Sand Casting Sand basic molding material used inexpensive
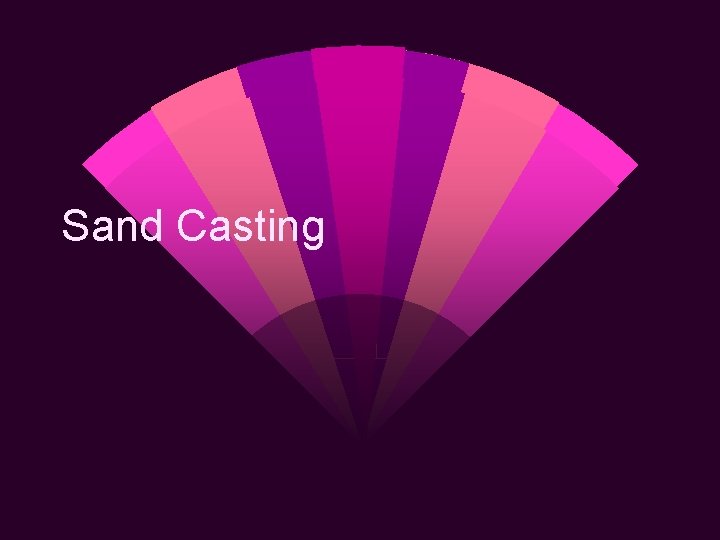
Sand Casting

Sand - basic molding material used inexpensive w refractory w simplest process of molding w

Flask: supports mold - has cope (top) and drag (bottom)

Prepared flask (ready to pour) consists of w w w parting line: seam between cope and drag pouring basin (cup): molten metal is poured in sprue: molten metal flows downward runner: channels carry metal from sprue to mold cavity gates: inlets into mold cavity cores: inserts made of sand - form

Making a mold: w w w ramming sand around pattern for compaction (by hand or mechanically) in cope and drag pattern removed from sand entrance of metal through sprue is from the top (cope) gating and runner systems usually in bottom (drag) cope is placed on drag section - closing

Equipment: Flask: cope and drag w Crucibles: melt metal in w parting dust: powder or aerosol - keeps sand from sticking to pattern or part w • powders: graphite, silica, flower, fine charcoal riddle - sifting sand w gate cutter and spoon w ingot mold w

Five types of Sand Molding

1. Green sand molds: moist sand at time of pour (used most often) 10 -20% clay - more clay will increase cohesiveness but reduce porosity and preventing w inexpensive w adaptable to automation w not as strong as other molds - damage by mishandling w

Green sand molds (Cont. ) because of moisture - must be careful of gasses created w sand grains rounded do not stick together as well as irregular grains which interlock - provide better structure when rammed - less clay is required w

Conditioning process - adding water to sand / clay while mixing Amount of water: squeeze in hand should stick together and leave distinct patter of fingerprints w sand can be reused and reconditioned but will eventually need to be replaced w

2. Dry sand molds: made with a binder that does not require moisture w binder is an oil which coats the grains of sand w when baked in an oven, the oil polymerizes to bond the grains together w

adv: resist metal erosion w stronger w no moisture related problems of gassing w

disadv: higher cost of oil binder w cost of baking molds w

3. Skin dried molds: remove water from surface of mold to eliminate pin holing of the metal w use of torch, hot air, electric lamp, w

4. Loam molding: to make large heavy castings of circular shape such as large cylinders etc. w sub structure of wood, brick, etc is built w slurry of sand, clay, and water is dabbed over base structure to approx shape w sweep board with proper contours is rotated about center axis w

Loam molding (Cont. ) mold is dried w reduced cost because no 3 -D pattern is needed w requires skilled crafters w See page 6 w

5. Pit molding: For large castings w pattern is set in a concrete lined pit (drag) w sand is rammed in and around the pattern w cope may set on drag at or above floor level w

Petro Bond molding sand: waterless mixture of fine sand, oil, Petro Bond bonding agent (trade name) and a catalyst. w Better surface finish - saves time for finishing operations w stronger w less gas generation without water w

Petro Bond molding (Cont. ) can reuse petrobond sand except the burnt fine layer next to the casting w can also use petrobond around the casting and fill rest of flask with green sand w never add water to petrobond w don=t ram too much - ensure vent holes are present w
- Slides: 19