Operations Management Chapter 7 Process Strategy Power Point
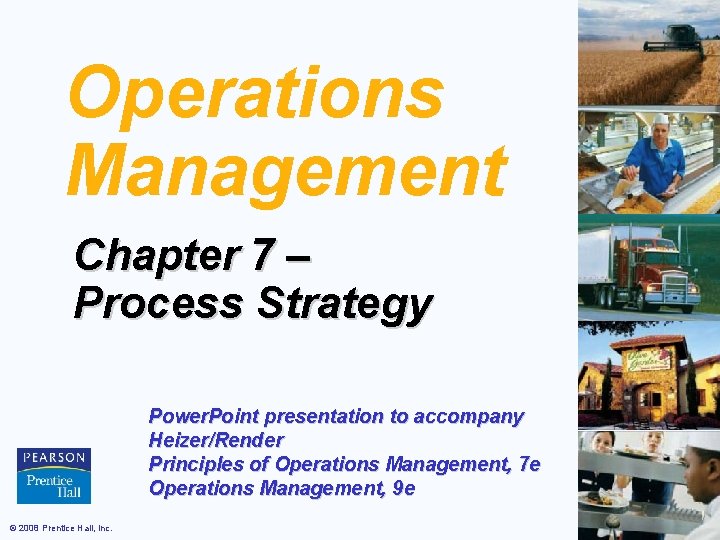
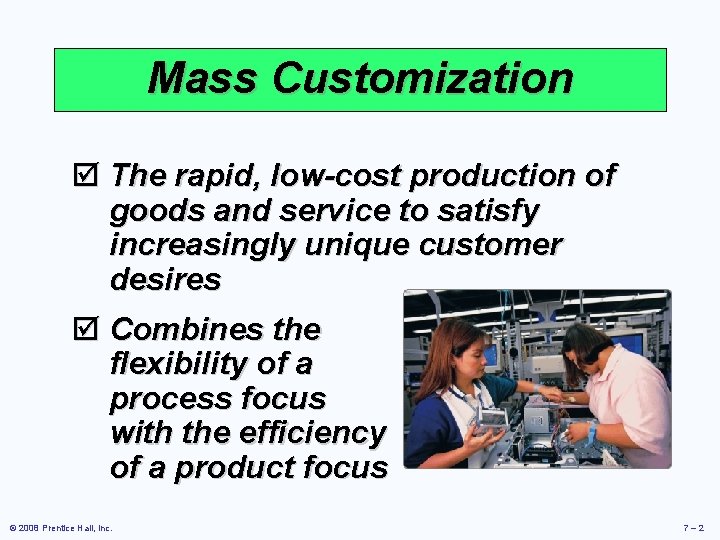
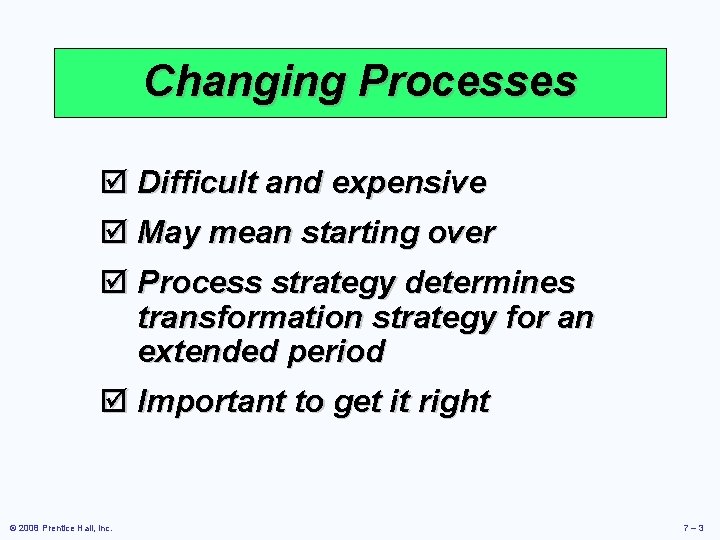
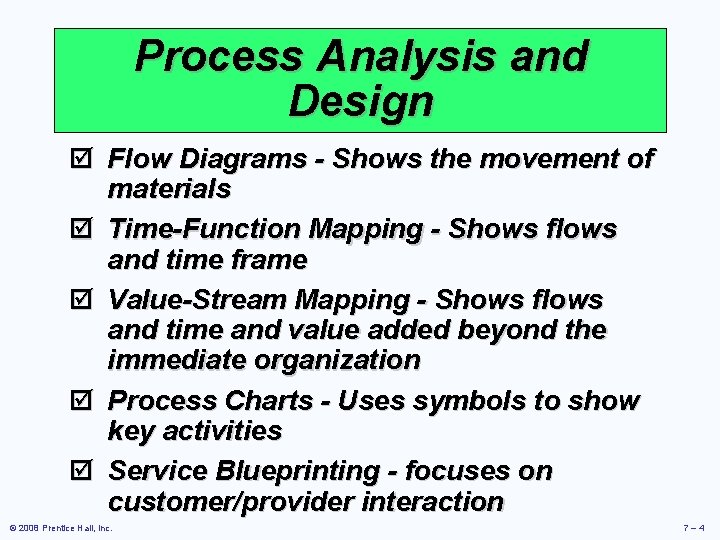
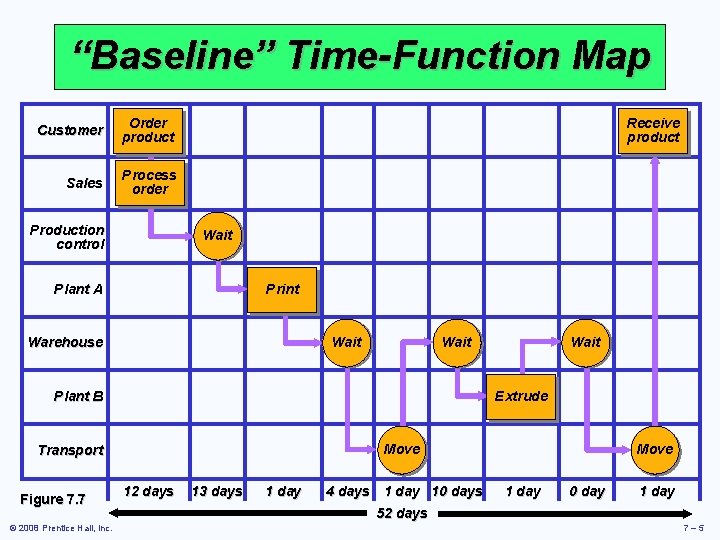
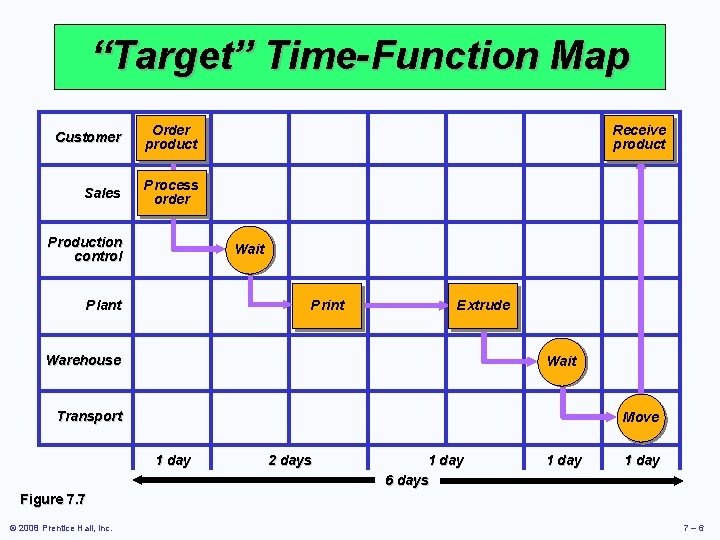
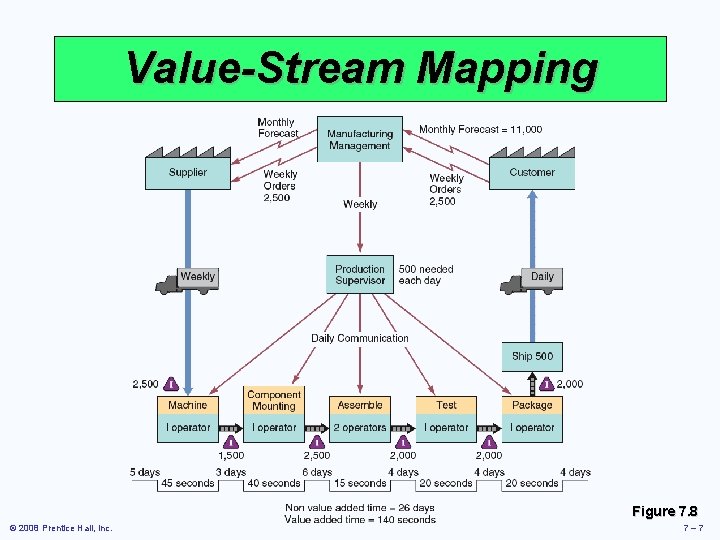
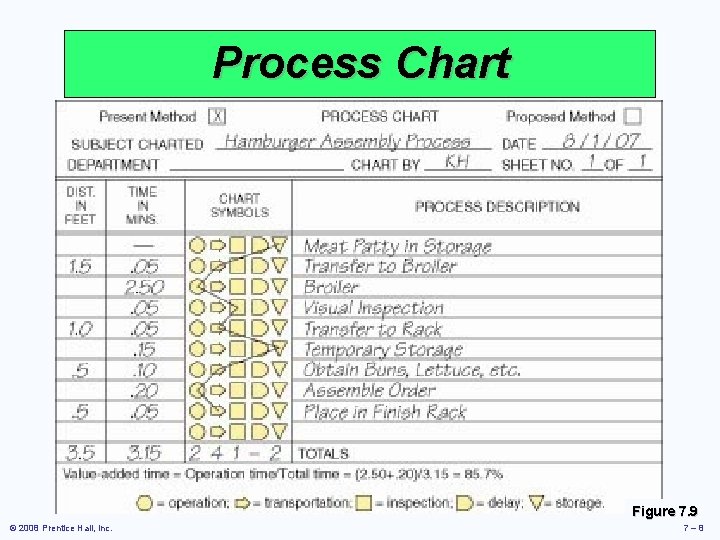
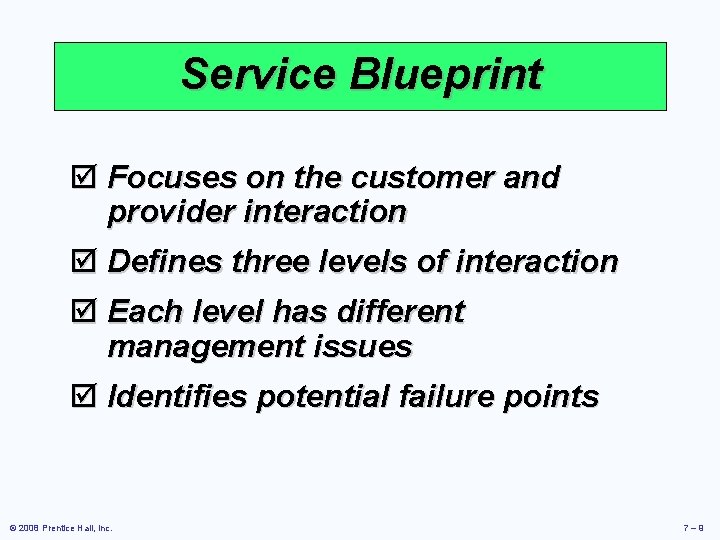
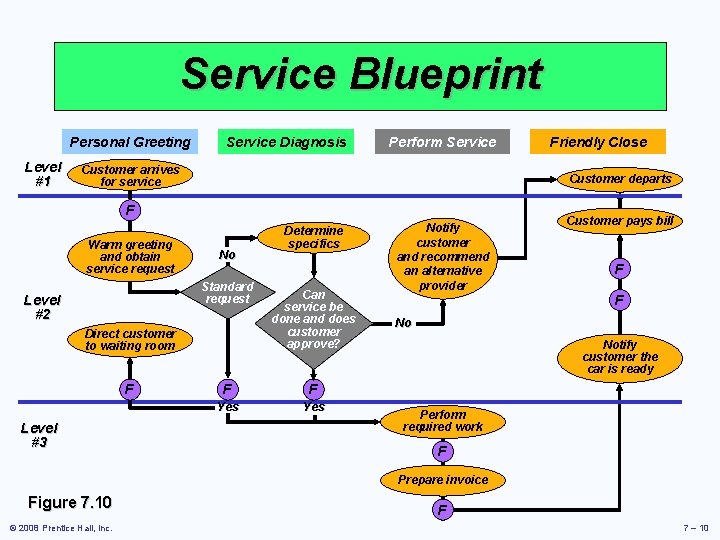
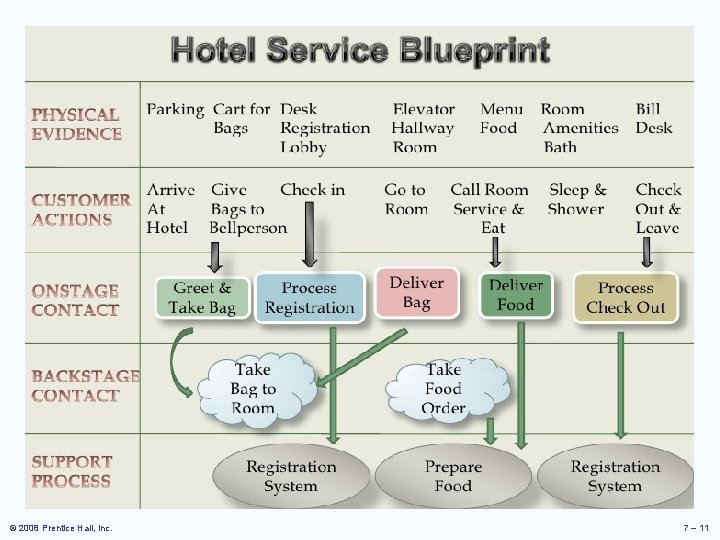
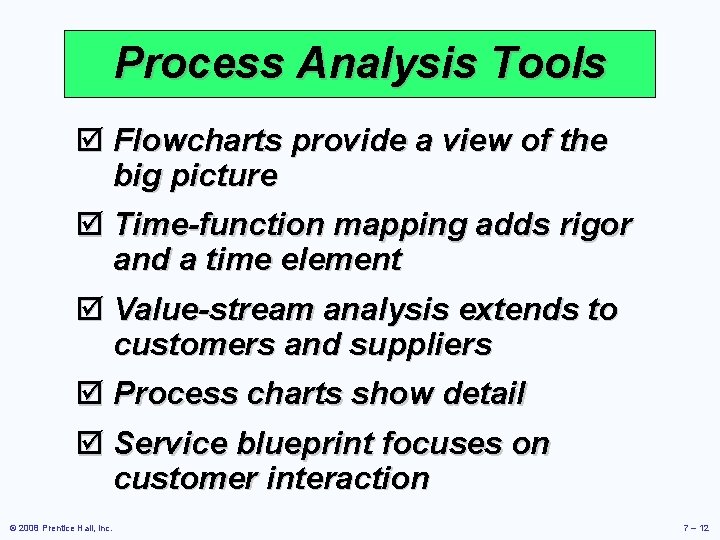
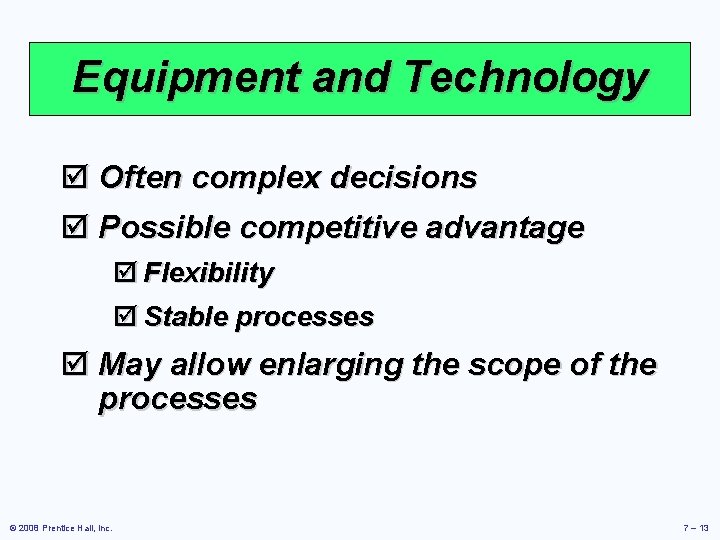
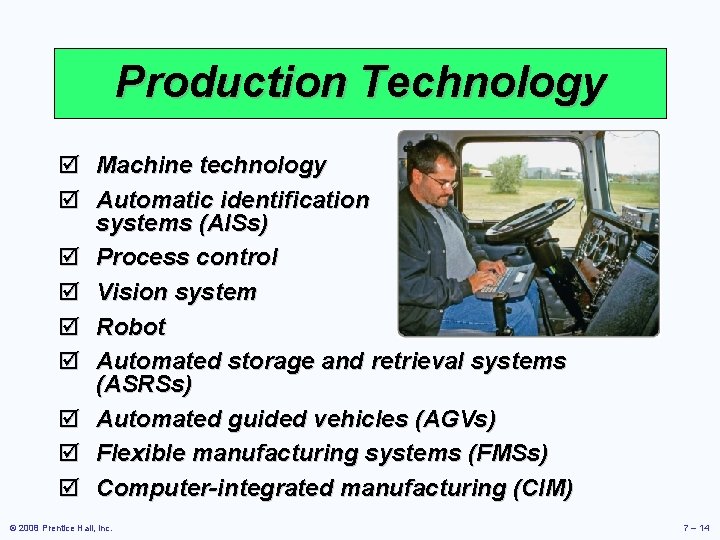
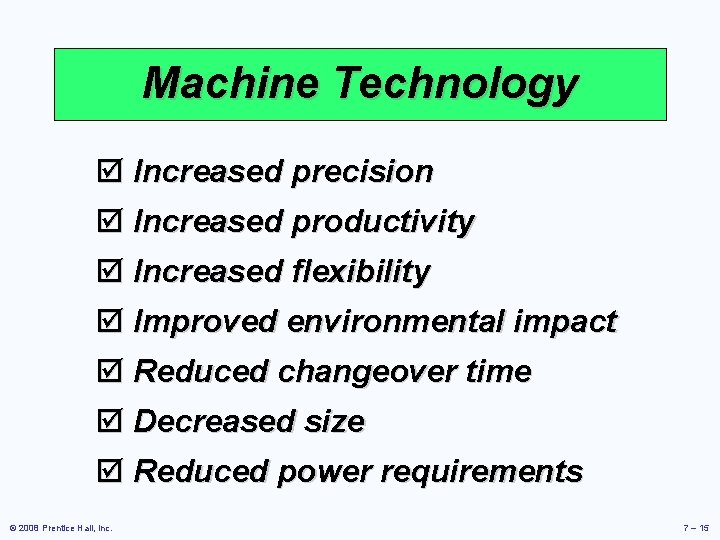
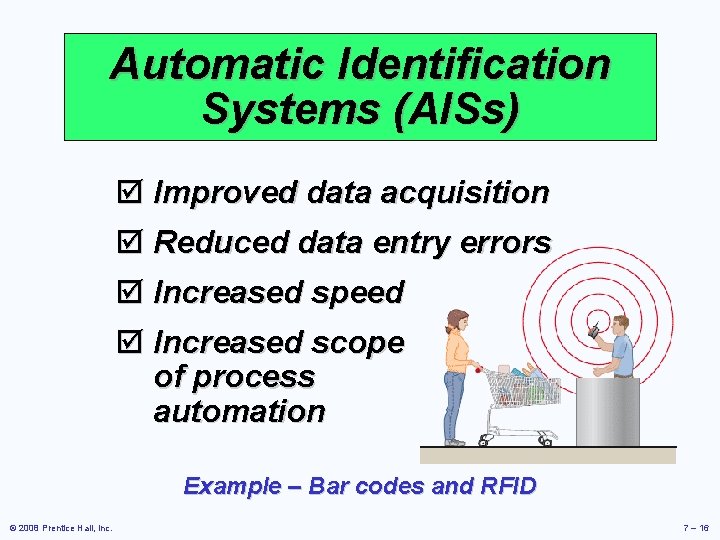
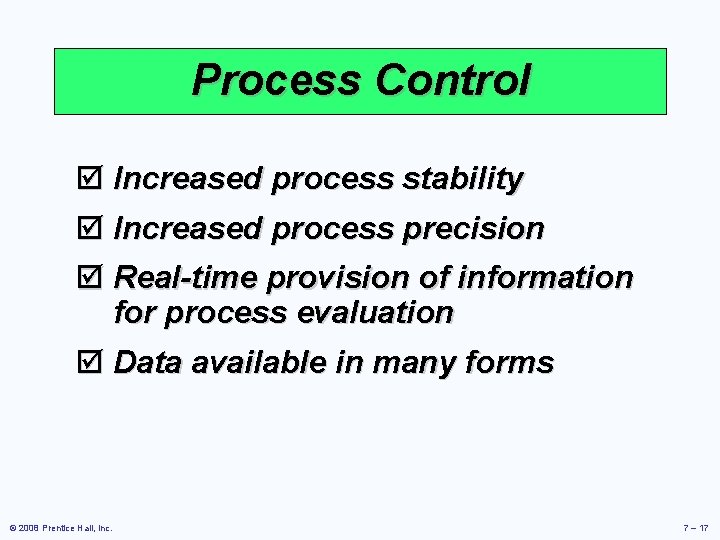
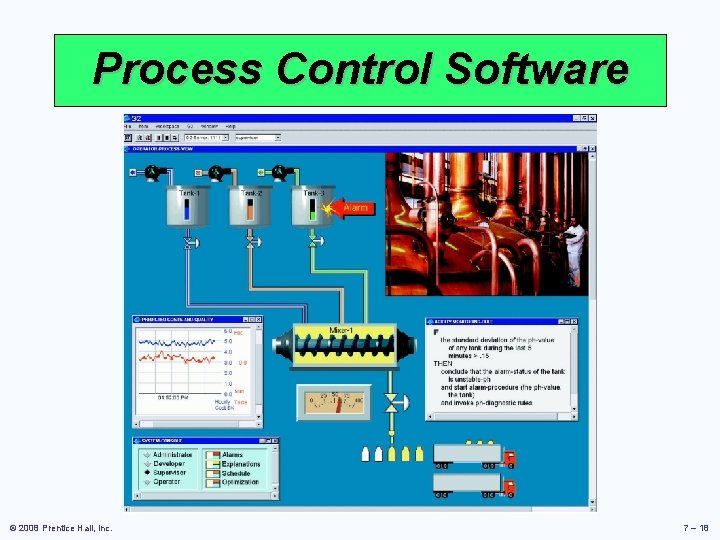

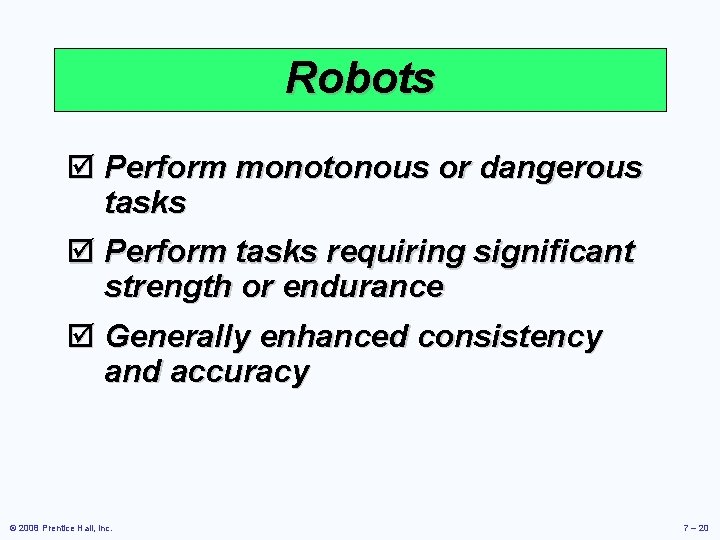
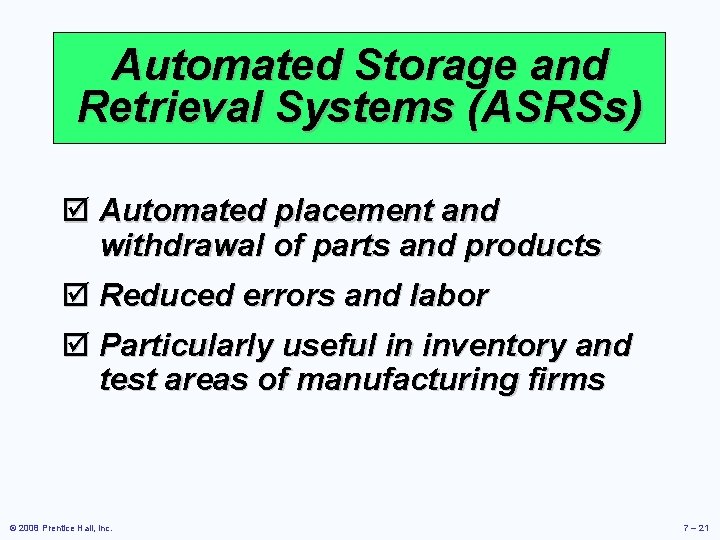
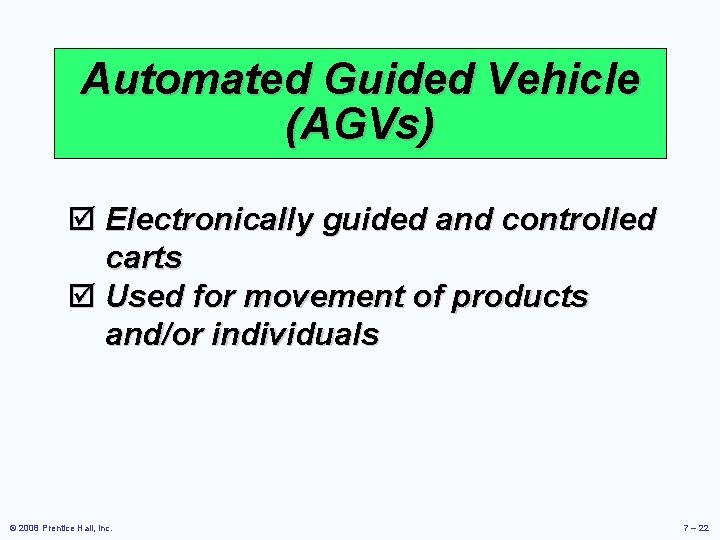
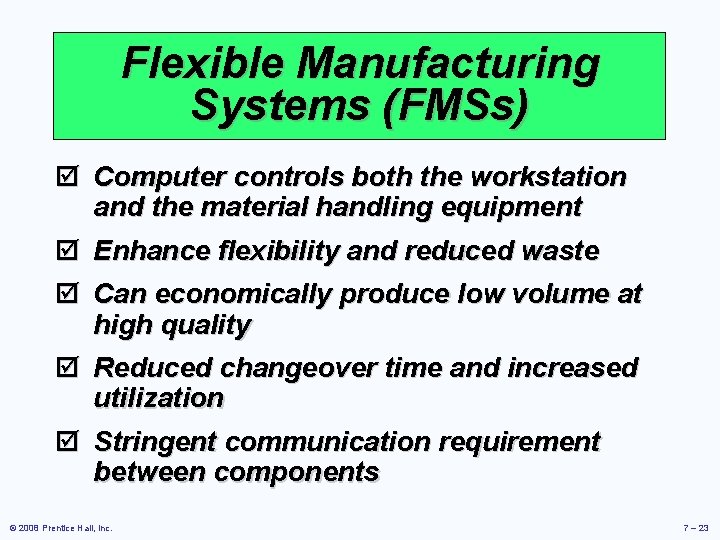
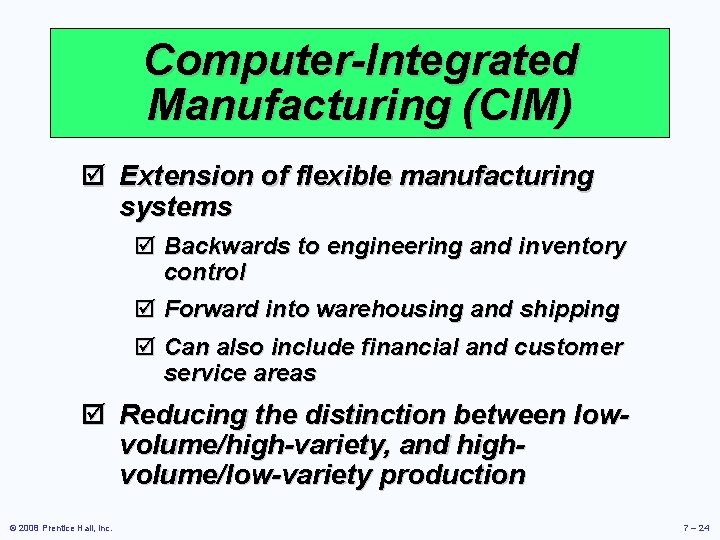
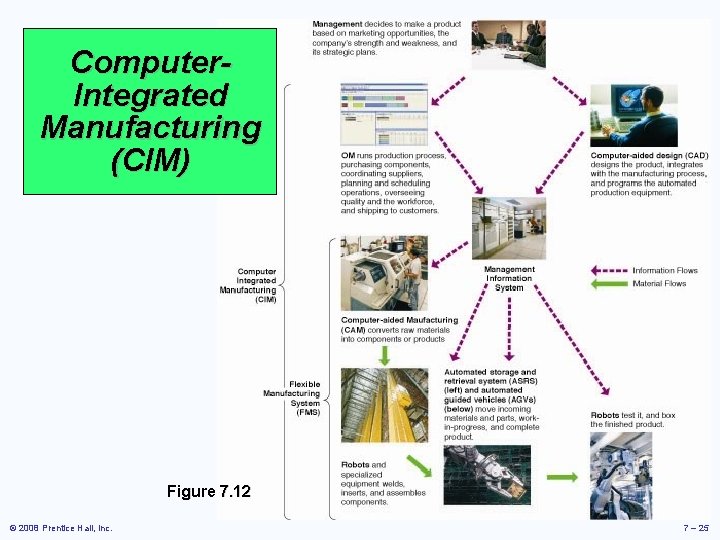
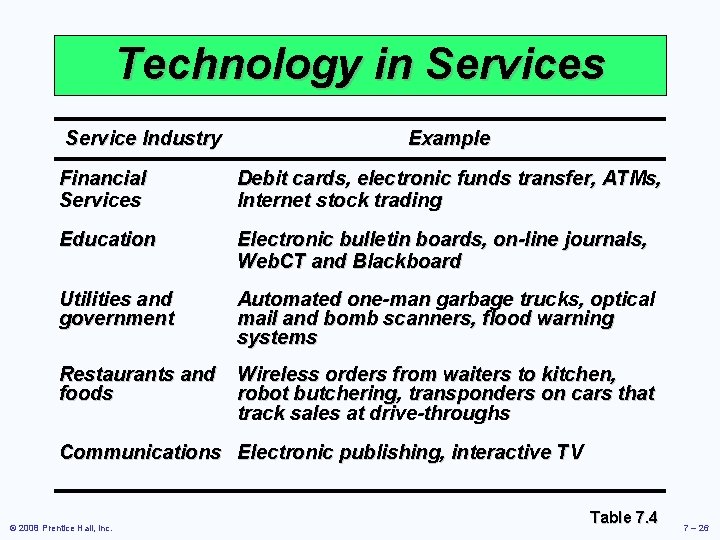
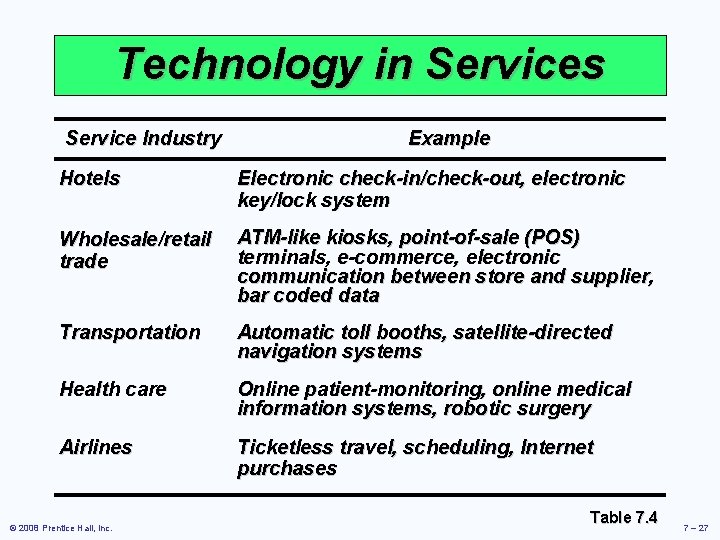
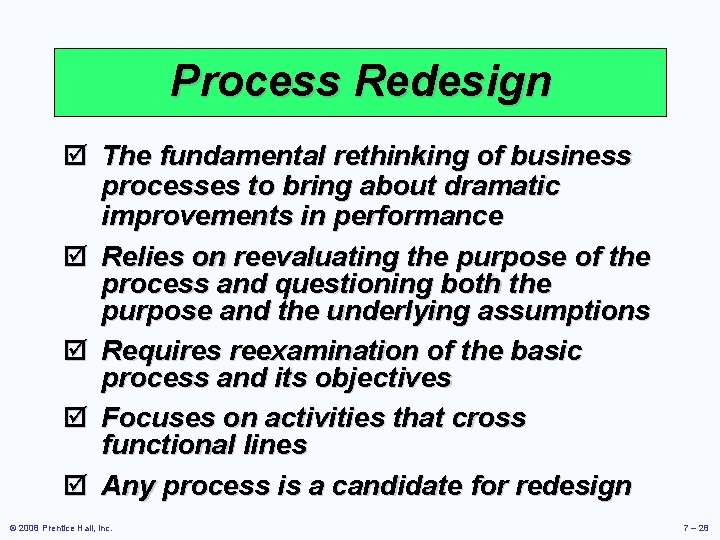
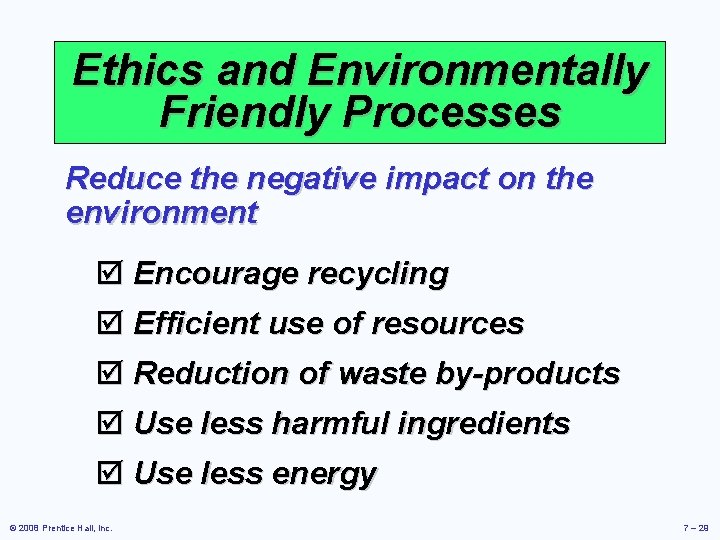
- Slides: 29
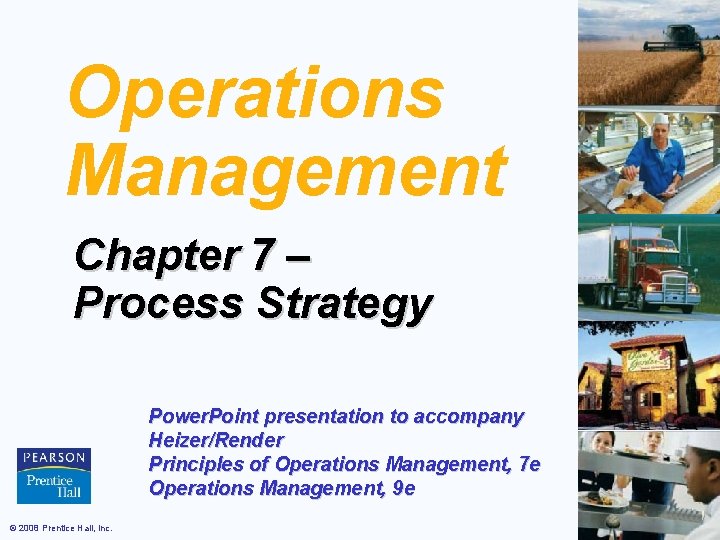
Operations Management Chapter 7 – Process Strategy Power. Point presentation to accompany Heizer/Render Principles of Operations Management, 7 e Operations Management, 9 e © 2008 Prentice Hall, Inc. 7– 1
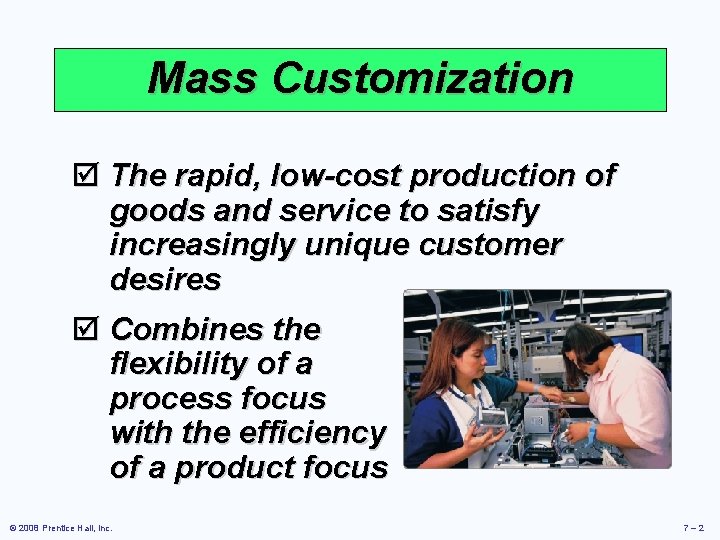
Mass Customization þ The rapid, low-cost production of goods and service to satisfy increasingly unique customer desires þ Combines the flexibility of a process focus with the efficiency of a product focus © 2008 Prentice Hall, Inc. 7– 2
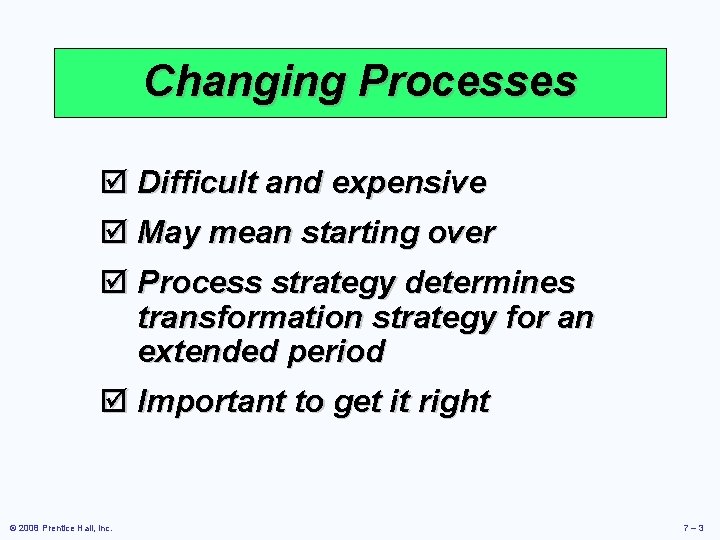
Changing Processes þ Difficult and expensive þ May mean starting over þ Process strategy determines transformation strategy for an extended period þ Important to get it right © 2008 Prentice Hall, Inc. 7– 3
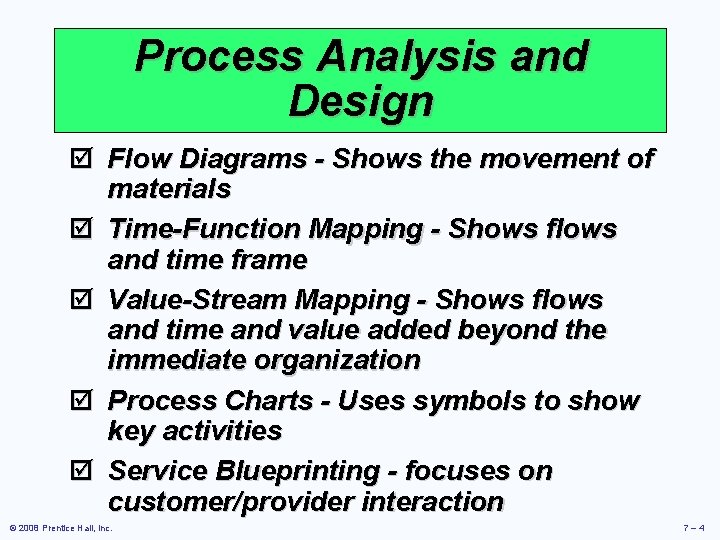
Process Analysis and Design þ Flow Diagrams - Shows the movement of materials þ Time-Function Mapping - Shows flows and time frame þ Value-Stream Mapping - Shows flows and time and value added beyond the immediate organization þ Process Charts - Uses symbols to show key activities þ Service Blueprinting - focuses on customer/provider interaction © 2008 Prentice Hall, Inc. 7– 4
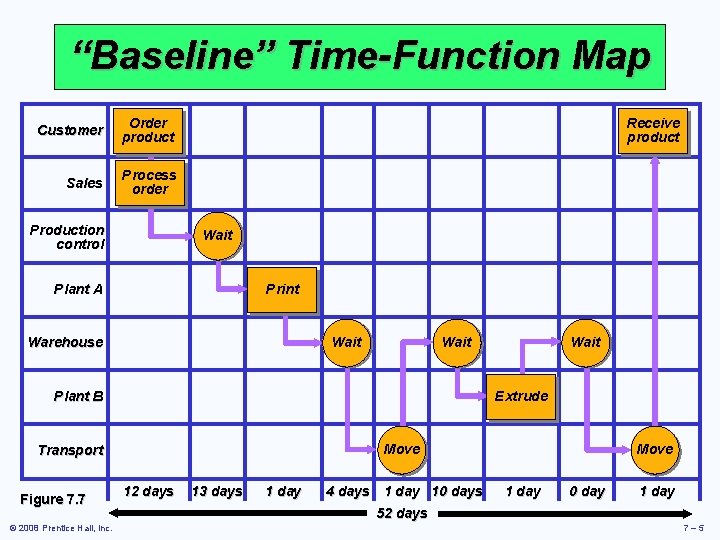
“Baseline” Time-Function Map Customer Order product Sales Process order Production control Receive product Wait Plant A Print Warehouse Wait Extrude Plant B Move Transport Figure 7. 7 © 2008 Prentice Hall, Inc. Wait 12 days 13 days 1 day 4 days 1 day 10 days Move 1 day 0 day 1 day 52 days 7– 5
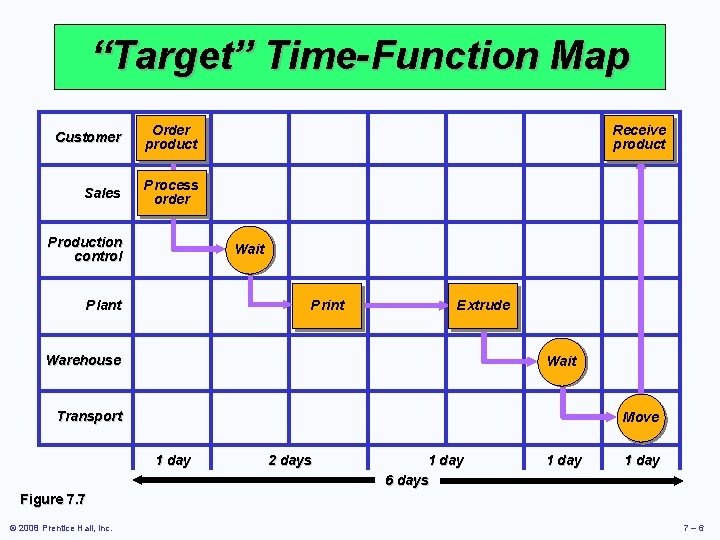
“Target” Time-Function Map Customer Order product Sales Process order Production control Receive product Wait Plant Print Extrude Warehouse Wait Transport Move 1 day 2 days 1 day 6 days 1 day Figure 7. 7 © 2008 Prentice Hall, Inc. 7– 6
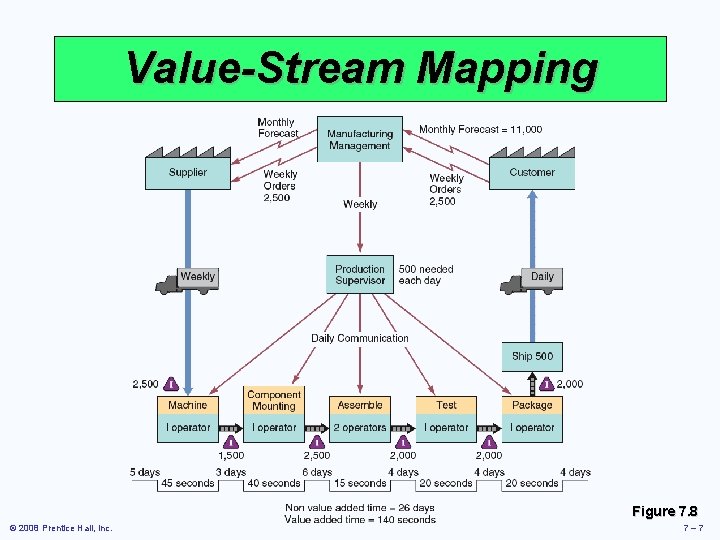
Value-Stream Mapping Figure 7. 8 © 2008 Prentice Hall, Inc. 7– 7
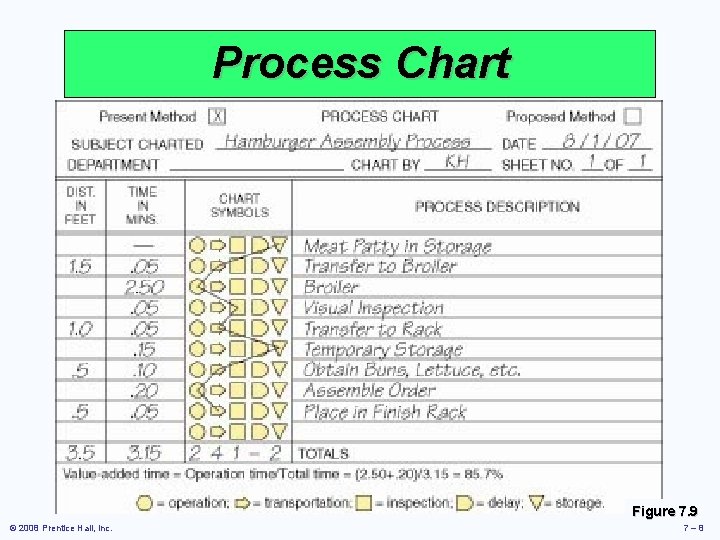
Process Chart Figure 7. 9 © 2008 Prentice Hall, Inc. 7– 8
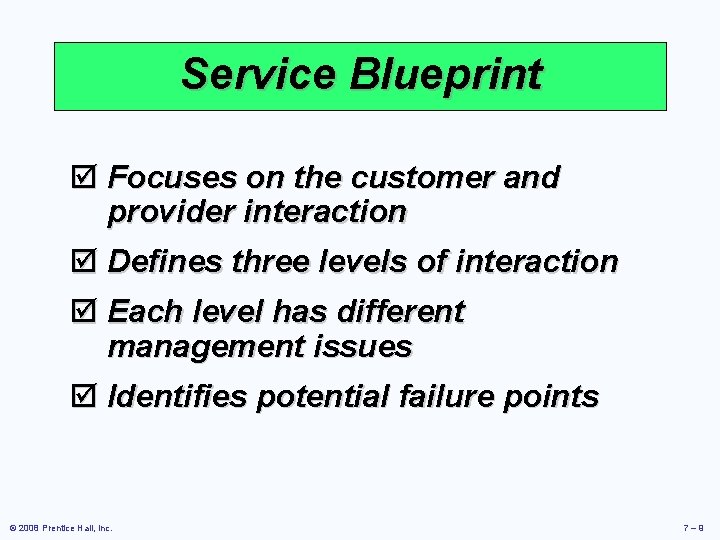
Service Blueprint þ Focuses on the customer and provider interaction þ Defines three levels of interaction þ Each level has different management issues þ Identifies potential failure points © 2008 Prentice Hall, Inc. 7– 9
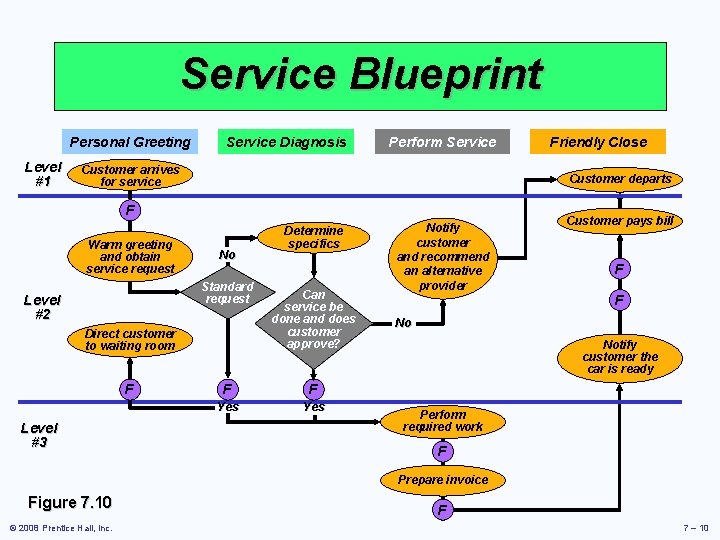
Service Blueprint Personal Greeting Level #1 Service Diagnosis Perform Service Customer arrives for service Customer departs F Warm greeting and obtain service request No Standard request Level #2 Direct customer to waiting room F Level #3 Friendly Close Determine specifics Can service be done and does customer approve? F F Yes Notify customer and recommend an alternative provider Customer pays bill F F No Notify customer the car is ready Perform required work F Prepare invoice Figure 7. 10 © 2008 Prentice Hall, Inc. F 7 – 10
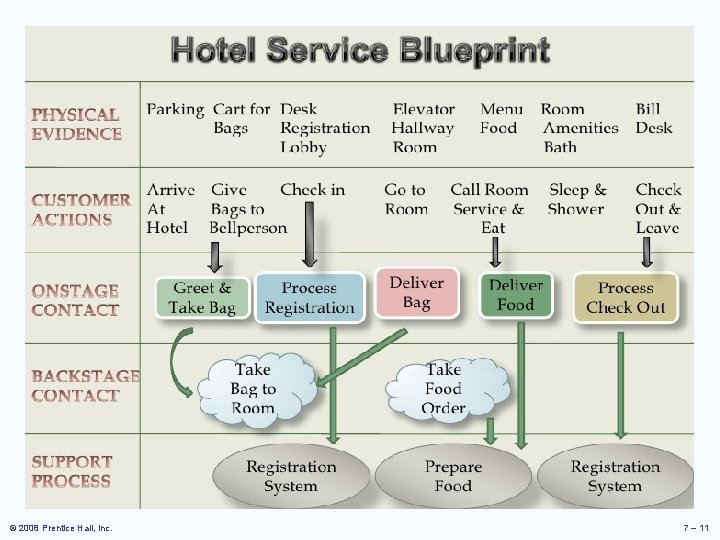
© 2008 Prentice Hall, Inc. 7 – 11
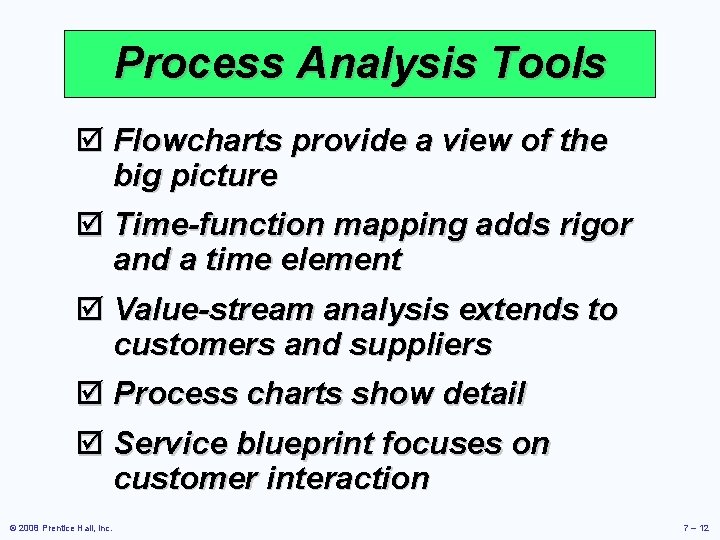
Process Analysis Tools þ Flowcharts provide a view of the big picture þ Time-function mapping adds rigor and a time element þ Value-stream analysis extends to customers and suppliers þ Process charts show detail þ Service blueprint focuses on customer interaction © 2008 Prentice Hall, Inc. 7 – 12
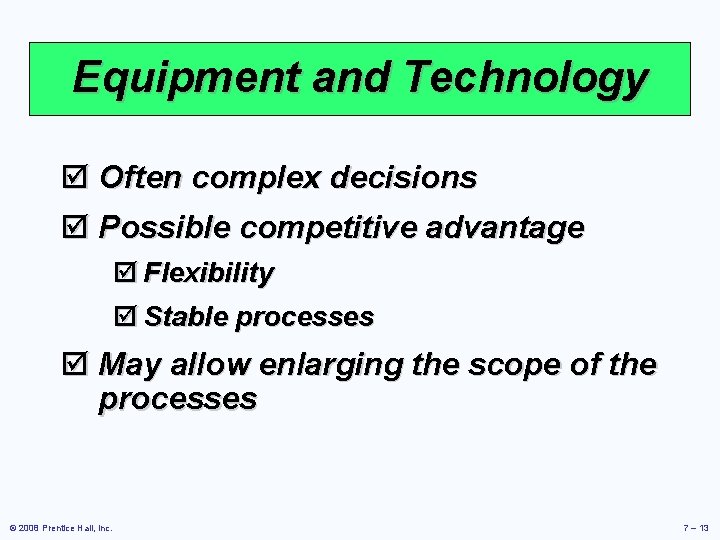
Equipment and Technology þ Often complex decisions þ Possible competitive advantage þ Flexibility þ Stable processes þ May allow enlarging the scope of the processes © 2008 Prentice Hall, Inc. 7 – 13
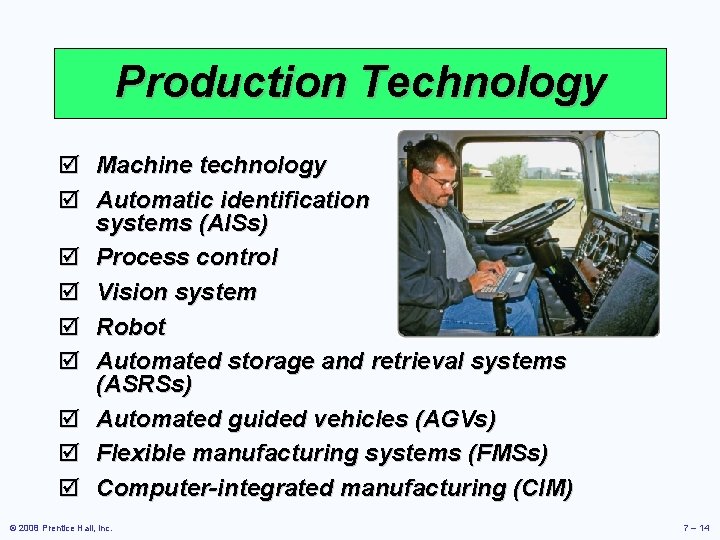
Production Technology þ Machine technology þ Automatic identification systems (AISs) þ Process control þ Vision system þ Robot þ Automated storage and retrieval systems (ASRSs) þ Automated guided vehicles (AGVs) þ Flexible manufacturing systems (FMSs) þ Computer-integrated manufacturing (CIM) © 2008 Prentice Hall, Inc. 7 – 14
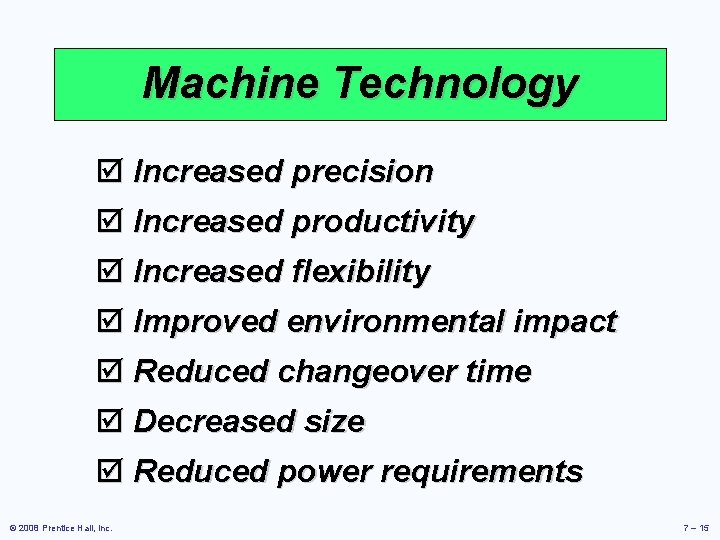
Machine Technology þ Increased precision þ Increased productivity þ Increased flexibility þ Improved environmental impact þ Reduced changeover time þ Decreased size þ Reduced power requirements © 2008 Prentice Hall, Inc. 7 – 15
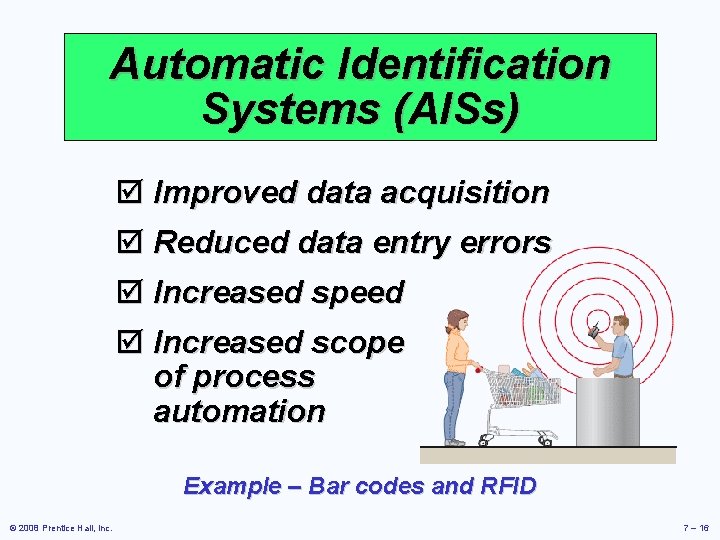
Automatic Identification Systems (AISs) þ Improved data acquisition þ Reduced data entry errors þ Increased speed þ Increased scope of process automation Example – Bar codes and RFID © 2008 Prentice Hall, Inc. 7 – 16
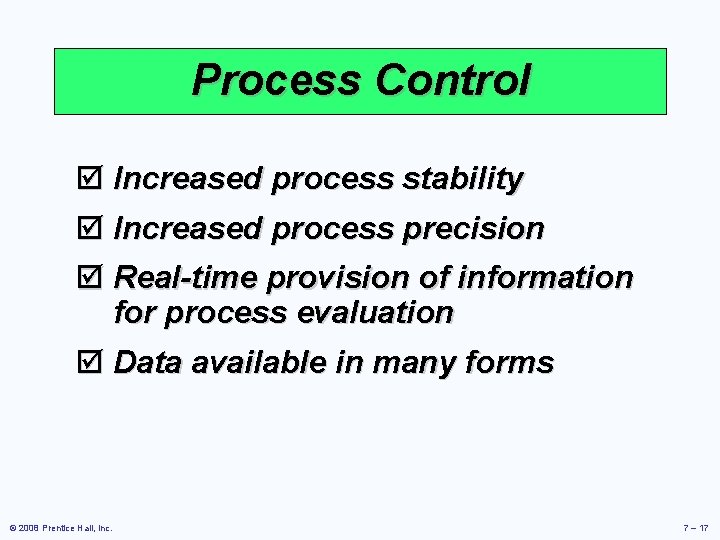
Process Control þ Increased process stability þ Increased process precision þ Real-time provision of information for process evaluation þ Data available in many forms © 2008 Prentice Hall, Inc. 7 – 17
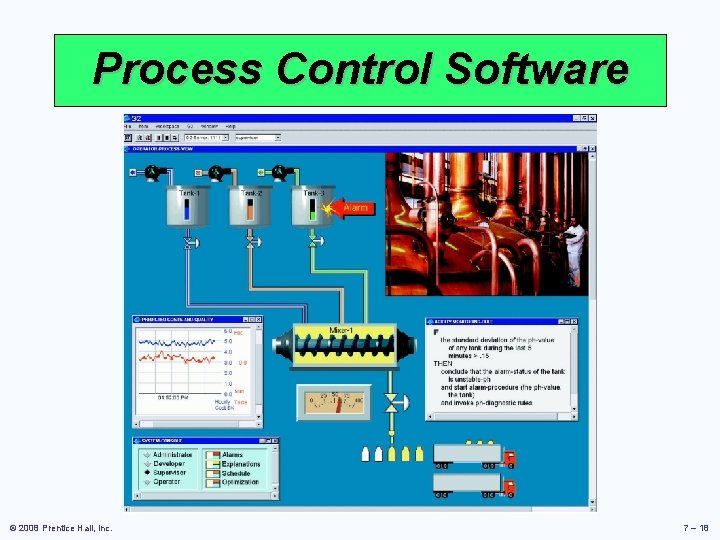
Process Control Software © 2008 Prentice Hall, Inc. 7 – 18

Vision Systems þ Particular aid to inspection þ Consistently accurate þ Never bored þ Modest cost þ Superior to individuals performing the same tasks © 2008 Prentice Hall, Inc. 7 – 19
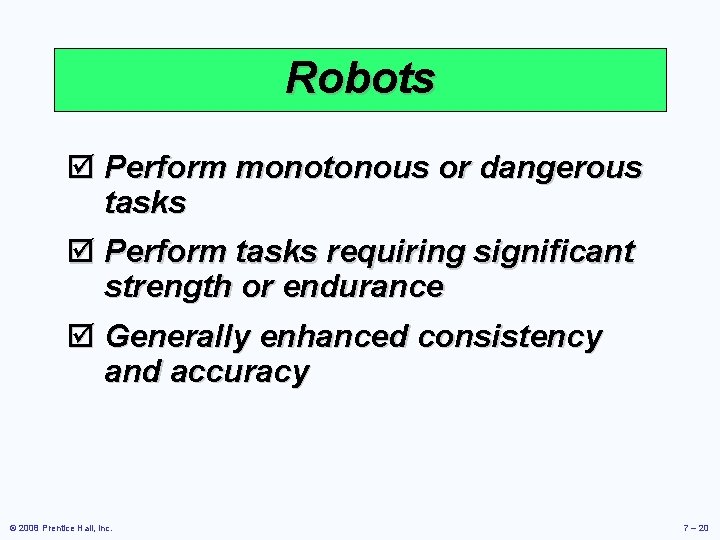
Robots þ Perform monotonous or dangerous tasks þ Perform tasks requiring significant strength or endurance þ Generally enhanced consistency and accuracy © 2008 Prentice Hall, Inc. 7 – 20
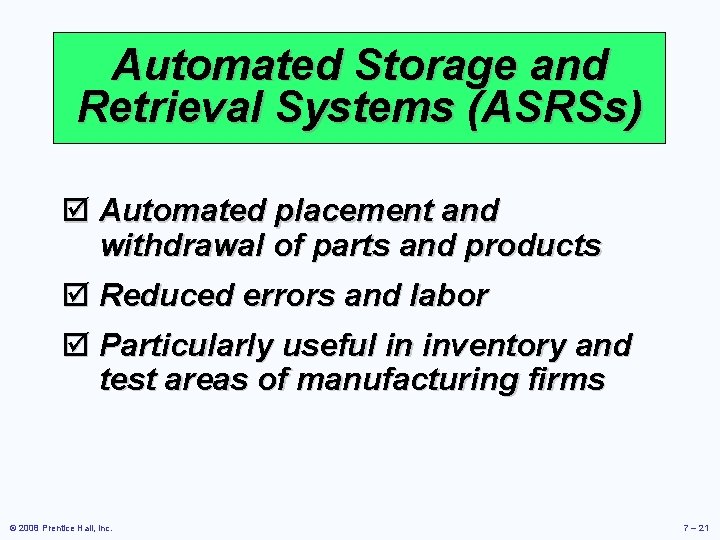
Automated Storage and Retrieval Systems (ASRSs) þ Automated placement and withdrawal of parts and products þ Reduced errors and labor þ Particularly useful in inventory and test areas of manufacturing firms © 2008 Prentice Hall, Inc. 7 – 21
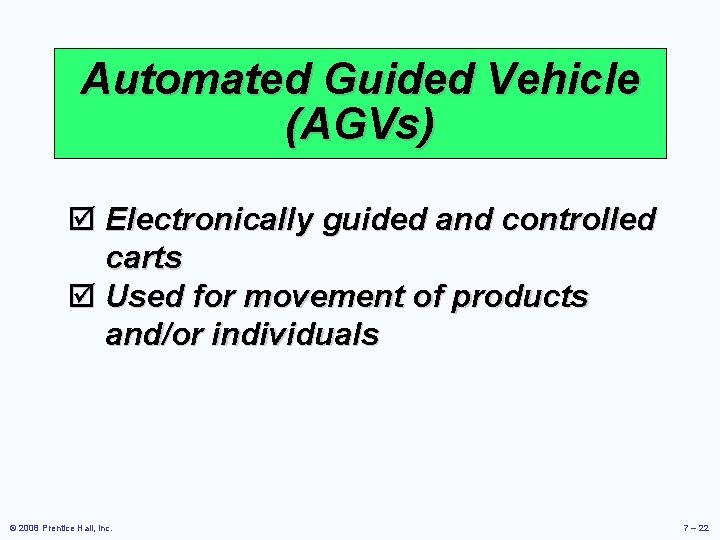
Automated Guided Vehicle (AGVs) þ Electronically guided and controlled carts þ Used for movement of products and/or individuals © 2008 Prentice Hall, Inc. 7 – 22
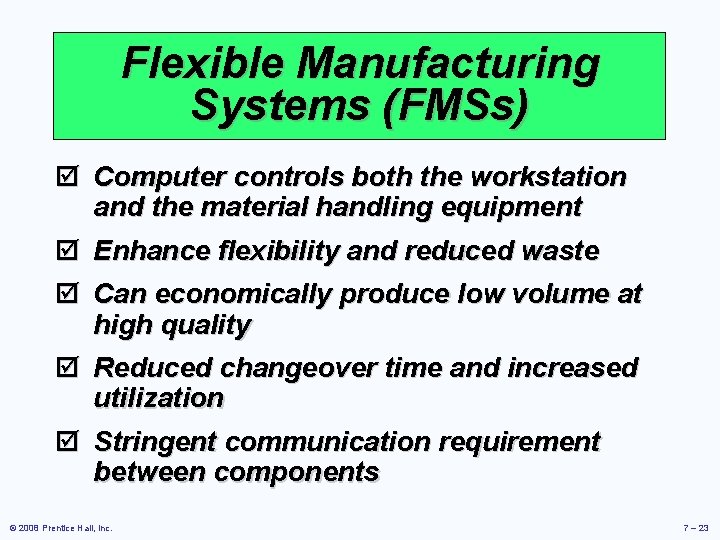
Flexible Manufacturing Systems (FMSs) þ Computer controls both the workstation and the material handling equipment þ Enhance flexibility and reduced waste þ Can economically produce low volume at high quality þ Reduced changeover time and increased utilization þ Stringent communication requirement between components © 2008 Prentice Hall, Inc. 7 – 23
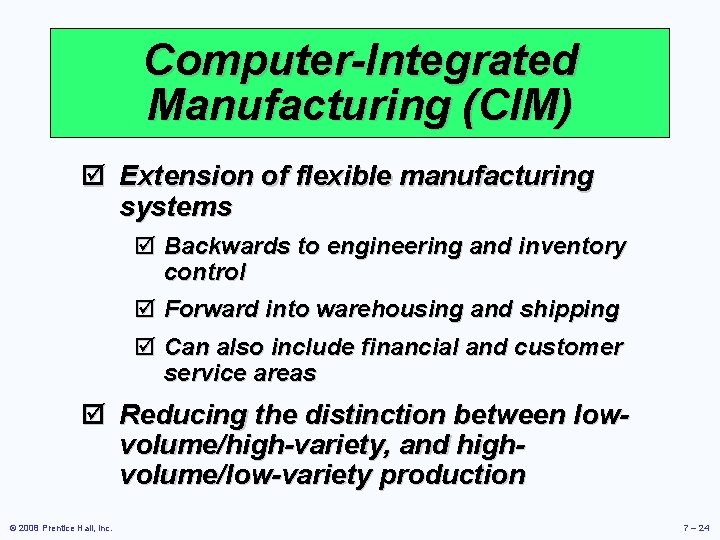
Computer-Integrated Manufacturing (CIM) þ Extension of flexible manufacturing systems þ Backwards to engineering and inventory control þ Forward into warehousing and shipping þ Can also include financial and customer service areas þ Reducing the distinction between lowvolume/high-variety, and highvolume/low-variety production © 2008 Prentice Hall, Inc. 7 – 24
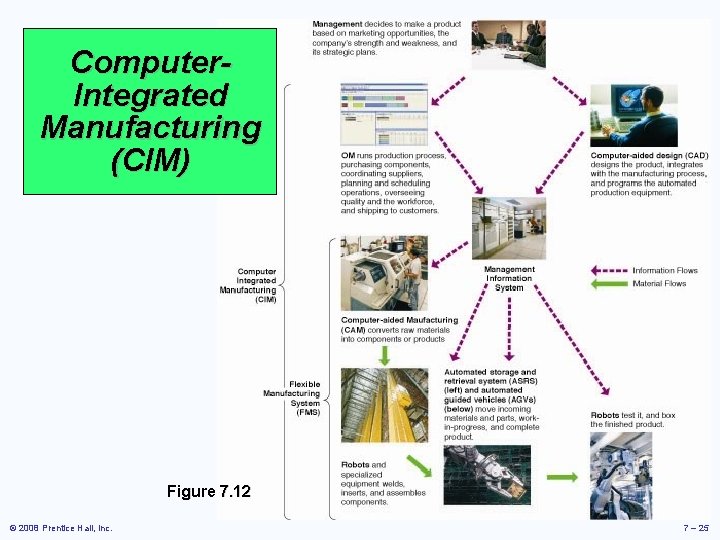
Computer. Integrated Manufacturing (CIM) Figure 7. 12 © 2008 Prentice Hall, Inc. 7 – 25
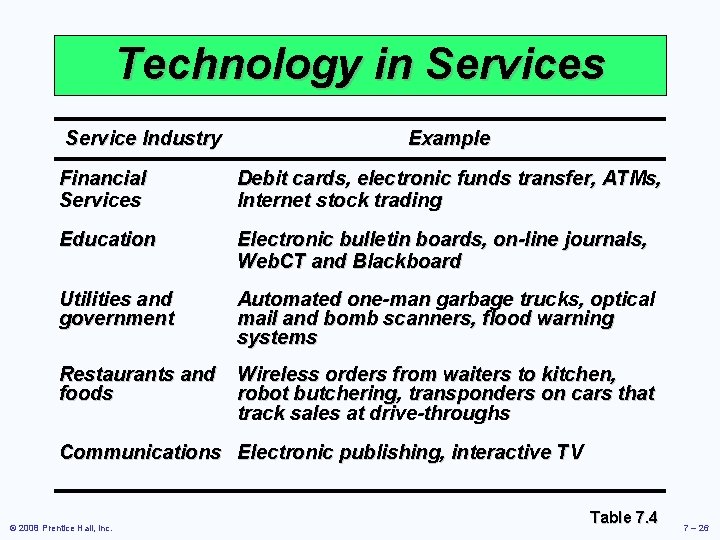
Technology in Services Service Industry Example Financial Services Debit cards, electronic funds transfer, ATMs, Internet stock trading Education Electronic bulletin boards, on-line journals, Web. CT and Blackboard Utilities and government Automated one-man garbage trucks, optical mail and bomb scanners, flood warning systems Restaurants and foods Wireless orders from waiters to kitchen, robot butchering, transponders on cars that track sales at drive-throughs Communications Electronic publishing, interactive TV © 2008 Prentice Hall, Inc. Table 7. 4 7 – 26
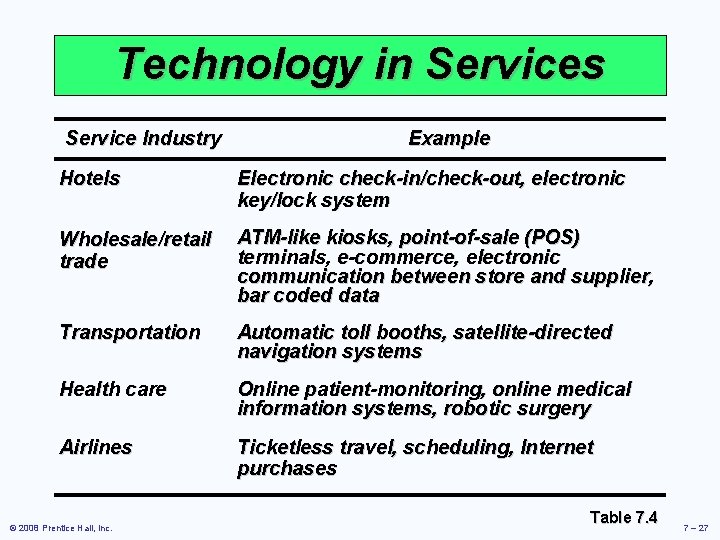
Technology in Services Service Industry Example Hotels Electronic check-in/check-out, electronic key/lock system Wholesale/retail trade ATM-like kiosks, point-of-sale (POS) terminals, e-commerce, electronic communication between store and supplier, bar coded data Transportation Automatic toll booths, satellite-directed navigation systems Health care Online patient-monitoring, online medical information systems, robotic surgery Airlines Ticketless travel, scheduling, Internet purchases © 2008 Prentice Hall, Inc. Table 7. 4 7 – 27
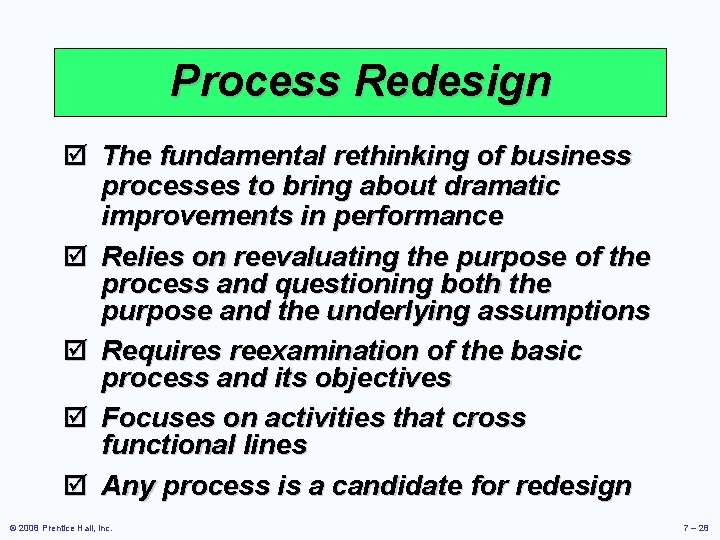
Process Redesign þ The fundamental rethinking of business processes to bring about dramatic improvements in performance þ Relies on reevaluating the purpose of the process and questioning both the purpose and the underlying assumptions þ Requires reexamination of the basic process and its objectives þ Focuses on activities that cross functional lines þ Any process is a candidate for redesign © 2008 Prentice Hall, Inc. 7 – 28
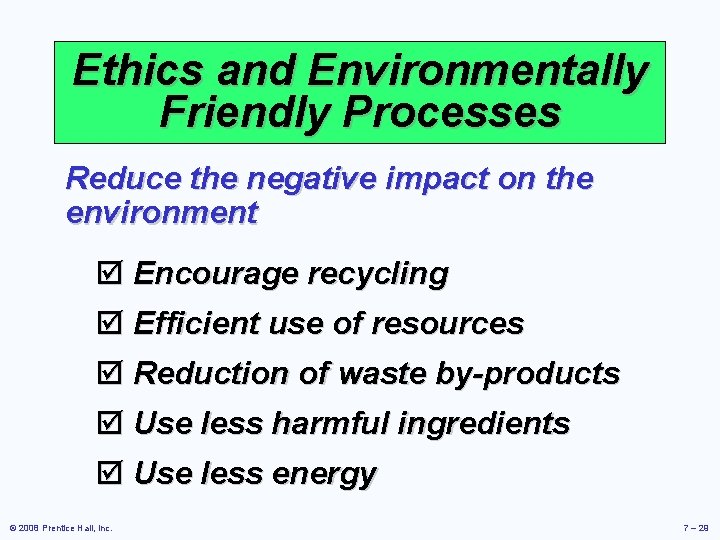
Ethics and Environmentally Friendly Processes Reduce the negative impact on the environment þ Encourage recycling þ Efficient use of resources þ Reduction of waste by-products þ Use less harmful ingredients þ Use less energy © 2008 Prentice Hall, Inc. 7 – 29