Mgr in Krystian Nowak Dr in Monika Grska
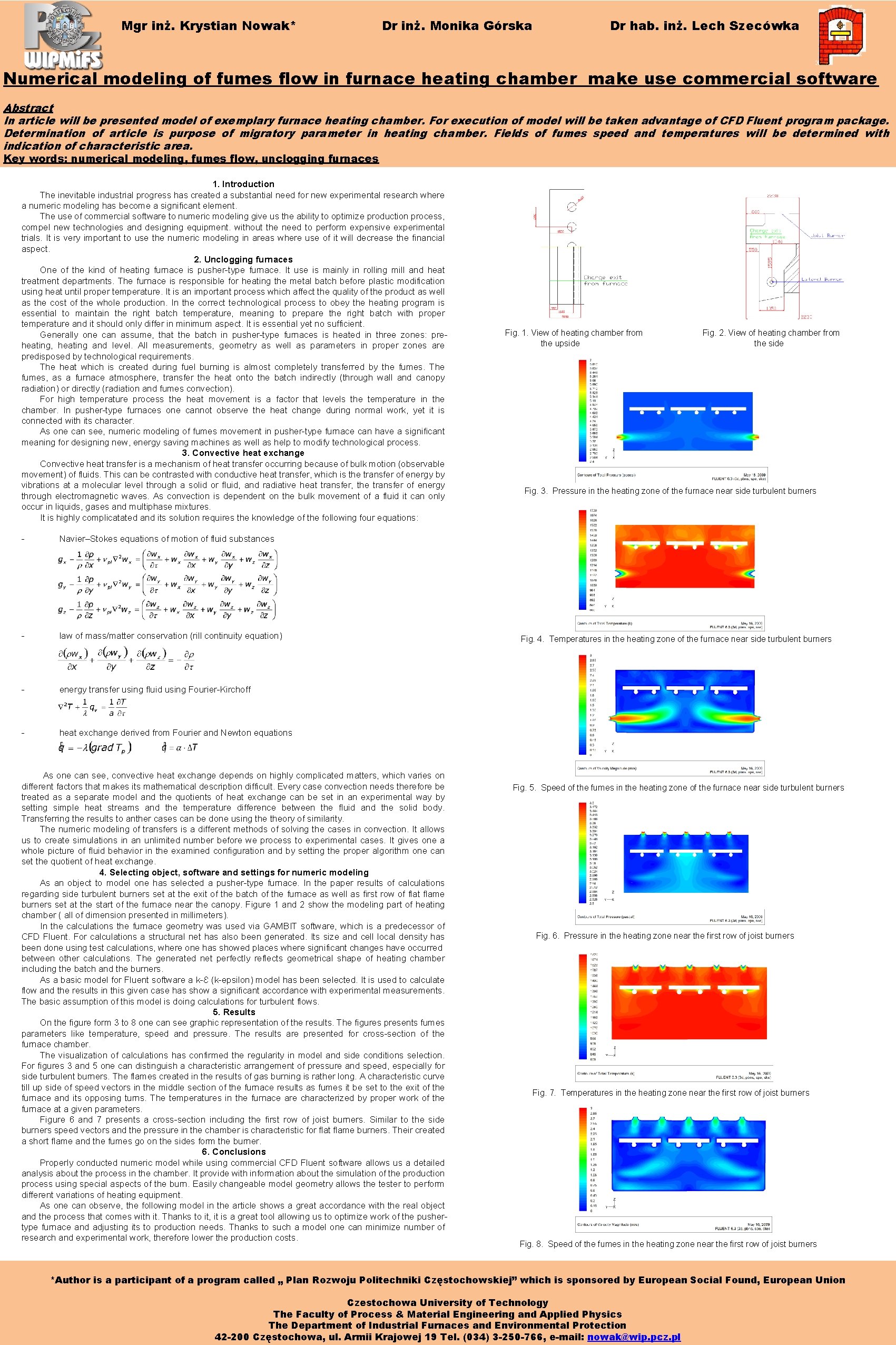
- Slides: 1
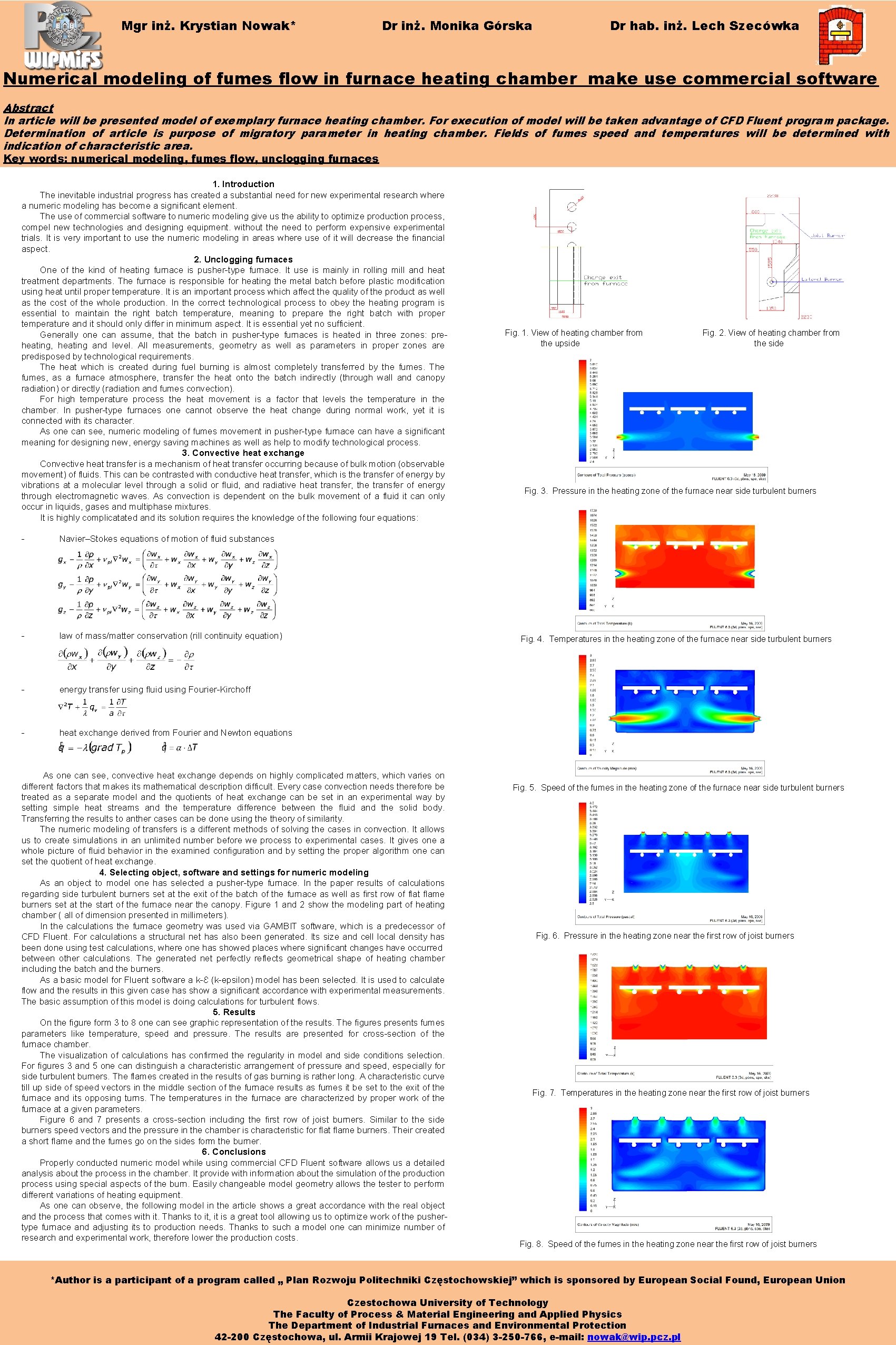
Mgr inż. Krystian Nowak* Dr inż. Monika Górska Dr hab. inż. Lech Szecówka Numerical modeling of fumes flow in furnace heating chamber make use commercial software Abstract In article will be presented model of exemplary furnace heating chamber. For execution of model will be taken advantage of CFD Fluent program package. Determination of article is purpose of migratory parameter in heating chamber. Fields of fumes speed and temperatures will be determined with indication of characteristic area. Key words: numerical modeling, fumes flow, unclogging furnaces 1. Introduction The inevitable industrial progress has created a substantial need for new experimental research where a numeric modeling has become a significant element. The use of commercial software to numeric modeling give us the ability to optimize production process, compel new technologies and designing equipment. without the need to perform expensive experimental trials. It is very important to use the numeric modeling in areas where use of it will decrease the financial aspect. 2. Unclogging furnaces One of the kind of heating furnace is pusher-type furnace. It use is mainly in rolling mill and heat treatment departments. The furnace is responsible for heating the metal batch before plastic modification using heat until proper temperature. It is an important process which affect the quality of the product as well as the cost of the whole production. In the correct technological process to obey the heating program is essential to maintain the right batch temperature, meaning to prepare the right batch with proper temperature and it should only differ in minimum aspect. It is essential yet no sufficient. Generally one can assume, that the batch in pusher-type furnaces is heated in three zones: preheating, heating and level. All measurements, geometry as well as parameters in proper zones are predisposed by technological requirements. The heat which is created during fuel burning is almost completely transferred by the fumes. The fumes, as a furnace atmosphere, transfer the heat onto the batch indirectly (through wall and canopy radiation) or directly (radiation and fumes convection). For high temperature process the heat movement is a factor that levels the temperature in the chamber. In pusher-type furnaces one cannot observe the heat change during normal work, yet it is connected with its character. As one can see, numeric modeling of fumes movement in pusher-type furnace can have a significant meaning for designing new, energy saving machines as well as help to modify technological process. 3. Convective heat exchange Convective heat transfer is a mechanism of heat transfer occurring because of bulk motion (observable movement) of fluids. This can be contrasted with conductive heat transfer, which is the transfer of energy by vibrations at a molecular level through a solid or fluid, and radiative heat transfer, the transfer of energy through electromagnetic waves. As convection is dependent on the bulk movement of a fluid it can only occur in liquids, gases and multiphase mixtures. It is highly complicatated and its solution requires the knowledge of the following four equations: - Navier–Stokes equations of motion of fluid substances - law of mass/matter conservation (rill continuity equation) - energy transfer using fluid using Fourier-Kirchoff - heat exchange derived from Fourier and Newton equations As one can see, convective heat exchange depends on highly complicated matters, which varies on different factors that makes its mathematical description difficult. Every case convection needs therefore be treated as a separate model and the quotients of heat exchange can be set in an experimental way by setting simple heat streams and the temperature difference between the fluid and the solid body. Transferring the results to anther cases can be done using theory of similarity. The numeric modeling of transfers is a different methods of solving the cases in convection. It allows us to create simulations in an unlimited number before we process to experimental cases. It gives one a whole picture of fluid behavior in the examined configuration and by setting the proper algorithm one can set the quotient of heat exchange. 4. Selecting object, software and settings for numeric modeling As an object to model one has selected a pusher-type furnace. In the paper results of calculations regarding side turbulent burners set at the exit of the batch of the furnace as well as first row of flat flame burners set at the start of the furnace near the canopy. Figure 1 and 2 show the modeling part of heating chamber ( all of dimension presented in millimeters). In the calculations the furnace geometry was used via GAMBIT software, which is a predecessor of CFD Fluent. For calculations a structural net has also been generated. Its size and cell local density has been done using test calculations, where one has showed places where significant changes have occurred between other calculations. The generated net perfectly reflects geometrical shape of heating chamber including the batch and the burners. As a basic model for Fluent software a k-Ɛ (k-epsilon) model has been selected. It is used to calculate flow and the results in this given case has show a significant accordance with experimental measurements. The basic assumption of this model is doing calculations for turbulent flows. 5. Results On the figure form 3 to 8 one can see graphic representation of the results. The figures presents fumes parameters like temperature, speed and pressure. The results are presented for cross-section of the furnace chamber. The visualization of calculations has confirmed the regularity in model and side conditions selection. For figures 3 and 5 one can distinguish a characteristic arrangement of pressure and speed, especially for side turbulent burners. The flames created in the results of gas burning is rather long. A characteristic curve till up side of speed vectors in the middle section of the furnace results as fumes it be set to the exit of the furnace and its opposing turns. The temperatures in the furnace are characterized by proper work of the furnace at a given parameters. Figure 6 and 7 presents a cross-section including the first row of joist burners. Similar to the side burners speed vectors and the pressure in the chamber is characteristic for flat flame burners. Their created a short flame and the fumes go on the sides form the burner. 6. Conclusions Properly conducted numeric model while using commercial CFD Fluent software allows us a detailed analysis about the process in the chamber. It provide with information about the simulation of the production process using special aspects of the burn. Easily changeable model geometry allows the tester to perform different variations of heating equipment. As one can observe, the following model in the article shows a great accordance with the real object and the process that comes with it. Thanks to it, it is a great tool allowing us to optimize work of the pushertype furnace and adjusting its to production needs. Thanks to such a model one can minimize number of research and experimental work, therefore lower the production costs. Fig. 1. View of heating chamber from the upside Fig. 2. View of heating chamber from the side Fig. 3. Pressure in the heating zone of the furnace near side turbulent burners Fig. 4. Temperatures in the heating zone of the furnace near side turbulent burners Fig. 5. Speed of the fumes in the heating zone of the furnace near side turbulent burners Fig. 6. Pressure in the heating zone near the first row of joist burners Fig. 7. Temperatures in the heating zone near the first row of joist burners Fig. 8. Speed of the fumes in the heating zone near the first row of joist burners *Author is a participant of a program called „ Plan Rozwoju Politechniki Częstochowskiej” which is sponsored by European Social Found, European Union Czestochowa University of Technology The Faculty of Process & Material Engineering and Applied Physics The Department of Industrial Furnaces and Environmental Protection 42 -200 Częstochowa, ul. Armii Krajowej 19 Tel. (034) 3 -250 -766, e-mail: nowak@wip. pcz. pl