Logistics Management An Introduction 1 Logistics Definition Logistics
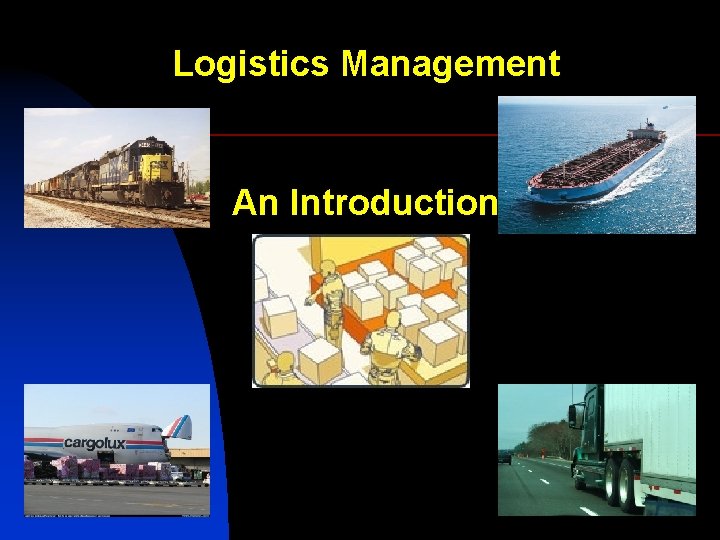
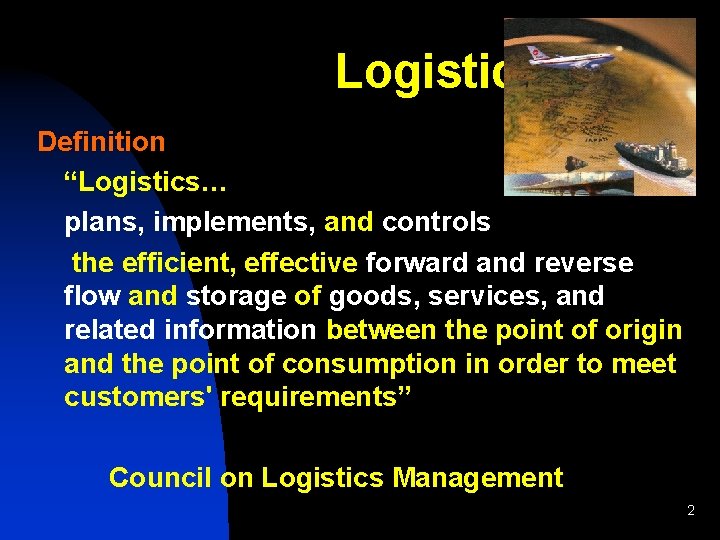

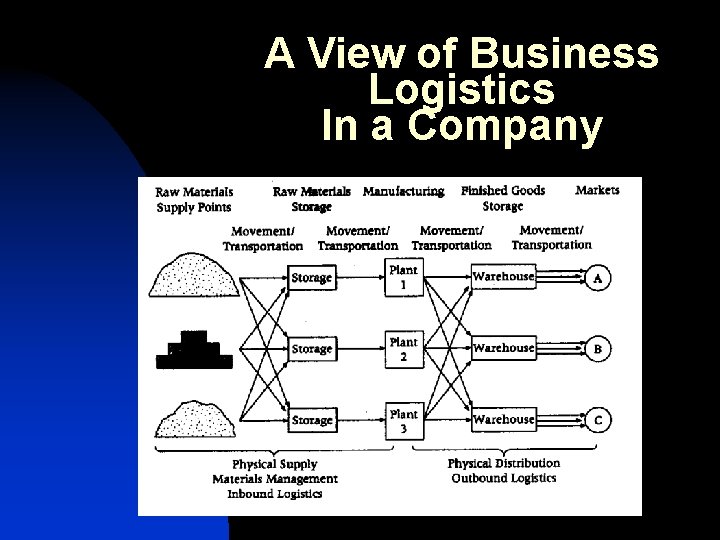
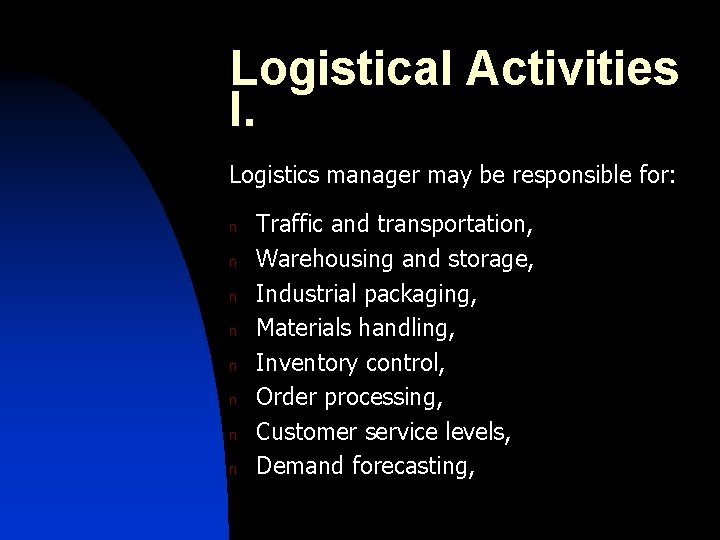
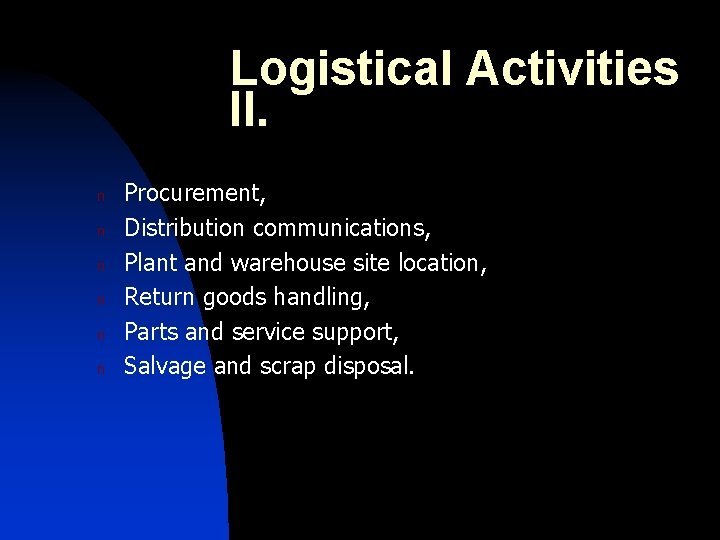
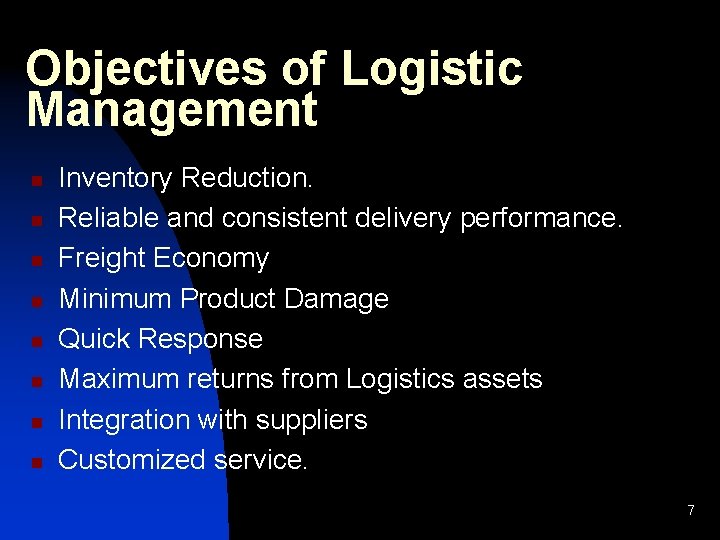
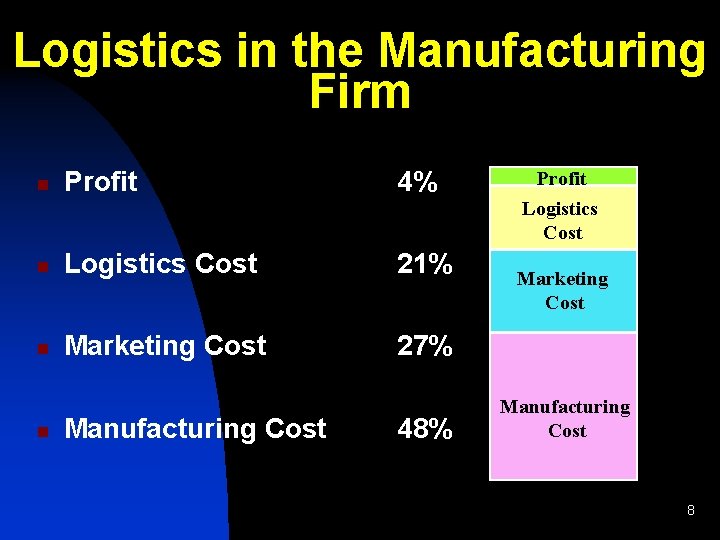
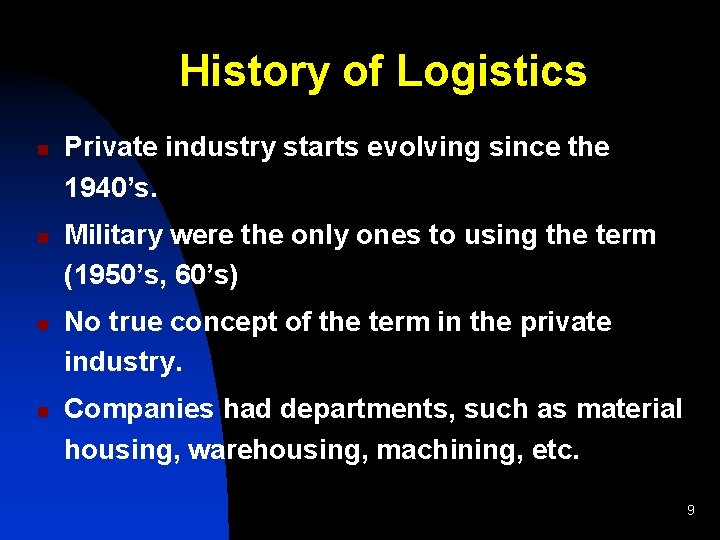
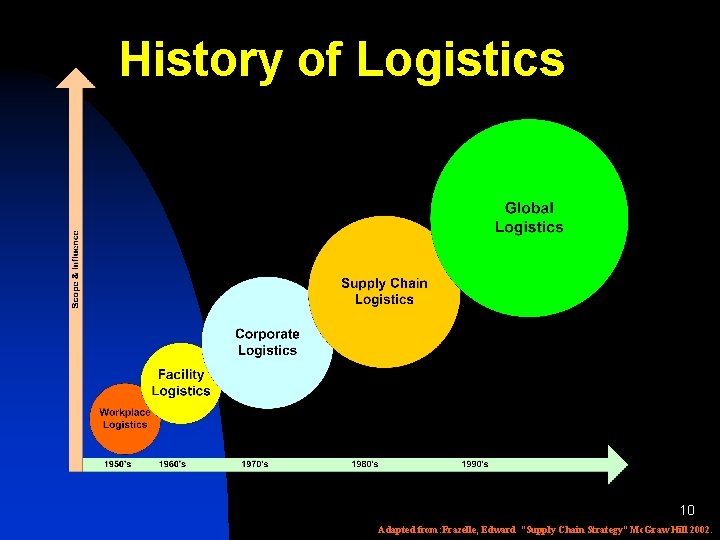
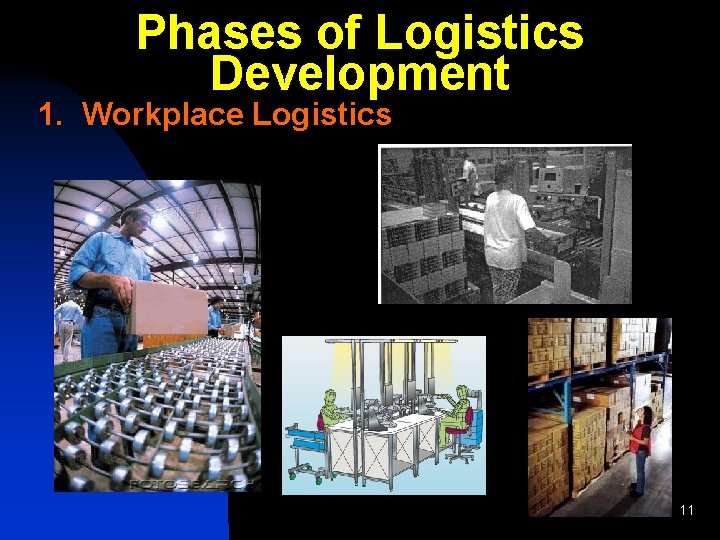
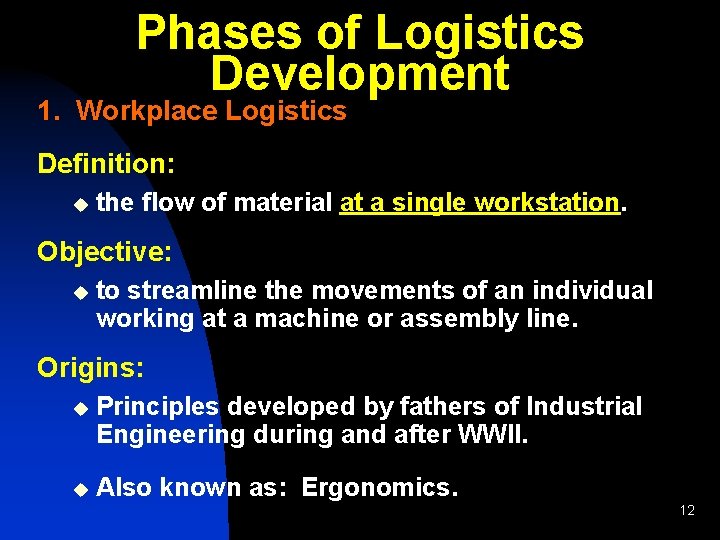
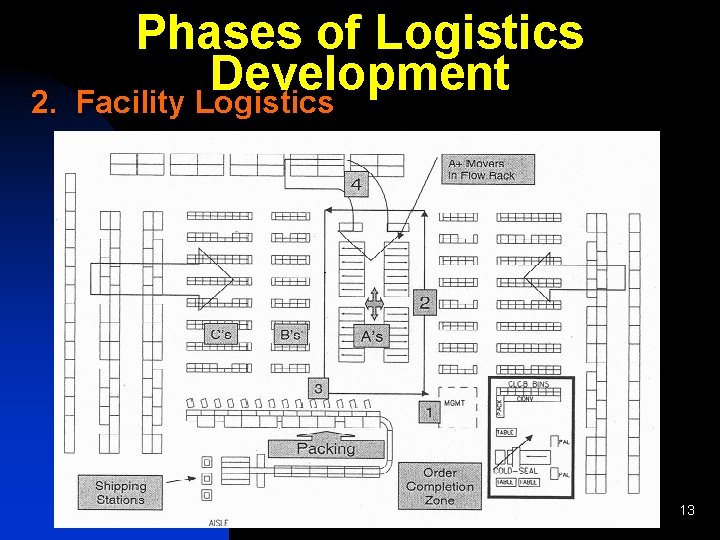
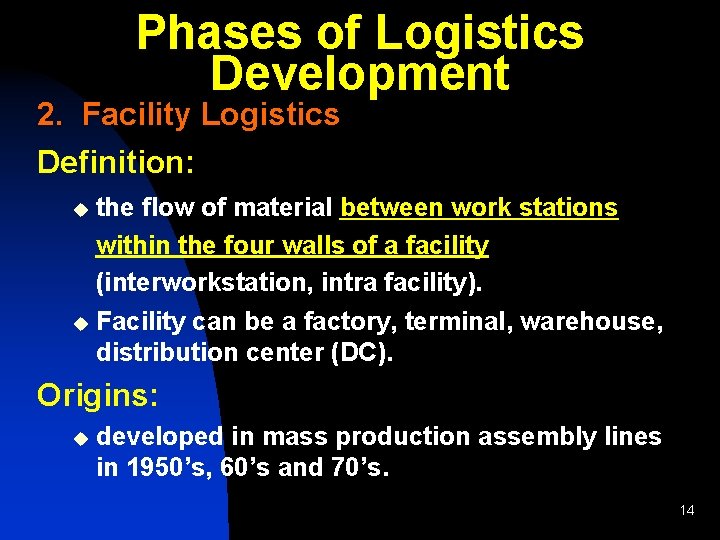
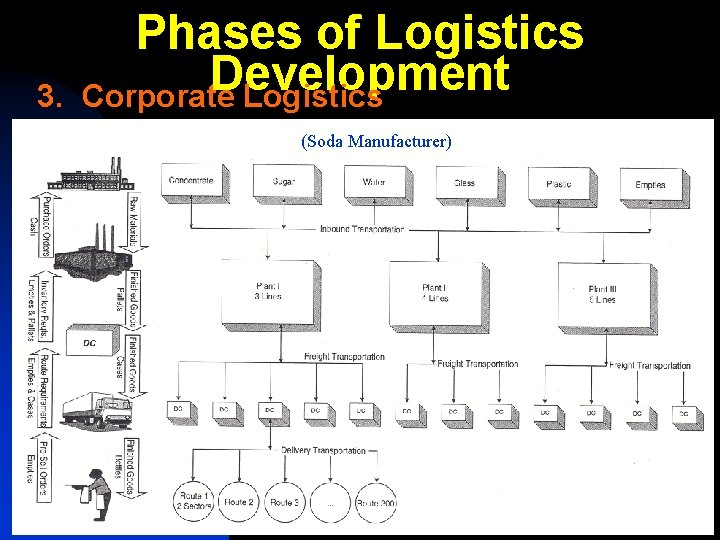
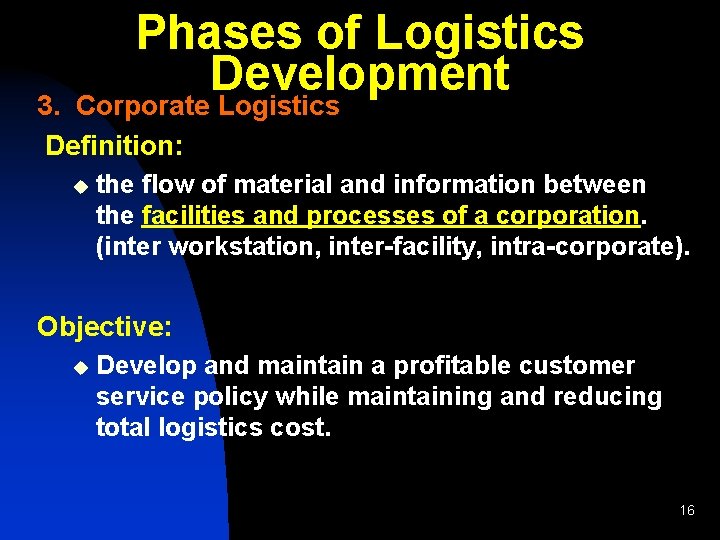
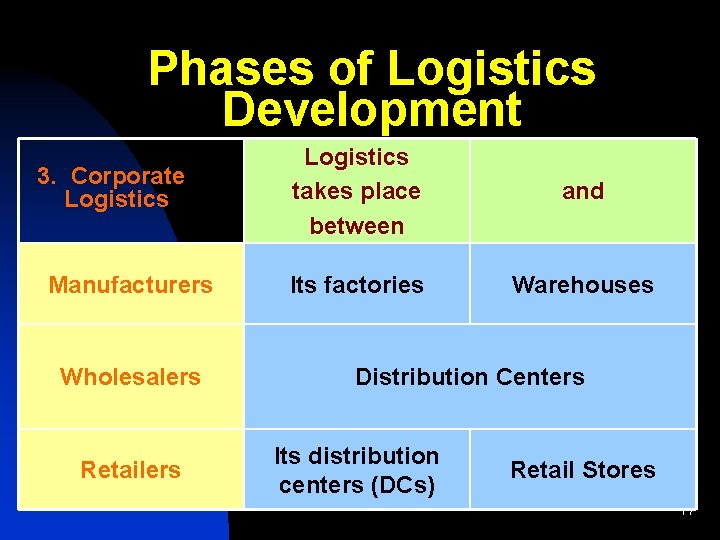
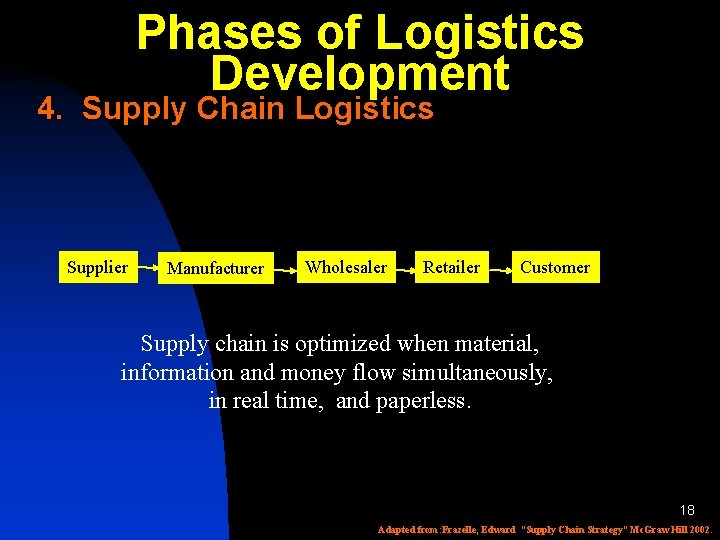
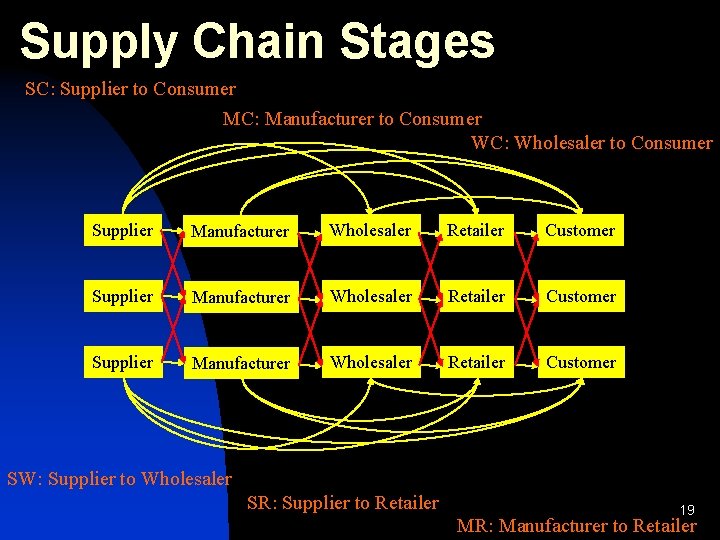
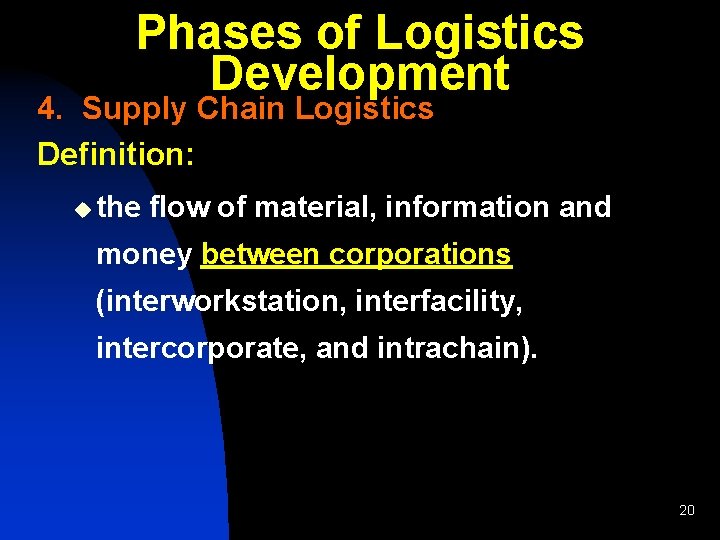
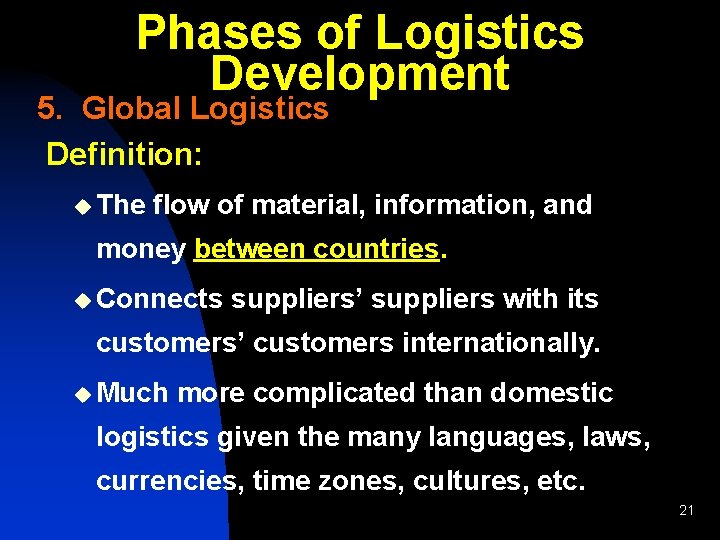
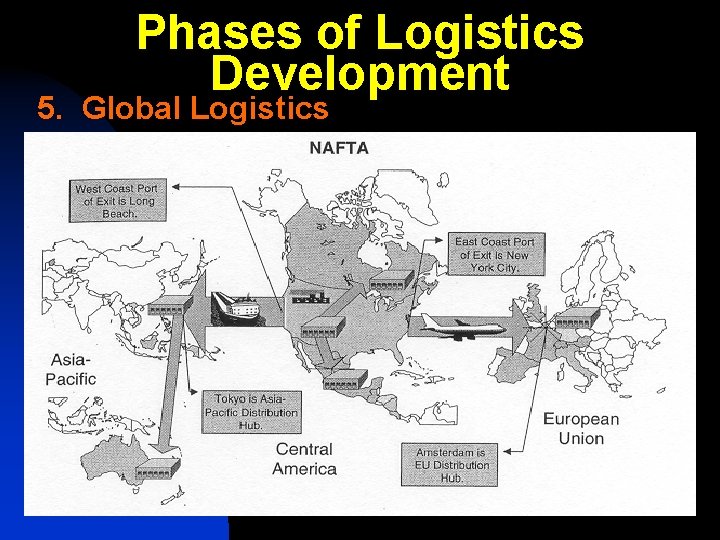
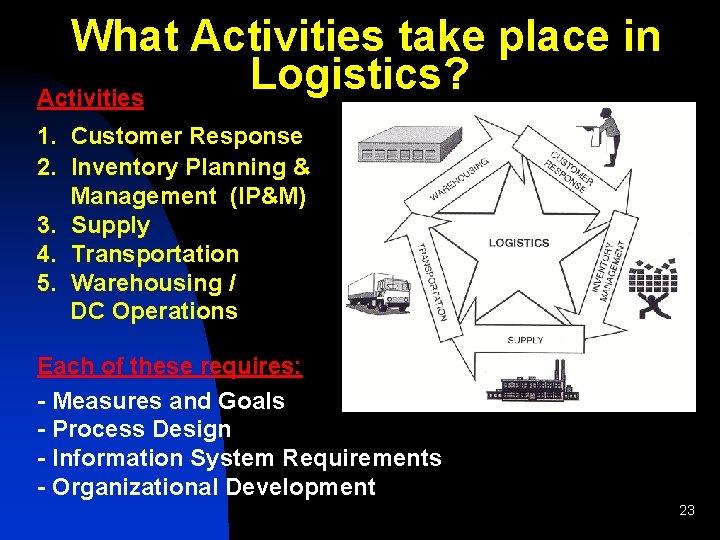
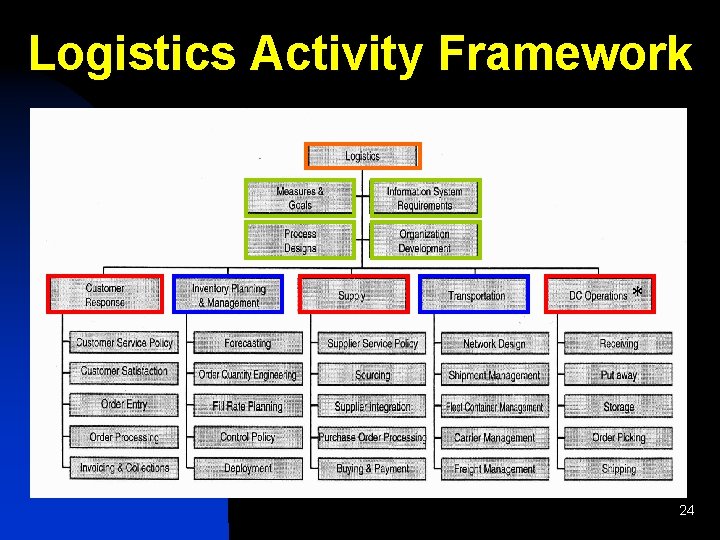

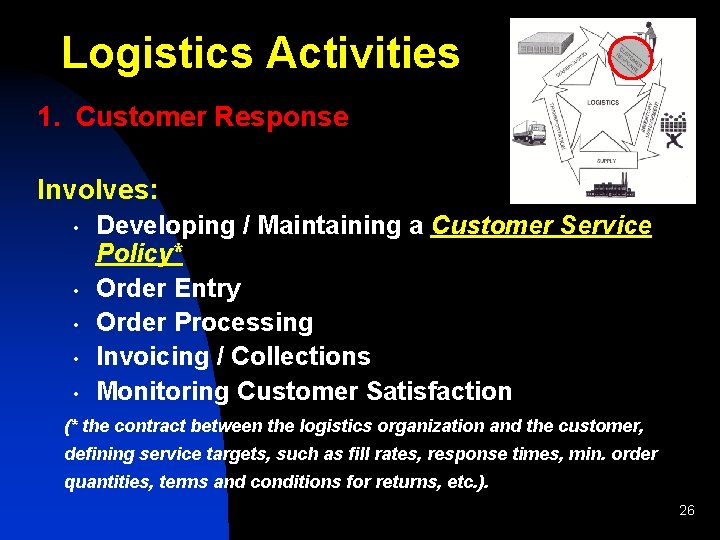
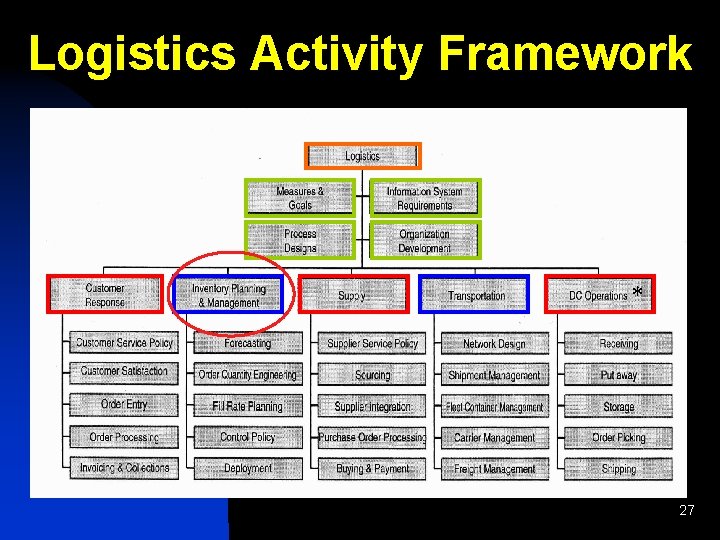
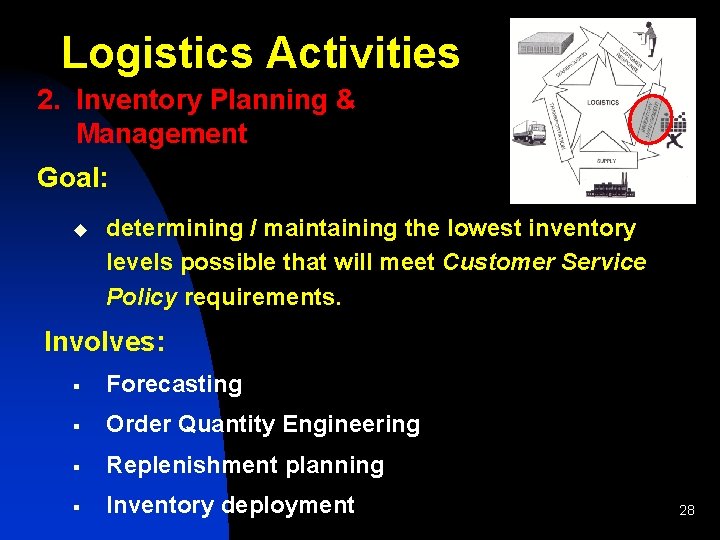
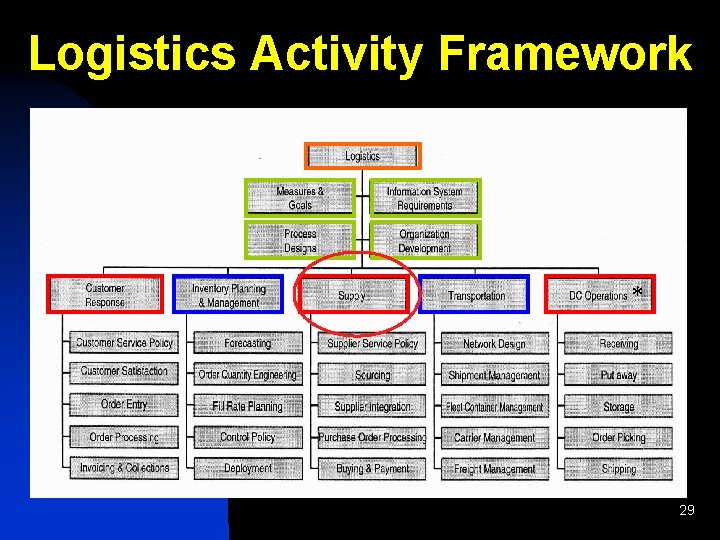
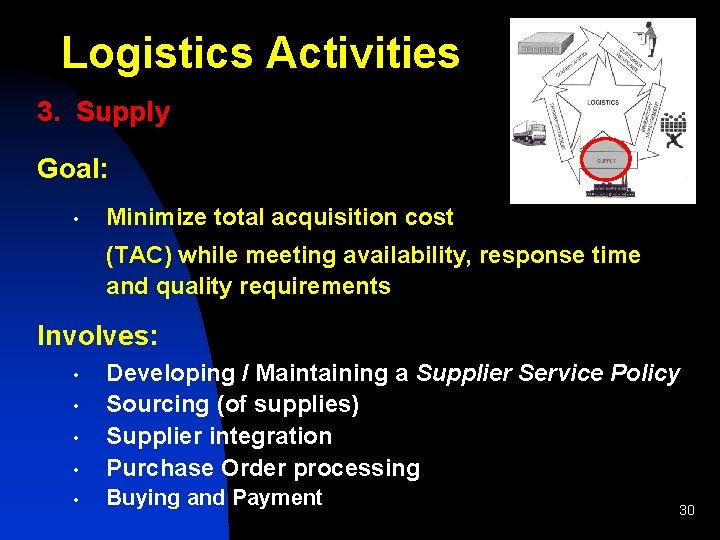
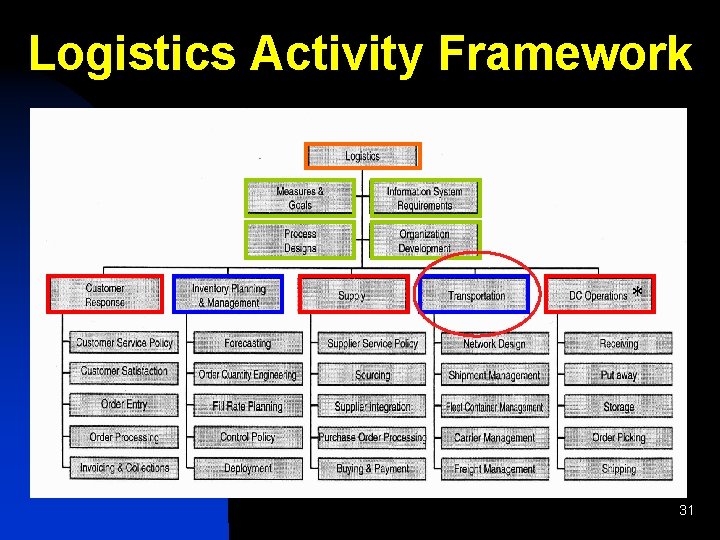
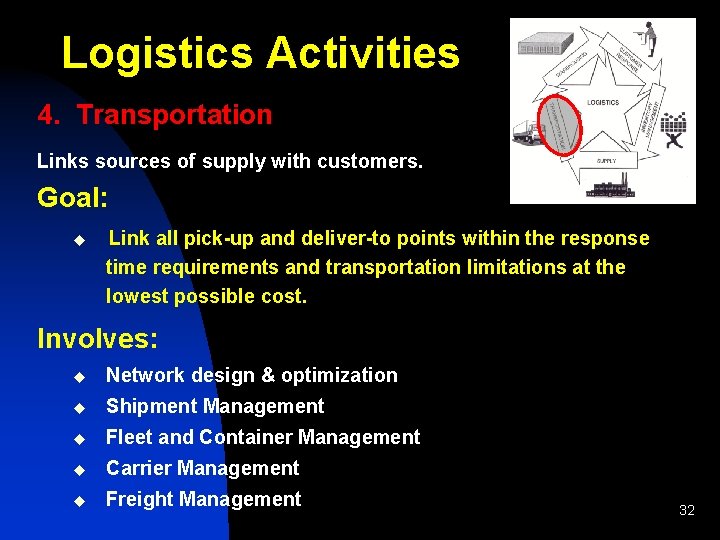
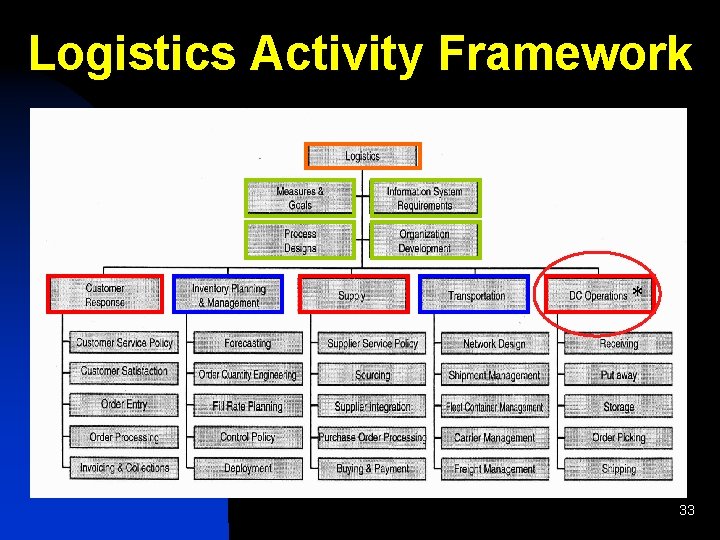
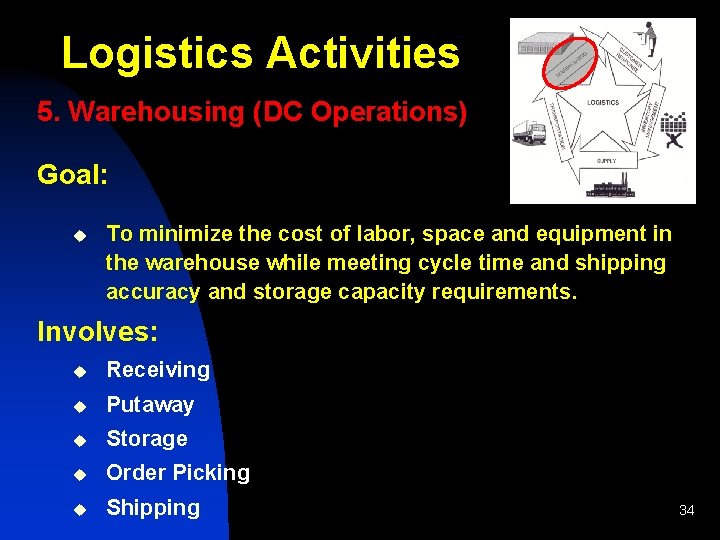
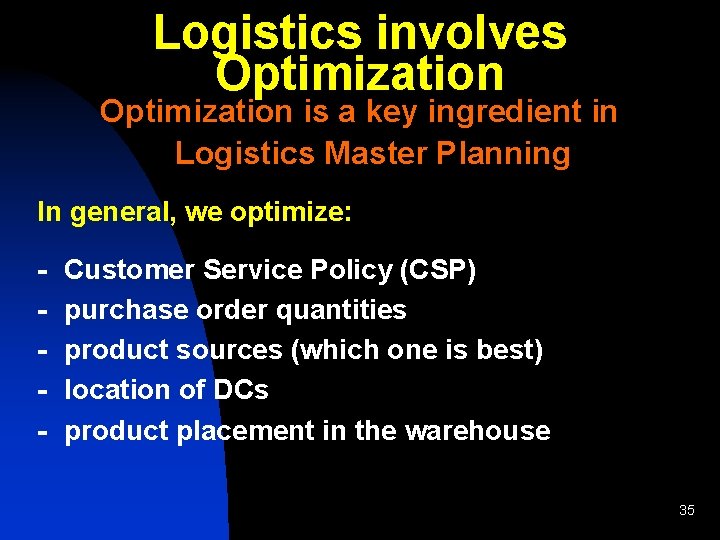
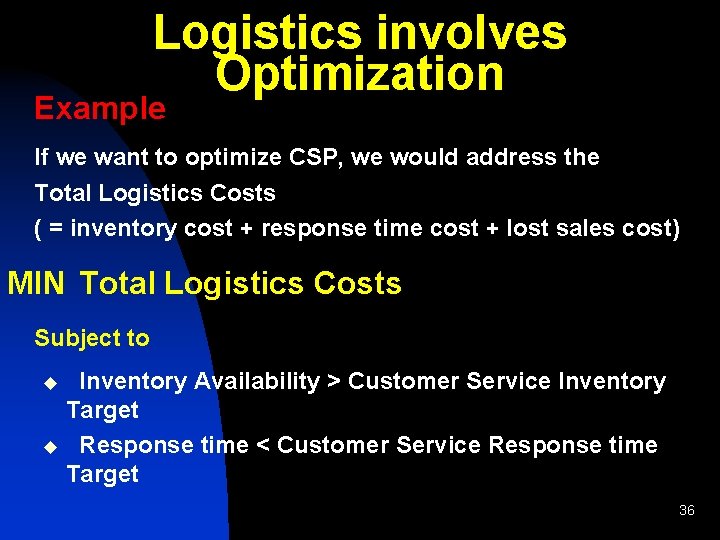
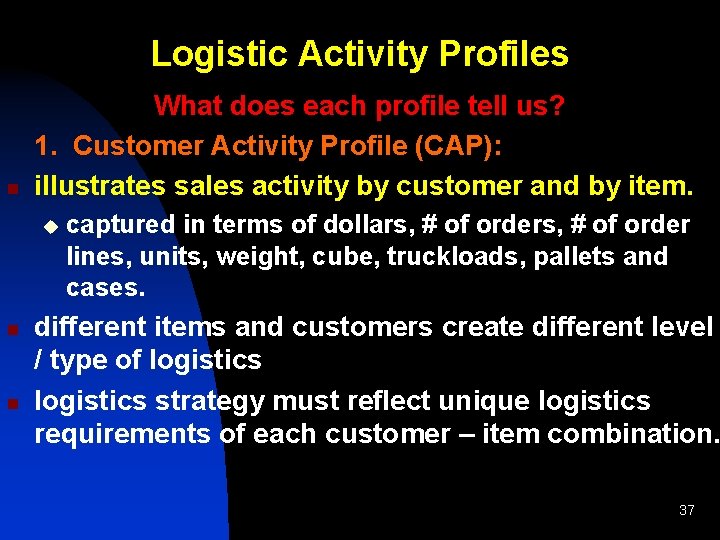
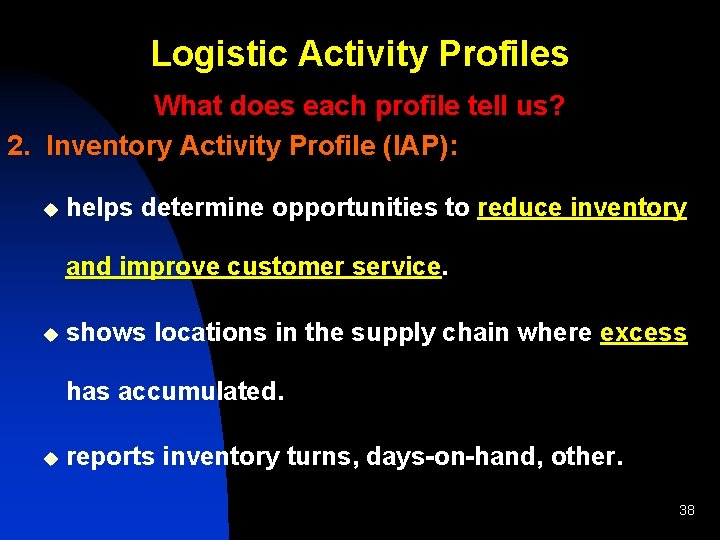
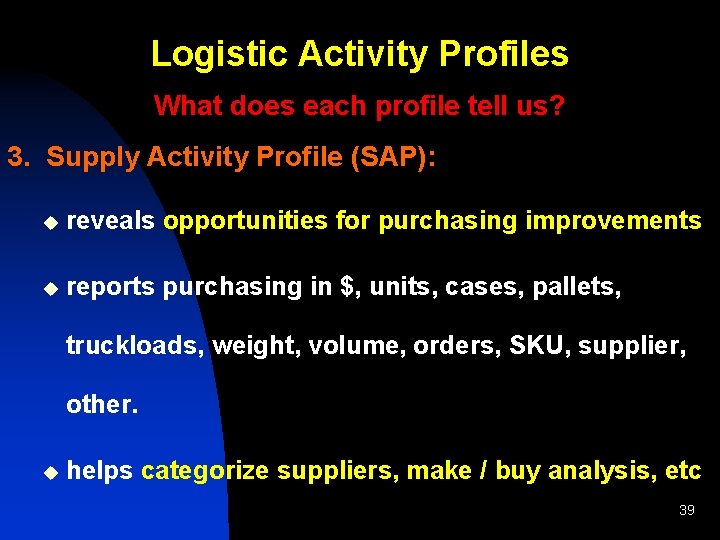
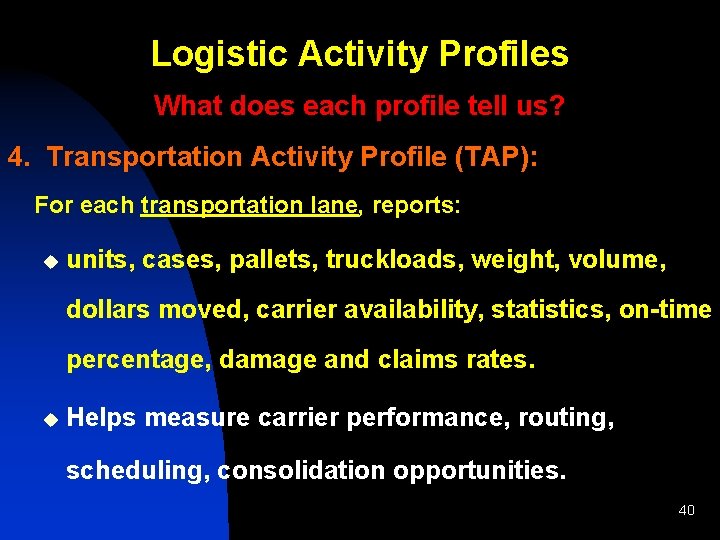
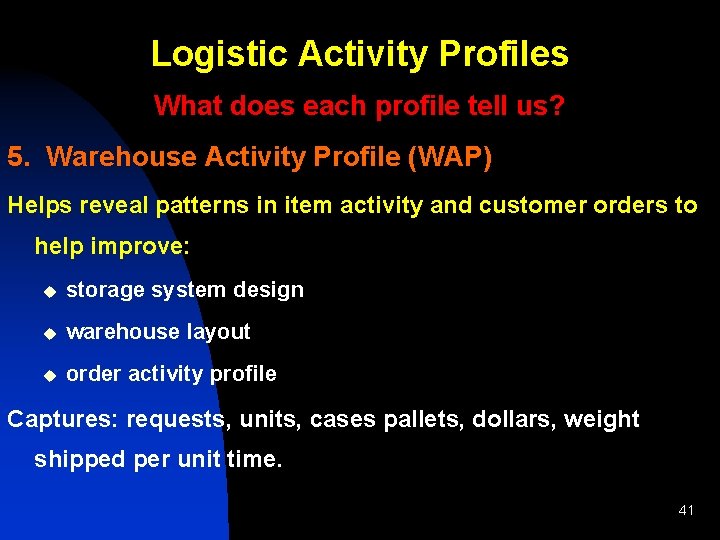
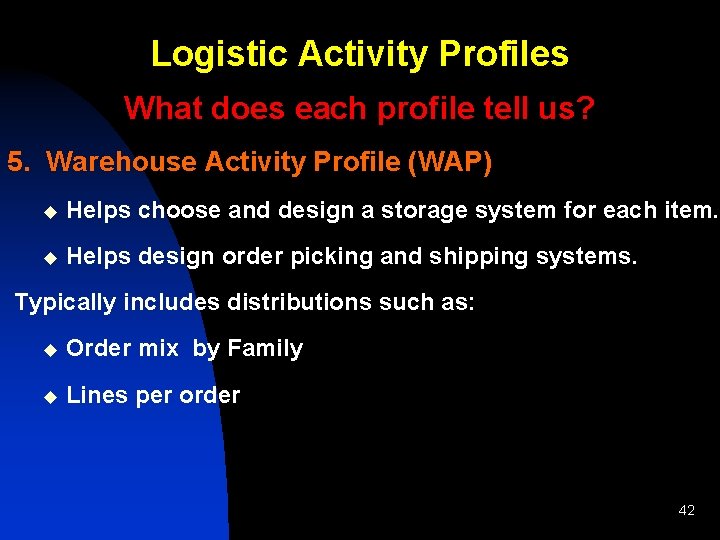
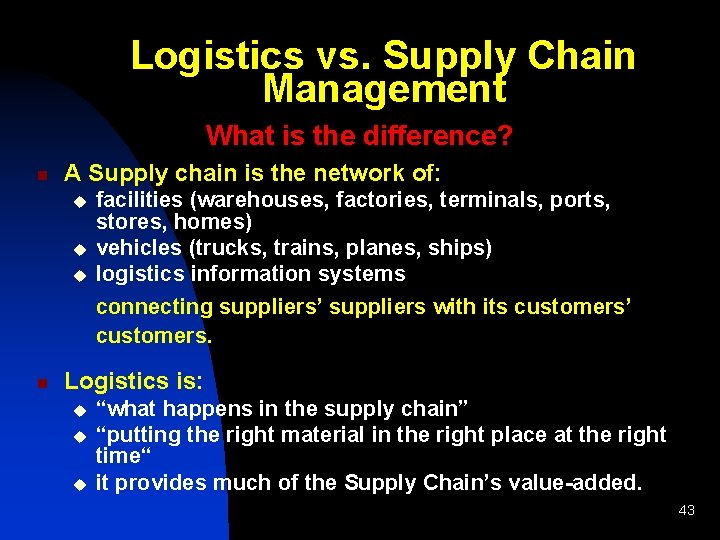
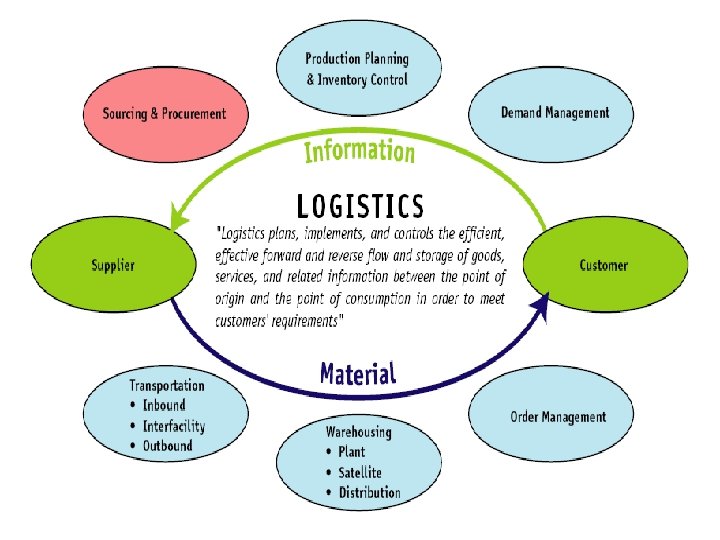
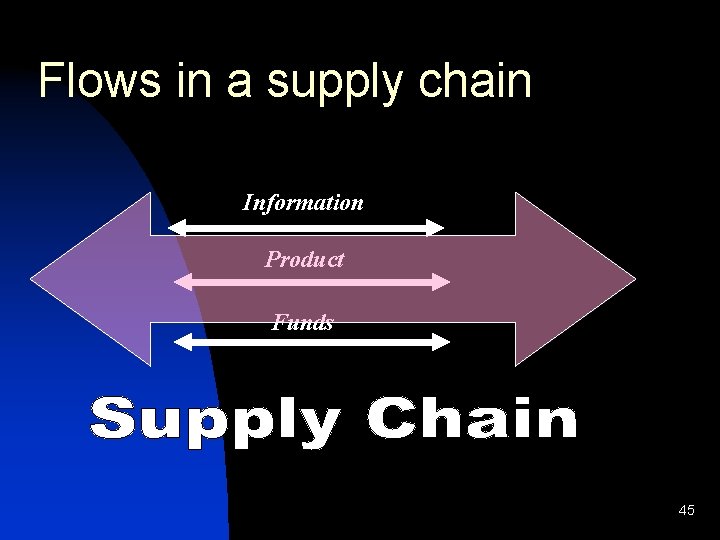
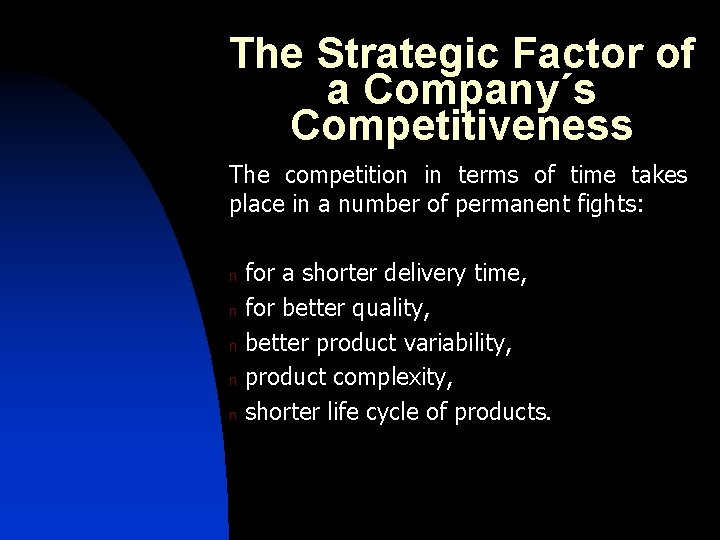
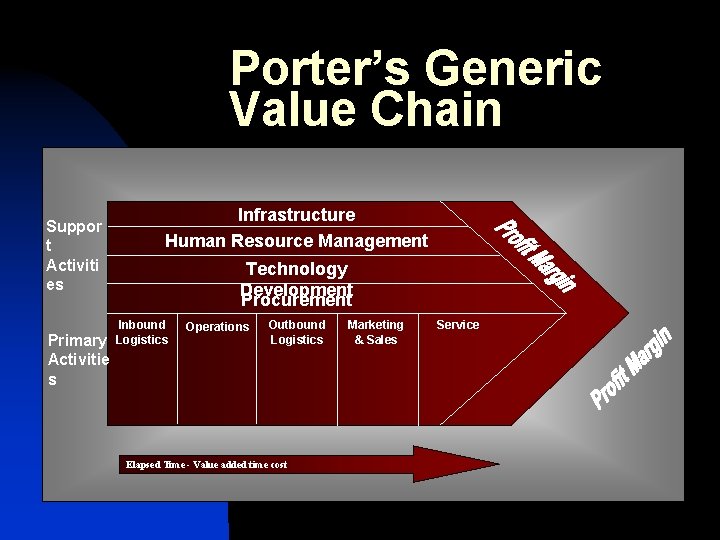
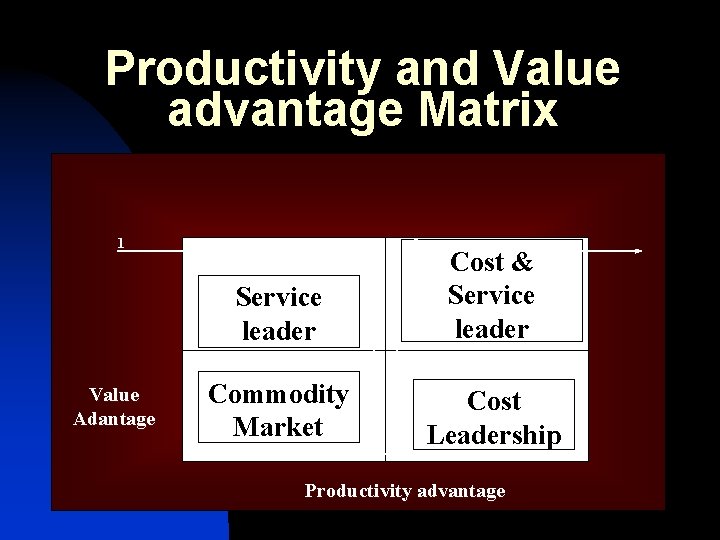
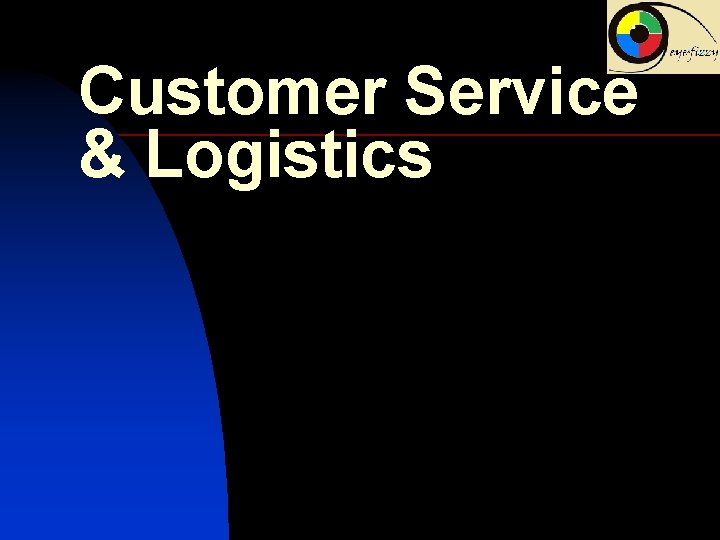
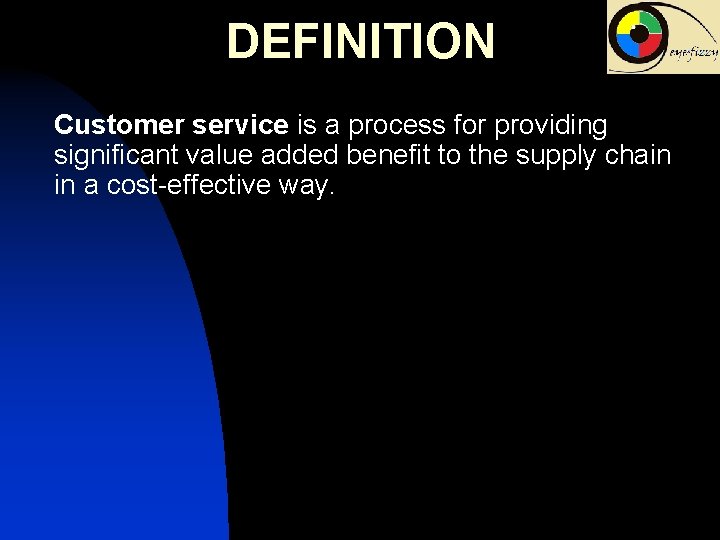
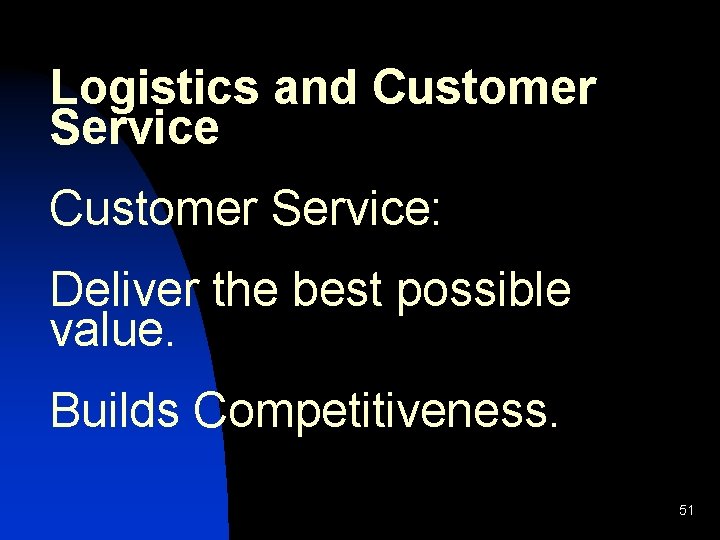
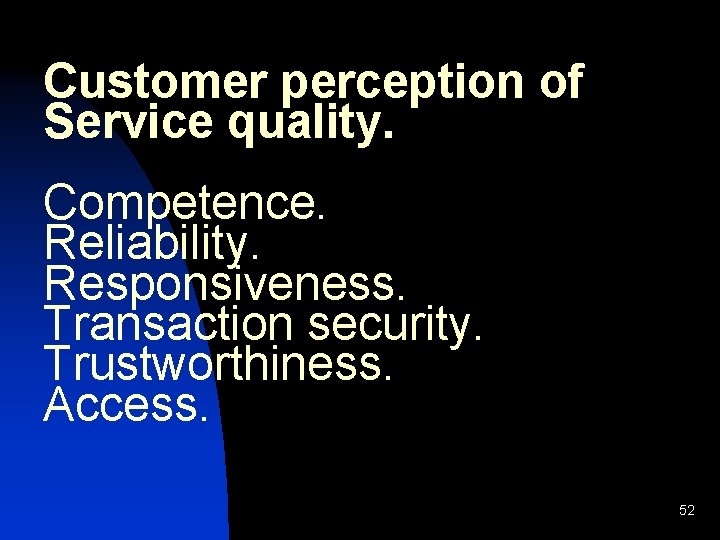
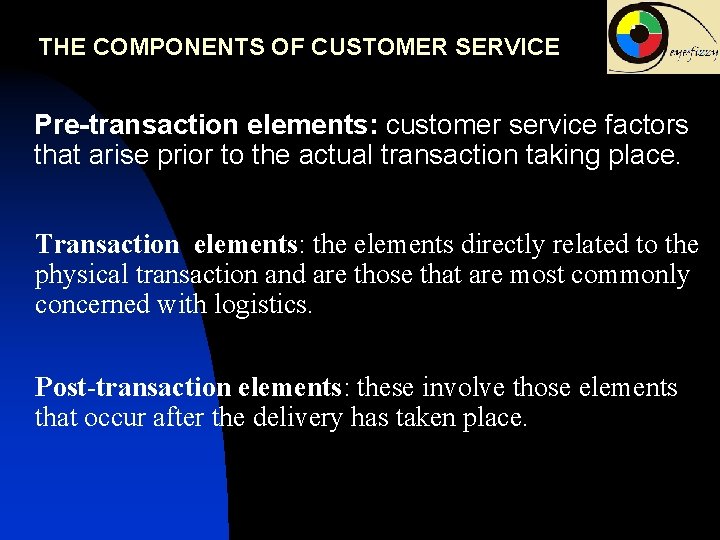
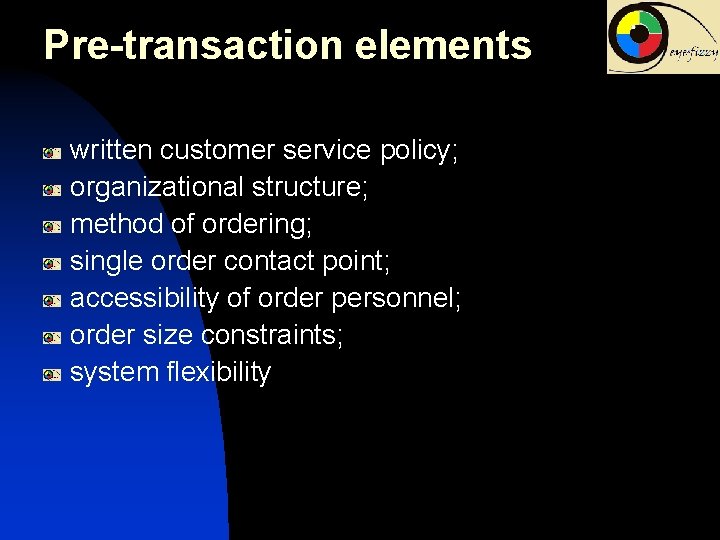
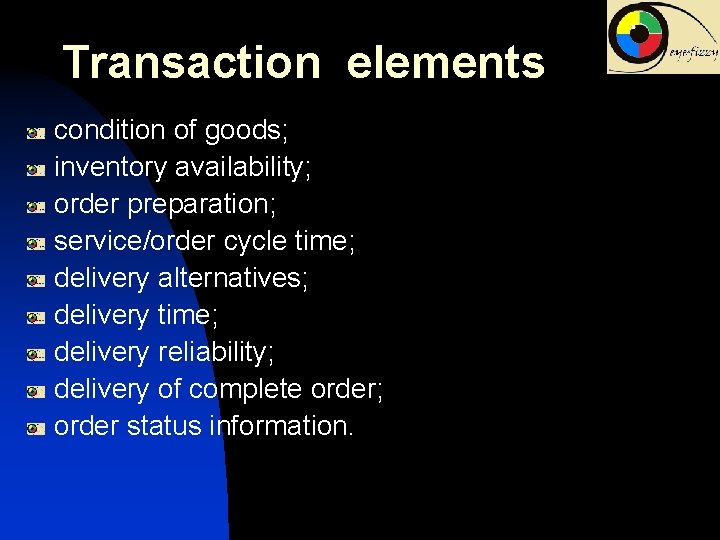
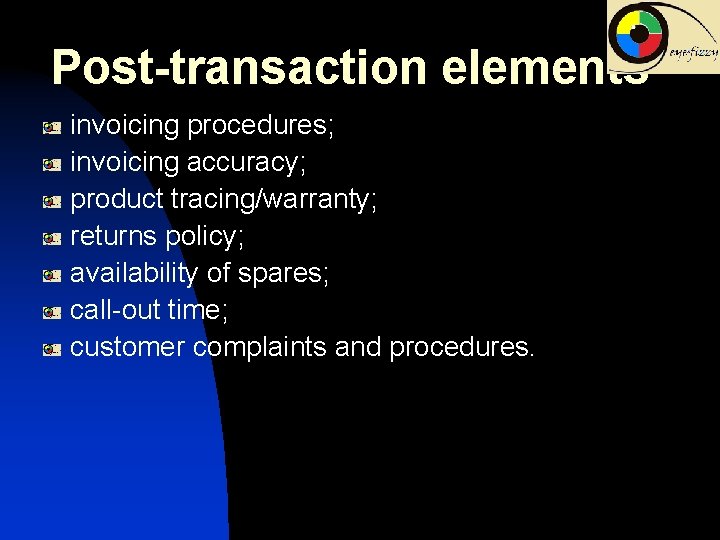
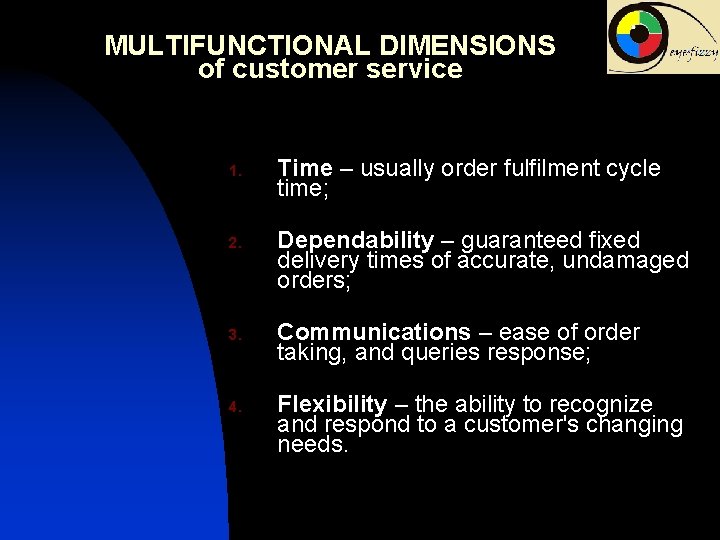
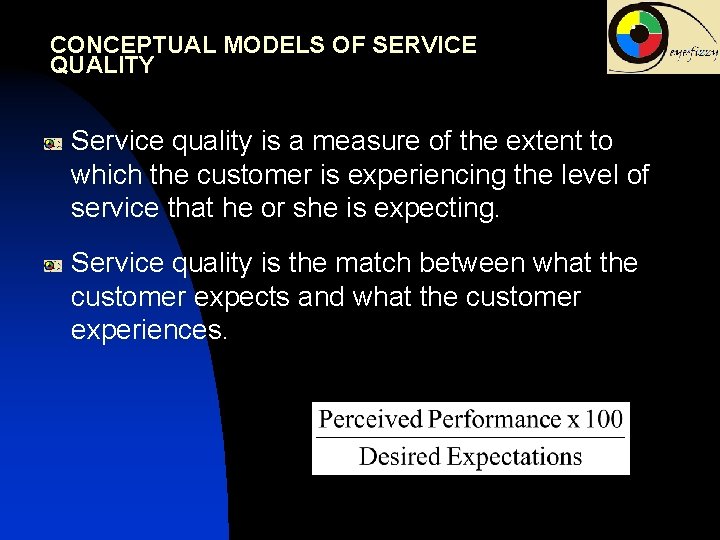
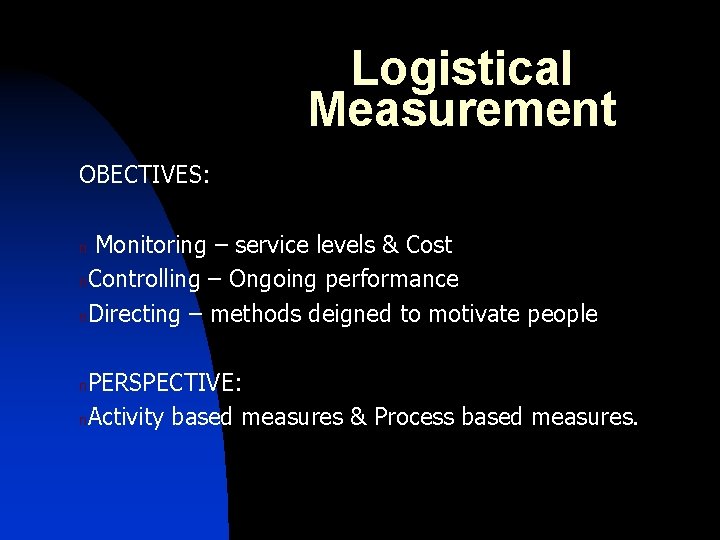
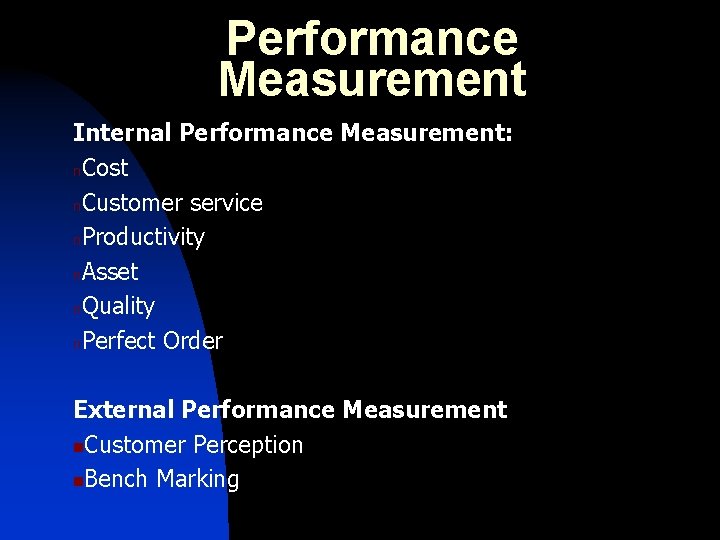
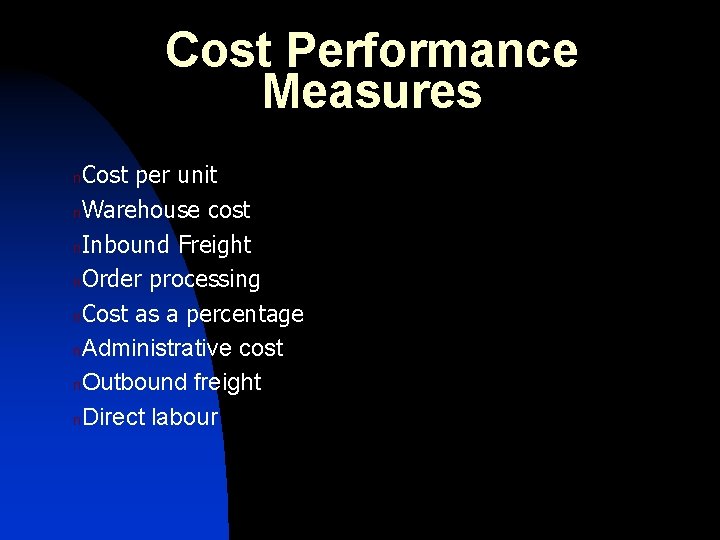
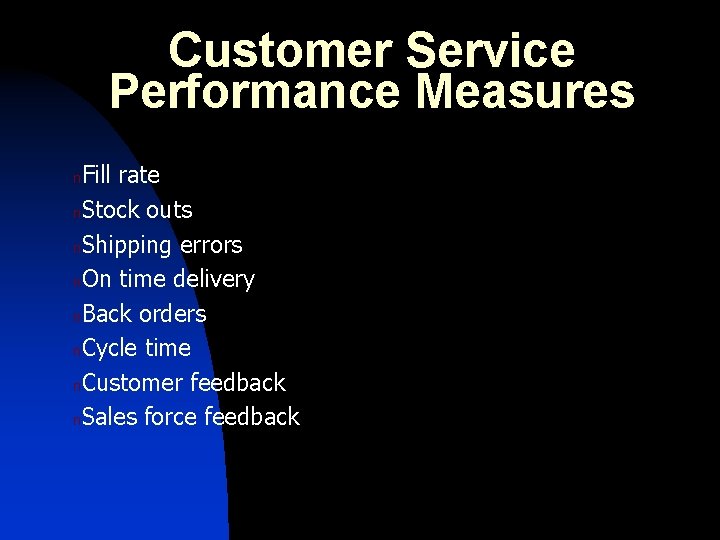
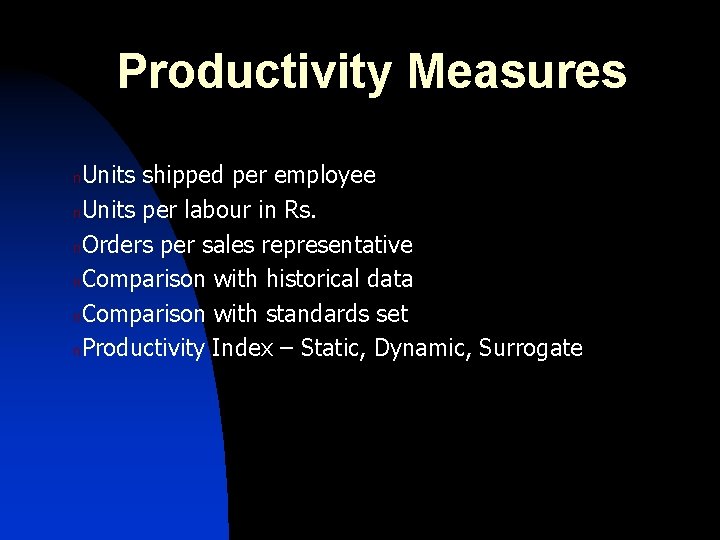
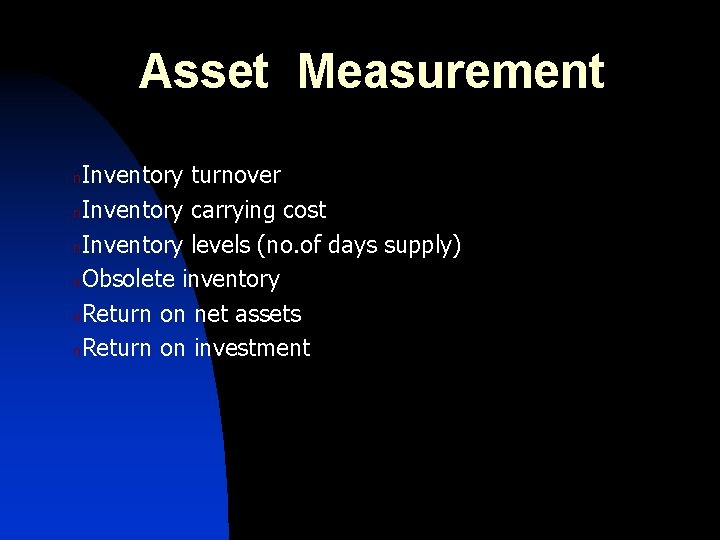
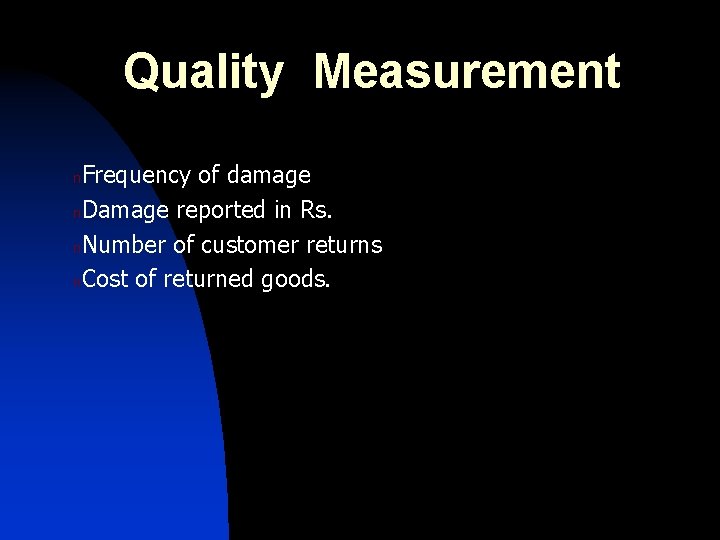
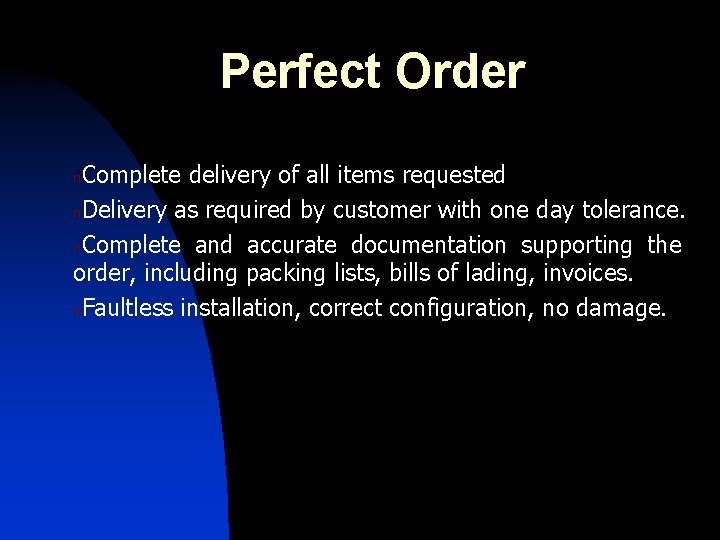
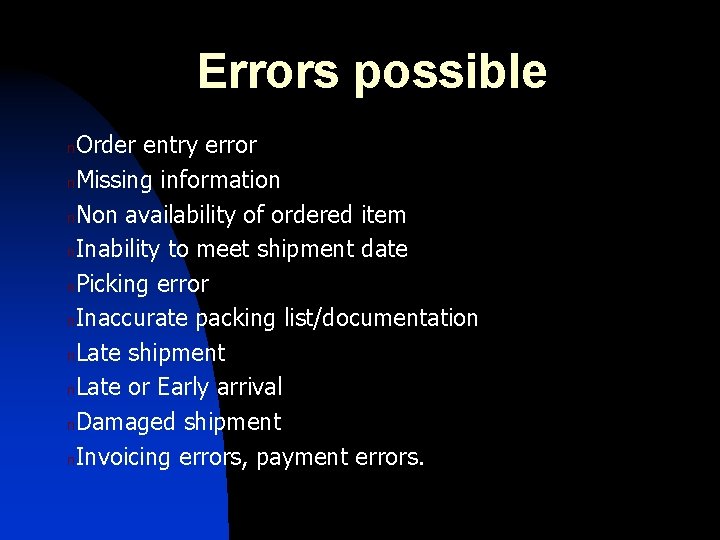
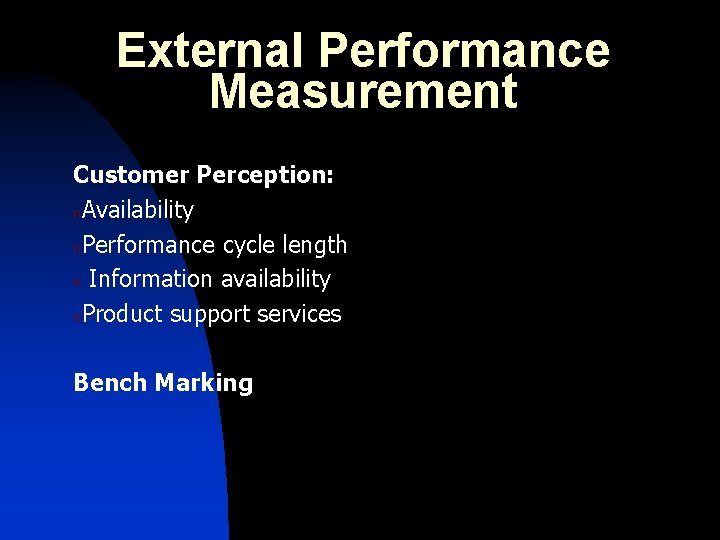
- Slides: 68
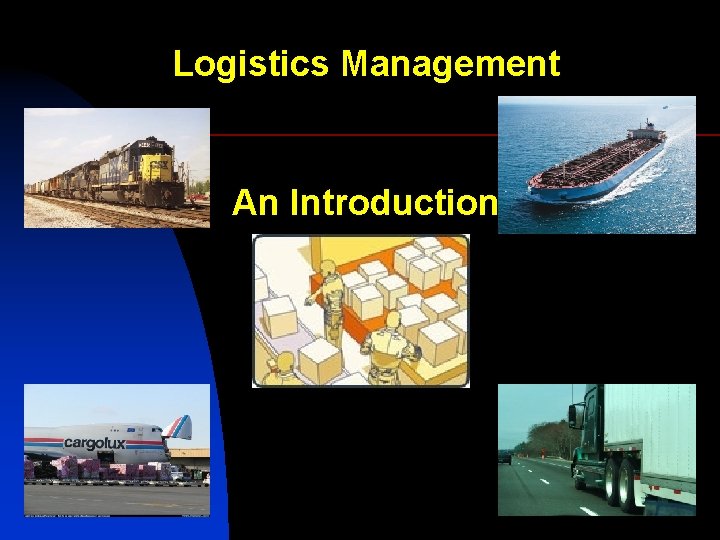
Logistics Management An Introduction 1
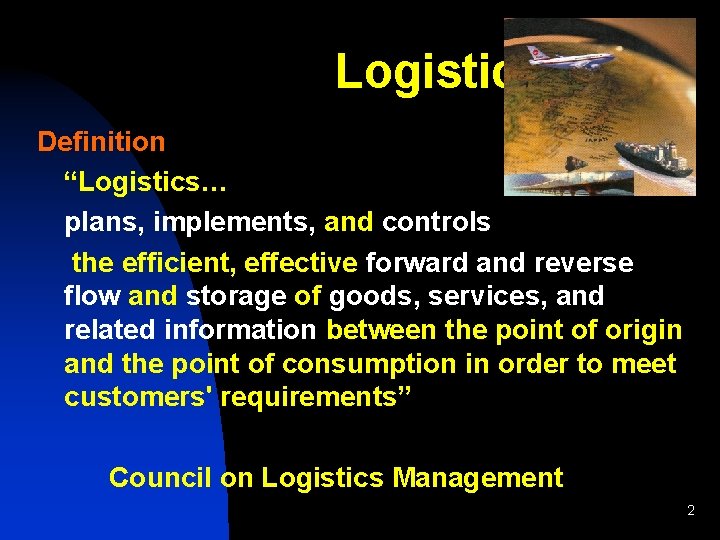
Logistics Definition “Logistics… plans, implements, and controls the efficient, effective forward and reverse flow and storage of goods, services, and related information between the point of origin and the point of consumption in order to meet customers' requirements” Council on Logistics Management 2

Definition of Logistics Seven “Rs” ensuring the availability of n n n n the RIGHT product, product in the RIGHT quantity and RIGHT condition, condition at the RIGHT place, place at the RIGHT time, time for the RIGHT customer, customer at the RIGHT costs Logistics) (Institute of
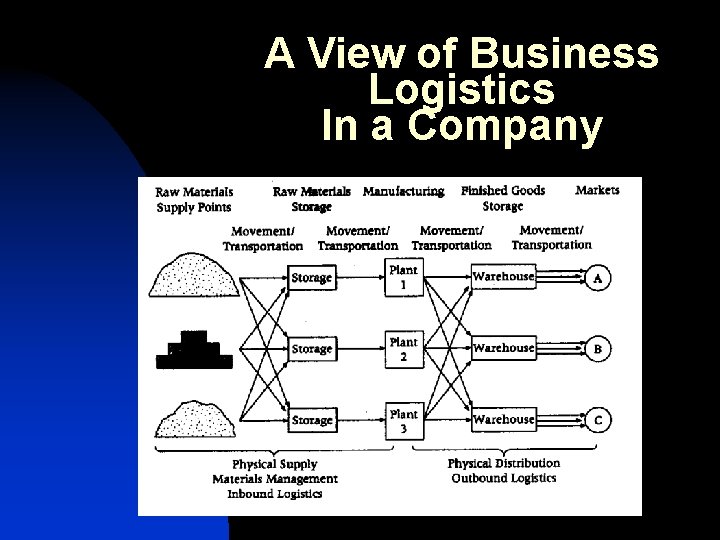
A View of Business Logistics In a Company
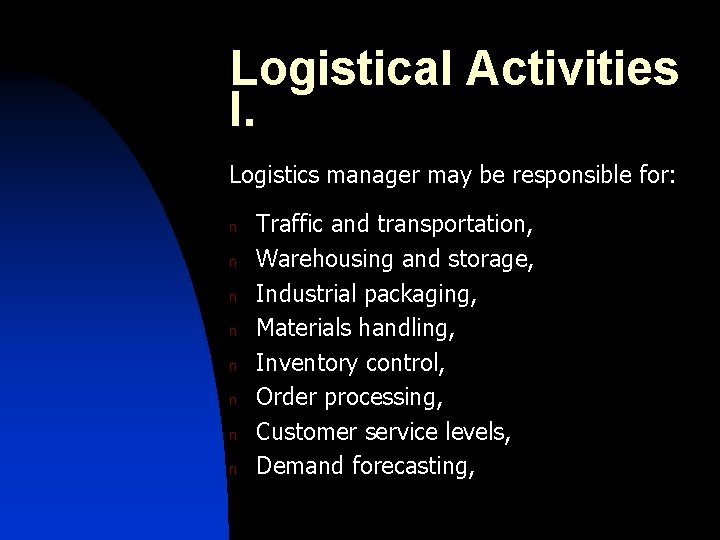
Logistical Activities I. Logistics manager may be responsible for: n n n n Traffic and transportation, Warehousing and storage, Industrial packaging, Materials handling, Inventory control, Order processing, Customer service levels, Demand forecasting,
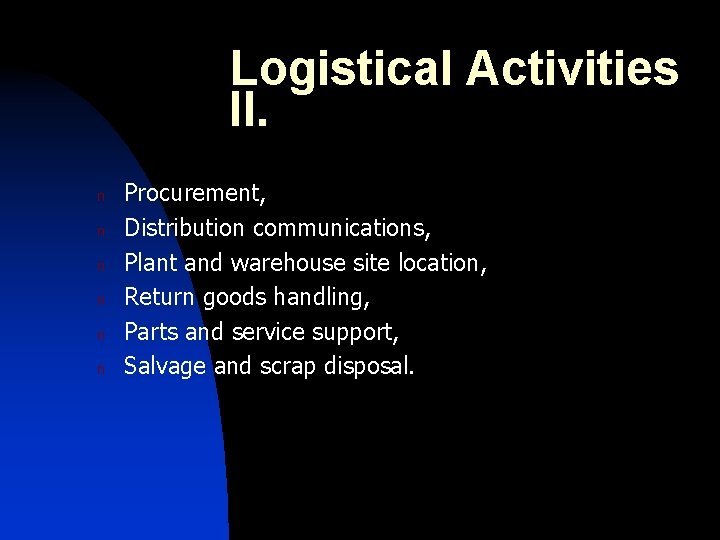
Logistical Activities II. n n n Procurement, Distribution communications, Plant and warehouse site location, Return goods handling, Parts and service support, Salvage and scrap disposal.
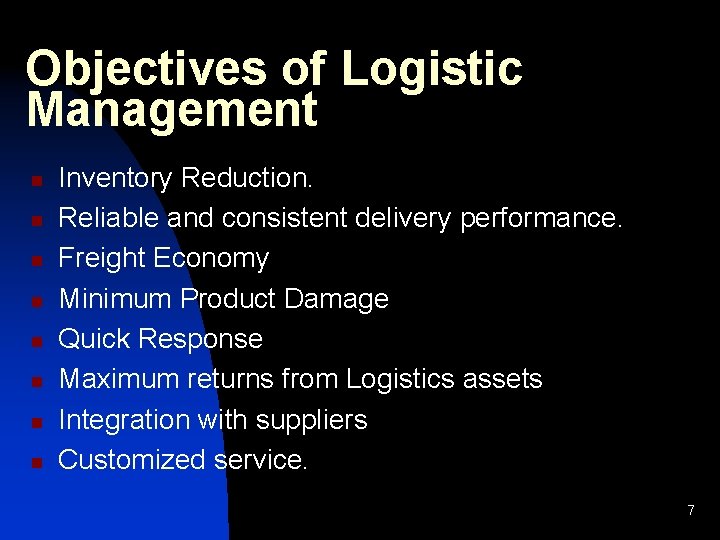
Objectives of Logistic Management n n n n Inventory Reduction. Reliable and consistent delivery performance. Freight Economy Minimum Product Damage Quick Response Maximum returns from Logistics assets Integration with suppliers Customized service. 7
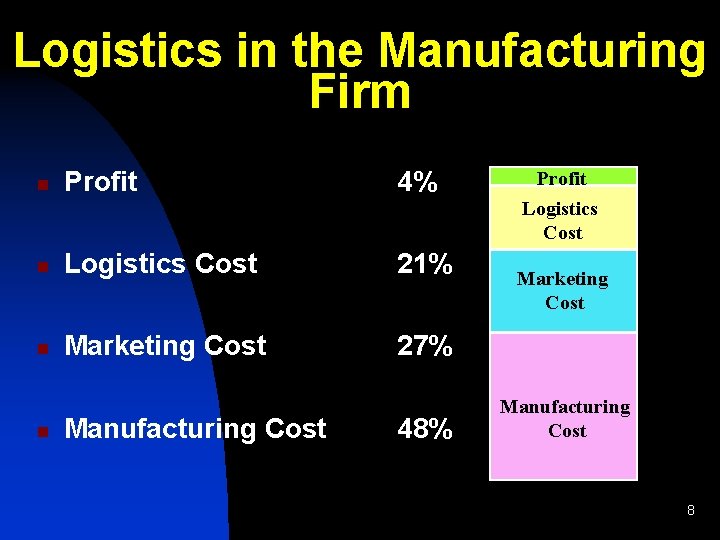
Logistics in the Manufacturing Firm n Profit 4% n Logistics Cost 21% n Marketing Cost 27% n Manufacturing Cost 48% Profit Logistics Cost Marketing Cost Manufacturing Cost 8
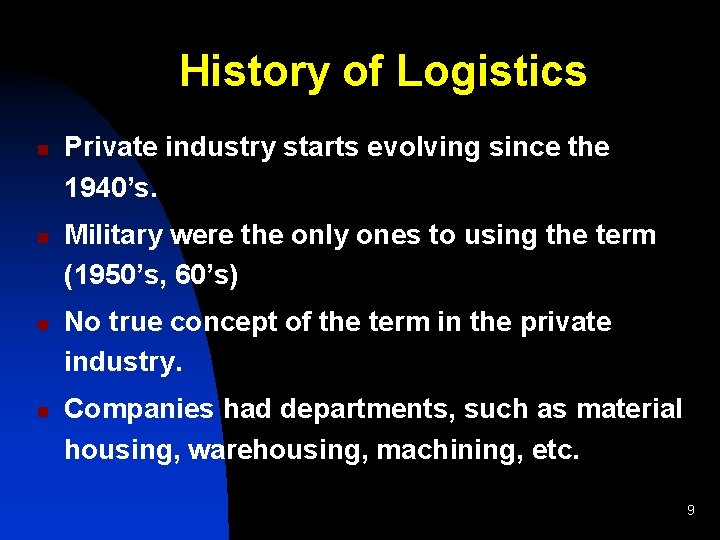
History of Logistics n n Private industry starts evolving since the 1940’s. Military were the only ones to using the term (1950’s, 60’s) No true concept of the term in the private industry. Companies had departments, such as material housing, warehousing, machining, etc. 9
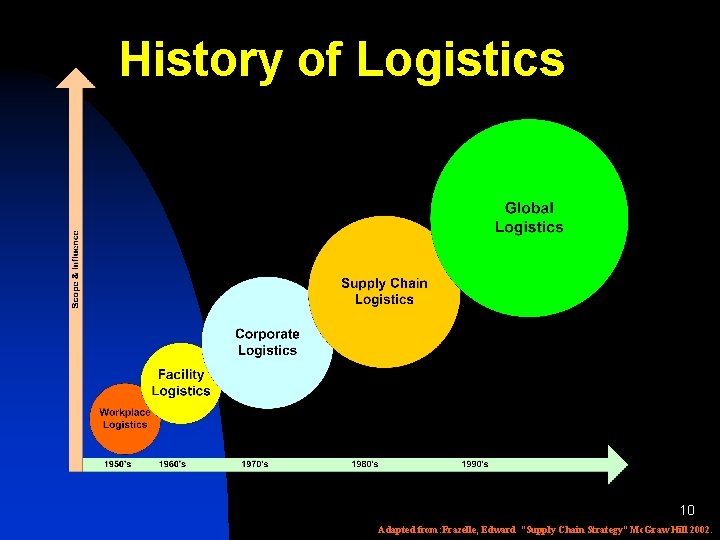
History of Logistics 10 Adapted from: Frazelle, Edward “Supply Chain Strategy” Mc. Graw Hill 2002.
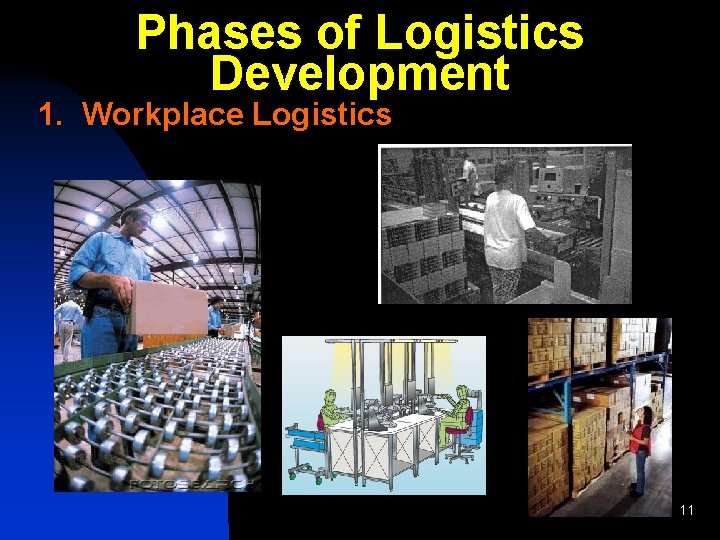
Phases of Logistics Development 1. Workplace Logistics 11
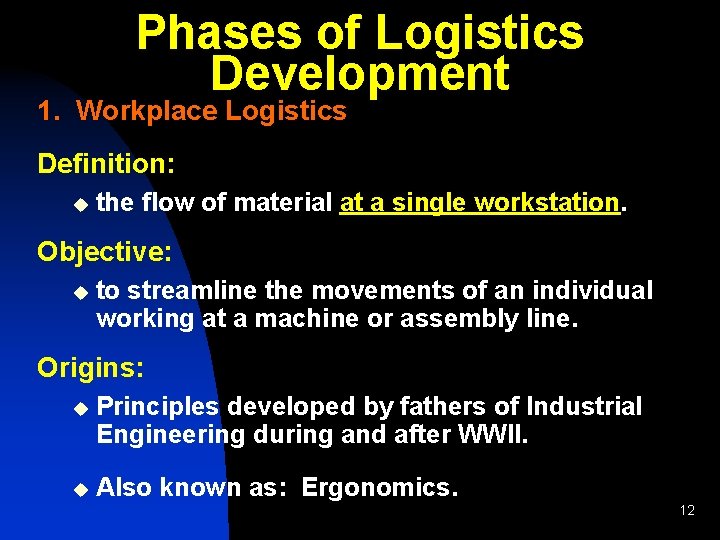
Phases of Logistics Development 1. Workplace Logistics Definition: u the flow of material at a single workstation. Objective: u to streamline the movements of an individual working at a machine or assembly line. Origins: u Principles developed by fathers of Industrial Engineering during and after WWII. u Also known as: Ergonomics. 12
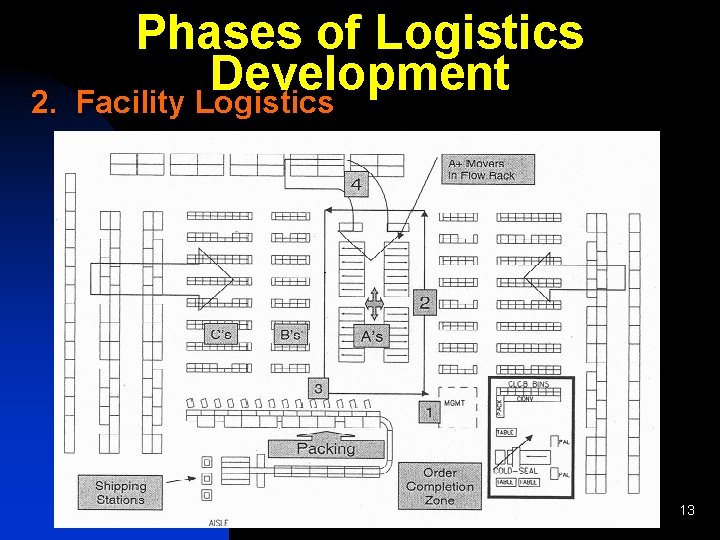
2. Phases of Logistics Development Facility Logistics 13
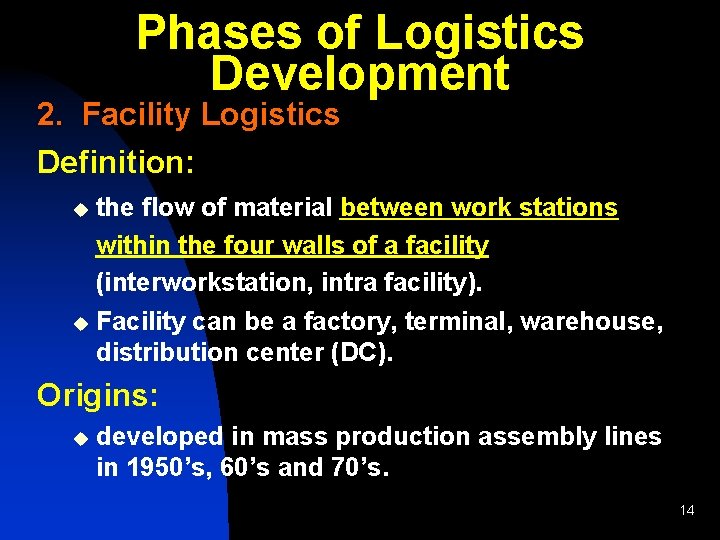
Phases of Logistics Development 2. Facility Logistics Definition: the flow of material between work stations within the four walls of a facility (interworkstation, intra facility). u Facility can be a factory, terminal, warehouse, distribution center (DC). u Origins: u developed in mass production assembly lines in 1950’s, 60’s and 70’s. 14
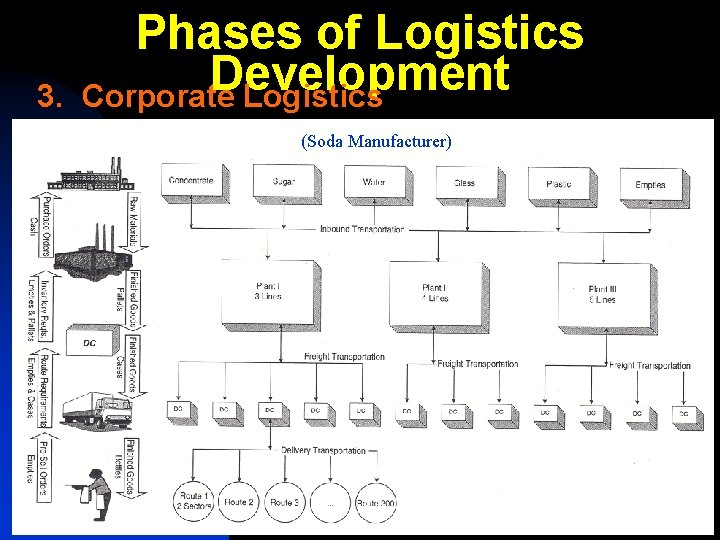
3. Phases of Logistics Development Corporate Logistics (Soda Manufacturer) 15
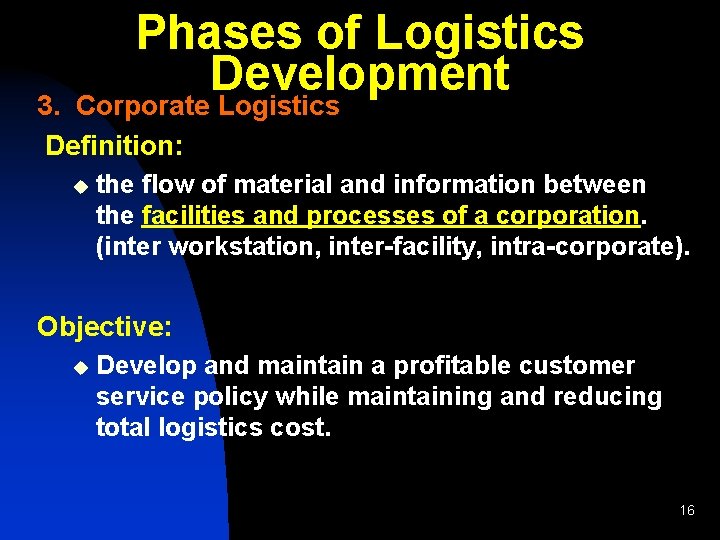
Phases of Logistics Development 3. Corporate Logistics Definition: u the flow of material and information between the facilities and processes of a corporation. (inter workstation, inter-facility, intra-corporate). Objective: u Develop and maintain a profitable customer service policy while maintaining and reducing total logistics cost. 16
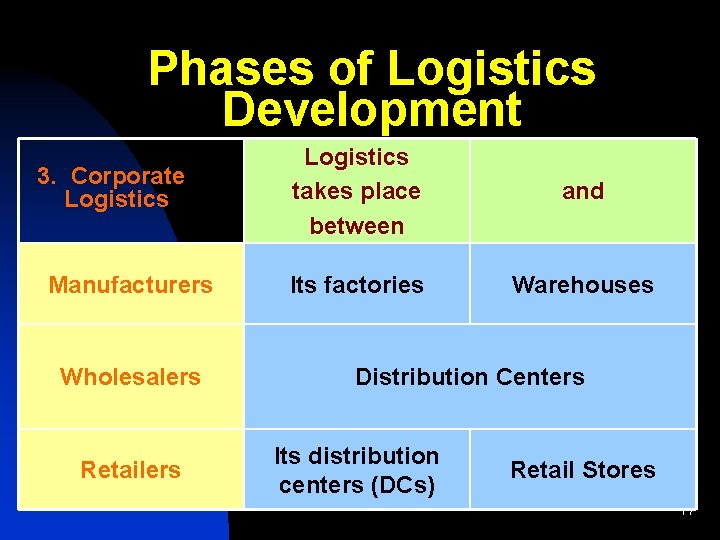
Phases of Logistics Development 3. Corporate Logistics Manufacturers Wholesalers Retailers Logistics takes place between and Its factories Warehouses Distribution Centers Its distribution centers (DCs) Retail Stores 17
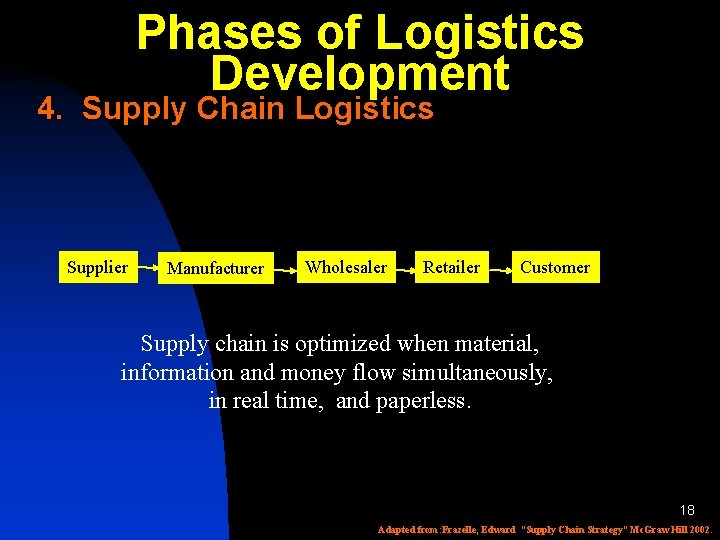
Phases of Logistics Development 4. Supply Chain Logistics Supplier Manufacturer Wholesaler Retailer Customer Supply chain is optimized when material, information and money flow simultaneously, in real time, and paperless. 18 Adapted from: Frazelle, Edward “Supply Chain Strategy” Mc. Graw Hill 2002.
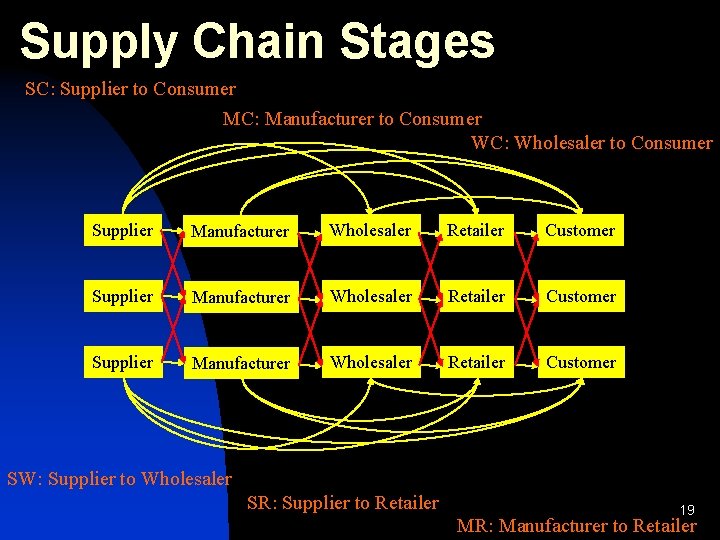
Supply Chain Stages SC: Supplier to Consumer MC: Manufacturer to Consumer WC: Wholesaler to Consumer Supplier Manufacturer Wholesaler Retailer Customer SW: Supplier to Wholesaler SR: Supplier to Retailer 19 MR: Manufacturer to Retailer
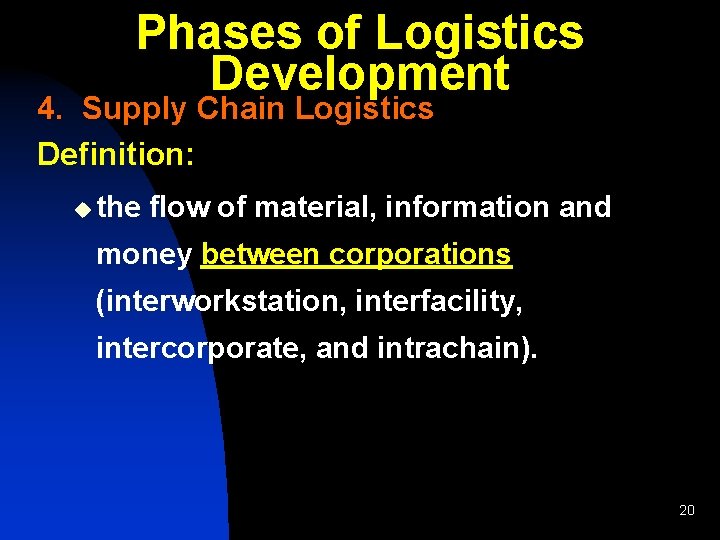
Phases of Logistics Development 4. Supply Chain Logistics Definition: u the flow of material, information and money between corporations (interworkstation, interfacility, intercorporate, and intrachain). 20
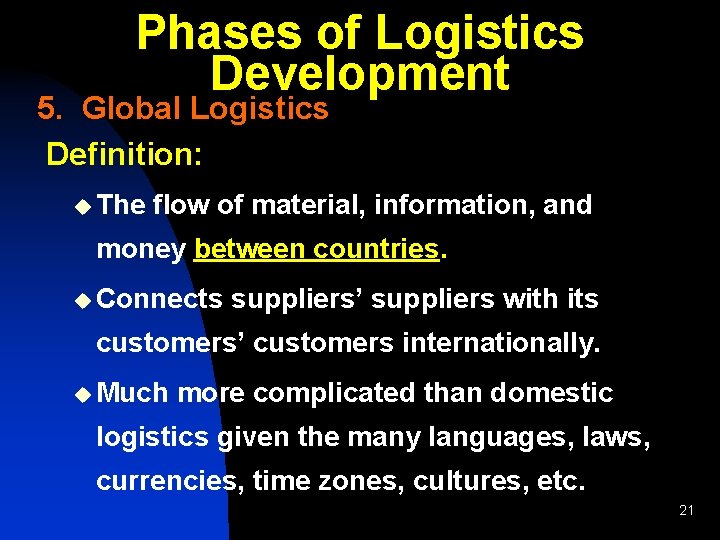
Phases of Logistics Development 5. Global Logistics Definition: u The flow of material, information, and money between countries. u Connects suppliers’ suppliers with its customers’ customers internationally. u Much more complicated than domestic logistics given the many languages, laws, currencies, time zones, cultures, etc. 21
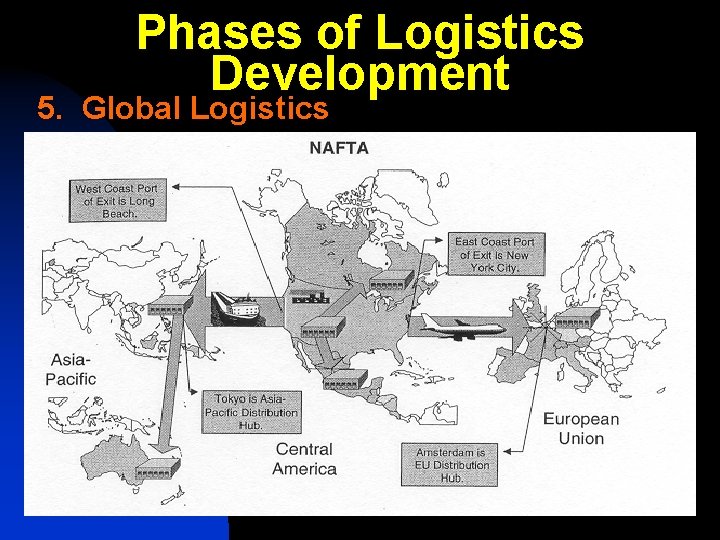
Phases of Logistics Development 5. Global Logistics 22
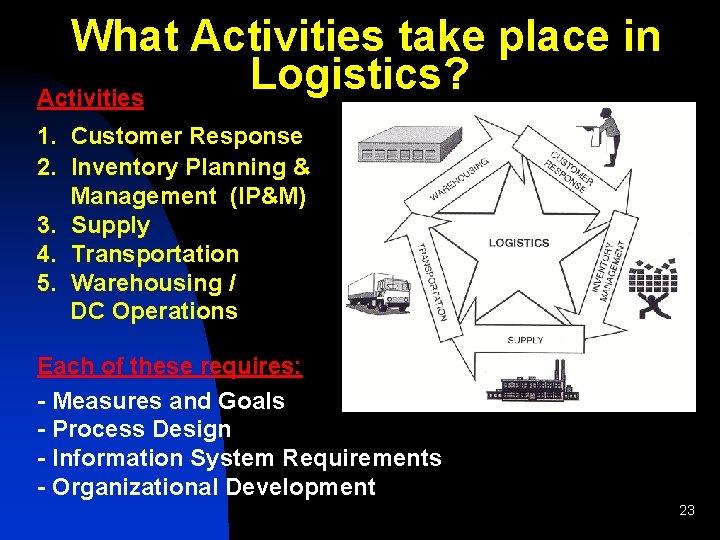
What Activities take place in Logistics? Activities 1. Customer Response 2. Inventory Planning & Management (IP&M) 3. Supply 4. Transportation 5. Warehousing / DC Operations Each of these requires: - Measures and Goals - Process Design - Information System Requirements - Organizational Development 23
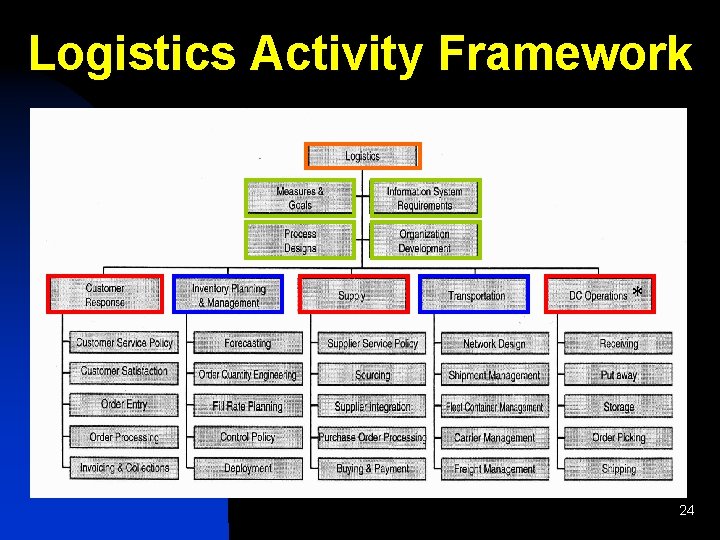
Logistics Activity Framework * 24

Logistics Activity Framework * 25
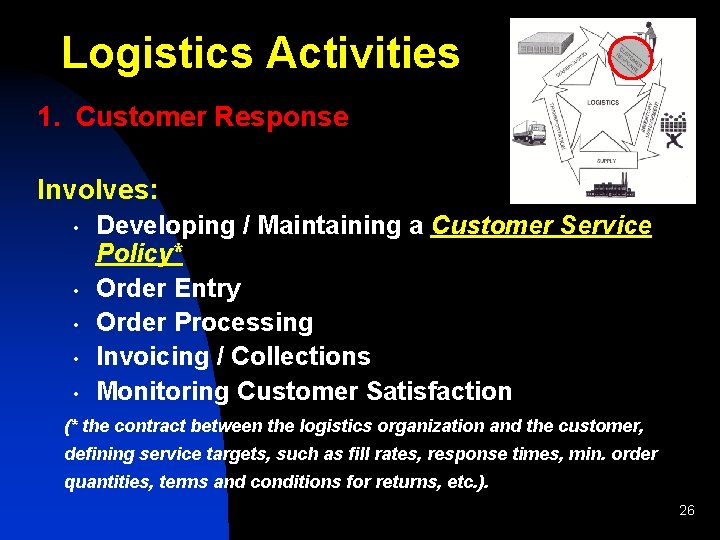
Logistics Activities 1. Customer Response Involves: • • • Developing / Maintaining a Customer Service Policy* Order Entry Order Processing Invoicing / Collections Monitoring Customer Satisfaction (* the contract between the logistics organization and the customer, defining service targets, such as fill rates, response times, min. order quantities, terms and conditions for returns, etc. ). 26
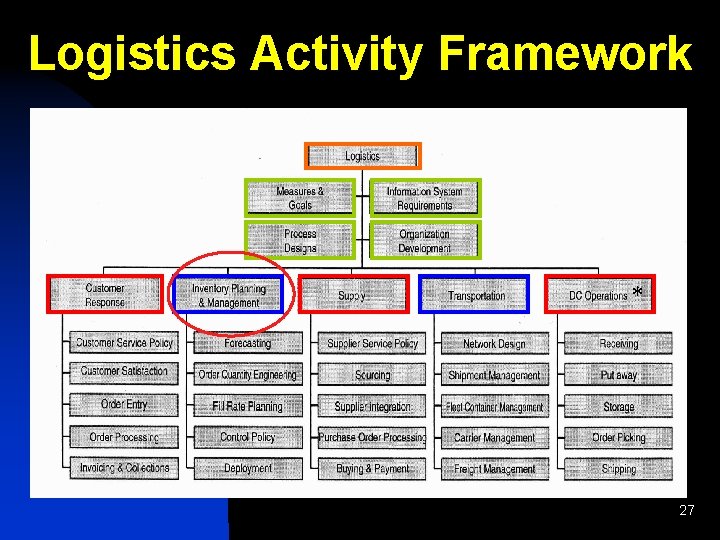
Logistics Activity Framework * 27
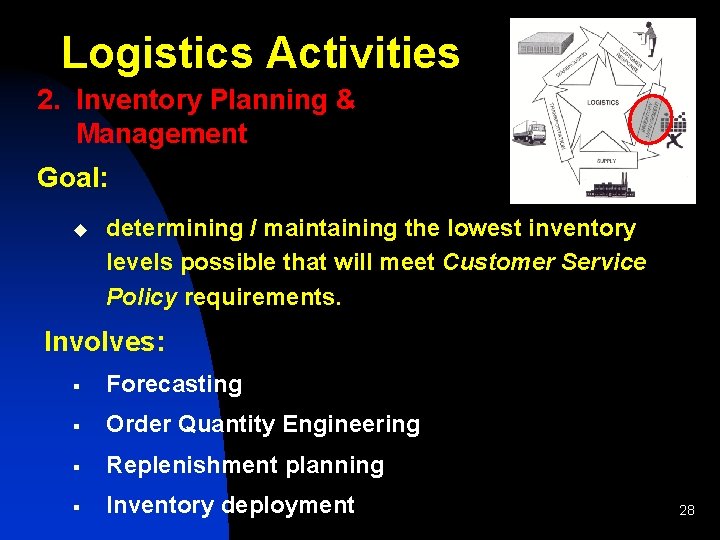
Logistics Activities 2. Inventory Planning & Management Goal: u determining / maintaining the lowest inventory levels possible that will meet Customer Service Policy requirements. Involves: § Forecasting § Order Quantity Engineering § Replenishment planning § Inventory deployment 28
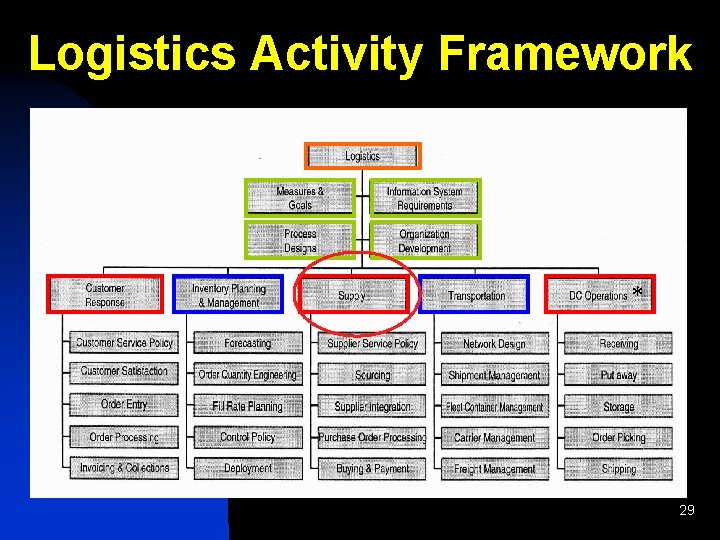
Logistics Activity Framework * 29
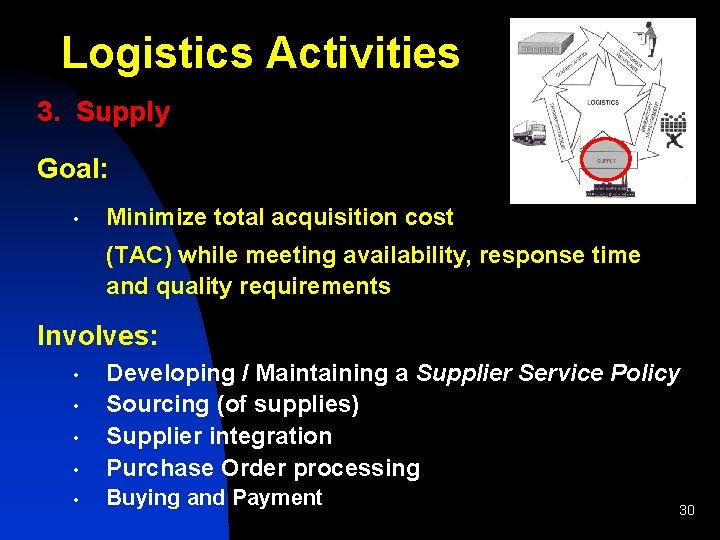
Logistics Activities 3. Supply Goal: • Minimize total acquisition cost (TAC) while meeting availability, response time and quality requirements Involves: • Developing / Maintaining a Supplier Service Policy Sourcing (of supplies) Supplier integration Purchase Order processing • Buying and Payment • • • 30
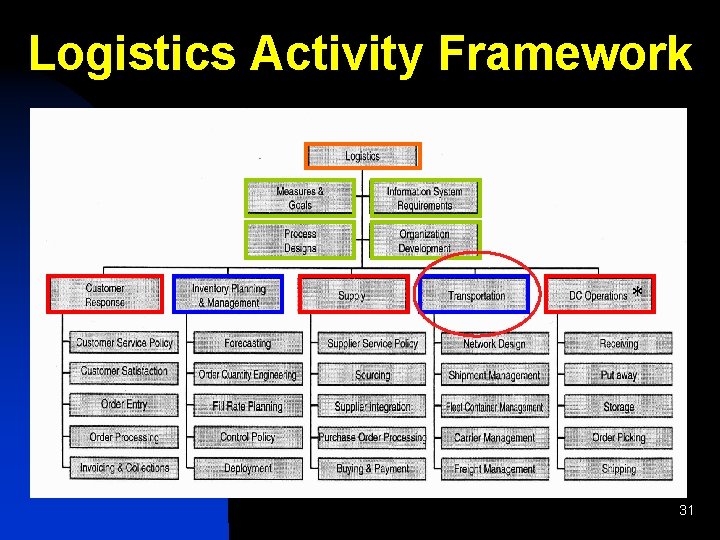
Logistics Activity Framework * 31
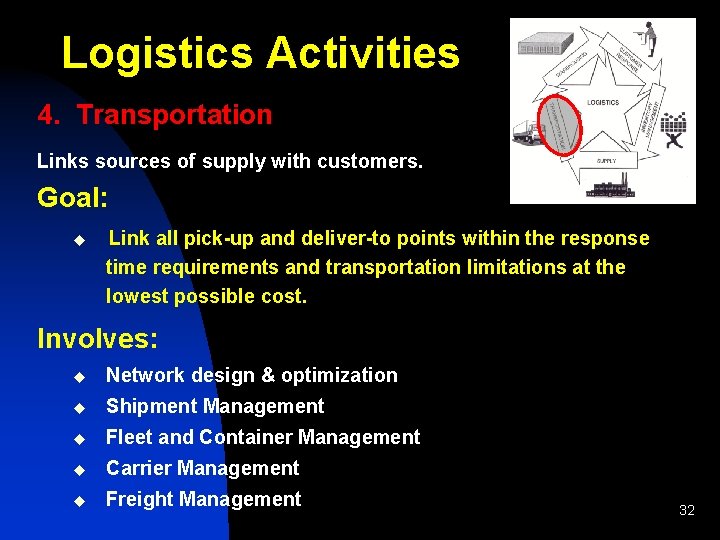
Logistics Activities 4. Transportation Links sources of supply with customers. Goal: u Link all pick-up and deliver-to points within the response time requirements and transportation limitations at the lowest possible cost. Involves: u Network design & optimization u Shipment Management u Fleet and Container Management u Carrier Management u Freight Management 32
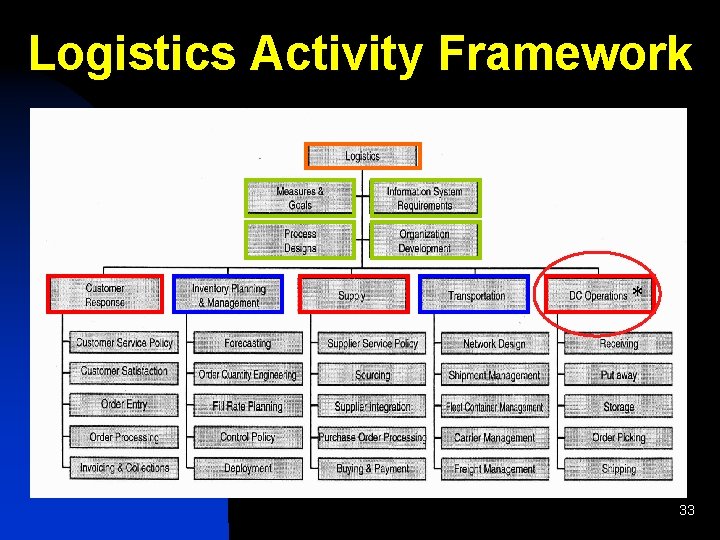
Logistics Activity Framework * 33
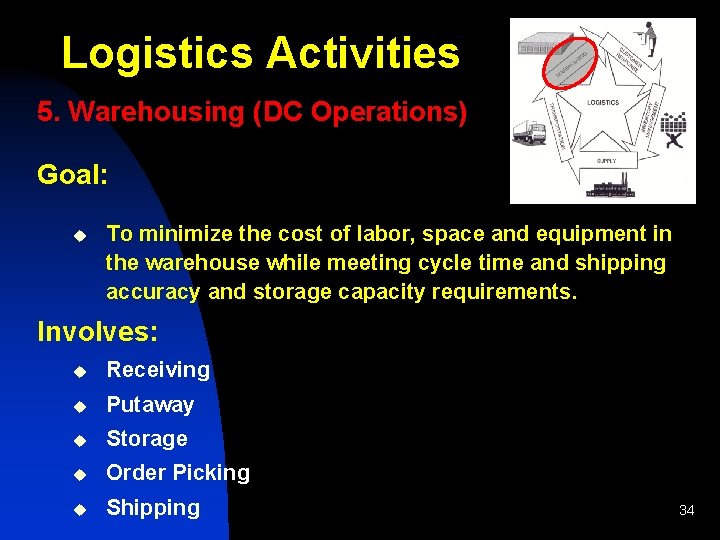
Logistics Activities 5. Warehousing (DC Operations) Goal: u To minimize the cost of labor, space and equipment in the warehouse while meeting cycle time and shipping accuracy and storage capacity requirements. Involves: u Receiving u Putaway u Storage u Order Picking u Shipping 34
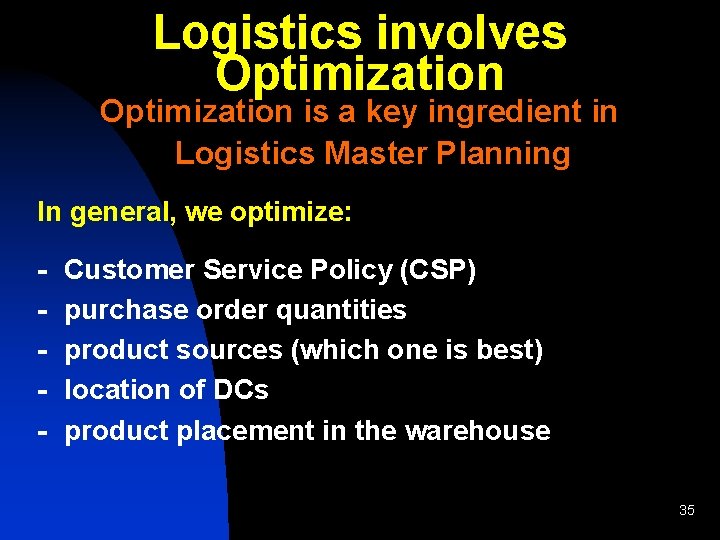
Logistics involves Optimization is a key ingredient in Logistics Master Planning In general, we optimize: - Customer Service Policy (CSP) purchase order quantities product sources (which one is best) location of DCs product placement in the warehouse 35
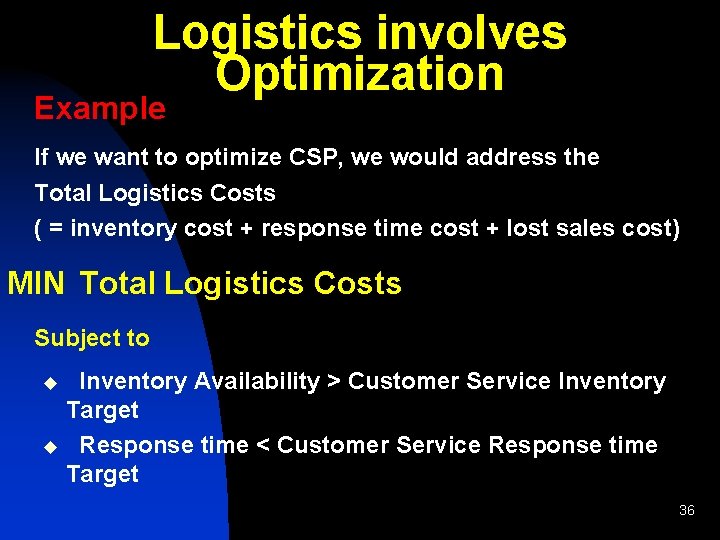
Logistics involves Optimization Example If we want to optimize CSP, we would address the Total Logistics Costs ( = inventory cost + response time cost + lost sales cost) MIN Total Logistics Costs Subject to Inventory Availability > Customer Service Inventory Target u Response time < Customer Service Response time Target u 36
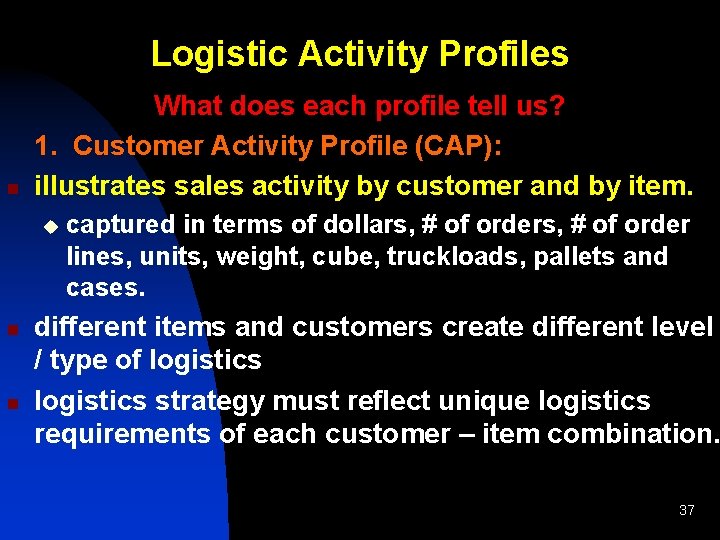
Logistic Activity Profiles n What does each profile tell us? 1. Customer Activity Profile (CAP): illustrates sales activity by customer and by item. u n n captured in terms of dollars, # of order lines, units, weight, cube, truckloads, pallets and cases. different items and customers create different level / type of logistics strategy must reflect unique logistics requirements of each customer – item combination. 37
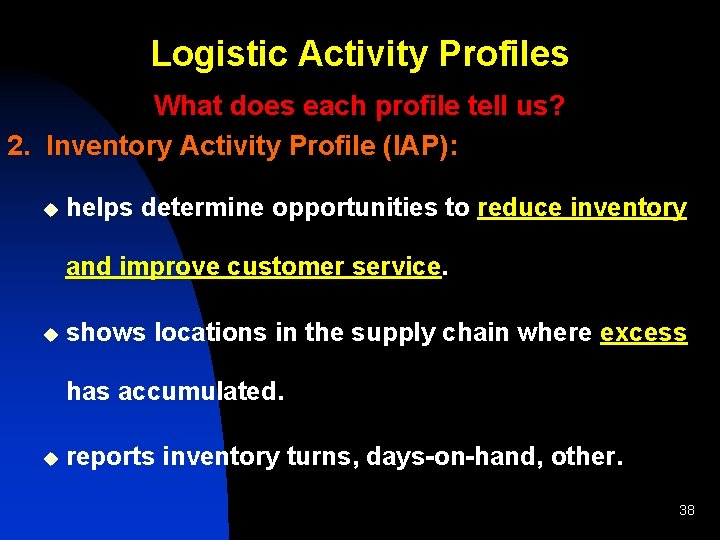
Logistic Activity Profiles What does each profile tell us? 2. Inventory Activity Profile (IAP): u helps determine opportunities to reduce inventory and improve customer service. u shows locations in the supply chain where excess has accumulated. u reports inventory turns, days-on-hand, other. 38
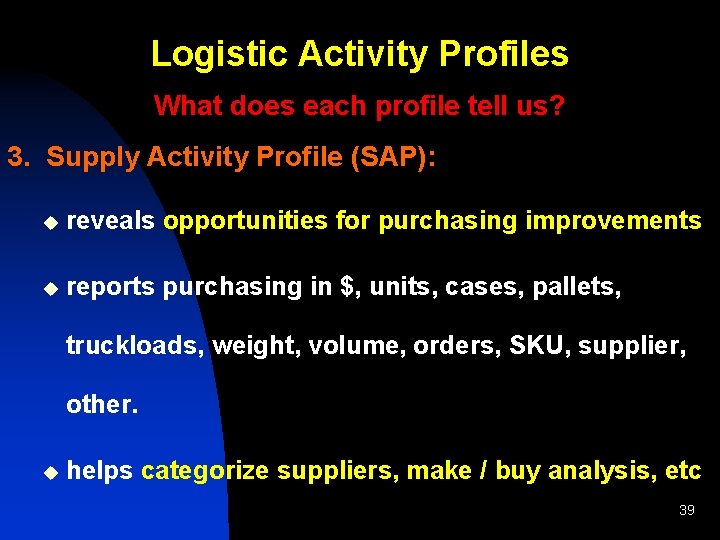
Logistic Activity Profiles What does each profile tell us? 3. Supply Activity Profile (SAP): u reveals opportunities for purchasing improvements u reports purchasing in $, units, cases, pallets, truckloads, weight, volume, orders, SKU, supplier, other. u helps categorize suppliers, make / buy analysis, etc 39
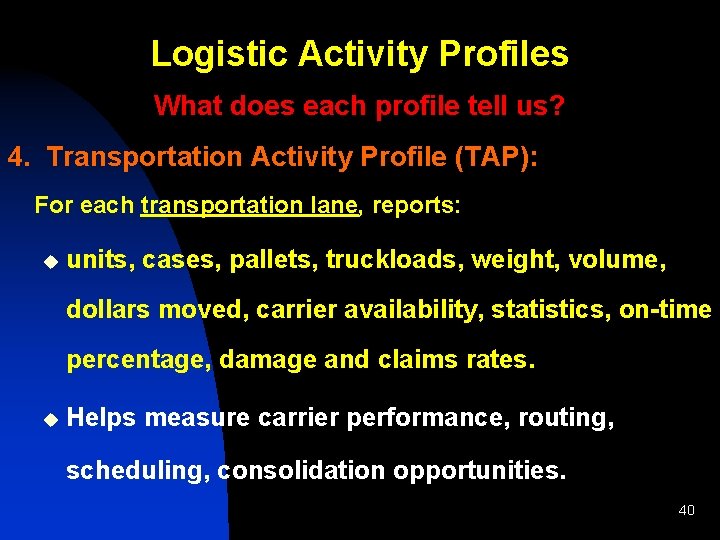
Logistic Activity Profiles What does each profile tell us? 4. Transportation Activity Profile (TAP): For each transportation lane, reports: u units, cases, pallets, truckloads, weight, volume, dollars moved, carrier availability, statistics, on-time percentage, damage and claims rates. u Helps measure carrier performance, routing, scheduling, consolidation opportunities. 40
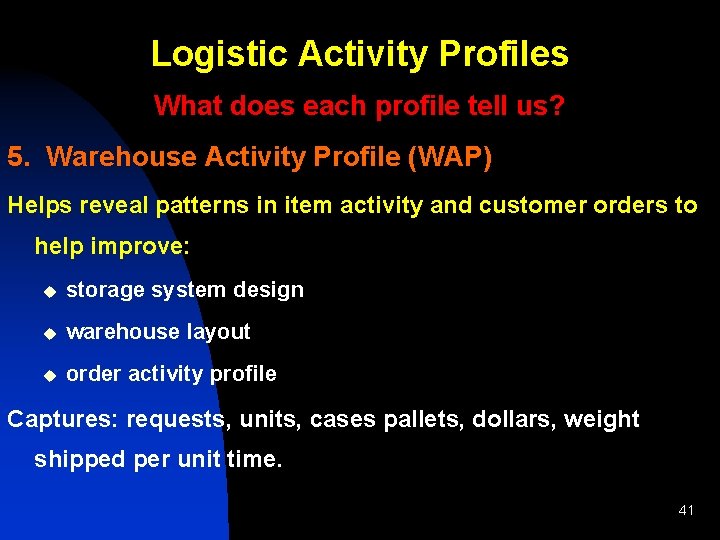
Logistic Activity Profiles What does each profile tell us? 5. Warehouse Activity Profile (WAP) Helps reveal patterns in item activity and customer orders to help improve: u storage system design u warehouse layout u order activity profile Captures: requests, units, cases pallets, dollars, weight shipped per unit time. 41
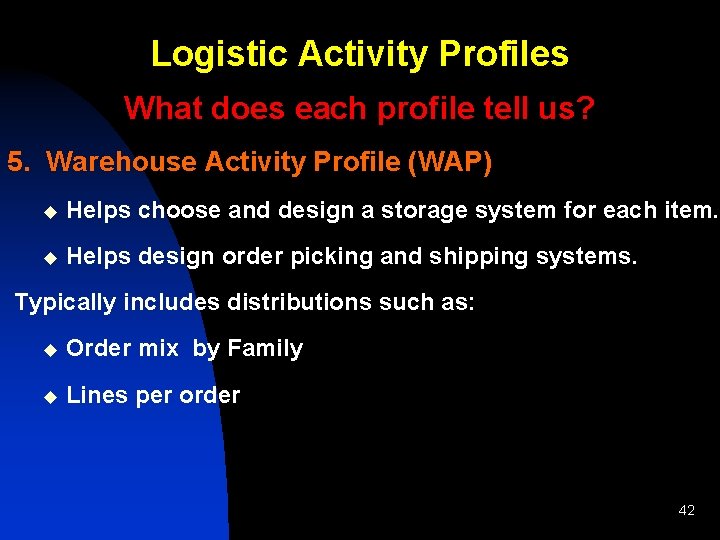
Logistic Activity Profiles What does each profile tell us? 5. Warehouse Activity Profile (WAP) u Helps choose and design a storage system for each item. u Helps design order picking and shipping systems. Typically includes distributions such as: u Order mix by Family u Lines per order 42
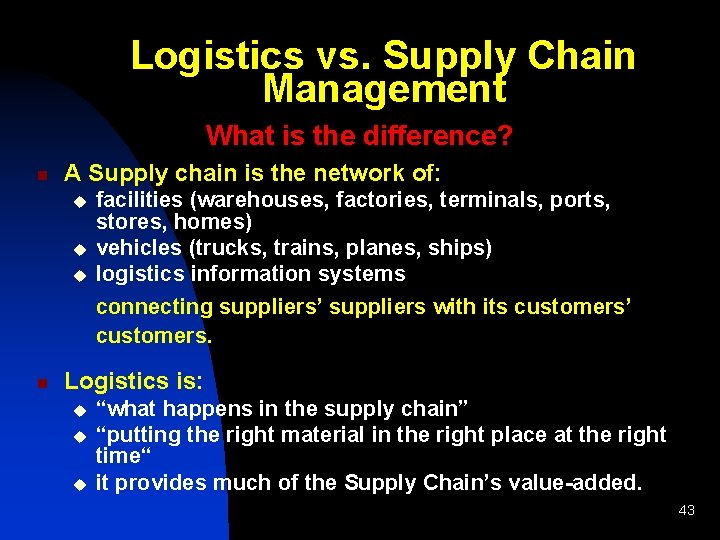
Logistics vs. Supply Chain Management What is the difference? n A Supply chain is the network of: u u u n facilities (warehouses, factories, terminals, ports, stores, homes) vehicles (trucks, trains, planes, ships) logistics information systems connecting suppliers’ suppliers with its customers’ customers. Logistics is: u u u “what happens in the supply chain” “putting the right material in the right place at the right time“ it provides much of the Supply Chain’s value-added. 43
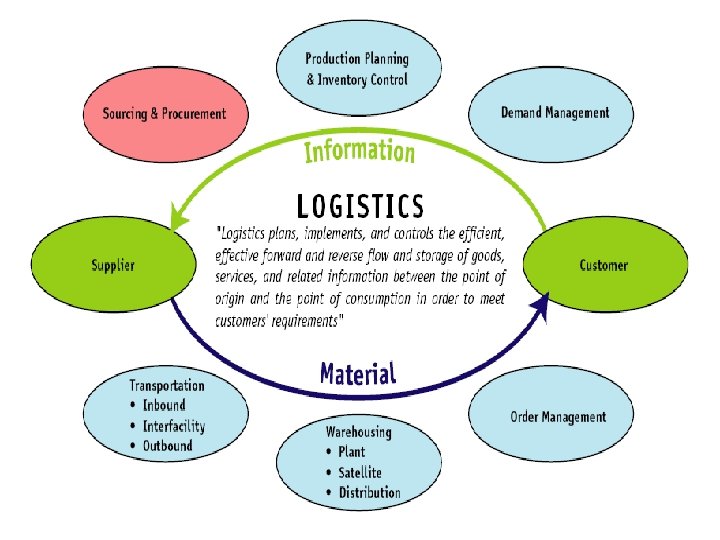
44
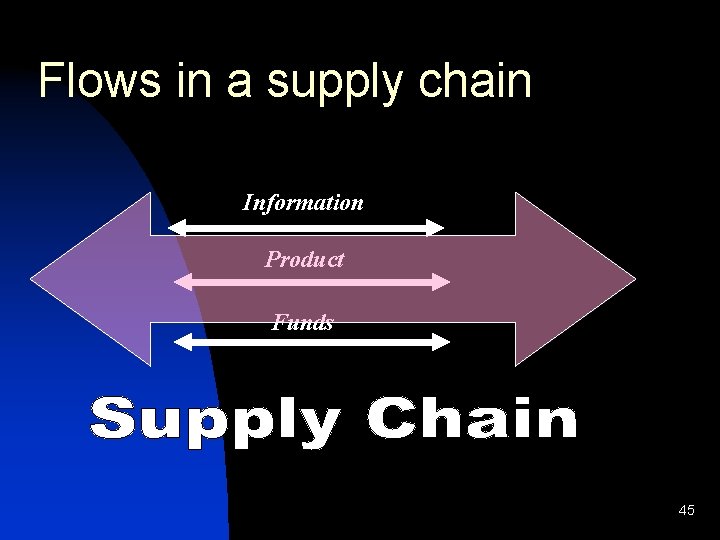
Flows in a supply chain Information Product Funds 45
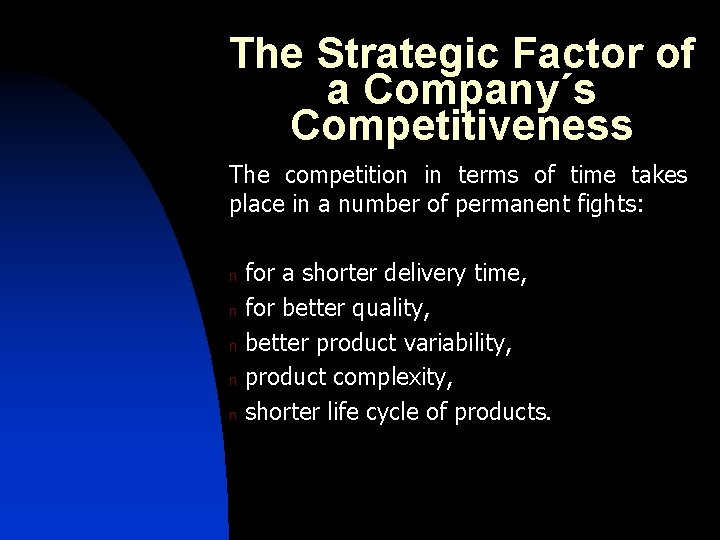
The Strategic Factor of a Company´s Competitiveness The competition in terms of time takes place in a number of permanent fights: n n n for a shorter delivery time, for better quality, better product variability, product complexity, shorter life cycle of products.
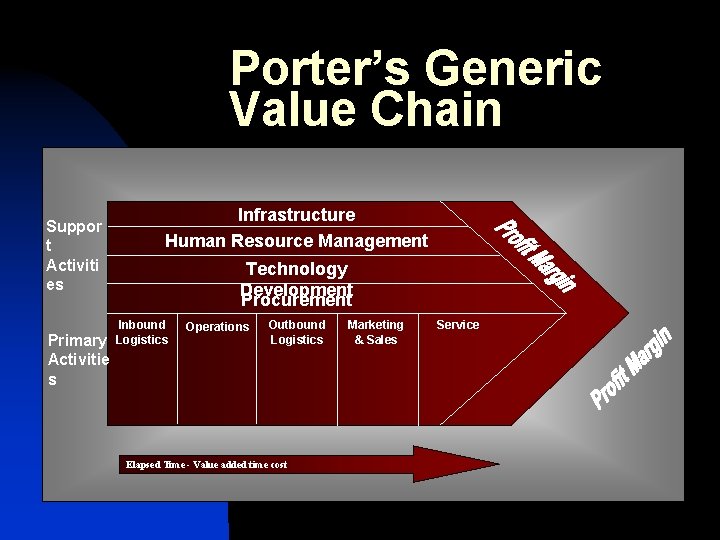
Porter’s Generic Value Chain Suppor t Activiti es Primary Activitie s Infrastructure Human Resource Management Technology Development Procurement Inbound Logistics Operations Outbound Logistics Elapsed Time - Value added time cost Marketing & Sales Service
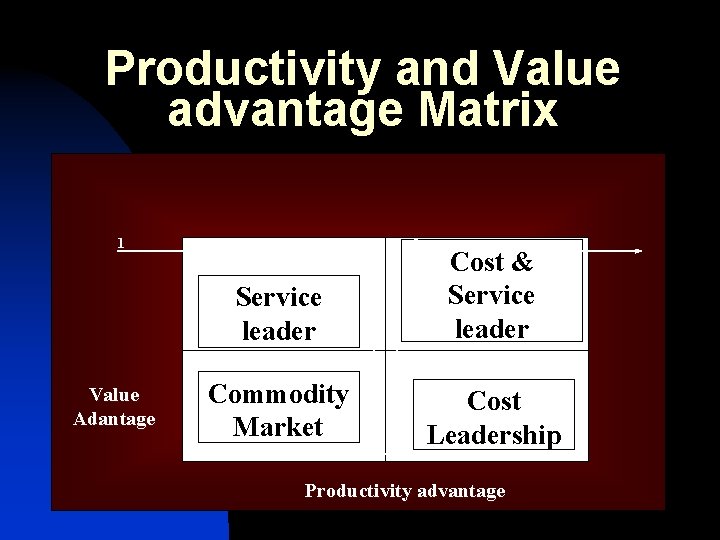
Productivity and Value advantage Matrix 1 5 Service leader Cost & Service leader Commodity Market Cost Leadership 2 Value Adantage 3 4 Productivity advantage
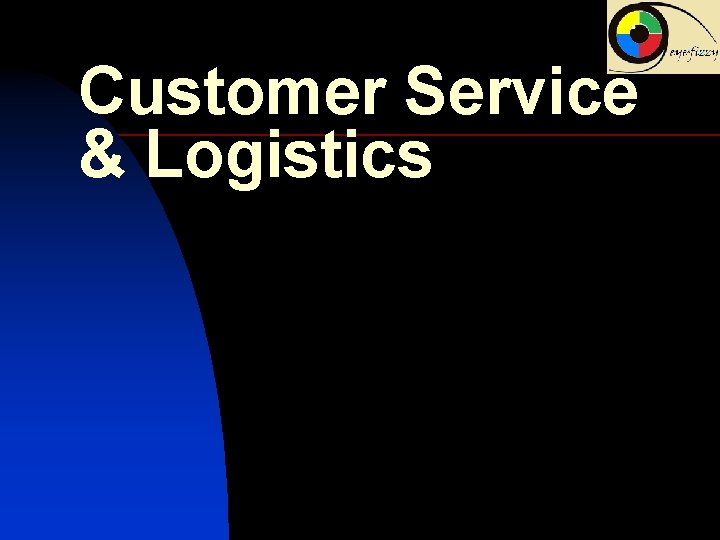
Customer Service & Logistics
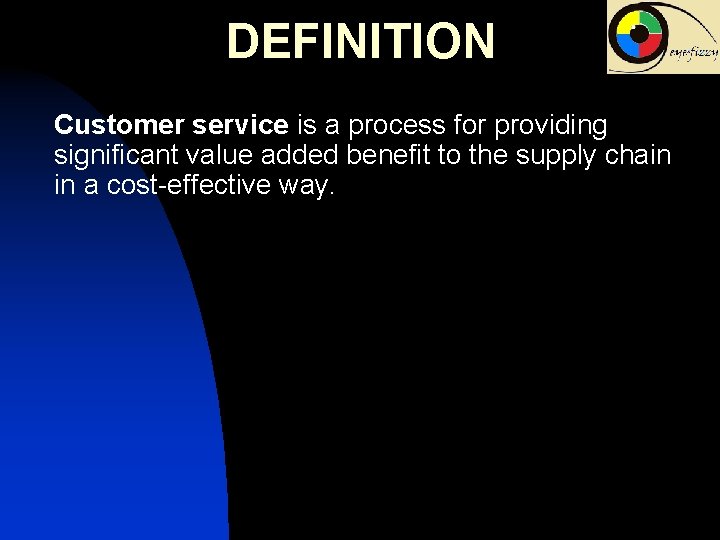
DEFINITION Customer service is a process for providing significant value added benefit to the supply chain in a cost-effective way.
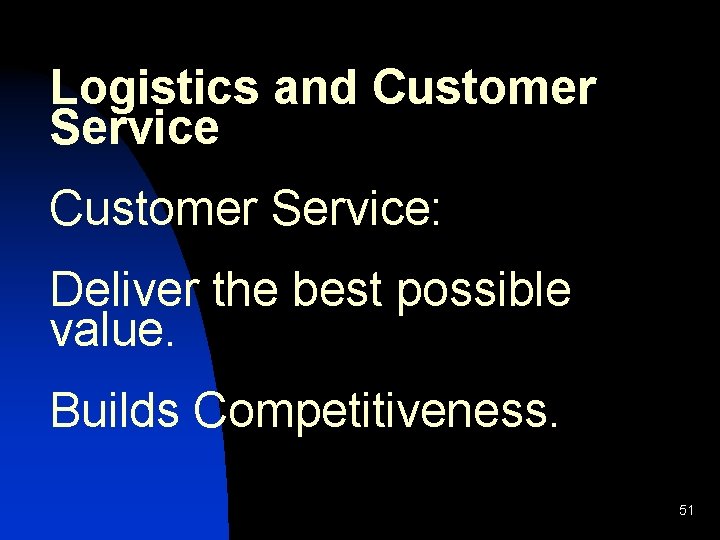
Logistics and Customer Service: Deliver the best possible value. Builds Competitiveness. 51
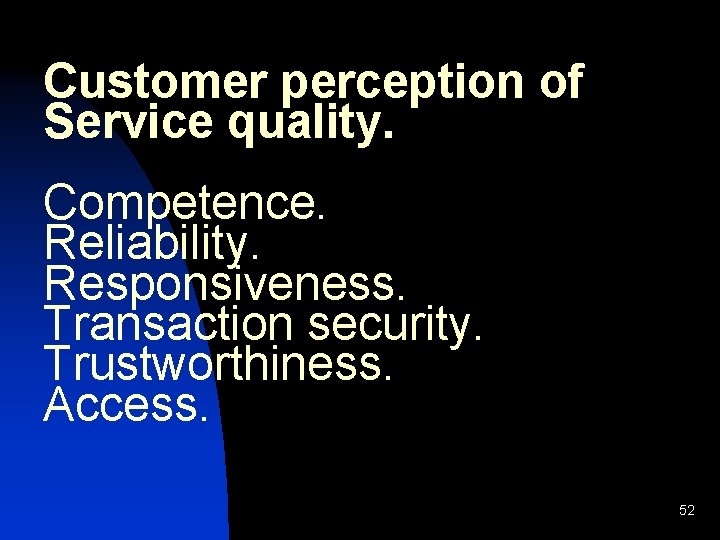
Customer perception of Service quality. Competence. Reliability. Responsiveness. Transaction security. Trustworthiness. Access. 52
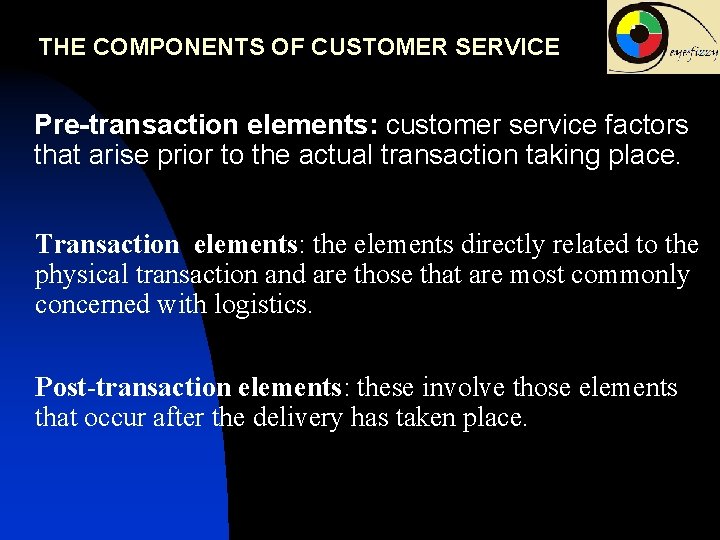
THE COMPONENTS OF CUSTOMER SERVICE Pre-transaction elements: customer service factors that arise prior to the actual transaction taking place. Transaction elements: the elements directly related to the physical transaction and are those that are most commonly concerned with logistics. Post-transaction elements: these involve those elements that occur after the delivery has taken place.
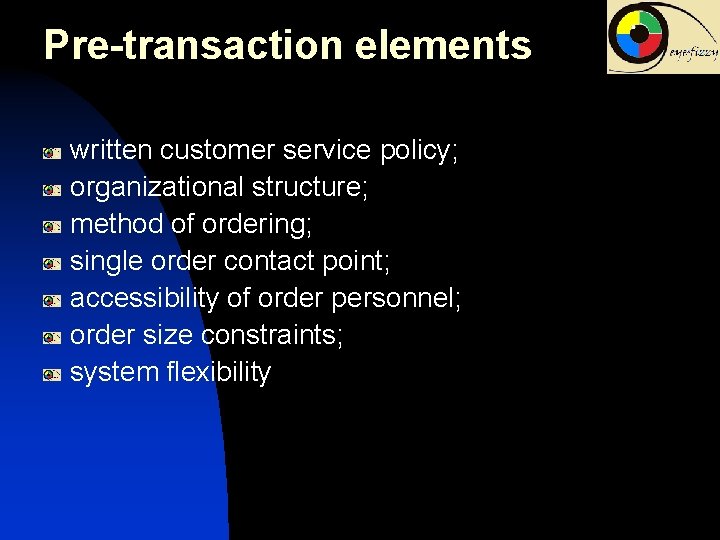
Pre-transaction elements written customer service policy; organizational structure; method of ordering; single order contact point; accessibility of order personnel; order size constraints; system flexibility
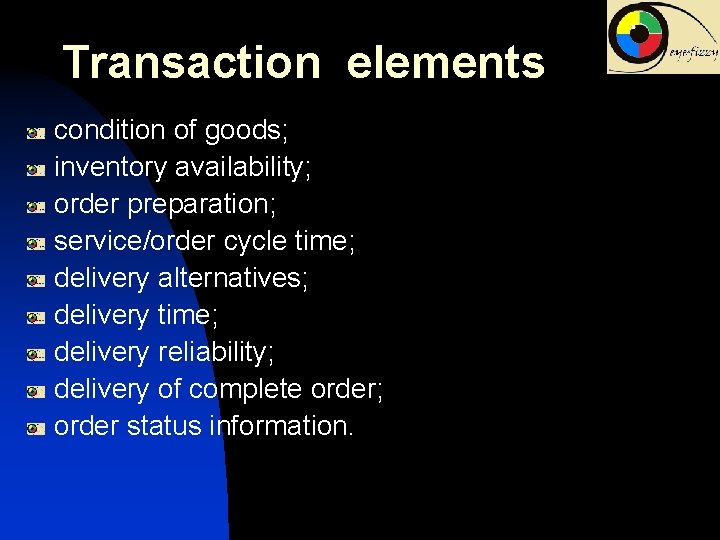
Transaction elements condition of goods; inventory availability; order preparation; service/order cycle time; delivery alternatives; delivery time; delivery reliability; delivery of complete order; order status information.
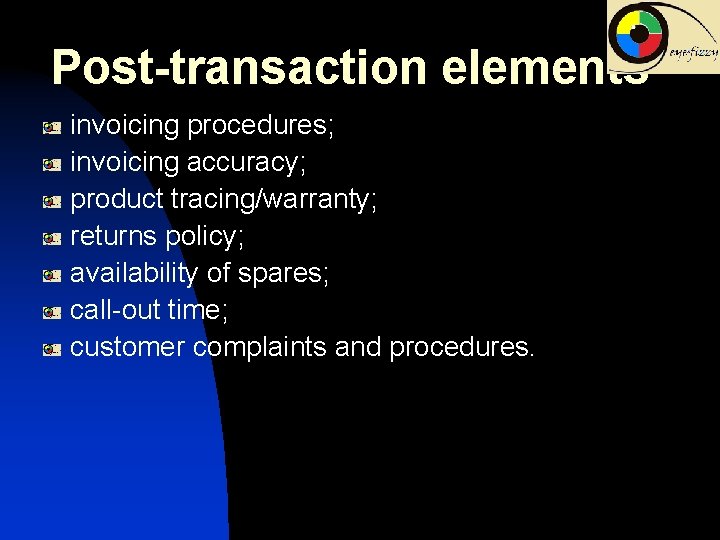
Post-transaction elements invoicing procedures; invoicing accuracy; product tracing/warranty; returns policy; availability of spares; call-out time; customer complaints and procedures.
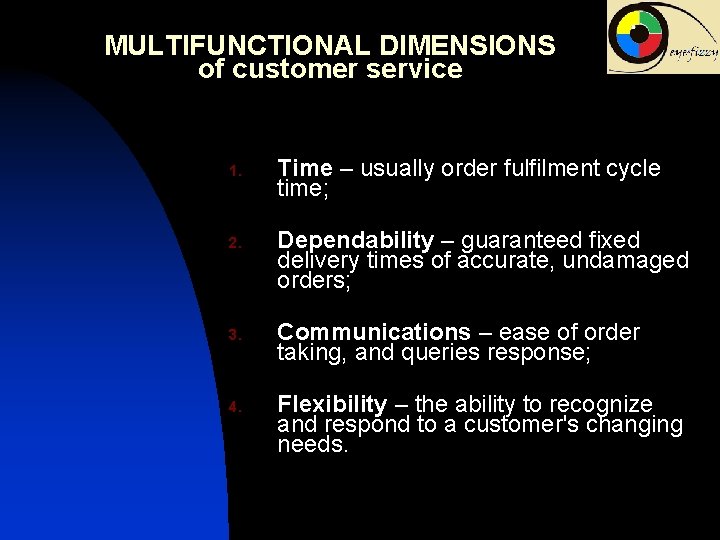
MULTIFUNCTIONAL DIMENSIONS of customer service 1. 2. 3. 4. Time – usually order fulfilment cycle time; Dependability – guaranteed fixed delivery times of accurate, undamaged orders; Communications – ease of order taking, and queries response; Flexibility – the ability to recognize and respond to a customer's changing needs.
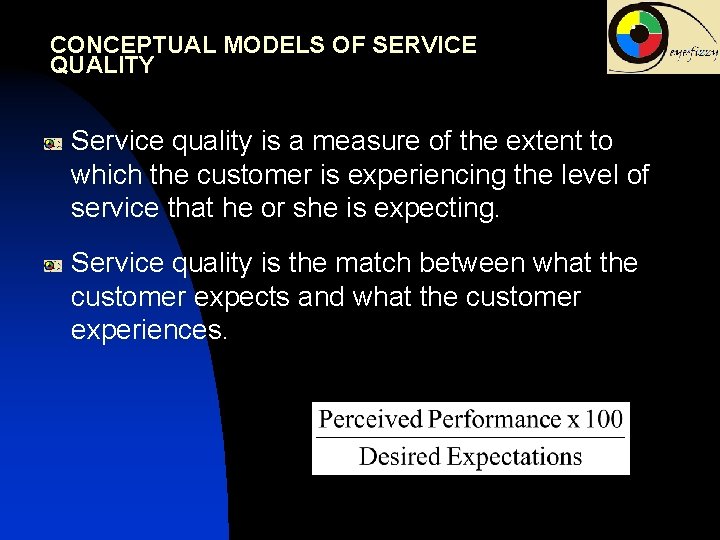
CONCEPTUAL MODELS OF SERVICE QUALITY Service quality is a measure of the extent to which the customer is experiencing the level of service that he or she is expecting. Service quality is the match between what the customer expects and what the customer experiences.
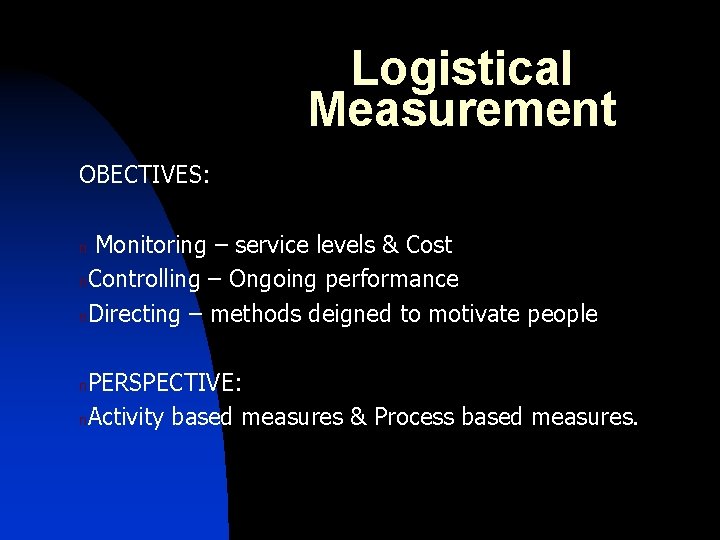
Logistical Measurement OBECTIVES: Monitoring – service levels & Cost n. Controlling – Ongoing performance n. Directing – methods deigned to motivate people n PERSPECTIVE: n. Activity based measures & Process based measures. n
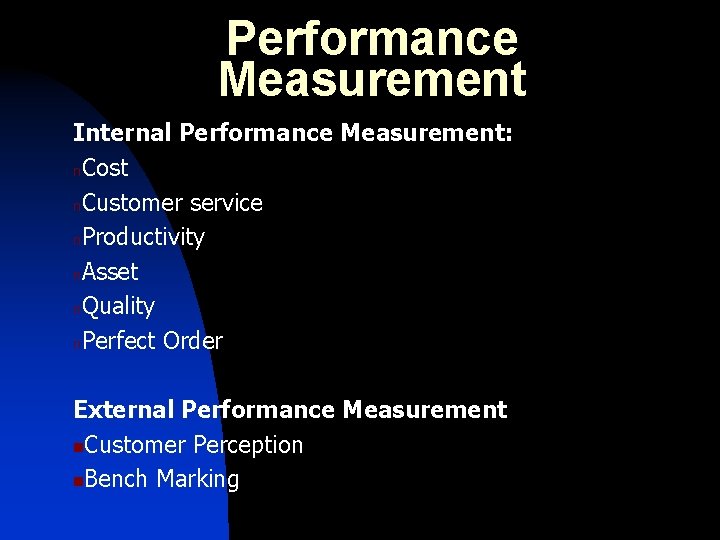
Performance Measurement Internal Performance Measurement: n. Cost n. Customer service n. Productivity n. Asset n. Quality n. Perfect Order External Performance Measurement n. Customer Perception n. Bench Marking
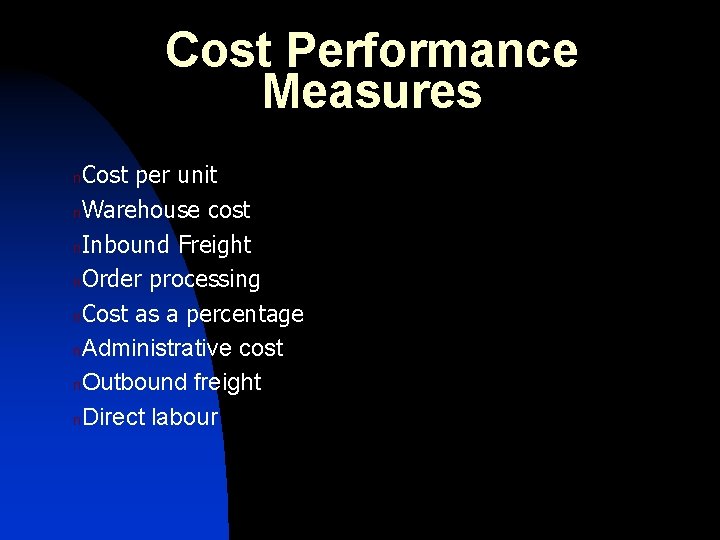
Cost Performance Measures Cost per unit n. Warehouse cost n. Inbound Freight n. Order processing n. Cost as a percentage n. Administrative cost n. Outbound freight n. Direct labour n
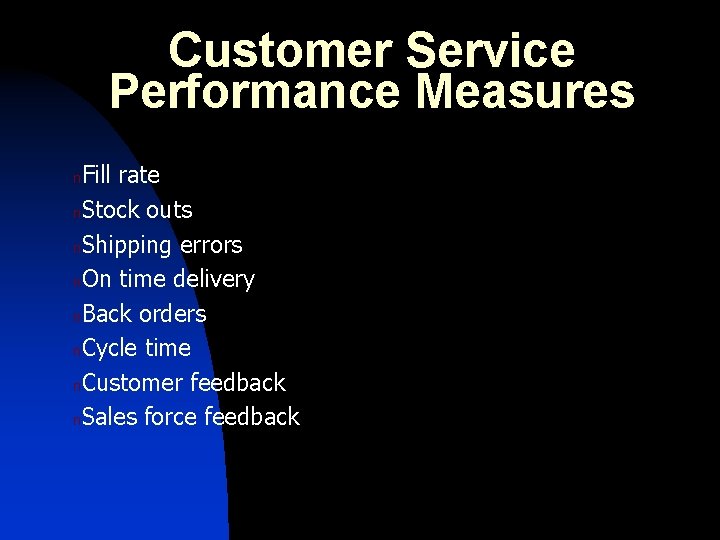
Customer Service Performance Measures Fill rate n. Stock outs n. Shipping errors n. On time delivery n. Back orders n. Cycle time n. Customer feedback n. Sales force feedback n
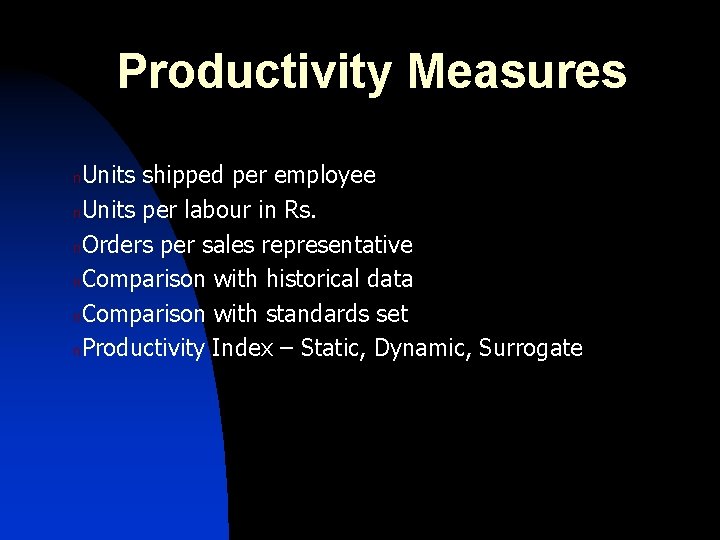
Productivity Measures Units shipped per employee n. Units per labour in Rs. n. Orders per sales representative n. Comparison with historical data n. Comparison with standards set n. Productivity Index – Static, Dynamic, Surrogate n
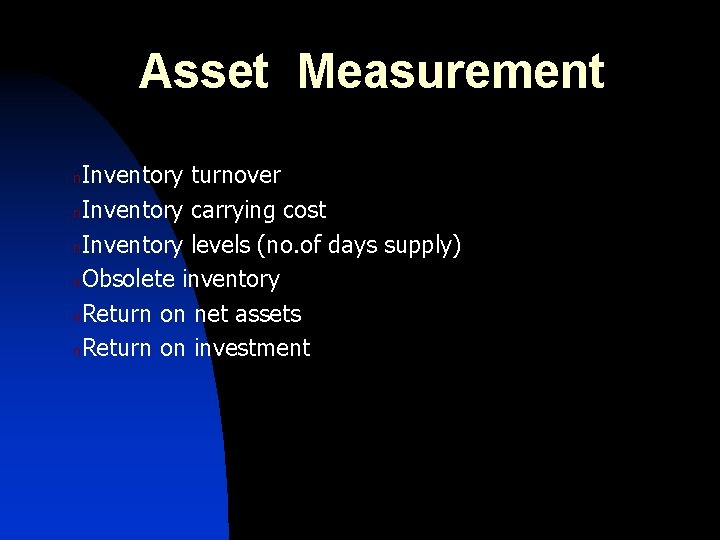
Asset Measurement Inventory turnover n. Inventory carrying cost n. Inventory levels (no. of days supply) n. Obsolete inventory n. Return on net assets n. Return on investment n
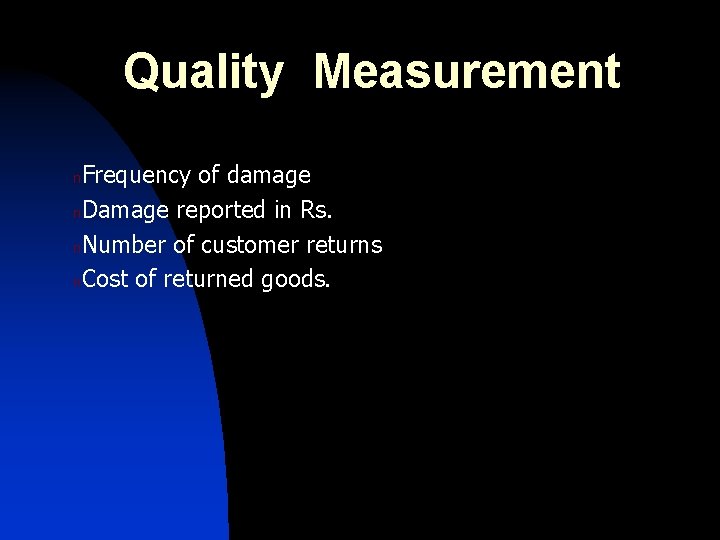
Quality Measurement Frequency of damage n. Damage reported in Rs. n. Number of customer returns n. Cost of returned goods. n
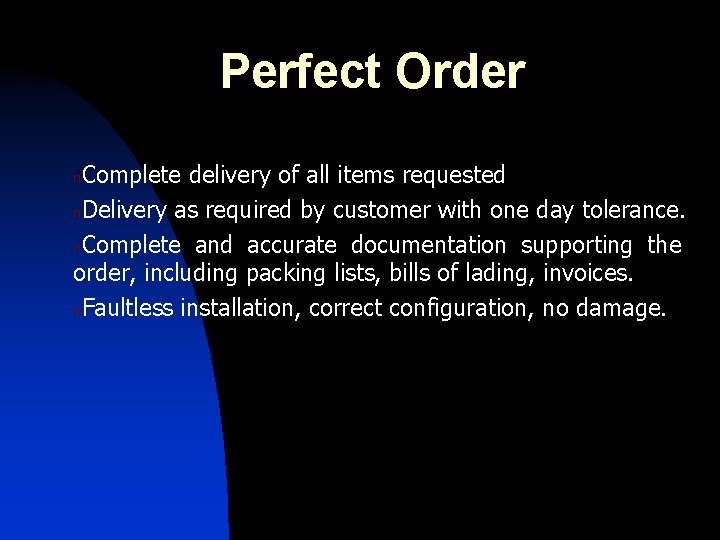
Perfect Order Complete delivery of all items requested n. Delivery as required by customer with one day tolerance. n. Complete and accurate documentation supporting the order, including packing lists, bills of lading, invoices. n. Faultless installation, correct configuration, no damage. n
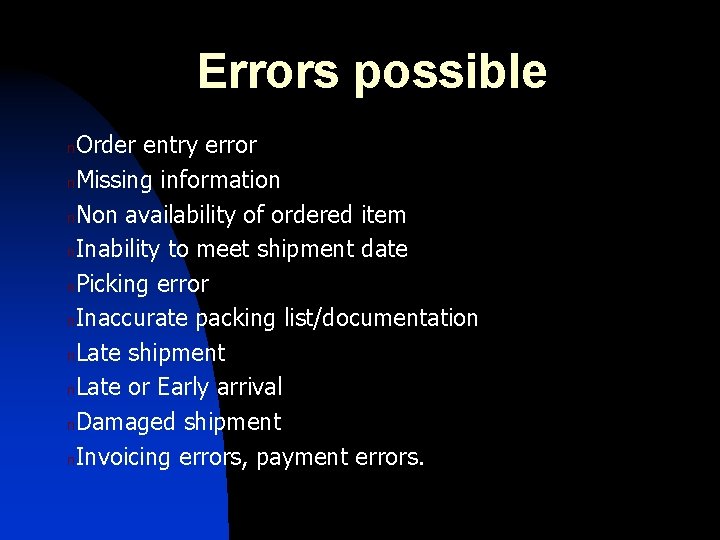
Errors possible Order entry error n. Missing information n. Non availability of ordered item n. Inability to meet shipment date n. Picking error n. Inaccurate packing list/documentation n. Late shipment n. Late or Early arrival n. Damaged shipment n. Invoicing errors, payment errors. n
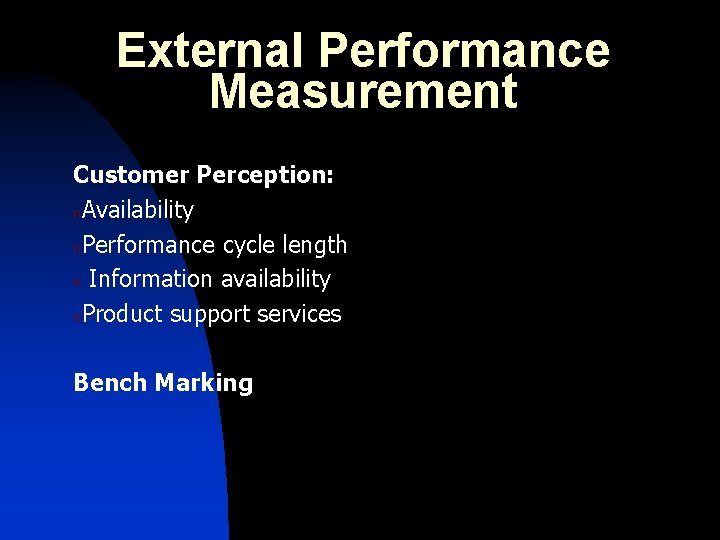
External Performance Measurement Customer Perception: n. Availability n. Performance cycle length n Information availability n. Product support services Bench Marking