Leak Tester The EPS Electronic Power Steering drive
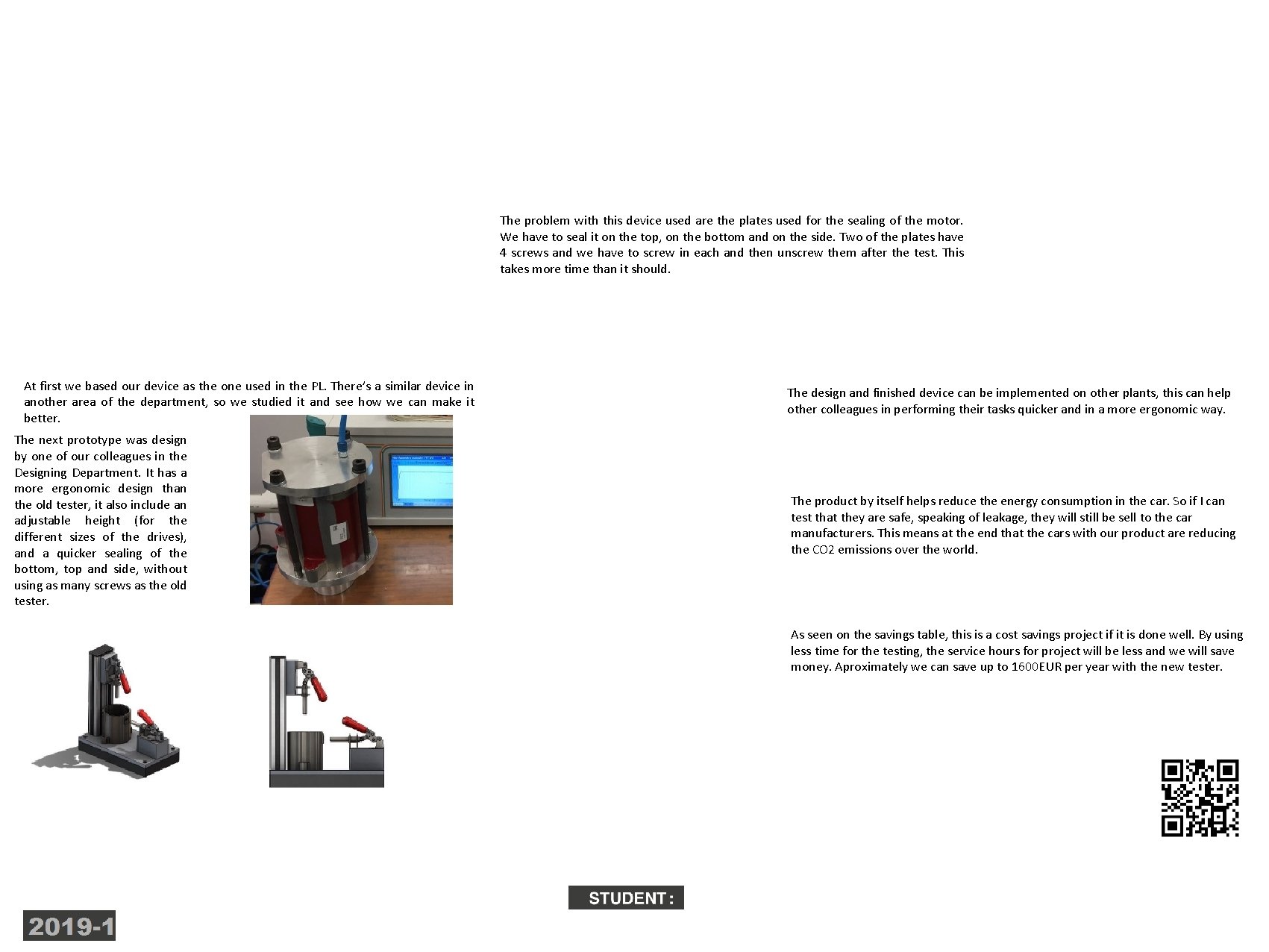
- Slides: 1
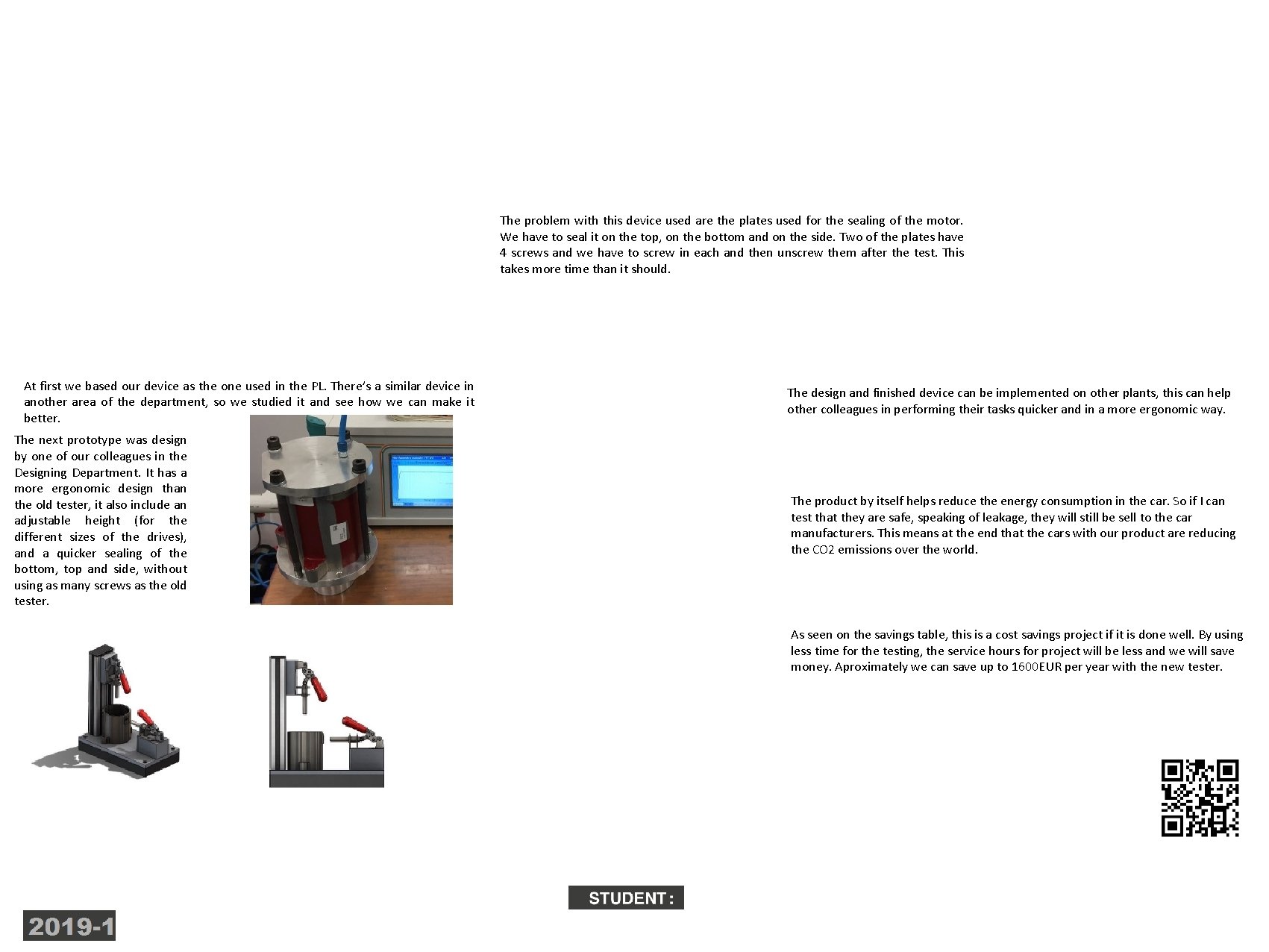
Leak Tester The EPS (Electronic Power Steering) drive is part of the power steering movement of the driver. Since the steering is a safety-relevant system, this motor should ensure utmost reliability and operating life. Therefore, one of the most important tasks is to ensure that the motor doesn’t have a leak area on its surface. If a liquid or a fine solid leaks into the drive, the drive may fail, thus compromising the safety the driver and passengers. Our goal is to develop a better leak tester than the one we have, so we can test with the same insurance than the one in the production line, but in a quicker and more efficient way. Keywords: Steering, Drive, Safety, Leak Tester. The problem with this device used are the plates used for the sealing of the motor. We have to seal it on the top, on the bottom and on the side. Two of the plates have 4 screws and we have to screw in each and then unscrew them after the test. This takes more time than it should. At first we based our device as the one used in the PL. There’s a similar device in another area of the department, so we studied it and see how we can make it better. NOR-BN-591048 -102 -Englisch The design and finished device can be implemented on other plants, this can help other colleagues in performing their tasks quicker and in a more ergonomic way. The next prototype was design by one of our colleagues in the Designing Department. It has a more ergonomic design than the old tester, it also include an adjustable height (for the different sizes of the drives), and a quicker sealing of the bottom, top and side, without using as many screws as the old tester. The product by itself helps reduce the energy consumption in the car. So if I can test that they are safe, speaking of leakage, they will still be sell to the car manufacturers. This means at the end that the cars with our product are reducing the CO 2 emissions over the world. As seen on the savings table, this is a cost savings project if it is done well. By using less time for the testing, the service hours for project will be less and we will save money. Aproximately we can save up to 1600 EUR per year with the new tester. • General Objective: Develop a vibrationmeasuring system on a final assembly machine to determine, using DFT, whether the assembled product is within the acceptable quality standards regarding noise. • Hypothesis: It is possible to observe a difference between a proper car-window elevator and a deficient one when being assembled, by applying DFT to a set of measurements by a 3 axis accelerometer attached to the stator. https: //electronics. howstuffworks. com/brushless-motor. htm https: //www. innomatec. com/products/leaktester/overview-leaktester/ltc-602 https: //www. viatran. com/static/media/uploads/technical_articles_notes/leak_ detection_through_pressure_decay_tech_note. pdf Guerra Guevara Luis Eduardo Exp. 246871