P 14042 UNACRUTCH Right Move Right Place Right
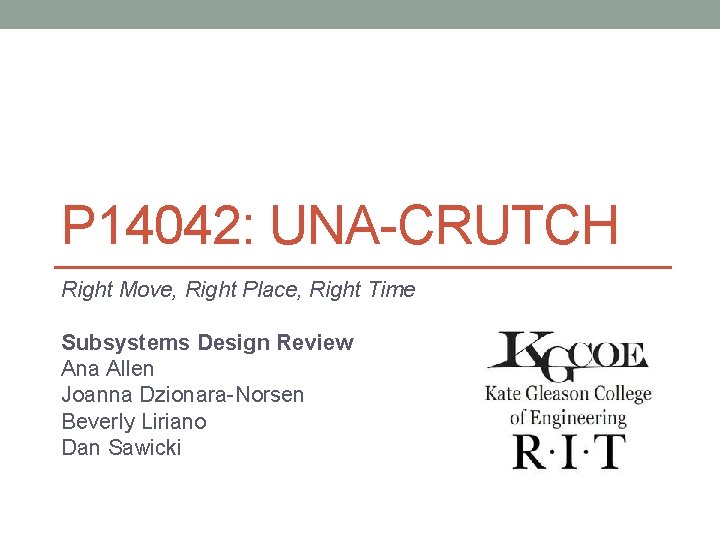
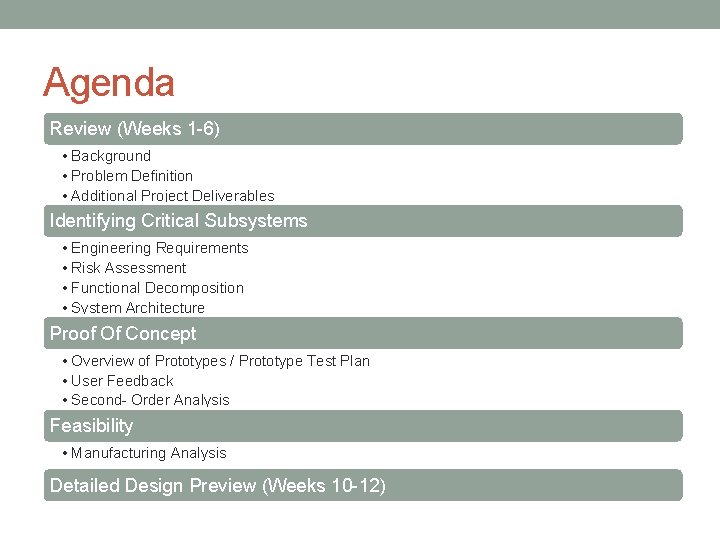
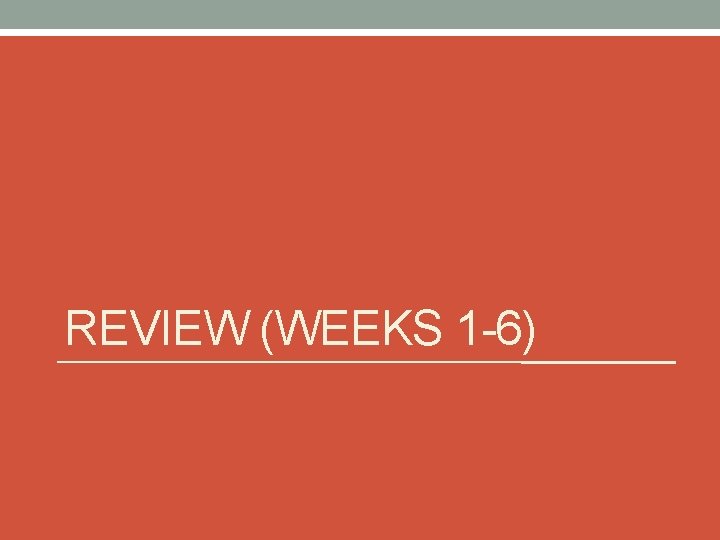
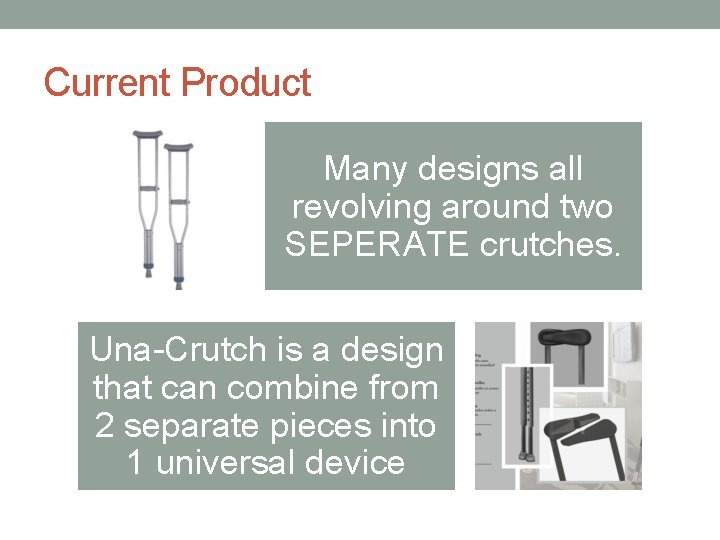
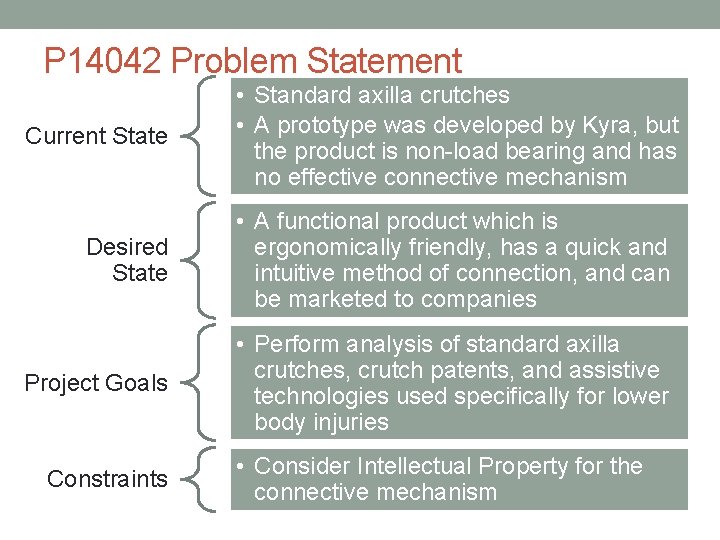
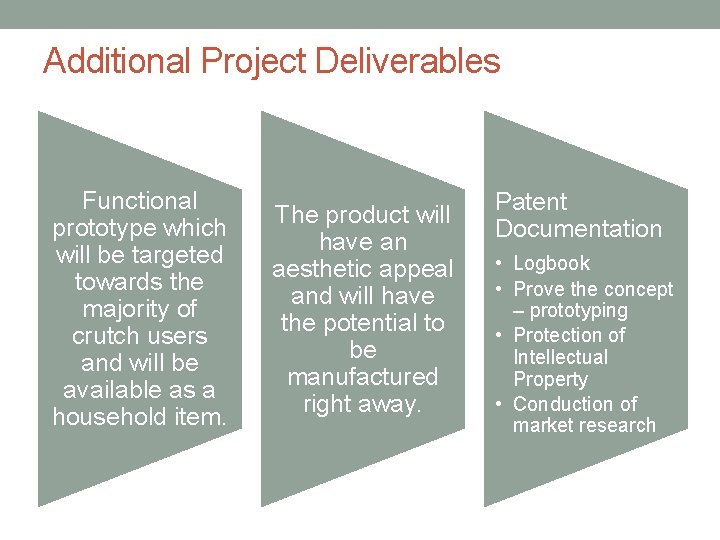
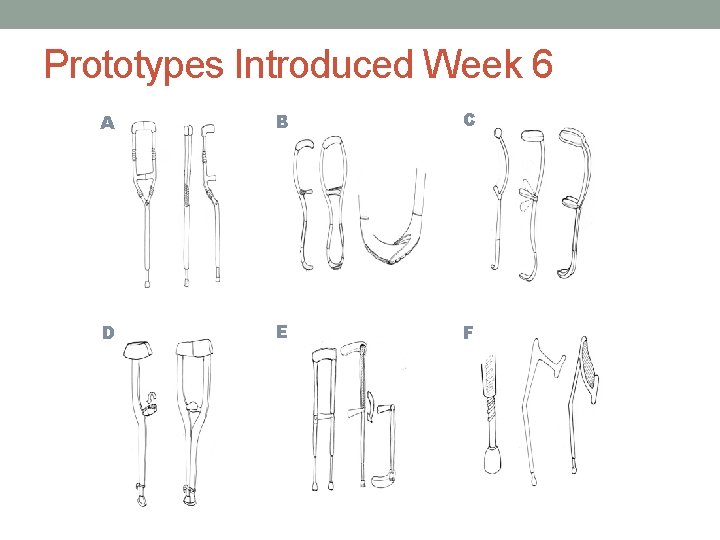
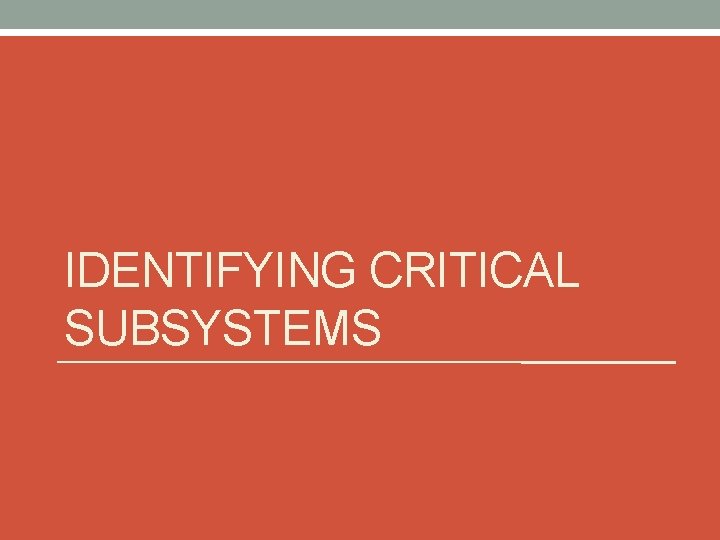
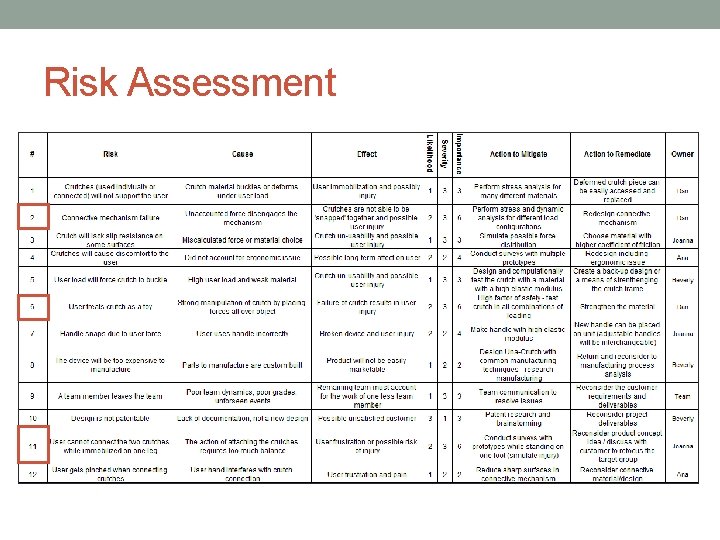
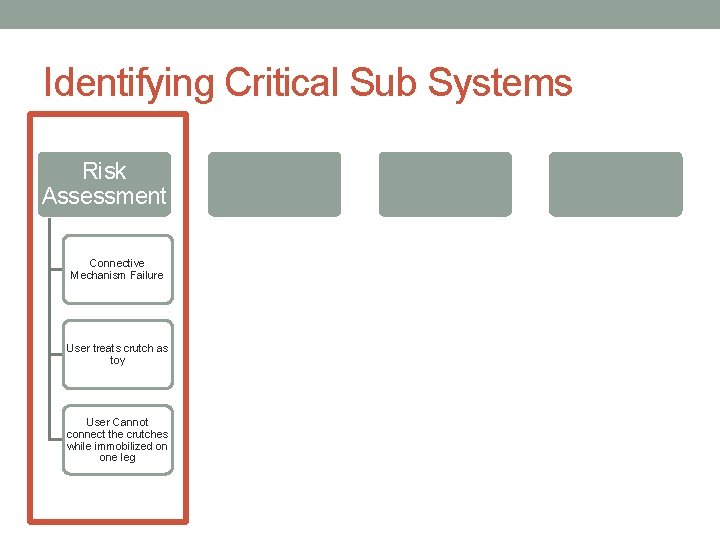
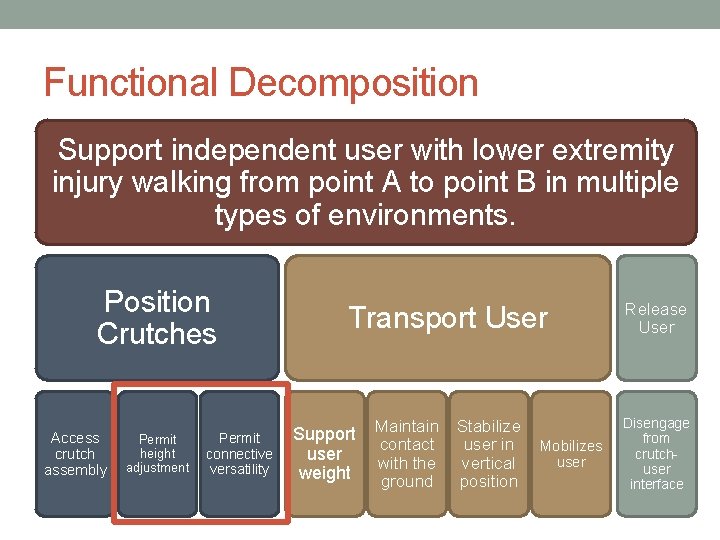
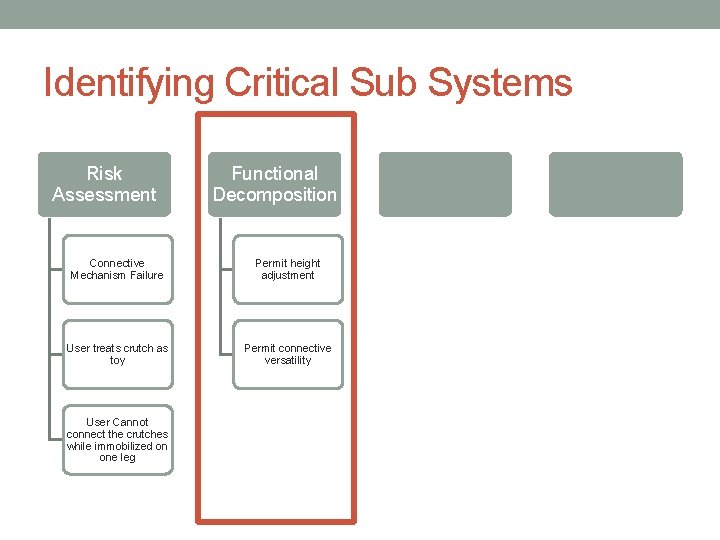
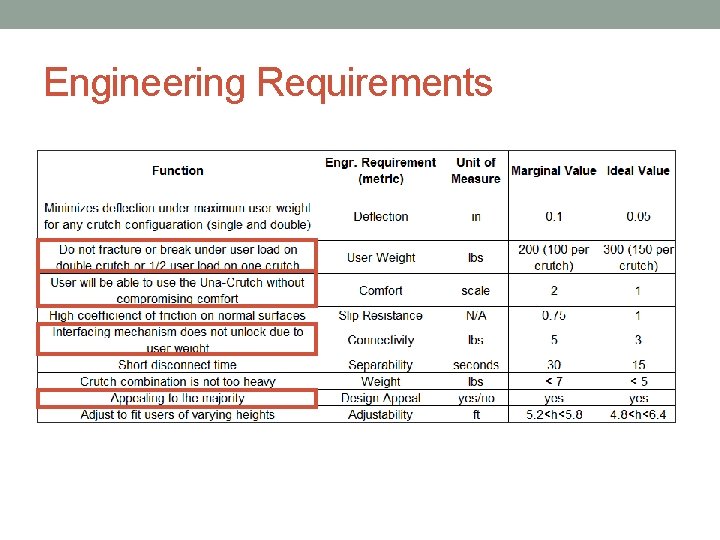
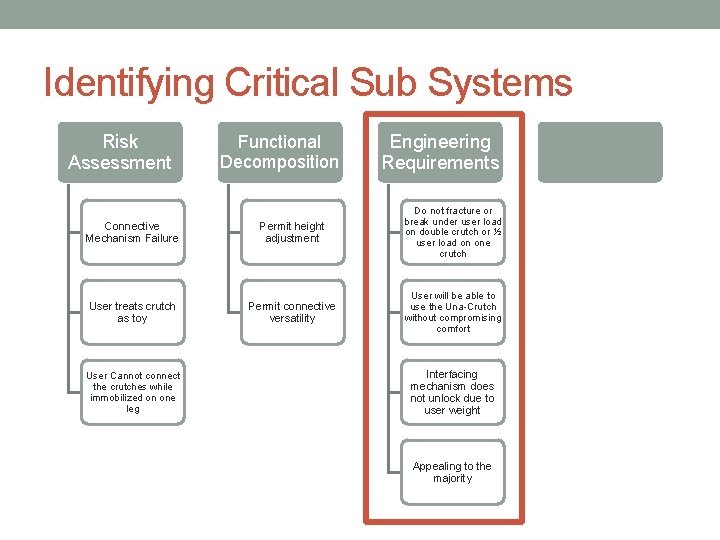
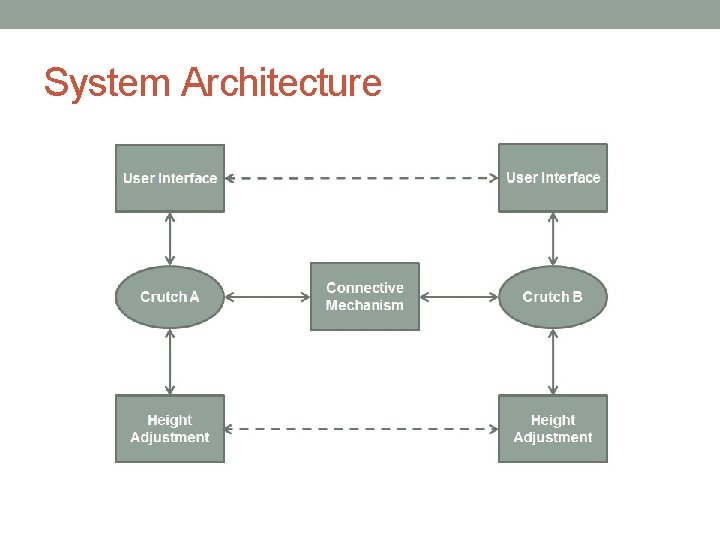
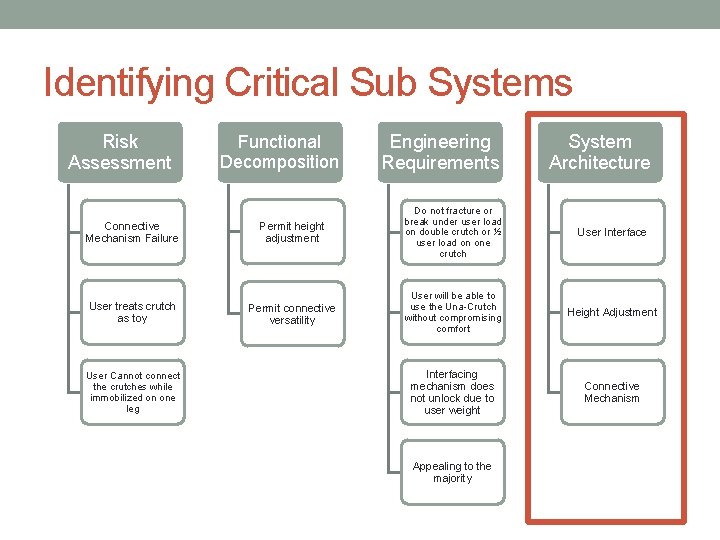
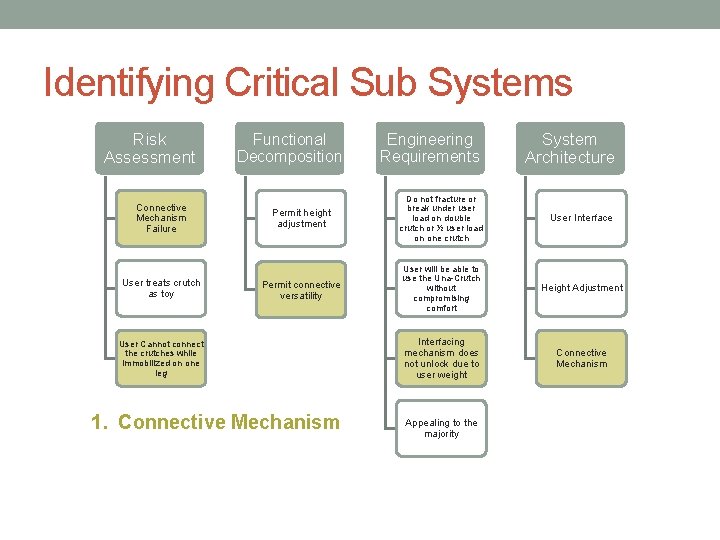
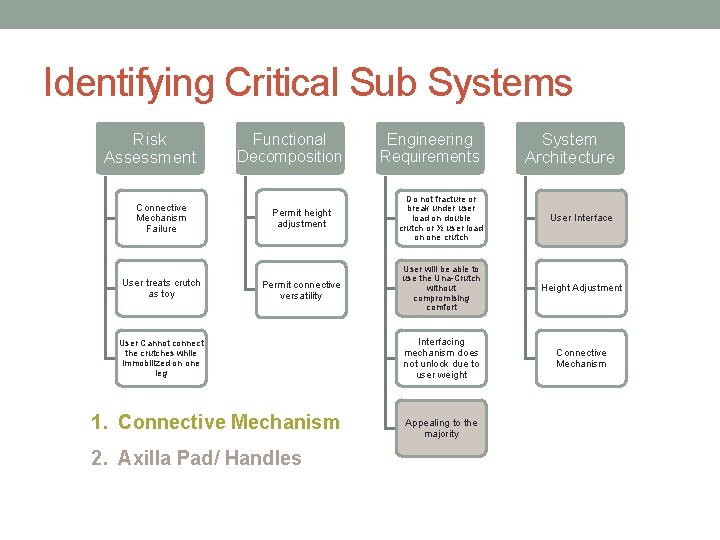
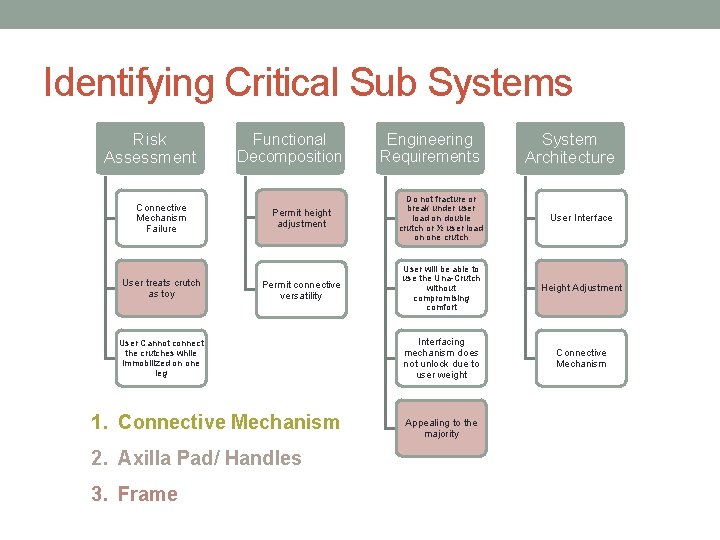
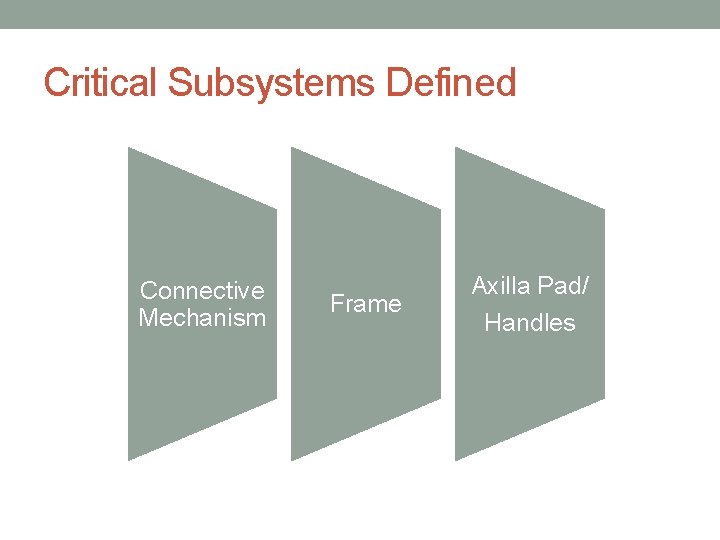
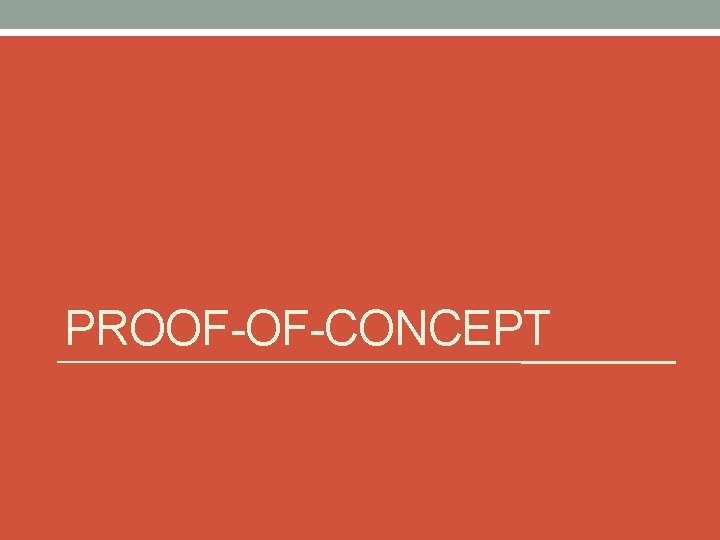
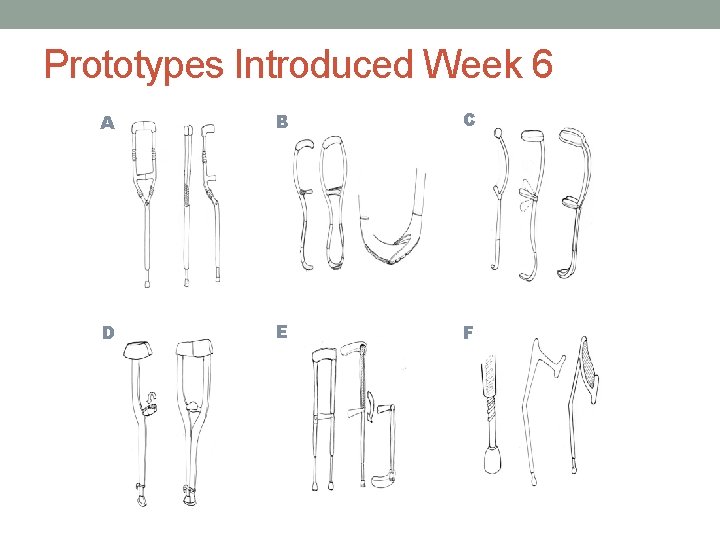
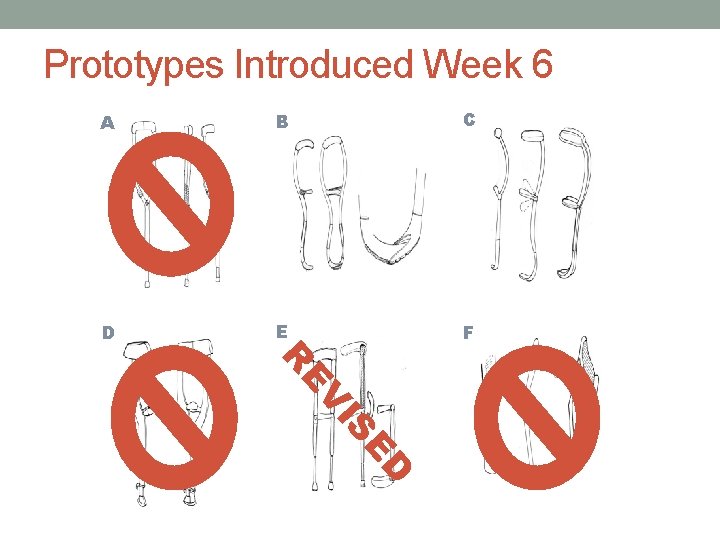
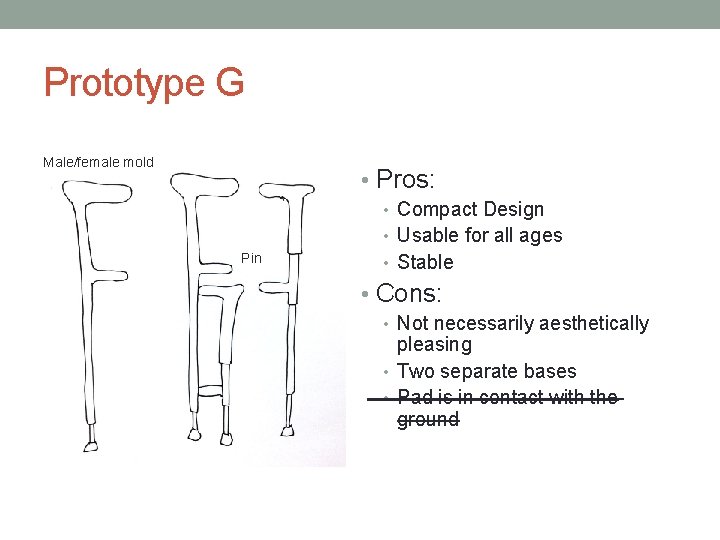
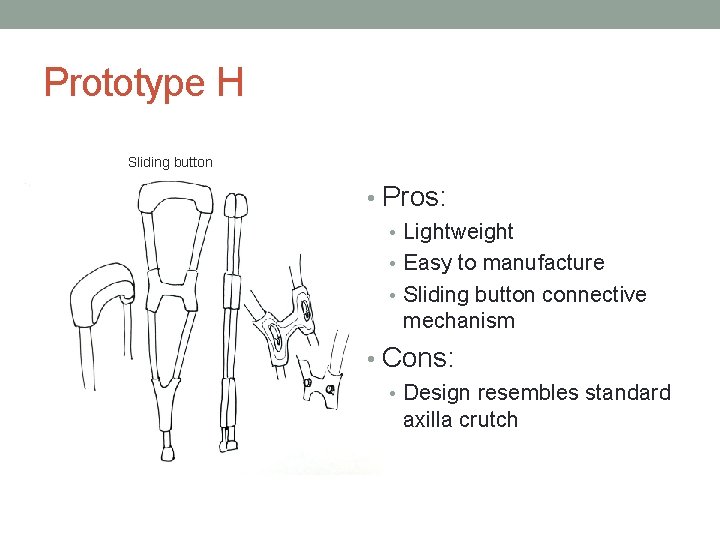
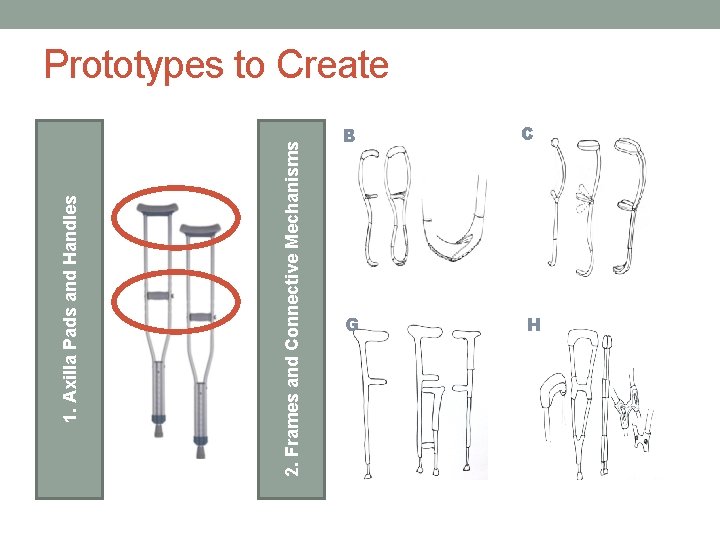
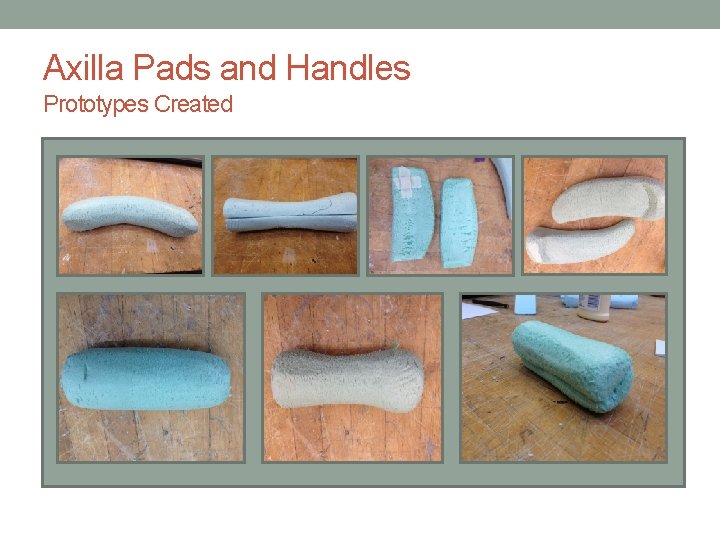
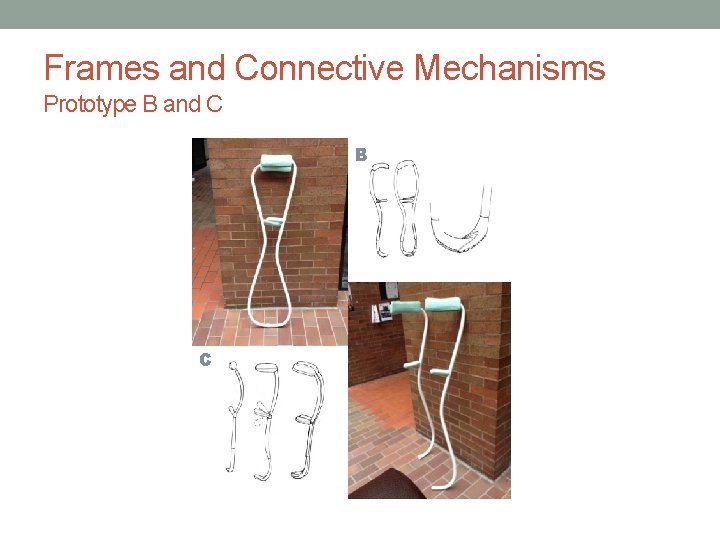
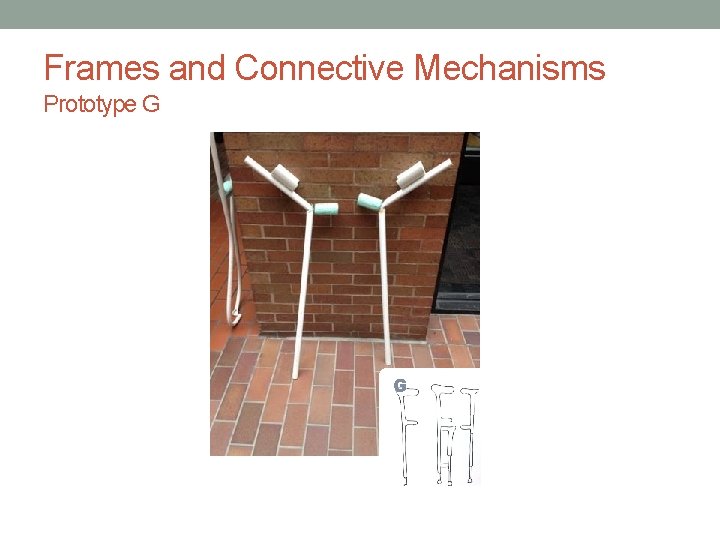
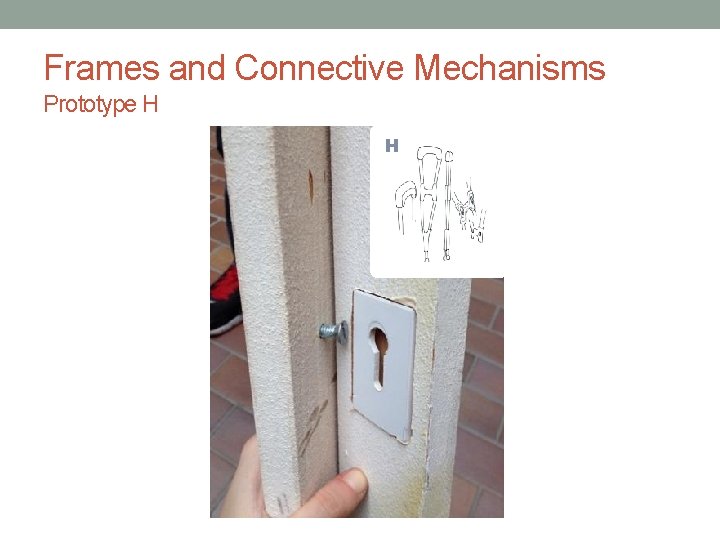
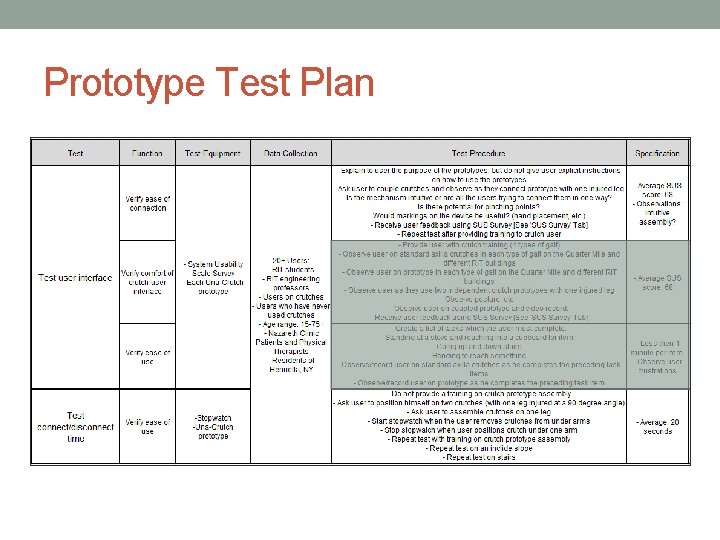
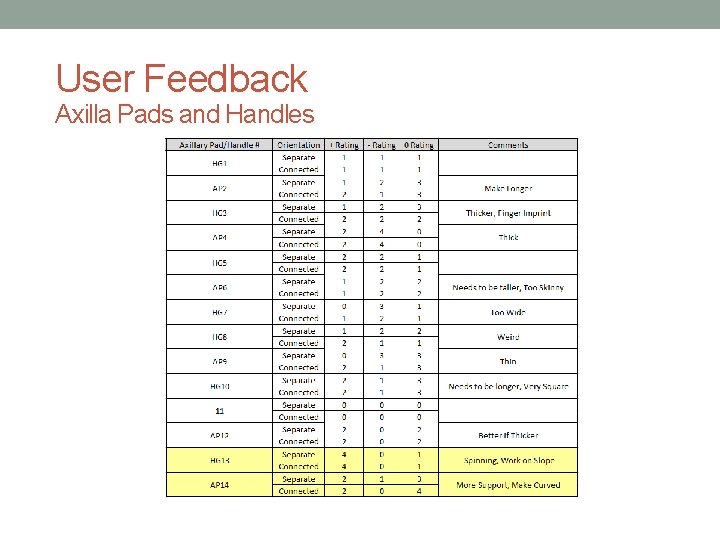
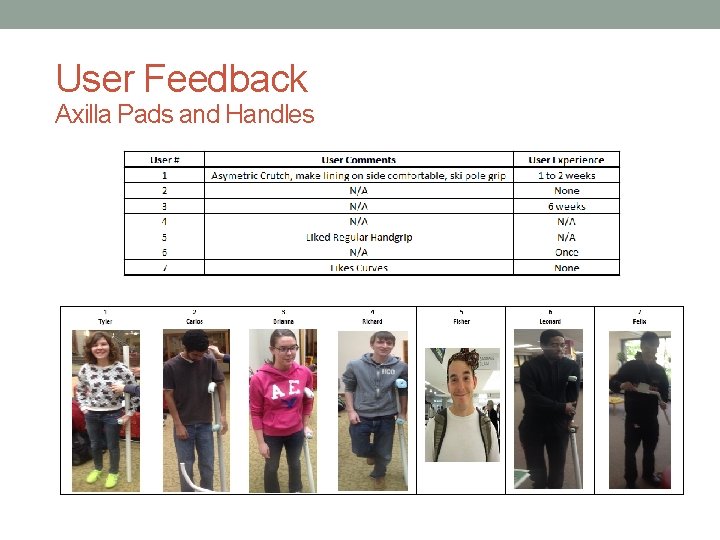
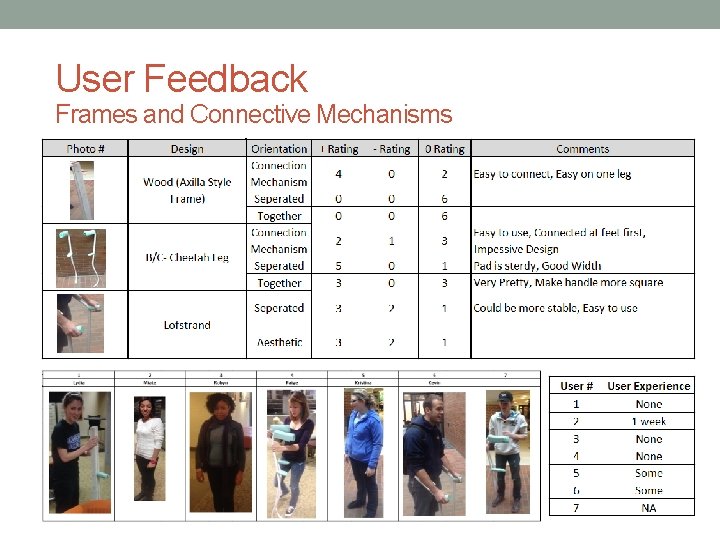
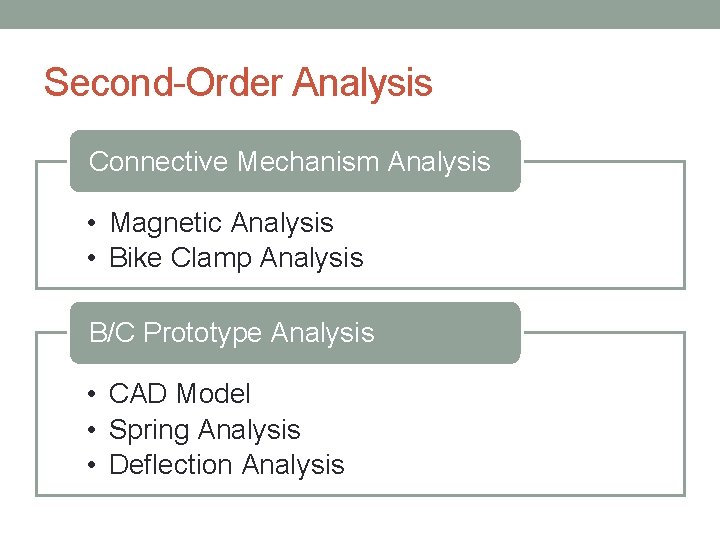
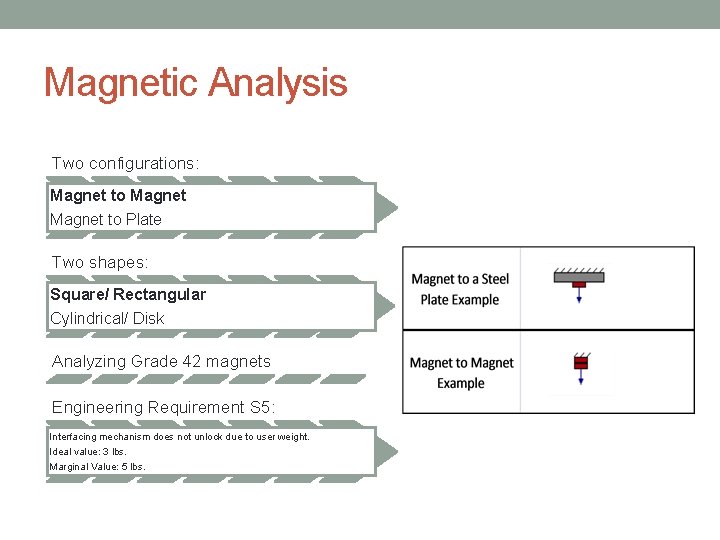
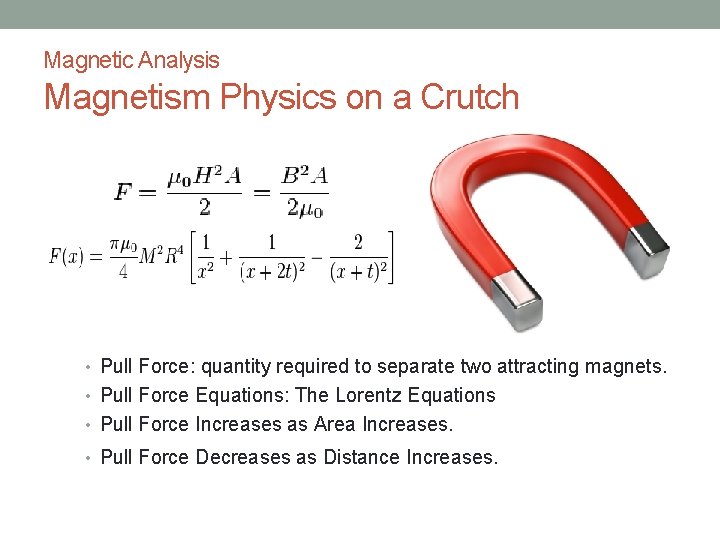
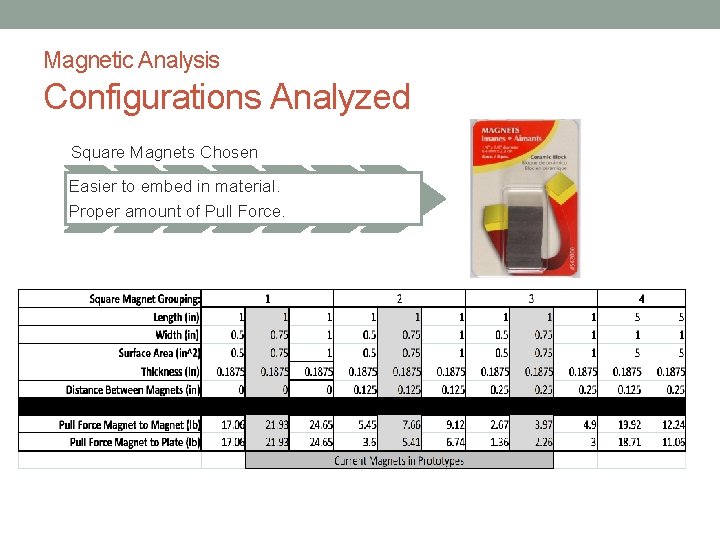
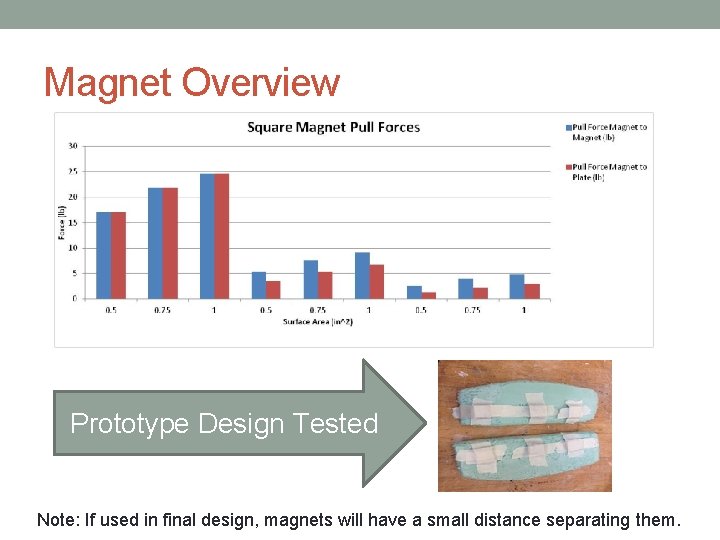
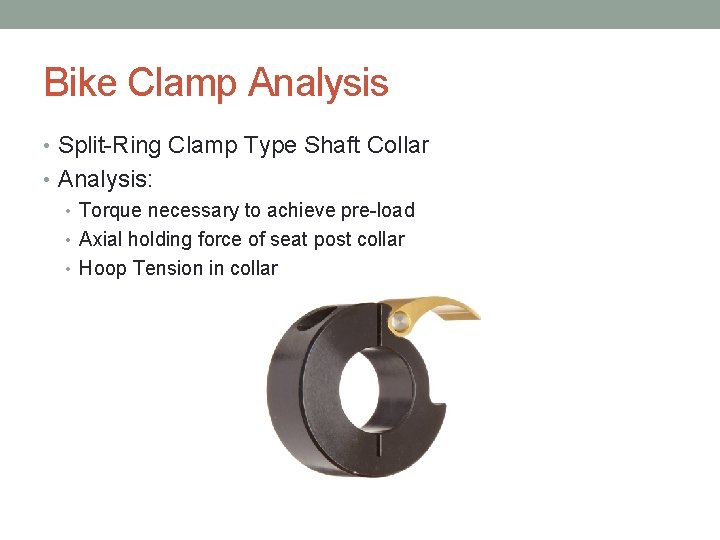
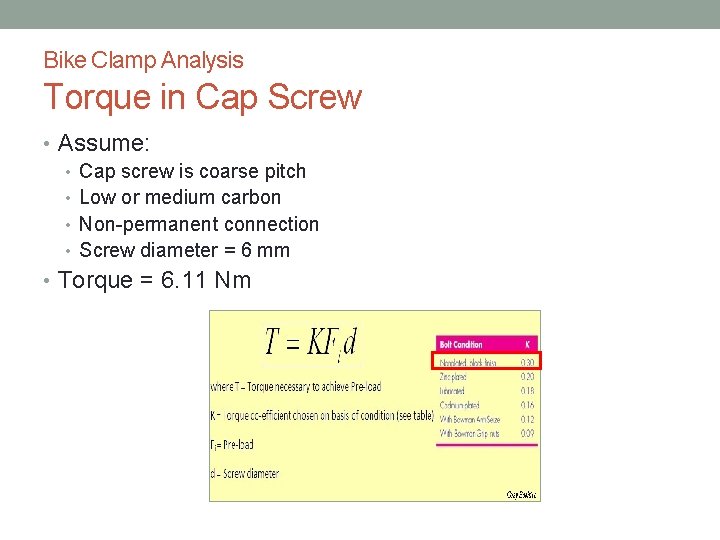
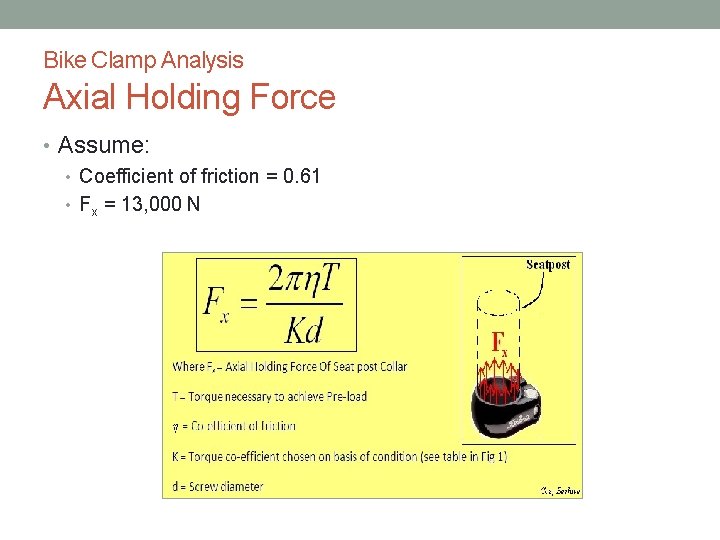
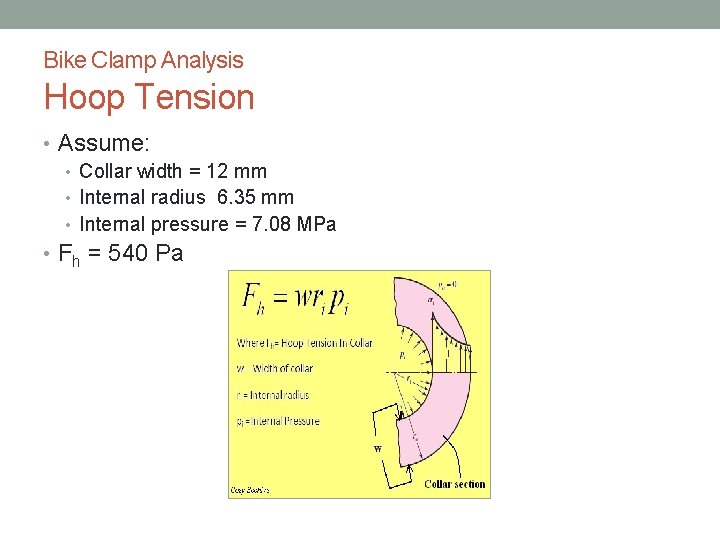
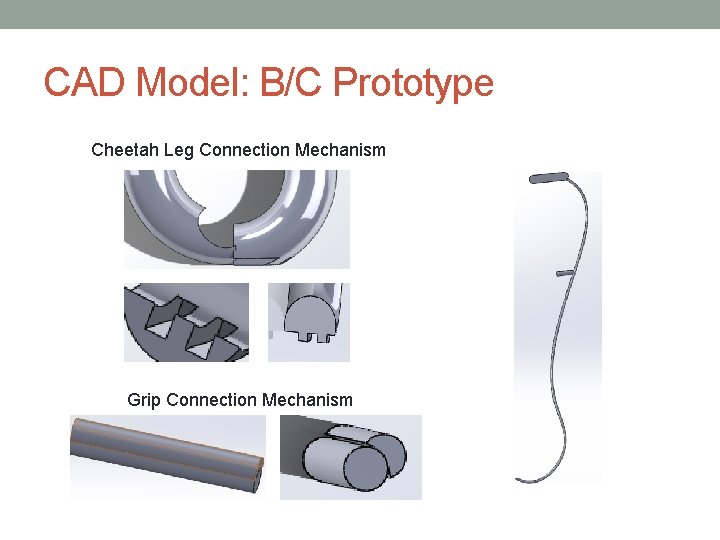
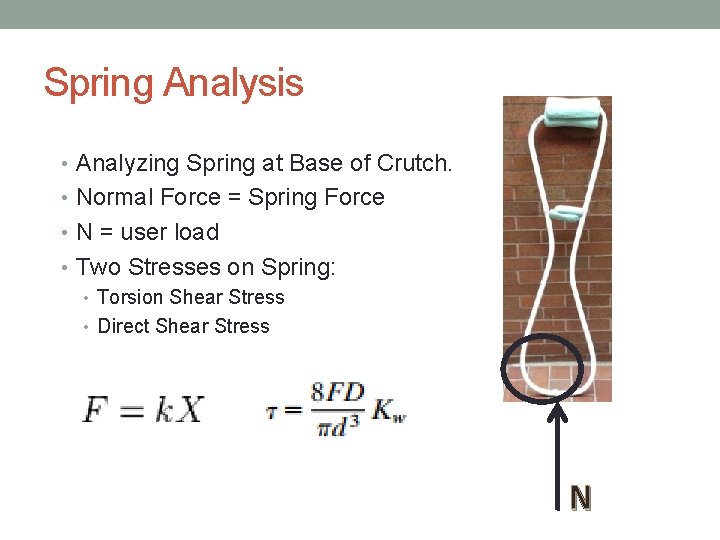
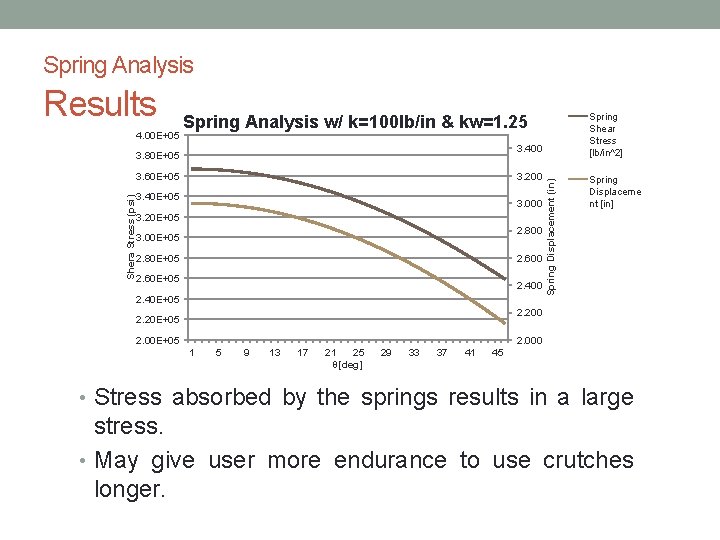

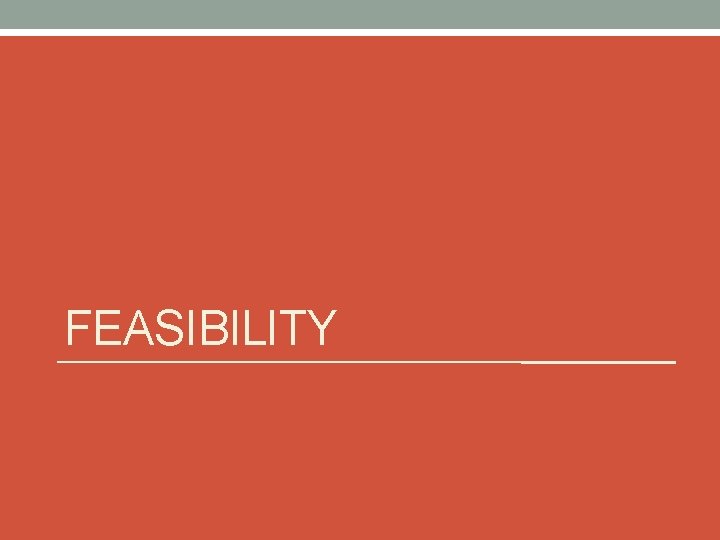
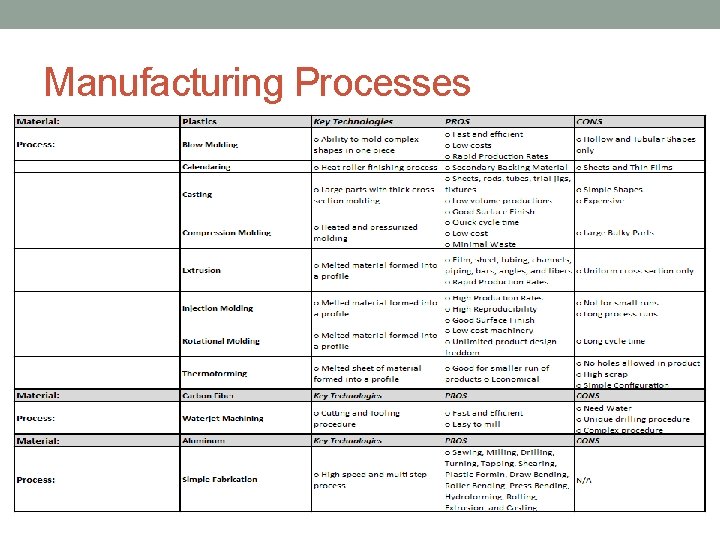
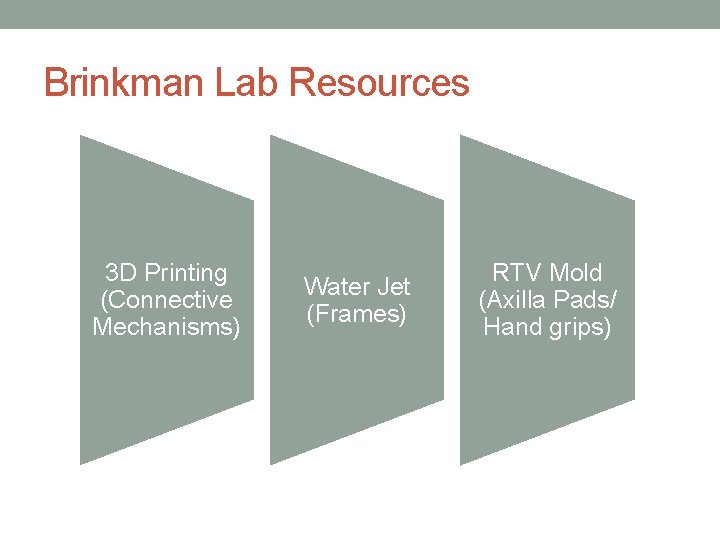
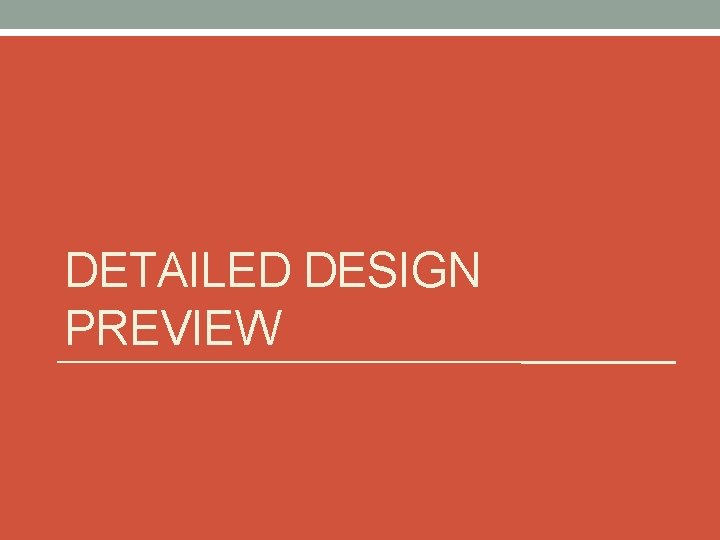
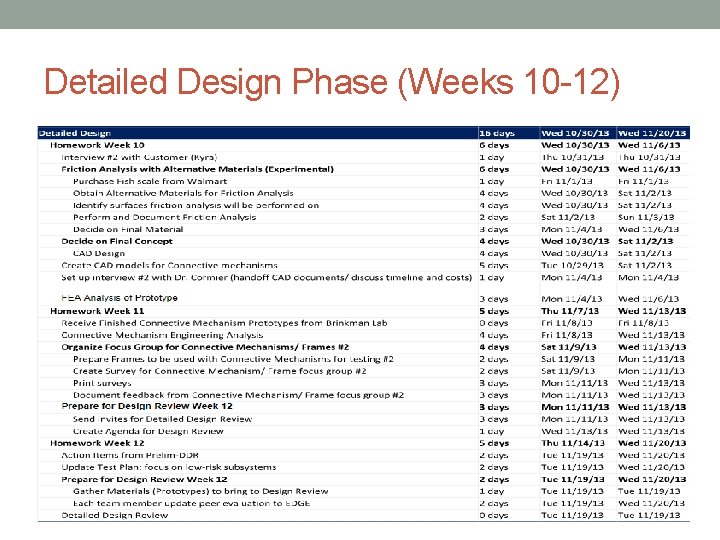
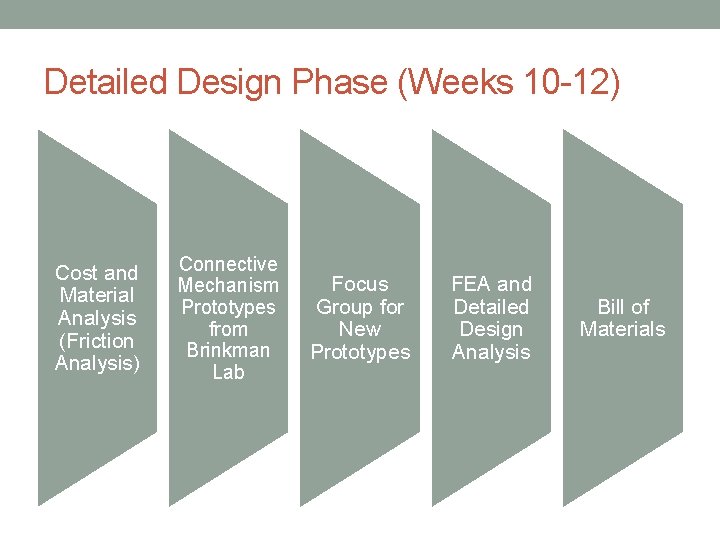
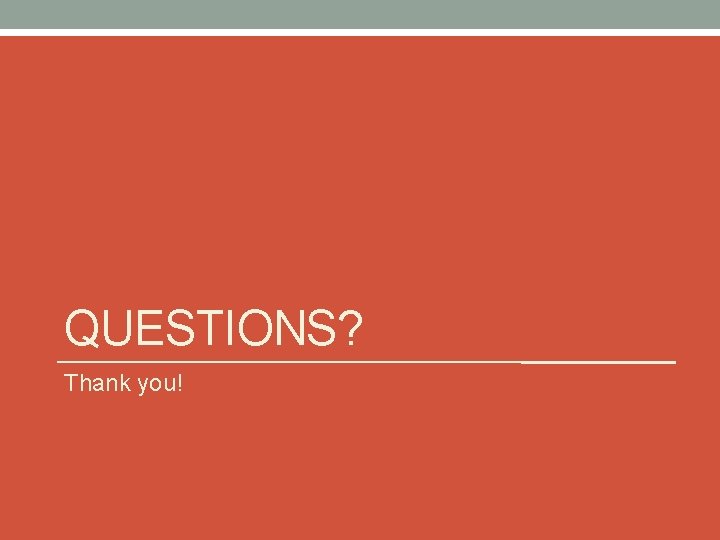
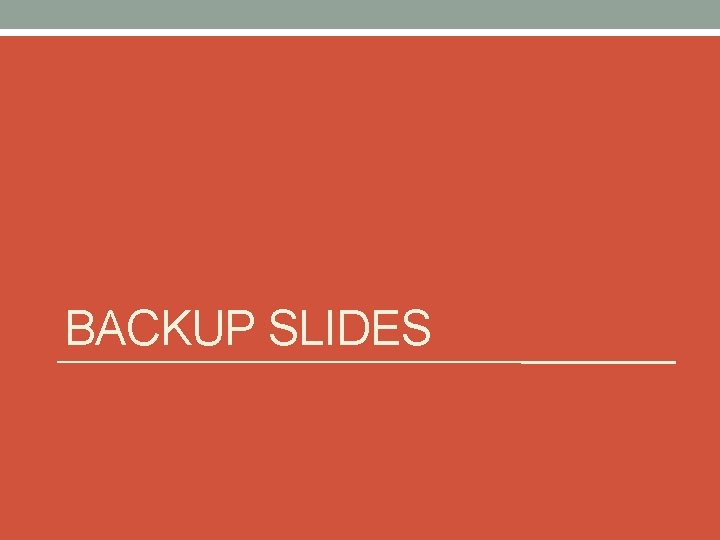
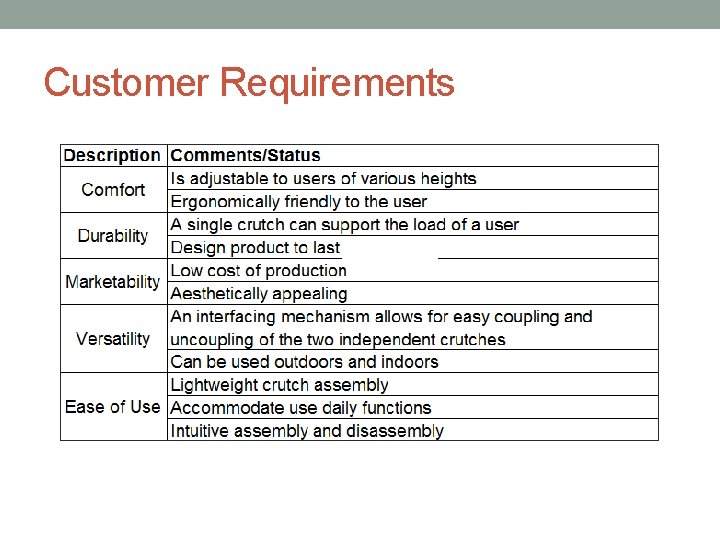
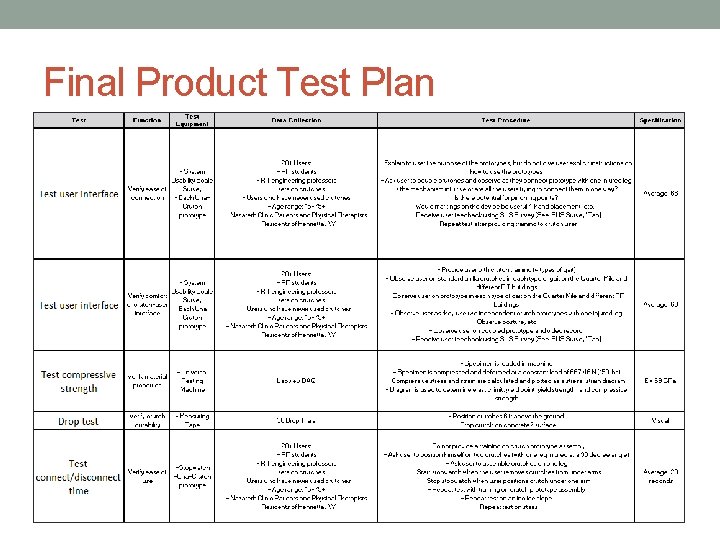
- Slides: 57
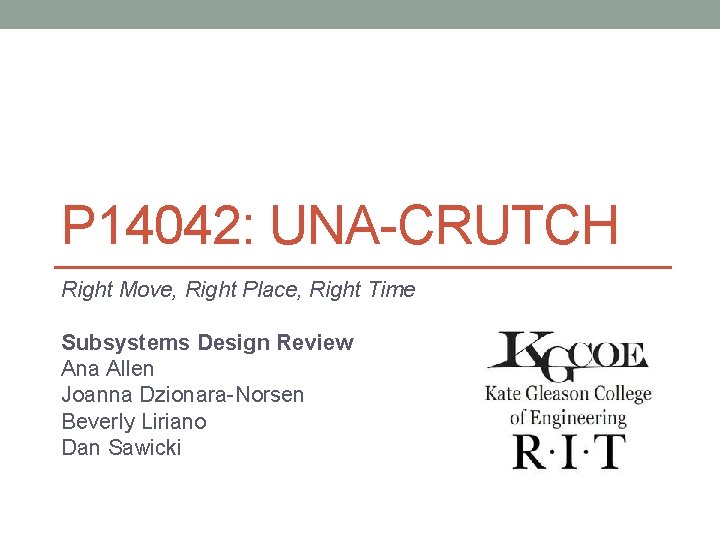
P 14042: UNA-CRUTCH Right Move, Right Place, Right Time Subsystems Design Review Ana Allen Joanna Dzionara-Norsen Beverly Liriano Dan Sawicki
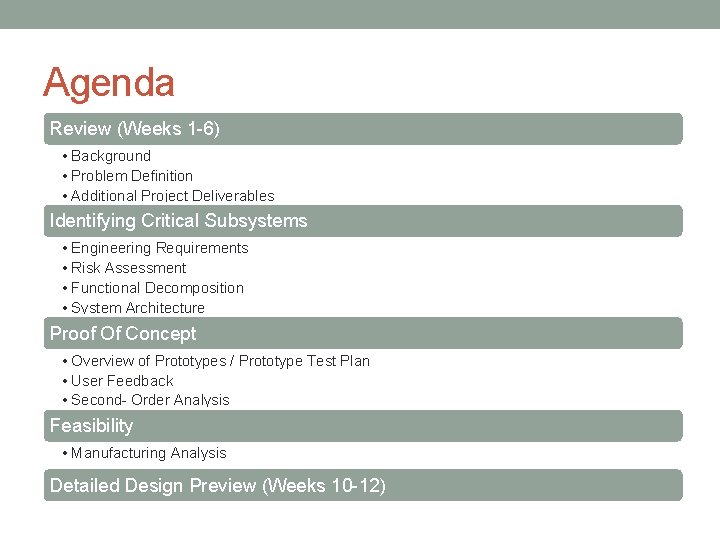
Agenda Review (Weeks 1 -6) • Background • Problem Definition • Additional Project Deliverables Identifying Critical Subsystems • Engineering Requirements • Risk Assessment • Functional Decomposition • System Architecture Proof Of Concept • Overview of Prototypes / Prototype Test Plan • User Feedback • Second- Order Analysis Feasibility • Manufacturing Analysis Detailed Design Preview (Weeks 10 -12)
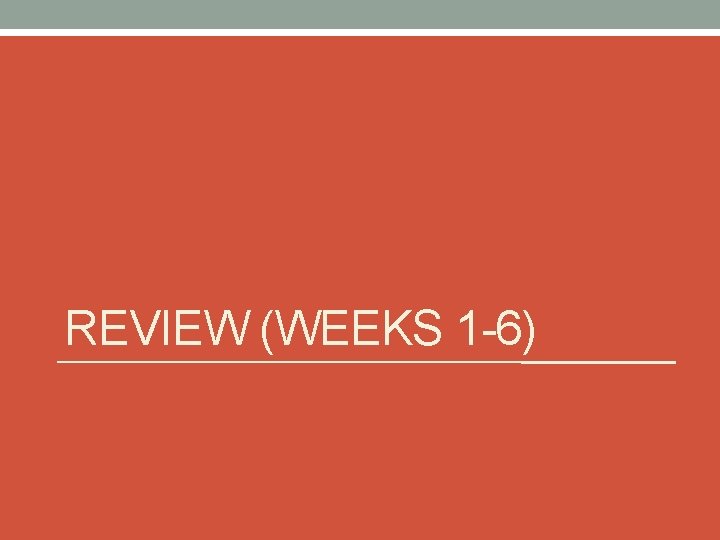
REVIEW (WEEKS 1 -6)
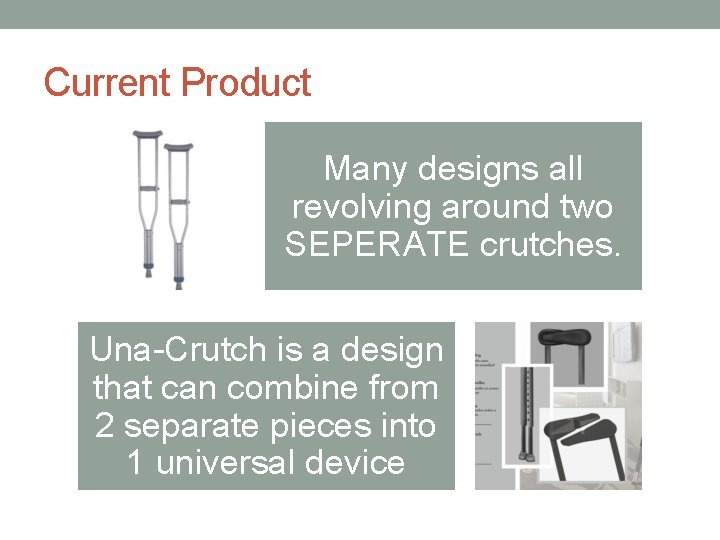
Current Product Many designs all revolving around two SEPERATE crutches. Una-Crutch is a design that can combine from 2 separate pieces into 1 universal device
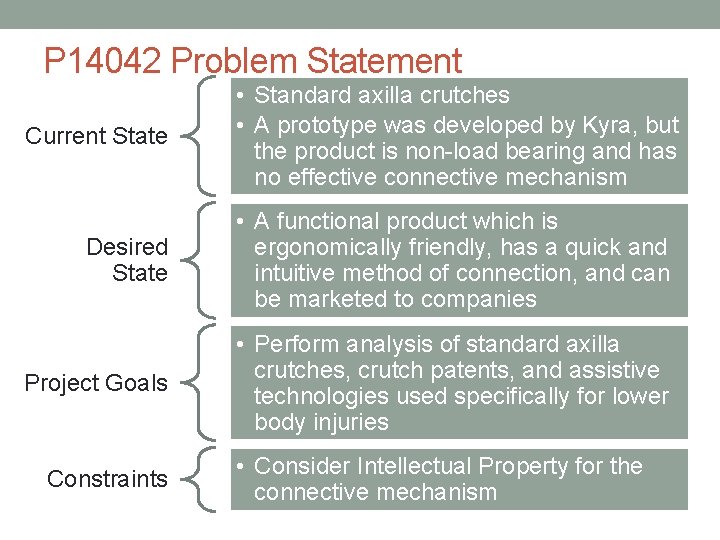
P 14042 Problem Statement Current State • Standard axilla crutches • A prototype was developed by Kyra, but the product is non-load bearing and has no effective connective mechanism Desired State • A functional product which is ergonomically friendly, has a quick and intuitive method of connection, and can be marketed to companies Project Goals • Perform analysis of standard axilla crutches, crutch patents, and assistive technologies used specifically for lower body injuries Constraints • Consider Intellectual Property for the connective mechanism
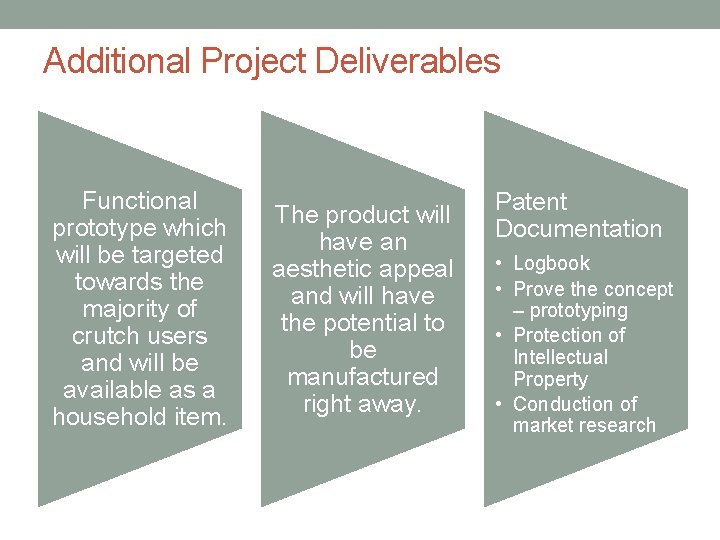
Additional Project Deliverables Functional prototype which will be targeted towards the majority of crutch users and will be available as a household item. The product will have an aesthetic appeal and will have the potential to be manufactured right away. Patent Documentation • Logbook • Prove the concept – prototyping • Protection of Intellectual Property • Conduction of market research
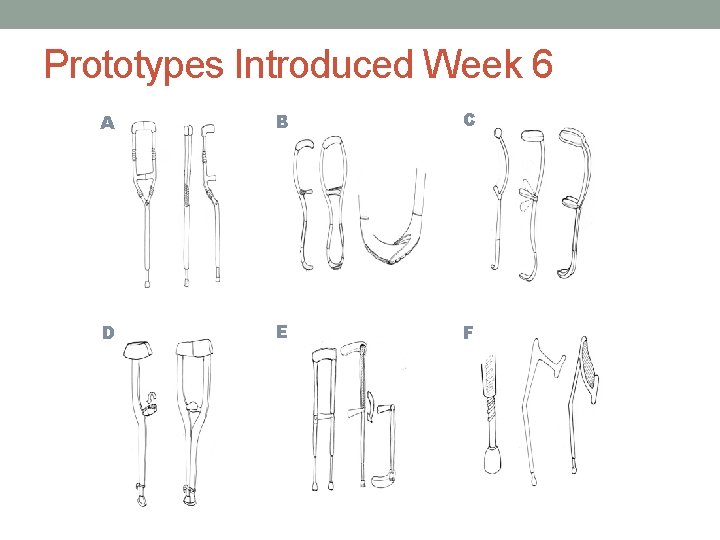
Prototypes Introduced Week 6 A B C D E F
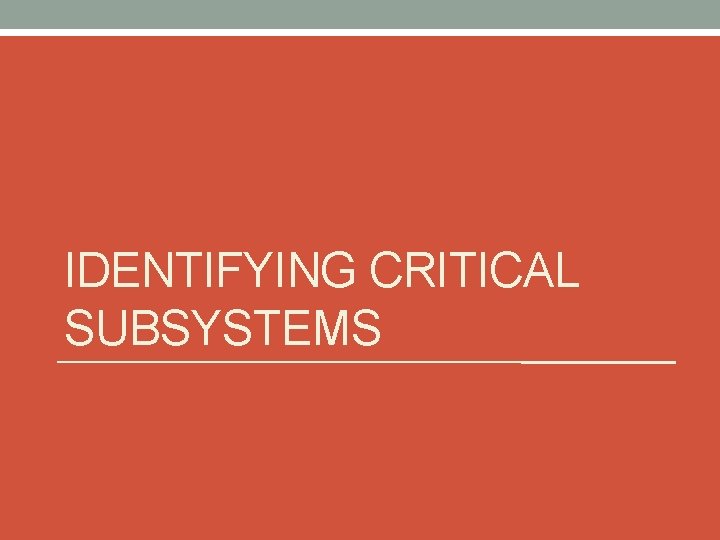
IDENTIFYING CRITICAL SUBSYSTEMS
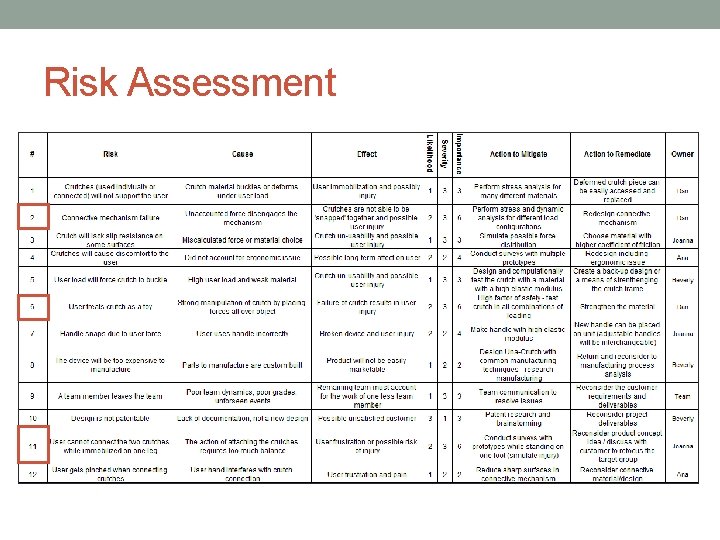
Risk Assessment
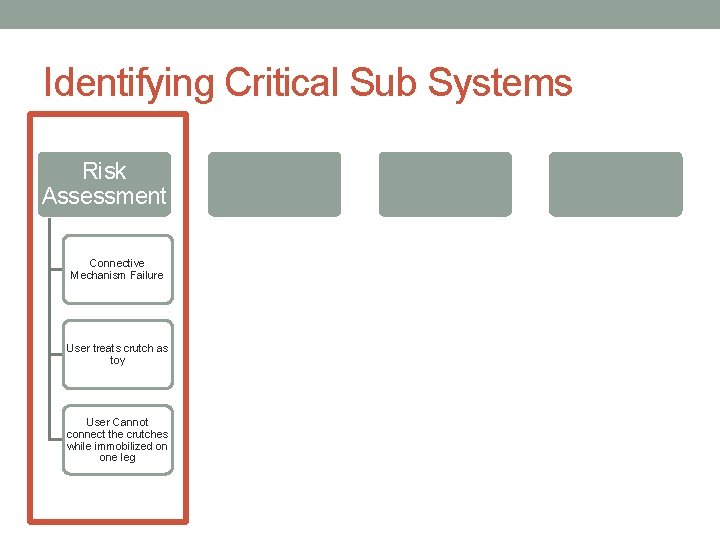
Identifying Critical Sub Systems Risk Assessment Connective Mechanism Failure User treats crutch as toy User Cannot connect the crutches while immobilized on one leg
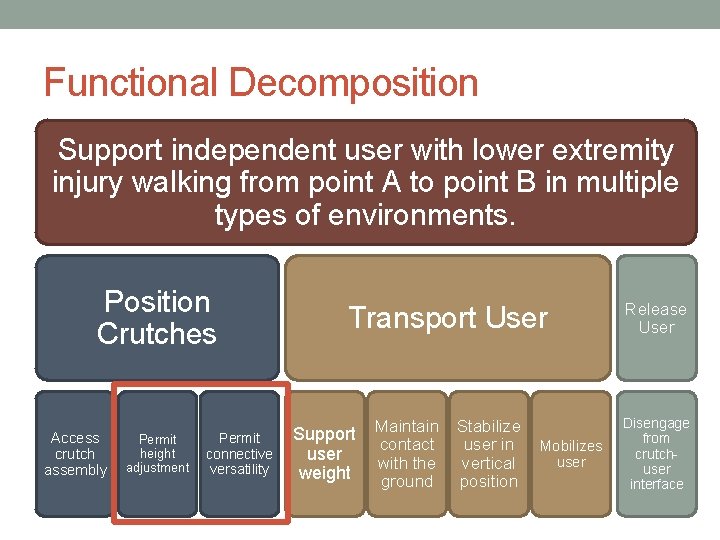
Functional Decomposition Support independent user with lower extremity injury walking from point A to point B in multiple types of environments. Position Crutches Access crutch assembly Permit height adjustment Permit connective versatility Transport User Support user weight Maintain contact with the ground Stabilize user in vertical position Mobilizes user Release User Disengage from crutchuser interface
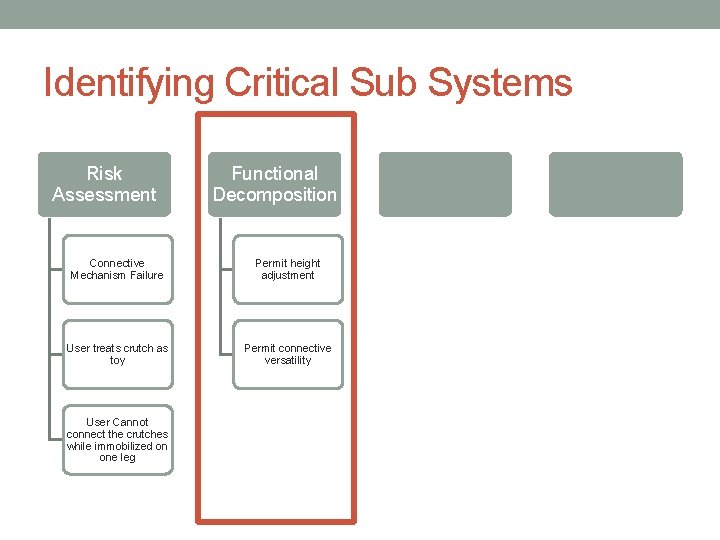
Identifying Critical Sub Systems Risk Assessment Functional Decomposition Connective Mechanism Failure Permit height adjustment User treats crutch as toy Permit connective versatility User Cannot connect the crutches while immobilized on one leg
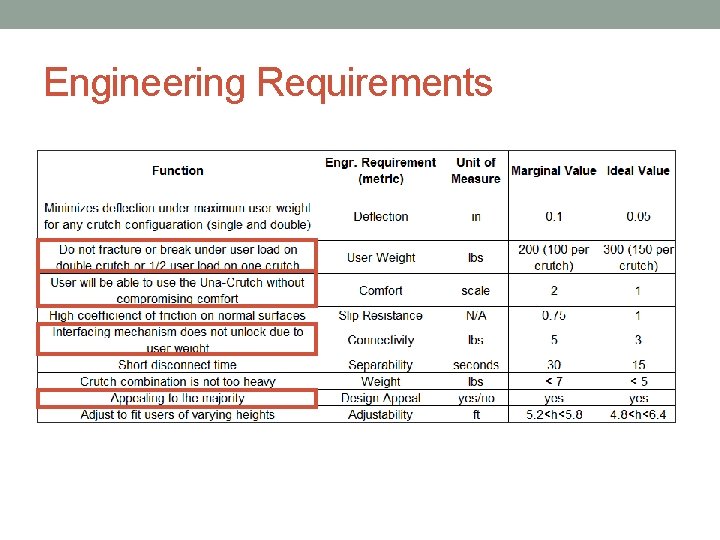
Engineering Requirements
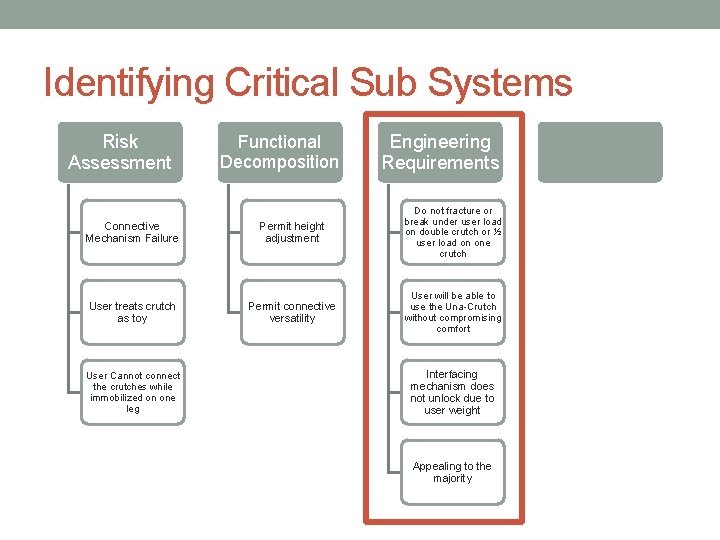
Identifying Critical Sub Systems Risk Assessment Functional Decomposition Engineering Requirements Connective Mechanism Failure Permit height adjustment Do not fracture or break under user load on double crutch or ½ user load on one crutch User treats crutch as toy Permit connective versatility User will be able to use the Una-Crutch without compromising comfort User Cannot connect the crutches while immobilized on one leg Interfacing mechanism does not unlock due to user weight Appealing to the majority
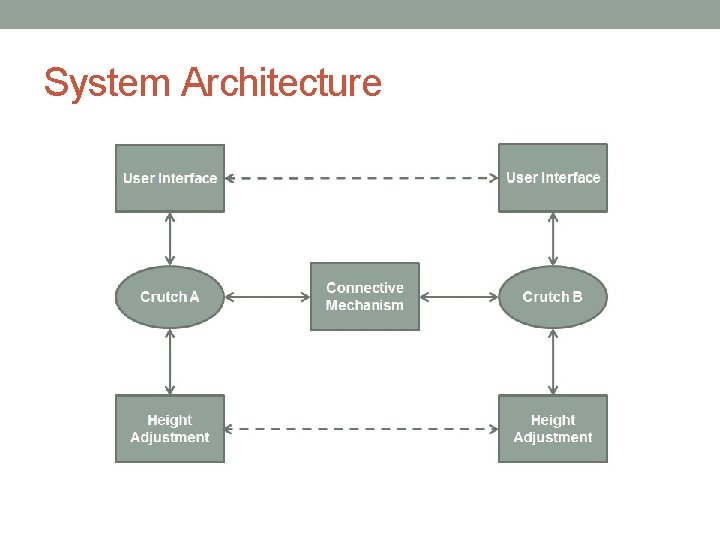
System Architecture
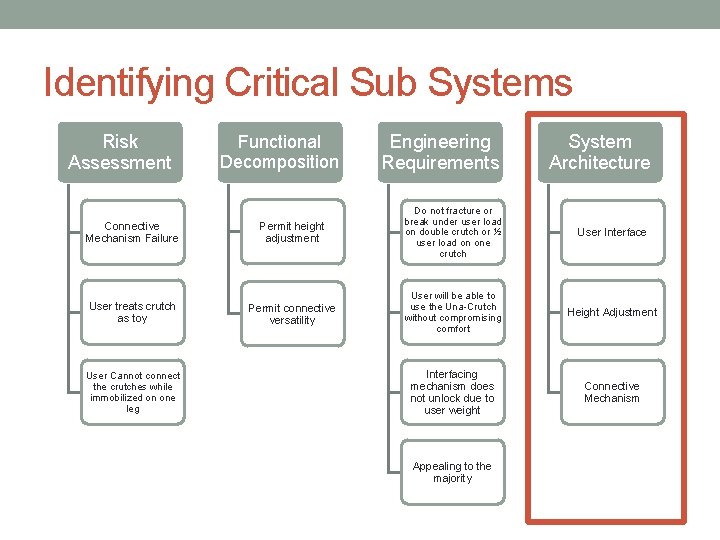
Identifying Critical Sub Systems Risk Assessment Functional Decomposition Engineering Requirements System Architecture Connective Mechanism Failure Permit height adjustment Do not fracture or break under user load on double crutch or ½ user load on one crutch User treats crutch as toy Permit connective versatility User will be able to use the Una-Crutch without compromising comfort Height Adjustment Interfacing mechanism does not unlock due to user weight Connective Mechanism User Cannot connect the crutches while immobilized on one leg Appealing to the majority User Interface
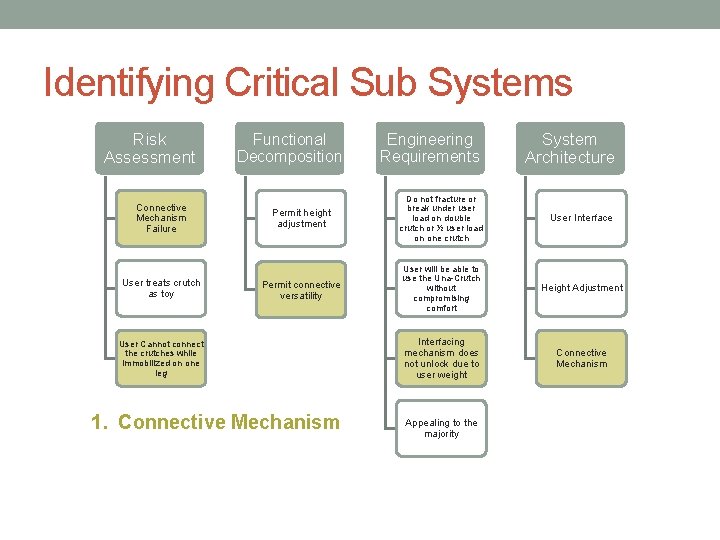
Identifying Critical Sub Systems Risk Assessment Connective Mechanism Failure User treats crutch as toy Functional Decomposition Engineering Requirements System Architecture Permit height adjustment Do not fracture or break under user load on double crutch or ½ user load on one crutch User Interface Permit connective versatility User will be able to use the Una-Crutch without compromising comfort Height Adjustment Interfacing mechanism does not unlock due to user weight Connective Mechanism User Cannot connect the crutches while immobilized on one leg 1. Connective Mechanism Appealing to the majority
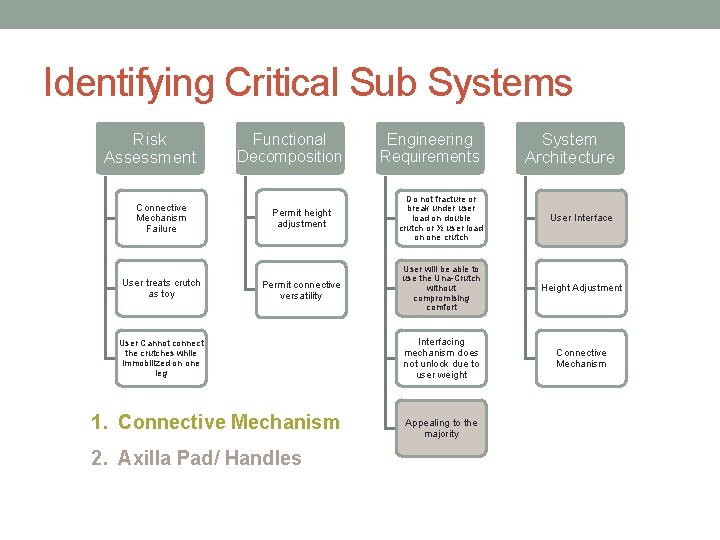
Identifying Critical Sub Systems Risk Assessment Connective Mechanism Failure User treats crutch as toy Functional Decomposition Engineering Requirements System Architecture Permit height adjustment Do not fracture or break under user load on double crutch or ½ user load on one crutch User Interface Permit connective versatility User will be able to use the Una-Crutch without compromising comfort Height Adjustment Interfacing mechanism does not unlock due to user weight Connective Mechanism User Cannot connect the crutches while immobilized on one leg 1. Connective Mechanism 2. Axilla Pad/ Handles Appealing to the majority
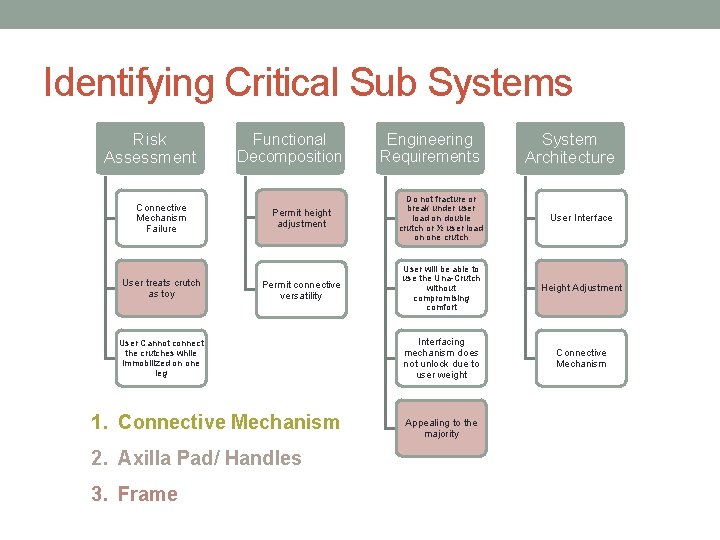
Identifying Critical Sub Systems Risk Assessment Connective Mechanism Failure User treats crutch as toy Functional Decomposition System Architecture Permit height adjustment Do not fracture or break under user load on double crutch or ½ user load on one crutch User Interface Permit connective versatility User will be able to use the Una-Crutch without compromising comfort Height Adjustment Interfacing mechanism does not unlock due to user weight Connective Mechanism User Cannot connect the crutches while immobilized on one leg 1. Connective Mechanism 2. Axilla Pad/ Handles 3. Frame Engineering Requirements Appealing to the majority
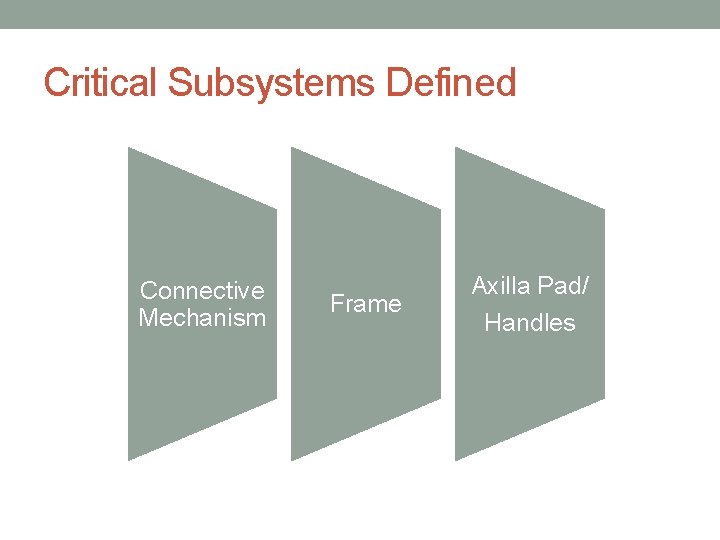
Critical Subsystems Defined Connective Mechanism Frame Axilla Pad/ Handles
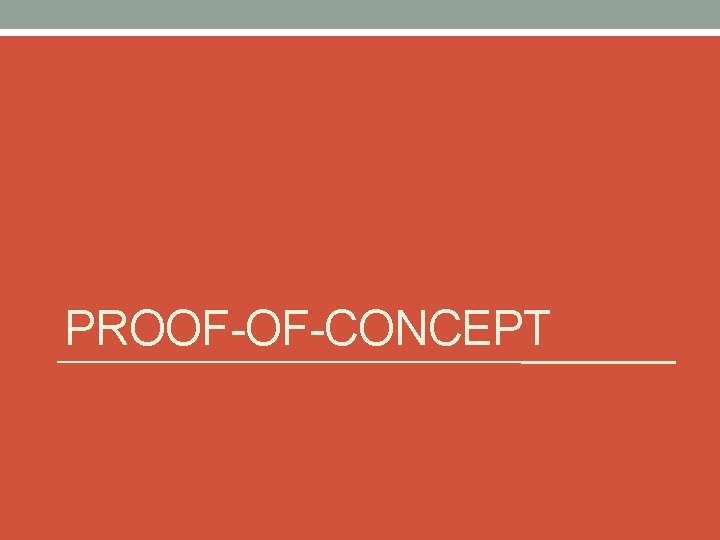
PROOF-OF-CONCEPT
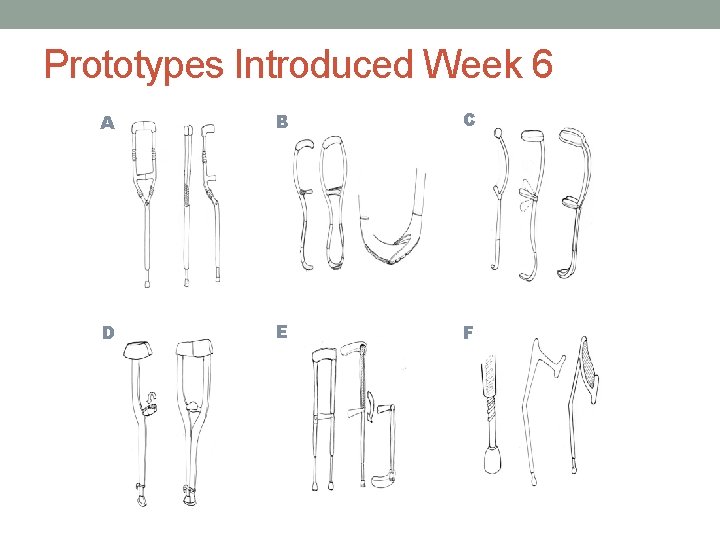
Prototypes Introduced Week 6 A B C D E F
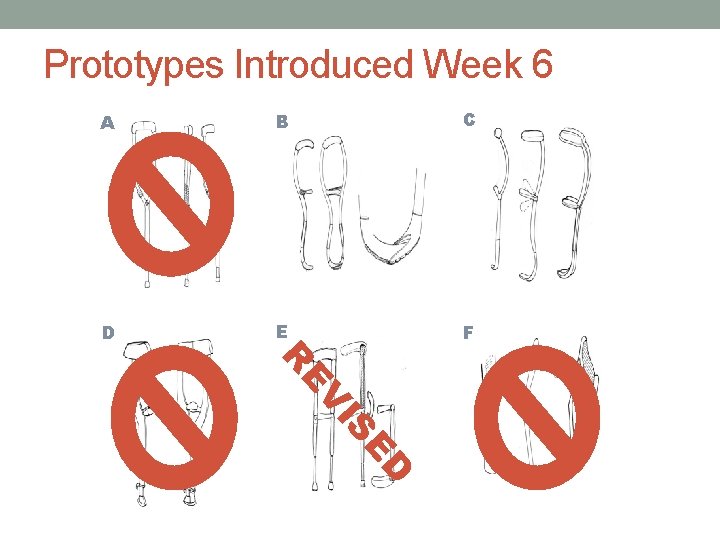
Prototypes Introduced Week 6 A B C D E F ED IS EV R
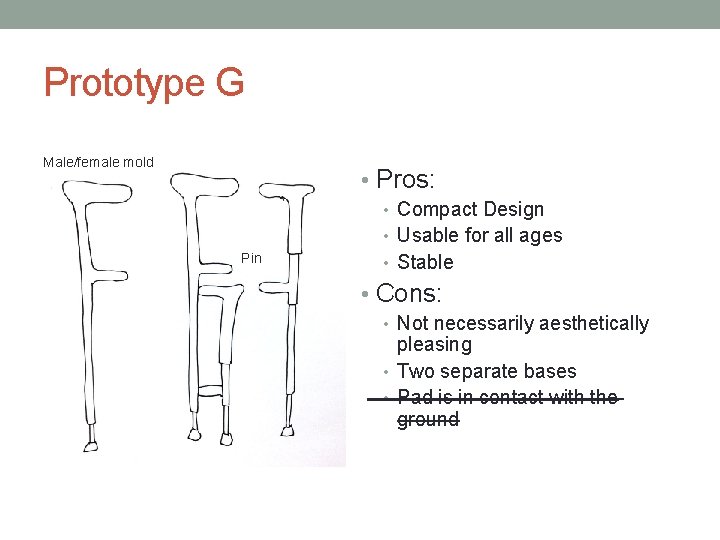
Prototype G Male/female mold • Pros: • Compact Design • Usable for all ages Pin • Stable • Cons: • Not necessarily aesthetically pleasing • Two separate bases • Pad is in contact with the ground
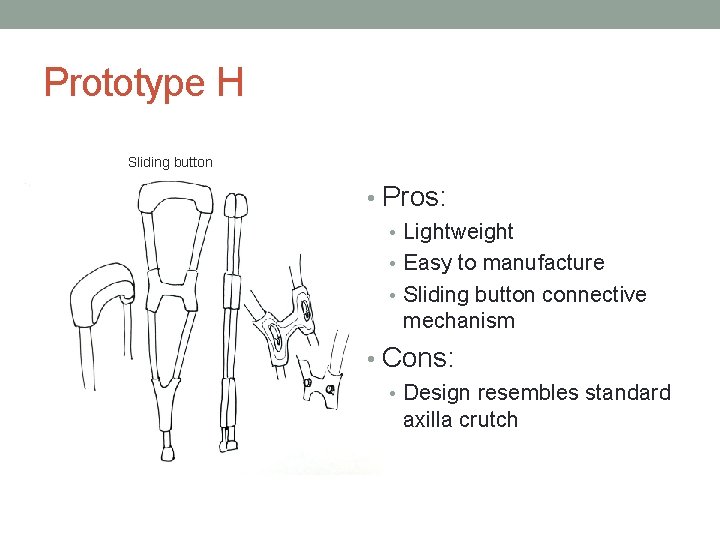
Prototype H Sliding button • Pros: • Lightweight • Easy to manufacture • Sliding button connective mechanism • Cons: • Design resembles standard axilla crutch
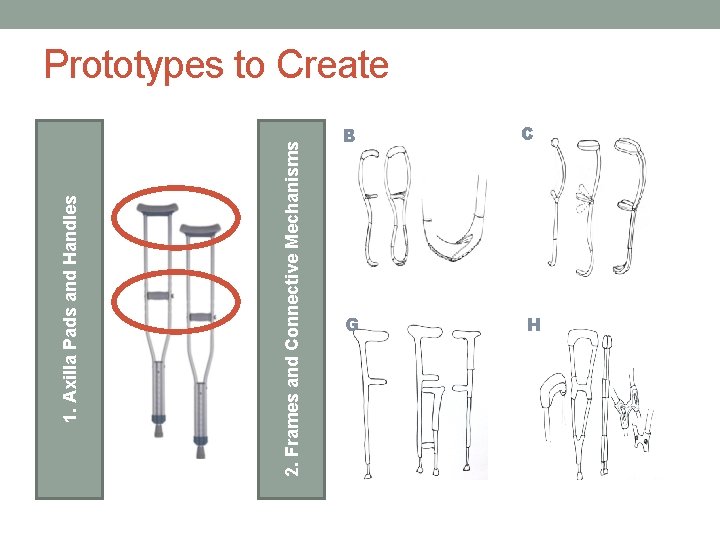
2. Frames and Connective Mechanisms 1. Axilla Pads and Handles Prototypes to Create B G C H
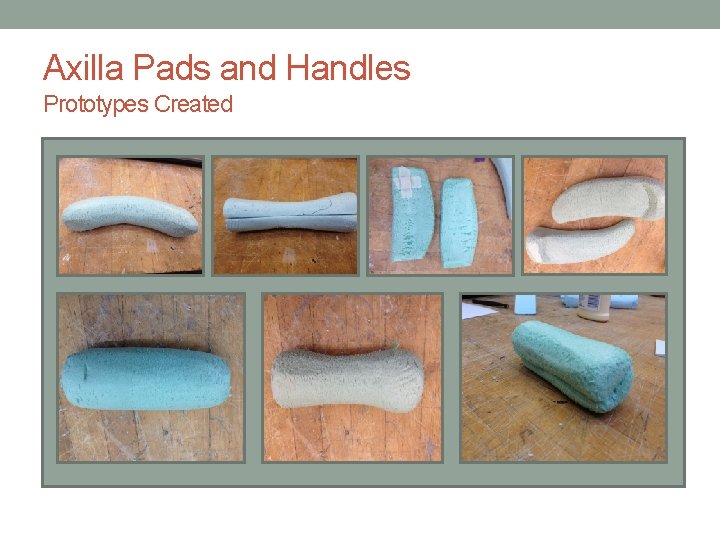
Axilla Pads and Handles Prototypes Created
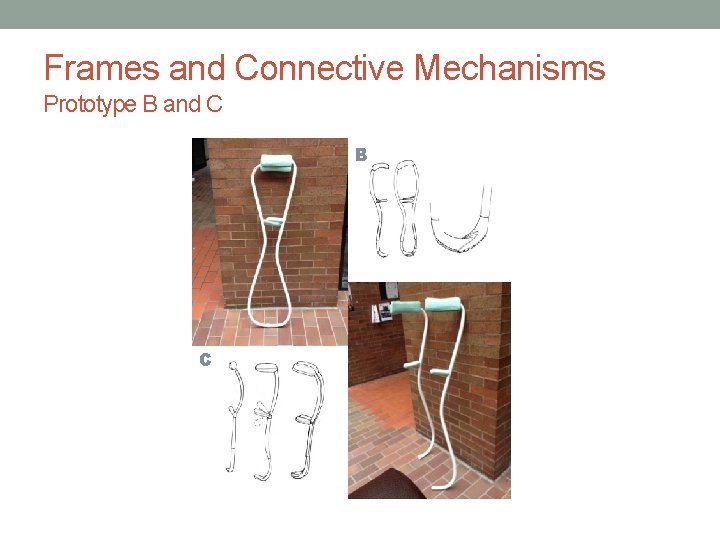
Frames and Connective Mechanisms Prototype B and C B C
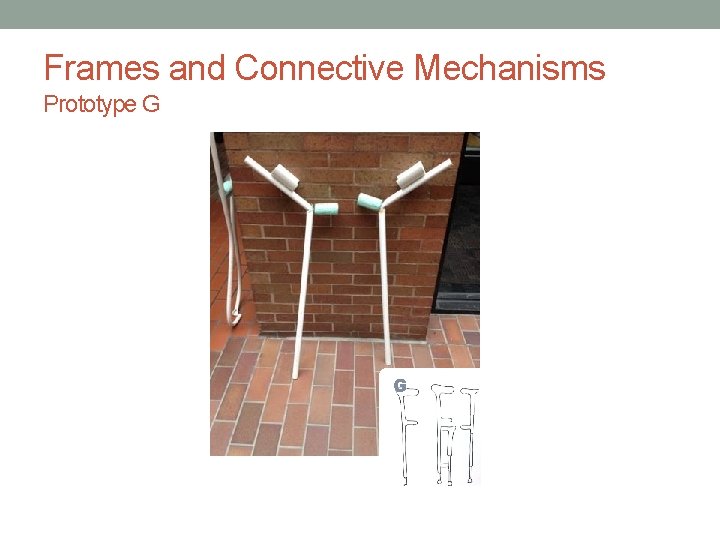
Frames and Connective Mechanisms Prototype G G
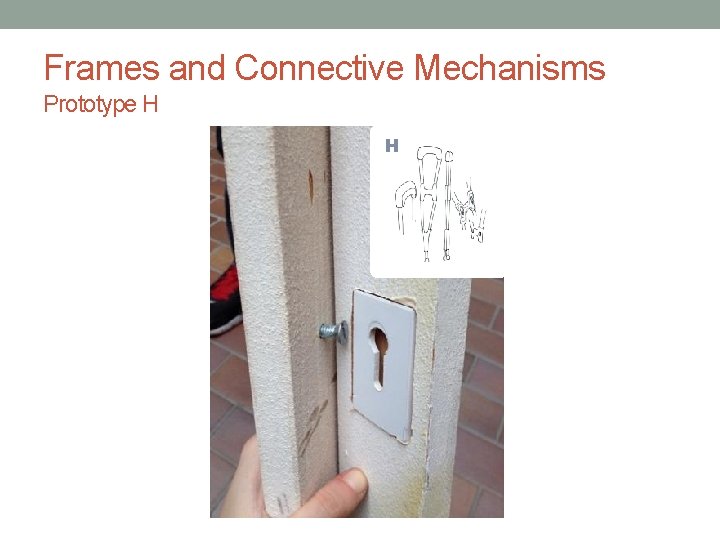
Frames and Connective Mechanisms Prototype H H
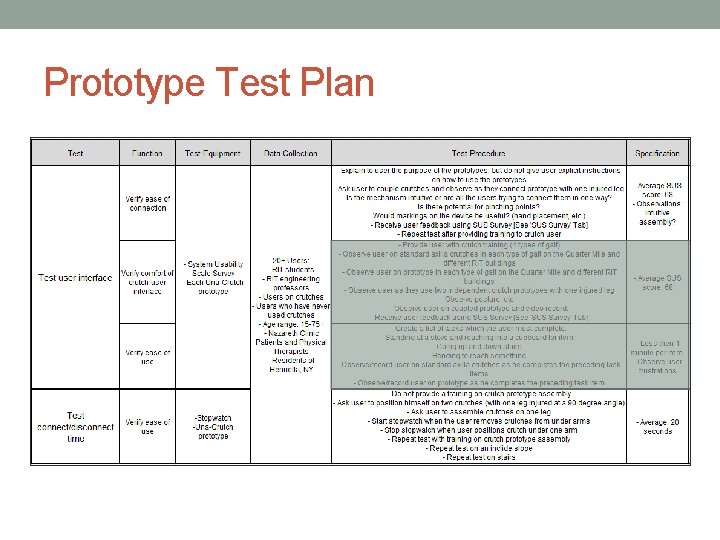
Prototype Test Plan
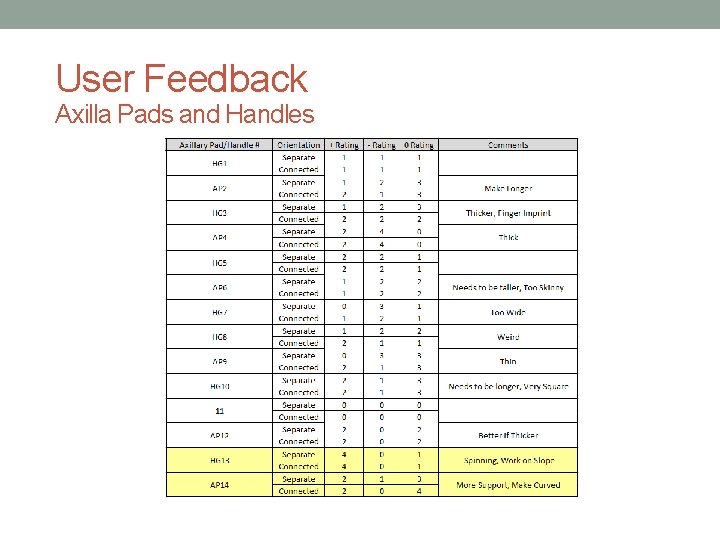
User Feedback Axilla Pads and Handles
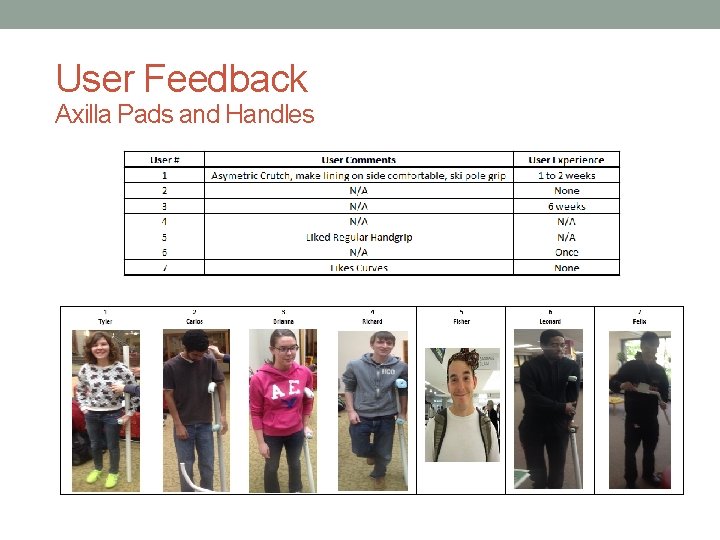
User Feedback Axilla Pads and Handles
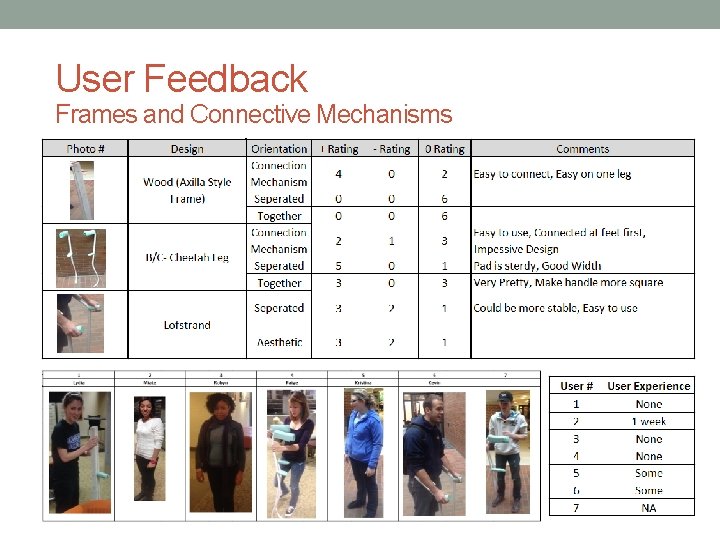
User Feedback Frames and Connective Mechanisms
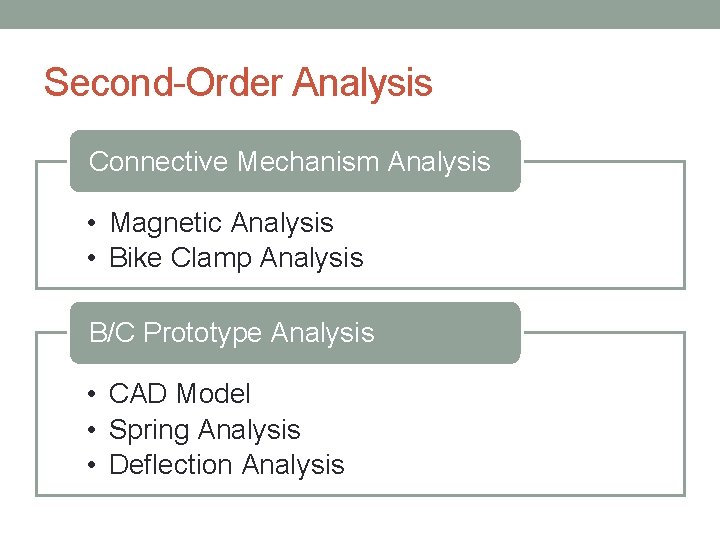
Second-Order Analysis Connective Mechanism Analysis • Magnetic Analysis • Bike Clamp Analysis B/C Prototype Analysis • CAD Model • Spring Analysis • Deflection Analysis
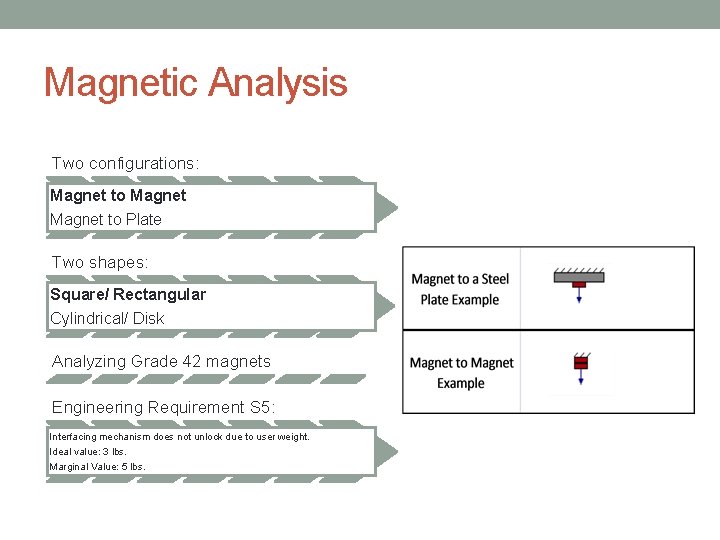
Magnetic Analysis Two configurations: Magnet to Plate Two shapes: Square/ Rectangular Cylindrical/ Disk Analyzing Grade 42 magnets Engineering Requirement S 5: Interfacing mechanism does not unlock due to user weight. Ideal value: 3 lbs. Marginal Value: 5 lbs.
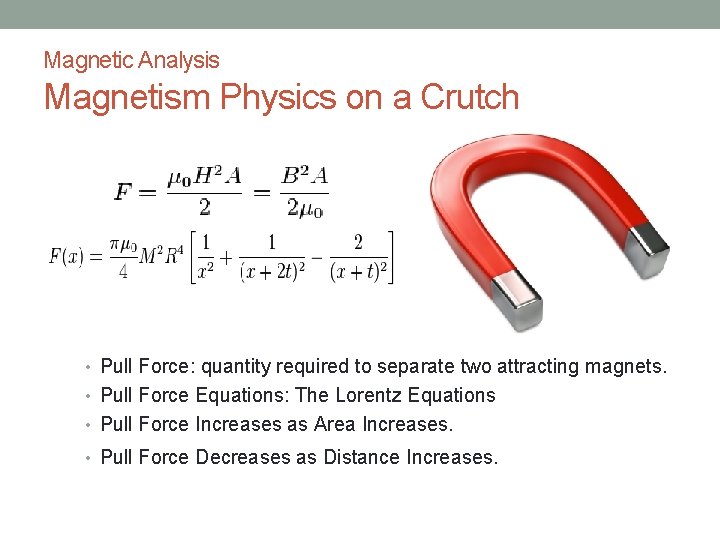
Magnetic Analysis Magnetism Physics on a Crutch • Pull Force: quantity required to separate two attracting magnets. • Pull Force Equations: The Lorentz Equations • Pull Force Increases as Area Increases. • Pull Force Decreases as Distance Increases.
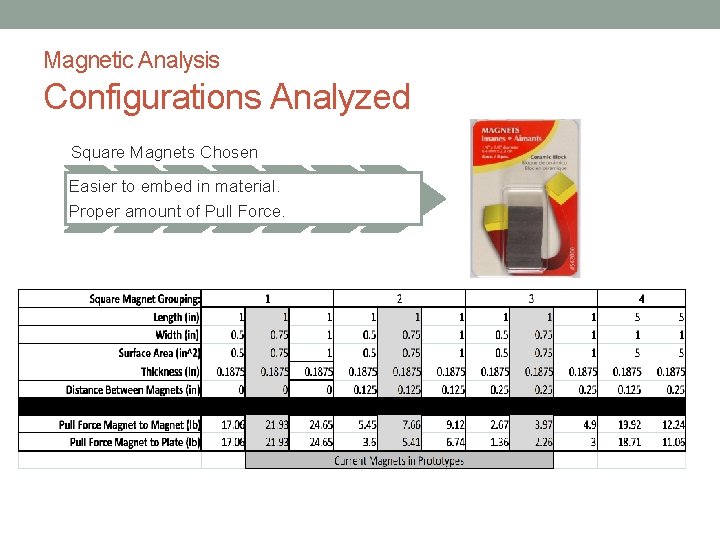
Magnetic Analysis Configurations Analyzed Square Magnets Chosen Easier to embed in material. Proper amount of Pull Force.
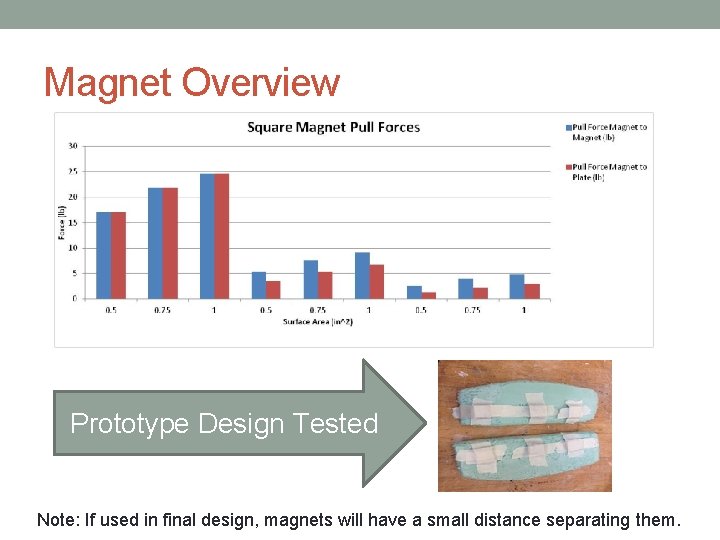
Magnet Overview Prototype Design Tested Note: If used in final design, magnets will have a small distance separating them.
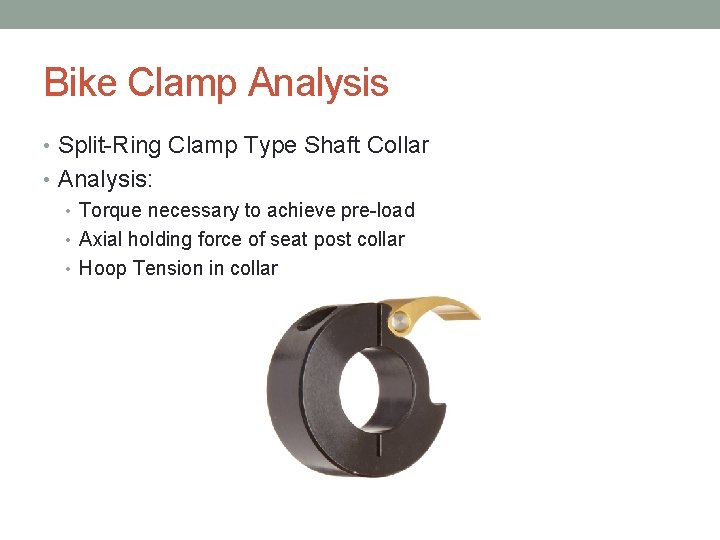
Bike Clamp Analysis • Split-Ring Clamp Type Shaft Collar • Analysis: • Torque necessary to achieve pre-load • Axial holding force of seat post collar • Hoop Tension in collar
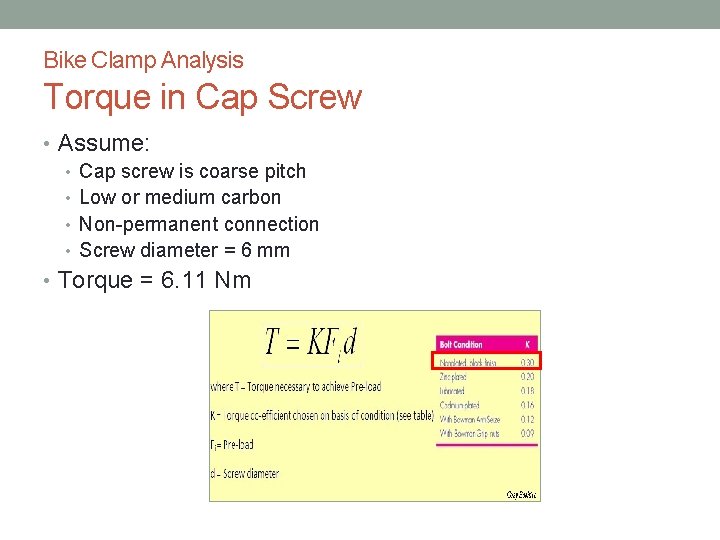
Bike Clamp Analysis Torque in Cap Screw • Assume: • Cap screw is coarse pitch • Low or medium carbon • Non-permanent connection • Screw diameter = 6 mm • Torque = 6. 11 Nm
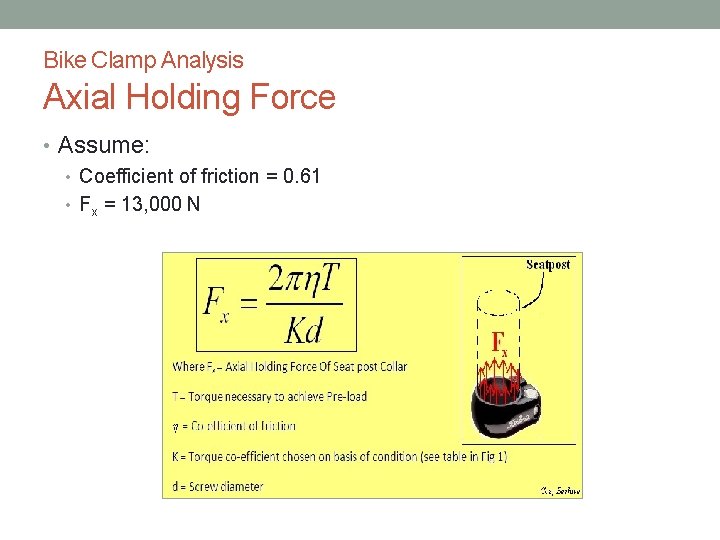
Bike Clamp Analysis Axial Holding Force • Assume: • Coefficient of friction = 0. 61 • Fx = 13, 000 N
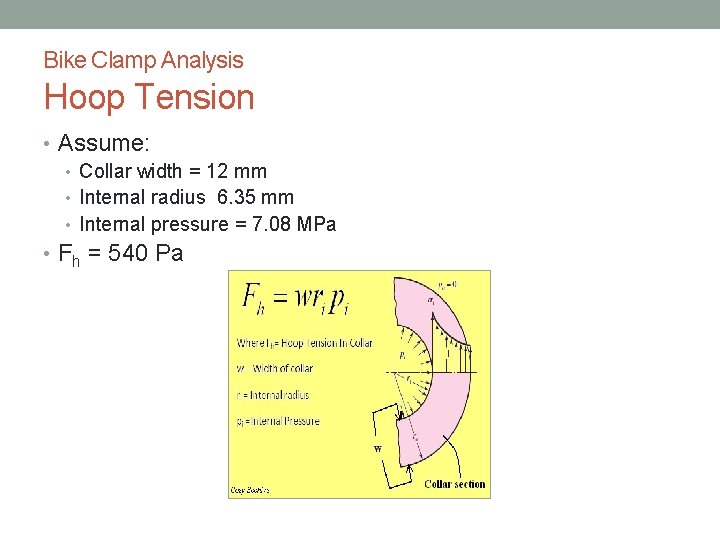
Bike Clamp Analysis Hoop Tension • Assume: • Collar width = 12 mm • Internal radius 6. 35 mm • Internal pressure = 7. 08 MPa • Fh = 540 Pa
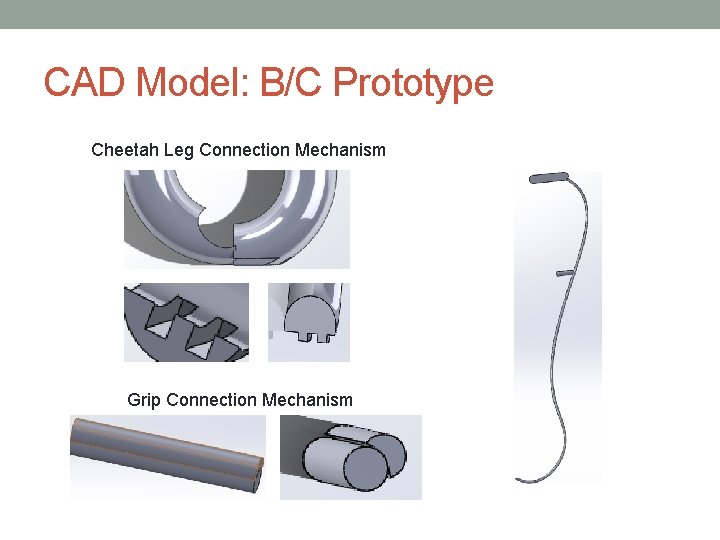
CAD Model: B/C Prototype Cheetah Leg Connection Mechanism Grip Connection Mechanism
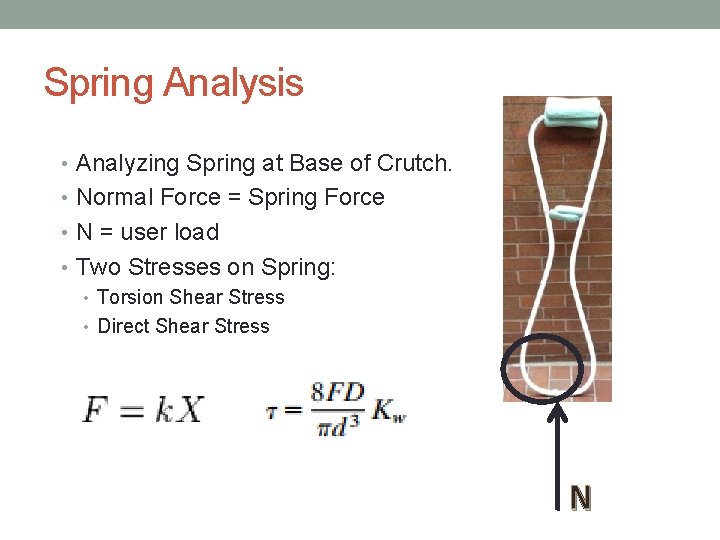
Spring Analysis • Analyzing Spring at Base of Crutch. • Normal Force = Spring Force • N = user load • Two Stresses on Spring: • Torsion Shear Stress • Direct Shear Stress N
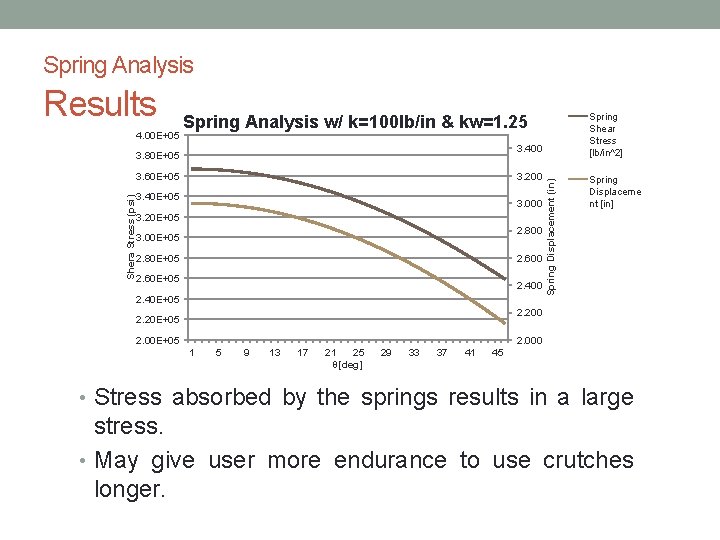
Spring Analysis 4. 00 E+05 3. 400 3. 80 E+05 3. 60 E+05 Shera Stress (psi) Spring Shear Stress [lb/in^2] Spring Analysis w/ k=100 lb/in & kw=1. 25 3. 200 3. 40 E+05 3. 000 3. 20 E+05 2. 800 3. 00 E+05 2. 80 E+05 2. 600 2. 60 E+05 2. 400 2. 40 E+05 Spring Displacement (in) Results Spring Displaceme nt [in] 2. 200 2. 20 E+05 2. 000 1 5 9 13 17 21 25 θ[deg] 29 33 37 41 45 • Stress absorbed by the springs results in a large stress. • May give user more endurance to use crutches longer.

Deflection of Cheetah Leg Base P • Assume: • Carbon fiber material • Circular cross-section • r = 0. 75 in = 1. 91 x 10 -2 m • R 2 = 0. 3 m • Deflection = 0. 08 in = 0. 002 m M P R 2 D P
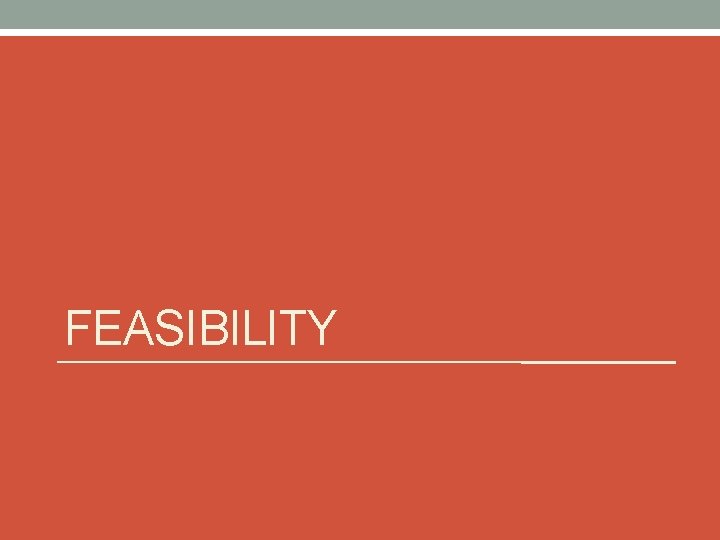
FEASIBILITY
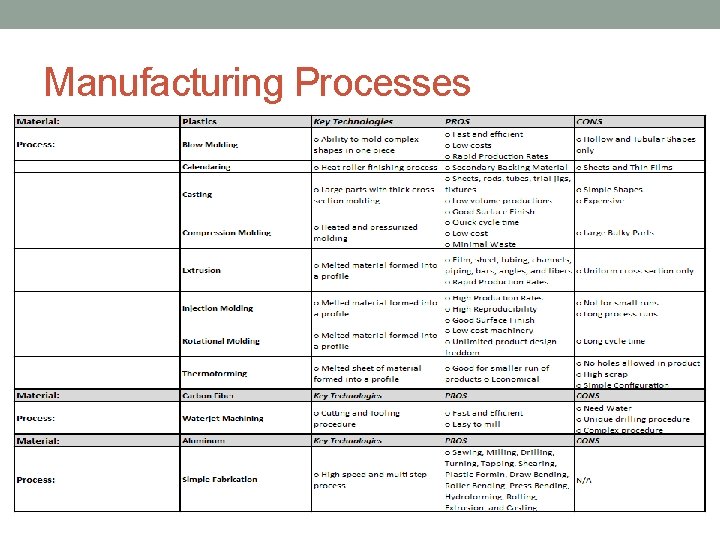
Manufacturing Processes
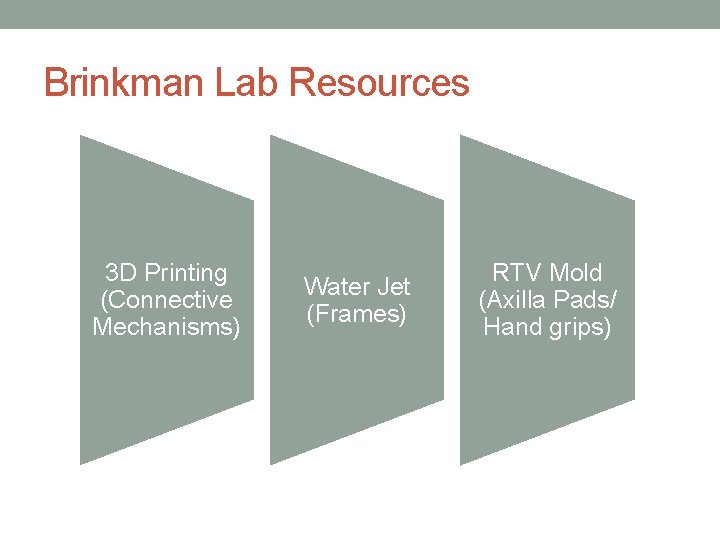
Brinkman Lab Resources 3 D Printing (Connective Mechanisms) Water Jet (Frames) RTV Mold (Axilla Pads/ Hand grips)
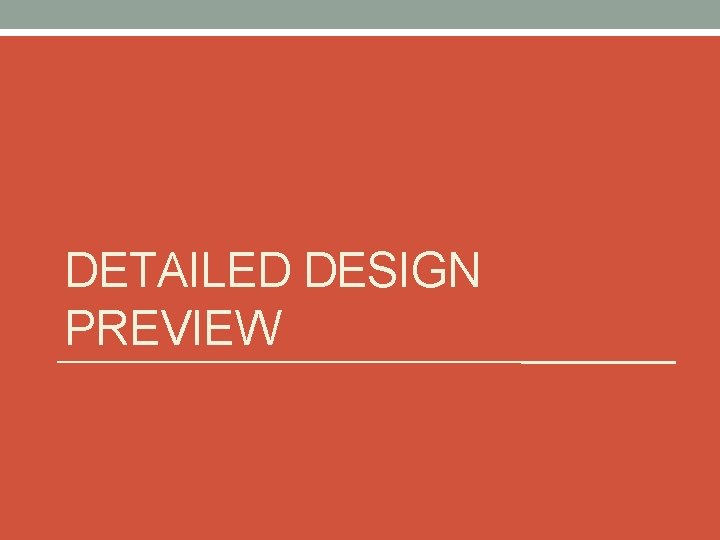
DETAILED DESIGN PREVIEW
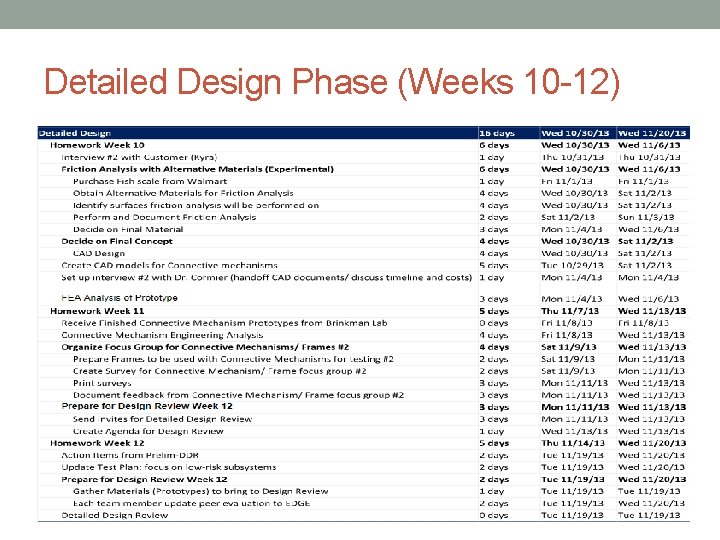
Detailed Design Phase (Weeks 10 -12)
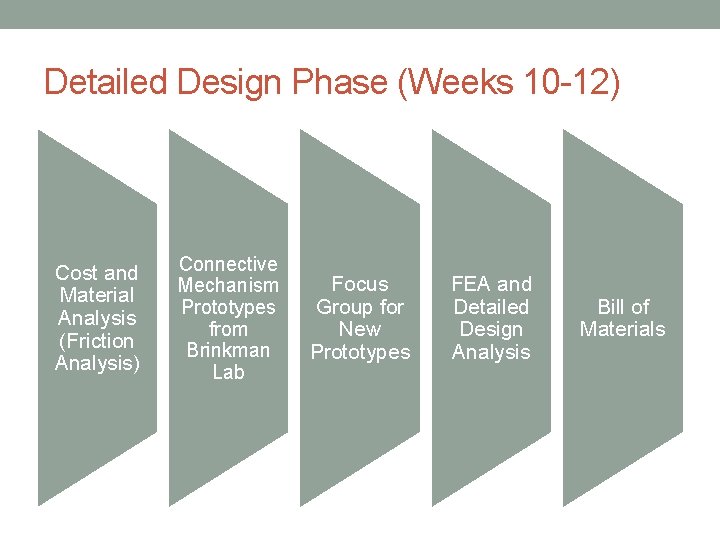
Detailed Design Phase (Weeks 10 -12) Cost and Material Analysis (Friction Analysis) Connective Mechanism Prototypes from Brinkman Lab Focus Group for New Prototypes FEA and Detailed Design Analysis Bill of Materials
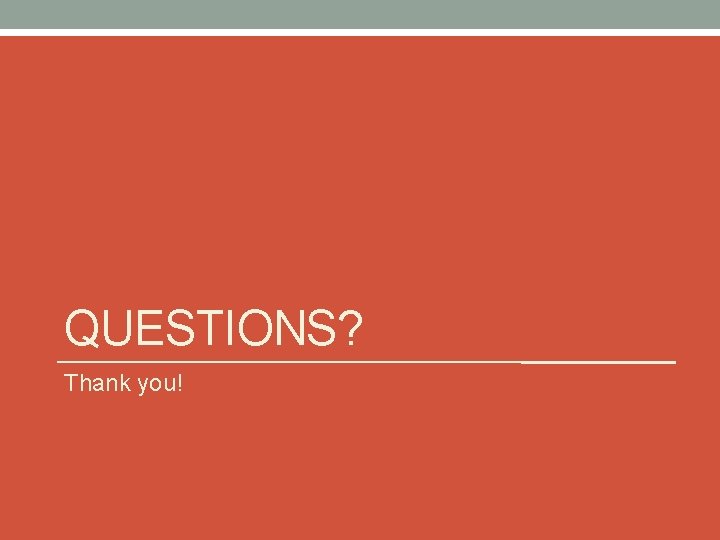
QUESTIONS? Thank you!
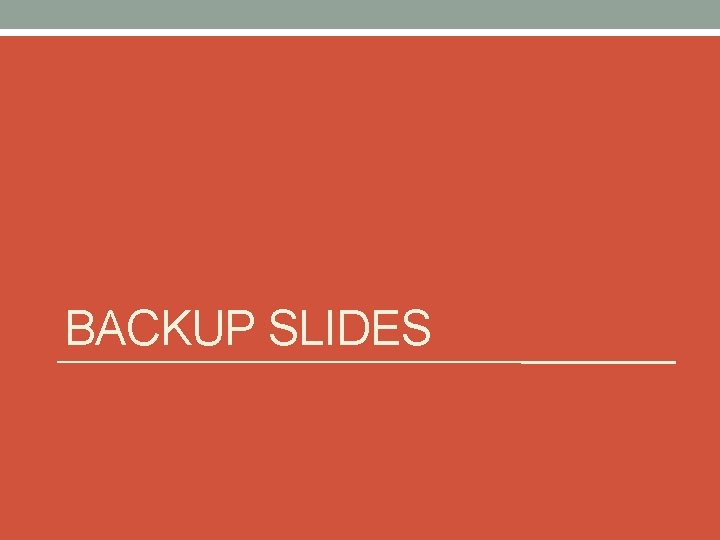
BACKUP SLIDES
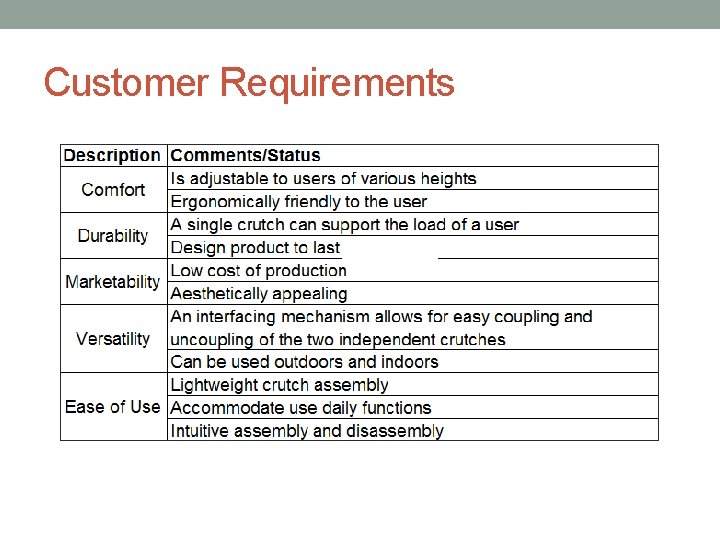
Customer Requirements
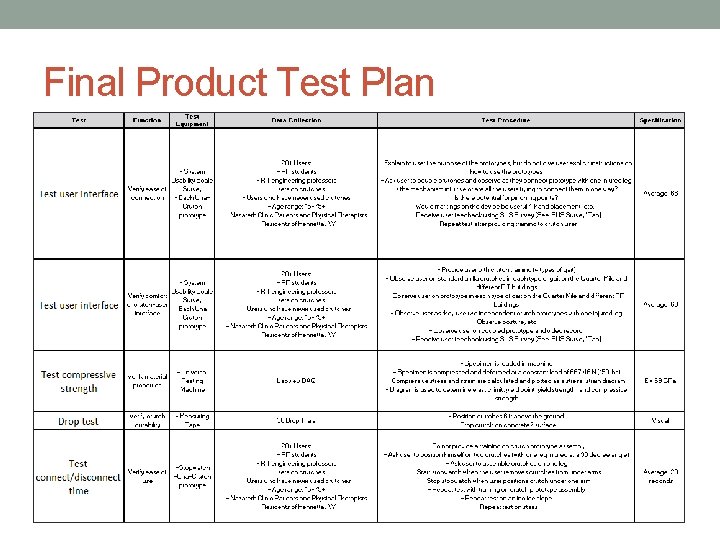
Final Product Test Plan