Process Instrumentation ERT 213 Piping and Instrumentation Diagram
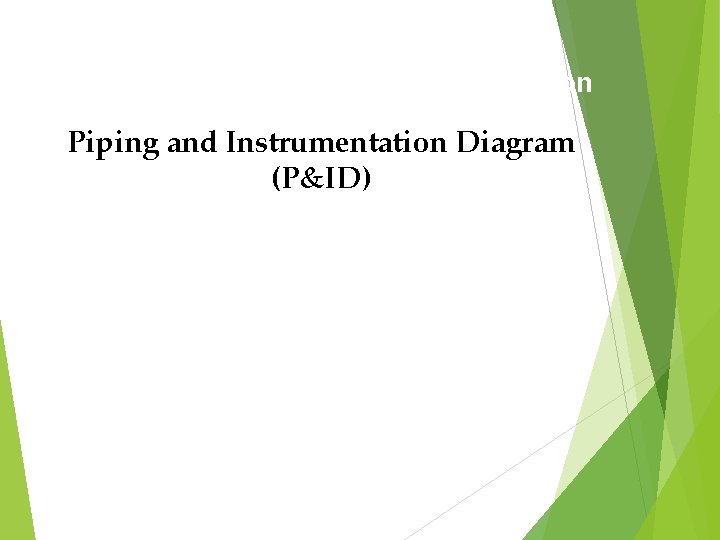
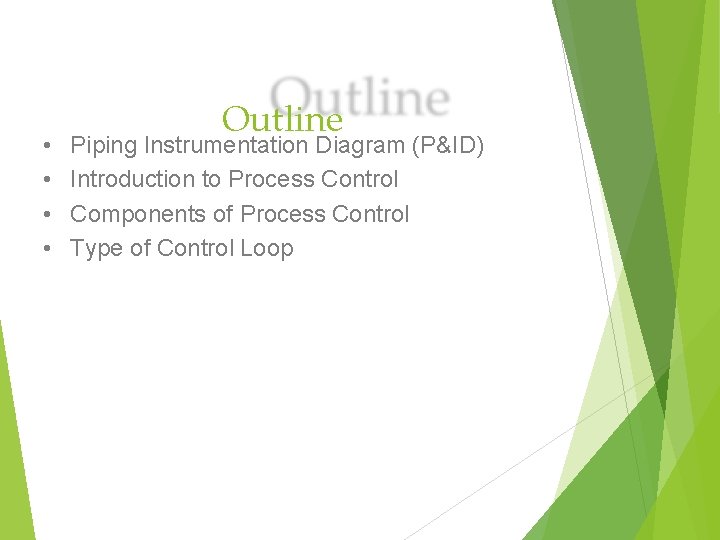
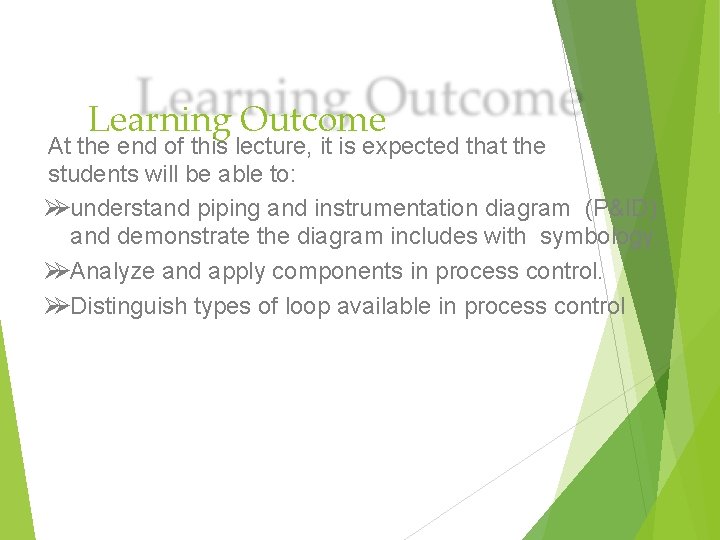
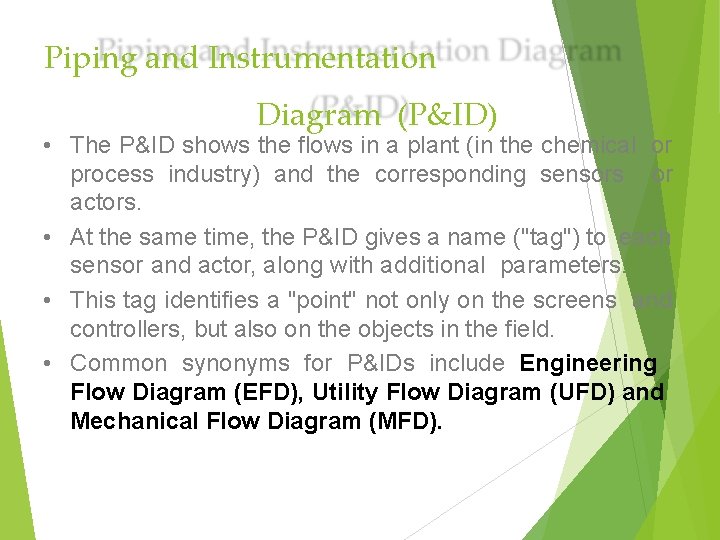
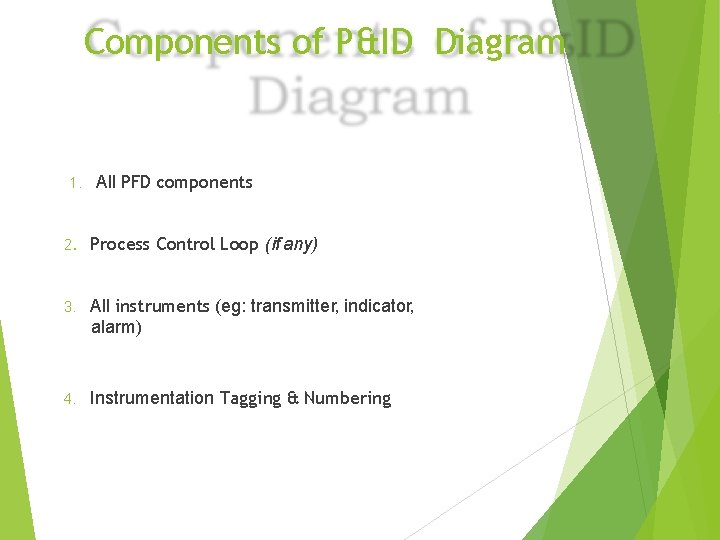
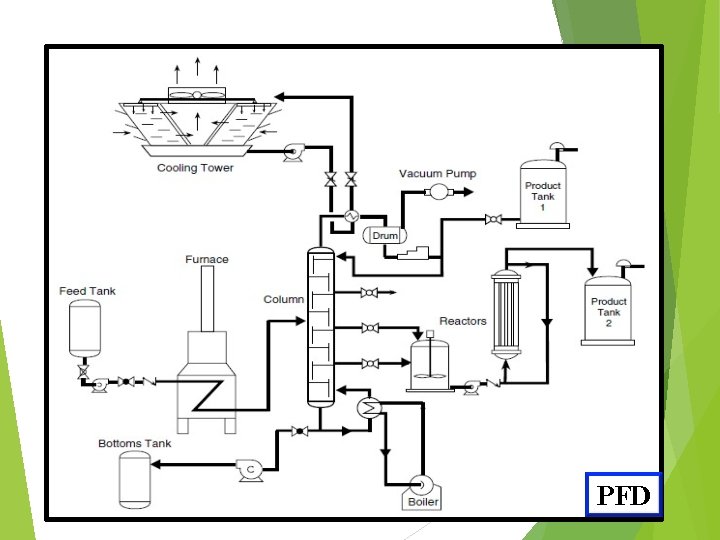
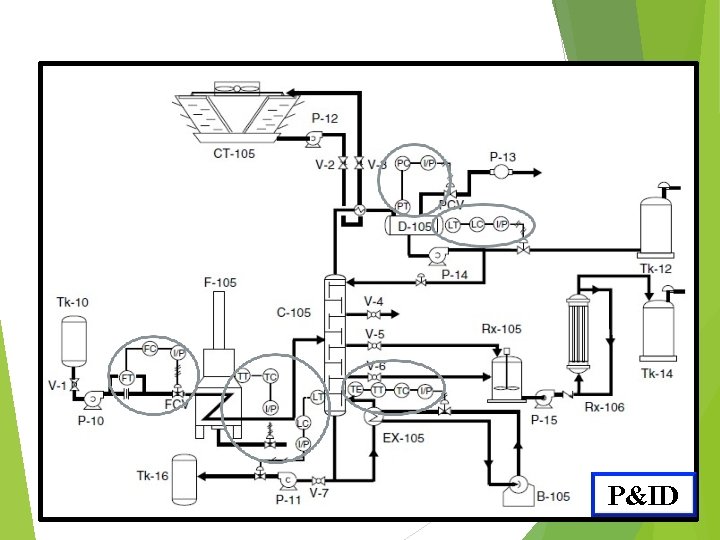
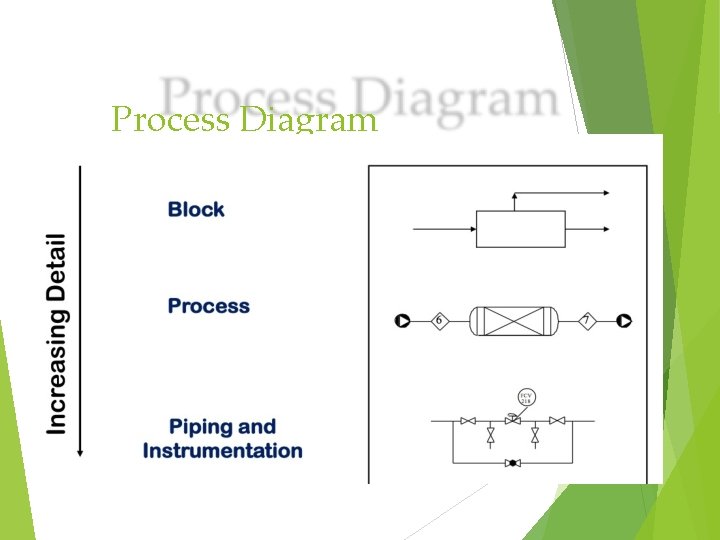
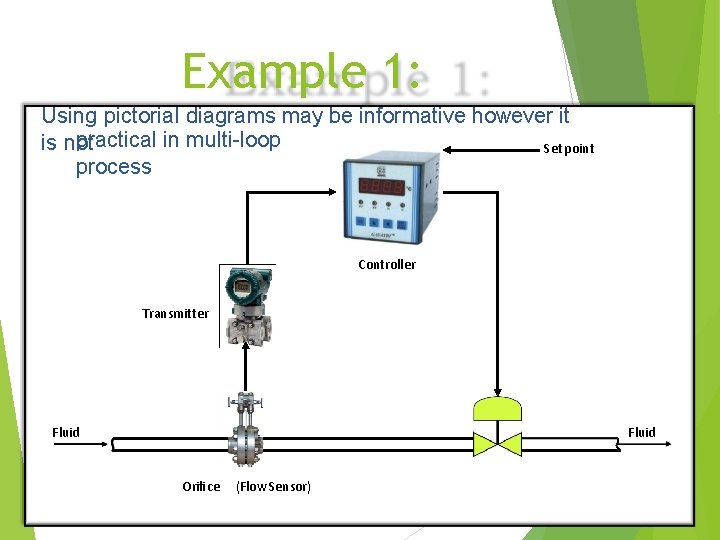
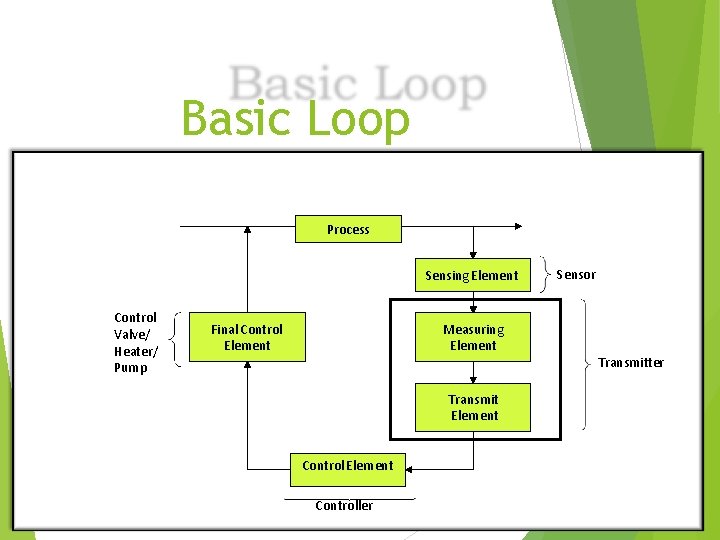
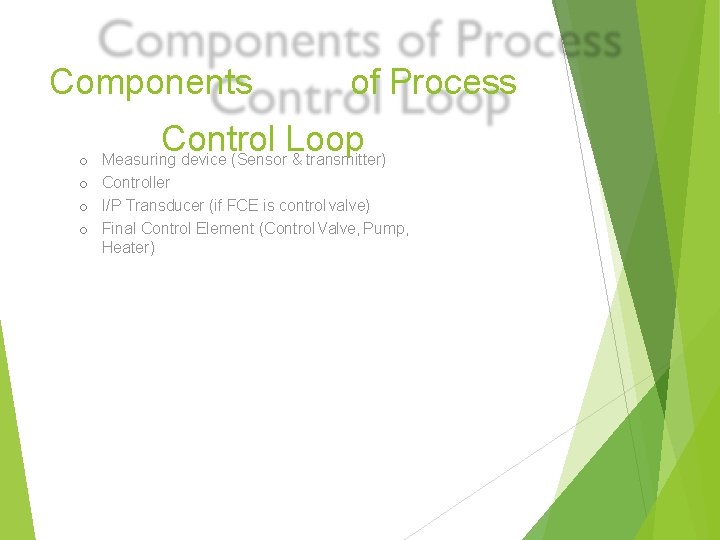
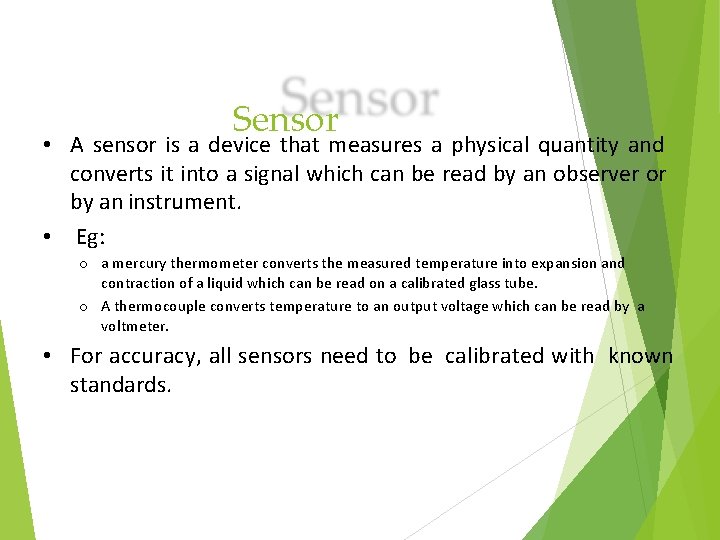
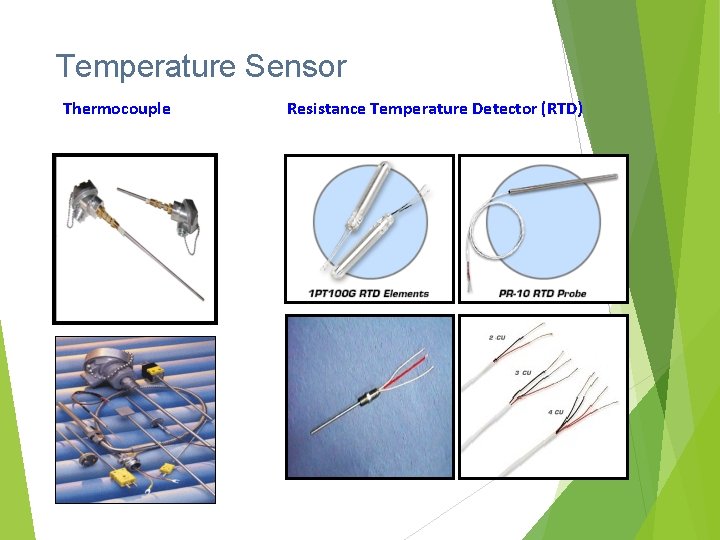
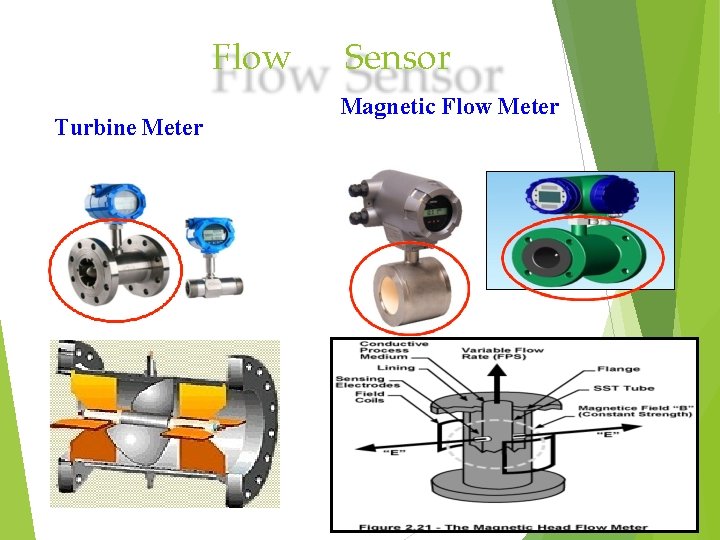
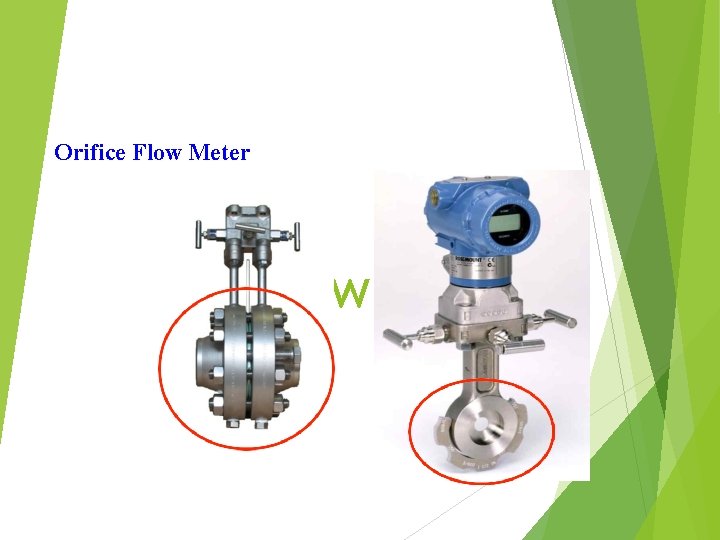
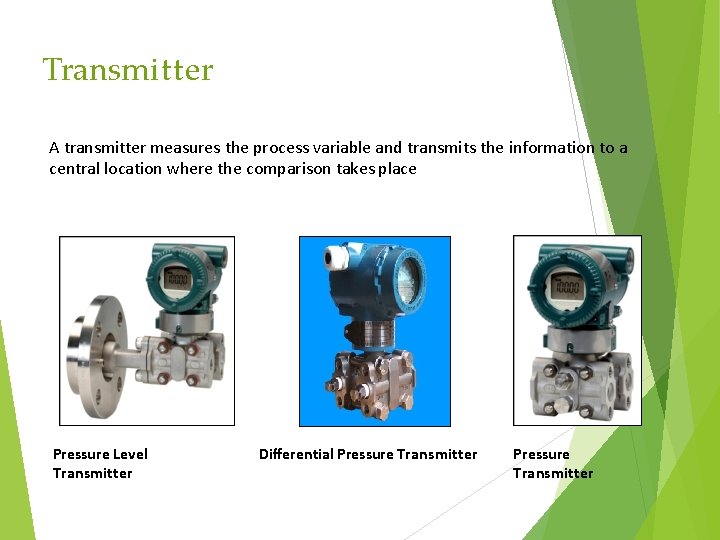
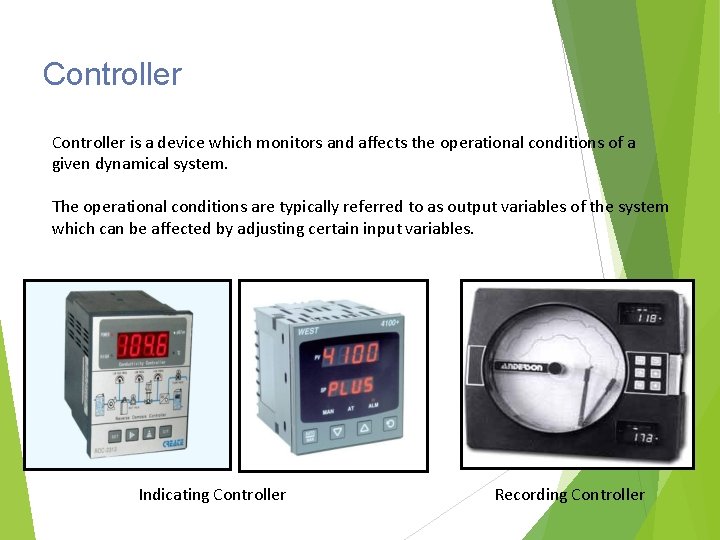
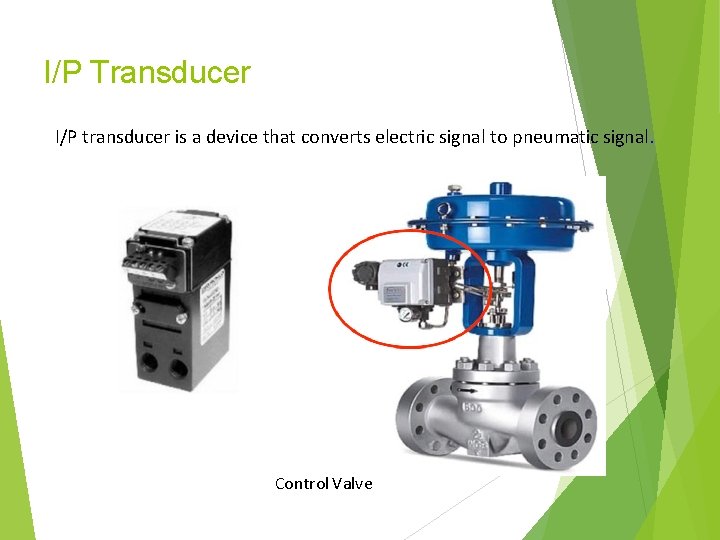
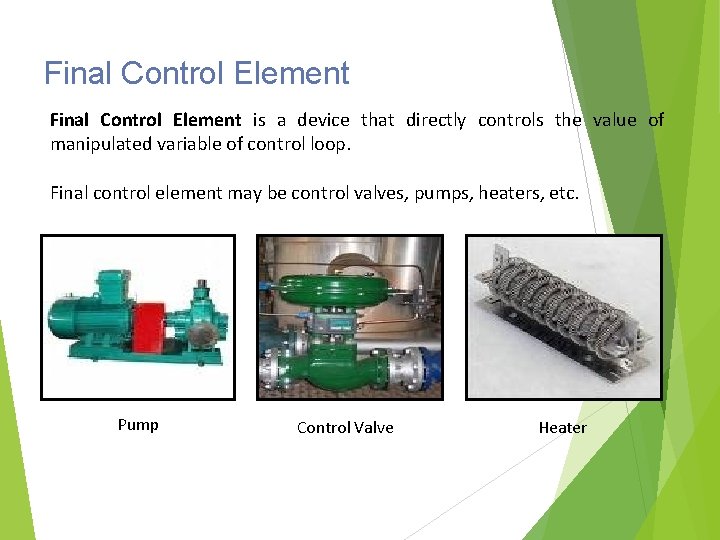
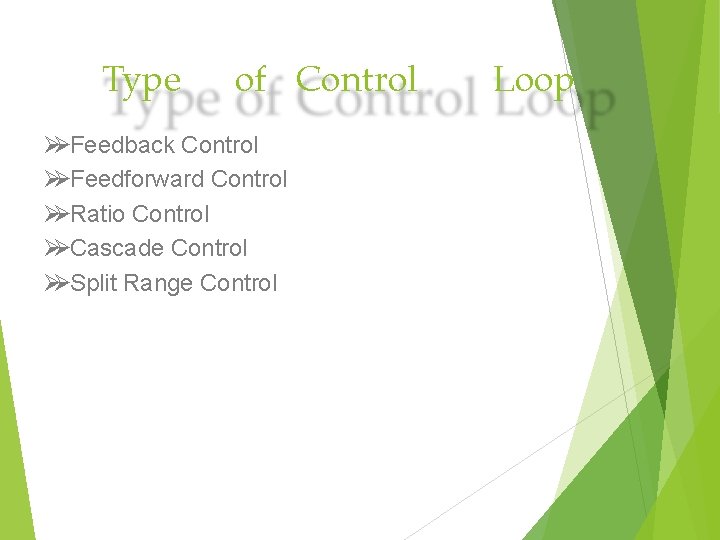
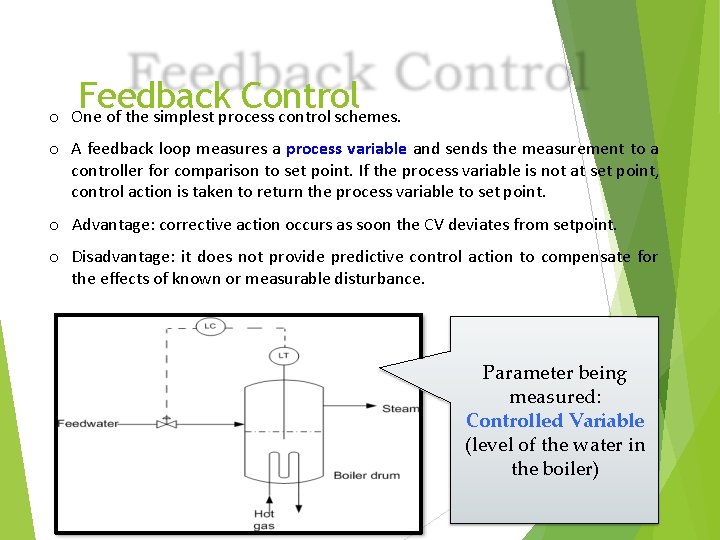
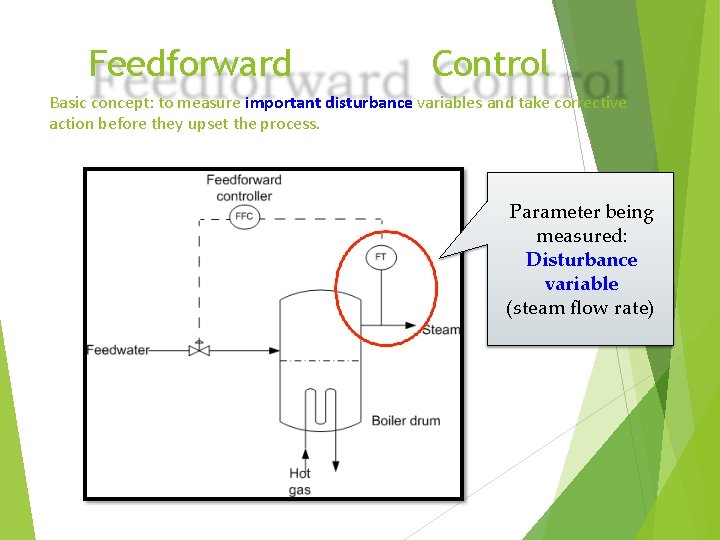
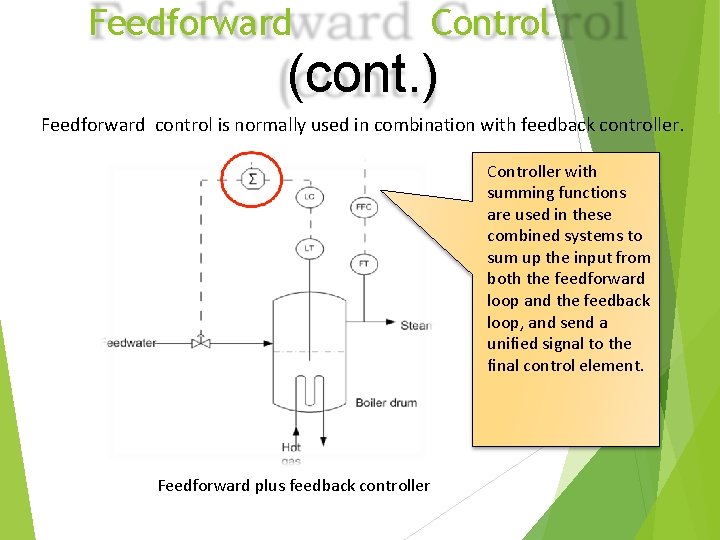
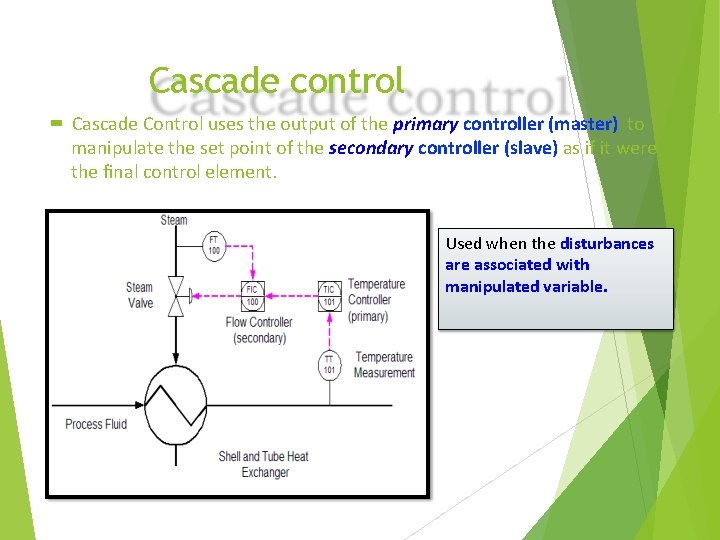
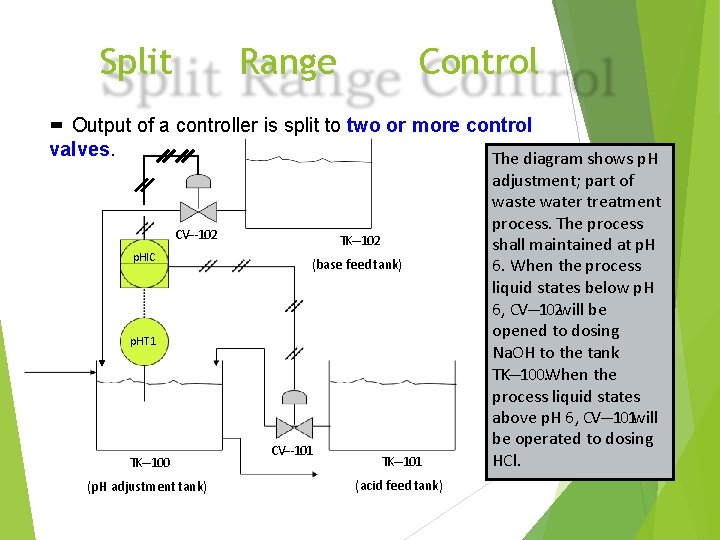
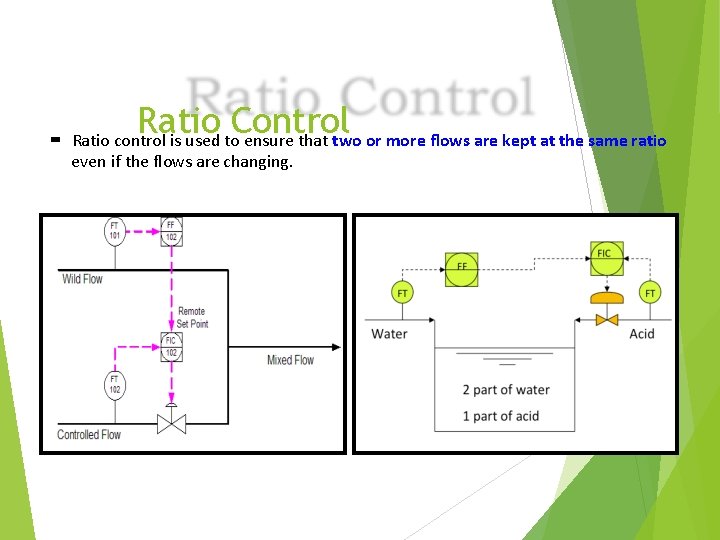
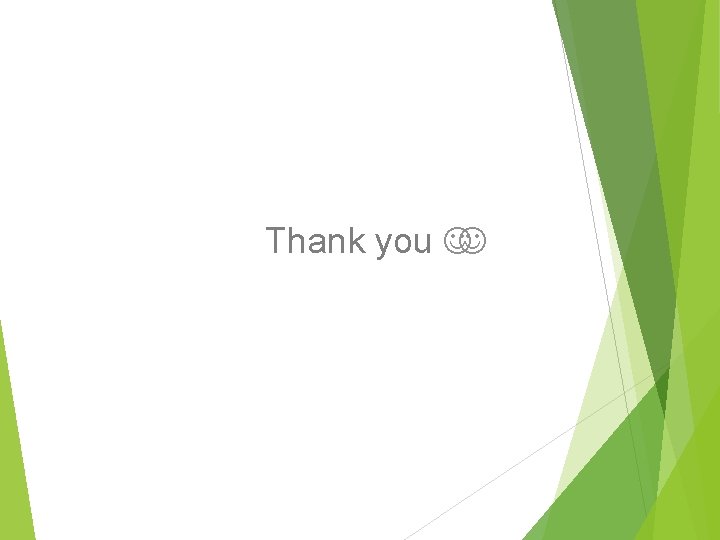
- Slides: 27
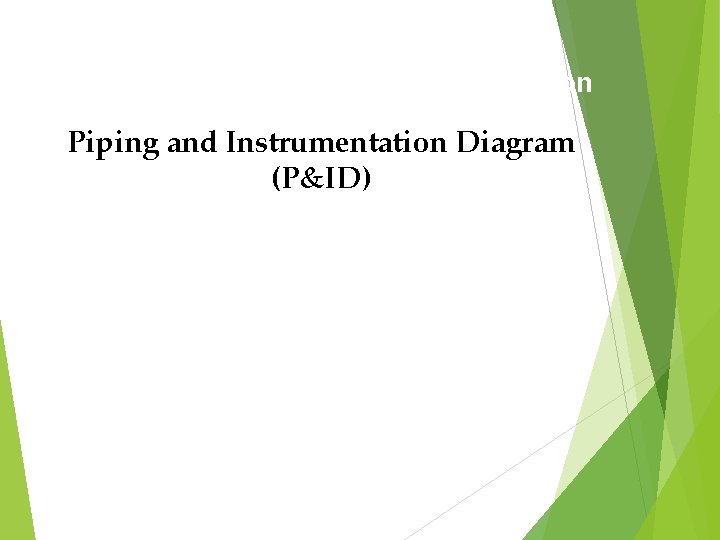
Process Instrumentation ERT 213 Piping and Instrumentation Diagram (P&ID)
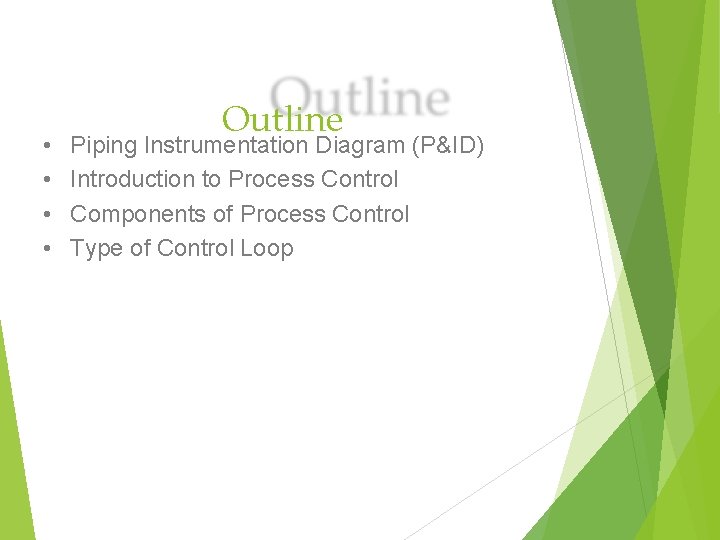
• • Outline Piping Instrumentation Diagram (P&ID) Introduction to Process Control Components of Process Control Type of Control Loop
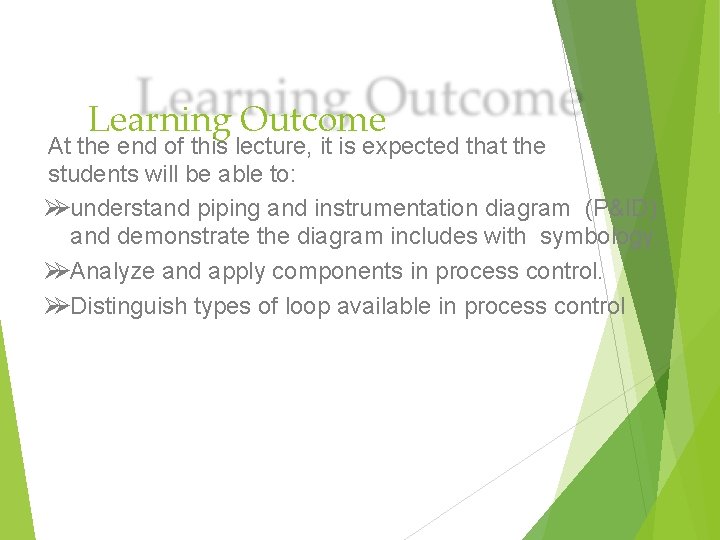
Learning Outcome At the end of this lecture, it is expected that the students will be able to: understand piping and instrumentation diagram (P&ID) and demonstrate the diagram includes with symbology. Analyze and apply components in process control. Distinguish types of loop available in process control
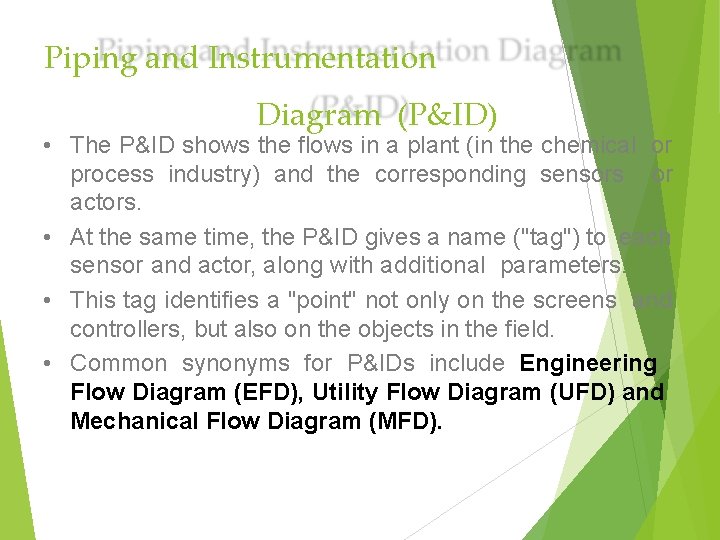
Piping and Instrumentation Diagram (P&ID) • The P&ID shows the flows in a plant (in the chemical or process industry) and the corresponding sensors or actors. • At the same time, the P&ID gives a name ("tag") to each sensor and actor, along with additional parameters. • This tag identifies a "point" not only on the screens and controllers, but also on the objects in the field. • Common synonyms for P&IDs include Engineering Flow Diagram (EFD), Utility Flow Diagram (UFD) and Mechanical Flow Diagram (MFD).
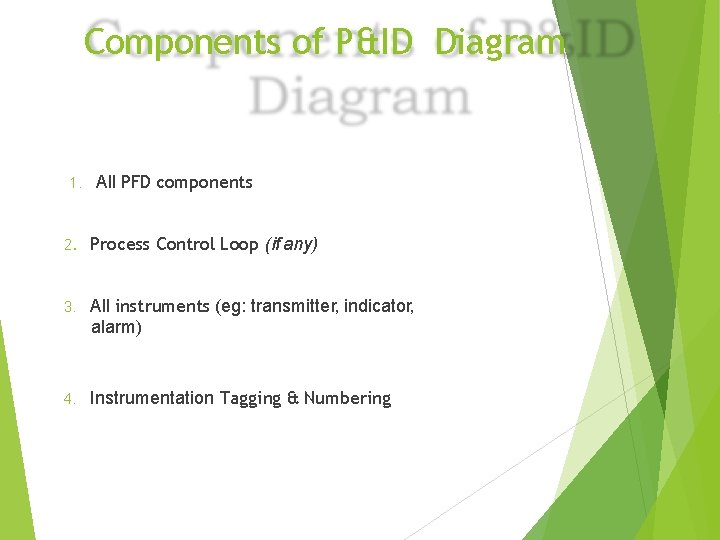
Components of P&ID Diagram 1. All PFD components 2. Process Control Loop (if any) 3. All instruments (eg: transmitter, indicator, alarm) 4. Instrumentation Tagging & Numbering
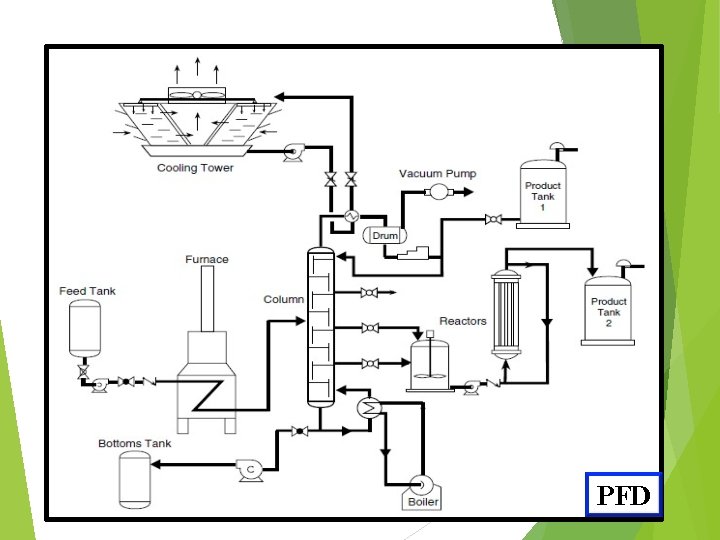
PFD
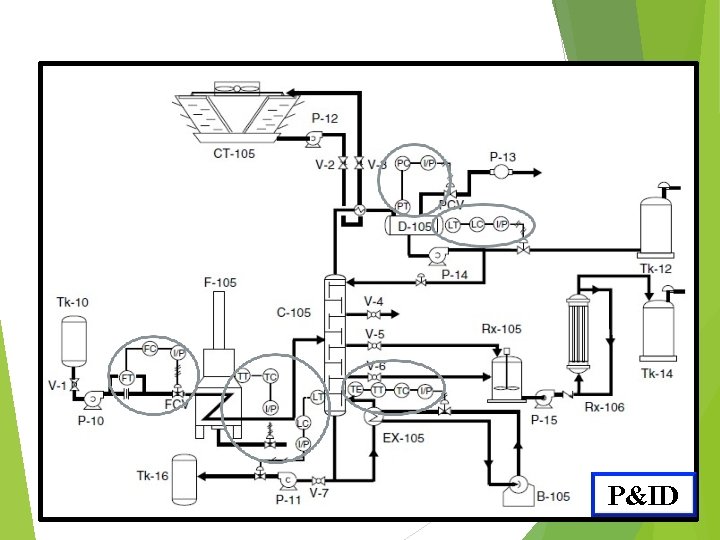
P&ID
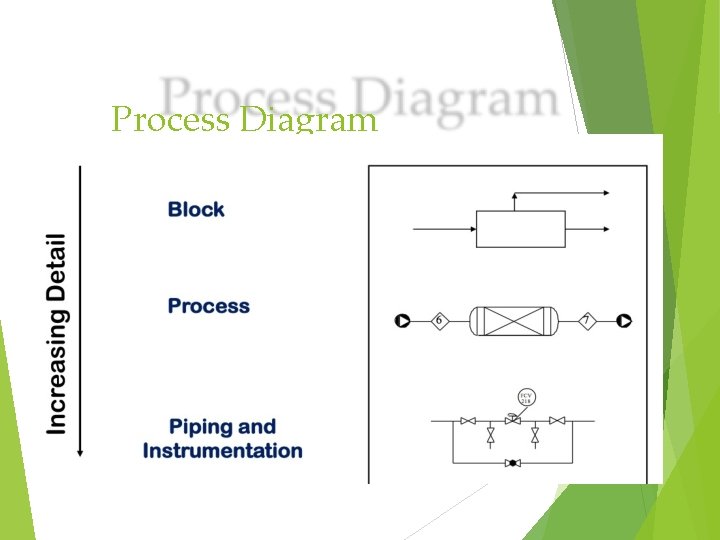
Process Diagram
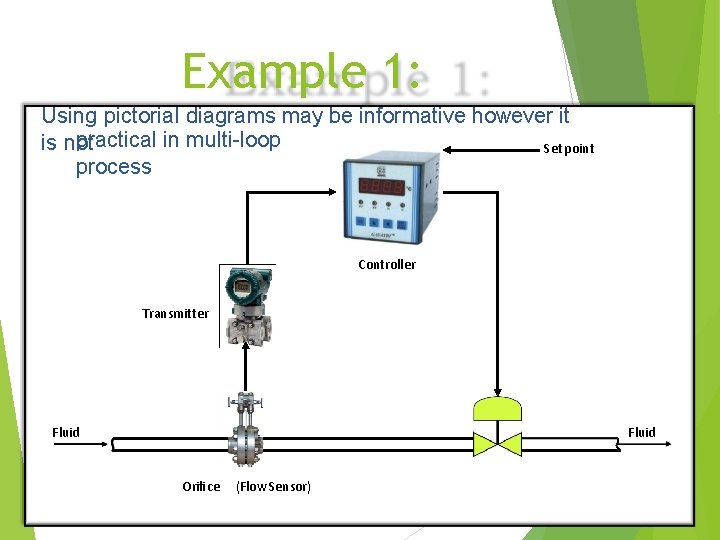
Example 1: Using pictorial diagrams may be informative however it practical in multi-loop is not Set point process Controller Transmitter Fluid Orifice (Flow Sensor)
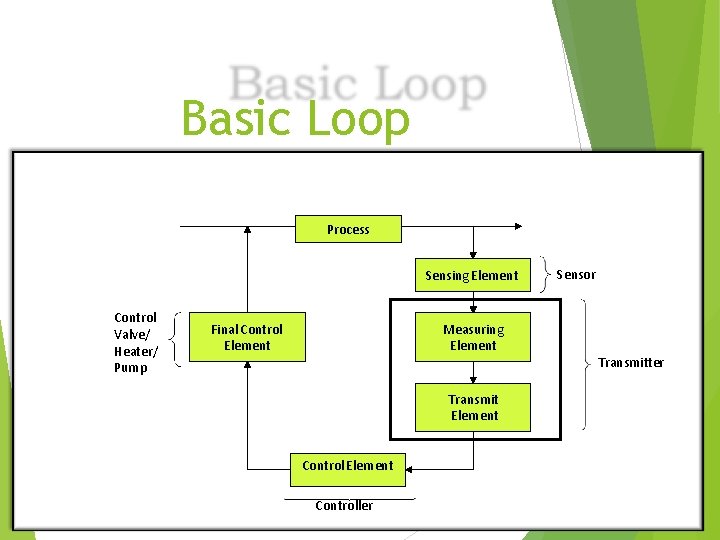
Basic Loop Process Sensing Element Control Valve/ Heater/ Pump Final Control Element Measuring Element Transmit Element Controller Sensor Transmitter
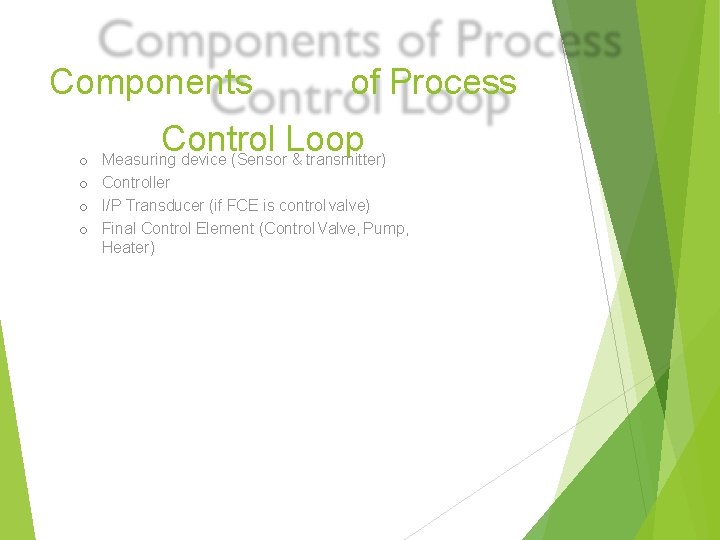
Components of Process Control Loop Measuring device (Sensor & transmitter) o o Controller o I/P Transducer (if FCE is control valve) o Final Control Element (Control Valve, Pump, Heater)
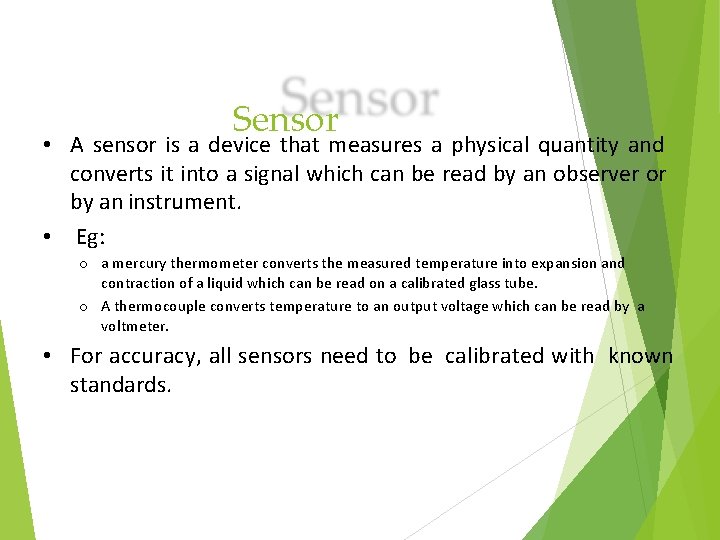
Sensor • A sensor is a device that measures a physical quantity and converts it into a signal which can be read by an observer or by an instrument. • Eg: o a mercury thermometer converts the measured temperature into expansion and contraction of a liquid which can be read on a calibrated glass tube. o A thermocouple converts temperature to an output voltage which can be read by a voltmeter. • For accuracy, all sensors need to be calibrated with known standards.
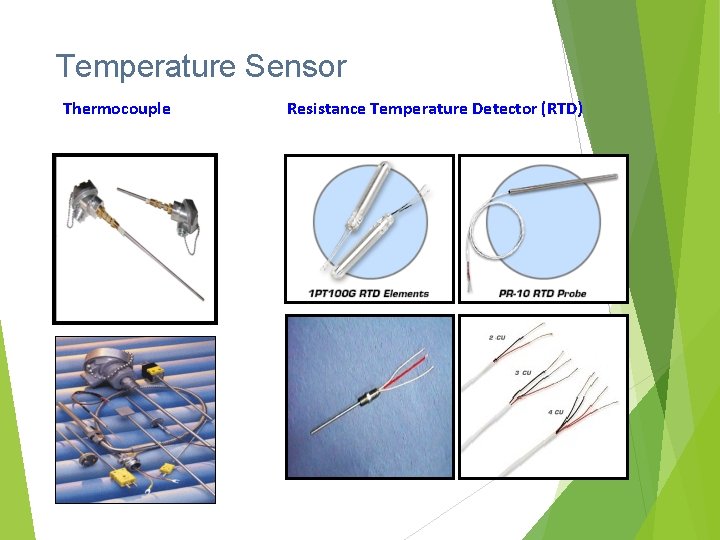
Temperature Sensor Thermocouple Resistance Temperature Detector (RTD)
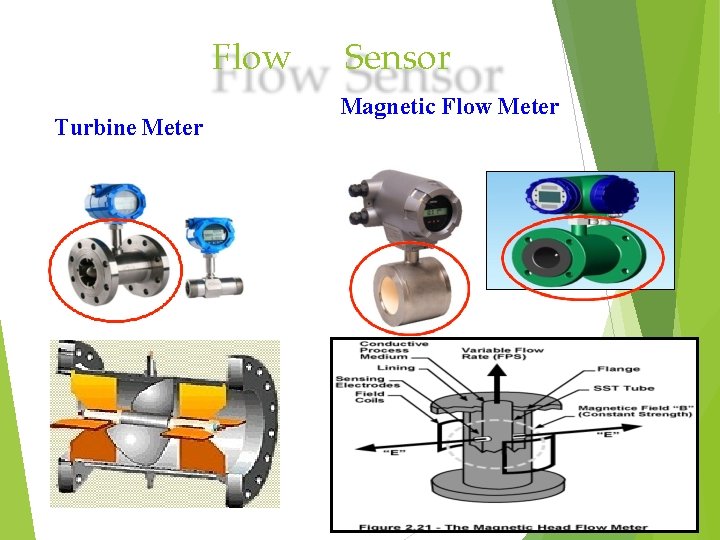
Flow Turbine Meter Sensor Magnetic Flow Meter
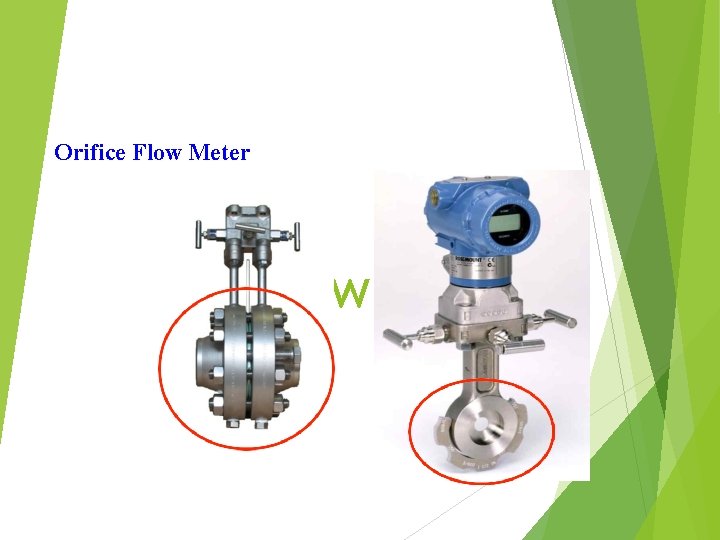
Orifice Flow Meter Flow Sensor
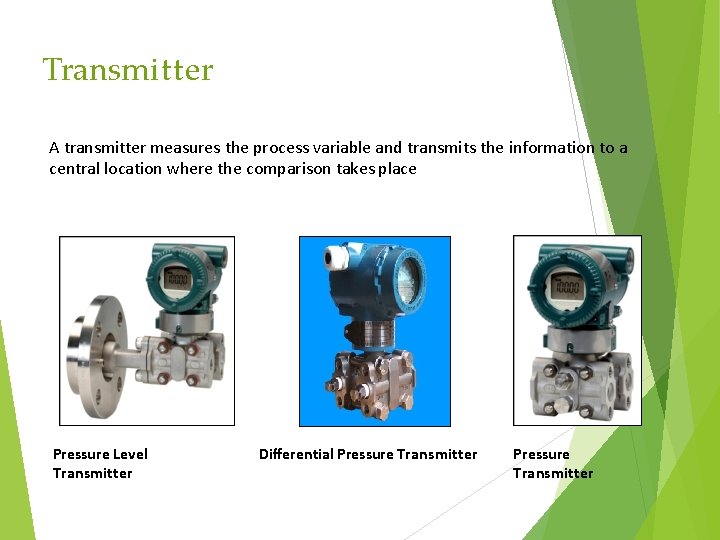
Transmitter A transmitter measures the process variable and transmits the information to a central location where the comparison takes place Pressure Level Transmitter Differential Pressure Transmitter
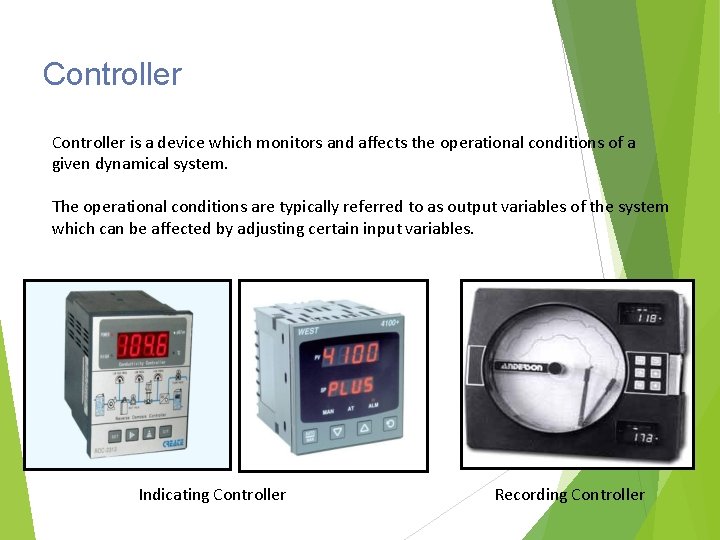
Controller is a device which monitors and affects the operational conditions of a given dynamical system. The operational conditions are typically referred to as output variables of the system which can be affected by adjusting certain input variables. Indicating Controller Recording Controller
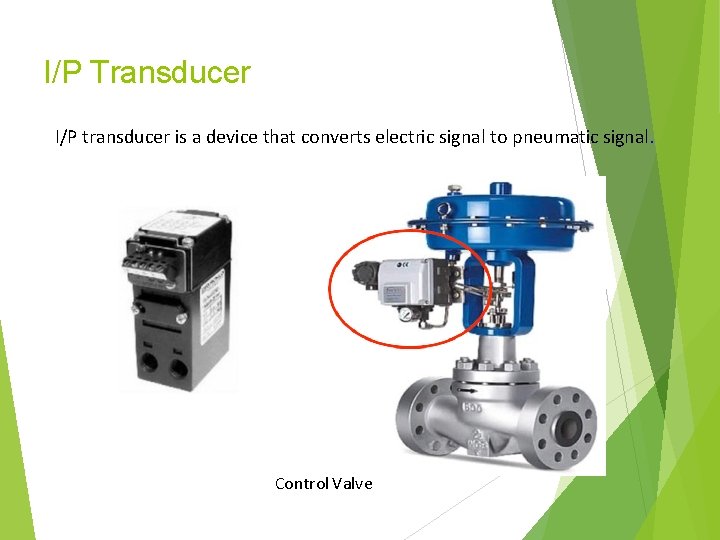
I/P Transducer I/P transducer is a device that converts electric signal to pneumatic signal. Control Valve
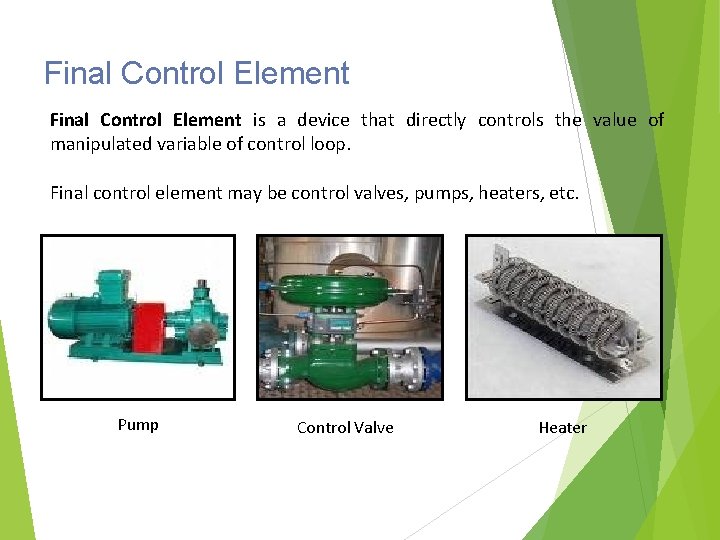
Final Control Element is a device that directly controls the value of manipulated variable of control loop. Final control element may be control valves, pumps, heaters, etc. Pump Control Valve Heater
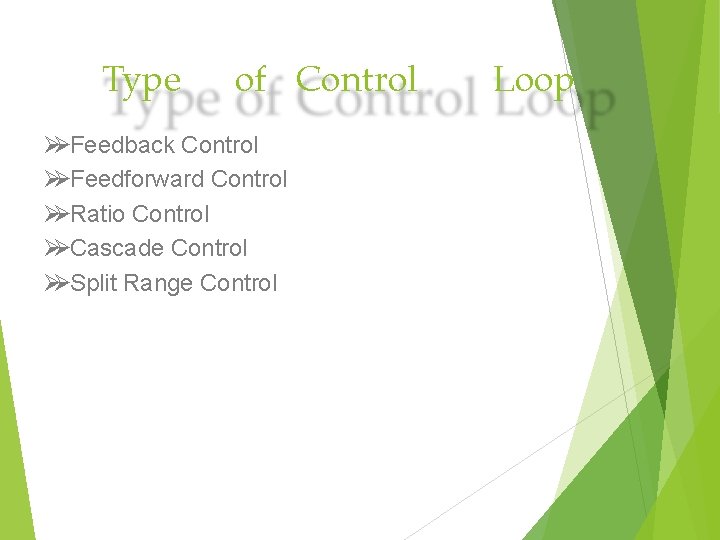
Type of Control Feedback Control Feedforward Control Ratio Control Cascade Control Split Range Control Loop
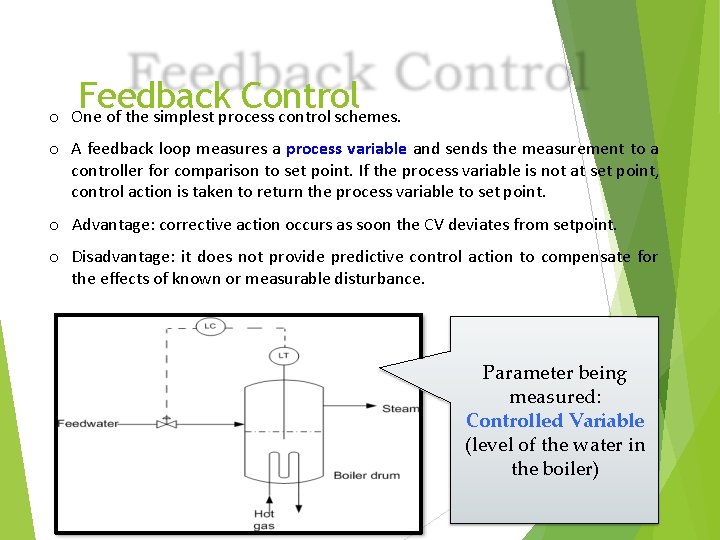
Feedback Control o One of the simplest process control schemes. o A feedback loop measures a process variable and sends the measurement to a controller for comparison to set point. If the process variable is not at set point, control action is taken to return the process variable to set point. o Advantage: corrective action occurs as soon the CV deviates from setpoint. o Disadvantage: it does not provide predictive control action to compensate for the effects of known or measurable disturbance. Parameter being measured: Controlled Variable (level of the water in the boiler)
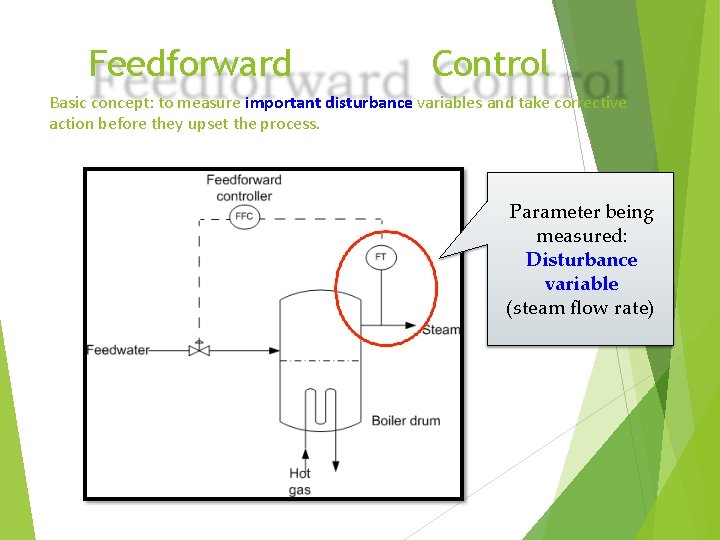
Feedforward Control Basic concept: to measure important disturbance variables and take corrective action before they upset the process. Parameter being measured: Disturbance variable (steam flow rate)
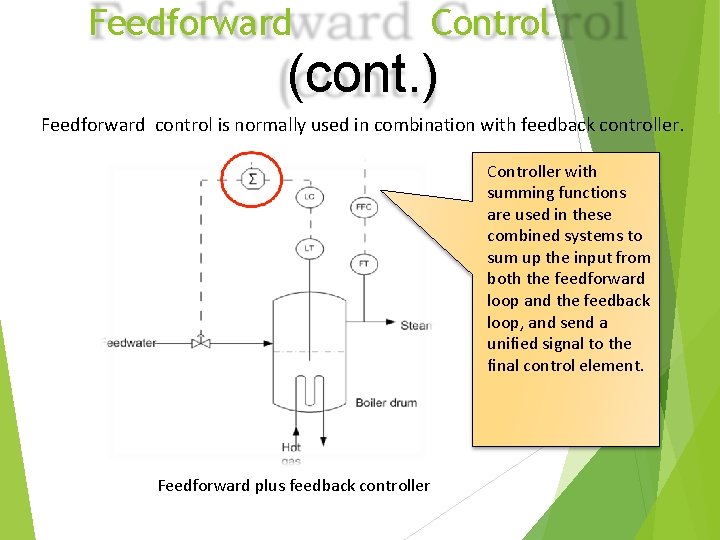
Feedforward Control (cont. ) Feedforward control is normally used in combination with feedback controller. Controller with summing functions are used in these combined systems to sum up the input from both the feedforward loop and the feedback loop, and send a unified signal to the final control element. Feedforward plus feedback controller
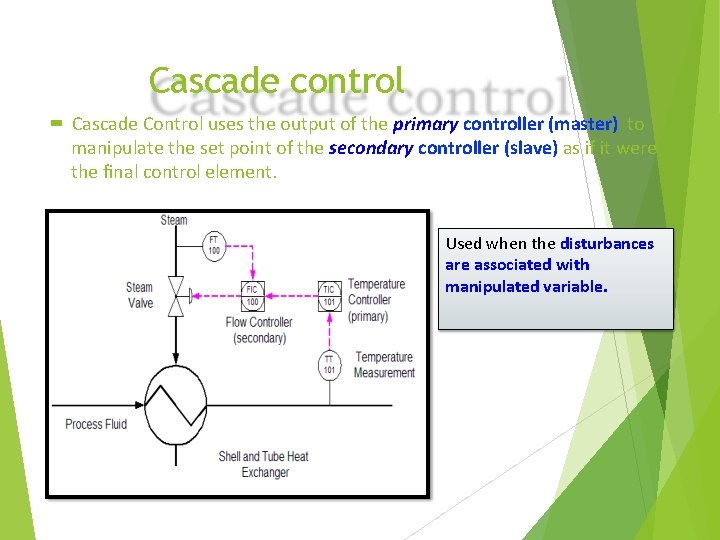
Cascade control Cascade Control uses the output of the primary controller (master) to manipulate the set point of the secondary controller (slave) as if it were the final control element. Used when the disturbances are associated with manipulated variable.
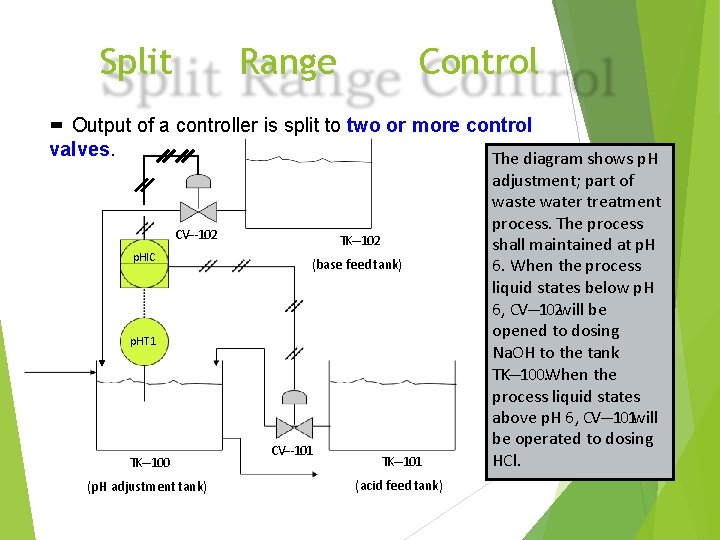
Split Range Control Output of a controller is split to two or more control valves. The diagram shows p. H CV‐‐‐ 102 p. HIC TK‐‐‐ 102 (base feed tank) p. HT 1 TK‐‐‐ 100 (p. H adjustment tank) CV‐‐‐ 101 TK‐‐‐ 101 (acid feed tank) adjustment; part of waste water treatment process. The process shall maintained at p. H 6. When the process liquid states below p. H 6, CV‐‐‐ 102 will be opened to dosing Na. OH to the tank TK‐‐‐ 100. When the process liquid states above p. H 6, CV‐‐‐ 101 will be operated to dosing HCl.
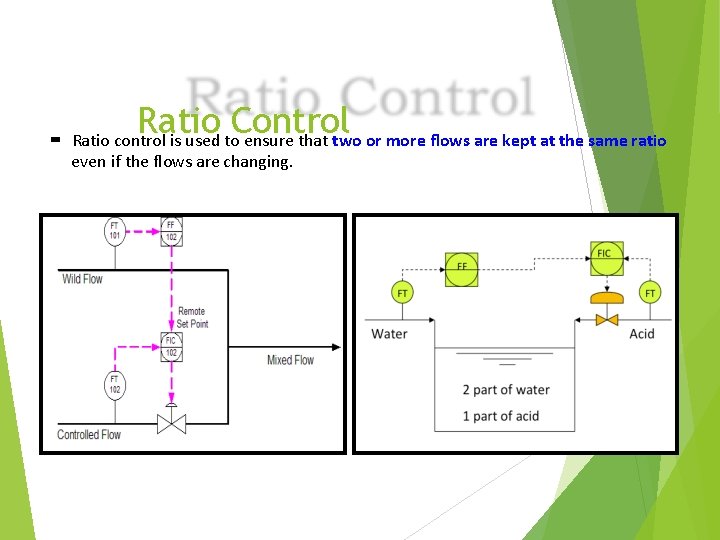
Ratio Control Ratio control is used to ensure that two or more flows are kept at the same ratio even if the flows are changing.
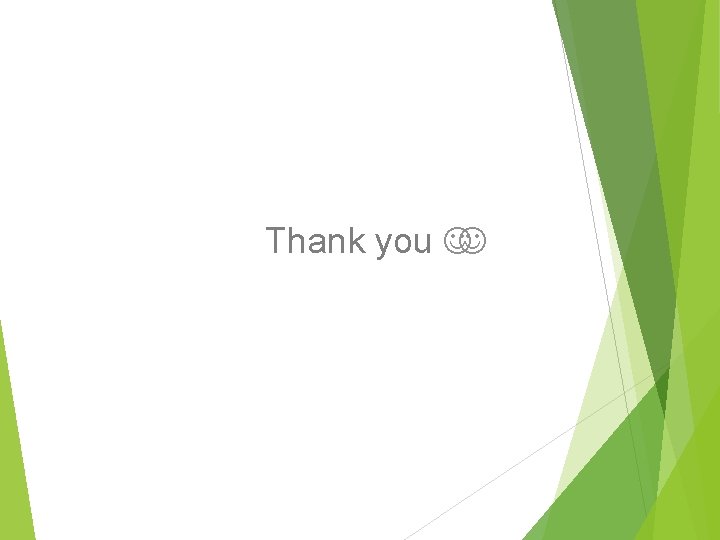
Thank you