Index Overview Wet etchDry etch Etch characteristics requirements
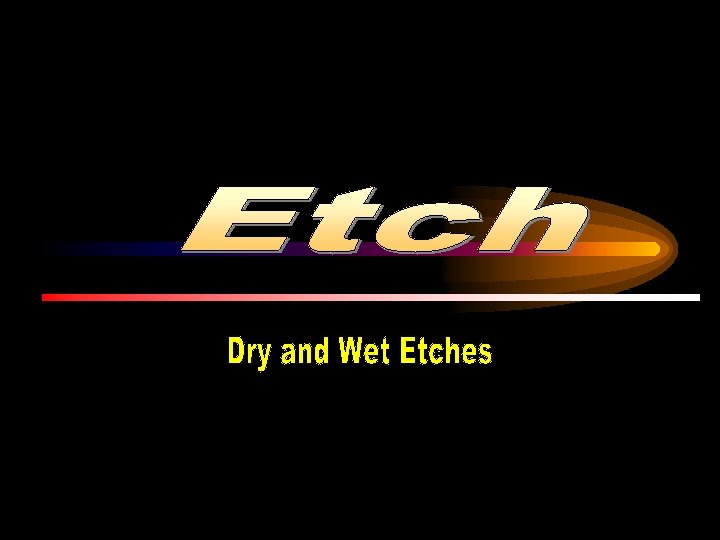
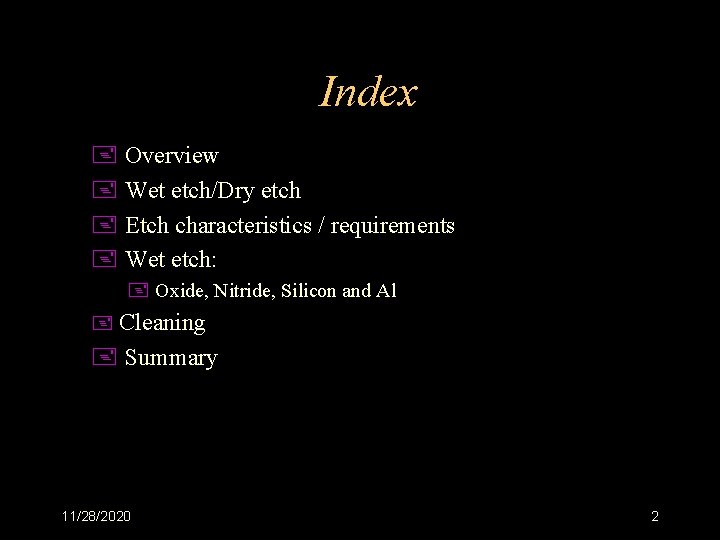
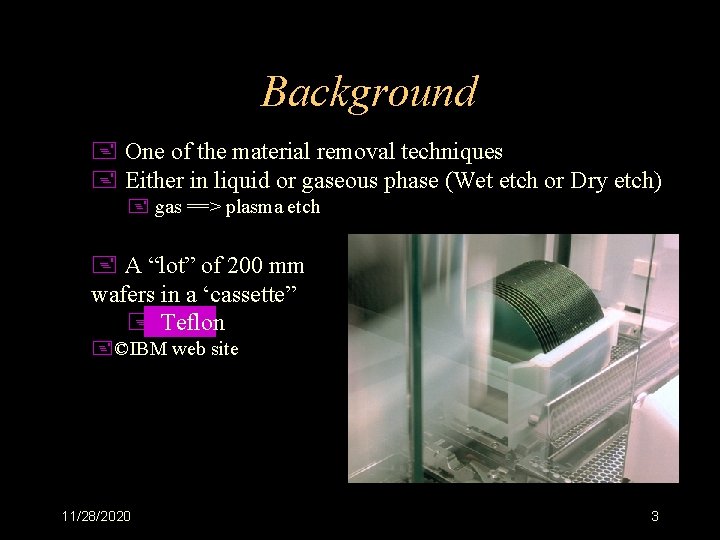
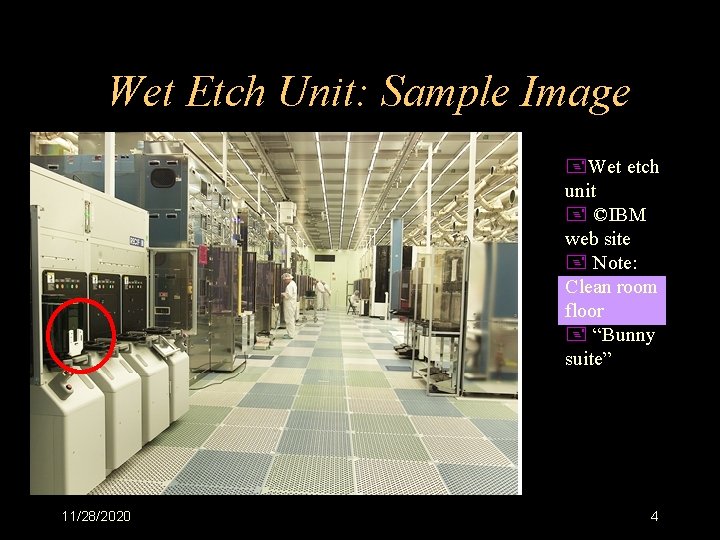
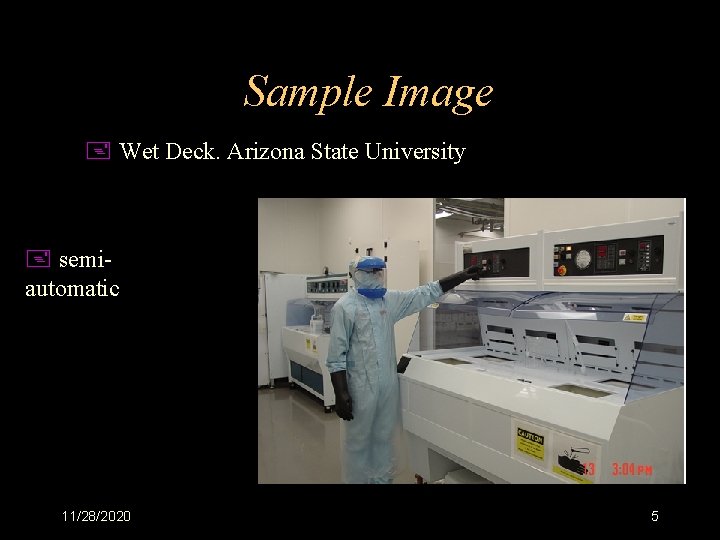
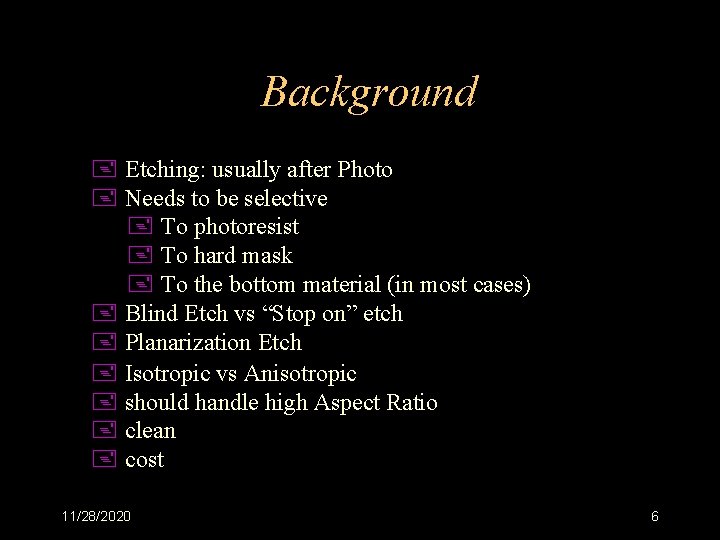
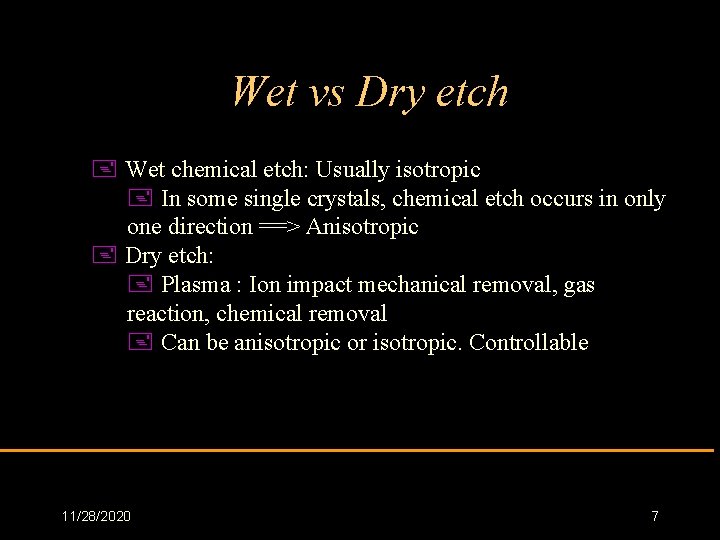
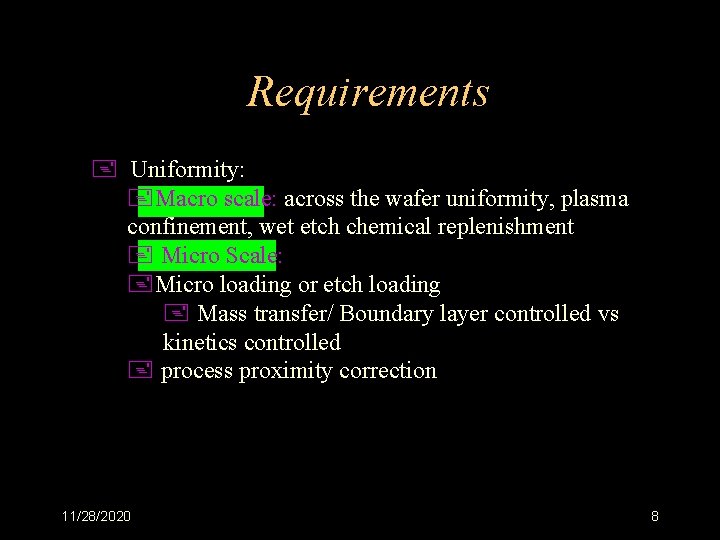
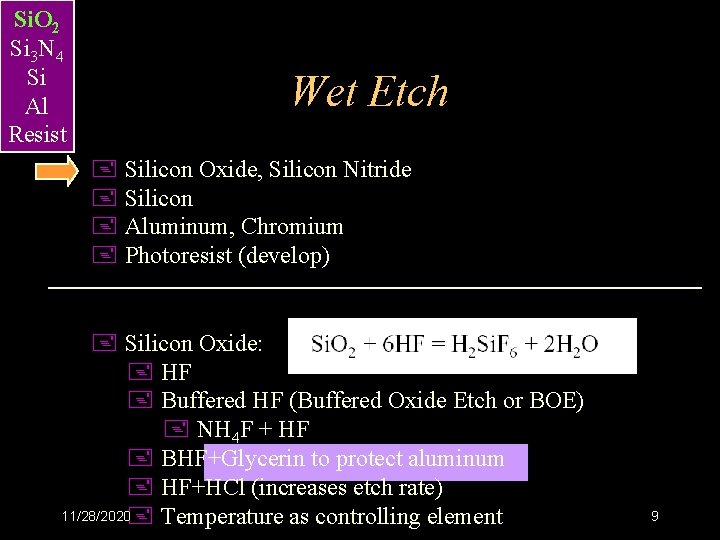

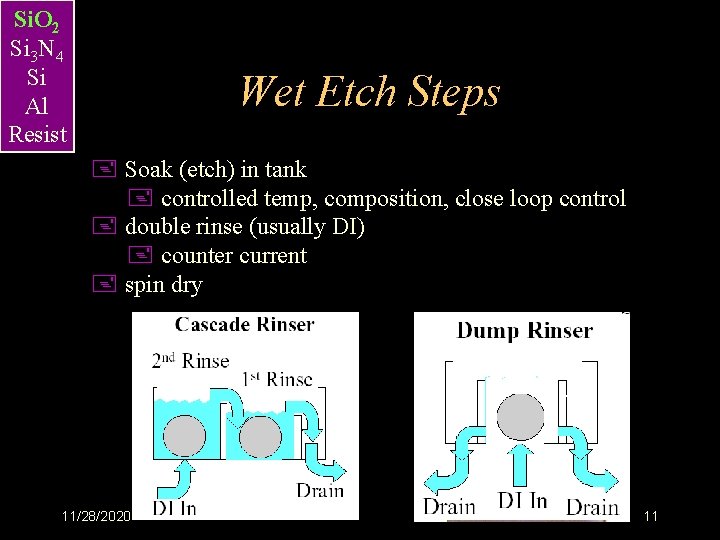
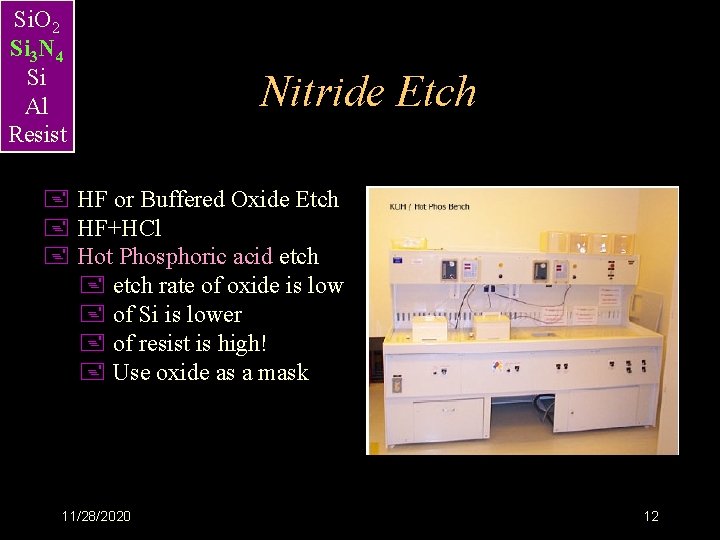
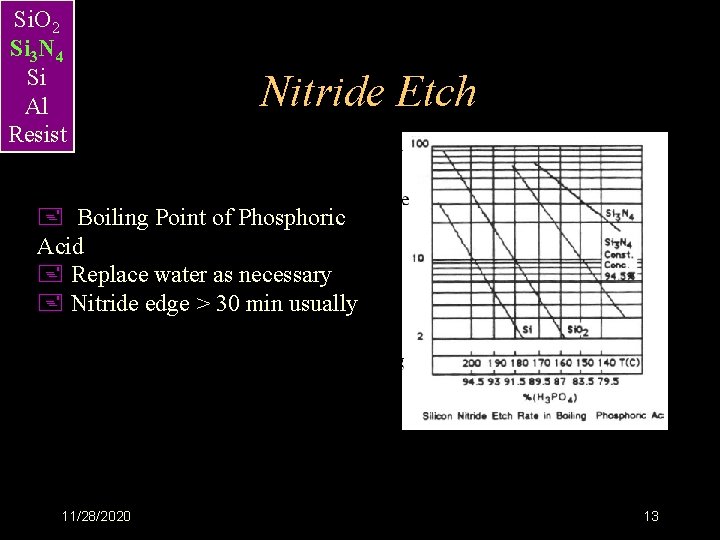
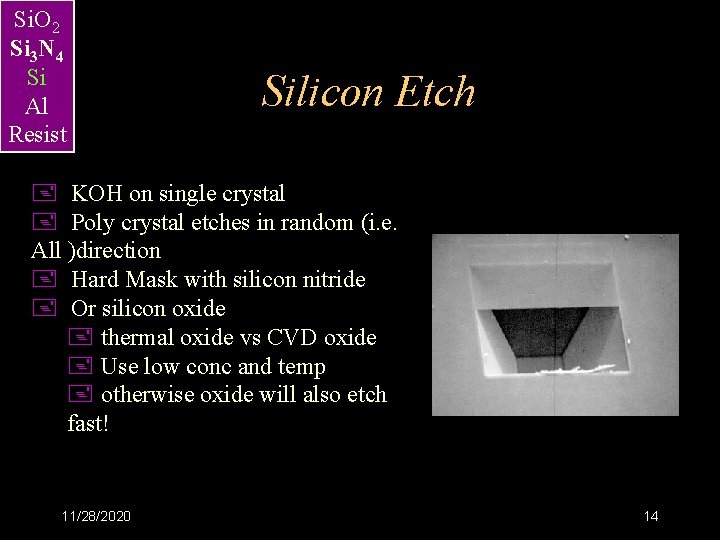
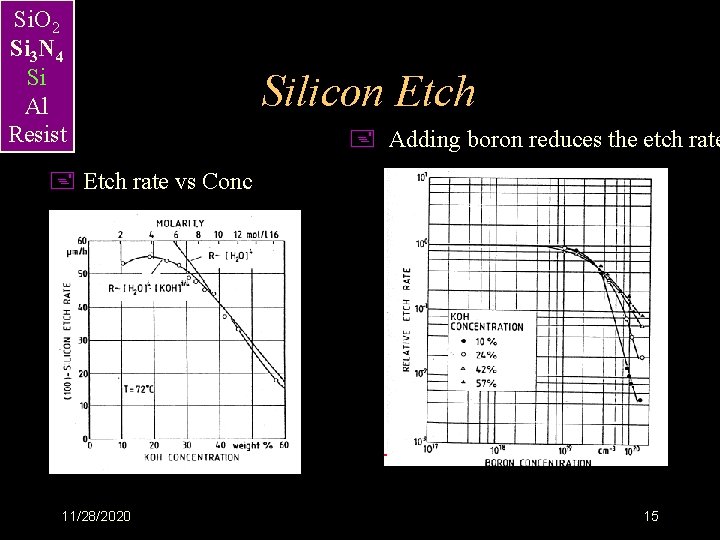
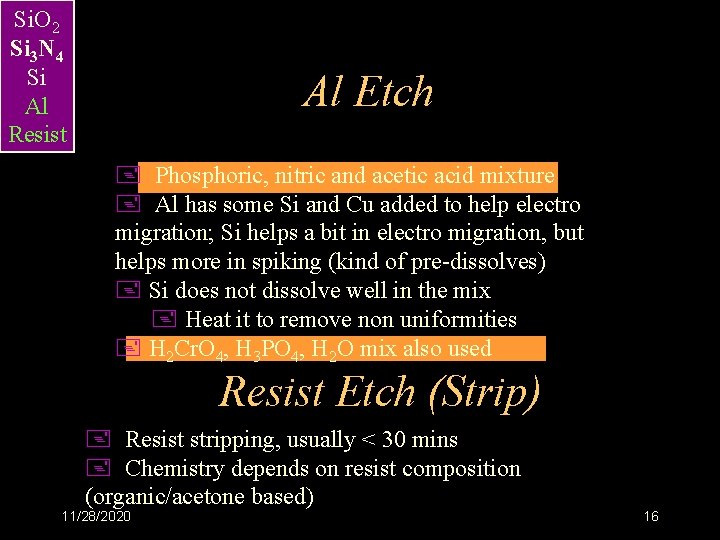
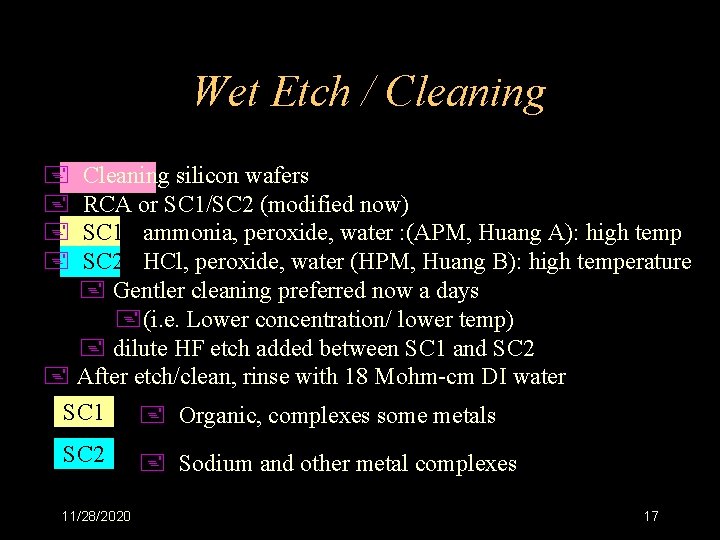

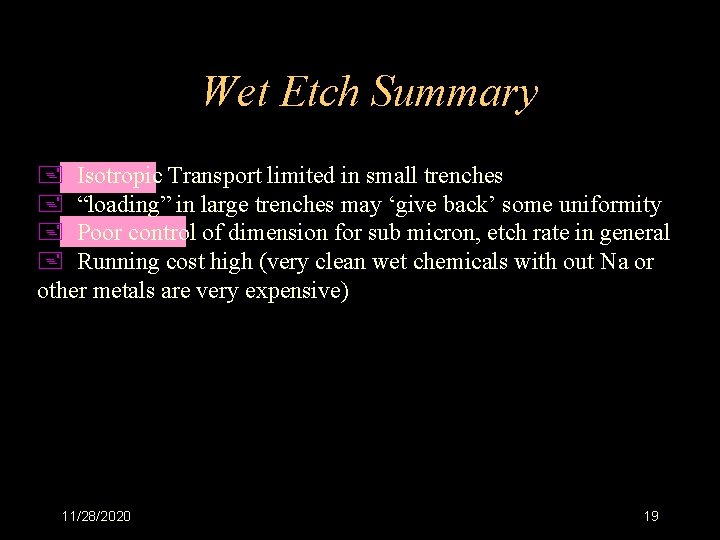
- Slides: 19
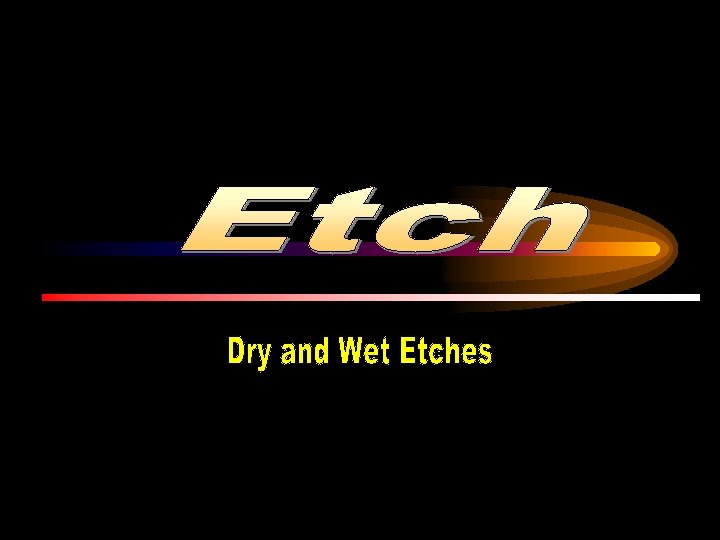
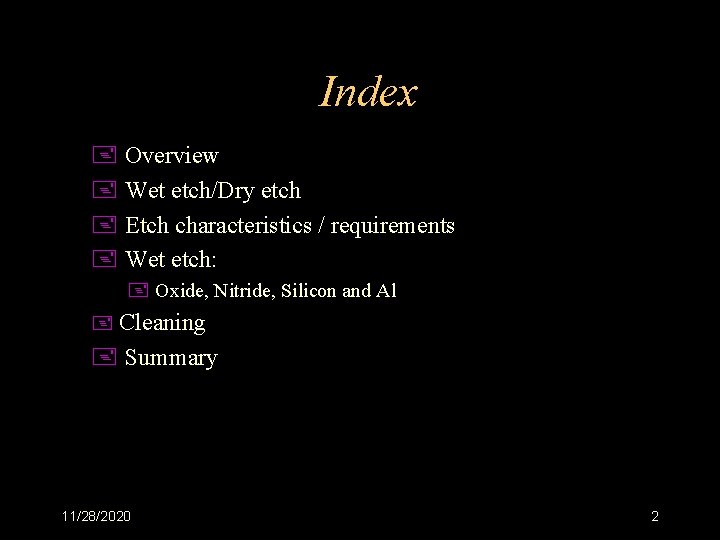
Index + Overview + Wet etch/Dry etch + Etch characteristics / requirements + Wet etch: + Oxide, Nitride, Silicon and Al + Cleaning + Summary 11/28/2020 2
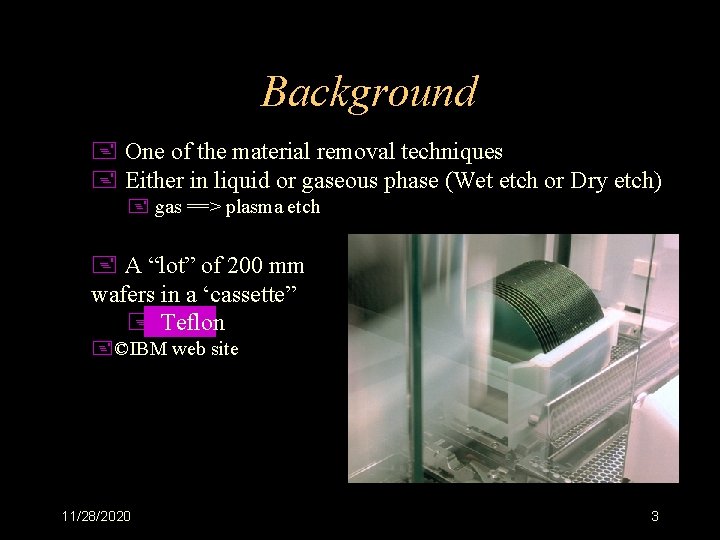
Background + One of the material removal techniques + Either in liquid or gaseous phase (Wet etch or Dry etch) + gas ==> plasma etch + A “lot” of 200 mm wafers in a ‘cassette” + Teflon +©IBM web site 11/28/2020 3
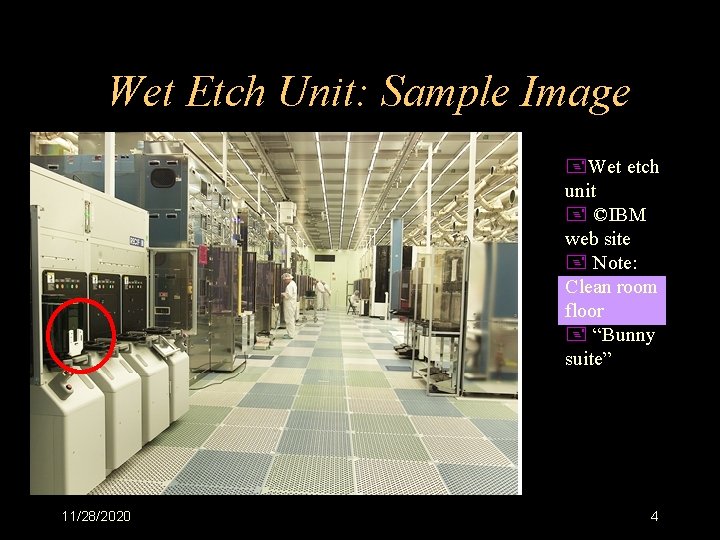
Wet Etch Unit: Sample Image +Wet etch unit + ©IBM web site + Note: Clean room floor + “Bunny suite” 11/28/2020 4
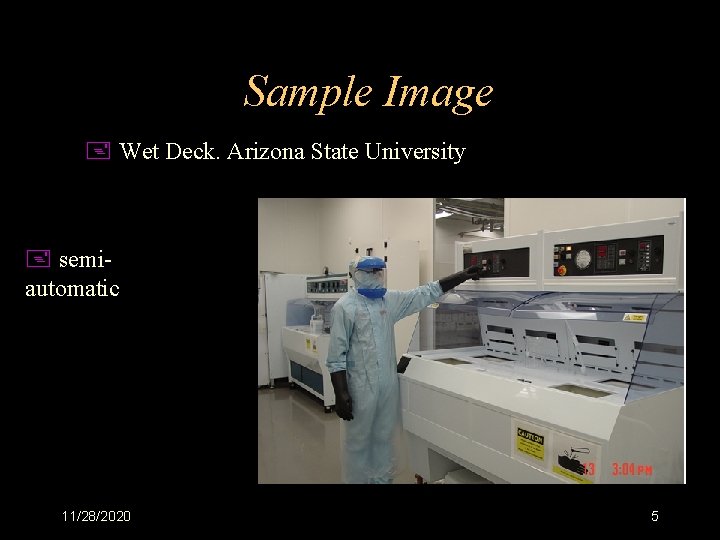
Sample Image + Wet Deck. Arizona State University + semiautomatic 11/28/2020 5
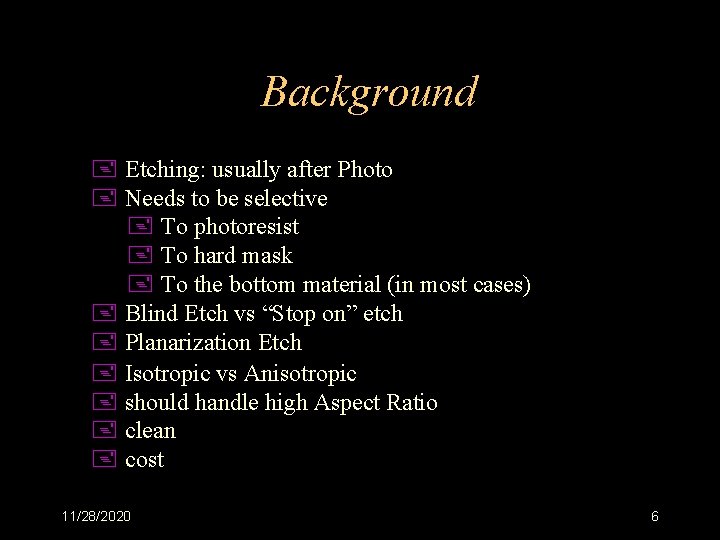
Background + Etching: usually after Photo + Needs to be selective + To photoresist + To hard mask + To the bottom material (in most cases) + Blind Etch vs “Stop on” etch + Planarization Etch + Isotropic vs Anisotropic + should handle high Aspect Ratio + clean + cost 11/28/2020 6
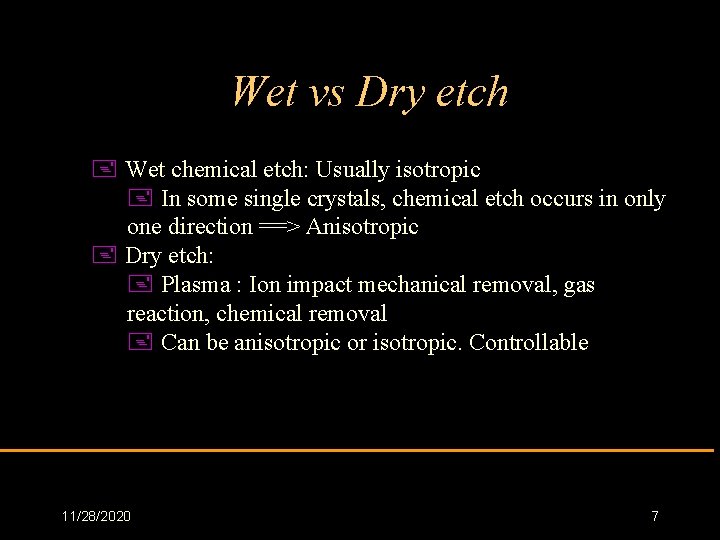
Wet vs Dry etch + Wet chemical etch: Usually isotropic + In some single crystals, chemical etch occurs in only one direction ==> Anisotropic + Dry etch: + Plasma : Ion impact mechanical removal, gas reaction, chemical removal + Can be anisotropic or isotropic. Controllable 11/28/2020 7
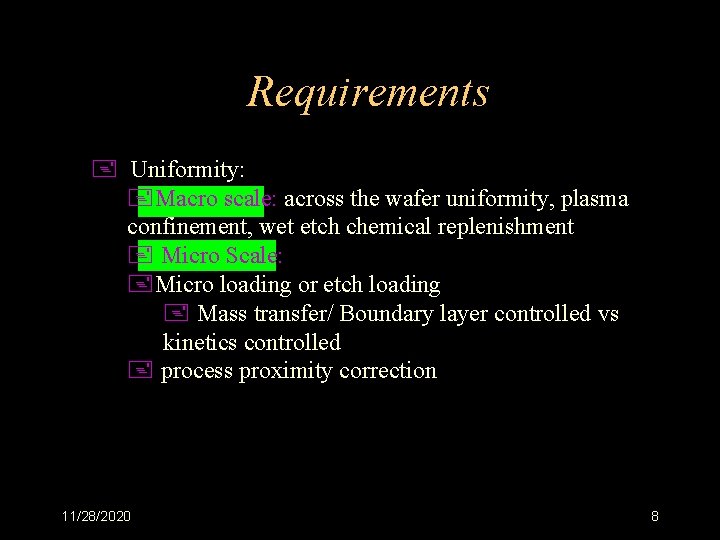
Requirements + Uniformity: +Macro scale: across the wafer uniformity, plasma confinement, wet etch chemical replenishment + Micro Scale: +Micro loading or etch loading + Mass transfer/ Boundary layer controlled vs kinetics controlled + process proximity correction 11/28/2020 8
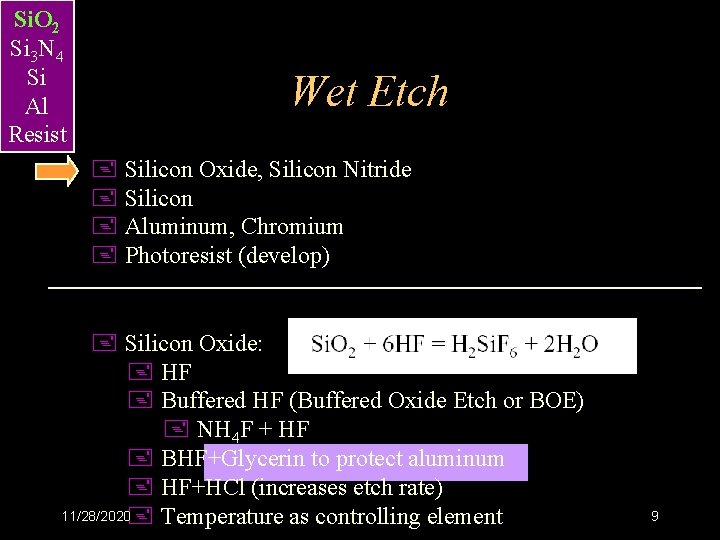
Si. O 2 Si 3 N 4 Si Al Resist Wet Etch + Silicon Oxide, Silicon Nitride + Silicon + Aluminum, Chromium + Photoresist (develop) + Silicon Oxide: + HF + Buffered HF (Buffered Oxide Etch or BOE) + NH 4 F + HF + BHF+Glycerin to protect aluminum + HF+HCl (increases etch rate) 11/28/2020+ Temperature as controlling element 9

Si. O 2 Si 3 N 4 Si Al Resist Wet Etch + Etch rates in um/min + Etch rate strongly depends on type of oxide: + Thermal oxide has low etch rate + BSG has low etch rate + PSG, CVD oxide high etch rate 11/28/2020 10
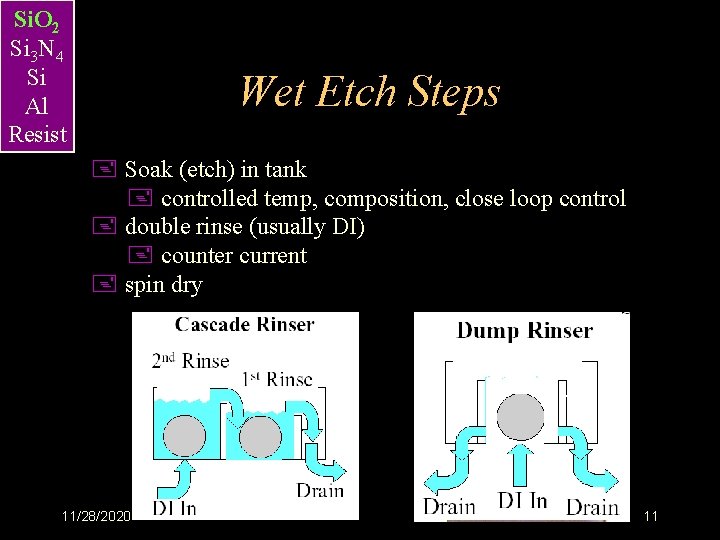
Si. O 2 Si 3 N 4 Si Al Resist Wet Etch Steps + Soak (etch) in tank + controlled temp, composition, close loop control + double rinse (usually DI) + counter current + spin dry 11/28/2020 11
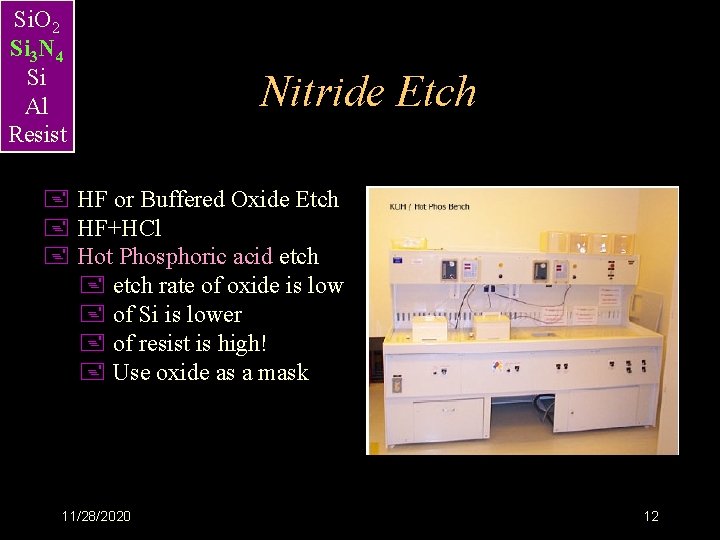
Si. O 2 Si 3 N 4 Si Al Resist Nitride Etch + HF or Buffered Oxide Etch + HF+HCl + Hot Phosphoric acid etch + etch rate of oxide is low + of Si is lower + of resist is high! + Use oxide as a mask 11/28/2020 12
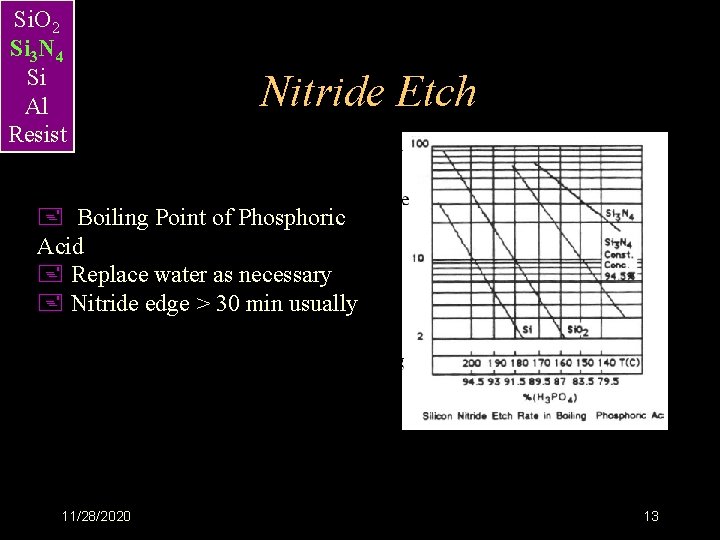
Si. O 2 Si 3 N 4 Si Al Resist Nitride Etch + Boiling Point of Phosphoric Acid + Replace water as necessary + Nitride edge > 30 min usually 11/28/2020 13
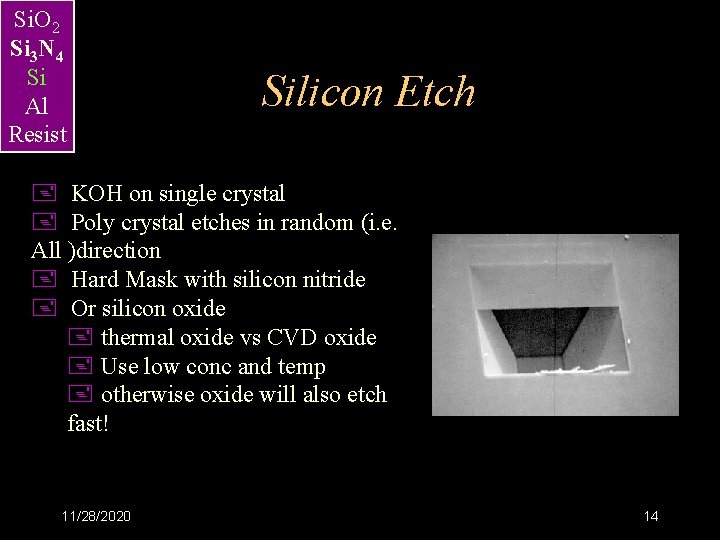
Si. O 2 Si 3 N 4 Si Al Resist Silicon Etch + KOH on single crystal + Poly crystal etches in random (i. e. All )direction + Hard Mask with silicon nitride + Or silicon oxide + thermal oxide vs CVD oxide + Use low conc and temp + otherwise oxide will also etch fast! 11/28/2020 14
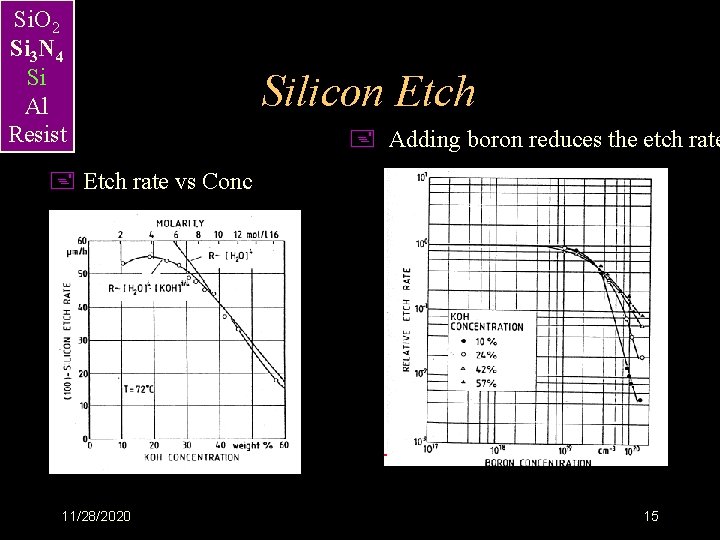
Si. O 2 Si 3 N 4 Si Al Resist Silicon Etch + Adding boron reduces the etch rate + Etch rate vs Conc 11/28/2020 15
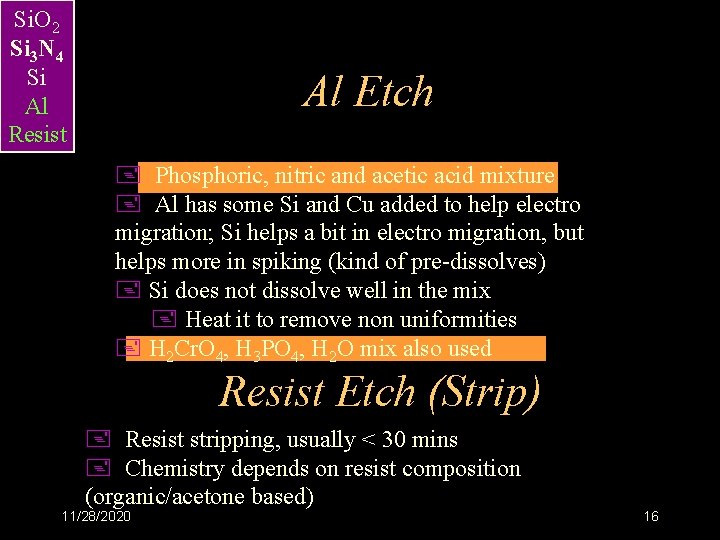
Si. O 2 Si 3 N 4 Si Al Resist Al Etch + Phosphoric, nitric and acetic acid mixture + Al has some Si and Cu added to help electro migration; Si helps a bit in electro migration, but helps more in spiking (kind of pre-dissolves) + Si does not dissolve well in the mix + Heat it to remove non uniformities + H 2 Cr. O 4, H 3 PO 4, H 2 O mix also used Resist Etch (Strip) + Resist stripping, usually < 30 mins + Chemistry depends on resist composition (organic/acetone based) 11/28/2020 16
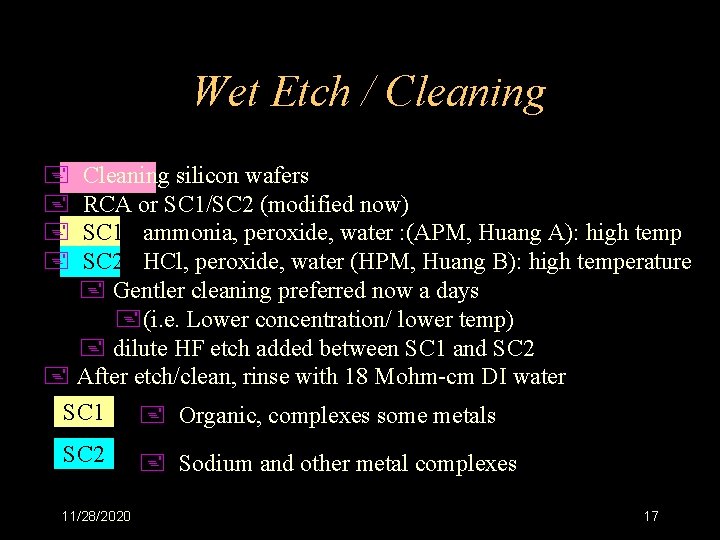
Wet Etch / Cleaning + + Cleaning silicon wafers RCA or SC 1/SC 2 (modified now) SC 1 : ammonia, peroxide, water : (APM, Huang A): high temp SC 2: HCl, peroxide, water (HPM, Huang B): high temperature + Gentler cleaning preferred now a days +(i. e. Lower concentration/ lower temp) + dilute HF etch added between SC 1 and SC 2 + After etch/clean, rinse with 18 Mohm-cm DI water SC 1 + Organic, complexes some metals SC 2 11/28/2020 + Sodium and other metal complexes 17

Wet Etch Summary + Wet etch is low temperature, high selectivity + Charge issues: ESD (electrostatic discharge) in dry etch + Increased reliability for wet etch + Of late, photochemical reactions and electrochemical dissolution are becoming important in wet etch and wet cleaning + Cheap equipment cost + Fast etch rate, Any material can be etched + + Surfactant to enhance wetting Batch processing is easy Inline monitoring/End Point Detection is not easy Is the only method for cleaning equipment/labware 11/28/2020 18
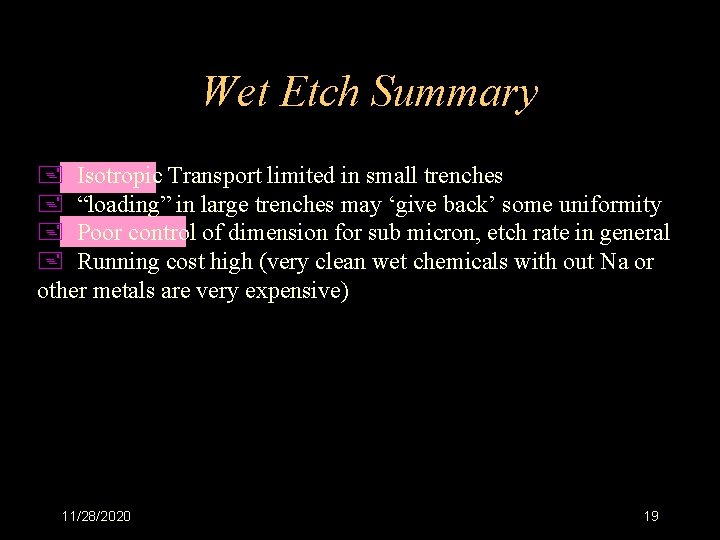
Wet Etch Summary + Isotropic Transport limited in small trenches + “loading” in large trenches may ‘give back’ some uniformity + Poor control of dimension for sub micron, etch rate in general + Running cost high (very clean wet chemicals with out Na or other metals are very expensive) 11/28/2020 19