IA 3112 Automatiseringsteknikk Hsten 2018 Modelbased Predictive Control
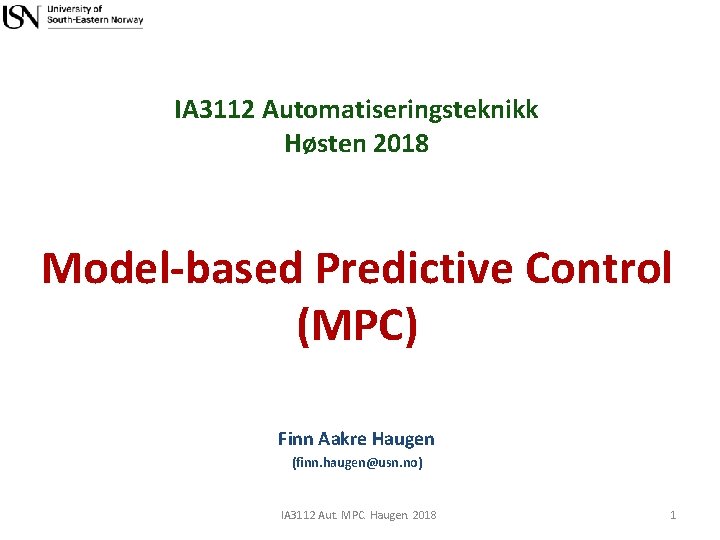
IA 3112 Automatiseringsteknikk Høsten 2018 Model-based Predictive Control (MPC) Finn Aakre Haugen (finn. haugen@usn. no) IA 3112 Aut. MPC. Haugen. 2018 1
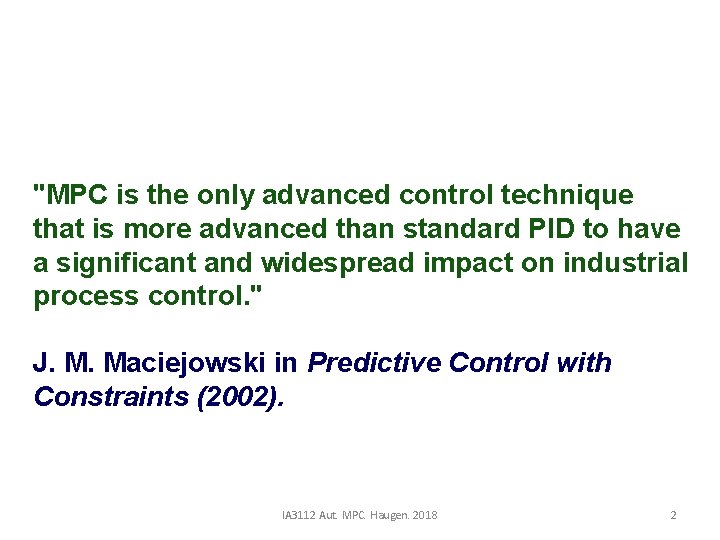
"MPC is the only advanced control technique that is more advanced than standard PID to have a significant and widespread impact on industrial process control. " J. M. Maciejowski in Predictive Control with Constraints (2002). IA 3112 Aut. MPC. Haugen. 2018 2
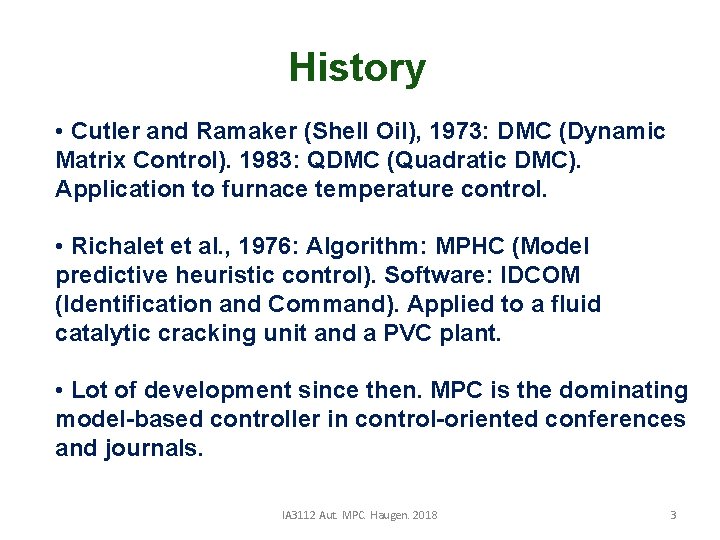
History • Cutler and Ramaker (Shell Oil), 1973: DMC (Dynamic Matrix Control). 1983: QDMC (Quadratic DMC). Application to furnace temperature control. • Richalet et al. , 1976: Algorithm: MPHC (Model predictive heuristic control). Software: IDCOM (Identification and Command). Applied to a fluid catalytic cracking unit and a PVC plant. • Lot of development since then. MPC is the dominating model-based controller in control-oriented conferences and journals. IA 3112 Aut. MPC. Haugen. 2018 3

Some MPC products • Delta. V (Emerson Process Partner) • 800 x. A APC (ABB) • Matlab MPC Toolbox, also for Simulink • Lab. VIEW Predictive Control palette in Control Design toolkit • Septic (Statoil, no external use). . . IA 3112 Aut. MPC. Haugen. 2018 4
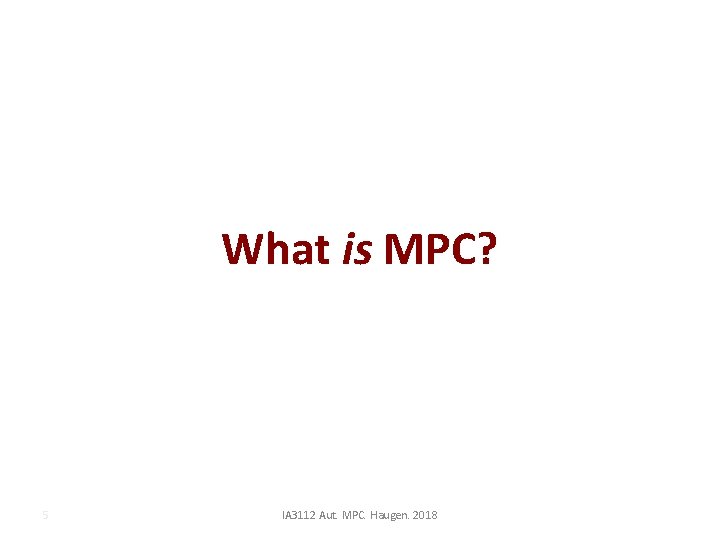
What is MPC? 5 IA 3112 Aut. MPC. Haugen. 2018
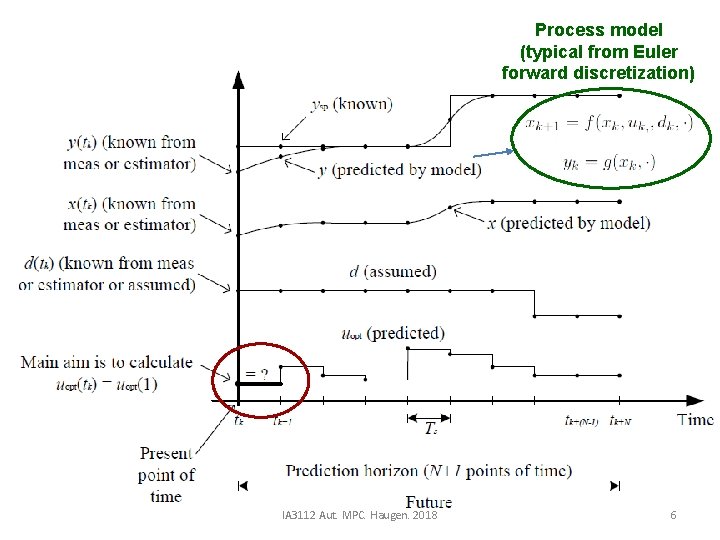
Process model (typical from Euler forward discretization) IA 3112 Aut. MPC. Haugen. 2018 6
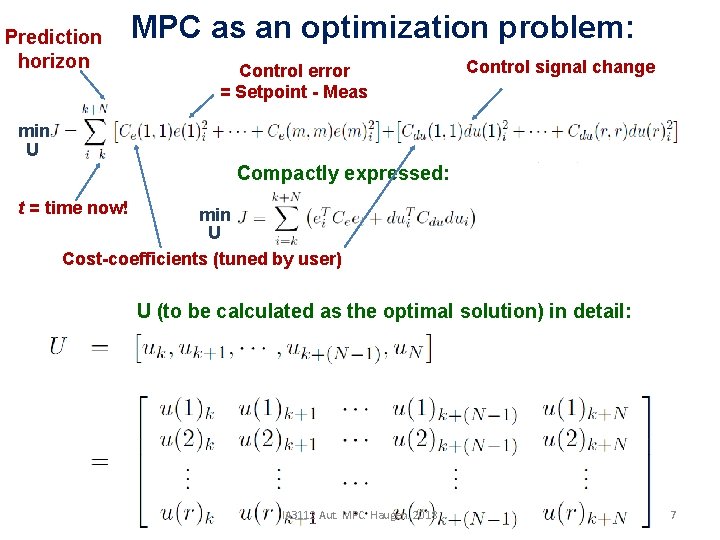
Prediction horizon MPC as an optimization problem: Control error = Setpoint - Meas Control signal change min U Compactly expressed: t = time now! min U Cost-coefficients (tuned by user) U (to be calculated as the optimal solution) in detail: IA 3112 Aut. MPC. Haugen. 2018 7
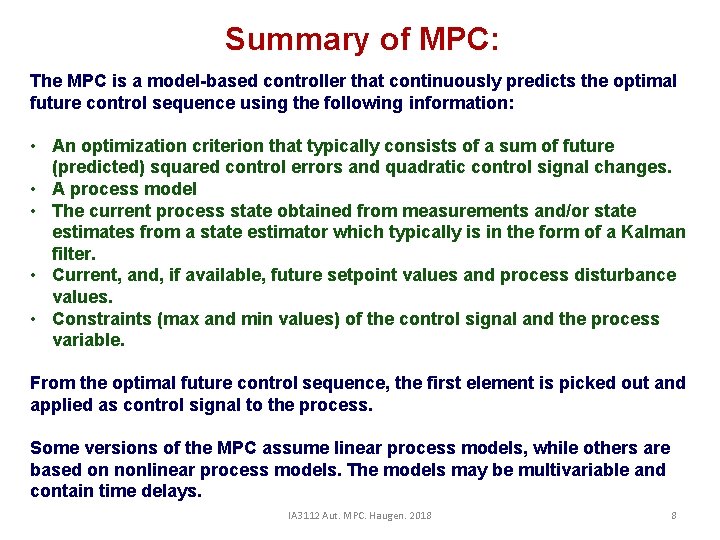
Summary of MPC: The MPC is a model-based controller that continuously predicts the optimal future control sequence using the following information: • An optimization criterion that typically consists of a sum of future (predicted) squared control errors and quadratic control signal changes. • A process model • The current process state obtained from measurements and/or state estimates from a state estimator which typically is in the form of a Kalman filter. • Current, and, if available, future setpoint values and process disturbance values. • Constraints (max and min values) of the control signal and the process variable. From the optimal future control sequence, the first element is picked out and applied as control signal to the process. Some versions of the MPC assume linear process models, while others are based on nonlinear process models. The models may be multivariable and contain time delays. IA 3112 Aut. MPC. Haugen. 2018 8
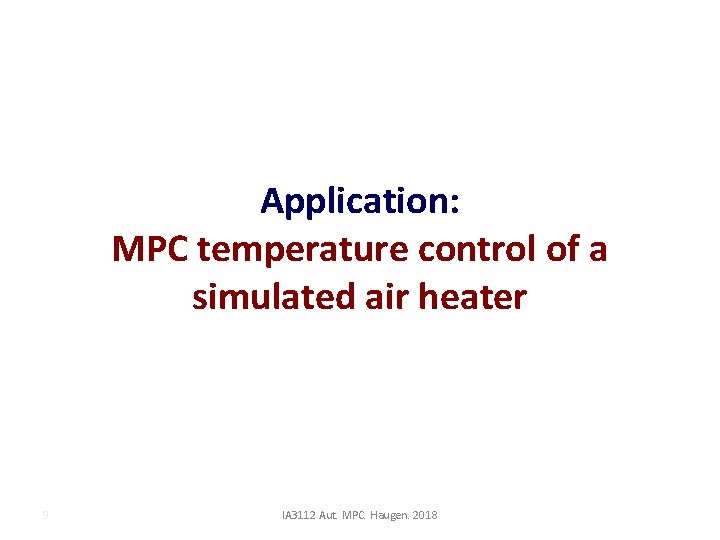
Application: MPC temperature control of a simulated air heater 9 IA 3112 Aut. MPC. Haugen. 2018
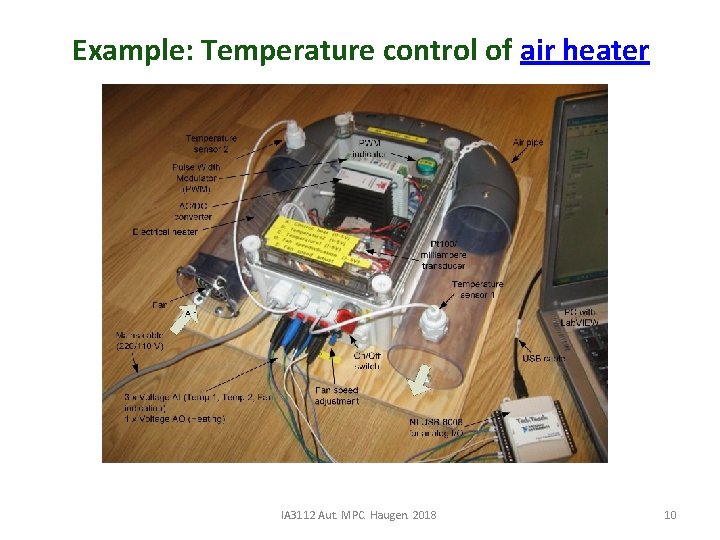
Example: Temperature control of air heater IA 3112 Aut. MPC. Haugen. 2018 10
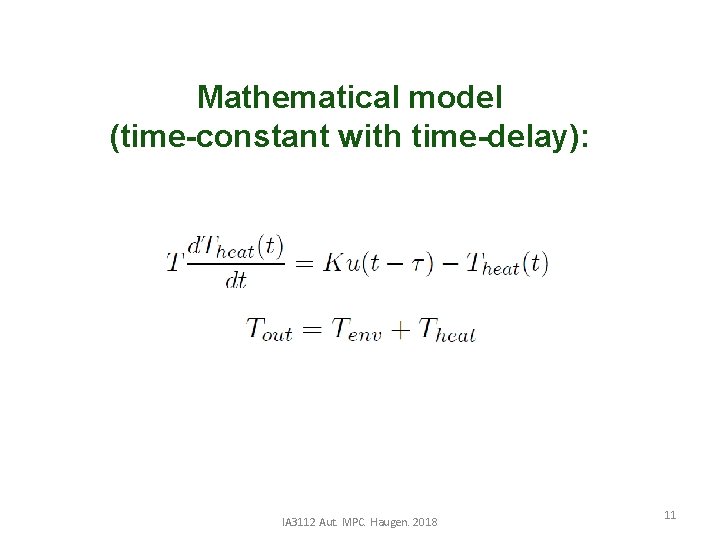
Mathematical model (time-constant with time-delay): IA 3112 Aut. MPC. Haugen. 2018 11
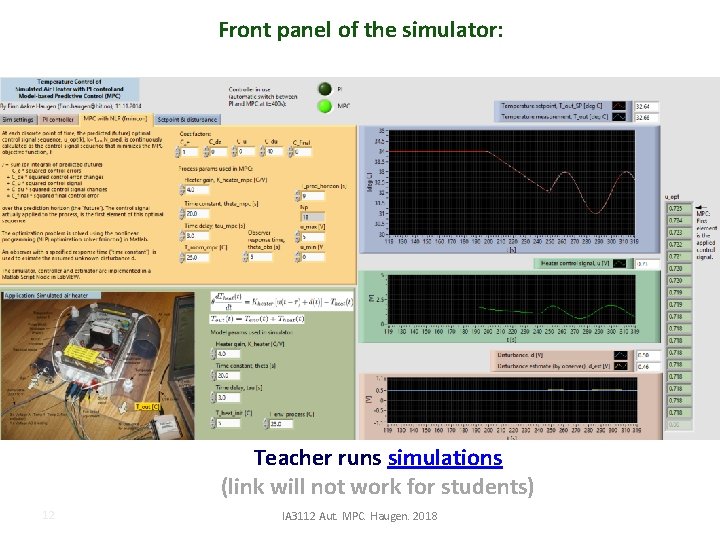
Front panel of the simulator: Teacher runs simulations (link will not work for students) 12 IA 3112 Aut. MPC. Haugen. 2018
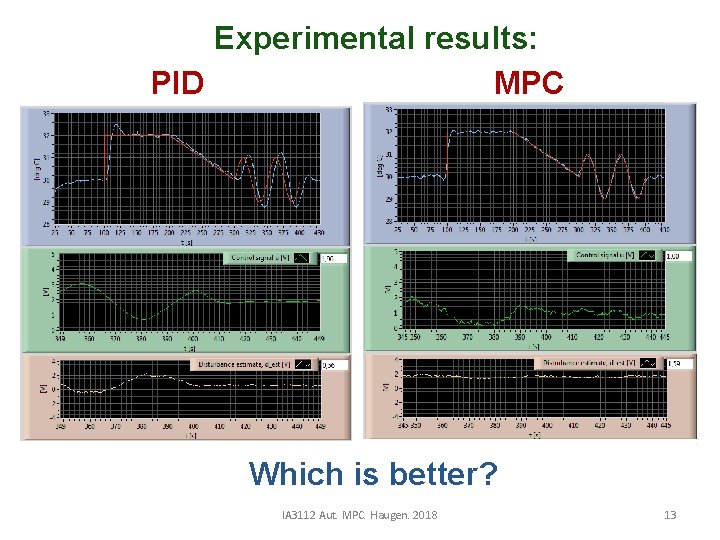
Experimental results: PID MPC Which is better? IA 3112 Aut. MPC. Haugen. 2018 13
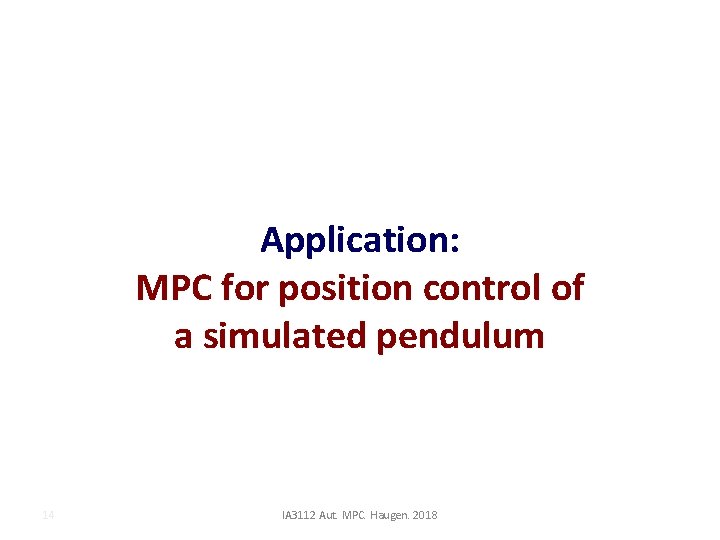
Application: MPC for position control of a simulated pendulum 14 IA 3112 Aut. MPC. Haugen. 2018
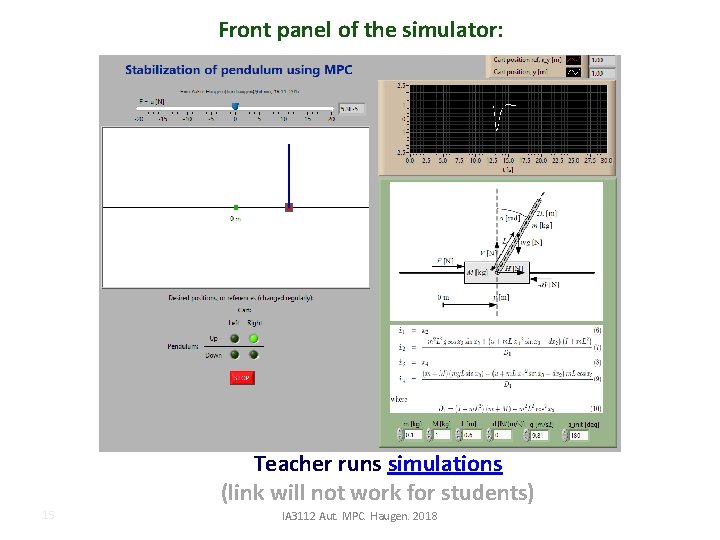
Front panel of the simulator: Teacher runs simulations (link will not work for students) 15 IA 3112 Aut. MPC. Haugen. 2018
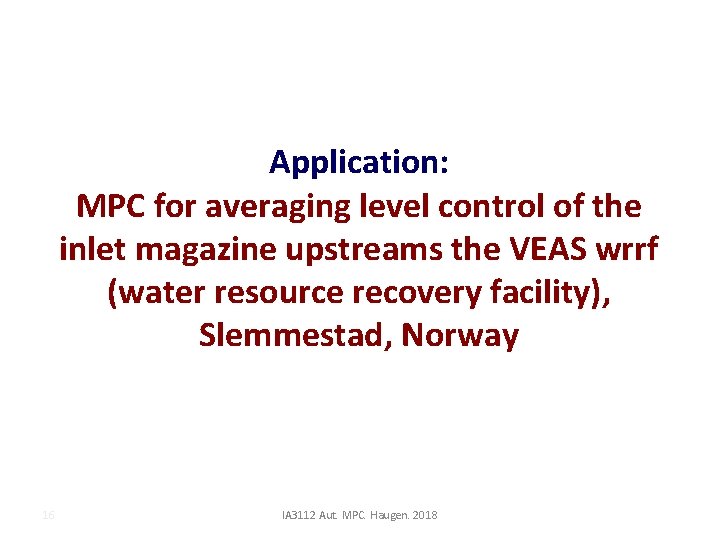
Application: MPC for averaging level control of the inlet magazine upstreams the VEAS wrrf (water resource recovery facility), Slemmestad, Norway 16 IA 3112 Aut. MPC. Haugen. 2018
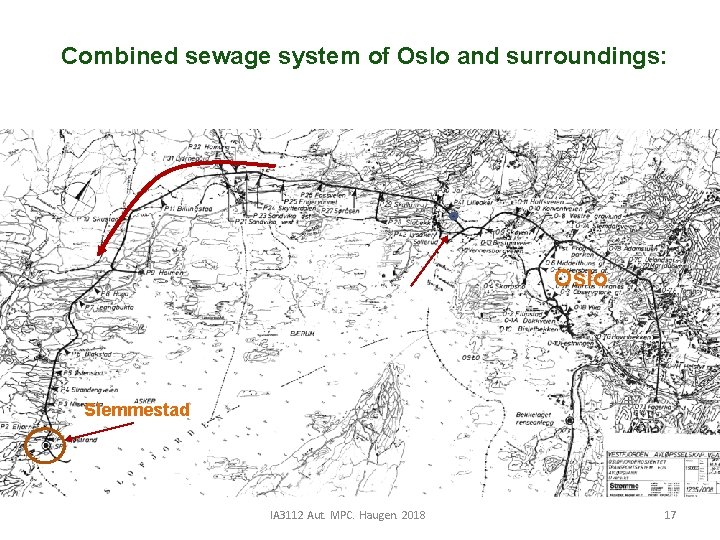
Combined sewage system of Oslo and surroundings: Oslo Slemmestad IA 3112 Aut. MPC. Haugen. 2018 17
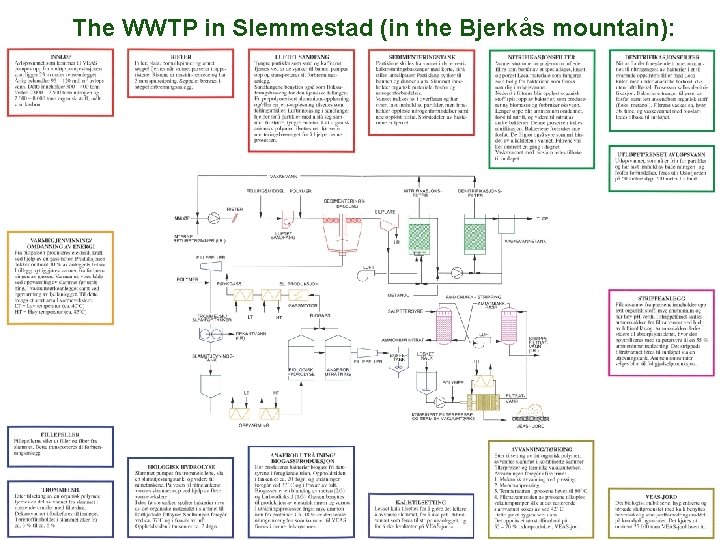
The WWTP in Slemmestad (in the Bjerkås mountain): IA 3112 Aut. MPC. Haugen. 2018 18
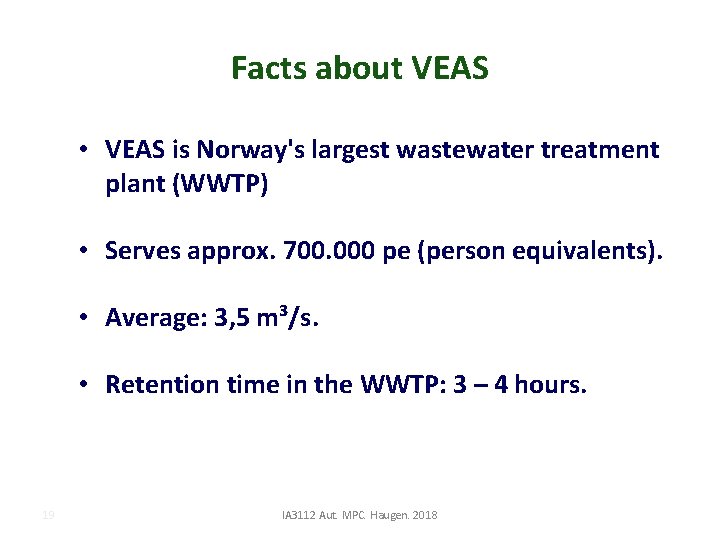
Facts about VEAS • VEAS is Norway's largest wastewater treatment plant (WWTP) • Serves approx. 700. 000 pe (person equivalents). • Average: 3, 5 m³/s. • Retention time in the WWTP: 3 – 4 hours. 19 IA 3112 Aut. MPC. Haugen. 2018
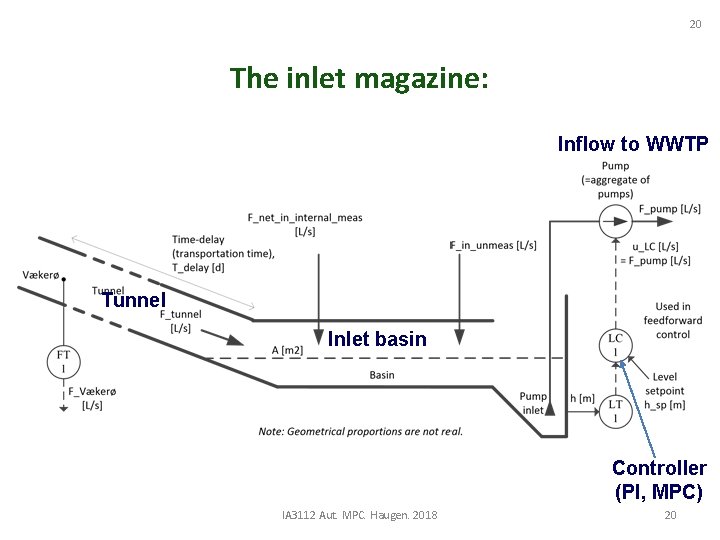
20 The inlet magazine: Inflow to WWTP Tunnel Inlet basin Controller (PI, MPC) IA 3112 Aut. MPC. Haugen. 2018 20
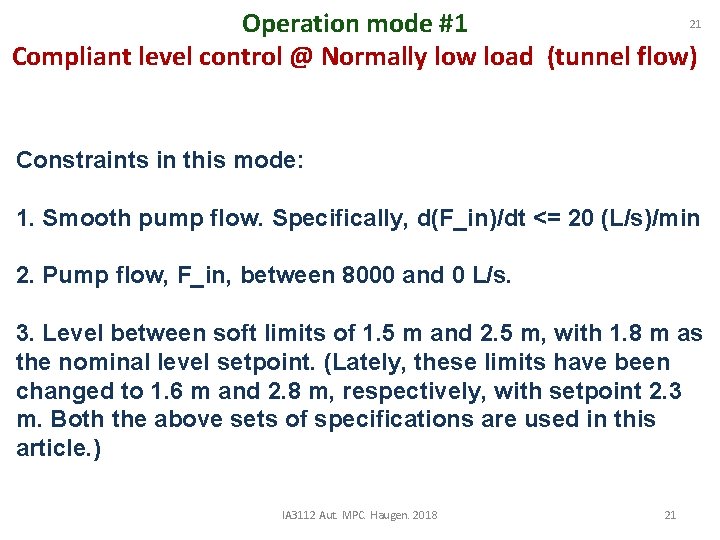
21 Operation mode #1 Compliant level control @ Normally low load (tunnel flow) Constraints in this mode: 1. Smooth pump flow. Specifically, d(F_in)/dt <= 20 (L/s)/min 2. Pump flow, F_in, between 8000 and 0 L/s. 3. Level between soft limits of 1. 5 m and 2. 5 m, with 1. 8 m as the nominal level setpoint. (Lately, these limits have been changed to 1. 6 m and 2. 8 m, respectively, with setpoint 2. 3 m. Both the above sets of specifications are used in this article. ) IA 3112 Aut. MPC. Haugen. 2018 21
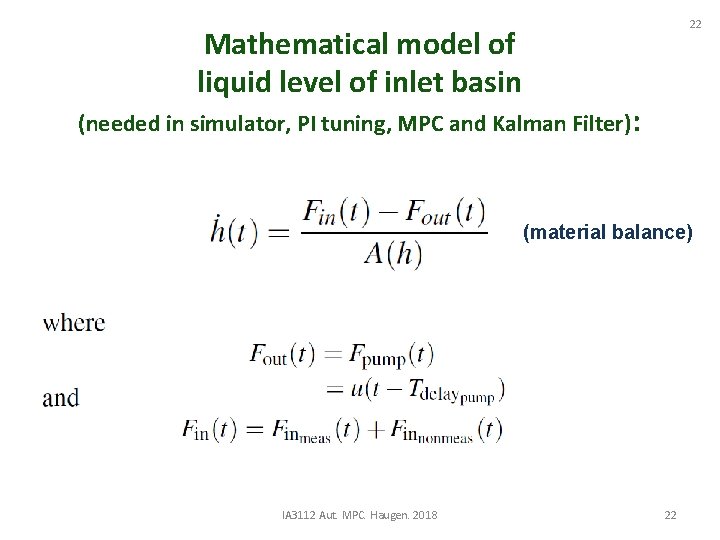
22 Mathematical model of liquid level of inlet basin (needed in simulator, PI tuning, MPC and Kalman Filter): (material balance) IA 3112 Aut. MPC. Haugen. 2018 22
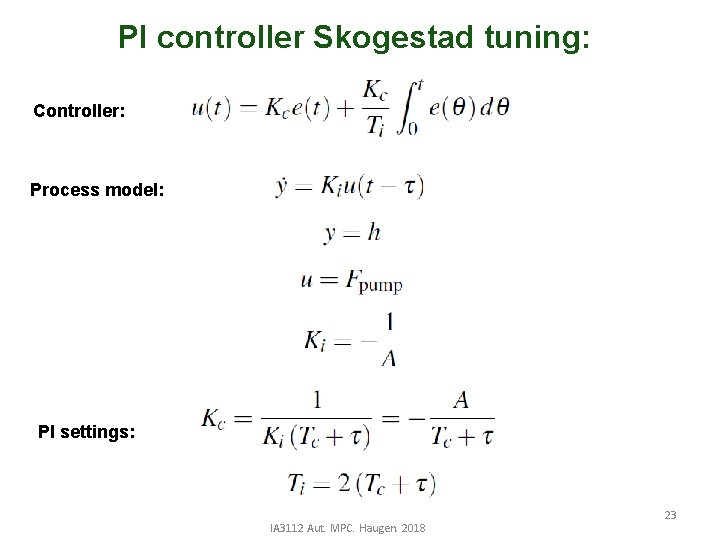
PI controller Skogestad tuning: Controller: Process model: PI settings: IA 3112 Aut. MPC. Haugen. 2018 23
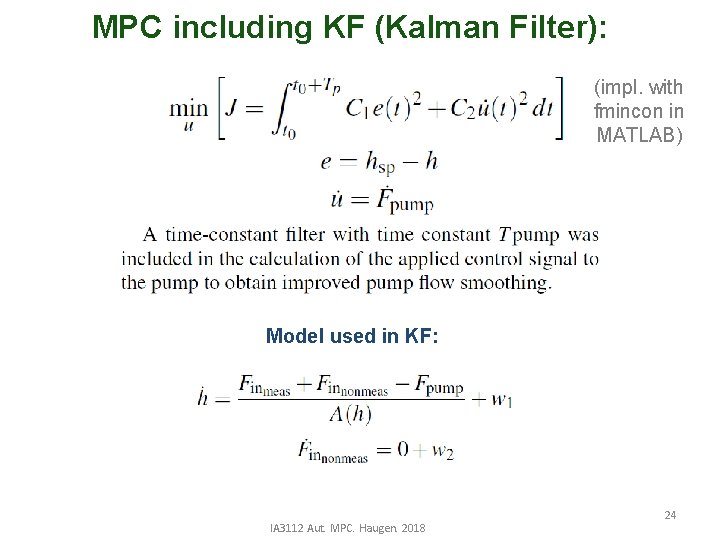
MPC including KF (Kalman Filter): (impl. with fmincon in MATLAB) Model used in KF: IA 3112 Aut. MPC. Haugen. 2018 24

Let's look at real results of three various level control solutions • PI control with original PI settings • PI control with Skogestad (or optimized) PI settings (cf. previous lecture) • MPC 25 IA 3112 Aut. MPC. Haugen. 2018
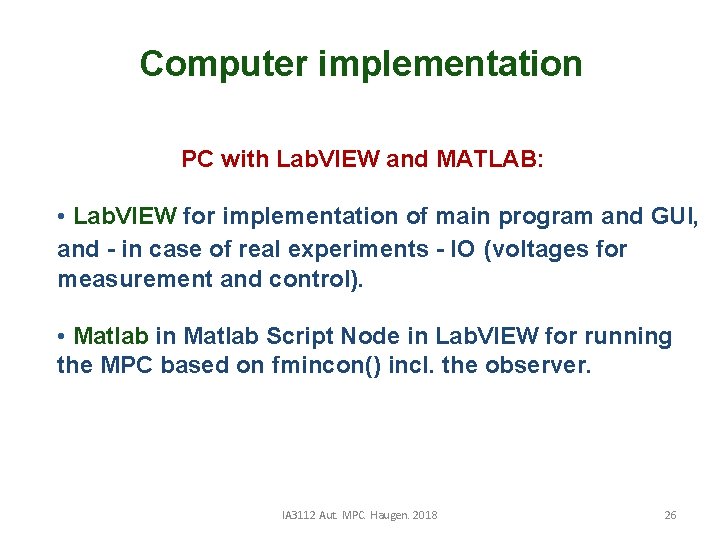
Computer implementation PC with Lab. VIEW and MATLAB: • Lab. VIEW for implementation of main program and GUI, and - in case of real experiments - IO (voltages for measurement and control). • Matlab in Matlab Script Node in Lab. VIEW for running the MPC based on fmincon() incl. the observer. IA 3112 Aut. MPC. Haugen. 2018 26
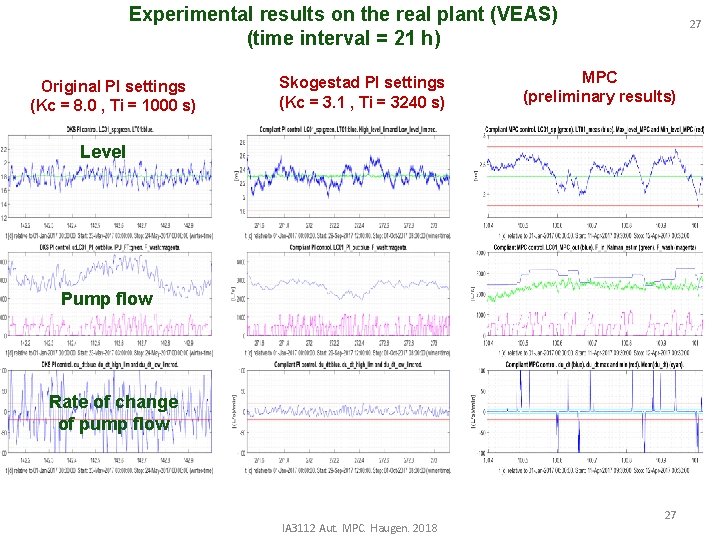
Experimental results on the real plant (VEAS) (time interval = 21 h) Original PI settings (Kc = 8. 0 , Ti = 1000 s) Skogestad PI settings (Kc = 3. 1 , Ti = 3240 s) 27 MPC (preliminary results) Level Pump flow Rate of change of pump flow IA 3112 Aut. MPC. Haugen. 2018 27
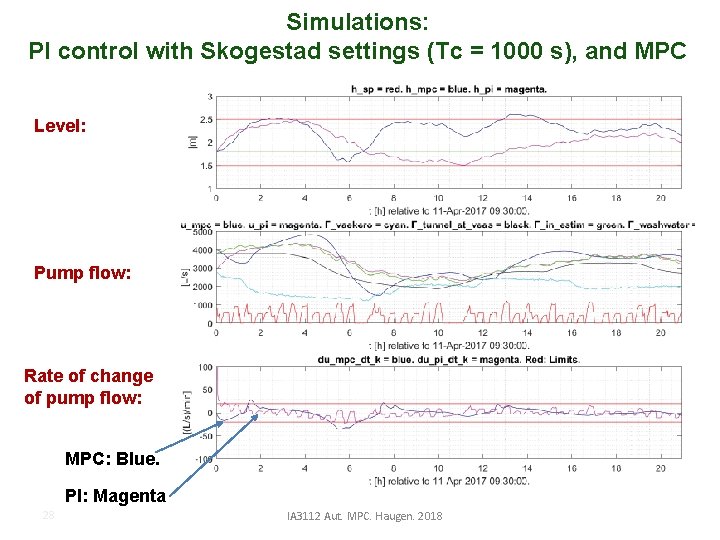
Simulations: PI control with Skogestad settings (Tc = 1000 s), and MPC Level: Pump flow: Rate of change of pump flow: MPC: Blue. PI: Magenta 28 IA 3112 Aut. MPC. Haugen. 2018
- Slides: 28