Modernization of the mechanical presses Solution Partner Customer
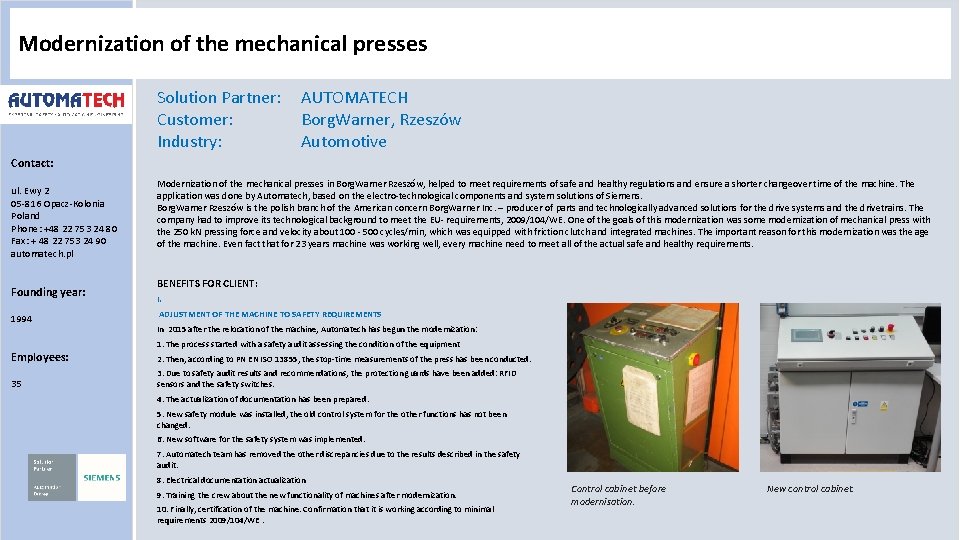
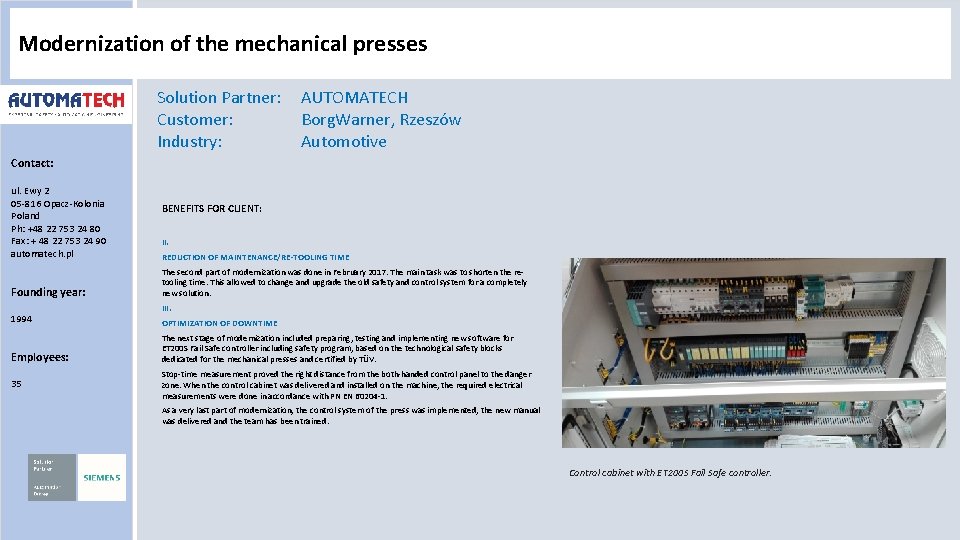
- Slides: 2
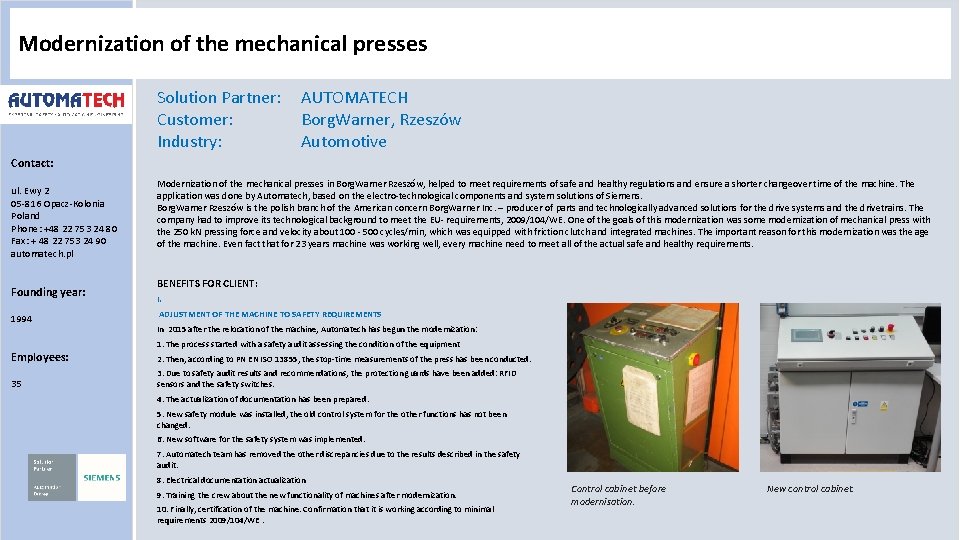
Modernization of the mechanical presses Solution Partner: Customer: Industry: AUTOMATECH Borg. Warner, Rzeszów Automotive Contact: ul. Ewy 2 05 -816 Opacz-Kolonia Poland Phone: +48 22 753 24 80 Fax: + 48 22 753 24 90 automatech. pl Founding year: 1994 Modernization of the mechanical presses in Borg. Warner Rzeszów, helped to meet requirements of safe and healthy regulations and ensure a shorter changeover time of the machine. The application was done by Automatech, based on the electro-technological components and system solutions of Siemens. Borg. Warner Rzeszów is the polish branch of the American concern Borg. Warner Inc. – producer of parts and technologically advanced solutions for the drive systems and the drivetrains. The company had to improve its technological background to meet the EU- requirements, 2009/104/WE. One of the goals of this modernization was some modernization of mechanical press with the 250 k. N pressing force and velocity about 100 - 500 cycles/min, which was equipped with friction clutch and integrated machines. The important reason for this modernization was the age of the machine. Even fact that for 23 years machine was working well, every machine need to meet all of the actual safe and healthy requirements. BENEFITS FOR CLIENT: I. ADJUSTMENT OF THE MACHINE TO SAFETY REQUIREMENTS In 2015 after the relocation of the machine, Automatech has begun the modernization: 1. The process started with a safety audit assessing the condition of the equipment Employees: 2. Then, according to PN EN ISO 13855, the stop-time measurements of the press has been conducted. 35 3. Due to safety audit results and recommendations, the protection guards have been added: RFID sensors and the safety switches. 4. The actualization of documentation has been prepared. 5. New safety module was installed, the old control system for the other functions has not been changed. 6. New software for the safety system was implemented. 7. Automatech team has removed the other discrepancies due to the results described in the safety audit. 8. Electrical documentation actualization 9. Training the crew about the new functionality of machines after modernization. 10. Finally, certification of the machine. Confirmation that it is working according to minimal requirements 2009/104/WE. Control cabinet before modernisation. New control cabinet.
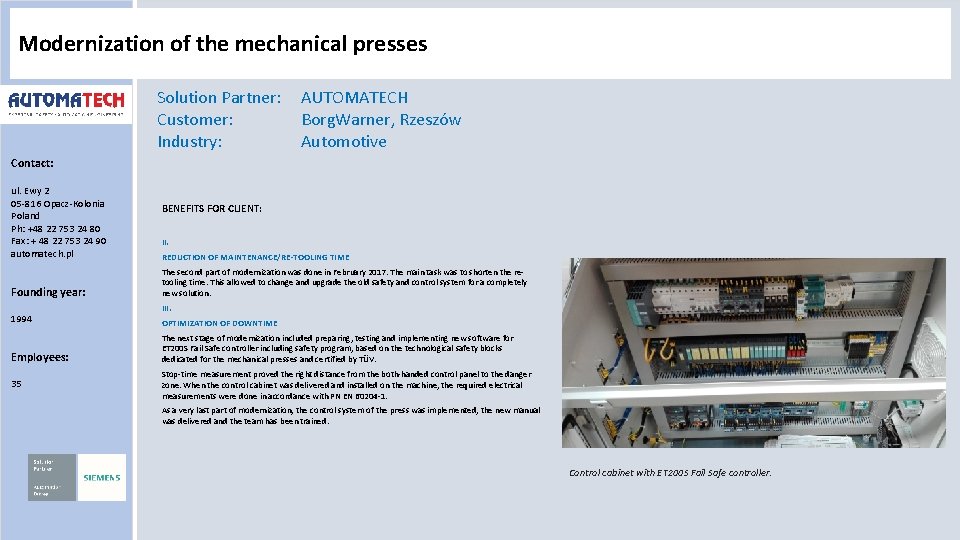
Modernization of the mechanical presses Solution Partner: Customer: Industry: AUTOMATECH Borg. Warner, Rzeszów Automotive Contact: ul. Ewy 2 05 -816 Opacz-Kolonia Poland Ph: +48 22 753 24 80 Fax: + 48 22 753 24 90 automatech. pl Founding year: 1994 Employees: 35 BENEFITS FOR CLIENT: II. REDUCTION OF MAINTENANCE/RE-TOOLING TIME The second part of modernization was done in February 2017. The main task was to shorten the retooling time. This allowed to change and upgrade the old safety and control system for a completely new solution. III. OPTIMIZATION OF DOWNTIME The next stage of modernization included preparing, testing and implementing new software for ET 200 S Fail Safe controller including safety program, based on the technological safety blocks dedicated for the mechanical presses and certified by TÜV. Stop-time measurement proved the right distance from the both-handed control panel to the danger zone. When the control cabinet was delivered and installed on the machine, the required electrical measurements were done in accordance with PN EN 60204 -1. As a very last part of modernization, the control system of the press was implemented, the new manual was delivered and the team has been trained. Control cabinet with ET 200 S Fail Safe controller.