SUBSTRUCTURE AND FOUNDATION CODE Second Revision 2013 Corrected
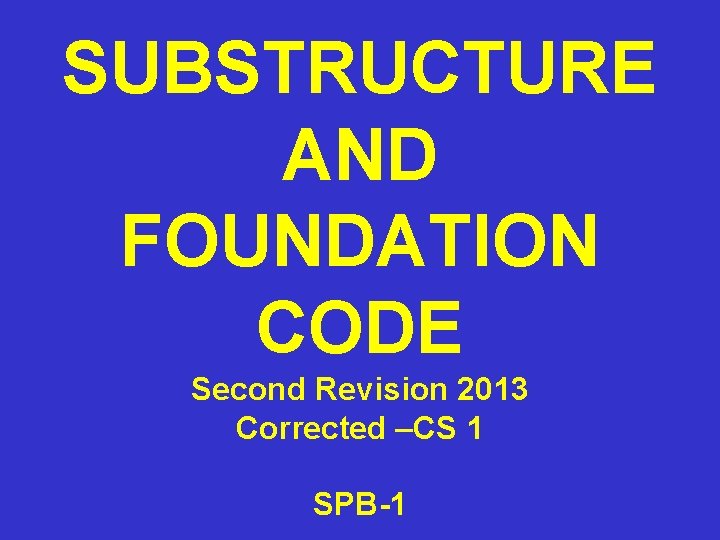
SUBSTRUCTURE AND FOUNDATION CODE Second Revision 2013 Corrected –CS 1 SPB-1
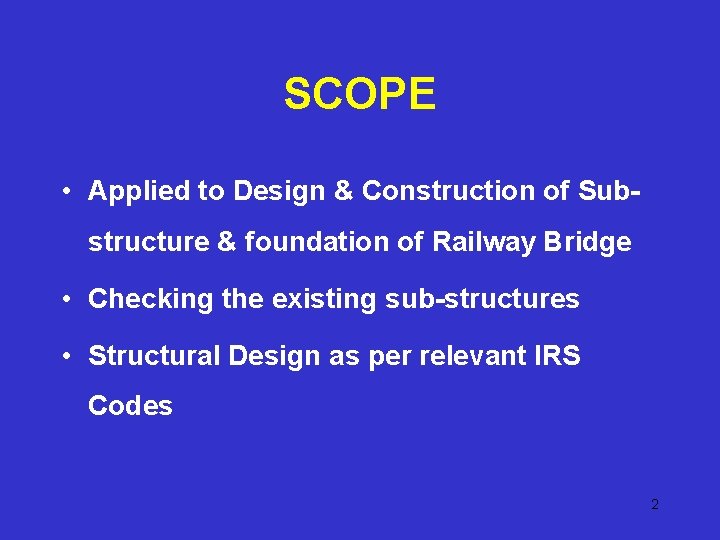
SCOPE • Applied to Design & Construction of Substructure & foundation of Railway Bridge • Checking the existing sub-structures • Structural Design as per relevant IRS Codes 2
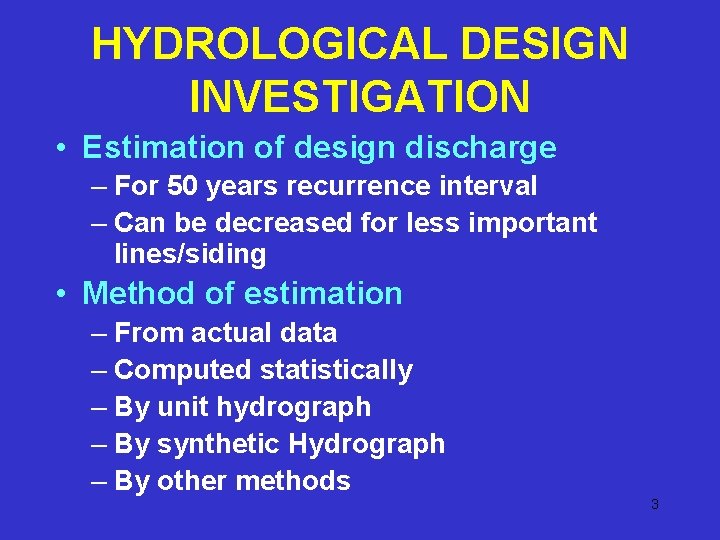
HYDROLOGICAL DESIGN INVESTIGATION • Estimation of design discharge – For 50 years recurrence interval – Can be decreased for less important lines/siding • Method of estimation – From actual data – Computed statistically – By unit hydrograph – By synthetic Hydrograph – By other methods 3
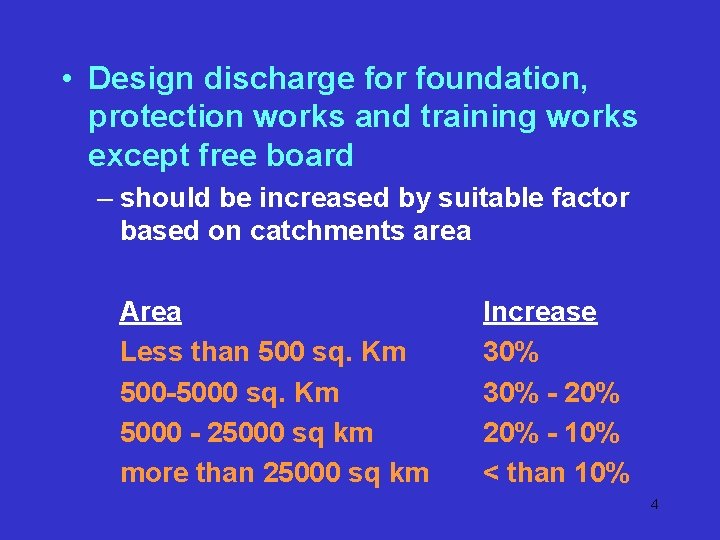
• Design discharge for foundation, protection works and training works except free board – should be increased by suitable factor based on catchments area Area Less than 500 sq. Km 500 -5000 sq. Km 5000 - 25000 sq km more than 25000 sq km Increase 30% - 20% - 10% < than 10% 4
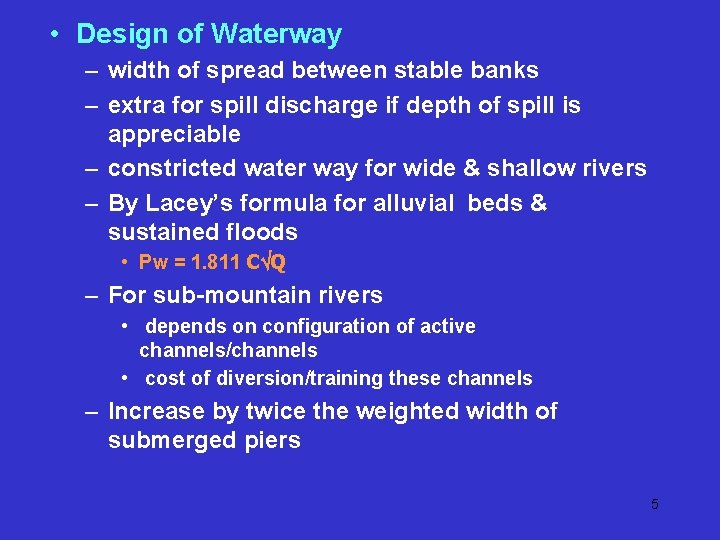
• Design of Waterway – width of spread between stable banks – extra for spill discharge if depth of spill is appreciable – constricted water way for wide & shallow rivers – By Lacey’s formula for alluvial beds & sustained floods • Pw = 1. 811 C Q – For sub-mountain rivers • depends on configuration of active channels/channels • cost of diversion/training these channels – Increase by twice the weighted width of submerged piers 5
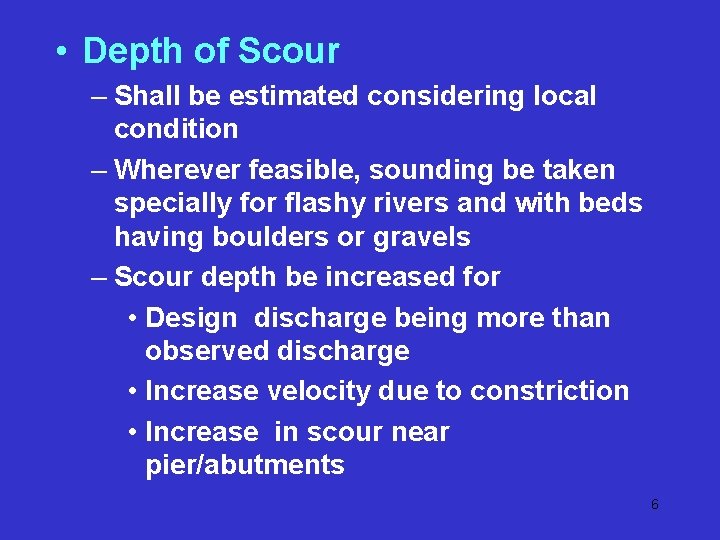
• Depth of Scour – Shall be estimated considering local condition – Wherever feasible, sounding be taken specially for flashy rivers and with beds having boulders or gravels – Scour depth be increased for • Design discharge being more than observed discharge • Increase velocity due to constriction • Increase in scour near pier/abutments 6
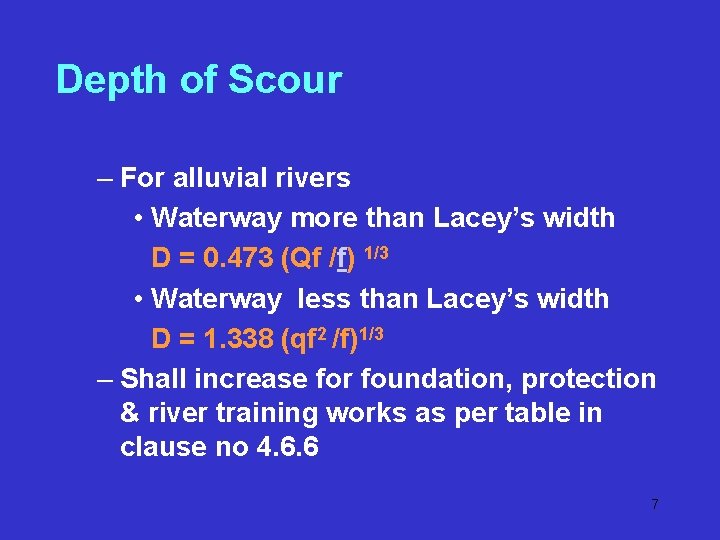
Depth of Scour – For alluvial rivers • Waterway more than Lacey’s width D = 0. 473 (Qf /f) 1/3 • Waterway less than Lacey’s width D = 1. 338 (qf 2 /f)1/3 – Shall increase for foundation, protection & river training works as per table in clause no 4. 6. 6 7
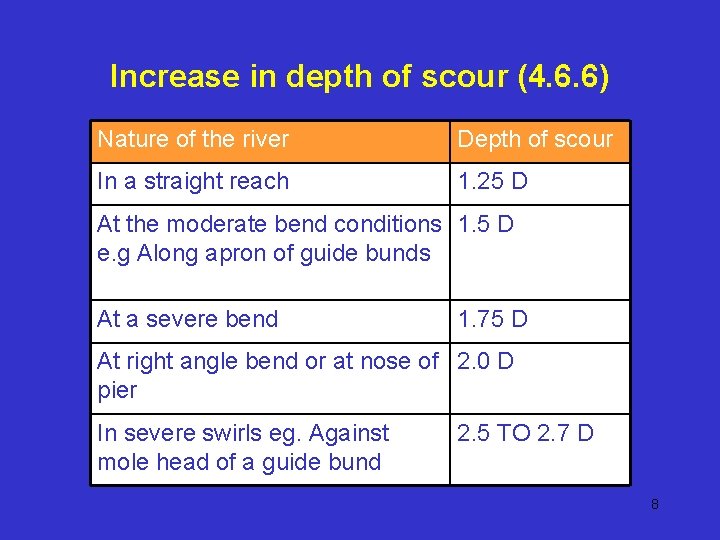
Increase in depth of scour (4. 6. 6) Nature of the river Depth of scour In a straight reach 1. 25 D At the moderate bend conditions 1. 5 D e. g Along apron of guide bunds At a severe bend 1. 75 D At right angle bend or at nose of 2. 0 D pier In severe swirls eg. Against mole head of a guide bund 2. 5 TO 2. 7 D 8
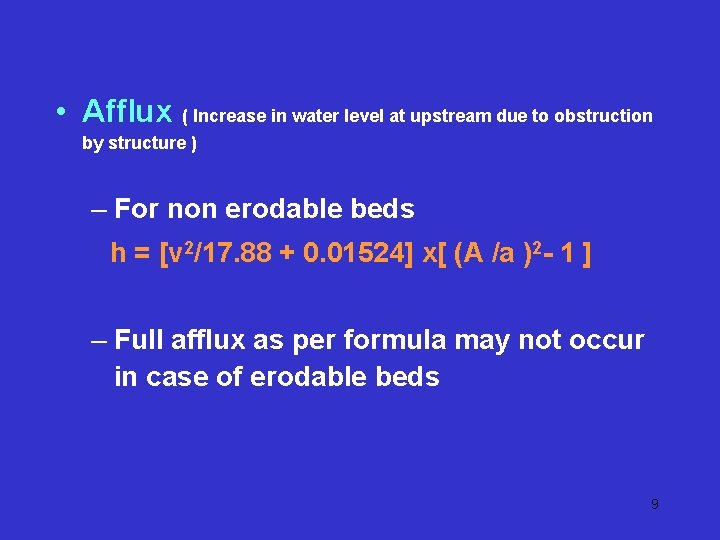
• Afflux ( Increase in water level at upstream due to obstruction by structure ) – For non erodable beds h = [v 2/17. 88 + 0. 01524] x[ (A /a )2 - 1 ] – Full afflux as per formula may not occur in case of erodable beds 9
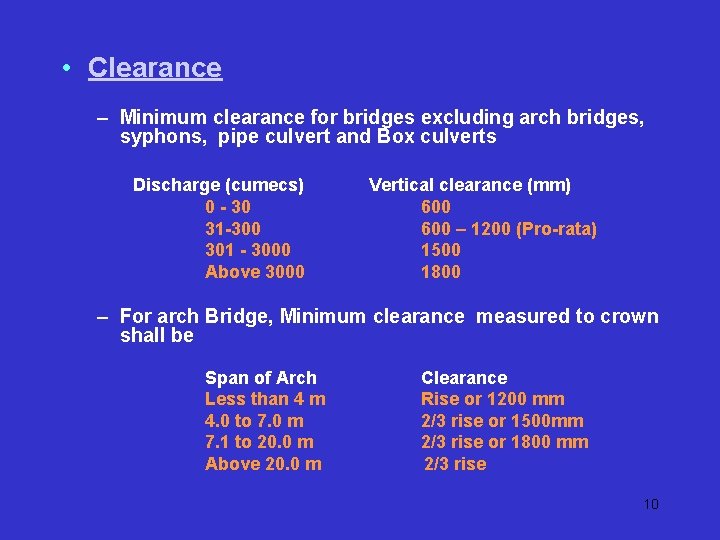
• Clearance – Minimum clearance for bridges excluding arch bridges, syphons, pipe culvert and Box culverts Discharge (cumecs) 0 - 30 31 -300 301 - 3000 Above 3000 Vertical clearance (mm) 600 – 1200 (Pro-rata) 1500 1800 – For arch Bridge, Minimum clearance measured to crown shall be Span of Arch Less than 4 m 4. 0 to 7. 0 m 7. 1 to 20. 0 m Above 20. 0 m Clearance Rise or 1200 mm 2/3 rise or 1500 mm 2/3 rise or 1800 mm 2/3 rise 10
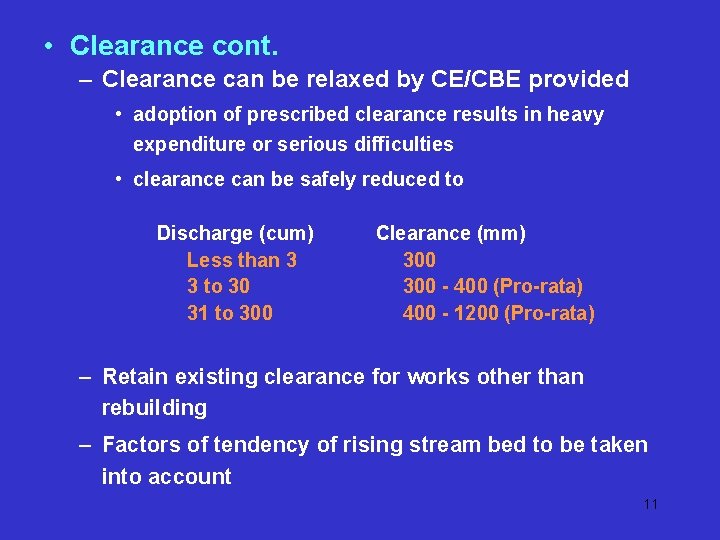
• Clearance cont. – Clearance can be relaxed by CE/CBE provided • adoption of prescribed clearance results in heavy expenditure or serious difficulties • clearance can be safely reduced to Discharge (cum) Less than 3 3 to 30 31 to 300 Clearance (mm) 300 - 400 (Pro-rata) 400 - 1200 (Pro-rata) – Retain existing clearance for works other than rebuilding – Factors of tendency of rising stream bed to be taken into account 11
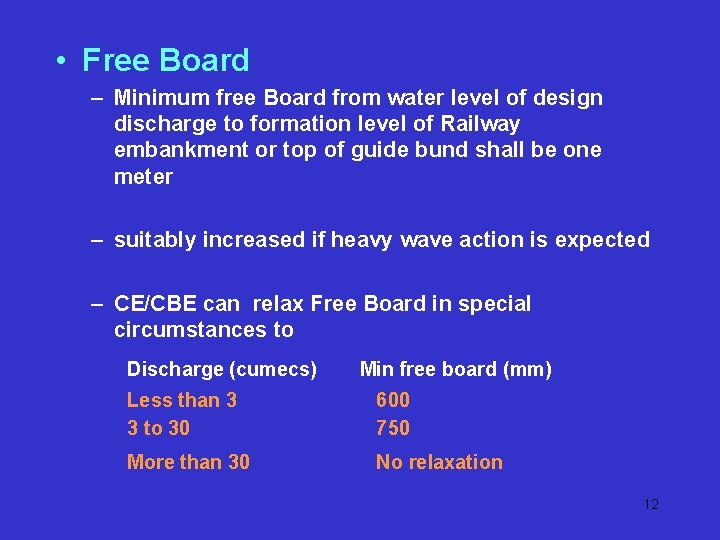
• Free Board – Minimum free Board from water level of design discharge to formation level of Railway embankment or top of guide bund shall be one meter – suitably increased if heavy wave action is expected – CE/CBE can relax Free Board in special circumstances to Discharge (cumecs) Min free board (mm) Less than 3 3 to 30 600 750 More than 30 No relaxation 12
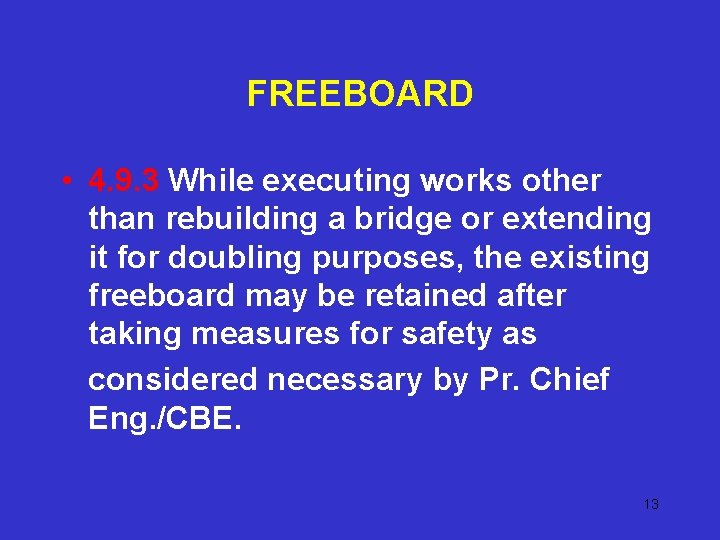
FREEBOARD • 4. 9. 3 While executing works other than rebuilding a bridge or extending it for doubling purposes, the existing freeboard may be retained after taking measures for safety as considered necessary by Pr. Chief Eng. /CBE. 13
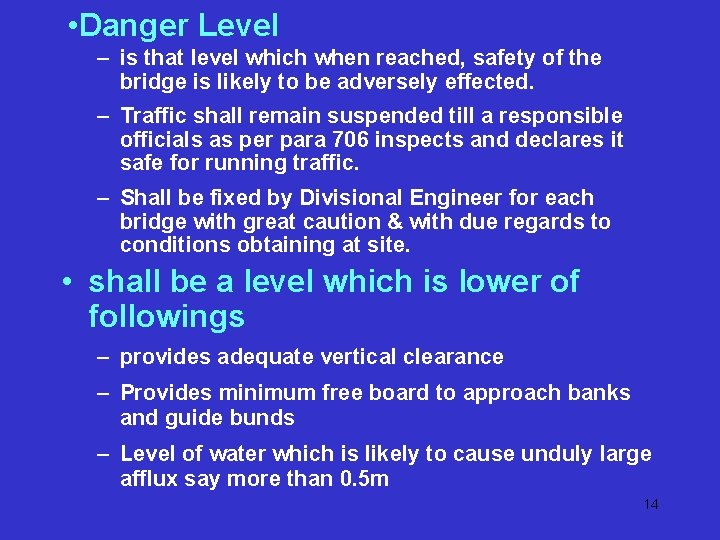
• Danger Level – is that level which when reached, safety of the bridge is likely to be adversely effected. – Traffic shall remain suspended till a responsible officials as per para 706 inspects and declares it safe for running traffic. – Shall be fixed by Divisional Engineer for each bridge with great caution & with due regards to conditions obtaining at site. • shall be a level which is lower of followings – provides adequate vertical clearance – Provides minimum free board to approach banks and guide bunds – Level of water which is likely to cause unduly large afflux say more than 0. 5 m 14
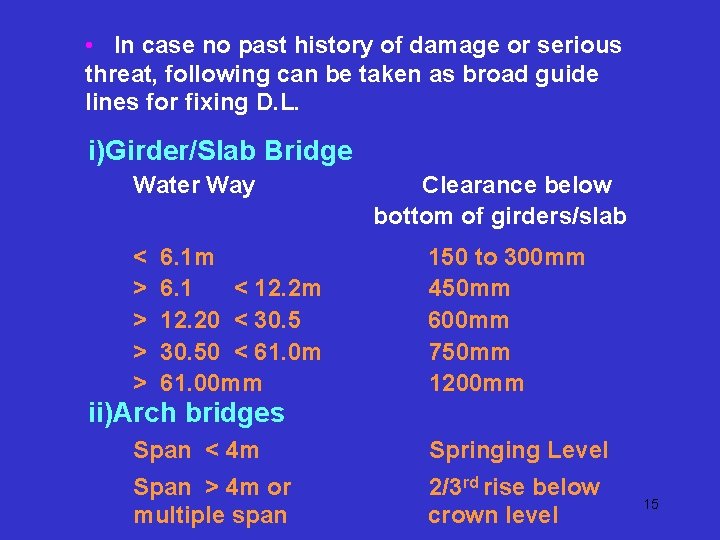
• In case no past history of damage or serious threat, following can be taken as broad guide lines for fixing D. L. i)Girder/Slab Bridge Water Way < > > 6. 1 m 6. 1 < 12. 2 m 12. 20 < 30. 50 < 61. 0 m 61. 00 mm Clearance below bottom of girders/slab 150 to 300 mm 450 mm 600 mm 750 mm 1200 mm ii)Arch bridges Span < 4 m Springing Level Span > 4 m or multiple span 2/3 rd rise below crown level 15
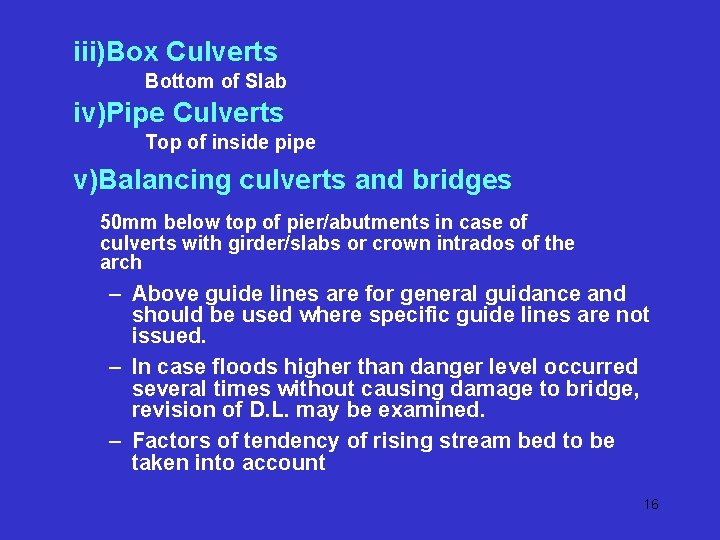
iii)Box Culverts Bottom of Slab iv)Pipe Culverts Top of inside pipe v)Balancing culverts and bridges 50 mm below top of pier/abutments in case of culverts with girder/slabs or crown intrados of the arch – Above guide lines are for general guidance and should be used where specific guide lines are not issued. – In case floods higher than danger level occurred several times without causing damage to bridge, revision of D. L. may be examined. – Factors of tendency of rising stream bed to be taken into account 16
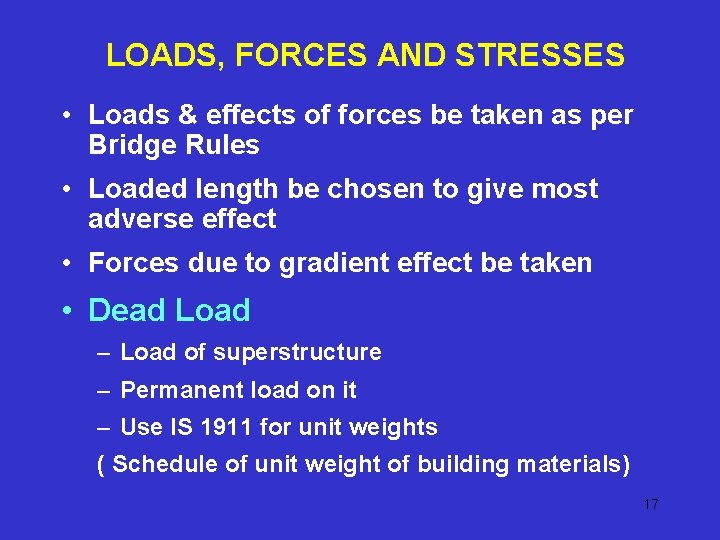
LOADS, FORCES AND STRESSES • Loads & effects of forces be taken as per Bridge Rules • Loaded length be chosen to give most adverse effect • Forces due to gradient effect be taken • Dead Load – Load of superstructure – Permanent load on it – Use IS 1911 for unit weights ( Schedule of unit weight of building materials) 17
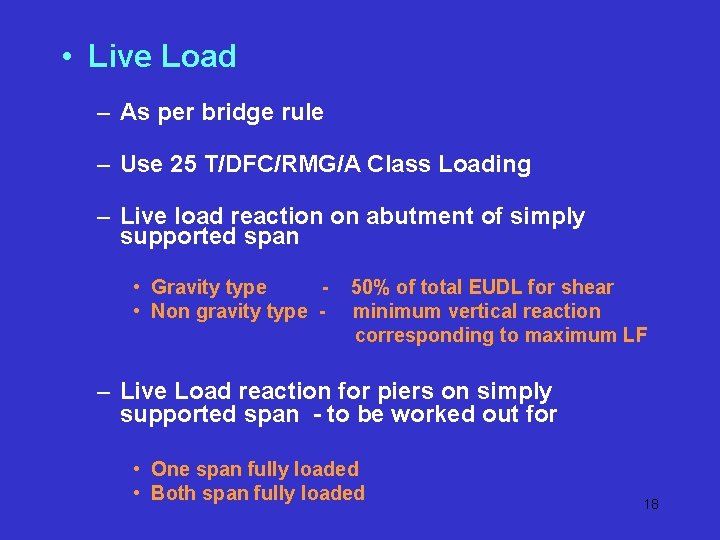
• Live Load – As per bridge rule – Use 25 T/DFC/RMG/A Class Loading – Live load reaction on abutment of simply supported span • Gravity type • Non gravity type - 50% of total EUDL for shear minimum vertical reaction corresponding to maximum LF – Live Load reaction for piers on simply supported span - to be worked out for • One span fully loaded • Both span fully loaded 18
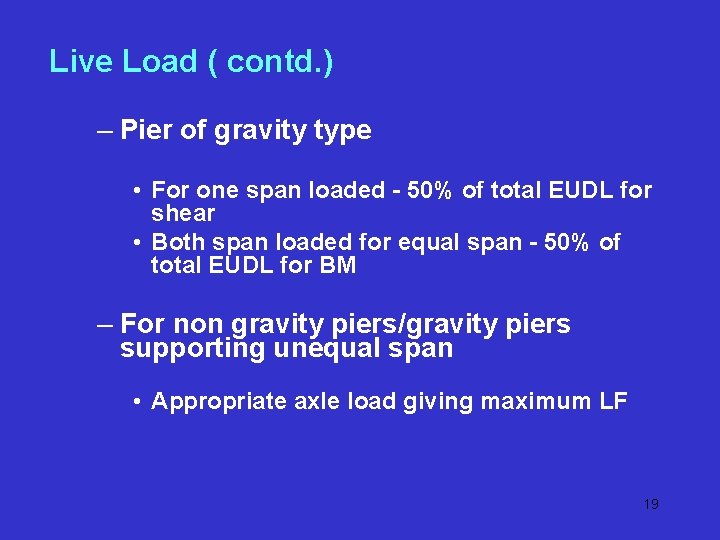
Live Load ( contd. ) – Pier of gravity type • For one span loaded - 50% of total EUDL for shear • Both span loaded for equal span - 50% of total EUDL for BM – For non gravity piers/gravity piers supporting unequal span • Appropriate axle load giving maximum LF 19
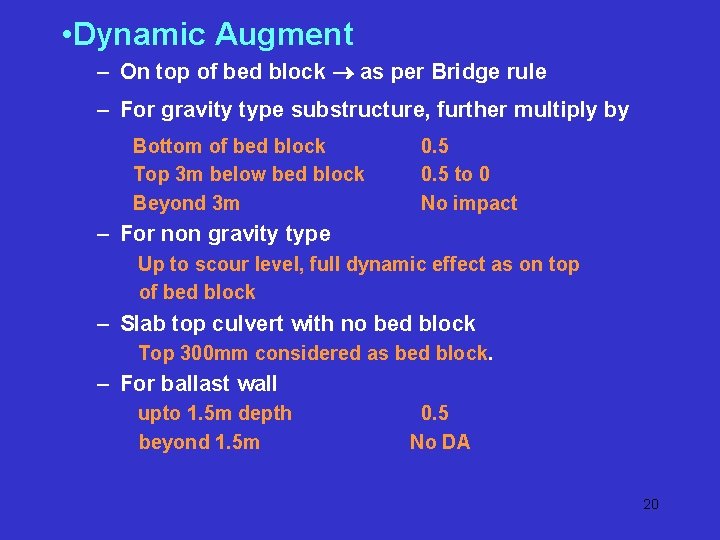
• Dynamic Augment – On top of bed block as per Bridge rule – For gravity type substructure, further multiply by Bottom of bed block Top 3 m below bed block Beyond 3 m 0. 5 to 0 No impact – For non gravity type Up to scour level, full dynamic effect as on top of bed block – Slab top culvert with no bed block Top 300 mm considered as bed block. – For ballast wall upto 1. 5 m depth beyond 1. 5 m 0. 5 No DA 20
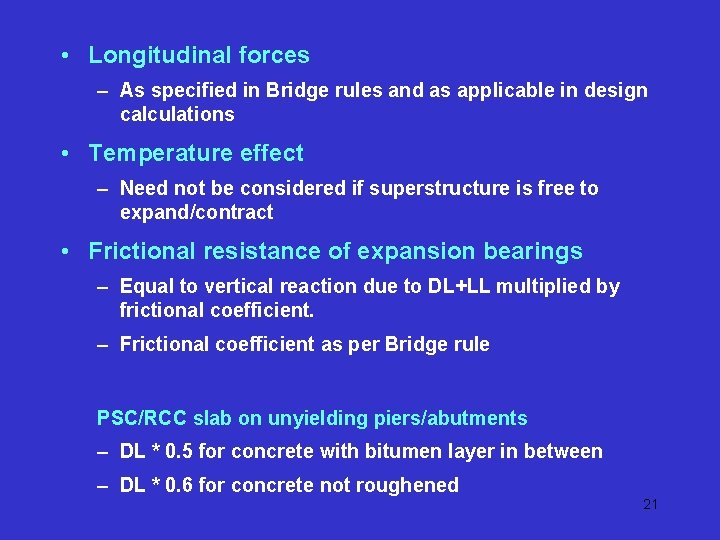
• Longitudinal forces – As specified in Bridge rules and as applicable in design calculations • Temperature effect – Need not be considered if superstructure is free to expand/contract • Frictional resistance of expansion bearings – Equal to vertical reaction due to DL+LL multiplied by frictional coefficient. – Frictional coefficient as per Bridge rule PSC/RCC slab on unyielding piers/abutments – DL * 0. 5 for concrete with bitumen layer in between – DL * 0. 6 for concrete not roughened 21
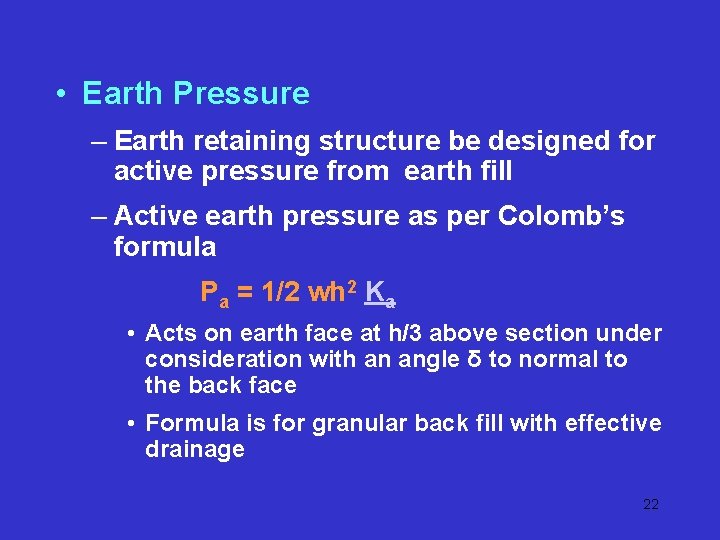
• Earth Pressure – Earth retaining structure be designed for active pressure from earth fill – Active earth pressure as per Colomb’s formula Pa = 1/2 wh 2 Ka • Acts on earth face at h/3 above section under consideration with an angle δ to normal to the back face • Formula is for granular back fill with effective drainage 22
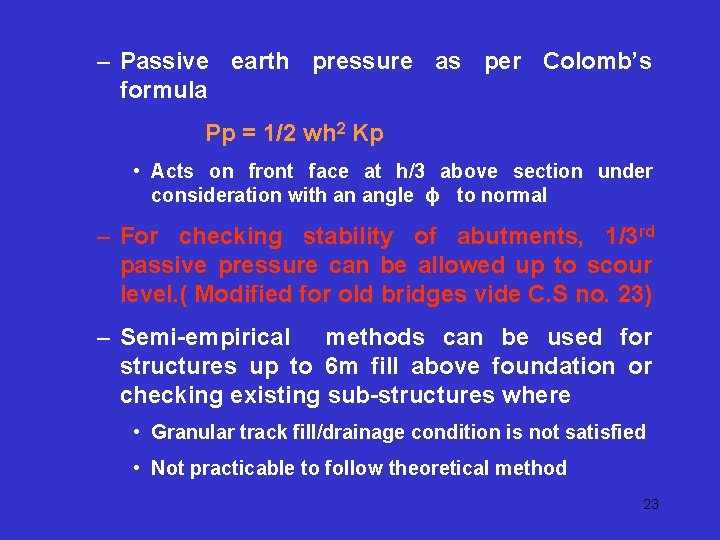
– Passive earth pressure as per Colomb’s formula Pp = 1/2 wh 2 Kp • Acts on front face at h/3 above section under consideration with an angle ϕ to normal – For checking stability of abutments, 1/3 rd passive pressure can be allowed up to scour level. ( Modified for old bridges vide C. S no. 23) – Semi-empirical methods can be used for structures up to 6 m fill above foundation or checking existing sub-structures where • Granular track fill/drainage condition is not satisfied • Not practicable to follow theoretical method 23
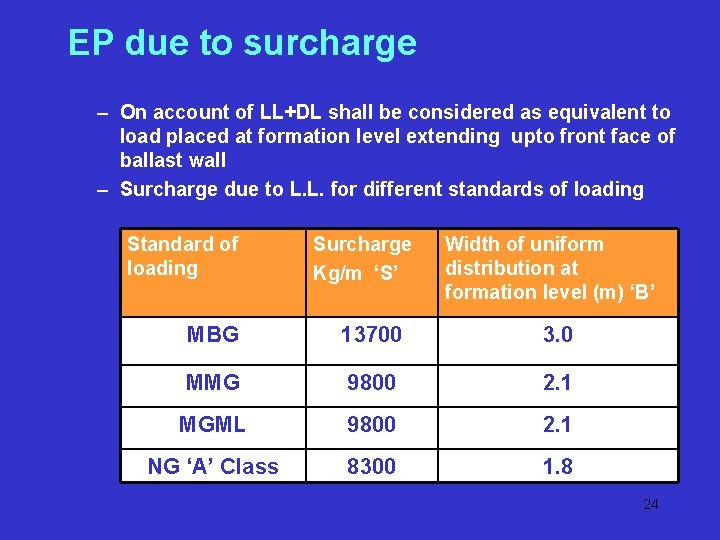
EP due to surcharge – On account of LL+DL shall be considered as equivalent to load placed at formation level extending upto front face of ballast wall – Surcharge due to L. L. for different standards of loading Standard of loading Surcharge Kg/m ‘S’ Width of uniform distribution at formation level (m) ‘B’ MBG 13700 3. 0 MMG 9800 2. 1 MGML 9800 2. 1 NG ‘A’ Class 8300 1. 8 24
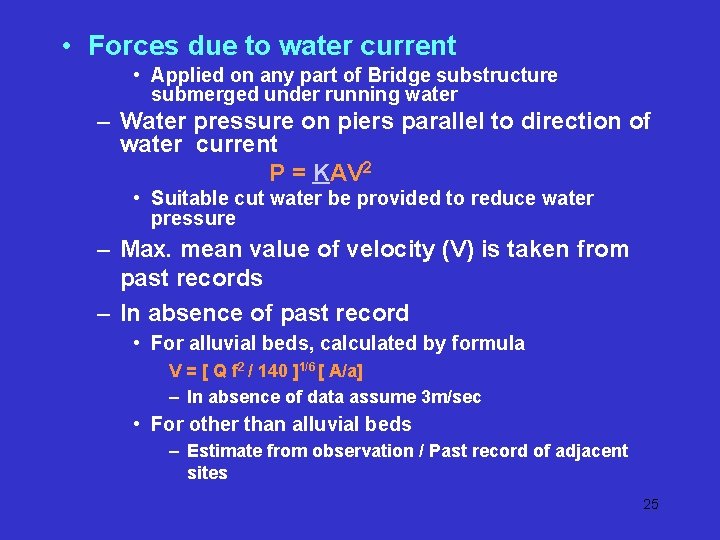
• Forces due to water current • Applied on any part of Bridge substructure submerged under running water – Water pressure on piers parallel to direction of water current P = KAV 2 • Suitable cut water be provided to reduce water pressure – Max. mean value of velocity (V) is taken from past records – In absence of past record • For alluvial beds, calculated by formula V = [ Q f 2 / 140 ]1/6 [ A/a] – In absence of data assume 3 m/sec • For other than alluvial beds – Estimate from observation / Past record of adjacent sites 25
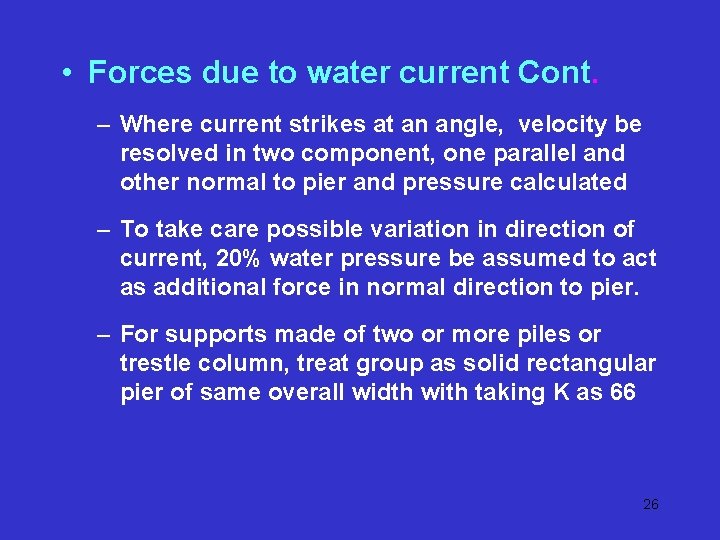
• Forces due to water current Cont. – Where current strikes at an angle, velocity be resolved in two component, one parallel and other normal to pier and pressure calculated – To take care possible variation in direction of current, 20% water pressure be assumed to act as additional force in normal direction to pier. – For supports made of two or more piles or trestle column, treat group as solid rectangular pier of same overall width with taking K as 66 26
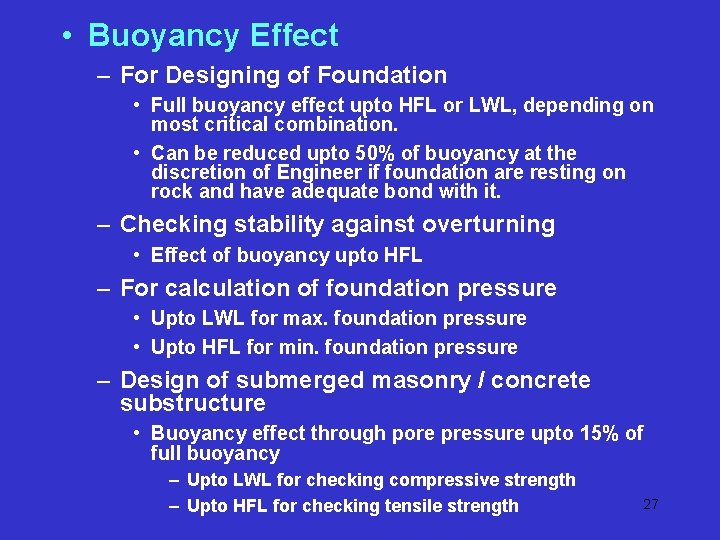
• Buoyancy Effect – For Designing of Foundation • Full buoyancy effect upto HFL or LWL, depending on most critical combination. • Can be reduced upto 50% of buoyancy at the discretion of Engineer if foundation are resting on rock and have adequate bond with it. – Checking stability against overturning • Effect of buoyancy upto HFL – For calculation of foundation pressure • Upto LWL for max. foundation pressure • Upto HFL for min. foundation pressure – Design of submerged masonry / concrete substructure • Buoyancy effect through pore pressure upto 15% of full buoyancy – Upto LWL for checking compressive strength – Upto HFL for checking tensile strength 27
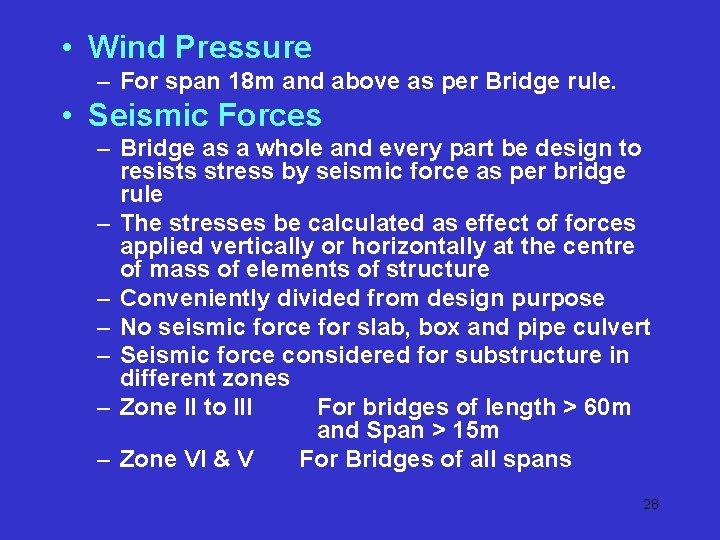
• Wind Pressure – For span 18 m and above as per Bridge rule. • Seismic Forces – Bridge as a whole and every part be design to resists stress by seismic force as per bridge rule – The stresses be calculated as effect of forces applied vertically or horizontally at the centre of mass of elements of structure – Conveniently divided from design purpose – No seismic force for slab, box and pipe culvert – Seismic force considered for substructure in different zones – Zone II to III For bridges of length > 60 m and Span > 15 m – Zone VI & V For Bridges of all spans 28
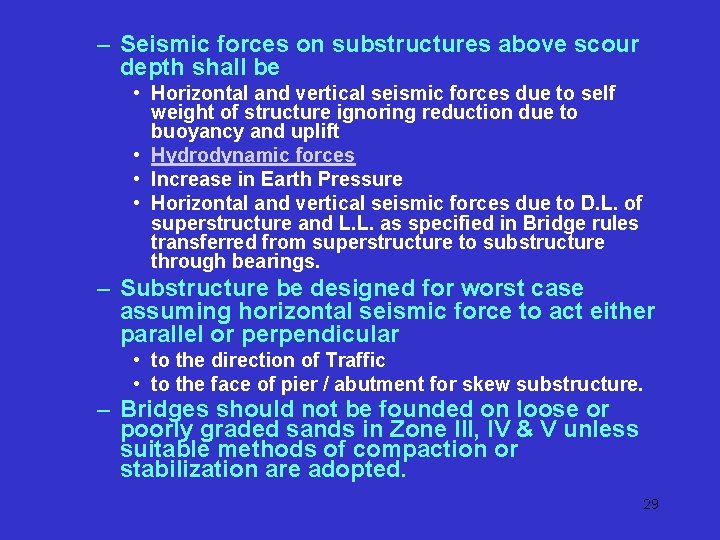
– Seismic forces on substructures above scour depth shall be • Horizontal and vertical seismic forces due to self weight of structure ignoring reduction due to buoyancy and uplift • Hydrodynamic forces • Increase in Earth Pressure • Horizontal and vertical seismic forces due to D. L. of superstructure and L. L. as specified in Bridge rules transferred from superstructure to substructure through bearings. – Substructure be designed for worst case assuming horizontal seismic force to act either parallel or perpendicular • to the direction of Traffic • to the face of pier / abutment for skew substructure. – Bridges should not be founded on loose or poorly graded sands in Zone III, IV & V unless suitable methods of compaction or stabilization are adopted. 29
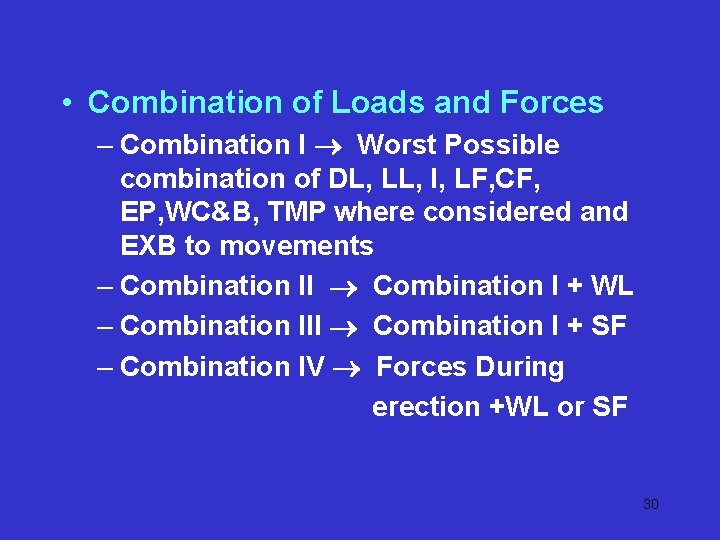
• Combination of Loads and Forces – Combination I Worst Possible combination of DL, LL, I, LF, CF, EP, WC&B, TMP where considered and EXB to movements – Combination II Combination I + WL – Combination III Combination I + SF – Combination IV Forces During erection +WL or SF 30
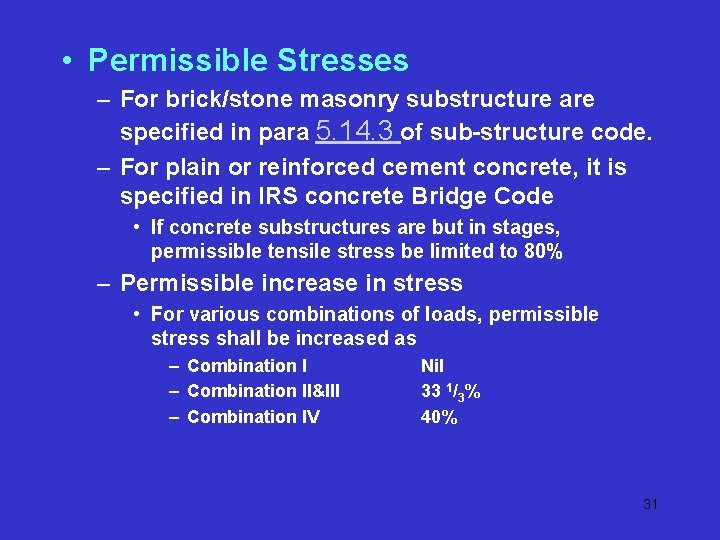
• Permissible Stresses – For brick/stone masonry substructure are specified in para 5. 14. 3 of sub-structure code. – For plain or reinforced cement concrete, it is specified in IRS concrete Bridge Code • If concrete substructures are but in stages, permissible tensile stress be limited to 80% – Permissible increase in stress • For various combinations of loads, permissible stress shall be increased as – Combination II&III – Combination IV Nil 33 1/3% 40% 31
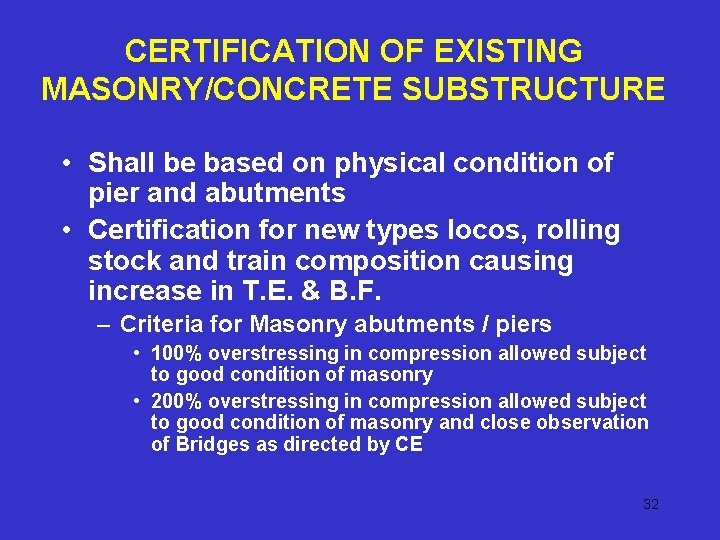
CERTIFICATION OF EXISTING MASONRY/CONCRETE SUBSTRUCTURE • Shall be based on physical condition of pier and abutments • Certification for new types locos, rolling stock and train composition causing increase in T. E. & B. F. – Criteria for Masonry abutments / piers • 100% overstressing in compression allowed subject to good condition of masonry • 200% overstressing in compression allowed subject to good condition of masonry and close observation of Bridges as directed by CE 32
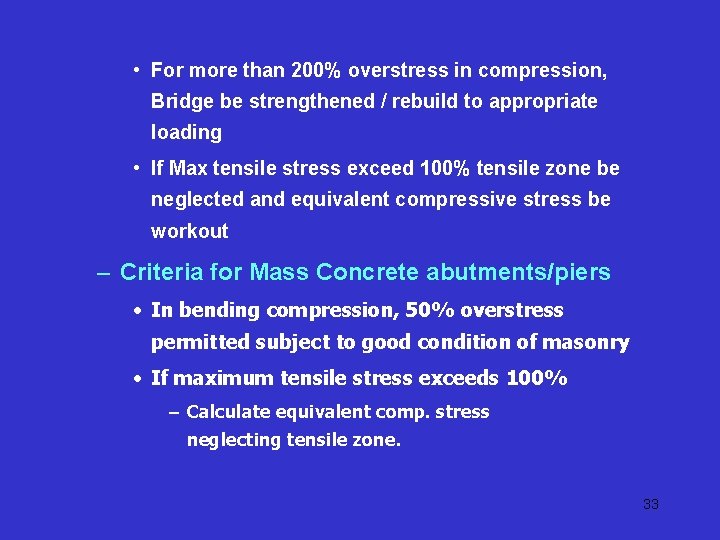
• For more than 200% overstress in compression, Bridge be strengthened / rebuild to appropriate loading • If Max tensile stress exceed 100% tensile zone be neglected and equivalent compressive stress be workout – Criteria for Mass Concrete abutments/piers • In bending compression, 50% overstress permitted subject to good condition of masonry • If maximum tensile stress exceeds 100% – Calculate equivalent comp. stress neglecting tensile zone. 33
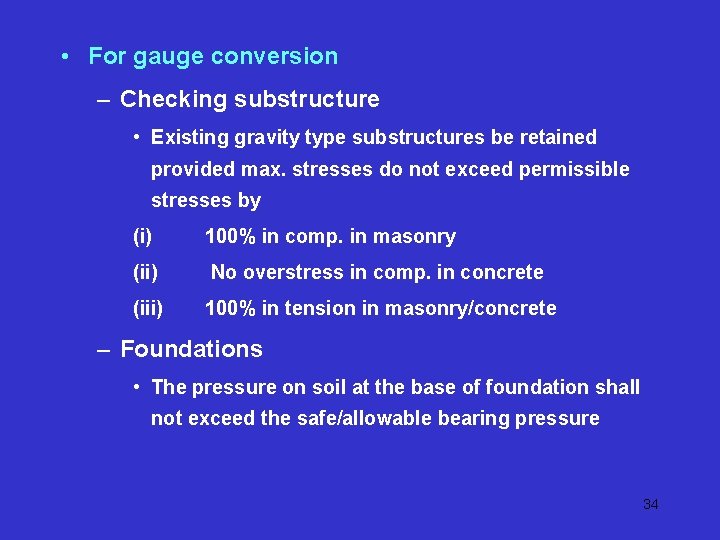
• For gauge conversion – Checking substructure • Existing gravity type substructures be retained provided max. stresses do not exceed permissible stresses by (i) 100% in comp. in masonry (ii) No overstress in comp. in concrete (iii) 100% in tension in masonry/concrete – Foundations • The pressure on soil at the base of foundation shall not exceed the safe/allowable bearing pressure 34
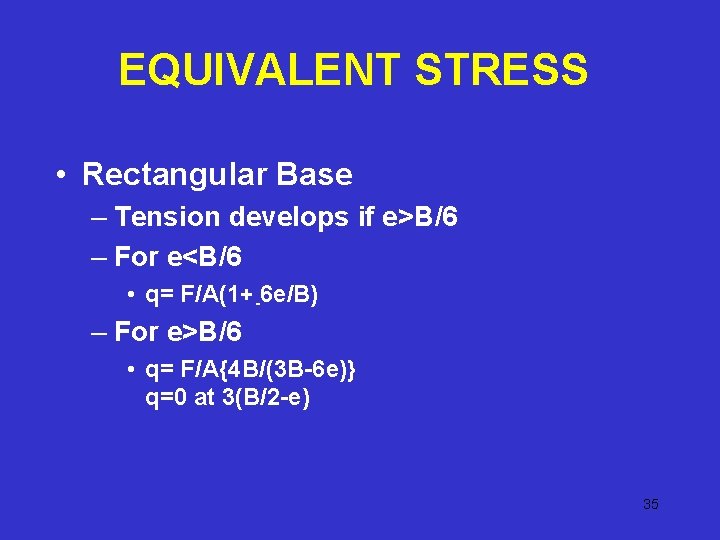
EQUIVALENT STRESS • Rectangular Base – Tension develops if e>B/6 – For e<B/6 • q= F/A(1+-6 e/B) – For e>B/6 • q= F/A{4 B/(3 B-6 e)} q=0 at 3(B/2 -e) 35
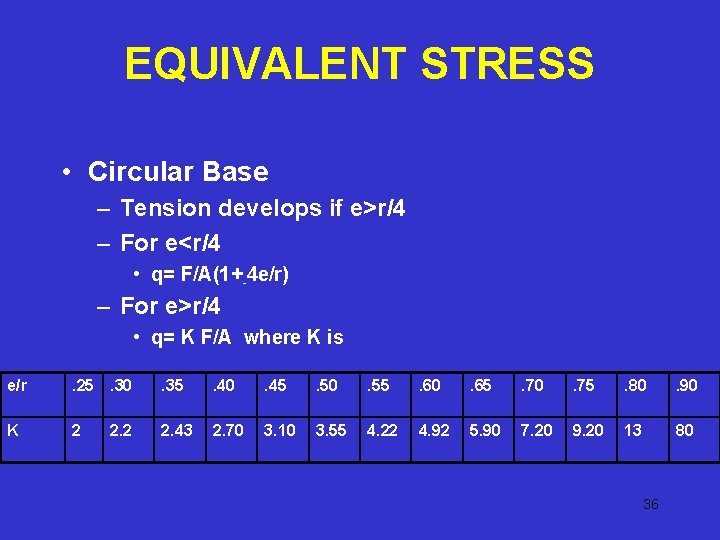
EQUIVALENT STRESS • Circular Base – Tension develops if e>r/4 – For e<r/4 • q= F/A(1+-4 e/r) – For e>r/4 • q= K F/A where K is e/r . 25. 30 . 35 . 40 . 45 . 50 . 55 . 60 . 65 . 70 . 75 . 80 . 90 K 2 2. 43 2. 70 3. 10 3. 55 4. 22 4. 92 5. 90 7. 20 9. 20 13 80 2. 2 36
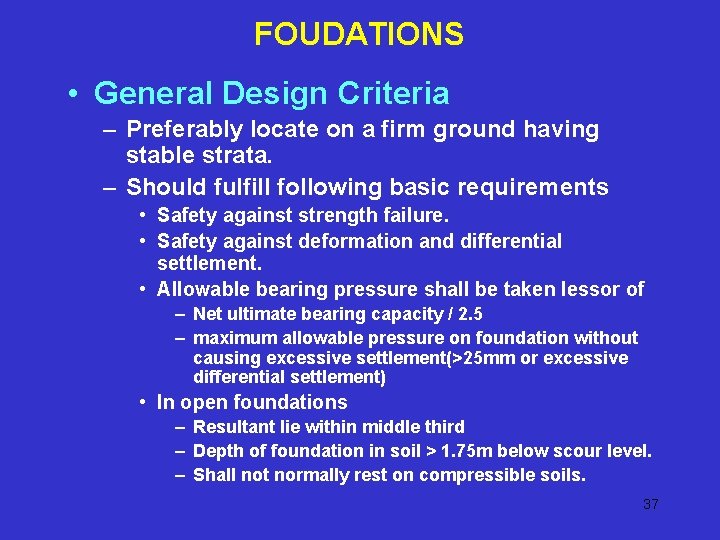
FOUDATIONS • General Design Criteria – Preferably locate on a firm ground having stable strata. – Should fulfill following basic requirements • Safety against strength failure. • Safety against deformation and differential settlement. • Allowable bearing pressure shall be taken lessor of – Net ultimate bearing capacity / 2. 5 – maximum allowable pressure on foundation without causing excessive settlement(>25 mm or excessive differential settlement) • In open foundations – Resultant lie within middle third – Depth of foundation in soil > 1. 75 m below scour level. – Shall not normally rest on compressible soils. 37
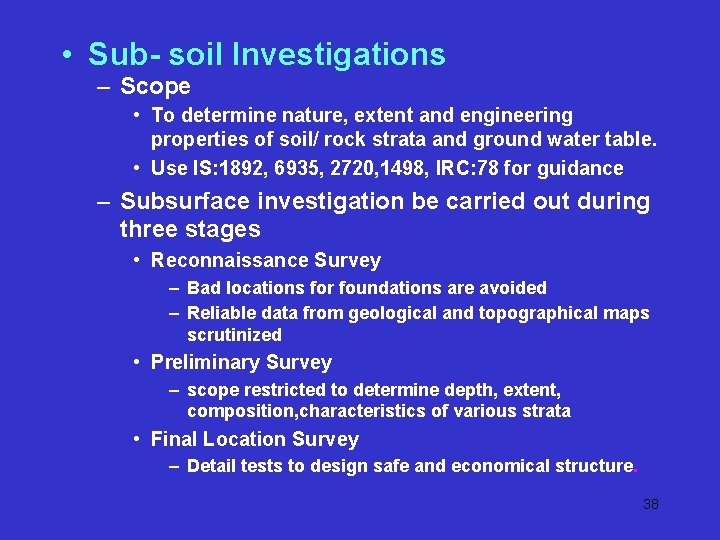
• Sub- soil Investigations – Scope • To determine nature, extent and engineering properties of soil/ rock strata and ground water table. • Use IS: 1892, 6935, 2720, 1498, IRC: 78 for guidance – Subsurface investigation be carried out during three stages • Reconnaissance Survey – Bad locations for foundations are avoided – Reliable data from geological and topographical maps scrutinized • Preliminary Survey – scope restricted to determine depth, extent, composition, characteristics of various strata • Final Location Survey – Detail tests to design safe and economical structure. 38
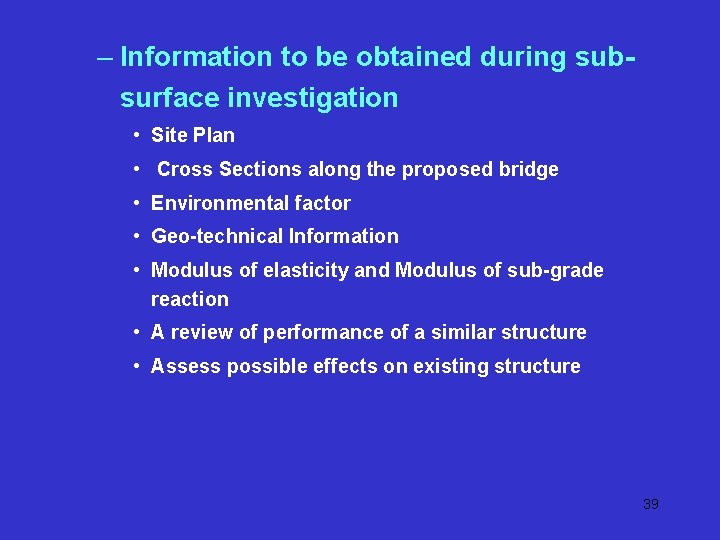
– Information to be obtained during subsurface investigation • Site Plan • Cross Sections along the proposed bridge • Environmental factor • Geo-technical Information • Modulus of elasticity and Modulus of sub-grade reaction • A review of performance of a similar structure • Assess possible effects on existing structure 39
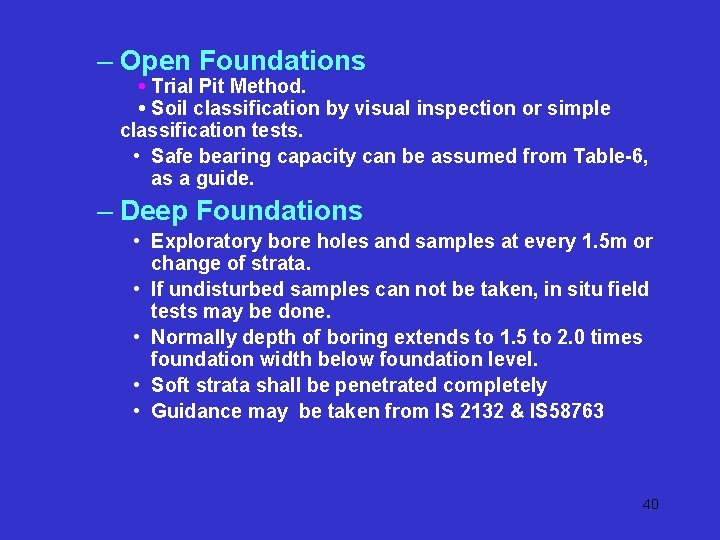
– Open Foundations • Trial Pit Method. • Soil classification by visual inspection or simple classification tests. • Safe bearing capacity can be assumed from Table-6, as a guide. – Deep Foundations • Exploratory bore holes and samples at every 1. 5 m or change of strata. • If undisturbed samples can not be taken, in situ field tests may be done. • Normally depth of boring extends to 1. 5 to 2. 0 times foundation width below foundation level. • Soft strata shall be penetrated completely • Guidance may be taken from IS 2132 & IS 58763 40
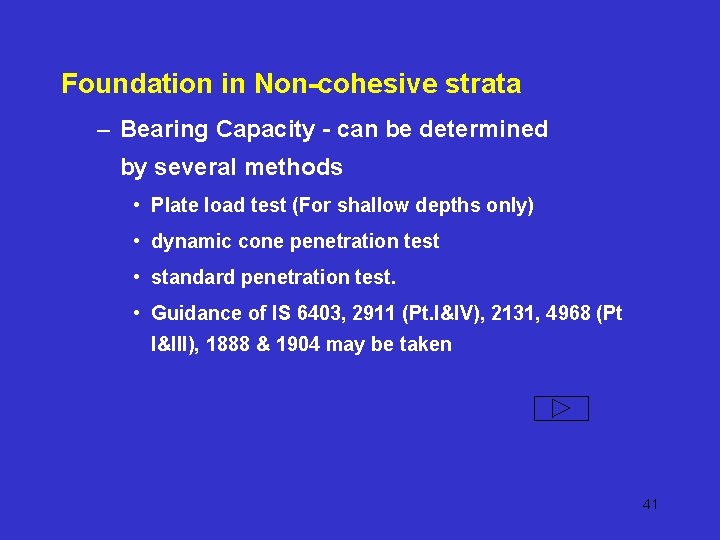
Foundation in Non-cohesive strata – Bearing Capacity - can be determined by several methods • Plate load test (For shallow depths only) • dynamic cone penetration test • standard penetration test. • Guidance of IS 6403, 2911 (Pt. I&IV), 2131, 4968 (Pt I&III), 1888 & 1904 may be taken 41
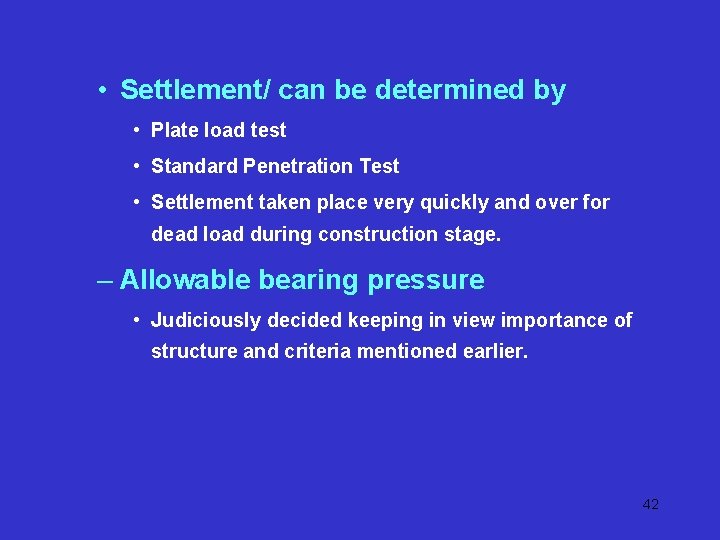
• Settlement/ can be determined by • Plate load test • Standard Penetration Test • Settlement taken place very quickly and over for dead load during construction stage. – Allowable bearing pressure • Judiciously decided keeping in view importance of structure and criteria mentioned earlier. 42
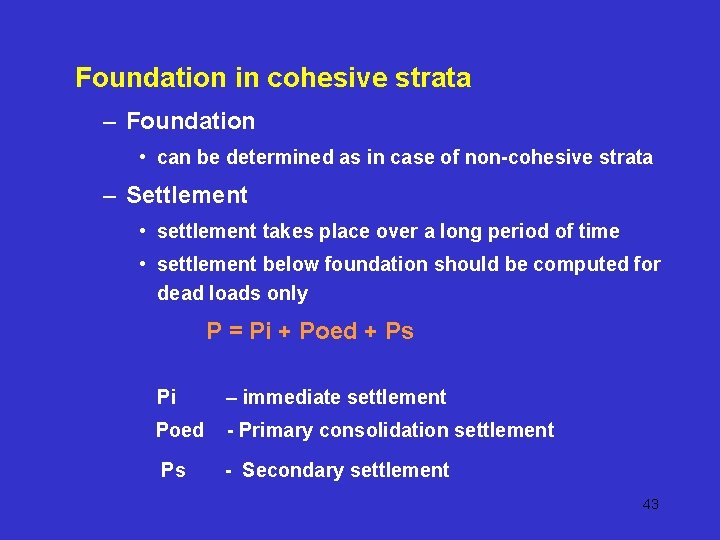
Foundation in cohesive strata – Foundation • can be determined as in case of non-cohesive strata – Settlement • settlement takes place over a long period of time • settlement below foundation should be computed for dead loads only P = Pi + Poed + Ps Pi – immediate settlement Poed - Primary consolidation settlement Ps - Secondary settlement 43
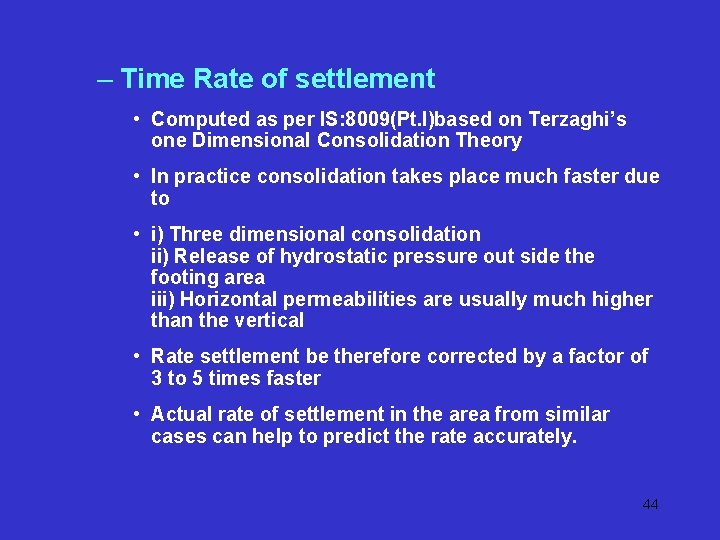
– Time Rate of settlement • Computed as per IS: 8009(Pt. I)based on Terzaghi’s one Dimensional Consolidation Theory • In practice consolidation takes place much faster due to • i) Three dimensional consolidation ii) Release of hydrostatic pressure out side the footing area iii) Horizontal permeabilities are usually much higher than the vertical • Rate settlement be therefore corrected by a factor of 3 to 5 times faster • Actual rate of settlement in the area from similar cases can help to predict the rate accurately. 44
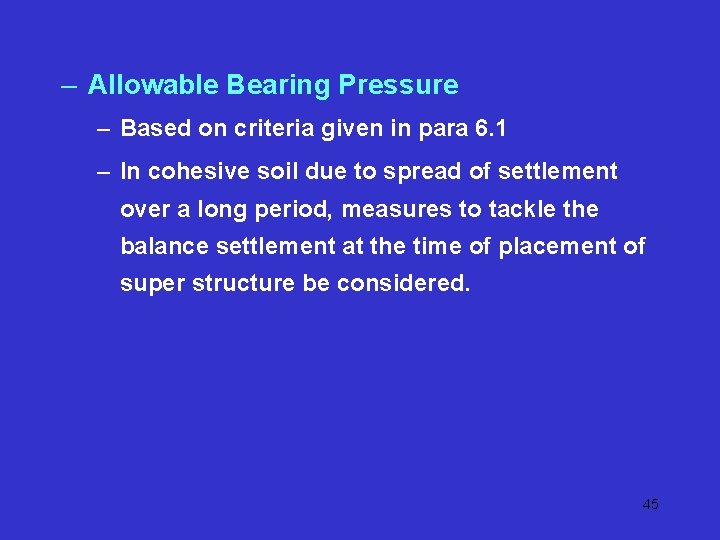
– Allowable Bearing Pressure – Based on criteria given in para 6. 1 – In cohesive soil due to spread of settlement over a long period, measures to tackle the balance settlement at the time of placement of super structure be considered. 45
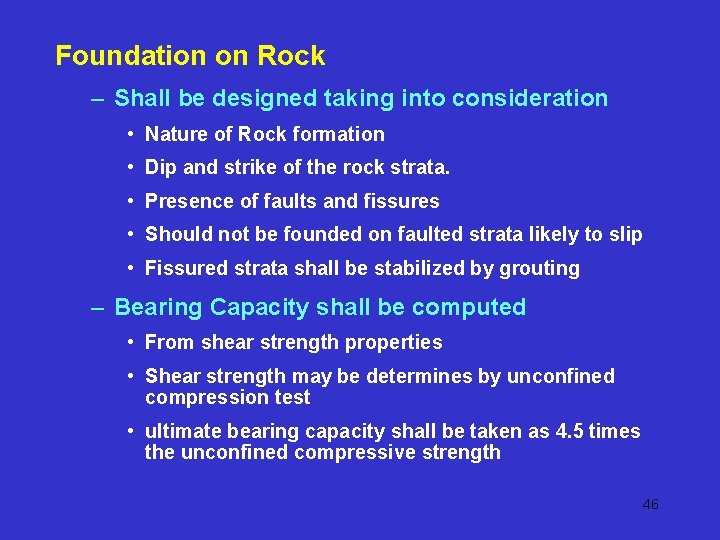
Foundation on Rock – Shall be designed taking into consideration • Nature of Rock formation • Dip and strike of the rock strata. • Presence of faults and fissures • Should not be founded on faulted strata likely to slip • Fissured strata shall be stabilized by grouting – Bearing Capacity shall be computed • From shear strength properties • Shear strength may be determines by unconfined compression test • ultimate bearing capacity shall be taken as 4. 5 times the unconfined compressive strength 46
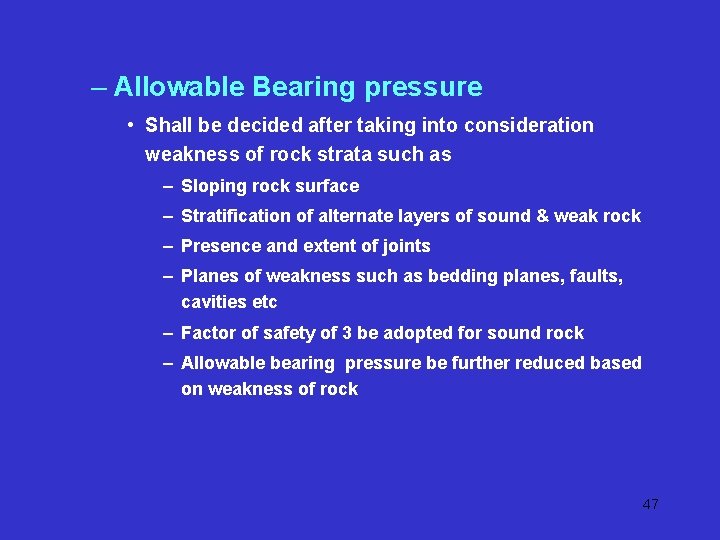
– Allowable Bearing pressure • Shall be decided after taking into consideration weakness of rock strata such as – Sloping rock surface – Stratification of alternate layers of sound & weak rock – Presence and extent of joints – Planes of weakness such as bedding planes, faults, cavities etc – Factor of safety of 3 be adopted for sound rock – Allowable bearing pressure be further reduced based on weakness of rock 47
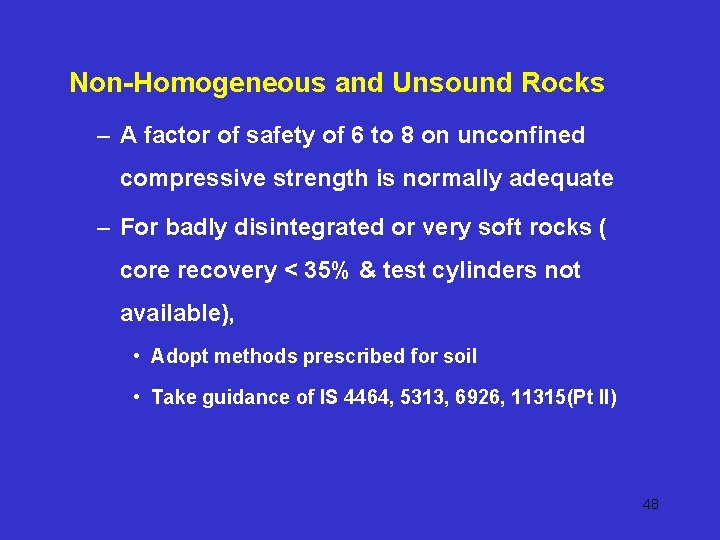
Non-Homogeneous and Unsound Rocks – A factor of safety of 6 to 8 on unconfined compressive strength is normally adequate – For badly disintegrated or very soft rocks ( core recovery < 35% & test cylinders not available), • Adopt methods prescribed for soil • Take guidance of IS 4464, 5313, 6926, 11315(Pt II) 48
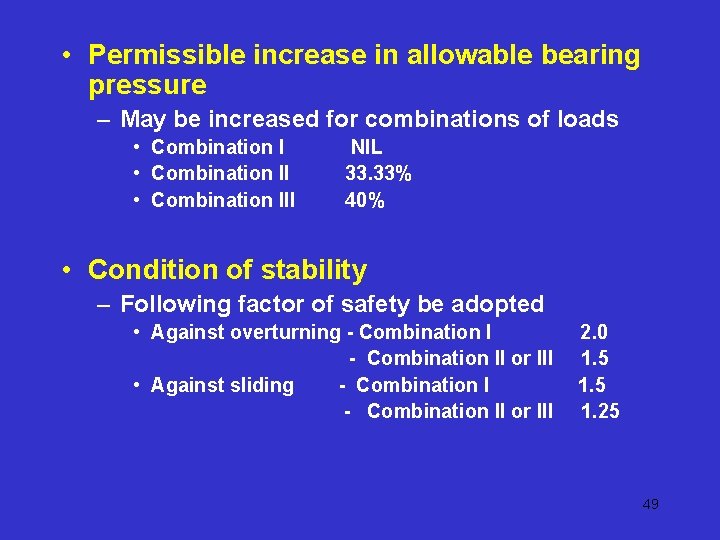
• Permissible increase in allowable bearing pressure – May be increased for combinations of loads • Combination III NIL 33. 33% 40% • Condition of stability – Following factor of safety be adopted • Against overturning - Combination II or III • Against sliding - Combination II or III 2. 0 1. 5 1. 25 49
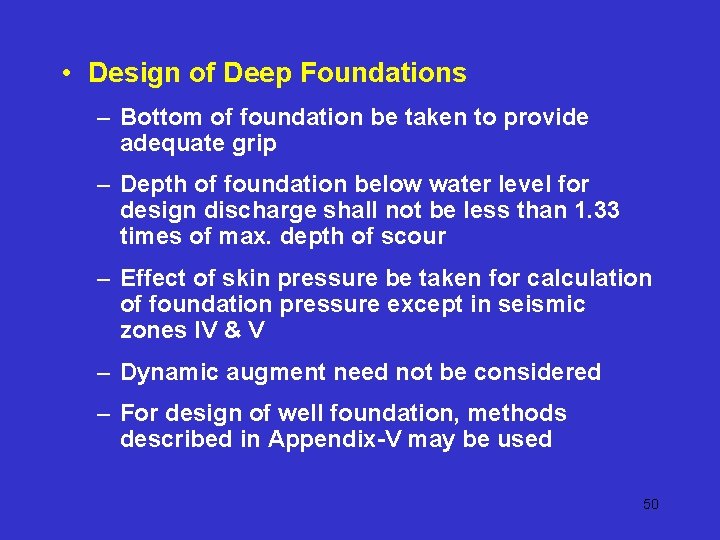
• Design of Deep Foundations – Bottom of foundation be taken to provide adequate grip – Depth of foundation below water level for design discharge shall not be less than 1. 33 times of max. depth of scour – Effect of skin pressure be taken for calculation of foundation pressure except in seismic zones IV & V – Dynamic augment need not be considered – For design of well foundation, methods described in Appendix-V may be used 50
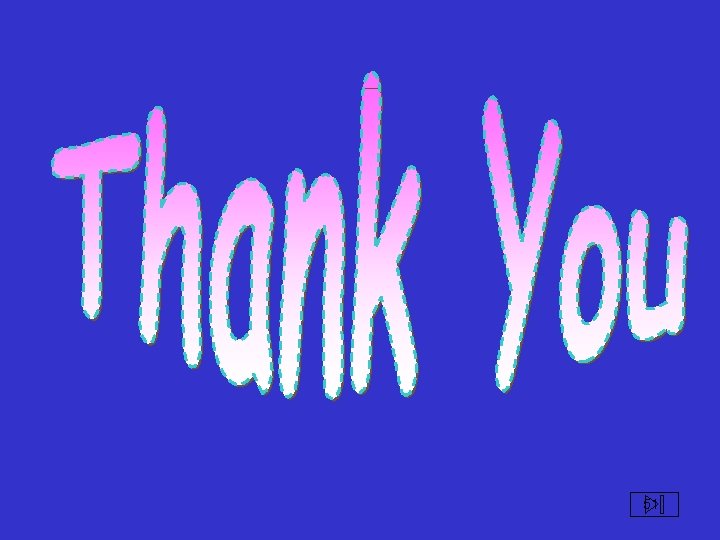
51
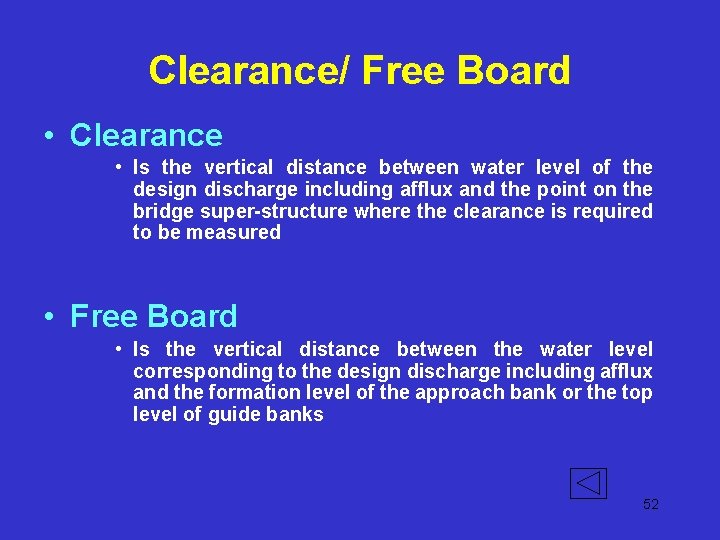
Clearance/ Free Board • Clearance • Is the vertical distance between water level of the design discharge including afflux and the point on the bridge super-structure where the clearance is required to be measured • Free Board • Is the vertical distance between the water level corresponding to the design discharge including afflux and the formation level of the approach bank or the top level of guide banks 52
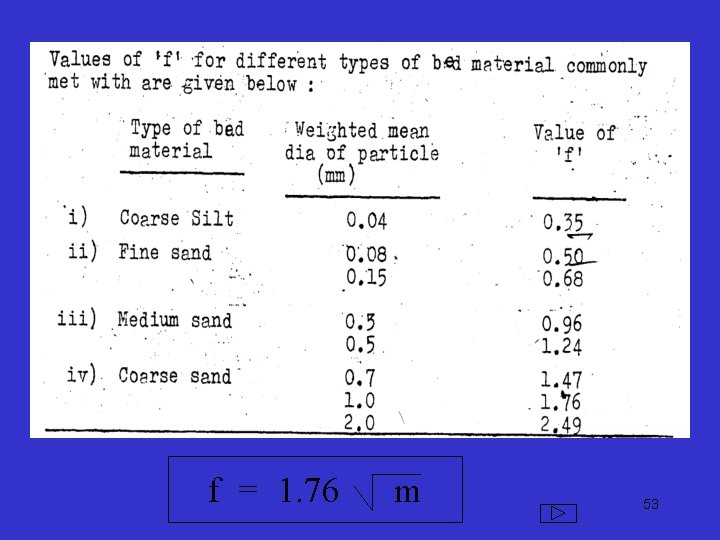
f = 1. 76 m 53
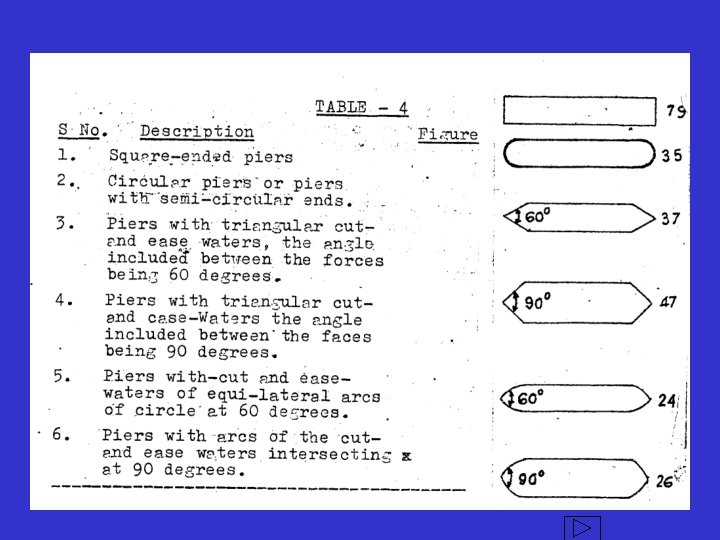
54
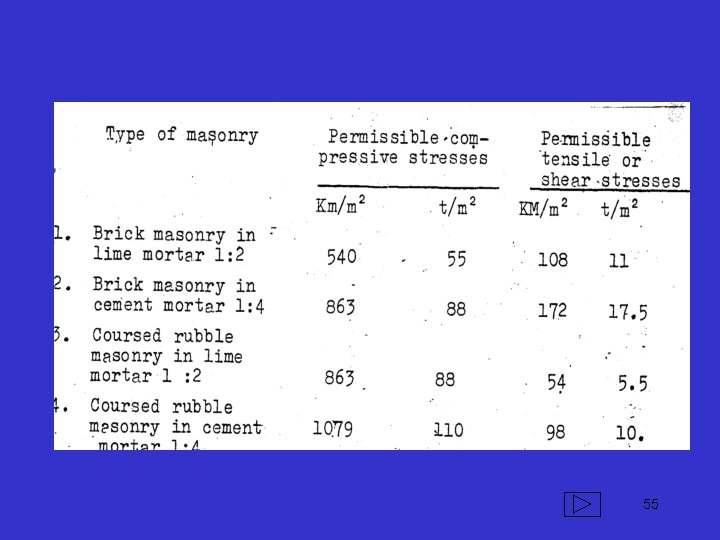
55
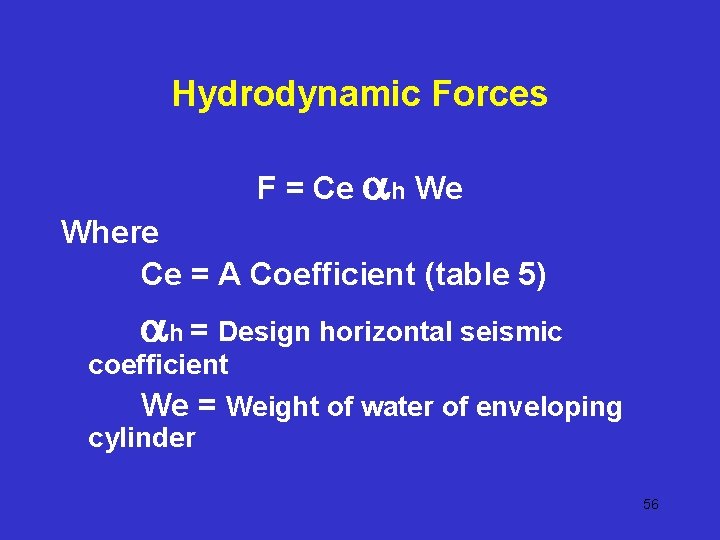
Hydrodynamic Forces F = Ce h We Where Ce = A Coefficient (table 5) h = Design horizontal seismic coefficient We = Weight of water of enveloping cylinder 56
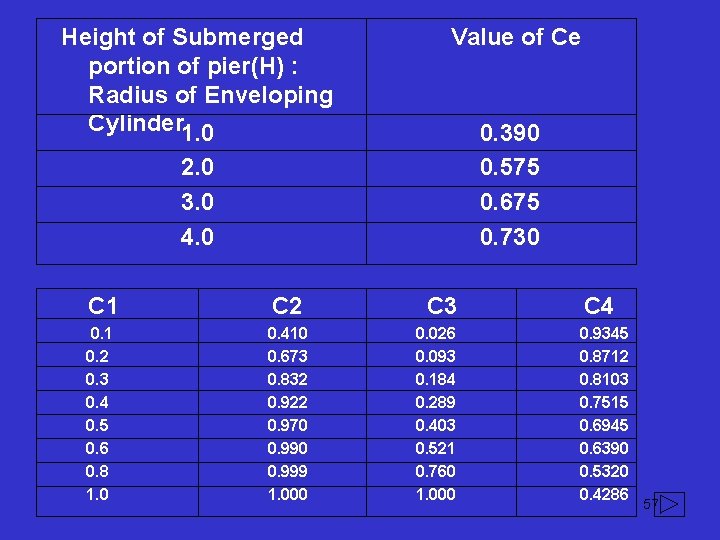
Height of Submerged portion of pier(H) : Radius of Enveloping Cylinder 1. 0 Value of Ce 0. 390 0. 575 0. 675 0. 730 2. 0 3. 0 4. 0 C 1 C 2 0. 1 0. 2 0. 3 0. 4 0. 5 0. 6 0. 8 1. 0 0. 410 0. 673 0. 832 0. 922 0. 970 0. 999 1. 000 C 3 0. 026 0. 093 0. 184 0. 289 0. 403 0. 521 0. 760 1. 000 C 4 0. 9345 0. 8712 0. 8103 0. 7515 0. 6945 0. 6390 0. 5320 0. 4286 57
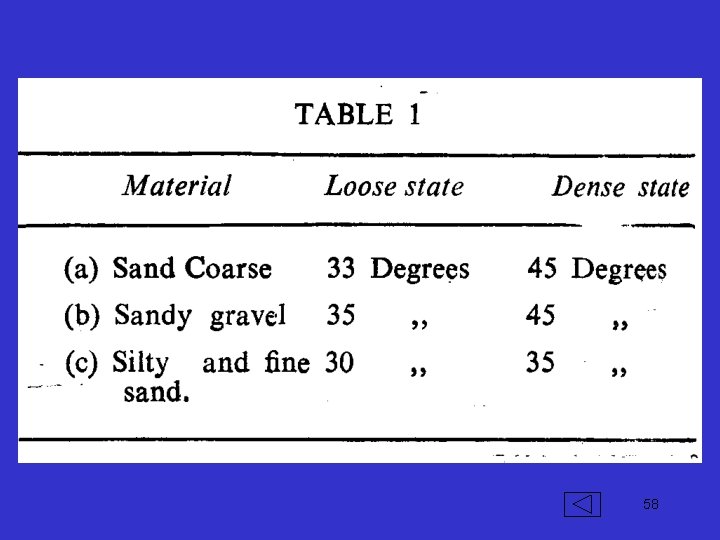
58
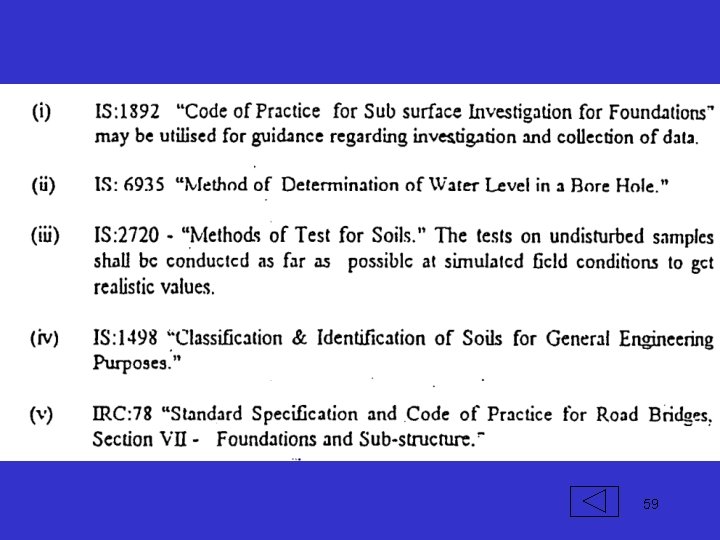
59
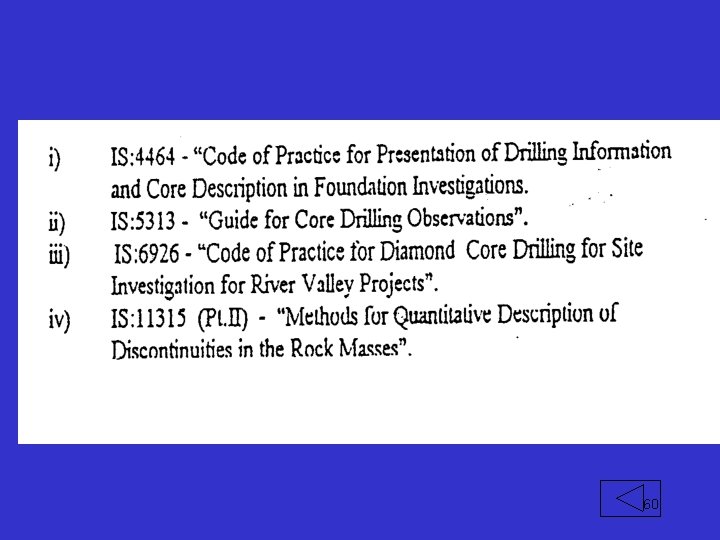
60
- Slides: 60