Powering Interlocks Quench back of corrector magnets vs
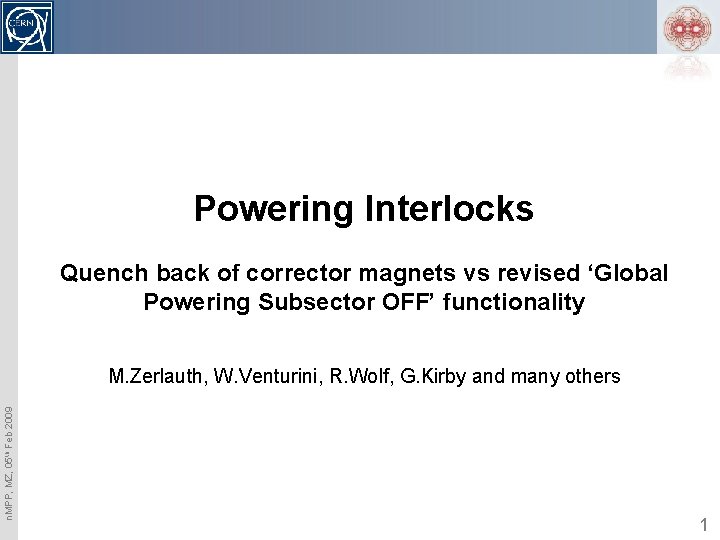
Powering Interlocks Quench back of corrector magnets vs revised ‘Global Powering Subsector OFF’ functionality n. MPP, MZ, 05 th Feb 2009 M. Zerlauth, W. Venturini, R. Wolf, G. Kirby and many others 1
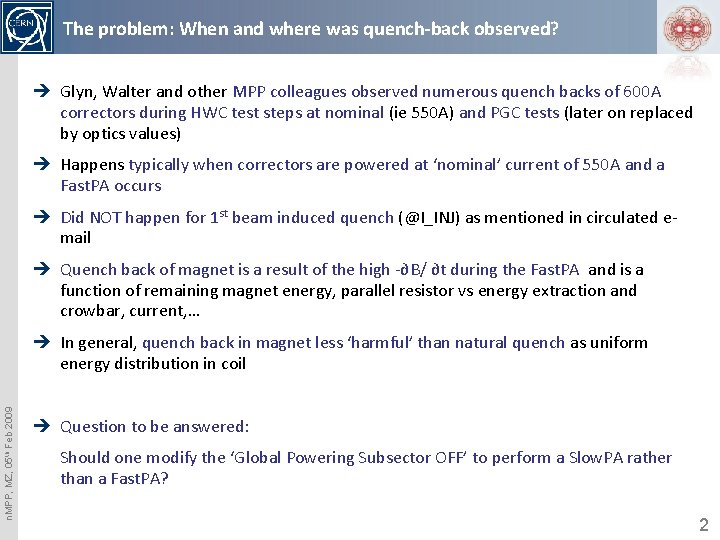
The problem: When and where was quench-back observed? è Glyn, Walter and other MPP colleagues observed numerous quench backs of 600 A correctors during HWC test steps at nominal (ie 550 A) and PGC tests (later on replaced by optics values) è Happens typically when correctors are powered at ‘nominal’ current of 550 A and a Fast. PA occurs è Did NOT happen for 1 st beam induced quench (@I_INJ) as mentioned in circulated email è Quench back of magnet is a result of the high -∂B/ ∂t during the Fast. PA and is a function of remaining magnet energy, parallel resistor vs energy extraction and crowbar, current, … n. MPP, MZ, 05 th Feb 2009 è In general, quench back in magnet less ‘harmful’ than natural quench as uniform energy distribution in coil è Question to be answered: Should one modify the ‘Global Powering Subsector OFF’ to perform a Slow. PA rather than a Fast. PA? 2
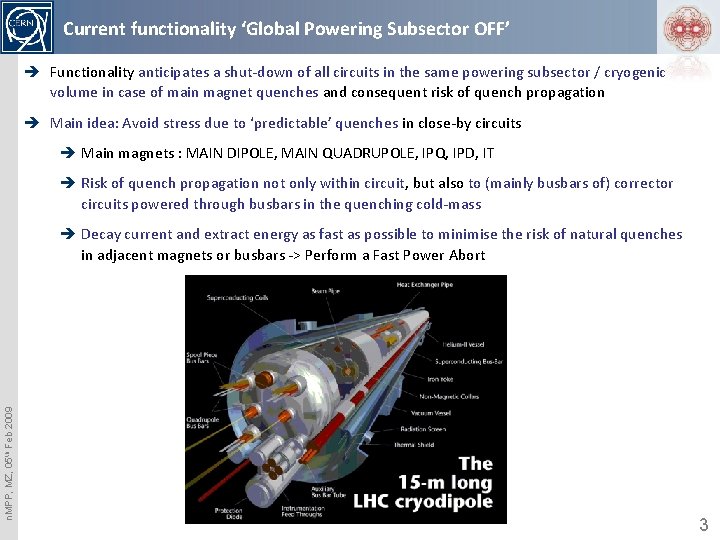
Current functionality ‘Global Powering Subsector OFF’ è Functionality anticipates a shut-down of all circuits in the same powering subsector / cryogenic volume in case of main magnet quenches and consequent risk of quench propagation è Main idea: Avoid stress due to ‘predictable’ quenches in close-by circuits è Main magnets : MAIN DIPOLE, MAIN QUADRUPOLE, IPQ, IPD, IT è Risk of quench propagation not only within circuit, but also to (mainly busbars of) corrector circuits powered through busbars in the quenching cold-mass n. MPP, MZ, 05 th Feb 2009 è Decay current and extract energy as fast as possible to minimise the risk of natural quenches in adjacent magnets or busbars -> Perform a Fast Power Abort 3
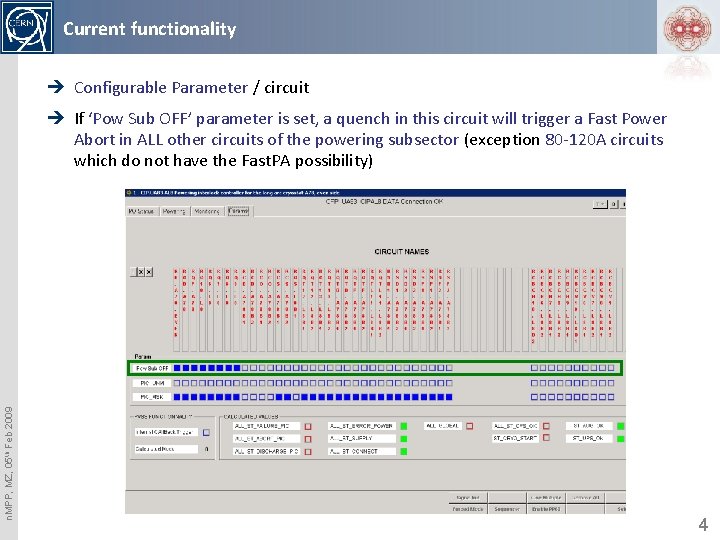
Current functionality è Configurable Parameter / circuit n. MPP, MZ, 05 th Feb 2009 è If ‘Pow Sub OFF’ parameter is set, a quench in this circuit will trigger a Fast Power Abort in ALL other circuits of the powering subsector (exception 80 -120 A circuits which do not have the Fast. PA possibility) 4
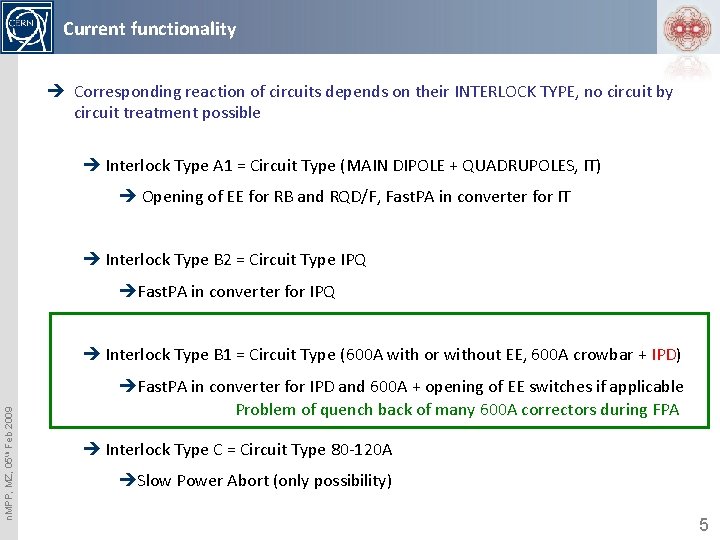
Current functionality è Corresponding reaction of circuits depends on their INTERLOCK TYPE, no circuit by circuit treatment possible è Interlock Type A 1 = Circuit Type (MAIN DIPOLE + QUADRUPOLES, IT) è Opening of EE for RB and RQD/F, Fast. PA in converter for IT è Interlock Type B 2 = Circuit Type IPQ èFast. PA in converter for IPQ n. MPP, MZ, 05 th Feb 2009 è Interlock Type B 1 = Circuit Type (600 A with or without EE, 600 A crowbar + IPD) èFast. PA in converter for IPD and 600 A + opening of EE switches if applicable Problem of quench back of many 600 A correctors during FPA è Interlock Type C = Circuit Type 80 -120 A èSlow Power Abort (only possibility) 5
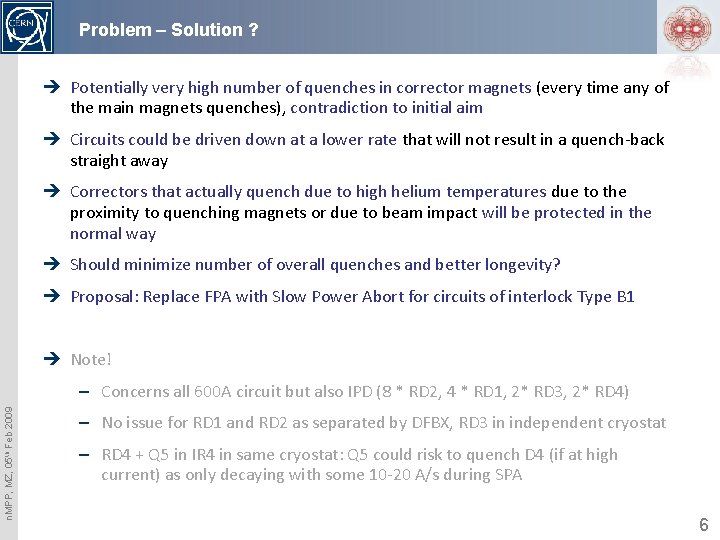
Problem – Solution ? è Potentially very high number of quenches in corrector magnets (every time any of the main magnets quenches), contradiction to initial aim è Circuits could be driven down at a lower rate that will not result in a quench-back straight away è Correctors that actually quench due to high helium temperatures due to the proximity to quenching magnets or due to beam impact will be protected in the normal way è Should minimize number of overall quenches and better longevity? è Proposal: Replace FPA with Slow Power Abort for circuits of interlock Type B 1 è Note! n. MPP, MZ, 05 th Feb 2009 – Concerns all 600 A circuit but also IPD (8 * RD 2, 4 * RD 1, 2* RD 3, 2* RD 4) – No issue for RD 1 and RD 2 as separated by DFBX, RD 3 in independent cryostat – RD 4 + Q 5 in IR 4 in same cryostat: Q 5 could risk to quench D 4 (if at high current) as only decaying with some 10 -20 A/s during SPA 6
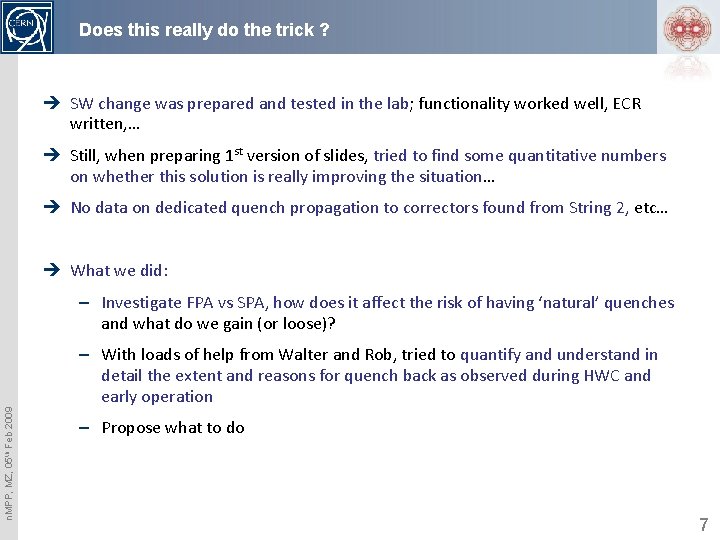
Does this really do the trick ? è SW change was prepared and tested in the lab; functionality worked well, ECR written, … è Still, when preparing 1 st version of slides, tried to find some quantitative numbers on whether this solution is really improving the situation… è No data on dedicated quench propagation to correctors found from String 2, etc… è What we did: – Investigate FPA vs SPA, how does it affect the risk of having ‘natural’ quenches and what do we gain (or loose)? n. MPP, MZ, 05 th Feb 2009 – With loads of help from Walter and Rob, tried to quantify and understand in detail the extent and reasons for quench back as observed during HWC and early operation – Propose what to do 7
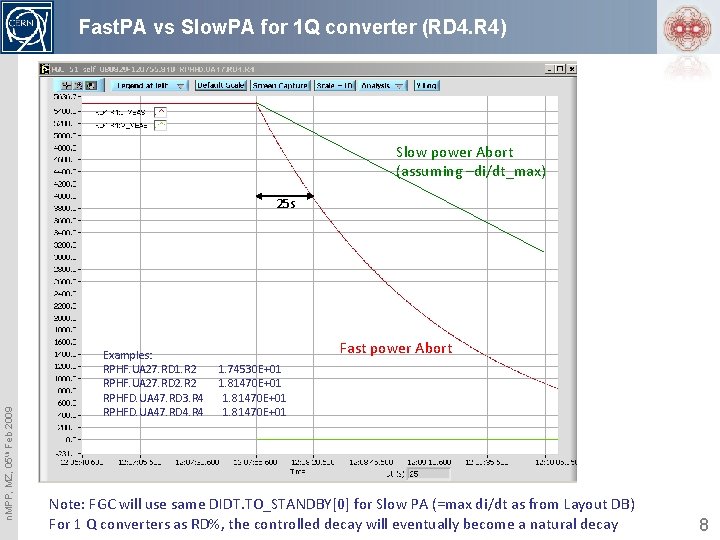
Fast. PA vs Slow. PA for 1 Q converter (RD 4. R 4) Slow power Abort (assuming –di/dt_max) n. MPP, MZ, 05 th Feb 2009 25 s Examples: RPHF. UA 27. RD 1. R 2 RPHF. UA 27. RD 2. R 2 RPHFD. UA 47. RD 3. R 4 RPHFD. UA 47. RD 4. R 4 Fast power Abort 1. 74530 E+01 1. 81470 E+01 Note: FGC will use same DIDT. TO_STANDBY[0] for Slow PA (=max di/dt as from Layout DB) For 1 Q converters as RD%, the controlled decay will eventually become a natural decay 8
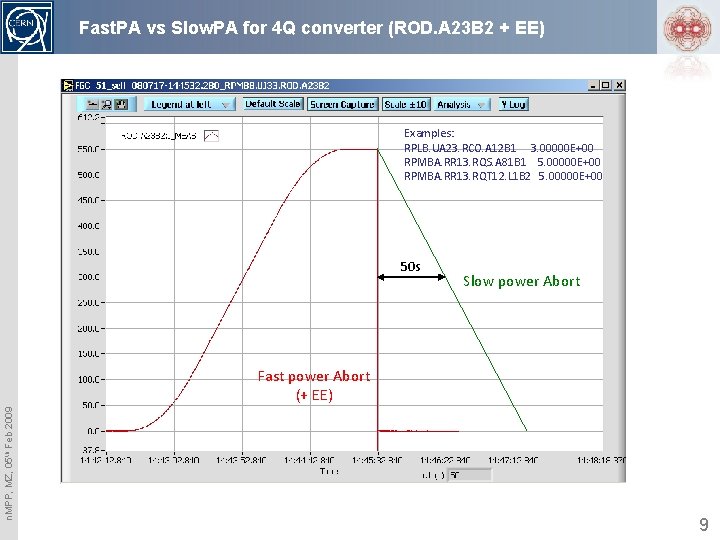
Fast. PA vs Slow. PA for 4 Q converter (ROD. A 23 B 2 + EE) Examples: RPLB. UA 23. RCO. A 12 B 1 3. 00000 E+00 RPMBA. RR 13. RQS. A 81 B 1 5. 00000 E+00 RPMBA. RR 13. RQT 12. L 1 B 2 5. 00000 E+00 50 s Slow power Abort n. MPP, MZ, 05 th Feb 2009 Fast power Abort (+ EE) 9
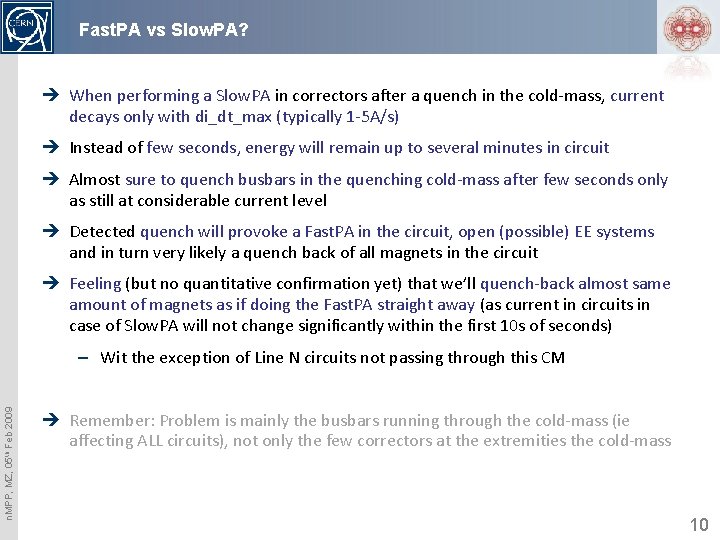
Fast. PA vs Slow. PA? è When performing a Slow. PA in correctors after a quench in the cold-mass, current decays only with di_dt_max (typically 1 -5 A/s) è Instead of few seconds, energy will remain up to several minutes in circuit è Almost sure to quench busbars in the quenching cold-mass after few seconds only as still at considerable current level è Detected quench will provoke a Fast. PA in the circuit, open (possible) EE systems and in turn very likely a quench back of all magnets in the circuit è Feeling (but no quantitative confirmation yet) that we’ll quench-back almost same amount of magnets as if doing the Fast. PA straight away (as current in circuits in case of Slow. PA will not change significantly within the first 10 s of seconds) n. MPP, MZ, 05 th Feb 2009 – Wit the exception of Line N circuits not passing through this CM è Remember: Problem is mainly the busbars running through the cold-mass (ie affecting ALL circuits), not only the few correctors at the extremities the cold-mass 10
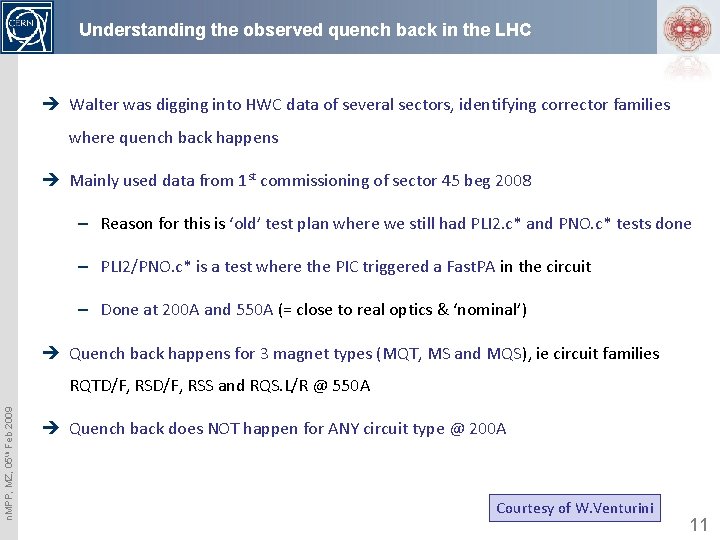
Understanding the observed quench back in the LHC è Walter was digging into HWC data of several sectors, identifying corrector families where quench back happens è Mainly used data from 1 st commissioning of sector 45 beg 2008 – Reason for this is ‘old’ test plan where we still had PLI 2. c* and PNO. c* tests done – PLI 2/PNO. c* is a test where the PIC triggered a Fast. PA in the circuit – Done at 200 A and 550 A (= close to real optics & ‘nominal’) è Quench back happens for 3 magnet types (MQT, MS and MQS), ie circuit families n. MPP, MZ, 05 th Feb 2009 RQTD/F, RSS and RQS. L/R @ 550 A è Quench back does NOT happen for ANY circuit type @ 200 A Courtesy of W. Venturini 11
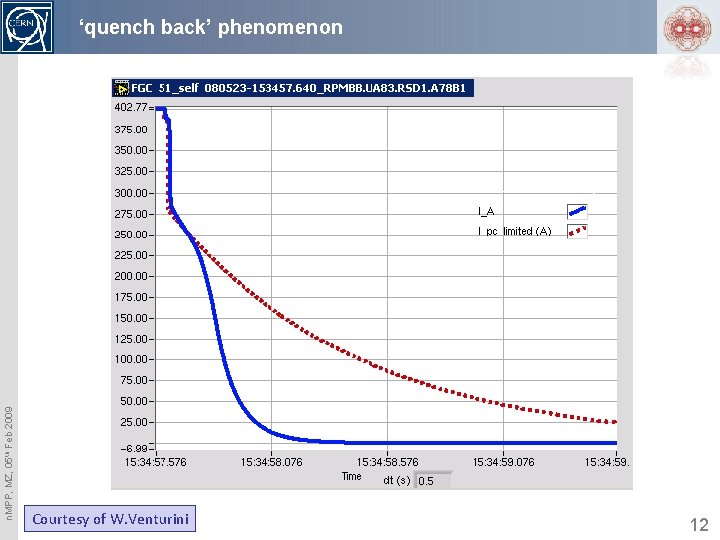
n. MPP, MZ, 05 th Feb 2009 ‘quench back’ phenomenon Courtesy of W. Venturini 12
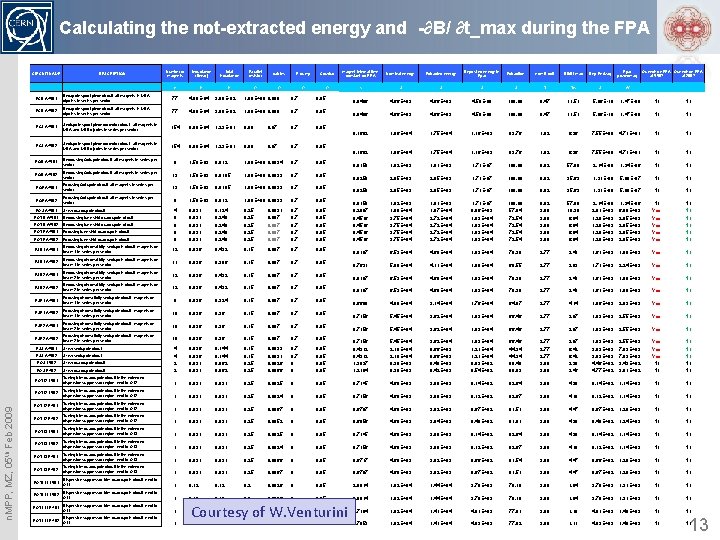
Calculating the not-extracted energy and -∂B/ ∂t_max during the FPA CIRCUIT NAME DESCRIPTION Number of magnets Inductance (linear) n. MPP, MZ, 05 th Feb 2009 # total inductance H Parallel resistor cables Ω Ω H R dump Crowbar Ω magnet internal time constant for FPA Ω RCD. A 45 B 1 Decapole spool piece circuit, all magnets in MBA dipoles in series per sector 77 4. 00 E-04 3. 08 E-02 1. 00 E+09 0. 008 0. 7 0. 05 RCD. A 45 B 2 Decapole spool piece circuit, all magnets in MBA dipoles in series per sector 77 4. 00 E-04 3. 08 E-02 1. 00 E+09 0. 008 0. 7 0. 05 RCS. A 45 B 1 Sextupole spool piece corrector circuit, all magnets in MBA and MBB dipoles in series per sector 154 8. 00 E-04 1. 23 E-01 0. 08 0. 07 0. 05 RCS. A 45 B 2 Sextupole spool piece corrector circuit, all magnets in MBA and MBB dipoles in series per sector 154 8. 00 E-04 1. 23 E-01 0. 08 0. 07 0. 05 ROD. A 45 B 1 Defocusing Octupole circuit, all magnets in series per sector 8 1. 50 E-03 0. 012 1. 00 E+09 0. 0034 0. 7 0. 05 ROD. A 45 B 2 Defocusing Octupole circuit, all magnets in series per sector 13 1. 50 E-03 0. 0195 1. 00 E+09 0. 0033 0. 7 0. 05 ROF. A 45 B 1 Focusing Octupole circuit, all magnets in series per sector 13 1. 50 E-03 0. 0195 1. 00 E+09 0. 0033 0. 7 0. 05 ROF. A 45 B 2 Focusing Octupole circuit, all magnets in series per sector 8 1. 50 E-03 0. 012 1. 00 E+09 0. 0033 0. 7 0. 05 RQS. A 45 B 1 Skew quadrupole circuit 4 8 8 0. 031 0. 124 0. 248 0. 25 0. 0031 0. 007 0. 7 0. 05 0. 05 Nominal energy Extracted energy Deposited energy in Rpar Extraction nom B coil DB/Dt max Dep En/Mag J Rpar power/mag Quench on FPA at 550? at 200? s J J J % T T/s 0. 0406 4. 66 E+03 4. 59 E-08 100. 00 0. 47 11. 51 5. 96 E-10 1. 47 E-08 W No No 0. 0406 4. 66 E+03 4. 59 E-08 100. 00 0. 47 11. 51 5. 96 E-10 1. 47 E-08 No No 0. 1602 1. 86 E+04 1. 75 E+04 1. 16 E+03 93. 76 1. 02 6. 36 7. 55 E+00 4. 71 E+01 No No 0. 0159 1. 82 E+03 1. 81 E+03 1. 71 E-07 100. 00 0. 92 57. 90 2. 14 E-08 1. 34 E-06 No No 0. 0259 2. 95 E+03 1. 71 E-07 100. 00 0. 92 35. 63 1. 31 E-08 5. 08 E-07 No No 0. 0159 0. 2887 0. 4516 1. 82 E+03 1. 88 E+04 3. 75 E+04 1. 81 E+03 1. 07 E+04 2. 72 E+04 1. 71 E-07 8. 06 E+03 1. 03 E+04 100. 00 57. 04 72. 54 0. 92 3. 00 57. 90 10. 39 6. 64 2. 14 E-08 2. 01 E+03 1. 29 E+03 1. 34 E-06 6. 98 E+03 2. 85 E+03 No Yes Yes Yes No No No 0. 8107 6. 53 E+04 4. 60 E+04 1. 93 E+04 70. 39 2. 77 3. 41 1. 61 E+03 1. 99 E+03 Yes No 0. 7631 5. 99 E+04 4. 11 E+04 1. 88 E+04 68. 55 2. 77 3. 63 1. 71 E+03 2. 24 E+03 Yes No 0. 8107 6. 53 E+04 4. 60 E+04 1. 93 E+04 70. 39 2. 77 3. 41 1. 61 E+03 1. 99 E+03 Yes No 0. 6680 4. 90 E+04 3. 14 E+04 1. 76 E+04 64. 07 2. 77 4. 14 1. 96 E+03 2. 93 E+03 Yes No 0. 7156 5. 45 E+04 3. 62 E+04 1. 83 E+04 66. 46 2. 77 3. 87 1. 83 E+03 2. 55 E+03 Yes No 5. 45 E+04 2. 18 E+04 9. 38 E+03 3. 62 E+04 9. 66 E+03 8. 48 E+03 8. 42 E+03 1. 83 E+04 1. 21 E+04 8. 93 E+02 9. 54 E+02 66. 46 44. 34 90. 48 89. 83 2. 77 3. 00 3. 87 6. 42 2. 30 2. 46 1. 83 E+03 3. 03 E+03 4. 46 E+02 4. 77 E+02 2. 55 E+03 7. 03 E+03 3. 43 E+02 3. 91 E+02 Yes Yes No No RQTD. A 45 B 1 Defocusing tune shift quadrupole circuit RQTD. A 45 B 2 Defocusing tune shift quadrupole circuit RQTF. A 45 B 1 Focusing tune shift quadrupole circuit RQTF. A 45 B 2 Focusing tune shift quadrupole circuit RSD 1. A 45 B 1 Defocusing chromaticity sextupole circuit. magnets on beam 1 in series per sector 12 0. 036 0. 432 0. 15 0. 007 0. 05 RSD 1. A 45 B 2 Defocusing chromaticity sextupole circuit. magnets on beam 1 in series per sector 11 0. 036 0. 396 0. 15 0. 007 0. 05 RSD 2. A 45 B 1 Defocusing chromaticity sextupole circuit, magnets on beam 2 in series per sector 12 0. 036 0. 432 0. 15 0. 007 0. 05 RSD 2. A 45 B 2 Defocusing chromaticity sextupole circuit, magnets on beam 2 in series per sector 12 0. 036 0. 432 0. 15 0. 007 0. 05 RSF 1. A 45 B 1 Focusing chromaticity sextupole circuit, magnets on beam 1 in series per sector 9 0. 036 0. 324 0. 15 0. 007 0. 05 RSF 1. A 45 B 2 Focusing chromaticity sextupole circuit, magnets on beam 1 in series per sector 10 0. 036 0. 15 0. 007 0. 05 RSF 2. A 45 B 1 Focusing chromaticity sextupole circuit, magnets on beam 2 in series per sector 10 0. 036 0. 15 0. 007 0. 05 RSF 2. A 45 B 2 Focusing chromaticity sextupole circuit, magnets on beam 2 in series per sector 10 0. 036 0. 15 0. 007 0. 05 RSS. A 45 B 1 Skew sextupole circuit RSS. A 45 B 2 Skew sextupole circuit 4 4 0. 036 0. 144 0. 15 0. 0033 0. 0031 0. 7 0. 05 RQS. L 5 B 2 Skew quadrupole circuit RQS. R 4 B 2 Skew quadrupole circuit 2 2 0. 031 0. 062 0. 25 0. 0026 0. 0066 0 0 0. 05 0. 7156 0. 4312 1. 3027 1. 2194 RQT 12. L 5 B 1 Tuning trim quadrupole circuit in the extended dispersion suppressor region, next to Q 12 1 0. 031 0. 25 0. 0025 0 0. 05 0. 7145 4. 69 E+03 3. 88 E+03 8. 14 E+02 82. 64 3. 00 4. 20 8. 14 E+02 1. 14 E+03 No No RQT 12. L 5 B 2 Tuning trim quadrupole circuit in the extended dispersion suppressor region, next to Q 12 1 0. 031 0. 25 0. 0024 0 0. 05 0. 7156 4. 69 E+03 3. 88 E+03 8. 12 E+02 82. 67 3. 00 4. 19 8. 12 E+02 1. 14 E+03 No No RQT 12. R 4 B 1 Tuning trim quadrupole circuit in the extended dispersion suppressor region, next to Q 12 1 0. 031 0. 25 0. 0067 0 0. 05 0. 6707 4. 69 E+03 3. 82 E+03 8. 67 E+02 81. 51 3. 00 4. 47 8. 67 E+02 1. 29 E+03 No No RQT 12. R 4 B 2 Tuning trim quadrupole circuit in the extended dispersion suppressor region, next to Q 12 1 0. 031 0. 25 0. 0052 0 0. 05 0. 6856 4. 69 E+03 3. 84 E+03 8. 48 E+02 81. 91 3. 00 4. 38 8. 48 E+02 1. 24 E+03 No No RQT 13. L 5 B 1 Tuning trim quadrupole circuit in the extended dispersion suppressor region, next to Q 13 1 0. 031 0. 25 0. 0025 0 0. 05 0. 7145 4. 69 E+03 3. 88 E+03 8. 14 E+02 82. 64 3. 00 4. 20 8. 14 E+02 1. 14 E+03 No No RQT 13. L 5 B 2 Tuning trim quadrupole circuit in the extended dispersion suppressor region, next to Q 13 1 0. 031 0. 25 0. 0024 0 0. 05 0. 7156 4. 69 E+03 3. 88 E+03 8. 12 E+02 82. 67 3. 00 4. 19 8. 12 E+02 1. 14 E+03 No No RQT 13. R 4 B 1 Tuning trim quadrupole circuit in the extended dispersion suppressor region, next to Q 13 1 0. 031 0. 25 0. 0066 0 0. 05 0. 6717 4. 69 E+03 3. 82 E+03 8. 66 E+02 81. 54 3. 00 4. 47 8. 66 E+02 1. 29 E+03 No No RQT 13. R 4 B 2 Tuning trim quadrupole circuit in the extended dispersion suppressor region, next to Q 13 1 0. 031 0. 25 0. 0067 0 0. 05 0. 6707 4. 69 E+03 3. 82 E+03 8. 67 E+02 81. 51 3. 00 4. 47 8. 67 E+02 1. 29 E+03 No No RQTL 11. L 5 B 1 Dispersion suppressor trim quadrupole circuit, next to Q 11 1 0. 12 0. 0026 0 0. 05 2. 8814 1. 82 E+04 1. 44 E+04 3. 78 E+03 79. 18 3. 00 1. 04 3. 78 E+03 1. 31 E+03 No No RQTL 11. L 5 B 2 Dispersion suppressor trim quadrupole circuit, next to Q 11 1 0. 12 0. 0026 0 0. 05 2. 8814 1. 82 E+04 1. 44 E+04 3. 78 E+03 79. 18 3. 00 1. 04 3. 78 E+03 1. 31 E+03 No No RQTL 11. R 4 B 1 Dispersion suppressor trim quadrupole circuit, next to Q 11 1 0. 12 0. 0067 0 0. 05 2. 7164 1. 82 E+04 1. 41 E+04 4. 01 E+03 77. 91 3. 00 1. 10 4. 01 E+03 1. 48 E+03 No No RQTL 11. R 4 B 2 Dispersion suppressor trim quadrupole circuit, next to Q 11 1 0. 12 0. 007 0 0. 05 2. 7053 1. 82 E+04 1. 41 E+04 4. 03 E+03 77. 82 3. 00 1. 11 4. 03 E+03 1. 49 E+03 No No Courtesy of W. Venturini 13
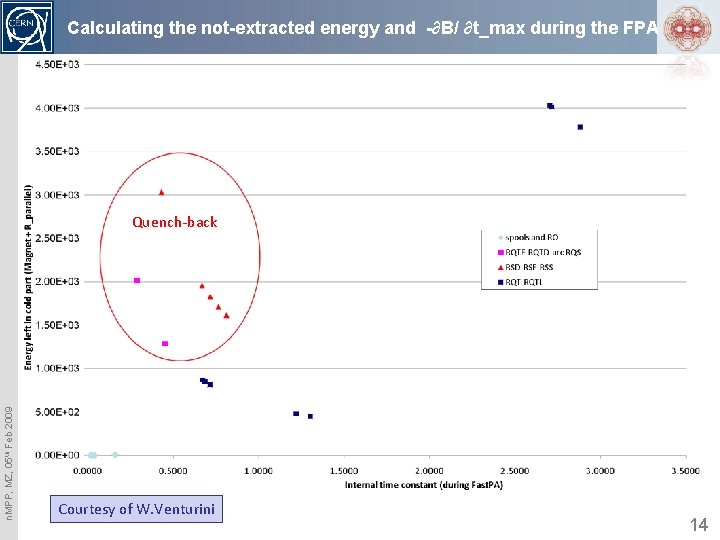
Calculating the not-extracted energy and -∂B/ ∂t_max during the FPA n. MPP, MZ, 05 th Feb 2009 Quench-back Courtesy of W. Venturini 14
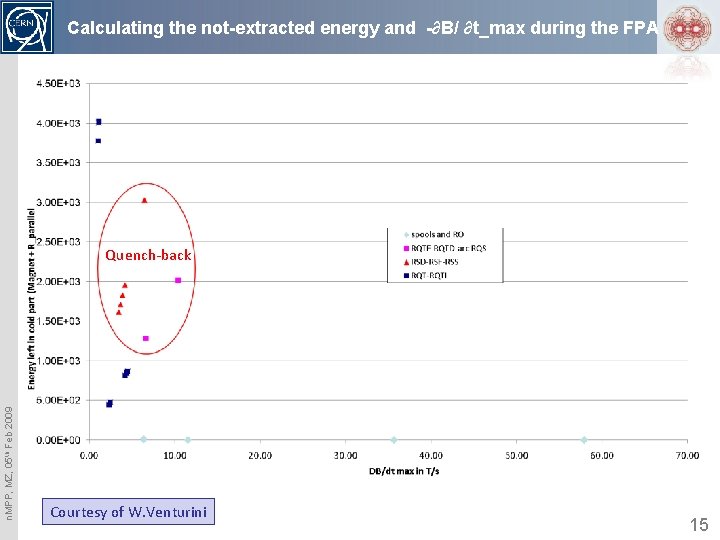
Calculating the not-extracted energy and -∂B/ ∂t_max during the FPA n. MPP, MZ, 05 th Feb 2009 Quench-back Courtesy of W. Venturini 15
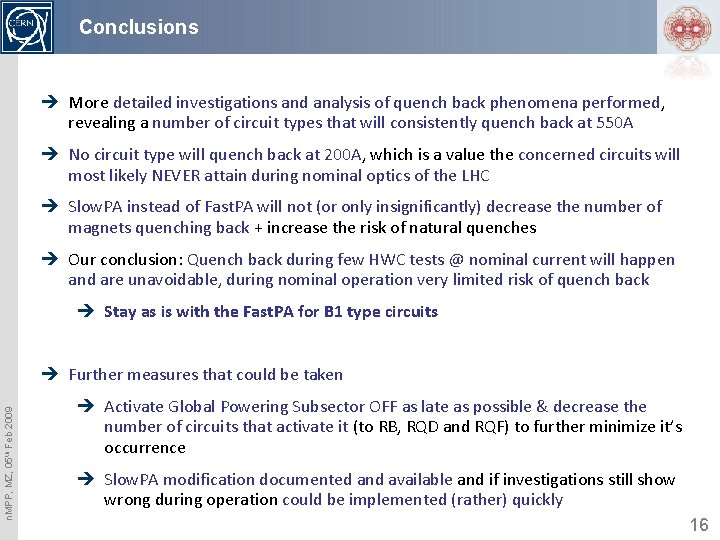
Conclusions è More detailed investigations and analysis of quench back phenomena performed, revealing a number of circuit types that will consistently quench back at 550 A è No circuit type will quench back at 200 A, which is a value the concerned circuits will most likely NEVER attain during nominal optics of the LHC è Slow. PA instead of Fast. PA will not (or only insignificantly) decrease the number of magnets quenching back + increase the risk of natural quenches è Our conclusion: Quench back during few HWC tests @ nominal current will happen and are unavoidable, during nominal operation very limited risk of quench back è Stay as is with the Fast. PA for B 1 type circuits n. MPP, MZ, 05 th Feb 2009 è Further measures that could be taken è Activate Global Powering Subsector OFF as late as possible & decrease the number of circuits that activate it (to RB, RQD and RQF) to further minimize it’s occurrence è Slow. PA modification documented and available and if investigations still show wrong during operation could be implemented (rather) quickly 16
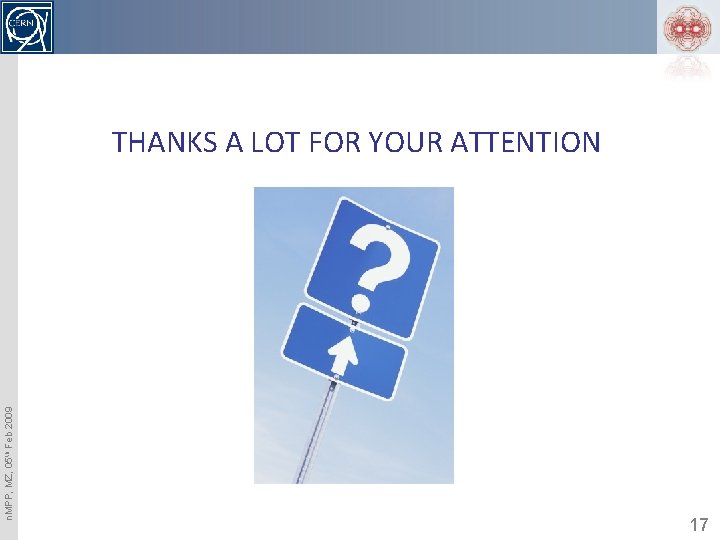
n. MPP, MZ, 05 th Feb 2009 THANKS A LOT FOR YOUR ATTENTION 17
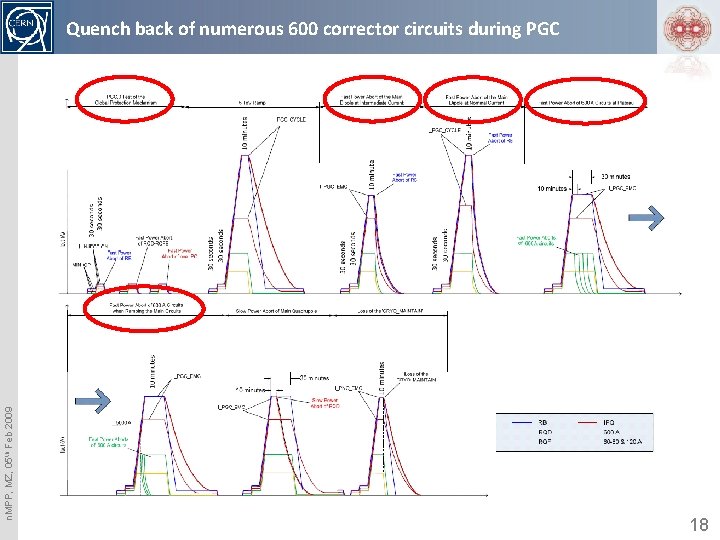
n. MPP, MZ, 05 th Feb 2009 Quench back of numerous 600 corrector circuits during PGC 18
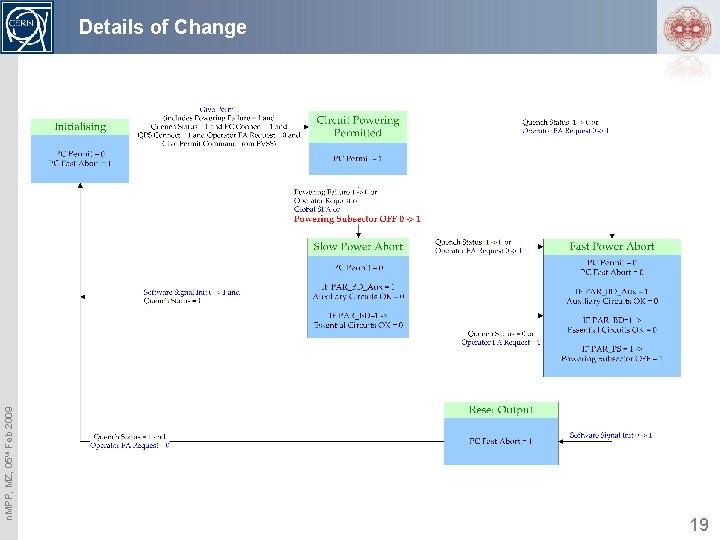
n. MPP, MZ, 05 th Feb 2009 Details of Change 19
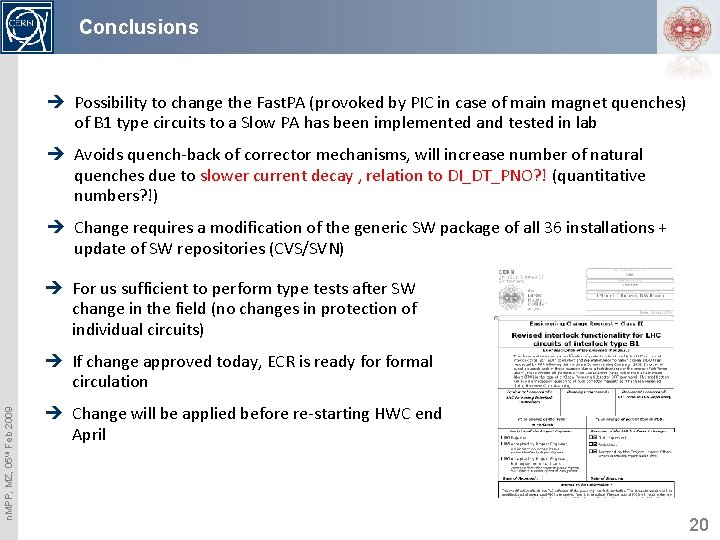
Conclusions è Possibility to change the Fast. PA (provoked by PIC in case of main magnet quenches) of B 1 type circuits to a Slow PA has been implemented and tested in lab è Avoids quench-back of corrector mechanisms, will increase number of natural quenches due to slower current decay , relation to DI_DT_PNO? ! (quantitative numbers? !) è Change requires a modification of the generic SW package of all 36 installations + update of SW repositories (CVS/SVN) è For us sufficient to perform type tests after SW change in the field (no changes in protection of individual circuits) n. MPP, MZ, 05 th Feb 2009 è If change approved today, ECR is ready formal circulation è Change will be applied before re-starting HWC end April 20
- Slides: 20