Highly Stretchable and Sensitive Unidirectional Strain Sensor via
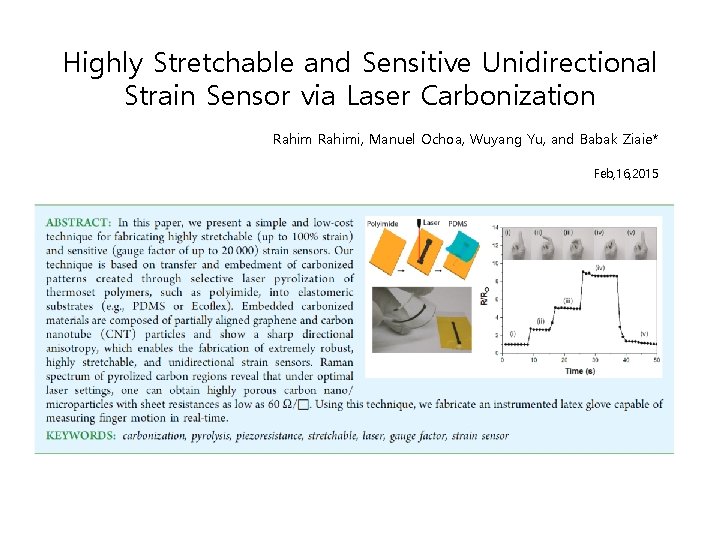
Highly Stretchable and Sensitive Unidirectional Strain Sensor via Laser Carbonization Rahimi, Manuel Ochoa, Wuyang Yu, and Babak Ziaie* Feb, 16, 2015
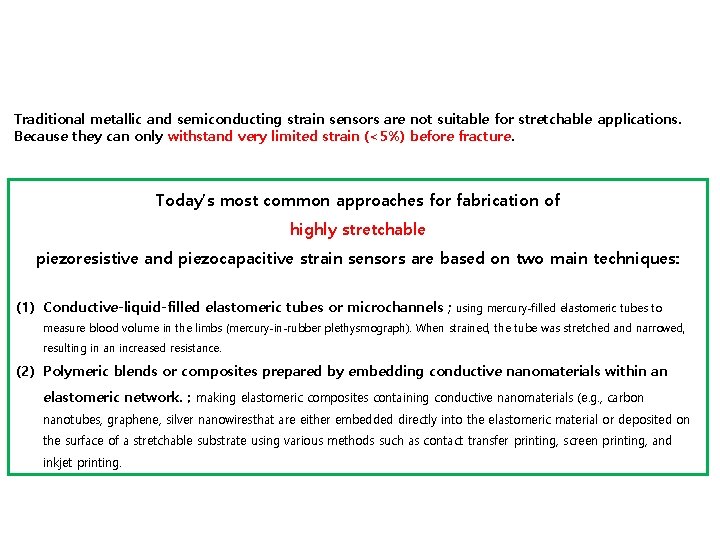
Traditional metallic and semiconducting strain sensors are not suitable for stretchable applications. Because they can only withstand very limited strain (<5%) before fracture. Today’s most common approaches for fabrication of highly stretchable piezoresistive and piezocapacitive strain sensors are based on two main techniques: (1) Conductive-liquid-filled elastomeric tubes or microchannels ; using mercury-filled elastomeric tubes to measure blood volume in the limbs (mercury-in-rubber plethysmograph). When strained, the tube was stretched and narrowed, resulting in an increased resistance. (2) Polymeric blends or composites prepared by embedding conductive nanomaterials within an elastomeric network. ; making elastomeric composites containing conductive nanomaterials (e. g. , carbon nanotubes, graphene, silver nanowiresthat are either embedded directly into the elastomeric material or deposited on the surface of a stretchable substrate using various methods such as contact transfer printing, screen printing, and inkjet printing.
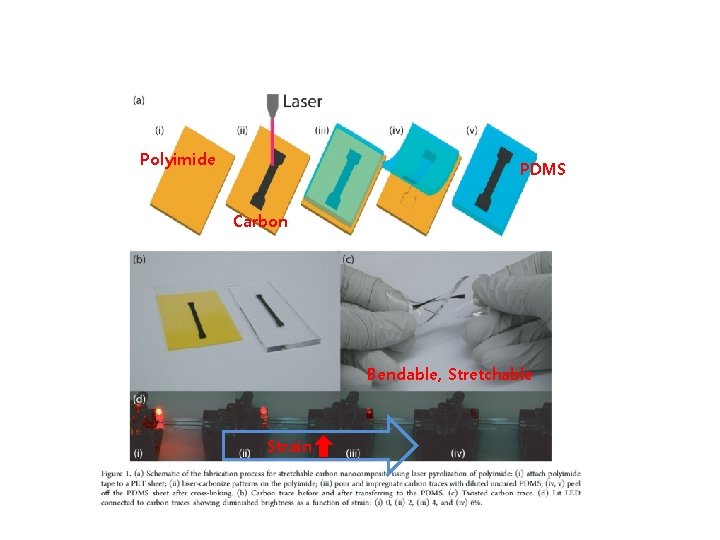
Polyimide PDMS Carbon Bendable, Stretchable Strain
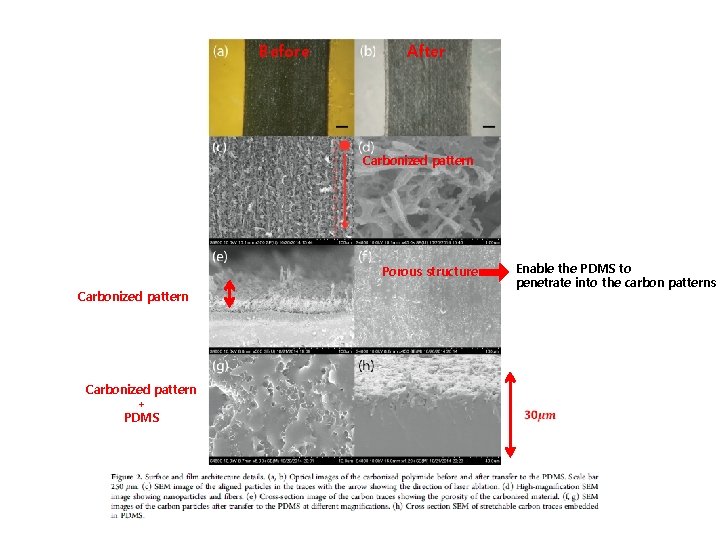
Before After Carbonized pattern Porous structure Carbonized pattern + PDMS Enable the PDMS to penetrate into the carbon patterns
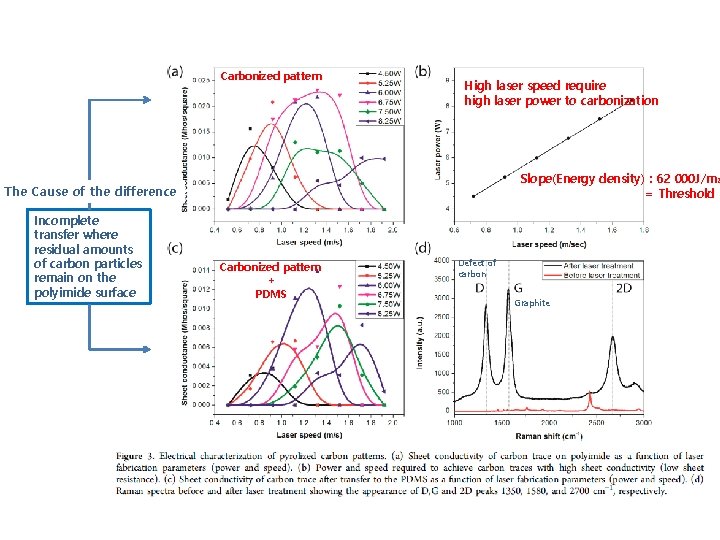
Carbonized pattern High laser speed require high laser power to carbonization Slope(Energy density) : 62 000 J/m 2 = Threshold The Cause of the difference Incomplete transfer where residual amounts of carbon particles remain on the polyimide surface Carbonized pattern + PDMS Defect of carbon Graphite
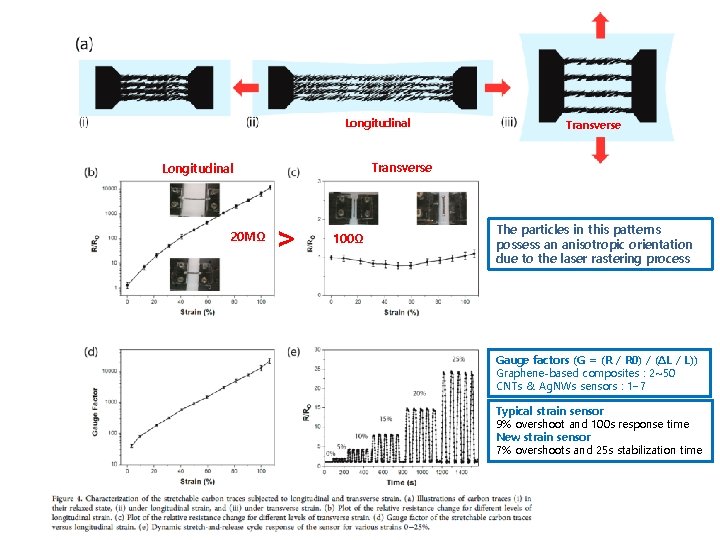
Longitudinal Transverse Longitudinal 20 MΩ Transverse > 100Ω The particles in this patterns possess an anisotropic orientation due to the laser rastering process Gauge factors (G = (R / R 0) / (ΔL / L)) Graphene-based composites : 2~50 CNTs & Ag. NWs sensors : 1− 7 Typical strain sensor 9% overshoot and 100 s response time New strain sensor 7% overshoots and 25 s stabilization time
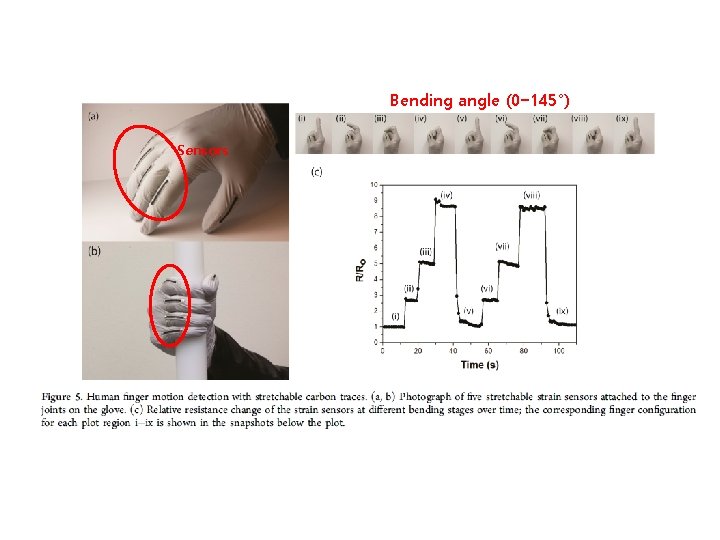
Bending angle (0− 145°) Sensors
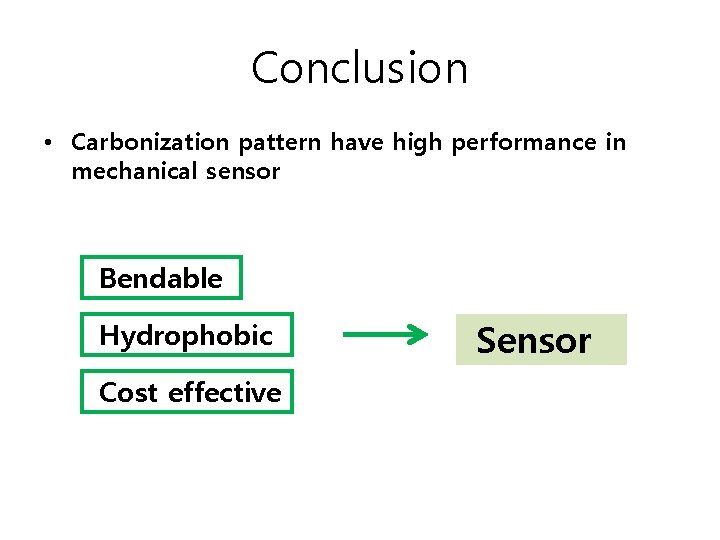
Conclusion • Carbonization pattern have high performance in mechanical sensor Bendable Hydrophobic Cost effective Sensor
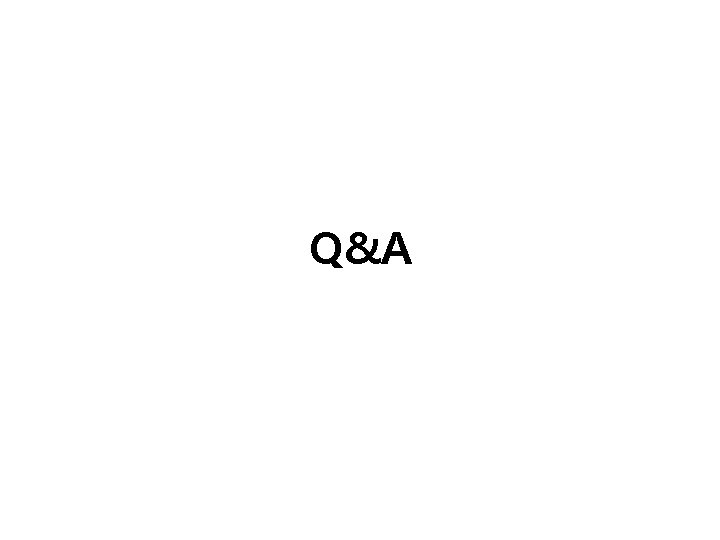
Q&A
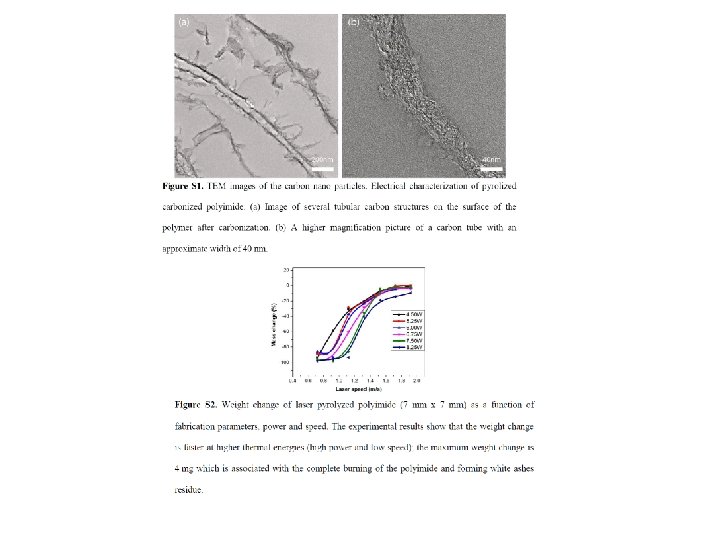
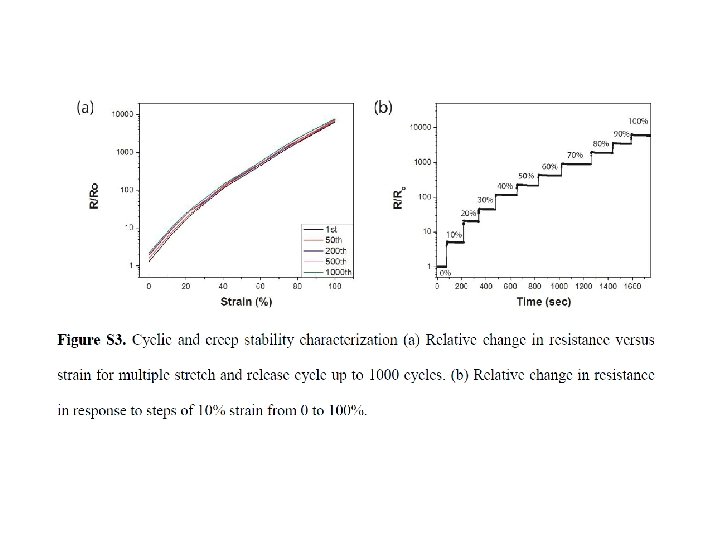
- Slides: 11