Horizontal Carousel System Good carousel stock is typically
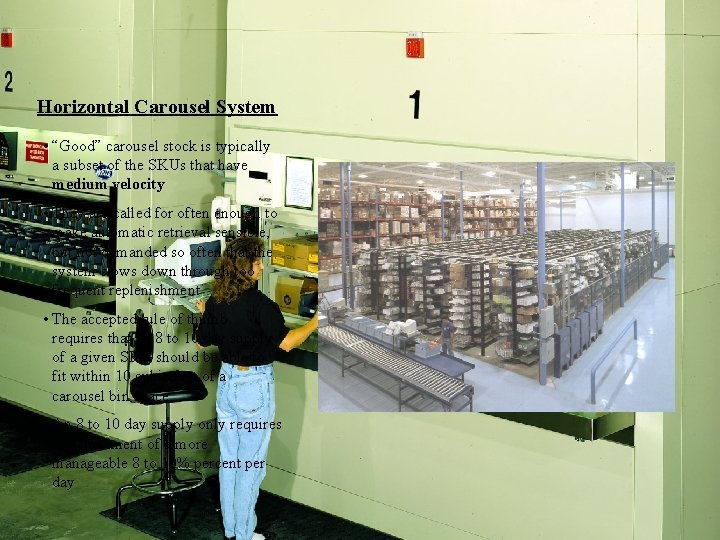
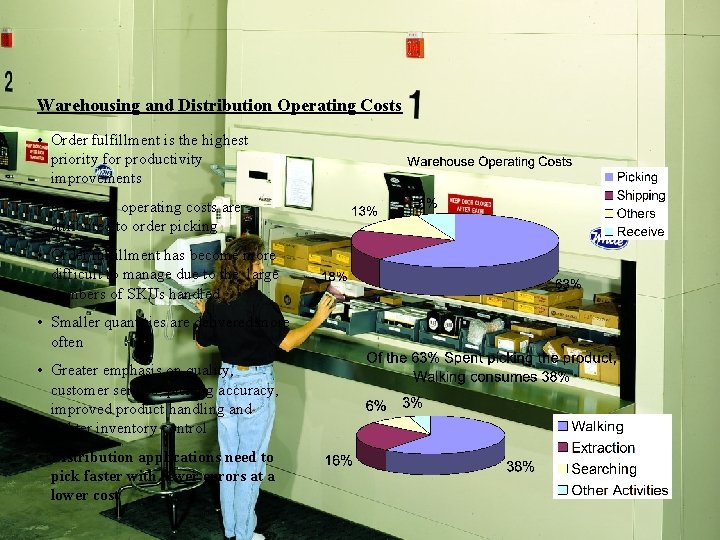
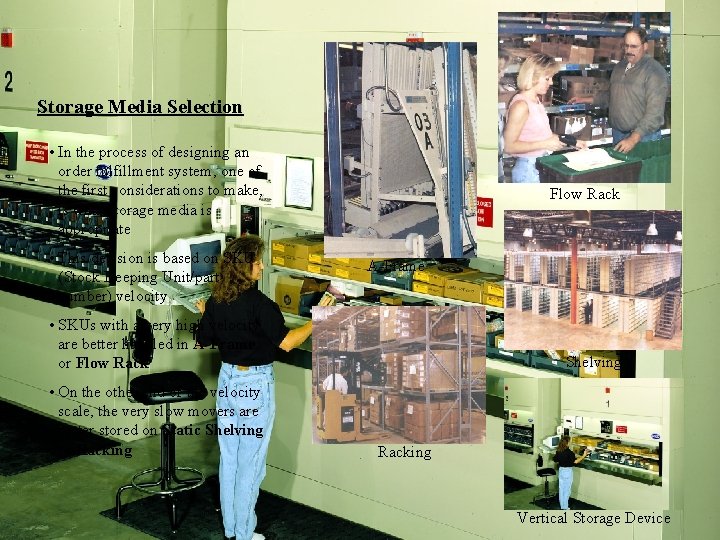
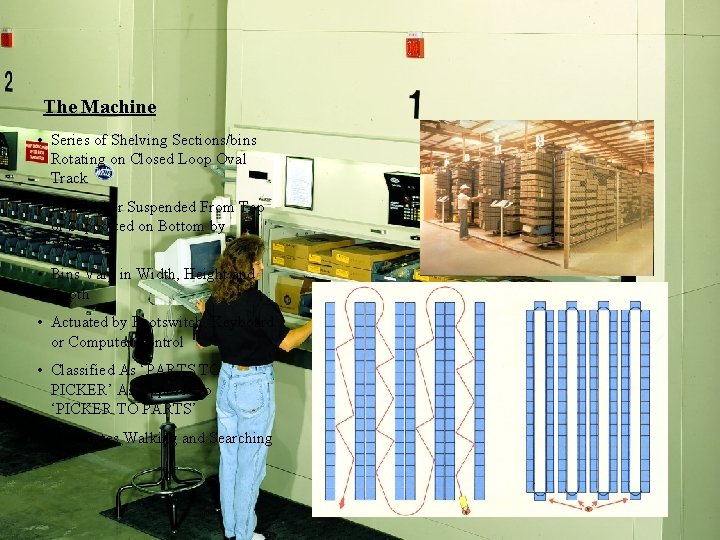
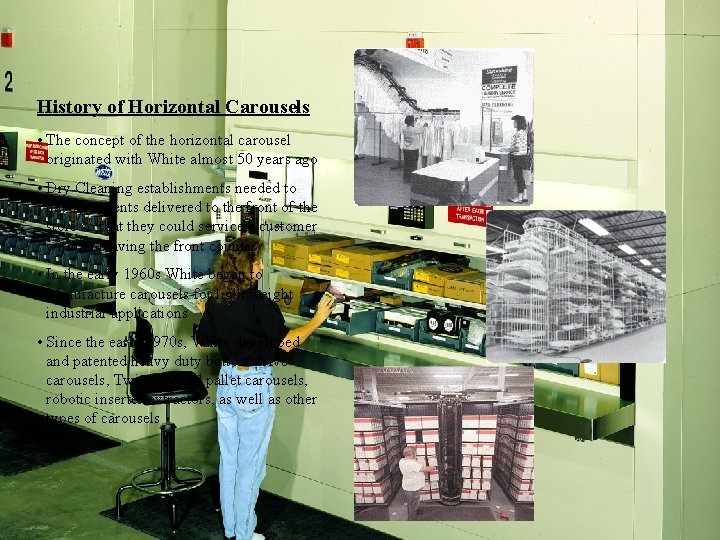
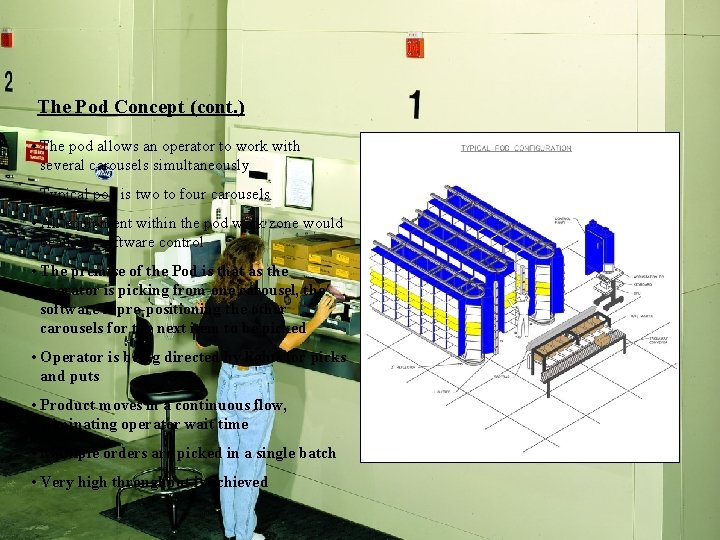
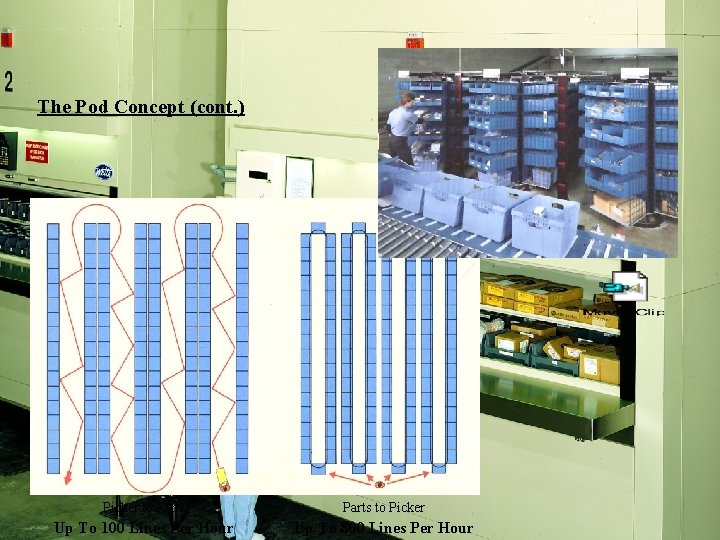
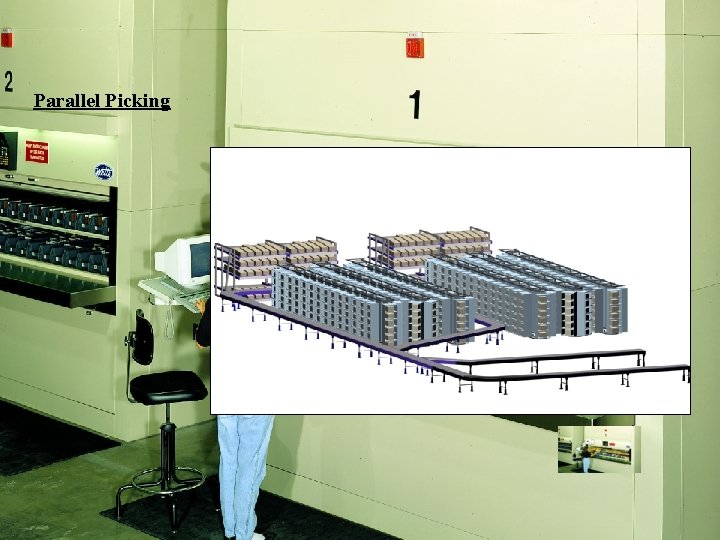
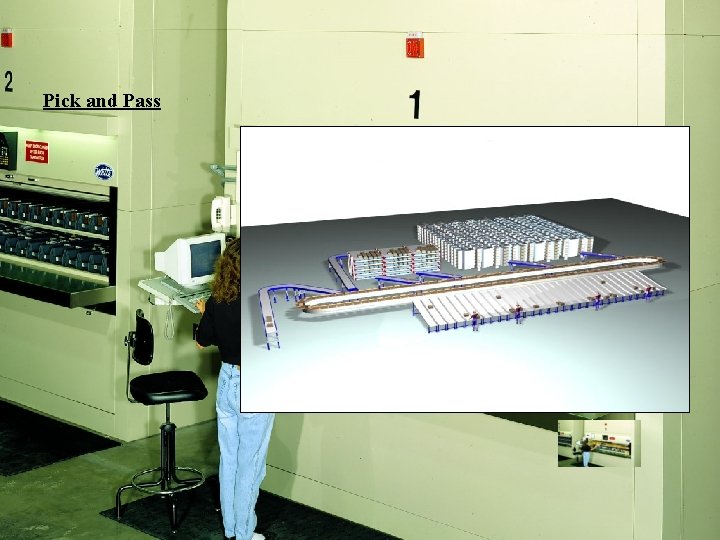
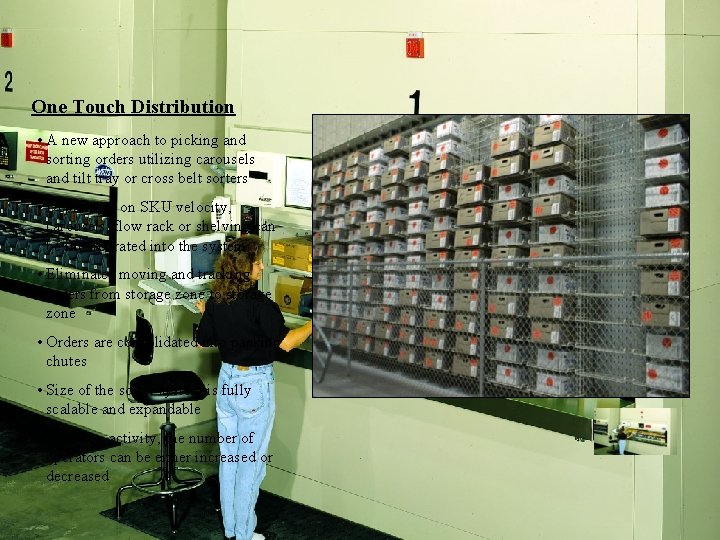
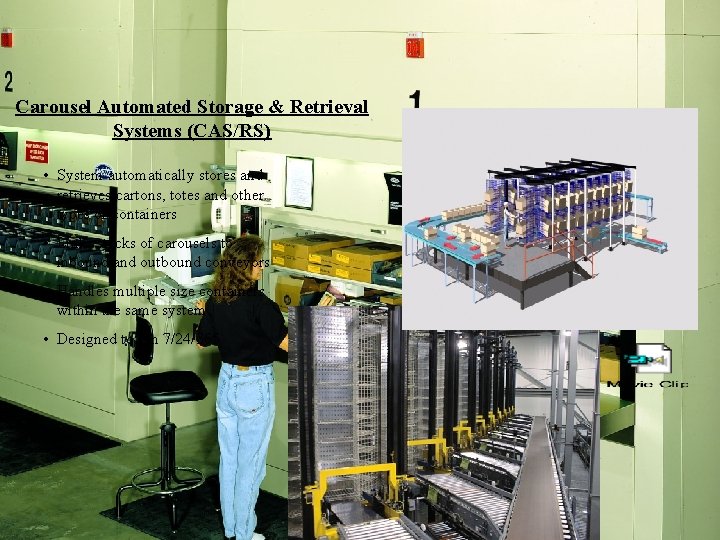
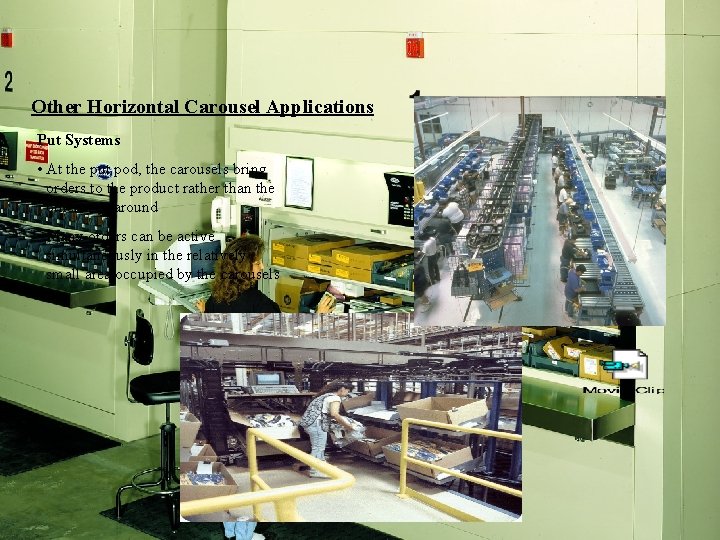
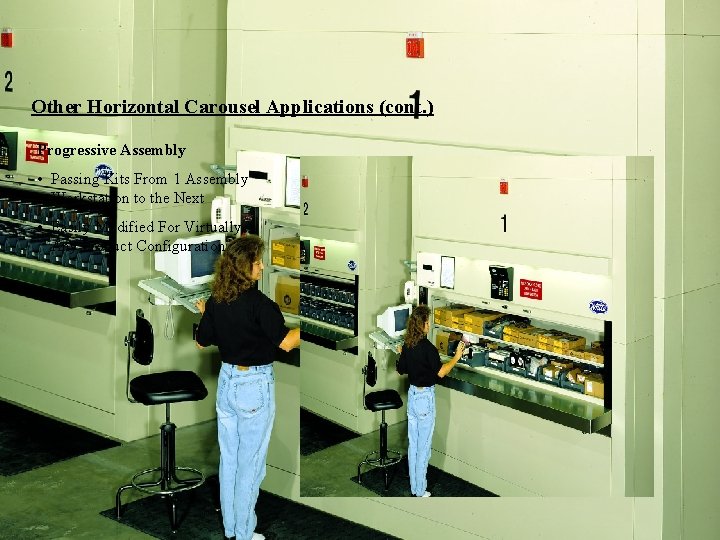
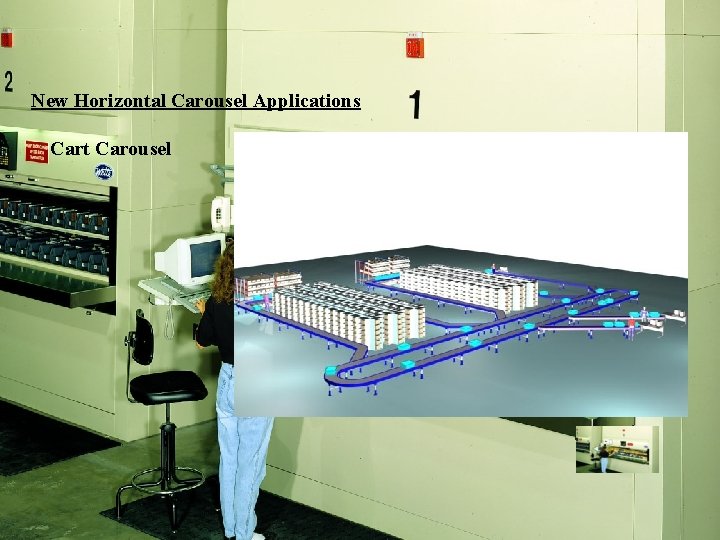
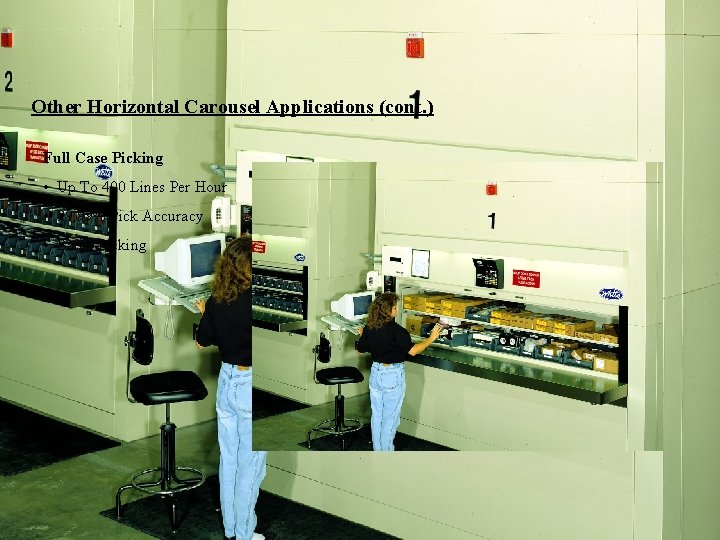
- Slides: 15
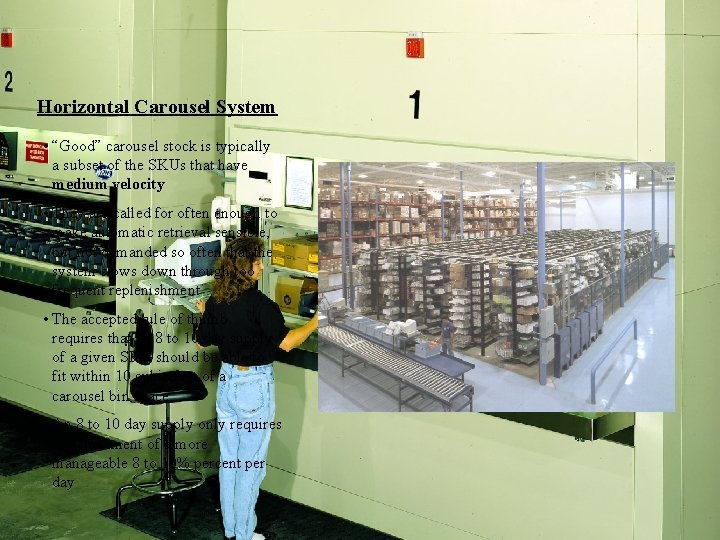
Horizontal Carousel System • “Good” carousel stock is typically a subset of the SKUs that have medium velocity • They are called for often enough to make automatic retrieval sensible, but not demanded so often that the system slows down through too frequent replenishment • The accepted rule of thumb requires that an 8 to 10 day supply of a given SKU should be able to fit within 10 cubic feet of a carousel bin space • An 8 to 10 day supply only requires replenishment of a more manageable 8 to 10% percent per day
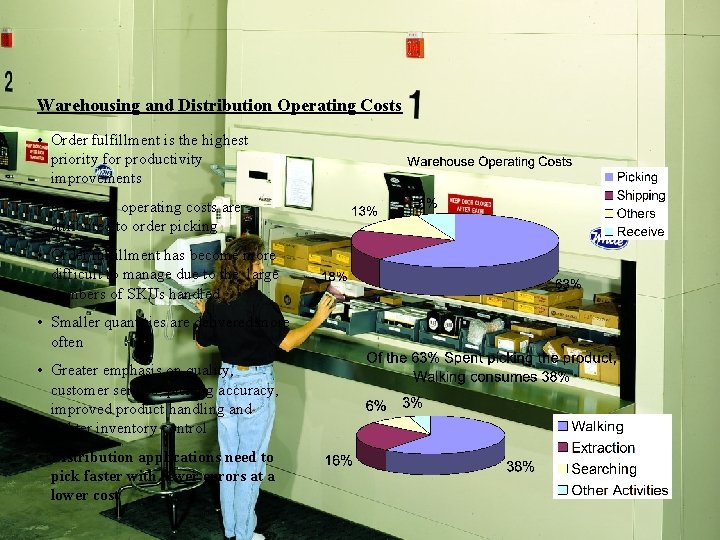
Warehousing and Distribution Operating Costs • Order fulfillment is the highest priority for productivity improvements • 63% of all operating costs are attributed to order picking • Order fulfillment has become more difficult to manage due to the large numbers of SKUs handled • Smaller quantities are delivered more often • Greater emphasis on quality, customer service, picking accuracy, improved product handling and tighter inventory control • Distribution applications need to pick faster with fewer errors at a lower cost
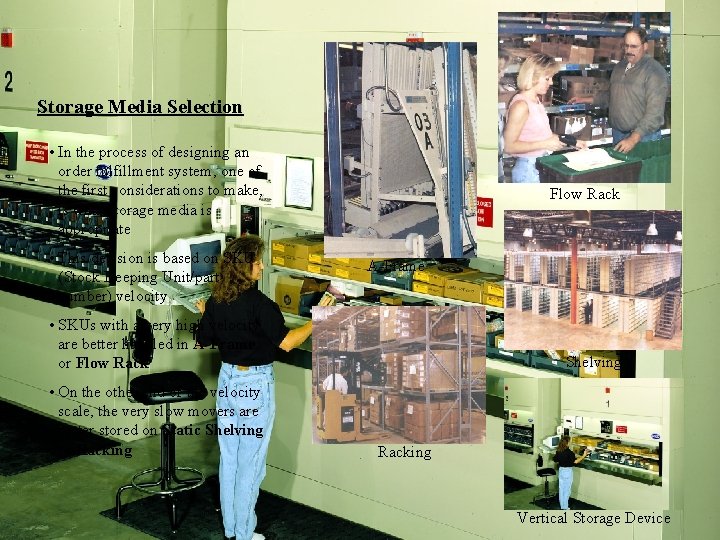
Storage Media Selection • In the process of designing an order fulfillment system, one of the first considerations to make, is what storage media is appropriate • This decision is based on SKU (Stock Keeping Unit/part number) velocity Flow Rack A-Frame • SKUs with a very high velocity are better handled in A-Frame or Flow Rack • On the other end of the velocity scale, the very slow movers are better stored on Static Shelving or Racking Shelving Racking Vertical Storage Device
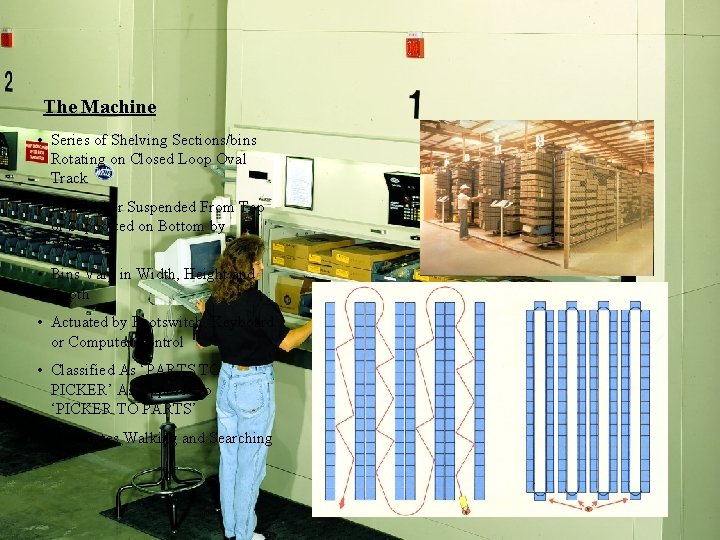
The Machine • Series of Shelving Sections/bins Rotating on Closed Loop Oval Track • Bins Either Suspended From Top or Supported on Bottom by Wheels • Bins Vary in Width, Height and Depth • Actuated by Footswitch, Keyboard or Computer Control • Classified As ‘PARTS TO PICKER’ As Opposed to ‘PICKER TO PARTS’ • Eliminates Walking and Searching
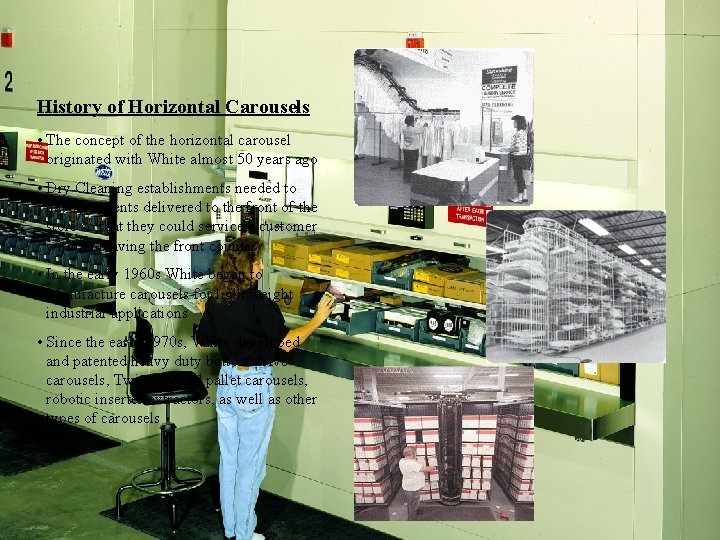
History of Horizontal Carousels • The concept of the horizontal carousel originated with White almost 50 years ago • Dry Cleaning establishments needed to have garments delivered to the front of the store so that they could service a customer without leaving the front counter • In the early 1960 s White began to manufacture carousels for light weight industrial applications • Since the early 1970 s, White developed and patented heavy duty bottom drive carousels, Twin Bin and pallet carousels, robotic inserter/extractors, as well as other types of carousels
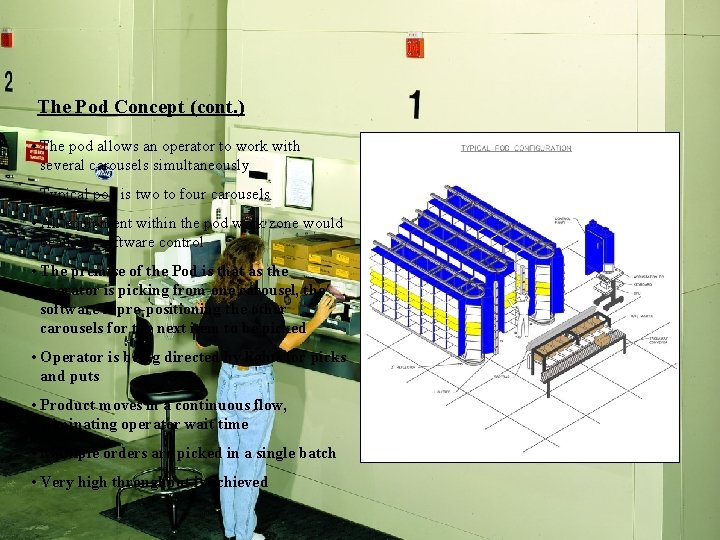
The Pod Concept (cont. ) • The pod allows an operator to work with several carousels simultaneously • Typical pod is two to four carousels • All equipment within the pod work zone would be under software control • The premise of the Pod is that as the operator is picking from one carousel, the software is pre-positioning the other carousels for the next item to be picked • Operator is being directed by lights for picks and puts • Product moves in a continuous flow, eliminating operator wait time • Multiple orders are picked in a single batch • Very high throughput is achieved
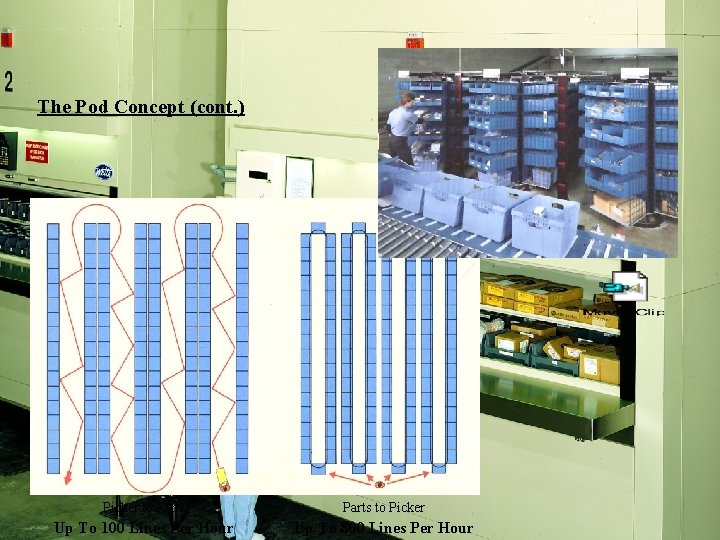
The Pod Concept (cont. ) Picker to Parts to Picker Up To 100 Lines Per Hour Up To 800 Lines Per Hour
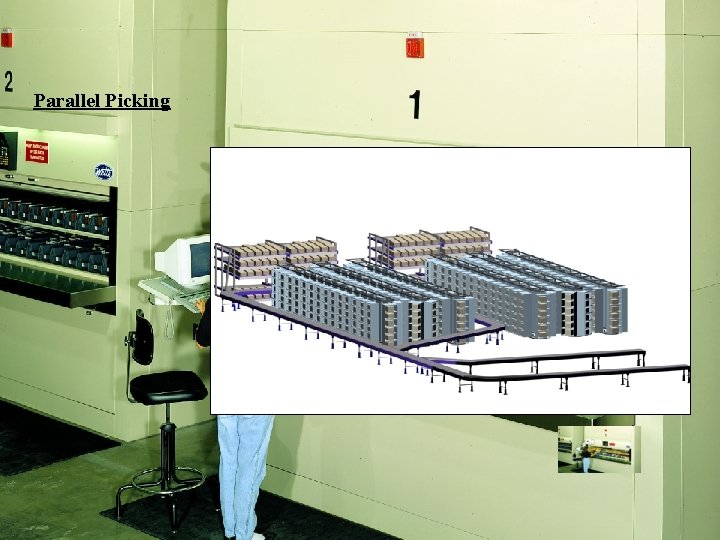
Parallel Picking
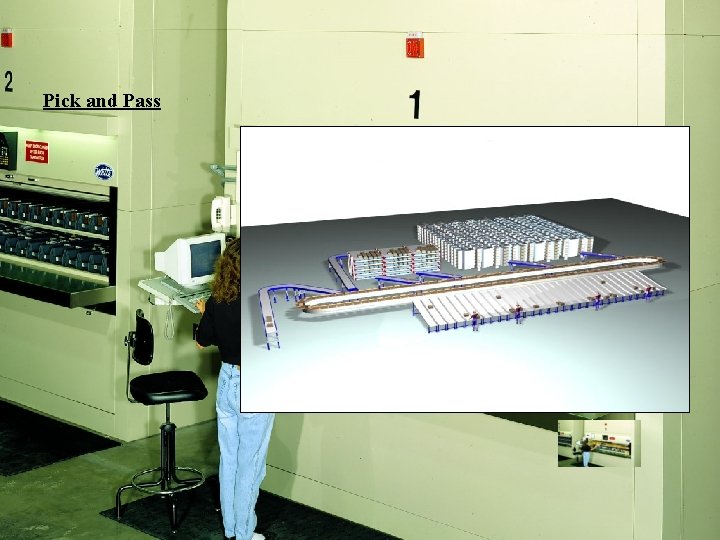
Pick and Pass
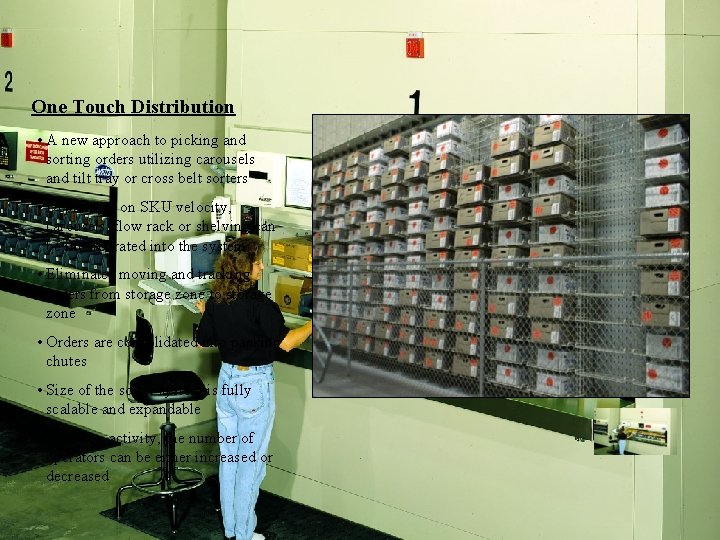
One Touch Distribution • A new approach to picking and sorting orders utilizing carousels and tilt tray or cross belt sorters • Depending on SKU velocity, carousels, flow rack or shelving can be incorporated into the system • Eliminates moving and tracking orders from storage zone to storage zone • Orders are consolidated into packing chutes • Size of the sorter system is fully scalable and expandable • Based on activity, the number of operators can be either increased or decreased
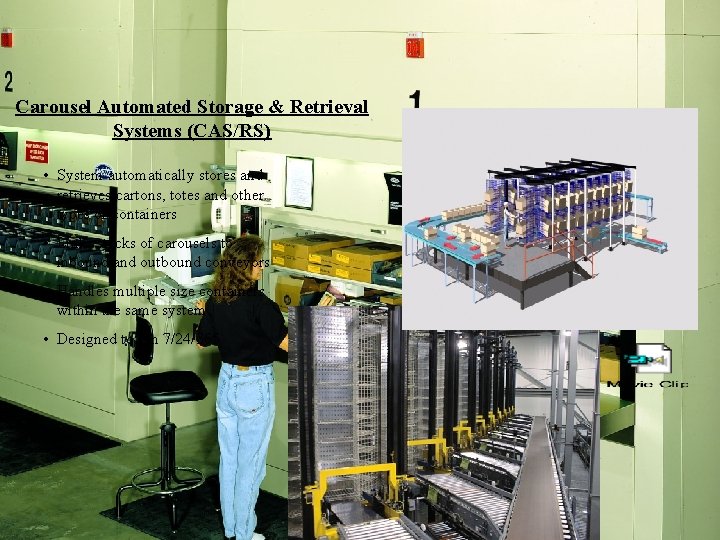
Carousel Automated Storage & Retrieval Systems (CAS/RS) • System automatically stores and retrieves cartons, totes and other types of containers • Links stacks of carousels to inbound and outbound conveyors • Handles multiple size containers within the same system • Designed to run 7/24/365
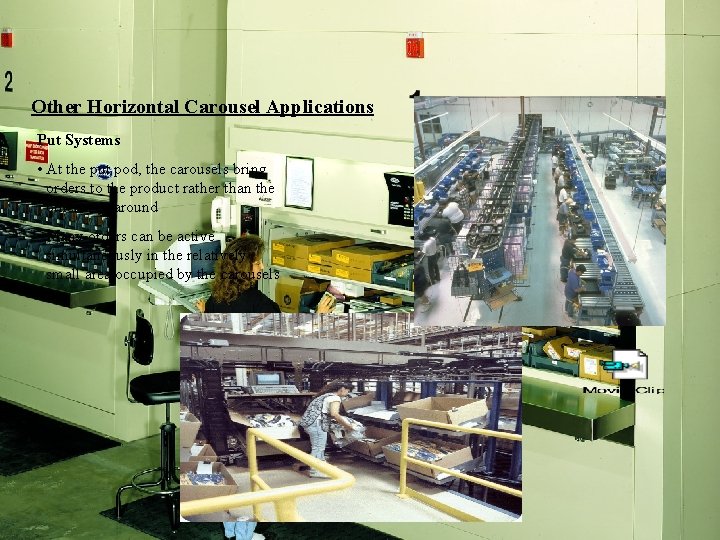
Other Horizontal Carousel Applications Put Systems • At the put pod, the carousels bring orders to the product rather than the other way around • Many orders can be active simultaneously in the relatively small area occupied by the carousels
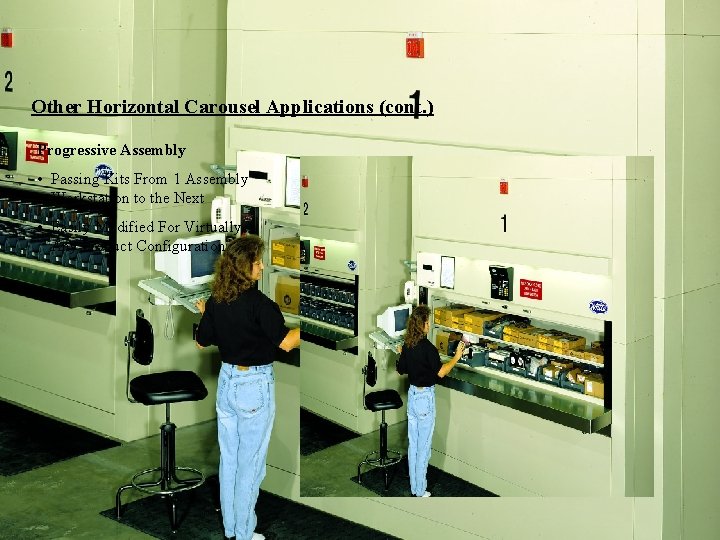
Other Horizontal Carousel Applications (cont. ) Progressive Assembly • Passing Kits From 1 Assembly Workstation to the Next • Easily Modified For Virtually Any Product Configuration
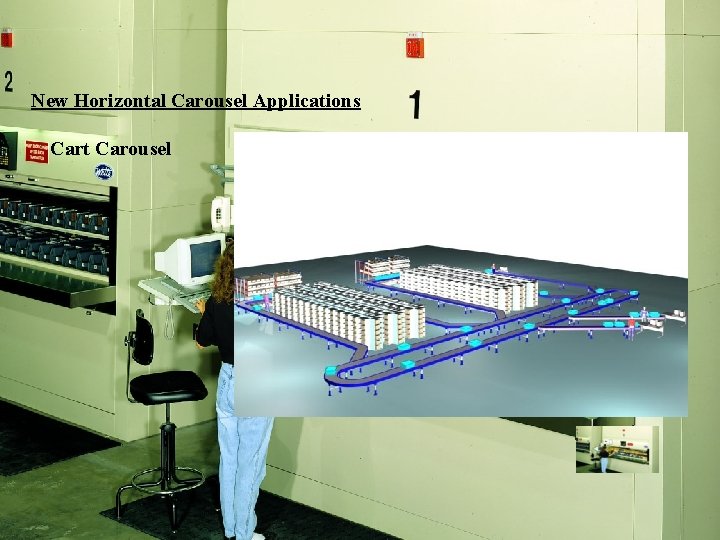
New Horizontal Carousel Applications Cart Carousel
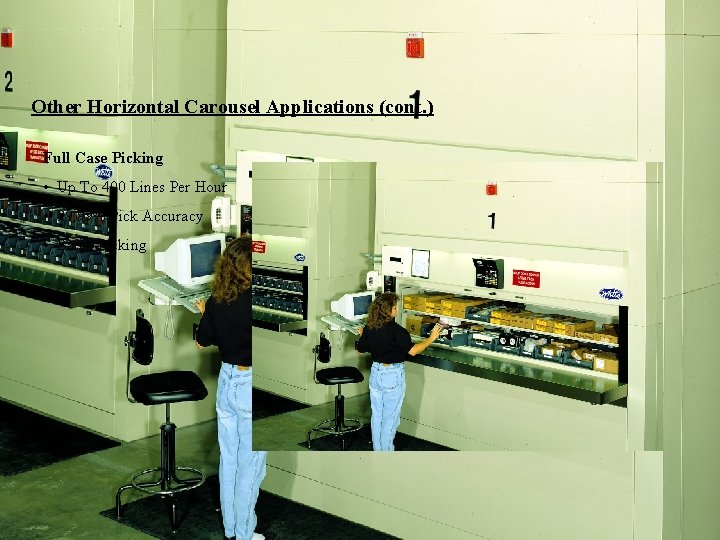
Other Horizontal Carousel Applications (cont. ) Full Case Picking • Up To 400 Lines Per Hour • 99. 99% Pick Accuracy • Batch Picking