RTK Contractor Management Process Book White Book Quick
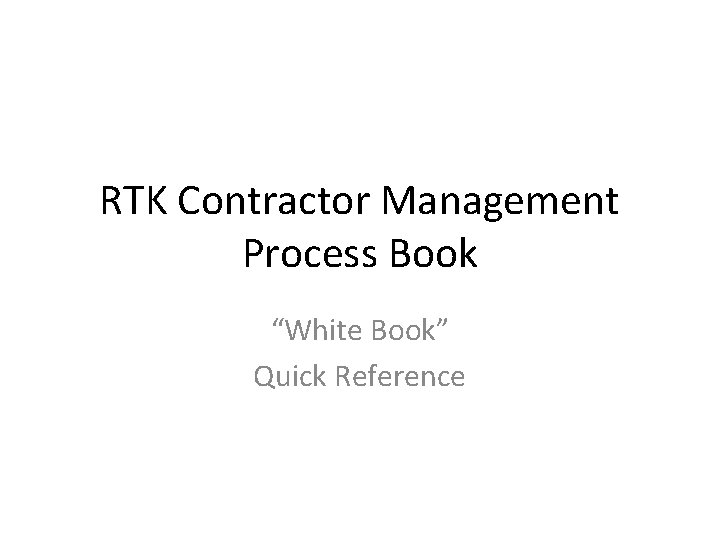
RTK Contractor Management Process Book “White Book” Quick Reference
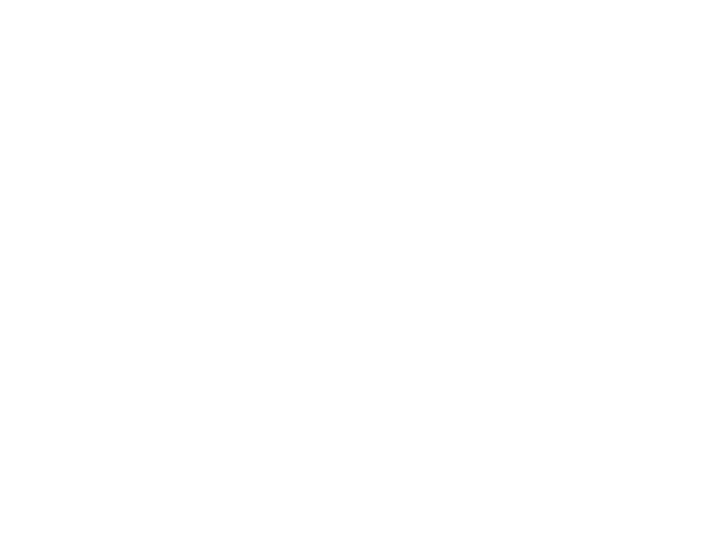
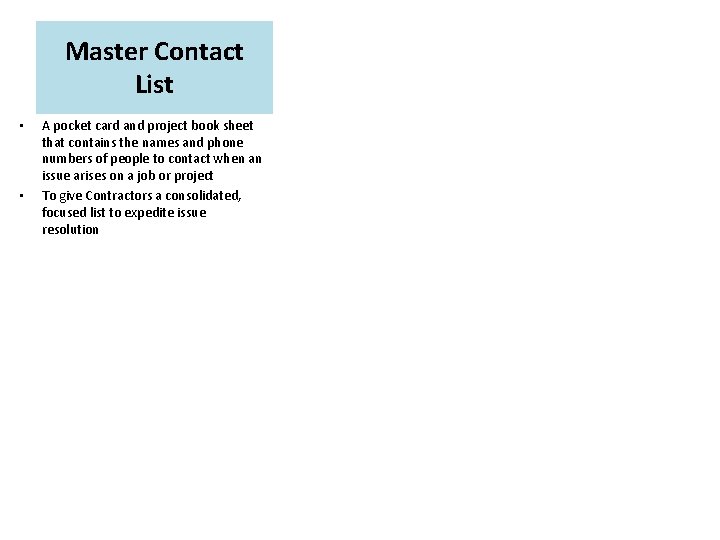
Master Contact List • • A pocket card and project book sheet that contains the names and phone numbers of people to contact when an issue arises on a job or project To give Contractors a consolidated, focused list to expedite issue resolution
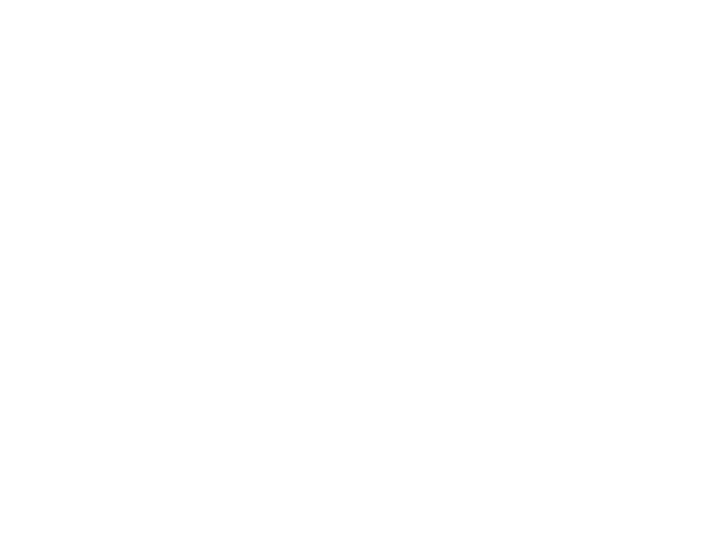
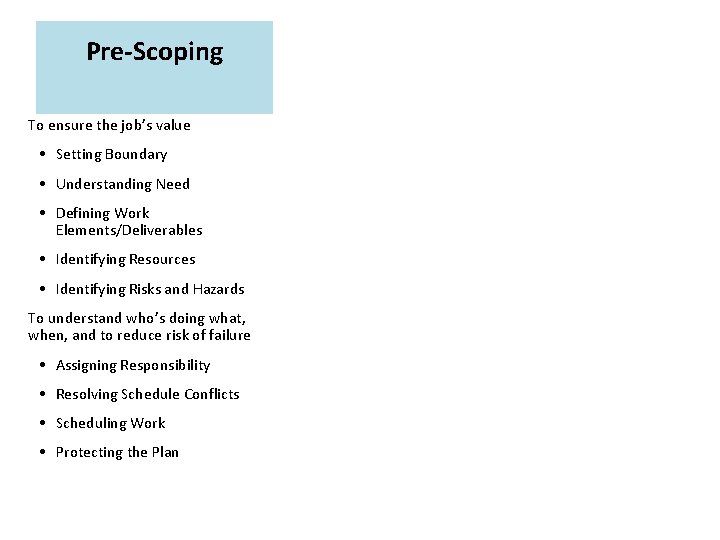
Pre-Scoping To ensure the job’s value • Setting Boundary • Understanding Need • Defining Work Elements/Deliverables • Identifying Resources • Identifying Risks and Hazards To understand who’s doing what, when, and to reduce risk of failure • Assigning Responsibility • Resolving Schedule Conflicts • Scheduling Work • Protecting the Plan
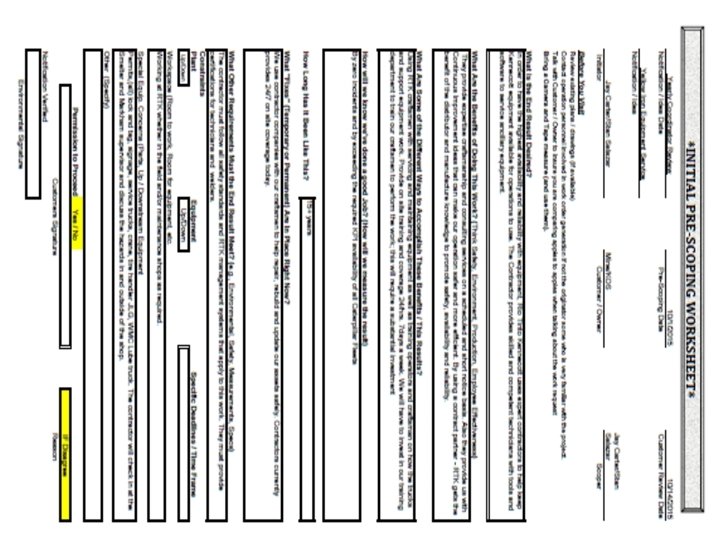
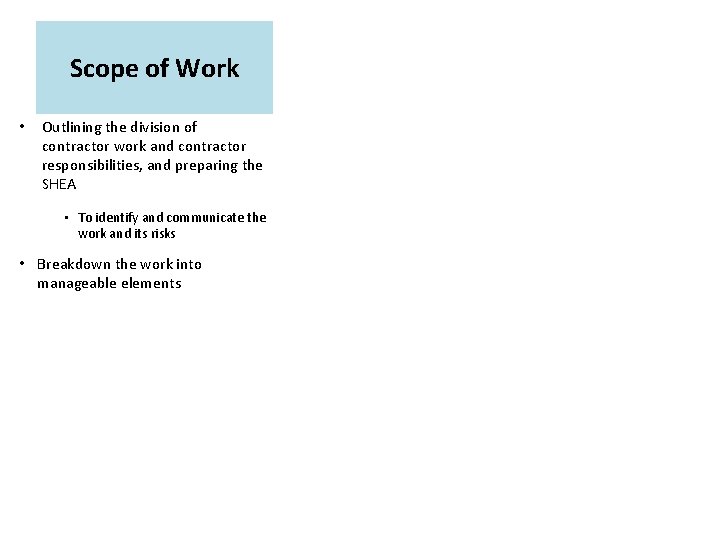
Scope of Work • Outlining the division of contractor work and contractor responsibilities, and preparing the SHEA • To identify and communicate the work and its risks • Breakdown the work into manageable elements
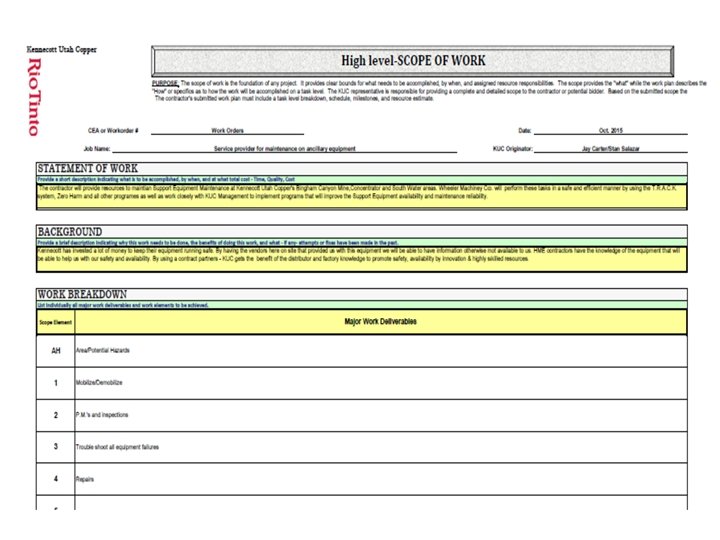
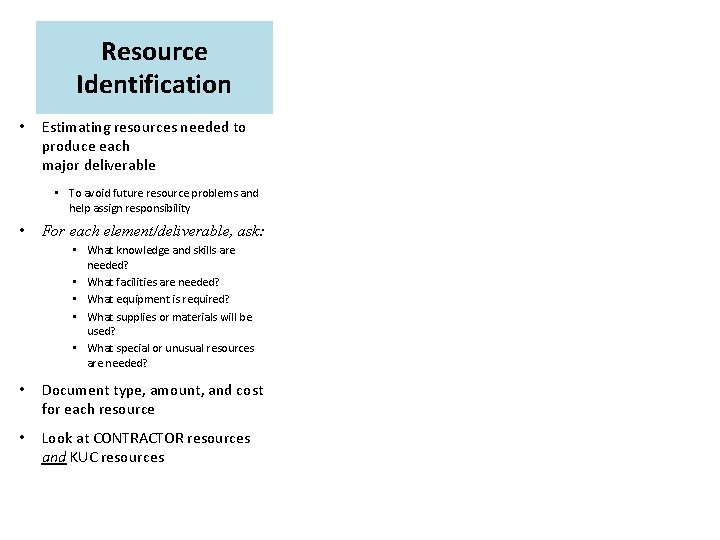
Resource Identification • Estimating resources needed to produce each major deliverable • To avoid future resource problems and help assign responsibility • For each element/deliverable, ask: • What knowledge and skills are needed? • What facilities are needed? • What equipment is required? • What supplies or materials will be used? • What special or unusual resources are needed? • Document type, amount, and cost for each resource • Look at CONTRACTOR resources and KUC resources
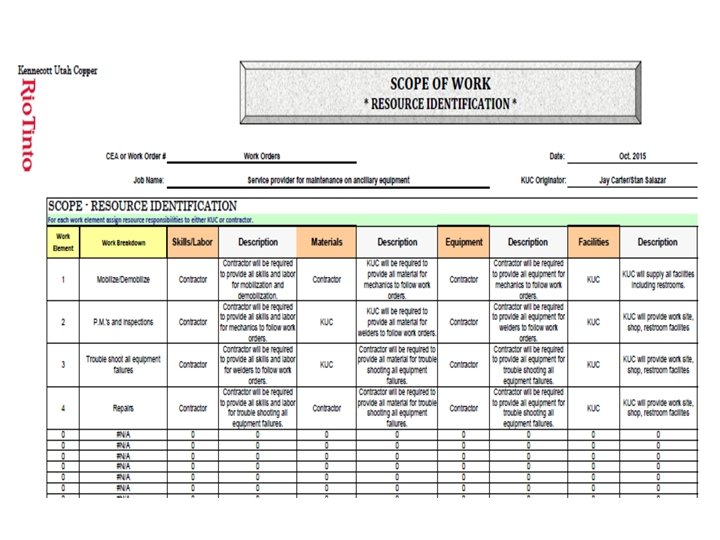
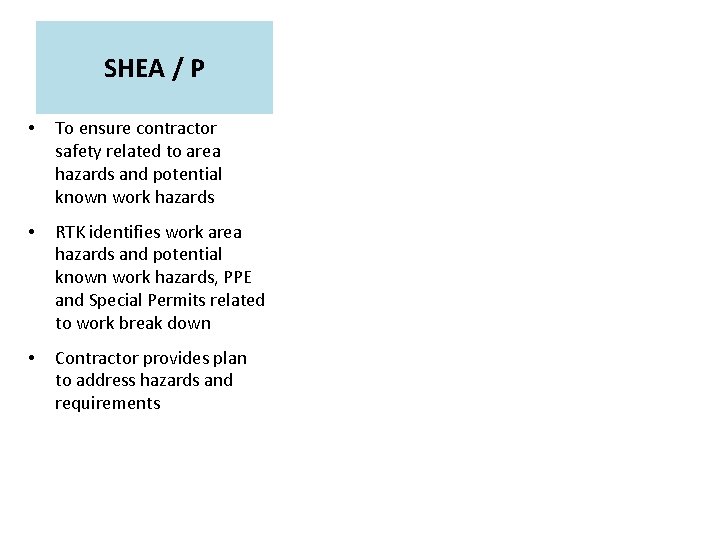
SHEA / P • To ensure contractor safety related to area hazards and potential known work hazards • RTK identifies work area hazards and potential known work hazards, PPE and Special Permits related to work break down • Contractor provides plan to address hazards and requirements
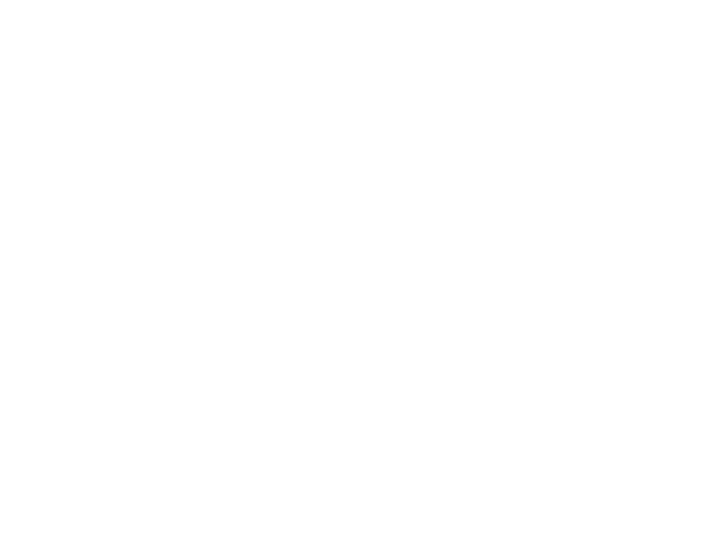
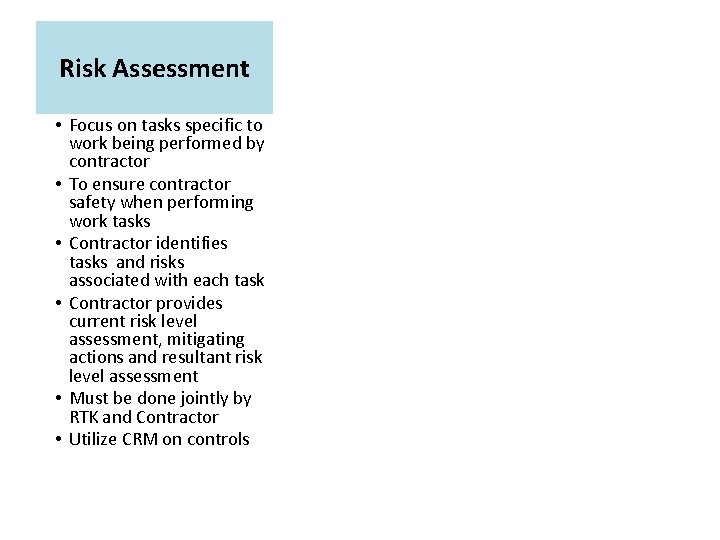
Risk Assessment • Focus on tasks specific to work being performed by contractor • To ensure contractor safety when performing work tasks • Contractor identifies tasks and risks associated with each task • Contractor provides current risk level assessment, mitigating actions and resultant risk level assessment • Must be done jointly by RTK and Contractor • Utilize CRM on controls
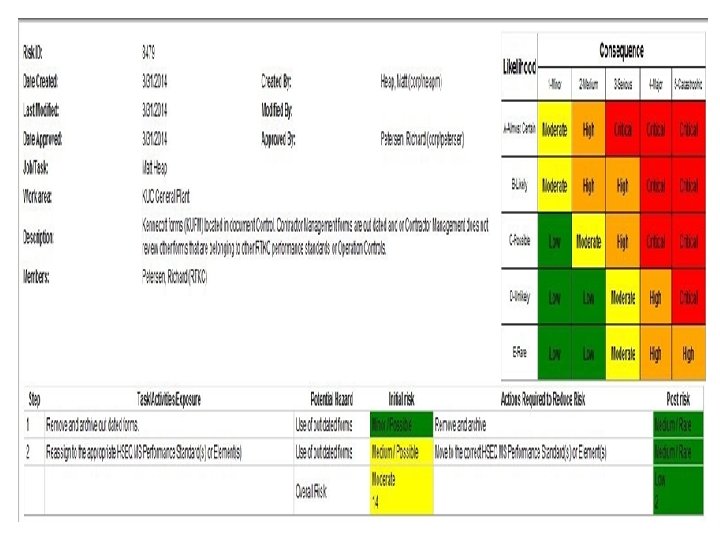
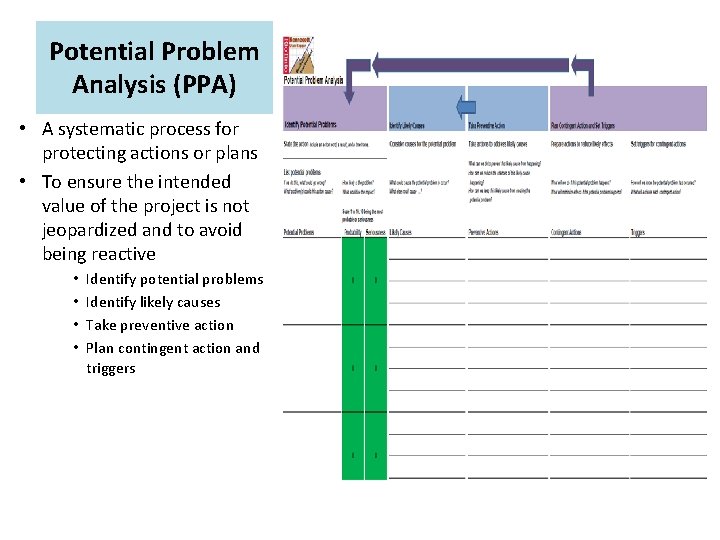
Potential Problem Analysis (PPA) • A systematic process for protecting actions or plans • To ensure the intended value of the project is not jeopardized and to avoid being reactive • • Identify potential problems Identify likely causes Take preventive action Plan contingent action and triggers
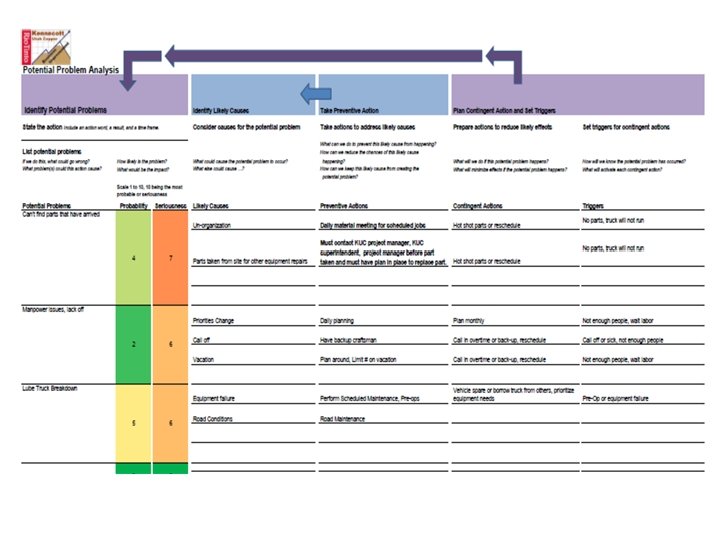
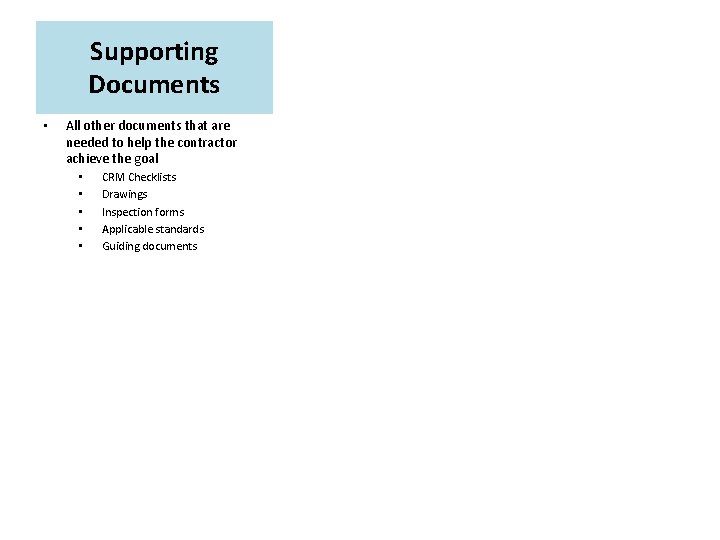
Supporting Documents • All other documents that are needed to help the contractor achieve the goal • • • CRM Checklists Drawings Inspection forms Applicable standards Guiding documents
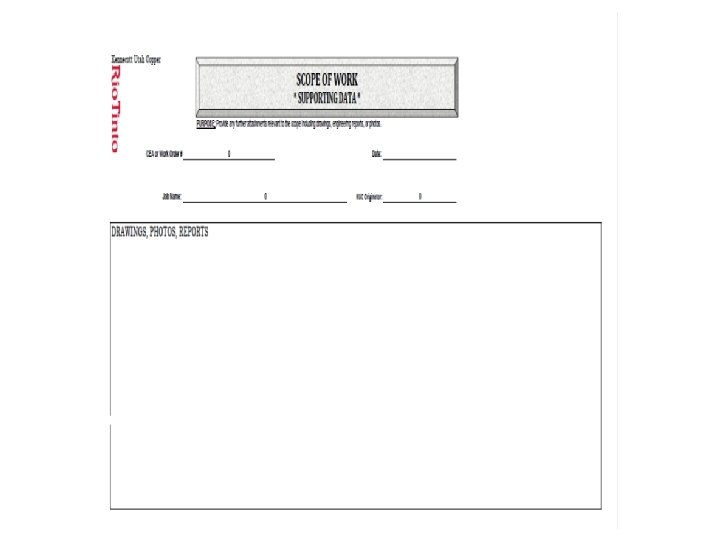
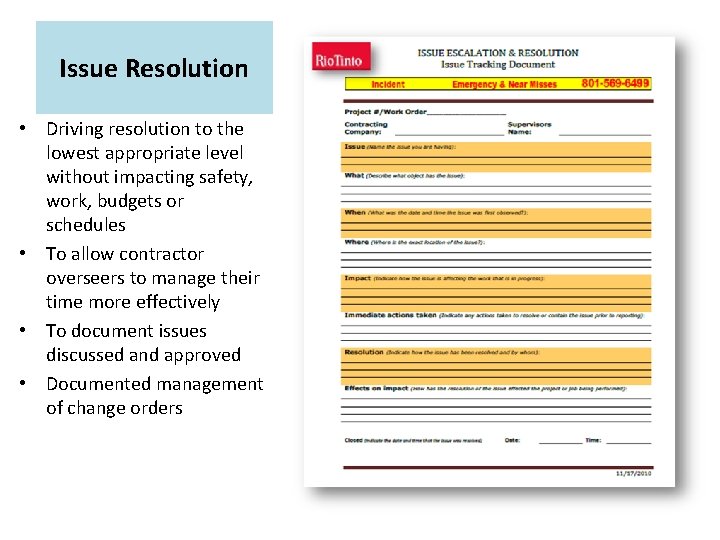
Issue Resolution • Driving resolution to the lowest appropriate level without impacting safety, work, budgets or schedules • To allow contractor overseers to manage their time more effectively • To document issues discussed and approved • Documented management of change orders
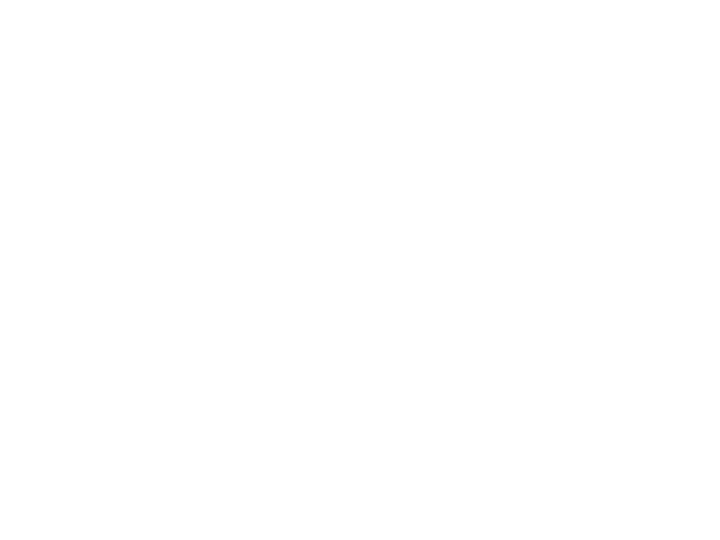
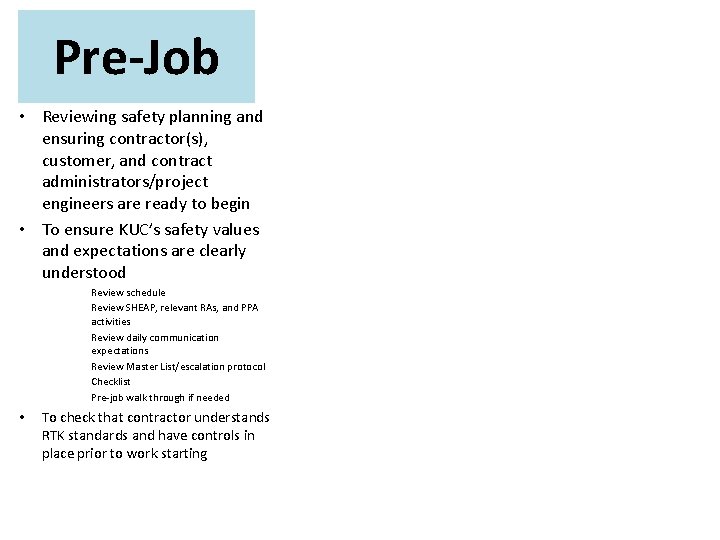
Pre-Job • Reviewing safety planning and ensuring contractor(s), customer, and contract administrators/project engineers are ready to begin • To ensure KUC’s safety values and expectations are clearly understood Review schedule Review SHEAP, relevant RAs, and PPA activities Review daily communication expectations Review Master List/escalation protocol Checklist Pre-job walk through if needed • To check that contractor understands RTK standards and have controls in place prior to work starting
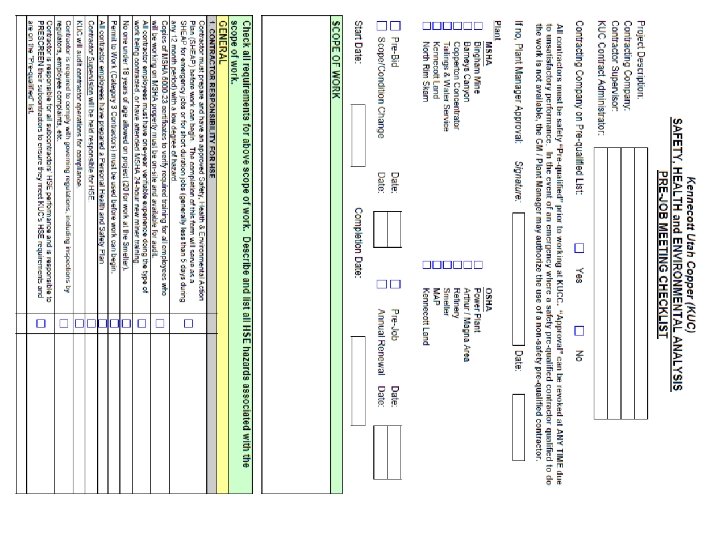
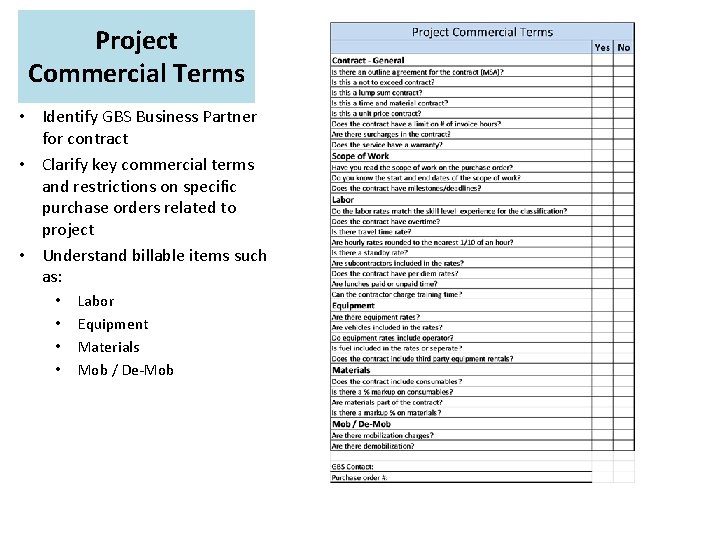
Project Commercial Terms • Identify GBS Business Partner for contract • Clarify key commercial terms and restrictions on specific purchase orders related to project • Understand billable items such as: • • Labor Equipment Materials Mob / De-Mob
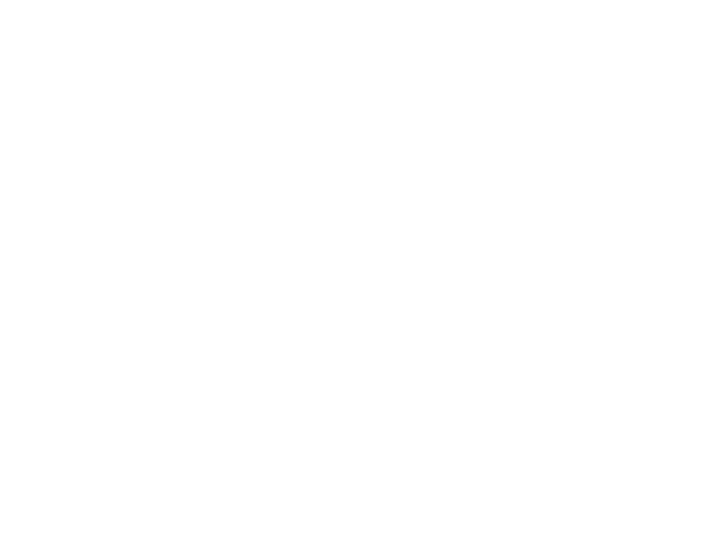
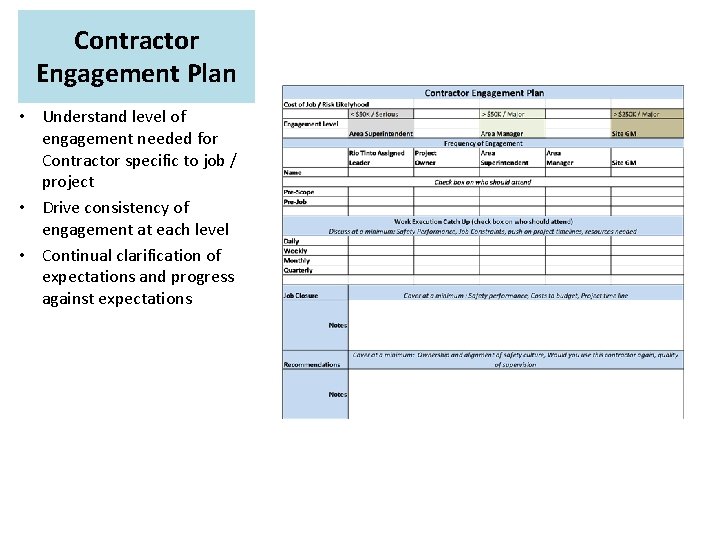
Contractor Engagement Plan • Understand level of engagement needed for Contractor specific to job / project • Drive consistency of engagement at each level • Continual clarification of expectations and progress against expectations
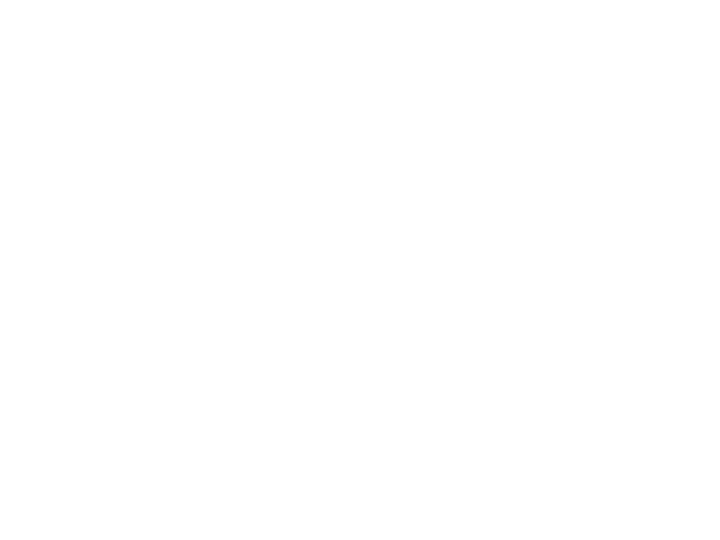
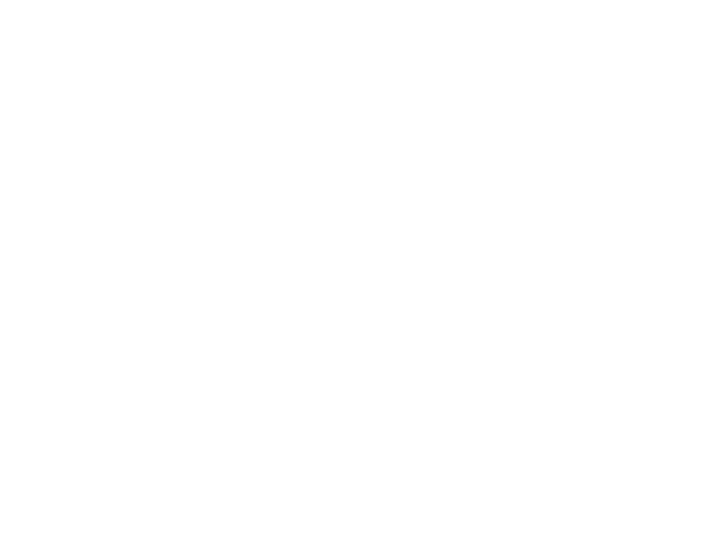
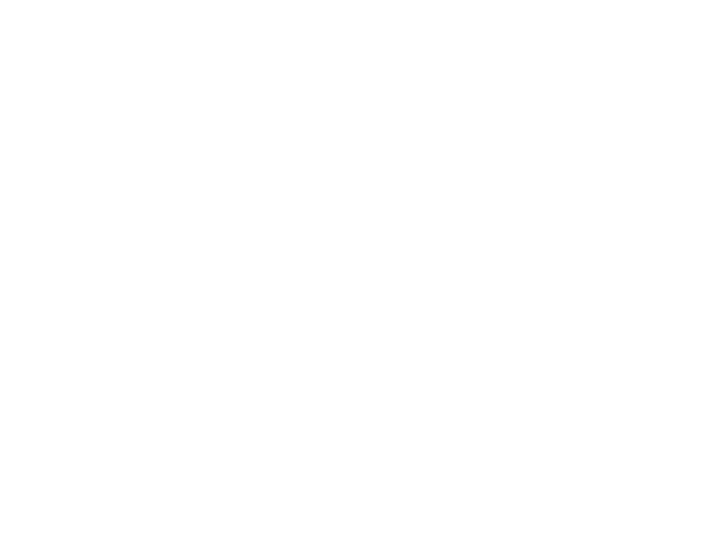
- Slides: 28