Sub45 nm CD Uniformity in Semiconductor Manufacture Terrence
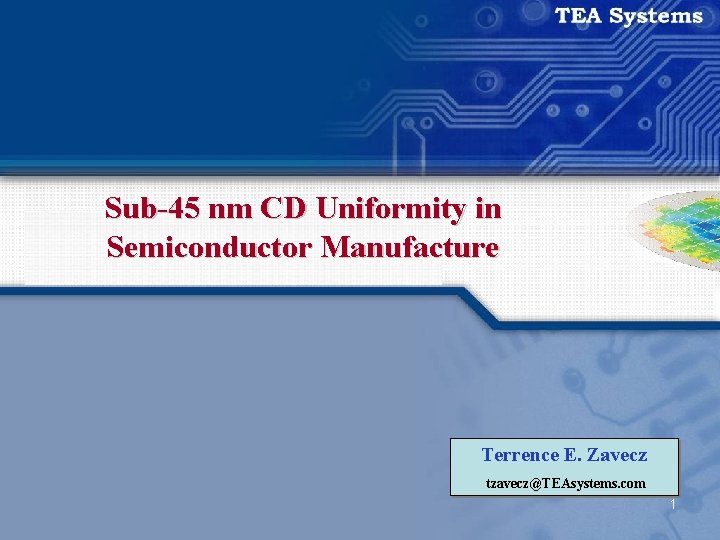
Sub-45 nm CD Uniformity in Semiconductor Manufacture Terrence E. Zavecz tzavecz@TEAsystems. com 1
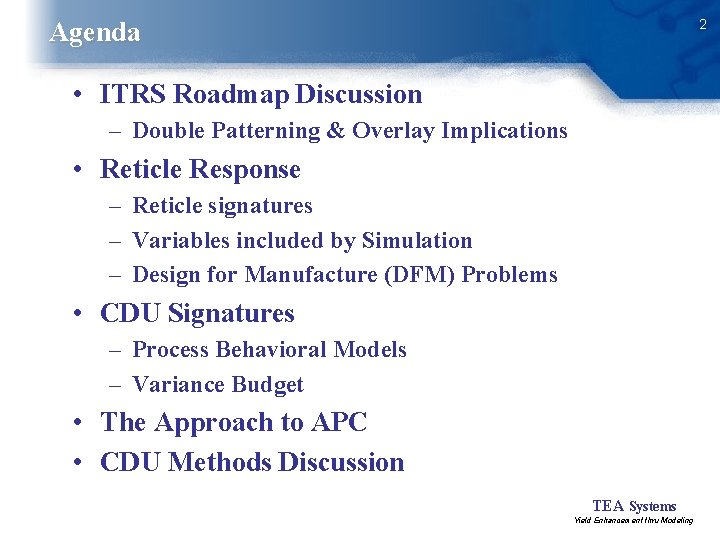
2 Agenda • ITRS Roadmap Discussion – Double Patterning & Overlay Implications • Reticle Response – Reticle signatures – Variables included by Simulation – Design for Manufacture (DFM) Problems • CDU Signatures – Process Behavioral Models – Variance Budget • The Approach to APC • CDU Methods Discussion TEA Systems Yield Enhancement thru Modeling
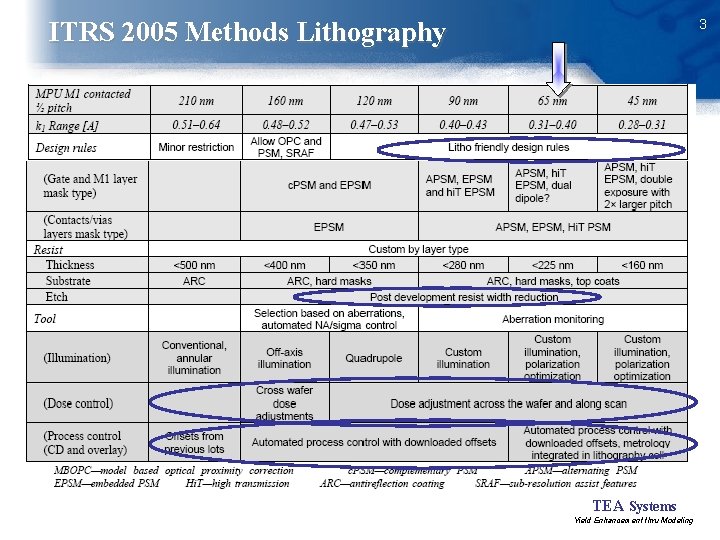
3 ITRS 2005 Methods Lithography TEA Systems Yield Enhancement thru Modeling

4 Technology Requirements EUV Problem: Lens materials TEA Systems Yield Enhancement thru Modeling
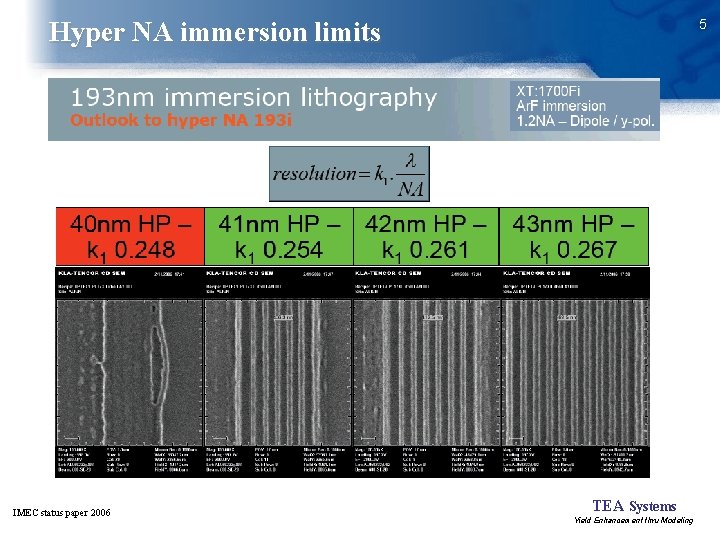
5 Hyper NA immersion limits IMEC status paper 2006 TEA Systems Yield Enhancement thru Modeling
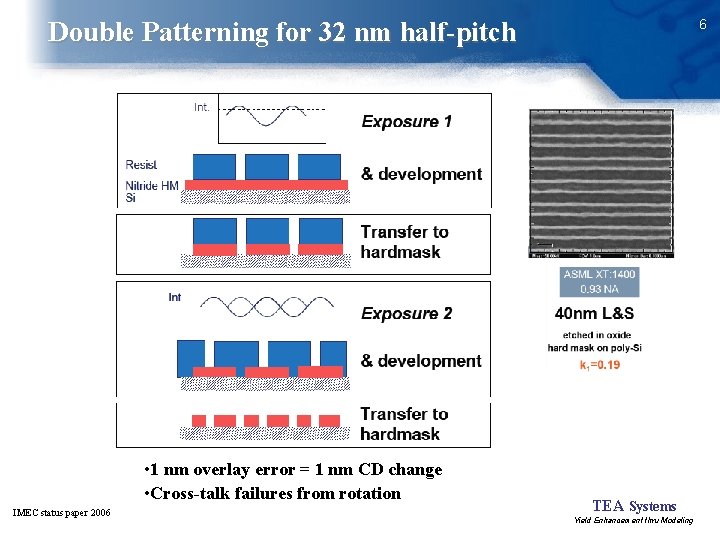
6 Double Patterning for 32 nm half-pitch • 1 nm overlay error = 1 nm CD change • Cross-talk failures from rotation IMEC status paper 2006 TEA Systems Yield Enhancement thru Modeling
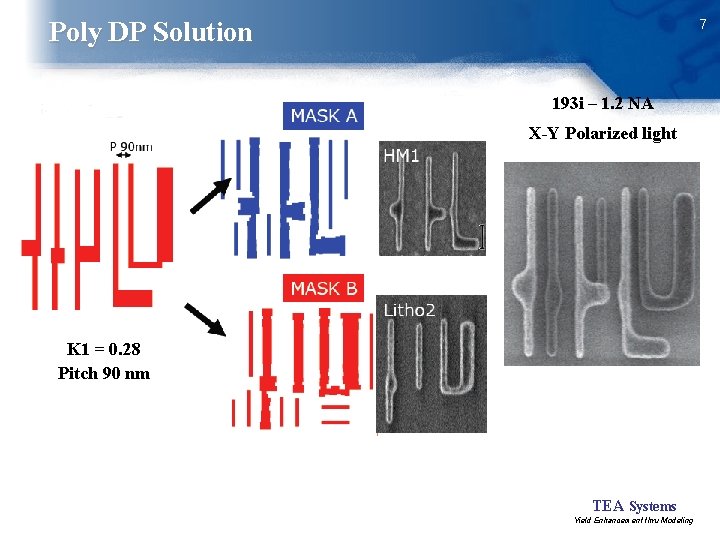
7 Poly DP Solution 193 i – 1. 2 NA X-Y Polarized light K 1 = 0. 28 Pitch 90 nm TEA Systems Yield Enhancement thru Modeling

8 Exposure Tool Solutions Double Patterning TEA Systems Yield Enhancement thru Modeling
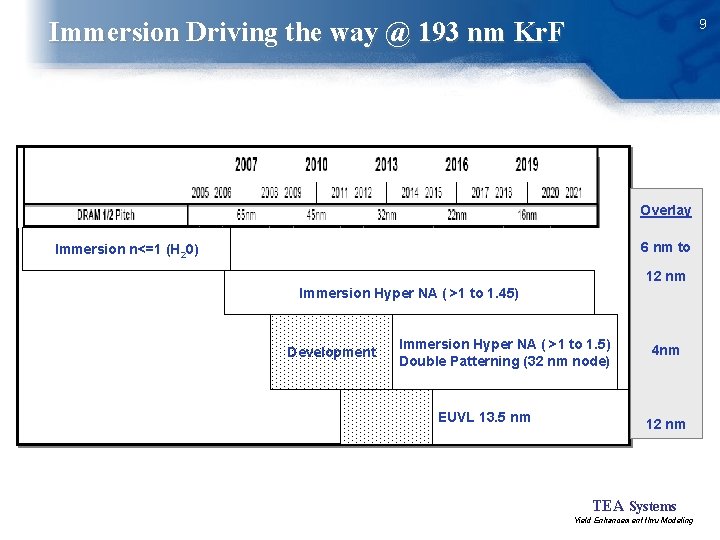
9 Immersion Driving the way @ 193 nm Kr. F Overlay 6 nm to Immersion n<=1 (H 20) 12 nm Immersion Hyper NA ( >1 to 1. 45) Development Immersion Hyper NA ( >1 to 1. 5) Double Patterning (32 nm node) EUVL 13. 5 nm 4 nm 12 nm TEA Systems Yield Enhancement thru Modeling
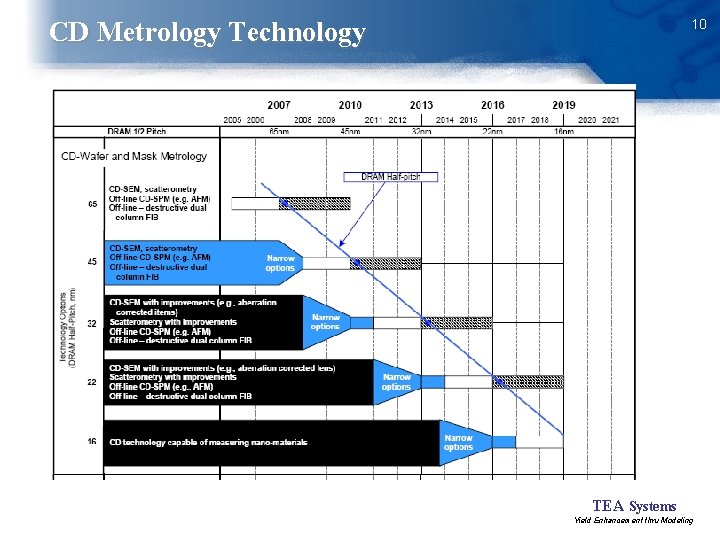
10 CD Metrology Technology TEA Systems Yield Enhancement thru Modeling
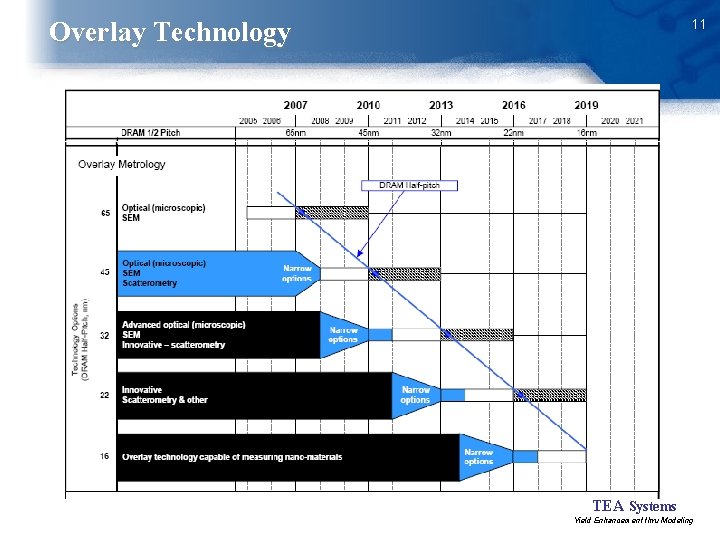
11 Overlay Technology TEA Systems Yield Enhancement thru Modeling
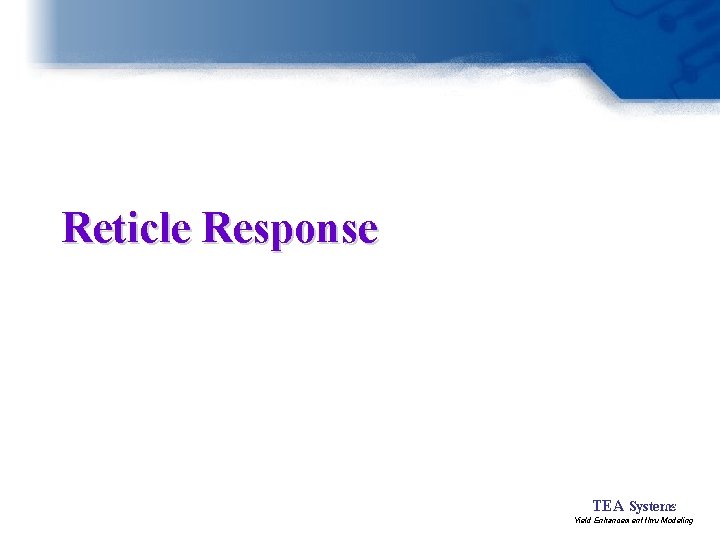
Reticle Response 12 TEA Systems Yield Enhancement thru Modeling
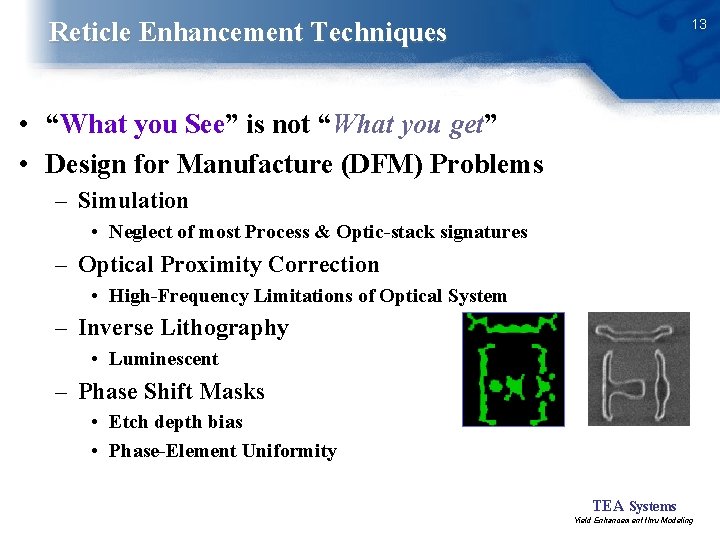
13 Reticle Enhancement Techniques • “What you See” is not “What you get” • Design for Manufacture (DFM) Problems – Simulation • Neglect of most Process & Optic-stack signatures – Optical Proximity Correction • High-Frequency Limitations of Optical System – Inverse Lithography • Luminescent – Phase Shift Masks • Etch depth bias • Phase-Element Uniformity TEA Systems Yield Enhancement thru Modeling
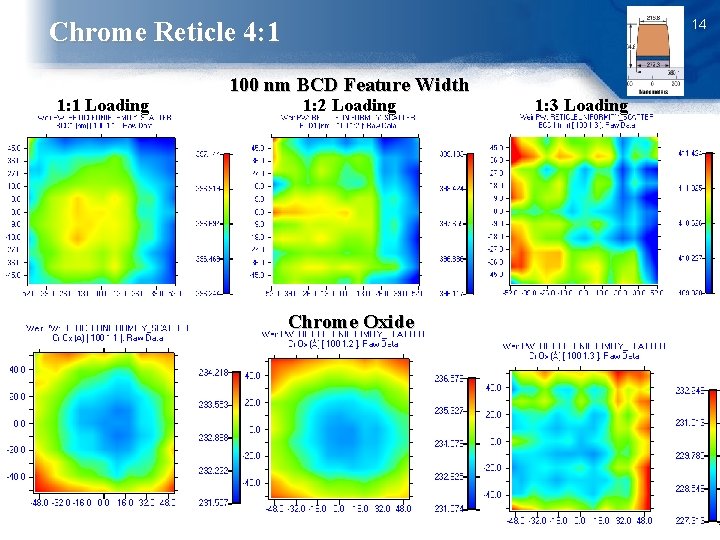
14 Chrome Reticle 4: 1 1: 1 Loading 100 nm BCD Feature Width 1: 2 Loading 1: 3 Loading Chrome Oxide TEA Systems Yield Enhancement thru Modeling

15 What Effect on Wafer? Mo. Si. ON Fingerprint on Reticle Nanometrics Atlas M Scatterometry TEA Systems Weir PW Data Analysis TEA Systems Yield Enhancement thru Modeling

16 Photoresist & BCD due to Moly Signature Raw Photoresist Thickness Modeled BCD Mo. Si. ON Signature • Photoresist – 1: 1 90 nm features Modeled BCD • BCD Full-Field Symmetric Model – BCD component due to Mo. Si. ON – Piston & high-order removed TEA Systems – 4. 5 nm Range Yield Enhancement thru Modeling
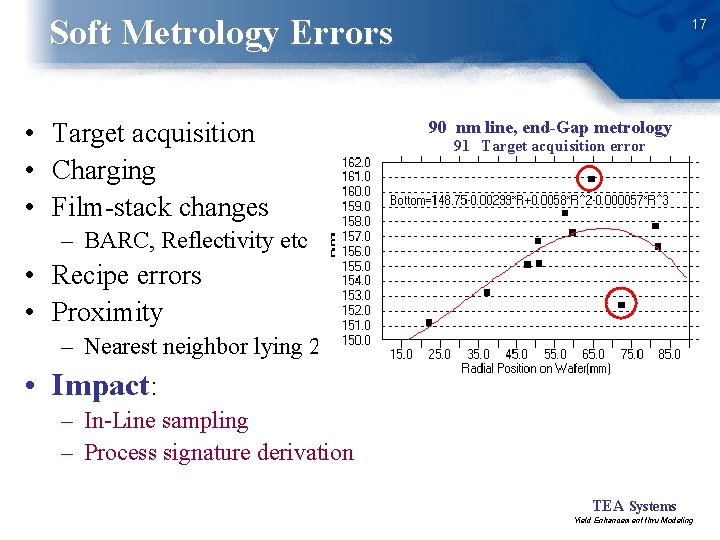
Soft Metrology Errors • Target acquisition • Charging • Film-stack changes 17 90 nm line, end-Gap metrology 91 Target acquisition error – BARC, Reflectivity etc • Recipe errors • Proximity – Nearest neighbor lying 2. 5 * image size • Impact: – In-Line sampling – Process signature derivation TEA Systems Yield Enhancement thru Modeling
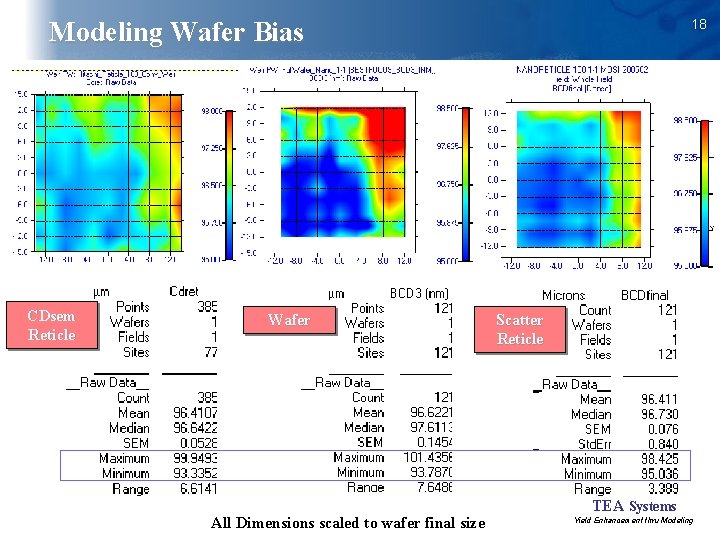
18 Modeling Wafer Bias CDsem Reticle Wafer All Dimensions scaled to wafer final size Scatter Reticle TEA Systems Yield Enhancement thru Modeling
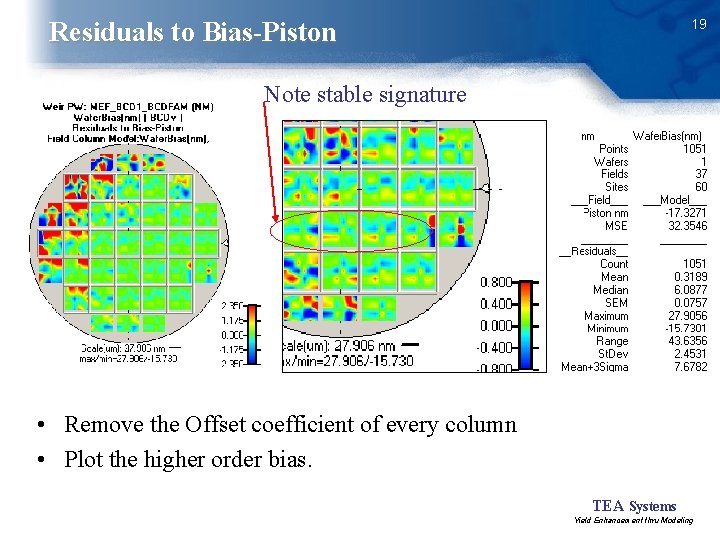
19 Residuals to Bias-Piston Note stable signature • Remove the Offset coefficient of every column • Plot the higher order bias. TEA Systems Yield Enhancement thru Modeling
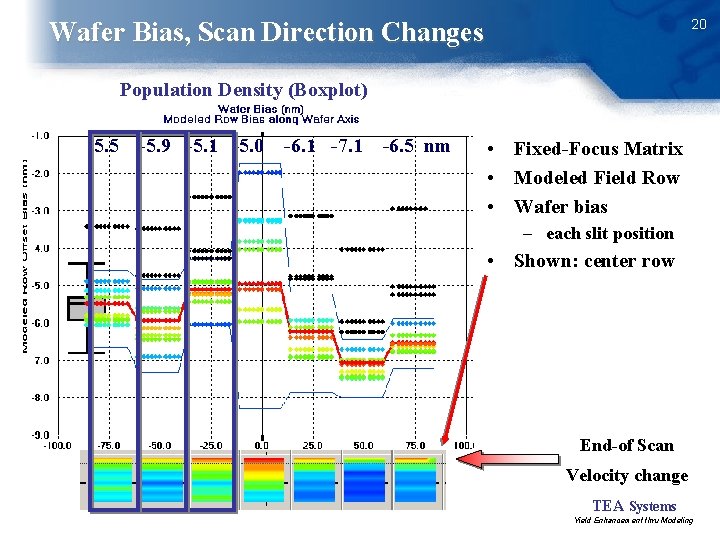
20 Wafer Bias, Scan Direction Changes Population Density (Boxplot) -5. 5 -5. 9 -5. 1 -5. 0 -6. 1 -7. 1 -6. 5 nm • Fixed-Focus Matrix • Modeled Field Row • Wafer bias – each slit position • Shown: center row End-of Scan Velocity change TEA Systems Yield Enhancement thru Modeling
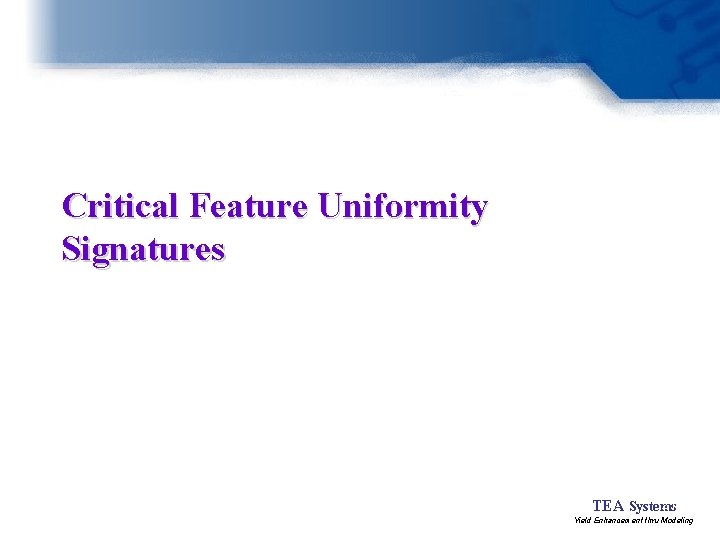
Critical Feature Uniformity Signatures 21 TEA Systems Yield Enhancement thru Modeling
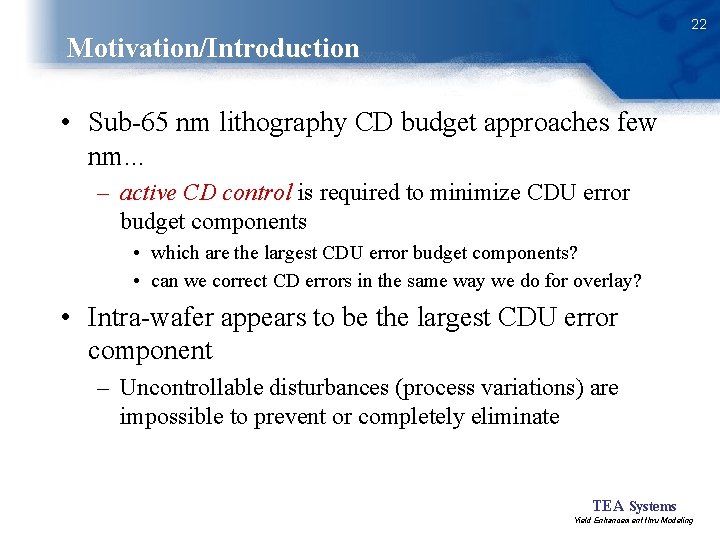
22 Motivation/Introduction • Sub-65 nm lithography CD budget approaches few nm. . . – active CD control is required to minimize CDU error budget components • which are the largest CDU error budget components? • can we correct CD errors in the same way we do for overlay? • Intra-wafer appears to be the largest CDU error component – Uncontrollable disturbances (process variations) are impossible to prevent or completely eliminate TEA Systems Yield Enhancement thru Modeling
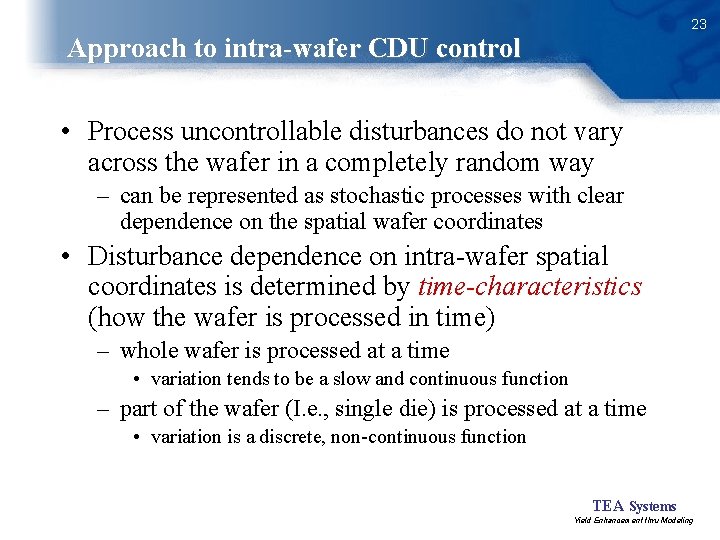
23 Approach to intra-wafer CDU control • Process uncontrollable disturbances do not vary across the wafer in a completely random way – can be represented as stochastic processes with clear dependence on the spatial wafer coordinates • Disturbance dependence on intra-wafer spatial coordinates is determined by time-characteristics (how the wafer is processed in time) – whole wafer is processed at a time • variation tends to be a slow and continuous function – part of the wafer (I. e. , single die) is processed at a time • variation is a discrete, non-continuous function TEA Systems Yield Enhancement thru Modeling
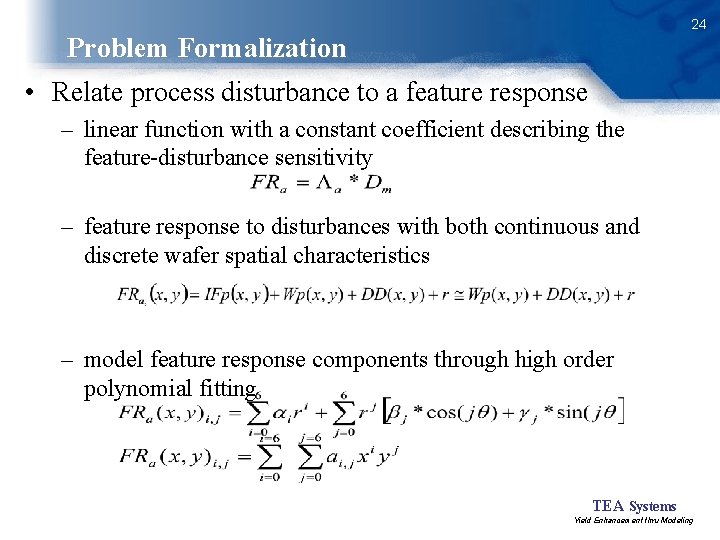
24 Problem Formalization • Relate process disturbance to a feature response – linear function with a constant coefficient describing the feature-disturbance sensitivity – feature response to disturbances with both continuous and discrete wafer spatial characteristics – model feature response components through high order polynomial fitting TEA Systems Yield Enhancement thru Modeling
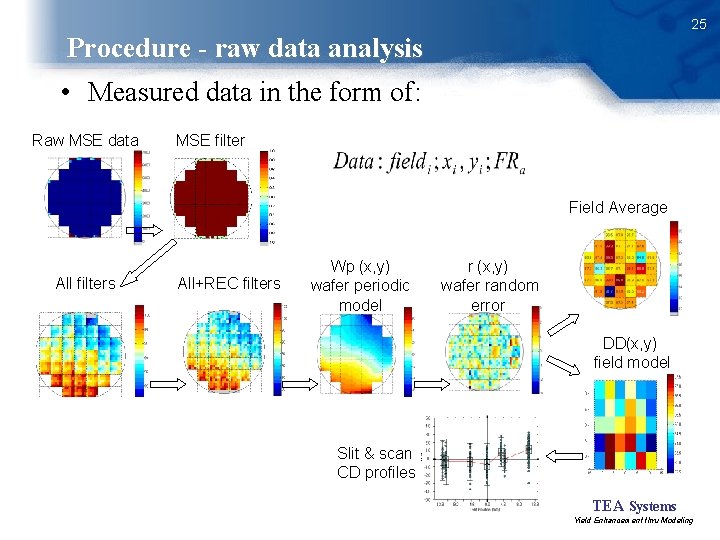
25 Procedure - raw data analysis • Measured data in the form of: Raw MSE data MSE filter Field Average All filters All+REC filters Wp (x, y) wafer periodic model r (x, y) wafer random error DD(x, y) field model Slit & scan CD profiles TEA Systems Yield Enhancement thru Modeling
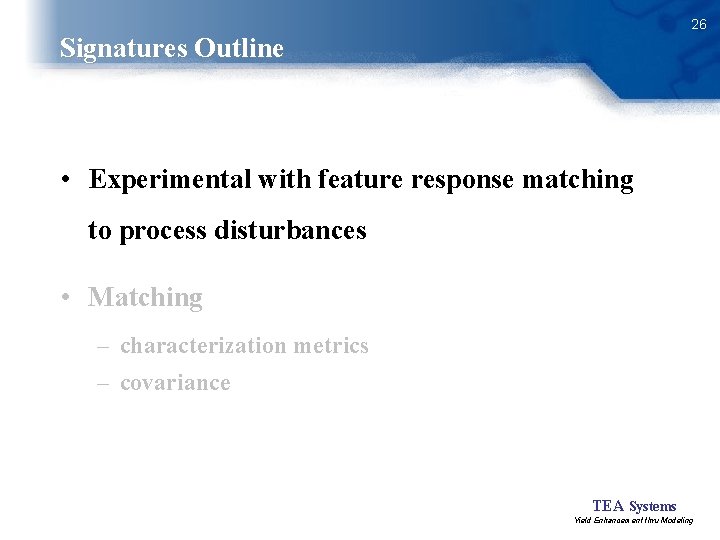
26 Signatures Outline • Experimental with feature response matching to process disturbances • Matching – characterization metrics – covariance TEA Systems Yield Enhancement thru Modeling
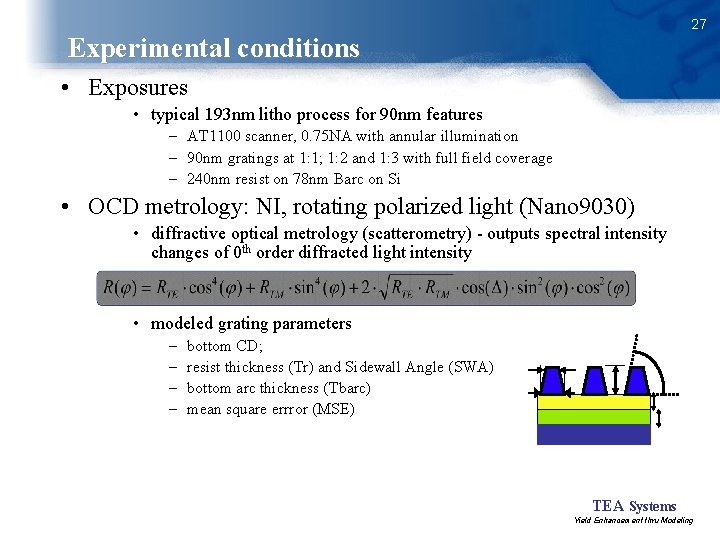
27 Experimental conditions • Exposures • typical 193 nm litho process for 90 nm features – AT 1100 scanner, 0. 75 NA with annular illumination – 90 nm gratings at 1: 1; 1: 2 and 1: 3 with full field coverage – 240 nm resist on 78 nm Barc on Si • OCD metrology: NI, rotating polarized light (Nano 9030) • diffractive optical metrology (scatterometry) - outputs spectral intensity changes of 0 th order diffracted light intensity • modeled grating parameters – – bottom CD; resist thickness (Tr) and Sidewall Angle (SWA) bottom arc thickness (Tbarc) mean square errror (MSE) TEA Systems Yield Enhancement thru Modeling
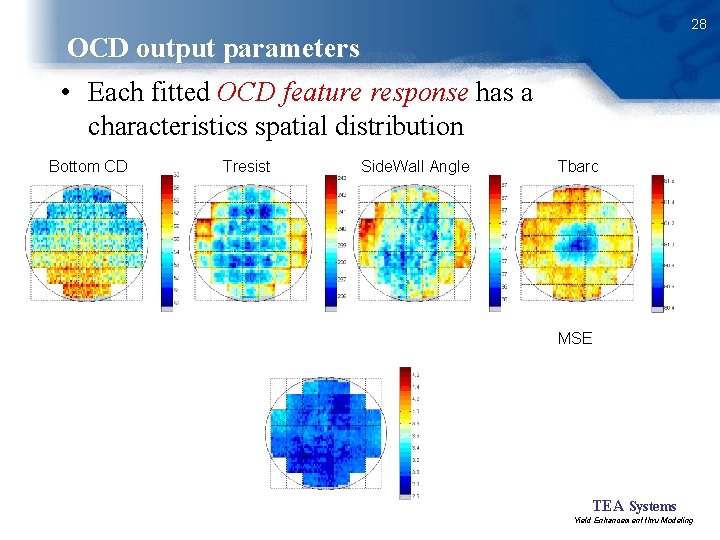
28 OCD output parameters • Each fitted OCD feature response has a characteristics spatial distribution Bottom CD Tresist Side. Wall Angle Tbarc MSE TEA Systems Yield Enhancement thru Modeling
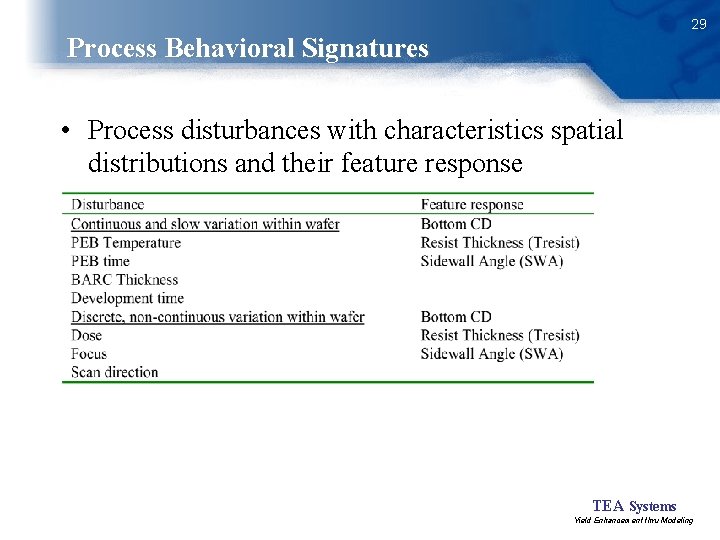
29 Process Behavioral Signatures • Process disturbances with characteristics spatial distributions and their feature response TEA Systems Yield Enhancement thru Modeling
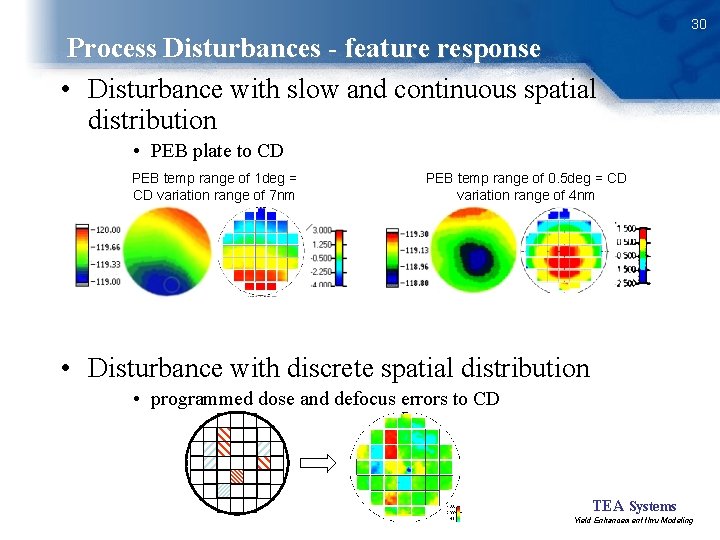
Process Disturbances - feature response • Disturbance with slow and continuous spatial distribution 30 • PEB plate to CD PEB temp range of 1 deg = CD variation range of 7 nm PEB temp range of 0. 5 deg = CD variation range of 4 nm • Disturbance with discrete spatial distribution • programmed dose and defocus errors to CD TEA Systems Yield Enhancement thru Modeling
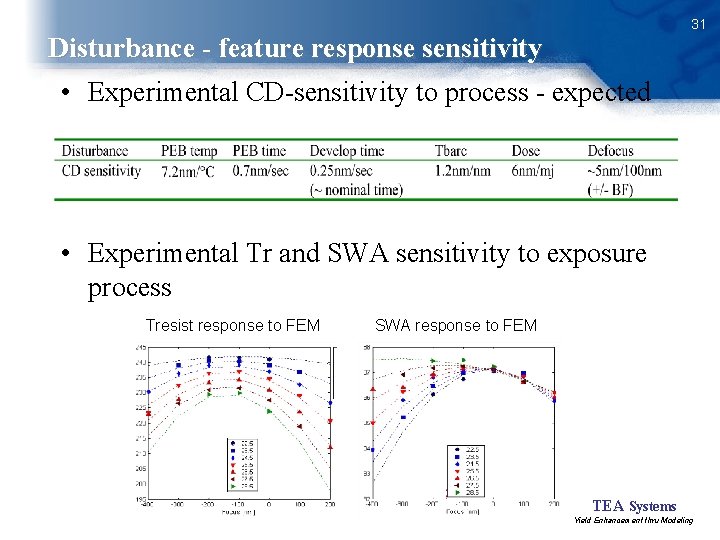
31 Disturbance - feature response sensitivity • Experimental CD-sensitivity to process - expected • Experimental Tr and SWA sensitivity to exposure process Tresist response to FEM SWA response to FEM TEA Systems Yield Enhancement thru Modeling
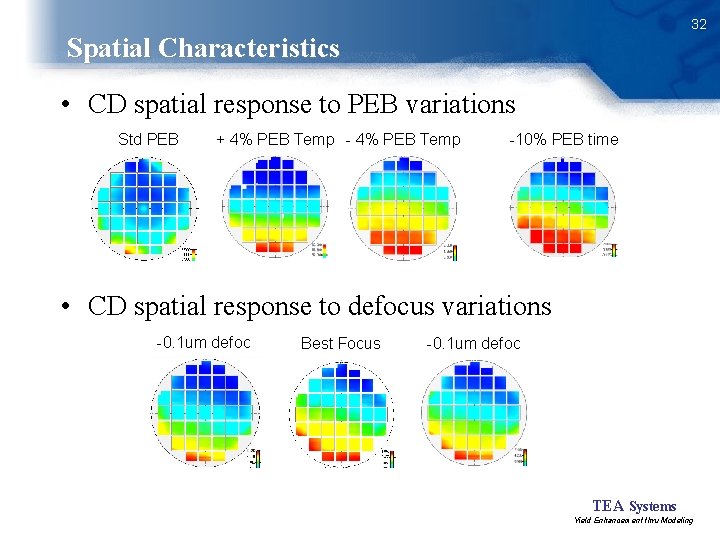
32 Spatial Characteristics • CD spatial response to PEB variations Std PEB + 4% PEB Temp -10% PEB time • CD spatial response to defocus variations -0. 1 um defoc Best Focus -0. 1 um defoc TEA Systems Yield Enhancement thru Modeling
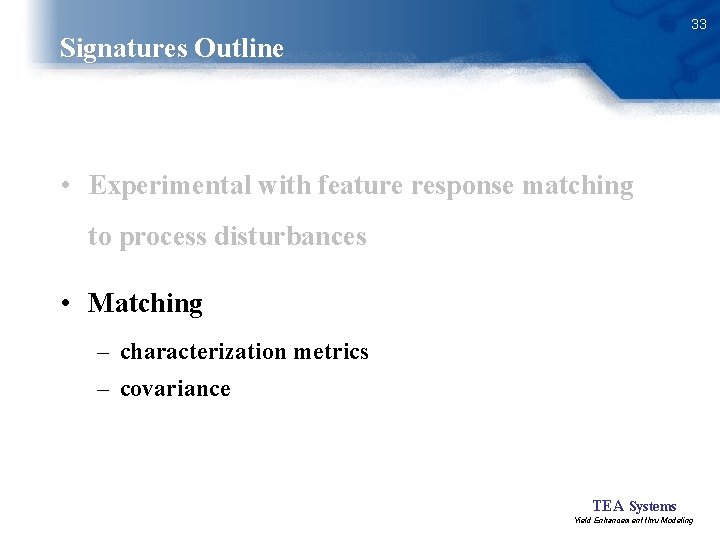
33 Signatures Outline • Experimental with feature response matching to process disturbances • Matching – characterization metrics – covariance TEA Systems Yield Enhancement thru Modeling
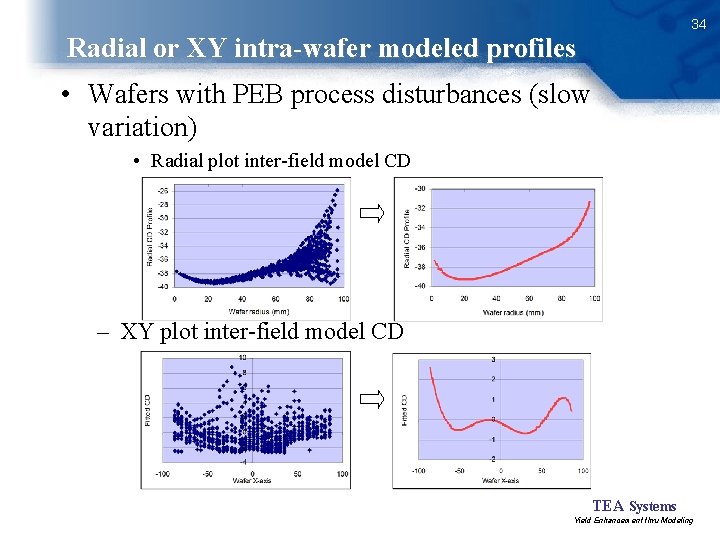
34 Radial or XY intra-wafer modeled profiles • Wafers with PEB process disturbances (slow variation) • Radial plot inter-field model CD – XY plot inter-field model CD TEA Systems Yield Enhancement thru Modeling
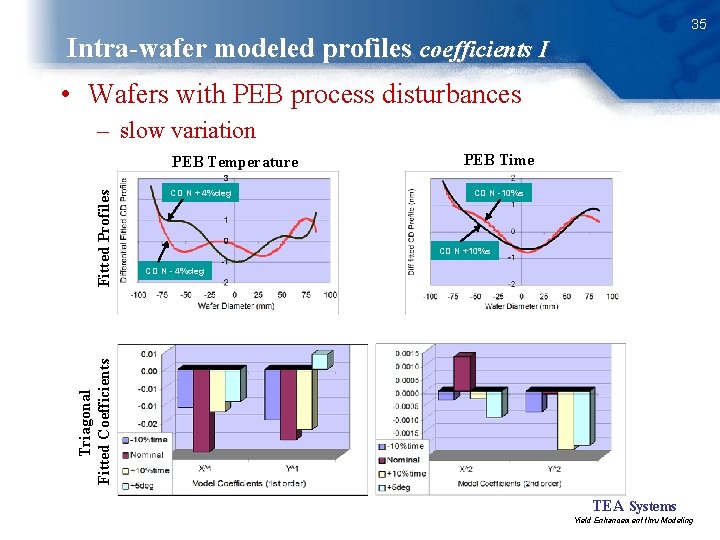
35 Intra-wafer modeled profiles coefficients I • Wafers with PEB process disturbances – slow variation CD N + 4%deg PEB Time CD N -10%s CD N +10%s CD N - 4%deg Triagonal Fitted Coefficients Fitted Profiles PEB Temperature TEA Systems Yield Enhancement thru Modeling
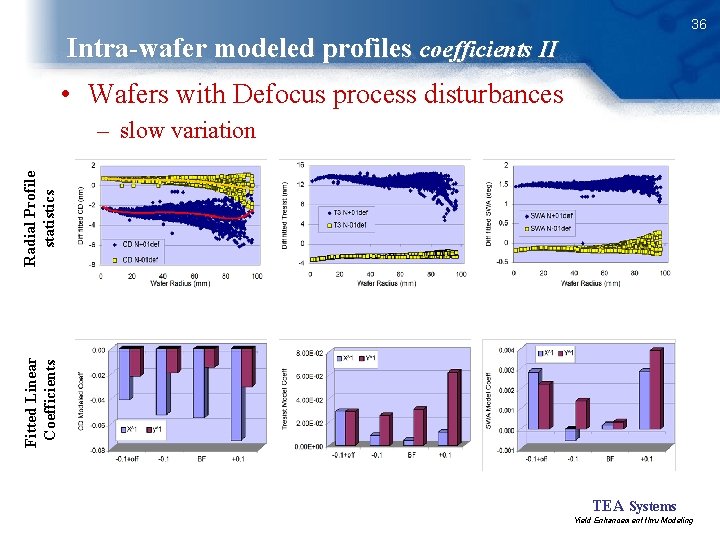
36 Intra-wafer modeled profiles coefficients II • Wafers with Defocus process disturbances Fitted Linear Coefficients Radial Profile statistics – slow variation TEA Systems Yield Enhancement thru Modeling
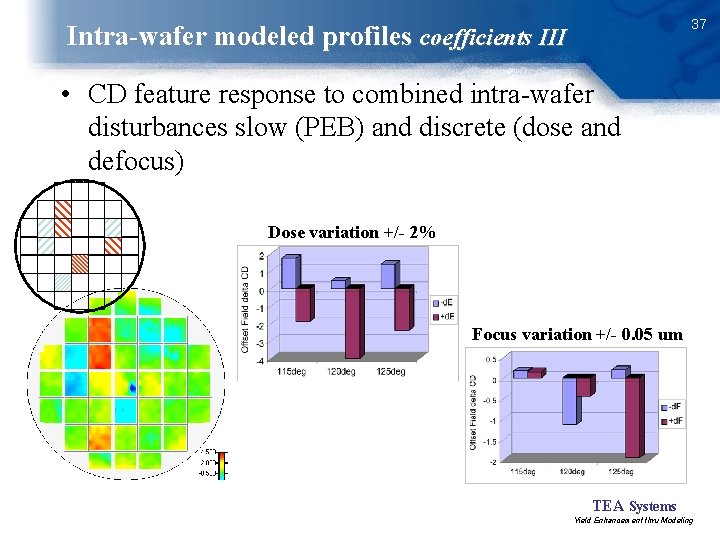
37 Intra-wafer modeled profiles coefficients III • CD feature response to combined intra-wafer disturbances slow (PEB) and discrete (dose and defocus) Dose variation +/- 2% Focus variation +/- 0. 05 um TEA Systems Yield Enhancement thru Modeling
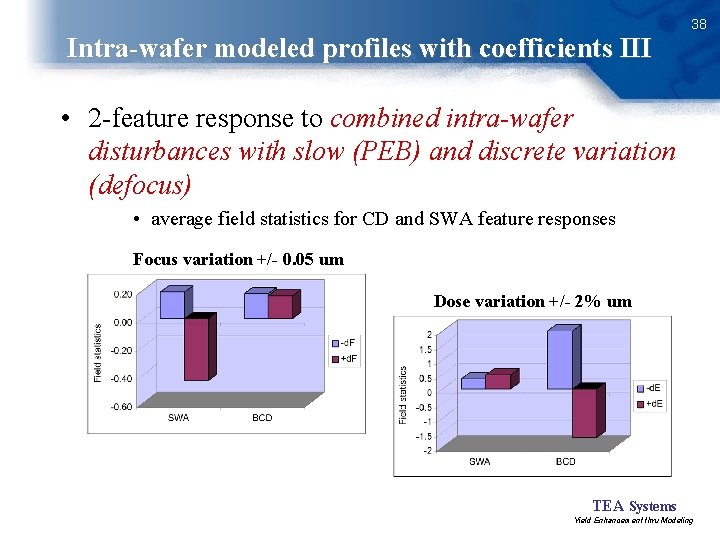
Intra-wafer modeled profiles with coefficients III 38 • 2 -feature response to combined intra-wafer disturbances with slow (PEB) and discrete variation (defocus) • average field statistics for CD and SWA feature responses Focus variation +/- 0. 05 um Dose variation +/- 2% um TEA Systems Yield Enhancement thru Modeling
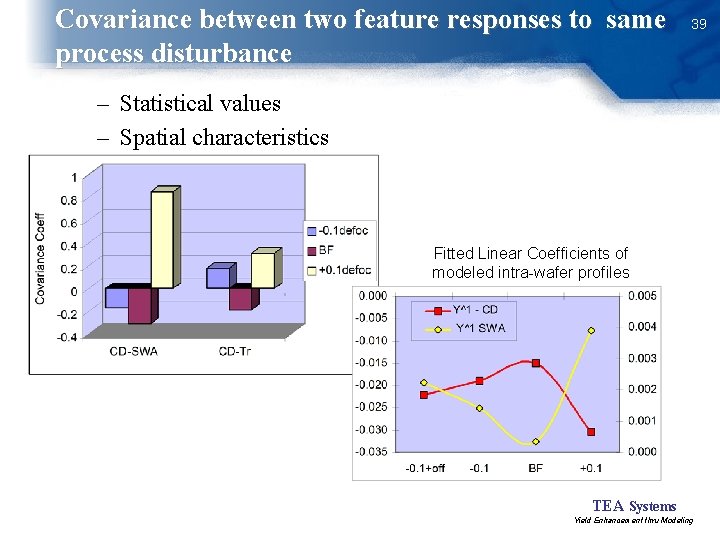
Covariance between two feature responses to same process disturbance 39 – Statistical values – Spatial characteristics Fitted Linear Coefficients of modeled intra-wafer profiles TEA Systems Yield Enhancement thru Modeling
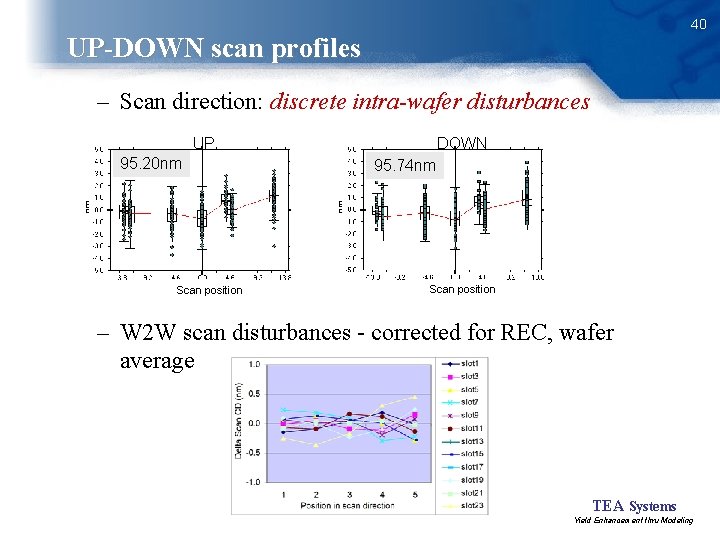
40 UP-DOWN scan profiles – Scan direction: discrete intra-wafer disturbances UP 95. 20 nm Scan position DOWN 95. 74 nm Scan position – W 2 W scan disturbances - corrected for REC, wafer average TEA Systems Yield Enhancement thru Modeling
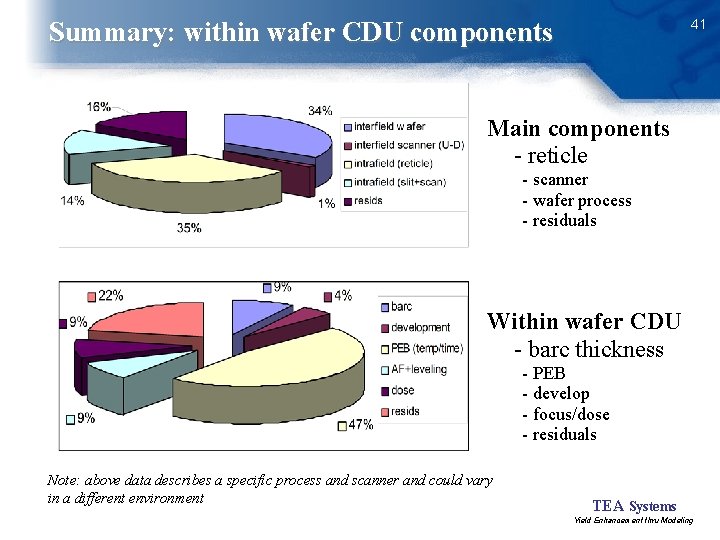
41 Summary: within wafer CDU components Main components - reticle - scanner - wafer process - residuals Within wafer CDU - barc thickness - PEB - develop - focus/dose - residuals Note: above data describes a specific process and scanner and could vary in a different environment TEA Systems Yield Enhancement thru Modeling
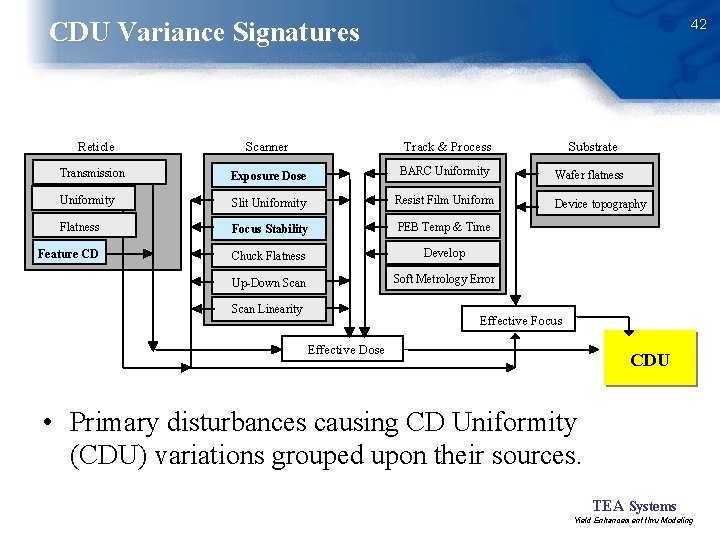
42 CDU Variance Signatures Reticle Scanner Track & Process Transmission Exposure Dose BARC Uniformity Slit Uniformity Resist Film Uniform Flatness Focus Stability PEB Temp & Time Feature CD Chuck Flatness Develop Up-Down Scan Soft Metrology Error Scan Linearity Substrate Wafer flatness Device topography Effective Focus Effective Dose CDU • Primary disturbances causing CD Uniformity (CDU) variations grouped upon their sources. TEA Systems Yield Enhancement thru Modeling

BARC modeled wafer uniformity SPIE Vol. 5378 -11 43 TEA Systems Yield Enhancement thru Modeling
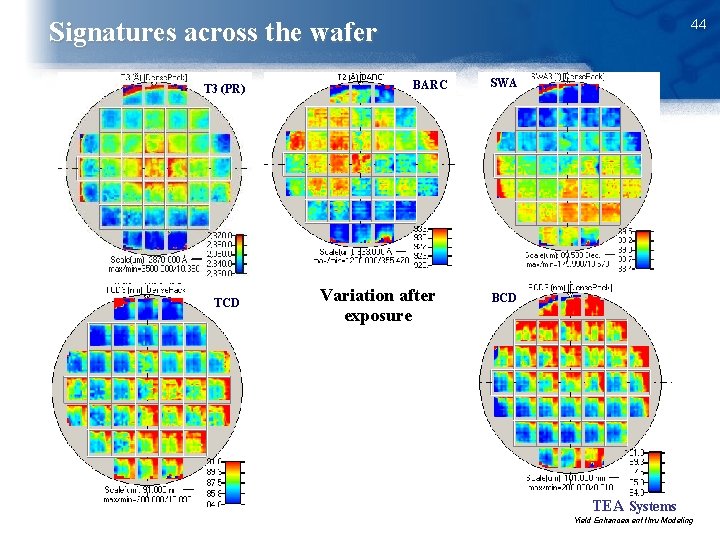
44 Signatures across the wafer T 3 (PR) TCD BARC Variation after exposure SWA BCD TEA Systems Yield Enhancement thru Modeling
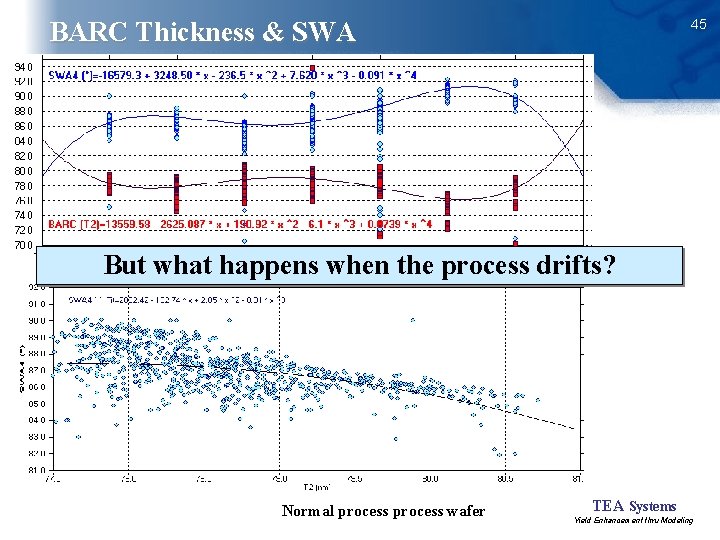
45 BARC Thickness & SWA But what happens when the process drifts? Normal process wafer TEA Systems Yield Enhancement thru Modeling
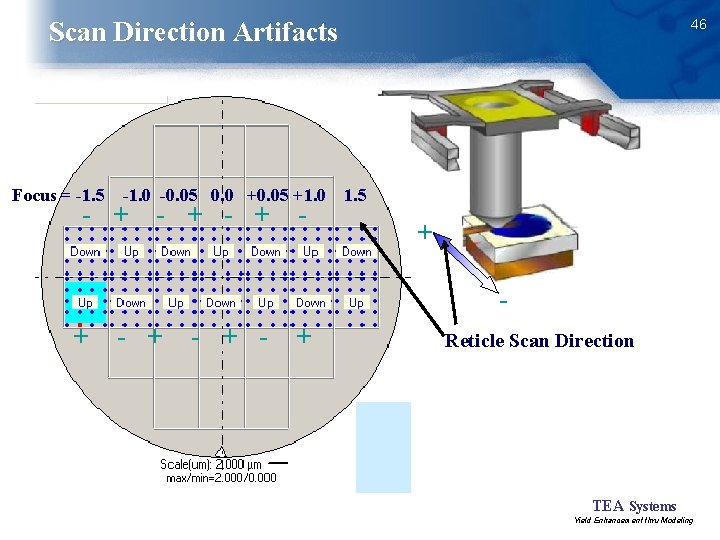
46 Scan Direction Artifacts Focus = -1. 5 -1. 0 -0. 05 0. 0 +0. 05 +1. 0 - + - + - 1. 5 + - + - + Reticle Scan Direction TEA Systems Yield Enhancement thru Modeling
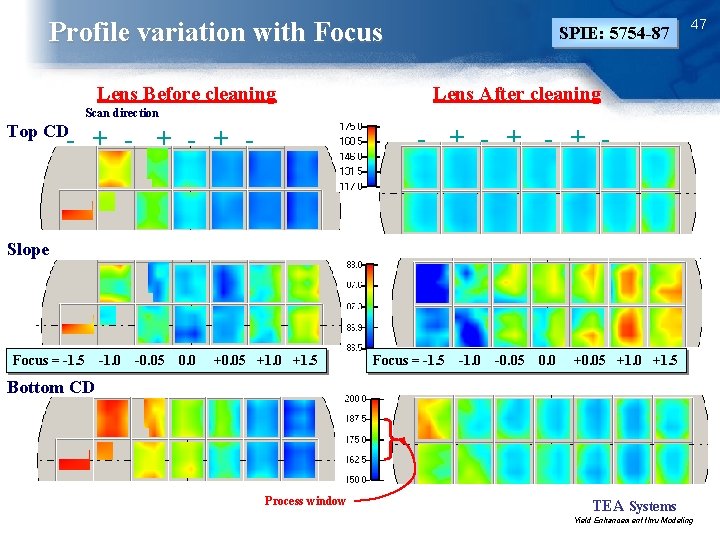
Profile variation with Focus SPIE: 5754 -87 Lens Before cleaning 47 Lens After cleaning Scan direction Top CD - + + - + - + - + Slope Focus = -1. 5 -1. 0 -0. 05 0. 0 +0. 05 +1. 0 +1. 5 Bottom CD Process window TEA Systems Yield Enhancement thru Modeling
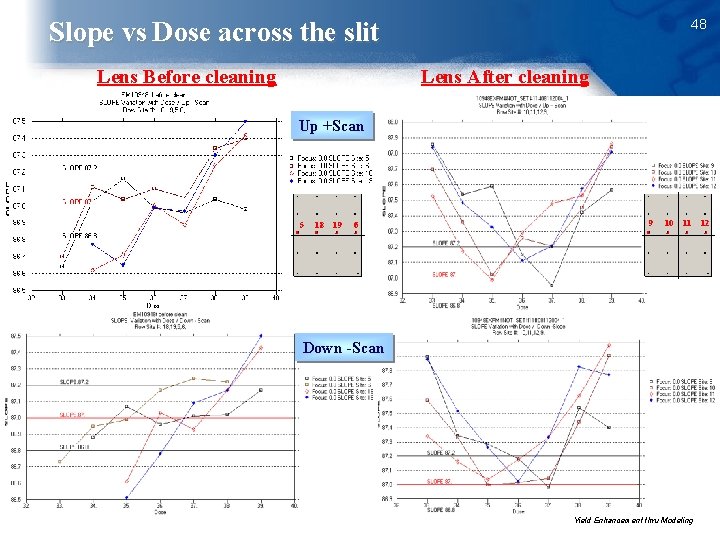
48 Slope vs Dose across the slit Lens Before cleaning Lens After cleaning Up +Scan 5 18 19 6 9 10 11 Down -Scan TEA Systems Yield Enhancement thru Modeling 12
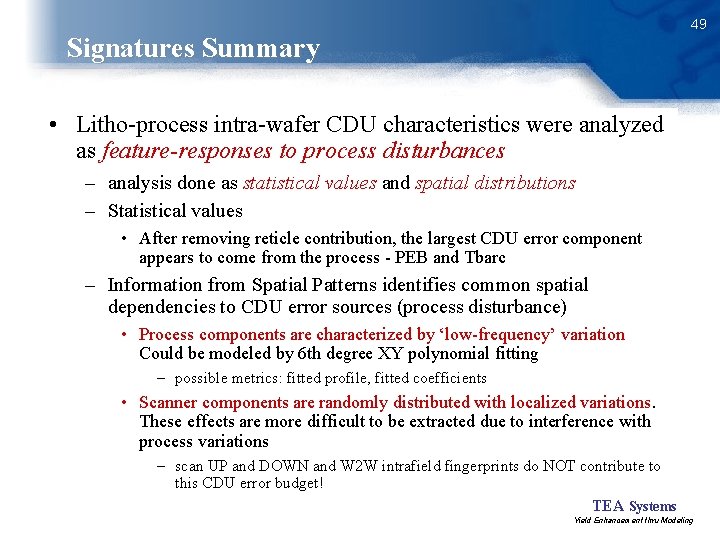
49 Signatures Summary • Litho-process intra-wafer CDU characteristics were analyzed as feature-responses to process disturbances – analysis done as statistical values and spatial distributions – Statistical values • After removing reticle contribution, the largest CDU error component appears to come from the process - PEB and Tbarc – Information from Spatial Patterns identifies common spatial dependencies to CDU error sources (process disturbance) • Process components are characterized by ‘low-frequency’ variation Could be modeled by 6 th degree XY polynomial fitting – possible metrics: fitted profile, fitted coefficients • Scanner components are randomly distributed with localized variations. These effects are more difficult to be extracted due to interference with process variations – scan UP and DOWN and W 2 W intrafield fingerprints do NOT contribute to this CDU error budget! TEA Systems Yield Enhancement thru Modeling
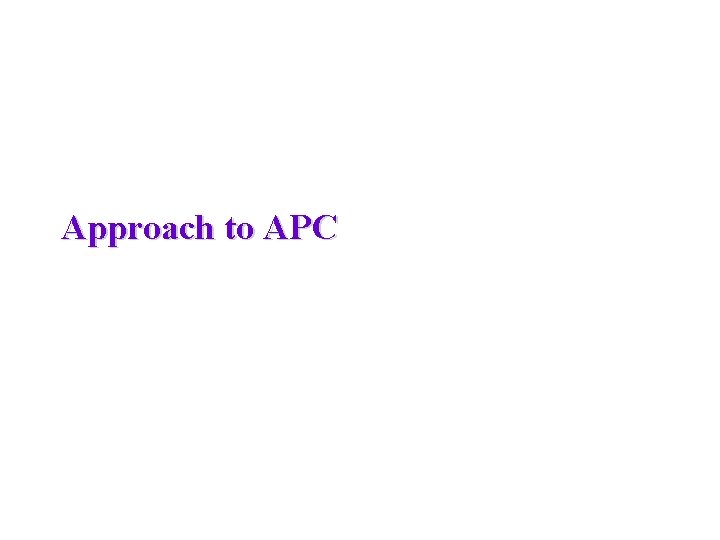
Approach to APC 50
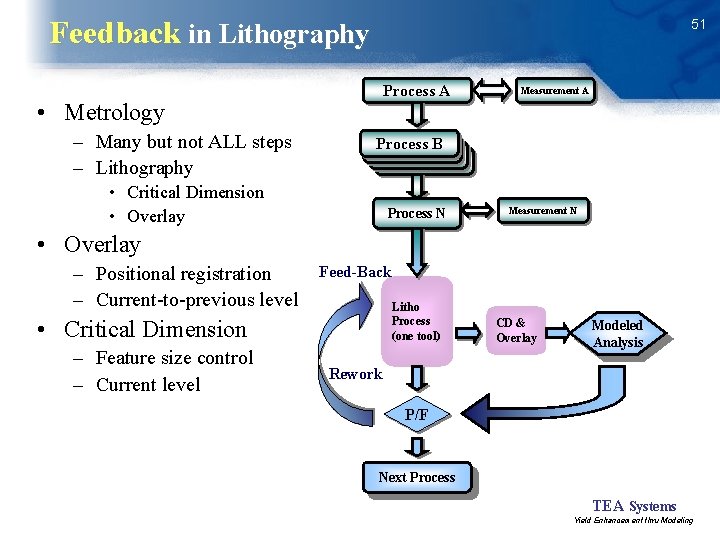
Feedback in Lithography 51 Process A • Metrology – Many but not ALL steps – Lithography Measurement A Process B • Critical Dimension • Overlay Process N Measurement N • Overlay – Positional registration – Current-to-previous level Feed-Back Litho Process (one tool) • Critical Dimension – Feature size control – Current level CD & Overlay Modeled Analysis Rework P/F Next Process TEA Systems Yield Enhancement thru Modeling
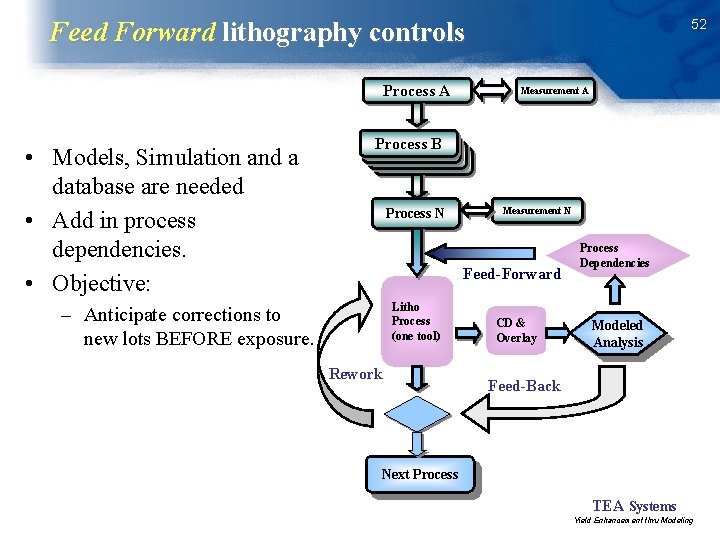
52 Feed Forward lithography controls Process A • Models, Simulation and a database are needed • Add in process dependencies. • Objective: Measurement A Process B Process N Measurement N Feed-Forward Litho Process (one tool) – Anticipate corrections to new lots BEFORE exposure. Rework CD & Overlay Process Dependencies Modeled Analysis Feed-Back Next Process TEA Systems Yield Enhancement thru Modeling
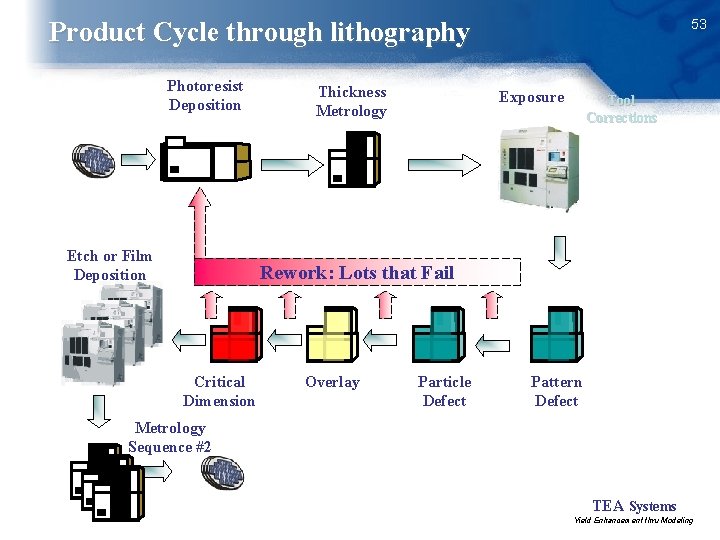
53 Product Cycle through lithography Photoresist Deposition Etch or Film Deposition Thickness Metrology Exposure Tool Corrections Rework: Lots that Fail Critical Dimension Overlay Particle Defect Pattern Defect Metrology Sequence #2 TEA Systems Yield Enhancement thru Modeling
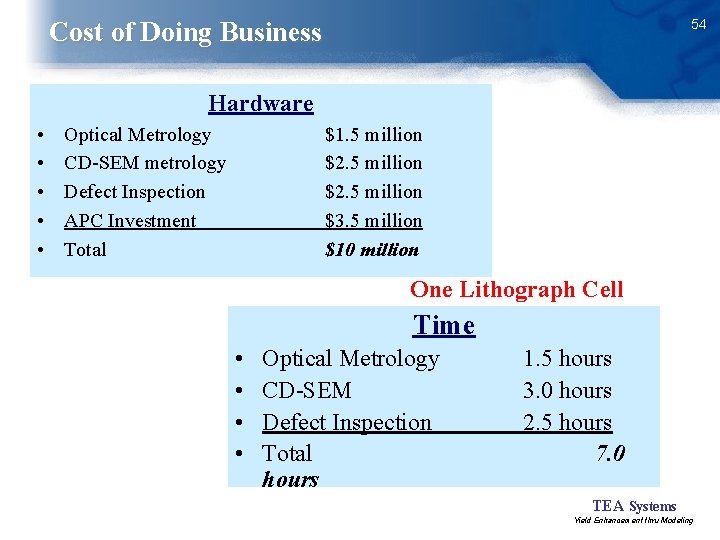
54 Cost of Doing Business Hardware • • • Optical Metrology CD-SEM metrology Defect Inspection APC Investment Total $1. 5 million $2. 5 million $3. 5 million $10 million One Lithograph Cell Time • • Optical Metrology CD-SEM Defect Inspection Total hours 1. 5 hours 3. 0 hours 2. 5 hours 7. 0 TEA Systems Yield Enhancement thru Modeling
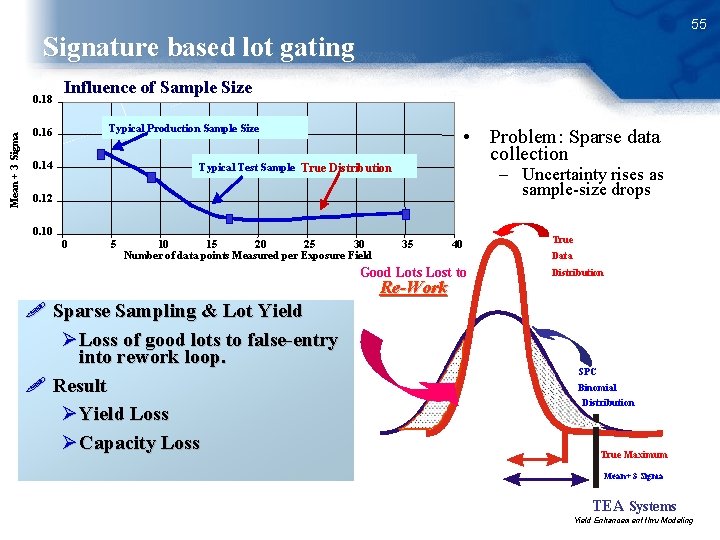
55 Signature based lot gating Mean + 3 Sigma 0. 18 Influence of Sample Size Typical Production Sample Size 0. 16 0. 14 • Problem: Sparse data collection Typical Test Sample True Distribution – Uncertainty rises as sample-size drops 0. 12 0. 10 0 5 10 15 20 25 30 Number of data points Measured per Exposure Field 35 40 Good Lots Lost to Re-Work ! Sparse Sampling & Lot Yield Ø Loss of good lots to false-entry into rework loop. ! Result Ø Yield Loss Ø Capacity Loss True Data Distribution SPC Binomial Distribution True Maximum Mean+ 3 Sigma TEA Systems Yield Enhancement thru Modeling

56 Feed Forward Techniques • EWMA – Exponentially Weighted Moving Average – Assumes a stable, continuous process • Enhanced EWMA – Include separate estimates and trend charts for: • Exposure Tool combinations • Process steps – Problems • ASIC or Logic fabs with many processes and devices • Each process-stream must maintain separate tracking and trends for each process and reticle set. • Short Lifetime devices • Long device start intervals • Behavioral Model Signatures – Include systematic modeling of tools and process – Compensate by adding systematic signatures prior to exposure. • Signatures for processes and tools used in lot history. • Signatures for target tools of next process step. TEA Systems Yield Enhancement thru Modeling
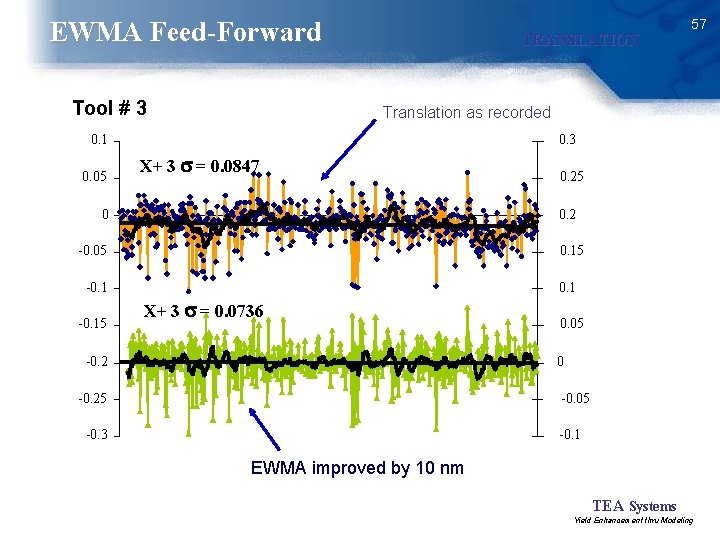
EWMA Feed-Forward Tool # 3 TRANSLATION Translation as recorded 0. 1 0. 05 0. 3 X+ 3 s = 0. 0847 0 0. 25 0. 2 -0. 05 0. 15 -0. 15 57 0. 1 X+ 3 s = 0. 0736 -0. 2 0. 05 0 -0. 25 -0. 05 -0. 3 -0. 1 EWMA improved by 10 nm TEA Systems Yield Enhancement thru Modeling
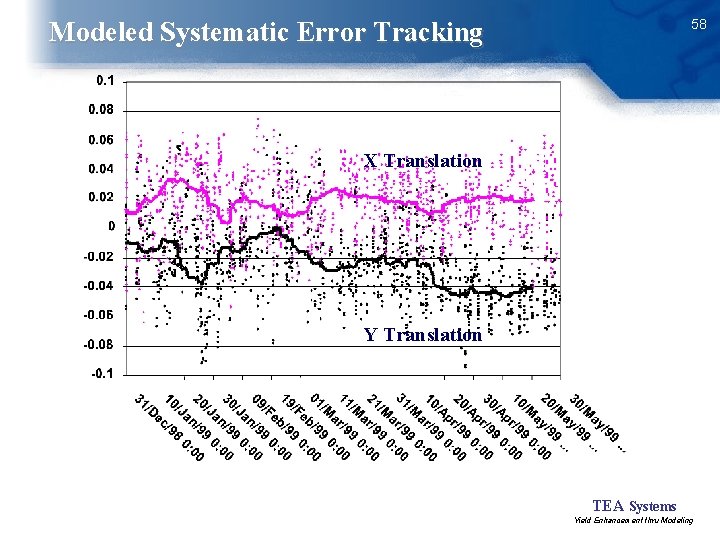
58 Modeled Systematic Error Tracking X Translation Y Translation TEA Systems Yield Enhancement thru Modeling
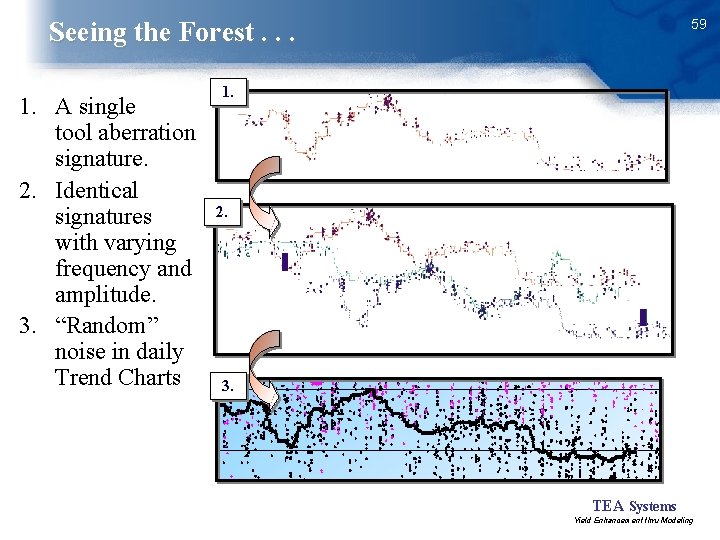
59 Seeing the Forest. . . 1. A single tool aberration signature. 2. Identical signatures with varying frequency and amplitude. 3. “Random” noise in daily Trend Charts 1. 2. 3. TEA Systems Yield Enhancement thru Modeling
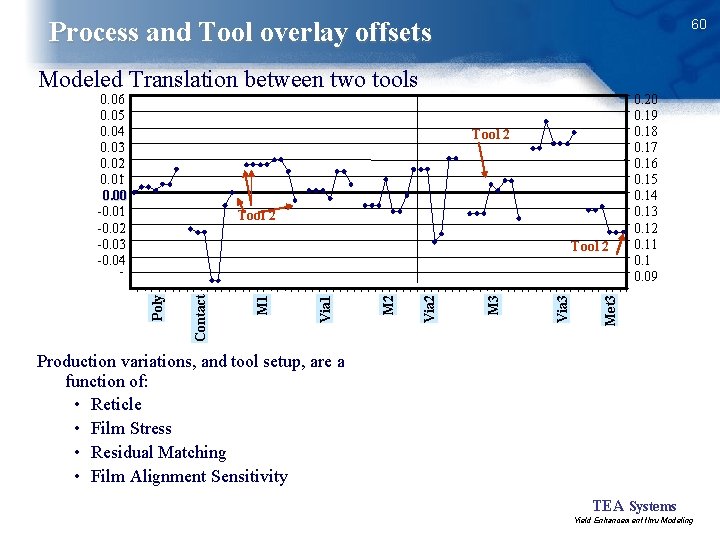
60 Process and Tool overlay offsets Modeled Translation between two tools 0. 06 0. 05 0. 04 0. 03 0. 02 0. 01 0. 00 -0. 01 -0. 02 -0. 03 -0. 04 Tool 2 Met 3 Via 3 M 3 Via 2 M 2 Via 1 M 1 Contact Poly Tool 2 0. 20 0. 19 0. 18 0. 17 0. 16 0. 15 0. 14 0. 13 0. 12 0. 11 0. 09 Production variations, and tool setup, are a function of: • Reticle • Film Stress • Residual Matching • Film Alignment Sensitivity TEA Systems Yield Enhancement thru Modeling
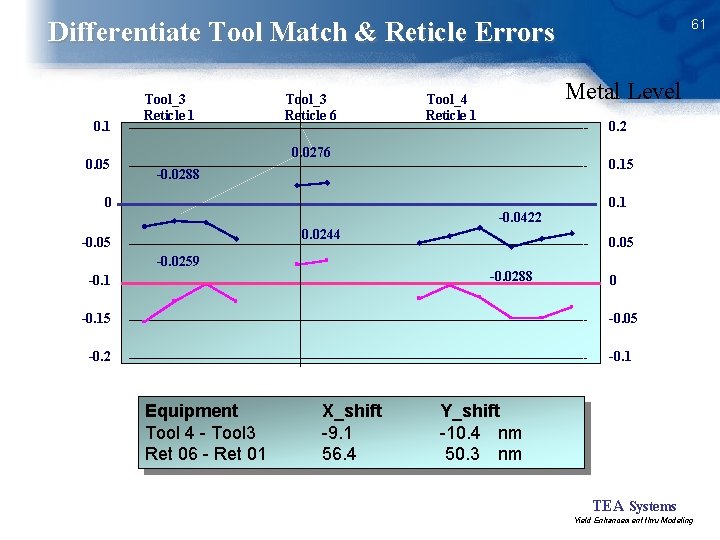
61 Differentiate Tool Match & Reticle Errors 0. 1 0. 05 Tool_3 Reticle 1 Tool_3 Reticle 6 Metal Level Tool_4 Reticle 1 0. 2 0. 0276 0. 15 -0. 0288 0 -0. 0422 0. 0244 -0. 05 -0. 0259 0. 05 -0. 0288 -0. 1 0 -0. 15 -0. 05 -0. 2 -0. 1 Equipment Tool 4 - Tool 3 Ret 06 - Ret 01 X_shift -9. 1 56. 4 Y_shift -10. 4 nm 50. 3 nm TEA Systems Yield Enhancement thru Modeling
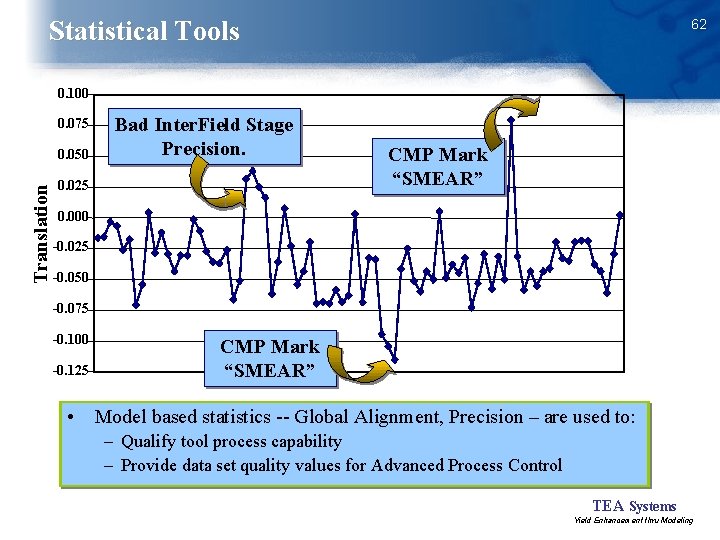
Statistical Tools 62 0. 100 0. 075 Translation 0. 050 Bad Inter. Field Stage Precision. 0. 025 CMP Mark “SMEAR” 0. 000 -0. 025 -0. 050 -0. 075 -0. 100 -0. 125 CMP Mark “SMEAR” • Model based statistics -- Global Alignment, Precision – are used to: – Qualify tool process capability – Provide data set quality values for Advanced Process Control TEA Systems Yield Enhancement thru Modeling
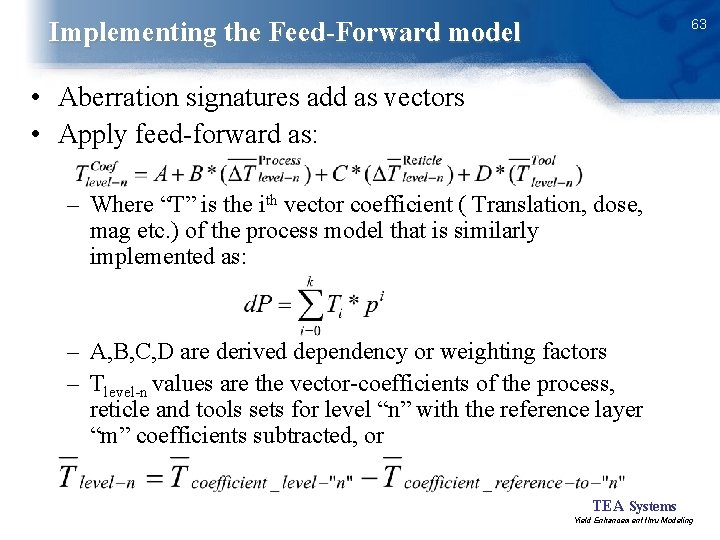
63 Implementing the Feed-Forward model • Aberration signatures add as vectors • Apply feed-forward as: – Where “T” is the ith vector coefficient ( Translation, dose, mag etc. ) of the process model that is similarly implemented as: – A, B, C, D are derived dependency or weighting factors – Tlevel-n values are the vector-coefficients of the process, reticle and tools sets for level “n” with the reference layer “m” coefficients subtracted, or TEA Systems Yield Enhancement thru Modeling
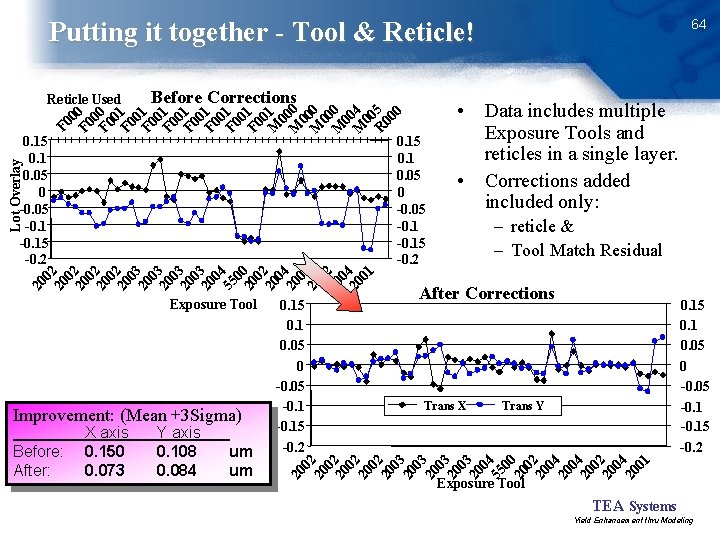
64 Putting it together - Tool & Reticle! Before Corrections F 0 0 0 F 0 1 0 F 0 1 0 M 00 00 M 04 00 R 5 00 0 Reticle Used 0. 15 0. 1 0. 05 0 -0. 05 -0. 15 -0. 2 20 0 20 2 0 20 3 0 55 4 0 20 0 0 20 2 0 20 4 01 Lot Overlay 0. 15 0. 1 0. 05 0 -0. 05 -0. 15 -0. 2 Improvement: (Mean +3 Sigma) Before: After: X axis 0. 150 0. 073 Y axis 0. 108 0. 084 um um 0. 15 0. 1 0. 05 0 -0. 05 -0. 15 -0. 2 – reticle & – Tool Match Residual After Corrections Trans X 0. 15 0. 1 0. 05 0 -0. 05 -0. 15 -0. 2 Trans Y 20 02 20 0 20 2 02 20 03 20 04 55 00 20 02 20 04 20 0 20 2 04 20 01 Exposure Tool • Data includes multiple Exposure Tools and reticles in a single layer. • Corrections added included only: Exposure Tool TEA Systems Yield Enhancement thru Modeling
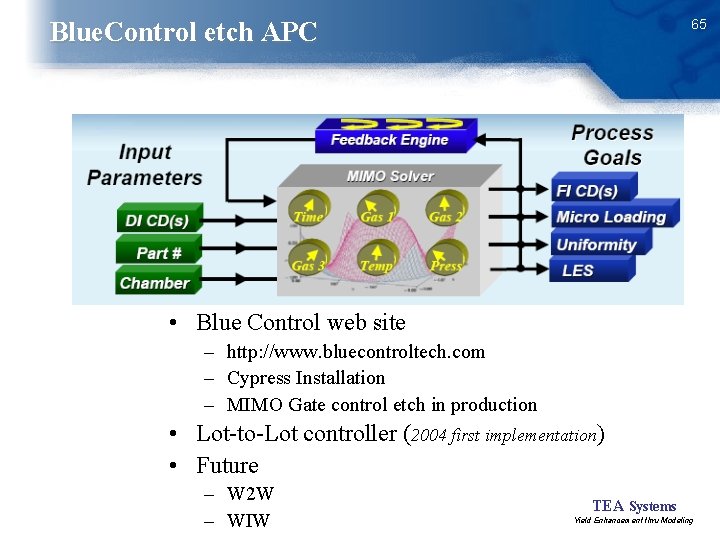
65 Blue. Control etch APC • Blue Control web site – http: //www. bluecontroltech. com – Cypress Installation – MIMO Gate control etch in production • Lot-to-Lot controller (2004 first implementation) • Future – W 2 W – WIW TEA Systems Yield Enhancement thru Modeling
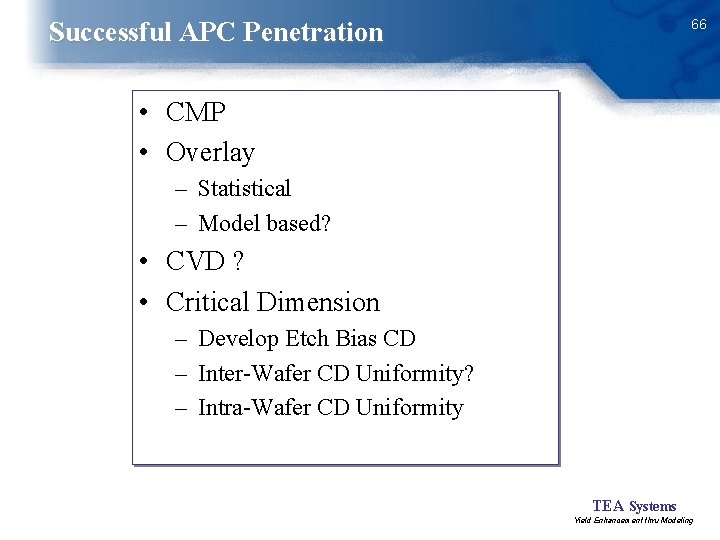
66 Successful APC Penetration • CMP • Overlay – Statistical – Model based? • CVD ? • Critical Dimension – Develop Etch Bias CD – Inter-Wafer CD Uniformity? – Intra-Wafer CD Uniformity TEA Systems Yield Enhancement thru Modeling
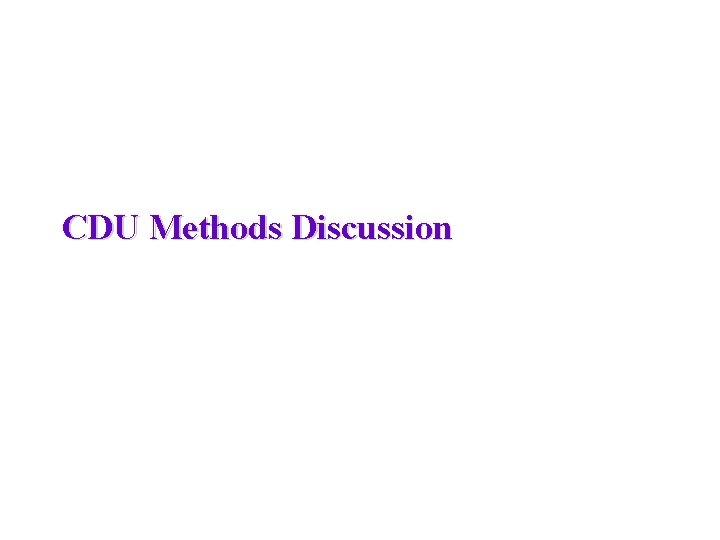
CDU Methods Discussion 67
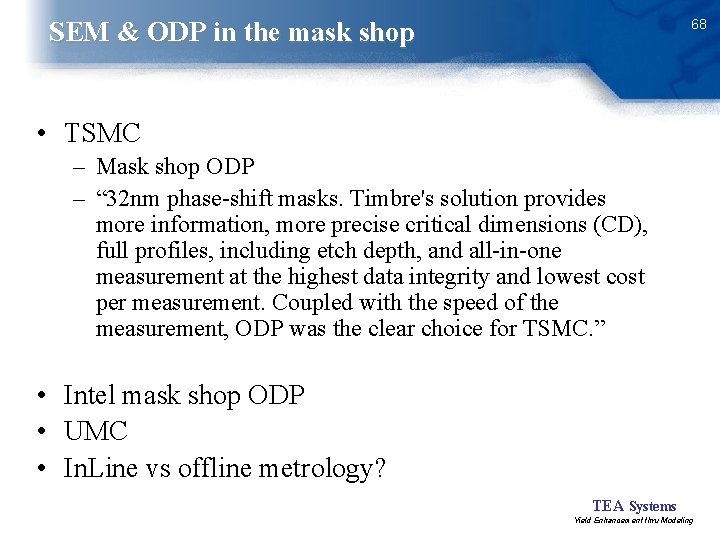
68 SEM & ODP in the mask shop • TSMC – Mask shop ODP – “ 32 nm phase-shift masks. Timbre's solution provides more information, more precise critical dimensions (CD), full profiles, including etch depth, and all-in-one measurement at the highest data integrity and lowest cost per measurement. Coupled with the speed of the measurement, ODP was the clear choice for TSMC. ” • Intel mask shop ODP • UMC • In. Line vs offline metrology? TEA Systems Yield Enhancement thru Modeling
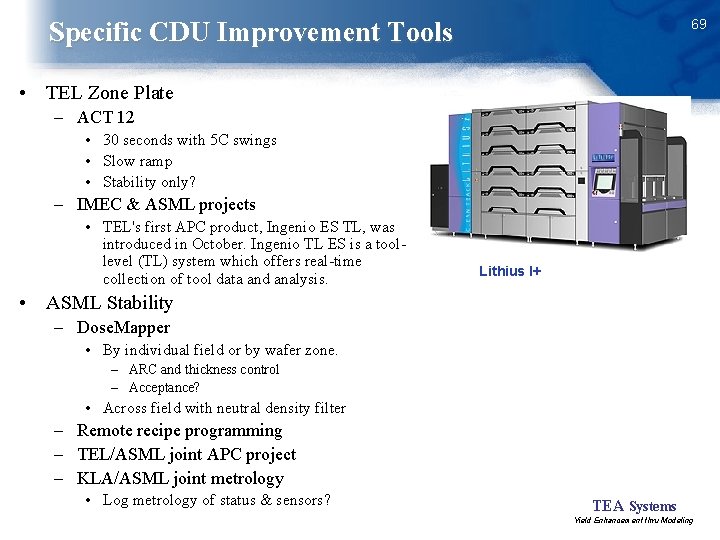
69 Specific CDU Improvement Tools • TEL Zone Plate – ACT 12 • 30 seconds with 5 C swings • Slow ramp • Stability only? – IMEC & ASML projects • TEL's first APC product, Ingenio ES TL, was introduced in October. Ingenio TL ES is a toollevel (TL) system which offers real-time collection of tool data and analysis. Lithius I+ • ASML Stability – Dose. Mapper • By individual field or by wafer zone. – ARC and thickness control – Acceptance? • Across field with neutral density filter – Remote recipe programming – TEL/ASML joint APC project – KLA/ASML joint metrology • Log metrology of status & sensors? TEA Systems Yield Enhancement thru Modeling
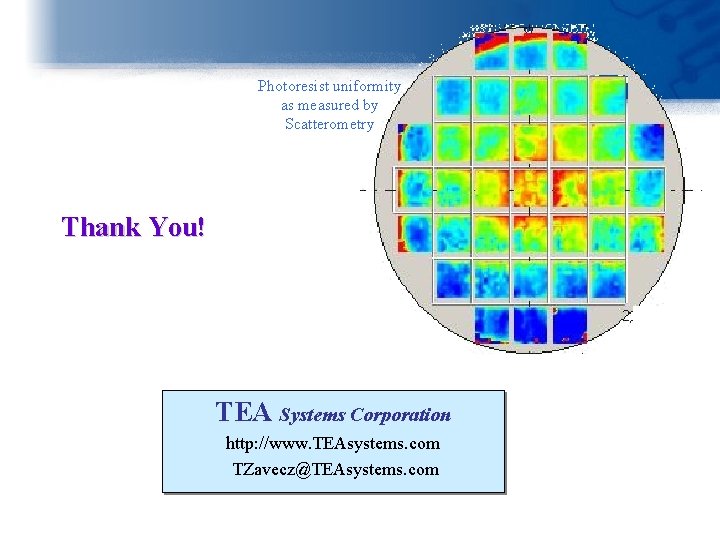
Photoresist uniformity as measured by Scatterometry Thank You! TEA Systems Corporation http: //www. TEAsystems. com TZavecz@TEAsystems. com 70
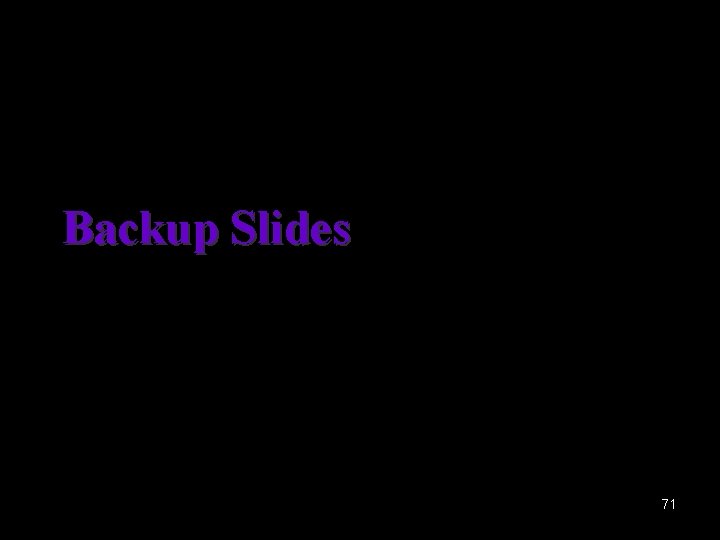
Backup Slides 71
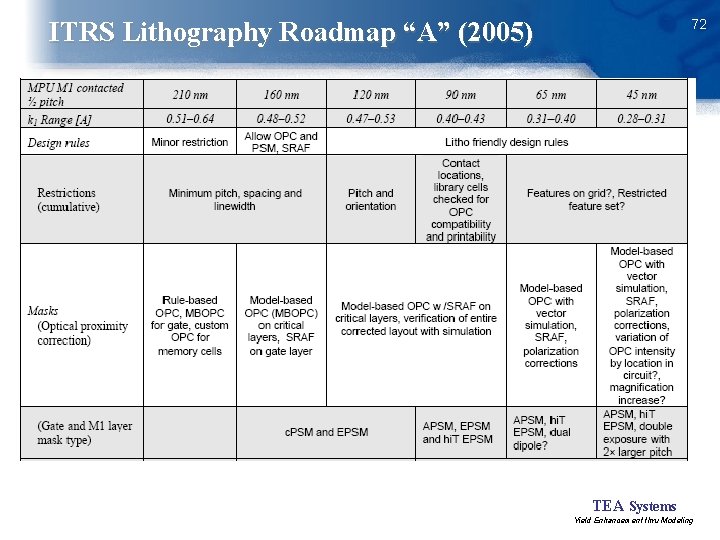
72 ITRS Lithography Roadmap “A” (2005) TEA Systems Yield Enhancement thru Modeling
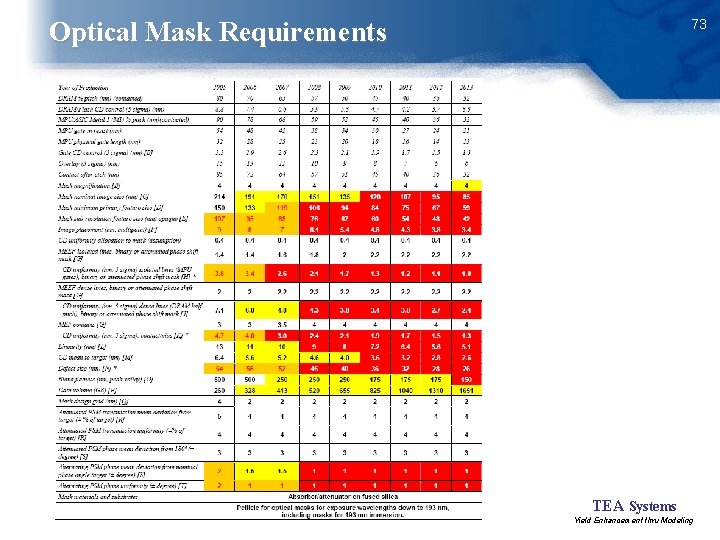
73 Optical Mask Requirements TEA Systems Yield Enhancement thru Modeling
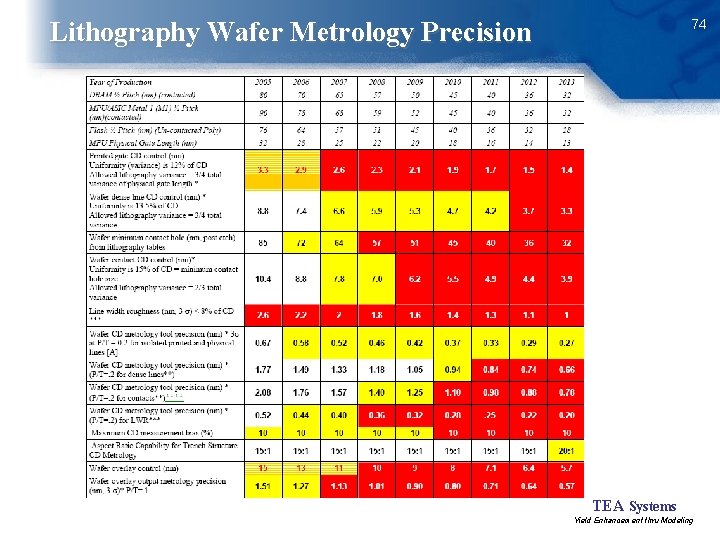
74 Lithography Wafer Metrology Precision TEA Systems Yield Enhancement thru Modeling
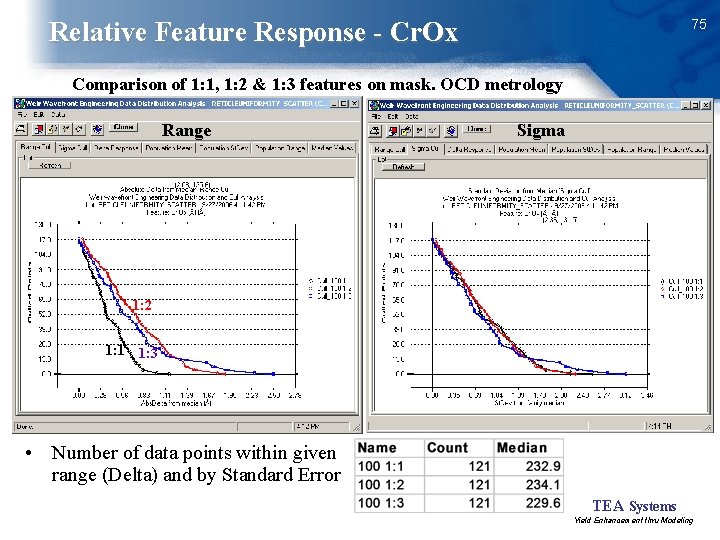
75 Relative Feature Response - Cr. Ox Comparison of 1: 1, 1: 2 & 1: 3 features on mask. OCD metrology Range Sigma 1: 2 1: 1 1: 3 • Number of data points within given range (Delta) and by Standard Error TEA Systems Yield Enhancement thru Modeling
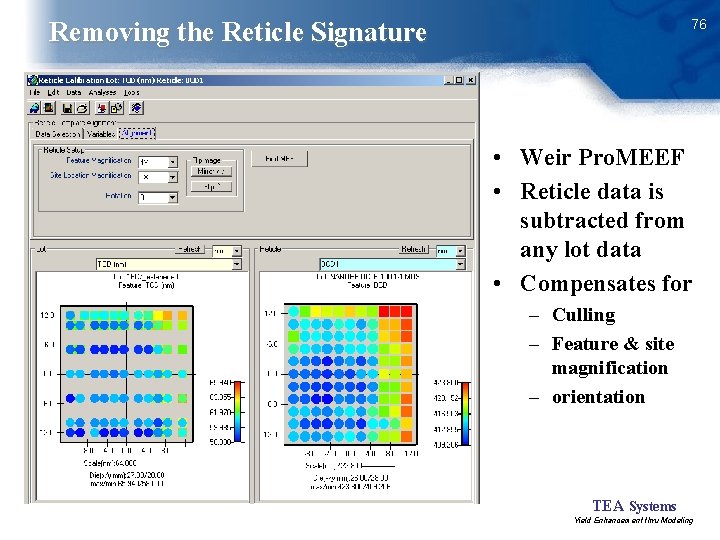
76 Removing the Reticle Signature • Weir Pro. MEEF • Reticle data is subtracted from any lot data • Compensates for – Culling – Feature & site magnification – orientation TEA Systems Yield Enhancement thru Modeling
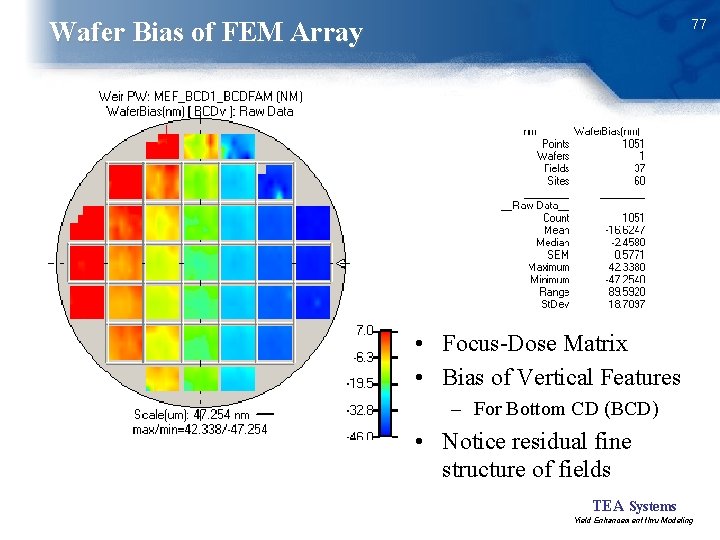
77 Wafer Bias of FEM Array • Focus-Dose Matrix • Bias of Vertical Features – For Bottom CD (BCD) • Notice residual fine structure of fields TEA Systems Yield Enhancement thru Modeling
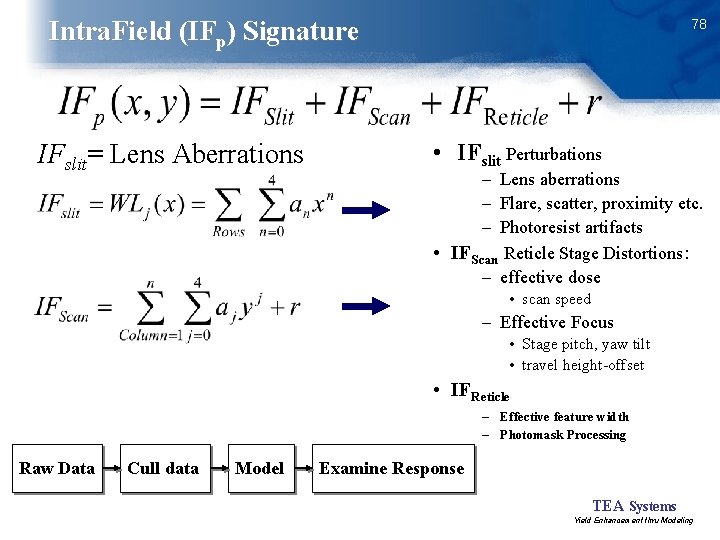
Intra. Field (IFp) Signature IFslit= Lens Aberrations 78 • IFslit Perturbations – Lens aberrations – Flare, scatter, proximity etc. – Photoresist artifacts • IFScan Reticle Stage Distortions: – effective dose • scan speed – Effective Focus • Stage pitch, yaw tilt • travel height-offset • IFReticle – Effective feature width – Photomask Processing Raw Data Cull data Model Examine Response TEA Systems Yield Enhancement thru Modeling
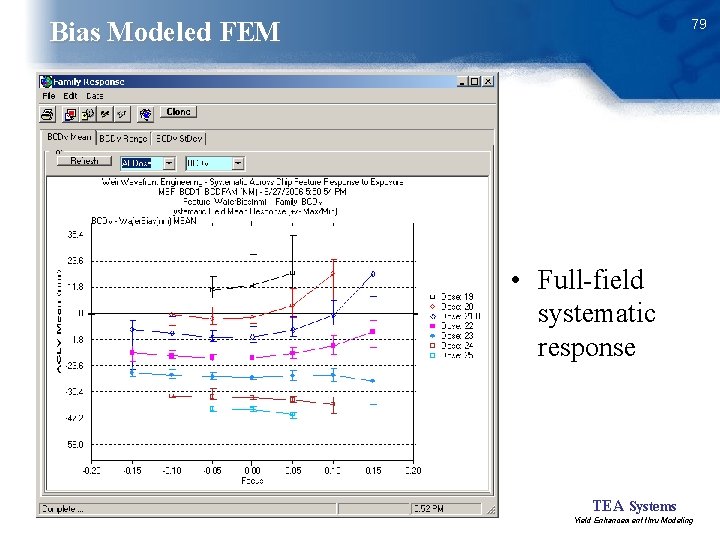
79 Bias Modeled FEM • Full-field systematic response TEA Systems Yield Enhancement thru Modeling
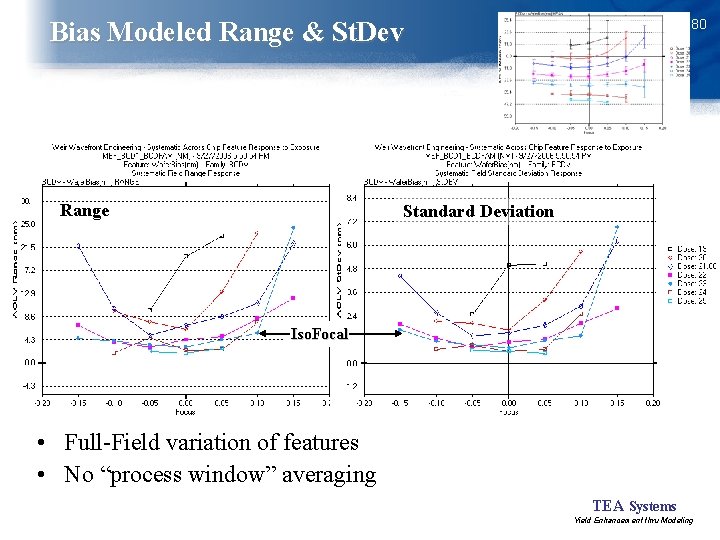
80 Bias Modeled Range & St. Dev Range Standard Deviation Iso. Focal • Full-Field variation of features • No “process window” averaging TEA Systems Yield Enhancement thru Modeling
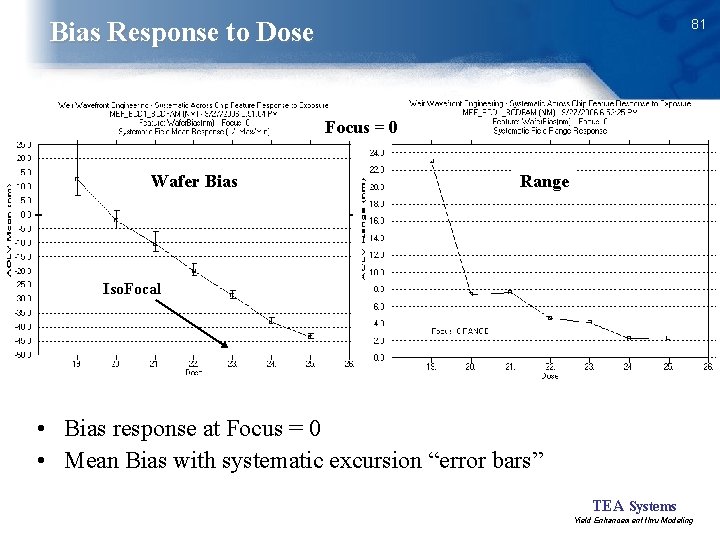
81 Bias Response to Dose Focus = 0 Wafer Bias Range Iso. Focal • Bias response at Focus = 0 • Mean Bias with systematic excursion “error bars” TEA Systems Yield Enhancement thru Modeling
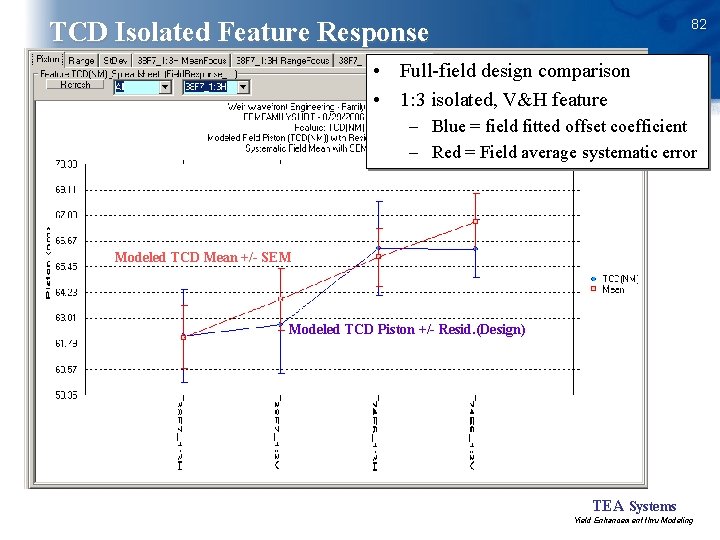
82 TCD Isolated Feature Response • Full-field design comparison • 1: 3 isolated, V&H feature – Blue = field fitted offset coefficient – Red = Field average systematic error Modeled TCD Mean +/- SEM Modeled TCD Piston +/- Resid. (Design) TEA Systems Yield Enhancement thru Modeling
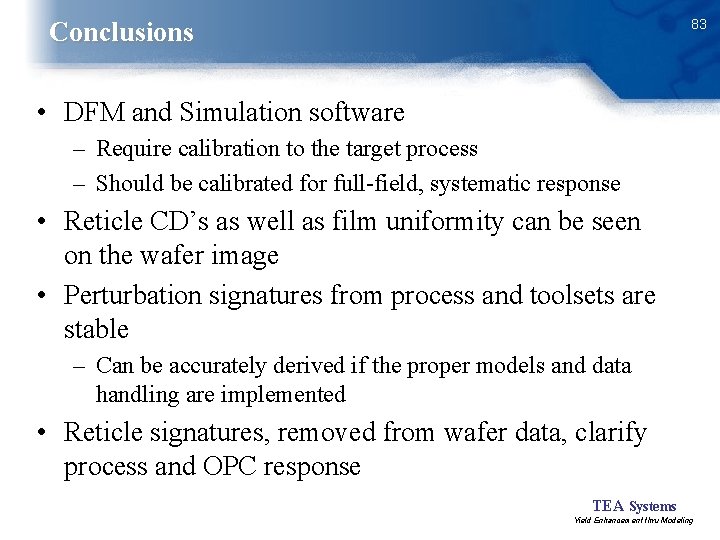
83 Conclusions • DFM and Simulation software – Require calibration to the target process – Should be calibrated for full-field, systematic response • Reticle CD’s as well as film uniformity can be seen on the wafer image • Perturbation signatures from process and toolsets are stable – Can be accurately derived if the proper models and data handling are implemented • Reticle signatures, removed from wafer data, clarify process and OPC response TEA Systems Yield Enhancement thru Modeling
- Slides: 83