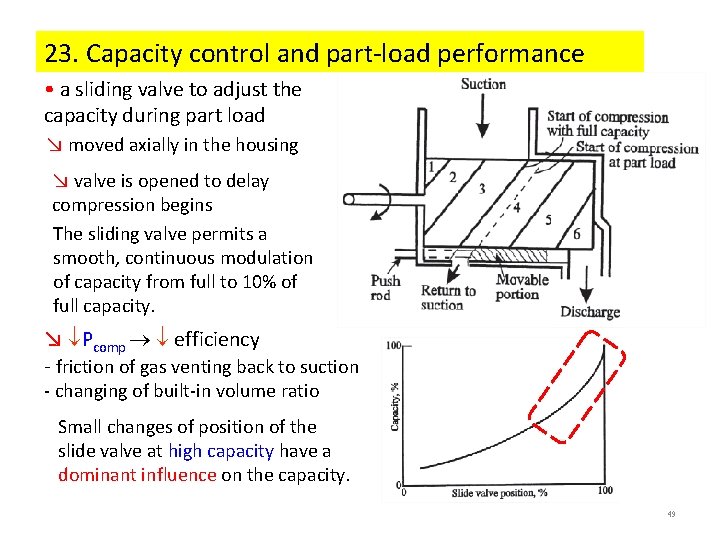
23. Capacity control and part-load performance • a sliding valve to adjust the capacity during part load ↘ moved axially in the housing ↘ valve is opened to delay compression begins The sliding valve permits a smooth, continuous modulation of capacity from full to 10% of full capacity. ↘ Pcomp efficiency - friction of gas venting back to suction - changing of built-in volume ratio Small changes of position of the slide valve at high capacity have a dominant influence on the capacity. 49
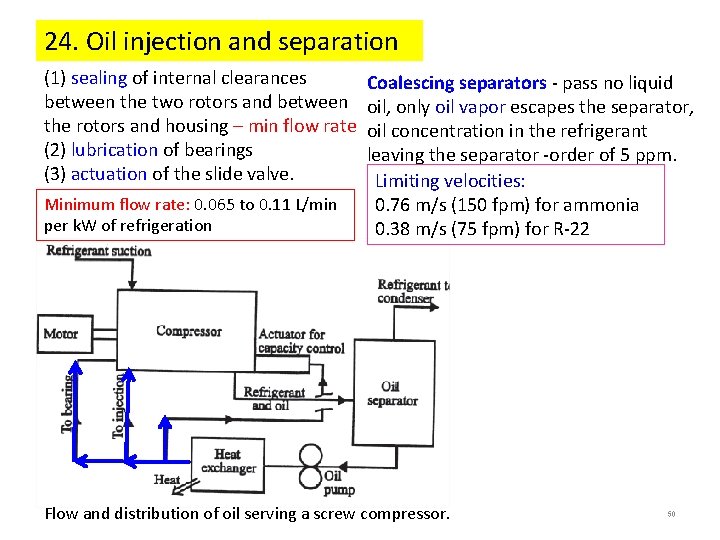
24. Oil injection and separation (1) sealing of internal clearances between the two rotors and between the rotors and housing – min flow rate (2) lubrication of bearings (3) actuation of the slide valve. Minimum flow rate: 0. 065 to 0. 11 L/min per k. W of refrigeration Coalescing separators - pass no liquid oil, only oil vapor escapes the separator, oil concentration in the refrigerant leaving the separator -order of 5 ppm. Limiting velocities: 0. 76 m/s (150 fpm) for ammonia 0. 38 m/s (75 fpm) for R-22 Flow and distribution of oil serving a screw compressor. 50
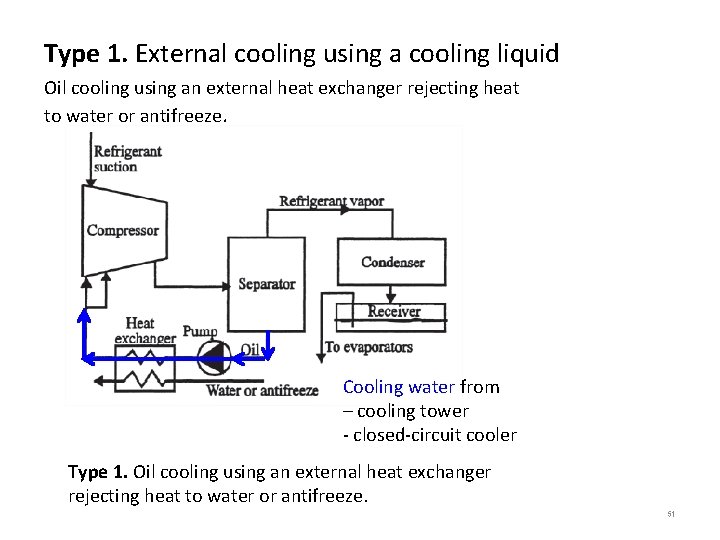
Type 1. External cooling using a cooling liquid Oil cooling using an external heat exchanger rejecting heat to water or antifreeze. Cooling water from – cooling tower - closed-circuit cooler Type 1. Oil cooling using an external heat exchanger rejecting heat to water or antifreeze. 51
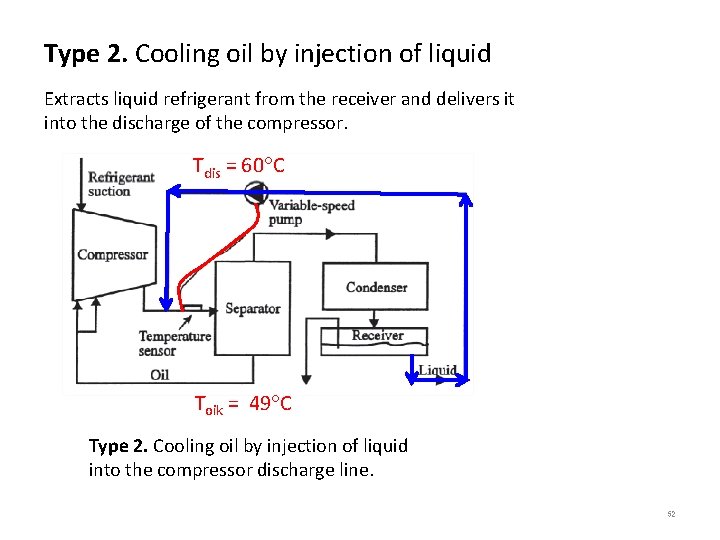
Type 2. Cooling oil by injection of liquid Extracts liquid refrigerant from the receiver and delivers it into the discharge of the compressor. Tdis = 60 C Toik = 49 C Type 2. Cooling oil by injection of liquid into the compressor discharge line. 52
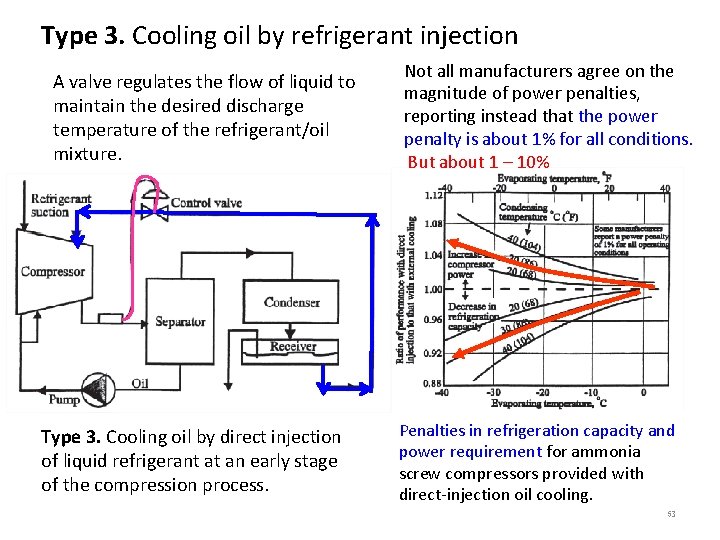
Type 3. Cooling oil by refrigerant injection A valve regulates the flow of liquid to maintain the desired discharge temperature of the refrigerant/oil mixture. Type 3. Cooling oil by direct injection of liquid refrigerant at an early stage of the compression process. Not all manufacturers agree on the magnitude of power penalties, reporting instead that the power penalty is about 1% for all conditions. But about 1 – 10% Penalties in refrigeration capacity and power requirement for ammonia screw compressors provided with direct-injection oil cooling. 53
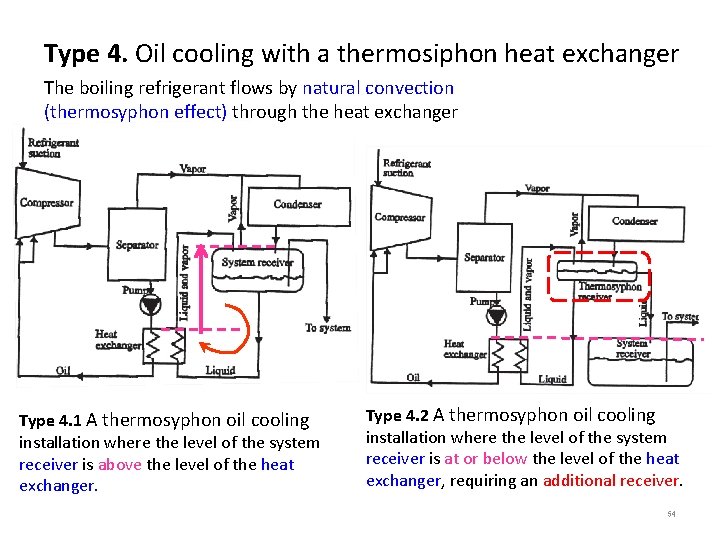
Type 4. Oil cooling with a thermosiphon heat exchanger The boiling refrigerant flows by natural convection (thermosyphon effect) through the heat exchanger Type 4. 1 A thermosyphon oil cooling installation where the level of the system receiver is above the level of the heat exchanger. Type 4. 2 A thermosyphon oil cooling installation where the level of the system receiver is at or below the level of the heat exchanger, requiring an additional receiver. 54
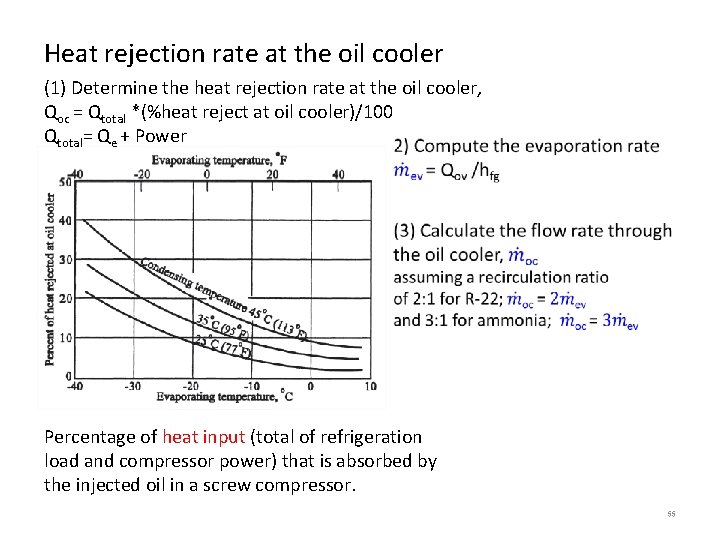
Heat rejection rate at the oil cooler (1) Determine the heat rejection rate at the oil cooler, Qoc = Qtotal *(%heat reject at oil cooler)/100 Qtotal= Qe + Power Percentage of heat input (total of refrigeration load and compressor power) that is absorbed by the injected oil in a screw compressor. 55
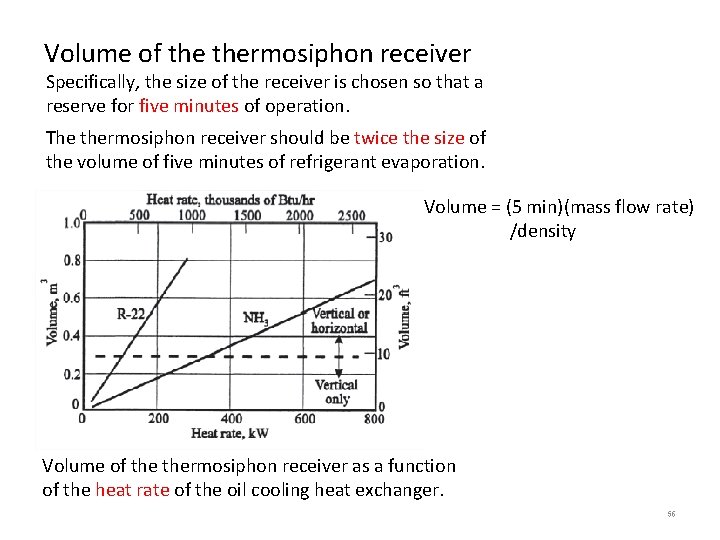
Volume of thermosiphon receiver Specifically, the size of the receiver is chosen so that a reserve for five minutes of operation. The thermosiphon receiver should be twice the size of the volume of five minutes of refrigerant evaporation. Volume = (5 min)(mass flow rate) /density Volume of thermosiphon receiver as a function of the heat rate of the oil cooling heat exchanger. 56
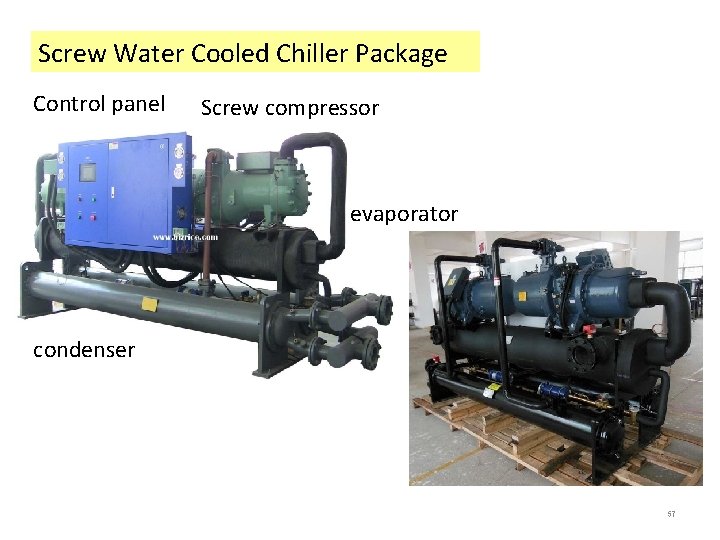
Screw Water Cooled Chiller Package Control panel Screw compressor evaporator condenser 57
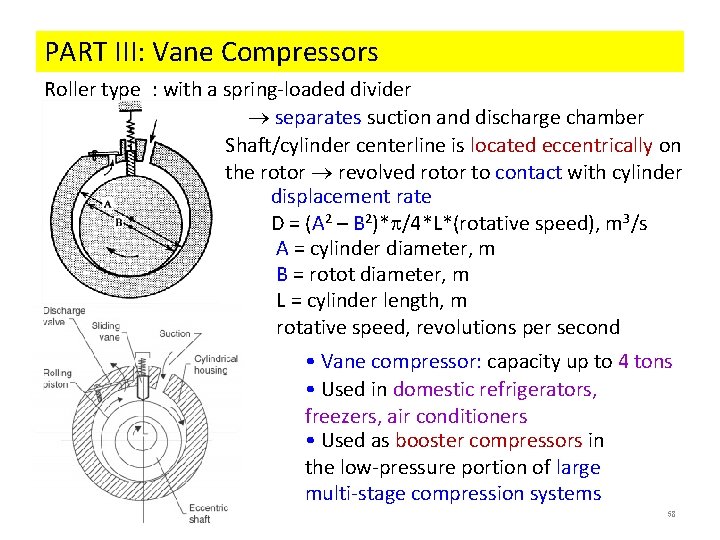
PART III: Vane Compressors Roller type : with a spring-loaded divider separates suction and discharge chamber Shaft/cylinder centerline is located eccentrically on the rotor revolved rotor to contact with cylinder displacement rate D = (A 2 – B 2)* /4*L*(rotative speed), m 3/s A = cylinder diameter, m B = rotot diameter, m L = cylinder length, m rotative speed, revolutions per second • Vane compressor: capacity up to 4 tons • Used in domestic refrigerators, freezers, air conditioners • Used as booster compressors in the low-pressure portion of large multi-stage compression systems 58
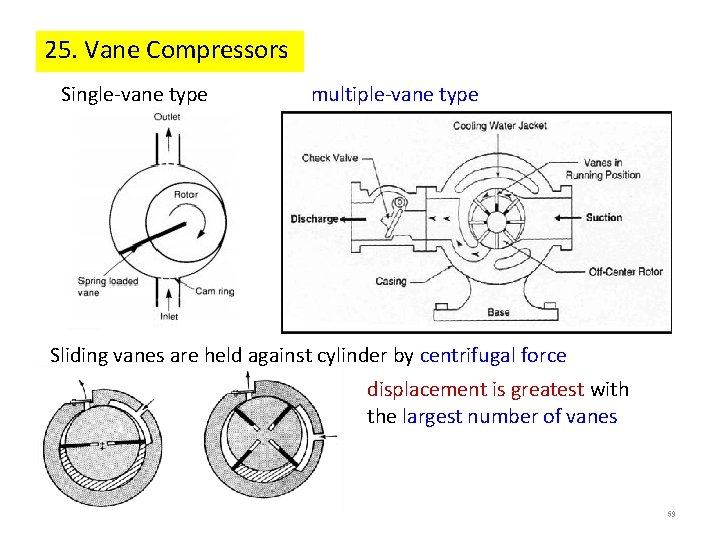
25. Vane Compressors Single-vane type multiple-vane type Sliding vanes are held against cylinder by centrifugal force displacement is greatest with the largest number of vanes 59
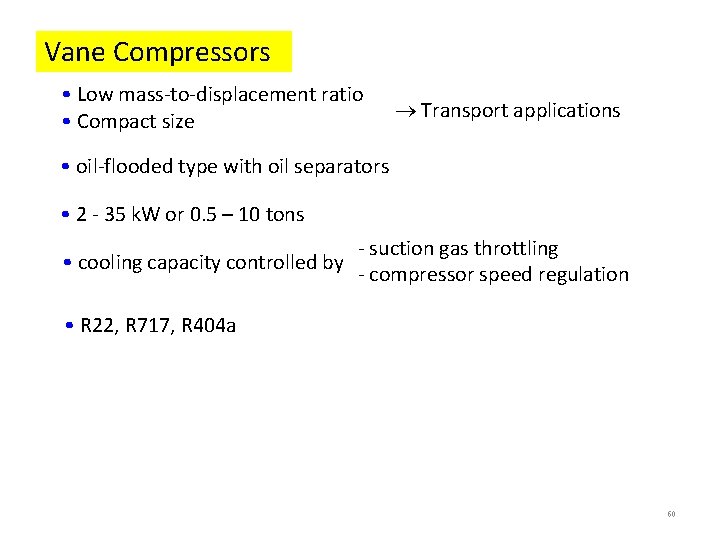
Vane Compressors • Low mass-to-displacement ratio • Compact size Transport applications • oil-flooded type with oil separators • 2 - 35 k. W or 0. 5 – 10 tons - suction gas throttling • cooling capacity controlled by - compressor speed regulation • R 22, R 717, R 404 a 60
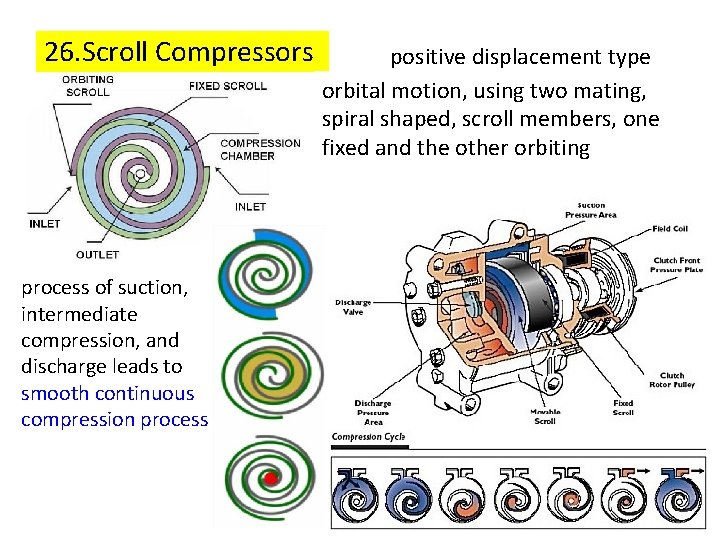
26. Scroll Compressors positive displacement type orbital motion, using two mating, spiral shaped, scroll members, one fixed and the other orbiting process of suction, intermediate compression, and discharge leads to smooth continuous compression process 61
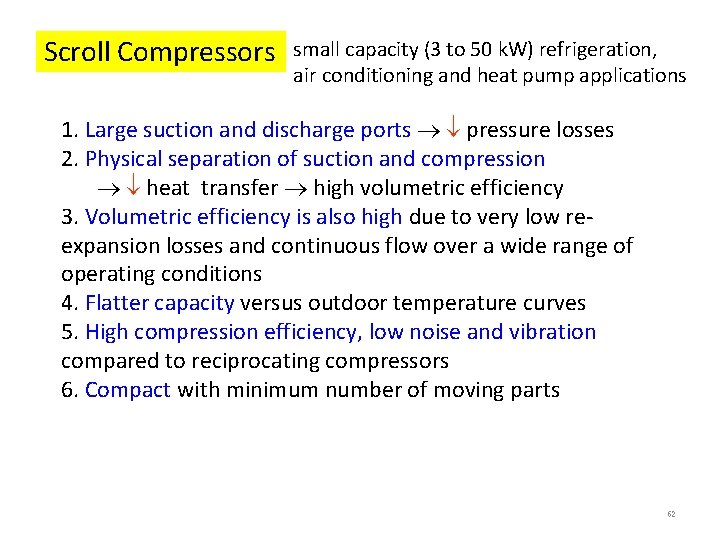
Scroll Compressors small capacity (3 to 50 k. W) refrigeration, air conditioning and heat pump applications 1. Large suction and discharge ports pressure losses 2. Physical separation of suction and compression heat transfer high volumetric efficiency 3. Volumetric efficiency is also high due to very low reexpansion losses and continuous flow over a wide range of operating conditions 4. Flatter capacity versus outdoor temperature curves 5. High compression efficiency, low noise and vibration compared to reciprocating compressors 6. Compact with minimum number of moving parts 62
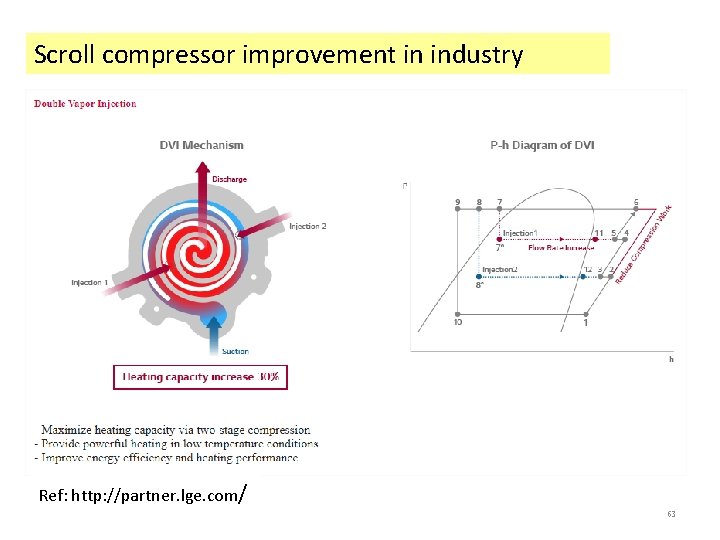
Scroll compressor improvement in industry Ref: http: //partner. lge. com/ 63
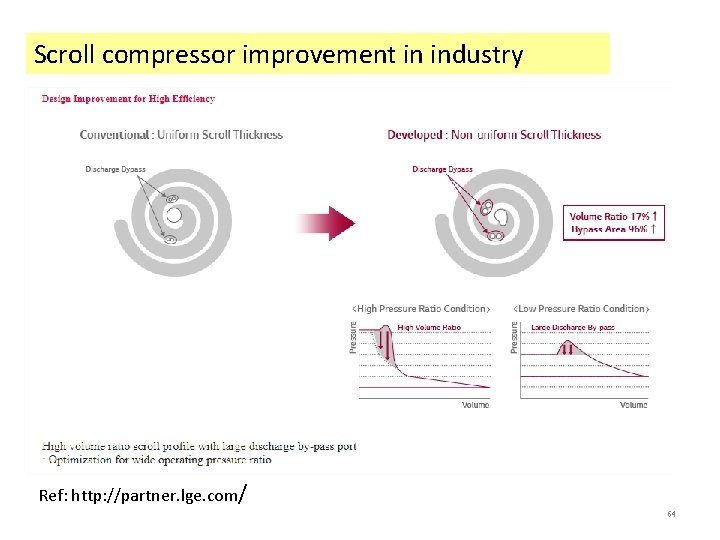
Scroll compressor improvement in industry Ref: http: //partner. lge. com/ 64
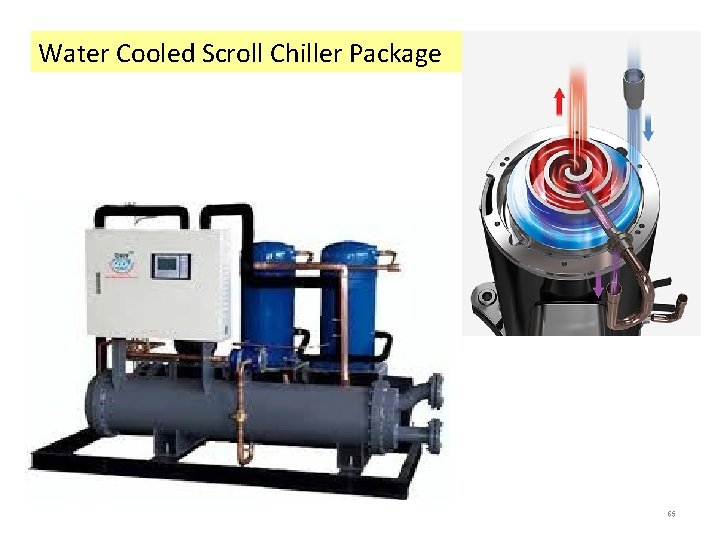
Water Cooled Scroll Chiller Package 65
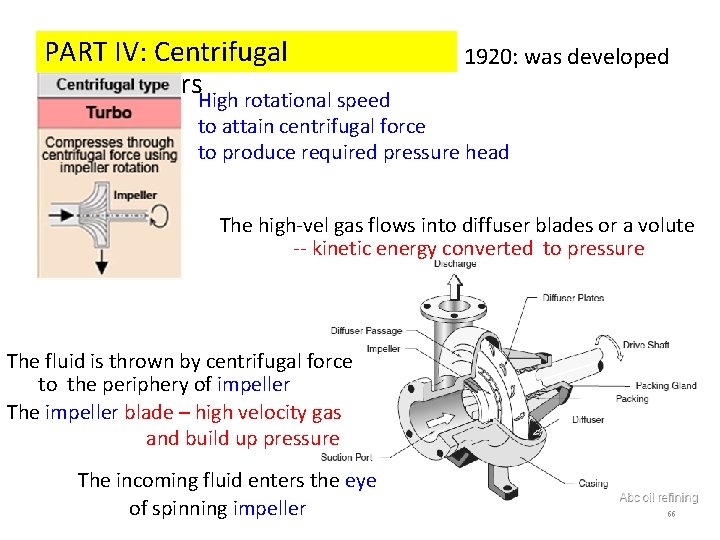
PART IV: Centrifugal Compressors. High rotational speed 1920: was developed to attain centrifugal force to produce required pressure head The high-vel gas flows into diffuser blades or a volute -- kinetic energy converted to pressure The fluid is thrown by centrifugal force to the periphery of impeller The impeller blade – high velocity gas and build up pressure The incoming fluid enters the eye of spinning impeller 66
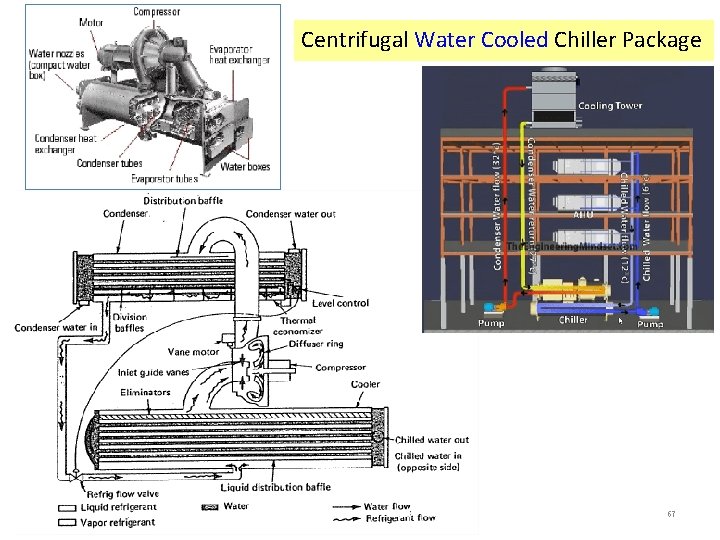
Centrifugal Water Cooled Chiller Package 67
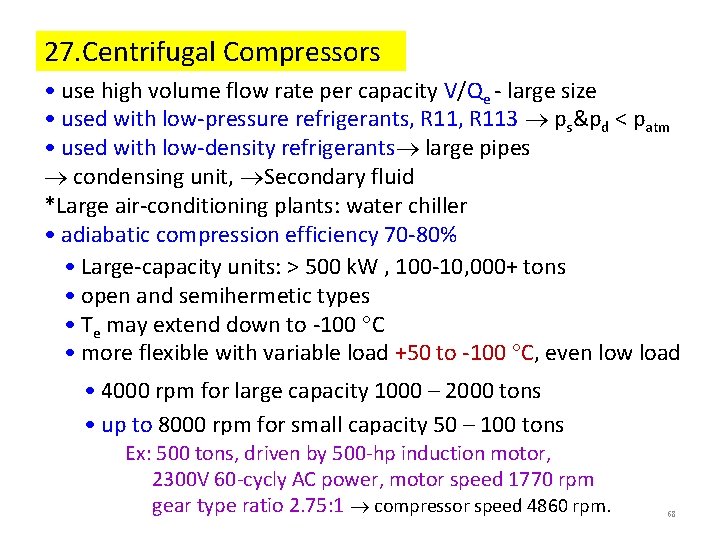
27. Centrifugal Compressors • use high volume flow rate per capacity V/Qe - large size • used with low-pressure refrigerants, R 113 ps&pd < patm • used with low-density refrigerants large pipes condensing unit, Secondary fluid *Large air-conditioning plants: water chiller • adiabatic compression efficiency 70 -80% • Large-capacity units: > 500 k. W , 100 -10, 000+ tons • open and semihermetic types • Te may extend down to -100 C • more flexible with variable load +50 to -100 C, even low load • 4000 rpm for large capacity 1000 – 2000 tons • up to 8000 rpm for small capacity 50 – 100 tons Ex: 500 tons, driven by 500 -hp induction motor, 2300 V 60 -cycly AC power, motor speed 1770 rpm gear type ratio 2. 75: 1 compressor speed 4860 rpm. 68
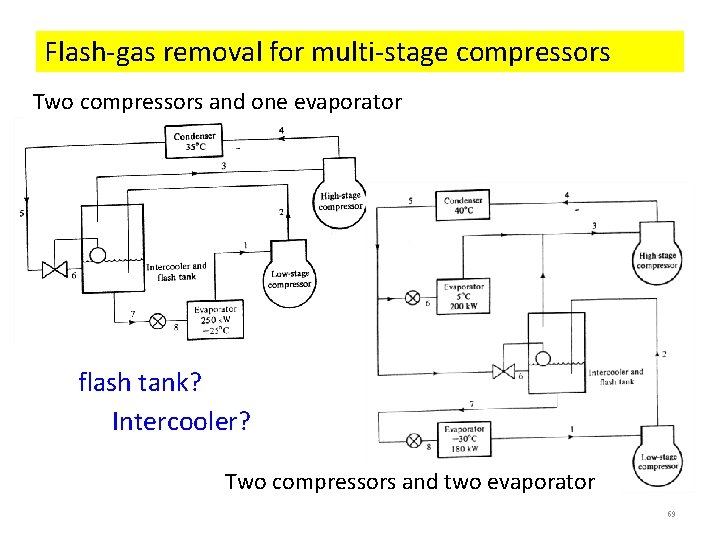
Flash-gas removal for multi-stage compressors Two compressors and one evaporator flash tank? Intercooler? Two compressors and two evaporator 69
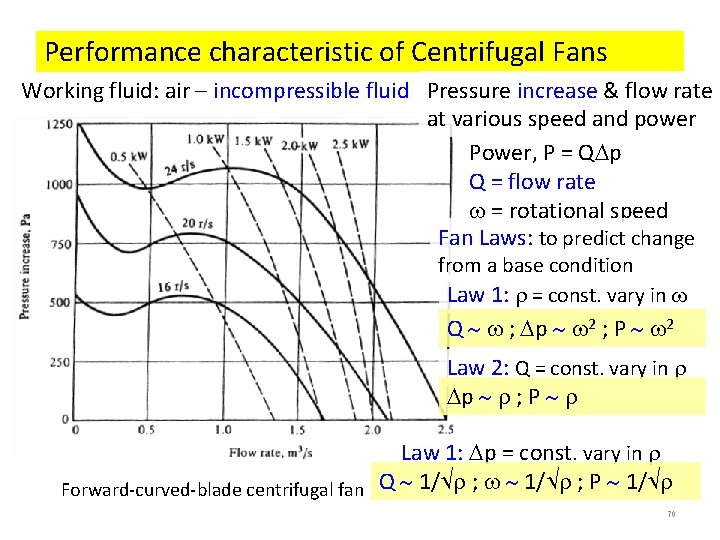
Performance characteristic of Centrifugal Fans Working fluid: air – incompressible fluid Pressure increase & flow rate at various speed and power Power, P = Q p Q = flow rate = rotational speed Fan Laws: to predict change from a base condition Law 1: = const. vary in Q ; p 2 ; P 2 Law 2: Q = const. vary in p ; P Law 1: p = const. vary in Forward-curved-blade centrifugal fan Q 1/ ; P 1/ 70
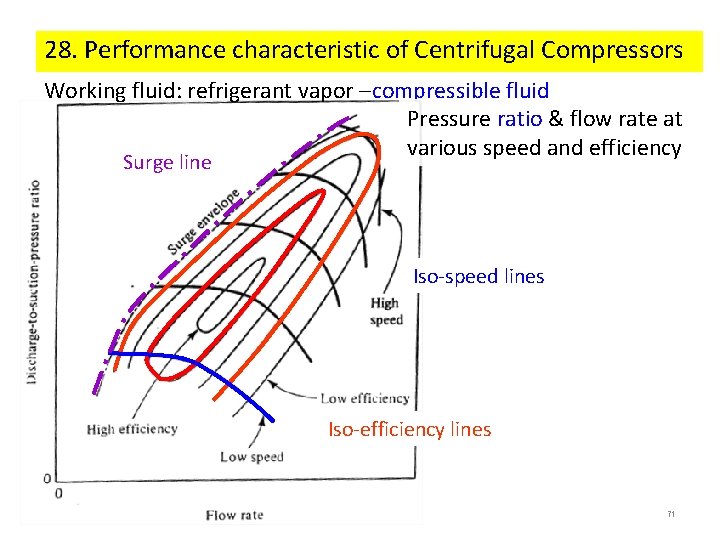
28. Performance characteristic of Centrifugal Compressors Working fluid: refrigerant vapor –compressible fluid Pressure ratio & flow rate at various speed and efficiency Surge line Iso-speed lines Iso-efficiency lines 71
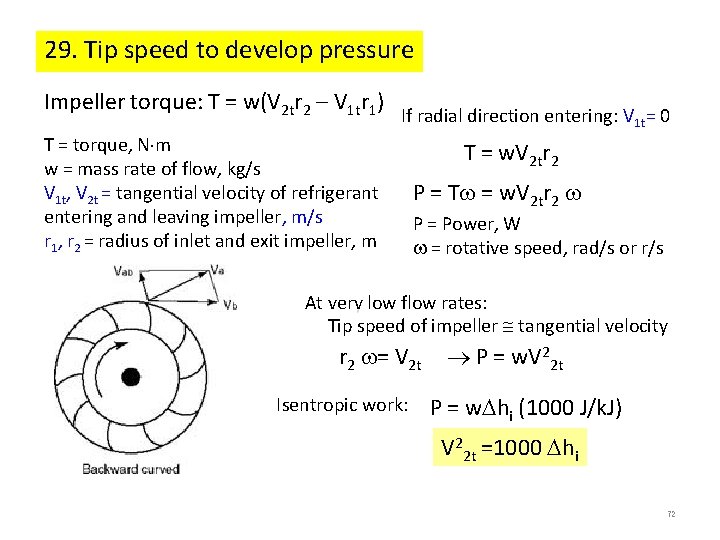
29. Tip speed to develop pressure Impeller torque: T = w(V 2 tr 2 – V 1 tr 1) If radial direction entering: V 1 t= 0 T = torque, N m w = mass rate of flow, kg/s V 1 t, V 2 t = tangential velocity of refrigerant entering and leaving impeller, m/s r 1, r 2 = radius of inlet and exit impeller, m T = w. V 2 tr 2 P = T = w. V 2 tr 2 P = Power, W = rotative speed, rad/s or r/s At very low flow rates: Tip speed of impeller tangential velocity r 2 = V 2 t Isentropic work: P = w. V 22 t P = w hi (1000 J/k. J) V 22 t =1000 hi 72
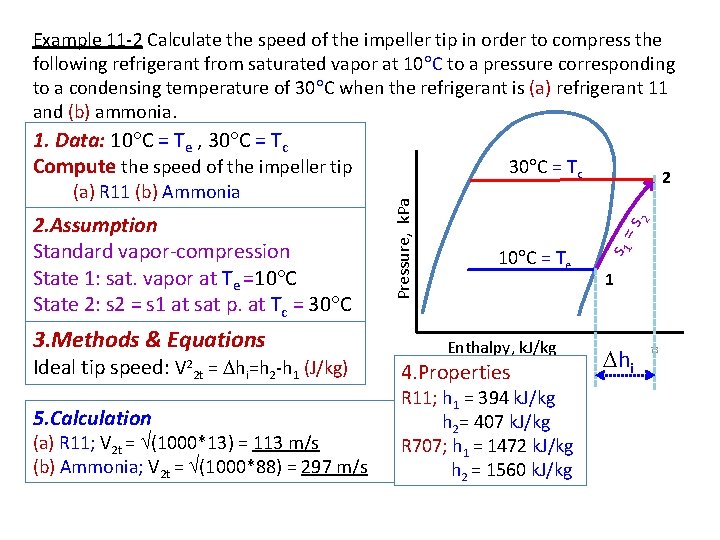
Example 11 -2 Calculate the speed of the impeller tip in order to compress the following refrigerant from saturated vapor at 10 C to a pressure corresponding to a condensing temperature of 30 C when the refrigerant is (a) refrigerant 11 and (b) ammonia. 1. Data: 10 C = Te , 30 C = Tc Compute the speed of the impeller tip 3. Methods & Equations Ideal tip speed: V 22 t = hi=h 2 -h 1 (J/kg) 5. Calculation (a) R 11; V 2 t = (1000*13) = 113 m/s (b) Ammonia; V 2 t = (1000*88) = 297 m/s 10 C = Te Enthalpy, k. J/kg 4. Properties R 11; h 1 = 394 k. J/kg h 2= 407 k. J/kg R 707; h 1 = 1472 k. J/kg h 2 = 1560 k. J/kg 2 s 1 = s 2 2. Assumption Standard vapor-compression State 1: sat. vapor at Te =10 C State 2: s 2 = s 1 at sat p. at Tc = 30 C Pressure, k. Pa (a) R 11 (b) Ammonia 30 C = Tc 1 hi 73
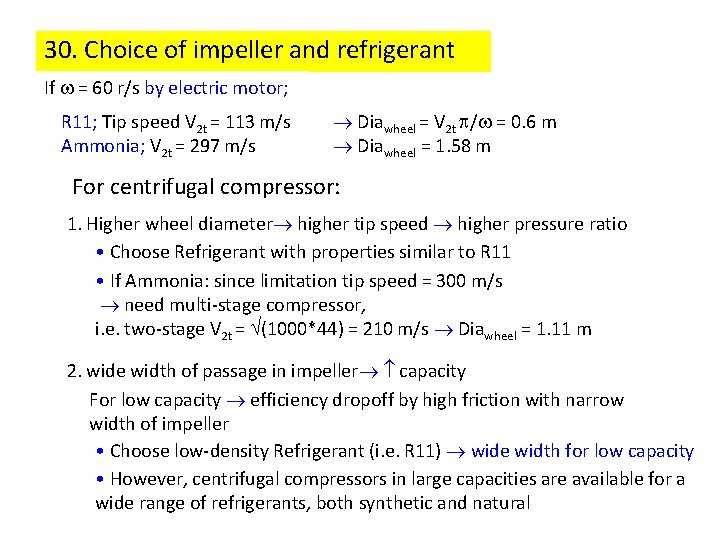
30. Choice of impeller and refrigerant If = 60 r/s by electric motor; R 11; Tip speed V 2 t = 113 m/s Ammonia; V 2 t = 297 m/s Diawheel = V 2 t / = 0. 6 m Diawheel = 1. 58 m For centrifugal compressor: 1. Higher wheel diameter higher tip speed higher pressure ratio • Choose Refrigerant with properties similar to R 11 • If Ammonia: since limitation tip speed = 300 m/s need multi-stage compressor, i. e. two-stage V 2 t = (1000*44) = 210 m/s Diawheel = 1. 11 m 2. wide width of passage in impeller capacity For low capacity efficiency dropoff by high friction with narrow width of impeller • Choose low-density Refrigerant (i. e. R 11) wide width for low capacity • However, centrifugal compressors in large capacities are available for a wide range of refrigerants, both synthetic and natural 74
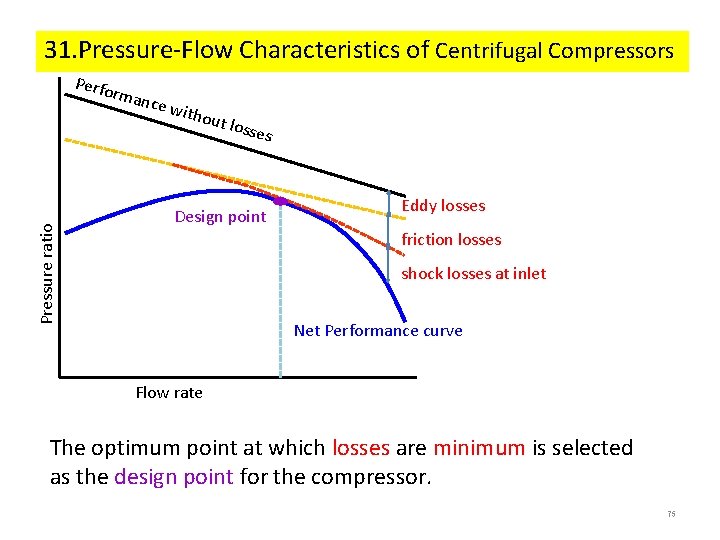
31. Pressure-Flow Characteristics of Centrifugal Compressors Perfo r Pressure ratio manc e wit hout loss es Design point Eddy losses friction losses shock losses at inlet Net Performance curve Flow rate The optimum point at which losses are minimum is selected as the design point for the compressor. 75
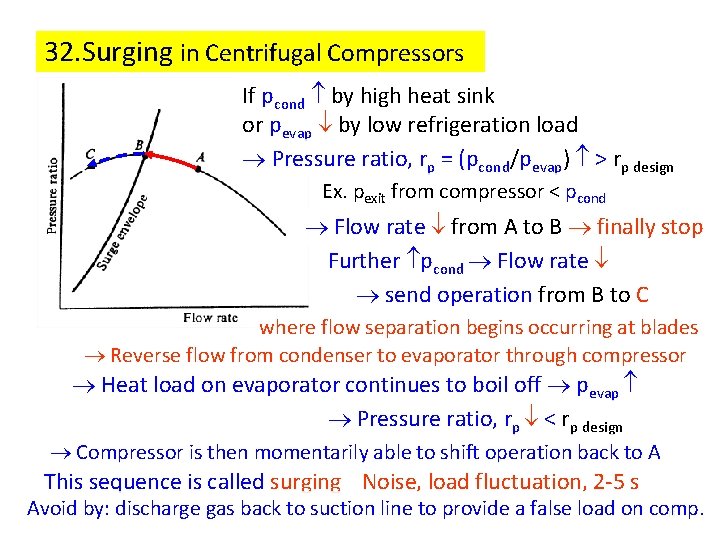
32. Surging in Centrifugal Compressors If pcond by high heat sink or pevap by low refrigeration load Pressure ratio, rp = (pcond/pevap) > rp design Ex. pexit from compressor < pcond Flow rate from A to B finally stop Further pcond Flow rate send operation from B to C where flow separation begins occurring at blades Reverse flow from condenser to evaporator through compressor Heat load on evaporator continues to boil off pevap Pressure ratio, rp < rp design Compressor is then momentarily able to shift operation back to A This sequence is called surging Noise, load fluctuation, 2 -5 s Avoid by: discharge gas back to suction line to provide a false load on comp. 76
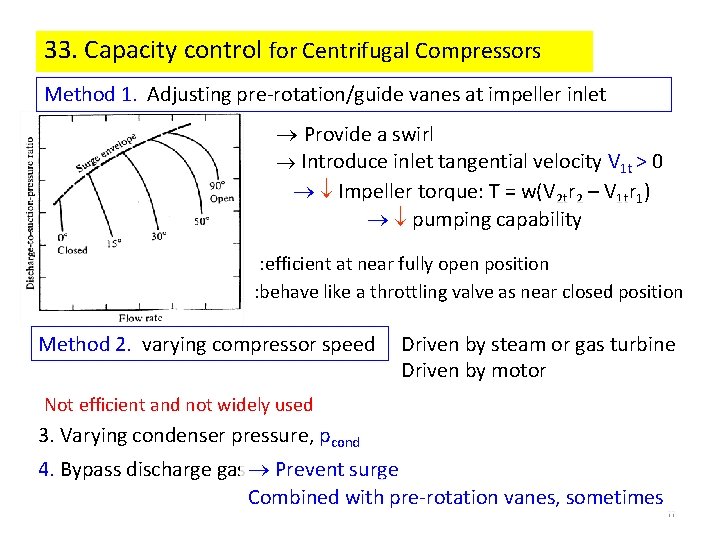
33. Capacity control for Centrifugal Compressors Method 1. Adjusting pre-rotation/guide vanes at impeller inlet Provide a swirl Introduce inlet tangential velocity V 1 t > 0 Impeller torque: T = w(V 2 tr 2 – V 1 tr 1) pumping capability : efficient at near fully open position : behave like a throttling valve as near closed position Method 2. varying compressor speed Driven by steam or gas turbine Driven by motor Not efficient and not widely used 3. Varying condenser pressure, pcond 4. Bypass discharge gas Prevent surge Combined with pre-rotation vanes, sometimes 77
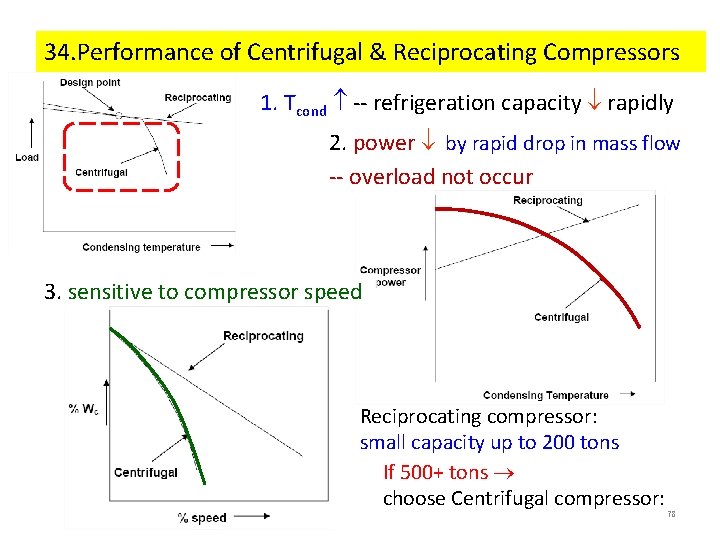
34. Performance of Centrifugal & Reciprocating Compressors 1. Tcond -- refrigeration capacity rapidly 2. power by rapid drop in mass flow -- overload not occur 3. sensitive to compressor speed Reciprocating compressor: small capacity up to 200 tons If 500+ tons choose Centrifugal compressor: 78
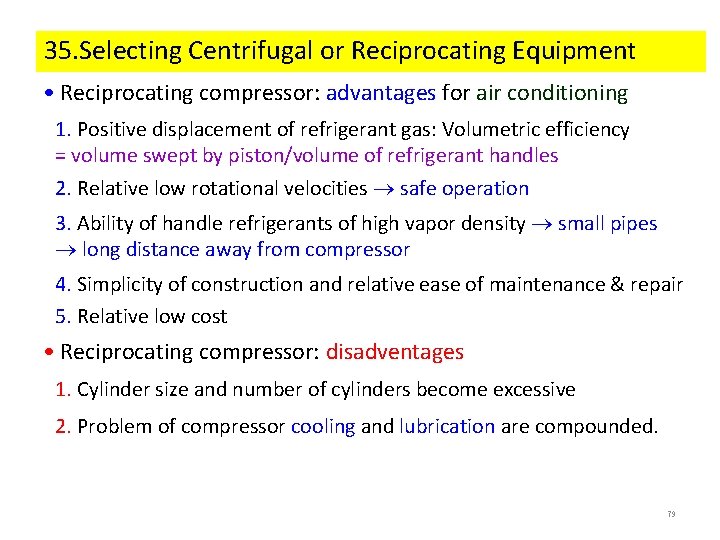
35. Selecting Centrifugal or Reciprocating Equipment • Reciprocating compressor: advantages for air conditioning 1. Positive displacement of refrigerant gas: Volumetric efficiency = volume swept by piston/volume of refrigerant handles 2. Relative low rotational velocities safe operation 3. Ability of handle refrigerants of high vapor density small pipes long distance away from compressor 4. Simplicity of construction and relative ease of maintenance & repair 5. Relative low cost • Reciprocating compressor: disadventages 1. Cylinder size and number of cylinders become excessive 2. Problem of compressor cooling and lubrication are compounded. 79
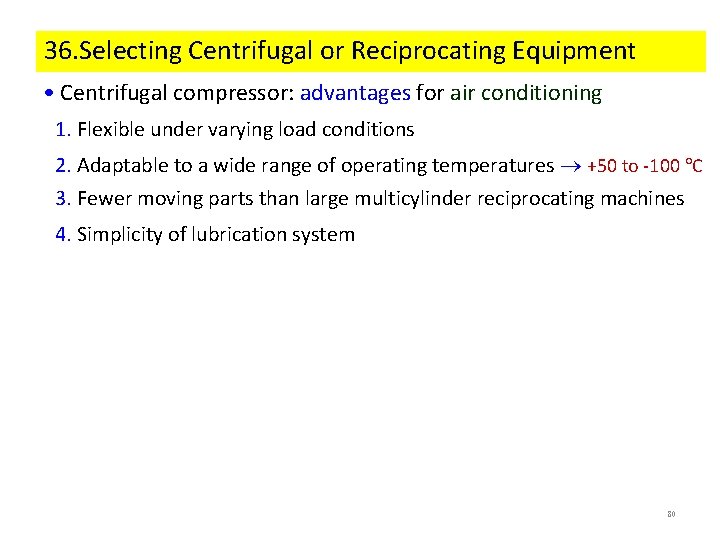
36. Selecting Centrifugal or Reciprocating Equipment • Centrifugal compressor: advantages for air conditioning 1. Flexible under varying load conditions 2. Adaptable to a wide range of operating temperatures +50 to -100 C 3. Fewer moving parts than large multicylinder reciprocating machines 4. Simplicity of lubrication system 80

37. Criteria for Equipment Selection Capacity Most often used Sometimes used Seldom used 0 – 10 tons Package/Unit system Near conditioned space (35 k. W) Unit central system + Duct distribution Built-up central system 10 -100 tons Unitary system + Duct (350 k. W) distribution (Reciprocating Unit/Package system Near conditioned space Compression/ Absorption systems Built-up central system Factory designed central 100 -500 system + Reciprocating com. , tons (1750 k. W) + Water chiller Built-up central system + Multiple-unit Centrifugal or Absorption systems + Duct + Water chillers work; Absorption 500 -5000 Built-up central system + Centrifugal com. , + Water tons (17500 k. W) chiller/Absorption systems Built-up central system + Absorption/Steam-jet machines + Water chillers Reciprocating com. + DX coils) Rooftop units in multiple Built-up central system + Reciprocating compressors 81
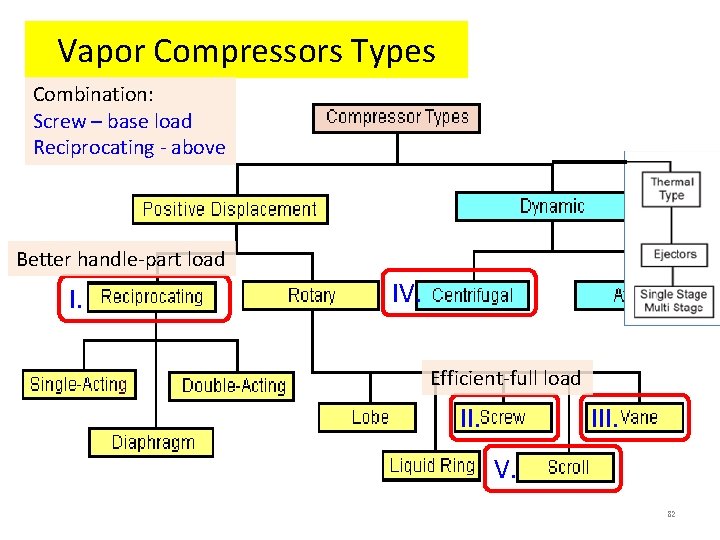
Vapor Compressors Types Combination: Screw – base load Reciprocating - above Better handle-part load I. IV. Efficient-full load II. III. V. 82
- Slides: 82