Production Operations management 8 1 Using resources Operations
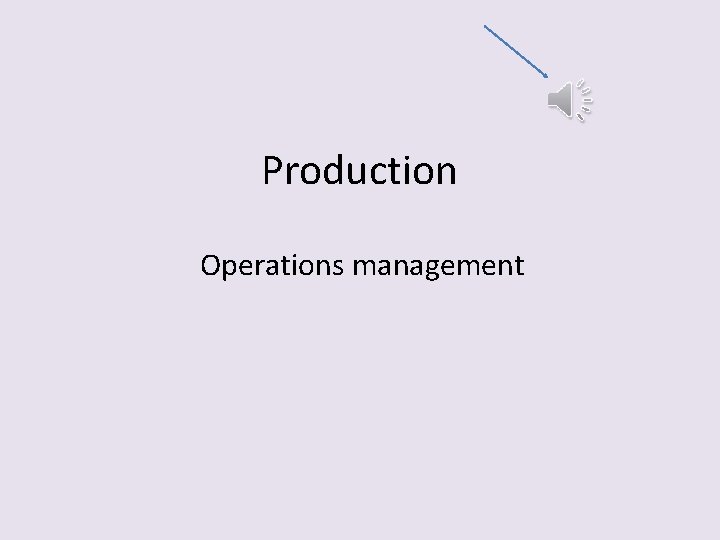

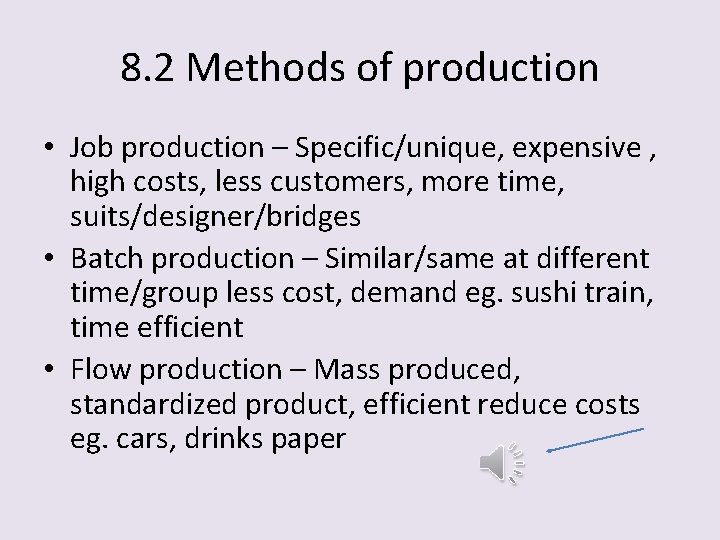
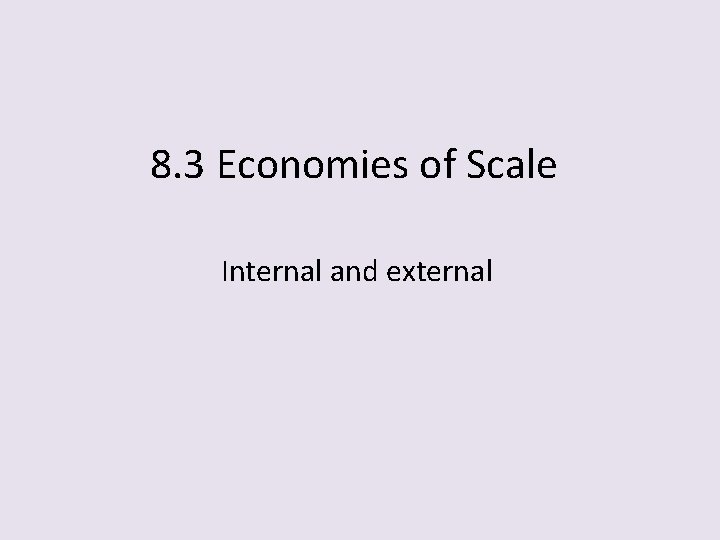
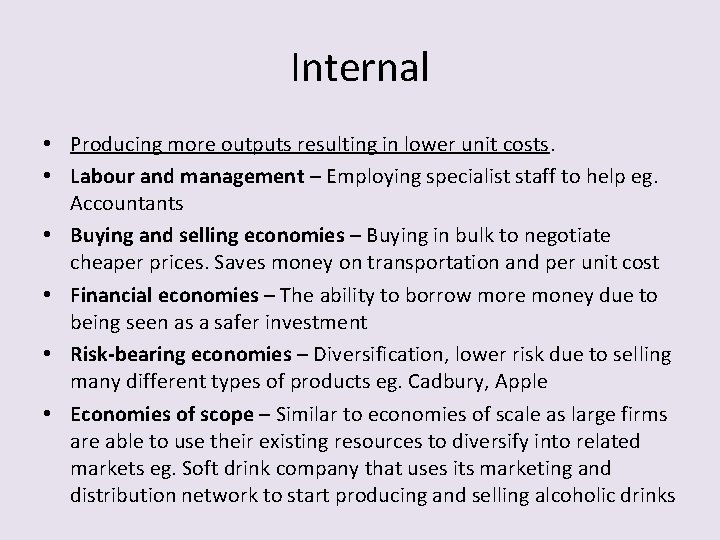
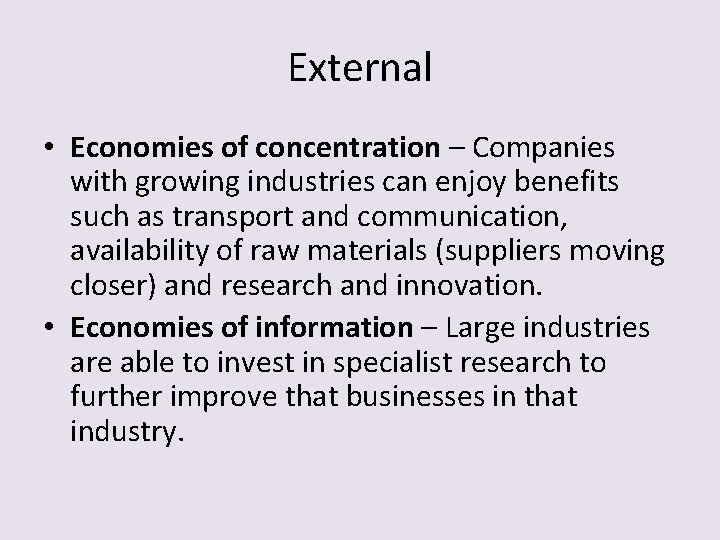
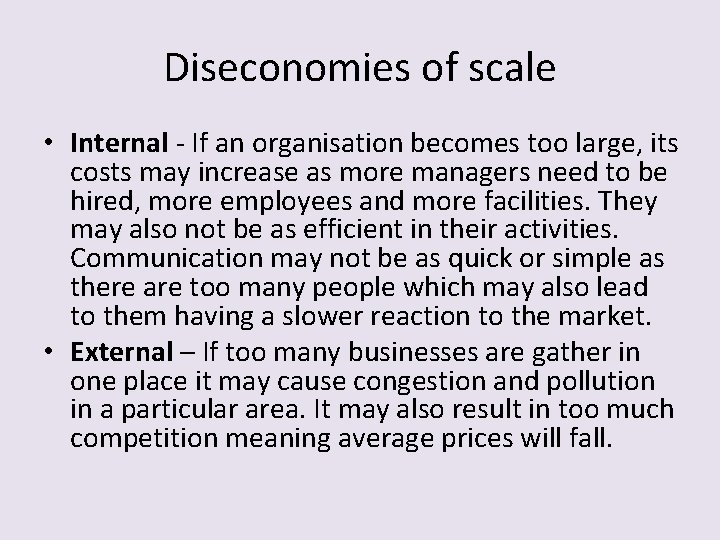
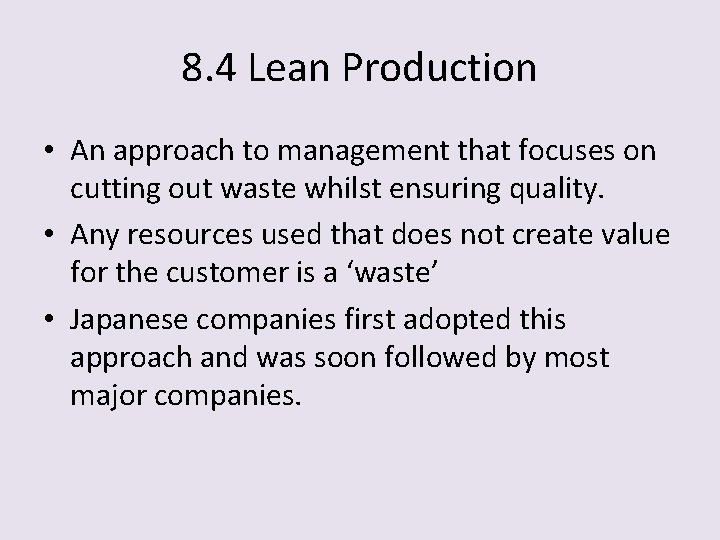
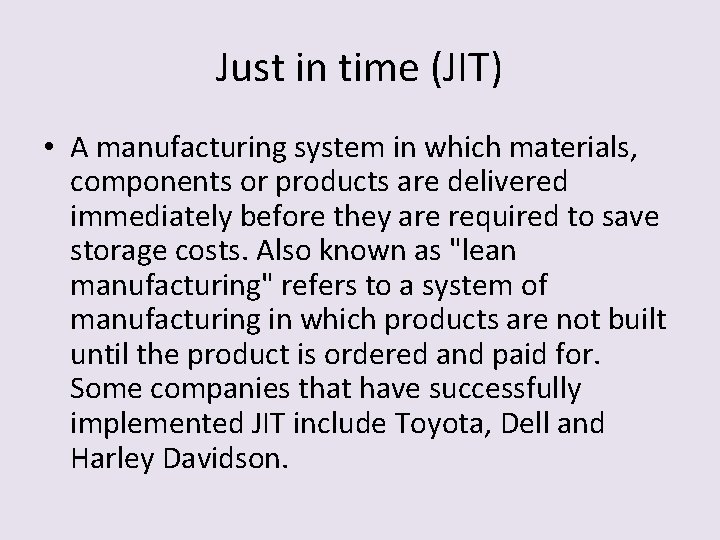
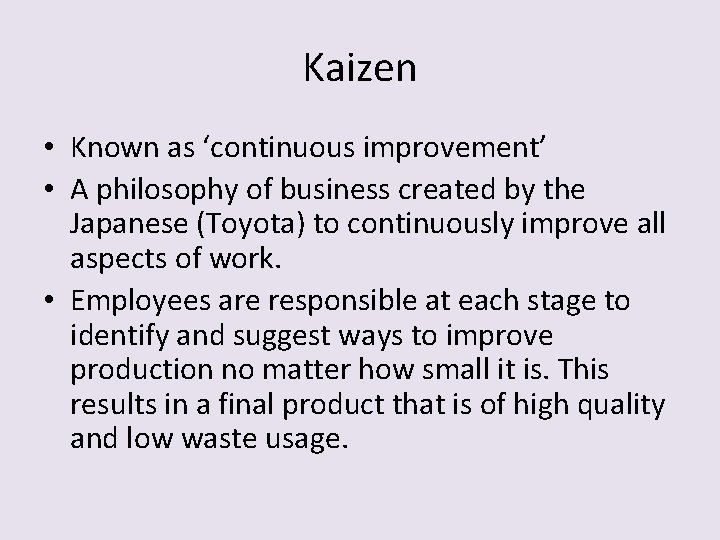
- Slides: 10
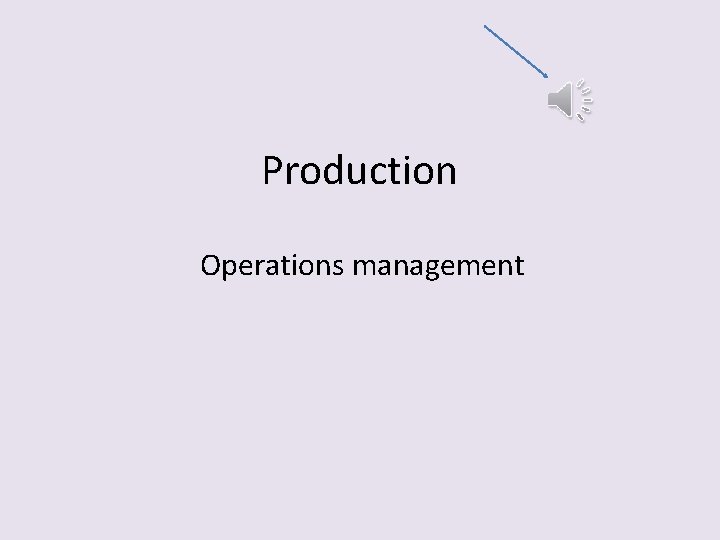
Production Operations management

8. 1 Using resources • Operations – Organised work tasks • Inputs - Resources used in the production process; includes capital, labour, materials and energy • Outputs – The final goods and services produced by the business • Productivity – How effective resources are in producing goods • Understand the difference between productivity and production
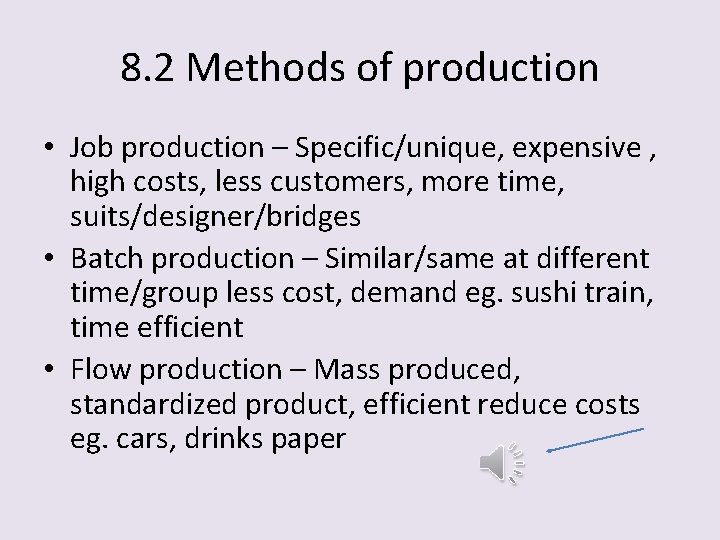
8. 2 Methods of production • Job production – Specific/unique, expensive , high costs, less customers, more time, suits/designer/bridges • Batch production – Similar/same at different time/group less cost, demand eg. sushi train, time efficient • Flow production – Mass produced, standardized product, efficient reduce costs eg. cars, drinks paper
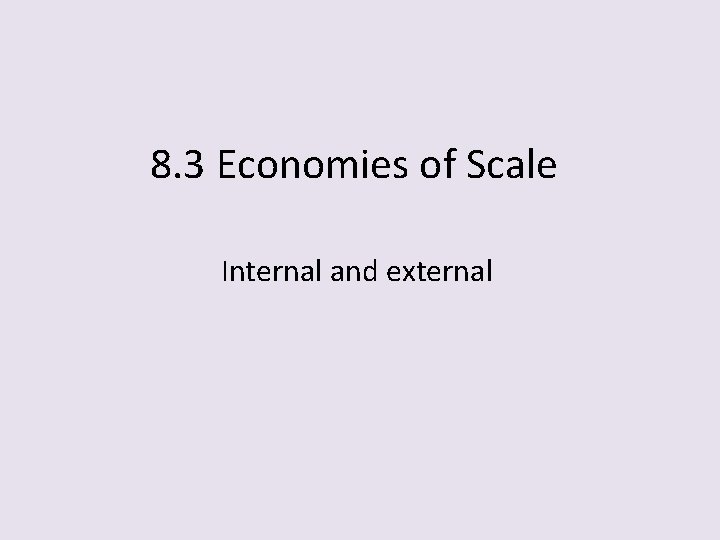
8. 3 Economies of Scale Internal and external
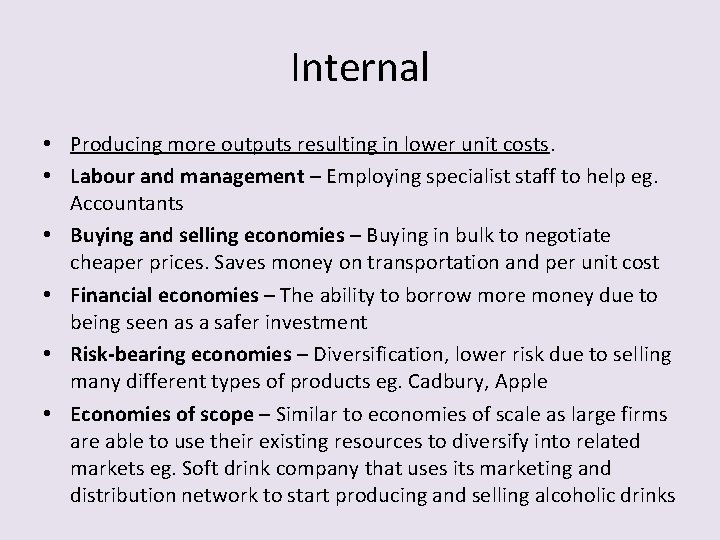
Internal • Producing more outputs resulting in lower unit costs. • Labour and management – Employing specialist staff to help eg. Accountants • Buying and selling economies – Buying in bulk to negotiate cheaper prices. Saves money on transportation and per unit cost • Financial economies – The ability to borrow more money due to being seen as a safer investment • Risk-bearing economies – Diversification, lower risk due to selling many different types of products eg. Cadbury, Apple • Economies of scope – Similar to economies of scale as large firms are able to use their existing resources to diversify into related markets eg. Soft drink company that uses its marketing and distribution network to start producing and selling alcoholic drinks
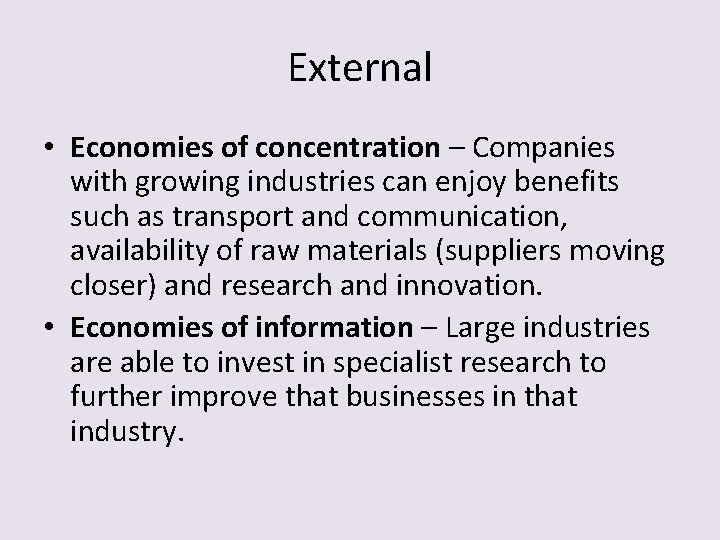
External • Economies of concentration – Companies with growing industries can enjoy benefits such as transport and communication, availability of raw materials (suppliers moving closer) and research and innovation. • Economies of information – Large industries are able to invest in specialist research to further improve that businesses in that industry.
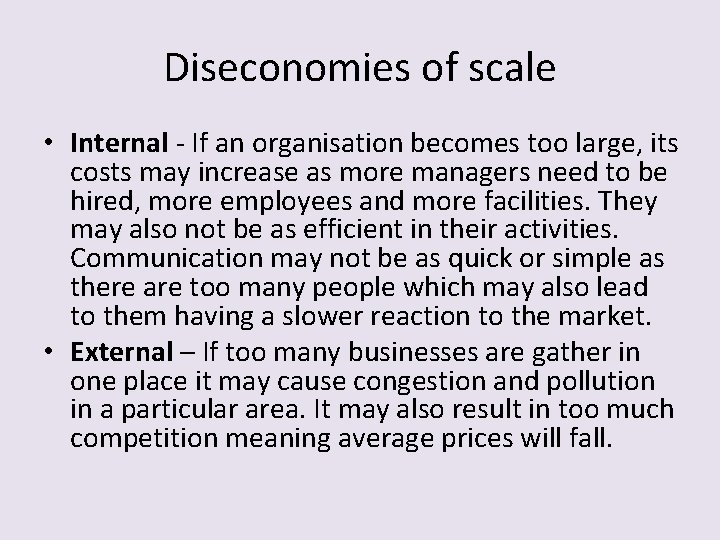
Diseconomies of scale • Internal - If an organisation becomes too large, its costs may increase as more managers need to be hired, more employees and more facilities. They may also not be as efficient in their activities. Communication may not be as quick or simple as there are too many people which may also lead to them having a slower reaction to the market. • External – If too many businesses are gather in one place it may cause congestion and pollution in a particular area. It may also result in too much competition meaning average prices will fall.
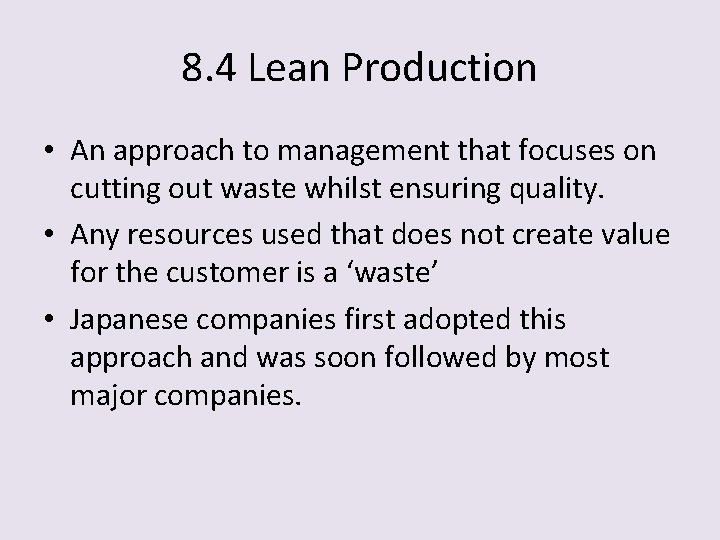
8. 4 Lean Production • An approach to management that focuses on cutting out waste whilst ensuring quality. • Any resources used that does not create value for the customer is a ‘waste’ • Japanese companies first adopted this approach and was soon followed by most major companies.
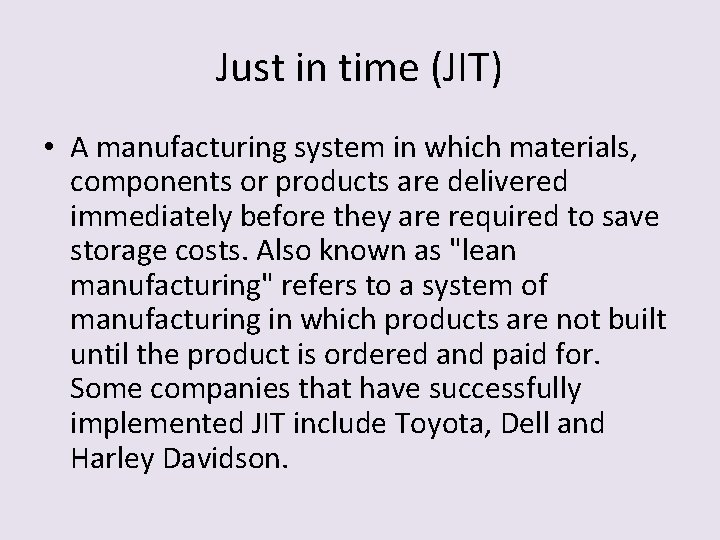
Just in time (JIT) • A manufacturing system in which materials, components or products are delivered immediately before they are required to save storage costs. Also known as "lean manufacturing" refers to a system of manufacturing in which products are not built until the product is ordered and paid for. Some companies that have successfully implemented JIT include Toyota, Dell and Harley Davidson.
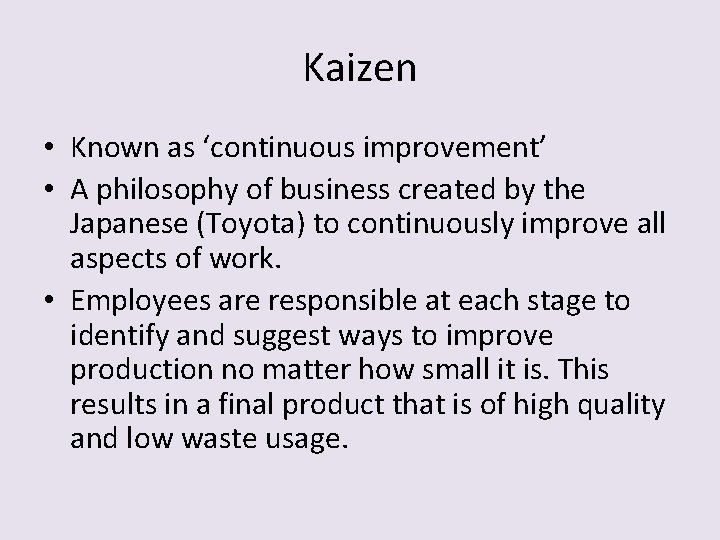
Kaizen • Known as ‘continuous improvement’ • A philosophy of business created by the Japanese (Toyota) to continuously improve all aspects of work. • Employees are responsible at each stage to identify and suggest ways to improve production no matter how small it is. This results in a final product that is of high quality and low waste usage.
Apa yang dimaksud dengan pre production process
Human resources and job design in operations management
Tps in operations management
Production and operations management
Operation management chapter 3
What is transformation process
Fixed resources examples
Renewable resources vs nonrenewable resources
It is a practice of using resources wisely
Chapter 2 skills and applications
Wisely using resources to achieve goals is known as