ME 485 Heat Exchanger and Steam Generator Design
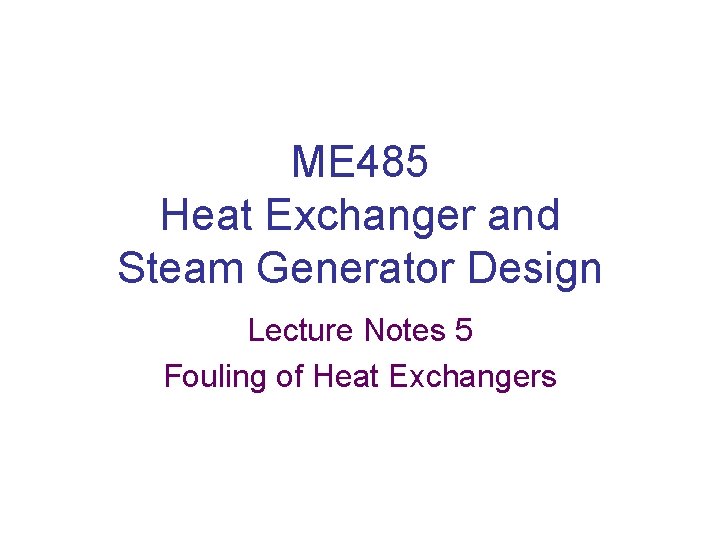
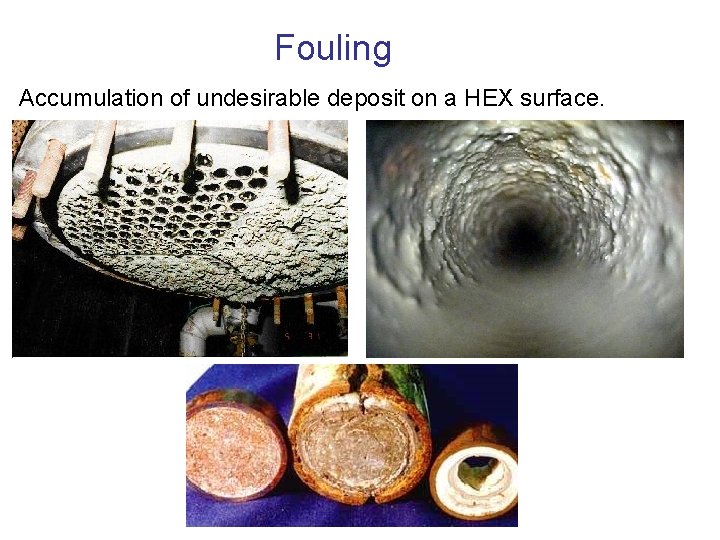
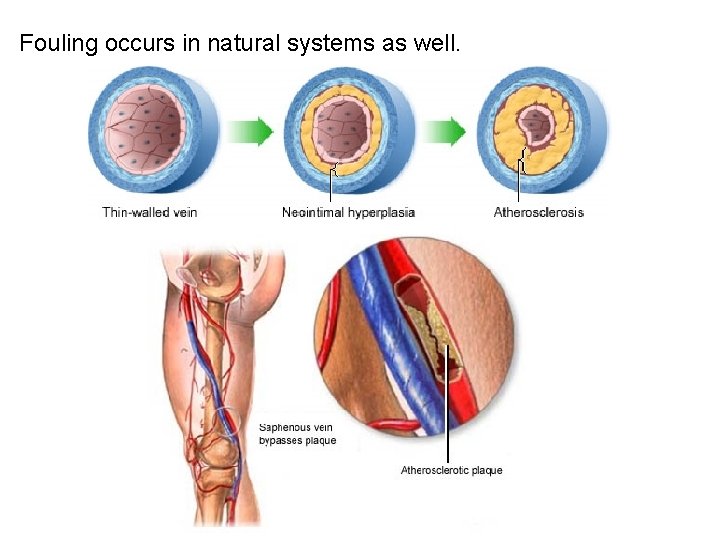
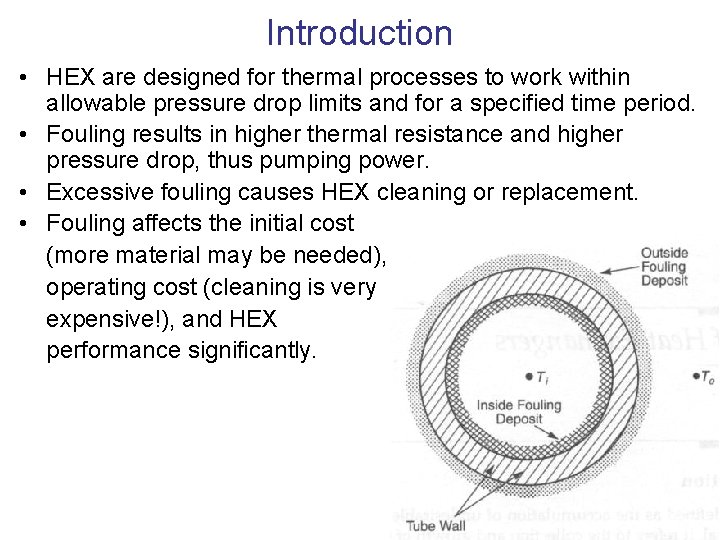
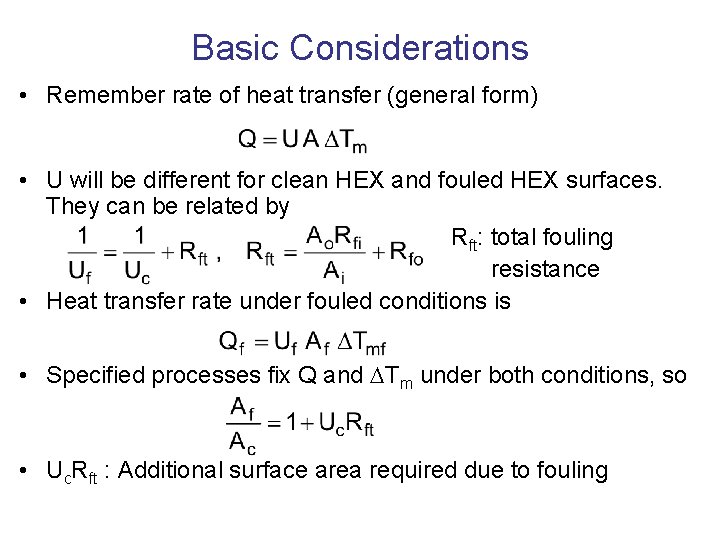
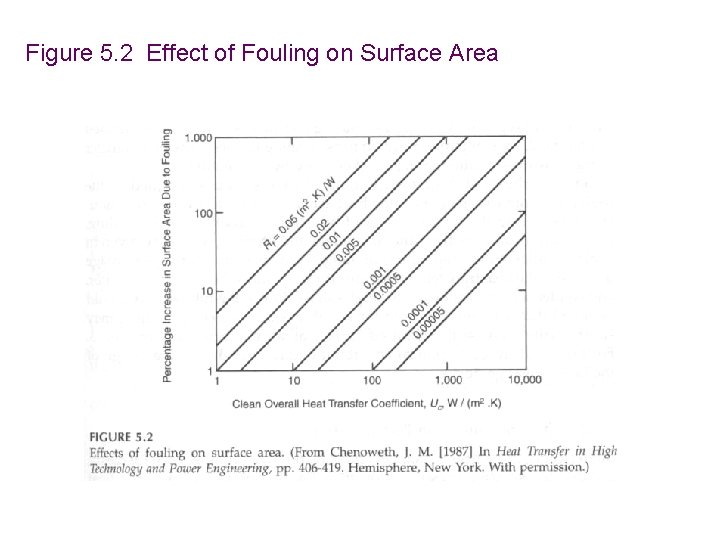
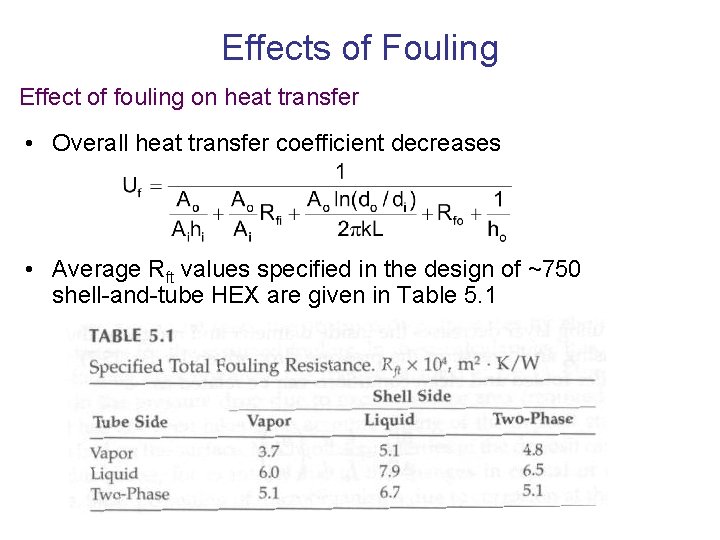
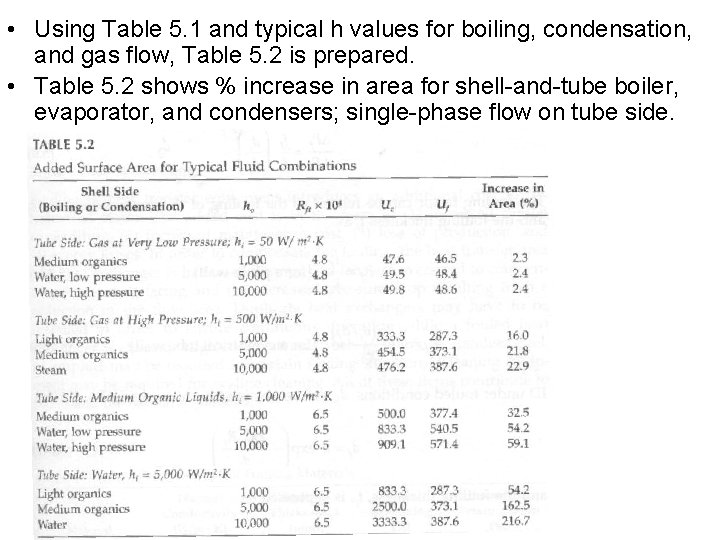
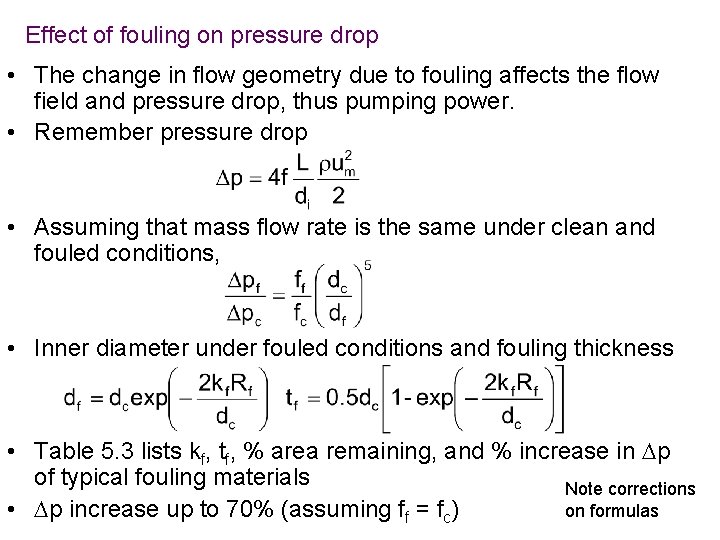
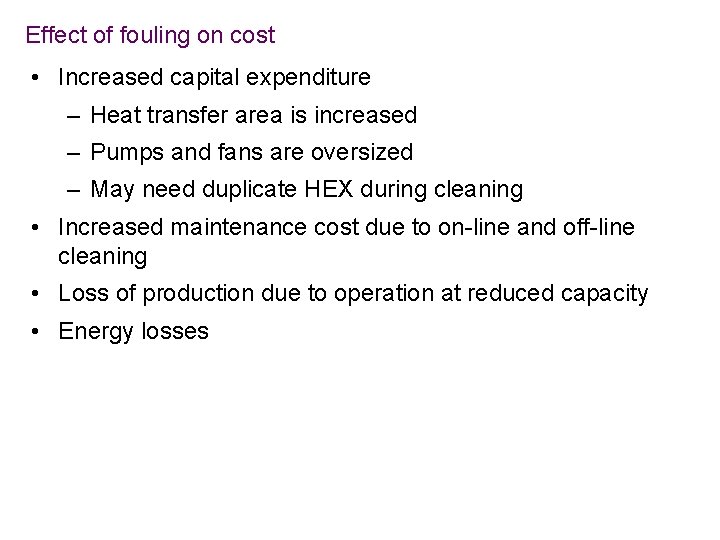
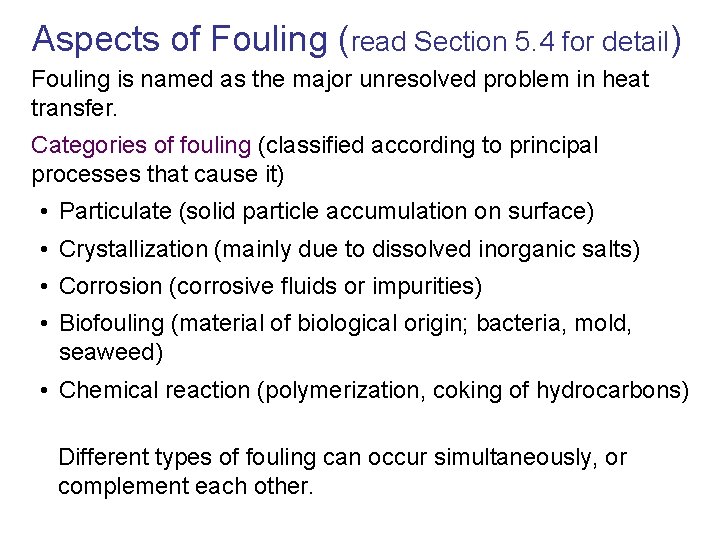
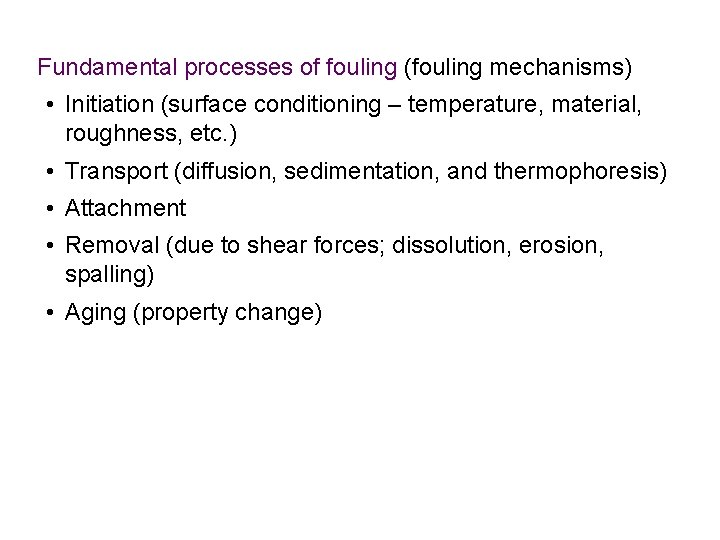
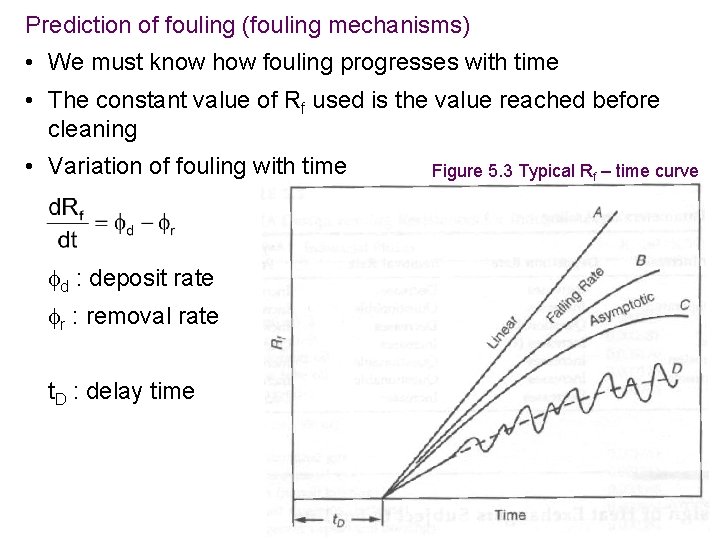
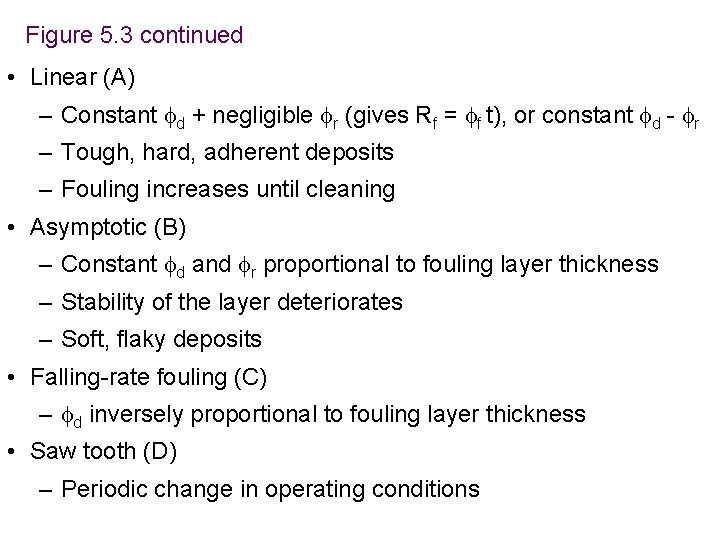
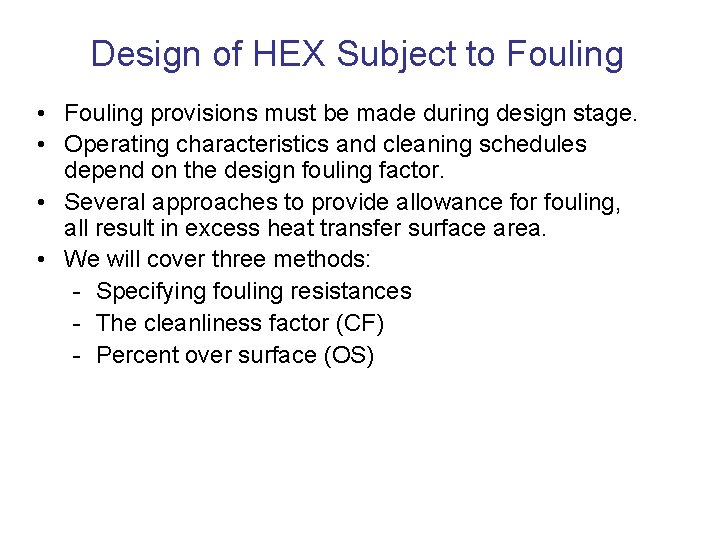
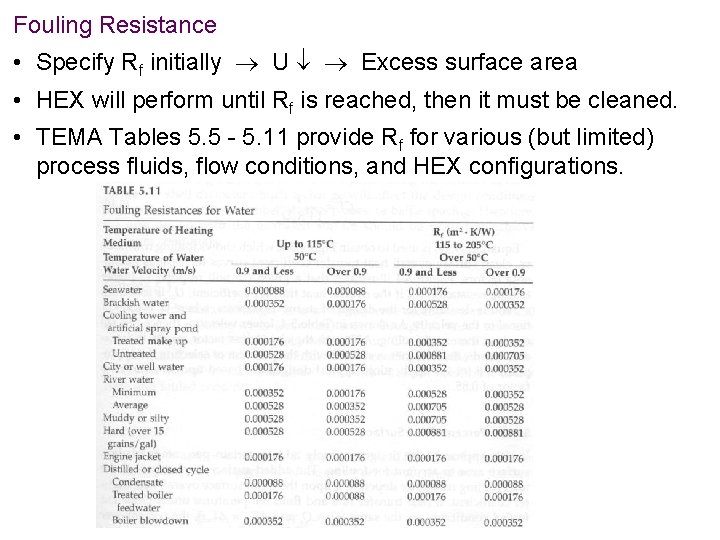
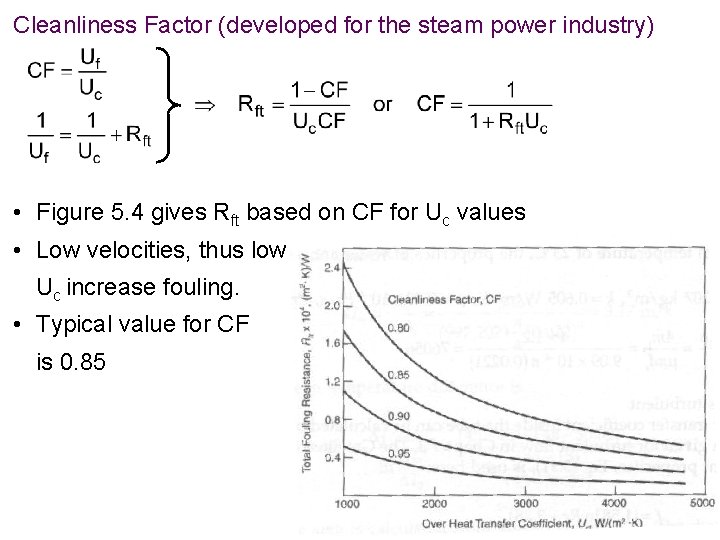
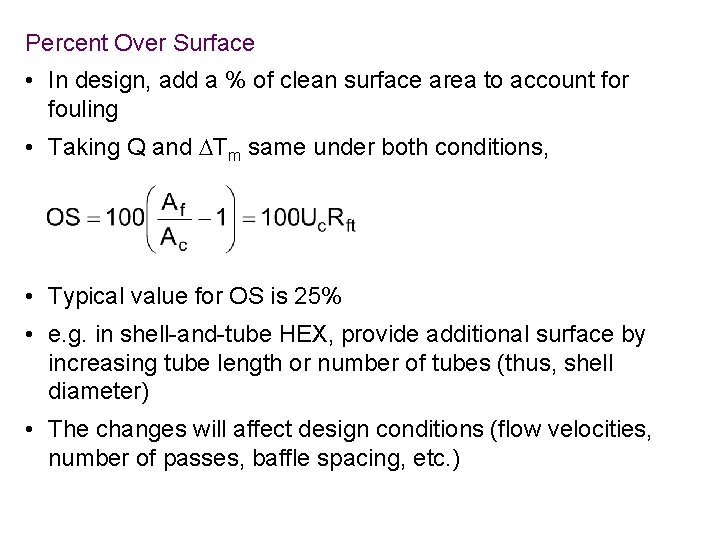
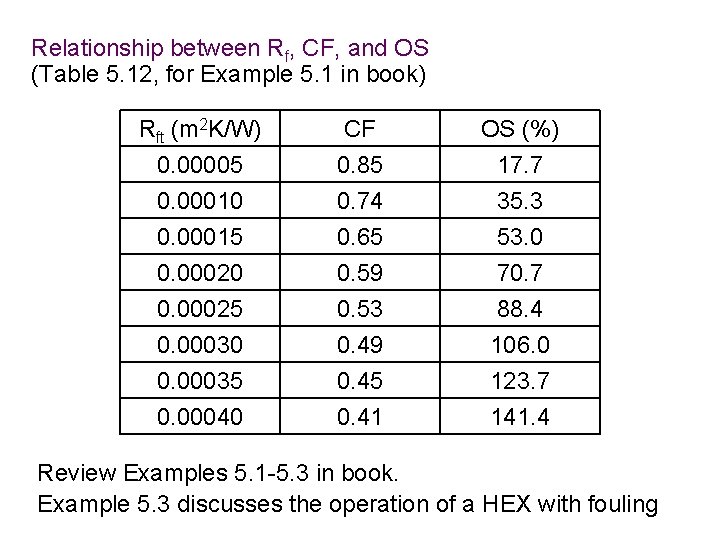
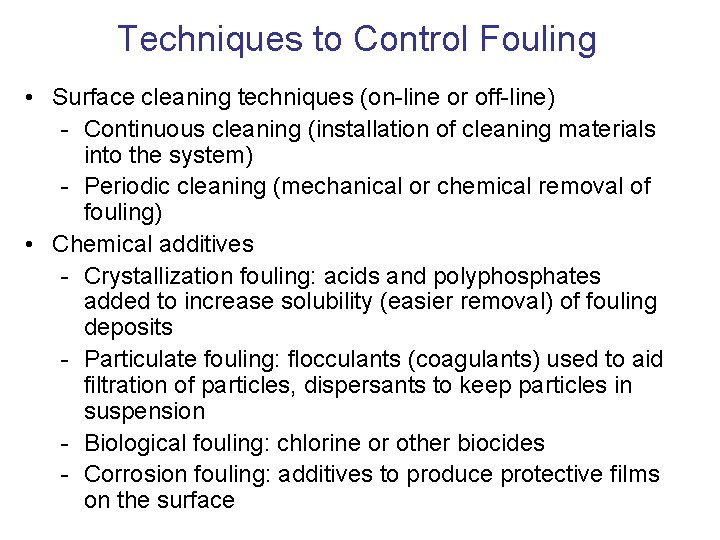
- Slides: 20
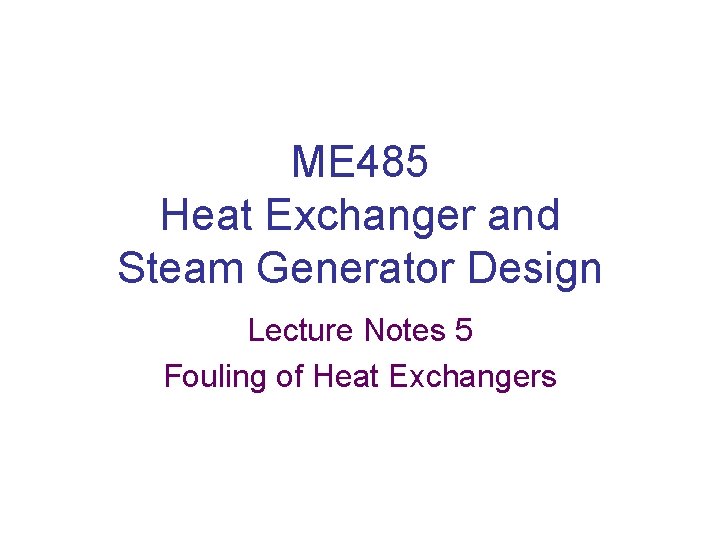
ME 485 Heat Exchanger and Steam Generator Design Lecture Notes 5 Fouling of Heat Exchangers
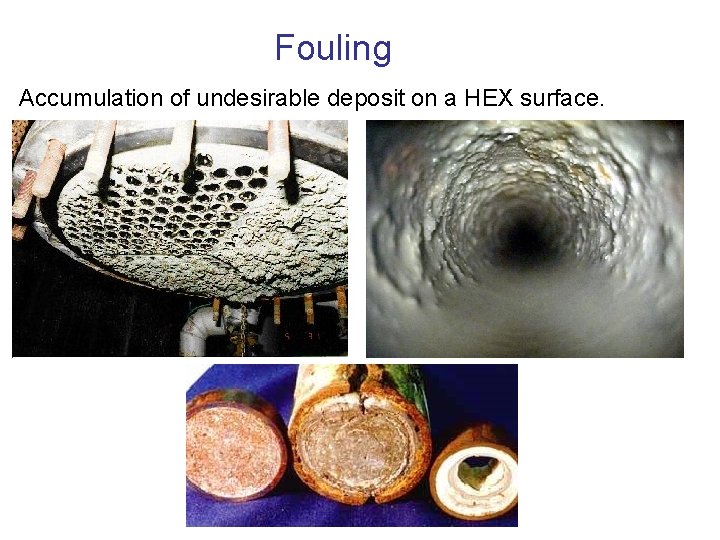
Fouling Accumulation of undesirable deposit on a HEX surface.
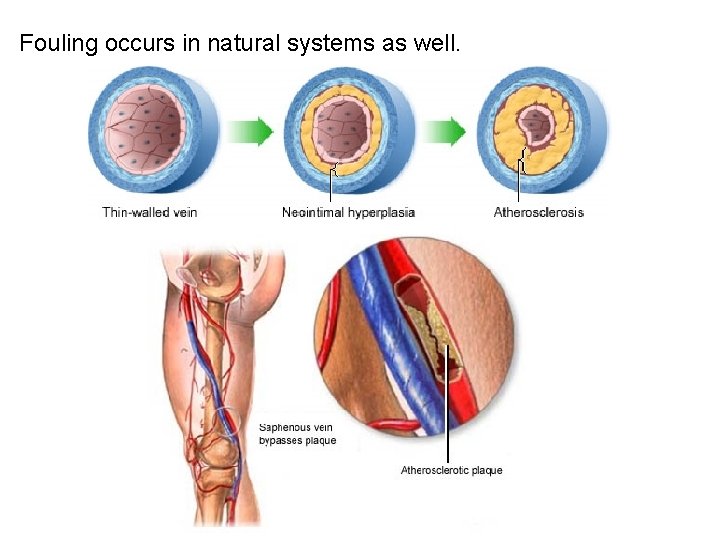
Fouling occurs in natural systems as well.
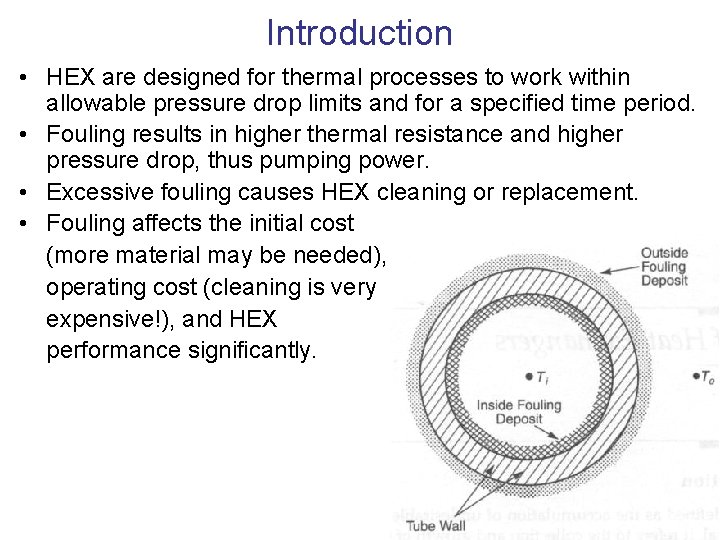
Introduction • HEX are designed for thermal processes to work within allowable pressure drop limits and for a specified time period. • Fouling results in higher thermal resistance and higher pressure drop, thus pumping power. • Excessive fouling causes HEX cleaning or replacement. • Fouling affects the initial cost (more material may be needed), operating cost (cleaning is very expensive!), and HEX performance significantly.
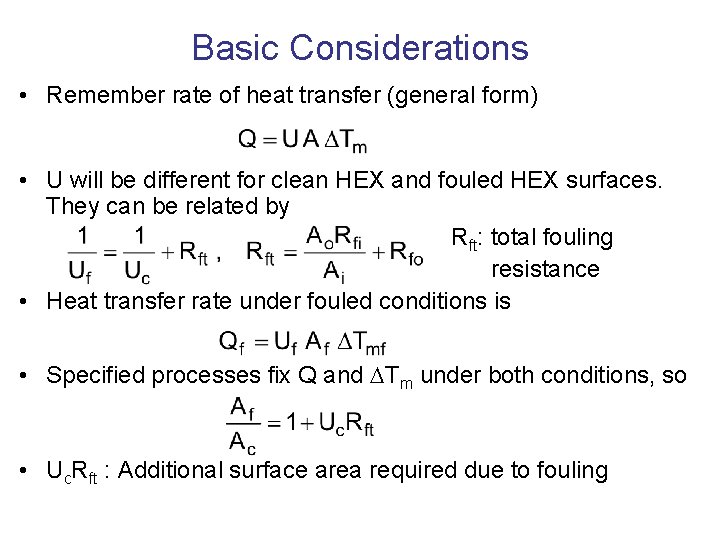
Basic Considerations • Remember rate of heat transfer (general form) • U will be different for clean HEX and fouled HEX surfaces. They can be related by Rft: total fouling resistance • Heat transfer rate under fouled conditions is • Specified processes fix Q and Tm under both conditions, so • Uc. Rft : Additional surface area required due to fouling
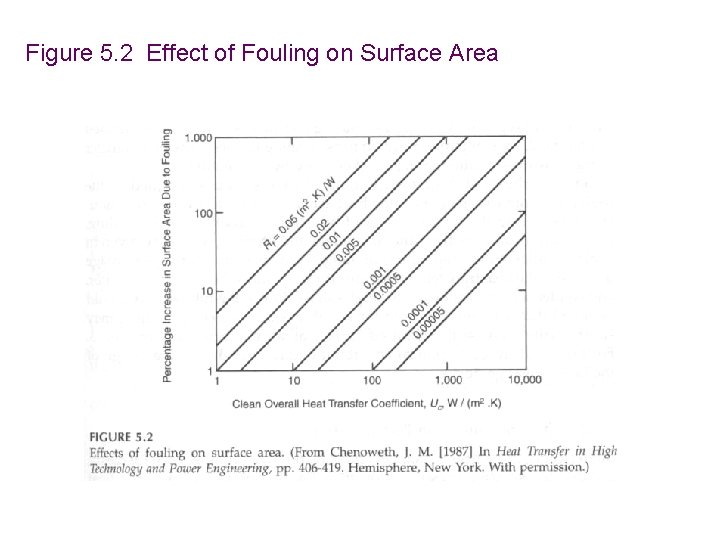
Figure 5. 2 Effect of Fouling on Surface Area
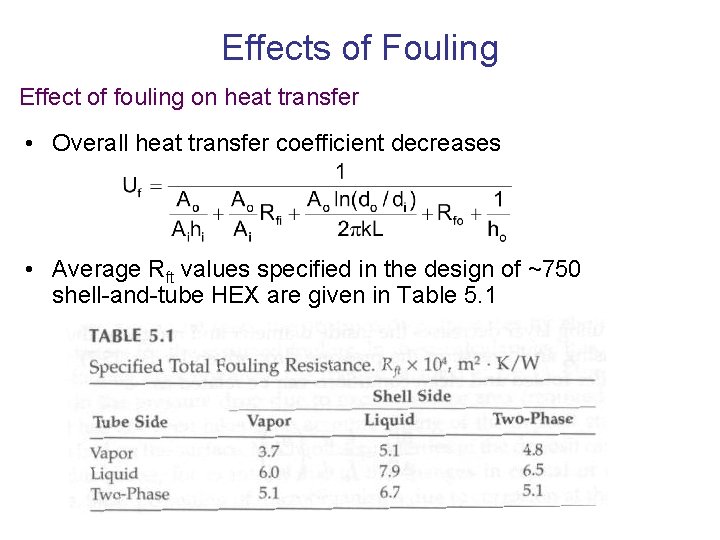
Effects of Fouling Effect of fouling on heat transfer • Overall heat transfer coefficient decreases • Average Rft values specified in the design of ~750 shell-and-tube HEX are given in Table 5. 1
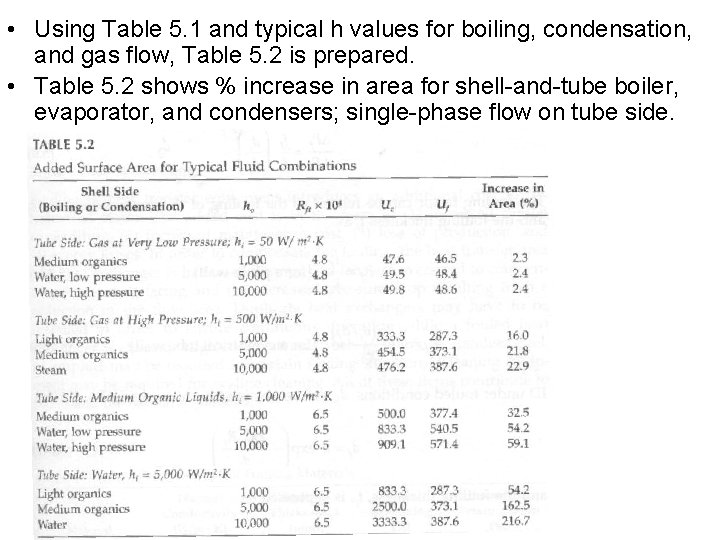
• Using Table 5. 1 and typical h values for boiling, condensation, and gas flow, Table 5. 2 is prepared. • Table 5. 2 shows % increase in area for shell-and-tube boiler, evaporator, and condensers; single-phase flow on tube side.
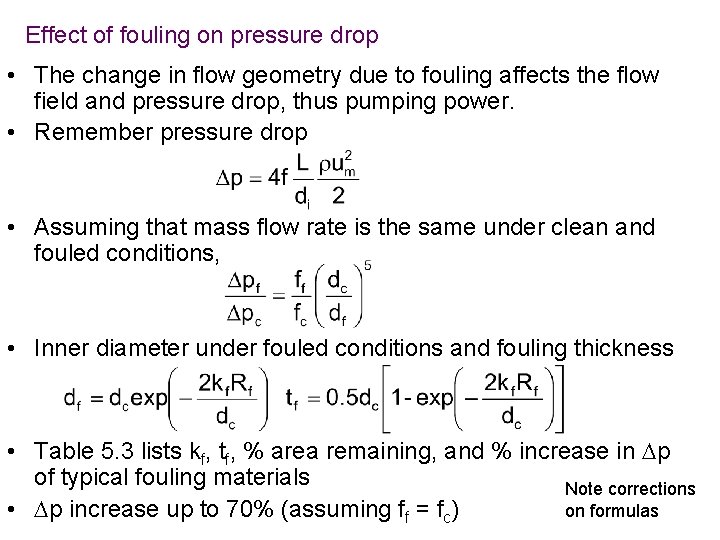
Effect of fouling on pressure drop • The change in flow geometry due to fouling affects the flow field and pressure drop, thus pumping power. • Remember pressure drop • Assuming that mass flow rate is the same under clean and fouled conditions, • Inner diameter under fouled conditions and fouling thickness • Table 5. 3 lists kf, tf, % area remaining, and % increase in p of typical fouling materials Note corrections on formulas • p increase up to 70% (assuming ff = fc)
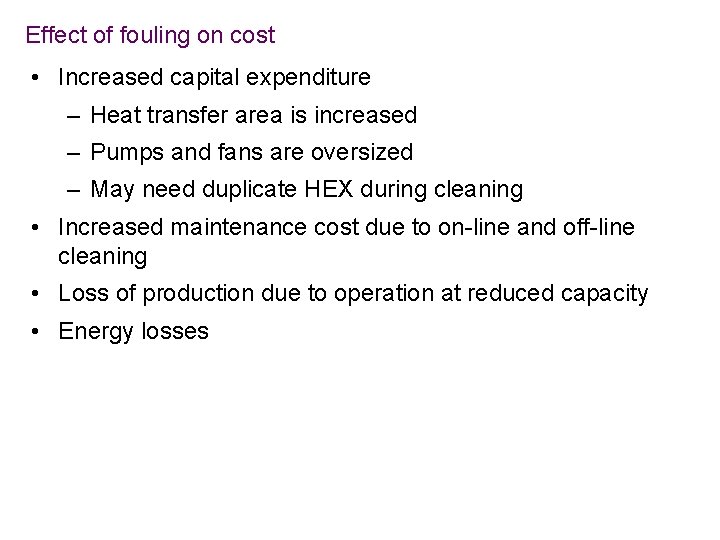
Effect of fouling on cost • Increased capital expenditure – Heat transfer area is increased – Pumps and fans are oversized – May need duplicate HEX during cleaning • Increased maintenance cost due to on-line and off-line cleaning • Loss of production due to operation at reduced capacity • Energy losses
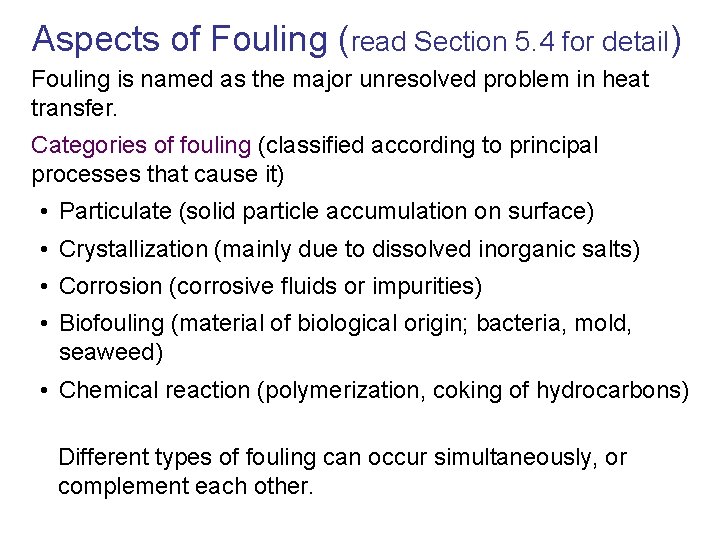
Aspects of Fouling (read Section 5. 4 for detail) Fouling is named as the major unresolved problem in heat transfer. Categories of fouling (classified according to principal processes that cause it) • Particulate (solid particle accumulation on surface) • Crystallization (mainly due to dissolved inorganic salts) • Corrosion (corrosive fluids or impurities) • Biofouling (material of biological origin; bacteria, mold, seaweed) • Chemical reaction (polymerization, coking of hydrocarbons) Different types of fouling can occur simultaneously, or complement each other.
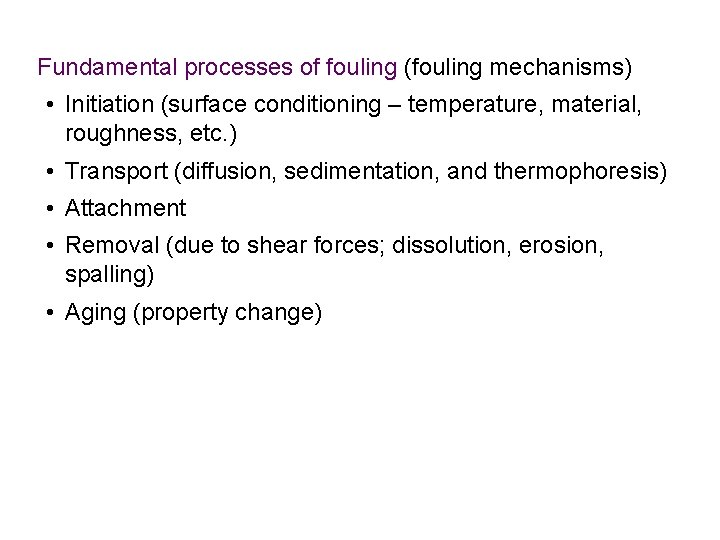
Fundamental processes of fouling (fouling mechanisms) • Initiation (surface conditioning – temperature, material, roughness, etc. ) • Transport (diffusion, sedimentation, and thermophoresis) • Attachment • Removal (due to shear forces; dissolution, erosion, spalling) • Aging (property change)
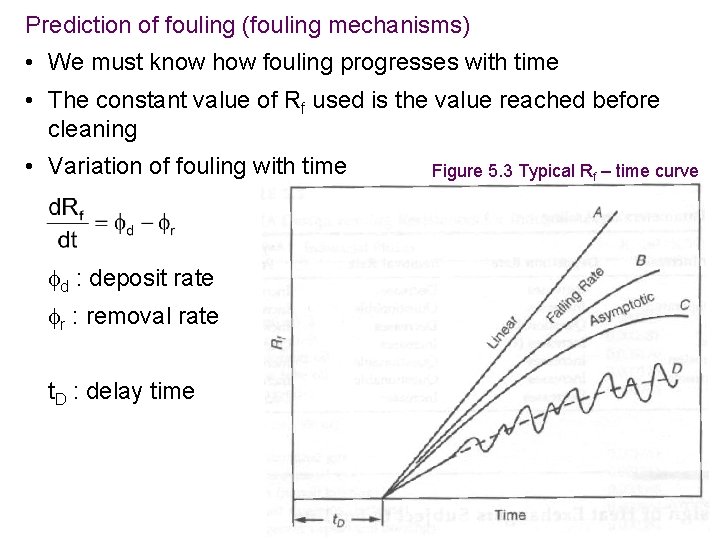
Prediction of fouling (fouling mechanisms) • We must know how fouling progresses with time • The constant value of Rf used is the value reached before cleaning • Variation of fouling with time d : deposit rate r : removal rate t. D : delay time Figure 5. 3 Typical Rf – time curve
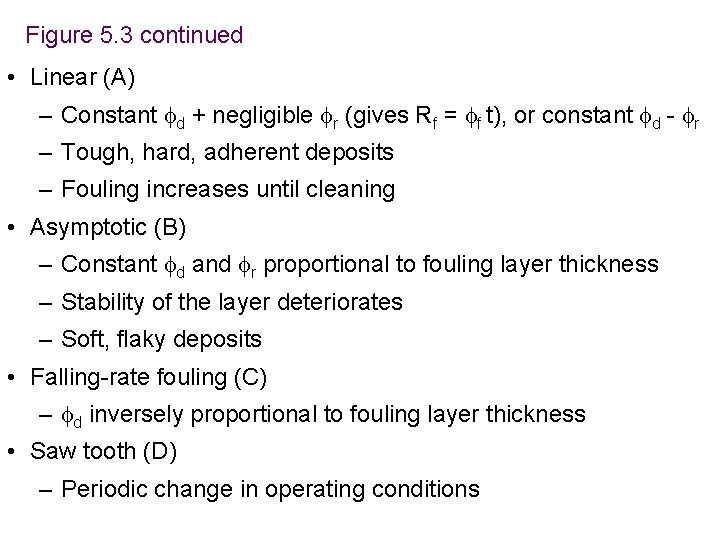
Figure 5. 3 continued • Linear (A) – Constant d + negligible r (gives Rf = f t), or constant d - r – Tough, hard, adherent deposits – Fouling increases until cleaning • Asymptotic (B) – Constant d and r proportional to fouling layer thickness – Stability of the layer deteriorates – Soft, flaky deposits • Falling-rate fouling (C) – d inversely proportional to fouling layer thickness • Saw tooth (D) – Periodic change in operating conditions
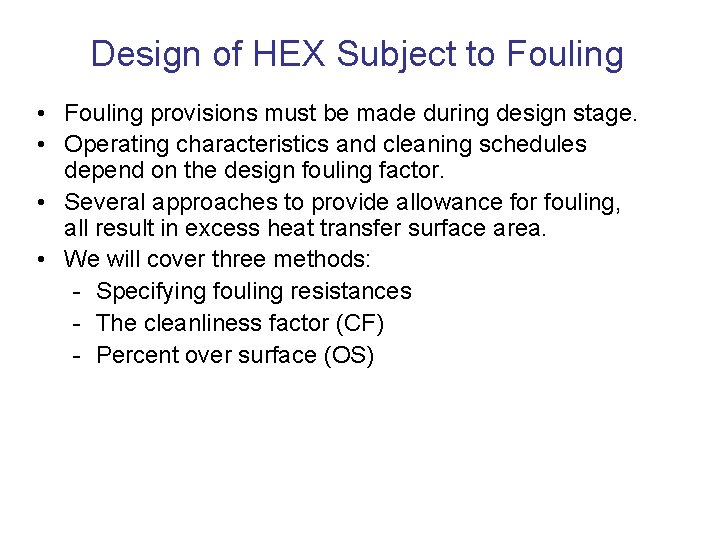
Design of HEX Subject to Fouling • Fouling provisions must be made during design stage. • Operating characteristics and cleaning schedules depend on the design fouling factor. • Several approaches to provide allowance for fouling, all result in excess heat transfer surface area. • We will cover three methods: - Specifying fouling resistances - The cleanliness factor (CF) - Percent over surface (OS)
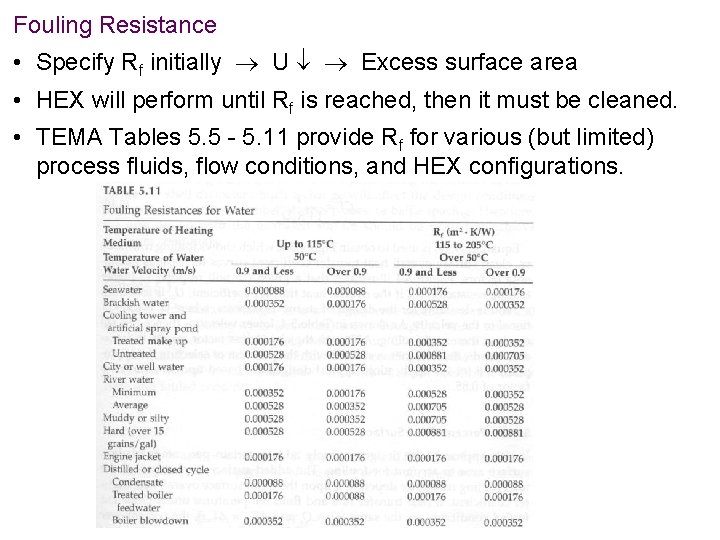
Fouling Resistance • Specify Rf initially U Excess surface area • HEX will perform until Rf is reached, then it must be cleaned. • TEMA Tables 5. 5 - 5. 11 provide Rf for various (but limited) process fluids, flow conditions, and HEX configurations.
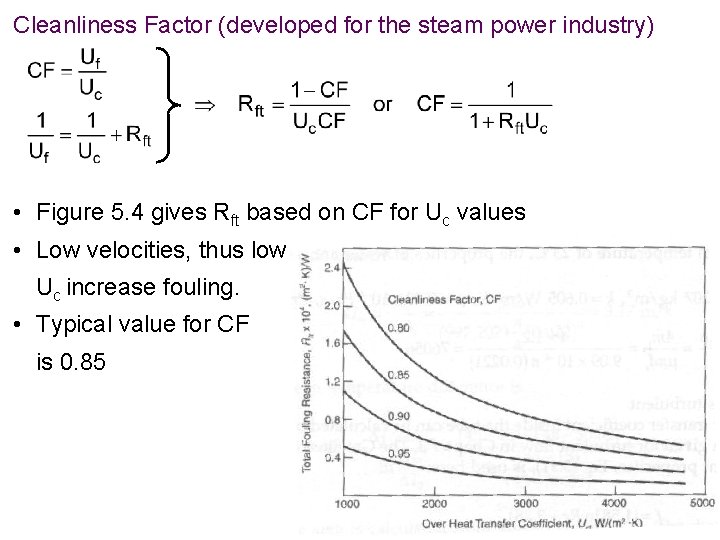
Cleanliness Factor (developed for the steam power industry) • Figure 5. 4 gives Rft based on CF for Uc values • Low velocities, thus low Uc increase fouling. • Typical value for CF is 0. 85
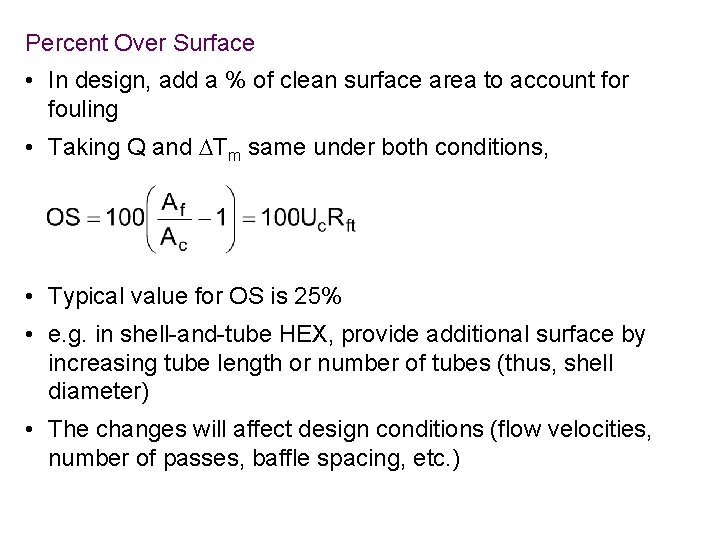
Percent Over Surface • In design, add a % of clean surface area to account for fouling • Taking Q and Tm same under both conditions, • Typical value for OS is 25% • e. g. in shell-and-tube HEX, provide additional surface by increasing tube length or number of tubes (thus, shell diameter) • The changes will affect design conditions (flow velocities, number of passes, baffle spacing, etc. )
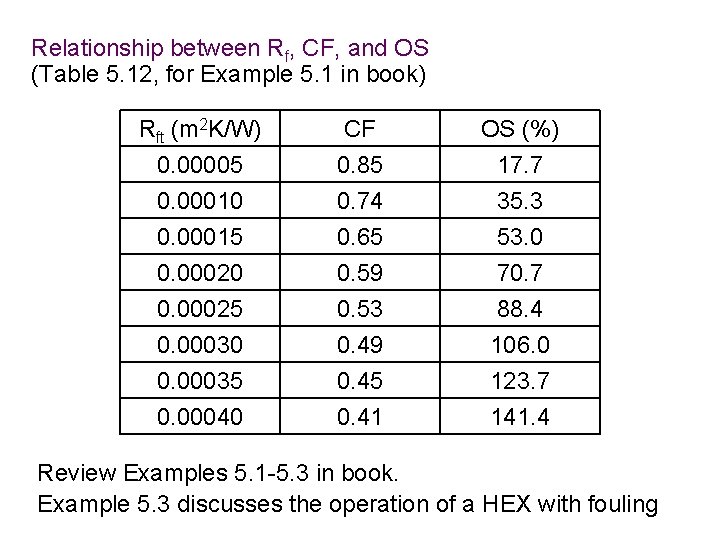
Relationship between Rf, CF, and OS (Table 5. 12, for Example 5. 1 in book) Rft (m 2 K/W) 0. 00005 0. 00010 0. 00015 CF 0. 85 0. 74 0. 65 OS (%) 17. 7 35. 3 53. 0 0. 00025 0. 00030 0. 00035 0. 00040 0. 59 0. 53 0. 49 0. 45 0. 41 70. 7 88. 4 106. 0 123. 7 141. 4 Review Examples 5. 1 -5. 3 in book. Example 5. 3 discusses the operation of a HEX with fouling
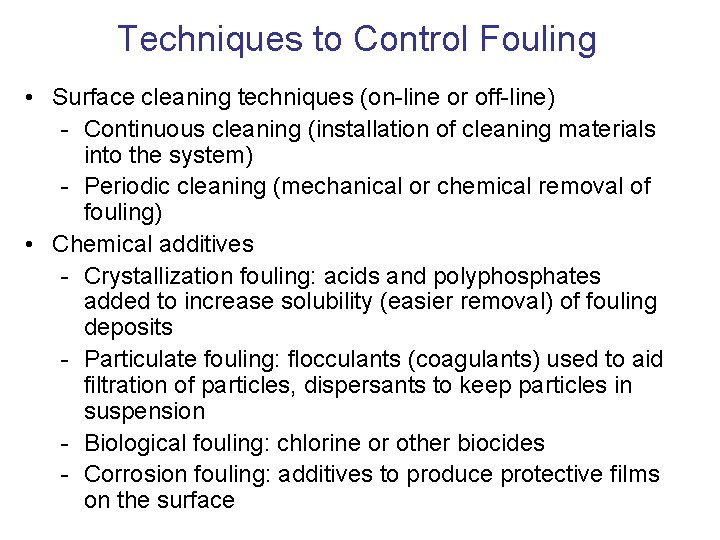
Techniques to Control Fouling • Surface cleaning techniques (on-line or off-line) - Continuous cleaning (installation of cleaning materials into the system) - Periodic cleaning (mechanical or chemical removal of fouling) • Chemical additives - Crystallization fouling: acids and polyphosphates added to increase solubility (easier removal) of fouling deposits - Particulate fouling: flocculants (coagulants) used to aid filtration of particles, dispersants to keep particles in suspension - Biological fouling: chlorine or other biocides - Corrosion fouling: additives to produce protective films on the surface