P 15462 Tethered Wind Energy Plane Energy Motion
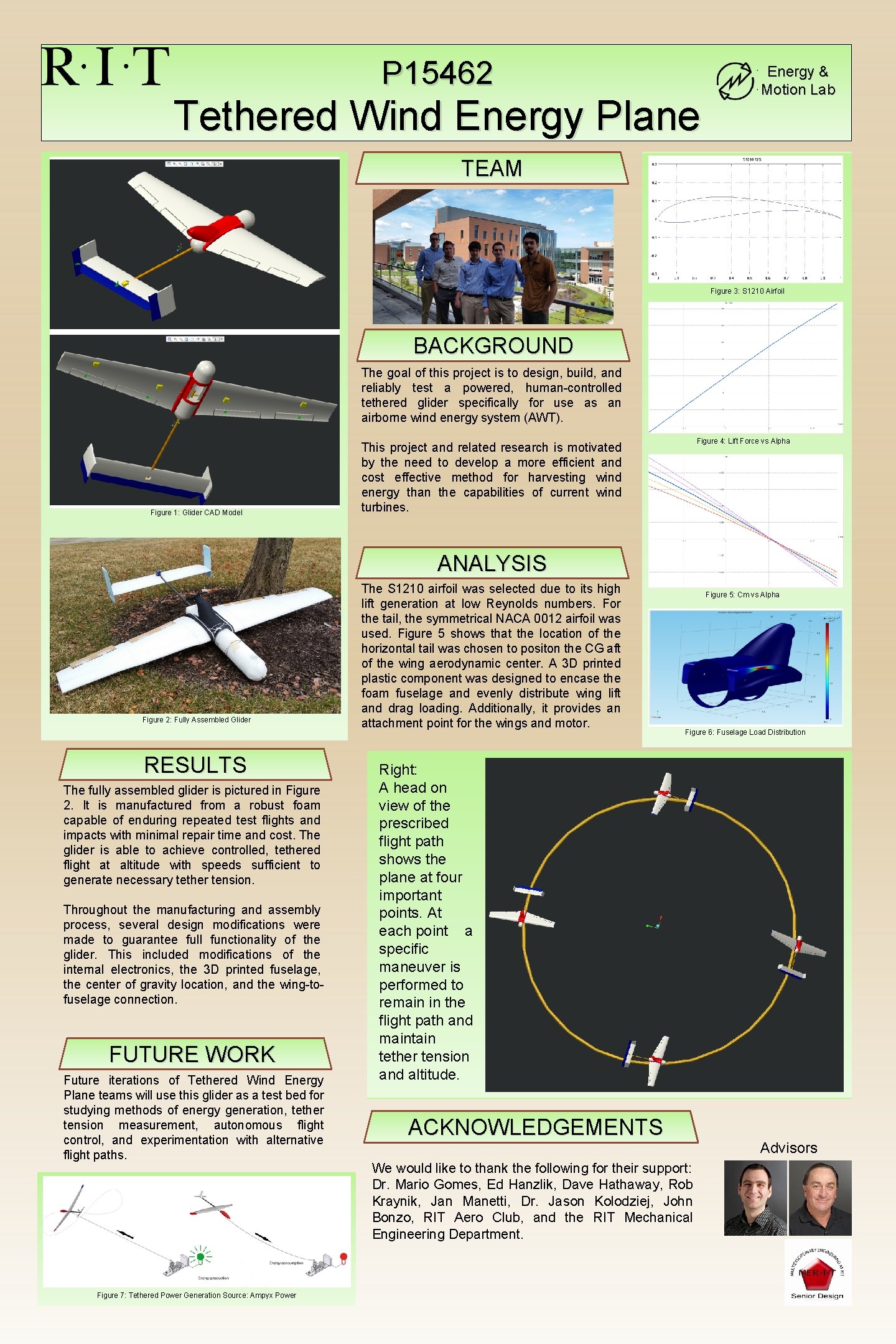
- Slides: 1
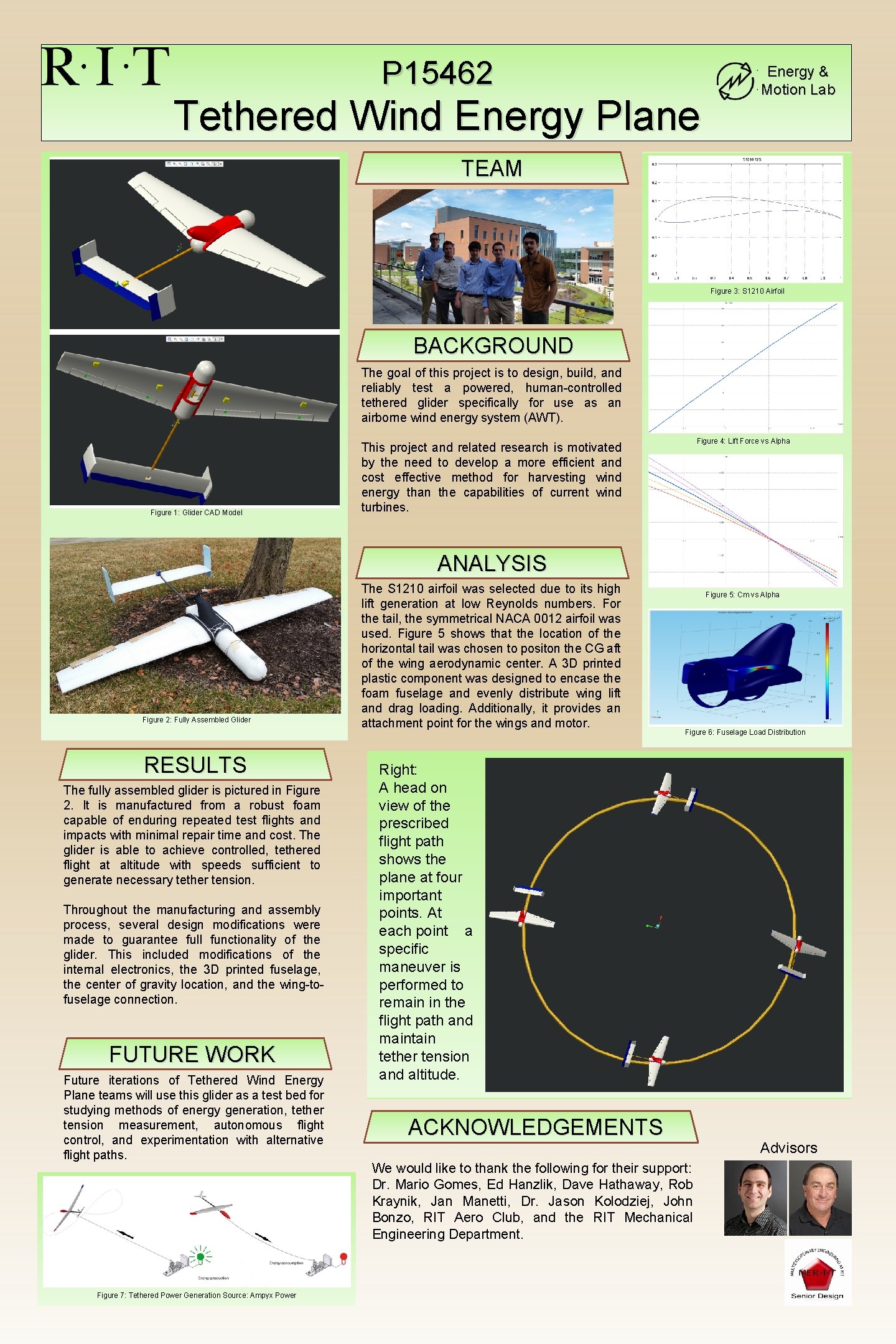
P 15462 Tethered Wind Energy Plane Energy & Motion Lab TEAM Figure 3: S 1210 Airfoil BACKGROUND The goal of this project is to design, build, and reliably test a powered, human-controlled tethered glider specifically for use as an airborne wind energy system (AWT). Figure 1: Glider CAD Model Figure 4: Lift Force vs Alpha This project and related research is motivated by the need to develop a more efficient and cost effective method for harvesting wind energy than the capabilities of current wind turbines. ANALYSIS Figure 2: Fully Assembled Glider RESULTS The fully assembled glider is pictured in Figure 2. It is manufactured from a robust foam capable of enduring repeated test flights and impacts with minimal repair time and cost. The glider is able to achieve controlled, tethered flight at altitude with speeds sufficient to generate necessary tether tension. Throughout the manufacturing and assembly process, several design modifications were made to guarantee full functionality of the glider. This included modifications of the internal electronics, the 3 D printed fuselage, the center of gravity location, and the wing-tofuselage connection. FUTURE WORK Future iterations of Tethered Wind Energy Plane teams will use this glider as a test bed for studying methods of energy generation, tether tension measurement, autonomous flight control, and experimentation with alternative flight paths. Figure 7: Tethered Power Generation Source: Ampyx Power The S 1210 airfoil was selected due to its high lift generation at low Reynolds numbers. For the tail, the symmetrical NACA 0012 airfoil was used. Figure 5 shows that the location of the horizontal tail was chosen to positon the CG aft of the wing aerodynamic center. A 3 D printed plastic component was designed to encase the foam fuselage and evenly distribute wing lift and drag loading. Additionally, it provides an attachment point for the wings and motor. Figure 5: Cm vs Alpha Figure 6: Fuselage Load Distribution Right: A head on view of the prescribed flight path shows the plane at four important points. At each point a specific maneuver is performed to remain in the flight path and maintain tether tension and altitude. ACKNOWLEDGEMENTS We would like to thank the following for their support: Dr. Mario Gomes, Ed Hanzlik, Dave Hathaway, Rob Kraynik, Jan Manetti, Dr. Jason Kolodziej, John Bonzo, RIT Aero Club, and the RIT Mechanical Engineering Department. Advisors