Six Sigma Savings Lessons Learned and Guidelines Key
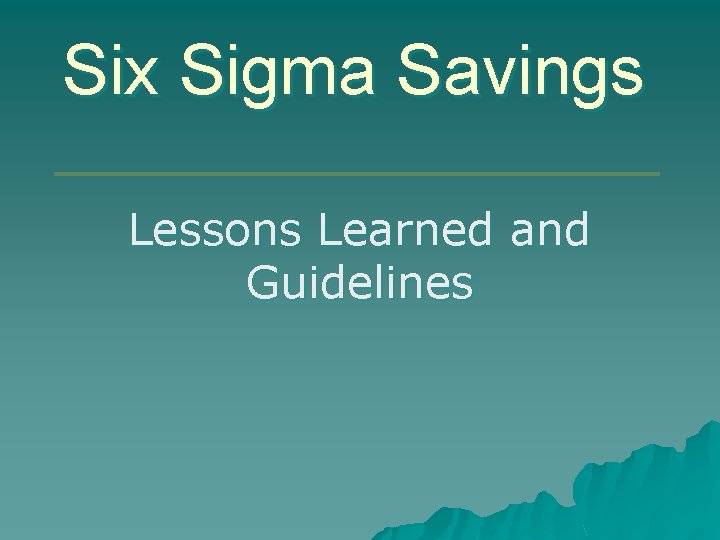
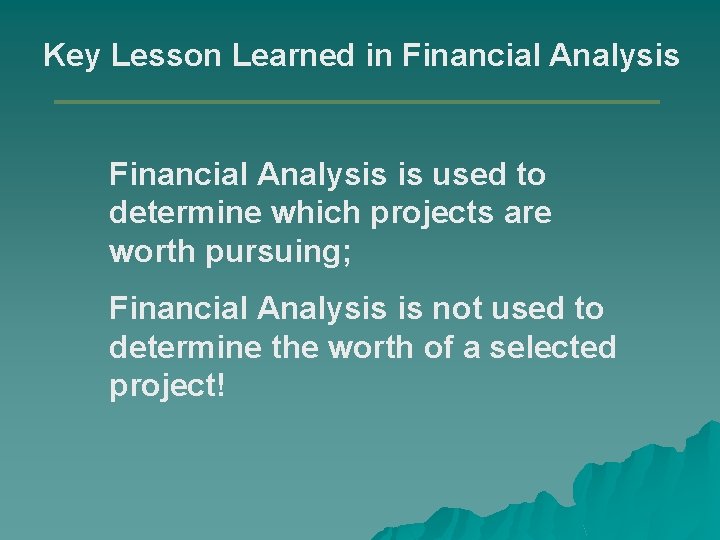
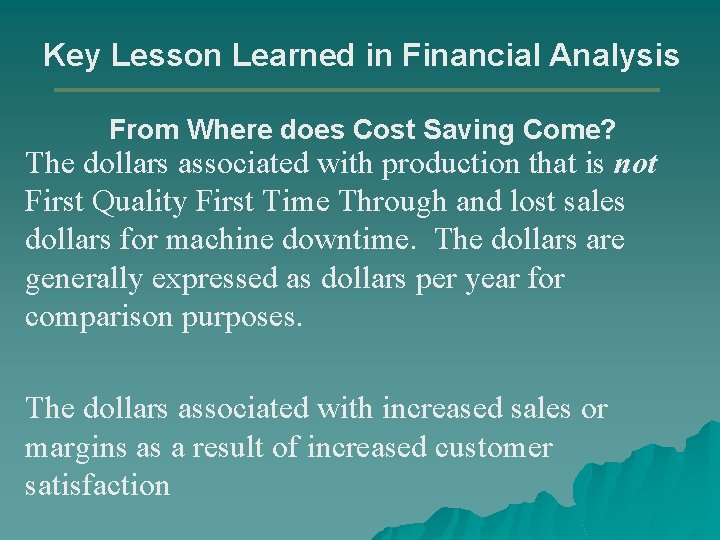
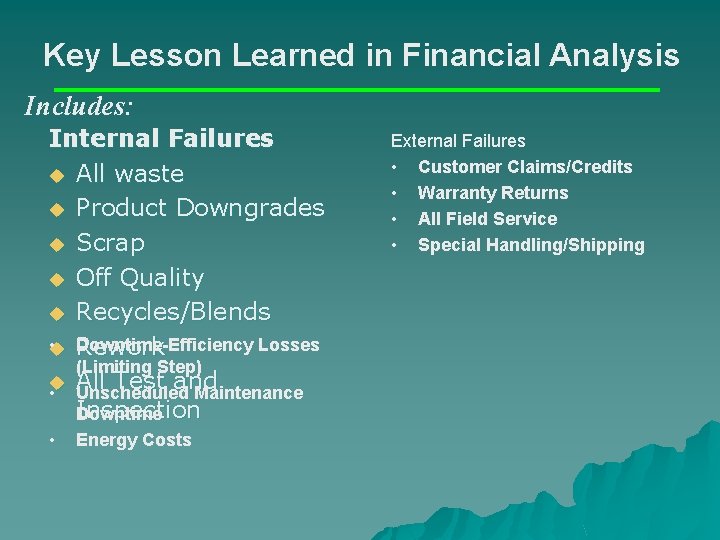
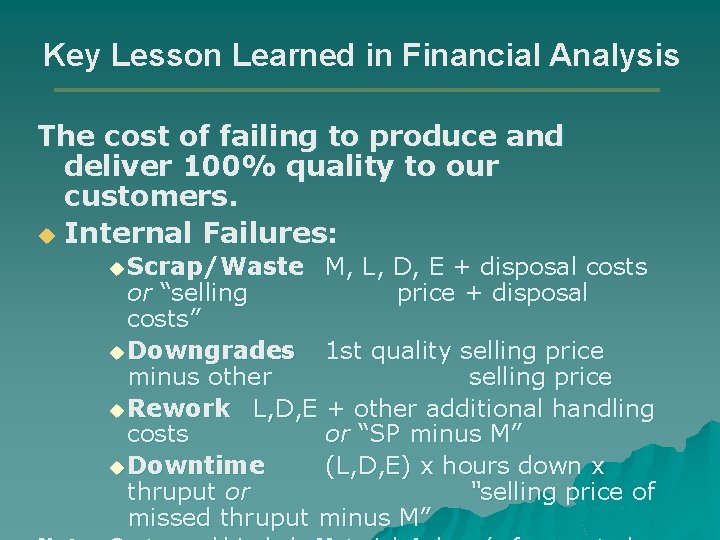
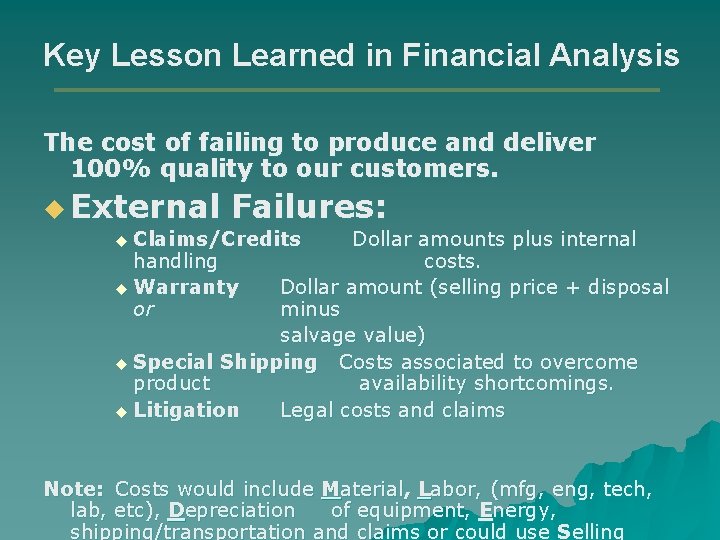
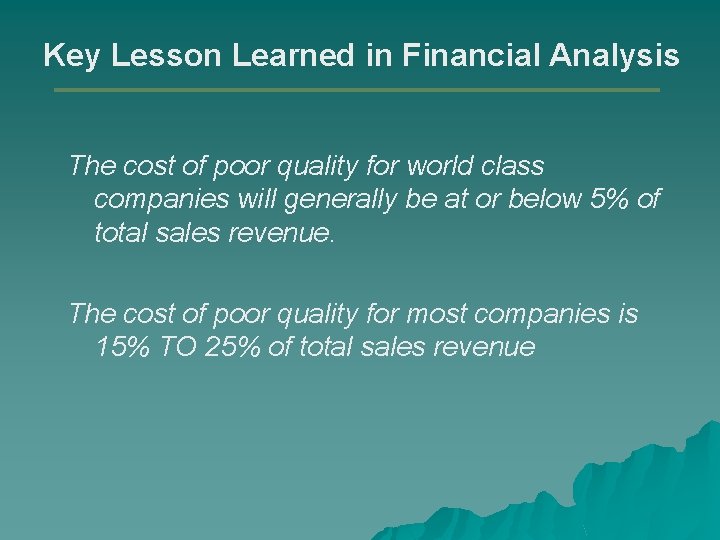
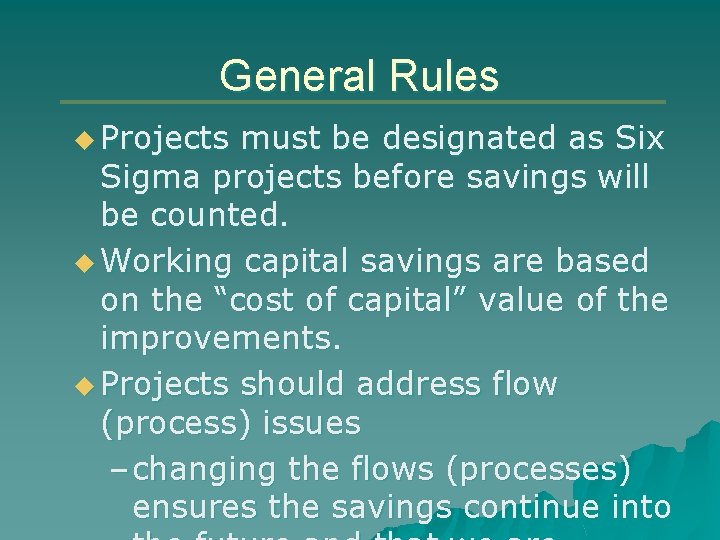
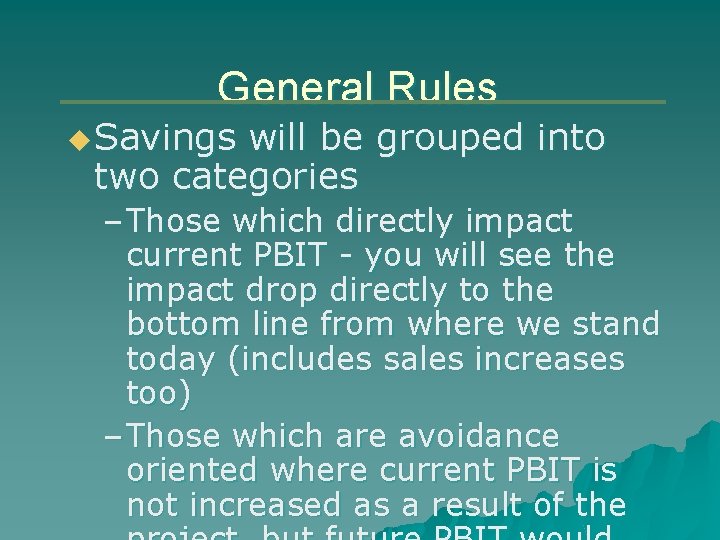
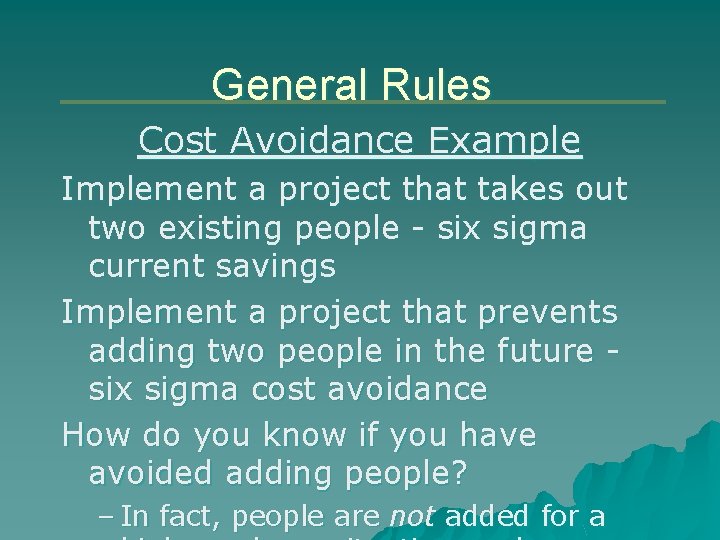
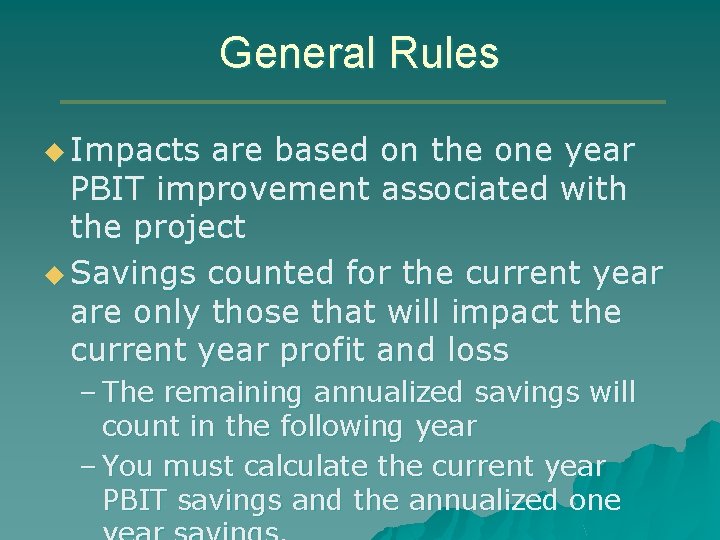
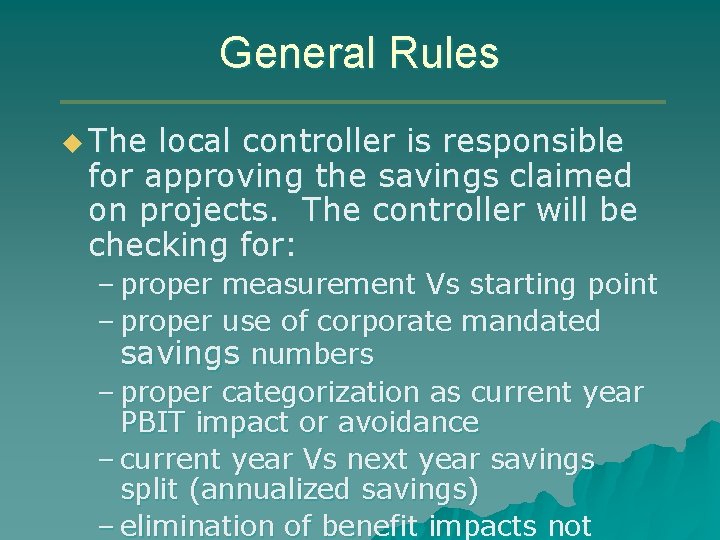

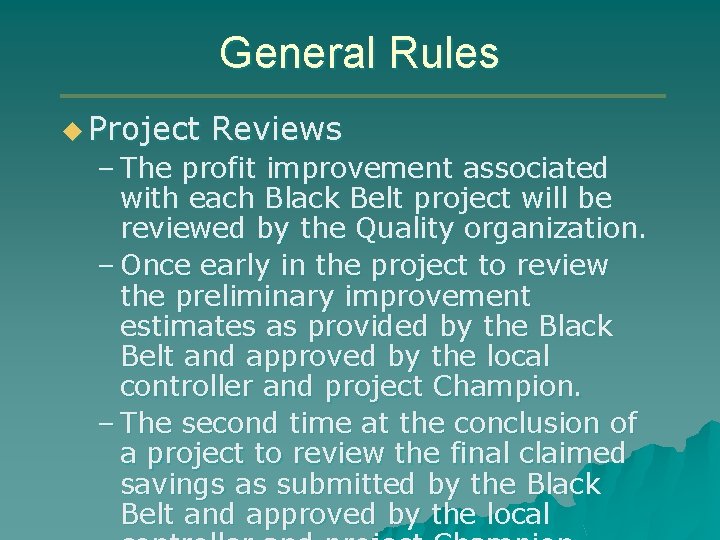
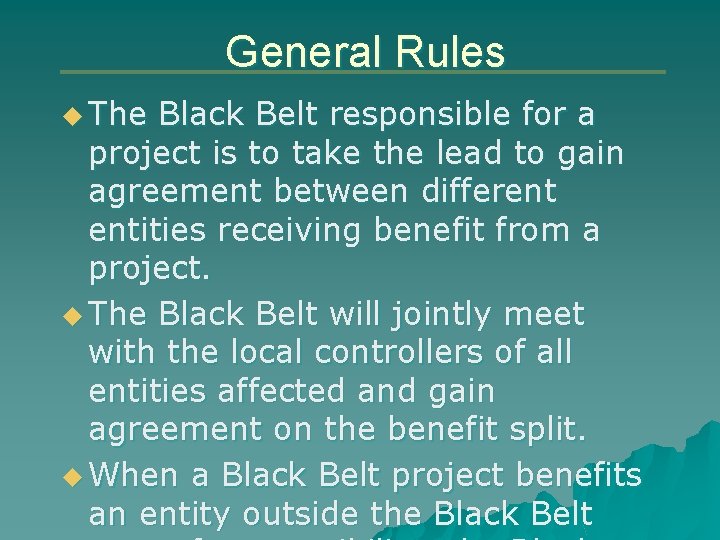
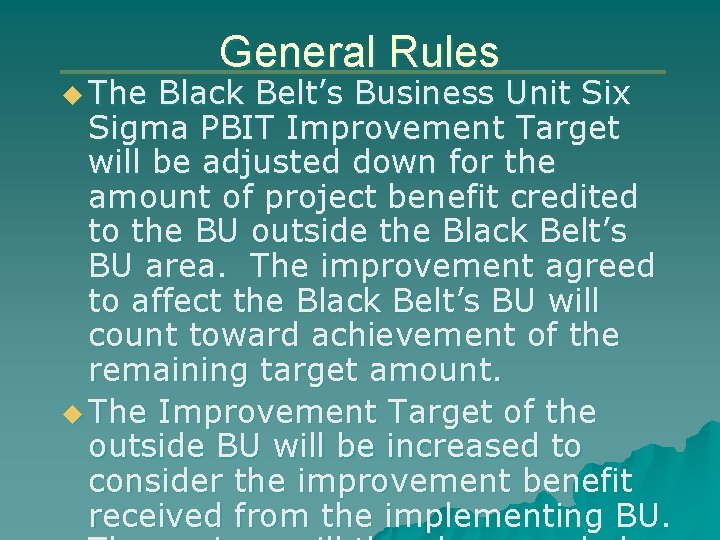
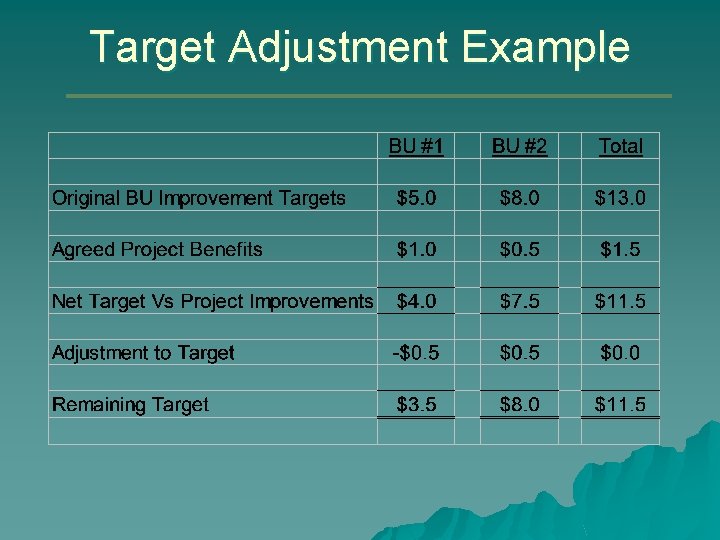
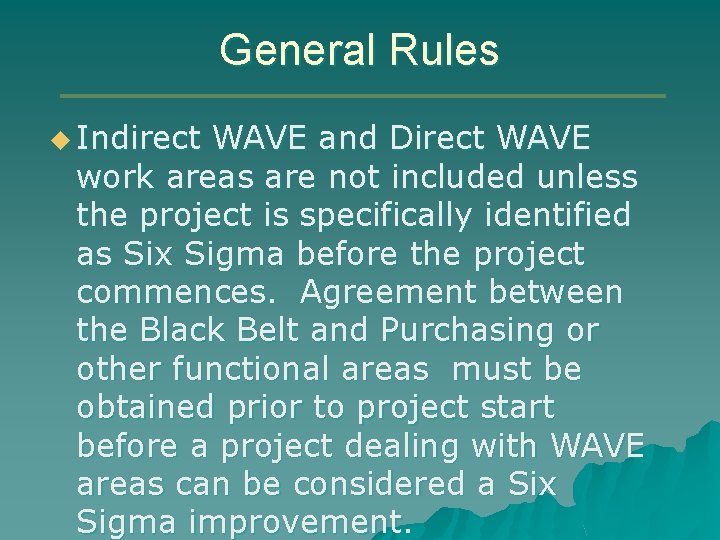
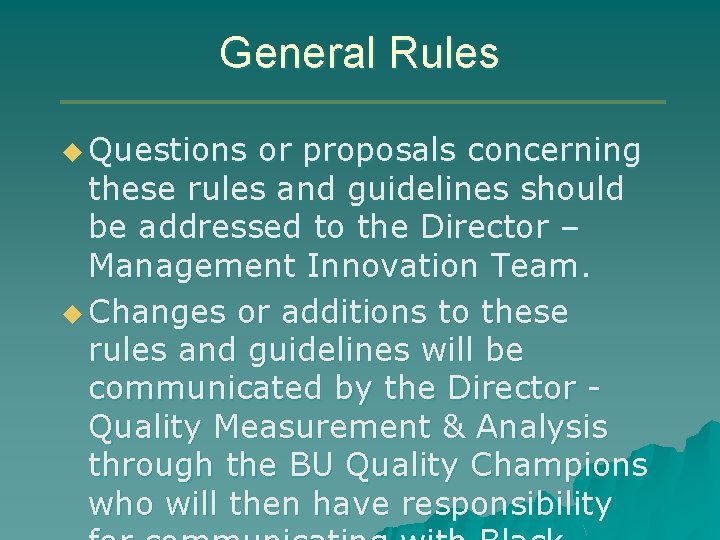
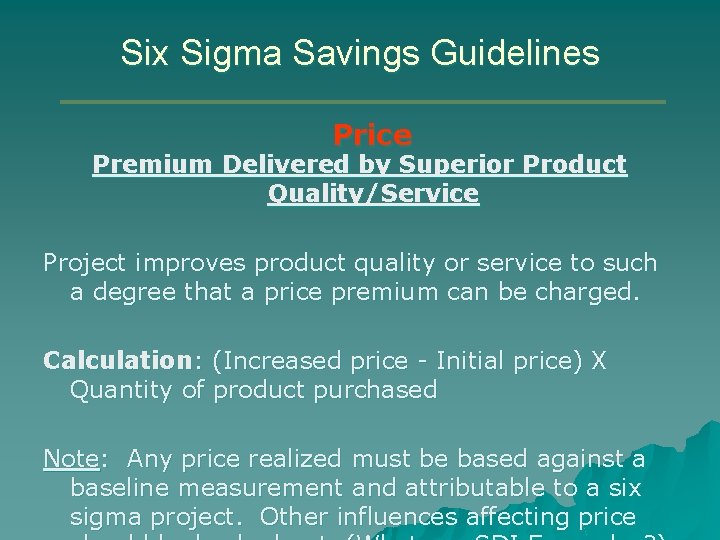
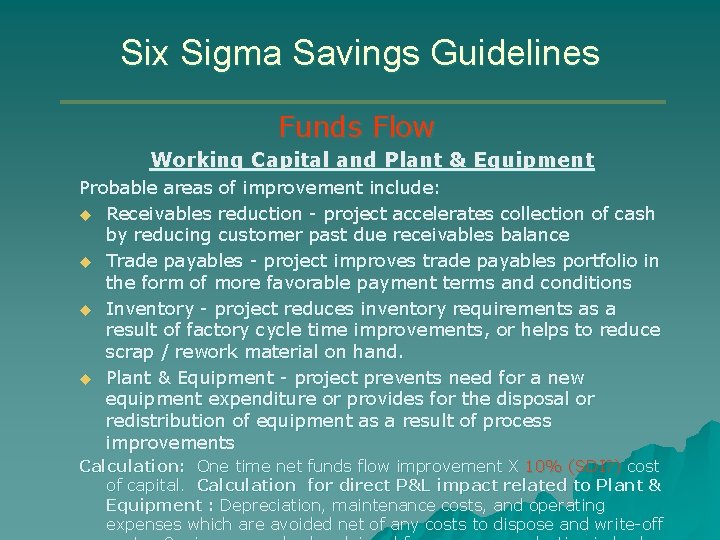
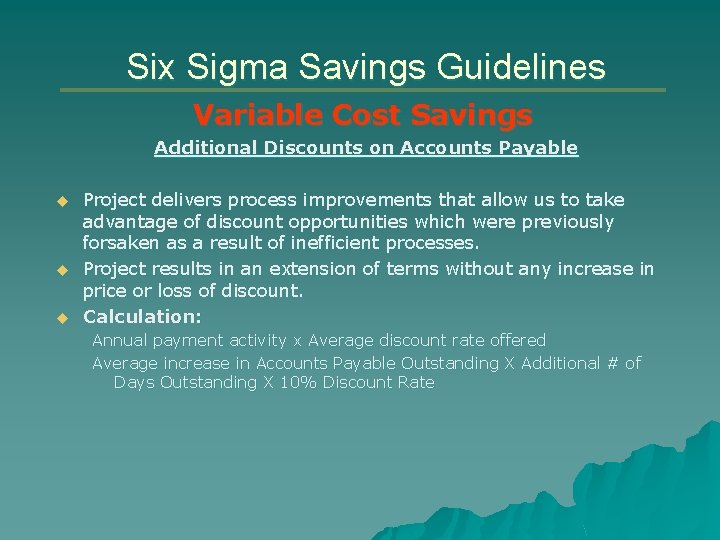
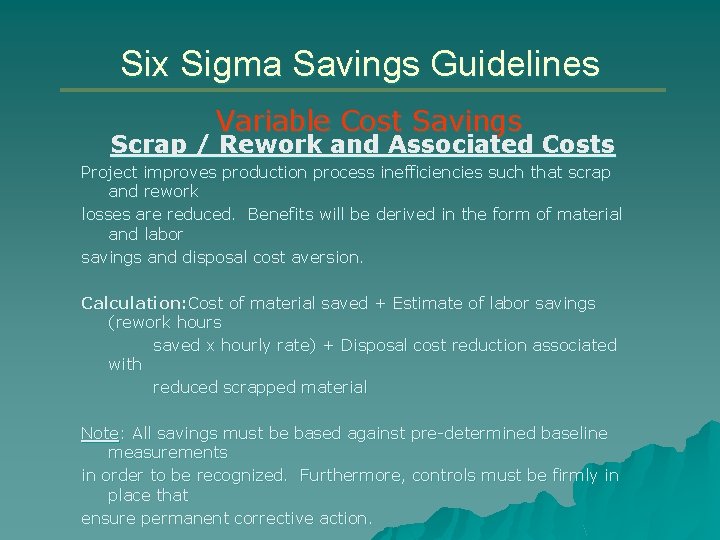
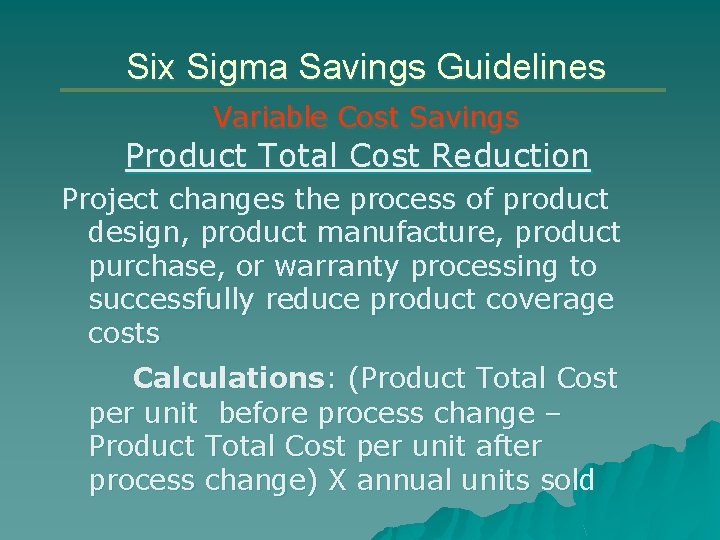
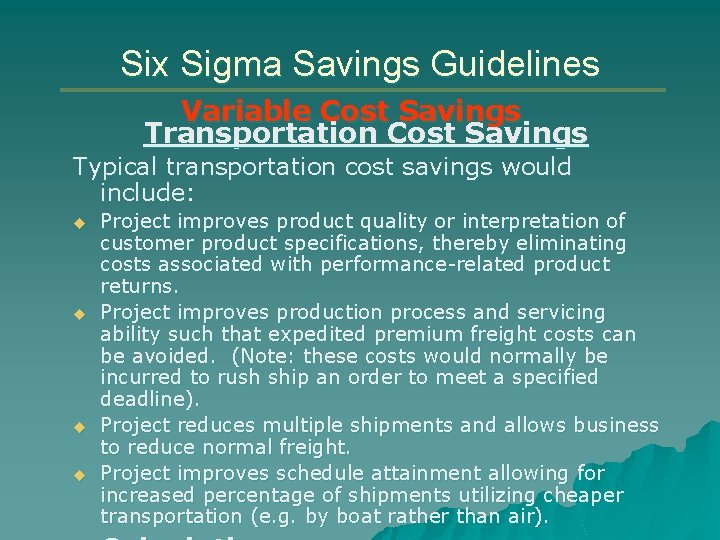
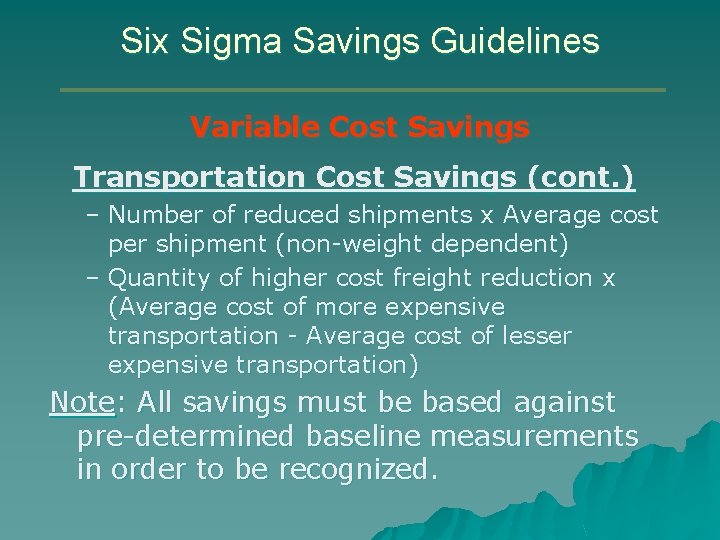
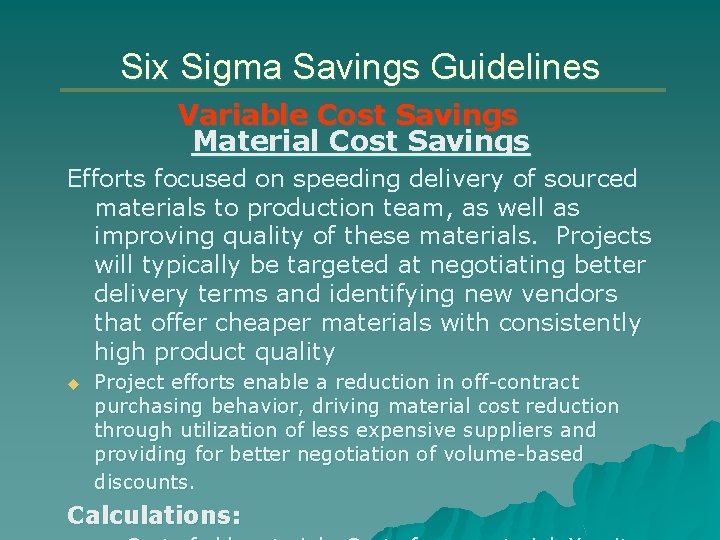
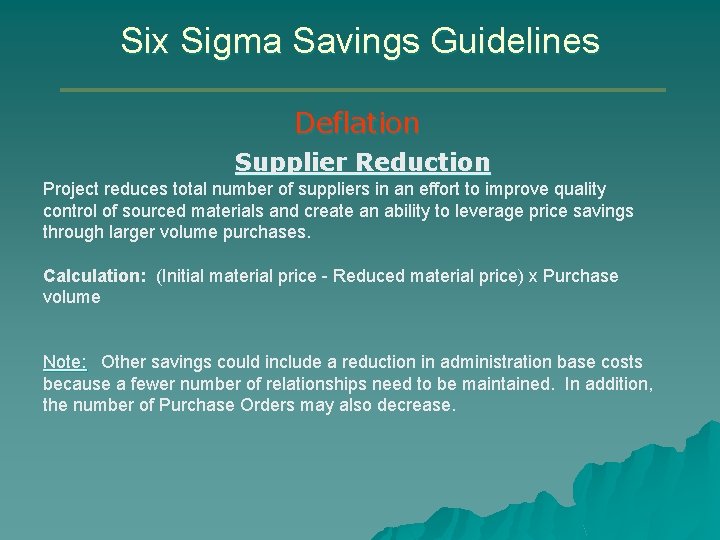
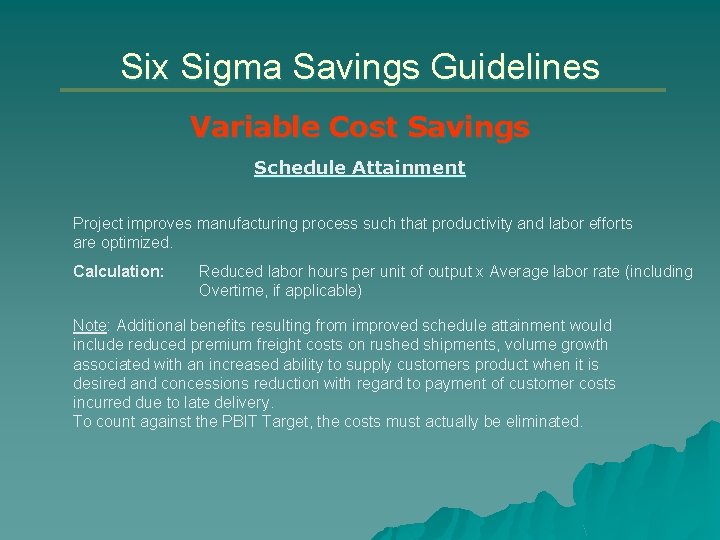
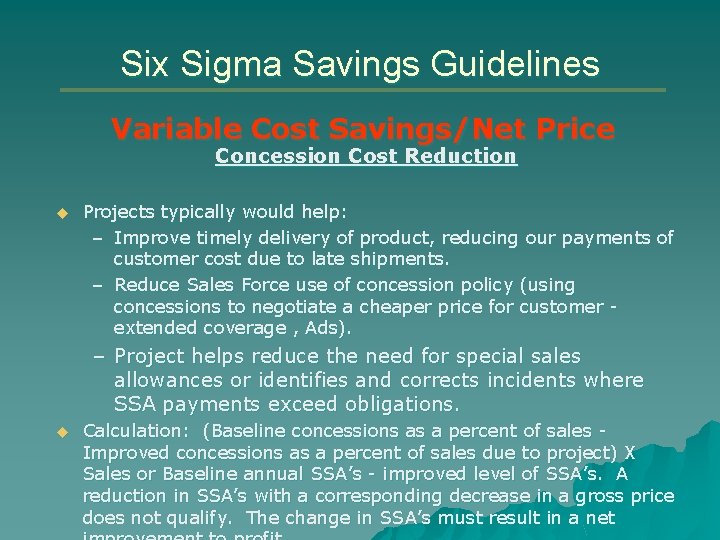
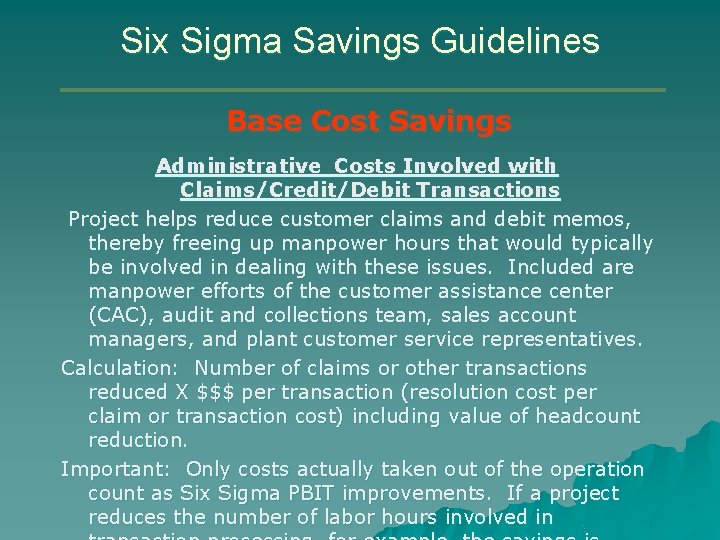
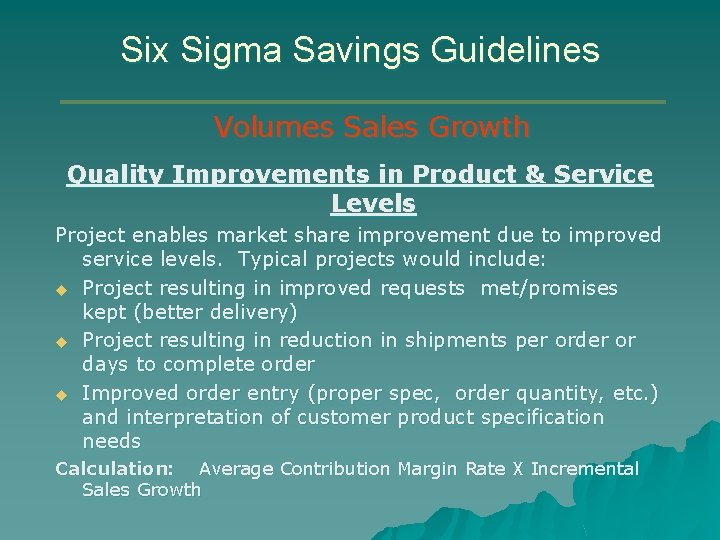
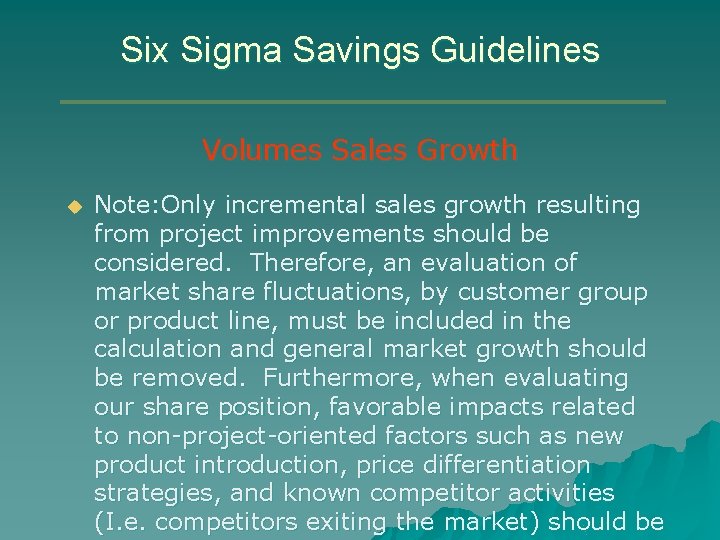
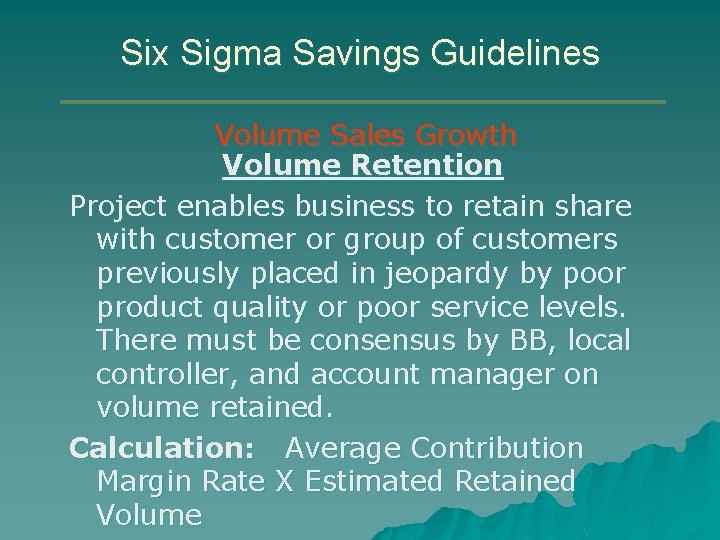
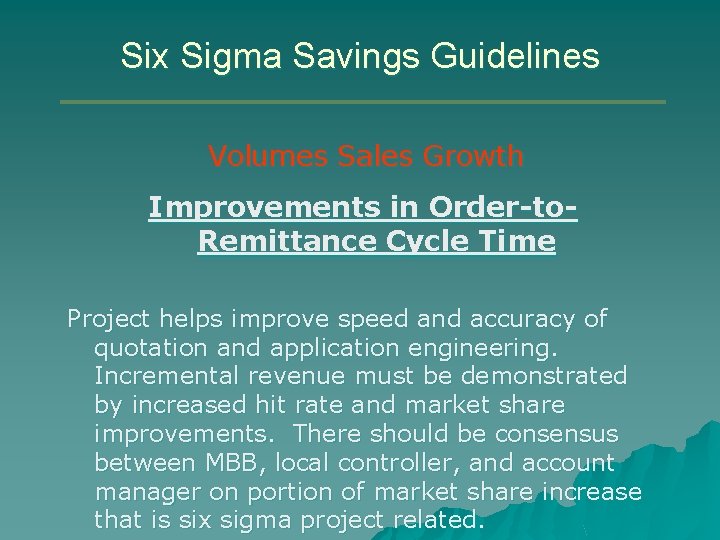
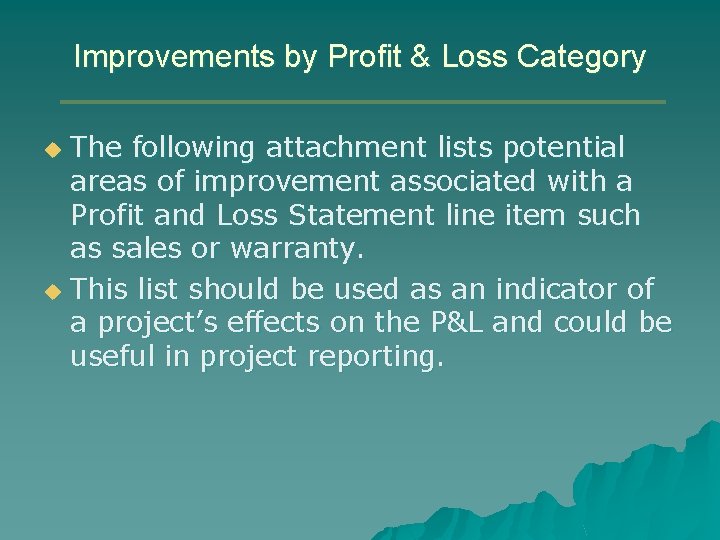
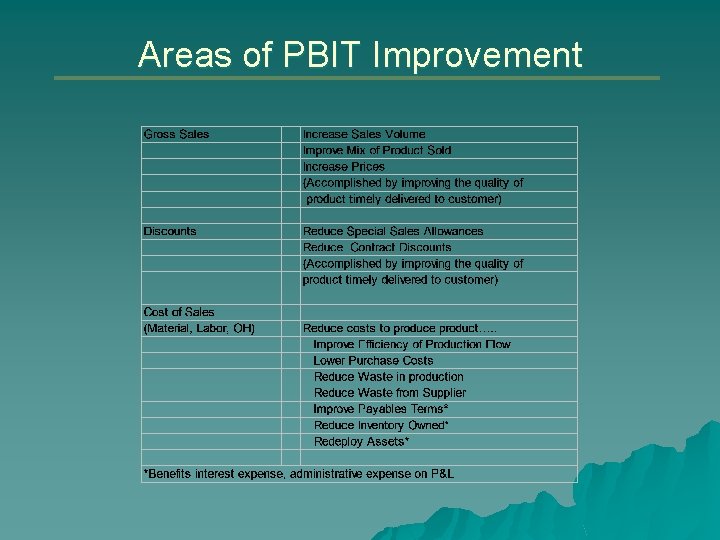
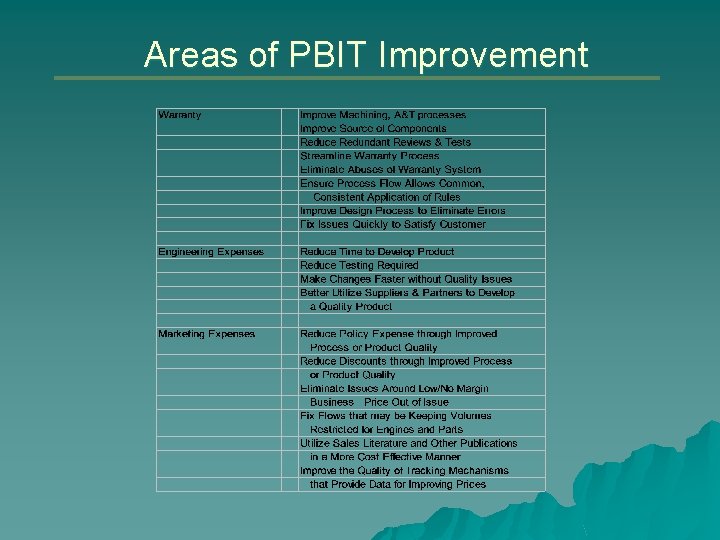
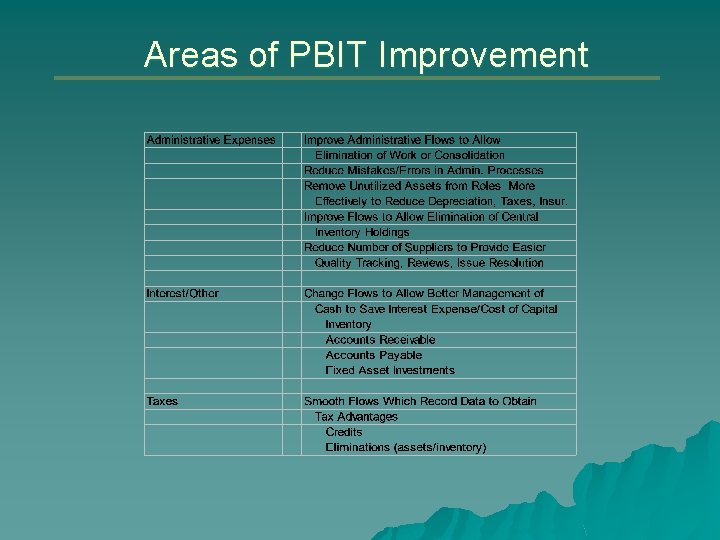
- Slides: 39
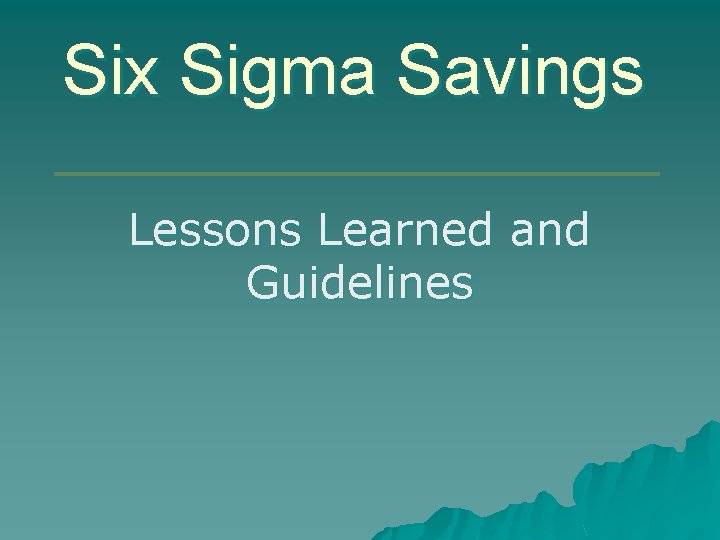
Six Sigma Savings Lessons Learned and Guidelines
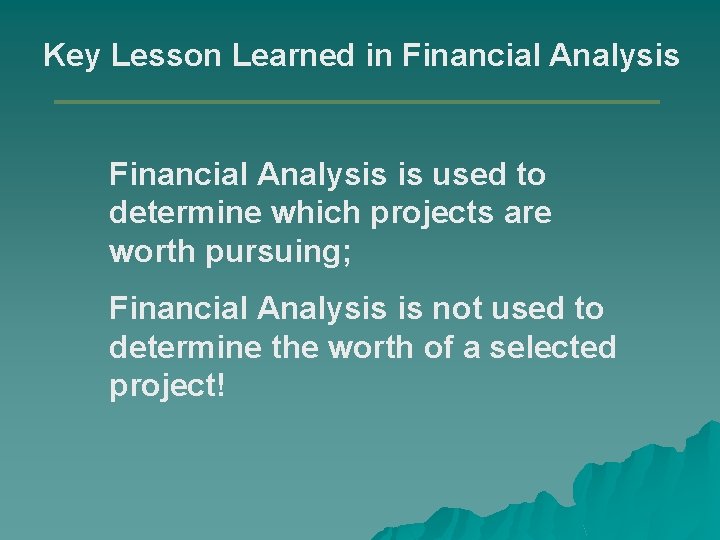
Key Lesson Learned in Financial Analysis is used to determine which projects are worth pursuing; Financial Analysis is not used to determine the worth of a selected project!
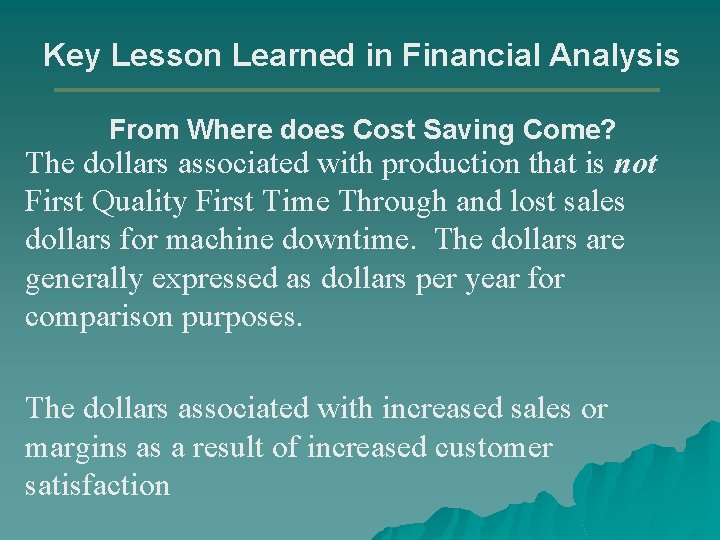
Key Lesson Learned in Financial Analysis From Where does Cost Saving Come? The dollars associated with production that is not First Quality First Time Through and lost sales dollars for machine downtime. The dollars are generally expressed as dollars per year for comparison purposes. The dollars associated with increased sales or margins as a result of increased customer satisfaction
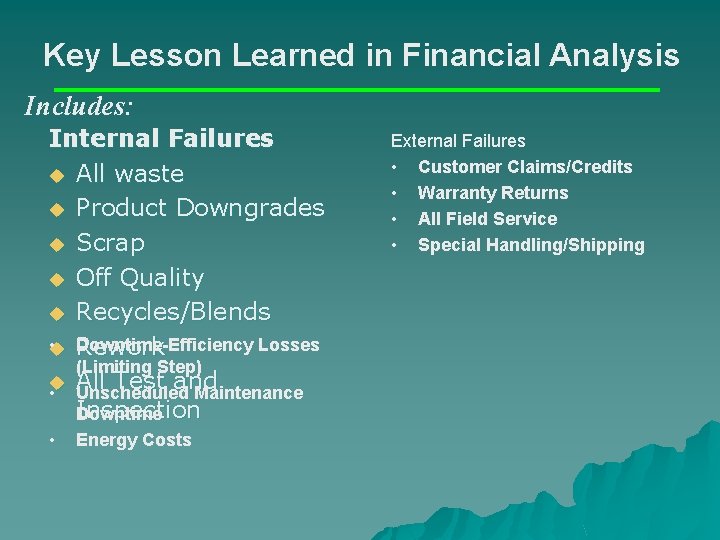
Key Lesson Learned in Financial Analysis Includes: Internal Failures u All waste u Product Downgrades u Scrap u Off Quality u Recycles/Blends • u Downtime-Efficiency Losses Rework (Limiting Step) u All Test and • Unscheduled Maintenance Inspection Downtime • Energy Costs External Failures • Customer Claims/Credits • Warranty Returns • All Field Service • Special Handling/Shipping
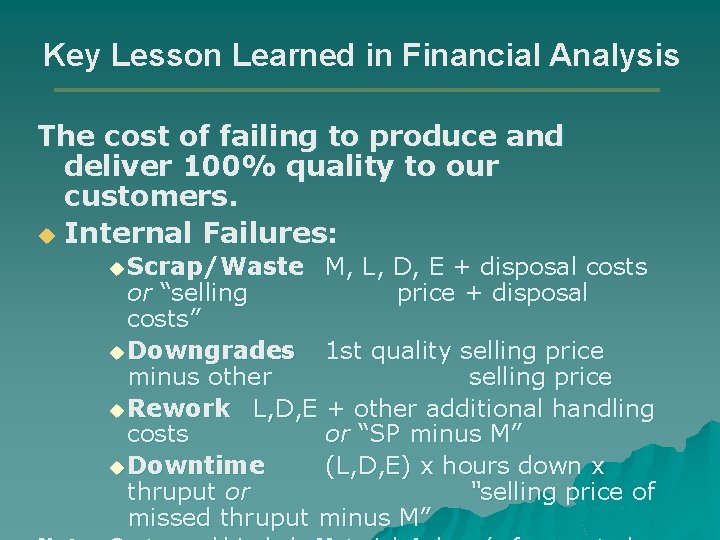
Key Lesson Learned in Financial Analysis The cost of failing to produce and deliver 100% quality to our customers. u Internal Failures: u Scrap/Waste M, L, D, E + disposal costs price + disposal or “selling costs” u Downgrades 1 st quality selling price minus other selling price u Rework L, D, E + other additional handling costs or “SP minus M” u Downtime (L, D, E) x hours down x thruput or “selling price of missed thruput minus M”
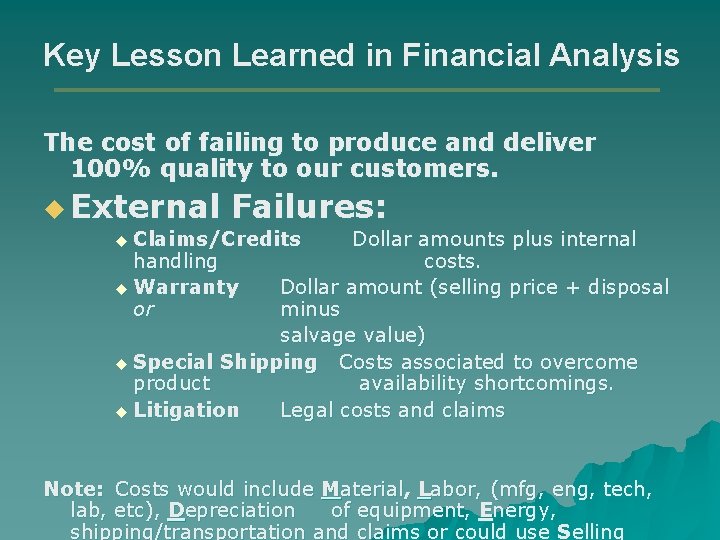
Key Lesson Learned in Financial Analysis The cost of failing to produce and deliver 100% quality to our customers. u External Failures: u Claims/Credits Dollar amounts plus internal handling costs. u Warranty Dollar amount (selling price + disposal or minus salvage value) u Special Shipping Costs associated to overcome product availability shortcomings. u Litigation Legal costs and claims Note: Costs would include Material, Labor, (mfg, eng, tech, lab, etc), Depreciation of equipment, Energy, shipping/transportation and claims or could use Selling
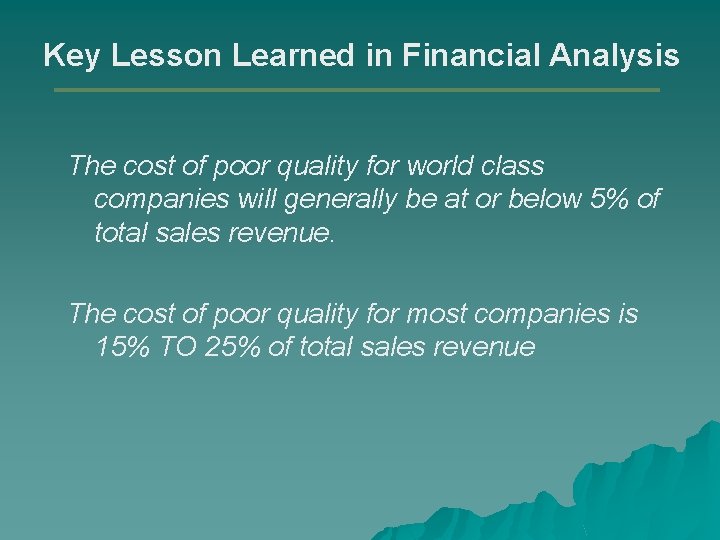
Key Lesson Learned in Financial Analysis The cost of poor quality for world class companies will generally be at or below 5% of total sales revenue. The cost of poor quality for most companies is 15% TO 25% of total sales revenue
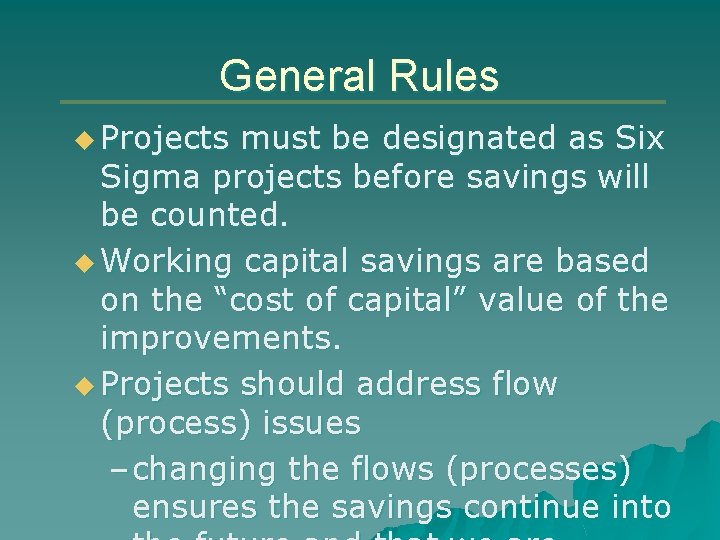
General Rules u Projects must be designated as Six Sigma projects before savings will be counted. u Working capital savings are based on the “cost of capital” value of the improvements. u Projects should address flow (process) issues – changing the flows (processes) ensures the savings continue into
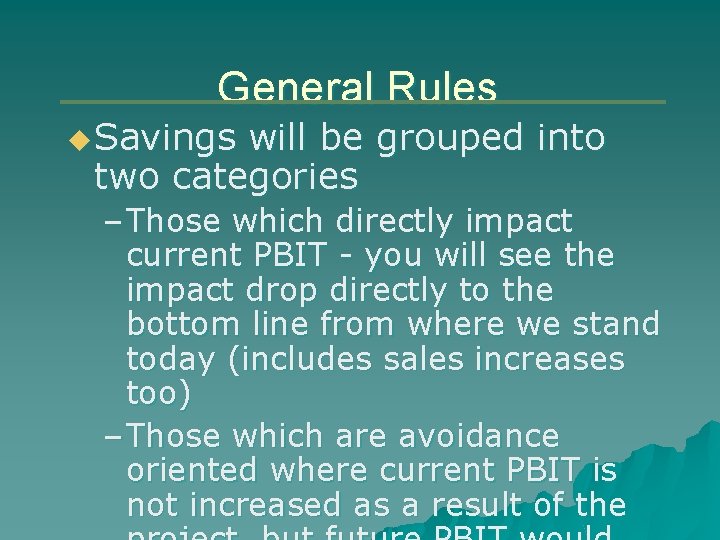
General Rules u Savings will be grouped into two categories – Those which directly impact current PBIT - you will see the impact drop directly to the bottom line from where we stand today (includes sales increases too) – Those which are avoidance oriented where current PBIT is not increased as a result of the
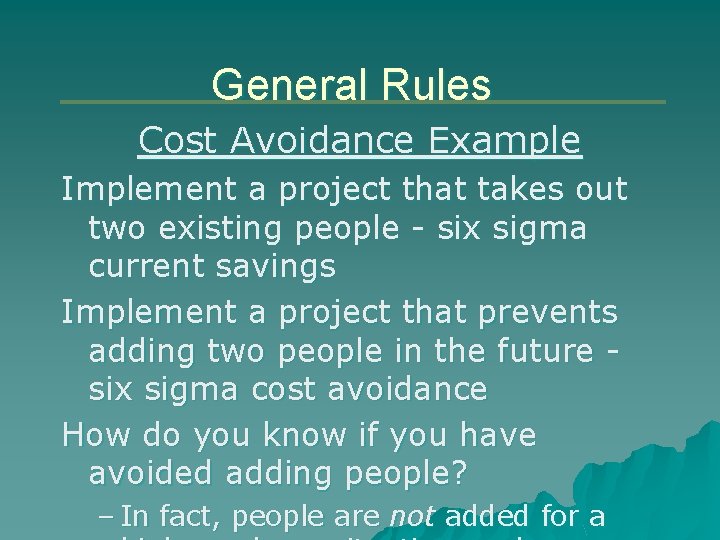
General Rules Cost Avoidance Example Implement a project that takes out two existing people - six sigma current savings Implement a project that prevents adding two people in the future six sigma cost avoidance How do you know if you have avoided adding people? – In fact, people are not added for a
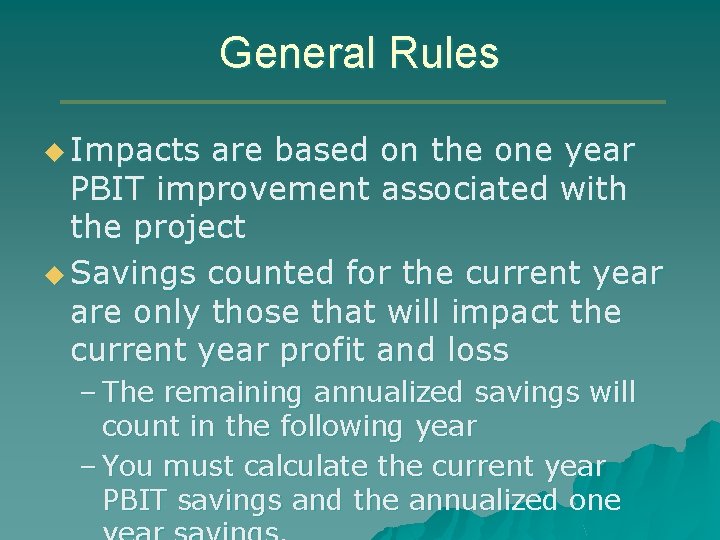
General Rules u Impacts are based on the one year PBIT improvement associated with the project u Savings counted for the current year are only those that will impact the current year profit and loss – The remaining annualized savings will count in the following year – You must calculate the current year PBIT savings and the annualized one
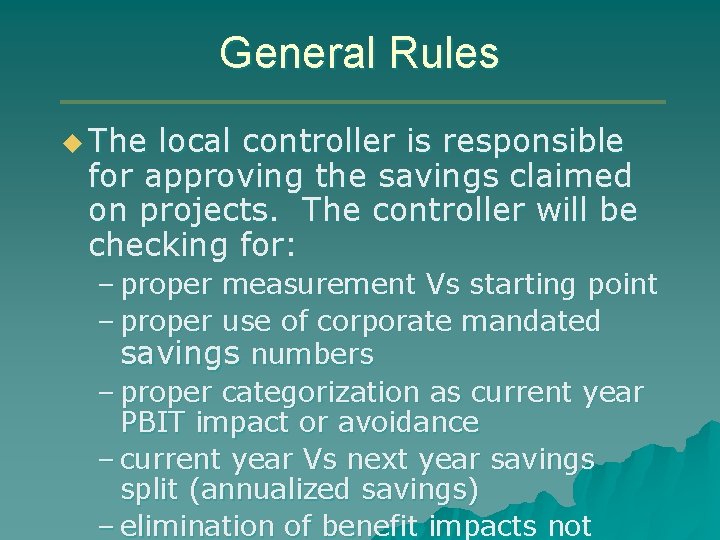
General Rules u The local controller is responsible for approving the savings claimed on projects. The controller will be checking for: – proper measurement Vs starting point – proper use of corporate mandated savings numbers – proper categorization as current year PBIT impact or avoidance – current year Vs next year savings split (annualized savings) – elimination of benefit impacts not

General Rules u Controller Responsibility cont’d – The local controller is responsible for reviewing the savings estimates claimed on Project Charters within the first two weeks of the project start date. – The controller should sign the Project Charter as evidence of such review and agreement with estimated savings. – At the conclusion of a project, the controller is responsible for approval of the final savings determination for a local project. By signing off on a
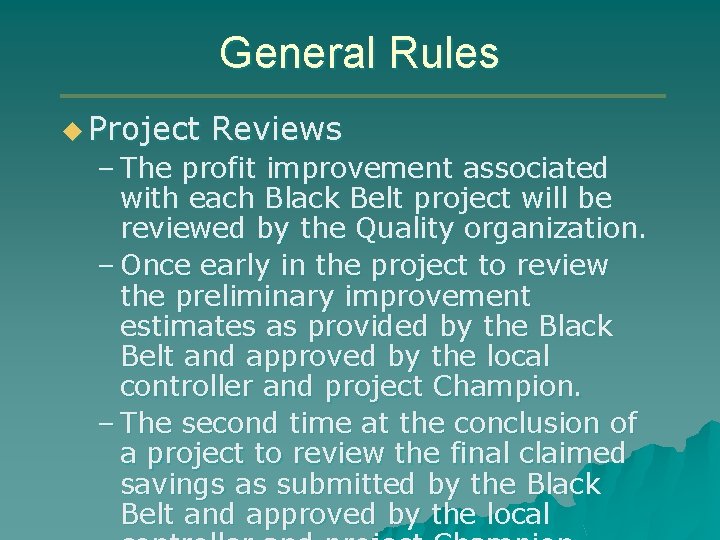
General Rules u Project Reviews – The profit improvement associated with each Black Belt project will be reviewed by the Quality organization. – Once early in the project to review the preliminary improvement estimates as provided by the Black Belt and approved by the local controller and project Champion. – The second time at the conclusion of a project to review the final claimed savings as submitted by the Black Belt and approved by the local
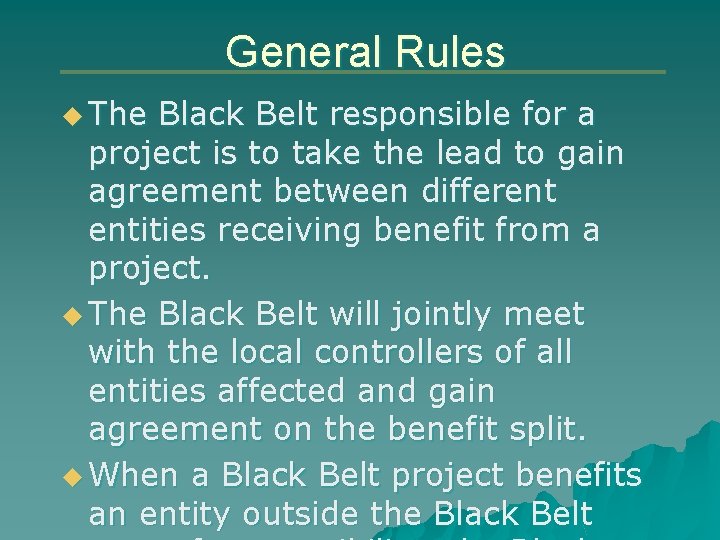
General Rules u The Black Belt responsible for a project is to take the lead to gain agreement between different entities receiving benefit from a project. u The Black Belt will jointly meet with the local controllers of all entities affected and gain agreement on the benefit split. u When a Black Belt project benefits an entity outside the Black Belt
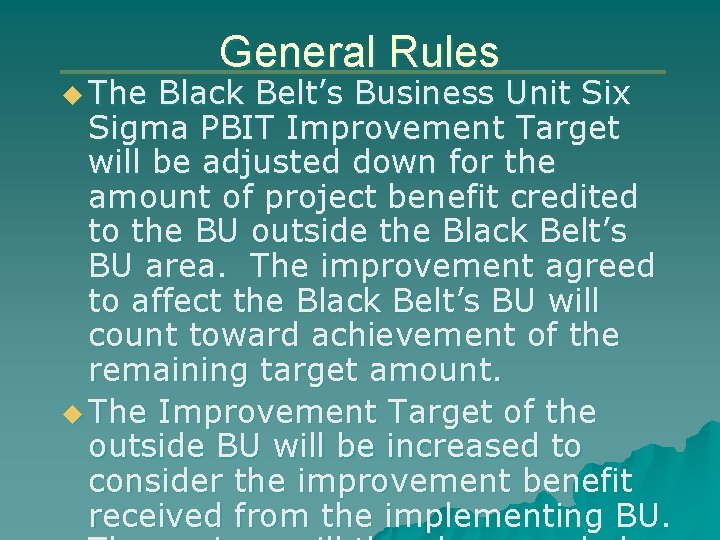
u The General Rules Black Belt’s Business Unit Six Sigma PBIT Improvement Target will be adjusted down for the amount of project benefit credited to the BU outside the Black Belt’s BU area. The improvement agreed to affect the Black Belt’s BU will count toward achievement of the remaining target amount. u The Improvement Target of the outside BU will be increased to consider the improvement benefit received from the implementing BU.
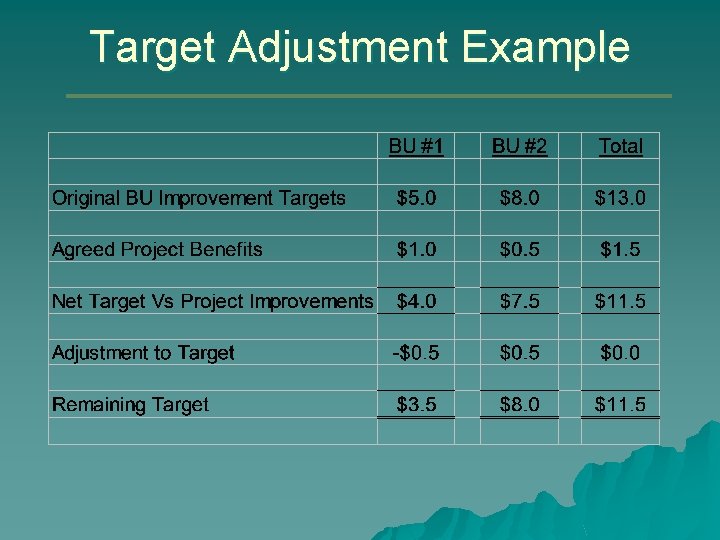
Target Adjustment Example
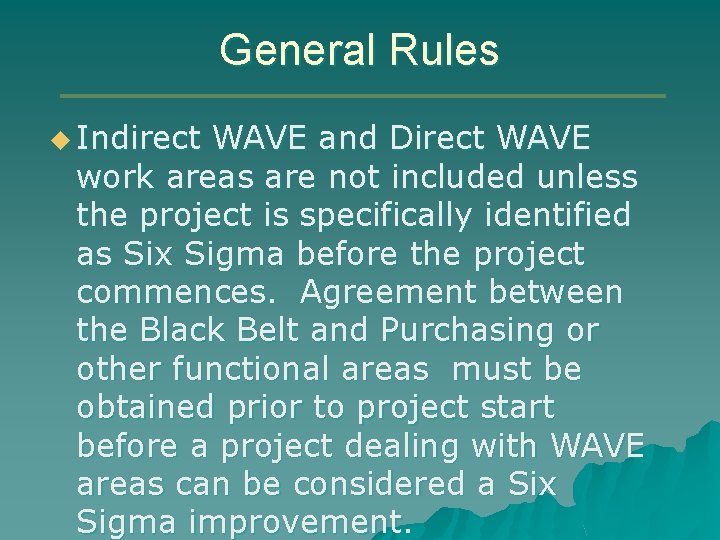
General Rules u Indirect WAVE and Direct WAVE work areas are not included unless the project is specifically identified as Six Sigma before the project commences. Agreement between the Black Belt and Purchasing or other functional areas must be obtained prior to project start before a project dealing with WAVE areas can be considered a Six Sigma improvement.
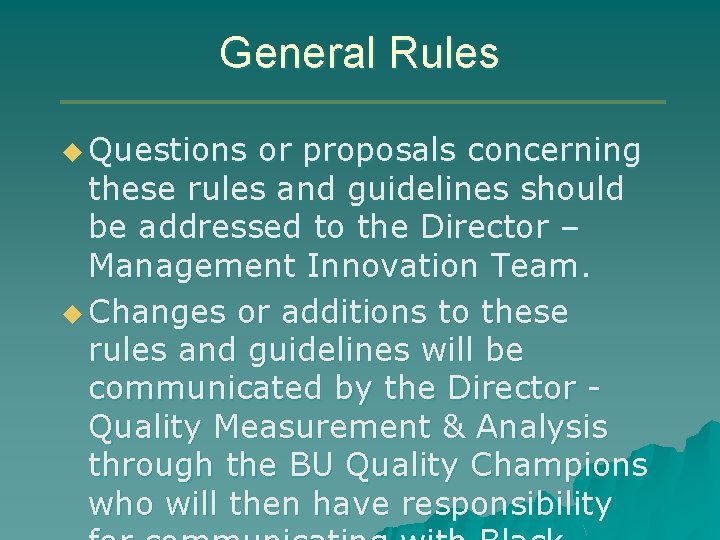
General Rules u Questions or proposals concerning these rules and guidelines should be addressed to the Director – Management Innovation Team. u Changes or additions to these rules and guidelines will be communicated by the Director Quality Measurement & Analysis through the BU Quality Champions who will then have responsibility
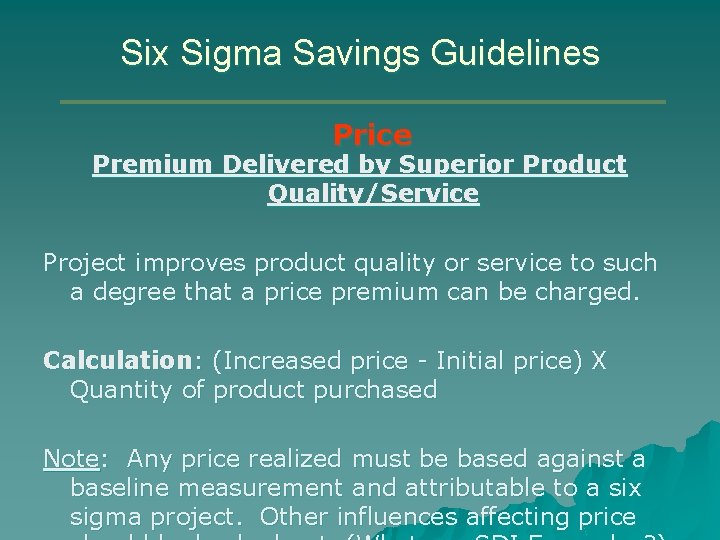
Six Sigma Savings Guidelines Price Premium Delivered by Superior Product Quality/Service Project improves product quality or service to such a degree that a price premium can be charged. Calculation: (Increased price - Initial price) X Quantity of product purchased Note: Any price realized must be based against a baseline measurement and attributable to a six sigma project. Other influences affecting price
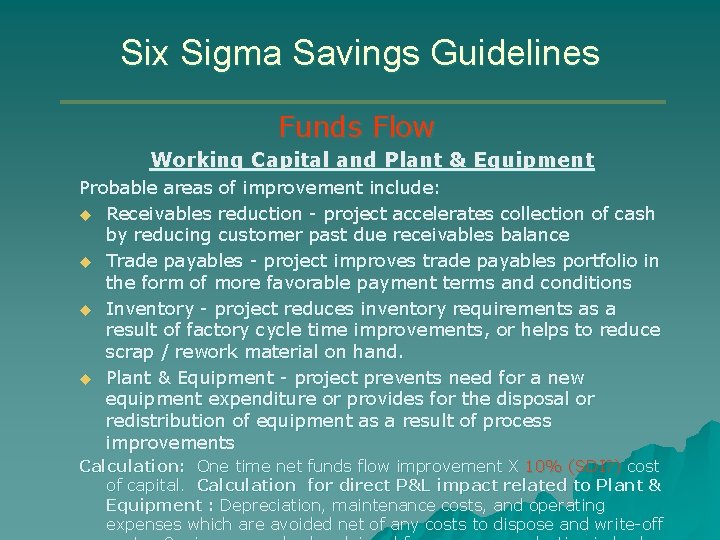
Six Sigma Savings Guidelines Funds Flow Working Capital and Plant & Equipment Probable areas of improvement include: u Receivables reduction - project accelerates collection of cash by reducing customer past due receivables balance u Trade payables - project improves trade payables portfolio in the form of more favorable payment terms and conditions u Inventory - project reduces inventory requirements as a result of factory cycle time improvements, or helps to reduce scrap / rework material on hand. u Plant & Equipment - project prevents need for a new equipment expenditure or provides for the disposal or redistribution of equipment as a result of process improvements Calculation: One time net funds flow improvement X 10% (SDI? ) cost of capital. Calculation for direct P&L impact related to Plant & Equipment : Depreciation, maintenance costs, and operating expenses which are avoided net of any costs to dispose and write-off
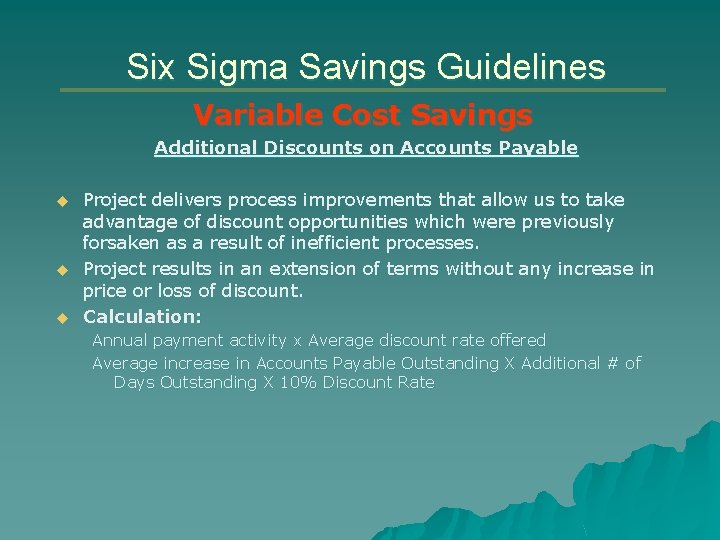
Six Sigma Savings Guidelines Variable Cost Savings Additional Discounts on Accounts Payable u u u Project delivers process improvements that allow us to take advantage of discount opportunities which were previously forsaken as a result of inefficient processes. Project results in an extension of terms without any increase in price or loss of discount. Calculation: Annual payment activity x Average discount rate offered Average increase in Accounts Payable Outstanding X Additional # of Days Outstanding X 10% Discount Rate
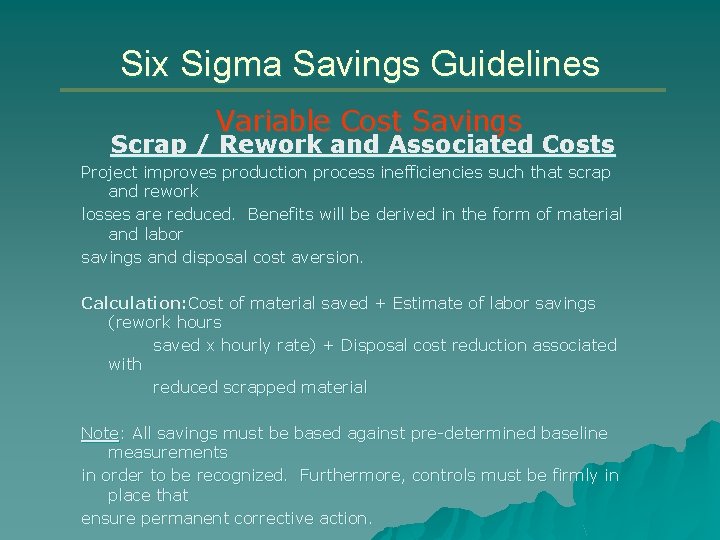
Six Sigma Savings Guidelines Variable Cost Savings Scrap / Rework and Associated Costs Project improves production process inefficiencies such that scrap and rework losses are reduced. Benefits will be derived in the form of material and labor savings and disposal cost aversion. Calculation: Cost of material saved + Estimate of labor savings (rework hours saved x hourly rate) + Disposal cost reduction associated with reduced scrapped material Note: All savings must be based against pre-determined baseline measurements in order to be recognized. Furthermore, controls must be firmly in place that ensure permanent corrective action.
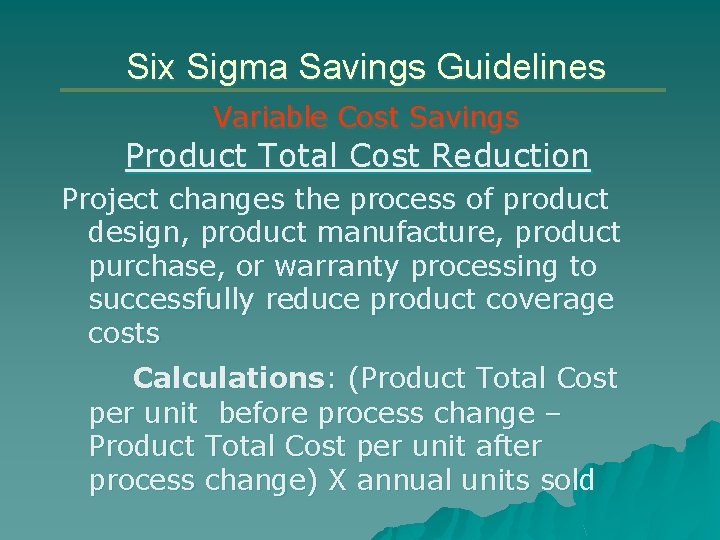
Six Sigma Savings Guidelines Variable Cost Savings Product Total Cost Reduction Project changes the process of product design, product manufacture, product purchase, or warranty processing to successfully reduce product coverage costs Calculations: (Product Total Cost per unit before process change – Product Total Cost per unit after process change) X annual units sold
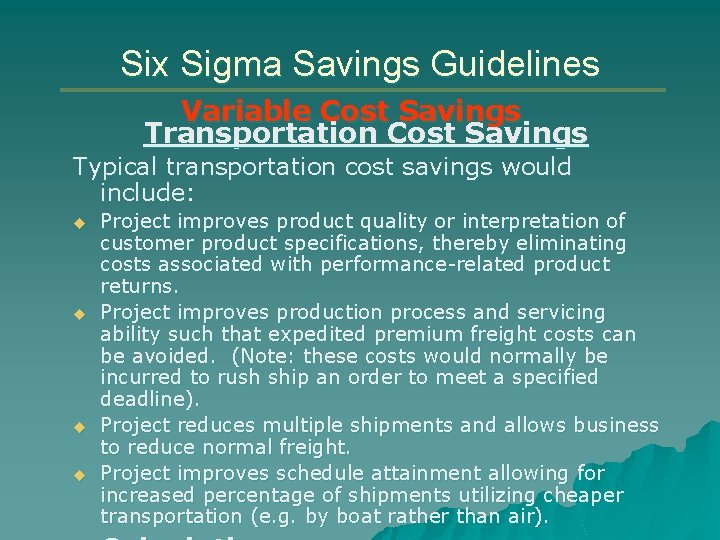
Six Sigma Savings Guidelines Variable Cost Savings Transportation Cost Savings Typical transportation cost savings would include: u u Project improves product quality or interpretation of customer product specifications, thereby eliminating costs associated with performance-related product returns. Project improves production process and servicing ability such that expedited premium freight costs can be avoided. (Note: these costs would normally be incurred to rush ship an order to meet a specified deadline). Project reduces multiple shipments and allows business to reduce normal freight. Project improves schedule attainment allowing for increased percentage of shipments utilizing cheaper transportation (e. g. by boat rather than air).
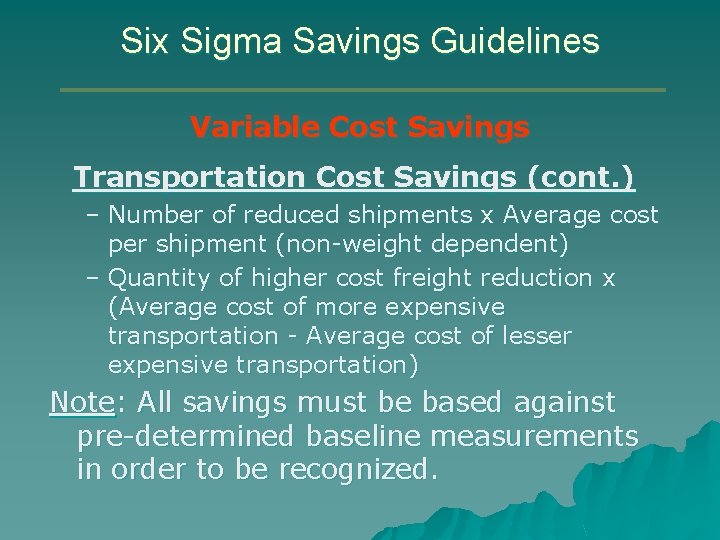
Six Sigma Savings Guidelines Variable Cost Savings Transportation Cost Savings (cont. ) – Number of reduced shipments x Average cost per shipment (non-weight dependent) – Quantity of higher cost freight reduction x (Average cost of more expensive transportation - Average cost of lesser expensive transportation) Note: All savings must be based against pre-determined baseline measurements in order to be recognized.
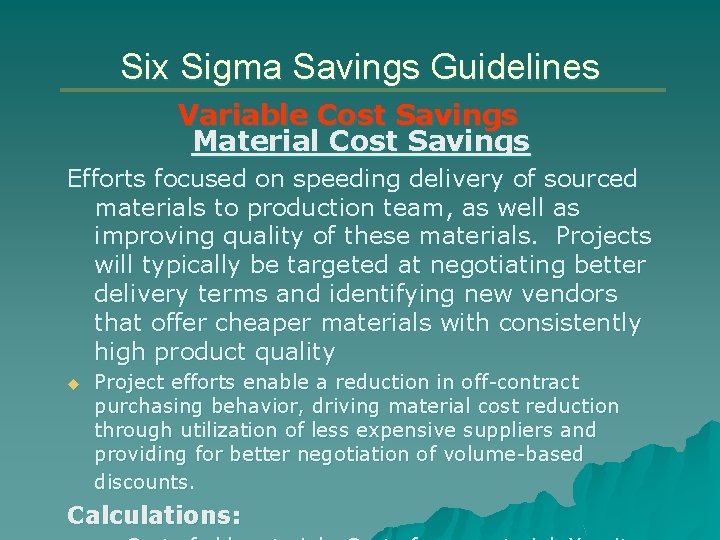
Six Sigma Savings Guidelines Variable Cost Savings Material Cost Savings Efforts focused on speeding delivery of sourced materials to production team, as well as improving quality of these materials. Projects will typically be targeted at negotiating better delivery terms and identifying new vendors that offer cheaper materials with consistently high product quality u Project efforts enable a reduction in off-contract purchasing behavior, driving material cost reduction through utilization of less expensive suppliers and providing for better negotiation of volume-based discounts. Calculations:
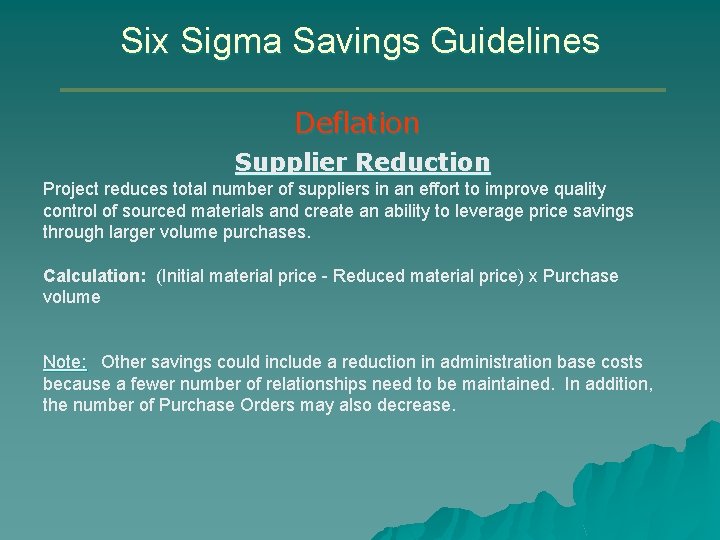
Six Sigma Savings Guidelines Deflation Supplier Reduction Project reduces total number of suppliers in an effort to improve quality control of sourced materials and create an ability to leverage price savings through larger volume purchases. Calculation: (Initial material price - Reduced material price) x Purchase volume Note: Other savings could include a reduction in administration base costs because a fewer number of relationships need to be maintained. In addition, the number of Purchase Orders may also decrease.
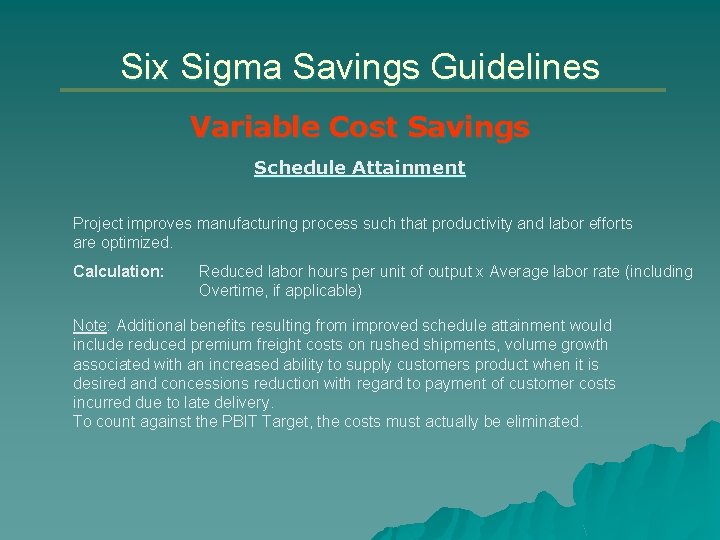
Six Sigma Savings Guidelines Variable Cost Savings Schedule Attainment Project improves manufacturing process such that productivity and labor efforts are optimized. Calculation: Reduced labor hours per unit of output x Average labor rate (including Overtime, if applicable) Note: Additional benefits resulting from improved schedule attainment would include reduced premium freight costs on rushed shipments, volume growth associated with an increased ability to supply customers product when it is desired and concessions reduction with regard to payment of customer costs incurred due to late delivery. To count against the PBIT Target, the costs must actually be eliminated.
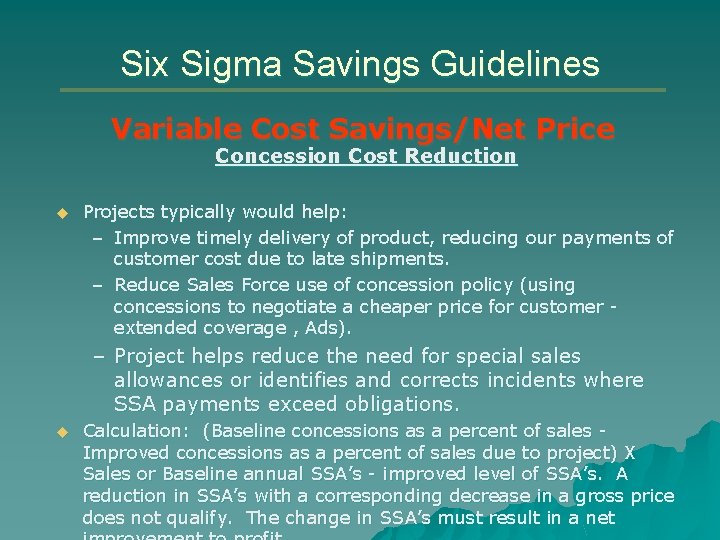
Six Sigma Savings Guidelines Variable Cost Savings/Net Price Concession Cost Reduction u Projects typically would help: – Improve timely delivery of product, reducing our payments of customer cost due to late shipments. – Reduce Sales Force use of concession policy (using concessions to negotiate a cheaper price for customer extended coverage , Ads). – Project helps reduce the need for special sales allowances or identifies and corrects incidents where SSA payments exceed obligations. u Calculation: (Baseline concessions as a percent of sales Improved concessions as a percent of sales due to project) X Sales or Baseline annual SSA’s - improved level of SSA’s. A reduction in SSA’s with a corresponding decrease in a gross price does not qualify. The change in SSA’s must result in a net
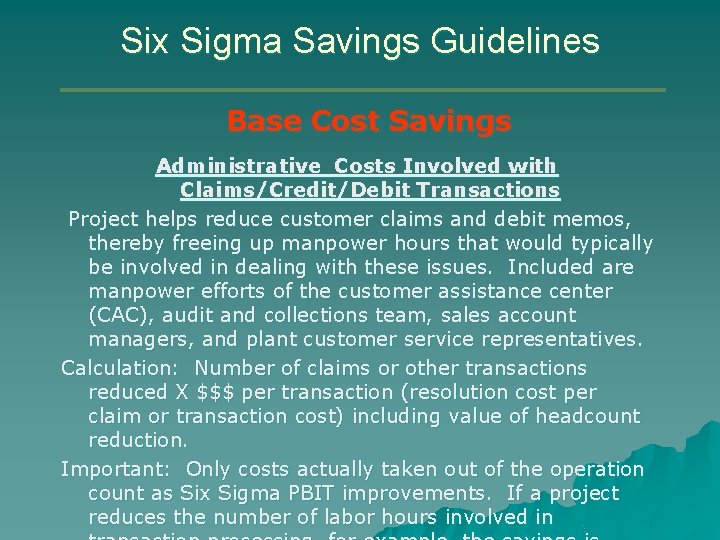
Six Sigma Savings Guidelines Base Cost Savings Administrative Costs Involved with Claims/Credit/Debit Transactions Project helps reduce customer claims and debit memos, thereby freeing up manpower hours that would typically be involved in dealing with these issues. Included are manpower efforts of the customer assistance center (CAC), audit and collections team, sales account managers, and plant customer service representatives. Calculation: Number of claims or other transactions reduced X $$$ per transaction (resolution cost per claim or transaction cost) including value of headcount reduction. Important: Only costs actually taken out of the operation count as Six Sigma PBIT improvements. If a project reduces the number of labor hours involved in
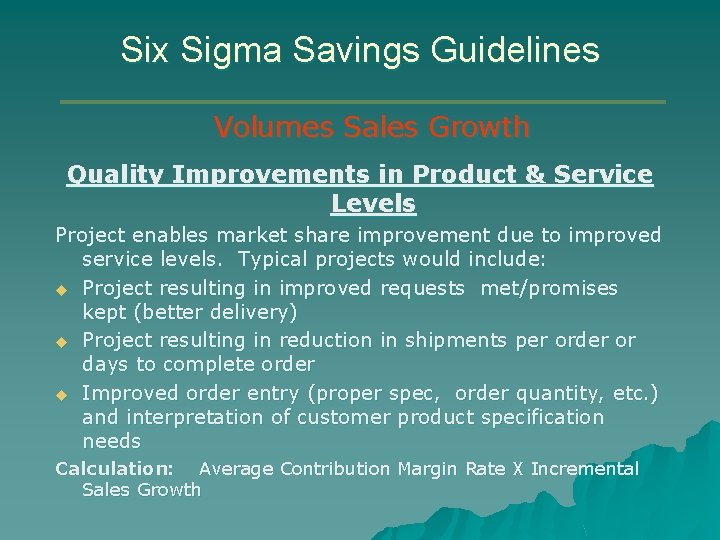
Six Sigma Savings Guidelines Volumes Sales Growth Quality Improvements in Product & Service Levels Project enables market share improvement due to improved service levels. Typical projects would include: u Project resulting in improved requests met/promises kept (better delivery) u Project resulting in reduction in shipments per order or days to complete order u Improved order entry (proper spec, order quantity, etc. ) and interpretation of customer product specification needs Calculation: Average Contribution Margin Rate X Incremental Sales Growth
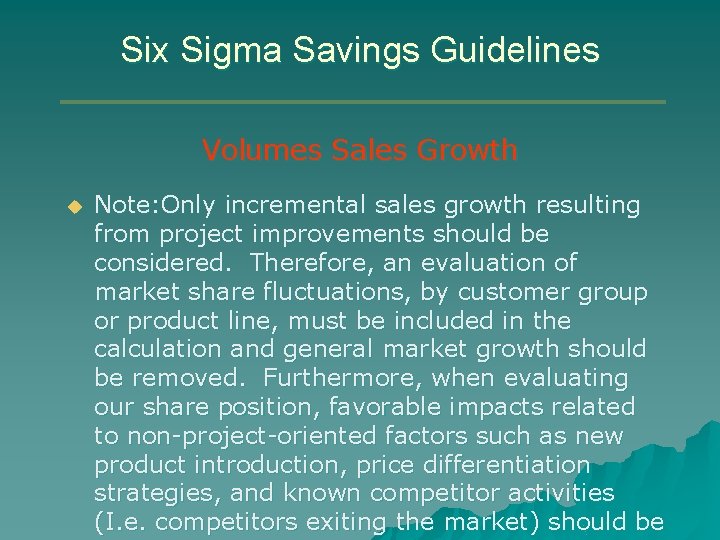
Six Sigma Savings Guidelines Volumes Sales Growth u Note: Only incremental sales growth resulting from project improvements should be considered. Therefore, an evaluation of market share fluctuations, by customer group or product line, must be included in the calculation and general market growth should be removed. Furthermore, when evaluating our share position, favorable impacts related to non-project-oriented factors such as new product introduction, price differentiation strategies, and known competitor activities (I. e. competitors exiting the market) should be
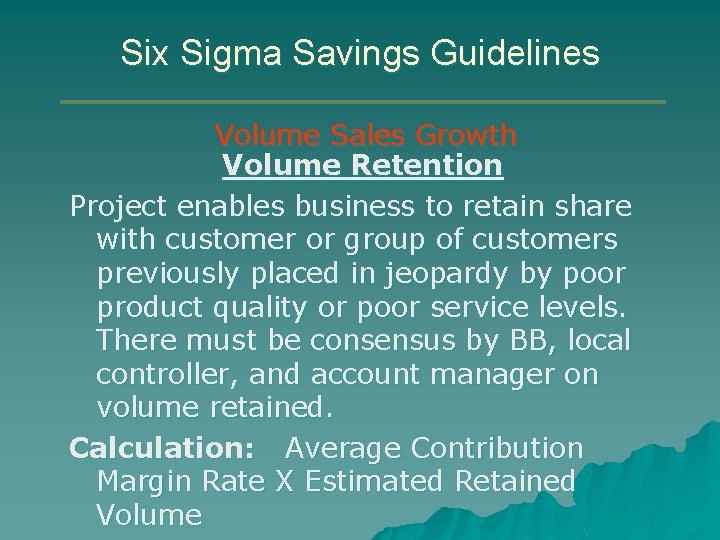
Six Sigma Savings Guidelines Volume Sales Growth Volume Retention Project enables business to retain share with customer or group of customers previously placed in jeopardy by poor product quality or poor service levels. There must be consensus by BB, local controller, and account manager on volume retained. Calculation: Average Contribution Margin Rate X Estimated Retained Volume
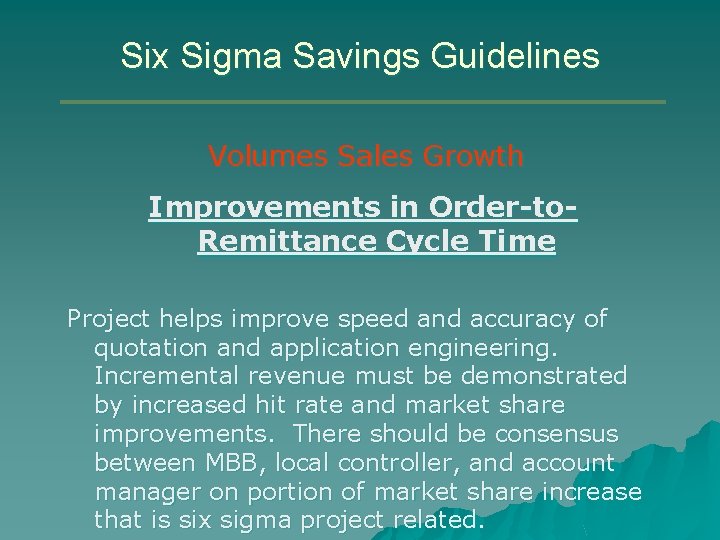
Six Sigma Savings Guidelines Volumes Sales Growth Improvements in Order-to. Remittance Cycle Time Project helps improve speed and accuracy of quotation and application engineering. Incremental revenue must be demonstrated by increased hit rate and market share improvements. There should be consensus between MBB, local controller, and account manager on portion of market share increase that is six sigma project related.
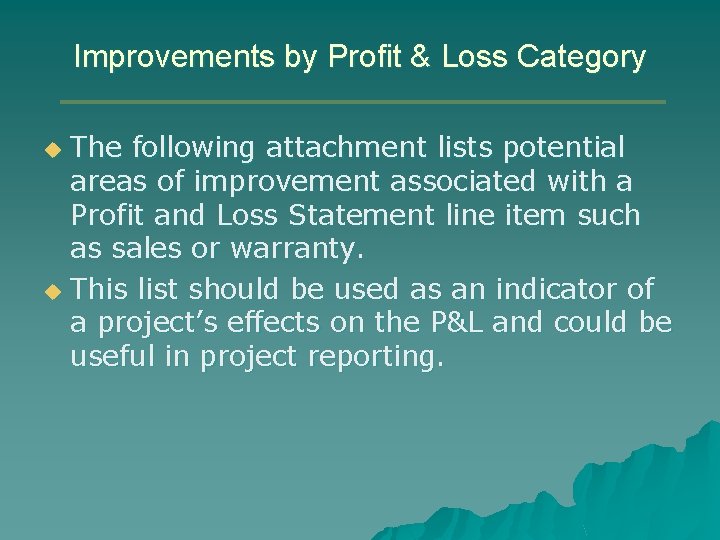
Improvements by Profit & Loss Category The following attachment lists potential areas of improvement associated with a Profit and Loss Statement line item such as sales or warranty. u This list should be used as an indicator of a project’s effects on the P&L and could be useful in project reporting. u
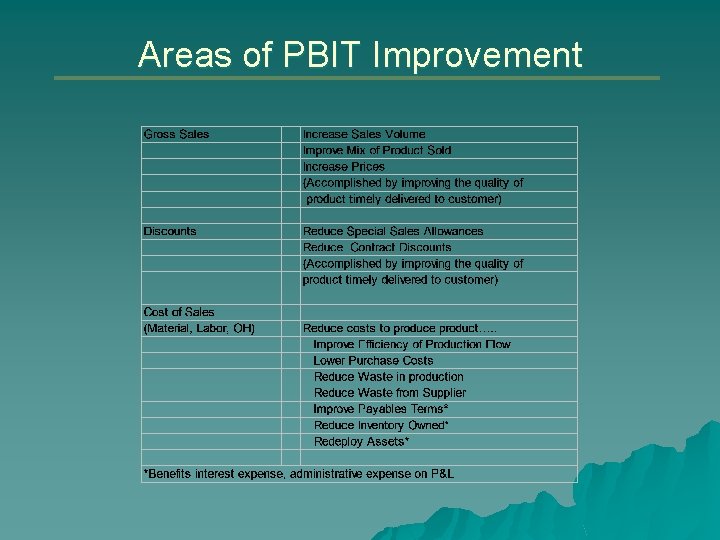
Areas of PBIT Improvement
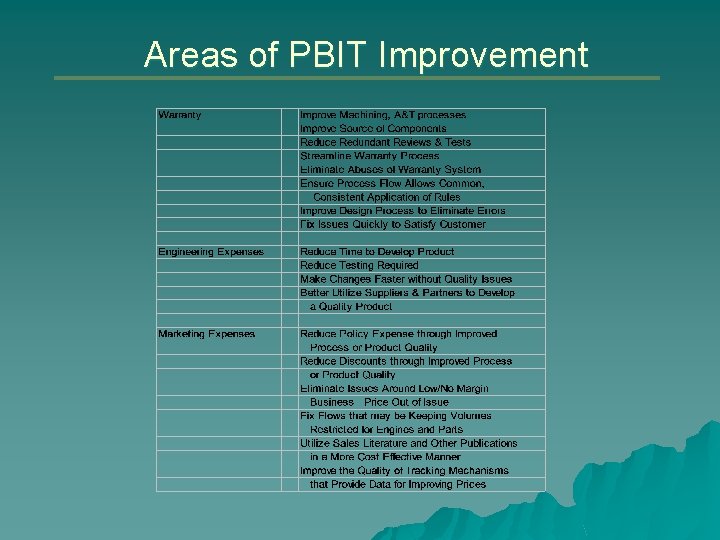
Areas of PBIT Improvement
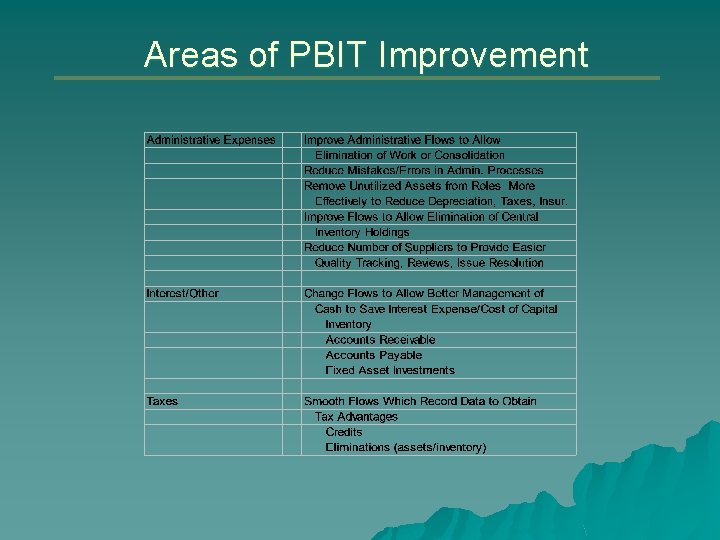
Areas of PBIT Improvement