NCSX TOROIDAL FIELD COIL DESIGN M KALISH L
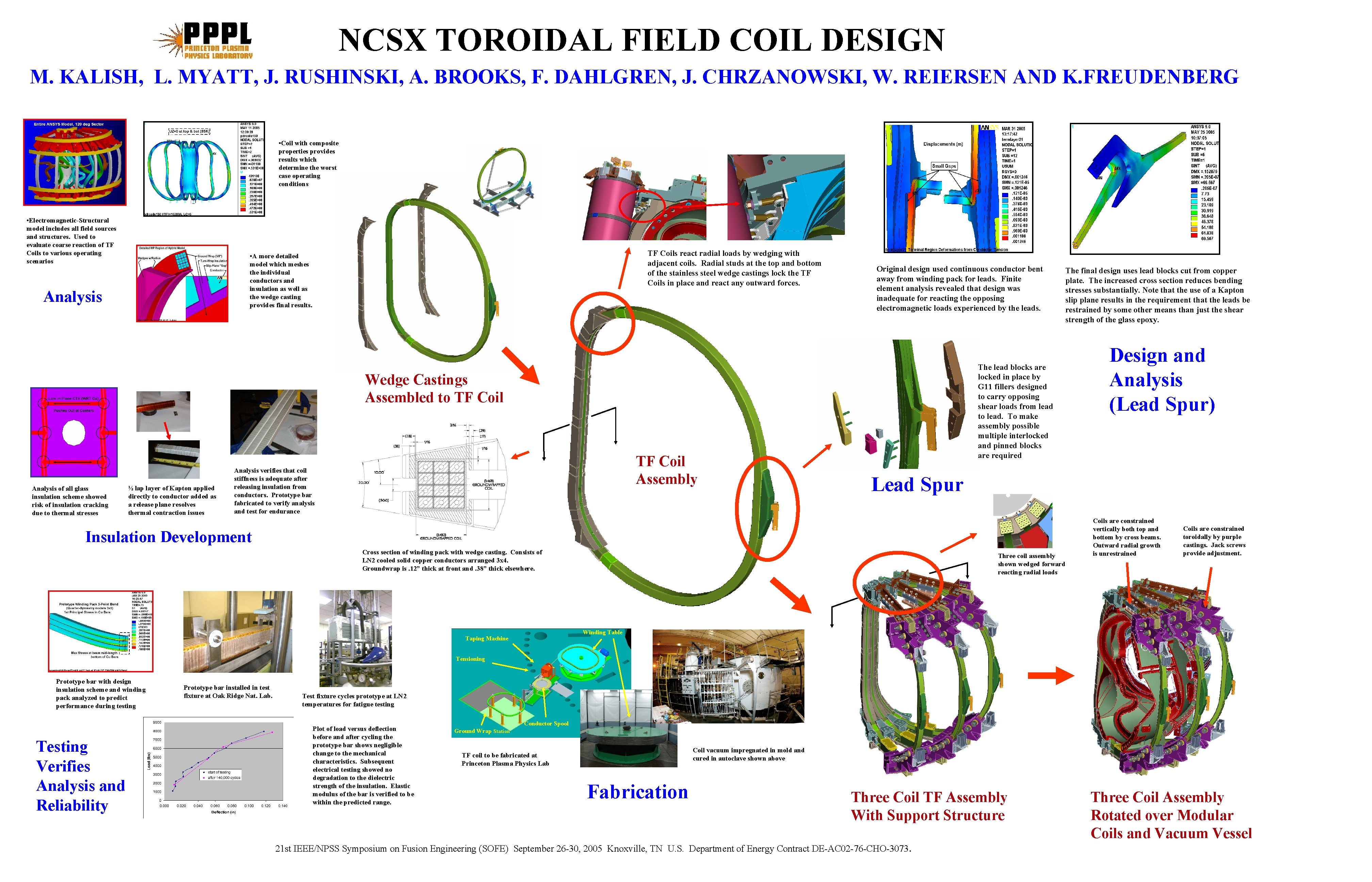
- Slides: 1
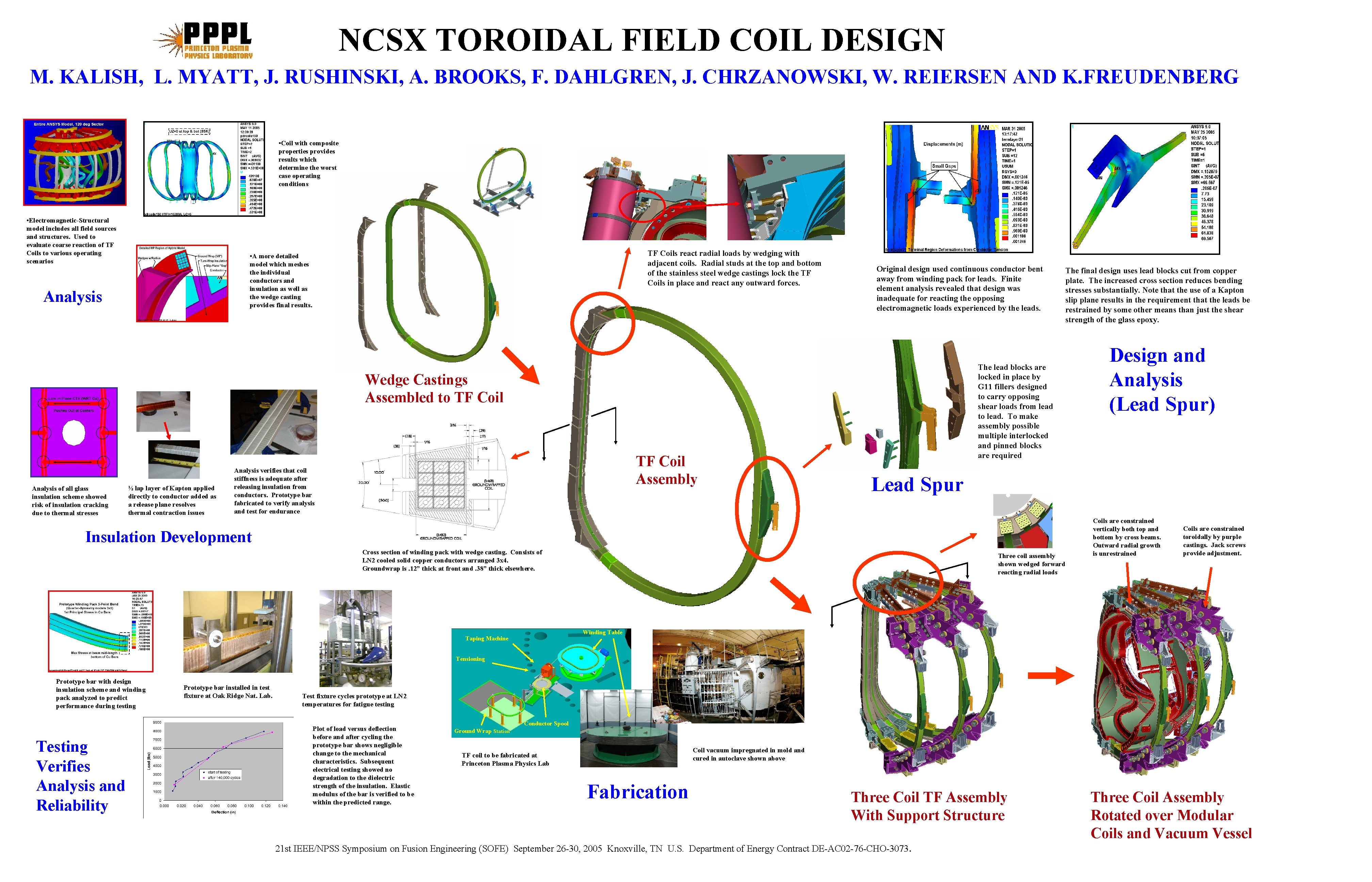
NCSX TOROIDAL FIELD COIL DESIGN M. KALISH, L. MYATT, J. RUSHINSKI, A. BROOKS, F. DAHLGREN, J. CHRZANOWSKI, W. REIERSEN AND K. FREUDENBERG • Coil with composite properties provides results which determine the worst case operating conditions • Electromagnetic-Structural model includes all field sources and structures. Used to evaluate coarse reaction of TF Coils to various operating scenarios TF Coils react radial loads by wedging with adjacent coils. Radial studs at the top and bottom of the stainless steel wedge castings lock the TF Coils in place and react any outward forces. • A more detailed model which meshes the individual conductors and insulation as well as the wedge casting provides final results. Analysis Original design used continuous conductor bent away from winding pack for leads. Finite element analysis revealed that design was inadequate for reacting the opposing electromagnetic loads experienced by the leads. The lead blocks are locked in place by G 11 fillers designed to carry opposing shear loads from lead to lead. To make assembly possible multiple interlocked and pinned blocks are required Wedge Castings Assembled to TF Coil Analysis of all glass insulation scheme showed risk of insulation cracking due to thermal stresses ½ lap layer of Kapton applied directly to conductor added as a release plane resolves thermal contraction issues TF Coil Assembly Analysis verifies that coil stiffness is adequate after releasing insulation from conductors. Prototype bar fabricated to verify analysis and test for endurance The final design uses lead blocks cut from copper plate. The increased cross section reduces bending stresses substantially. Note that the use of a Kapton slip plane results in the requirement that the leads be restrained by some other means than just the shear strength of the glass epoxy. Design and Analysis (Lead Spur) Lead Spur Insulation Development Cross section of winding pack with wedge casting. Consists of LN 2 cooled solid copper conductors arranged 3 x 4. Groundwrap is. 12” thick at front and. 38” thick elsewhere. Three coil assembly shown wedged forward reacting radial loads Coils are constrained vertically both top and bottom by cross beams. Outward radial growth is unrestrained Coils are constrained toroidally by purple castings. Jack screws provide adjustment. Winding Table Taping Machine Tensioning Prototype bar with design insulation scheme and winding pack analyzed to predict performance during testing Testing Verifies Analysis and Reliability Prototype bar installed in test fixture at Oak Ridge Nat. Lab. Test fixture cycles prototype at LN 2 temperatures for fatigue testing Plot of load versus deflection before and after cycling the prototype bar shows negligible change to the mechanical characteristics. Subsequent electrical testing showed no degradation to the dielectric strength of the insulation. Elastic modulus of the bar is verified to be within the predicted range. Conductor Spool Ground Wrap Station Coil vacuum impregnated in mold and cured in autoclave shown above TF coil to be fabricated at Princeton Plasma Physics Lab Fabrication Three Coil TF Assembly With Support Structure 21 st IEEE/NPSS Symposium on Fusion Engineering (SOFE) September 26 -30, 2005 Knoxville, TN U. S. Department of Energy Contract DE-AC 02 -76 -CHO-3073. Three Coil Assembly Rotated over Modular Coils and Vacuum Vessel